In today's fast-paced business environment, efficient work order management is crucial for ensuring seamless operations and maximizing productivity. Work orders, which detail the tasks required to maintain or repair equipment, facilities, and systems, are the backbone of operational management in industries ranging from manufacturing to facility management.
The importance of work order management has grown significantly, as reflected by the work order management systems market's rapid expansion.
According to Data Bridge Market Research, the global work order management systems market was valued at USD 532.50 million in 2021 and is projected to reach USD 1,176.80 million by 2029, growing at a compound annual growth rate (CAGR) of 10.42% during the forecast period.
This growth underscores the increasing demand for solutions that streamline and automate work order processes, enabling organizations to operate more efficiently and cost-effectively.
One such solution that stands out is Deskera MRP, a comprehensive Material Requirements Planning software designed to enhance work order management. Deskera MRP offers powerful features such as real-time tracking, automated scheduling, and seamless integration with inventory management.
These capabilities ensure that businesses can optimize their production processes, reduce downtime, and maintain accurate records, all of which are critical for achieving operational excellence.
As companies continue to seek ways to improve their work order management, adopting advanced tools like Deskera MRP will be key to staying competitive in an increasingly demanding market.
What is a Work Order?
A work order is a formal document or request that outlines the details of a task or maintenance activity that needs to be completed. It serves as a crucial link between various departments, ensuring that everyone involved understands what needs to be done, who is responsible, and when the task should be completed.
The key components of a work order typically include:
- Task Description: A clear and concise explanation of the work to be performed.
- Priority Level: An indication of the urgency of the task, helping to prioritize work.
- Assigned Personnel: The individual or team responsible for carrying out the work.
- Deadline: The date and time by which the task should be completed.
- Resources Needed: Any tools, materials, or equipment required to perform the task.
- Approval Signatures: Authorization from relevant supervisors or managers to proceed with the work.
Work orders are an essential part of the work order management process, ensuring that tasks are systematically tracked from initiation to completion. By providing a structured approach to task management, work orders help organizations maintain order and efficiency in their operations.
What is Work Order Management?
Work order management is the process of systematically handling and tracking work orders within an organization to ensure that tasks are completed efficiently and effectively.
It involves creating, assigning, prioritizing, tracking, and documenting work orders, typically through a work order management system or software.
This process is crucial in industries such as manufacturing, facility management, property management, and maintenance, where timely execution of tasks is essential for smooth operations.
Key aspects of work order management include:
- Work Order Creation: Generating work orders that clearly outline the tasks to be performed, including details like task descriptions, deadlines, assigned personnel, and necessary resources.
- Task Assignment and Prioritization: Ensuring that the right tasks are assigned to the appropriate personnel based on their skills and availability, while also prioritizing tasks according to urgency or importance.
- Tracking and Monitoring: Continuously monitoring the progress of work orders, often using work order management software, to ensure tasks are completed on time and to address any issues that may arise during the process.
- Completion and Documentation: Finalizing the work orders once the tasks are completed, including proper documentation and record-keeping for future reference or audits.
Effective work order management helps organizations streamline their processes, reduce downtime, improve productivity, and maintain high levels of service quality.
Utilizing the best work order management software can further enhance these benefits by automating many aspects of the process, providing real-time updates, and enabling better communication and collaboration across teams.
Types of Work Order Management
Work order management can be classified into various types, depending on the nature of the tasks, the objectives of the organization, and the industry in which it is applied. Each type of work order management serves a specific purpose, ensuring that tasks are completed efficiently and effectively.
Below are the common types of work order management:
1. Preventive Maintenance Work Order Management
- Objective: To perform regular, scheduled maintenance on equipment or systems to prevent unexpected breakdowns and extend the lifespan of assets.
- Examples: Routine inspections, lubrication of machinery, replacing worn-out parts before they fail.
- Benefits: Reduces the likelihood of costly repairs, minimizes downtime, and enhances the reliability of equipment.
2. Corrective Maintenance Work Order Management
- Objective: To address and fix unexpected equipment failures or issues as they arise.
- Examples: Repairing a malfunctioning HVAC system, replacing a broken conveyor belt, fixing a leaking pipe.
- Benefits: Ensures quick restoration of normal operations, minimizes disruption, and maintains productivity.
3. Inspection Work Order Management
- Objective: To conduct regular inspections of equipment, facilities, or systems to identify potential issues before they become major problems.
- Examples: Safety inspections, regulatory compliance checks, visual inspections of machinery.
- Benefits: Helps in early detection of problems, ensuring safety and compliance with industry standards.
4. Installation Work Order Management
- Objective: To manage the setup and configuration of new equipment or systems within an organization.
- Examples: Installing new machinery in a manufacturing plant, setting up IT infrastructure, installing a new HVAC system.
- Benefits: Ensures proper installation and configuration, reducing the risk of future operational issues.
5. Emergency Work Order Management
- Objective: To handle urgent, unplanned tasks that require immediate attention due to their potential impact on safety or operations.
- Examples: Responding to a fire alarm, repairing a burst pipe, fixing a critical system outage.
- Benefits: Protects the safety of personnel and assets, minimizes the impact of unexpected events on operations.
6. Predictive Maintenance Work Order Management
- Objective: To perform maintenance based on the actual condition of equipment, using data and analytics to predict when maintenance should be performed.
- Examples: Replacing a component based on vibration analysis data, performing maintenance when certain thresholds are reached.
- Benefits: Reduces unnecessary maintenance, optimizes equipment performance, and extends asset life.
7. Property Management Work Order Management
- Objective: To manage maintenance and repair tasks specific to property management, ensuring that tenants' needs are met promptly.
- Examples: Fixing a broken appliance in a rental unit, repairing leaks, performing seasonal maintenance.
- Benefits: Enhances tenant satisfaction, maintains property value, and ensures regulatory compliance.
8. Work Order Management for IT and Software
- Objective: To manage tasks related to IT and software development, including troubleshooting, system updates, and software installations.
- Examples: Deploying software updates, troubleshooting network issues, managing helpdesk tickets.
- Benefits: Ensures smooth IT operations, supports business continuity, and enhances user satisfaction.
9. Environmental and Safety Work Order Management
- Objective: To manage tasks related to environmental sustainability and workplace safety.
- Examples: Managing waste disposal, performing safety audits, ensuring compliance with environmental regulations.
- Benefits: Promotes a safe and sustainable working environment, ensures compliance with regulations, and enhances corporate responsibility.
Each type of work order management plays a crucial role in maintaining the efficiency and effectiveness of operations within an organization.
Implementing a robust work order management system or utilizing work order software tailored to these specific needs can significantly enhance the management process, leading to improved productivity, reduced costs, and better overall outcomes.
The Role of Work Orders in Operations
Work orders are essential tools that play a pivotal role in the smooth functioning of operations across various industries. They provide a structured approach to managing tasks, ensuring that every job is tracked, assigned, and completed efficiently.
Here's how work orders contribute to operational success:
1. Streamlining Processes
Work orders standardize the way tasks are handled, from initiation to completion. By clearly defining the scope of work, the resources needed, and the timeline for completion, work orders eliminate ambiguity and ensure that everyone involved understands their responsibilities.
This streamlining is particularly important in complex operations, where multiple teams and departments need to coordinate their efforts.
A well-organized work order management system ensures that tasks are completed in a logical sequence, reducing bottlenecks and delays.
2. Enhancing Productivity
Effective work order management directly impacts productivity. When work orders are created and assigned efficiently, tasks are prioritized according to their urgency and importance.
