In the dynamic landscape of industrial machinery equipment manufacturing, the prowess of a workforce is paramount. The ability of employees to effectively operate, maintain, and innovate within this sector directly impacts the productivity, quality, and competitiveness of organizations.
In this context, the optimization of skills management emerges as a critical imperative for success. Industrial machinery equipment ERP systems stand at the forefront of this endeavor, offering a comprehensive suite of tools and functionalities designed to streamline skills management processes.
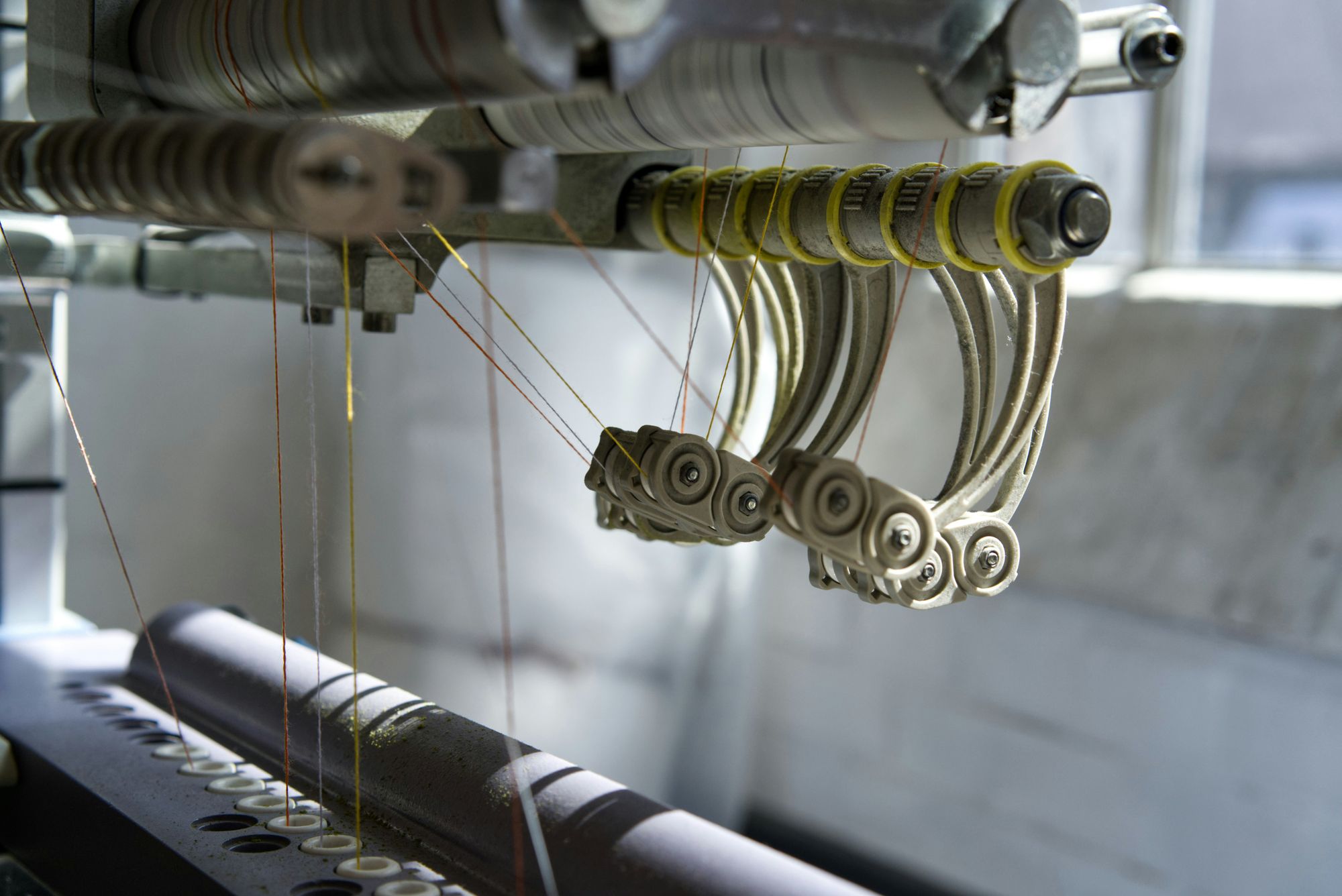
By seamlessly integrating skill tracking, training management, and performance evaluation within a centralized platform, industrial machinery equipment ERP solutions empower organizations to nurture talent, bridge skill gaps, and foster a highly skilled workforce.
This article delves into the significance of optimizing skills management with industrial machinery equipment ERP, exploring how these systems drive efficiency, enhance productivity, and propel growth in the industrial machinery equipment industry.
The topics covered in this article are:
- What is Skills Management?
- Importance of Optimizing Skills Management in Industrial Machinery Equipment Industry
- What is Industrial Machinery Equipment ERP?
- Optimizing Skills Management with Industrial Machinery Equipment ERP
- How can Deskera as an Industrial Machinery Equipment ERP Help in Optimizing Skills Management?
- Key Takeaways
- Related Articles
What is Skills Management?
Skillset management refers to the systematic process of identifying, acquiring, developing, and deploying the skills and competencies required for individuals to effectively perform their roles within an organization.
It involves assessing the existing skillsets of employees, identifying skill gaps, and implementing strategies to address these gaps through training, development programs, recruitment, or talent management initiatives.
Key components of skills management include:
- Skill Identification: This involves identifying the specific skills and competencies needed for various roles within the organization. These skills can be technical, such as machinery operation or software proficiency, or soft skills like communication and problem-solving abilities.
- Skill Assessment: Skills management involves assessing the current skill levels of employees through various methods such as performance evaluations, competency assessments, and skills tests. This helps in understanding the strengths and weaknesses of the workforce.
- Skill Development: Once skill gaps are identified, skillset management focuses on developing these skills through training programs, workshops, mentoring, on-the-job learning, or other learning initiatives. The goal is to enhance the capabilities of employees to meet the demands of their roles effectively.
- Skill Deployment: Skills management also involves deploying skilled employees to roles or projects where their abilities are best suited. This includes matching employees' skills with job requirements and ensuring that the right people are in the right positions to maximize productivity, profitability ratio and performance.
- Continuous Improvement: Skills management is an ongoing process that requires continuous monitoring and adjustment. It involves tracking changes in skill requirements, evolving technological advancements, and industry trends to ensure that the workforce remains adaptable and competitive.
Overall, effective skills management is essential for organizations to build a skilled and competent workforce capable of driving innovation, achieving business objectives, and maintaining a competitive edge in the marketplace.
Importance of Optimizing Skills Management in Industrial Machinery Equipment Industry
Optimizing skills management in the industrial machinery equipment industry is crucial for several reasons:
- Maximizing Operational Efficiency: Having employees with the right skills ensures that machinery and equipment are operated, maintained, and optimized efficiently. Skilled workers can identify issues, troubleshoot problems, and perform tasks more effectively, minimizing downtime and maximizing productivity.
- Ensuring Safety and Compliance: Skilled workers are better equipped to adhere to safety protocols and regulatory requirements associated with operating industrial machinery. Optimized skills management ensures that employees receive proper training and certification, reducing the risk of accidents and non-compliance with industry standards.
- Enhancing Product Quality: Skilled workers contribute to higher product quality by operating machinery correctly, detecting defects early, and implementing quality control measures effectively. Optimized skills management ensures that employees possess the necessary competencies to maintain quality standards throughout the manufacturing process.
- Reducing Costs: Investing in skills management can lead to cost savings by minimizing errors, reducing rework, and improving efficiency. Skilled workers are more adept at problem-solving and continuous innovation, leading to optimized processes and resource utilization.
- Supporting Technological Advancements: The industrial machinery equipment industry is constantly evolving with new technologies and advancements. Optimized skills management ensures that employees are trained to adapt to technological changes, operate advanced machinery, and utilize digital tools effectively.
- Fostering Employee Engagement and Retention: Employees are more engaged and satisfied when they receive opportunities for skill development and advancement. Optimized skills management promotes a culture of learning and growth, leading to higher employee retention, morale, and loyalty.
- Facilitating Flexibility and Adaptability: In today's rapidly changing business environment, organizations must be agile and adaptable. Optimized skills management enables organizations to quickly reallocate resources, train employees in new skills, and respond to market demands effectively.
- Driving Innovation and Competitiveness: Skilled employees are essential for driving innovation and maintaining competitiveness in the industrial machinery equipment industry. Optimized skills management fosters a workforce capable of implementing new technologies, improving processes, and staying ahead of competitors.
- Meeting Customer Expectations: Customers expect high-quality products, timely delivery, and excellent service from industrial machinery equipment manufacturers. Optimized skills management ensures that employees have the skills and knowledge needed to meet customer expectations and deliver superior products and services.
- Sustaining Long-Term Growth: Skills management is essential for sustaining long-term growth and success in the industrial machinery equipment industry. By investing in employee development and talent management initiatives, organizations can build a skilled workforce capable of driving innovation, adapting to change, and achieving strategic objectives over time.
What is Industrial Machinery Equipment ERP?
