In 2021, the U.S. Consumer Product Safety Commission (CPSC) issued a recall for over 165,000 dressers due to tip-over hazards. The recalled dressers did not comply with the industry standard for stability and posed a risk of injury or death to consumers. (Source: CPSC)
According to a study by the Furniture Industry Research Association, 89% of furniture manufacturers in the UK believe that compliance with regulations is essential for their business success. (Source: Furniture Industry Research Association)
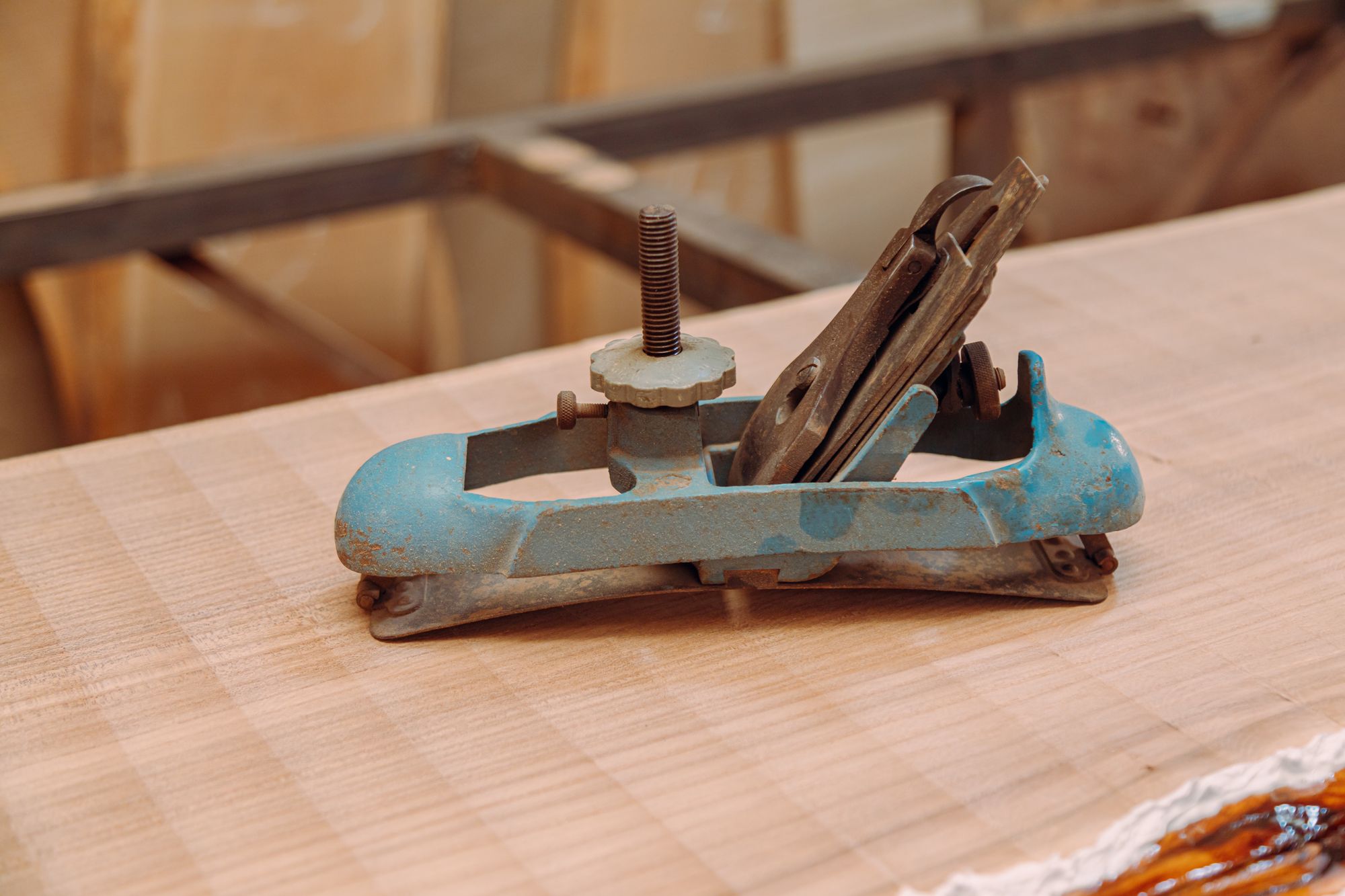
In 2020, the California Air Resources Board (CARB) issued over $2 million in fines for companies that violated formaldehyde emission standards for composite wood products, including furniture. (Source: CARB)
The Occupational Safety and Health Administration (OSHA) issued 129 citations to furniture manufacturers in 2020 for violations related to machine guarding, hazardous energy control, and respiratory protection. (Source: OSHA)
A survey of consumers in the United States found that 62% were concerned about the safety of the furniture they buy, with 87% indicating that they would pay more for furniture that meets safety standards. (Source: Consumer Reports)
These statistics demonstrate the importance of complying with regulations in the furniture manufacturing industry, both for consumer safety and business success.
This article will help you in understanding the latest regulations for furniture manufacturing by covering the following topics:
- Introduction related to the Latest Regulations for Furniture Manufacturing
- Importance of Regulations in Furniture Manufacturing
- Why is it Important to Stay Up-to-Date with the Latest Regulations in Furniture Manufacturing?
- The Latest Regulations for Furniture Manufacturing
- Comparison of the Latest Regulations for Furniture Manufacturing with the Previous Regulations
- The Role of Regulations in Addressing Environmental Concerns of the Furniture Manufacturing Industry
- The Role of Regulations in Addressing Safety Concerns of the Furniture Manufacturing Industry
- The Role of Regulations in Addressing Transparency Concerns of the Furniture Manufacturing Industry
- The Role of Regulations in Addressing Changes in Manufacturing Practices of the Furniture Manufacturing Industry
- The Role of Regulations in Addressing Economic Concerns of the Furniture Manufacturing Industry
- Key Changes and Impacts Due to the Regulations of Furniture Manufacturing
- Challenges Faced by Furniture Manufacturing Companies in Complying with the Latest Regulations
- Opportunities Available for Furniture Manufacturing Companies in Complying with the Latest Regulations
- Consequence of Non-Compliance with Regulations of Furniture Manufacturing
- How can the Implementation of MRP Software Help in Complying with Regulations of Furniture Manufacturing?
- How can Deskera Help You with Furniture Manufacturing?
- Key Takeaways
- Related Articles
Introduction related to the Latest Regulations for Furniture Manufacturing
In recent years, the furniture manufacturing industry has become subject to increasingly strict regulations aimed at ensuring the safety and quality of furniture products. These regulations cover a wide range of issues, from product safety standards to environmental regulations, and they are enforced by government agencies and other organizations around the world.
The furniture industry is particularly vulnerable to safety risks, such as tip-over hazards, flammable materials, and toxic chemicals used in production. As a result, regulatory bodies have introduced new standards and guidelines to ensure that furniture products meet certain safety requirements.
Manufacturers in the furniture industry must keep up with the latest regulations and standards to ensure compliance and avoid costly fines, penalties, and legal action. In addition, they must implement effective quality control measures to ensure that their products meet these standards and protect the safety of consumers.
In this context, it is important for furniture manufacturers to stay informed about the latest regulations and best practices related to their industry. This can help them avoid potential legal and financial consequences, protect their reputation, and build trust with consumers.
Importance of Regulations in Furniture Manufacturing
Regulations play a crucial role in the furniture manufacturing industry. There are several reasons why regulations are essential, including:
- Health and Safety: Regulations ensure that furniture is manufactured in a way that doesn't pose any risks to human health and safety. For example, regulations may require furniture to be made using non-toxic materials that don't emit harmful chemicals into the air.
