Do you feel you need to optimize your supply chain management to ensure the success of your business in the metal fabrication industry? If your answer to this question is yes, then you are on the right page.
Metal fabrication ERP systems have revolutionized supply chain management in the metal fabrication industry. These specialized software solutions are tailored to the unique needs of metal fabrication companies, providing comprehensive tools and functionalities to optimize various aspects of the supply chain.
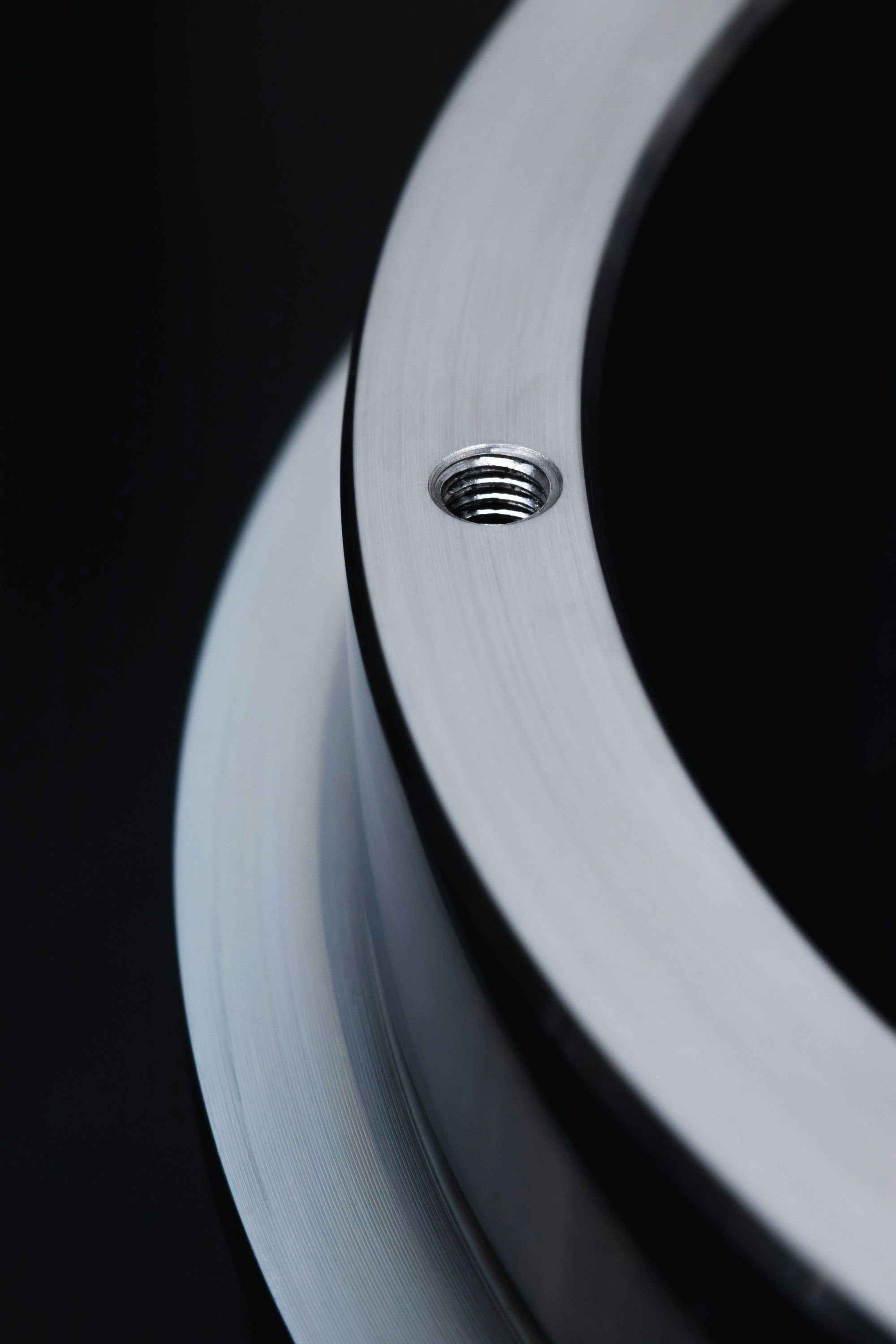
From production planning and inventory management to supplier collaboration and quality control, ERP for metal industry transforms supply chain management by streamlining processes, enhancing visibility, and driving efficiency.
In this article, we will explore how metal fabrication ERP systems have transformed supply chain management, enabling companies to improve productivity, reduce costs, and gain a competitive edge in the market.
The topics covered in this article are:
- What is the Metal Fabrication Industry?
- What is Supply Chain Management?
- Importance of Supply Chain Management in the Metal Fabrication Industry
- What is Metal Fabrication ERP?
- How Metal Fabrication ERP Transforms Supply Chain Management
- How can Deskera as a Metal Fabrication ERP Help with Supply Chain Management?
- Key Takeaways
- Related Articles
What is the Metal Fabrication Industry?
The metal fabrication industry encompasses a wide range of activities involved in shaping metal into finished products or components through various processes such as cutting, bending, welding, machining, and assembling. This industry serves diverse sectors including construction, automotive, aerospace, electronics, and manufacturing.
Key aspects of the metal fabrication industry include:
- Manufacturing Processes: Metal fabrication involves a variety of manufacturing processes tailored to different materials and product requirements. These processes may include sheet metal fabrication, machining, casting, forging, stamping, and extrusion.
- Materials: Metal fabrication works with a variety of metals including steel, aluminum, copper, brass, and alloys. The choice of material depends on factors such as strength, durability, conductivity, and corrosion resistance required for the specific application.
- Products: The metal fabrication industry produces a wide range of products including structural components, machinery parts, enclosures, frameworks, panels, and decorative elements. These products serve various industries and applications, from heavy machinery and equipment to architectural structures and consumer goods.
- Customization: Metal fabrication often involves customization to meet the specific requirements of customers or projects. Fabricators work closely with clients to understand their needs and preferences, providing tailored solutions that meet quality standards and regulatory requirements.
- Technology and Innovation: The metal fabrication industry continually evolves with advancements in technology and innovation. Automation, robotics, computer-aided design (CAD), and computer-aided manufacturing (CAM) have revolutionized fabrication processes, enabling greater precision, efficiency, and productivity.
- Supply Chain: The metal fabrication industry relies on a complex supply chain involving raw material suppliers, equipment manufacturers, subcontractors, and distribution channels. Effective supply chain management is crucial for ensuring a steady supply of materials, optimizing production processes, and delivering products to customers on time.
- Quality Control and Safety: Quality control and safety are paramount in the metal fabrication industry to ensure product quality, reliability, and compliance with regulatory standards. Fabricators implement rigorous quality control processes and safety protocols throughout the fabrication process to minimize defects, errors, and workplace accidents.
Overall, the metal fabrication industry plays a vital role in the manufacturing and construction sectors, providing essential components and products that form the backbone of various industries and applications.
With its diverse capabilities, technological advancements, and commitment to quality, the metal fabrication industry continues to thrive and innovate in response to evolving market demands and customer needs.
What is Supply Chain Management?
Supply chain management (SCM) refers to the strategic coordination and integration of key business processes within a network of interconnected organizations involved in the production and distribution of goods and services.
It encompasses the entire lifecycle of a product, from raw material sourcing to delivery to the end customer, and involves the efficient movement of materials, information, and finances across the supply chain.
Key components of supply chain management include:
- Planning: This involves forecasting demand, developing production plans, and determining inventory levels to meet customer needs while minimizing costs.
- Sourcing: This involves selecting suppliers, negotiating contracts, and managing relationships with vendors to ensure a reliable supply of materials and components.
- Manufacturing: This involves transforming raw materials into finished products through production processes that are efficient, cost-effective, and of high quality.
- Logistics: This involves the coordination of transportation, warehousing, and distribution activities to ensure products are delivered to customers in a timely and cost-effective manner.
- Inventory Management: This involves managing inventory levels to balance the costs of carrying inventory against the risk of stockouts, ensuring that products are available when needed without overstocking.
- Supplier Relationship Management: This involves building and maintaining strong relationships with suppliers to foster collaboration, innovation, and continuous improvement throughout the supply chain.
- Demand Management: This involves understanding customer demand patterns and aligning production and distribution activities to meet customer needs while minimizing excess inventory and stockouts.
