Batch Manufacturing Records (BMR) are essential to any pharmaceutical or medical device manufacturing. These documents allow manufacturers to track and document the production process and ensure product quality.
From start to finish, batch records provide an audit trail of the manufacturing process and the materials used. Thus, enabling manufacturers to maintain control of the production process and ensure regulatory compliance.
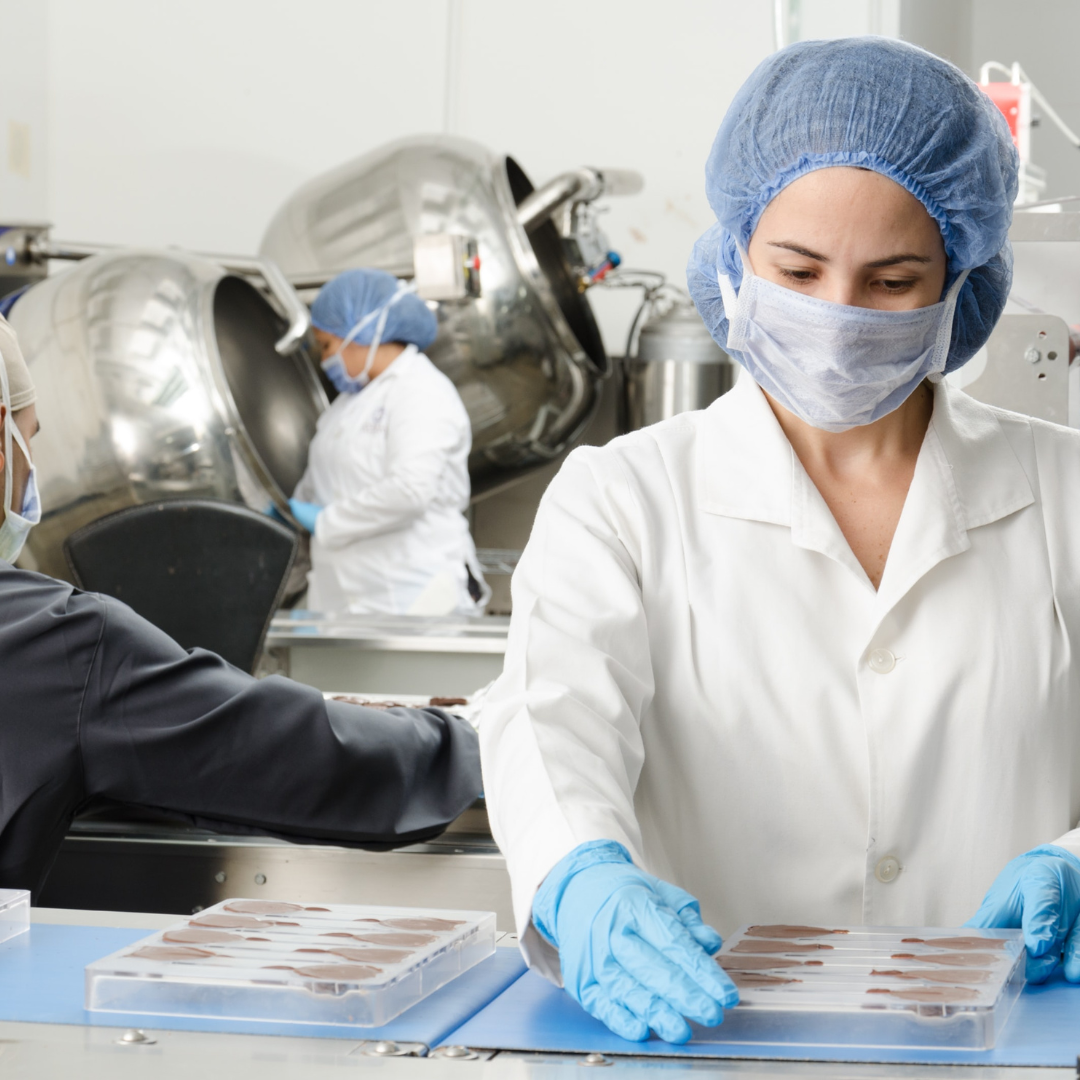
In this article, we will explore the importance of batch records, their benefits, and the steps involved in creating them.
- What is a Batch?
- What are Batch Manufacturing Records?
- Importance of Batch Manufacturing Records
- Types of Batch Manufacturing Records
- What is included in a Batch Manufacturing Record?
- Requirements of Batch Manufacturing Records
- Benefits of Using Software Solutions for Batch Manufacturing Records
- How to Select the Best BMR Software?
- 8 Best Practices for Batch Manufacturing Records
- Conclusion
- How can Deskera Help You?
- Key Takeaways
- Related Articles
What is a Batch?
A batch in pharma manufacturing is a specific quantity of a drug product intended to have uniform character and quality within specified limits. It can be produced according to single or multiple production orders during the same cycle of manufacture and is intended to be available as a homogenous product.
A batch has a unique identification number that is clearly identified and recorded during production.
What are Batch Manufacturing Records?
Batch Manufacturing Records are documents used to track production batches throughout the manufacturing process. These records typically include detailed instructions on how to manufacture a product, quality control procedures, test results, and other relevant data.
This data is used to ensure that the product meets the required specifications and safety standards set by the regulatory bodies.
However, before the BMR can be created, chemical and process manufacturers must first establish another document: the master formula record (MFR).
What Precisely is a Master Formula Record (MFR)?
The MFR is a collection of instructions that teaches you how to make a product batch. It differs from a BMR as a BMR is a record of what you made.
Consider this method to be similar to the process of making a loaf of bread.
- The MFR is your recipe; it tells you how much flour to use and how many eggs to use.