Industrial machinery equipment ERP (Enterprise Resource Planning) is a specialized software solution designed to meet the unique needs and requirements of companies operating in the industrial machinery and equipment manufacturing sector.
It integrates various business processes and functions within a single, centralized platform to streamline operations, improve efficiency, and enhance overall productivity.
Here are some key features and functionalities of industrial machinery equipment ERP:
- Manufacturing Operations Management: Industrial machinery ERP systems offer modules for managing manufacturing processes, including production planning, scheduling, and execution. It enables companies to optimize production workflows, track work orders, and monitor equipment utilization to meet production targets efficiently.
- Supply Chain Management: Manufacturing ERP systems for industrial machinery equipment provide tools for managing the supply chain, including procurement, inventory management, and supplier collaboration. It helps companies ensure the availability of raw materials, components, and parts needed for manufacturing while minimizing inventory costs and supply chain disruptions.
- Quality Management: Quality control is critical in the industrial machinery equipment industry to maintain product quality and compliance with industry standards. Manufacturing software systems include features for quality management, such as inspection tracking, non-conformance management, and corrective action workflows, to ensure that products meet or exceed quality requirements.
- Service and Maintenance Management: Industrial machinery equipment often requires regular maintenance and servicing to ensure optimal performance and reliability. MRP software systems include service management modules for scheduling maintenance activities, managing service contracts, and tracking equipment maintenance history to minimize downtime and extend equipment lifespan.
- Project Management: Many industrial machinery equipment manufacturers undertake complex projects involving custom-designed machinery or equipment. Manufacturing ERP systems include project management functionalities for planning, budgeting, resource allocation, and project tracking to ensure the successful execution of projects within scope, time, and budget constraints.
- Financial Management: Manufacturing software systems provide comprehensive financial management capabilities, including accounting, budgeting, invoicing, and financial reporting. It enables companies to manage financial transactions, track costs, and analyze financial performance to make informed business decisions and ensure regulatory compliance.
- Human Resource Management: Industrial machinery equipment ERP systems include modules for managing human resources, such as employee data management, payroll processing, workforce scheduling, and performance evaluation. It helps companies effectively manage their workforce and optimize labor utilization.
- Business Intelligence and Analytics: MRP software systems incorporate business intelligence and analytics tools to provide insights into business performance, trends, and opportunities. It enables companies to analyze data from various sources, generate reports, and make data-driven decisions to improve operational efficiency and drive business growth.
- Skills Management: Industrial machinery equipment ERP systems include modules for skills management, allowing companies to assess, track, and develop employee skills. These modules facilitate the identification of skill gaps, the creation of training programs, and the monitoring of employee progress. By integrating skills management into manufacturing ERP, organizations can ensure that employees have the necessary competencies to operate machinery effectively, troubleshoot issues, and perform tasks efficiently.
Overall, industrial machinery equipment ERP is a comprehensive software solution designed to address the specific needs and challenges of companies in the industrial machinery and equipment manufacturing sector.
By integrating various business functions and providing centralized data management, manufacturing ERP systems help companies streamline operations, improve visibility, and achieve greater control over their business processes.
Optimizing Skills Management with Industrial Machinery Equipment ERP
In the fast-paced realm of industrial machinery equipment manufacturing, the proficiency of the workforce plays a pivotal role in driving operational excellence and maintaining a competitive edge.
Leveraging industrial machinery equipment ERP systems for optimizing skills management emerges as a strategic imperative, offering a comprehensive approach to nurture talent, bridge skill gaps, and maximize workforce efficiency.
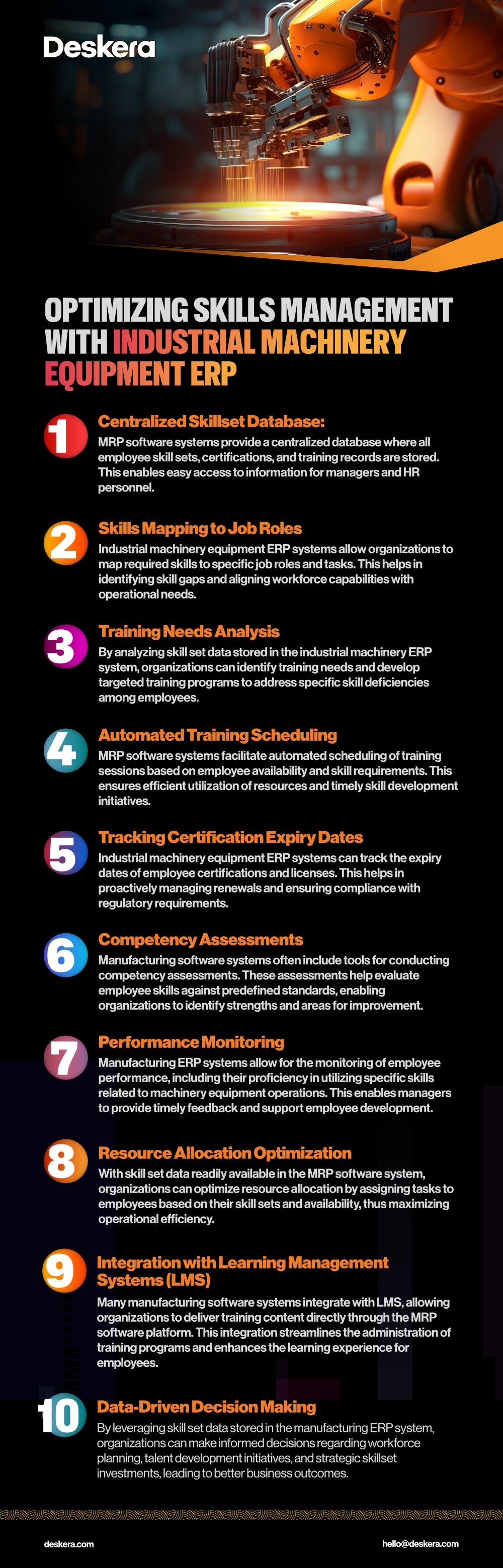
The 10 ways in which ERP for industrial equipment helps in optimizing skills management are:
Centralized Skillset Database
Optimizing skills management with industrial machinery equipment ERP involves leveraging the capabilities of ERP systems tailored specifically for the industrial machinery sector.
One key aspect of this optimization is the establishment of a centralized skillset database within the ERP environment. This centralized repository serves as a cornerstone for efficient skills management, enabling organizations to streamline operations and maximize workforce productivity.
In the realm of industrial machinery equipment ERP, having a centralized skillset database means consolidating all relevant information related to employee qualifications, certifications, and expertise into a single, easily accessible platform. This database encompasses various aspects of skills management, including proficiency in machinery operation, technical competencies, and specialized training.
With an industrial machinery ERP solution in place, companies can capitalize on the following benefits associated with a centralized skillset database:
- Streamlined Information Access: By housing skill set data within the manufacturing ERP system, organizations eliminate the need to sift through disparate sources or rely on manual record-keeping processes. This streamlines information access for HR personnel, managers, and employees alike.
- Efficient Skillset Tracking: ERP for industrial equipment offers robust capabilities for tracking employee skill sets over time. From initial onboarding to ongoing professional development, the manufacturing ERP platform maintains a comprehensive record of each employee's qualifications and training history.
- Enhanced Visibility and Transparency: With real-time visibility into skillset data, decision-makers can gain valuable insights into workforce capabilities and identify areas for improvement. This transparency fosters informed decision-making and strategic planning initiatives.
- Alignment with Operational Needs: By aligning skill sets with specific job roles and operational requirements, industrial machinery ERP systems ensure that employees possess the necessary competencies to perform their duties effectively. This alignment optimizes resource allocation and minimizes downtime associated with skills mismatches.
- Compliance Management: Manufacturing software solutions for industrial machinery equipment often include features for managing regulatory compliance and certifications. A centralized skillset database facilitates proactive monitoring of certification expiry dates and ensures adherence to industry standards and regulations.
- Integration with Manufacturing Software: The integration of skills management functionalities with core manufacturing software components, such as MRP and production scheduling modules, enables seamless coordination between workforce capabilities and production processes.
- Facilitation of Training Programs: Leveraging the centralized skillset database, organizations can develop targeted training programs tailored to address specific skill gaps or emerging industry trends. The MRP software platform simplifies the administration of these programs, from enrollment to tracking training progress and outcomes.
- Support for Talent Development Initiatives: With insights derived from skillset data analytics, organizations can implement strategic talent development initiatives aimed at nurturing high-potential employees and fostering a culture of continuous learning and improvement.
In conclusion, establishing a centralized skillset database within an industrial machinery ERP environment is essential for optimizing skills management in manufacturing settings.
By leveraging the capabilities of manufacturing ERP solutions tailored to the industrial machinery sector, organizations can enhance operational efficiency, ensure regulatory compliance, and drive workforce excellence.
Skills Mapping to Job Roles
Optimizing skills management with industrial machinery equipment ERP involves strategically mapping employee skill sets to specific job roles within manufacturing operations. This process is essential for ensuring that workforce capabilities align effectively with the demands of various tasks and responsibilities.
