The global wood-based products market size was valued at USD 500.1 billion in 2020 and is expected to reach USD 742.6 billion by 2028, growing at a CAGR of 4.8% from 2021 to 2028. (Source: Grand View Research)
As a wood manufacturer, it is thus important to identify the wood manufacturing techniques most suitable for your business as well as the needs of your buyer personas. This will help you maximize your net revenue, net profit ratio, and returns on investment.
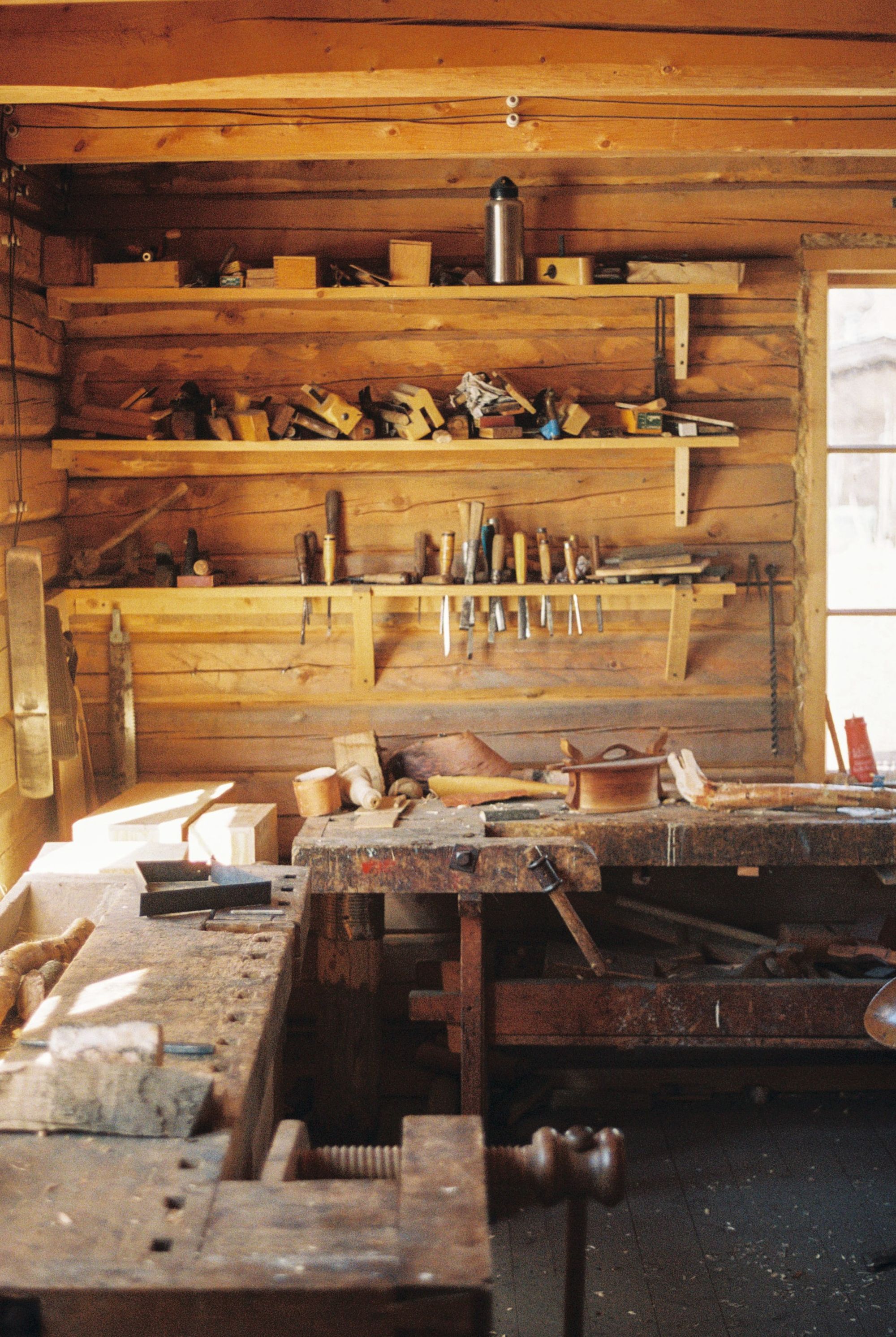
Wood manufacturing techniques are a set of processes and methods used to transform raw wood materials into finished products. These techniques are used to create a wide range of products, including furniture, flooring, cabinetry, decorative items, and musical instruments, among others.
There are several different wood manufacturing techniques available, each with its own unique advantages and disadvantages.
This article will help you understand some of the most common wood manufacturing techniques by covering the following topics:
- All About Wood Manufacturing Techniques
- The Pros and Cons of Different Wood Manufacturing Techniques
- Upcoming Trends in the Wood Manufacturing Techniques
- Factors for Determining the Most Suitable Wood Manufacturing Technique for Your Business
- What are Some Eco-Friendly and Sustainable Wood Manufacturing Techniques that You Can Implement?
- How can Deskera Help You with Wood Manufacturing?
- Key Takeaways
- Related Articles
All About Wood Manufacturing Techniques
Wood manufacturing techniques have been used for centuries to create beautiful and functional products from wood. These techniques have evolved over time, with new technologies and innovations constantly being developed to improve the efficiency and precision of the manufacturing process.