- Risk Management: This involves identifying and mitigating risks that may disrupt the supply chain, such as supplier disruptions, natural disasters, geopolitical events, or market fluctuations.
Effective supply chain management requires collaboration and coordination among various stakeholders, including suppliers, manufacturers, distributors, retailers, and customers.
By optimizing processes, reducing costs, and enhancing efficiency throughout the supply chain, organizations can improve customer satisfaction and customer retention, increase profitability, and gain a competitive advantage in the marketplace.
Importance of Supply Chain Management in the Metal Fabrication Industry
Supply chain management (SCM) is of paramount importance in the metal fabrication industry for several reasons:
- Raw Material Sourcing: Metal fabrication relies heavily on raw materials such as steel, aluminum, and various alloys. Effective supply chain management ensures a steady and reliable supply of these materials at competitive prices. By optimizing sourcing strategies and building strong relationships with suppliers, metal fabrication companies can minimize procurement costs and mitigate the risk of material shortages or price fluctuations.
- Production Efficiency: SCM plays a critical role in optimizing production processes and enhancing efficiency in metal fabrication. Through effective planning, scheduling, and coordination of production activities, SCM helps minimize idle time, reduce setup costs, and improve overall equipment effectiveness (OEE). This leads to increased productivity, faster turnaround times, and higher throughput rates in manufacturing operations.
- Inventory Management: Metal fabrication involves managing a diverse range of materials, components, and finished products. Efficient inventory management is essential to ensure that the right materials are available when needed, without excessive stockpiling or stockouts. SCM helps optimize inventory levels, reduce carrying costs, and minimize the risk of obsolescence by implementing strategies such as just-in-time (JIT) inventory and vendor-managed inventory (VMI).
- Quality Control: Maintaining high product quality is crucial in the metal fabrication industry to meet customer specifications and regulatory standards. SCM facilitates effective quality control by ensuring that materials meet specified standards, production processes are monitored and controlled, and finished products undergo rigorous inspection before delivery. This helps minimize defects, rework, and customer complaints, leading to improved customer satisfaction and customer loyalty.
- Logistics and Distribution: SCM encompasses the management of logistics and distribution activities involved in transporting materials and products throughout the supply chain. In the metal fabrication industry, this includes managing transportation, warehousing, and distribution networks to ensure the timely delivery of finished products to customers. Efficient logistics and distribution practices help minimize lead times, reduce transportation costs, and optimize delivery routes, enhancing customer service levels and competitiveness.
- Supplier Collaboration: Metal fabrication companies rely on a network of suppliers and subcontractors to provide materials, components, and specialized services. Effective supplier collaboration is essential for ensuring a reliable and responsive supply chain. SCM facilitates communication, collaboration, and information sharing with suppliers, enabling companies to build strong relationships, negotiate favorable terms, and drive continuous improvement throughout the supply chain.
- Risk Mitigation: The metal fabrication industry is subject to various risks, including supply chain disruptions, market volatility, and regulatory changes. SCM helps identify, assess, and mitigate these risks by implementing contingency plans, diversifying sourcing options, and establishing robust supply chain resilience strategies. By proactively managing risks, metal fabrication companies can minimize disruptions, protect against unforeseen events, and maintain business continuity.
In summary, supply chain management is crucial for the success of the metal fabrication industry as it enables companies to optimize sourcing, enhance production efficiency, manage inventory effectively, maintain product quality, streamline logistics, foster supplier collaboration, and mitigate risks.
A well-managed supply chain not only improves operational performance but also enhances competitiveness and profitability in the marketplace.
What is Metal Fabrication ERP?
Metal fabrication ERP (Enterprise Resource Planning) is a specialized software solution designed to meet the unique needs of metal fabrication companies. It provides comprehensive tools and functionalities to manage and optimize various aspects of the business, including production, inventory, procurement, scheduling, quality control, and customer relationship management.
Key features of metal fabrication ERP include:
- Production Management: Metal fabrication ERP helps plan, schedule, and track production activities, including job costing, work orders, and routing. It enables companies to optimize production processes, improve efficiency, and minimize downtime.
- Inventory Control: Metal fabrication ERP facilitates inventory management by tracking raw materials, components, and finished goods. It helps optimize inventory levels, reduce excess stock, and ensure materials are available when needed for production.
- Procurement: Metal fabrication ERP streamlines the procurement process by automating purchasing workflows, managing supplier relationships, and tracking supplier performance. It helps companies source materials, negotiate contracts, and ensure timely delivery of goods.
- Quality Management: Metal fabrication ERP includes tools for quality control and assurance, such as inspection criteria, non-conformance tracking, and corrective action management. It helps companies maintain product quality, comply with industry standards, and meet customer requirements.
- Shop Floor Control: Metal fabrication ERP provides visibility into shop floor operations, including machine utilization, labor tracking, and job progress. It enables real-time monitoring of production activities and helps optimize resource allocation.
- Supply Chain Integration: Metal fabrication ERP integrates with other systems within the supply chain, such as CRM (Customer Relationship Management) software, supplier databases, and accounting systems. It facilitates seamless communication and collaboration among stakeholders, from suppliers to customers.
- Reporting and Analytics: Metal fabrication ERP generates reports and analytics to provide insights into key performance metrics, such as production efficiency, inventory turnover, and customer satisfaction. It helps companies make data-driven decisions and identify opportunities for improvement.
Overall, metal fabrication ERP enables metal fabrication companies to streamline operations, improve efficiency, reduce costs, and enhance customer satisfaction. By providing a centralized platform for managing all aspects of the business, metal fabrication ERP helps companies gain a competitive edge in the market.
How Metal Fabrication ERP Transforms Supply Chain Management
Metal fabrication ERP systems play a crucial role in transforming supply chain management within the industry. Here's how:
Streamlined Processes
Metal fabrication ERP systems are powerful tools that revolutionize supply chain management in the metal industry. These comprehensive solutions integrate various functions within the manufacturing process, streamlining operations and optimizing efficiency.
Here's how ERP for metal industry transforms supply chain management:
- Centralized Data Management: Metal fabrication ERP consolidates all relevant data into a single, centralized system. From inventory levels to production schedules, every aspect of the supply chain is managed within the manufacturing ERP platform. This centralized approach eliminates data silos and enables seamless communication between different departments, resulting in more efficient processes.
- Automated Workflows: With manufacturing ERP, manual tasks such as order processing, scheduling, and inventory management are automated. This reduces the risk of human error and speeds up the execution of critical processes. Automated workflows ensure that tasks are completed accurately and on time, improving overall productivity and customer satisfaction.
- Real-time Monitoring: MRP software provides real-time visibility into every stage of the manufacturing process. Managers can monitor production progress, track inventory levels, and identify bottlenecks in real time. This level of visibility allows for proactive decision-making, enabling companies to respond quickly to changing market demands and production requirements.
- Integrated Supply Chain: Manufacturing software integrates seamlessly with other systems within the supply chain, such as CRM software and supplier databases. This integration enables smooth coordination between different stakeholders, from suppliers to customers, ensuring a more responsive and agile supply chain.
- Optimized Resource Allocation: By analyzing data on production capacity, material availability, and resource utilization, metal fabrication ERP helps optimize resource allocation. Companies can allocate resources more effectively, reducing waste and maximizing efficiency. This leads to lower production costs and improved profitability.
- Streamlined Communication: ERP for metal industry facilitates communication and collaboration among team members across different departments. Features such as messaging tools, shared calendars, and task assignments ensure that everyone is on the same page. Streamlined communication fosters teamwork and enhances overall operational efficiency.
In conclusion, metal fabrication ERP software revolutionizes supply chain management in the metal industry by centralizing data management, automating workflows, providing real-time monitoring, integrating the supply chain, optimizing resource allocation, and streamlining communication.
With its comprehensive features and capabilities, metal fabrication ERP drives efficiency, agility, and profitability in manufacturing operations.
Real-Time Visibility
Real-time visibility is a crucial aspect of supply chain management in the metal industry, and metal fabrication ERP software plays a key role in transforming this aspect.
With features tailored to the specific needs of metal fabrication companies, such as inventory tracking and production monitoring, manufacturing ERP systems provide unparalleled visibility into the supply chain.
Here's how ERP for metal industry transforms supply chain management through real-time visibility:
- Instant Access to Data: Metal fabrication ERP systems offer instant access to critical data related to inventory levels, production status, and order fulfillment. With all information stored in a centralized database, stakeholders can retrieve real-time updates at any time, ensuring they are always well-informed about the current state of operations.
