Avoiding expenses related to late deliveries improves a manufacturer's financial success. Running a business requires proper understanding of how long a task will take to finish.
A manufacturer can improve its production procedures, increase profits, or boost its productivity to achieve this goal by knowing the company's throughput time.
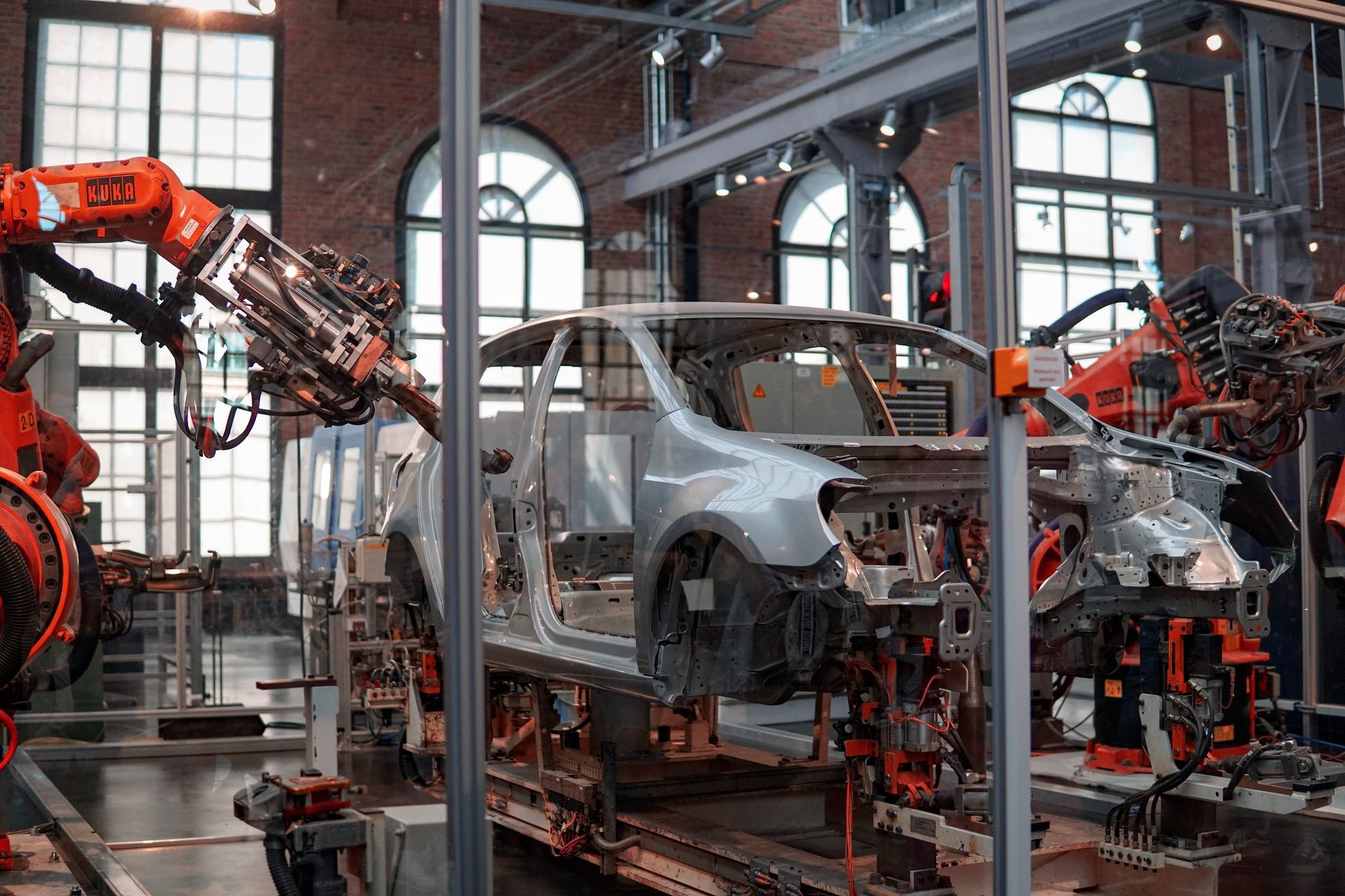
For daily tasks, long-term projects, and industrial processes alike, knowledge is power. As your understanding of your processes grows, monitoring waste becomes easier. One way to achieve any logistics goals is to speed up the rate at which a work-in-progress goes through the production stages which can be done through throughput time.
To calculate the throughput time, manufacturers use a throughput efficiency formula. To help you thrive in the manufacturing sector, we define throughput time in this post, outline its advantages, and go over how to calculate it.
Following are the topics covered:
- What Is Throughput Time?
- Why Is Throughput Time Analysis Important?
- How to Use Throughput Time to Assess the Performance?
- How to Increase Throughput?
- Throughput Time Vs Cycle Time
- Throughput Time Vs Response Time
- Throughput Time Vs Lead Time
- Throughput Time in Manufacturing
- Throughput Time in IT
- Key Takeaways
What Is Throughput Time?
In the business world, throughput refers to the quantity of a product or service that a business can produce and provide to a customer within a defined time frame taking into account all processes, inspections, transport, and wait times.
