Are you tired of never being able to find the right warehouse for your products? Do you want to get a leg up on your competition? This is the perfect guide for you.
Warehouse slotting is a process that allows businesses to better handle their product inventory. By placing their products in specific slots in a warehouse, they can optimize their storage and reduce costs.
If you want to take advantage of this strategy, you need to understand how it works. In today’s guide, we’ll learn about warehouse slotting in detail and its related concepts. Let’s learn:
- Understanding Warehouse Slotting
- Warehouse Slotting Explained
- Significance of Warehouse Slotting
- Warehouse Slotting Objectives
- 3 Different Types of Warehouse Slotting
- Advantages of Warehouse Slotting
- Best Tactics and Strategies for Warehouse Slotting
- Optimization of Warehouse Slotting
- Identify Item Characteristics
- When You Should Reslot the Warehouse
- Use a 3PL for Outsourcing and Take Advantage of Warehouse Slotting
- How Deskera Can Assist You?
- Final Takeaways
Let's Start!
Understanding Warehouse Slotting
The process of structuring a warehouse for optimum order fulfilment effectiveness is known as warehouse slotting. At first glance, it seems easy. There are, nonetheless, a few crucial tactics for optimizing this procedure.
Furthermore, advanced planning and product placement that is suited for your business are required for warehouse slotting.
Finally, warehouse slotting can increase production and storage capacity, which will positively affect your business's bottom line.
Warehouse Slotting Explained
The warehouse is composed of items, pallets, and slots.
The items are the goods that warehouses ship. Slots, which are shelves or sections of shelves, are used to store these items.
Further, a forklift is designed to pick up a frame known as a pallet. Workers take items out of slots and pack them into pallets. They are subsequently loaded into trucks and driven away using a forklift.
Planners choose the best warehousing location for each item. A facilities manager might, for instance, place a product that sells more quickly in a location closer to the loading dock. It loads more rapidly as a result.
Warehouse slotting could be a daunting process since every item has a distinct set of features. Additionally, because dealing with conflicting priorities is a prerequisite of slotting items, complications occur. Along with speed, safety should be considered.
Moreover, to prevent top-heavy or imbalanced pallets, all of a company's best-selling products should be positioned closest to the loading dock. That could endanger employees and result in property damage.
Understanding warehouse slotting requires evaluating numerous important factors. A successful outcome offers many advantages, including improvements in efficiency, security, and client pleasure.
Significance of Warehouse Slotting
Slotting can actually impact how well-functioning your warehouse staff is. This is because it can minimize labor costs by reducing the time and effort required to choose things, which in turn can enhance productivity.
Furthermore, a well-defined and well-thought-out slotting system greatly simplifies the process of choosing items for shipment.
Moreover, pickers know where to find each item thanks to your strategy, so they don't have to waste time searching for them. It's comparable to having a map that enables each picker to locate each sorted item in the shortest amount of time possible.
A simple and thoughtful slotting method greatly streamlines the process of choosing items for shipping. Because of your strategy, pickers don't have to waste time hunting for every item because they already know where to look. It works much like a map that enables each picker to locate every item that has been organized rapidly.
Warehouse Slotting Objectives
Following we've discussed warehouse slotting objectives. Let's take a look:
- Place the swiftly moving goods close to the shipping dock and on the lowest levels of the pallet rack when putting non-consumables on pallets. Put heavier, slower-moving items higher up and farther away from the pier.
- Higher and heavier loads are usually stored closer to the pick area of the warehouse. A lower level or the ground floor is preferable for faster-moving freight.
- To keep activity on each horizontal carousel in the POD at an even pace. Place things that move more slowly on the intermediate shelves and distribute items that move more quickly throughout the carousels.
- To evenly spread the burden among the flow rack's parts. In a carton flow rack, it is feasible to add a slot for fast-moving shipments, with the quickest on the middle levels.
- Put items that move more swiftly closer to the take-away conveyor, and place slower-moving items on shelves. On the middle levels, look for the heavier items.
3 Different Types of Warehouse Slotting
Following we’ve discussed three different types of warehouse slotting. Let’s learn:
Random Slotting
Items are randomly slotted into the warehouse without being assigned to a specific pick-up location. They are offered a variety of options for where to go.