- Monitoring Production Progress: Manufacturing ERP enables real-time monitoring of production progress across different stages of the manufacturing process. Managers can track the status of work orders, monitor machine utilization, and identify any delays or bottlenecks as they occur. This proactive approach allows for timely interventions to ensure production stays on track.
- Inventory Tracking and Management: MRP software includes robust inventory tracking and management features that provide real-time visibility into stock levels, locations, and movements. With accurate inventory data available at their fingertips, companies can avoid stockouts, minimize excess inventory, and optimize procurement decisions to maintain optimal inventory levels.
- Forecasting and Planning: By analyzing real-time data on production trends, market demand, and resource availability, metal fabrication ERP systems support better forecasting and planning processes. Companies can anticipate future demand, adjust production schedules accordingly, and make informed decisions to optimize resource utilization and minimize costs.
- Responsive Decision-Making: With real-time visibility into the supply chain, metal fabrication companies can make more responsive and agile decisions. Whether it's reallocating resources to meet changing demand or adjusting production schedules to accommodate urgent orders, manufacturing software empowers companies to adapt quickly to evolving market conditions and customer requirements.
In summary, metal fabrication ERP software transforms supply chain management in the metal industry by providing real-time visibility into inventory, production, and demand.
Through instant access to critical data and proactive monitoring of operations, MRP software systems enable companies to optimize production processes, minimize costs, and enhance customer satisfaction.
Inventory Optimization
Inventory optimization is a critical aspect of supply chain management in the metal fabrication industry, and metal fabrication ERP software plays a vital role in transforming how companies manage their inventory.
With advanced features tailored to the specific needs of metal fabrication companies, such as demand forecasting and material requirements planning, manufacturing ERP for metal industry enables more efficient inventory management.
Here's how metal fabrication ERP transforms supply chain management through inventory optimization:
- Accurate Demand Forecasting: Metal fabrication ERP software utilizes historical data, market trends, and customer insights to accurately forecast demand for raw materials and finished products. By analyzing this data, companies can anticipate fluctuations in demand and adjust their inventory levels accordingly, ensuring they have the right amount of stock on hand to meet customer needs without overstocking or stockouts.
- Material Requirements Planning (MRP): Metal fabrication ERP includes robust MRP functionality that helps companies plan and manage their material requirements more effectively. By considering factors such as lead times, production schedules, and inventory levels, MRP software calculates optimal reorder points and quantities, ensuring that materials are ordered and replenished at the right time to support production without excess inventory.
- Optimized Inventory Levels: With MRP software, companies can maintain optimal inventory levels by balancing the costs of carrying inventory against the costs of stockouts. Manufacturing ERP systems provide visibility into inventory levels across multiple locations and allow companies to set minimum and maximum stock thresholds to prevent excess inventory buildup. By optimizing inventory levels, companies can reduce carrying costs, improve cash flow, and free up capital for other investments.
- Vendor Management: Metal fabrication ERP software facilitates better vendor management by providing insights into supplier performance, lead times, and pricing. Companies can identify and collaborate with reliable suppliers who offer competitive pricing and timely delivery, ensuring a steady supply of materials without overreliance on any single supplier. This diversification helps mitigate supply chain risks and enhances overall resilience.
- Warehouse Optimization: Metal fabrication ERP systems optimize warehouse operations by streamlining receiving, picking, packing, and shipping processes. By automating these tasks and optimizing storage layouts, companies can improve warehouse efficiency, reduce handling costs, and minimize errors. This results in faster order fulfillment, improved customer satisfaction, and reduced overall inventory holding costs.
In summary, metal fabrication ERP software transforms supply chain management in the metal industry by optimizing inventory levels, improving demand forecasting, streamlining material requirements planning, enhancing vendor management, and optimizing warehouse operations.
By leveraging advanced features and functionality, manufacturing ERP systems enable companies to achieve better inventory control, reduce costs, and enhance overall operational efficiency.
Supplier Collaboration
Supplier collaboration is essential for optimizing supply chain management in the metal fabrication industry, and metal fabrication ERP software facilitates seamless communication and coordination between companies and their suppliers.
With features tailored to supplier management and procurement, manufacturing ERP systems play a crucial role in transforming how metal fabrication companies collaborate with their suppliers.
Here's how ERP for metal industry transforms supply chain management through supplier collaboration:
- Streamlined Communication: Metal fabrication ERP software provides a centralized platform for communication between companies and their suppliers. Through features such as supplier portals and messaging tools, ERP systems enable seamless communication, allowing companies to exchange information, discuss orders, and address any issues or concerns in real time.
- Electronic Data Interchange (EDI): Metal fabrication ERP systems support electronic data interchange (EDI), allowing companies to exchange documents, such as purchase orders and invoices, electronically with their suppliers. EDI streamlines the procurement process, reduces paperwork, and minimizes errors associated with manual data entry, leading to faster order processing and improved accuracy.
- Supplier Performance Monitoring: MRP software includes functionality for monitoring supplier performance, such as on-time delivery, quality of goods, and adherence to contractual agreements. By tracking key performance indicators (KPIs) related to supplier performance, companies can identify top-performing suppliers and address any issues with underperforming ones, fostering stronger relationships and improving overall supply chain efficiency.
- Collaborative Forecasting: Manufacturing software enables collaborative forecasting between companies and their suppliers, allowing them to share demand forecasts, production schedules, and inventory plans. By aligning their forecasts and production schedules, companies and suppliers can better anticipate demand fluctuations, optimize inventory levels, and minimize supply chain disruptions.
- Vendor Managed Inventory (VMI): Metal fabrication ERP systems support vendor-managed inventory (VMI) programs, where suppliers take responsibility for managing inventory levels at the customer's location. Through integration with ERP systems, suppliers can access real-time inventory data and automatically replenish stock as needed, ensuring that customers always have the right amount of inventory on hand without overstocking.
- Supplier Collaboration Tools: ERP for metal industry offers a range of collaboration tools, such as shared calendars, task assignments, and document sharing, to facilitate closer collaboration between companies and their suppliers. These tools enable better coordination of activities, faster resolution of issues, and greater transparency throughout the supply chain.
In summary, metal fabrication ERP software transforms supply chain management in the metal industry by facilitating closer collaboration between companies and their suppliers.
Through streamlined communication, electronic data interchange, supplier performance monitoring, collaborative forecasting, VMI programs, and collaboration tools, manufacturing software systems enable companies to optimize procurement processes, improve supplier relationships, and enhance overall supply chain efficiency.
Quality Control
Quality control is paramount in the metal fabrication industry, ensuring that products meet rigorous standards and customer expectations.
Metal fabrication ERP software plays a pivotal role in transforming quality control processes by providing comprehensive tools and functionalities to monitor, manage, and improve product quality across the supply chain.
Here's how metal fabrication ERP transforms supply chain management through quality control:
- Integrated Quality Management: Metal fabrication ERP systems offer integrated quality management modules that allow companies to establish and enforce quality control processes throughout the manufacturing process. These modules facilitate the identification of quality standards, the creation of inspection criteria, and the monitoring of quality metrics to ensure compliance with industry regulations and customer requirements.
- Real-time Quality Monitoring: ERP for metal industry enables real-time monitoring of quality metrics across all stages of the production process. From raw material inspection to final product testing, companies can track quality parameters, such as dimensions, tolerances, and material properties, to identify any deviations or defects as soon as they occur. This proactive approach enables companies to take corrective actions promptly, minimizing the risk of defective products reaching customers.
- Traceability and Compliance: Manufacturing ERP systems facilitate traceability by capturing and documenting key information, such as material certifications, production records, and inspection reports, in a centralized database. This ensures full visibility into the production process and enables companies to trace the origin of materials and components, track changes, and demonstrate compliance with regulatory standards and customer specifications.
- Root Cause Analysis: MRP software includes tools for conducting root cause analysis to identify the underlying causes of quality issues or defects. By analyzing data collected from various sources within the ERP system, such as production logs, inspection records, and customer feedback, companies can pinpoint areas for improvement and implement corrective actions to prevent the recurrence of similar issues in the future.
- Supplier Quality Management: Manufacturing software systems support supplier quality management by enabling companies to evaluate and monitor the quality performance of their suppliers. Through integration with supplier databases and quality metrics tracking, companies can assess supplier compliance with quality standards, address any quality issues or discrepancies, and collaborate with suppliers to improve quality across the supply chain.