Leveraging an industrial machinery equipment ERP platform facilitates seamless skills mapping to job roles, offering numerous benefits for enhanced operational efficiency and workforce productivity.
In the context of industrial machinery ERP solutions, skillset mapping to job roles entails the following key aspects:
- Comprehensive Skill Assessment: Industrial machinery ERP systems enable organizations to conduct thorough assessments of employee skill sets. These assessments encompass technical competencies, machinery operation proficiency, specialized training, and certifications relevant to specific job functions.
- Identification of Job Role Requirements: By analyzing the skill requirements associated with different job roles within manufacturing operations, organizations can gain insights into the essential competencies and qualifications needed for optimal performance. This step involves understanding the intricacies of each role and its contribution to the overall production process.
- Alignment with Operational Needs: Industrial machinery ERP platforms facilitate the alignment of employee skill sets with the operational needs of the organization. By matching the capabilities of individual employees to the requirements of specific job roles, companies can optimize resource allocation, minimize skills gaps, and enhance workforce agility.
- Customized Job Role Profiles: Within the manufacturing software system, organizations can create customized profiles for each job role, outlining the requisite skills, qualifications, and experience levels. These profiles serve as a reference point for HR personnel and managers when assigning tasks and evaluating employee suitability for various positions.
- Dynamic Skills Matrix: Industrial machinery ERP solutions support the creation of dynamic skills matrices that depict the correlation between employee skill sets and job roles. These matrices evolve to accommodate changes in workforce capabilities, technological advancements, and shifting business priorities.
- Optimized Workforce Planning: By leveraging skills mapping capabilities within the ERP system, organizations can develop strategic workforce plans that align with long-term business objectives. This includes forecasting future skill requirements, identifying potential skill shortages, and implementing proactive talent development initiatives.
- Integration with MRP Software: ERP for industrial equipment seamlessly integrates with MRP software, enabling organizations to synchronize workforce capabilities with production schedules and material requirements. This integration ensures that the right personnel with the necessary skills are available to support manufacturing activities at all times.
- Continuous Skill Development: Skills mapping to job roles facilitates targeted training and development initiatives aimed at enhancing employee proficiency in key areas. Industrial machinery ERP systems enable organizations to identify skill gaps, prioritize training needs, and track the effectiveness of training programs over time.
- Enhanced Employee Engagement: Clear alignment between employee skill sets and job roles fosters a sense of purpose and accountability among workforce members. Employees feel valued when their skills are recognized and utilized effectively within the organization, leading to higher levels of engagement and job satisfaction.
- Data-Driven Decision Making: By leveraging skills mapping data stored within the manufacturing ERP system, organizations can make informed decisions regarding recruitment, promotion, and succession planning. These decisions are based on a comprehensive understanding of employee capabilities and their alignment with strategic business objectives.
In summary, skills mapping to job roles is a critical component of optimizing skills management with industrial machinery equipment ERP. By strategically aligning workforce capabilities with operational needs, organizations can drive efficiency, productivity, and innovation within their manufacturing operations.
Training Needs Analysis
Optimizing skills management with industrial machinery equipment ERP involves conducting a comprehensive analysis of training needs to ensure that employees possess the necessary competencies to perform their roles effectively within manufacturing operations.
Leveraging the capabilities of an industrial machinery ERP platform facilitates seamless training needs analysis, offering numerous benefits for enhancing workforce skills and driving operational excellence.
Here's how an industrial machinery equipment ERP system supports training needs analysis:
- Data-Driven Assessment: Manufacturing software systems provide a wealth of data related to employee skill sets, job roles, and performance metrics. By analyzing this data, organizations can identify skill gaps, trends, and areas for improvement, serving as a foundation for training needs assessment.
- Identification of Skill Deficiencies: Through the MRP software platform, organizations can pinpoint specific skill deficiencies among employees, whether related to machinery operation, technical knowledge, or safety protocols. This allows for targeted training interventions to address identified gaps effectively.
- Alignment with Business Objectives: ERP for industrial equipment enables organizations to align training needs analysis with strategic business objectives. By understanding the skills required to support key initiatives and production goals, companies can prioritize training efforts accordingly.
- Regulatory Compliance Management: Manufacturing ERP systems incorporate features for managing regulatory compliance and certification requirements. Training needs analysis ensures that employees receive the necessary training to maintain compliance with industry standards and safety regulations.
- Integration with Learning Management Systems (LMS): Many Industrial Machinery Equipment ERP platforms seamlessly integrate with Learning Management Systems (LMS). This integration streamlines the administration of training programs, from course enrollment to tracking progress and assessing outcomes, ensuring efficient training needs analysis and delivery.
- Resource Optimization: By accurately assessing training needs, organizations can optimize resource allocation for training initiatives. This includes allocating budgetary resources, scheduling training sessions, and assigning trainers based on identified skill gaps and priority areas.
- Continuous Improvement: Training needs analysis is an iterative process that evolves. Industrial machinery ERP systems support continuous improvement by providing mechanisms for ongoing assessment, feedback collection, and adjustment of training programs based on changing business needs and employee development.
- Tailored Training Programs: With insights derived from training needs analysis, organizations can develop tailored training programs that address specific skill gaps and learning objectives. These programs may include a combination of classroom instruction, hands-on training, e-learning modules, and mentorship opportunities.
- Performance Monitoring and Evaluation: Industrial machinery equipment ERP systems enable organizations to monitor the effectiveness of training programs through performance tracking and evaluation metrics. This feedback loop allows for the refinement of training initiatives based on observed outcomes and employee feedback.
- Employee Engagement and Retention: Investing in training needs analysis and development demonstrates a commitment to employee growth and development, leading to higher levels of engagement and retention. Employees are more likely to stay with organizations that provide opportunities for skill enhancement and career advancement.
In summary, training needs analysis is a crucial component of optimizing skillset management with industrial machinery equipment ERP. By leveraging the capabilities of manufacturing ERP systems tailored to the manufacturing sector, organizations can identify skill gaps, prioritize training initiatives, and empower employees to achieve their full potential within the workplace.
Automated Training Scheduling
Automated training scheduling is a pivotal feature of industrial machinery equipment ERP systems, streamlining the process of planning, organizing, and managing training sessions for employees.
This functionality enhances skills management within manufacturing organizations by ensuring that training initiatives are efficiently executed and aligned with workforce development goals.
Let's delve into how automated training scheduling optimizes skills management within the realm of industrial machinery ERP:
- Efficient Resource Utilization: Industrial machinery equipment ERP systems automate the scheduling of training sessions based on factors such as employee availability, skill requirements, and resource availability. This ensures optimal utilization of training facilities, trainers, and other resources, minimizing downtime and maximizing productivity.
- Real-time Visibility: With automated training scheduling, managers and HR personnel have real-time visibility into the training calendar within the manufacturing software system. This enables them to quickly assess training availability, allocate resources, and make informed decisions regarding employee development initiatives.
- Adaptability to Changing Needs: Industrial machinery ERP platforms allow organizations to adapt training schedules dynamically in response to changing business needs, employee skill gaps, or production priorities. This agility ensures that training efforts remain aligned with evolving organizational objectives.
- Integration with Employee Profiles: Automated training scheduling seamlessly integrates with employee profiles stored within the MRP software system, enabling organizations to identify training needs based on individual skill sets, job roles, and career development goals. This personalized approach enhances the relevance and effectiveness of training programs.
- Compliance Management: ERP for industrial equipment incorporates features for managing regulatory compliance and certification requirements. Automated training scheduling ensures that employees receive mandatory training within specified timeframes, helping organizations maintain compliance with industry standards and regulations.
- Streamlined Communication: Automated training scheduling streamlines communication by sending notifications, reminders, and updates to employees regarding upcoming training sessions. This ensures that employees are adequately prepared and informed, leading to higher engagement and participation rates.
- Centralized Training Records: Training scheduling automation centralizes training records within the manufacturing ERP system, providing a comprehensive repository of completed and upcoming training activities. This facilitates easy access to training history, progress tracking, and compliance reporting for auditing purposes.
- Efficient Training Program Management: Industrial machinery equipment ERP systems support the efficient management of training programs by automating tasks such as registration, attendance tracking, and evaluation. This reduces administrative overhead, allowing trainers and administrators to focus on delivering high-quality training experiences.
- Optimized Workforce Development: By automating training scheduling, industrial machinery ERP systems enable organizations to strategically plan and execute workforce development initiatives. This includes identifying priority areas for skill enhancement, scheduling relevant training sessions, and measuring the impact of training on employee performance and productivity.
- Continuous Improvement: Automated training scheduling facilitates continuous improvement by providing data-driven insights into training effectiveness, employee feedback, and skill development trends. This information empowers organizations to refine their training strategies over time, ensuring that skillset management efforts remain aligned with business objectives.
In summary, automated training scheduling is a critical component of skills management within industrial machinery equipment ERP systems. By automating the process of planning, organizing, and managing training initiatives, organizations can enhance workforce development, maintain compliance, and drive operational excellence within the manufacturing sector.