- It also instructs you about the duration and temperature of cooking.
- It also documents the most critical test for a baker or a manufacturer, which is quality control.
- The BMR is a record of how that bread turned out, including how much dough was wasted along the way.
Importance of Batch Manufacturing Records
Batch manufacturing records are essential for ensuring that products are produced safely and consistently. They provide a detailed and organized record of all the steps in the manufacturing process. This includes raw materials and packaging, as well as any intermediate processes such as blending, mixing, and packaging.
Batch records also provide a valuable audit trail to ensure that the product meets all regulatory requirements and standards. They enable manufacturers to track the production process and enable them to make necessary adjustments for future batches. Batch manufacturing records are also essential for getting FDA approval for new products.
Here’s how we can summarize the importance of batch records:
- Establishes a Product’s Quality Standards: Batch manufacturing records document the step-by-step processes used to manufacture a product. This information can then be used to set quality standards that must be met during production.
- Provides Traceability and Reproducibility: Batch manufacturing records provide an audit trail of each product that is produced. This allows the manufacturer to trace the product back to its original raw materials and reproduce the product if needed.
- Enhances Product Safety: When manufacturers have detailed batch records, they can quickly identify and recall products that may have been contaminated or have otherwise become unsafe for consumption.
- Ensures Regulatory Compliance: Regulatory agencies often use batch manufacturing records to ensure that quality standards and safety protocols are being followed.
- Improves Efficiency: By having detailed batch records, manufacturers can streamline their production process and reduce the amount of time it takes to produce a product.
- Facilitates Communication: Batch records often serve as a way for different departments, such as quality control and production, to communicate with each other. This ensures that everyone is on the same page and that the product being produced meets the required standards.
Types of Batch Manufacturing Records
There are various types of batch records. Let’s learn about each of them.
- Master Batch Records: These records provide the product's overall description and detailed manufacturing and testing instructions.
- Production Batch Records: These records provide detailed instructions for each step in the process and are used to record data such as temperature, pressure, and time for each step.
- Quality Control Batch Records: These records provide instructions for testing the product and recording the results of the tests.
- Packaging Batch Records: These records provide instructions for packaging the product and recording the results of the packaging process.
- Validation Batch Records: These records provide instructions for validating the product and recording the results of the validation process.
What is included in a Batch Manufacturing Record?
A batch manufacturing record typically includes a batch number, product name, date, operator name, ingredients, and quantities used. It may also include the manufacturing instructions, batch yield, in-process testing results, packaging details, storage conditions, and expiration date.
When properly structured, every BMR should comprise the following sections:
Bill of Materials
The bill of materials (BOM) should include all raw materials utilized in the batch, including ingredients and packaging components. This is done to confirm that each component complies with cGMP batch record criteria and is safe to use.
Crucial Dates
This section should provide the batch's start and finish dates and any additional milestone dates. These are necessary to track the batch's progress and ensure it is completed on schedule.
Manufacturing Process
This is a summary of the actions taken to complete the batch, beginning with mixing and blending ingredients and finishing with packaging and labeling. Any changes from the normal method should be documented in this section.
Hazards
Medical products may comprise potential hazards that must be introduced to the user. If there are any hazards, those must be notified in this space.
Quality Control
This section describes all of the tests that will be done on the product. It should include guidelines and recommendations for how the test should be carried out and what equipment is required. Once completed, the findings will be posted here, with any noteworthy anomalies indicated.
Equipment
All of the equipment utilized in the process should be listed. This guarantees that all machinery and tools are up to date and correctly calibrated to achieve the best results.
Maintenance Guidelines
Any maintenance chores performed during the batch process, as well as any unforeseen maintenance concerns, should be recorded here. Dates, persons, and other pertinent information should be mentioned.
Batch Details
This part should provide the batch's name, identification number, and amount. This helps to guarantee that each batch is traceable and that any issues are detected and remedied as soon as possible.
Compliance Record
This part should include any documents relating to batch records GMP compliance. Signatures of approval and materials from third-party testing should be added.
Requirements of Batch Manufacturing Records
So far, we have learned that batch manufacturing records are required because they provide evidence that a product has been manufactured according to the specified standards and in a consistent manner.
This is important for companies to ensure that their products are safe and meet quality standards. The records also help companies track production processes and identify any issues that may arise. Additionally, batch manufacturing records can be used as evidence in legal cases.