- Continuous Improvement Initiatives: ERP for metal industry fosters a culture of continuous improvement by providing tools and analytics for measuring, analyzing, and optimizing quality performance over time. Companies can leverage data-driven insights to identify trends, benchmark performance against industry standards, and implement initiatives for process optimization and quality enhancement.
In summary, metal fabrication ERP software transforms supply chain management in the metal industry by facilitating integrated quality management, real-time quality monitoring, traceability and compliance, root cause analysis, supplier quality management, and continuous improvement initiatives.
By ensuring product quality throughout the supply chain, ERP systems help companies enhance customer satisfaction, mitigate risks, and maintain a competitive edge in the market.
Cost Reduction
Cost reduction is a key objective for metal fabrication companies aiming to maintain competitiveness and improve profitability. Metal fabrication ERP software plays a crucial role in transforming supply chain management by implementing strategies to minimize costs across various operational aspects.
Here's how ERP for metal industry transforms supply chain management through cost reduction:
- Efficient Resource Utilization: Metal fabrication ERP systems optimize resource utilization by analyzing production schedules, material requirements, and machine capacities. By identifying inefficiencies and bottlenecks, companies can streamline operations, reduce idle time, and maximize the utilization of resources, ultimately lowering production costs.
- Inventory Management: MRP software implements inventory management techniques to minimize carrying costs and avoid stockouts. Through accurate demand forecasting, inventory optimization algorithms, and just-in-time inventory practices, companies can maintain optimal inventory levels, reduce excess stock, and minimize storage costs.
- Labor Efficiency: Manufacturing ERP systems automate repetitive tasks and streamline workflows, reducing the need for manual intervention and optimizing labor efficiency. By eliminating inefficiencies, reducing downtime, and improving productivity, companies can lower labor costs while maintaining high levels of output and quality.
- Procurement Optimization: ERP for metal industry facilitates procurement optimization by automating the procurement process, identifying cost-effective suppliers, and negotiating favorable terms. By centralizing procurement activities, companies can leverage economies of scale, consolidate purchasing, and reduce procurement costs.
- Waste Reduction: Metal fabrication ERP systems implement measures to minimize waste and optimize material usage throughout the production process. By tracking material consumption, identifying sources of waste, and implementing lean manufacturing principles, companies can reduce scrap, minimize rework, and lower material costs.
- Energy Efficiency: Manufacturing ERP software enables companies to monitor and analyze energy consumption across manufacturing operations. By identifying energy-intensive processes, implementing energy-saving measures, and optimizing equipment utilization, companies can reduce energy costs and improve overall operational efficiency.
- Maintenance Optimization: Metal fabrication ERP systems implement predictive maintenance strategies to minimize downtime and reduce maintenance costs. By analyzing equipment performance data, predicting potential failures, and scheduling maintenance proactively, companies can avoid costly unplanned downtime and extend the lifespan of their assets.
In summary, metal fabrication ERP software transforms supply chain management in the metal industry by implementing cost-reduction strategies across various operational aspects.
By optimizing resource utilization, inventory management, labor efficiency, procurement practices, waste reduction, energy efficiency, and maintenance optimization, ERP for metal industry helps companies lower production costs, improve profitability, and maintain a competitive edge in the market.
Compliance and Traceability
Compliance and traceability are critical aspects of supply chain management in the metal fabrication industry, ensuring adherence to regulatory requirements and quality standards.
Metal fabrication ERP software plays a pivotal role in transforming supply chain management by providing robust tools and functionalities for compliance management and traceability.
Here's how ERP for metal industry transforms supply chain management through compliance and traceability:
- Regulatory Compliance Management: Metal fabrication ERP systems enable companies to manage regulatory compliance by capturing and documenting relevant information, such as material certifications, safety data sheets, and compliance documents. By maintaining a centralized repository of compliance-related data, companies can ensure adherence to industry regulations and standards, mitigating the risk of non-compliance penalties and legal liabilities.
- Quality Standards Adherence: Manufacturing ERP software facilitates adherence to quality standards, such as ISO 9001 or AS9100, by implementing quality management processes and workflows. By establishing inspection criteria, documenting quality control procedures, and conducting regular audits, companies can ensure that products meet stringent quality requirements, enhancing customer satisfaction and brand reputation.
- Material Traceability: MRP software systems provide traceability features that enable companies to track the origin and movement of materials throughout the supply chain. By capturing data on material sourcing, production processes, and product distribution, companies can trace materials back to their source, identify any quality issues or defects, and implement corrective actions to prevent recurrence.
- Product Traceability: Metal fabrication ERP facilitates product traceability by assigning unique identifiers, such as serial numbers or batch numbers, to individual products or components. By recording data on product specifications, manufacturing processes, and shipping details, companies can trace products through the entire lifecycle, from production to delivery, ensuring transparency and accountability.
- Document Management: Manufacturing software includes document management functionality that enables companies to organize, store, and retrieve compliance-related documents easily. By digitizing documents, automating document workflows, and enforcing document control policies, companies can ensure that employees have access to the latest compliance documents and regulatory updates, reducing the risk of errors and omissions.
- Audit Trail Tracking: Metal fabrication ERP systems maintain audit trails that record changes to critical data and documents, providing a comprehensive history of actions taken within the system. By tracking user activities, document revisions, and system modifications, companies can demonstrate compliance with audit requirements, regulatory standards, and industry best practices.
In summary, metal fabrication ERP software transforms supply chain management in the metal industry by facilitating compliance management and traceability.
Through regulatory compliance management, quality standards adherence, material and product traceability, document management, and audit trail tracking, ERP systems help companies ensure regulatory compliance, maintain product quality, and enhance transparency throughout the supply chain.
Data-Driven Decision-Making
Data-driven decision-making is essential for optimizing supply chain management in the metal fabrication industry, enabling companies to leverage data insights to improve efficiency, reduce costs, and enhance competitiveness.
Metal fabrication ERP software plays a pivotal role in transforming supply chain management by providing comprehensive tools and analytics for data analysis and decision-making.
Here's how ERP for metal industry transforms supply chain management through data-driven decision-making:
- Comprehensive Data Analysis: Metal fabrication ERP systems enable comprehensive data analysis by consolidating data from various sources within the supply chain, such as inventory levels, production metrics, and customer demand. By leveraging advanced analytics tools, companies can analyze this data to identify trends, patterns, and correlations, providing valuable insights for decision-making.
- Demand Forecasting: Manufacturing ERP software facilitates demand forecasting by analyzing historical sales data, market trends, and customer behavior. By predicting future demand more accurately, companies can optimize production schedules, adjust inventory levels, and allocate resources effectively to meet customer needs while minimizing costs.
- Inventory Optimization: Manufacturing software systems use data analysis techniques to optimize inventory levels, balancing the costs of carrying inventory against the risk of stockouts. By analyzing demand patterns, lead times, and supplier performance data, companies can set optimal reorder points, safety stock levels, and replenishment strategies to minimize inventory holding costs while ensuring product availability.
- Production Planning and Scheduling: MRP software enables data-driven production planning and scheduling by analyzing production capacity, resource availability, and order priorities. By optimizing production schedules based on demand forecasts and resource constraints, companies can minimize idle time, reduce setup costs, and improve overall production efficiency.
- Supplier Performance Analysis: Metal fabrication ERP software includes tools for analyzing supplier performance data, such as on-time delivery rates, quality metrics, and pricing trends. By evaluating supplier performance against predefined KPIs, companies can identify top-performing suppliers, negotiate better terms, and mitigate risks associated with underperforming suppliers.
- Cost Analysis: Manufacturing ERP systems provide tools for cost analysis, allowing companies to track and analyze costs associated with production, procurement, inventory management, and distribution. By conducting cost-benefit analyses, variance analysis, and profitability analysis, companies can identify cost-saving opportunities, optimize spending, and improve overall financial performance.
- Risk Management: Metal fabrication ERP facilitates data-driven risk management by analyzing data on supply chain risks, such as supplier disruptions, demand fluctuations, and market volatility. By identifying potential risks and assessing their impact on operations, companies can develop proactive mitigation strategies, such as alternative sourcing options or inventory buffers, to minimize disruptions and maintain continuity.
In summary, metal fabrication ERP software transforms supply chain management in the metal industry by enabling data-driven decision-making across various aspects of the supply chain.