There are many different wood manufacturing techniques available today, each with its own unique advantages and disadvantages. From sawing and planing to carving and turning, these techniques can be used to create a wide range of products, from furniture and cabinetry to decorative items and musical instruments.
Choosing the right wood manufacturing technique for your business requires careful consideration of several factors, including the type of product you are producing, the volume of production, the skill level of your employees, and the environmental impact of your manufacturing process.
In this era of sustainability, there is also an increasing focus on using eco-friendly and sustainable manufacturing techniques that minimize waste and reduce the environmental impact of the production process.
As technology continues to advance, we can expect to see even more innovations and improvements in the field of wood manufacturing, leading to more efficient, precise, and sustainable techniques.
The Pros and Cons of Different Wood Manufacturing Techniques
There are various wood manufacturing techniques used in the woodworking industry. Some of the most common techniques include:
Sawing
Sawing is a common wood manufacturing technique used to cut the wood into pieces of the desired shape and size. It can be done manually using hand saws or with the help of machines such as table saws, band saws, or circular saws.
Hand sawing involves using a saw blade to cut through the wood by applying force and moving the saw back and forth. This technique requires skill and can be time-consuming, especially for larger pieces of wood.
Machine sawing is faster and more efficient than hand sawing, and it is often used in commercial woodworking operations. Table saws, for example, use a circular saw blade mounted on a table to cut the wood as it is pushed through the blade. Band saws use a long, continuous blade that runs between two wheels to cut through the wood.
Sawing can be used for a variety of purposes, such as cutting lumber for construction or cutting boards for furniture making. It is also used in the production of plywood, which involves cutting thin layers of wood and gluing them together to create a strong, durable material.
Pros of sawing as a wood manufacturing technique:
- Versatility: Sawing is a versatile technique that can be used to cut the wood into a variety of shapes and sizes, making it suitable for a wide range of applications.
- Precision: With the use of machines, sawing can be highly accurate, allowing for precise cuts and shapes.
- Efficiency: Sawing machines can cut wood quickly and efficiently, saving time, reducing manufacturing costs, and increasing productivity.
- Consistency: Machine sawing ensures that cuts are consistent, making it ideal for producing large quantities of identical pieces.
- Waste reduction: Sawing can help reduce waste by allowing the wood to be cut into the desired size and shape, minimizing leftover materials, and therefore promoting sustainability.
Cons of sawing as a wood manufacturing technique:
- Cost: Investing in sawing machinery can be expensive, making it difficult for smaller woodworking operations to afford.
- Noise: Machine sawing can be loud and may require hearing protection.
- Dust: Sawing produces sawdust, which can be a health hazard if inhaled, so proper ventilation and dust collection systems are necessary.
- Limited design possibilities: Sawing is a linear technique that is best suited for straight cuts and simple shapes. More complex designs may require other techniques, such as carving or routing.
- Safety concerns: Sawing machines can be dangerous if not used properly, and workers must be trained in proper safety procedures to prevent accidents.
Planing
Planing is a wood manufacturing technique used to create a smooth and flat surface on a piece of wood. It involves removing a thin layer of wood from the surface to create a desired thickness or finish. Planing can be done using hand planes or machine planers.
Hand planing involves using a hand-held tool called a plane to shave off thin layers of wood. It requires skill and practice to achieve a consistent and even finish, but it allows for more control over the thickness and surface of the wood.
Machine planing is faster and more efficient than hand planing and is often used in commercial woodworking operations. A machine planer uses a rotating cutter head to remove a thin layer of wood from the surface of the board as it is passed through the machine.
Pros of planing as a wood manufacturing technique:
- Smooth and flat finish: Planing can create a smooth and flat surface on a piece of wood, making it ideal for furniture making and other woodworking applications.
- Accuracy: Machine planing can produce a highly accurate and consistent finish, which is important for creating straight edges and precise thicknesses.
- Efficiency: Machine planing is faster and more efficient than hand planing, saving time and increasing productivity. This will help in improving cash flow, as well as increase your gross profits.
- Waste reduction: Planing allows for the use of rough or uneven pieces of wood by removing the surface imperfections and creating a flat, usable surface.
- Versatility: Planing can be used in a wide range of woods and sizes, making it suitable for a variety of woodworking projects.
Cons of planing as a wood manufacturing technique:
- Cost: Investing in a planing machine can be expensive, making it difficult for smaller woodworking operations to afford it.
- Noise: Planing machines can be loud and may require hearing protection.
- Dust: Planing produces sawdust, which can be a health hazard if inhaled, so proper ventilation and dust collection systems are necessary.
- Limited design possibilities: Planing is a linear technique that is best suited for creating flat surfaces and straight edges. More complex designs may require other techniques such as carving or routing.
- Safety concerns: Planing machines can be dangerous if not used properly, and workers must be trained in proper safety procedures to prevent accidents.
Turning
Turning is a wood manufacturing technique that involves rotating a piece of wood on a lathe while a cutting tool is used to shape it into a desired form. This technique can be used to create a wide range of shapes, including bowls, vases, furniture legs, and decorative pieces.
Turning can be done using hand-held tools or with the use of computer-controlled lathes.
Pros of turning as a wood manufacturing technique:
- Versatility: Turning can be used to create a wide range of shapes and designs, making it suitable for a variety of woodworking projects.
- Efficiency: Turning machines can produce pieces quickly and efficiently, saving time and increasing productivity.
- Precision: Turning allows for precise shaping and sizing of wood, creating consistent and uniform pieces.