This prioritization allows teams to focus on the most critical tasks first, ensuring that resources are allocated where they are needed most.
The use of work order management software further enhances productivity by automating routine tasks, reducing manual errors, and providing real-time updates on the status of work orders. This automation frees up valuable time for teams to focus on more strategic activities.
3. Improving Accountability
Work orders provide a clear record of who is responsible for each task and when it needs to be completed. This level of accountability is crucial for maintaining high standards of work and ensuring that deadlines are met.
With a work order management system, organizations can track the progress of each work order in real-time, ensuring that tasks are completed on schedule.
In addition, work order software often includes features that allow for the easy documentation of completed tasks, providing a transparent record that can be reviewed during audits or performance evaluations.
4. Supporting Data-Driven Decision Making
Work orders generate valuable data that can be used to improve operations. By analyzing work order histories, organizations can identify patterns and trends that reveal inefficiencies or areas for improvement.
For example, recurring issues highlighted in work orders might indicate the need for preventive maintenance or a review of current processes.
Modern work order management apps and software often include reporting and analytics features that allow managers to make data-driven decisions, optimizing operations and improving overall efficiency.
5. Ensuring Compliance and Safety
In industries where safety and regulatory compliance are critical, work orders play a vital role in ensuring that all necessary checks and maintenance are performed according to standards.
Work order management systems can be configured to include mandatory safety checks and compliance requirements, ensuring that no step is overlooked. This is particularly important in property management, where property management work order software can help track and document compliance with local regulations, enhancing tenant safety and satisfaction.
In summary, work orders are more than just task lists; they are integral to the efficient and effective management of operations.
By streamlining processes, enhancing productivity, improving accountability, supporting data-driven decision-making, and ensuring compliance, work orders help organizations achieve their operational goals while maintaining high standards of quality and safety.
Adopting the best work order management software can further enhance these benefits, providing organizations with the tools they need to stay competitive in a demanding market.
Key Elements of Work Order Management
Effective work order management is essential for the seamless execution of tasks within an organization. It involves several key elements that ensure tasks are planned, tracked, and completed efficiently.
Understanding these elements is crucial for optimizing work order management processes and improving overall operational performance.
Here are the key elements of work order framework:
1. Work Order Creation
- Description: The first step in work order management is creating a detailed work order that outlines the task to be completed. This includes a clear and concise description of the work, the purpose of the task, and any specific instructions or requirements.
- Importance: A well-defined work order ensures that all parties involved understand the scope of the task, reducing the risk of errors or miscommunication.
2. Prioritization
- Description: Work orders must be prioritized based on urgency and importance. This involves assigning a priority level to each work order, indicating whether the task is critical, high, medium, or low priority.
- Importance: Prioritization helps ensure that the most urgent tasks are addressed first, preventing delays in critical operations and optimizing resource allocation.
3. Assignment
- Description: Work orders are assigned to the appropriate personnel or teams based on their skills, expertise, and availability. This step also includes specifying the resources, tools, or materials required to complete the task.
- Importance: Proper assignment ensures that tasks are handled by qualified individuals, leading to more efficient and effective execution.
4. Scheduling
- Description: Scheduling involves setting deadlines for the completion of work orders and planning the timing of tasks to align with overall operational schedules. This includes considering factors such as equipment availability, personnel schedules, and other ongoing work.
- Importance: Effective scheduling ensures that work is completed on time without disrupting other operations, helping to maintain workflow continuity.
5. Tracking and Monitoring
- Description: Throughout the work order lifecycle, it is essential to track the progress of each task. This involves monitoring the status of work orders, ensuring that tasks are progressing as planned, and identifying any issues that may arise.
- Importance: Continuous tracking and monitoring help detect delays or problems early, allowing for timely interventions and adjustments to keep projects on schedule.
6. Communication
- Description: Effective communication is crucial at every stage of work order management. This includes ensuring that all stakeholders are informed about work order details, changes, and progress updates.
- Importance: Clear communication helps prevent misunderstandings and ensures that everyone involved in the task is on the same page, which is vital for the smooth execution of work orders.
7. Documentation and Record-Keeping
- Description: Documenting each step of the work order process is essential for maintaining accurate records. This includes logging all work performed, materials used, and any issues encountered during the task.
- Importance: Proper documentation provides a detailed history of work orders, which is valuable for audits, performance evaluations, and future planning. It also supports compliance with industry regulations.
8. Completion and Close-Out
- Description: Once a task is completed, the work order must be formally closed. This involves verifying that all aspects of the task have been completed to the required standards, obtaining necessary approvals, and updating the work order status in the management system.
- Importance: Closing out work orders ensures that tasks are fully completed and allows for the transition to the next steps in the workflow. It also provides an opportunity to review and assess the efficiency of the work order management process.
9. Reporting and Analysis
- Description: After work orders are closed, the data collected during the process can be analyzed to generate reports. These reports provide insights into work order trends, resource utilization, and areas for improvement.
- Importance: Reporting and analysis help organizations refine their work order management process, identify inefficiencies, and make data-driven decisions to enhance overall operational performance.
10. Integration with Other Systems
- Description: Work order management systems should be integrated with other operational systems, such as inventory management, procurement, and asset management. This integration ensures that all relevant information is available in one place.
- Importance: Integration streamlines operations by reducing the need for manual data entry, minimizing errors, and improving overall efficiency across departments.
11. Feedback and Improvement
- Description: Collecting feedback from users and stakeholders on the work order management process and implementing improvements.
- Importance: Helps in refining processes and addressing any challenges or inefficiencies identified.
In conclusion, these key elements form the foundation of an effective work order management process. By focusing on each of these areas and utilizing the best work order management software, organizations can streamline their operations, improve task completion rates, and ensure a higher level of productivity and efficiency.
Benefits of Efficient Work Order Management
Efficient work order management is crucial for the smooth operation of any organization, especially in industries where timely task execution and resource management are critical.
Implementing an effective work order management process offers numerous benefits that can significantly enhance productivity, reduce costs, and improve overall operational efficiency.
Here are the key benefits:

1. Increased Productivity
- Description: Efficient work order management ensures that tasks are clearly defined, prioritized, and assigned to the right personnel, leading to faster and more effective task execution.
- Impact: By streamlining the process of task allocation and monitoring, employees can focus on completing work orders without unnecessary delays or confusion, resulting in higher productivity.
2. Cost Savings
- Description: Proper management of work orders helps organizations avoid unnecessary expenses by optimizing resource utilization and reducing downtime.
- Impact: Efficient scheduling, timely maintenance, and the prevention of equipment breakdowns lead to cost savings, as organizations can avoid expensive emergency repairs and minimize operational disruptions.
3. Improved Resource Allocation
- Description: Work order management systems allow organizations to allocate resources—such as personnel, tools, and materials—more effectively by tracking availability and usage in real-time.
- Impact: This ensures that resources are used optimally, reducing waste and ensuring that tasks are completed with the right tools and personnel, enhancing overall operational efficiency.
4. Enhanced Accountability
- Description: Work order management systems provide a clear record of who is responsible for each task, including deadlines and progress updates.
- Impact: This transparency fosters a culture of accountability, as employees are more likely to complete tasks on time and to the required standards when their responsibilities are clearly defined and monitored.
5. Better Communication and Collaboration
- Description: Work order management systems facilitate communication between different teams and departments by providing a centralized platform where all relevant information is accessible.
- Impact: Improved communication reduces the risk of miscommunication and ensures that everyone involved in a task is on the same page, leading to better collaboration and more efficient workflows.