- Environmental Protection: Regulations help protect the environment by ensuring that furniture is manufactured in an eco-friendly manner. This can include requirements for sustainable materials, energy-efficient manufacturing processes, and proper waste disposal.
- Consumer Protection: Regulations can help protect consumers by ensuring that furniture meets certain standards of quality and safety. This can include requirements for durability, stability, and flame resistance.
- Fair Competition: Regulations can help ensure fair competition in the furniture manufacturing industry. This can include requirements for labeling, advertising, and marketing practices to prevent false or misleading claims.
- International Trade: Regulations can facilitate international trade by establishing standards that are recognized and accepted globally. This can help prevent trade barriers and promote fair competition among manufacturers from different countries.
In summary, regulations are essential in furniture manufacturing as they help ensure health and safety, protect the environment, provide consumer protection, promote fair competition, and facilitate international trade.
Why is it Important to Stay Up-to-Date with the Latest Regulations in Furniture Manufacturing?
Staying up-to-date with the latest regulations in furniture manufacturing is crucial for several reasons, including:
- Compliance: Regulations change over time, and it's important to stay up-to-date to ensure compliance with the latest standards. Failure to comply with regulations can result in legal penalties, fines, or even the closure of a business.
- Safety: Regulations are put in place to ensure the safety of consumers and workers. Staying up-to-date with the latest regulations helps manufacturers ensure that their products are safe to use and meet all relevant safety standards.
- Quality: Regulations often set minimum quality standards for furniture. Staying up-to-date with the latest regulations can help manufacturers ensure that their products meet these standards and are of high quality.
- Innovation: Regulations can also drive continuous innovation in the furniture manufacturing industry. By staying up-to-date with the latest regulations, manufacturers can identify new materials or manufacturing processes that can help them produce better, safer, and more environmentally-friendly products.
- Reputation: Adhering to the latest regulations can also help manufacturers build a positive reputation with customers and other stakeholders. Consumers are increasingly concerned about environmental and social issues, and manufacturers that show a commitment to compliance with regulations can differentiate themselves in the marketplace.
- Legal Compliance: Non-compliance with regulations can lead to legal consequences, such as fines, penalties, and legal action. Compliance with regulations helps to avoid these consequences and ensure that a company is operating within the law.
- Competitive Advantage: Compliance with regulations can also provide a competitive advantage. Consumers are increasingly concerned about safety and environmental issues, and companies that prioritize compliance with regulations can differentiate themselves from competitors and build brand trust.
- Ethical Responsibility: Companies have an ethical responsibility to operate in a way that is safe and sustainable. Compliance with regulations is one way to fulfill this responsibility and demonstrate a commitment to ethical business practices.
In conclusion, staying up-to-date with the latest regulations in furniture manufacturing is essential to ensure compliance, safety, quality, innovation, and reputation.
Manufacturers who keep abreast of changes in regulations can adapt their products and processes to stay ahead of the curve and meet the evolving needs of consumers and society. This will lead to higher sales velocity and net profit ratio.
The Latest Regulations for Furniture Manufacturing
Some of the recent and upcoming regulations that may impact furniture manufacturing are:
- Formaldehyde Emission Standards: The US Environmental Protection Agency (EPA) has set limits on formaldehyde emissions from composite wood products, including furniture. These regulations went into effect in 2018 and are designed to protect consumers from the harmful effects of formaldehyde exposure.
- Chemicals of Concern: Several states and countries, including California and the European Union, have implemented regulations to restrict the use of certain chemicals in furniture manufacturing, such as flame retardants and phthalates. Manufacturers need to be aware of these regulations to ensure their products meet the required standards.
- Occupational Safety and Health Administration (OSHA) regulations: These regulations cover workplace safety standards, including the use of machinery, handling of materials, and hazardous materials exposure. Furniture manufacturers must comply with OSHA standards to protect the safety and health of their employees.
- Environmental Protection Agency (EPA) regulations: These regulations govern the disposal of hazardous waste, such as paint and chemicals used in furniture manufacturing. Furniture manufacturers must dispose of these materials in compliance with EPA regulations to protect the environment and public health.
- California's Proposition 65: In 2018, new regulations were introduced under California's Proposition 65 that require furniture manufacturers to provide warnings about potential exposure to certain chemicals that are known to cause cancer or reproductive harm. This includes formaldehyde, which is commonly used in the production of composite wood products.
- EU Timber Regulation: The European Union's Timber Regulation came into effect in 2013 and aims to prevent the trade of illegally harvested timber. It requires companies to carry out due diligence on their supply chains to ensure that the wood they use has been legally harvested.
- Restriction of Hazardous Substances (RoHS) Directive: The RoHS Directive is a European Union directive that restricts the use of certain hazardous substances in electrical and electronic equipment, including furniture with electrical components.
- Consumer Product Safety Improvement Act (CPSIA): The CPSIA is a United States federal law that sets safety standards for consumer products, including furniture. It includes requirements for labeling, testing, and certification.
- Chemicals Management Regulation (REACH): The European Union's REACH Regulation is a comprehensive chemicals management system that requires manufacturers to register, evaluate, and authorize the use of chemicals used in the production of furniture and other products.
- Sustainability Standards: With increasing concerns over climate change and environmental degradation, sustainability has become a key focus in the furniture manufacturing industry. Several organizations, such as the Forest Stewardship Council (FSC) and the Sustainable Furnishings Council (SFC), have developed sustainability standards for furniture. Manufacturers may need to comply with these standards to market their products as environmentally friendly.
- Consumer Product Safety: The US Consumer Product Safety Commission (CPSC) has established regulations for the safety of furniture products, including requirements for stability, tip-over resistance, and labeling. Manufacturers need to ensure that their products meet these standards to ensure consumer safety.
- Trade Regulations: Furniture manufacturers may also need to comply with trade regulations, such as those established by the World Trade Organization (WTO) and regional trade agreements. These regulations may impact issues such as tariffs, labeling, and import/export procedures.
- Flame Retardant Regulations: Several states in the US, as well as the European Union, have introduced regulations that restrict the use of flame retardants in furniture manufacturing. These regulations aim to reduce exposure to harmful chemicals while maintaining fire safety.
In conclusion, furniture manufacturers need to stay up-to-date with the latest regulations in order to ensure compliance and protect the health and safety of consumers, as well as meet sustainability and trade standards.
Comparison of the Latest Regulations for Furniture Manufacturing with the Previous Regulations
The latest regulations for furniture manufacturing have evolved significantly over the past few decades. Here are some of the key differences between the latest regulations and previous regulations:
- Environmental Regulations: Environmental regulations have become much more stringent in recent years. For example, the European Union's REACH regulation, which came into effect in 2007, requires companies to register and evaluate the risks of chemicals used in their products. Similarly, the US Environmental Protection Agency (EPA) has implemented regulations such as the Toxic Substances Control Act (TSCA) and the Resource Conservation and Recovery Act (RCRA), which regulate the use and disposal of hazardous materials.
- Labor Regulations: Labor regulations have also become more stringent in recent years. For example, the International Labor Organization (ILO) has established conventions and recommendations related to working conditions, child labor, and forced labor. Additionally, many countries have implemented regulations related to minimum wages, working hours, and workplace safety.
- Product Safety Regulations: Product safety regulations have also become more comprehensive and detailed. For example, the Consumer Product Safety Improvement Act (CPSIA) in the United States requires testing and certification of children's products, and the European Union's General Product Safety Directive (GPSD) requires manufacturers to ensure that their products are safe and meet specific requirements.
- Material Restrictions: Regulations related to the use of specific materials have also become more stringent. For example, many countries have implemented regulations related to the use of flame retardants, which are often used in furniture foam. Similarly, regulations related to the use of formaldehyde and other volatile organic compounds (VOCs) have become more comprehensive and detailed.