Through comprehensive data analysis, demand forecasting, inventory optimization, production planning, supplier performance analysis, cost analysis, and risk management, ERP systems help companies optimize operations, reduce costs, and improve competitiveness in the market.
Enhanced Demand Forecasting
Effective demand forecasting is crucial for optimizing supply chain management in the metal fabrication industry. Metal fabrication ERP systems play a vital role in transforming demand forecasting processes, leveraging advanced analytics and data-driven insights to enhance accuracy and efficiency.
Here's how ERP for metal industry transforms supply chain management through enhanced demand forecasting:
- Utilization of Historical Data: Metal fabrication ERP systems utilize historical data from past sales, production records, and market trends to develop accurate demand forecasts. By analyzing historical patterns and trends, MRP software systems can identify seasonality, cyclical fluctuations, and other factors influencing demand.
- Integration of Market Insights: Manufacturing ERP integrates market insights and customer feedback into demand forecasting models. This enables companies to incorporate external factors such as changing consumer preferences, competitor strategies, and economic trends into their demand forecasts, resulting in more accurate predictions.
- Customer Segmentation Analysis: MRP software systems facilitate customer segmentation analysis, allowing companies to categorize customers based on purchasing behavior, preferences, and demand patterns. By understanding the unique needs of different customer segments, companies can tailor their demand forecasts to specific market segments, improving forecast accuracy.
- Scenario Planning and Simulation: Manufacturing software enables scenario planning and simulation, allowing companies to model various demand scenarios and assess the potential impact on production, inventory, and resource allocation. This proactive approach helps companies anticipate demand fluctuations and develop contingency plans to mitigate risks.
- Collaboration with Sales and Marketing: Metal fabrication ERP systems facilitate collaboration between sales, marketing, and supply chain teams, enabling cross-functional alignment on demand forecasting objectives and strategies. By integrating sales forecasts, promotional plans, and market intelligence into demand forecasting processes, ERP systems ensure a holistic approach to demand planning.
- Continuous Improvement Initiatives: ERP for metal industry supports continuous improvement initiatives by providing tools for performance tracking, variance analysis, and forecast accuracy measurement. By monitoring forecast performance over time and identifying areas for improvement, companies can refine their demand forecasting models and processes, driving ongoing optimization.
In summary, metal fabrication ERP systems transform supply chain management by enhancing demand forecasting through the utilization of historical data, integration of market insights, customer segmentation analysis, scenario planning and simulation, collaboration with sales and marketing teams, and continuous improvement initiatives.
By leveraging advanced analytics and data-driven insights, ERP systems enable metal fabrication companies to develop more accurate demand forecasts, optimize inventory levels, and improve overall operational efficiency in the supply chain.
Integration with Advanced Manufacturing Technologies
Integration with advanced manufacturing technologies is a key aspect of how metal fabrication ERP systems revolutionize supply chain management in the metal industry.
These manufacturing ERP solutions seamlessly incorporate technologies such as IoT (Internet of Things), robotics, and AI-driven automation into supply chain processes, leading to enhanced efficiency, reduced downtime, and improved overall performance.
Here's how ERP for metal industry transforms supply chain management through integration with advanced manufacturing technologies:
- IoT Integration: Metal fabrication ERP systems integrate IoT devices and sensors into manufacturing equipment and processes. These IoT-enabled devices collect real-time data on machine performance, production metrics, and environmental conditions, providing valuable insights into equipment health, energy consumption, and production efficiency.
- Robotics Integration: Metal fabrication ERP facilitates integration with robotics and automated systems to streamline production processes and improve productivity. Robotics automation reduces manual labor, accelerates production cycles, and enhances precision in tasks such as welding, cutting, and material handling, leading to higher throughput and lower production costs.
- AI-driven Automation: Metal fabrication ERP leverages artificial intelligence (AI) and machine learning algorithms to automate decision-making processes and optimize production workflows. AI-driven automation enables predictive maintenance, predictive quality control, and predictive scheduling, allowing companies to anticipate and address potential issues before they occur, minimizing downtime and disruptions in production.
- Real-time Monitoring and Control: Metal fabrication ERP systems provide real-time monitoring and control capabilities, allowing companies to track production activities, monitor equipment performance, and adjust operations as needed. This real-time visibility enables proactive decision-making, rapid response to changes in demand or supply, and optimization of production schedules to meet customer requirements.
- Data-driven Insights: Metal fabrication ERP systems analyze data collected from integrated manufacturing technologies to generate actionable insights and recommendations for process optimization. By leveraging advanced analytics and reporting tools, companies can identify trends, patterns, and inefficiencies in production processes, enabling continuous improvement and optimization of supply chain performance.
- Collaborative Workflows: Metal fabrication ERP fosters collaboration and communication among cross-functional teams involved in supply chain management. Integrated manufacturing technologies enable seamless data exchange and communication between production, procurement, inventory management, and logistics functions, facilitating coordinated workflows and decision-making across the supply chain.
In summary, metal fabrication ERP systems transform supply chain management in the metal industry by integrating advanced manufacturing technologies such as IoT, robotics, and AI-driven automation.
By harnessing the power of these technologies, ERP systems enable companies to achieve greater efficiency, productivity, and agility in their supply chain operations, driving competitive advantage and success in the marketplace.
How can Deskera as a Metal Fabrication ERP Help with Supply Chain Management?
Deskera offers comprehensive metal fabrication ERP solutions tailored to the needs of metal fabrication companies, helping them transform their supply chain management processes.
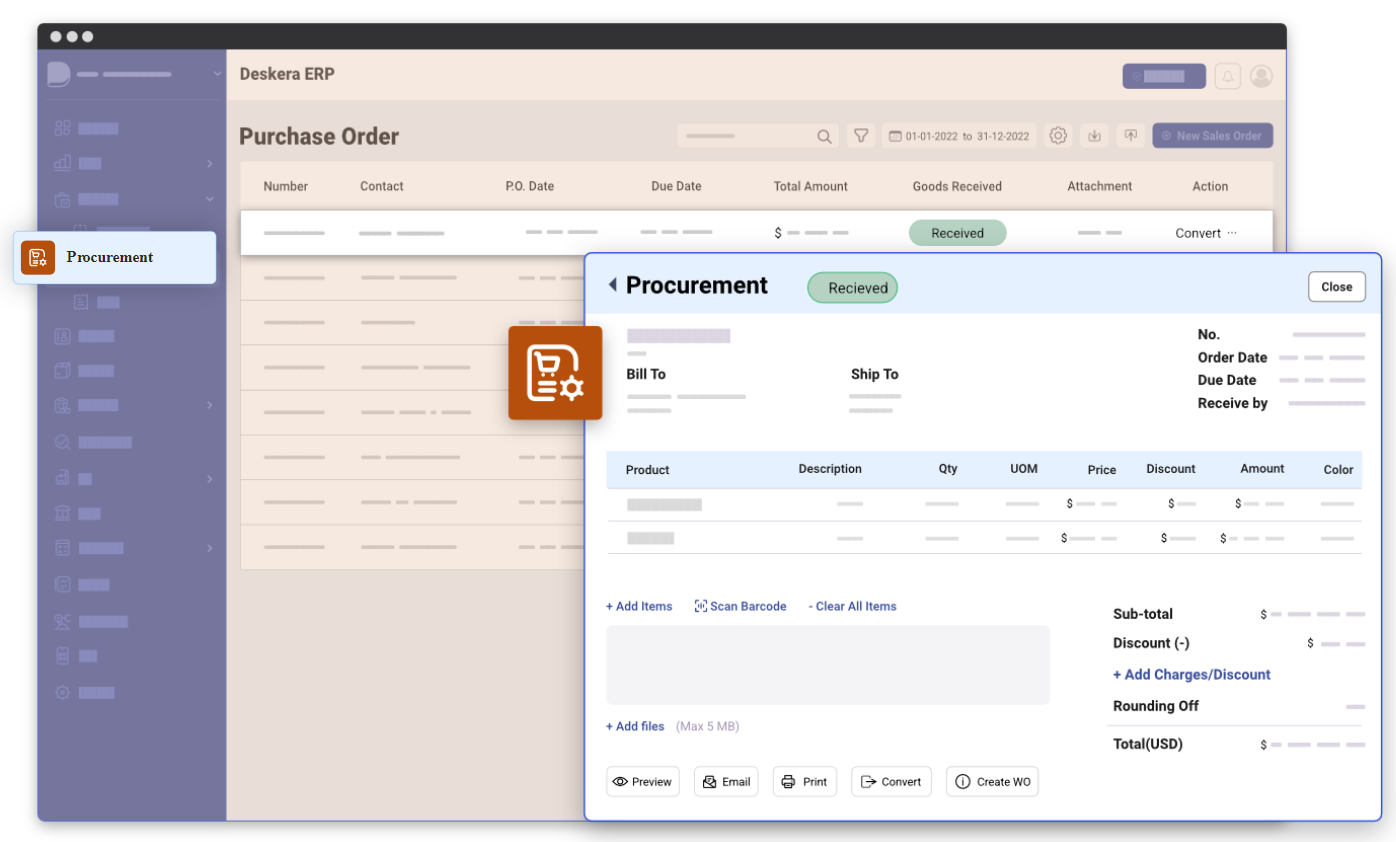
Here's how Deskera as metal fabrication ERP can help:
- Centralized Data Management: Deskera ERP centralizes all supply chain data, including production schedules, inventory levels, procurement records, and supplier information. This allows for easy access to critical information, ensuring that all stakeholders have real-time visibility into the supply chain.