The expression is used to describe a company's production rate or how something is processed. Because high throughput suggests that a company can provide a good or service more effectively than its rivals, businesses with high throughput levels can steal market share from their lower throughput peers.
- The concept of throughput is included in the theory of limitations.
- This idea is based on the axiom that any link in a chain can only be as strong as its weakest counterpart.
- Business managers want to maximize throughput for the product's consumers while minimizing the negative effects of the weakest connections on a business's ability to succeed.
- After maximizing throughput and removing inefficiencies to allow inputs and outputs to flow in the most efficient manner, a business can maximize revenue.
- Production capacity and throughput are linked, and management may assume different things about capacity.
- Although even if the management is using theoretical capacity, this level of capacity cannot be attained if the business anticipates uninterrupted output.
No industrial process can ever function at maximum production since machinery needs to be maintained and repaired as well as because employees require vacation time. Using practical capacity, which takes into account machine repairs, wait times, and holidays is more realistic for enterprises.
Throughput Time Formula
Throughput can be calculated using the following formula:
T = I/F
where:
- T = Throughput
- I = Inventory (the number of units in the production process)
- F = The time the inventory units spend in production from start to finish
The four steps of the manufacturing process—process time, inspection time, move time, and wait time—are added to determine a product's throughput time.
- The process time is the period of time required by the business to generate the product.
- The finished product has to be examined.
- The product then needs to be transported to a storage facility until it is ready to ship because the majority of businesses don't send products right away after they are inspected.
- The item can be taken out of storage and transported to the purchaser once it is ready for sale.
- It should be noted that the process time is the process that is considered value-added time in the throughput time calculation.
- Only this process results in a finished good.
- The rest of the time is wasted on administrative and logistical tasks.
Because increasing expenses from non-value-added time diminish profit margins on otherwise profitable products, lean factories use the throughput calculation to cut non-value-added time. Cycle efficiency is the most common term for reducing non-value-added time.
Why Is Throughput Time Analysis Important?
Throughput time analysis is crucial because it enables businesses to understand how the amount of time spent producing goods affects their total revenue. Businesses can use it to assess whether their production is at its most effective level.
A business may be aware that it needs to find ways to make its manufacturing processes more effective if its throughput time falls short of its goals. The term "throughput time" describes the total amount of time needed to complete a specific process from beginning to end.
For instance, a manufacturer can determine how long it takes to make a product, from the time the customer places the initial order to the time the product is manufactured and sold.
The benefits of understanding throughput time are as follows:
- Understanding throughput time helps manufacturing companies determine what is required to meet demand. This could result in more work, more shifts, or the need to buy new tools.
- Throughput time aids in the management of inventory and the supply chain.
- This can assist in negotiating bulk raw material contracts, planning precise deliveries for businesses adopting Just-in-Time (JIT) production processes, or staggering supplies to enhance cash flow and manage warehouse space and associated holding costs.
- By managing their workflow and enhancing manufacturing efficiency, firms can benefit from an understanding of throughput time.
- Manufacturing managers can aim to cut down on inspection, line, and waiting times and improve those for the process by utilizing tried-and-true continuous improvement approaches.
- They can combine these techniques with adaptable and agile MRP and ERP software to automate the processes and reflect them in Bills of Material (BOM), freeing them up to take on more improvement projects.
- Knowing your throughput time will help you determine other business processes including throughput efficiency, net profit, and the worth of your company's assets.
- Once your calculations are complete, you can check them over time and establish benchmarks for your throughput by comparing them to similar businesses in your industry.
- This gives you the opportunity to change your manufacturing procedures so that you can achieve and keep up your ideal throughput rates.
Determining a company's total throughput rate, also known as flow time, is a crucial step in maximizing profitability and a workflow that is effective in the operations management and business senses.
Here are explanations for why a company could perform a throughput calculation:
Knowing your production process- Throughput rate can help you create a manufacturing style that is as efficient as possible, which promotes lean manufacturing. A lesser unit of time spent on any one product equals less time spent on all items put together.
Once all inefficiencies have been removed, the manufacturing process will run more quickly and with fewer delays and moving parts.
Getting rid of bottlenecks- A good technique to spot locations where manufacturing processes are getting backed up is to know how long it takes for a current production process to proceed from work-in-process to completion.
Only if you are aware of your manufacturing throughput time can you remove these obstacles. When you take care of them, you'll be better able to prepare your goods in advance rather than before delivery.
To cut back on operating costs- Your operating costs can be reduced if your items undergo less processing time. When the lead time for design and production shortens, less money may need to be spent on unneeded extra labor, materials, and other costs.
Getting rid of inefficiencies- Calculating how long it takes to turn your raw materials into the number of units you need to sell can reveal portions of your process that aren't running at their full potential.
- You need to speed up the inspection process or boost production efficiency elsewhere. But, removing this form of downtime can cut down on needless product latency.
- Maintaining your throughput time benchmark will usually result in greater efficiency.
- Efficiency in business terms refers to a company's capacity to use its resources to the fullest extent possible.
- The ability to generate large quantities of inventory while lowering labor costs and raising product quality is made possible by optimal throughput times.
- You may run your firm more by optimizing the return on your resources, such as money and time.
Customer satisfaction- Long delivery delays for requested goods are one of the major sources of dissatisfaction for customers. Throughput time analysis identifies areas of the process that can be reduced, cutting down on the amount of time it takes to produce and distribute goods.