For instance, the same item will be picked up from a different location that will then be marked as a pick zone if a pick zone's inventory runs out. The objective is to reduce the time required for replenishment because incoming items will be stuck in put away mode right away.
Although an inventory reserve is required, replenishment times will be decreased because a large portion of pathways will go to direct placements.
Fixed Slotting
Fixed slot implies that items are sent to certain bin locations for packing reasons. Each designated pick-up time in the warehouse management system has a consistent minimum and maximum amount for the assigned item.
When production orders are made available for picking, if stock in the fixed location runs out before the minimum order quantity is reached, a replenishment job will be initiated to refill the stock from a different inventory pick site. Replacement inventories are handled carelessly and frequently kept near the pick slot.
Dynamic Slotting
Dynamic slotting is a new concept that has not yet been standardized. This typically indicates that the WMS has the ability to create brand-new or transient slots for commodities intended for well-known shipments.
Therefore, if the warehouse team anticipates having a high percentage of picks for a certain item, they may choose to create a new temporary slot right next to the picking/shipping location rather than sending the picker to the regular slot.
Advantages of Warehouse Slotting
Following we have discussed some crucial advantages of warehouse slotting. Let’s discuss:
Enhanced Item Handling and Management
Making sure that goods are not destroyed in transit or storage is essential in a warehouse setting. Correct item storage, such as storing perishable food in refrigerator-safe containers, is ensured by good inventory slotting. Thus, goods are delivered to clients in good shape.
Reduced Product Damage
Product damage can be decreased by allocating locations based on SKU attributes (e.g., avoiding carton live storage for fragile objects and putting heavy items in a sweet zone etc.). Heavy items must be placed on a pallet, in a tote, or in a carton first, however, they can be placed at the beginning of pick runs to prevent crushing other products.
Improved Safety
Facility managers can design a pick order that puts heavier products on the bottom of a pallet and lighter things on top using warehouse slotting. Thus, the risk of product damage during shipment is reduced and a safer pallet is produced, one that is not top-heavy or uneven.
Optimized Storage
It takes funds to store goods in a warehouse setting. Effectively slotted things take up less room, allowing you to store more goods in the same location.
Accelerated Order Fulfilment
Warehouse slotting improves the entire order fulfilment process, choosing items and shipping become simple. Finding things inside the warehouse is relatively straightforward with warehouse slotting, which improves picking and reduces pick-up errors.
If the warehouse offers packing services, the slotting technique helps to separate the packaging components and place them in their allocated pickup area after packaging.
Seamless Fulfillment
The usage of warehouse slots makes it simpler for staff to pick and pack things. For instance, by making sure workers choosing smaller things rarely have to wait while someone picks pallets with a forklift, you can lessen "traffic jams."
Increased Security
Using warehouse slotting, facility managers can create a pick order that places heavier goods on the bottom of a pallet and lighter goods on top. As a result, there is a lower chance of product damage during shipping, and a safer pallet is created because it is not top-heavy or uneven.
Boost Storage Capacity
Slotting significantly contributes to boosting storage capacity. Rethinking how inventory is currently held is a terrific approach to reclaim much-needed inventory space if you believe your warehouse to be full. By taking the effort to optimize your warehouse, you can postpone growing and incurring additional fees for a second warehouse.
Do not minimize the significance of warehouse slotting. Facility managers can enhance practically every element of their operations, going beyond their department and into the company as a whole, by carrying out an efficient slotting procedure. But developing a slotting procedure requires picking new words and making difficult decisions.
Best Tactics and Strategies for Warehouse Slotting
Numerous methods can be used to slot products in a warehouse. In order to choose the best strategy for your eCommerce business, you need data—lots and lots of data—on product sizes and weights, sales velocity, typical order contents and volume, seasonality, available warehouse capacity, and much more.
It is ideal if your fulfilment center or third-party logistics supplier already has a solid warehouse management system (WMS) and a reliable inventory management system.
Analyzing the data and choosing the best method may require some trial and error. You might even utilize a variety of tactics at different times of the year, in different parts of the warehouse, and in different fulfilment centers.