- Production Planning and Scheduling: Deskera's production planning and scheduling tools enable metal fabrication companies to optimize production schedules, allocate resources efficiently, and minimize idle time. This helps improve overall production efficiency and reduce lead times.
- Inventory Management: Deskera ERP provides robust inventory management capabilities, allowing companies to track raw materials, work-in-progress, and finished goods across multiple locations. With features such as barcode scanning and serial number tracking, Deskera helps streamline inventory processes and minimize stockouts.
- Procurement Optimization: Deskera facilitates procurement optimization by automating purchasing workflows, managing supplier relationships, and tracking procurement metrics. With Deskera, metal fabrication companies can ensure the timely delivery of materials, negotiate favorable terms with suppliers, and reduce procurement costs.
- Quality Control and Assurance: Deskera includes tools for quality control and assurance, allowing companies to define quality standards, conduct inspections, and track non-conformance issues. By implementing Deskera's quality management features, metal fabrication companies can ensure that products meet specified standards and customer requirements.
- Reporting and Analytics: Deskera offers robust reporting and analytics capabilities, providing insights into key supply chain metrics such as production efficiency, inventory turnover, and supplier performance. With Deskera's reporting tools, metal fabrication companies can make data-driven decisions, identify areas for improvement, and drive continuous optimization of their supply chain processes.
Key Takeaways
Metal fabrication ERP systems play a transformative role in supply chain management in these 10 ways:
- Streamlined Processes: Metal fabrication ERP systems integrate various functions across the supply chain, including inventory management, procurement, production planning, scheduling, and distribution. By streamlining these processes, metal fabrication companies can achieve greater efficiency and reduce lead times.
- Real-time Visibility: Manufacturing ERP systems provide real-time visibility into inventory levels, production status, and order fulfillment. This visibility enables better decision-making and allows companies to respond quickly to changes in demand or supply.
- Inventory Optimization: With accurate demand forecasting and inventory tracking, metal fabrication ERP systems help optimize inventory levels. This prevents stockouts and overstocking, reducing carrying costs and improving cash flow.
- Supplier Collaboration: Manufacturing ERP systems facilitate collaboration with suppliers through features such as electronic data interchange (EDI) and supplier portals. This enables smoother communication, faster order processing, and better inventory management throughout the supply chain.
- Quality Control: MRP software systems can include modules for quality management, allowing companies to track quality metrics throughout the production process. By identifying and addressing quality issues early, metal fabrication companies can reduce rework, minimize scrap, and improve overall product quality.
- Cost Reduction: By automating repetitive tasks, optimizing processes, and reducing waste, metal fabrication ERP systems help metal fabrication companies cut costs. This includes savings from improved inventory management, reduced labor costs, and increased operational efficiency.
- Compliance and Traceability: Metal fabrication ERP systems often include features for compliance management and traceability. This is particularly important in industries with stringent regulations or quality standards, such as aerospace or automotive. Manufacturing software systems help companies track materials, processes, and documentation to ensure compliance with regulatory requirements.
- Data-driven Decision Making: MRP software systems collect and analyze vast amounts of data from various sources within the supply chain. By leveraging analytics and reporting tools, metal fabrication companies can gain insights into their operations, identify trends, and make data-driven decisions to optimize performance and improve profitability.
- Enhanced Demand Forecasting: Metal fabrication ERP systems leverage historical data, market trends, and customer insights to improve demand forecasting accuracy. By predicting demand more effectively, companies can optimize production schedules, reduce excess inventory, and minimize stockouts. This not only improves customer satisfaction by ensuring products are available when needed but also optimizes resource utilization and reduces costs associated with inventory holding.
- Integration with Advanced Manufacturing Technologies: ERP for metal industry often integrates with advanced manufacturing technologies such as IoT (Internet of Things), robotics, and AI-driven automation. This integration enables seamless data exchange between manufacturing equipment and the ERP system, facilitating real-time monitoring of production processes, predictive maintenance, and optimization of equipment utilization. By harnessing the power of these technologies, metal fabrication companies can further enhance operational efficiency, reduce downtime, and improve overall supply chain performance.
By centralizing data, automating workflows, and providing insights through advanced analytics, these specialized software solutions enable metal fabrication companies to optimize production, reduce costs, and enhance competitiveness in the marketplace.
As the metal fabrication industry continues to evolve, leveraging the capabilities of ERP systems will be essential for companies seeking to stay ahead of the curve and meet the demands of an increasingly complex and competitive market landscape.
Overall, Deskera empowers metal fabrication companies to streamline supply chain management processes, improve efficiency, and enhance competitiveness in the market. With its comprehensive features and user-friendly interface, Deskera provides a powerful solution for managing all aspects of the supply chain in the metal fabrication industry.
