For SME manufacturers, the daily struggle of keeping the production line running smoothly is usual. Every day, they have to face a multitude of challenges that can quickly derail the operations, from unexpected material shortages to equipment breakdowns and tight deadlines.
These issues not only cause frustration but also cost valuable time and money. When stakes are that high, you need to adopt solutions strategically and quickly. That's where SMEs turn to Material Requirements Planning (MRP) software, like Deskera MRP.
Gartner says, in 2024 alone, 54 percent of manufacturers will spend on software solutions for their production inefficiencies. This gives us an idea of how important tools like MRP are for SMEs to function properly and run operations smoothly.
This tool is designed specifically to address the unique needs of SME manufacturers. It will help in streamlining production processes, reducing waste, and improving overall efficiency.
Let's get an in-depth understanding of Material Requirements Planning (MRP) software in this blog:
What is Material Requirements Planning (MRP)?
MRP in business stands for Material Requirements Planning. It is a system used for efficient inventory management and production planning.
MRP ensures that materials and products are available for production and delivery to customers by calculating the quantities and timing needed for each component. It takes into account sales forecasts, bills of materials, and inventory data.
MRP is part of a broader category of solutions called Manufacturing Resource Planning (MRP II). MRP II includes additional features like resource capacity planning, shop floor control, and financial integration.
MRP helps determine what materials to order and when. By analyzing demand and supply, MRP generates a detailed production schedule. This schedule outlines the materials, parts, and components needed at each stage of production.
The main objectives of Material Requirements Planning (MRP) software are:
- Ensuring materials are available when required
- Maintaining the lowest possible inventory levels
- Planning manufacturing activities and purchase orders
MRP is especially beneficial for businesses with complex manufacturing processes. It helps manage materials with long lead times or dependent demand. Dependent demand items are components used to make finished products.
How does Material Requirements Planning work
In operations management, Material Requirements Planning (MRP) works by processing various inputs to generate a detailed production plan. The MRP system analyzes sales and demand forecasts, inventory levels, and bills of materials (BOMs) to determine the required materials and their quantities.
The Material Requirements Planning process involves the following steps:
1. Input Gathering
The MRP system collects data from various sources. This includes sales forecasts, BOMs, inventory records, and open orders.
2. Bill of Materials Explosion
MRP breaks down the finished product into its component parts and raw materials. This process, called BOM explosion, helps determine the quantities of each item needed.
3. Inventory Check
The system checks current inventory levels and compares them with the required quantities. It identifies any shortages or excess stock.
4. Lead Time Offsetting
MRP considers the lead times for each component. Lead time is the time required to procure or produce an item. MRP schedules the orders based on these lead times to ensure timely availability.
5. Generating Planned Orders
Based on the above information, MRP generates a schedule of planned orders. These orders specify the quantities and timing for purchasing or producing each item.
6. Capacity Check
MRP verifies if the planned orders can be fulfilled within the available production capacity. If capacity is insufficient, the system may suggest overtime or reschedule orders.
7. Order Release
Once the plan is finalized, MRP releases the orders to the purchasing and production departments for execution.
Material Requirements Planning software constantly updates the plan based on changes in demand, inventory, or capacity. This dynamic nature helps businesses adapt to fluctuations in these key variables.
MRP vs ERP
Material Requirements Planning (MRP) and Enterprise Resource Planning (ERP) are both software solutions used by businesses to manage their operations. However, there are some key differences between the two.
Material Requirements Planning focuses primarily on inventory management and production planning. It helps businesses plan and control their manufacturing processes. It ensures the right materials are available when needed for production.
On the other hand, Enterprise Resource Planning or ERP is a more comprehensive solution. It integrates various business functions into a single system. ERP modules can include:
- Financial management
- Human resources
- Customer relationship management (CRM)
- Supply chain management
- Manufacturing
- Project management
ERP aims to provide a unified view of a company's operations. It enables data sharing and collaboration across departments.
While MRP is a crucial component of manufacturing businesses, ERP is suitable for a wider range of industries. ERP can be used by manufacturers, distributors, service providers, and other businesses.
Another difference is the scope of the systems. MRP focuses on materials and production, while ERP includes a broader set of business functions. ERP includes MRP as a module, but also offers additional features like financial management and HR.
In terms of implementation, MRP is generally less complex than ERP. MRP can be implemented as a standalone system or as part of an ERP solution. ERP implementations are usually more time-consuming and resource-intensive due to their broader scope.
Who uses Material Requirements Planning software?