Slotting Tactic No. 1: Slotting based on Sales Volume
The fastest-moving products are placed next to one another using this method, which is the most widely utilized slotting strategy.
In order to prevent workers from stumbling over one another in the same area, orders can be picked up in waves.
Slotting Tactic #2: Slotting by Storage Type and Item Level
There are some goods that are sold singly, by the case, and by the pallet. Within the same warehouse, other goods are distributed in all three ways.
Slotting products according to their storage and sale methods guarantees that single-item pickers may work without avoiding forklifts and that forklifts are contained to one region of the warehouse to enhance productivity.
Slotting Tactic #3: Choosing Products Frequently Paired
Cat food and cat litter are two products that are usually purchased in combination. Pickers don't need to travel far to satisfy orders if these things are stacked close to one another.
Slotting Tactic #4: Seasonality
It might make sense to temporarily transfer things into a high-volume category if the sales volume of those particular items fluctuates noticeably with the seasons, like swimwear or holiday gifts.
Optimization of Warehouse Slotting
You'll need a slotting plan if you're thinking about implementing warehouse slotting. This entails establishing a system to adhere to where goods are arranged according to particular categories. The key is to plan ahead. The best strategy to categorize products for your selection requirements should be carefully considered.
Consider the supplies you currently have. What goods are usually purchased in unison? Exist more well-liked things? Which items can be moved around, and which cannot? It is initially necessary to consider things like these in order to create an effective slotting strategy.
Following we have discussed few things to consider when optimizing slotting based on the needs of your company.
Sort Slots by Priority for Simple Access
Prior to assigning items to slots in your warehouse, it is helpful to know which products belong there. Prioritizing slots is one way to make things easier for your warehouse staff.
Inventory should be organized by SKU velocity or item size, and the slots in the front pick zone should be matched with the products with higher SKU velocity. Large or fast-moving objects will travel a shorter distance to the loading port as a result of this.
When your SKUs and storage strategy are in sync, selecting efficiency can be greatly increased.
Verify the Facility's Flow
Growth typically calls for constant changes to your work process. As you get more orders, your strategy will need to be more effective. As a result, it's critical to constantly evaluate the flow of your facilities.
The procedure should follow a logical flow, starting with receiving and ending with shipping after stocking and picking. It's crucial to keep your facility's flow as you grow if you want to keep your procedure straightforward and efficient. This will allow your team to function effectively throughout each shift.
Plan out a Picking Order
Following a picking sequence will let you pick items in the most efficient manner. It makes speedy, accurate, and orderly selecting of items for pallet assembly and transportation possible.
The warehouse slotting strategy and the picking sequence are closely related. When slots are organized in tandem with the picking sequence and vice versa, workers can easily complete their picking routes.
Finding the ideal picking order and slotting approach requires striking a balance. When deciding which things to place where and in what sequence to choose them, you can have conflicting priorities.
For instance, it could be a good idea to stash larger, heavier products close to the loading dock and choose those first. This is due to the shorter transportation distance and the fact that the "heavier goods first" mentality results in more durable pallets.
But bigger, heavier things might not be your quickest sellers, and you might also want to put your fastest-moving products in a prime position so that many of your purchases are quick and simple to choose.
You should think about speed, productivity, and proper shipping procedures. Furthermore, achieving the ideal balance between your slotting and sequencing will enable optimal warehouse management.
Identify Item Characteristics
You must be aware of each item's key characteristics in order to position it appropriately. Understanding the following characteristics is essential when putting your slotting strategy into action.
Unit dimension:
It will be required to know an item's width, length, and depth in order to place it in the appropriate slot.
Item Data:
By taking into account how frequently an item is purchased in comparison to other items, you may determine its position. Popular things usually do well in prominent places. Otherwise, inactive items can be pushed further back or may be better off in ASRS.
Unit Weight/Slotting Unit Weight:
For quality control purposes, weight should be calculated for each item and slotting unit to ensure that any stacking that takes place in the warehouse does not compromise the quality of the products below.
Pallet Building:
Make sure to determine how many of each item will fit on a pallet and how they will stack in order to make the process of making pallets for storage or transport easier.
