If you're a manufacturer and finding it difficult to estimate your manufacturing costs for WIP. Your problems are over now. Fortunately, there is a formula, and if you understand it, everything will run smoothly.
In modern production, this typically means concentrating on your WIP manufacturing, also known as Work-in-Progress manufacturing.
WIP manufacturing refers to all the expenses for labor, overhead, and materials related to products that are still being created.
By examining these details, you can develop a plan for your manufacturing to become much more cost-effective while also increasing efficiency.
In today’s article, we’ll learn about Work in Progress (WIP) manufacturing, formula, and its related concepts. Let’s take a look at table of content:
- What is WIP Manufacturing?
- Understanding Work in Progress (WIP)
- Calculating WIP in Manufacturing
- Work in Process Manufacturing Formula & Example
- Ways To Reduce WIP in Manufacturing
- Importance of Reducing WIP for Manufacturers
- Benefits of Automating WIP Management
- How to Track and Manage WIP
- What Does Work-in-Progress Mean in Accounting?
- Take WIP Manufacturing to the Top Level
- Frequently Asked Questions (FAQs) Associated with WIP
- How Deskera Can Assist You?
Let’s Start!
What is WIP Manufacturing?
Work in progress (WIP) refers to any inventory that has begun the manufacturing process but is not yet a finished good. WIP refers to the labor, raw materials, and overhead costs incurred on goods that are in various stages of manufacturing.
Reducing WIP is one of the most important elements in attaining lean manufacturing. Since it increases liquidity, promotes a smoother workflow, and enhances performance overall.
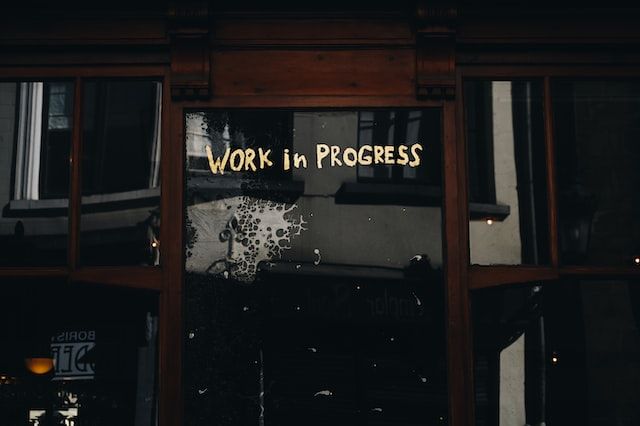
WIPs is one component of the inventory asset account on the balance sheet. These costs are then charged to the finished goods account, which ultimately affects the cost of sales.
The WIP figure only accounts for the value of those products at various intermediate stages of production. The price of unprocessed raw materials that haven't yet been turned into a finished good for sale is not included.
Additionally, the WIP figure also excludes the value of finished goods kept in stock in anticipation of future sales.
Understanding Work in Progress (WIP)
The term "work in progress" (WIP) is used to describe how manufacturing costs move from one stage of production to another. Production costs include the cost of raw materials, labor used to assemble products, and allocated overhead.
The overall production expenses incurred for partially finished goods are represented by the balance in WIP.
For the purpose of making bicycles— certain elements are employed as the primary component. It includes saddles, gear shifts, wheels, brakes, and so on.
The costs of all these products, the labor put into them, and the manufacturing overheads linked with them are now the assets for current inventory on your balance sheet.
The costs of all these products, the labor put into them, and the manufacturing overheads linked with them are now the assets for current inventory on your balance sheet. The finished goods account and, eventually, your cost of goods sold (COGS) are then added to them.
They constitute a cost that must be kept apart from your finished goods until they do, though. The benefit of doing this is that you will find that many of your production bottlenecks and opportunities for possible improvement are in the fabrication of WIP.
For instance, issues may develop if there is no method in place for procuring materials or if some materials are more prone to breaking.
Note: When compared to a business that sells highly customized products (like handmade products), one that purchases finished goods directly from a manufacturer or supplier is less likely to manage the WIP inventory process.
Calculating WIP in Manufacturing
The calculation is more challenging for work-in-progress inventory (WIP) because there are more moving parts than there are for finished goods.
However, we must first understand some terms and calculations before attempting to calculate the value of WIP inventory.
Beginning WIP Inventory Cost:
The WIP balance from the balance sheet for the previous period is the starting WIP inventory cost. In other words, the beginning balance for the new period is determined using the closing WIP inventory from the previous period.
Manufacturing Costs:
Manufacturing expenses are any costs incurred during the production of the completed good. It pays for labor, supplies, and overhead costs. As the quantity of WIP inventory grows during the manufacturing process, the cost of labor and raw materials increases.
The formula for manufacturing cost is as follows:
Cost of Finished Goods (COGS):
The last thing you need to determine is the cost of finished goods, which is the entire cost of your sellable inventory. This includes the cost of raw supplies, manufacturing costs, and administrative costs.
Following the determination of the aforementioned factors, the following formula is used to determine the WIP inventory:
Work in Progress Manufacturing Formula & Example
Today's manufacturers are aware that concentrating on their WIP manufacturing enables them to spot the areas in which their production processes need improvement.
Further, to get the most out of this measure, just make sure that your labor and overhead costs are precise.
Check the basic formula for your WIP manufacturing:
Remember that this is typically computed both annually and during a monthly accounting period.
Consider a manufacturer who wants to determine the amount of work that is still unfinished (WIP) as of the end of the most recent fiscal year, 2021.
If the starting work in progress (WIP) balance is $30 million, he manufacturing costs are $280 million, and the cost of goods manufactured (COGM) is $265 million, what is the final WIP balance?