Material Requirements Planning (MRP) is used by a wide range of businesses, particularly those involved in manufacturing and assembly. Some common industries that benefit from Material Requirements Planning systems include:
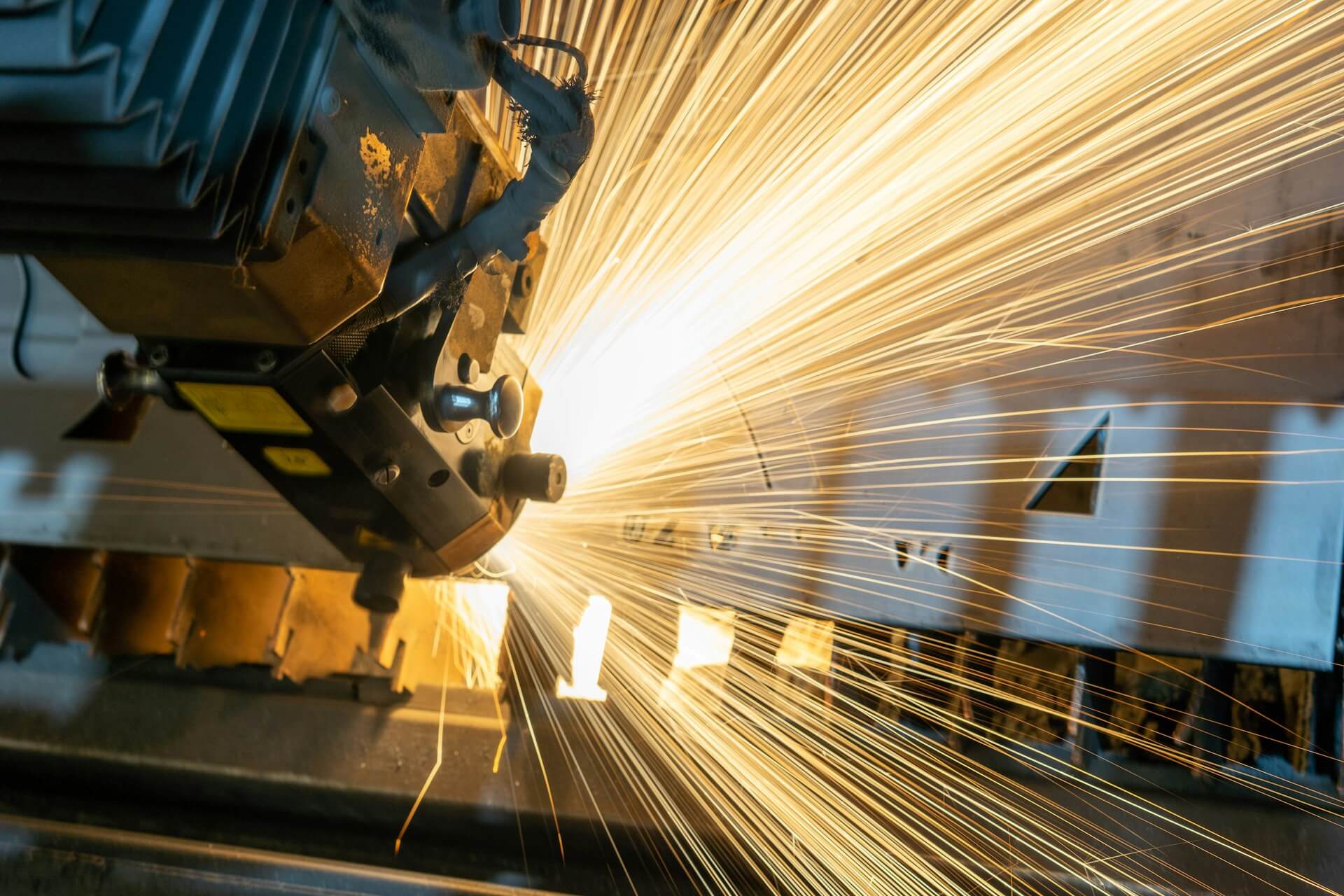
1. Discrete manufacturing
Companies that produce distinct, countable products use MRP. Examples include automotive, electronics, and furniture manufacturers.
2. Process manufacturing
Businesses that produce products through a series of steps or formulas also use MRP. This includes food and beverage, chemical, and pharmaceutical companies.
3. Make-to-Order (MTO) manufacturers
MTO companies produce goods based on specific customer orders. MRP helps them plan and schedule production based on these orders.
4. Make-to-Stock (MTS) manufacturers
MTS companies produce goods based on sales forecasts and store them as inventory. MRP helps them maintain optimal stock levels and plan production accordingly.
5. Assemble-to-Order (ATO) manufacturers
ATO companies produce components and assemble them based on customer orders. MRP helps them manage component inventory and plan assembly operations.
6. Job shops
Job shop manufacturing is the type of manufacturing that produces small batches of custom products. MRP helps job shops manage the unique materials and processes required for each job.