Ergonomic Picking:
Recognize which products require picking equipment to improve the ergonomics of the picking process (such as a forklift or cart).
Pick Path Number:
A pick path number must be assigned to each item in order to ensure that it is correctly incorporated into the selecting flow.
Lines/Frequency:
Learn how many times the item has been viewed during a particular period of demand.
X, Y, Z Coordinates:
On a birds-eye view map of the warehouse or storage area, locate the x, y, and z coordinates that will assist you locate an item.
When You Should Reslot the Warehouse
As your business grows and you start selling more products, think about re-slotting to include any new inventory in the fulfilment process.
Determining whether using the full warehouse to move items is really worth it can be difficult. Some businesses desire efficiency but are unsure if the process will be beneficial in the long run.
If you don't position each product correctly, you face the risk of losing your optimized flow when products change over time—possibly because one didn't perform as well as predicted, you needed to scale up, or a new one was just introduced for a new season.
When doing maintenance moves, don't reslot.
Re-slotting is occasionally necessary, although it can be very time-consuming and uncomfortable. If you are currently unable to do so, a maintenance move is an alternative to re-slotting.
Use a 3PL for Outsourcing and Take Advantage of Warehouse Slotting
The amount of work required is obvious whether you've attempted slotting or are thinking about slotting your warehouse. It will take a lot of planning and preparation before we can finish it all. Many growing businesses just don't have the time or resources to stop running their current business in order to invest in warehouse slotting.
The good news is that you may permanently wave goodbye to slotting issues by outsourcing inventory management and warehousing. Allowing a third-party organization to handle all warehouse-related operations, such as handling, shipping, and slotting, allows you to concentrate on growing your business.
Lowers Expenses
A third-party logistics service can assist you in managing your outgoing shipments, product returns, and incoming orders (3PL). Additionally, costs related to labor, handling, and storage space can be reduced.
Picking and processing orders can be one of the most expensive parts of fulfilling orders since warehouse systems are so complex. You can be sure it will be finished successfully and affordably if a qualified 3PL handles it for you, though.
Saves Time
By outsourcing your warehouse, you can cut down on the time spent picking, packing, and shipping. These responsibilities are all finished for you, allowing you to focus more time and energy on other areas of your business that foster growth.
How Deskera Can Assist You?