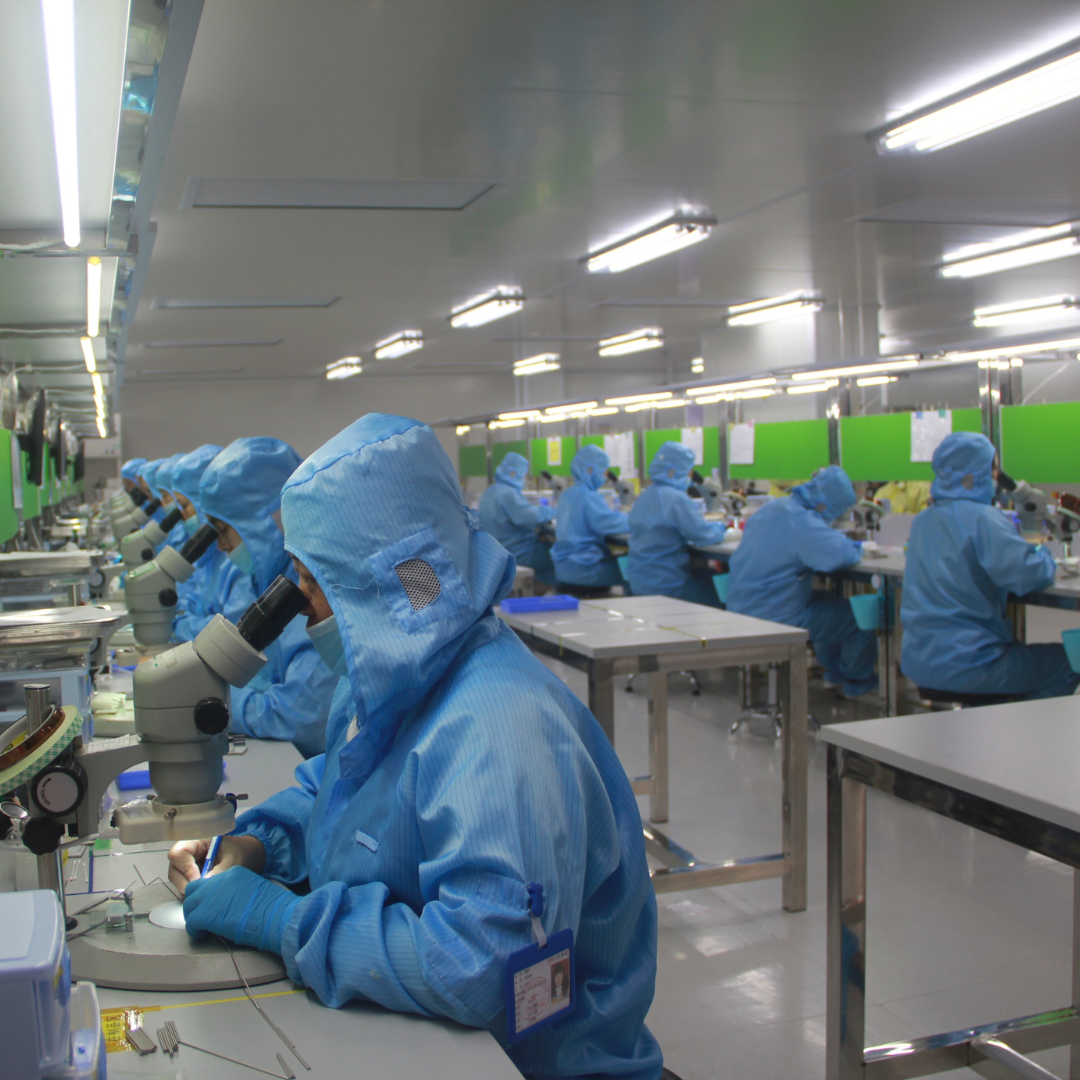
Yet, there are regulatory and audit requirements for batch manufacturing records. Depending on the industry and product, these requirements may vary. Generally, batch records must include information about the raw materials used, process steps followed, and tests performed to verify quality during the batch manufacturing process.
Additionally, these records must be kept up to date, securely stored, and readily available to regulatory authorities or auditors.
Regulatory Requirements
Regulatory requirements of batch manufacturing records dictate that all relevant information related to the production of a product must be documented and tracked in a batch record. These records must include the raw materials and ingredients used, the production process, the completed product, and all other quality control measures.
Also, a quality assurance representative must verify and sign all batch records to ensure accuracy and compliance with regulatory standards. Furthermore, all records must be stored and maintained in a secure location for a minimum of five years.
Auditing Requirements
Auditing batch manufacturing records is the process of reviewing and verifying the accuracy and completeness of the logs associated with the production of a single batch of a product. This includes reviewing records of raw materials and ingredients, equipment, batch production processes, finished product specifications, and test results.
Auditing is important to ensure compliance with applicable regulations and standards, product quality and safety, and the records accurately reflect the production process. Auditing requirements will vary by industry but generally include the following:
- Review of all raw materials and ingredients used in the production process, including associated test results and certificates of analysis.
- Review of all production processes, including process parameters, instrument readings, equipment settings, and operator documentation.
- Review of all finished product specifications, including test results.
- Review of all records associated with the release of the finished product, including certificates of analysis, release records, and sterility testing.
- Review of any changes to the batch production process, including any changes to the raw materials or ingredients used.
- Verify the accuracy and completeness of the batch records by comparing them to the production process.
Benefits of Using Software Solutions for Batch Manufacturing Records
BMRs are lengthy and complex documents. Completing them by hand or with manual methods such as spreadsheets takes time and is tiresome. Also, this method is prone to human error. It also exposes your organization to regulatory infractions, which can result in significant fines. Therefore, creating electronic batch records with BMR software greatly simplifies this procedure. It saves time, enhances accuracy, and assures compliance while shortening production cycles.
Choosing an ERP system that has batch production records capabilities ensures that all company data is kept up to date while optimizing operations. BMRs must also interface with the rest of your company's data so that inventory, sales, accounting, marketing, and other critical business processes are synced throughout the organization.
Here are a few advantages of utilizing batch manufacturing-specific ERP software.
Updates in Real Time
Changes to MFRs, BMRs, formulas, inventories, and other data are instantaneously reflected by integrated ERP systems with BMR software. Thus, ensuring that everyone in your organization always has the most up-to-date information.
Accurate Data for Decision-Making
You can make decisions based on accurate data. Also, you can view batch production schedules and track quality control tests to have complete visibility into the manufacturing process and make better decisions.
Streamlined Production
You can have a streamlined production procedure. Also, you can prepare and stage items ahead of time by establishing a bill of materials before completing the BMR, resulting in a more efficient production workflow. The software also includes workflows for streamlined batch manufacturing record routing, review, and approval.
Enhanced Efficiency
There will be no more handwriting entries, looking for documents, or double-entering data. By automating critical procedures like data entry, computations, conversions, document retrieval, and equipment readings, electronic BMR software substantially enhances efficiency.