In addition to manufacturers, other businesses that use MRP include:
- Distributors: Companies that purchase and resell products use MRP to manage inventory and plan purchases.
- Service providers: Businesses that offer services requiring materials, such as construction or equipment repair, use MRP to plan and manage their material needs.
- Retailers: Some retailers use MRP to manage their private label products or to plan inventory for high-demand items.
Regardless of the industry, businesses that deal with complex bills of materials, long lead times, or dependent demand can benefit from MRP.
Benefits of using Material Requirements Planning software
Implementing a Material Requirements Planning (MRP) system offers numerous benefits to businesses. Some of the key advantages include:
1. Improved inventory management
MRP helps businesses maintain optimal inventory levels. By analyzing demand and supply, MRP reduces the risk of stockouts and overstocking. This leads to lower inventory costs and improved cash flow.
2. Enhanced production planning
MRP generates detailed production schedules based on sales forecasts and BOMs. This helps businesses plan their manufacturing activities more efficiently. By considering lead times and capacity constraints, MRP ensures a smooth flow of materials and resources.
3. Increased efficiency
MRP automates many manual tasks associated with inventory management and production planning. This reduces the time and effort required to manage these processes. By streamlining operations, MRP helps businesses improve overall efficiency and productivity.
4. Better customer service
MRP helps businesses deliver products on time by ensuring material availability. By reducing stockouts and improving production scheduling, MRP enhances a company's ability to meet customer demand. This leads to higher customer satisfaction and loyalty.
5. Cost savings
MRP helps businesses reduce various costs associated with inventory and production. By optimizing inventory levels, MRP minimizes the costs of holding excess stock. By improving production planning, MRP reduces the costs of overtime, expediting, and obsolescence.
6. Improved decision-making
MRP provides businesses with real-time data and insights into their inventory and production processes. This information helps managers make informed decisions about purchasing, scheduling, and capacity planning. By enabling data-driven decision-making, MRP helps businesses respond quickly to changes in demand or supply.
7. Competitive advantage
By improving efficiency, reducing costs, and enhancing customer service, MRP helps businesses gain a competitive edge in their market. Companies that effectively leverage MRP can deliver products faster, cheaper, and with higher quality than their competitors.
Challenges in using a Material Requirements Planning software
While Material Requirements Planning (MRP) offers many benefits, businesses may also face some challenges when implementing and using these systems. Some common challenges include:
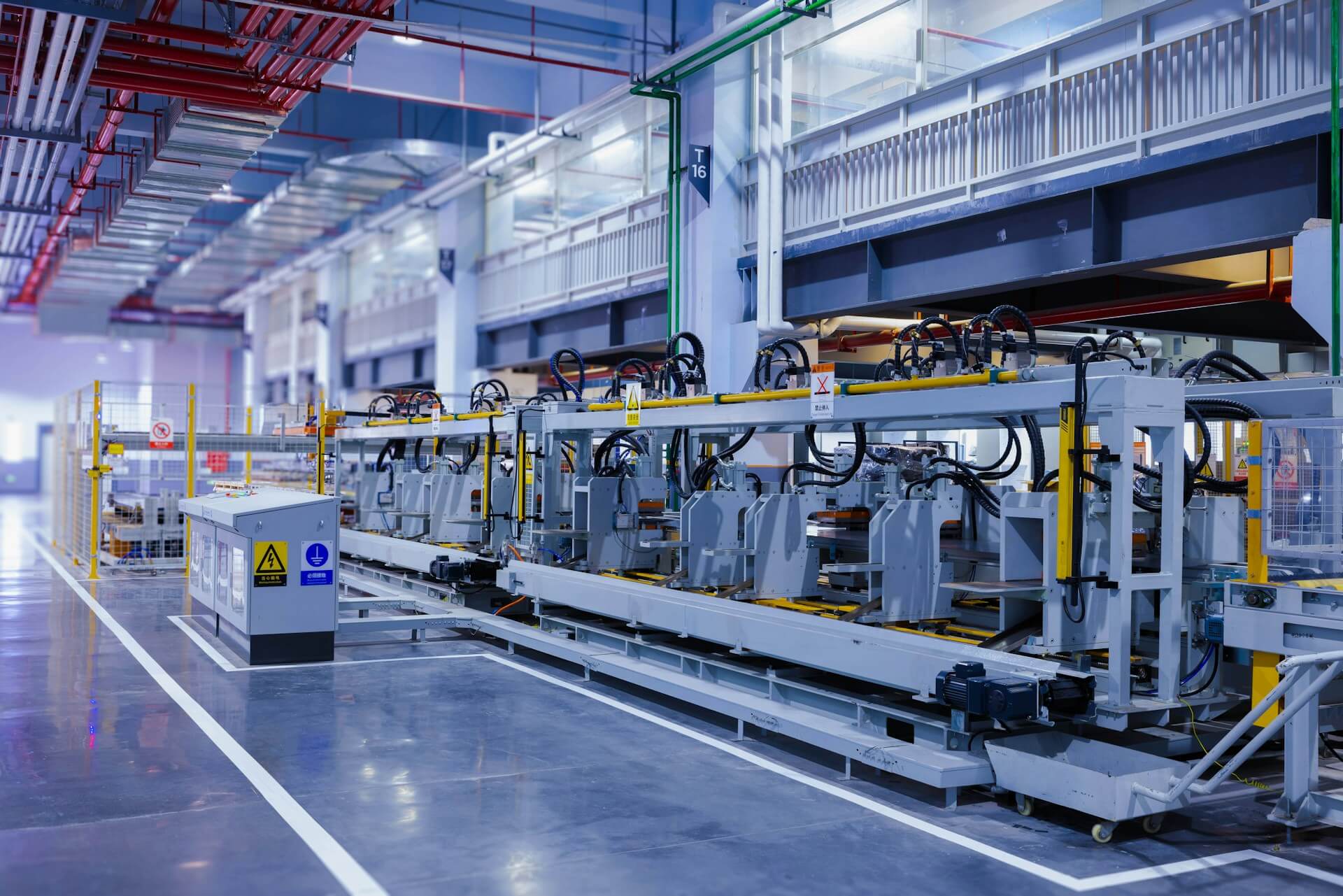
1. Data accuracy
MRP relies on accurate data inputs to generate reliable plans. Inaccurate information about inventory levels, BOMs, or lead times can result in flawed plans. Ensuring data accuracy requires discipline and regular updates to the system.
2. Integration with other systems
MRP often needs to integrate with other business systems, such as CRM or ERP. Integrating disparate systems can be complex and time-consuming. Incompatible data formats or legacy systems can further complicate the process.