In conclusion, the latest regulations for furniture manufacturing are much more comprehensive, detailed, and stringent than previous regulations. These regulations reflect an increased focus on environmental responsibility, labor practices, product safety, and material restrictions.
While compliance with these regulations can present challenges for furniture manufacturers, it also presents opportunities for companies to differentiate themselves and build a more sustainable and socially responsible business.
The Role of Regulations in Addressing Environmental Concerns of the Furniture Manufacturing Industry
Regulations play a crucial role in addressing environmental concerns in the furniture manufacturing industry. Here are some of the ways that regulations can help address these concerns:
- Reduction of Emissions: Regulations can help reduce emissions from furniture manufacturing processes by setting limits on the amount of pollutants that can be released into the environment. For example, regulations such as the Clean Air Act in the United States set standards for emissions from industrial sources, including furniture manufacturing facilities.
- Waste Reduction: Regulations can help reduce waste from furniture manufacturing processes by setting standards for waste reduction, recycling, and disposal. For example, regulations such as the European Union's Waste Framework Directive require companies to reduce their waste generation and increase their recycling and reuse of materials.
- Material Restrictions: Regulations can restrict the use of materials that are harmful to the environment. For example, regulations such as the European Union's REACH regulation restrict the use of certain chemicals in furniture manufacturing processes, and the California Air Resources Board's formaldehyde regulations limit the amount of formaldehyde that can be used in furniture products.
- Sustainability: Regulations can promote sustainable practices in the furniture manufacturing industry. For example, regulations such as the Forest Stewardship Council's certification program promote the use of sustainably harvested wood in furniture products, while the Cradle to Cradle certification program promotes the use of environmentally safe and healthy materials.
In conclusion, regulations play a critical role in addressing environmental concerns in the furniture manufacturing industry.
By setting standards for emissions, waste reduction, material restrictions, and sustainability, regulations can help promote environmentally responsible practices and mitigate the negative impact of furniture manufacturing on the environment.
Compliance with these regulations can present challenges for furniture manufacturers, but it also presents opportunities for companies to differentiate themselves and build a more sustainable and socially responsible business.
The Role of Regulations in Addressing Safety Concerns of the Furniture Manufacturing Industry
Regulations play a crucial role in addressing safety concerns in the furniture manufacturing industry. These regulations set standards for the quality of materials used, the design and construction of furniture, and the safety of workers in the industry.
By ensuring that these standards are met, regulations can help to prevent accidents and injuries, protect workers' health and safety, and minimize the risk of harm to consumers.
Some specific ways in which regulations can address safety concerns in the furniture manufacturing industry include:
- Materials standards: Regulations can set standards for the quality of materials used in furniture production, such as restrictions on the use of toxic chemicals or other hazardous substances. This can help to prevent exposure to harmful substances that can cause health problems for workers and consumers.
- Design and construction standards: Regulations can also set standards for the design and construction of furniture to ensure that it is sturdy and safe to use. For example, regulations may require that furniture be designed to withstand a certain amount of weight or force without collapsing or tipping over.
- Worker safety standards: Regulations can also address safety concerns related to the workers who manufacture furniture. This may include requirements for personal protective equipment, training programs for handling hazardous materials, or regulations related to workplace ergonomics to minimize the risk of repetitive stress injuries.
- Inspection and enforcement: Regulations may require regular inspections of furniture manufacturing facilities to ensure compliance with safety standards and may include penalties or fines for non-compliance.
Overall, regulations play a crucial role in ensuring the safety and well-being of workers and consumers in the furniture manufacturing industry.
By establishing standards for materials, design, and worker safety, regulations can help to prevent accidents and injuries and promote a safer and healthier industry for everyone involved.
The Role of Regulations in Addressing Transparency Concerns of the Furniture Manufacturing Industry
Regulations can also play an important role in addressing transparency concerns in the furniture manufacturing industry. Transparency refers to the extent to which manufacturers disclose information about their products, materials, and production processes.
This information is important for consumers who want to make informed purchasing decisions and for workers who want to understand the conditions under which furniture is produced.
Regulations can help to address transparency concerns in several ways, including:
- Labeling requirements: Regulations can require manufacturers to provide detailed information on product labels, such as the materials used, the country of origin, and any certifications or safety standards met. This can help consumers to make informed decisions about the products they purchase.
- Disclosure requirements: Regulations can require manufacturers to disclose information about their production processes, such as the chemicals used, waste disposal methods, and working conditions. This can help workers and consumers to understand the impact of the production process on the environment and on workers' health and safety.
- Reporting requirements: Regulations can require manufacturers to report on their sustainability and social responsibility practices, such as their use of renewable materials, their efforts to reduce waste and energy consumption, and their compliance with labor laws. This can help to promote greater transparency and accountability in the industry.
- Certification requirements: Regulations can require manufacturers to obtain third-party certifications that verify their compliance with certain standards, such as those related to sustainability, worker safety, or product quality. This can help to build trust with consumers and ensure that products are produced in an ethical and responsible manner.
Overall, regulations can play an important role in promoting greater transparency in the furniture manufacturing industry.
By requiring manufacturers to disclose information about their products and production processes, regulations can help consumers and workers to make informed decisions and promote greater accountability in the industry.
The Role of Regulations in Addressing Changes in Manufacturing Practices of the Furniture Manufacturing Industry
Regulations can also play a key role in addressing changes in manufacturing practices in the furniture manufacturing industry. As new technologies and practices emerge, regulations can help to ensure that these changes are implemented in a safe and sustainable way that protects the environment and the health and safety of workers and consumers.
Some ways in which regulations can address changes in manufacturing practices in the furniture manufacturing industry include:
- Updating standards: Regulations can be updated to reflect changes in manufacturing practices, such as the use of new materials or manufacturing processes. This can help to ensure that standards remain relevant and effective in promoting safety and sustainability.
- Implementing new regulations: In some cases, new regulations may be needed to address emerging issues related to new manufacturing practices. For example, regulations may be needed to address the environmental impact of new materials or the health and safety risks associated with new manufacturing processes.
- Providing guidance: Regulations can also provide guidance to manufacturers on best practices for implementing new manufacturing processes or technologies in a safe and sustainable way. This can help to ensure that manufacturers are able to adopt new practices while minimizing risks to workers and consumers.
- Monitoring and enforcement: Regulations can include monitoring and enforcement mechanisms to ensure that manufacturers comply with new regulations and standards related to changes in manufacturing practices. This can help to promote accountability and ensure that manufacturers are taking the necessary steps to protect the environment and promote worker and consumer safety.
Overall, regulations can play a crucial role in addressing changes in manufacturing practices in the furniture manufacturing industry.
By updating standards, implementing new regulations, providing guidance, and enforcing compliance, regulations can help to ensure that the industry evolves in a safe and sustainable way that protects workers, consumers, and the environment.
The Role of Regulations in Addressing Economic Concerns of the Furniture Manufacturing Industry
Regulations can also play a significant role in addressing economic concerns in the furniture manufacturing industry. These concerns may include issues such as fair competition, consumer protection, and the economic impact of the industry on local communities.
Some ways in which regulations can address economic concerns in the furniture manufacturing industry include:
- Antitrust regulations: Regulations can help to promote fair competition in the industry by prohibiting anti-competitive practices such as price fixing, market allocation, and monopolies. This can help to ensure that consumers have access to a variety of furniture products at fair prices.
- Consumer protection regulations: Regulations can help to protect consumers from fraudulent or deceptive practices in the industry, such as false advertising or mislabeling. This can help to promote consumer confidence and trust in the industry.
- Labor regulations: Regulations can help to ensure that workers in the industry are paid fair wages and have safe working conditions. This can help to prevent the exploitation of workers and promote economic stability in local communities.