6. Minimized Downtime
- Description: By prioritizing and scheduling maintenance tasks effectively, work order management can significantly reduce equipment downtime.
- Impact: Regular preventive maintenance and timely corrective actions help keep equipment in optimal condition, minimizing unplanned downtime and ensuring continuous operation.
7. Improved Compliance and Safety
- Description: Work order management systems can be configured to include mandatory safety checks and regulatory compliance tasks, ensuring that all necessary steps are followed.
- Impact: This helps organizations maintain compliance with industry regulations and enhances workplace safety by ensuring that all safety protocols are adhered to during task execution.
8. Data-Driven Decision Making
- Description: Efficient work order management generates valuable data that can be analyzed to identify trends, inefficiencies, and areas for improvement.
- Impact: Organizations can use this data to make informed decisions about process improvements, resource allocation, and maintenance strategies, leading to more effective and efficient operations.
9. Higher Quality of Service
- Description: Efficient work order management ensures that tasks are completed accurately and on time, which directly impacts the quality of service provided to customers or clients.
- Impact: Consistently meeting or exceeding service expectations enhances customer satisfaction and strengthens the organization's reputation.
10. Scalability
- Description: A well-designed work order management system can easily scale to accommodate the growing needs of an organization as it expands.
- Impact: This flexibility allows organizations to manage increasing volumes of work orders without compromising on efficiency or effectiveness, supporting long-term growth.
In summary, efficient work order management is a critical factor in achieving operational excellence. By increasing productivity, reducing costs, enhancing resource allocation, and improving overall service quality, organizations can gain a competitive edge and ensure sustainable growth.
Implementing the best work order management software or system tailored to the organization's specific needs can further amplify these benefits, leading to even greater operational success.
Challenges in Work Order Management
While work order management is essential for streamlining operations and enhancing productivity, it also presents several challenges that organizations must navigate to maintain efficiency. Addressing these challenges is crucial for ensuring that work orders are managed effectively and that operational goals are met.
Here are some of the common challenges in work order management:
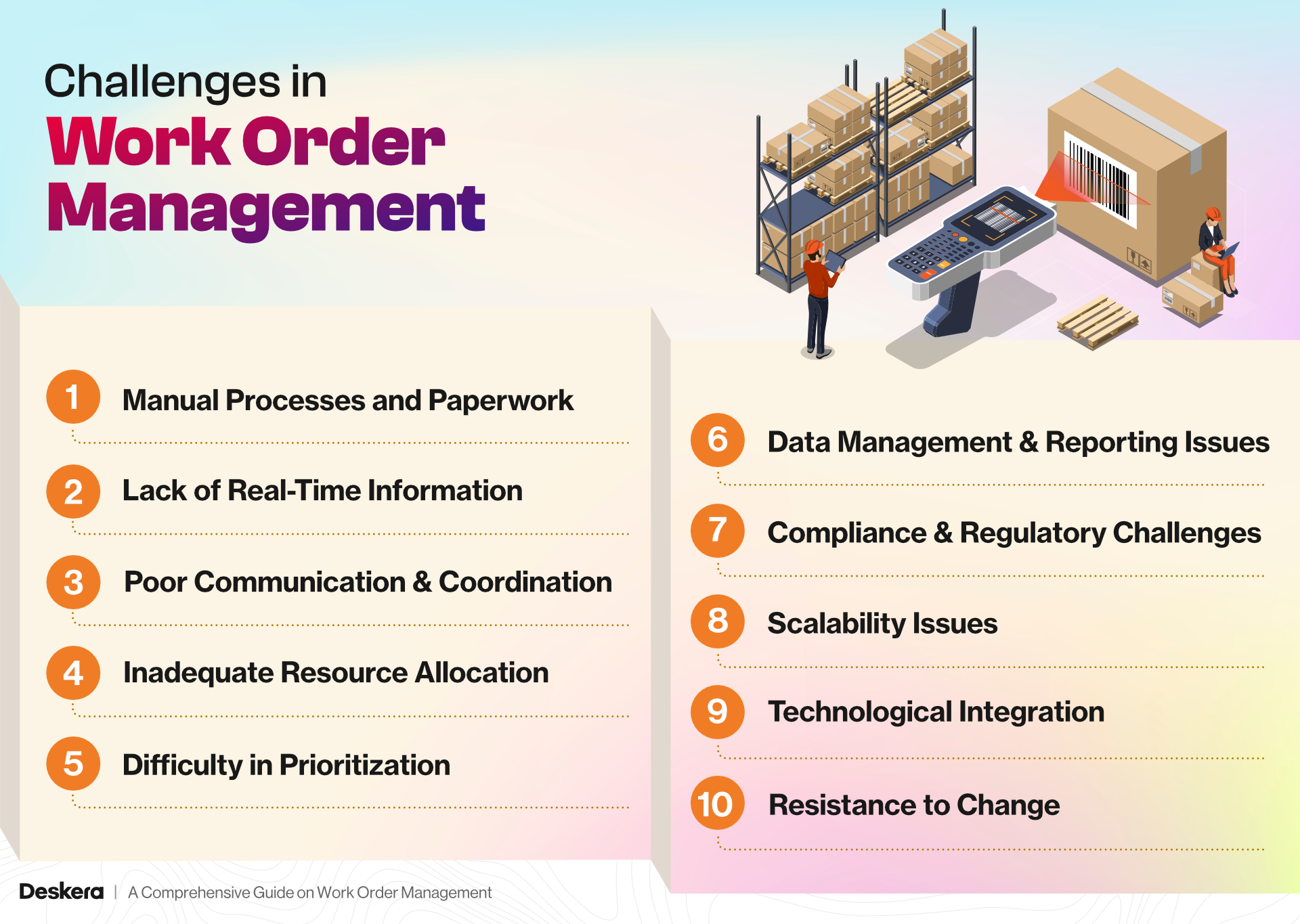
1. Manual Processes and Paperwork
- Description: Many organizations still rely on manual processes and paperwork to manage work orders, which can be time-consuming, error-prone, and difficult to track.
- Impact: This can lead to delays, lost or misplaced work orders, and inaccuracies in task execution, ultimately reducing overall efficiency and productivity.
2. Lack of Real-Time Information
- Description: Without real-time tracking and updates, it can be challenging to monitor the status of work orders, leading to a lack of visibility into ongoing tasks.
- Impact: This can result in delayed responses to issues, miscommunication between teams, and difficulties in prioritizing urgent tasks, negatively affecting the workflow and project timelines.
3. Poor Communication and Coordination
- Description: Effective work order management requires seamless communication and coordination between various departments and teams. However, communication breakdowns are common, especially in larger organizations or those with dispersed teams.
- Impact: Poor communication can lead to misunderstandings, duplication of work, and delays, ultimately compromising the quality and timeliness of task completion.
4. Inadequate Resource Allocation
- Description: Allocating the right resources (personnel, tools, materials) to the right tasks is a critical aspect of work order management. However, organizations often struggle with resource allocation due to limited visibility into resource availability and capabilities.
- Impact: Inefficient resource allocation can lead to underutilization or overburdening of resources, causing delays and impacting the quality of work.
5. Difficulty in Prioritization
- Description: With multiple work orders in the pipeline, prioritizing tasks based on urgency and importance can be challenging, especially without a clear framework for decision-making.
- Impact: Failure to prioritize effectively can result in critical tasks being delayed, while less important tasks consume valuable time and resources.