- A manufacturer's goal is to provide a vast quantity of high-quality items that meet the demands of its target market.
- You might be able to achieve this aim and keep your current customer base if you maintain a throughput time that works for your business.
- When people have a positive impression of your brand, they may spread the word about it and recommend your goods, which could lead to more people being your customers.
Inventory control- You may check how your production time compares to your inventory and established standards by tracking your throughput time.
You can establish an inventory benchmark by changing your manufacturing time and seeing if it results in more or fewer products in your inventory.
You might think about implementing your throughput rates as a business standard once you discover the right mix between cutting down wasteful time and minimizing product faults.
Increased profitability- By speeding up throughput, producers can produce more goods in a shorter amount of time. As a result, companies are able to lower their production costs, which increases profitability.
Competitive advantage- You can make sure you're placing as many of your products on the market as you can at the most profitable prices for your business by boosting your throughput time and inventory production.
- By keeping your business procedures as efficient as possible, you may reduce waste and labor costs, which could lead to higher profits or more aggressive marketing.
- These advantages can help you outpace existing rivals and protect your business from potential market entrants.
- Company managers can address bottlenecks, slowdowns, and backlogs to increase productivity if they can spot these areas. Faster throughput times boost profitability and return on investment (ROI).
How to Increase Throughput?
Company managers should strive to increase throughput while reducing throughput time. As a result, there are several approaches to assist in achieving this goal. One is to put in place technologically facilitated real-time monitoring and data analysis of production operations.
- Throughput analysis software can immediately spot slowdowns or other irregularities so that they can be fixed.
- Using a standardized checklist of procedures that must be completed each time is another tried-and-true technique.
- While adhering to a checklist can speed up operations and drop errors, it may appear tiresome and unnecessary at first.
- Using a scorecard to create some friendly rivalry among employees, where speed and efficiency are rewarded and inefficiency is identified as a problem area, is a strategy that is employed by businesses across a variety of industries.
Avoid Operating Bottlenecks
One of the most effective ways to increase throughput in data-driven manufacturing is to examine the current operational and production processes for potential bottlenecks.
- Manufacturers can then work to remove that bottleneck to prevent delays, wastage, and losses.
- Manufacturers come up with ways to streamline a lengthy process queue to make it more effective, or they might even do away with the process altogether and adopt a new one.
- The best option depends on many variables, including available floor space, equipment replacement costs, current process flow, potential dangers, etc.
Use Automatic Manufacturing Techniques
Manual tasks always have a high risk of human errors with high production and supply chain costs, time involved, and a compromise on quality to a great extent. Often, having the right tool for the job can have a massive impact on productivity.
- Manufacturers may increase final throughput and enhance the quality of the product and working conditions by automating manufacturing procedures.
- Task automation makes it possible to achieve consistency in production, the required level of precision, and the avoidance of unforeseen risks.
- Equipment maintenance Regular, proactive equipment maintenance is necessary since machines on the shop floor are subject to wear and tear over time from heavy use and frequent downtime.
- This downtime can be decreased by keeping machinery and equipment well-maintained, which will help firms maintain their production process more steadily.
In the end, manufacturers shouldn't wait for equipment to malfunction. Instead, to avoid downtime brought on by equipment breakdown and repairs, the equipment should be maintained under a planned maintenance schedule.
Improve Manufacturing Safety
Losing crucial time to worker safety and accident prevention is the biggest roadblock to boosting manufacturing throughput. The just-in-time manufacturing process can be affected by an injured worker on the factory floor, which can also interrupt vital operational activity.
Worker and process safety is essential to prevent the following: the loss of a skilled and productive employee; temporary or permanent floor closures for thorough investigations into any incident; accidental insurance claims that may also be false; high insurance costs; and permanent equipment damage.
Optimize Workflow
As we've observed over the past few years, manufacturers have maintained their support for labor augmentation to enhance operator workflows and productivity.
Businesses can lessen the occurrence of quality errors brought on by human mistakes and also lessen any friction present within current production processes by using technologies like digital work instructions.
Limit Equipment Downtime
Equipment downtime may have a big impact on how quickly products are produced, thus it's crucial for manufacturers to select a solution that offers real-time downtime visibility so they can seek and receive support.
Predicting machine downtime can assist prevent delays in maintenance and instead use that time to increase manufacturing throughput.
How to Use Throughput Time to Assess the Performance?
The efficiency with which a business handles its supply chain, which is the relationship it has with its suppliers, also affects how much business it can process. Throughput is negatively affected when materials are not accessible as a manufacturing input, regardless of the cause.
Two items may start production using the same technique, in which case the shared expenses are divided among the two products. Yet, the goods are created utilizing different procedures until production reaches the split-off point. It is more challenging to maintain high throughput in this circumstance.