- Aesthetics: Turning can create beautiful and intricate designs, adding visual appeal to the finished product.
- Waste reduction: Turning can be used to create functional and decorative pieces from smaller, leftover pieces of wood that may have been discarded otherwise.
Cons of turning as a wood manufacturing technique:
- Cost: Investing in a turning machine can be expensive, making it difficult for smaller woodworking operations to afford it.
- Noise: Turning machines can be loud and may require hearing protection.
- Dust: Turning produces sawdust, which can be a health hazard if inhaled, so proper ventilation and dust collection systems are necessary.
- Limited to round shapes: Turning is limited to creating round shapes, so it may not be suitable for certain designs or projects.
- Safety concerns: Turning machines can be dangerous if not used properly, and workers must be trained in proper safety procedures to prevent accidents.
Routing
Routing is a wood manufacturing technique that involves using a router to carve or shape a piece of wood. A router is a powerful tool that spins a cutting bit at high speed to remove material from the wood, allowing for precise cuts and shaping.
Routing can be used to create a variety of shapes and designs, including decorative edges, grooves, and inlays. It is often used in cabinetry, furniture making, and other woodworking applications.
Pros of routing as a wood manufacturing technique:
- Versatility: Routing can be used to create a wide range of shapes and designs, making it suitable for a variety of woodworking projects.
- Precision: Routing allows for precise cuts and shaping, creating consistent and uniform pieces.
- Efficiency: Routing machines can produce pieces quickly and efficiently, saving time and increasing productivity.
- Aesthetics: Routing can create intricate and decorative designs, adding visual appeal to the finished product.
- Waste reduction: Routing can be used to create functional and decorative pieces from smaller, leftover pieces of wood that may have been discarded otherwise.
Cons of routing as a wood manufacturing technique:
- Cost: Investing in a routing machine can be expensive, making it difficult for smaller woodworking operations to afford it.
- Noise: Routing machines can be loud and may require hearing protection.
- Dust: Routing produces sawdust, which can be a health hazard if inhaled, so proper ventilation and dust collection systems are necessary.
- Limited depth of cut: Routing is limited by the depth of the cutting bit, so it may not be suitable for certain designs or projects.
- Safety concerns: Routing machines can be dangerous if not used properly, and workers must be trained in proper safety procedures to prevent accidents.
Sanding
Sanding is a wood manufacturing technique that involves using abrasive materials to smooth and refine the surface of the wood. Sanding can be done by hand or with the use of power tools, such as sanders and sandpaper.
Sanding is an important step in the wood manufacturing process, as it prepares the wood for finishing and enhances its visual appeal.
Pros of sanding as a wood manufacturing technique:
- Smooth finish: Sanding can produce a smooth and even finish on wood, creating a professional and polished look.
- Versatility: Sanding can be used on a variety of wood types and finishes, making it suitable for many different woodworking projects.
- Refinement: Sanding can refine and enhance the natural beauty of wood, bringing out its unique grain patterns and colors.
- Efficiency: Power sanding tools can speed up the sanding process, saving time and increasing productivity.
- Health benefits: Sanding can improve the air quality in a woodshop by removing sawdust and other particles from the air.
Cons of sanding as a wood manufacturing technique:
- Time-consuming: Sanding can be a time-consuming process, particularly if done by hand.
- Cost: Investing in quality sanding equipment can be expensive, particularly for larger woodworking operations.
- Dust: Sanding produces sawdust, which can be a health hazard if inhaled, so proper ventilation and dust collection systems are necessary.
- Risk of damage: Over-sanding or using the wrong grit of sandpaper can damage the wood, leading to costly mistakes.
- Repetitive motion injuries: Sanding can cause repetitive motion injuries, such as carpal tunnel syndrome if proper precautions are not taken.
Joinery
Joinery is a wood manufacturing technique that involves connecting two or more pieces of wood together to form a larger, more complex structure. Joinery can be done using a variety of techniques and tools, including hand tools, power tools, and specialized machinery.
Joinery is a critical step in many woodworking projects, as it ensures that the finished product is strong, stable, and durable.
Pros of joinery as a wood manufacturing technique:
- Strength: Joinery can create strong and stable structures that can withstand wear and tear.
- Versatility: Joinery can be used to create a wide range of structures, from simple boxes to complex furniture pieces.
- Aesthetics: Joinery can create decorative and visually appealing structures, adding value and beauty to the finished product.
- Precision: Joinery requires precision and attention to detail, ensuring that the pieces fit together perfectly.
- Durability: Properly executed joinery can ensure that the finished product will last for many years without needing repairs.
Cons of joinery as a wood manufacturing technique:
- Time-consuming: Joinery can be a time-consuming process, particularly for complex structures or designs.
- Skill required: Joinery requires a high level of skill and expertise, making it difficult for beginners or hobbyists to master.
- Cost: Joinery requires specialized tools and equipment, which can be expensive for smaller woodworking operations.
- Complexity: Some types of joinery, such as dovetail joints, can be complex and challenging to execute properly.
- Limitations: Joinery is limited by the strength and stability of the wood being used, and certain types of joints may not be suitable for all types of wood or designs.
Carving
Carving is a wood manufacturing technique that involves using hand tools or power tools to remove material from a piece of wood to create a desired shape or design. Carving can range from simple, decorative designs to highly complex, intricate sculptures.
Carving is often used in woodworking for creating decorative elements on furniture, ornamental carvings, and sculptures.