The assumptions that our model will use are as follows.
Beginning Work in Progress = $30 million
Manufacturing Costs = $280 million
Cost of Goods Manufactured (COGM) = $265 million
The beginning balance is added to, manufacturing costs are then added, and finally the cost of manufactured goods (COGM) is subtracted from the ending work-in-progress inventory roll-forward.
The ending work-in-progress inventory roll-forward begins with the beginning balance, adds manufacturing costs, and then subtracts the cost of manufactured goods (COGM).
Ways To Reduce WIP in Manufacturing
Investigating your WIP production without looking at your raw material inventory would be a little meaningless. The availability of your raw materials, which form the foundation of your production, is crucial to the overall success of your manufacturing business.
So, we determined how much it would cost to produce our WIP. But doing that serves little purpose unless we also use the numbers.
That calls for looking into methods of reducing these expenses and streamlining procedures.
Because many manufacturing companies actually encounter bottlenecks during the production stage, which is where WIP is located, this is the case.
The following techniques can be used to increase productivity in WIP manufacturing:
Just in Time Manufacturing (JIT)
Just-in-time and cellular manufacturing are closely linked concepts. With this approach, a company may deliver the products clients need, in the amounts they need, at the right time.
Just in time (JIT) can balance production by spreading out the manufacturing process evenly over a predetermined amount of time and encouraging a smooth flow between the various processes involved.
Furthermore, JIT offers a practical way to manufacture a variety of goods on a single line when it becomes necessary to do so without encountering major issues.
Just-in-time production and cellular manufacturing are related concepts. With the help of this tactic, a company may give clients the goods they want, when they want them, in the amounts they want.
JIT can balance production by spreading out the manufacturing process over a predetermined amount of time and encouraging a smooth flow between the various processes involved. When it's required, JIT provides a practical way to manufacture a range of goods on a single line without encountering major issues.
Recognize Faulty Machinery
One of the keys to lowering your WIP costs is identifying where your bottlenecks are. The equipment's dependability is another issue that is usually disregarded.
You should look into why a particular set of goods using the same machinery are accruing significant overhead expenses. It's possible that the machine is breaking too many parts and needs replacement parts.
Your machine might then need to be upgraded or fixed. The money and resources you save over time will make it worthwhile, despite the fact that it might seem counterintuitive.
Prepare for Demand
If you begin to carefully examine your sales projections, you'll be able to employ demand planning strategies and heighten your awareness on the factory floor.
With good preparation, many WIP manufacturing expenditures can be avoided. However, if you're aware of when your high and low seasons are starting, you can set the right reorder points for your inventory and keep going lean.
Identifying Obstacles
A bottleneck is a production stage that is designed to handle more jobs than it can produce at its maximum capacity. Simple bottlenecks can occur, such as a sluggish Wi-Fi connection or delaying the commencement of a project.
Employees are compelled to labor longer hours or give up other pursuits when a bottleneck develops in the work process. The WIP time will decrease as a result of removing these bottlenecks, enhancing output.
These bottlenecks can be removed by allocating more resources, usually personnel or materials, to that stage. When the Work in Progress reaches stage C, the manufacturing process will become backed up; this is the bottleneck.
Get in Touch with your Suppliers
Make sure you and your suppliers are on the same page in order to maximize your WIP manufacturing. Using faulty or improper parts can considerably slow down your production operations, despite the fact that it can appear unimportant.
You should be courteous with your suppliers so that you may fully understand what demands you have. Be as clear as you can about how the materials will be used and how they will benefit your project.
Coordinate
Make certain that everyone in the team is focused on the same goal. Every employee should be aware of each step in the manufacturing process because doing so will enable them to finish their work more quickly.
Workers are better able to organize the steps that come before and after them, which speeds up task completion. A modest amount of time saved at each phase results in a large reduction in the production WIP.
Upgrade
Some of the best approaches to reduce WIP in manufacturing environments involve upgrading personnel and equipment. The first and most economical action is to provide training.
Employees will become experts in their fields by developing in-depth training sessions and guidance on how to complete jobs, decreasing WIP. While having skilled workers is essential, their productivity is limited by the speed of their tools.
Upgrading the equipment that they use is essential since training employees won't be effective unless their instruments enable them to complete tasks quickly. Keeping equipment in top condition is frequently the most important aspect of lowering WIP.
Additional ways to improve include increasing the number of staff, resolving network problems, and providing incentives to workers.
WIP Levels and Forecasting
It's a terrific approach to make sure that manufacturing processes work smoothly to keep track of WIP and inventory levels. In order to maintain a smooth operational flow, it is desirable to find the smallest batch sizes and WIP levels.
It's a big challenge to make the right decisions based on demand. The tracking of WIP using a 30,000-foot predictive performance reporting style assists in this decision-making process.
Planning that works well is a result of raising awareness through effective forecasts. The desired outcome is a decreased buffer size because there will be sufficient components to sustain continuous flow without the danger of overstocking.
Therefore, it is essential to collect updated visible WIP level data on a frequent basis utilizing a system that is simple and adaptable to requirements.
Sharing Capacity
The capacity of manufacturing operations is typically greater than the demand that must be satisfied through line production. Companies must identify their bottlenecks in order to develop a policy that enables them to shift some of the workload from the bottleneck operation to nearby activities with higher levels of capacity.
Organizations should continue to be able to share information at predetermined periods. A barrier is that some operators or organizational structure/policies may hinder this way of thinking.
