Are you trying to uncover the tool of the multi-level bill of materials that empowers manufacturers to navigate challenges, make informed decisions, and drive continuous improvement across all aspects of their manufacturing operations? If your answer is yes, then you are on the right page.
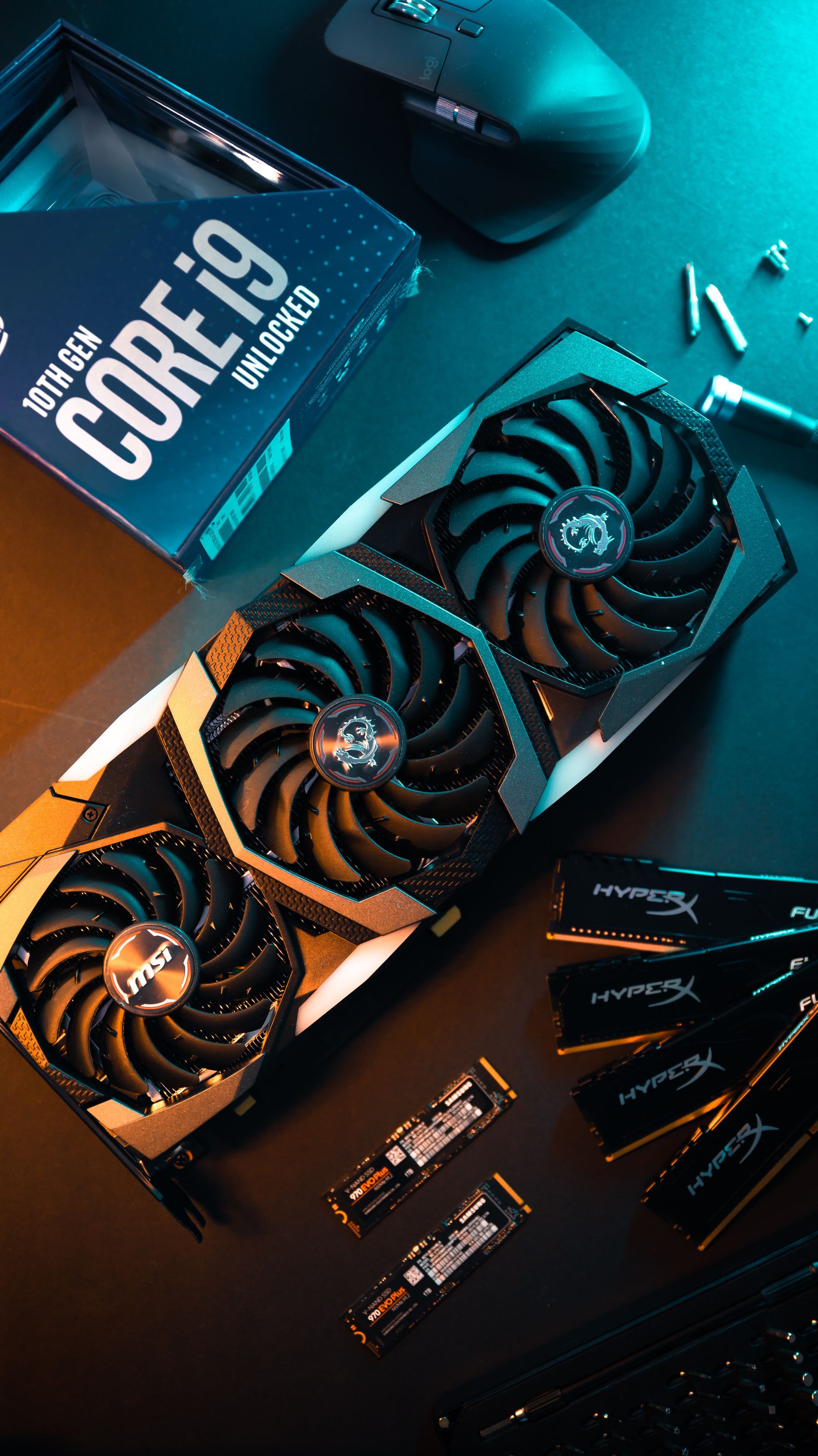
In the complex world of modern manufacturing, the successful production of goods relies on the seamless coordination of numerous components, processes, and stakeholders.
At the heart of this intricate dance lies the Multi-Level Bill of Materials (BOM), a fundamental tool that serves as a blueprint for understanding, organizing, and executing the intricate relationships within a product's structure.
The Multi-Level BOM transcends the simple listing of parts and materials; it holds the key to unlocking efficiency, accuracy, and control in manufacturing operations.
In this article, we delve into the crucial role that the Multi-Level BOM plays in the manufacturing landscape. The topics covered in this article are:
- All About Multi-Level Bill of Materials
- What is Manufacturing?
- Understanding the Crucial Role of Multi-Level BOM in Manufacturing
- How Can Deskera Help You with a Multi-Level Bill of Materials?
- Key Takeaways
- Related Articles
All About Multi-Level Bill of Materials
A Multi-Level Bill of Materials (BOM) is a hierarchical representation of the components, subassemblies, and raw materials needed to manufacture a final product.
It provides a comprehensive view of the entire production process, from the top-level finished product down to the smallest parts and materials required for its assembly.
Multi-level BOMs are widely used in manufacturing, engineering, and production planning to facilitate accurate resource allocation, procurement, production scheduling, and cost estimation.
Key components of a multi-level BOM include:
- Hierarchy: Multi-level BOMs consist of different levels of components. The top level represents the final product, while subsequent levels break down the product into its subassemblies and further into individual parts. This hierarchical structure enables a clear understanding of the product's composition.
- Part Numbers and Descriptions: Each component in the BOM is identified by a part number and accompanied by a description that provides information about the component, such as its name, specifications, dimensions, and materials.
- Quantities: The BOM specifies the quantity of each component required to assemble one unit of the final product. These quantities help in planning procurement, managing inventory, and calculating the total material needed for production.
- Reference Designators: In electronic and electrical industries, reference designators are used to uniquely identify each component in the BOM. These designators assist in locating components on a physical assembly.
- Routing Information: In addition to the component list, a BOM may also include routing information that outlines the steps required for assembling the product. This information helps in production scheduling and resource allocation.
- Indented Structure: The BOM is often presented in an indented or hierarchical structure, where each level of components is indented relative to the previous level. This visual representation makes it easier to understand the assembly process.
- Substitute Components: BOMs may include alternate or substitute components that can be used if the primary components are not available. This helps in managing supply chain disruptions.
- Phantom Assemblies: Sometimes, certain subassemblies may not physically exist but are used conceptually to simplify the BOM structure. These are known as phantom assemblies and are useful for planning and documentation purposes.
Benefits of Multi-Level BOMs:
- Accurate Planning: Multi-level BOMs enable accurate production planning, as they provide a detailed breakdown of all components required for manufacturing.
- Efficient Procurement: With clear visibility into the entire assembly process, procurement teams can accurately order the necessary materials and components, reducing excess inventory and shortages.
- Resource Allocation: Production managers can allocate resources, such as labor, equipment, and time, more effectively by understanding the sequential assembly steps.
- Cost Estimation: Multi-level BOMs aid in accurate cost estimation by capturing all the components, labor, and other resources needed for production.
- Design Changes: When design changes occur, a multi-level BOM helps identify the impact on the entire production process and facilitates necessary adjustments.
- Documentation: BOMs serve as crucial documentation for regulatory compliance, quality control, and historical reference.
In conclusion, a Multi-Level Bill of Materials is a fundamental tool for managing the complex process of product assembly, providing a detailed and structured view of the components, subassemblies, and materials required to manufacture a final product. It enhances efficiency, accuracy, and control throughout the production lifecycle.
What is Manufacturing?