Tracking Certification Expiry Dates
Optimizing skills management with Industrial Machinery Equipment ERP involves efficiently tracking certification expiry dates to ensure that employees maintain the necessary qualifications and credentials for their roles within manufacturing operations.
Leveraging an industrial machinery equipment ERP platform streamlines this process, providing numerous benefits for compliance management, workforce readiness, and operational continuity.
Here's how tracking certification expiry dates optimize skills management within the realm of industrial machinery equipment ERP:
- Compliance Assurance: Industrial machinery equipment ERP systems automate the tracking of certification expiry dates, ensuring that employees remain compliant with industry regulations, safety standards, and licensing requirements. This proactive approach helps organizations avoid penalties, fines, and regulatory non-compliance issues.
- Alerts and Notifications: Manufacturing ERP platforms for industrial machinery equipment send alerts and notifications to relevant stakeholders, such as HR managers and supervisors, regarding upcoming certification expirations. This ensures timely action to renew certifications, schedule refresher courses, or update training as needed.
- Centralized Certification Records: By centralizing certification records within the MRP software system, organizations have a comprehensive overview of employee credentials, expiry dates, and renewal statuses. This centralized repository simplifies record-keeping, audit preparation, and compliance reporting processes.
- Integration with Employee Profiles: Tracking certification expiry dates seamlessly integrates with employee profiles stored within the industrial machinery ERP system. This allows organizations to link certifications to individual employee records, facilitating easy access to relevant information and ensuring accurate skillset management.
- Risk Mitigation: Timely tracking of certification expiry dates mitigates the risk of workforce shortages or disruptions due to expired credentials. By proactively managing certifications, organizations minimize the potential impact on production schedules, project timelines, and overall operational efficiency.
- Resource Planning: Industrial machinery equipment ERP systems leverage certification expiry data to inform resource planning and allocation decisions. By identifying upcoming expirations, organizations can allocate resources for training, certification renewal, or workforce development initiatives as needed, ensuring uninterrupted operations.
- Training Needs Analysis: Tracking certification expiry dates enables organizations to conduct ongoing training needs analysis based on evolving skill requirements and regulatory changes. This data-driven approach ensures that training programs remain relevant, effective, and aligned with organizational objectives.
- Employee Development: ERP for industrial equipment supports employee development initiatives by tracking certification expiry dates and facilitating ongoing skill enhancement. By identifying skill gaps and renewal deadlines, organizations can provide targeted training opportunities to support career growth and advancement.
- Audit Preparedness: Centralized tracking of certification expiry dates within the manufacturing ERP system simplifies audit preparation and compliance verification processes. Organizations can quickly generate reports, documentation, and evidence of employee certifications to demonstrate adherence to regulatory requirements.
- Continuous Improvement: By continuously monitoring and tracking certification expiry dates, organizations can identify opportunities for process improvement, efficiency gains, and cost savings. This data-driven approach enables organizations to refine their skillset management strategies and adapt to changing industry dynamics effectively.
In summary, tracking certification expiry dates is a crucial aspect of optimizing skills management with industrial machinery equipment ERP.
By leveraging the capabilities of manufacturing ERP systems tailored to the manufacturing sector, organizations can ensure compliance, mitigate risks, and empower employees to maintain the skills necessary for success in their roles within industrial machinery operations.
Competency Assessments
Optimizing skills management with industrial machinery equipment ERP involves conducting competency assessments to evaluate employee skills and proficiency levels in various aspects related to machinery operations and industrial processes.
Leveraging the competency assessment features within an industrial machinery equipment ERP platform offers several benefits for skills management, workforce development, and operational excellence.
Here's how competency assessments optimize skillset management within the realm of industrial machinery equipment ERP:
- Objective Evaluation: Industrial machinery equipment ERP systems provide structured competency assessment frameworks that enable objective evaluation of employee skills. This ensures consistency and fairness in assessing skill levels across the workforce.
- Customized Assessment Criteria: Competency assessments within manufacturing ERP platforms for industrial machinery equipment allow organizations to define customized assessment criteria tailored to specific job roles, tasks, and performance expectations. This ensures that assessments accurately reflect the skills required for success in each position.
- Identification of Skill Gaps: Competency assessments help organizations identify skill gaps and areas for improvement among employees. By pinpointing areas of weakness or deficiency, organizations can develop targeted training programs to address these gaps and enhance workforce capabilities.
- Benchmarking Performance: Industrial machinery ERP systems enable organizations to benchmark employee performance against predefined competency standards or industry best practices. This allows for comparisons across teams, departments, or organizational units, highlighting areas of excellence and areas needing improvement.
- Strategic Workforce Planning: Competency assessment data serves as a valuable input for strategic workforce planning initiatives. By understanding the skill distribution and proficiency levels within the workforce, organizations can align talent management strategies with business objectives and future skill requirements.
- Performance Improvement Plans: Competency assessments help identify employees who may benefit from performance improvement plans or targeted development interventions. These plans can include additional training, coaching, or mentoring to enhance employee skills and performance levels.
- Succession Planning: ERP for industrial equipment supports succession planning efforts by providing insights into employee readiness and potential for advancement. Competency assessments help identify high-potential employees who may be groomed for future leadership roles within the organization.
- Feedback and Developmental Opportunities: Competency assessments facilitate constructive feedback discussions between managers and employees regarding skill strengths, areas for improvement, and career development opportunities. This feedback loop fosters a culture of continuous learning and skill enhancement within the organization.
- Compliance Management: Competency assessments within manufacturing ERP systems help ensure compliance with industry regulations, safety standards, and certification requirements. By assessing employee competence in relevant areas, organizations can demonstrate compliance with regulatory mandates and accreditation standards.
- Data-Driven Decision-Making: Competency assessment data generated within the manufacturing software system serves as valuable input for data-driven decision-making. By analyzing trends and patterns in employee skills and performance, organizations can make informed decisions regarding talent management, training investments, and strategic initiatives.
In summary, competency assessments play a vital role in optimizing skills management with industrial machinery equipment ERP. By leveraging the competency assessment features within MRP software platforms, organizations can enhance workforce capabilities, drive performance improvements, and achieve operational excellence in manufacturing environments.
Performance Monitoring
Optimizing skills management with industrial machinery equipment ERP involves implementing robust performance monitoring mechanisms to track and evaluate employee performance regarding their skill sets and job responsibilities.
Leveraging the performance monitoring features within an industrial machinery equipment ERP platform offers numerous benefits for skills management, talent development, and operational efficiency.
Here's how performance monitoring optimizes skillset management within the realm of industrial machinery ERP:
- Real-Time Performance Tracking: Industrial machinery equipment ERP systems enable real-time monitoring of employee performance, allowing managers to track productivity, efficiency, and adherence to quality standards. This real-time feedback facilitates timely intervention and corrective action when performance issues arise.
- Alignment with Key Performance Indicators (KPIs): Performance monitoring within manufacturing ERP platforms for industrial machinery equipment allows organizations to align performance metrics with key business objectives and KPIs. This ensures that performance evaluations focus on outcomes that are directly relevant to organizational success.
- Skill-Specific Performance Metrics: Industrial machinery ERP systems facilitate the tracking of skill-specific performance metrics, allowing organizations to assess employee proficiency levels in key areas related to machinery operation, technical expertise, and process efficiency.
- Identification of Training Needs: Performance monitoring helps identify employees who may benefit from additional training or skill development initiatives. By analyzing performance data, organizations can pinpoint skill gaps and prioritize training interventions to address areas of weakness.
- Continuous Feedback Loops: Manufacturing software platforms support continuous feedback loops between managers and employees, fostering a culture of performance improvement and skill development. Regular performance reviews and constructive feedback discussions enable employees to understand expectations and identify growth opportunities.
- Goal Setting and Performance Management: Performance monitoring within industrial machinery equipment ERP systems facilitates goal setting and performance management processes. By setting clear performance objectives aligned with skill set requirements, organizations can evaluate employee progress and provide targeted support as needed.
- Data-Driven Insights: Performance monitoring generates valuable data and insights that inform decision-making processes related to skills management and talent development. By analyzing performance trends and patterns, organizations can identify opportunities for process optimization, resource allocation, and skill enhancement.
- Reward and Recognition Programs: Manufacturing software platforms enable organizations to implement reward and recognition programs based on performance metrics and skill achievements. Recognizing employees who demonstrate exceptional skills and performance reinforces desired behaviors and motivates others to excel.
- Succession Planning and Career Development: Performance monitoring data serves as a basis for succession planning and career development initiatives within the organization. By identifying high-potential employees and assessing their readiness for advancement, organizations can groom future leaders and ensure a pipeline of skilled talent.
- Compliance Monitoring: Performance monitoring within industrial machinery equipment ERP systems helps ensure compliance with industry regulations, safety standards, and quality requirements. By monitoring performance metrics related to compliance, organizations can identify areas of non-conformance and take corrective action to mitigate risks.
In summary, performance monitoring is a critical component of optimizing skills management with industrial machinery equipment ERP. By leveraging performance monitoring features within MRP software platforms, organizations can enhance employee productivity, drive performance improvements, and achieve operational excellence in manufacturing environments.