Saving Time and Selecting the Appropriate Operator
To ensure that workflow is carried out easily and effectively, choose operators who have the best skill set for each task, particularly the bottleneck. For operational staff, having top-notch training is also crucial.
It's important to realize that not everyone is the perfect fit for every position. If someone doesn't perform well after receiving enough training, it should be considered whether to move them to another position or, if there are no open positions, whether to fire them.
Importance of Reducing WIP for Manufacturers
Since it has a significant impact on overall production efficiency, monitoring and minimizing work in progress is essential for manufacturing organizations. Therefore, efficient work-in-progress management has many benefits for manufacturing organizations.
Among the key benefits are:
Improved Warehouse Management:
By understanding how much work is currently in progress, manufacturers can assess the utilization of their warehouses and their storage needs. By showing whether the area has more work in progress than is necessary, this enables the prevention of both material and space waste.
Enhanced Inventory Management and Planning:
Manufacturing companies may better plan their inventory and manage their resources by having a better idea of the quantity of work that is currently being done. This makes inventory management and planning more simpler for businesses because they can only buy raw materials from vendors when they actually need them.
Increased Output and Productivity:
When businesses examine their manufacturing process, they frequently discover that there is a sizable quantity of work that is still in progress. This is a sign that the production process needs to be improved.
When WIP exceeds expectations, it may be a sign that production line bottlenecks are to blame for the buildup of unfinished goods. By effectively managing work in progress, businesses can assess their production procedures and optimize operations to increase efficiency.
Boost Customer Satisfaction:
The ability of manufacturers to satisfy demand and deliver orders on time will improve, which will lead to a rise in customer satisfaction. Enhancing client satisfaction requires, among other things, making sure that orders are completed on time.
WIP Reduction Has Advantages
The WIP levels can be increased by using time-saving techniques. Among other things, this can be accomplished by increasing the number of machines or by streamlining the production process to reduce errors and boost output.
Firm policies, such as those that promote successful departmental collaboration for the benefit of the overall business, can also have an effect.
By carefully planning and managing the reduction of WIP levels, businesses can benefit greatly. The business as a whole benefit from the ability to quickly identify and address issues.
Benefits of Automating WIP Management
To optimize manufacturing workflow on the shop floor and effectively manage work in progress, manufacturers must use the data collected by their ERP, MES, and other production systems.
Although it's a common misconception that using digital solutions to monitor production and gather data will take a lot of time and money, the benefits greatly transcend these early investments.
Digitalizing WIP management has the following benefits:
- Digital, data-driven process controls may effectively control a major percentage of the production line, freeing up employees to handle jobs that call for more cognitive ability.
- The solutions that are frequently employed in a production environment automatically gather data, eliminating human mistake, which is a significant cause of WIP.
- The insights offered by WIP management technologies frequently help continuous improvement within a production environment by routinely identifying inefficiencies and giving supervisors the ability to implement remedial actions.
- Workers can identify possible bottlenecks and take action before WIP builds up with the assistance of predictive analytics and well-integrated systems and equipment.
Deskera can connect people, equipment, and technologies in a manufacturing context to automate data collecting across the whole process. Manufacturers are better able to estimate and plan their production requirements with the aid of Deskera's insights, tackling the underlying source of unmanageable WIP.
How to Track and Manage WIP
The majority of e-commerce businesses rely on a supplier or manufacturer for their sellable goods. It's important to comprehend the process and movement of WIP inventory since it can show you how well your supplier or manufacturer generates finished goods.
By working closely with your supplier and other partners in your retail supply chain, such as a 3PL company, you can uncover ways to optimize the supply chain.
Choose the Right Supplier:
Unless you sell a highly customized product, you probably won't have much insight into the WIP inventory process. It is up to your manufacturer to keep an eye on WIP levels and look for ways to reduce costs while boosting labor, workforce, and production operations.
You do have some control over the manufacturer you decide to partner with and the items you source. You can ask your provider questions regarding items like:
- Can costs and lead times for production be lowered?
- Where are the raw resources coming from?
- Can a local factory produce your goods?
Implement Just-in-Time Manufacturing:
The pull system is required by manufacturers for just-in-time production. This lean approach ensures that production won't start before customers have placed their purchases.
Just-in-time production eliminates any additional work that can clog production lines or take up space in the warehouse. Materials are instead only prepared and transformed into finished goods in direct response to consumer demand.
Analyze and Forecast Demand with Precision:
In some operations, producers will choose for a push system rather than a pull system because of the increased demand for their products. As a result, these businesses are continuously striving to meet the ongoing, consistent demand.
However, these manufacturers frequently have a high level of WIP because forecasting errors or unexpected lulls in demand can happen. By analysing the market with advanced forecasting tools, manufacturers can gain a better understanding of market forces and increase the productivity of their production lines.
During times of low demand, these push system manufacturers should use event-driven dispatching systems on the work floor. These systems optimize production along the line by appropriately altering production volume in response to variations in demand.
Use a 3PL to Help with Inventory Management:
The inventory of an e-commerce business is typically its most valuable asset. Once your WIP inventory is converted into sellable items, you will need a system in place to monitor inventory as it is sold.
With the help of Deskera technology, you can easily manage all of your inventory and orders from a unified dashboard while they take care of order fulfilment on your behalf.
Working with a third-party logistics (3PL) provider like Deskera allows you to manage inventory in real-time, examine beginning inventory counts and inventory days on hand, use demand forecasting tools, discover more about inventory turnover, and do a lot more.
Invest in New Tools and Staff:
Operations bottlenecks might increase work-in-progress (WIP). A viable strategy is to modernize tools and equipment that can process work more swiftly and efficiently.