You can use the following steps to measure your operations' efficiency by calculating throughput time and other values:
1. Determine the throughput time
You can use the following calculation to determine throughput time:
Throughput time = Processing time + Inspection time + Move time + Queue time
2. Determine the throughput efficiency rate
Utilizing the formula below, you may calculate your throughput efficiency rate once you know your throughput time:
Throughput Efficiency rate = Inventory / Throughput time
3. Calculate ROI, net profit, and throughput
You can determine your throughput, net profit, and ROI to check the performance of your company after determining your throughput time and throughput efficiency rate. The throughput calculation formula is as follows:
Throughput = Revenue - Total Variable expenses
Following that, you can use that amount in the following method to determine the net profit of your business:
Net Profit = Throughput - Operating expenses
The following formula can then be used to determine the return on investment (ROI) for your business:
ROI = [(Total revenue - Total cost) / Total cost] x 100
Throughput Time Vs Cycle Time
Cycle Time Defined
Simply put, an object's cycle time is the length of time it takes it to move from position A to point B. This can be the period of time that passes between the initial introduction of a raw product into a machine and the moment when the completed part or product exits the machine.
Cycle time can be stated in a variety of ways, including:
Effective cycle time- The period of time needed to complete a cycle, including the load and unload times, applied switching times, and processing times for each item.
It could be argued that speeding up the procedure is the only method to reduce cycle time. But, it's likely that flaws would worsen, which could result in time being wasted through recycling.
How does Cycle Time Affect Throughput?
The quantity processed or generated within a given time frame is known as the throughput.
It can be used to calculate machine throughput for a single component of the final product or for a more thorough calculation of the full finished product from beginning to end, such as N number of screws produced during X period or Y finished screws produced during Z period.
- This can also be an estimation of the amount of time needed to receive raw materials, convert them into a product, then prepare that product for shipping.
- Calculations involving granularity or mass can be done using throughput. But it is, simply put, the number of units in a certain period of time. The duration is given in hours or minutes.
Throughput volume can also be stated in a variety of ways, depending on its application:
- Theoretical throughput is the highest throughput achievable if the machinery is operating at top efficiency and producing only high-quality parts.
- Total throughput is the sum of all units, including scrap, rework, and good units, that move through the process. This number illustrates the potential for increasing output volume by raising quality.
The amount of good units that pass through the operation within a predetermined time frame is known as effective or actual throughput. Due to the fact that only high-quality items may be supplied to clients, this number shows the processes' capacity to meet customer demand. But, cycle time and throughput time are correlated.
Advantages of Cycle Time
Standardization- Your production rate is predictable and simple to plan around with a consistent cycle time.
Maintaining an edge over the competition- By monitoring your cycle time and making modifications to stay ahead of the curve, you can outperform your rivals.
Identification of required adjustments- By examining your cycle time, you may be able to identify inefficiencies that can be enhanced.
Improved project scoping accuracy- You can provide your consumers with more precise estimations if you are aware of your cycle time.
Throughput Time Vs Response Time
Response time and throughput are related. The average transaction's response time often decreases as total throughput increases.
- By devoting an excessive amount of resources to a single query, you might reduce the response time for that query at the price of total throughput.
- By limiting the resources that the database allots to a huge query, you can maintain total throughput.
- When you attempt to strike a balance between the continual need for high transaction throughput and the urgent need to execute a sizable decision-support query, the trade-off between throughput and response time becomes clear.
- The greater the impact your query can have on transaction throughput, the fewer resources you have available to execute transactions after applying more resources to the query.
- The query will run more the fewer resources you give it.
Throughput Time Vs Lead Time
Lead Time- Lead time refers to the amount of time between when clients make an order and when they actually receive the product they ordered.
- Customers are more satisfied when lead times are short because they don't have to wait too long to use your product.
- They'll tell their co-workers and acquaintances about your effectiveness, which can result in more people placing orders.
- Long lead times frustrate clients who might be concerned about the status of their orders.
- They might request payment for their wait time or cancel their order, which raises your cost.
- They won't hesitate to place another purchase from you and will criticize you for being ineffective to anybody who will listen.
Throughput Time- Throughput time indicates the amount of time that passes between the collection of raw materials and the completion of the finished product.
- Lead time is the promise to deliver the finished product to your client.
- The total throughput time for all your products, including both value and non-added-value processes, is calculated.
Lead time as well as throughput time are crucial indicators of operational effectiveness. The length of time between a client order and actual delivery is called lead time. In contrast, throughput time just counts the amount of time it takes for an item or service to be produced.
Teams will be able to verify that the modifications or enhancements they are making are yielding the desired results by tracking these metrics on a regular basis.
It will be possible to identify patterns for a team by tracking its throughput and cycle time on a monthly basis. Let's keep doing what we're doing if the average increases. If it decreases, either let's stop what we started doing or identify what changed during that time.
Throughput Time in Manufacturing
Manufacturing businesses strive to offer clients high-quality goods in a timely, economical manner. Manufacturing companies can assess throughput time how long it takes to do particular operations, which can help them better understand how their processes affect their income.
- Understanding how to assess your business' throughput time will help you decide whether your operations are at their best or whether there is room for improvement to boost earnings.
- The length of time needed for a product to move through a manufacturing process and change from raw materials to completed goods is known as the manufacturing throughput time.
- The idea also holds true when raw materials are transformed into components or subassemblies.
The duration needed for anything to complete a manufacturing process encompasses the following time periods from the point at which it first enters manufacturing until it exits manufacturing:
Processing Time- Processing time is the amount of time a machine is actually producing something. Processing time is the period during which raw materials are turned into finished goods.