- Environmental regulations: Regulations can help to promote sustainable practices in the industry, such as reducing waste and minimizing the use of harmful chemicals. This can help to protect the environment and promote the long-term economic sustainability of the industry.
Overall, regulations can play an important role in addressing economic concerns in the furniture manufacturing industry.
By promoting fair competition, protecting consumers, ensuring fair labor practices, and promoting sustainability, regulations can help to promote economic stability and growth in the industry while also protecting the interests of consumers and workers.
Key Changes and Impacts Due to the Regulations of Furniture Manufacturing
The regulations of furniture manufacturing have brought about several key changes and impacts, including:
- Increased Safety: Regulations have led to increased safety in furniture manufacturing by limiting the use of harmful chemicals and setting safety standards for products. This has reduced the risk of accidents and injuries for consumers.
- Improved Environmental Sustainability: Regulations have encouraged the use of sustainable materials and reduced waste in furniture manufacturing. This has led to a more environmentally sustainable industry, which benefits both the planet and the people who live on it.
- Better Transparency: Regulations have required companies to be more transparent about their supply chains and manufacturing processes. This has led to greater accountability and better traceability of products, which helps to prevent illegal or unethical practices.
- Changes in Manufacturing Practices: Regulations have required companies to change their manufacturing practices to comply with safety and environmental standards. This has led to the development of new technologies and processes, such as the use of non-toxic adhesives and the recycling of waste materials.
- Economic Impacts: Regulations have had economic impacts on the furniture industry, with some manufacturers facing increased costs due to the need to comply with new regulations. However, these impacts have been balanced by the benefits of increased safety and environmental sustainability, as well as the potential for increased customer trust and customer loyalty.
In conclusion, the regulations of furniture manufacturing have brought about significant changes and impacts, including increased safety, improved environmental sustainability, better transparency, changes in manufacturing practices, and economic impacts.
While some of these changes may have posed challenges for manufacturers, the overall benefits of compliance with regulations are clear and important for the long-term sustainability of the industry.
Examples of Furniture Manufacturing Companies that Had to Make Changes to Comply with these Regulations
There are several regulations that furniture manufacturing companies may need to comply with, such as environmental regulations, safety regulations, and labor regulations. Here are some examples of furniture manufacturing companies that have made changes to comply with these regulations:
- IKEA: IKEA is a global furniture manufacturer that has made significant efforts to comply with environmental regulations. For example, the company has committed to using only renewable energy sources in its operations and has implemented several sustainability initiatives, such as the use of recycled materials in its products.
- Herman Miller: Herman Miller is a furniture manufacturer that has implemented several safety regulations to ensure the safety of its workers. For example, the company has implemented ergonomic workstations to reduce the risk of musculoskeletal disorders among its workers.
- Steelcase: Steelcase is a furniture manufacturer that has implemented several labor regulations to ensure fair working conditions for its employees. For example, the company has implemented a code of conduct that sets out minimum standards for working conditions and wages for its workers.
- HNI Corporation: HNI Corporation is a furniture manufacturer that has implemented several environmental regulations to reduce its impact on the environment. For example, the company has implemented a zero-waste program that aims to reduce waste and increase recycling in its operations.
- Knoll: Knoll is a furniture manufacturer that has implemented several sustainability initiatives to reduce its impact on the environment. For example, the company has implemented a program to reduce its carbon footprint and has committed to using sustainable materials in its products.
- Haworth: Haworth is a global furniture manufacturer that has made significant efforts to comply with environmental regulations. The company has implemented sustainable practices in its manufacturing processes, such as using recycled materials and reducing waste.
- Ashley Furniture Industries: Ashley Furniture Industries is a furniture manufacturer that has implemented several safety regulations to ensure the safety of its workers. The company has a safety program that includes regular training for employees and the use of safety equipment.
- Sauder Woodworking: Sauder Woodworking is a furniture manufacturer that has implemented several environmental regulations to reduce its impact on the environment. The company has implemented sustainable practices, such as using renewable energy sources and reducing waste.
- La-Z-Boy: La-Z-Boy is a furniture manufacturer that has implemented several safety regulations to ensure the safety of its workers. The company has a safety program that includes regular training for employees and the use of safety equipment.
- Flexsteel Industries: Flexsteel Industries is a furniture manufacturer that has implemented several labor regulations to ensure fair working conditions for its employees. The company has a code of conduct that sets out minimum standards for working conditions and wages for its workers.
- Bassett Furniture: Bassett Furniture is a furniture manufacturer that has implemented several sustainability initiatives to reduce its impact on the environment. The company has implemented a program to reduce its carbon footprint and has committed to using sustainable materials in its products.
Strategies that Furniture Manufacturing Companies can Implement to Ensure Compliance with the Latest Regulations
Furniture manufacturing companies can implement several strategies to ensure compliance with the latest regulations. Here are some examples:
- Conduct a regulatory compliance audit: The first step for furniture manufacturing companies is to conduct a comprehensive audit to identify the regulations that apply to their operations. This will help them understand their compliance obligations and identify areas where they need to make changes.
- Develop a compliance program: Once the regulatory requirements are identified, the furniture manufacturing company can develop a compliance program to address them. This program should include policies and procedures to ensure compliance with the regulations.
- Train employees: Training is critical for ensuring compliance with regulations. Furniture manufacturing companies should provide regular training to their employees to ensure they understand the regulations and how to comply with them.
- Use technology: Furniture manufacturing companies can leverage technology to ensure compliance with regulations. For example, they can use software to manage their compliance program, track compliance activities, and generate compliance reports.
- Work with suppliers: Furniture manufacturing companies should work with their suppliers to ensure that the materials and components used in their products meet the regulatory requirements.
- Conduct regular audits and reviews: Regular audits and reviews are essential to ensure ongoing compliance with regulations. Furniture manufacturing companies should conduct regular internal audits and reviews to identify areas where they need to improve their compliance program.
- Engage with regulatory authorities: Furniture manufacturing companies should engage with regulatory authorities to stay up-to-date with the latest regulations and obtain guidance on compliance requirements.
Overall, by implementing these strategies, furniture manufacturing companies can ensure compliance with the latest regulations and minimize the risk of non-compliance penalties and reputational damage.
Here are some benefits and drawbacks of the strategies mentioned above:
1.Conduct a regulatory compliance audit:
Benefits:
- Identifies regulatory requirements and gaps in compliance
- Helps prioritize compliance activities
- Provides a baseline for measuring ongoing compliance
Drawbacks:
- It can be time-consuming and costly
- It may require specialized expertise to conduct the audit effectively
2.Develop a compliance program:
Benefits:
- Provides a structured approach to compliance
- Helps ensure that all compliance requirements are addressed
- Demonstrates commitment to compliance with regulatory authorities and customers
Drawbacks:
- It can be time-consuming to develop and implement
- It may require ongoing resources to maintain and update the program
3.Train employees:
Benefits:
- Ensures employees understand regulatory requirements and compliance obligations
- Reduces the risk of compliance breaches due to employee error
- Demonstrates commitment to compliance with regulatory authorities and customers
Drawbacks:
- It can be costly and time-consuming to implement
- It may require ongoing resources to maintain and update training materials
4.Use technology:
Benefits:
- Streamlines compliance activities
- Improves accuracy and efficiency of compliance management
- Provides real-time visibility into compliance status
Drawbacks:
- It can be costly to implement and maintain
- It may require specialized expertise to implement effectively
5.Work with suppliers:
Benefits:
- Helps ensure that materials and components meet regulatory requirements
- Demonstrates commitment to compliance with regulatory authorities and customers
- Reduces the risk of non-compliance due to supplier error
Drawbacks:
- It may require additional resources to manage supplier relationships
- Supplier non-compliance can still result in non-compliance for the furniture manufacturing company
6.Conduct regular audits and reviews:
Benefits:
- Helps identify areas of non-compliance and gaps in compliance
- Provides a basis for ongoing improvement of the compliance program
- Demonstrates commitment to compliance with regulatory authorities and customers
Drawbacks:
- It can be time-consuming and costly to conduct audits
- It may require specialized expertise to conduct effective audits
7.Engage with regulatory authorities:
Benefits:
- Helps stay up-to-date with the latest regulations and compliance requirements
- Provides guidance on compliance obligations
- Demonstrates commitment to compliance with regulatory authorities
Drawbacks:
- It may require additional resources to manage relationships with regulatory authorities
- This may result in increased scrutiny of the furniture manufacturing company
Overall, while these strategies have benefits in terms of improving compliance with regulations, they may also have drawbacks in terms of cost, resource requirements, and the need for specialized expertise.