Deskera MRP allows you to closely monitor the manufacturing process. From the bill of materials to the production planning features, the solution helps you stay on top of your game and keep your company's competitive edge.
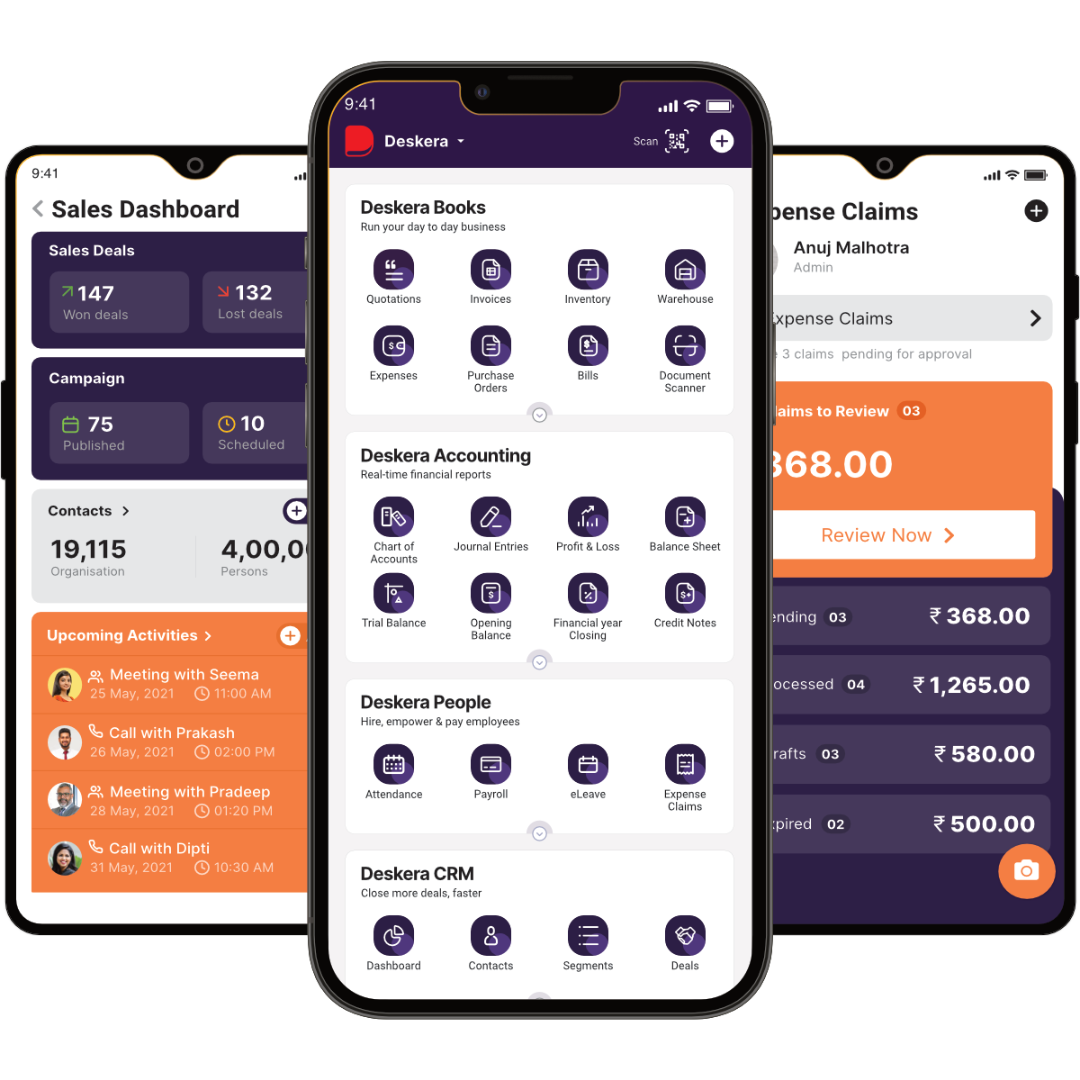
Deskera ERP and MRP system can help you:
- Manage production plans
- Maintain Bill of Materials
- Generate detailed reports
- Create a custom dashboard
Deskera ERP is a comprehensive system that allows you to maintain inventory, manage suppliers, and track supply chain activity in real-time, as well as streamline a variety of other corporate operations.
Deskera Books enables you to manage your accounts and finances more effectively. Maintain sound accounting practices by automating accounting operations such as billing, invoicing, and payment processing.
Deskera CRM is a strong solution that manages your sales and assists you in closing agreements quickly. It not only allows you to do critical duties such as lead generation via email, but it also provides you with a comprehensive view of your sales funnel.
Deskera People is a simple tool for taking control of your human resource management functions. The technology not only speeds up payroll processing but also allows you to manage all other activities such as overtime, benefits, bonuses, training programs, and much more. This is your chance to grow your business, increase earnings, and improve the efficiency of the entire production process.
Final Takeaways
We've arrived at the last section of this guide. Let's have a look at some of the most important points to remember:
- The process of structuring a warehouse for optimum order fulfilment effectiveness is known as warehouse slotting.
- Warehouse slotting could be a daunting process since every item has a distinct set of features. Additionally, because dealing with conflicting priorities is a prerequisite of slotting items, complications occur. Along with speed, safety should be considered.
- Slotting can actually impact how well-functioning your warehouse staff is. This is because it can minimize labor costs by reducing the time and effort required to choose things, which in turn can enhance productivity.
- Warehouse slotting improves the entire order fulfilment process, choosing items and shipping become simple. Finding things inside the warehouse is relatively straightforward with warehouse slotting, which improves picking and reduces pick-up errors.
- Slotting products according to their storage and sale methods guarantees that single-item pickers may work without avoiding forklifts and that forklifts are contained to one region of the warehouse to enhance productivity.
- Inventory should be organised by SKU velocity or item size, and the slots in the front pick zone should be matched with the products with higher SKU velocity. Large or fast moving objects will travel a shorter distance to the loading port as a result of this.