3. Complexity
MRP systems can be complex, especially for businesses with diverse product lines or multi-level BOMs. Understanding and managing the various parameters and settings can be challenging for users. This complexity can lead to errors or suboptimal results.
4. Resistance to change
Implementing MRP often requires changes to existing processes and workflows. Employees may resist these changes, especially if they are comfortable with the current methods. Overcoming this resistance requires effective change management and training.
5. Lack of flexibility
MRP systems are designed to optimize inventory and production based on certain assumptions and parameters. However, real-world conditions can be unpredictable. Changes in demand, supply disruptions, or quality issues can disrupt the MRP plans. Adapting to these changes may require manual interventions or system modifications.
6. Cost
Implementing and maintaining an MRP system can be costly, especially for small businesses. The costs include software licenses, hardware, training, and support. Justifying these costs requires a clear understanding of the expected benefits and ROI.
7. Dependency on technology
MRP systems are computer-based and rely on technology to function. Hardware failures, software glitches, or network issues can disrupt the MRP process. Businesses need robust IT infrastructure and support to minimize these risks.
Now let’s move on to understanding the key components involved in a Material Requirements Planning software.
The Key Components of Material Requirements Planning software
A Material Requirements Planning (MRP) system consists of several key components that work together to generate accurate production plans. These components include:
1. Master Production Schedule (MPS)
The Master Production Schedule or MPS is a high-level plan that outlines the quantity and timing of finished goods production. It is based on sales forecasts, customer orders, and inventory targets. The MPS drives the MRP process by specifying what needs to be produced and when.
2. Bill of Materials (BOM)
The BOM is a comprehensive list of all the raw materials, components, and subassemblies required to produce a finished product. It specifies the quantities and relationships between these items. The BOM is used by MRP to determine the material requirements for each level of production.
3. Inventory Records
MRP relies on accurate inventory records to determine the current stock levels of raw materials, components, and finished goods. These records include information about item quantities, locations, and statuses (e.g., reserved, allocated, or available).
4. Item Master
The item master is a database that contains detailed information about each item used in production. This includes item descriptions, lead times, suppliers, and lot sizing policies. MRP uses this information to generate purchase orders and production schedules.
5. MRP Engine
The MRP engine is the software component that processes the inputs (MPS, BOM, inventory records, and item master) to generate the output (planned orders). It uses complex algorithms to calculate material requirements, consider lead times, and adjust for inventory levels.
6. Planned Orders
Planned orders are the output of the MRP process. They specify the quantities and timing of materials to be purchased or produced to meet the MPS requirements. Planned orders are used to create purchase orders and production work orders.