Resource Allocation Optimization
Optimizing skills management with industrial machinery equipment ERP involves efficiently allocating resources, including human capital, to maximize productivity and operational efficiency.
Leveraging the resource allocation optimization features within an industrial machinery equipment ERP platform offers several benefits for skills management, workforce productivity, and overall business performance.
Here's how resource allocation optimization contributes to skillset management within the realm of industrial machinery equipment ERP:
- Skill-Based Resource Matching: Industrial machinery equipment ERP systems facilitate the matching of employee skill sets with specific tasks or projects. By aligning workforce capabilities with job requirements, organizations can ensure optimal resource allocation and maximize productivity.
- Dynamic Resource Planning: Manufacturing ERP platforms for industrial machinery equipment support dynamic resource planning processes, allowing organizations to adapt resource allocation strategies in response to changing demand, skill requirements, and production priorities.
- Real-Time Resource Visibility: ERP for industrial equipment provides real-time visibility into resource availability, including employee skills, availability, and workload. This enables managers to make informed decisions regarding resource allocation and workforce deployment.
- Efficient Workforce Utilization: Resource allocation optimization within manufacturing software platforms helps organizations optimize workforce utilization by assigning tasks to employees based on their skillsets, availability, and expertise. This ensures that employees are deployed effectively, minimizing downtime and maximizing productivity.
- Balanced Workload Distribution: MRP software systems enable organizations to distribute workloads evenly among employees, taking into account factors such as skill levels, experience, and capacity. This balanced workload distribution promotes fairness, reduces burnout, and enhances employee satisfaction.
- Cost Reduction: By optimizing resource allocation, industrial machinery ERP systems help organizations minimize costs associated with overstaffing, overtime, and idle time. This cost reduction contributes to improved profitability and operational efficiency.
- Cross-Training Opportunities: Resource allocation optimization facilitates cross-training initiatives, where employees are trained to perform multiple tasks or roles within the organization. This enhances workforce flexibility, reduces dependency on specific individuals, and mitigates risks associated with skill shortages.
- Strategic Talent Deployment: Manufacturing ERP platforms support strategic talent deployment by identifying employees with specialized skills or certifications needed for specific projects or initiatives. This strategic deployment ensures that the right people with the right skills are assigned to critical tasks, driving project success and organizational performance.
- Resource Forecasting: Industrial machinery ERP systems enable organizations to forecast resource requirements based on historical data, demand projections, and anticipated skill needs. This proactive approach allows organizations to anticipate resource constraints and plan accordingly, minimizing disruptions to operations.
- Continuous Improvement: By analyzing resource allocation data and performance metrics, organizations can identify opportunities for continuous improvement in skills management processes. This data-driven approach enables organizations to refine resource allocation strategies, optimize workforce utilization, and enhance overall operational effectiveness.
In summary, resource allocation optimization is essential for optimizing skills management with industrial machinery equipment ERP. By leveraging the resource allocation optimization features within manufacturing ERP platforms, organizations can maximize productivity, minimize costs, and achieve operational excellence in manufacturing environments.
Integration with Learning Management System
Optimizing skills management with industrial machinery equipment ERP involves seamless integration with Learning Management Systems (LMS) to facilitate efficient training and development initiatives.
Leveraging the integration capabilities between an industrial machinery equipment ERP and LMS offers numerous benefits for skillset management, employee training, and workforce development.
Here's how integration with a learning management system contributes to skills management within the realm of industrial machinery equipment ERP:
- Centralized Training Platform: Integration with LMS enables organizations to centralize training resources, courses, and materials within the industrial machinery equipment ERP platform. This centralized approach streamlines access to training content and ensures consistency in training delivery.
- Unified Skills Management: By integrating the LMS with the industrial machinery ERP, organizations can unify skillset management processes with training initiatives. This integration allows for seamless alignment between employee skill profiles, training needs, and competency assessments.
- Automated Training Enrollment: Integration between the manufacturing ERP and LMS automates the process of training enrollment, allowing employees to easily sign up for relevant courses directly within the manufacturing software platform. This automation saves time and eliminates manual administrative tasks associated with managing training registrations.
- Tracking Training Progress: Industrial machinery ERP systems integrated with LMS platforms enable organizations to track training progress and completion status in real time. This visibility into training activities facilitates ongoing monitoring of skill development and ensures compliance with training requirements.
- Personalized Learning Paths: Integration with an LMS allows organizations to create personalized learning paths tailored to individual employee skill sets, job roles, and career development goals. Employees can access customized training modules designed to address their specific skill gaps and professional development needs.
- Efficient Content Delivery: The integration between ERP for industrial equipment and LMS streamlines the delivery of training content, whether through e-learning modules, virtual classrooms, or instructor-led sessions. This efficiency ensures that employees have access to relevant training materials whenever and wherever they need them.
- Competency-Based Training: Industrial machinery equipment ERP systems integrated with LMS platforms support competency-based training initiatives. Employees can undergo training programs targeted at developing specific skills required for their roles, with progress tracked and assessed within the manufacturing ERP environment.
- Certification Management: Integration with an LMS enables organizations to manage certifications, licenses, and credentials within the industrial machinery ERP system. Employees can complete training modules, assessments, and exams to earn certifications directly through the manufacturing software platform.
- Data Synchronization: Integration between the MRP software and LMS ensures seamless data synchronization, eliminating discrepancies between employee skill profiles and training records. This synchronization enables accurate reporting, analytics, and decision-making regarding skills management and training effectiveness.
- Continuous Improvement: By integrating the manufacturing ERP with an LMS, organizations can continuously improve their skills management processes and training programs based on data-driven insights. Analyzing training outcomes and performance metrics allows for iterative refinement of training initiatives to optimize skill development and workforce capabilities.
In summary, integration with a learning management system is instrumental in optimizing skillset management with industrial machinery equipment ERP. By leveraging the capabilities of both systems, organizations can enhance training effectiveness, improve workforce skills, and drive operational excellence in manufacturing environments.
Data-Driven Decision Making
Optimizing skills management with industrial machinery equipment ERP involves leveraging data-driven decision-making processes to effectively manage and develop the workforce.
By utilizing the analytical capabilities of industrial machinery equipment ERP systems, organizations can make informed decisions regarding skills management strategies, training initiatives, and talent development programs.
Here's how data-driven decision-making contributes to skills management within the realm of industrial machinery equipment ERP:
- Skillset Analytics: Industrial machinery equipment ERP systems provide robust analytics tools that enable organizations to analyze employee skill sets, proficiency levels, and competency gaps. By leveraging skillset analytics, organizations can gain insights into the current capabilities of their workforce and identify areas for improvement.
- Training Effectiveness Evaluation: Data-driven decision-making allows organizations to evaluate the effectiveness of training programs based on performance metrics, completion rates, and skill acquisition outcomes. By analyzing training effectiveness, organizations can refine their training initiatives to better meet skill development goals.
- Resource Allocation Optimization: Industrial machinery equipment ERP systems enable data-driven optimization of resource allocation for training initiatives. By analyzing skill set data alongside resource availability and business objectives, organizations can allocate resources efficiently to support skill development efforts.
- Talent Identification and Development: Data-driven decision-making facilitates the identification of high-potential employees and the development of tailored talent development plans. By analyzing performance data, skill assessments, and career aspirations, organizations can nurture talent and prepare employees for future roles.
- Predictive Analytics for Skill Needs: ERP for industrial equipment leverages predictive analytics to forecast future skill needs based on business projections, technological advancements, and industry trends. By anticipating skill requirements, organizations can proactively develop training programs to address future workforce needs.
- Benchmarking and Best Practices: Data-driven decision-making enables organizations to benchmark employee skill sets against industry standards and best practices. By comparing skill levels with industry benchmarks, organizations can identify areas where skill development is needed to remain competitive.
- Compliance Monitoring and Reporting: Industrial machinery ERP systems facilitate data-driven compliance monitoring and reporting by tracking employee certifications, licensing requirements, and regulatory standards. By analyzing compliance data, organizations can ensure that employees maintain the necessary qualifications to meet industry regulations.
- Performance Management and Feedback: Data-driven decision-making supports performance management initiatives by providing insights into employee performance trends, skill gaps, and areas for improvement. By analyzing performance data, organizations can provide targeted feedback and coaching to enhance employee skills and productivity.
- Continuous Improvement Initiatives: Data-driven decision-making fosters a culture of continuous improvement within organizations by providing actionable insights into skills management processes. By analyzing data on training outcomes, performance metrics, and workforce capabilities, organizations can identify opportunities for refinement and enhancement.
- Strategic Planning and Alignment: Data-driven decision-making enables organizations to align skills management strategies with broader business objectives and strategic priorities. By analyzing data on workforce capabilities alongside organizational goals, organizations can develop targeted skill development initiatives that support overall business success.
In summary, data-driven decision-making is essential for optimizing skills management with industrial machinery equipment ERP. By leveraging data analytics tools and insights, organizations can make informed decisions regarding training, talent development, resource allocation, and strategic planning, ultimately driving workforce excellence and operational efficiency.
How can Deskera as an Industrial Machinery Equipment ERP Help in Optimizing Skills Management?