This processing time includes blending, spinning, grinding, riveting, and countless other automated stages besides manual assembly.
Inspection Time- Inspection time is the total amount of time needed to check components, mixes, or sub-assemblies as they move through the production process since various commodities need varying levels of quality control.
This can involve both physical examination and automatic or electronic testing, including feel, stress testing, visual confirmation, and even things like taste and smell.
Move Time- While many factories are built with an eye toward optimizing product flow to cut movement and staging, other businesses could use older structures or eclectic space that necessitates a lot of staging and moving time for Work in Progress (WIP).
Move time must be measured and accounted for in throughput time regardless of the operation. This covers the time needed to travel between workstations, as well as the time it takes to move subassemblies or processed materials into and out of production areas.
Queue Time- Sometimes known as "wait time," is the period of time spent waiting before processing, inspection, and moving.
The idea of manufacturing throughput time is focused on reducing the amount of time needed for the production process so you may enhance the throughput flowing through your system and, as a result, increase profitability.
Net sales minus variable expenses is throughput. The majority of time spent in manufacturing is not in processing but rather in the inspection, transport, and queuing times. Thus, the quickest way to decrease manufacturing throughput time is to cut down as much as possible on inspection, move, and queue times.
Throughput Time in IT
The quantity of information units a system can handle in a specific period of time is known as throughput. It is used in systems ranging from organizations to different components of computer and network systems.
The rate at which a certain workload may be finished and reaction time, or the interval between a single interactive user request and receiving a response, are related measurements of system productivity.
Types of Throughput
Throughput has been used to compare the efficiency of large commercial computers that execute programs at once. The number of batch jobs finished in a day was an early indicator of throughput.
More modern approaches either presume a more complex mix of tasks or concentrate on a specific area of computer usage.
- A statistic for comparing the cost of raw computing over time or by the manufacturer is provided by terms like "trillion floating-point operations per second (TeraFLOPs or TFLOPS)".
- Throughput can be calculated using a benchmark.
- Network throughput in data transmission is the amount of data transferred from one location to another in a predetermined amount of time.
- It is measured in bits per second (bps), such as megabits per second (Mbps) or gigabits per second (Gbps).
Latency, Throughput, and Bandwidth
Latency, throughput, and bandwidth are three terms that are used in error.
Network bandwidth refers to the network's ability to carry a large amount of data at once, throughput indicates the volume of data, and latency denotes the pace at which data is transmitted. Together, throughput and latency show how well a network performs.
Throughput Vs Network Bandwidth
A wired or wireless network communications link's bandwidth is its ability to transport the most data possible via a computer network or internet connection in a specific period of time.
- Bandwidth is a synonym for capacity and refers to the speed of data movement.
- Contrary to popular belief, bandwidth does not represent the speed of a network.
- Modern network links have a higher capacity, which is often measured in millions of bits per second (megabits per second, or Mbps), or billions of bits per second (gigabits per second, or Gbps), as opposed to the old units of bandwidth (bps), which are used to describe bandwidth.
Throughput Vs Network Latency
The amount of time it takes for a data packet to go from one specified place to another is referred to as network latency.
Sending a packet that is returned to the sender and measuring the round-trip time is how latency is assessed in some situations. Latency should be as low as possible.
How Deskera Can Assist You?
Deskera is the One-Stop Platform for Managing Your Business. Get the advantages of ERP, Integrated Accounting, CRM, and HR Software for Business Growth — all in one place.
You can automate all the significant accounting tasks, including invoicing, expenses, and billing, with Deskera Books.
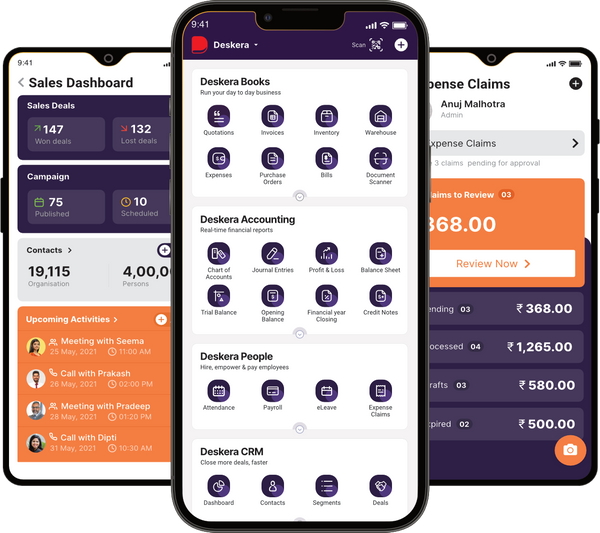
Deskera People is a specialized tool that simplifies the management of employee payroll, deductions, attendance, and leaves.
Deskera CRM is a platform that empowers you to drive better sales and close deals at lightning speed. It facilitates critical functions such as generating leads with emails, lead-generation landing pages, and amazing customer support.
Key Takeaways
- A crucial aspect of every industrial operation is throughput time. It gives businesses important business insight and a plan for where to focus on making changes.
- Throughput time is the amount of time, including lead time and processing time, that is needed for a product to complete a specific procedure from start to finish.
- The quantity of information units that may be processed in a given length of time is known as throughput in information systems. This metric was used for batch operations, but throughput time is now used in a wide range of tech-related contexts.