6. Data Management and Reporting Issues
- Description: Managing and analyzing the data generated by work orders is essential for making informed decisions. However, organizations often face challenges in consolidating, storing, and analyzing this data due to disparate systems or lack of integration.
- Impact: Poor data management can hinder the ability to generate accurate reports, identify trends, and make data-driven decisions, leading to suboptimal outcomes.
7. Compliance and Regulatory Challenges
- Description: Ensuring that work orders comply with industry regulations and safety standards is critical, particularly in highly regulated industries. However, managing compliance can be complex and time-consuming.
- Impact: Failure to adhere to compliance requirements can result in legal penalties, safety hazards, and reputational damage, making it a significant challenge for work order management.
8. Scalability Issues
- Description: As organizations grow, the volume of work orders increases, and the complexity of managing them escalates. Scaling up work order management processes can be difficult, especially without the right systems and tools in place.
- Impact: Inadequate scalability can lead to inefficiencies, bottlenecks, and an inability to meet growing operational demands, hindering the organization’s ability to expand.
9. Technological Integration
- Description: Integrating work order management systems with other operational systems (such as inventory management, procurement, and asset management) is essential for a seamless workflow. However, integration can be technically challenging and costly.
- Impact: Lack of integration can lead to data silos, manual data entry errors, and a disjointed workflow, reducing the overall efficiency of the work order management process.
10. Resistance to Change
- Description: Implementing new work order management software or processes often meets resistance from employees who are accustomed to existing workflows and systems.
- Impact: Resistance to change can slow down the adoption of more efficient work order management practices, leading to a prolonged transition period and potentially limiting the benefits of the new system.
In conclusion, while work order management is a critical aspect of operational efficiency, it comes with its set of challenges. Overcoming these challenges requires a combination of effective strategies, robust work order management software, and a commitment to continuous improvement.
By addressing these issues proactively, organizations can optimize their work order management processes, leading to better resource utilization, improved task execution, and enhanced overall performance.
What is Work Order Management Software?
Work order management software is a specialized tool designed to streamline the creation, assignment, tracking, and completion of work orders within an organization. This software automates and centralizes the entire work order management process, helping businesses efficiently manage tasks, resources, and workflows.
Work order management software is used across various industries, including manufacturing, facilities management, property management, and field services. In these industries, the software helps manage everything from routine maintenance tasks to complex project-based work orders, ensuring that all tasks are completed efficiently and effectively.
For example, property management work order software is tailored to the needs of property managers, helping them handle maintenance requests, tenant issues, and other property-related tasks efficiently. Similarly, in manufacturing, the best work order management software can help manage preventive maintenance, equipment repairs, and production tasks, ensuring minimal downtime and optimal production output.
In conclusion, work order management software is an essential tool for any organization looking to improve task management, resource allocation, and overall operational efficiency. By automating and centralizing work order processes, this software enables businesses to achieve higher levels of productivity, accountability, and cost-effectiveness.
Benefits of Work Order Management Software
Work order management software offers numerous advantages that can transform your organization’s operations. Here’s a comprehensive look at how this technology can benefit your business:
1. Optimized Operational Efficiency
- Description: Automating the work order process with dedicated software reduces the need for manual handling and paperwork, leading to smoother and more streamlined operations.
- Impact: This automation accelerates task completion, minimizes errors, and frees up time for staff to focus on more strategic activities.
2. Enhanced Resource Utilization
- Description: Work order management software provides real-time visibility into the availability and status of resources, including personnel, equipment, and materials.
- Impact: Effective resource allocation ensures that tasks are assigned appropriately, reducing idle time and improving overall productivity.
3. Increased Accountability and Clarity
- Description: The software maintains comprehensive records of work orders, including who is assigned to each task and the status of their completion.
- Impact: This level of detail fosters accountability and transparency, ensuring that responsibilities are clear and tasks are tracked accurately.
4. Improved Team Collaboration
- Description: Integrated communication tools within the software facilitate seamless interaction between team members, allowing for the easy sharing of updates and information.
- Impact: Better collaboration leads to fewer misunderstandings and more coordinated efforts, enhancing the efficiency of task execution.
5. Boosted Productivity
- Description: By automating repetitive tasks and providing immediate updates, work order management software helps teams operate more efficiently.
- Impact: Increased productivity results in the faster handling of work orders and the ability to manage a higher volume of tasks.
6. Cost Efficiency
- Description: Effective management of work orders helps in reducing operational expenses by decreasing downtime, avoiding unnecessary repairs, and improving resource allocation.
- Impact: Cost savings are achieved through minimized waste and more efficient use of resources, contributing to better financial performance.
7. Scalable Solutions
- Description: Work order management software is designed to scale with the growth of your business, accommodating an increasing number of work orders and tasks.
- Impact: Scalability ensures that the software remains effective as your organization expands, supporting sustained operational success.
8. Actionable Insights Through Data
- Description: The software provides advanced reporting and analytics capabilities, offering insights into work order trends, performance metrics, and resource utilization.
- Impact: Organizations can leverage this data to make informed decisions, optimize processes, and drive continuous improvement.
9. Regulatory Compliance and Safety Assurance
- Description: Work order management software can include features to ensure that tasks meet industry regulations and safety standards.
- Impact: This helps avoid legal issues, enhances workplace safety, and ensures that all compliance requirements are consistently met.
10. Accessible On-the-Go
- Description: Many work order management systems offer mobile applications, allowing users to manage and update work orders from any location.
- Impact: Mobile accessibility increases flexibility, enabling faster responses to issues and better management of tasks while on the move.
11. Enhanced Customer Service
- Description: The software often includes features for managing customer requests and tracking service levels, which improves response times and service quality.
- Impact: Better management of customer service requests leads to increased customer satisfaction and customer loyalty.
12. Reduced Administrative Overhead
- Description: Automating work order management reduces the need for manual tracking and administrative tasks.
- Impact: This reduction in administrative overhead allows staff to focus on more value-added activities, improving overall efficiency.
13. Improved Forecasting and Planning
- Description: Advanced analytics and historical data provided by the software aid in forecasting future work orders and planning maintenance schedules.
- Impact: Better forecasting and planning lead to more proactive maintenance, reducing the likelihood of unexpected issues and optimizing resource use.
14. Customizable Workflows
- Description: Work order management software often allows for customizable workflows and processes tailored to specific business needs.
- Impact: Customizable workflows ensure that the software aligns with your organization’s unique requirements, improving usability and effectiveness.
15. Integration with Other Systems
- Description: Many work order management solutions integrate seamlessly with other enterprise systems such as ERP, CRM, and asset management.
- Impact: Integration provides a holistic view of operations, enhances data accuracy, and streamlines processes across different systems.
In summary, work order management software offers a range of benefits that go beyond just task management. By optimizing efficiency, enhancing resource utilization, and providing valuable insights, this software supports improved productivity, cost savings, and overall operational success.
Additionally, features like mobile accessibility, customer service enhancements, and integration capabilities further bolster its value, making it an essential tool for modern organizations.
Best Practices for Work Order Management
Implementing best practices for work order management can significantly enhance operational efficiency and ensure that tasks are completed effectively and on time. Here are some key best practices to follow:
1. Clearly Define Work Order Details
- Description: Ensure that each work order includes comprehensive details such as task descriptions, priority levels, required resources, and deadlines.
- Best Practice: Use standardized templates to capture all necessary information consistently, reducing ambiguity and improving clarity.
2. Implement a Centralized System
- Description: Utilize a centralized work order management system to consolidate all work order information and processes.
- Best Practice: Choose software that integrates with other systems (e.g., ERP, CRM) to provide a unified view of operations and streamline information flow.