Integration
With an ERP, you can achieve integration across the organization. Choosing an ERP system that includes BMR tools unifies and simplifies activities across departments while making data easily accessible to the entire organization.
Increased Precision and Decreased Waste
ERP can provide the reduced possibility of human error and automatic computations. Thus, it improves accuracy with unit-of-measure conversions, machine integrations, and inventory changes.
It effectively aids in better quality control which ensures that recipes are followed correctly and that any changes from the process are noted. Thus, resulting in higher product quality and less waste.
Improved Reporting
ERP software can drastically improve your reporting. Built-in reporting and analytics capabilities simplify batch reporting and ensure that your results are accurate.
Compliance with Regulations
BMR software automates important components of compliance, such as information collection, organization, and reporting to regulatory agencies. This allows your organization to avoid fines and penalties while also keeping employees and customers safe.
How to Select the Best BMR Software?
The majority of BMR software is intended for discrete manufacturing, in which goods like phones or automobiles are assembled from pieces following a relatively simple bill of materials.
These systems may lack the capability to manage the complicated recipes, formulas, and computations required by chemical and process manufacturing. It may also be difficult to compute and track the loss factors, byproducts, and co-products that come with it.
In the chemical and process manufacturing industries, the following characteristics are also necessary for preparing batch production records. You must ensure the following features in the ERP you plan to select for batch manufacturing records:
Instructions and Authentications in Detail
Instructions and authentications are provided step by step by an ERP integrated with the BMR system. BMR software creates a duplicate of the master formula record, auto-populating instructions to lead users through the manufacturing process without leaving the program interface.
The system also keeps track of sign-offs and permissions for steps that require two-factor authentication.
Quality Control
Producing a high-quality product is critical for satisfying customers, maintaining your brand, and meeting regulatory obligations. Users can utilize the quality control capabilities to manage quality testing data and track deviations from the MFR. They also identify and analyze the source of any variances.
Control Feature for Security and Auditing
Certain processes in the manufacturing process and modifying MFRs and BMRs may be restricted to select employees. A second person may be required to sign off on safety precautions, cleaning and sanitizing processes, calculations, and material identifications in some circumstances.
BMR software designed for the chemical and process manufacturing industries also has a full audit trail and tamper-proof records for FDA compliance. Thus, these systems handle automatic logging and timestamping changes and assign a user ID to each.
Inventory Control
ERP systems with specific batch manufacturing record functionality update material usage as the record is completed by interacting with inventory and warehouse management modules, enabling real-time inventory counts through instant quantities and yields.
Management of Industry-specific Compliance
ERP systems with BMR software have industry-specific compliance management features. These features automatically collect and organize the information and paperwork required to meet FDA standards.
Each step includes health and safety hazards as well as essential PPE, and automatic software updates keep compliance information updated.
BMRs on the Go
You may view batch manufacturing records from anywhere, eliminate hard copies, record formula changes instantaneously, and monitor inventory while on the go. All this is possible using the mobile device capabilities of the systems.
Integration of Equipment
Some specialized BMR systems are directly integrated with chemical and process manufacturing equipment. These include scales, thermometers, and pressure sensors.
This implies that weight, temperature, pressure, and other readings are calculated and entered into the MFR or BMR automatically rather than needing users to manually enter them. This saves time and effort while significantly improving accuracy.
Dynamic Fields
BMR software enables you to connect data from earlier steps to the current phase and use dynamic fields to make computations and comparisons across steps. Meanwhile, the scale-up and down capability automatically updates the MFR when you need to alter product yields.
Records for Master Packaging and Batch Packaging
BMR software for the chemical industry includes specialized functionality for creating master packaging records (MPR) and batch packaging records (BPR). These are the packaged batch equivalents of MFRs and BMRs.
Because packaging is an additional step after the raw material is manufactured, these documents are utilized after the MFR and BMR to outline packing instructions.
Pharmaceuticals, for example, require specialized instructions and records since they involve taking a large volume of the bulk of finished commodities and packing them into another shape, such as tablets, pills, or capsules.
Conversions of Units of Measurement
Batch manufacturing records software designed specifically for the chemical and process manufacturing industries will convert units of measure and packaging into the basic units required to measure your inventory. This ensures precise quantities, prices, sales, and analytics data, while also assisting you in managing recipes and formulas.
8 Best Practices for Batch Manufacturing Records
Using best practices for batch manufacturing records helps to ensure product quality and safety, and reduces the risk of contamination. It also allows manufacturers to track and trace the production process.
Furthermore, it helps manufacturers to accurately document their production processes and make improvements to the process in the future.
Best Practices for drafting batch manufacturing records can be summed up through the following points:
- Follow Good Documentation Practices: It is important to follow good documentation practices in the manufacturing process to ensure the accuracy and completeness of documentation. This includes maintaining accurate records, using standard formats, and ensuring that all documents are properly reviewed, signed, and filed.
- Define Process Steps: Batch manufacturing records should include a detailed description of each step in the manufacturing process, including the type of equipment used, raw materials used, and any other relevant information.
- Keep Records of Production Output: Records of production output should be kept to track the number of products produced and any quality issues that arise during the production process.
- Monitor Equipment Performance: Monitoring the performance of equipment used in the manufacturing process is essential to ensure the quality and consistency of products.
- Track Raw Material Supply: Tracking the supply of raw materials used in the manufacturing process is important to ensure that materials are available when needed and are used in the correct amounts and ratios.
- Use Standardized Formats: Using standardized formats for batch manufacturing records helps to ensure that all records are complete, accurate, and consistent.
- Monitor Production Costs: Monitoring production costs is important to ensure that the production process is as efficient and cost-effective as possible.