Manufacturing refers to the process of transforming raw materials, components, or parts into finished goods through various physical, chemical, or mechanical processes. It involves the use of machinery, tools, labor, and techniques to create products that have commercial value and utility. Manufacturing plays a central role in the production of a wide range of goods, from simple everyday items to complex high-tech products.
Key aspects of manufacturing include:
- Production Processes: Manufacturing encompasses a diverse range of production processes, such as cutting, shaping, molding, assembling, welding, machining, and chemical reactions. These processes vary depending on the nature of the product being made.
- Raw Materials and Components: Manufacturing involves the utilization of raw materials, components, and parts. These materials can be sourced from various suppliers and are processed and transformed into the final product.
- Labor and Automation: Manufacturing can be labor-intensive or highly automated, depending on the complexity of the product and technological advancements. Labor plays a significant role in tasks that require manual dexterity and decision-making, while automation is employed for precision, efficiency, and consistency.
- Quality Control: Ensuring the quality of manufactured products is essential. Quality control processes are implemented to monitor and verify that products meet established standards and specifications.
- Supply Chain Management: Manufacturing is closely connected to supply chain management, which involves coordinating the flow of materials, information, and resources from suppliers to manufacturers and ultimately to customers.
- Lean Manufacturing: Lean manufacturing is an approach aimed at minimizing waste and maximizing efficiency in the manufacturing process. It involves techniques to eliminate non-value-added activities and optimize resource utilization.
- Mass Production vs. Customization: Manufacturing can involve mass production, where large quantities of identical products are made, or customization, where products are tailored to meet specific customer requirements.
- Types of Manufacturing: Manufacturing can be categorized into various types, including discrete manufacturing (individual products), process manufacturing (chemicals, food, etc.), batch production (limited quantities), and continuous production (24/7 production lines).
- Advanced Manufacturing Technologies: With advancements in technology, manufacturing has evolved to include cutting-edge techniques such as additive manufacturing (3D printing), advanced robotics, computer numerical control (CNC) machining, and the Internet of Things (IoT)-enabled smart manufacturing.
Manufacturing is a crucial sector of the economy, contributing to economic growth, job creation, and innovation. It plays a vital role in providing essential goods for daily life and driving technological advancements that shape various industries.
Understanding the Crucial Role of Multi-Level BOM in Manufacturing
The Multi-Level Bill of Materials (BOM) plays a crucial and foundational role in the manufacturing process. It serves as a comprehensive roadmap that guides and facilitates various aspects of production, ensuring efficient and accurate assembly of products.
Let's delve deeper into its crucial role:
Product Structure Clarity
It refers to the ability to clearly understand and visualize how a product is composed of various components, subassemblies, and raw materials. This clarity is essential for effective manufacturing and encompasses several key aspects:
- Hierarchical Representation: A Multi-Level BOM provides a hierarchical representation of a product's structure. It breaks down the product into different levels, with the top level representing the final assembled product and subsequent levels detailing the subassemblies and individual components that make up the product. This hierarchical structure helps manufacturers understand the relationship between different parts and how they come together to create the whole.
- Visualization: The Multi-Level BOM offers a visual representation of the product's composition. It can be presented in various formats, such as indented lists or tree diagrams, which make it easier to grasp the complex relationships between components. This visualization aids in communicating the product structure across different teams and departments involved in manufacturing.
- Component Relationships: The BOM specifies how various components are related to each other. It outlines parent-child relationships, indicating which components are part of a larger assembly. This information is crucial for understanding how components fit together during assembly and disassembly processes.
- Dependencies and Interconnections: The BOM highlights dependencies and interconnections between components. It shows how changes to one component can impact other parts of the product. This insight is vital for assessing the feasibility and implications of design changes or substitutions.
- Identifying Critical Components: Product structure clarity helps identify critical components that are essential for the product's functionality and performance. Manufacturers can prioritize the availability and quality of these critical components to ensure the overall quality of the final product.
- Subassembly Breakdown: Subassemblies are often used to group related components together. The Multi-Level BOM breaks down these subassemblies further into their constituent parts. This breakdown assists in understanding the hierarchy of components and the assembly sequence.
- Assembly Sequence: The BOM defines the sequence in which components and subassemblies are assembled to create the final product. This assembly sequence provides a step-by-step guide for production, helping manufacturers organize and plan their manufacturing processes.
- Exploded Views: Multi-Level BOMs often include exploded views, which illustrate how components fit together in a detailed and easily understandable manner. These views help visualize the spatial relationships between parts and aid in assembly and disassembly procedures.
- Documentation and Training: Product structure clarity is essential for creating comprehensive documentation and training materials. It enables the development of assembly instructions, user manuals, and training guides that accurately convey how to assemble, use, and maintain the product.
In summary, product structure clarity, facilitated by a Multi-Level BOM, is fundamental for effective communication, planning, and execution in manufacturing.
It ensures that everyone involved in the production process has a common understanding of the product's composition, how its components relate to each other, and how they come together to create the final product.
This clarity underpins successful manufacturing operations, quality control, and continuous improvement efforts.
Accurate Resource Planning
Accurate resource planning is a critical aspect of manufacturing operations, and a Multi-Level Bill of Materials (BOM) plays a significant role in facilitating this process.
Here's an elaboration on how a Multi-Level BOM contributes to accurate resource planning:
- Material Quantities and Types: The Multi-Level BOM specifies the quantities of each component, subassembly, and raw material required to manufacture the final product. This information is essential for determining how much of each material needs to be procured or kept in inventory. Accurate material planning prevents shortages, excess stock, and the associated costs of carrying inventory.
- Inventory Management: By breaking down the product structure, the BOM provides insights into the inventory requirements for each component and subassembly. Manufacturers can calculate reorder points, safety stock levels, and lead times based on the BOM data. This ensures that materials are available when needed, minimizing production delays.
- Lead Time Considerations: The BOM includes information about lead times for procuring components and materials. Manufacturers can plan production schedules based on these lead times to avoid bottlenecks and ensure a smooth production flow.
- Supplier Coordination: Accurate resource planning, driven by the Multi-Level BOM, enables manufacturers to communicate effectively with suppliers. They can provide precise information about material requirements, allowing suppliers to plan their production and delivery schedules accordingly.
- Resource Allocation: The BOM's breakdown of components and subassemblies helps in allocating labor, machinery, and equipment resources. Manufacturers can determine the specific skills and equipment needed at different stages of production, ensuring efficient resource utilization.
- Production Capacity: Manufacturers can assess their production capacity and capabilities based on the BOM. They can identify potential constraints and plan production volumes in alignment with available resources.
- Cost Estimation: Accurate resource planning, driven by the Multi-Level BOM, contributes to more precise cost estimation. Manufacturers can calculate labor costs, material costs, and overhead expenses associated with each component and process. This information aids in setting competitive prices and managing profitability.
- Scheduling Optimization: The BOM's hierarchical structure outlines the sequence of assembly operations. This sequence information is vital for creating realistic and achievable production schedules. Manufacturers can avoid overloading certain production stages and ensure a balanced workflow.
- Demand Forecasting: A Multi-Level BOM aids in forecasting material and component demands based on the production schedule. This forecasting helps procurement teams plan ahead and negotiate favorable terms with suppliers.
- Production Planning Flexibility: The BOM allows manufacturers to explore different production scenarios. By adjusting quantities, lead times, or suppliers, they can analyze how changes impact resource requirements, costs, and schedules, enabling informed decision-making.
In essence, accurate resource planning ensures that the right materials, labor, and equipment are available at the right time and in the right quantities. This prevents production disruptions, minimizes waste, optimizes resource utilization, and contributes to overall operational efficiency.
The Multi-Level BOM serves as a foundation for these planning efforts, providing a comprehensive and structured view of the product's components and their interrelationships.
Inventory Management
Inventory management is a crucial aspect of manufacturing operations, and a Multi-Level Bill of Materials (BOM) plays a significant role in optimizing inventory levels and ensuring smooth production processes.