It's important for furniture manufacturing companies to carefully consider their specific circumstances and regulatory requirements when implementing these strategies.
Challenges Faced by Furniture Manufacturing Companies in Complying with the Latest Regulations
Furniture manufacturing companies are subject to various regulations that are designed to ensure the safety of their products and protect the environment. Some of the main challenges faced by these companies in complying with the latest regulations include:
- Environmental Regulations: Furniture manufacturing companies are subject to a wide range of environmental regulations, including those related to the use of materials, waste disposal, and emissions. One of the main challenges is ensuring that the materials used in the manufacturing process are environmentally friendly and do not contain any harmful chemicals. Additionally, companies need to ensure that their waste disposal practices are compliant with local and national regulations.
- Safety Regulations: Safety regulations are put in place to ensure that furniture products are safe for consumers to use. Companies must comply with these regulations to avoid legal liabilities and protect their brand reputation. One of the main challenges is keeping up with the constantly evolving safety standards, which require regular updates and modifications to production processes.
- Labor Regulations: Furniture manufacturing companies must comply with various labor regulations related to worker safety, minimum wage, and working conditions. Compliance with these regulations can be challenging, particularly for smaller companies that may not have the resources to implement comprehensive safety programs or provide competitive wages and benefits.
- International Trade Regulations: Furniture manufacturing companies that engage in international trade must comply with various trade regulations, including tariffs, trade agreements, and customs regulations. Compliance with these regulations can be particularly challenging due to the complexity of the international trade system and the need to navigate multiple legal jurisdictions.
- Data Privacy Regulations: Furniture manufacturing companies must comply with various data privacy regulations, particularly those related to the handling of customer data. Compliance with these regulations can be challenging due to the complexity of data privacy laws and the need to implement comprehensive data protection measures.
In conclusion, compliance with the latest regulations can be challenging for furniture manufacturing companies due to the complexity of the regulations and the need to stay up-to-date with the latest requirements.
Companies must invest in training, resources, and systems to ensure that they can comply with these regulations and avoid legal liabilities and reputational damage.
Opportunities Available for Furniture Manufacturing Companies in Complying with the Latest Regulations
While complying with regulations can present challenges for furniture manufacturing companies, there are also opportunities available to those companies that are proactive in their approach to regulatory compliance.
Here are some of the opportunities available:
- Competitive Advantage: Companies that comply with the latest regulations can use this as a marketing tool to differentiate themselves from their competitors. By demonstrating a commitment to safety, environmental responsibility, and ethical labor practices, companies can attract customers who prioritize these values.
- Innovation: Compliance with regulations can encourage innovation within the manufacturing process. For example, restrictions on certain chemicals or materials can prompt companies to explore alternative materials or production methods, leading to new and potentially more sustainable products.
- Cost Savings: Compliance with regulations can lead to cost savings in the long run. For example, investing in energy-efficient equipment or implementing waste reduction programs can reduce energy and waste costs. Additionally, complying with safety regulations can reduce the risk of accidents and legal liabilities, leading to cost savings on insurance and legal fees.
- Access to new markets: Compliance with international trade regulations can provide companies with access to new markets and customers. For example, complying with the European Union's REACH (Registration, Evaluation, Authorization, and Restriction of Chemicals) regulation can enable companies to sell their products in the European market.
- Collaboration Opportunities: Companies that are proactive in their approach to compliance can also collaborate with regulatory agencies and other stakeholders to help shape future regulations. This can help ensure that regulations are feasible and practical for the industry while also improving product safety and environmental responsibility.
In conclusion, while complying with regulations can present challenges for furniture manufacturing companies, it also presents opportunities for companies to differentiate themselves from their competitors, innovate, and improve their operations.
By embracing compliance as an opportunity rather than a burden, companies can reap the benefits of regulatory compliance and build a more sustainable and profitable business.
Examples of Furniture Manufacturing Companies that Have Faced and Made the Most of These Challenges and Opportunities
There are several furniture manufacturing companies that have faced the challenges of regulatory compliance and turned them into opportunities for growth and success. Here are some examples:
- IKEA: IKEA is a multinational furniture retailer that has become known for its sustainable and affordable products. The company has faced challenges related to environmental and labor regulations but has used these challenges as opportunities to innovate and improve its operations. For example, IKEA has committed to using only renewable and recycled materials in its products by 2030 and has implemented a comprehensive code of conduct for its suppliers to ensure ethical labor practices.
- Steelcase: Steelcase is a furniture manufacturing company that specializes in office furniture. The company has faced challenges related to environmental regulations, particularly those related to emissions and waste. However, Steelcase has used these challenges as an opportunity to innovate and improve its operations. For example, the company has implemented a zero-waste-to-landfill program, which has helped it reduce its waste and carbon footprint.
- Herman Miller: Herman Miller is a furniture manufacturing company that specializes in modern and ergonomic furniture. The company has faced challenges related to environmental and labor regulations but has used these challenges as opportunities to improve its operations and build a more sustainable business. For example, Herman Miller has implemented a comprehensive sustainability program that includes initiatives such as reducing waste and emissions, sourcing sustainable materials, and promoting ethical labor practices.
- Haworth: Haworth is a furniture manufacturing company that specializes in office furniture. The company has faced challenges related to environmental regulations, particularly those related to emissions and waste. However, Haworth has used these challenges as an opportunity to innovate and improve its operations. For example, the company has implemented a closed-loop recycling program, which has helped it reduce its waste and carbon footprint.
In conclusion, these companies have demonstrated that regulatory compliance can be an opportunity for growth and success.
By embracing compliance as an opportunity to innovate, improve operations, and build a more sustainable business, these companies have differentiated themselves from their competitors and built a loyal customer base that values ethical and sustainable practices.
Consequence of Non-Compliance with Regulations of Furniture Manufacturing
Non-compliance with regulations of furniture manufacturing can have serious consequences for both manufacturers and consumers. Here are some potential consequences of non-compliance:
- Fines and penalties: Regulatory bodies may impose fines and penalties on furniture manufacturers who violate safety standards and regulations. These fines can be costly and can damage a company's reputation.
- Product recalls: If furniture products do not meet safety standards or pose a risk to consumers, regulatory bodies may require manufacturers to issue product recalls. Product recalls can be expensive and can damage a company's reputation.
- Legal action: In severe cases, non-compliance with safety regulations can result in legal action against furniture manufacturers. This can result in additional fines and penalties, as well as damage to a company's reputation and potential legal fees.
- Damage to reputation: Non-compliance with safety regulations can damage a furniture manufacturer's reputation, leading to decreased sales and difficulty in securing future contracts.
- Risk to consumer safety: Non-compliance with safety regulations can put consumers at risk of injury or illness. This can result in lawsuits against furniture manufacturers and damage to a company's reputation.
It is essential for furniture manufacturers to prioritize compliance with safety regulations to ensure the safety and well-being of consumers and avoid the potential consequences of non-compliance.