3. Prioritize Work Orders Effectively
- Description: Assign priority levels to work orders based on urgency, importance, and impact on operations.
- Best Practice: Use criteria such as customer impact, safety, and compliance to determine priority, ensuring that critical tasks are addressed promptly.
4. Schedule and Plan Proactively
- Description: Develop schedules and plans for work orders to manage resources and timelines effectively.
- Best Practice: Use forecasting tools and historical data to anticipate needs and avoid bottlenecks, ensuring a balanced workload.
5. Assign Tasks Based on Skills and Availability
- Description: Match work orders with personnel who have the appropriate skills and are available to complete the tasks.
- Best Practice: Maintain a skills matrix and availability schedule to make informed assignment decisions, optimizing resource utilization.
6. Monitor Progress in Real-Time
- Description: Track the status of work orders in real-time to identify any delays or issues.
- Best Practice: Use dashboards and alerts within your work order management software to keep stakeholders informed and address problems quickly.
7. Facilitate Effective Communication
- Description: Ensure clear communication between team members, stakeholders, and customers regarding work order details and status.
- Best Practice: Leverage integrated communication tools and regular updates to maintain alignment and prevent misunderstandings.
8. Document and Archive Work Orders
- Description: Maintain accurate records of completed work orders, including details of the work performed, resources used, and any issues encountered.
- Best Practice: Implement a robust documentation system to support future reference, compliance, and continuous improvement.
9. Review and Analyze Performance Regularly
- Description: Analyze work order data to evaluate performance, identify trends, and uncover areas for improvement.
- Best Practice: Use reports and analytics to gain insights into work order completion rates, resource utilization, and process efficiency.
10. Continuously Improve Processes
- Description: Use feedback and performance data to refine and enhance work order management processes.
- Best Practice: Implement a feedback loop with team members and stakeholders to identify challenges and opportunities for process optimization.
11. Ensure Compliance and Safety
- Description: Make sure that all work orders are executed in accordance with industry regulations and safety standards.
- Best Practice: Incorporate compliance checks and safety protocols into your work order management process to mitigate risks and ensure regulatory adherence.
12. Leverage Technology for Automation
- Description: Utilize technology to automate repetitive tasks within the work order management process.
- Best Practice: Implement automation features in your work order management software to streamline task creation, assignment, and tracking.
13. Train and Support Team Members
- Description: Provide training and support to ensure that team members are proficient in using work order management tools and understand best practices.
- Best Practice: Offer regular training sessions and resources to keep the team updated on new features and process improvements.
14. Integrate with Asset Management
- Description: Integrate work order management with asset management systems to track and maintain equipment and resources.
- Best Practice: Ensure seamless data exchange between systems to enhance visibility into asset conditions and maintenance needs.
15. Utilize Mobile Access
- Description: Enable mobile access to work order management systems to facilitate on-the-go task management.
- Best Practice: Implement mobile-friendly solutions to allow field technicians and remote workers to update and manage work orders efficiently.
By adhering to these best practices, organizations can optimize their work order management processes, enhance efficiency, and improve overall operational performance.
How Deskera MRP Can Help with Work Order Management
Deskera MRP (Material Requirements Planning) offers a range of features designed to streamline and enhance work order management processes.
Here’s how Deskera MRP can assist with managing work orders effectively:
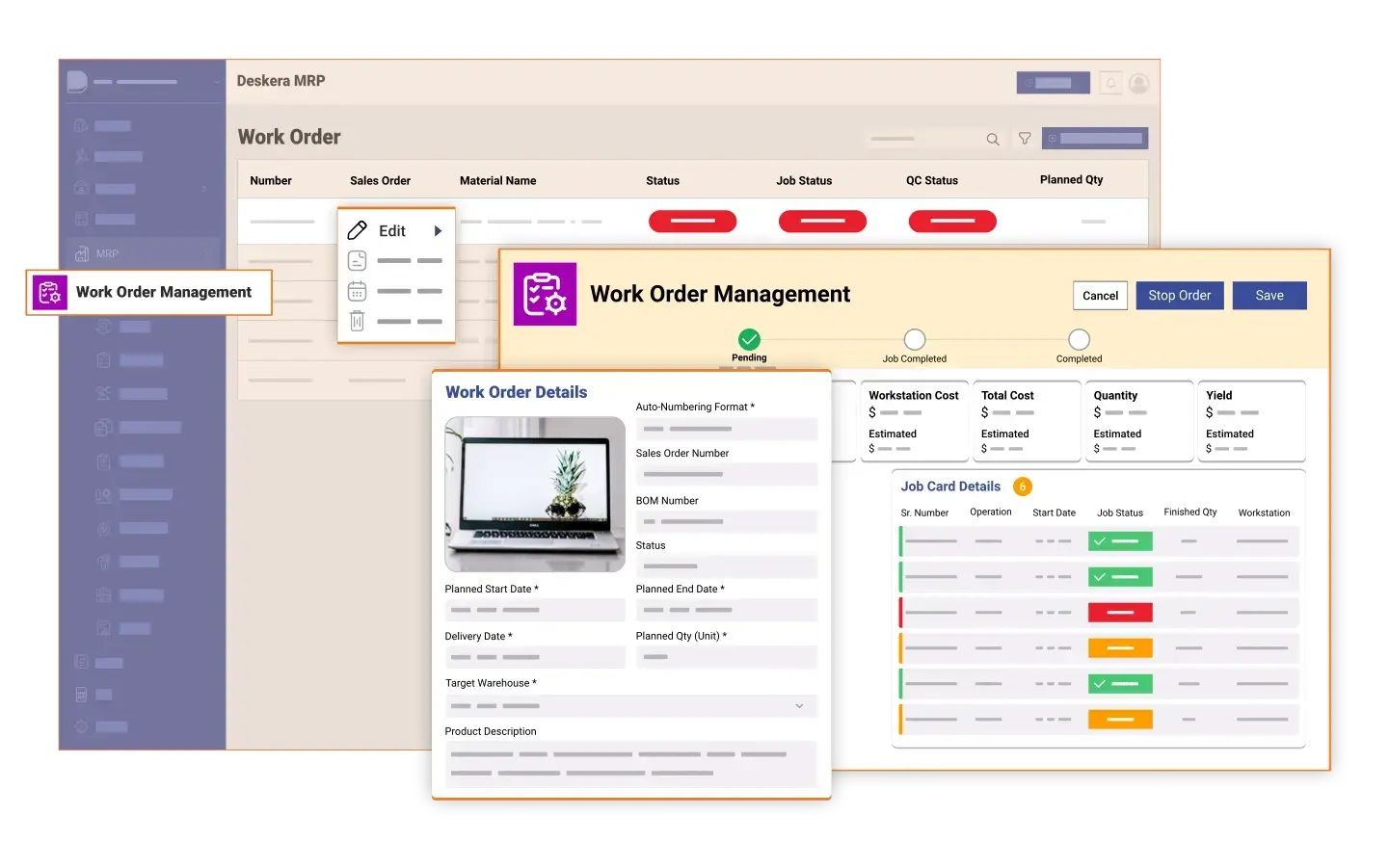
1. Automated Work Order Creation
- Description: Deskera MRP automates the creation of work orders based on material requirements and production schedules.
- Benefit: Reduces manual entry errors and ensures that work orders are generated promptly when needed, improving accuracy and efficiency.
2. Real-Time Work Order Tracking
- Description: The software provides real-time visibility into the status of work orders, including progress updates and completion statuses.