Here's an elaboration on how a Multi-Level BOM contributes to effective inventory management:
- Demand Forecasting: The BOM provides a detailed breakdown of the components and materials required to produce the final product. By analyzing the BOM, manufacturers can forecast the demand for each component based on the production schedule. This enables more accurate demand forecasting and helps suppliers prepare for fluctuations in material requirements.
- Reorder Points: The BOM specifies the quantities of each component needed for production. Manufacturers can use this information to set appropriate reorder points for each component. When inventory levels reach these points, it triggers a reorder, ensuring that materials are replenished in a timely manner.
- Safety Stock Calculation: Safety stock is the extra inventory held to mitigate the risk of unexpected supply chain disruptions or demand spikes. The BOM aids in calculating safety stock requirements by considering lead times, demand variability, and production cycle times for each component.
- Lead Time Considerations: The BOM includes lead time information for procuring components and materials. By incorporating lead times into inventory management calculations, manufacturers can avoid stockouts and production delays.
- Just-In-Time (JIT) Inventory: For manufacturers implementing JIT inventory practices, the BOM is instrumental. It allows them to precisely time material orders and deliveries to match production needs, minimizing excess inventory while ensuring materials are available when required.
- Component Availability: The BOM provides visibility into the availability of each component and its lead time. Manufacturers can cross-reference this information with current inventory levels to determine if they have enough stock to support production or if additional materials need to be procured.
- Reducing Excess Inventory: Excess inventory ties up valuable resources and incurs carrying costs. The BOM helps manufacturers avoid over-purchasing components by providing accurate quantity requirements for each production run.
- Obsolete Inventory Management: As products evolve and designs change, components can become obsolete. The BOM assists in identifying such components, allowing manufacturers to manage their inventory effectively and avoid holding obsolete stock.
- Supplier Coordination: With BOM-driven inventory management, manufacturers can communicate more effectively with suppliers. They can provide specific details about the quantities and types of components needed, allowing suppliers to plan their production and deliveries accordingly.
- Waste Reduction: Accurate inventory management based on the BOM helps minimize waste by preventing overproduction and excess inventory buildup. Manufacturers can align production with actual demand, reducing the likelihood of disposal due to obsolescence or expiry.
- Cost Savings: Optimized inventory management reduces carrying costs associated with excess inventory and frees up working capital. Manufacturers can allocate resources more efficiently, leading to cost savings in storage, handling, and financing.
- Consistent Production: The BOM ensures that all required components are available before production begins. This prevents production interruptions and maintains consistent product quality and output.
In summary, a Multi-Level BOM serves as a valuable tool for managing inventory effectively. It provides insights into component requirements, lead times, and demand patterns, enabling manufacturers to maintain optimal inventory levels, reduce costs, and enhance overall operational efficiency.
Procurement Efficiency
Procurement efficiency is a critical aspect of manufacturing operations, and a Multi-Level Bill of Materials (BOM) plays a significant role in streamlining the procurement process.
Here's an elaboration on how a Multi-Level BOM contributes to procurement efficiency:
- Accurate Material Requirements: The BOM provides a comprehensive list of all components, subassemblies, and raw materials needed to manufacture the final product. Procurement teams can use this information to accurately determine the quantities and types of materials to be ordered.
- Supplier Communication: The BOM serves as a clear and detailed communication tool between manufacturers and suppliers. Manufacturers can share the BOM with suppliers, specifying the exact components required. This reduces the likelihood of errors, misunderstandings, and incorrect orders.
- Batch Ordering: The BOM outlines the quantities of each component needed for production. Procurement teams can use this information to optimize ordering quantities and batch orders, which can lead to better pricing and reduced procurement costs.
- Lead Time Considerations: The BOM includes lead time information for each component. Procurement teams can take this into account when placing orders, ensuring that materials are received in time for production without causing delays.
- Supplier Selection: Procurement teams can analyze the BOM to identify critical components and assess the capabilities of potential suppliers. This helps in selecting reliable suppliers who can meet the specified quality standards and delivery timelines.
- Negotiations and Contracts: Armed with accurate BOM-based information, manufacturers can negotiate terms and conditions with suppliers more effectively. They can discuss pricing, lead times, and other terms based on the specific components and quantities involved.
- Consolidated Orders: The BOM helps in consolidating orders by grouping similar or related components from multiple suppliers. This consolidation can result in economies of scale, reduced administrative efforts, and lower shipping costs.
- Supplier Collaboration: Sharing the BOM with suppliers fosters collaboration and transparency. Suppliers can gain a better understanding of the product's requirements and offer suggestions for component improvements or cost savings.
- Customization and Substitutions: The BOM allows for easy identification of components that can be customized or substituted without affecting the final product's functionality. This flexibility can lead to more options in sourcing and potentially better pricing.
- Quality Assurance: The BOM ensures that the specified components are procured, maintaining consistent product quality. Procurement teams can verify that the received components match the BOM specifications, reducing the risk of quality issues.
- Reduced Overstock and Understock: Accurate BOM-based procurement prevents overstocking (excessive inventory) and understocking (shortages). Procurement teams can order the right quantities based on production requirements, optimizing inventory levels.
- Economic Order Quantity (EOQ): The BOM data helps calculate the Economic Order Quantity, which represents the optimal order quantity that minimizes total inventory costs. This ensures that procurement decisions are based on quantitative analysis.
In summary, a Multi-Level BOM serves as a guiding document that enhances procurement efficiency by providing clear, accurate, and detailed information about material requirements.
This enables manufacturers to make informed procurement decisions, reduce lead times, optimize costs, and ensure a steady flow of materials for smooth production processes.
Cost Estimation and Control
Cost estimation and control are essential aspects of manufacturing operations, and a Multi-Level Bill of Materials (BOM) plays a significant role in achieving accurate cost calculations and effective cost management.
Here's an elaboration on how a Multi-Level BOM contributes to cost estimation and control:
- Detailed Component Costs: The BOM provides a breakdown of all components, subassemblies, and raw materials required for the final product. Each component's cost can be associated with its entry in the BOM, allowing for accurate calculation of the total material cost.
- Labor and Overhead Costs: In addition to material costs, the BOM can include information about labor hours and overhead expenses associated with each assembly step. This enables a comprehensive calculation of the total production cost.
- Total Product Cost: By summing up the costs of individual components, labor, and overhead, manufacturers can accurately estimate the total cost of producing each unit of the final product.
- Scenario Analysis: Manufacturers can use the BOM to conduct scenario analyses and cost simulations. By adjusting quantities, production methods, or supplier choices in the BOM, they can assess how different factors impact the overall production cost.
- Accurate Pricing: Based on the total production cost calculated from the BOM, manufacturers can set appropriate selling prices that cover all expenses while ensuring competitiveness in the market.
- Budgeting: The BOM serves as a foundation for budgeting purposes. Manufacturers can allocate funds based on the estimated costs of materials, labor, and overhead derived from the BOM.
- Variance Analysis: During production, the BOM provides a benchmark against which actual costs can be compared. This enables variance analysis, where discrepancies between estimated and actual costs are identified and analyzed for corrective action.
- Cost Reduction Opportunities: The BOM facilitates the identification of cost reduction opportunities. By analyzing component costs and exploring alternative suppliers or materials, manufacturers can make informed decisions to lower production expenses.
- Substitute Component Evaluation: In cases where substitute components are permissible, the BOM allows for evaluating the cost impact of using different materials or parts. This helps in selecting cost-effective alternatives without compromising product quality.
- Accurate Quoting: When responding to requests for quotations (RFQs), manufacturers can use the BOM to generate accurate quotes that consider all cost factors. This prevents underquoting, which can lead to losses, or overquoting, which might deter potential customers.