How can the Implementation of MRP Software Help in Complying with Regulations of Furniture Manufacturing?
MRP (Material Requirements Planning) software can be a useful tool for furniture manufacturers to help comply with regulations related to their industry. Here are a few ways MRP software can assist with compliance:
- Automating compliance checks: MRP software can automate compliance checks for regulations related to material sourcing, product safety, and environmental impact. This can help manufacturers ensure that their products comply with the latest regulations and identify any potential issues early in the production process.
- Traceability and transparency: MRP software can provide traceability and transparency in the supply chain, allowing manufacturers to track materials and components from their source to the finished product. This can help ensure that materials are ethically sourced and meet environmental and safety standards.
- Quality control: MRP software can be used to implement quality control processes, such as product testing and inspection, to ensure that products meet safety and quality standards.
- Document management: MRP software can help manufacturers maintain accurate documentation related to compliance, such as material certifications and product testing reports. This can be helpful in demonstrating compliance with regulatory bodies.
- Inventory management: MRP software can help manufacturers optimize inventory management and reduce waste, which can be beneficial for complying with environmental regulations.
By using MRP software to help comply with regulations related to furniture manufacturing, manufacturers can streamline their compliance processes, reduce the risk of non-compliance, and maintain the safety and quality of their products.
How can Deskera Help You with Furniture Manufacturing?
Deskera is a cloud-based software solution that offers a range of features to help streamline and optimize the furniture manufacturing process. Here are some ways Deskera MRP can help you with furniture manufacturing:
- Inventory management: Deskera can help you manage your inventory levels and track the movement of raw materials and finished goods in real-time.
- Production planning: With Deskera, you can plan and schedule your production process, track progress, and monitor resource utilization to ensure efficient production.
- Quality control: Deskera offers tools to help you manage quality control throughout the manufacturing process, from design to finishing, to ensure that your products meet the required standards.
- Sales and distribution: Deskera can help you manage your sales orders, track customer orders, and manage your distribution channels, allowing you to manage your sales process more efficiently.
- Financial management: With Deskera, you can manage your financial transactions, track expenses, and generate financial reports, giving you greater visibility into your financial performance.
- Business intelligence: Deskera provides advanced analytics and reporting capabilities, allowing you to gain insights into your business performance and make data-driven decisions.
Key Takeaways
Here are some key takeaways related to the latest regulations in furniture manufacturing:
- The furniture manufacturing industry is subject to numerous regulations related to product safety, environmental impact, and workplace safety. Some of the latest regulations that this industry needs to adhere to are:
- Formaldehyde Emission Standards
- Chemicals of Concern
- Occupational Safety and Health Administration (OSHA) regulations