Furthermore, the workers at the station might not be able to control the process, leading to more bottlenecks and WIP.
Multiple training and skill development for employees may help them manage increasing WIP at their workstations.
Additionally, manufacturers have the option of hiring more knowledgeable and qualified operators.
What Does Work-in-Progress Mean in Accounting?
In supply-chain management, products that are only half finished are referred to as "work-in-progress" (WIP). They may also be referred to as "in-process stock."
This covers everything from overhead expenses to the raw components that come together to produce the completed product at a certain point in the manufacturing cycle. WIP is an inventory kind that is accounted for as a current asset.
Several diary entries contain the WIP inventory transactions. The accounting system generates the majority of transactions in a computerized setting. The diary entries for documenting the WIP inventory are, nonetheless, as follows.
For Purchase of Inventory:
Moving Raw Materials to Work-in-Process:
Recording Indirect Cost of Production:
Allocating the Overheads:
Take WIP Manufacturing to the Top Level
A range of raw materials are used to build your unfinished products. Nevertheless, one of the most important challenges is managing your material availability.
Since, despite our best efforts, maintaining materials at their highest levels is rarely that simple. The widespread usage of the same materials in products and assembly components is one of many causes, but it is also a common one.
Due to this, maintaining the correct inventory levels can be difficult without unintentionally stocking too much and raising your carrying costs.
If you use manufacturing ERP, your inventory of raw materials and finished goods will always be at the proper levels. The smart auto booking engine will provide material commitments for your manufacturing and sales orders.
However, Deskera provides more than just precise inventory management.
It's an all-inclusive product that lets you manage your manufacturing and sales from a single, visual interface. To focus on growing your business, you may conveniently follow your order fulfilment operations from start to finish.
Just a few benefits are as follows:
- Your preferred e-commerce, accounting, reporting, and CRM platforms should be connected and integrated.
- Using finished goods and raw material inventories to plan production
- Maintain a single platform for all of your business's operations.
- on-demand access to your manufacturing costs
- Plan your material purchases wisely.
- Excel spreadsheets should never again be used.
The major takeaway from this, though, is to not take your WIP manufacturing lightly. The path your materials take is just as important to the growth of your business as the final products themselves.
The road to growth might become much clearer if you locate your production bottlenecks and reduce your manufacturing costs.
Frequently Asked Questions (FAQs) Associated with WIP
Following we have discussed several frequently asked questions (FAQs) associated with WIP. Let's learn:
Que 1: Is Work-in-Progress a Form of Inventory?
Ans: Inventory items are labelled as "works in progress" when they involve both raw materials and labor from humans. The product's status goes from WIP to finished product after it is completed. The balance sheet depiction of a product moves from inventory to cost of goods sold when it is sold (COGS).
Que 2: What is the Difference between Works-in-Progress and Finished Goods?
Ans: Based on the inventory's relative completion status, which in this case corresponds to saleability, the distinction between work-in-progress (WIP) and finished goods is formed.
Work-in-progress inventory, or WIP for short, refers to items that began as raw materials but are currently undergoing development or assembly to become finished goods. The final stage of inventory, when a product has been finished and is prepared for sale to a customer, is referred to as "finished products."
The terms "work-in-progress" and "finished items" refer to the inventory accounting method used by a certain company. They are not intended to be a rigid definition of the products or materials themselves. It is incorrect to assume that items that are categorized as finished for one organization will likewise be so for another.
For instance, a company that manufactures industrial cabinets may view sheet plywood that has been readied for sale as a finished good, but a lumber mill may view it as a raw material.
Work-in-progress (WIP) and finished items are thus differentiated based on the inventory's level of completion relative to the total inventory. The middle and final stages of an inventory life cycle, respectively, are WIP and finalized products.
Que 3: What is the Difference between ‘Work in Process’ and ‘Work in Progress Inventory?’
Ans: Products that are currently being worked on are not nearly finished. The term "goods-in-process" is also used to describe these items.
The phrase "work-in-process" is sometimes used to refer to commodities that quickly change from being raw materials to finished goods. Manufacturing products might be considered a work-in-process.
As was already said, "work-in-progress" is a word occasionally used to refer to assets that take a very long time to complete, such consulting or building projects. Because this distinction may not always be the norm, both names can often be used to refer to incomplete products.
This inventory is shown on a manufacturing company's balance sheet. This inventory account, like the work-in-progress account, could comprise direct labor, supplies, and manufacturing costs.
Que 4: Role of Work in Process (WIP) Inventory in the Supply Chain
Ans: Even though WIP inventory cannot yet be sold, it is nonetheless counted as an asset on a retailer's balance sheet. Therefore, keeping as little WIP inventory on hand as possible is thought to be best practice.
In fact, a surplus of inventory for work-in-progress could indicate supply-chain bottlenecks. Too much WIP inventory on hand can result in the following factors increasing operating costs and lowering productivity:
- There must be a location to store WIP inventory and holding unsalable stock for an extended period of time will increase carry costs and lower profitability. Make space in the storage facility for completed goods that will bring in money.
- WIP inventory serves as a proxy for committed capital, which includes raw materials and overhead costs. You can reinvest your money in the form of finished, marketable goods by holding as little work-in-progress (WIP) inventory as possible.
- The longer products remain in an incomplete state, the greater the likelihood that they will be lost or destroyed during the process.
Que 5: How to Optimize Work in Process Inventory Flow
Ans: It is especially important to monitor supply network efficiency when there are significant supply chain disruptions that result in a shortage of raw materials and extended lead times.
Many shops now estimate demand and purchase items six months in advance as a result of these lengthier lead times (as opposed to historically forecasting on a quarterly basis).