Deskera, as an industrial machinery equipment ERP solution, can significantly contribute to optimizing skills management within manufacturing organizations.
Here's how Deskera can help:
- Skill Tracking and Assessment: Deskera provides modules for tracking and assessing employee skills. Managers can easily identify skill gaps and areas for improvement through comprehensive skill assessments, enabling targeted training initiatives.
- Competency Mapping: Deskera facilitates competency mapping by aligning employee skills with job roles and responsibilities. This ensures that employees are assigned tasks that match their competencies, maximizing productivity and performance.
- Performance Evaluation: Deskera enables performance evaluations based on predefined skill criteria. Managers can assess employee performance against skill benchmarks, providing valuable feedback for skill development and career progression.
- Resource Allocation Optimization: Deskera optimizes resource allocation by matching employee skill sets with project requirements. This ensures that projects are staffed with the right talent, minimizing bottlenecks and enhancing project outcomes.
- Integration with Learning Management Systems: Deskera seamlessly integrates with LMS, allowing organizations to leverage external training resources and content. This integration enhances the breadth and depth of training programs available to employees.
- Data-Driven Insights: Deskera provides data-driven insights into skillset management through advanced analytics and reporting capabilities. Organizations can analyze skill trends, identify training needs, and track skill development progress over time.
- Succession Planning: Deskera supports succession planning initiatives by identifying high-potential employees and assessing their readiness for advancement. Organizations can groom future leaders by providing targeted development opportunities based on skills assessments.