- Profitability Analysis: The BOM-derived cost estimation contributes to profitability analysis. Manufacturers can assess the margin between production costs and selling prices, helping them make informed decisions to improve profitability.
- Cost Tracking: Throughout the manufacturing process, the BOM provides a reference point for tracking costs at each production stage. This enables manufacturers to monitor cost variances and take corrective actions as needed.
In summary, a Multi-Level BOM is a powerful tool for cost estimation and control in manufacturing. It ensures that costs are accurately calculated, budgets are effectively managed, and profitability is maintained.
By providing a detailed breakdown of components, labor, and overhead, the BOM enables manufacturers to make informed decisions that optimize costs and contribute to the financial success of the organization.
Production Scheduling
Production scheduling is a crucial aspect of manufacturing operations, and a Multi-Level Bill of Materials (BOM) plays a significant role in creating efficient and effective production schedules.
Here's an elaboration on how a Multi-Level BOM contributes to production scheduling:
- Assembly Sequence: The BOM provides a hierarchical breakdown of components and subassemblies, outlining the precise assembly sequence required to build the final product. This sequence information is essential for determining the order in which different tasks and operations should be carried out during production.
- Task Prioritization: The BOM helps in prioritizing tasks and operations based on their order of assembly and criticality. This enables production managers to allocate resources to high-priority tasks and ensure that key components are assembled at the appropriate stages.
- Resource Allocation: With the BOM's information on assembly sequences, manufacturers can allocate labor, machinery, and equipment resources more effectively. This prevents bottlenecks and ensures that the right resources are available at the right time to maintain a smooth production flow.
- Lead Time Considerations: The BOM includes lead time information for procuring components and materials. Production managers can take these lead times into account when creating schedules to avoid delays caused by material shortages.
- Realistic Time Estimates: The BOM assists in creating accurate time estimates for each assembly step. By considering the time required for assembling different components and subassemblies, production managers can create more realistic production schedules.
- Capacity Planning: The BOM allows manufacturers to assess their production capacity based on the time estimates for each assembly step. This helps in determining whether the existing capacity is sufficient to meet production demands or if adjustments are needed.
- Resource Leveling: With insights from the BOM, production managers can balance workloads and resources across different assembly stages. This prevents overloading certain areas while underutilizing others, leading to smoother production operations.
- Reducing Idle Time: Accurate production scheduling based on the BOM minimizes the idle time between assembly steps. This ensures that resources are utilized efficiently, contributing to higher overall productivity.
- Minimizing Changeovers: The BOM's assembly sequence information aids in minimizing changeover times between different production runs. By sequencing products to minimize component changeovers, manufacturers can reduce downtime and increase output.
- Optimal Batch Sizes: The BOM helps in determining optimal batch sizes for production. Manufacturers can adjust batch sizes based on the quantities of components required, minimizing setup costs and reducing waste.
- Scheduling Flexibility: The BOM allows production managers to explore different scheduling scenarios. By adjusting quantities, production rates, or sequencing, they can assess how changes impact the production timeline and make informed decisions.
- Communication and Coordination: The BOM serves as a common reference point for various departments involved in production, such as manufacturing, procurement, and engineering. This facilitates effective communication and coordination, ensuring that everyone is aligned with the production schedule.
In summary, a Multi-Level BOM is a valuable tool for creating efficient and well-structured production schedules. It provides insights into assembly sequences, time estimates, and resource requirements, enabling production managers to optimize resource allocation, reduce idle time, and ensure that manufacturing operations run smoothly and on schedule.
Design Changes and Engineering
In the context of manufacturing, design changes, and engineering modifications are common occurrences that can significantly impact the production process. A Multi-Level Bill of Materials (BOM) plays a crucial role in managing these changes and ensuring that they are effectively communicated and implemented.
Here's an elaboration on how a Multi-Level BOM contributes to managing design changes and engineering modifications:
- Change Impact Assessment: When design changes are proposed, the Multi-Level BOM provides a comprehensive view of the product's structure and components. Manufacturers and engineers can assess the potential impact of the proposed changes on various levels of the BOM. This helps in understanding how modifications will ripple through the entire assembly process.
- Documentation and Version Control: The BOM serves as a historical record of the product's design and its various revisions. Each version of the BOM corresponds to a specific design iteration. This documentation helps in tracking changes over time and maintaining an organized record of design revisions.
- Cross-Functional Collaboration: Design changes often involve collaboration between different departments, such as engineering, manufacturing, and procurement. The BOM provides a shared reference point that allows teams to collaborate effectively, ensuring that all stakeholders are aware of the changes and their implications.
- Change Requests and Approvals: The BOM is used to document change requests and approvals. Design changes can be proposed, reviewed, and approved within the context of the BOM, ensuring that all relevant parties are informed and involved in the decision-making process.
- Visualization of Changes: The BOM's hierarchical structure and indented format make it easy to visualize the impact of design changes. Manufacturers can see how modifications affect different levels of the assembly and identify any potential conflicts or challenges.
- Supply Chain Coordination: Design changes may require adjustments in the procurement of components and materials. The BOM helps procurement teams understand which components are affected and provides accurate information for updating orders and communicating changes with suppliers.
- Cost Estimation and Control: Design changes can impact costs, including material costs, labor requirements, and production time. The BOM assists in estimating the cost implications of proposed changes, enabling manufacturers to make informed decisions that align with budgetary constraints.
- Production Process Alignment: The BOM ensures that the production process is aligned with the updated design. It helps production managers and operators understand how the changes affect the assembly sequence, reducing the risk of errors during manufacturing.
- Quality Assurance and Compliance: When design changes are made, the BOM can be updated to reflect any new quality standards or regulatory requirements. This ensures that the manufacturing process remains compliant with industry regulations.
- Historical Reference: The BOM serves as a historical reference for design decisions and changes. It allows manufacturers to trace the evolution of the product's design, facilitating future design iterations and improvements.
- Efficient Implementation: With the BOM as a reference, design changes can be implemented more efficiently. Manufacturers can identify the specific components, subassemblies, and processes that need to be modified, streamlining the implementation process.
In summary, a Multi-Level BOM is a vital tool for managing design changes and engineering modifications in manufacturing. It provides a structured and detailed representation of the product's components and their interrelationships, helping manufacturers, engineers, and other stakeholders effectively navigate and communicate changes throughout the production process.
Traceability and Compliance
Traceability and compliance are critical aspects of manufacturing, especially in industries where strict quality standards and regulatory requirements must be met. A Multi-Level Bill of Materials (BOM) plays a significant role in ensuring traceability and compliance throughout the production process.
Here's an elaboration on how a Multi-Level BOM contributes to traceability and compliance in manufacturing:
- Component Origins: The BOM provides a detailed breakdown of all components and materials required for the final product. This information helps manufacturers trace the origin of each component, ensuring that they come from approved and reputable suppliers.
- Supplier Verification: Manufacturers can cross-reference the BOM with supplier documentation to verify that components are sourced from trusted suppliers who meet quality and compliance standards.
- Material Certifications: The BOM can include information about material certifications, such as safety, environmental, and regulatory certifications. This ensures that materials used in production comply with industry-specific requirements.
- Quality Control Documentation: The BOM serves as a reference for quality control processes. Manufacturers can document inspection and testing procedures for each component and subassembly listed in the BOM, ensuring that quality standards are upheld.
- Change Control: The BOM documents design changes and engineering modifications. Manufacturers can ensure that changes are compliant with relevant regulations and that necessary approvals are obtained before implementation.
- Regulatory Reporting: In industries subject to regulatory oversight, the BOM provides the necessary information for regulatory reporting. Manufacturers can demonstrate compliance by providing detailed documentation of components, materials, and production processes.
- Batch and Lot Tracking: The BOM aids in batch and lot tracking, allowing manufacturers to trace components back to their specific batches or lots. This is crucial for identifying and addressing issues related to quality, safety, or recalls.