In order to avoid a buildup of WIP inventory, it is essential to work closely with suppliers to develop the most accurate lead time predictions possible.
Low WIP inventories require accurate inventory cycle counts, which an integrated warehouse management system makes possible (WMS). Accurate, in-the-moment inventory counts enable more precise forecasting, which makes it easier to communicate with vendors and freight forwarders in a more efficient manner.
By outsourcing fulfilment to a 3PL or 4PL, small to mid-sized retailers can gain access to enterprise-level inventory management systems to enhance their WIP inventory flow.
How Deskera Can Assist You?
Deskera MRP allows you to closely monitor the manufacturing process. From the bill of materials to the production planning features, the solution helps you stay on top of your game and keep your company's competitive edge.
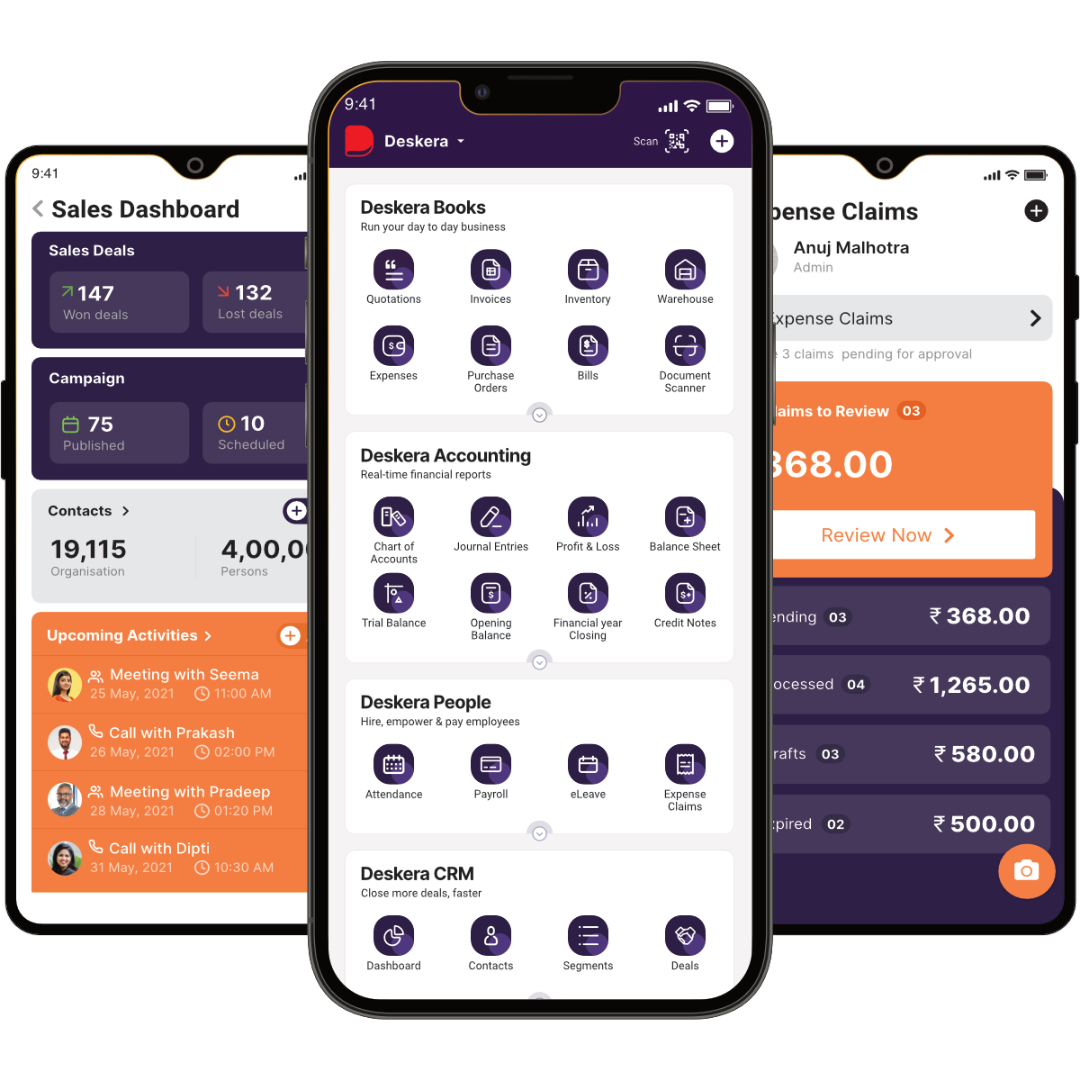
Deskera ERP and MRP system can help you:
- Manage production plans
- Maintain Bill of Materials
- Generate detailed reports
- Create a custom dashboard
Deskera ERP is a comprehensive system that allows you to maintain inventory, manage suppliers, and track supply chain activity in real time, as well as streamline a variety of other corporate operations.
Deskera Books enables you to manage your accounts and finances more effectively. Maintain sound accounting practices by automating accounting operations such as billing, invoicing, and payment processing.
Deskera CRM is a strong solution that manages your sales and assists you in closing agreements quickly. It not only allows you to do critical duties such as lead generation via email, but it also provides you with a comprehensive view of your sales funnel.
Deskera People is a simple tool for taking control of your human resource management functions. The technology not only speeds up payroll processing but also allows you to manage all other activities such as overtime, benefits, bonuses, training programs, and much more.
This is your chance to grow your business, increase earnings, and improve the efficiency of the entire production process.