Integrating MRP with Other Business Processes
Integrating Material Requirements Planning (MRP) with other business processes is essential for maximizing its benefits and ensuring a seamless flow of information across the organization. Some key areas where MRP integration can add value include:
1. Sales and Operations Planning (S&OP)
Integrating MRP with S&OP processes helps align production plans with sales forecasts and strategic goals. By sharing demand and capacity information between the two systems, businesses can make informed decisions about resource allocation, inventory levels, and production schedules.
2. Supply Chain Management (SCM)
Integrating MRP with Supply Chain Management (SCM) systems enables better coordination between suppliers, manufacturers, and customers. By sharing real-time information about material requirements, purchase orders, and delivery schedules, businesses can optimize their supply chain operations. This leads to reduced lead times, improved supplier performance, and better customer service.
3. Shop Floor Control (SFC)
Integrating MRP with SFC systems helps bridge the gap between planning and execution. By sharing production schedules and work orders, MRP ensures that the right materials are available when needed on the shop floor. SFC systems provide real-time feedback on production progress, quality issues, and resource utilization, which can be used to update the MRP plans.
4. Financial Management
Integrating MRP with financial systems, such as accounting or Enterprise Resource Planning (ERP), enables better cost control and financial visibility. By sharing information about material costs, inventory valuations, and purchase orders, businesses can accurately track their financial performance. This integration also facilitates better budgeting, cash flow management, and financial reporting.
5. Product Lifecycle Management (PLM)
Integrating MRP with PLM systems helps manage the entire lifecycle of a product, from concept to retirement. By sharing information about product designs, BOMs, and engineering changes, MRP ensures that the right materials and components are used in production. PLM integration also facilitates better collaboration between design, engineering, and manufacturing teams.
Choosing the Right MRP Solution for Your Business