- Recall Management: In the event of a product recall, the BOM helps manufacturers quickly identify the affected components and products. This facilitates the efficient removal of defective products from the market and minimizes the potential impact on consumers.
- Documentation for Audits: During audits or inspections, the BOM serves as a comprehensive source of information about the product's composition, production processes, and compliance with regulations. Auditors can review the BOM to assess adherence to industry standards.
- Supplier Collaboration: The BOM can be shared with suppliers to ensure they understand the compliance requirements for the components they provide. This collaborative approach helps maintain a consistent focus on compliance throughout the supply chain.
- Continuous Improvement: The BOM supports continuous improvement efforts by documenting lessons learned from previous compliance challenges or issues. This information can be used to implement corrective actions and prevent future non-compliance.
- Environmental and Sustainability Compliance: Manufacturers can use the BOM to track environmentally sensitive materials and ensure compliance with sustainability standards and initiatives.
In summary, a Multi-Level BOM enhances traceability and compliance in manufacturing by providing a comprehensive and structured record of product components, materials, processes, and design changes.
It helps manufacturers meet regulatory requirements, uphold quality standards, and maintain transparency throughout the production lifecycle. This contributes to product safety, consumer confidence, and overall operational excellence.
Collaboration and Communication
Collaboration and communication are vital elements in manufacturing operations, involving coordination among various departments and stakeholders to ensure a smooth and efficient production process. A Multi-Level Bill of Materials (BOM) serves as a central reference point that facilitates effective collaboration and communication.
Here's an elaboration on how a Multi-Level BOM contributes to collaboration and communication in manufacturing:
- Shared Reference: The BOM provides a standardized and comprehensive representation of the product's structure, components, and assembly sequence. It serves as a shared reference that all teams and departments can use to understand the product's composition and requirements.
- Cross-Functional Teams: Different departments, such as engineering, manufacturing, procurement, quality control, and logistics, are involved in the production process. The BOM enables cross-functional collaboration by presenting a unified view of the product that all teams can access and work from.
- Design Intent Clarification: The BOM helps communicate the design intent to all stakeholders. Engineers can create detailed BOMs that convey how components fit together, aiding in the understanding of the product's functionality and assembly process.
- Change Management: When design changes or modifications are proposed, the BOM serves as a platform for discussing, documenting, and implementing those changes. It ensures that all relevant teams are aware of the proposed modifications and their impact.
- Design Review and Feedback: Engineers, designers, and other stakeholders can collaborate using the BOM to review and provide feedback on product designs and changes. This iterative process helps refine designs and ensure alignment with manufacturing and assembly considerations.
- Supplier Collaboration: Sharing the BOM with suppliers enhances collaboration by providing clear information about component requirements and specifications. Suppliers can better understand what is needed, leading to smoother procurement processes.
- Real-time Updates: With a digital BOM management system, updates and modifications to the BOM can be made in real time. This ensures that all stakeholders have access to the latest information, reducing the risk of miscommunication due to outdated documents.
- Conflict Resolution: The BOM helps in resolving conflicts or discrepancies that may arise during the production process. Teams can refer to the BOM to identify the source of the issue and work collaboratively to find solutions.
- Training and Onboarding: The BOM serves as a training resource for new employees and team members. It helps them understand the product's structure, assembly process, and the roles of different components.
- Project Management: The BOM supports project managers in coordinating tasks, tracking progress, and ensuring that all teams are aligned with the project's goals and timelines.
- Communication with Customers: In some cases, customers may require information about the product's components or assembly process. The BOM can be shared with customers to provide transparency and build trust.
- Remote Collaboration: In the age of remote work and distributed teams, a digital BOM can be accessed and updated by team members from various locations, fostering seamless collaboration regardless of physical distance.
In summary, a Multi-Level BOM serves as a powerful communication tool that fosters collaboration among different departments, suppliers, and stakeholders involved in the manufacturing process.
It promotes transparency, shared understanding, and effective coordination, leading to improved product quality, efficiency, and successful project outcomes.
Continuous Improvement
Continuous improvement is a fundamental principle in manufacturing that involves consistently seeking ways to enhance processes, products, and operations. A Multi-Level Bill of Materials (BOM) plays a vital role in supporting continuous improvement initiatives within a manufacturing organization.
Here's an elaboration on how a Multi-Level BOM contributes to continuous improvement in manufacturing:
- Process Optimization: The BOM provides insights into the assembly sequence and production processes. Manufacturers can analyze this information to identify bottlenecks, inefficiencies, and areas for process optimization. By streamlining workflows, manufacturers can reduce cycle times and improve overall productivity.
- Root Cause Analysis: When issues or defects arise in the production process, the BOM helps trace back to the source of the problem. Manufacturers can pinpoint which components, subassemblies, or processes are contributing to the issue and take corrective actions.
- Performance Metrics: The BOM serves as a baseline for measuring key performance indicators (KPIs) related to production efficiency, quality, and cost. Manufacturers can track KPIs over time and use the BOM to evaluate the impact of improvement initiatives.
- Design Iteration: Engineers can use the BOM to identify opportunities for design improvements. By analyzing the performance and functionality of components, engineers can suggest design changes that enhance product quality and performance.
- Waste Reduction: The BOM helps manufacturers identify areas of waste in terms of excess materials, overproduction, and inefficient processes. By targeting these areas, manufacturers can implement strategies to reduce waste and optimize resource utilization.
- Supplier Collaboration: Continuous improvement extends beyond the manufacturing facility to suppliers. The BOM can be shared with suppliers to discuss potential enhancements in component quality, performance, or cost.
- Lean Manufacturing: The BOM supports the principles of lean manufacturing by highlighting non-value-added components, steps, or processes. Manufacturers can focus on eliminating waste and maximizing value throughout the production process.
- Kaizen Events: Manufacturers can use the BOM as a reference during Kaizen events, which are focused improvement workshops. Teams can analyze the BOM to identify improvement opportunities and implement changes in a structured manner.
- Quality Control: The BOM aids in implementing quality control measures. Manufacturers can establish inspection points, quality checks, and testing protocols based on the BOM data to ensure consistent product quality.
- Supplier Performance Evaluation: By tracking the performance of suppliers and comparing it with the BOM requirements, manufacturers can assess whether suppliers meet quality and delivery expectations. Continuous improvement efforts can extend to supplier relationships.
- Feedback Loop: The BOM serves as a feedback loop for gathering insights from production teams. Operators and technicians can provide feedback on component fit, assembly challenges, and potential improvements based on their experience with the BOM.
- Innovation: The BOM can inspire innovation by highlighting opportunities for introducing new materials, technologies, or processes that enhance product performance or reduce costs.
In summary, a Multi-Level BOM is a valuable tool for driving continuous improvement in manufacturing. It enables manufacturers to identify inefficiencies, address quality issues, optimize processes, and collaborate with stakeholders to enhance overall operations.
By leveraging the insights provided by the BOM, manufacturers can foster a culture of continuous improvement that leads to increased competitiveness, customer satisfaction, and operational excellence.
How Can Deskera Help You with a Multi-Level Bill of Materials?
Deskera MRP is an integrated software solution designed to help businesses manage their manufacturing processes, including multi-level bills of materials.
Here’s how Deskera can assist you with the multi-level bill of materials:
- Multi-Level BOM Creation and Management: Manage product structures with ease using the multi-level bill of materials. Assign multiple components to a single product. Identify components and subcomponents of each product, and easily track their usage, movement, and costs.
- Improve Productivity: Deskera will help you improve productivity because it facilitates the automatic generation of bills of materials, thereby helping to reach your production goals faster. It also automates the process of managing and maintaining multi-level bills of materials.
- Enhances Collaboration: By increasing the visibility and communication between the departments of your company, Deskera will help improve collaboration between different teams. In fact, it also allows multiple users to access and edit the bill of materials. All of this will also facilitate faster and more informed decision-making.