- Environmental Protection Agency (EPA) regulations
- California's Proposition 65
- EU Timber Regulation
- Restriction of Hazardous Substances (RoHS) Directive
- Consumer Product Safety Improvement Act (CPSIA)
- Chemicals Management Regulation (REACH)
- Sustainability Standards
- US Consumer Product Safety Commission (CPSC)
- Trade Regulations
- Flame Retardant Regulations
- Compliance with these regulations is essential to protect the safety of consumers, maintain industry standards, and avoid legal and financial consequences.
- Furniture manufacturers must implement internal controls, including regular testing and quality control measures, to ensure compliance with these regulations.
- Non-compliance with safety regulations can result in fines, product recalls, legal action, and damage to a company's reputation.
In conclusion, the furniture manufacturing industry must prioritize compliance with the latest regulations and standards to ensure the safety and well-being of consumers and protect their businesses from potential legal and financial consequences.
By staying informed about the latest regulations and implementing effective quality control measures, furniture manufacturers can build trust with consumers, maintain industry standards, and protect their reputations.
Lastly, by using Deskera's comprehensive suite of software tools, furniture manufacturers can streamline their operations, improve efficiency, ensure compliance with regulations, and reduce costs, resulting in better business performance and increased customer satisfaction.
Related Articles

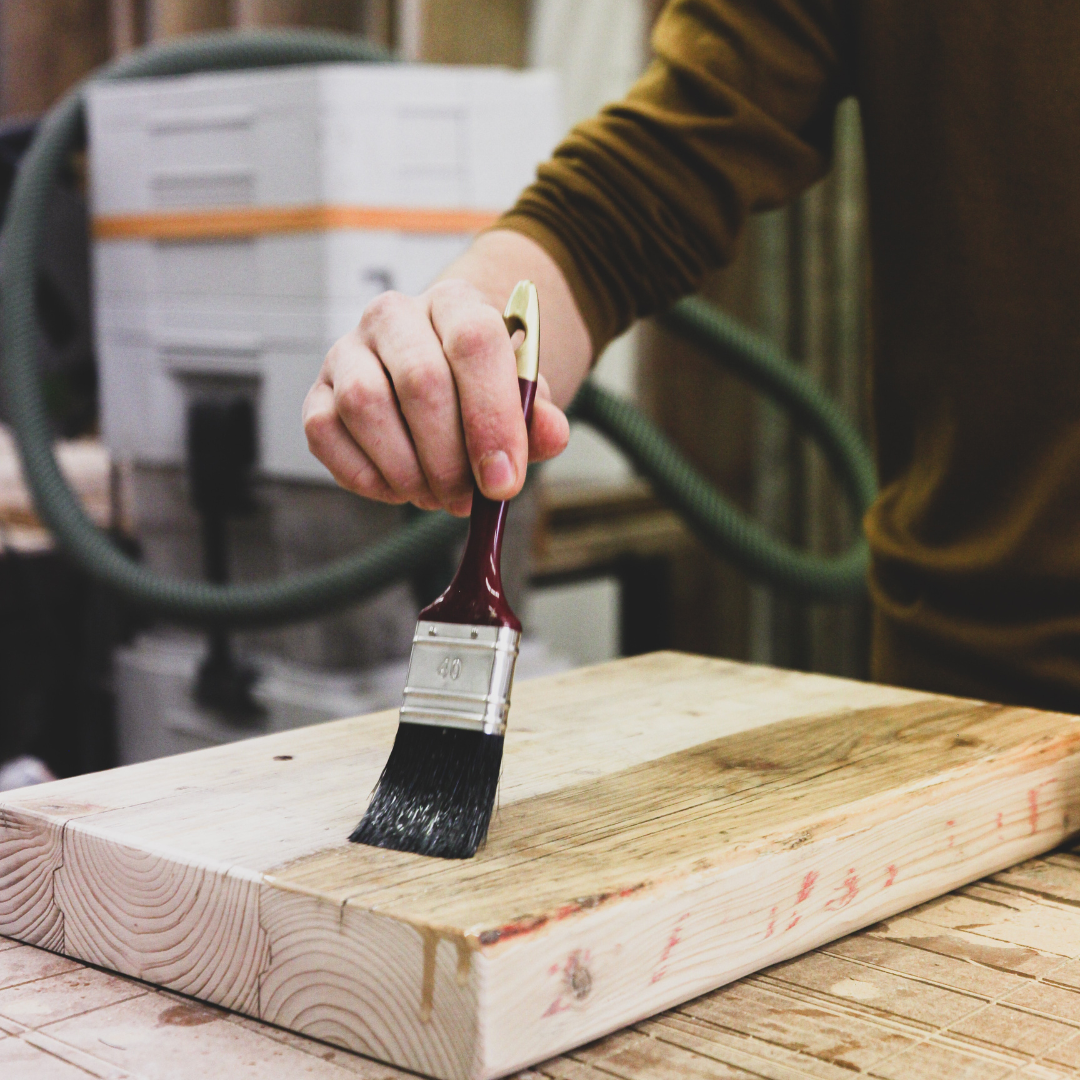
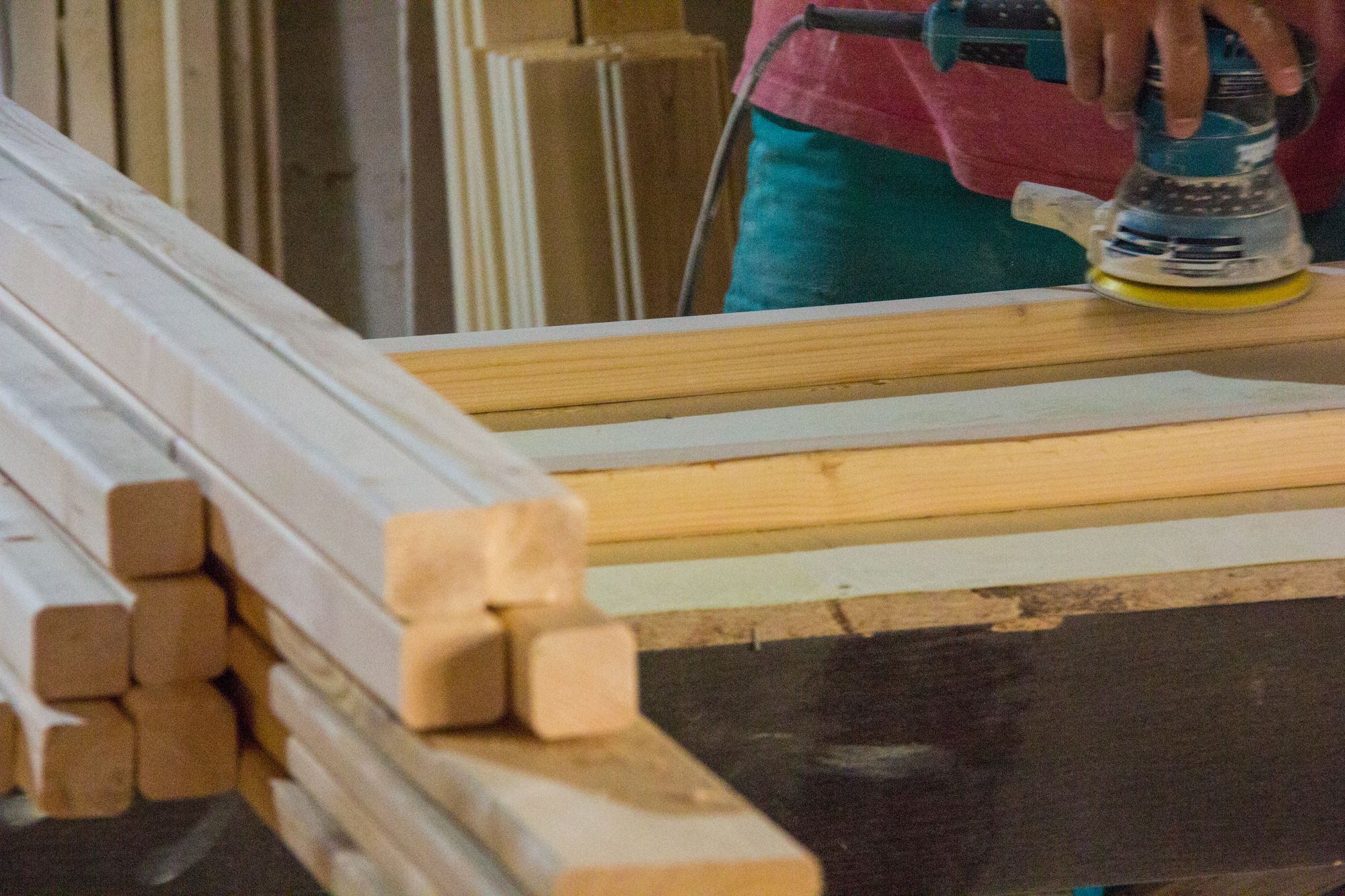
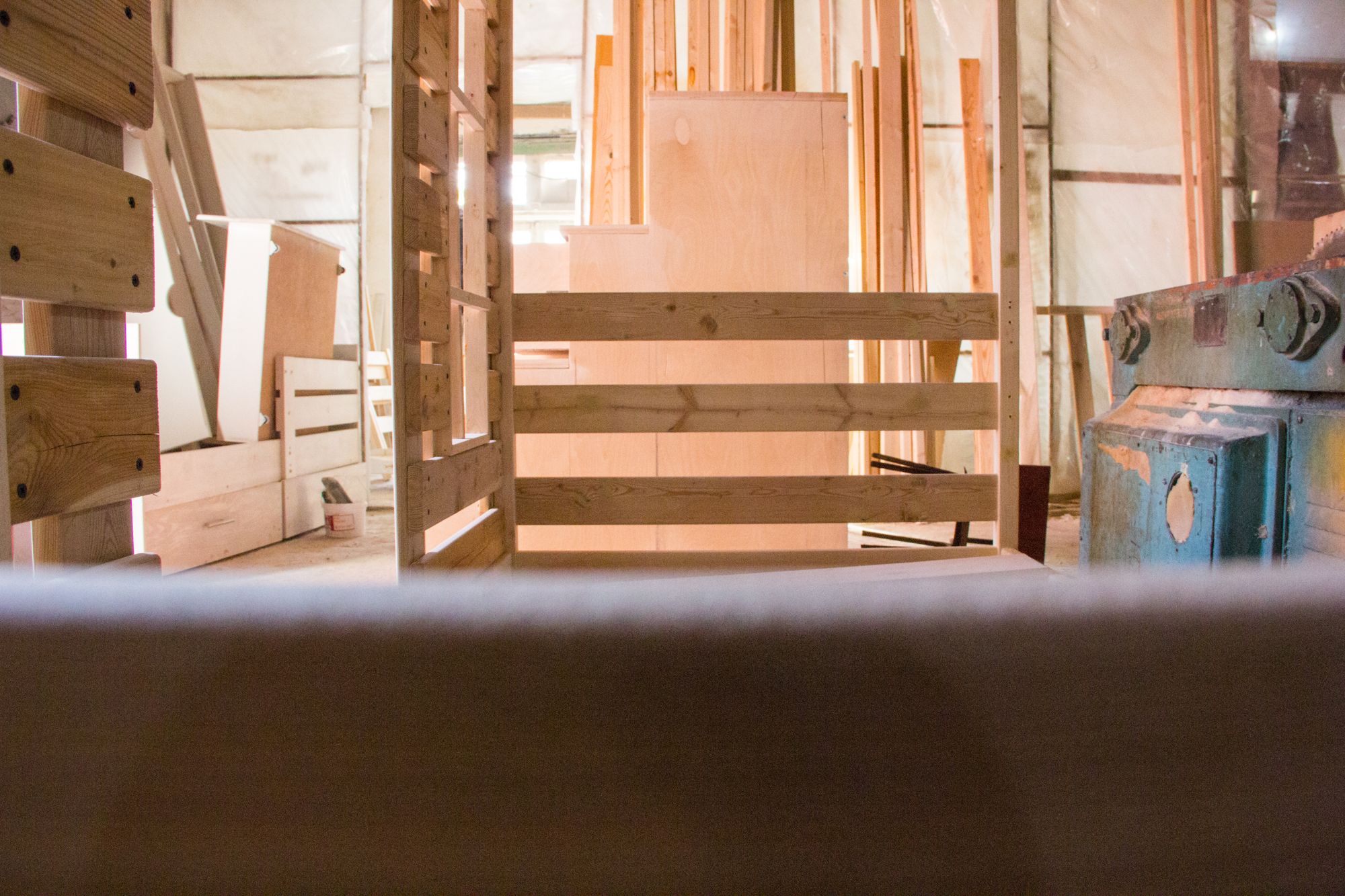
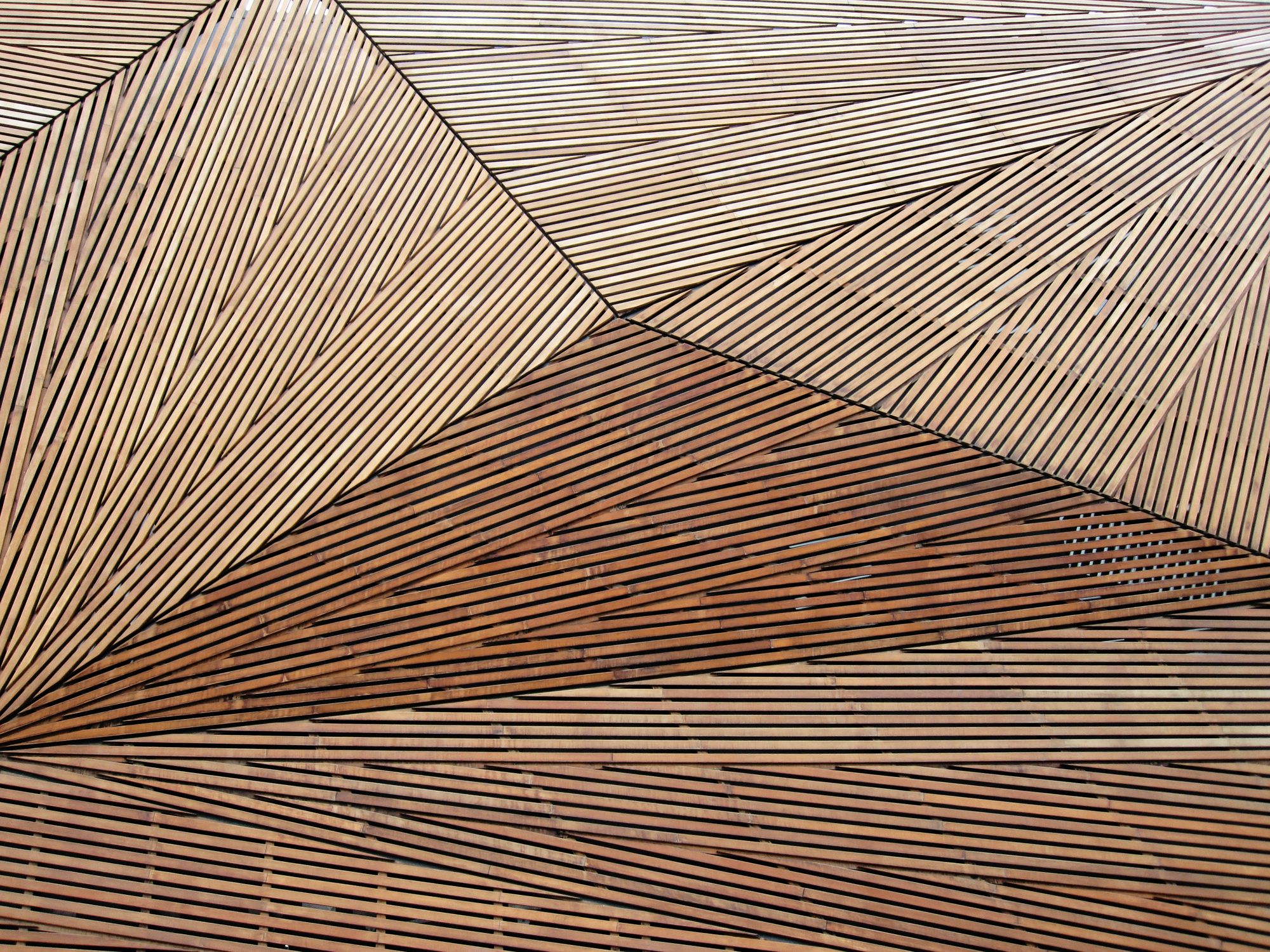
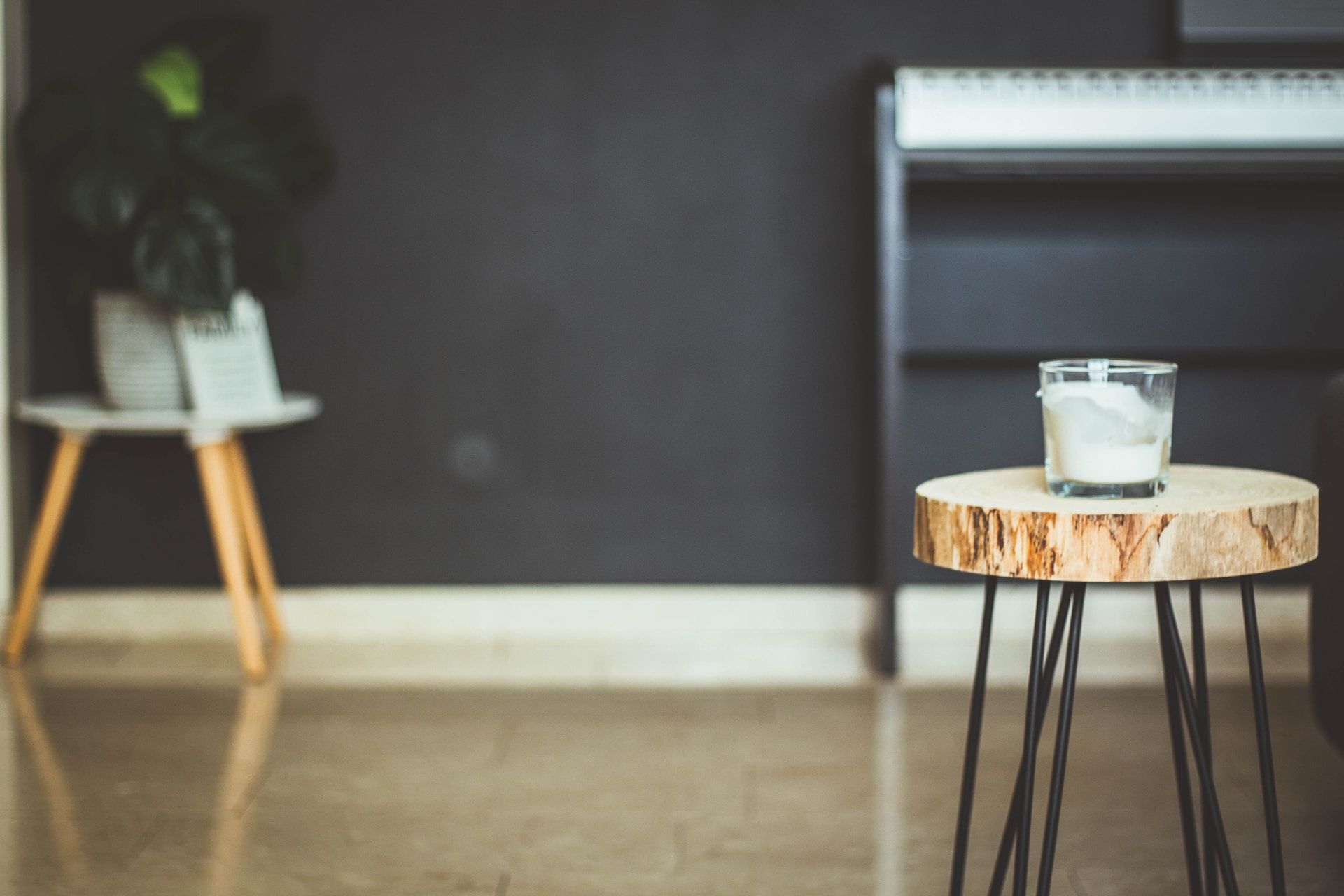