Pros of carving as a wood manufacturing technique:
- Versatility: Carving can be used to create a wide range of shapes and designs, making it suitable for a variety of woodworking projects.
- Aesthetics: Carving can create intricate and decorative designs, adding visual appeal to the finished product.
- Unique designs: Carving allows for the creation of unique and personalized designs that cannot be replicated by other manufacturing techniques.
- Flexibility: Carving can be done using hand tools or power tools, making it a flexible and adaptable technique.
- Craftsmanship: Carving is often associated with traditional craftsmanship and can add value and prestige to the finished product.
Cons of carving as a wood manufacturing technique:
- Time-consuming: Carving can be a time-consuming process, particularly for complex designs or intricate details.
- Skill required: Carving requires a high level of skill and expertise, making it difficult for beginners or hobbyists to master.
- Cost: Investing in quality carving tools can be expensive, particularly for larger woodworking operations.
- Waste: Carving produces a significant amount of sawdust and wood waste, which can be difficult to dispose of and may have environmental impacts.
- Safety concerns: Carving tools can be dangerous if not used properly, and workers must be trained in proper safety procedures to prevent accidents.
Veneering
Veneering is a wood manufacturing technique that involves covering a base or substrate with a thin layer of high-quality wood or other decorative material, typically using adhesives. The resulting composite material is called a veneer.
Veneering is often used to create furniture, cabinetry, and other decorative wood products. Veneers can be made from a wide variety of wood species and other materials and can be cut into different shapes and sizes to achieve the desired design.
Pros of veneering as a wood manufacturing technique:
- Aesthetics: Veneering can create a variety of decorative patterns and designs, enhancing the visual appeal of the finished product.
- Efficiency: Veneering can be used to create complex designs more efficiently than carving or other manual techniques.
- Durability: Veneering can improve the durability and strength of the base material, making it more resistant to wear and tear.
- Cost-effective: Veneering can be a cost-effective alternative to solid wood, as it uses less high-quality wood and can create a similar aesthetic effect.
- Versatility: Veneering can be used on a wide range of substrates, including wood, metal, and plastic, allowing for a high degree of versatility in design.
Cons of veneering as a wood manufacturing technique:
- Quality control: Veneering requires careful attention to detail to ensure that the veneer is properly adhered to the substrate and does not warp or peel over time.
- Limited repairability: Once a veneer is applied, it can be difficult to repair or replace without damaging the base material.
- Environmental concerns: Veneering often requires the use of adhesives, which may have environmental impacts if not disposed of properly.
- Cost: High-quality veneers can be expensive, particularly for larger woodworking operations.
- Complexity: Veneering can be a complex process, requiring specialized equipment and expertise to achieve the desired results.
Laminating
Laminating is a wood manufacturing technique that involves bonding multiple layers of wood together with an adhesive to create a thicker, stronger and more stable material. The resulting composite material is called laminate or engineered wood.
Laminating is often used to create structural components for buildings, furniture, and other products. It can also be used to create decorative wood panels with a wide range of textures and patterns.
Pros of laminating as a wood manufacturing technique:
- Strength and stability: Laminating creates a strong, stable material that is less likely to warp, twist, or crack than solid wood.
- Versatility: Laminating can be used to create a wide range of shapes and sizes, making it suitable for a variety of woodworking projects.
- Cost-effective: Laminating can be a cost-effective alternative to solid wood, as it uses less high-quality wood and can create a similar aesthetic effect.
- Durability: Laminating can improve the durability and resistance of the wood to weather, moisture, and other environmental factors.
- Sustainable: Laminating can be made from sustainably harvested wood, reducing the environmental impact of wood manufacturing.
Cons of laminating as a wood manufacturing technique:
- Quality control: Laminating requires careful attention to detail to ensure that each layer is properly aligned and bonded with the adhesive.
- Limited repairability: Once a laminate is created, it can be difficult to repair or replace without damaging the surrounding material.
- Complexity: Laminating can be a complex process, requiring specialized equipment and expertise to achieve the desired results.
- Environmental concerns: Laminating may use adhesives that contain formaldehyde, which can be harmful to human health and the environment if not managed properly.
- Appearance: The appearance of laminated wood may not be as natural or aesthetically pleasing as solid wood, particularly if low-quality materials are used.
Woodturning
Woodturning is a wood manufacturing technique that involves using a lathe to shape a piece of wood while it rotates on an axis.
The wood is held in place by a chuck or other holding device, and a cutting tool is used to remove material from the wood as it spins.
Woodturning can be used to create a variety of shapes, such as bowls, vases, and furniture legs.
Pros of woodturning as a wood manufacturing technique:
- Versatility: Woodturning can be used to create a wide range of shapes and sizes, making it suitable for a variety of woodworking projects.
- Efficiency: Woodturning can create complex shapes more efficiently than manual techniques, reducing the time and effort required to create a finished product.
- Aesthetics: Woodturning can create unique, intricate designs that enhance the visual appeal of the finished product.
- Sustainable: Woodturning can be made from sustainably harvested wood, reducing the environmental impact of wood manufacturing.
- Adaptability: Woodturning can be adapted to work with a wide range of wood species, allowing for greater flexibility in design.
Cons of woodturning as a wood manufacturing technique:
- Skill and expertise: Woodturning requires skill and expertise to achieve the desired results and can be difficult to master for beginners.
- Limited precision: Woodturning may not produce as precise results as other manufacturing techniques, particularly for very small or detailed designs.