- Continuous Improvement: Deskera fosters a culture of continuous improvement by facilitating ongoing skills assessments and development initiatives. Organizations can adapt quickly to changing business needs and technological advancements, ensuring that employees remain competitive in the industrial machinery equipment industry.
Key Takeaways
Optimizing skills management with industrial machinery equipment ERP is essential for organizations operating in this dynamic and competitive industry.
The 10 ways in which industrial machinery equipment ERP helps in optimizing skills management are:
- Centralized Skillset Database: MRP software systems provide a centralized database where all employee skill sets, certifications, and training records are stored. This enables easy access to information for managers and HR personnel, streamlining skillset management processes.
- Skills Mapping to Job Roles: Manufacturing ERP systems allow organizations to map required skills to specific job roles and tasks. This helps in identifying skill gaps and aligning workforce capabilities with operational needs.
- Training Needs Analysis: By analyzing skill set data stored in the industrial machinery ERP system, organizations can identify training needs and develop targeted training programs to address specific skill deficiencies among employees.
- Automated Training Scheduling: MRP software systems facilitate the automated scheduling of training sessions based on employee availability and skill requirements. This ensures efficient utilization of resources and timely skill development initiatives.
- Tracking Certification Expiry Dates: Manufacturing ERP systems can track the expiry dates of employee certifications and licenses. This helps in proactively managing renewals and ensuring compliance with regulatory requirements.
- Competency Assessments: Manufacturing software systems often include tools for conducting competency assessments. These assessments help evaluate employee skills against predefined standards, enabling organizations to identify strengths and areas for improvement.