Related Articles
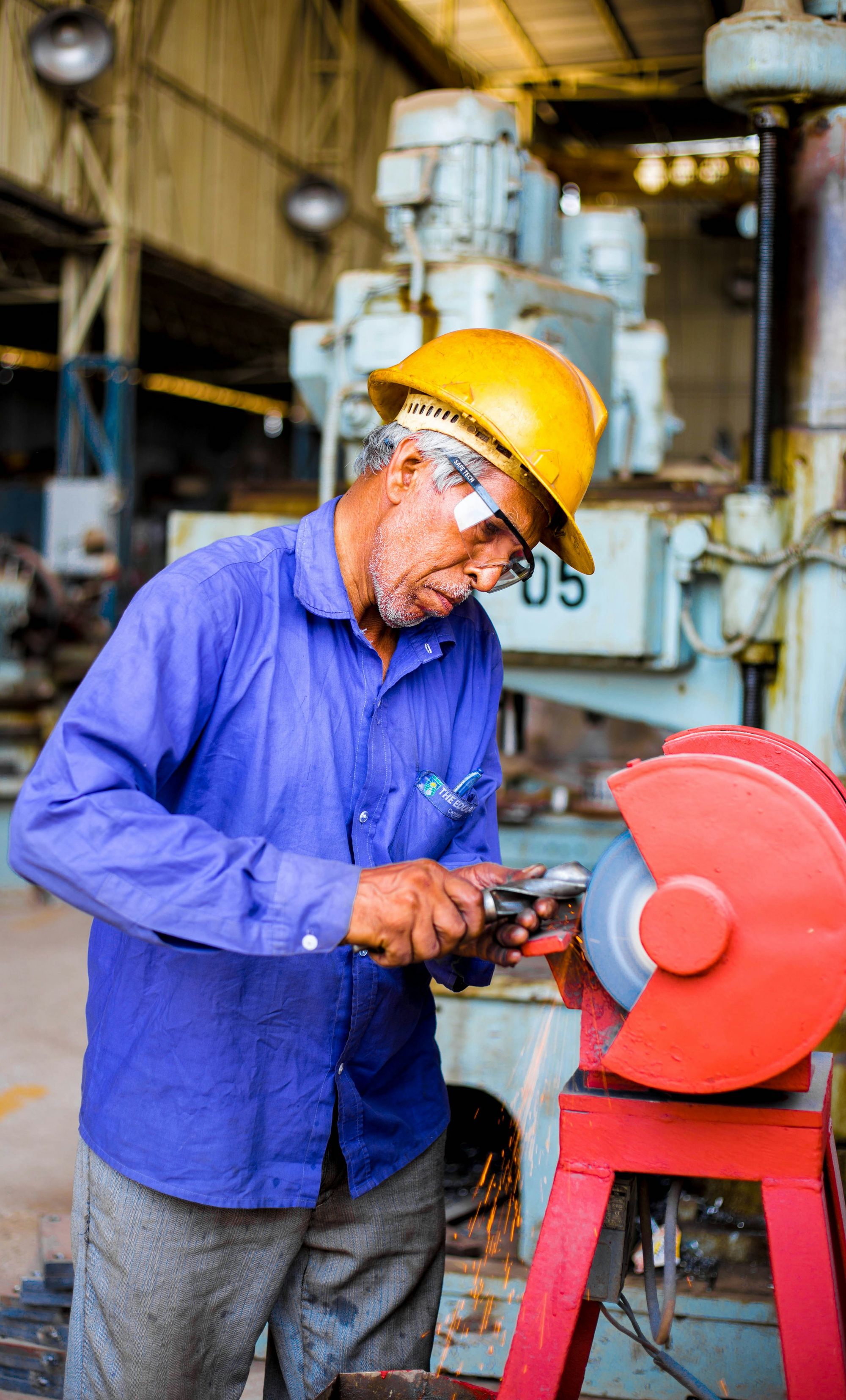
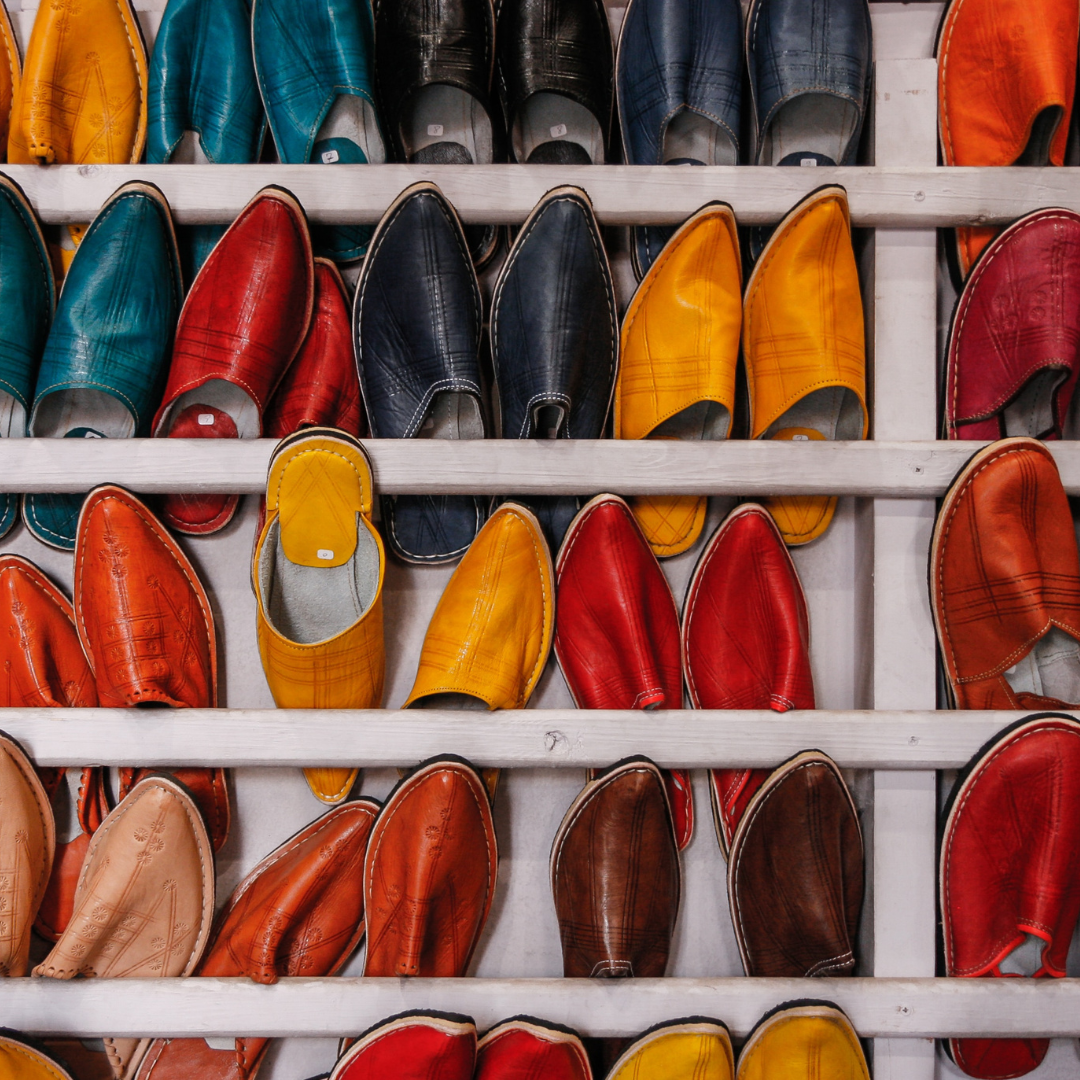