- Audit Manufacturing Processes: Auditing the manufacturing process regularly helps identify any issues or problems and allows for corrective action to be taken.
Conclusion
In conclusion, batch records are an essential part of the manufacturing process. They provide a record of all the steps of the manufacturing process, including what materials were used, the order of operations, and the results of the process. Without this information, it would be difficult to ensure quality control, maintain regulatory compliance, and ensure that the product is safe and effective.
Batch records are also an invaluable tool for tracking and analyzing production performance, which can help identify improvement areas and enhance the process's overall efficiency.
How can Deskera Help You?
Deskera ERP helps you to keep your business units organized. The system's primary functions are as follows:
- Keep track of your raw materials and final items inventories
- Control production schedules and routings
- Keep a bill of materials
- Produce thorough reports
- Make your own dashboards
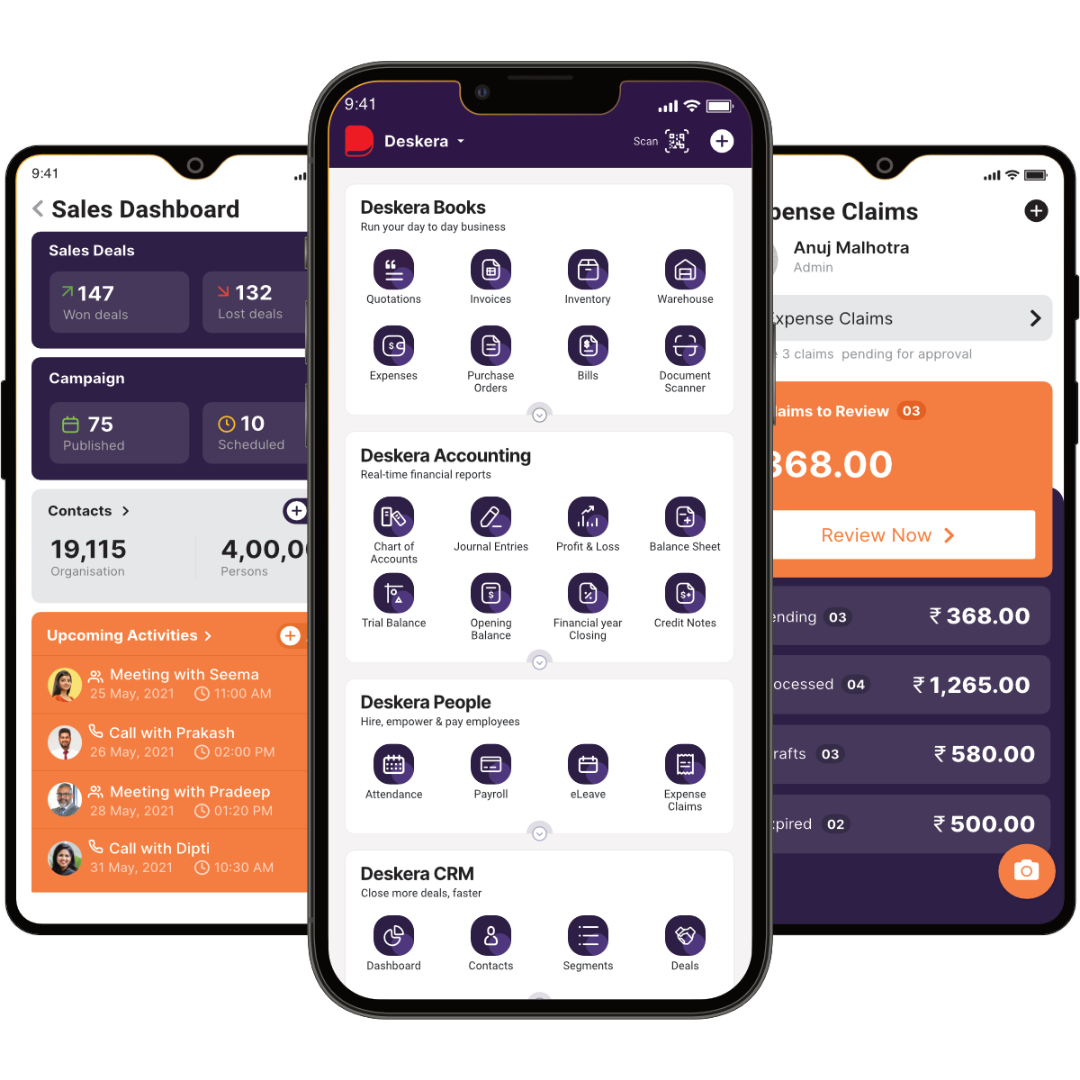
Deskera Books is accounting software for small businesses that helps them manage their finances and accounts. It is a cloud-based system that can be accessed at any time and from any location.
Employee onboarding, leave and shift management, time and attendance monitoring, payroll processing, benefits administration, and other features and capabilities are all available with Deskera People. The service assists businesses in more effectively managing their HR activities.
Deskera CRM is a full-service customer relationship management (CRM) solution that helps organizations of all sizes manage their customer interactions more effectively. The platform supports contact management, marketing automation, sales and customer service tracking, and connection with other company systems.
Key Takeaways
- Batch Manufacturing Records (BMR) are essential to any pharmaceutical or medical device manufacturing. These documents allow manufacturers to track and document the production process and ensure product quality.
- A batch in pharma manufacturing is a specific quantity of a drug product intended to have uniform character and quality within specified limits.
- Before the BMR can be created, chemical and process manufacturers must first establish another document: the master formula record (MFR).
- The MFR is a collection of instructions that teaches you how to make a product batch. It differs from a BMR as a BMR is a record of what you made.