When choosing a Material Requirements Planning (MRP) solution for your business, it's crucial to prioritize your specific manufacturing needs and goals over simply following industry trends.
You need a solution that aligns perfectly with your unique requirements, and this is where Deskera MRP shines.
Deskera MRP is designed to address the challenges faced by modern manufacturing businesses, offering a comprehensive set of features to streamline your processes and boost productivity.
With Deskera MRP, you get:
- Advanced inventory management
- Powerful production planning and scheduling
- Streamlined purchase order management
- Real-time analytics and reporting
- A scalable and flexible platform
- Seamless integration with other business functions
- User-friendly interface and customizable dashboards
- Cloud-based deployment for easy access and reduced IT costs
Choose Deskera MRP and experience the difference it can make for your manufacturing business.
Schedule a call with our experts today.
Key Takeaways
To summarize, here are the key takeaways from what we understood about Material Requirements Planning:
- Material Requirements Planning is a software-based system that helps businesses plan and control manufacturing processes, ensuring the right materials are available at the right time.
- Material Requirements Planning generates a detailed production schedule by taking into account sales forecasts, bills of materials, and inventory data.
- The main objectives of MRP are ensuring material availability, maintaining low inventory levels, and planning manufacturing activities and purchase orders.
- MRP focuses on inventory management and production planning, while ERP is a more comprehensive solution integrating various business functions.
- Businesses in manufacturing and assembly, such as discrete, process, and order-based manufacturers, commonly use MRP.
- Benefits of MRP include improved inventory management, production planning, efficiency, customer service, cost savings, decision-making, and competitive advantage.
- Challenges in using MRP include data accuracy, system integration, complexity, resistance to change, lack of flexibility, cost justification, and technology dependency.
Related Articles
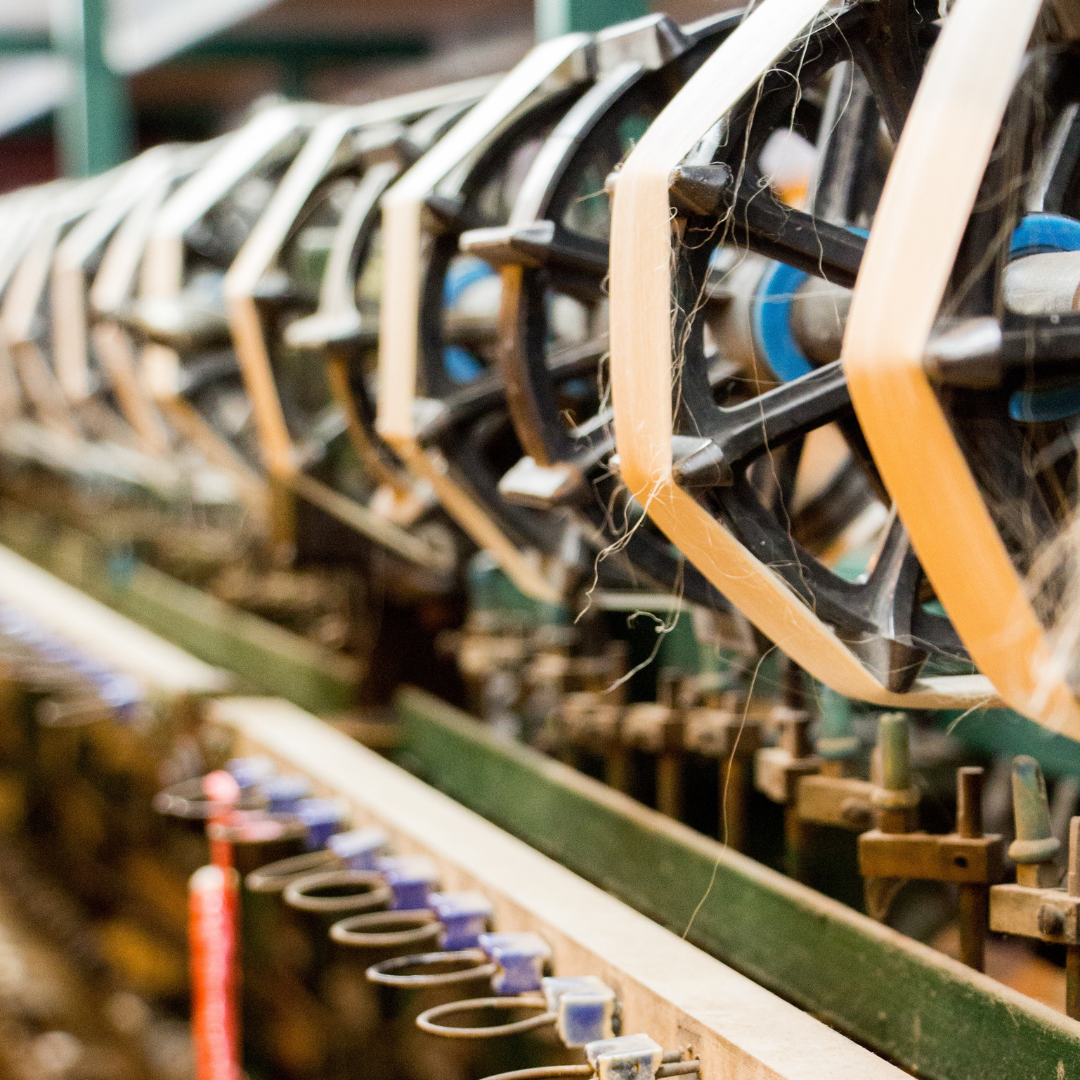
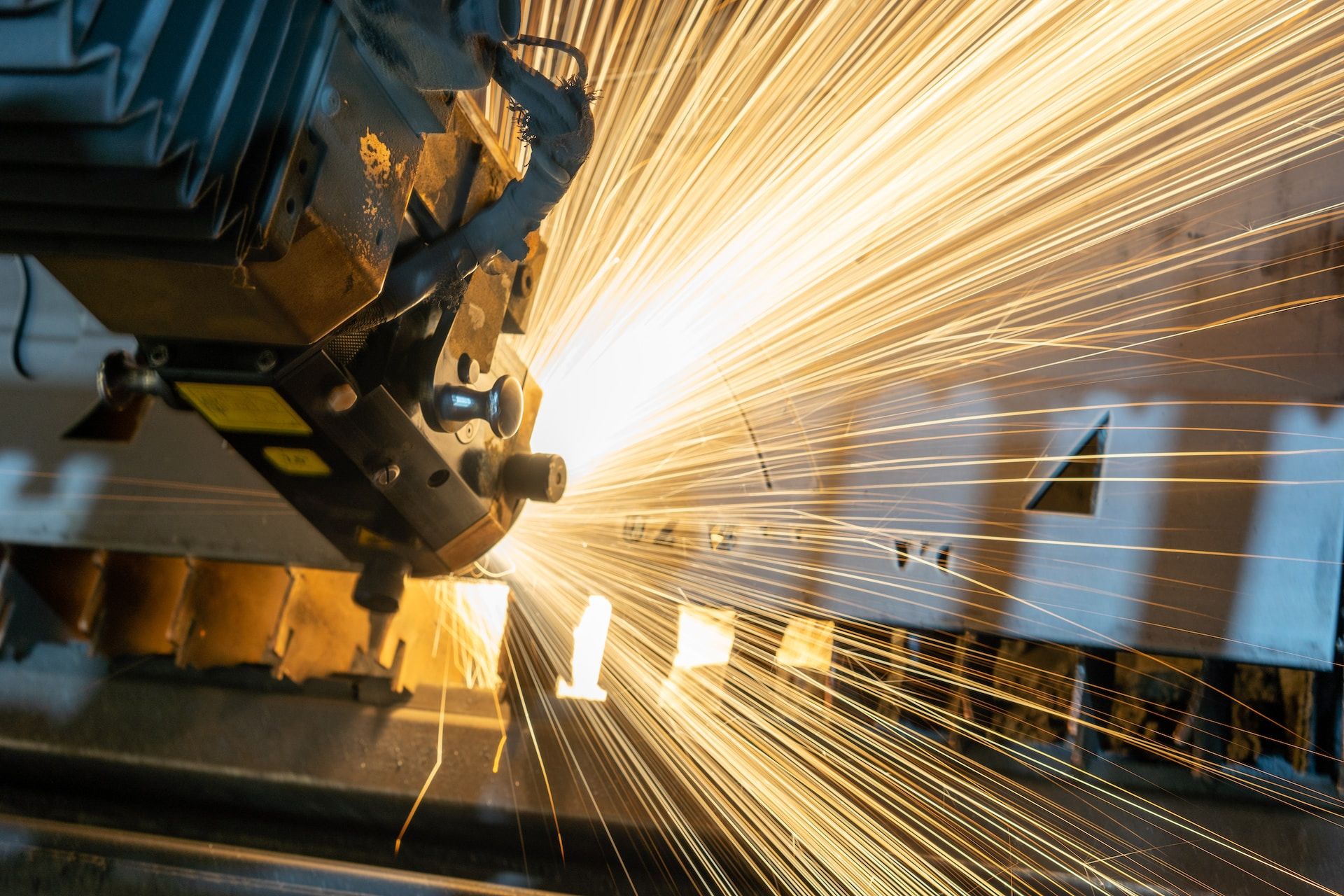
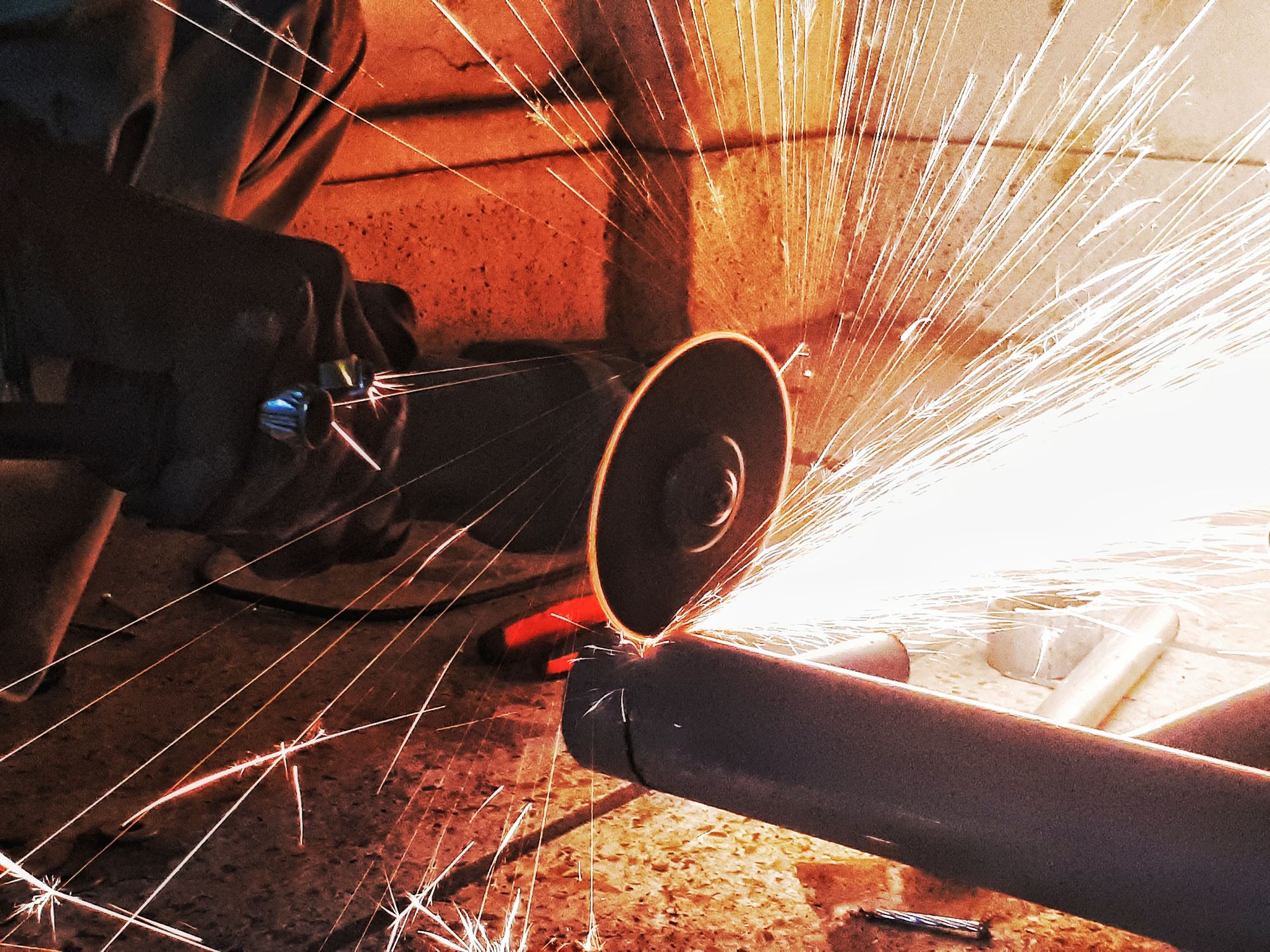
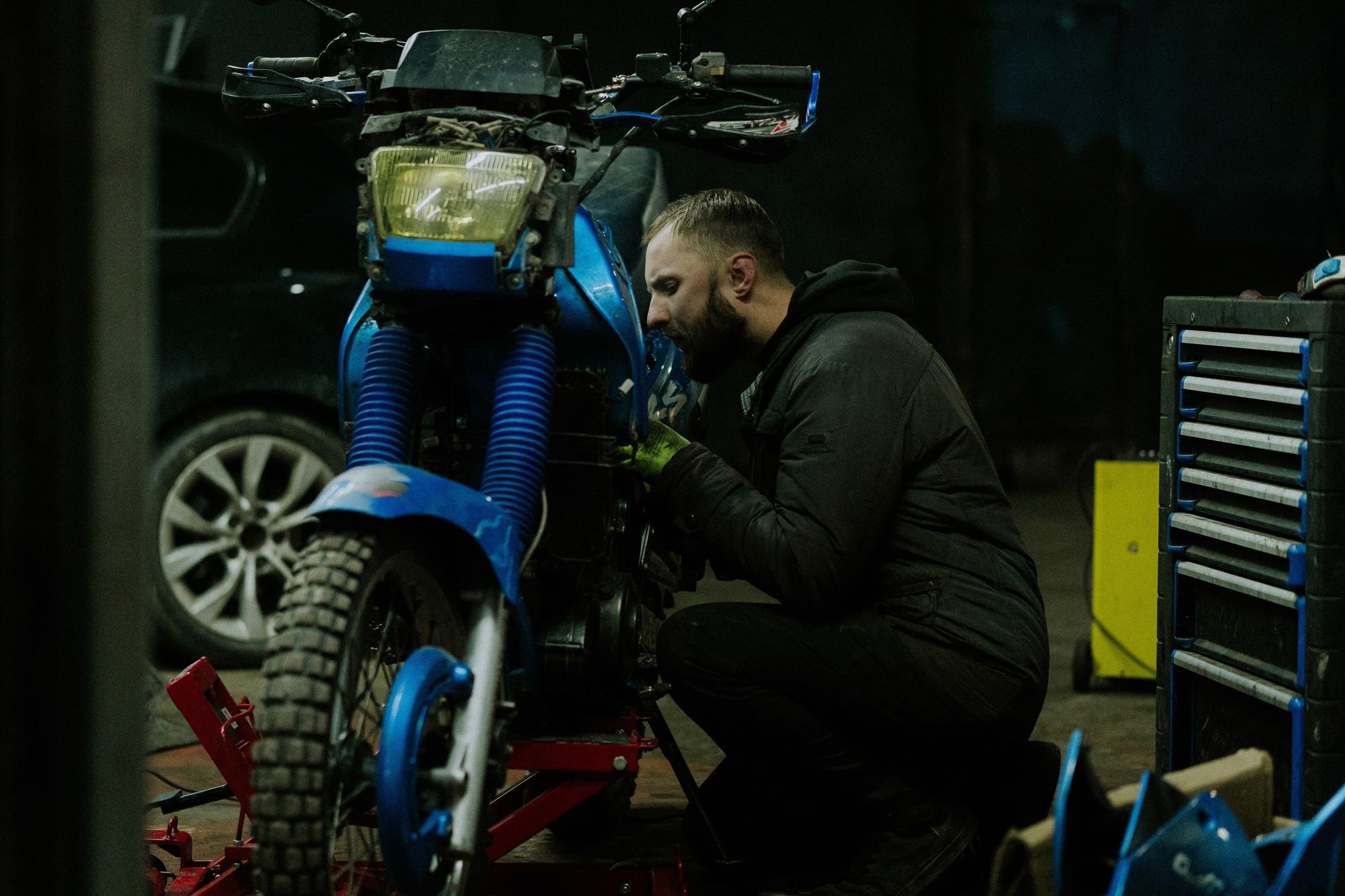