- Improve Inventory Costs: With Deskera, you will be able to improve your inventory costs as the accuracy of data with a single source of truth for the entire bill of materials is ensured. Through Deskera, all the required documents can be automatically generated from this single source of information. Lastly, through the automatic generation of a bill of materials, manual errors will be reduced.
- Reduce Production Costs: By streamlining the process of the bill of materials through Deskera, operation costs will be reduced. In fact, the time and resources spent on managing and updating complex bills of materials will also be reduced.
Key Takeaways
In the intricate realm of manufacturing, the Multi-Level Bill of Materials emerges as an indispensable tool that orchestrates the harmony of components, processes, and people.
Thus, the 10 ways in which multi-level BOM plays a crucial role in manufacturing are:
- Product Structure Clarity: A Multi-Level BOM provides a clear and detailed breakdown of the product's components, subassemblies, and raw materials. This hierarchy allows manufacturers to understand how all the parts fit together to create the final product. It's like a blueprint that helps visualize the entire manufacturing process.
- Accurate Resource Planning: By specifying quantities and types of components required at each level, a Multi-Level BOM assists in accurate resource planning. Manufacturers can determine the exact amount of materials needed, allocate labor and machinery resources, and schedule production tasks more efficiently.
- Inventory Management: Multi-Level BOMs aid in effective inventory management. Manufacturers can track the quantities of each component and sub-assembly required, helping to avoid shortages or excess stock. This leads to optimized inventory levels and reduces carrying costs.