- A third-party logistics service can assist you in managing your outgoing shipments, product returns, and incoming orders (3PL). Additionally, costs related to labor, handling, and storage space can be reduced.
- Picking and processing orders can be one of the most expensive parts of fulfilling orders since warehouse systems are so complex.
Related Articles
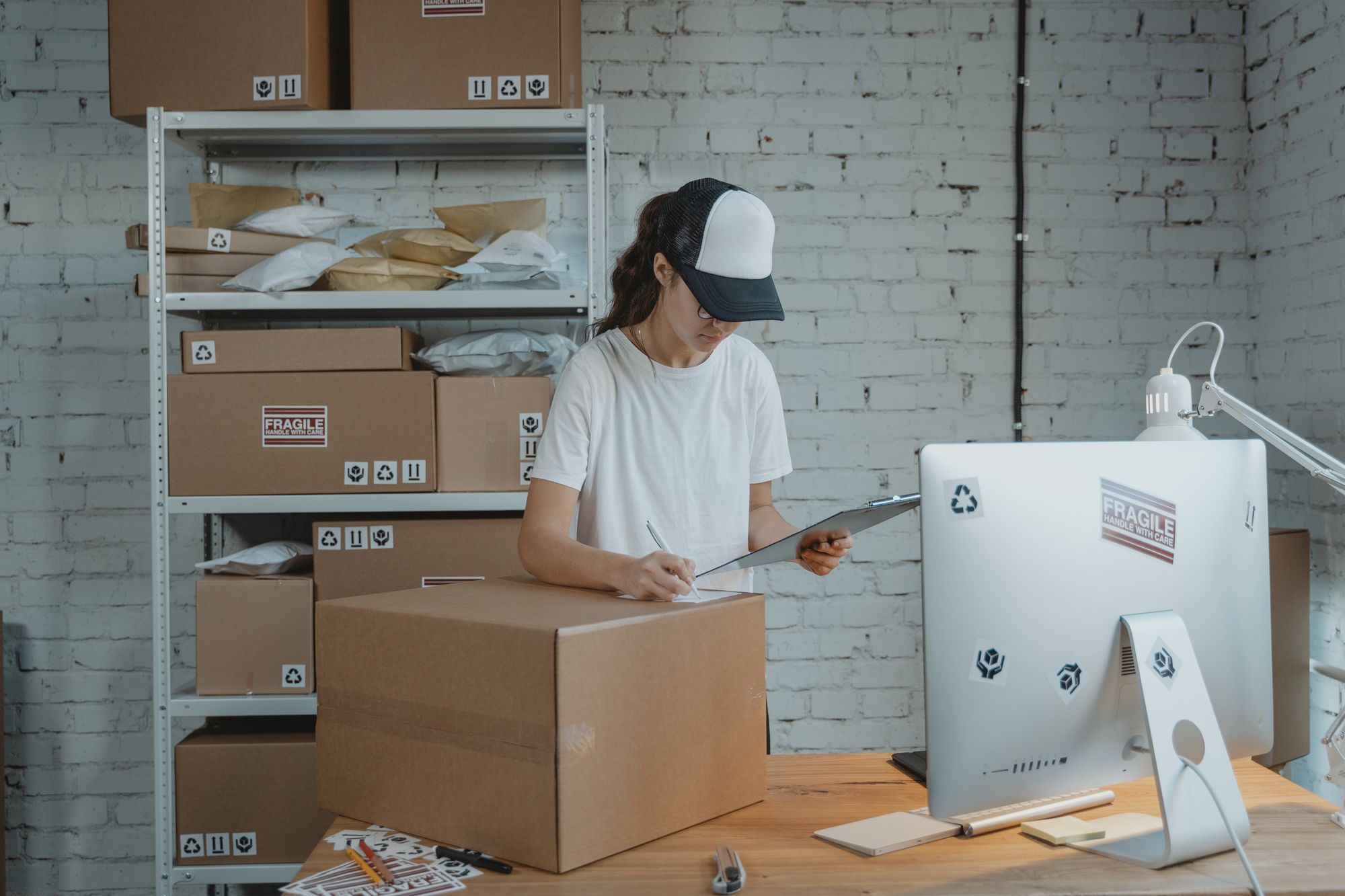
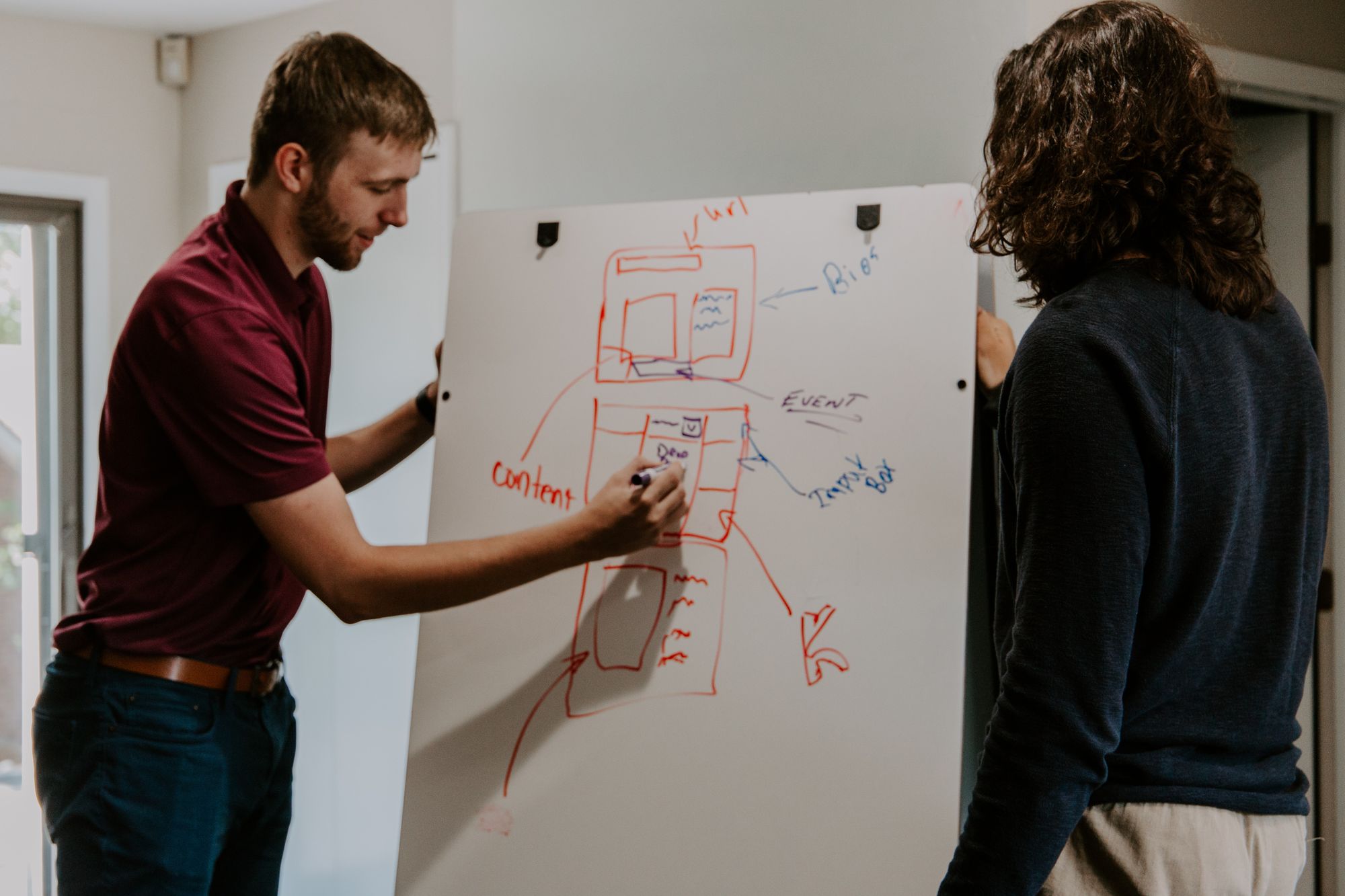