- Safety concerns: Woodturning can be a hazardous process, requiring careful attention to safety protocols and protective equipment.
- Cost: Woodturning can be an expensive process, requiring specialized equipment and tools to achieve the desired results.
- Environmental concerns: Woodturning may produce waste material that can be difficult to dispose of and may use electricity or other energy sources that have environmental impacts.
Upcoming Trends in the Wood Manufacturing Techniques
- Increased use of automation: Advances in robotics and artificial intelligence may lead to greater automation in wood manufacturing, allowing for more efficient and cost-effective production processes.
- Integration of digital technologies: The use of digital technologies, such as 3D printing and computer-aided design, may become more prevalent in wood manufacturing, allowing for more precise and complex designs.
- Sustainable practices: With a growing emphasis on environmental sustainability, wood manufacturers may adopt more eco-friendly practices, such as using reclaimed wood or implementing closed-loop manufacturing processes.
- Integration of smart technology: The use of sensors and other smart technologies may become more common in wood manufacturing, allowing for real-time monitoring of production processes and increased efficiency.
- Customization and personalization: With the rise of e-commerce and on-demand manufacturing, wood manufacturers may increasingly offer customized and personalized products tailored to individual customer needs and preferences.
- Hybrid manufacturing techniques: Combining different wood manufacturing techniques, such as 3D printing and traditional woodworking, may become more common, allowing for the creation of new and innovative designs.
- Collaboration and partnerships: Wood manufacturers may increasingly collaborate with designers, architects, and other stakeholders to create unique and innovative products that meet the evolving needs and preferences of customers.
- Use of sustainable and alternative wood materials: With growing concern over deforestation and the sustainability of traditional wood sources, manufacturers may turn to alternative materials, such as bamboo or recycled plastic lumber, as a more sustainable option.
- Greater emphasis on durability and longevity: As consumers become more aware of the impact of disposable products on the environment, wood manufacturers may shift towards creating products that are designed to last longer and withstand wear and tear.
- Digital manufacturing platforms: Online platforms that connect customers with manufacturers may become more common, allowing for more efficient communication and production processes.
- Adoption of lean manufacturing principles: Wood manufacturers may increasingly adopt lean manufacturing principles to reduce waste, increase efficiency, and improve overall quality.
- Integration of circular economy principles: Manufacturers may embrace the circular economy model, which emphasizes the use of renewable materials and closed-loop manufacturing processes to reduce waste and improve sustainability.
- Use of 3D scanning and printing for restoration and replication: 3D scanning and printing technology may be used to restore damaged or deteriorating historic woodwork or to replicate unique designs.
- Incorporation of augmented reality and virtual reality: AR and VR technologies may be used to allow customers to visualize and customize wood products in a more immersive and interactive way.
- Increased use of nanotechnology: Nanotechnology may be used to enhance the properties of wood, such as increased strength or resistance to moisture and decay.
- Emphasis on safety and ergonomics: Wood manufacturers may focus on creating products and production processes that are safer and more ergonomic for workers, reducing the risk of injury and improving productivity.
- Use of blockchain technology for supply chain transparency: Blockchain technology may be used to improve transparency and traceability in the wood supply chain, ensuring that wood products are ethically and sustainably sourced.
- Adoption of 5G technology: 5G technology may be used to improve communication and data transfer between machines and production systems, enabling more efficient and connected manufacturing processes.
- Greater use of robotics and cobots: Collaborative robots, or cobots, may become more common in wood manufacturing, working alongside human workers to improve efficiency and productivity.
Factors for Determining the Most Suitable Wood Manufacturing Technique for Your Business
There are several factors that you should consider when determining the most suitable wood manufacturing technique for your business. These include:
- Type of product: The type of product you are manufacturing will influence the wood manufacturing techniques you can use. For example, if you are producing furniture, you may need to use techniques like joinery, routing, and sanding, while if you are producing decorative wood items, you may use techniques like carving, turning, and veneering.
- Production volume: The volume of products you need to produce will impact your choice of wood manufacturing technique. If you are producing high volumes of products, you may need to use automated techniques like CNC routing or lamination, while if you are producing lower volumes, you may be able to use more manual techniques like hand carving or hand sanding.
- Cost: The cost of wood manufacturing techniques will also impact your choice. Automated techniques may be more expensive to set up initially but can save on labor costs in the long run, while manual techniques may be cheaper initially but can be more time-consuming and labor-intensive.
- Skill level of employees: The skill level of your employees will also impact your choice of wood manufacturing technique. Some techniques, like carving and turning, require a high level of skill and experience, while others, like sanding and planing, can be taught more easily.
- Materials used: The type of wood and other materials you use in your manufacturing process will also impact your choice of wood manufacturing technique. Some techniques may work better with certain types of wood or other materials, and you will need to consider the availability and cost of these materials when making your decision.
- Environmental impact: The environmental impact of your wood manufacturing process is also an important factor to consider. You should choose techniques that minimize waste and reduce your carbon footprint, such as using sustainable wood sources and implementing closed-loop manufacturing processes.
- Safety considerations: Finally, you should also consider the safety of your employees when choosing a wood manufacturing technique. Some techniques, like sawing and routing, can be more dangerous than others, and you will need to implement proper safety measures to ensure that your employees are not at risk of injury.
What are Some Eco-Friendly and Sustainable Wood Manufacturing Techniques that You Can Implement?