- Procurement Efficiency: When manufacturers have a clear understanding of the components needed for production, they can streamline procurement processes. They can order materials in the right quantities and at the right times, minimizing lead times and ensuring a smooth production flow.
- Cost Estimation and Control: Multi-Level BOMs contribute to accurate cost estimation. Manufacturers can calculate the costs associated with each component, subassembly, and process involved in production. This helps in setting competitive prices, budgeting, and controlling expenses.
- Production Scheduling: Multi-Level BOMs provide insights into the sequence of assembly operations required to build the final product. This information aids in creating production schedules, optimizing production lines, and reducing production bottlenecks.
- Design Changes and Engineering: When product designs change, the Multi-Level BOM is updated accordingly. This ensures that all departments, including engineering, manufacturing, and procurement, are aligned and aware of any modifications. It helps prevent errors, reduces rework, and ensures that the updated design is accurately reflected in production.
- Traceability and Compliance: In industries with stringent regulatory requirements, Multi-Level BOMs aid in traceability. Manufacturers can track the origin and history of each component, ensuring compliance with quality standards and regulatory guidelines.
- Collaboration and Communication: A Multi-Level BOM serves as a common reference point for various teams involved in the manufacturing process. Designers, engineers, production managers, and procurement specialists can collaborate effectively based on a shared understanding of the product structure.