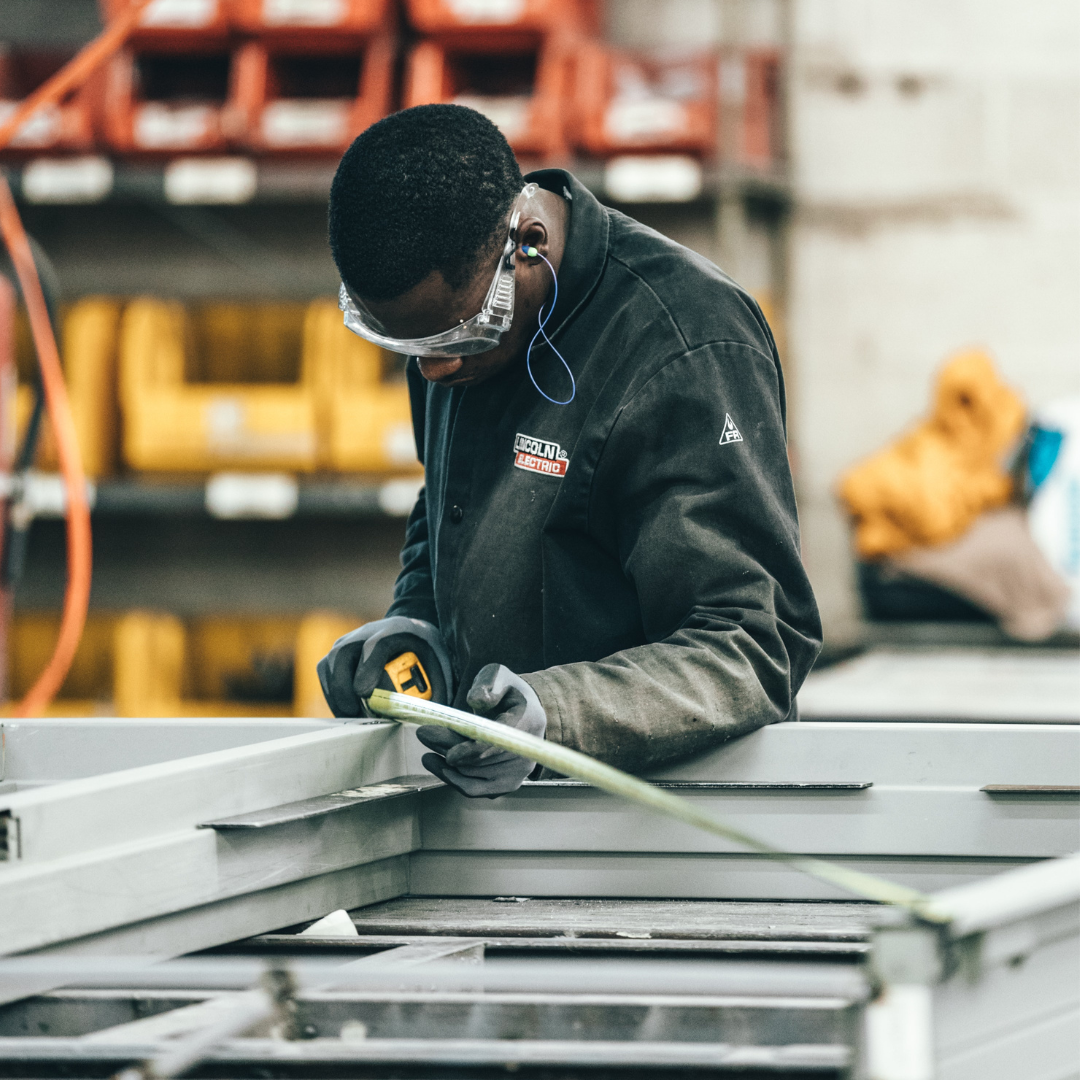
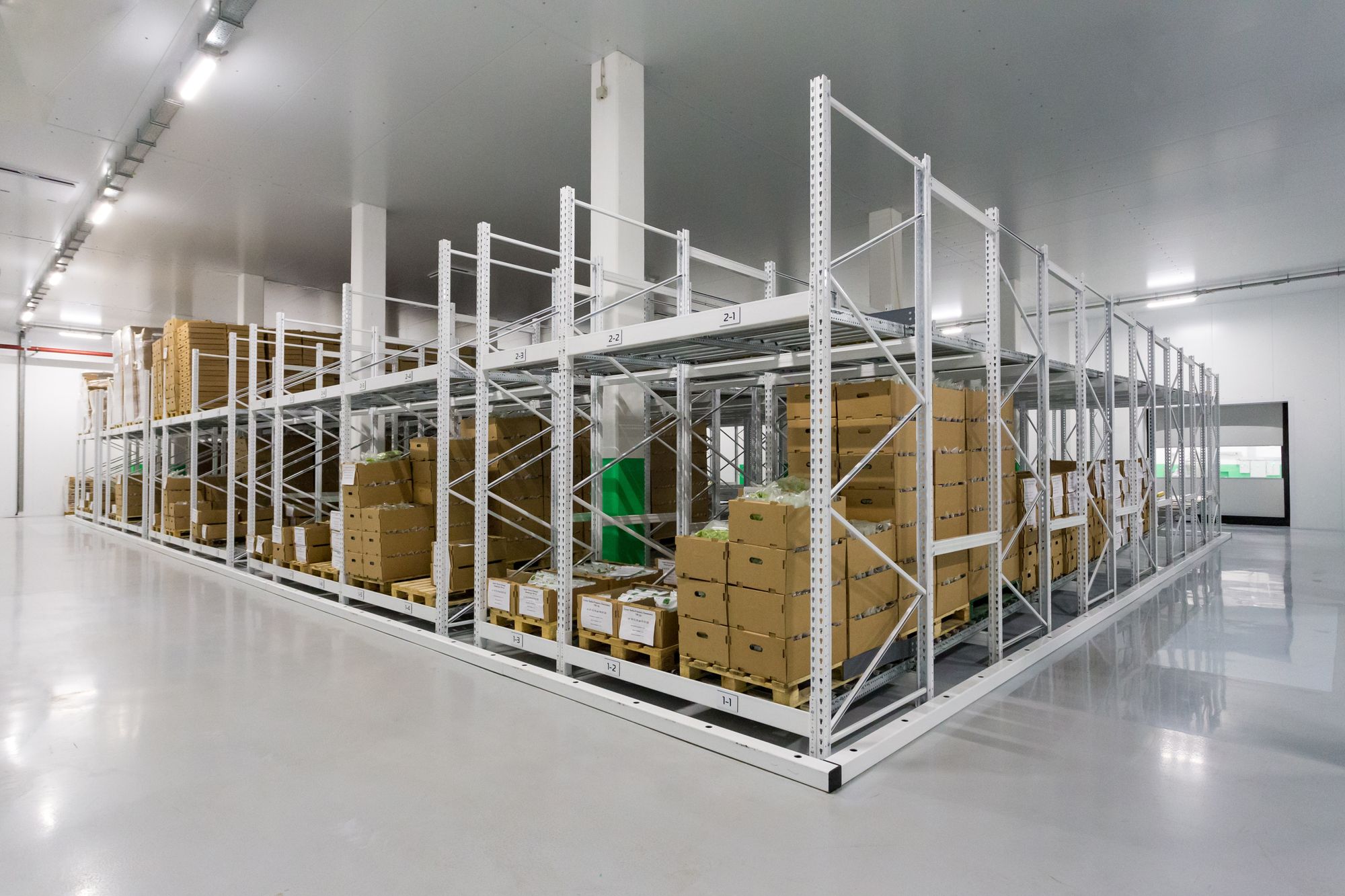
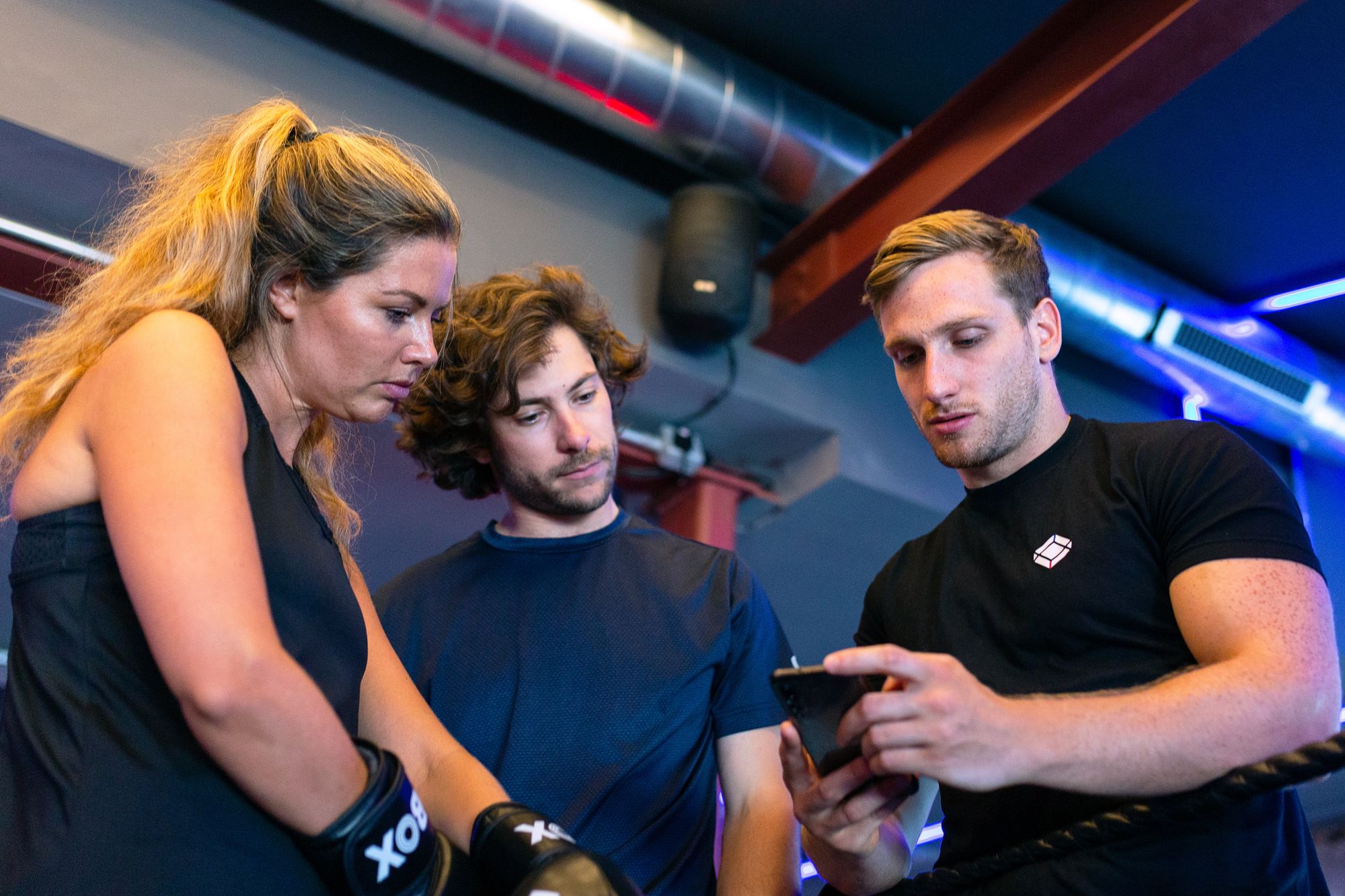