- Even businesses that are not engaged in the manufacture of goods need to understand the idea of throughput. For instance, it can be used to check how a business offers its clients services.
Related Articles
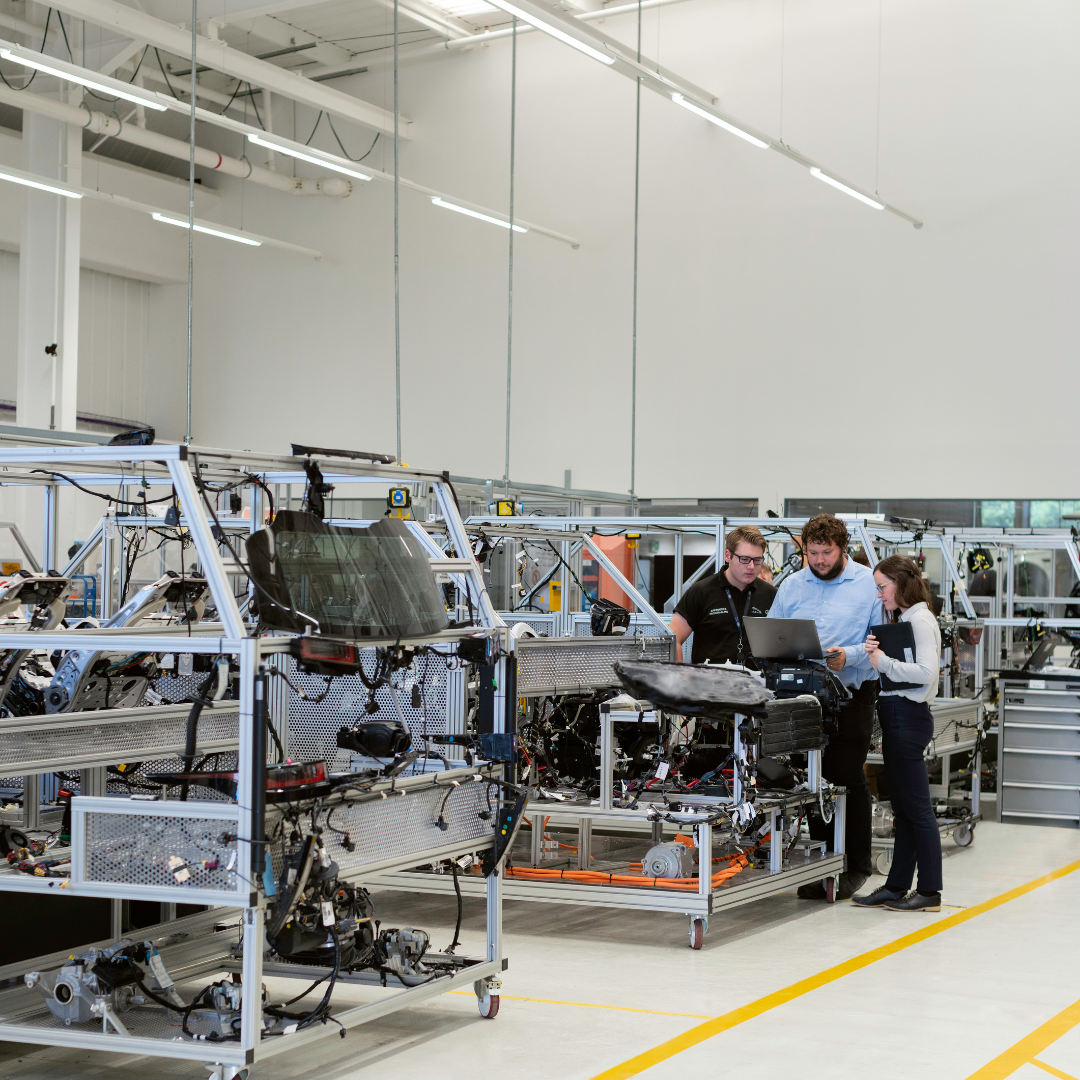