- Performance Monitoring: Manufacturing ERP systems allow for the monitoring of employee performance, including their proficiency in utilizing specific skills related to machinery equipment operations. This enables managers to provide timely feedback and support employee development.
- Resource Allocation Optimization: With skill set data readily available in the MRP software system, organizations can optimize resource allocation by assigning tasks to employees based on their skill sets and availability, thus maximizing operational efficiency.
- Integration with Learning Management Systems (LMS): Many manufacturing software systems integrate with LMS, allowing organizations to deliver training content directly through the MRP software platform. This integration streamlines the administration of training programs and enhances the learning experience for employees.
- Data-Driven Decision Making: By leveraging skill set data stored in the manufacturing ERP system, organizations can make informed decisions regarding workforce planning, talent development initiatives, and strategic skillset investments, leading to better business outcomes.
As technology continues to evolve and industry requirements change, investing in skills management with industrial machinery ERP becomes increasingly imperative for organizations seeking sustainable growth and success in the industrial machinery equipment sector.
In summary, Deskera serves as a comprehensive solution for optimizing skills management within industrial machinery equipment manufacturing organizations. By leveraging Deskera's features and capabilities, companies can enhance workforce capabilities, drive operational efficiency, and achieve business excellence.
Related Articles
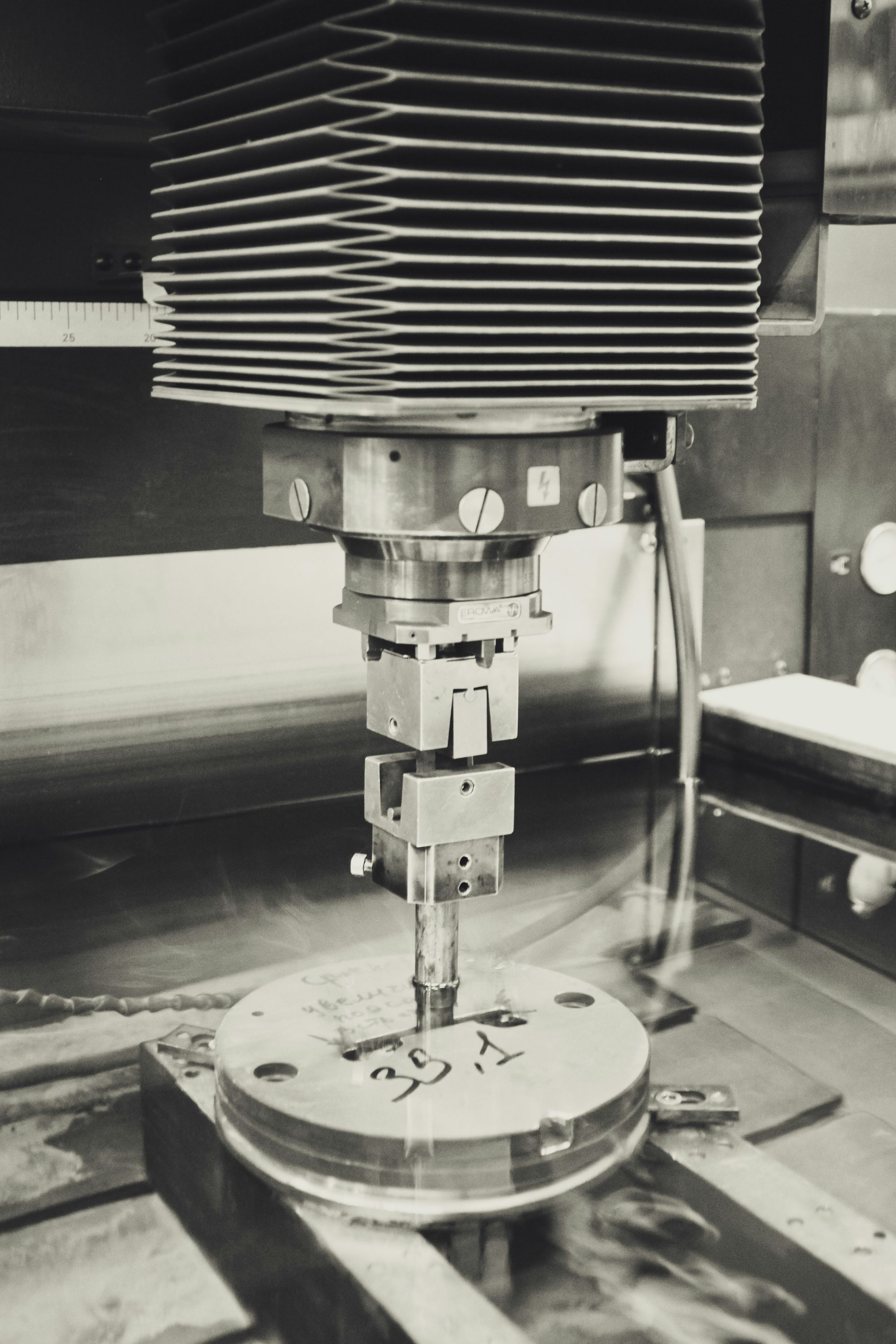
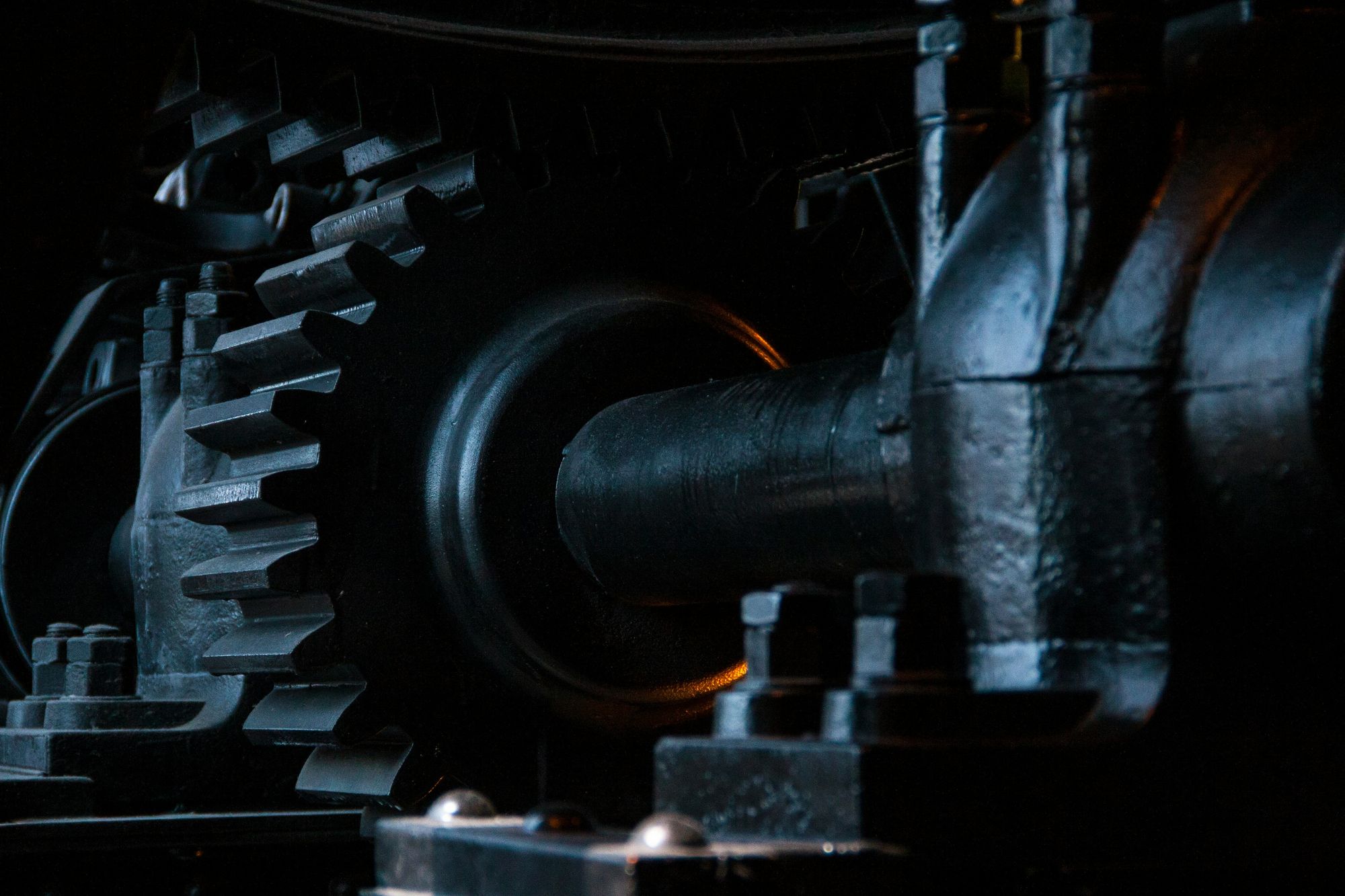
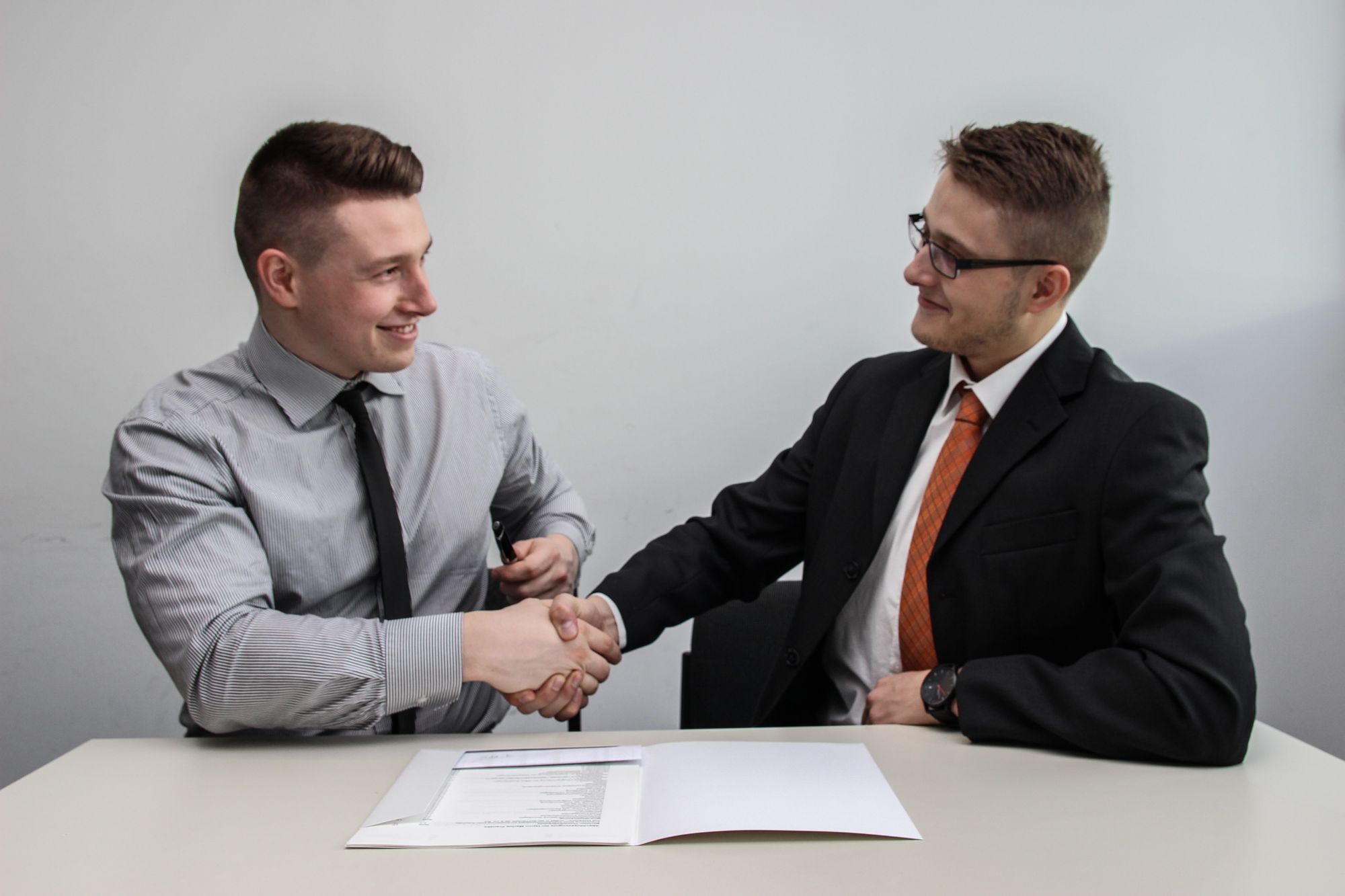
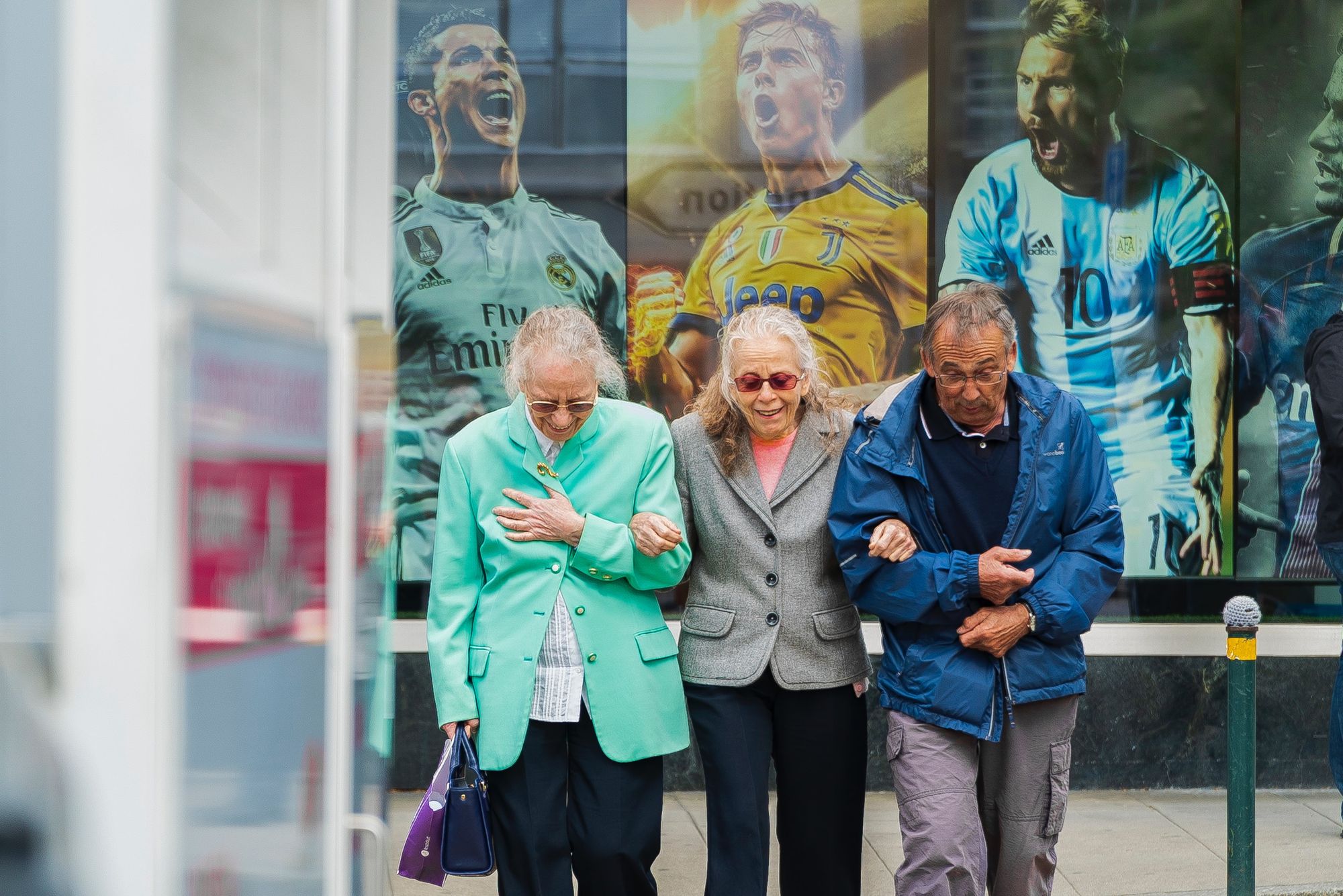
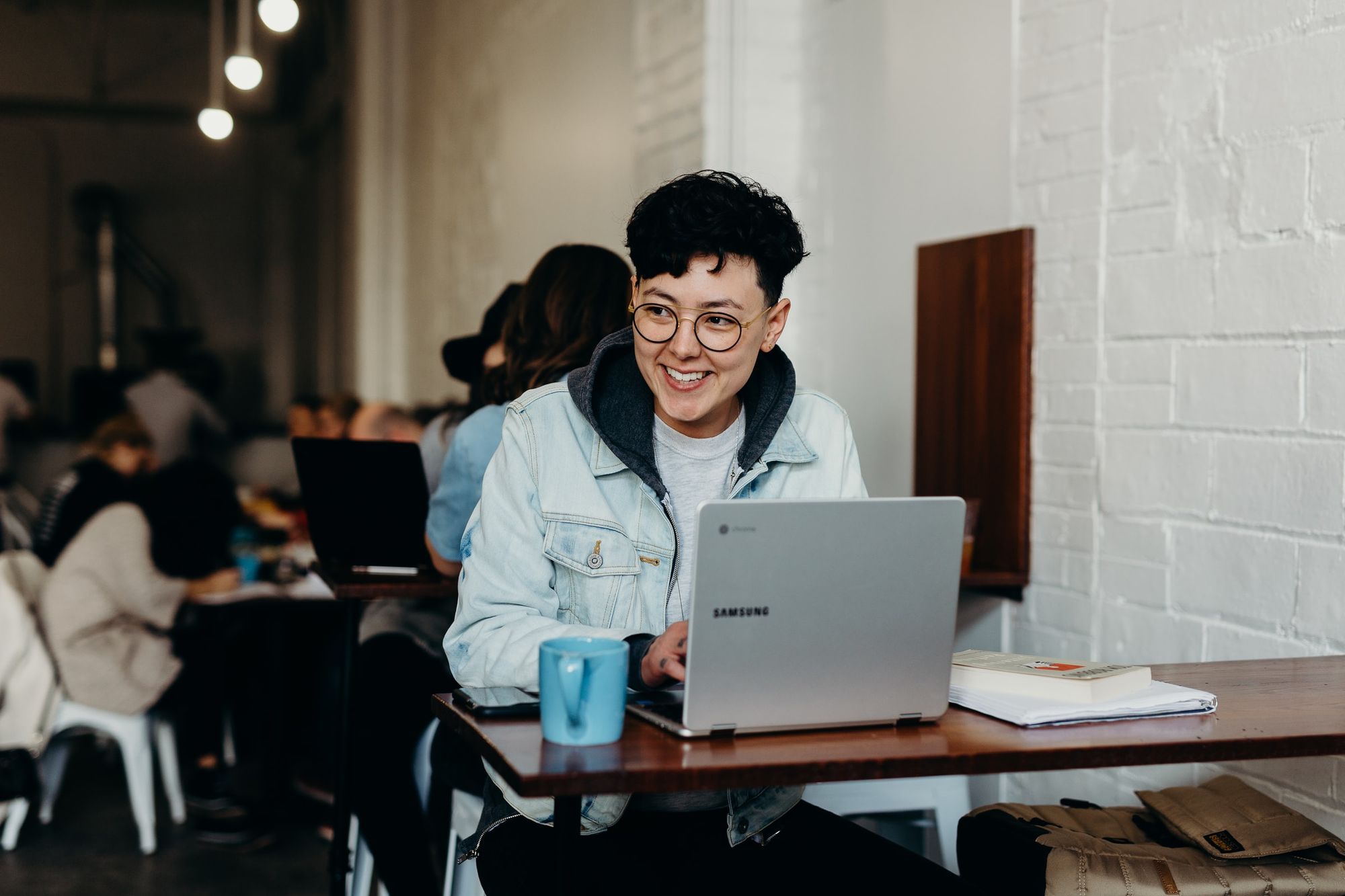
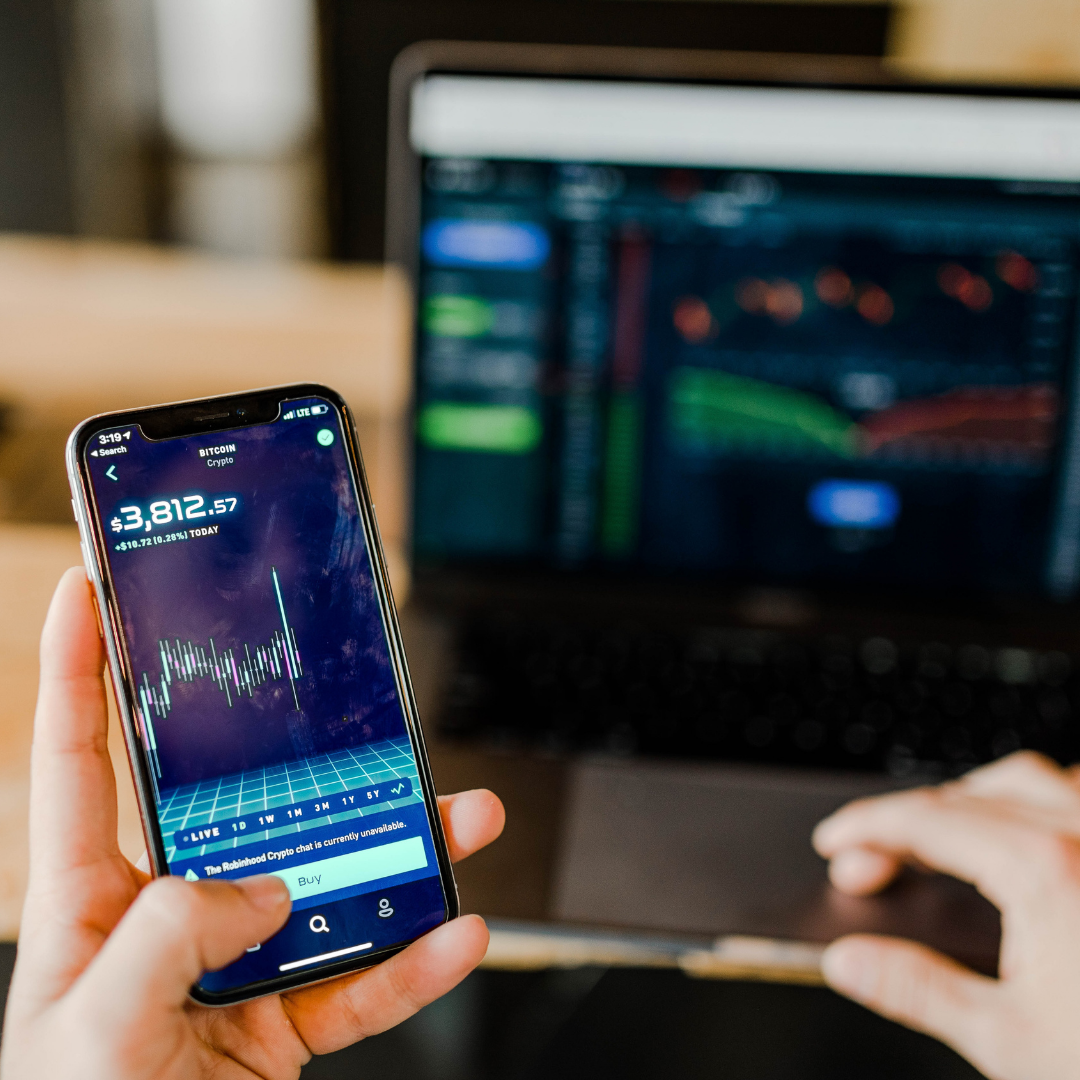