- Benefit: Enables managers to monitor work order progress, identify potential delays, and make adjustments as needed to keep operations on track.
3. Integrated Resource Planning
- Description: Deskera MRP integrates with resource planning tools to allocate the necessary personnel, equipment, and materials for each work order.
- Benefit: Ensures optimal resource utilization and helps avoid bottlenecks by matching resources with work order requirements.
4. Enhanced Scheduling and Planning
- Description: Deskera MRP offers advanced scheduling features to plan and prioritize work orders based on production needs and deadlines.
- Benefit: Improves task management by ensuring that work orders are scheduled in a way that aligns with production goals and resource availability.
5. Efficient Inventory Management
- Description: The software integrates work order management with inventory control, providing real-time updates on material availability and usage.
- Benefit: Prevents inventory shortages or excesses by ensuring that materials are ordered and used efficiently according to work order requirements.
6. Detailed Reporting and Analytics
- Description: Deskera MRP includes robust reporting and analytics capabilities to track work order performance, resource utilization, and production efficiency.
- Benefit: Provides valuable insights into work order management, helping identify trends, measure performance, and drive continuous improvement.
7. Automated Notifications and Alerts
- Description: The software sends automated notifications and alerts related to work order statuses, upcoming deadlines, and resource needs.
- Benefit: Keeps team members informed and proactive, reducing the risk of missed deadlines and ensuring timely completion of tasks.
8. Seamless Integration with Other Systems
- Description: Deskera MRP integrates seamlessly with other enterprise systems, such as ERP and CRM, for a unified approach to work order management.
- Benefit: Enhances data consistency and coordination across different departments, improving overall operational efficiency.
9. Mobile Access and Flexibility
- Description: Deskera MRP offers mobile access, allowing users to manage and update work orders from anywhere.
- Benefit: Increases flexibility and responsiveness, enabling field technicians and remote workers to stay connected and manage tasks on the go.
10. Customizable Workflows
- Description: The software allows for customizable workflows tailored to specific business needs and processes.
- Benefit: Ensures that the work order management process aligns with your organization’s unique requirements, enhancing usability and effectiveness.
11. Improved Compliance and Documentation
- Description: Deskera MRP helps maintain accurate records and documentation for work orders, including compliance with industry regulations.
- Benefit: Supports regulatory adherence and provides a reliable history of work orders for future reference and audits.