There are several eco-friendly and sustainable wood manufacturing techniques that you can implement in your business. Here are some examples:
- Use sustainable wood sources: One of the most important steps you can take is to ensure that the wood you use in your manufacturing process comes from sustainable sources. Look for wood that has been certified by organizations like the Forest Stewardship Council (FSC) or the Sustainable Forestry Initiative (SFI).
- Implement closed-loop manufacturing: Closed-loop manufacturing processes aim to minimize waste by recycling and reusing materials throughout the production process. For example, you could use wood waste from your manufacturing process to create wood pellets for use as fuel or to make composite wood products.
- Use water-based finishes: Instead of using solvent-based finishes, which can release harmful volatile organic compounds (VOCs) into the air, opt for water-based finishes. These are less harmful to the environment and to your employees' health.
- Implement energy-efficient practices: Look for ways to reduce your energy consumption, such as using energy-efficient lighting and equipment and optimizing your production schedule to minimize energy usage during peak demand periods.
- Use digital design and production technologies: Digital design and production technologies like Computer Numerical Control (CNC) routing and 3D printing can help to reduce material waste and improve production efficiency, leading to a more sustainable manufacturing process.
- Implement responsible waste disposal: Implement responsible waste disposal practices, such as recycling and composting, to reduce the amount of waste that your manufacturing process generates.
By implementing these and other sustainable wood manufacturing techniques, you can reduce your environmental impact and create a more sustainable and eco-friendly business.
How can Deskera Help You with Wood Manufacturing?
Deskera is a material requirements planning (MRP) software solution that can help wood manufacturing companies manage their operations more efficiently and effectively. Some ways Deskera can help include:
- Supply chain management: Deskera MRP can help wood manufacturing companies optimize their supply chain management by tracking inventory levels, managing suppliers, and streamlining procurement processes.
- Manufacturing operations: Deskera MRP can help wood manufacturing companies manage their manufacturing operations by optimizing production schedules, tracking work orders, and monitoring production costs.
- Financial management: Deskera Books can help wood manufacturing companies manage their finances by automating accounting processes, generating financial reports, and managing cash flow.
- Sales and customer management: Deskera CRM can help wood manufacturing companies manage their sales and customer relationships by tracking customer interactions, managing leads and opportunities, and providing customer support.
- Project management: Deskera MRP can help wood manufacturing companies manage their projects by tracking tasks, managing resources, and monitoring project timelines and budgets.
Key Takeaways
There are many different wood manufacturing techniques available, each with its own set of pros and cons. These techniques are:
- Sawing: This involves cutting the wood into pieces using saws, which can be done manually or with the help of machines.
- Planing: This technique involves removing a thin layer of wood from the surface to create a smooth, flat finish. It is typically done with a machine called a planer.
- Turning: This technique involves spinning a piece of wood on a lathe and shaping it into a desired form, such as a bowl or a spindle.
- Routing: This involves using a router to cut designs or shapes into the wood. It is often used for decorative purposes, such as creating intricate patterns on the furniture.
- Sanding: This involves smoothing the surface of the wood using sandpaper or a sanding machine. It can be done by hand or with the help of a machine.
- Joinery: This involves joining two or more pieces of wood together to create a larger structure, such as a table or a cabinet. Common joinery techniques include dovetail joints, mortise and tenon joints, and biscuit joints.
- Carving: This involves using knives or chisels to remove wood from a piece to create a desired shape or design.
- Veneering: This involves applying a thin layer of wood (known as a veneer) to the surface of another piece of wood to create a decorative finish.
- Laminating: This involves bonding two or more layers of wood together to create a stronger, more durable material.
- Woodturning: This is a specialized technique that involves spinning a block of wood on a lathe while using cutting tools to shape and carve the wood into a desired form. It is often used to create intricate designs and patterns on furniture and other wooden objects.
Choosing the right wood manufacturing technique for your business depends on several factors, including the type of product you are producing, the volume of production, the skill level of your employees, and the environmental impact of your manufacturing process.
While some techniques are more efficient and cost-effective, others may offer greater flexibility and customization options. It is important to carefully consider the pros and cons of each technique before deciding which one to use.
Additionally, sustainability is becoming an increasingly important consideration in the woodworking industry, and businesses should strive to implement eco-friendly and sustainable practices whenever possible.
Overall, by understanding the strengths and weaknesses of each technique, businesses can make informed decisions that will help them to create high-quality, sustainable products that meet the needs of their customers while minimizing their impact on the environment.
Overall, Deskera can provide wood manufacturing companies with a comprehensive MRP solution that can help them streamline their operations, reduce costs, and improve efficiency and profitability.