Key Takeaways
We've arrived at the last section of this guide. Let's have a look at some of the most important points to remember:
- Work in progress (WIP) refers to any inventory that has begun the manufacturing process but is not yet a finished good. WIP refers to the labor, raw materials, and overhead costs incurred on goods that are in various stages of manufacturing.
- The term "work in progress" (WIP) is used to describe how manufacturing costs move from one stage of production to another. Production costs include the cost of raw materials, labor used to assemble products, and allocated overhead.
- Just-in-time production and cellular manufacturing are closely linked concepts. With this approach, a company may deliver the products clients need, in the amounts they need, at the right time.
- Make sure you and your suppliers are on the same page in order to maximize your WIP manufacturing. Using faulty or improper parts can considerably slow down your production operations, despite the fact that it can appear unimportant.
- Upgrading the equipment that they use is essential since training employees won't be effective unless their instruments enable them to complete tasks quickly. Keeping equipment in top condition is frequently the most important aspect of lowering WIP.
- When businesses examine their manufacturing process, they frequently discover that there is a sizable quantity of work that is still in progress. This is a sign that the production process needs to be improved.
- Working with a third-party logistics (3PL) provider like Deskera allows you to manage inventory in real-time, examine beginning inventory counts and inventory days on hand, use demand forecasting tools, discover more about inventory turnover, and do a lot more.
Related Articles
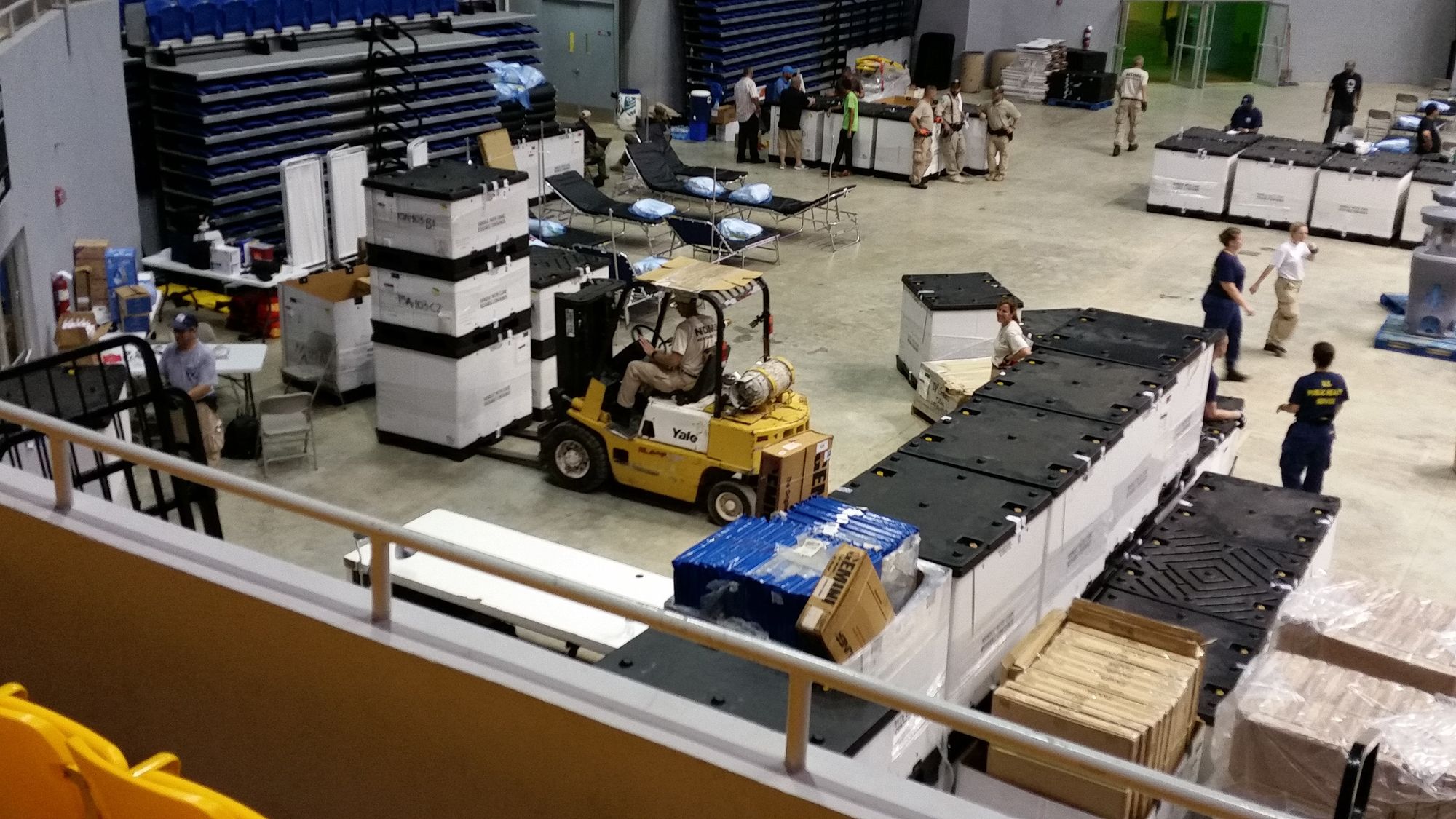
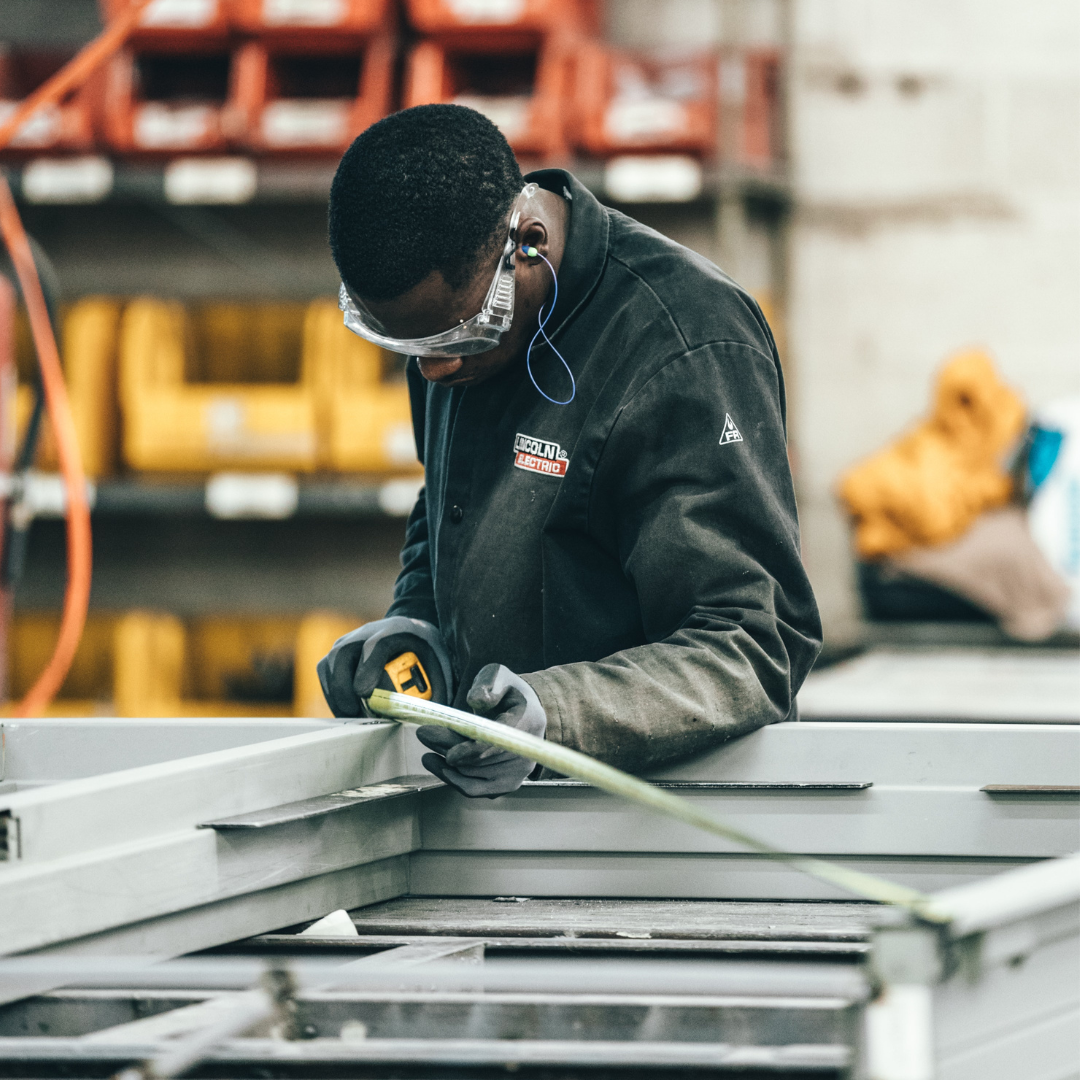
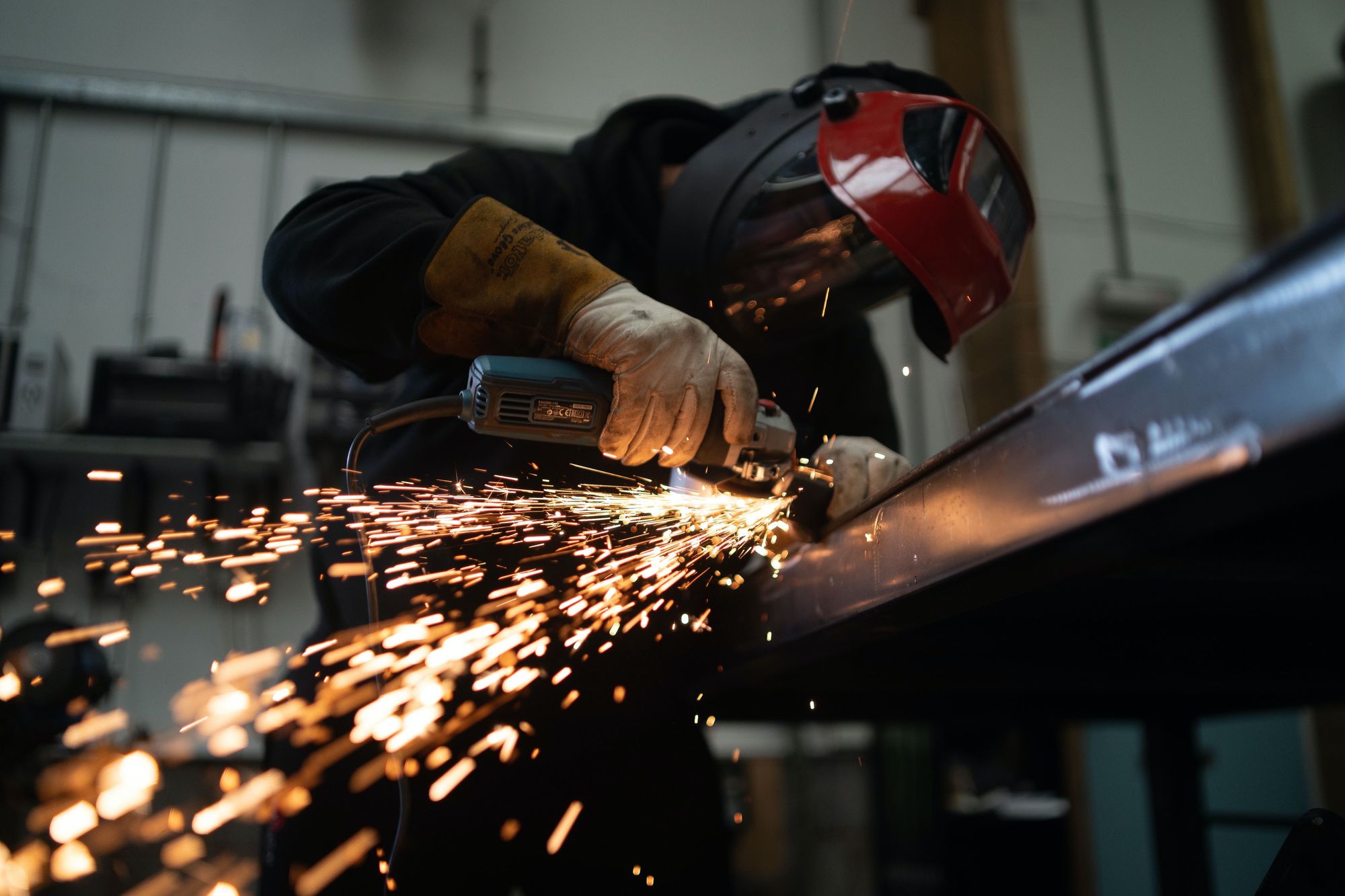
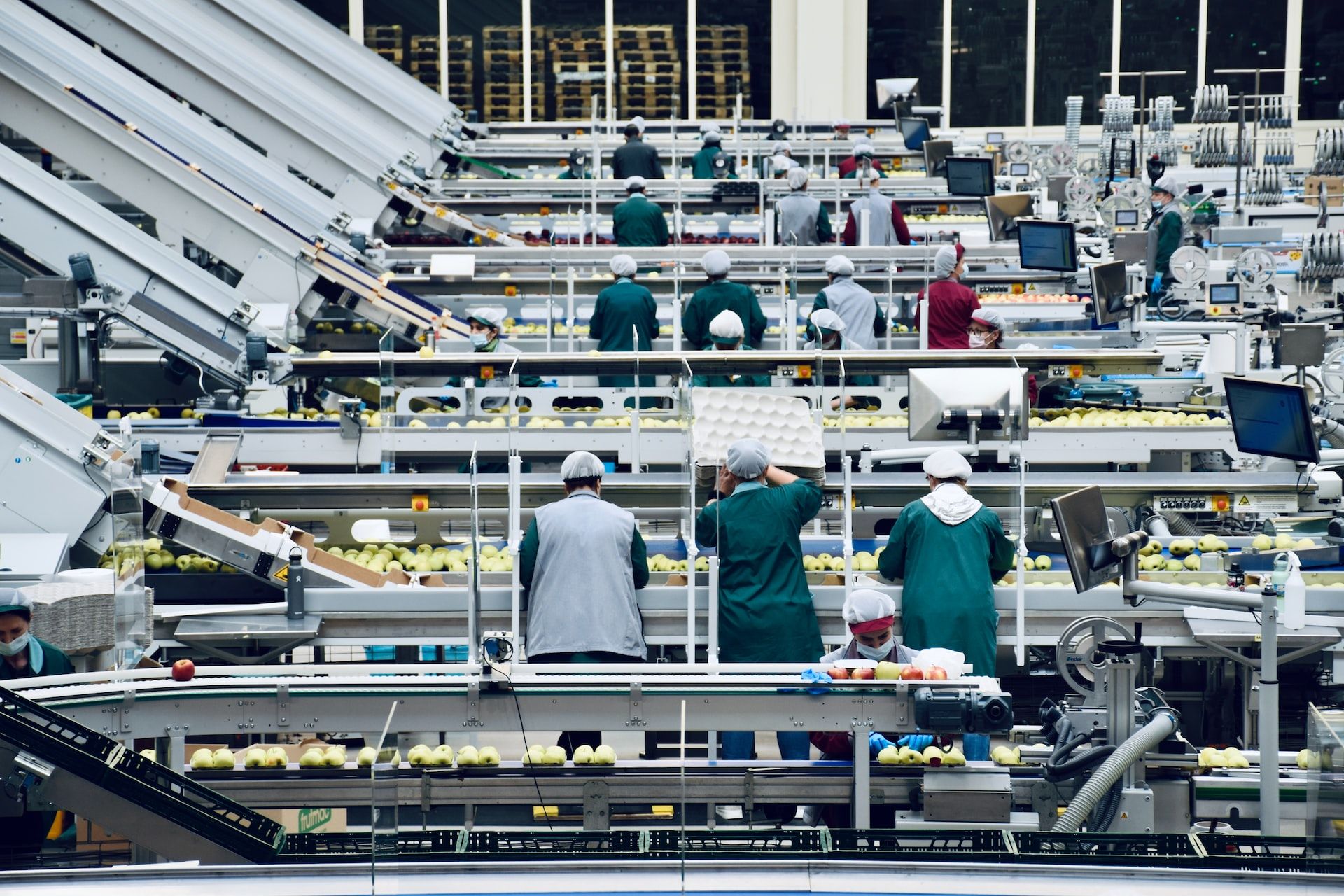