Key Takeaways
- Understanding Work Orders: Work orders are essential documents that outline tasks, resources, and timelines required to complete specific jobs. They are critical in various industries for maintaining operational efficiency and ensuring timely task completion.
- Importance of Work Order Management: Effective work order management streamlines processes, boosts productivity, and enhances communication among teams, leading to better resource utilization and minimized downtime.
- Benefits of Work Order Management Software: Implementing work order management software automates and optimizes the process, providing real-time tracking, improved scheduling, enhanced collaboration, and robust reporting capabilities.
- Overcoming Challenges: While work order management can present challenges such as complexity and coordination issues, adopting best practices and leveraging advanced software like Deskera MRP can help overcome these hurdles.
- Deskera MRP’s Role: Deskera MRP plays a crucial role in improving work order management by automating creation, tracking progress in real-time, optimizing resource allocation, and ensuring compliance with industry standards.
Related Articles
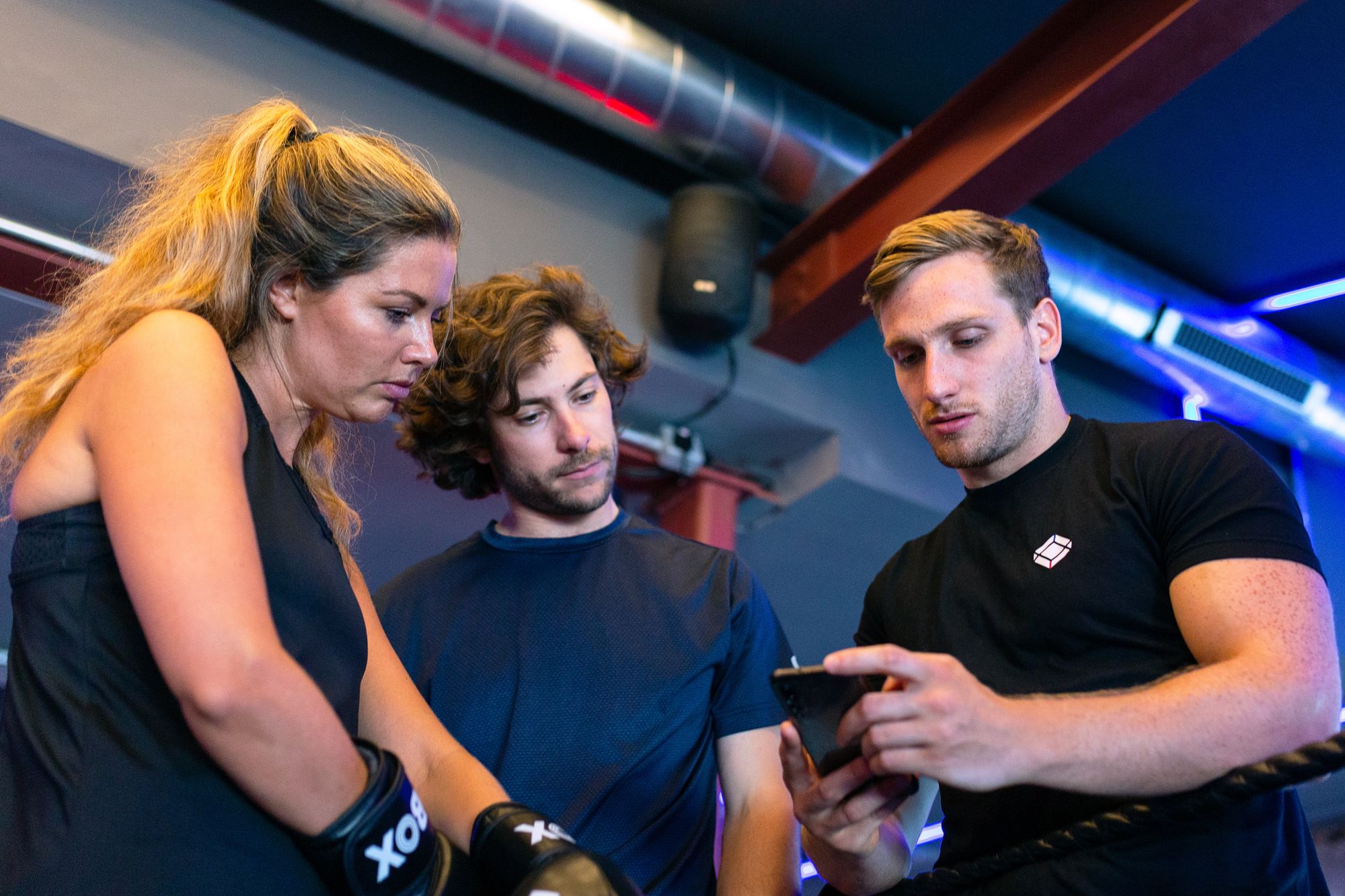

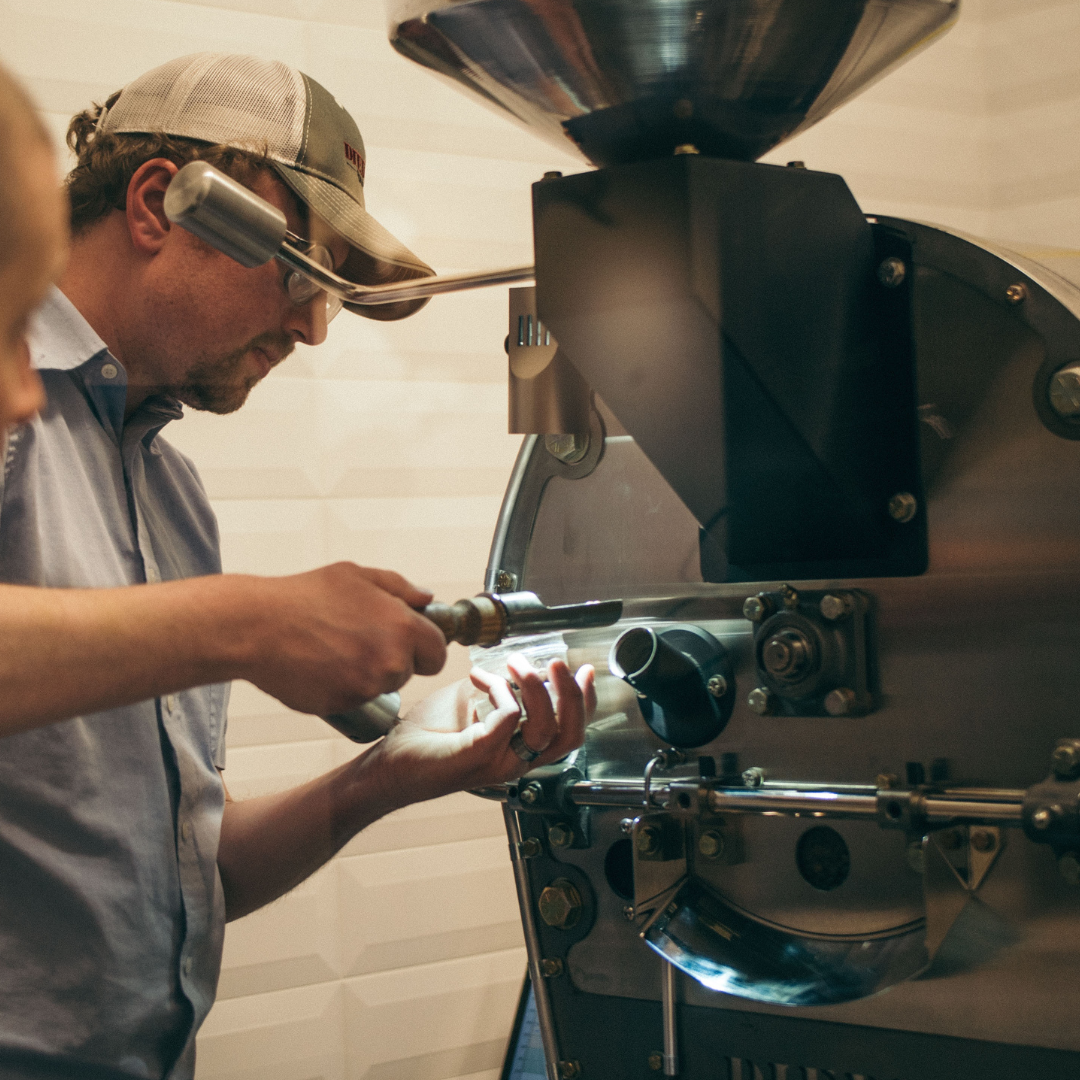
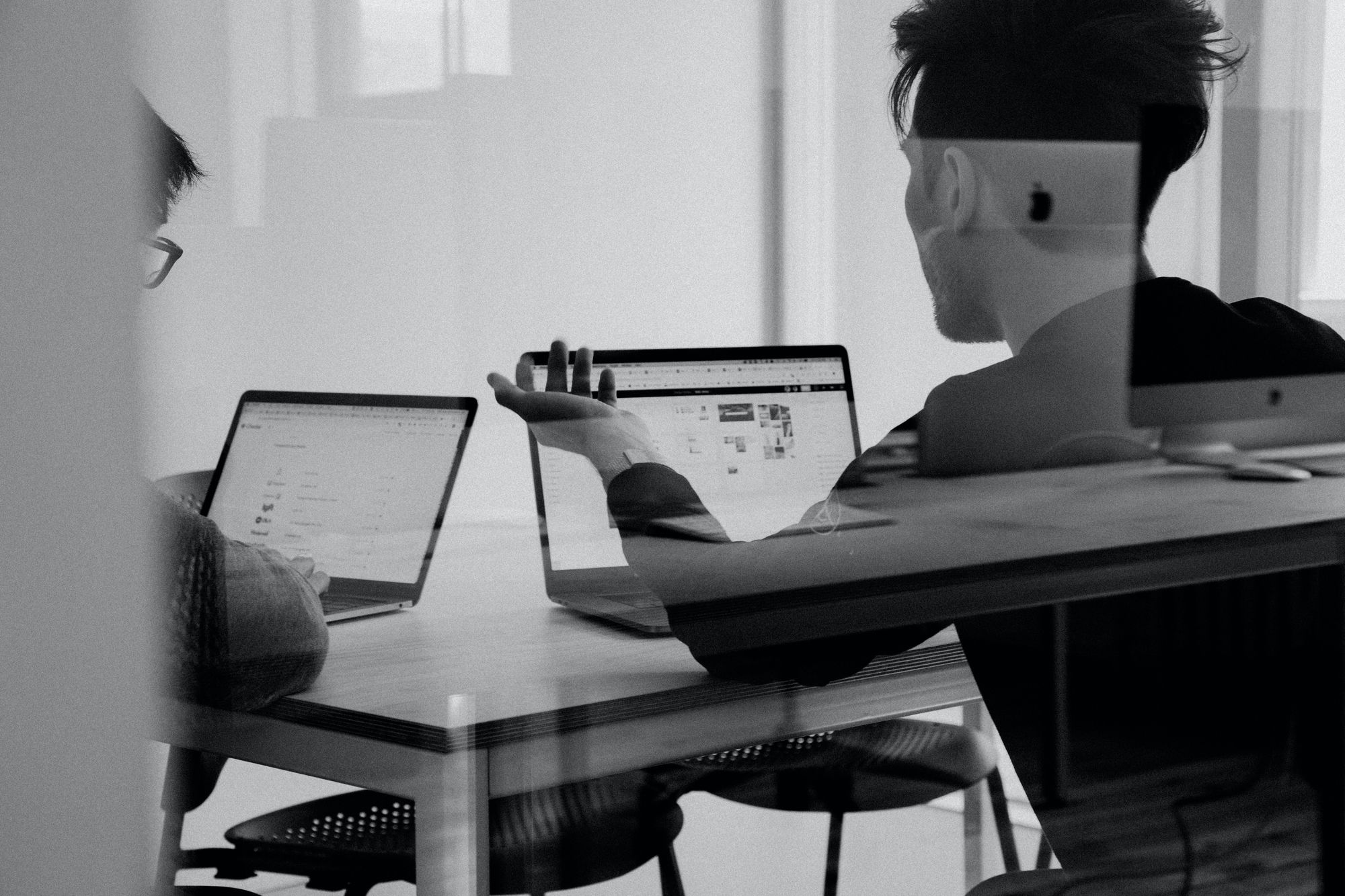
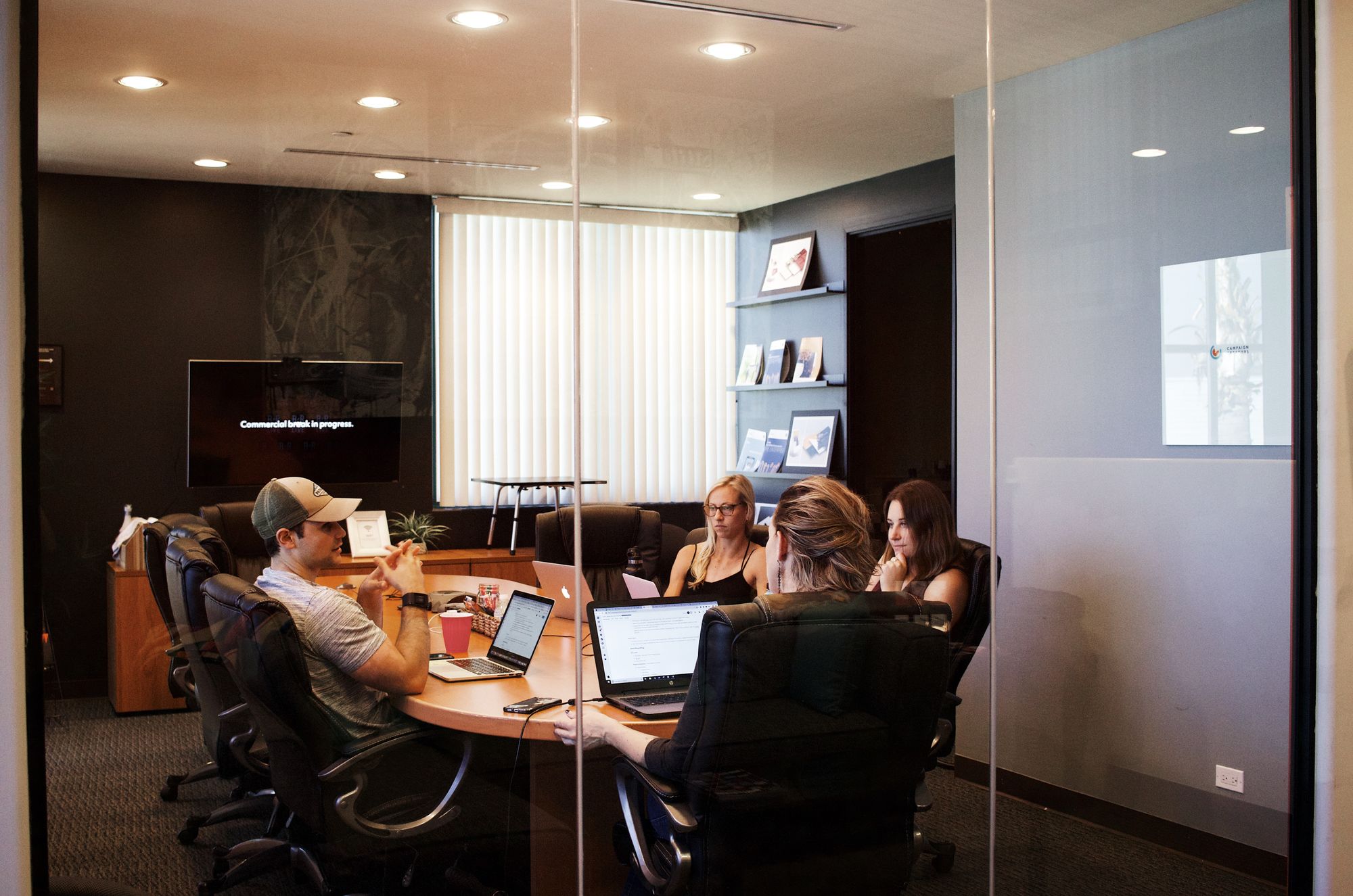
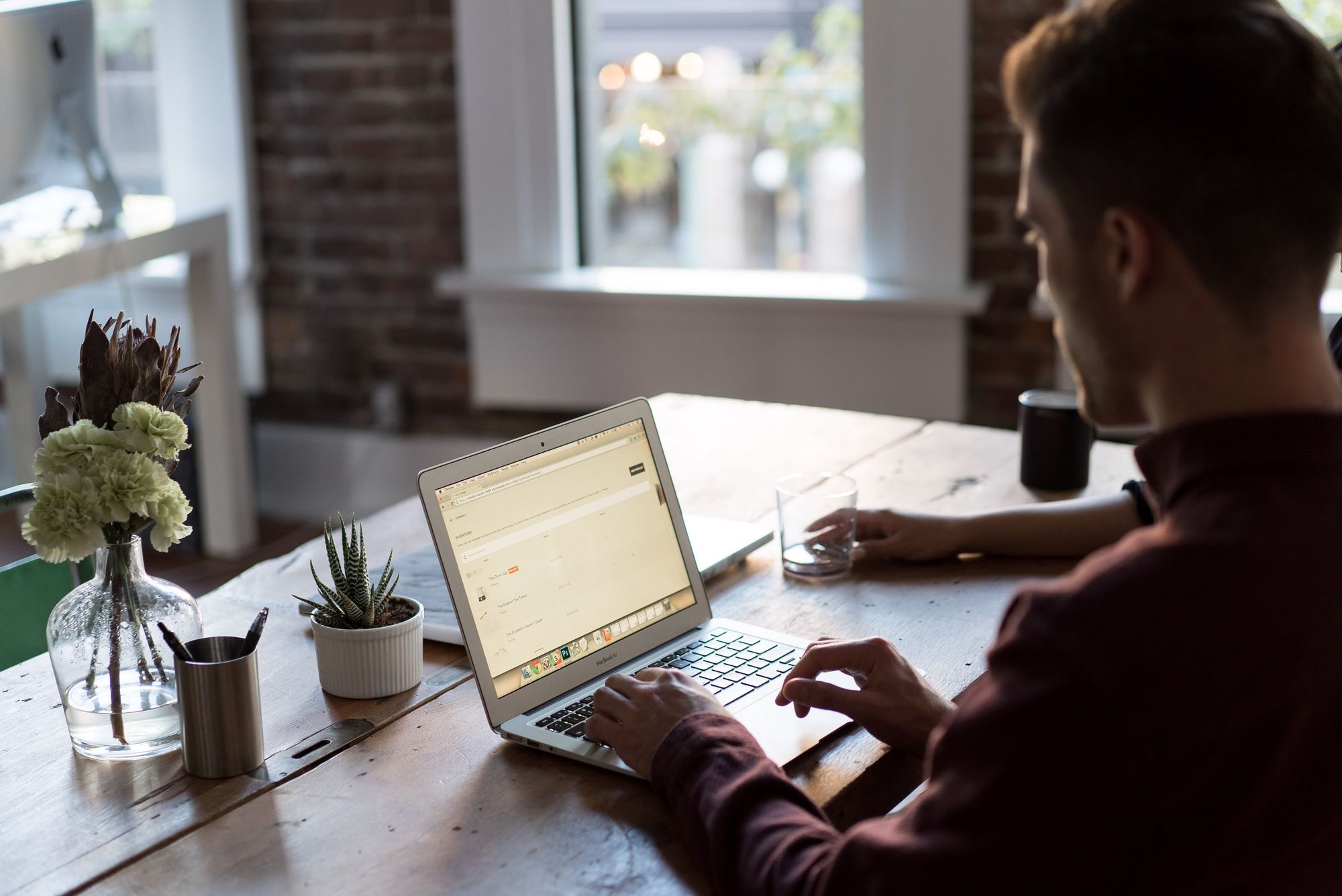