Related Articles
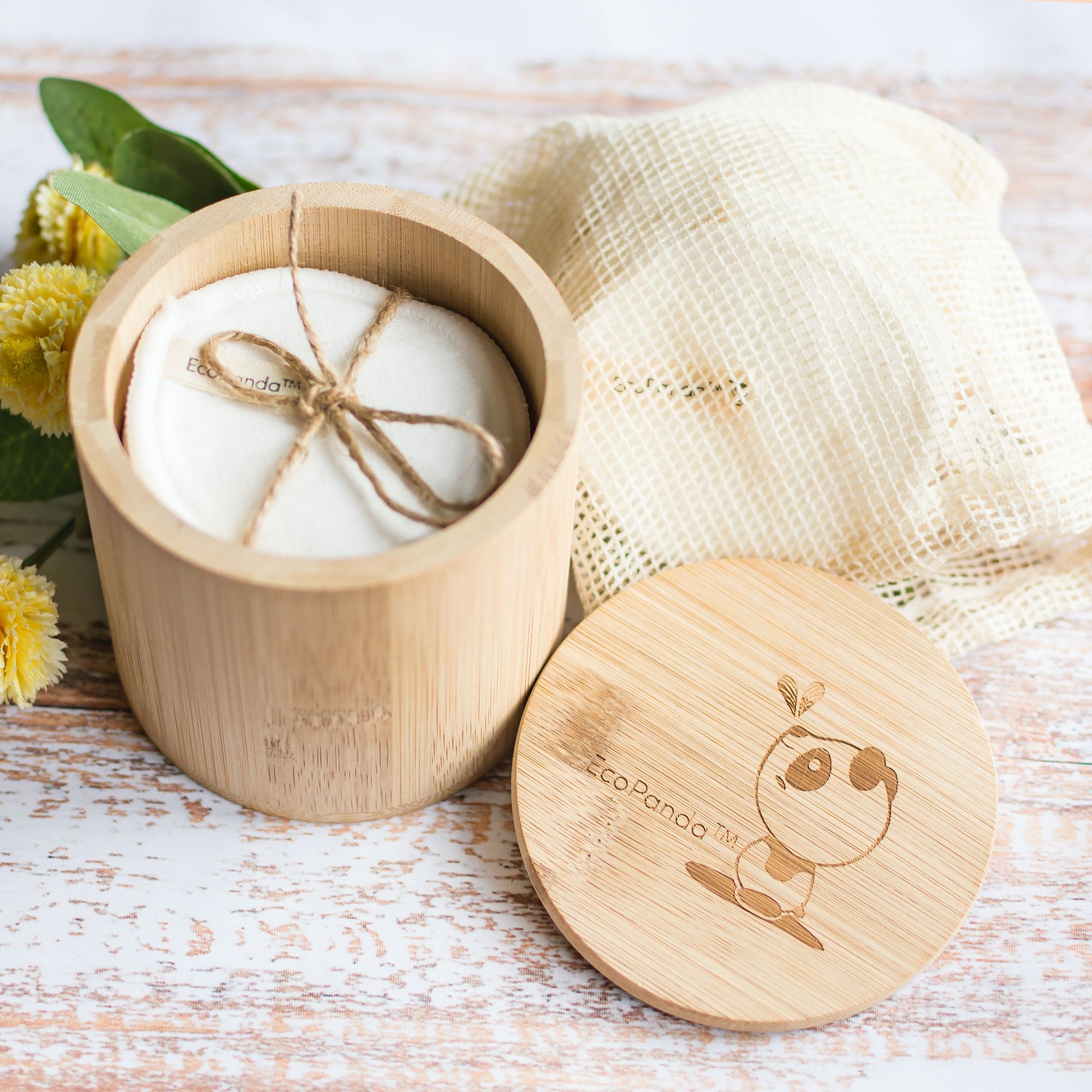