- Continuous Improvement: Multi-Level BOMs support continuous improvement initiatives. By analyzing the BOM and production processes, manufacturers can identify opportunities for efficiency gains, waste reduction, and quality enhancement.
In essence, a Multi-Level BOM is the backbone of manufacturing operations. It empowers manufacturers to plan, execute, and optimize production processes with precision. Its role extends beyond a mere list of parts; it acts as a strategic tool that aligns various functions within a manufacturing organization, contributing to overall operational excellence and successful product delivery.
Thus, by harnessing the power of the Multi-Level BOM, manufacturing organizations can navigate the complexities of production with confidence. With every component, assembly, and decision intricately woven into its fabric, the BOM empowers manufacturers to orchestrate their processes, optimize their resources, and deliver products of the highest quality. In embracing the crucial role of the Multi-Level BOM, manufacturers chart a course toward success in an ever-evolving manufacturing landscape.
Overall, Deskera MRP will serve as a comprehensive solution for managing multi-level bills of materials. It will help streamline your bill of materials, automate production processes, track production costs, monitor supplier performance, improve supply chain management, streamline production planning, reduce inventory errors, optimize production scheduling, track production costs, and help you maximize efficiency with the multi-level bill of materials.
Related Articles
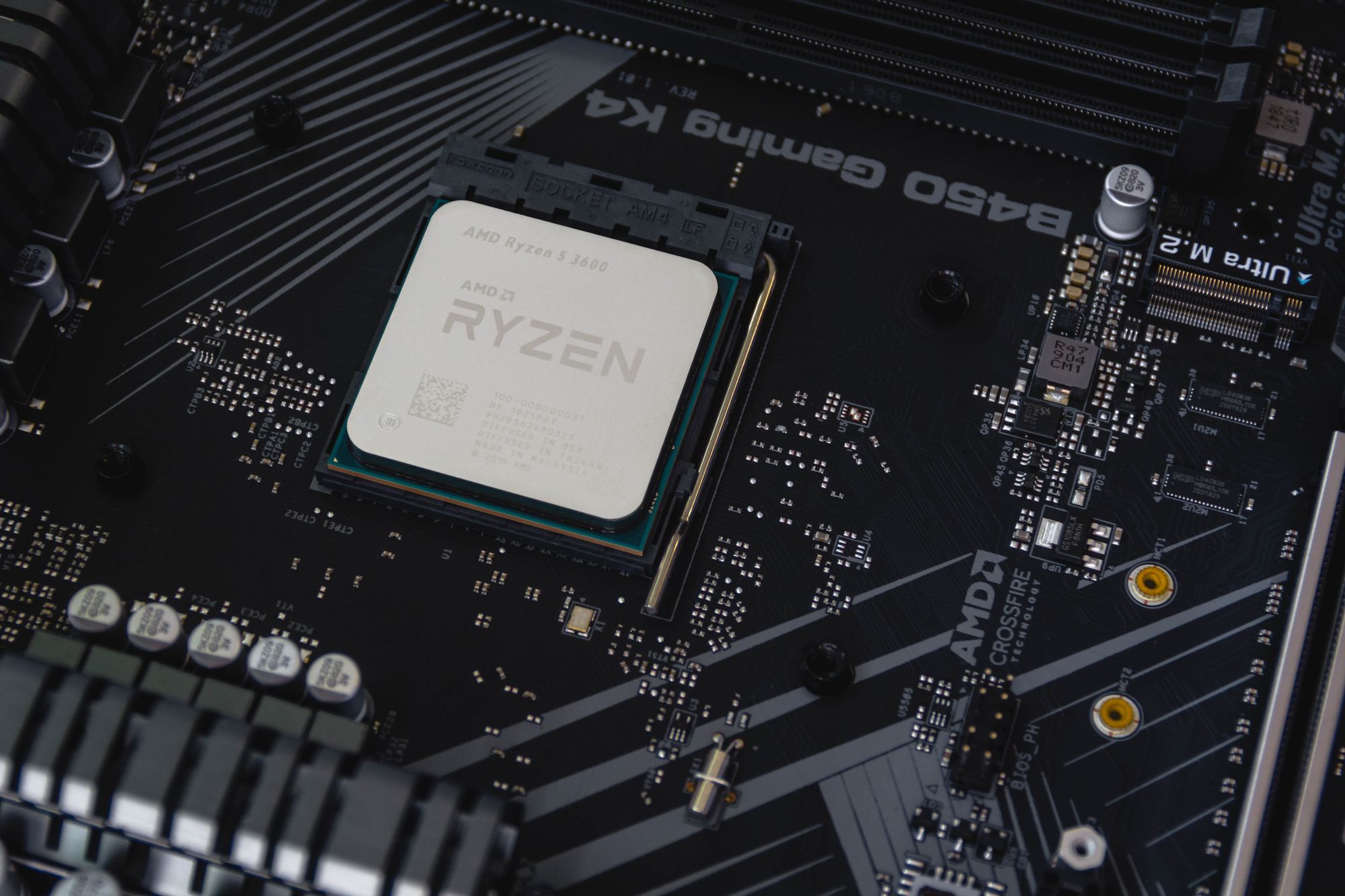
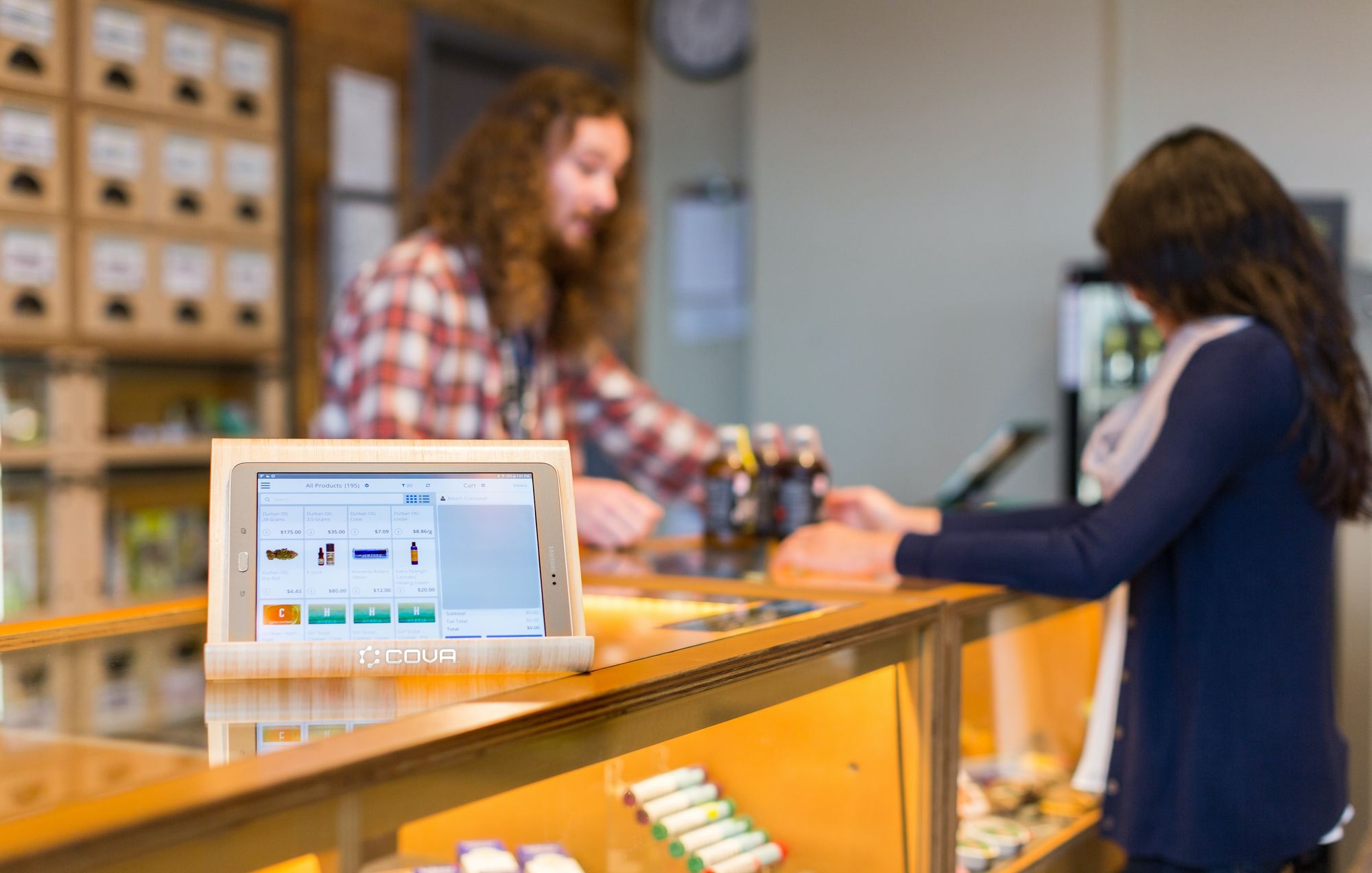
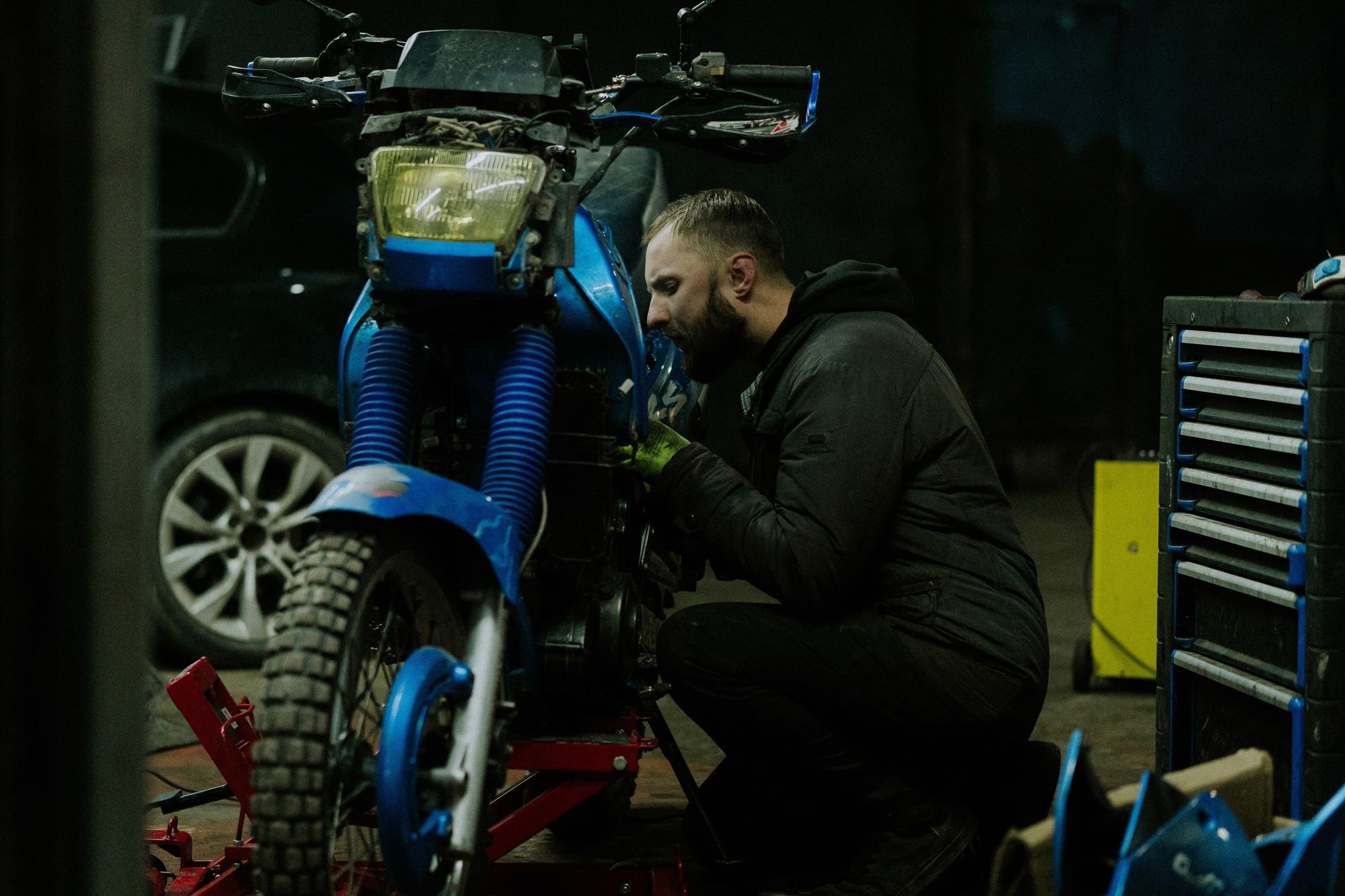
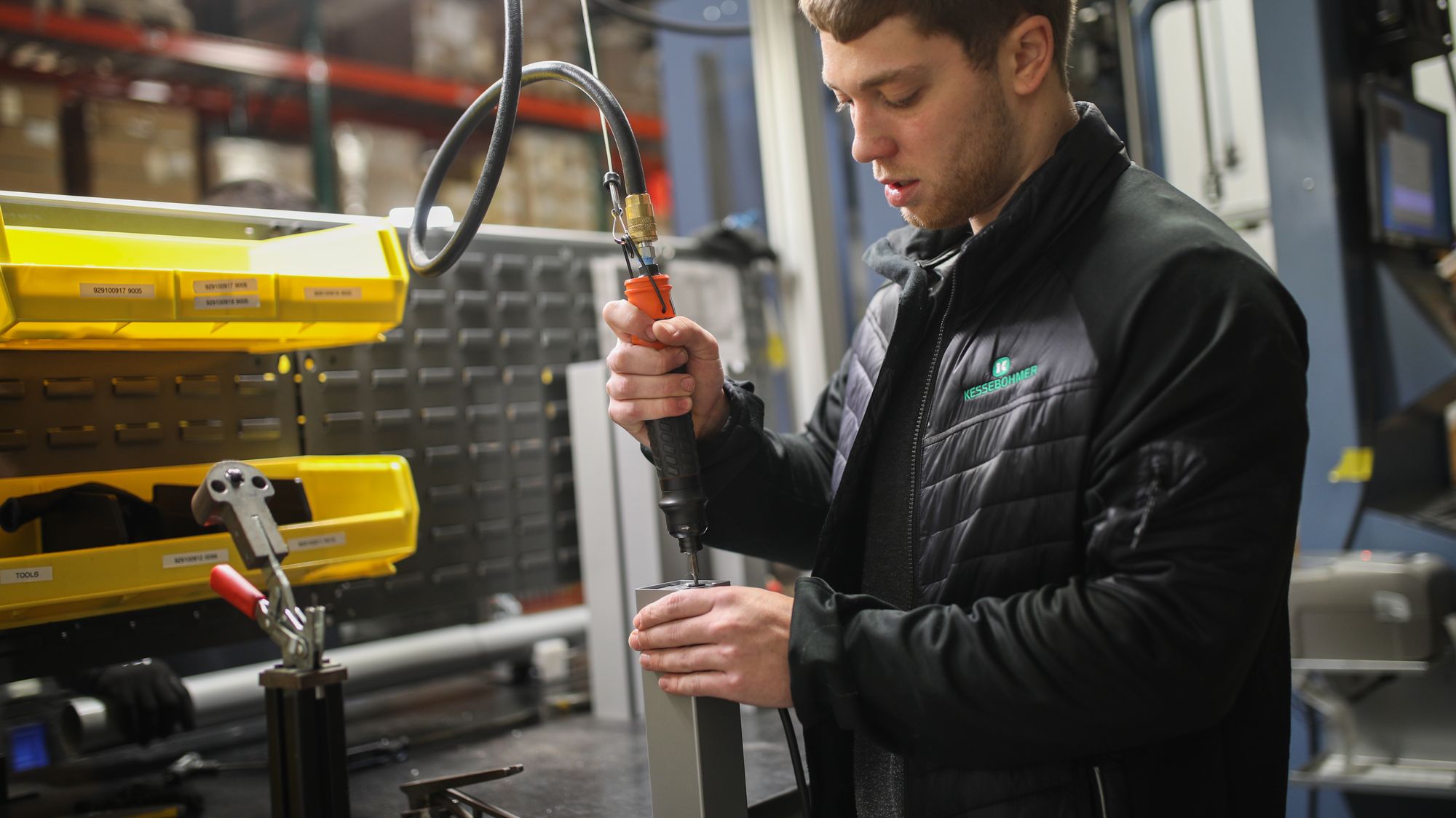
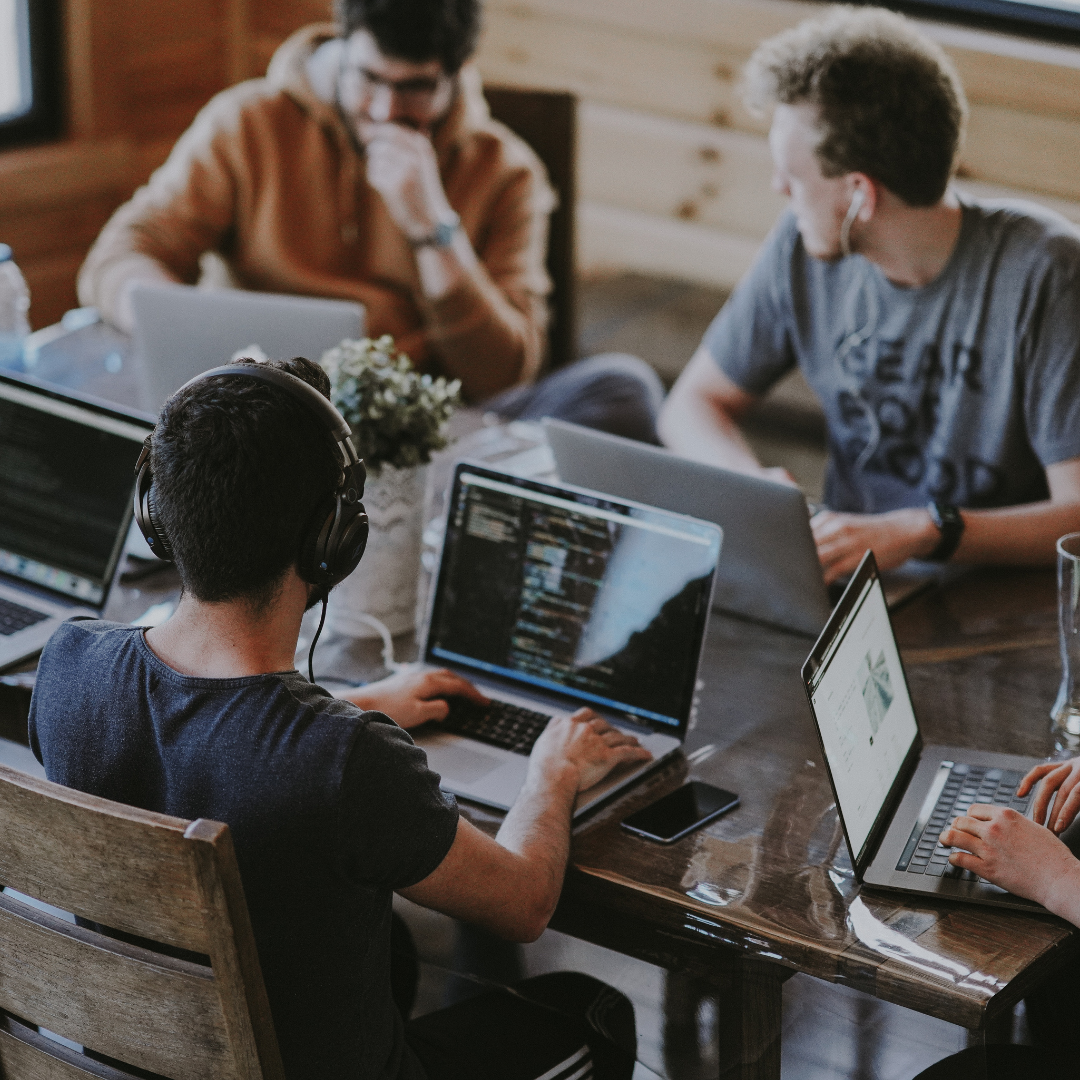