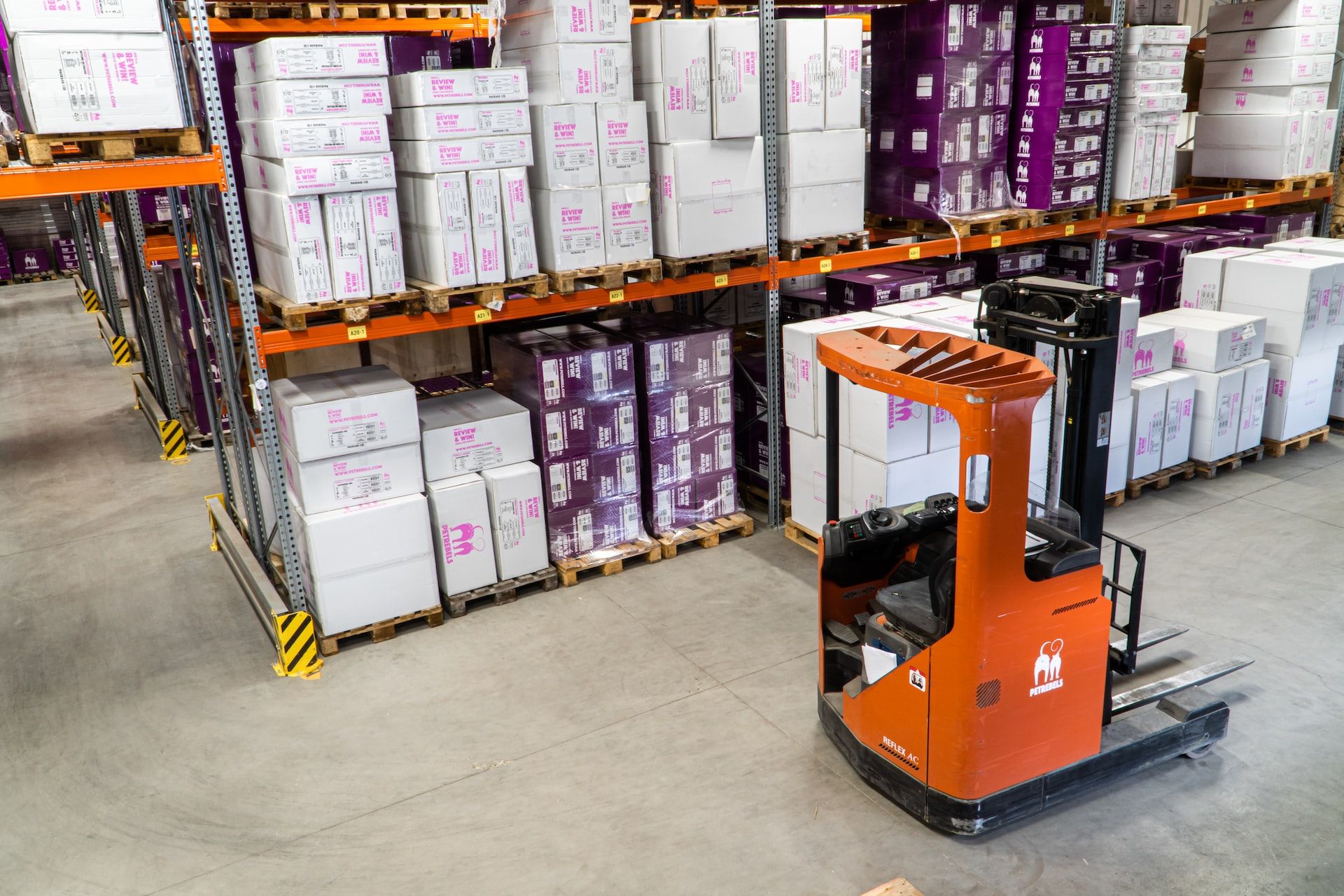
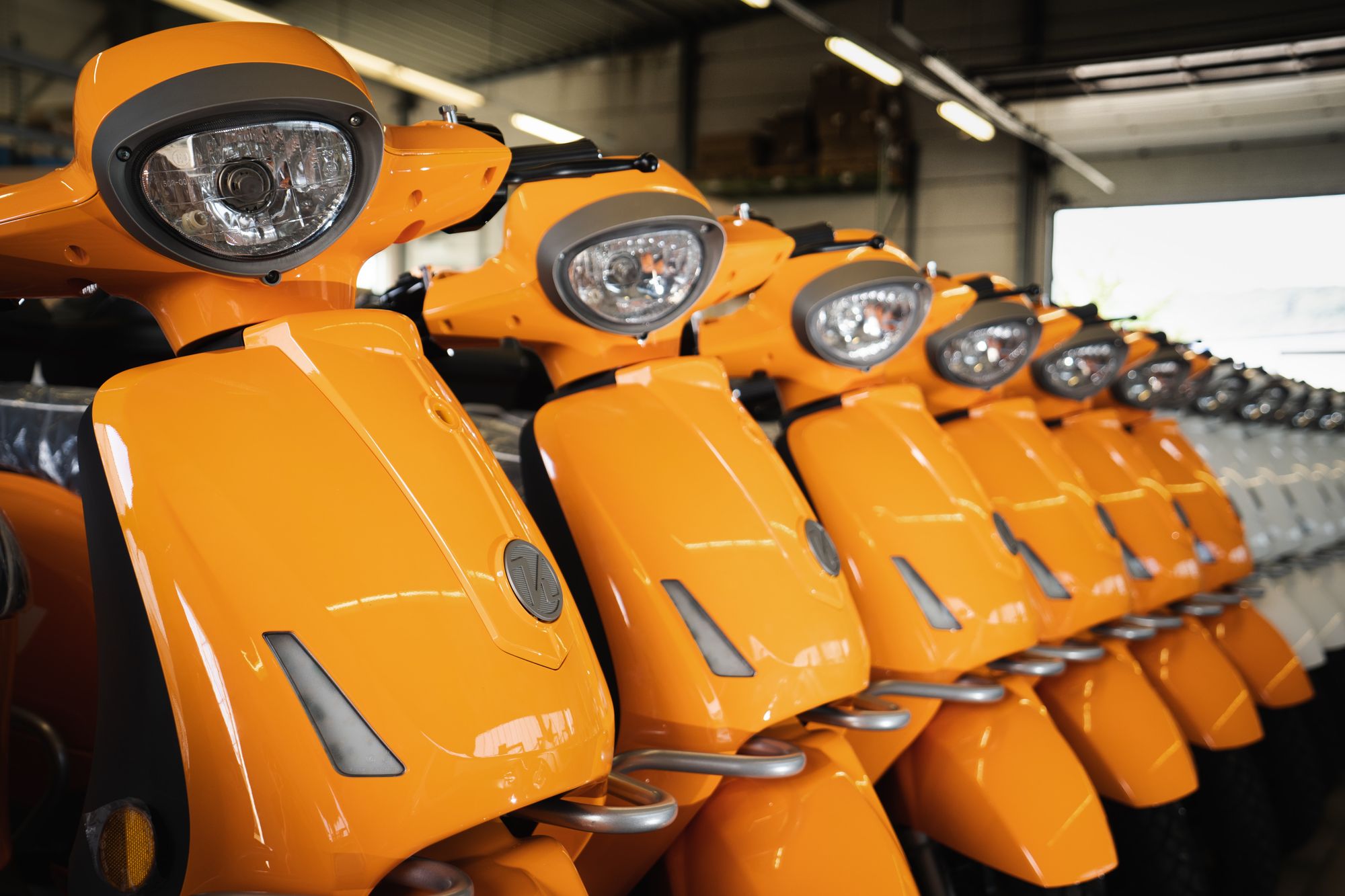
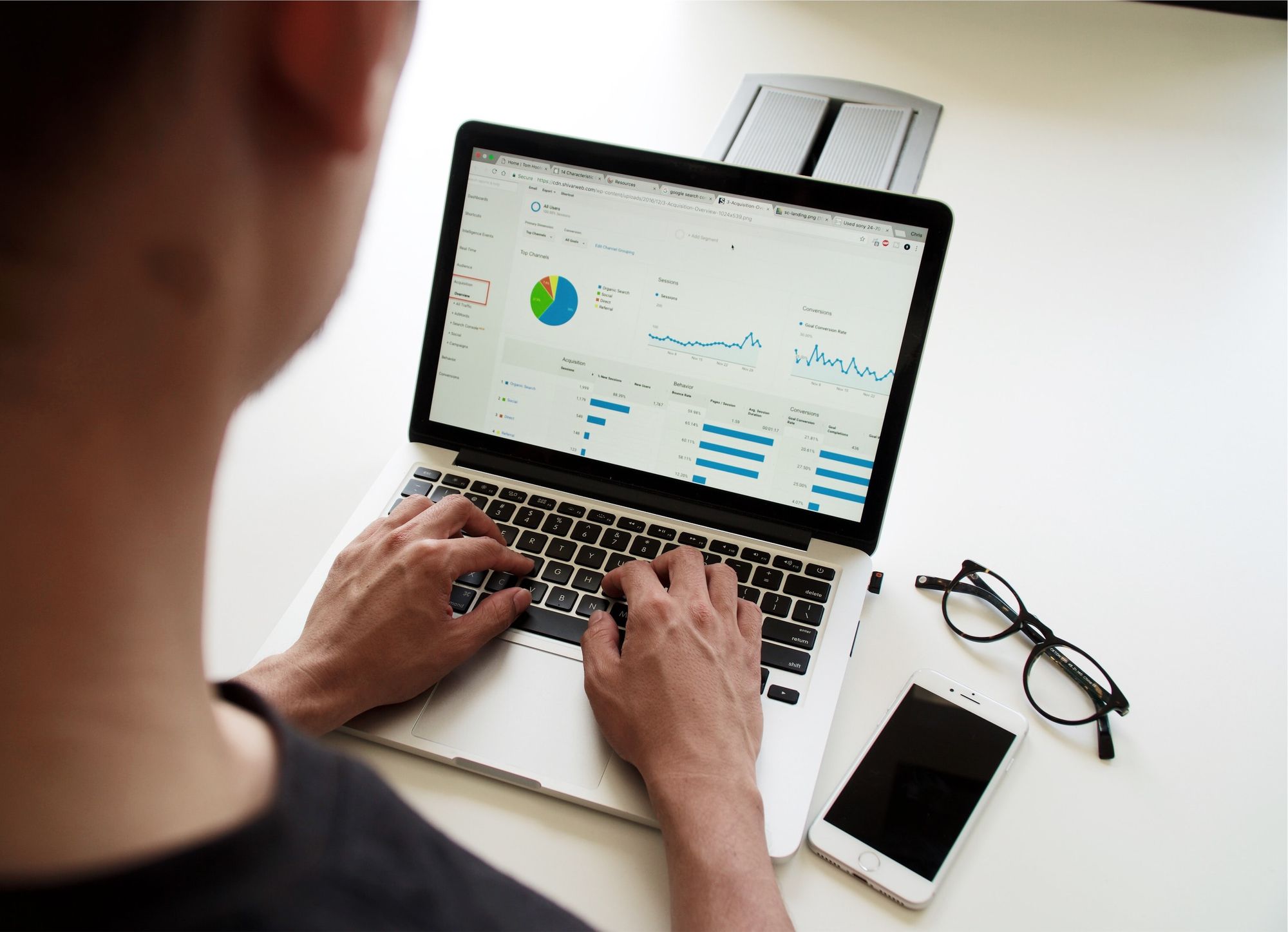