- Batch manufacturing records are essential for ensuring that products are produced safely and consistently.
- They provide a detailed and organized record of all the steps in the manufacturing process. This includes raw materials and packaging, as well as any intermediate processes such as blending, mixing, and packaging.
- Master batch records, production batch records, and quality control batch records are some of the types of BMRs.
- A batch manufacturing record typically includes a batch number, product name, date, operator name, ingredients, and quantities used.
- It may also include the manufacturing instructions, batch yield, in-process testing results, packaging details, storage conditions, and expiration date.
- There are regulatory and audit requirements for batch manufacturing records. Depending on the industry and product, these requirements may vary.
- Generally, batch records must include information about the raw materials used, process steps followed, and tests performed to verify quality during the batch manufacturing process.
- Regulatory requirements of batch manufacturing records dictate that all relevant information related to the production of a product must be documented and tracked in a batch record.
- Auditing batch manufacturing records is the process of reviewing and verifying the accuracy and completeness of the logs associated with the production of a single batch of a product.
- Creating electronic batch records with BMR software greatly simplifies this procedure. It saves time, enhances accuracy, and assures compliance while shortening production cycles.
- Choosing an ERP system that has batch production records capabilities ensures that all company data is kept up to date while optimizing operations.
- BMRs must also interface with the rest of your company's data so that inventory, sales, accounting, marketing, and other critical business processes are synced throughout the organization.
- Using best practices for batch manufacturing records helps to ensure product quality and safety, and reduces the risk of contamination. It also allows manufacturers to track and trace the production process.
Related Articles
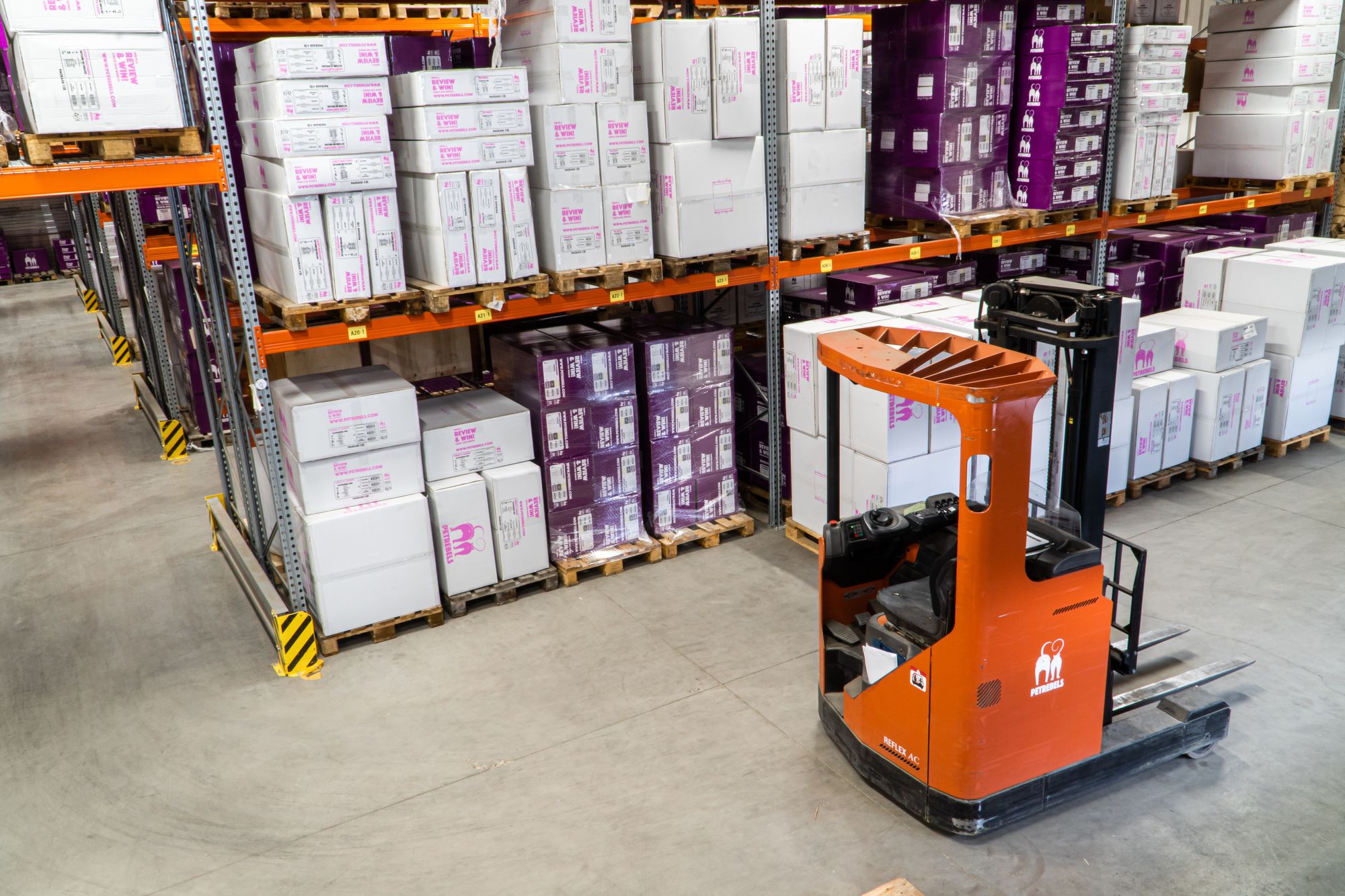
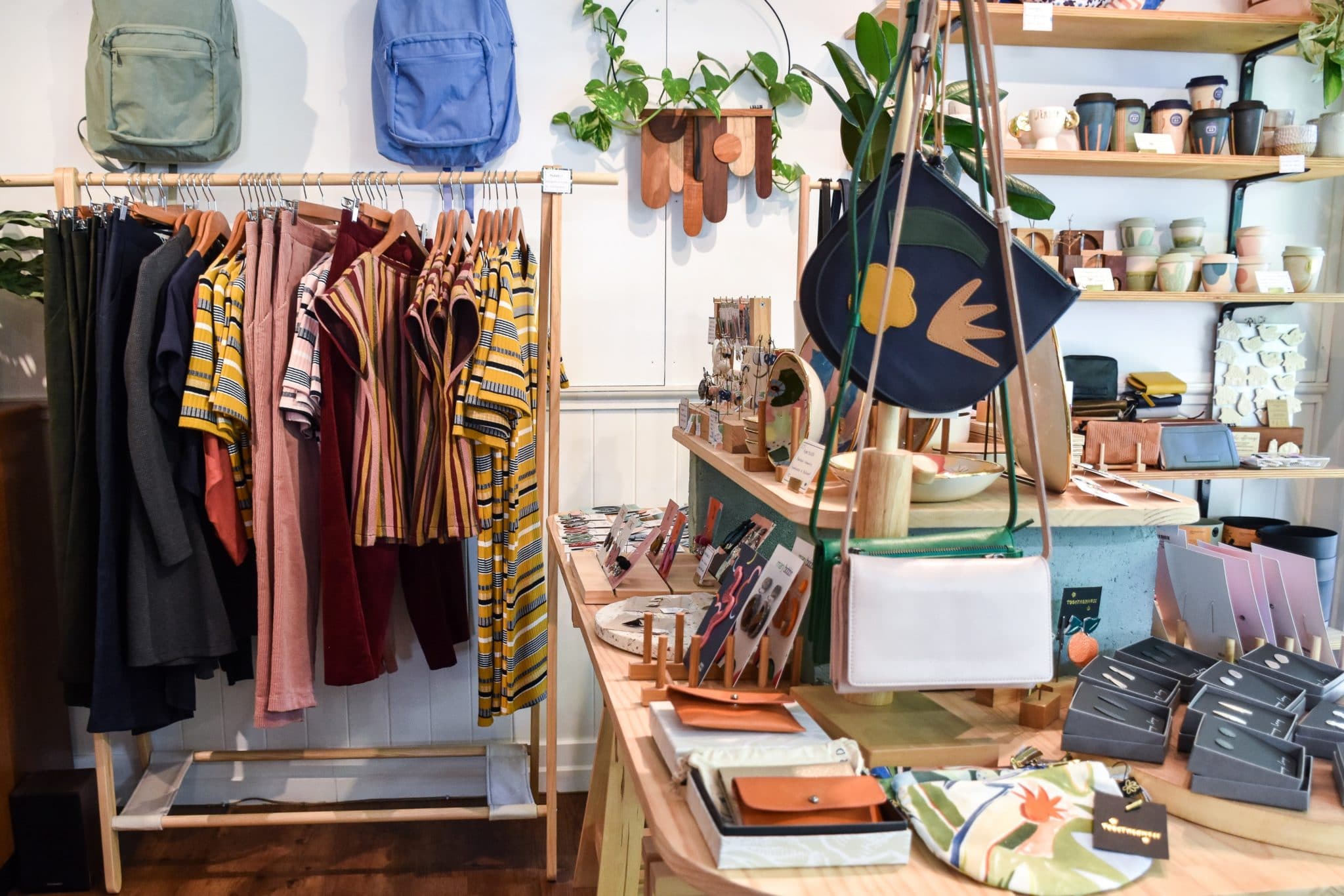
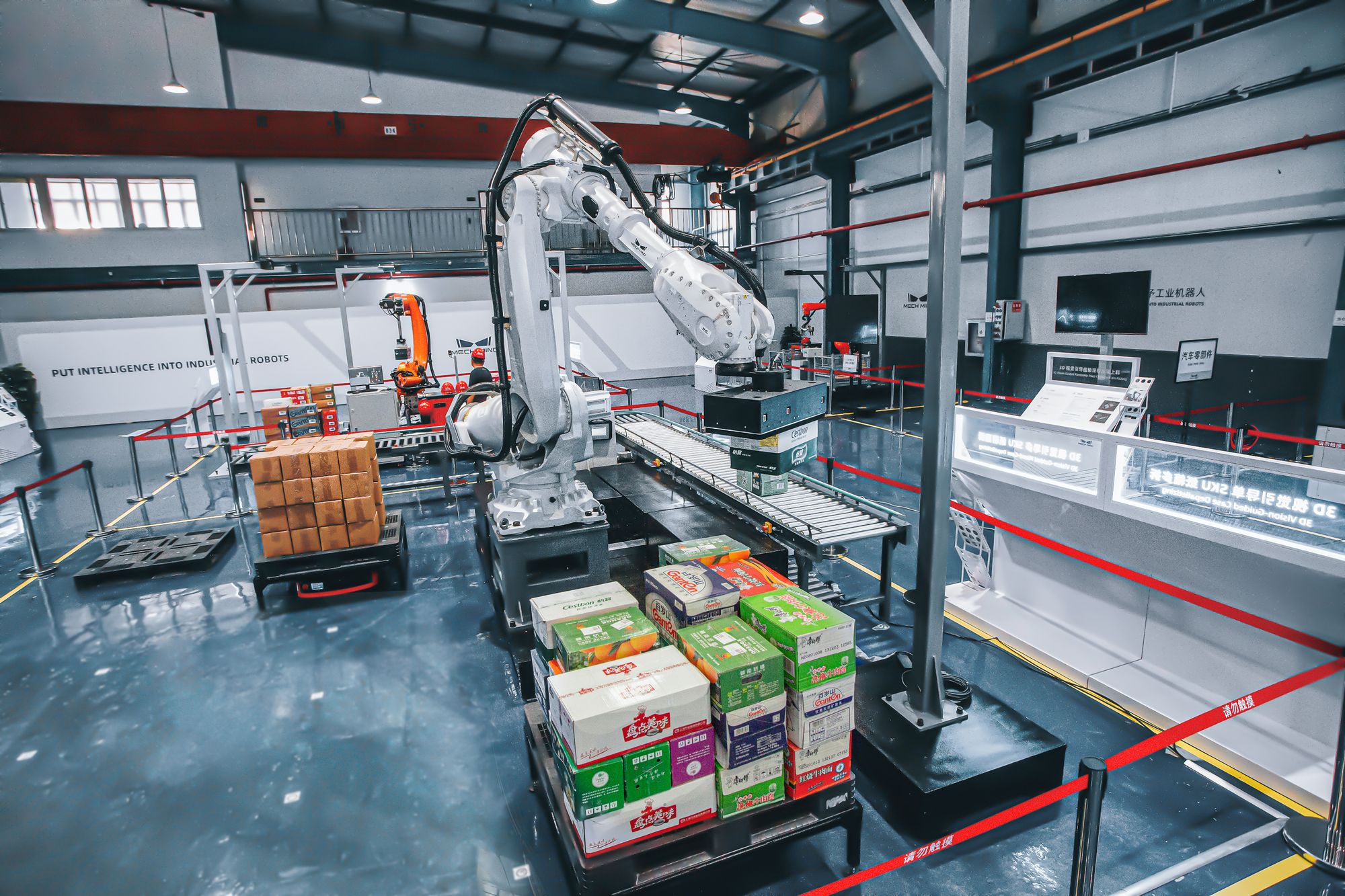
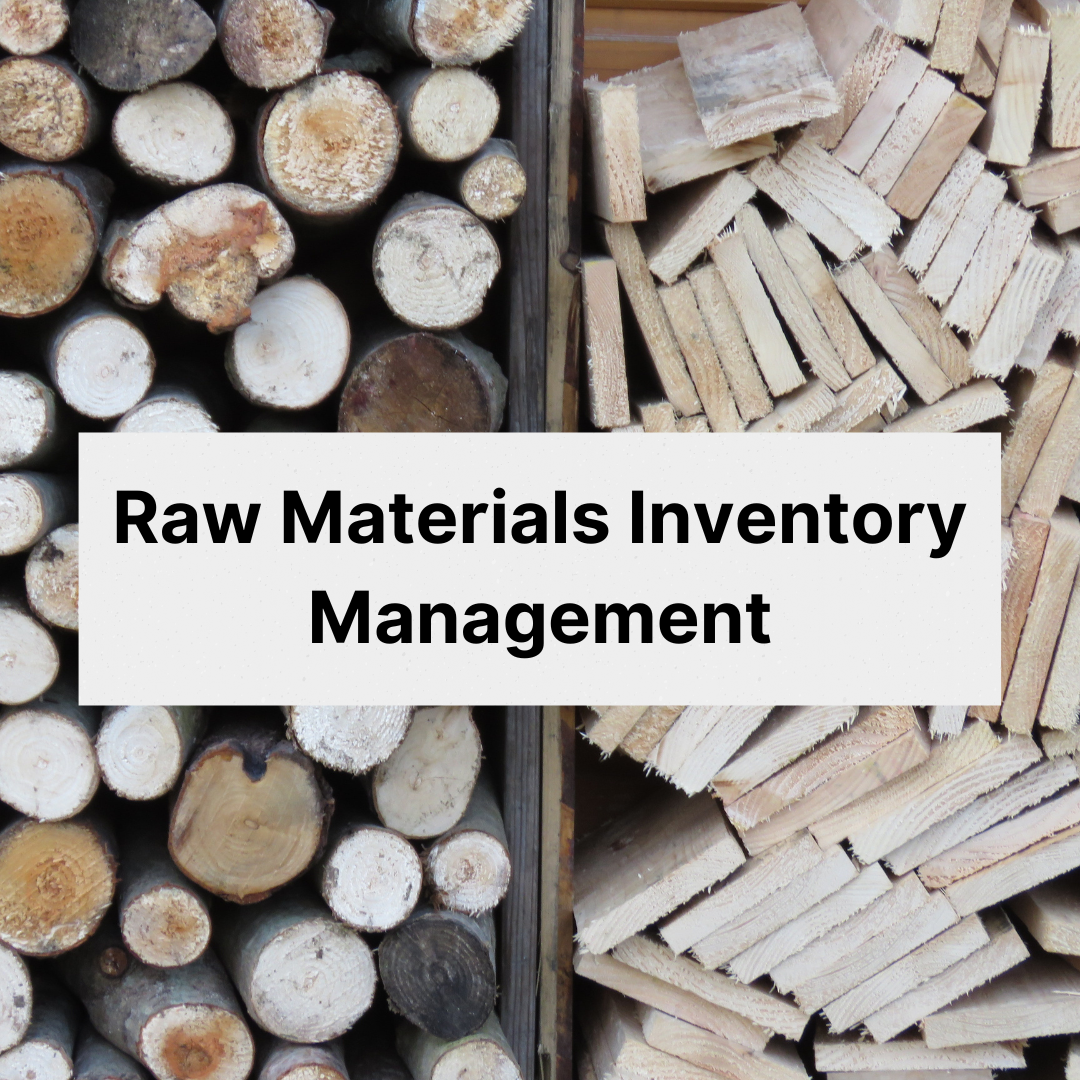