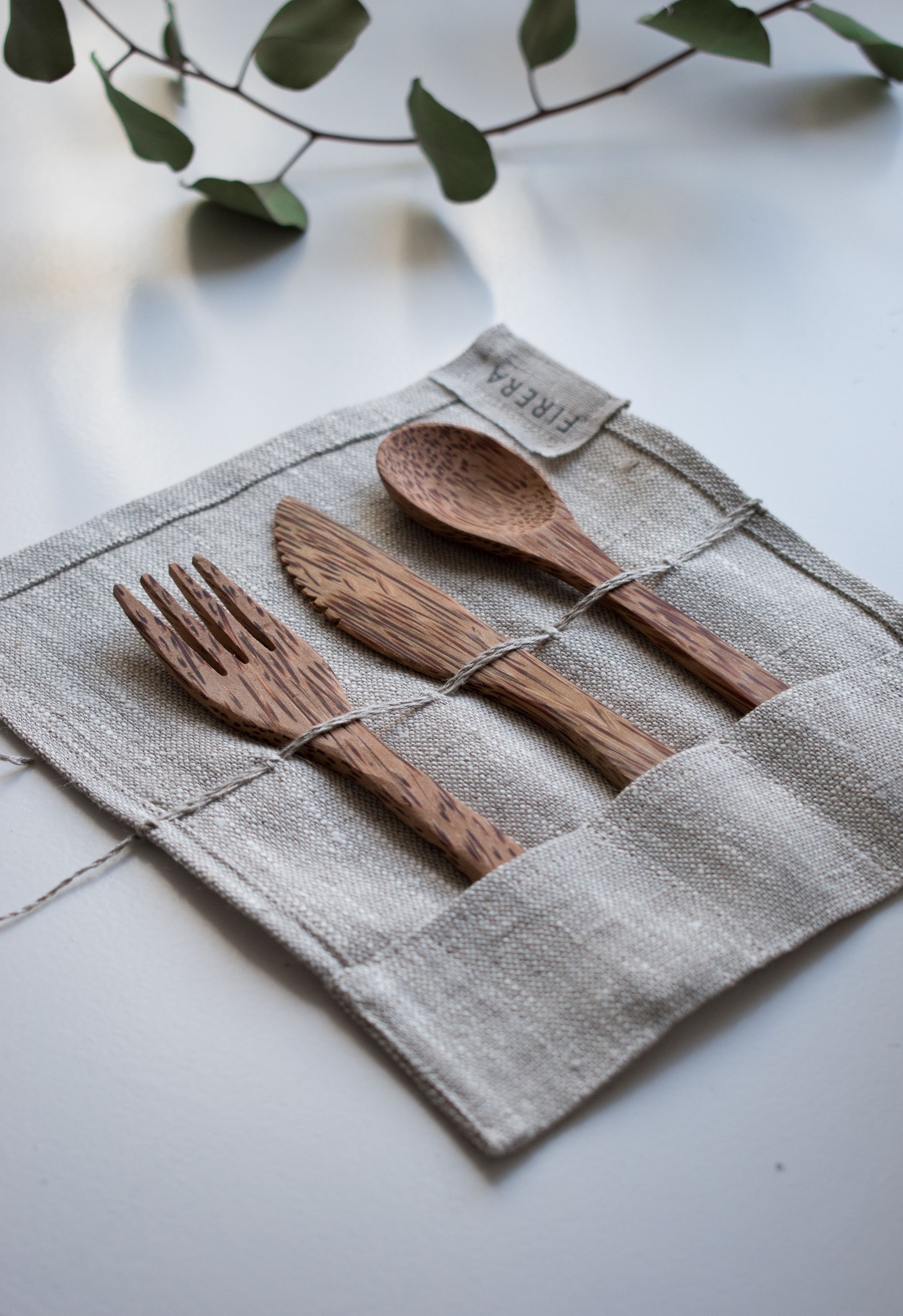

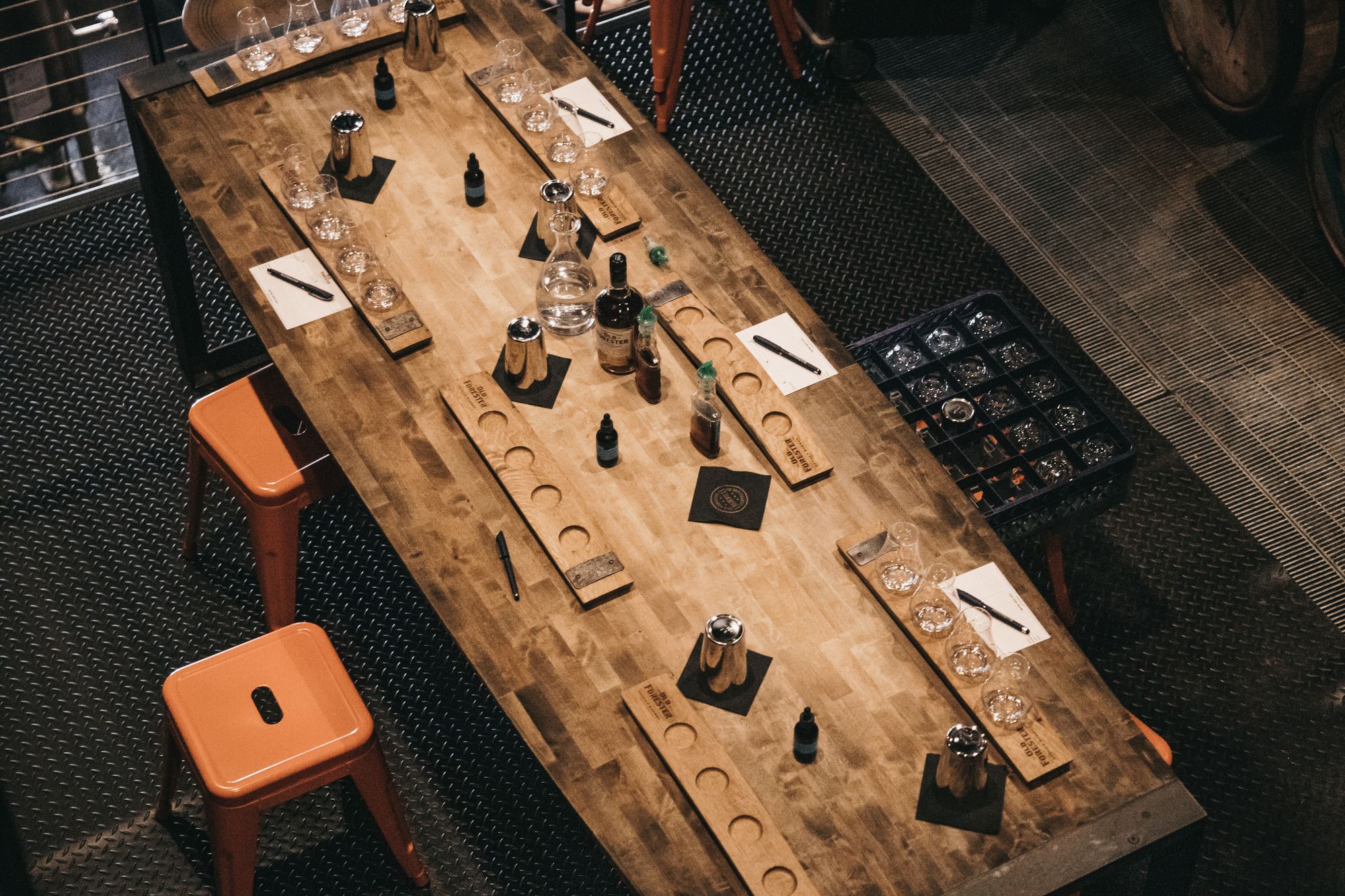
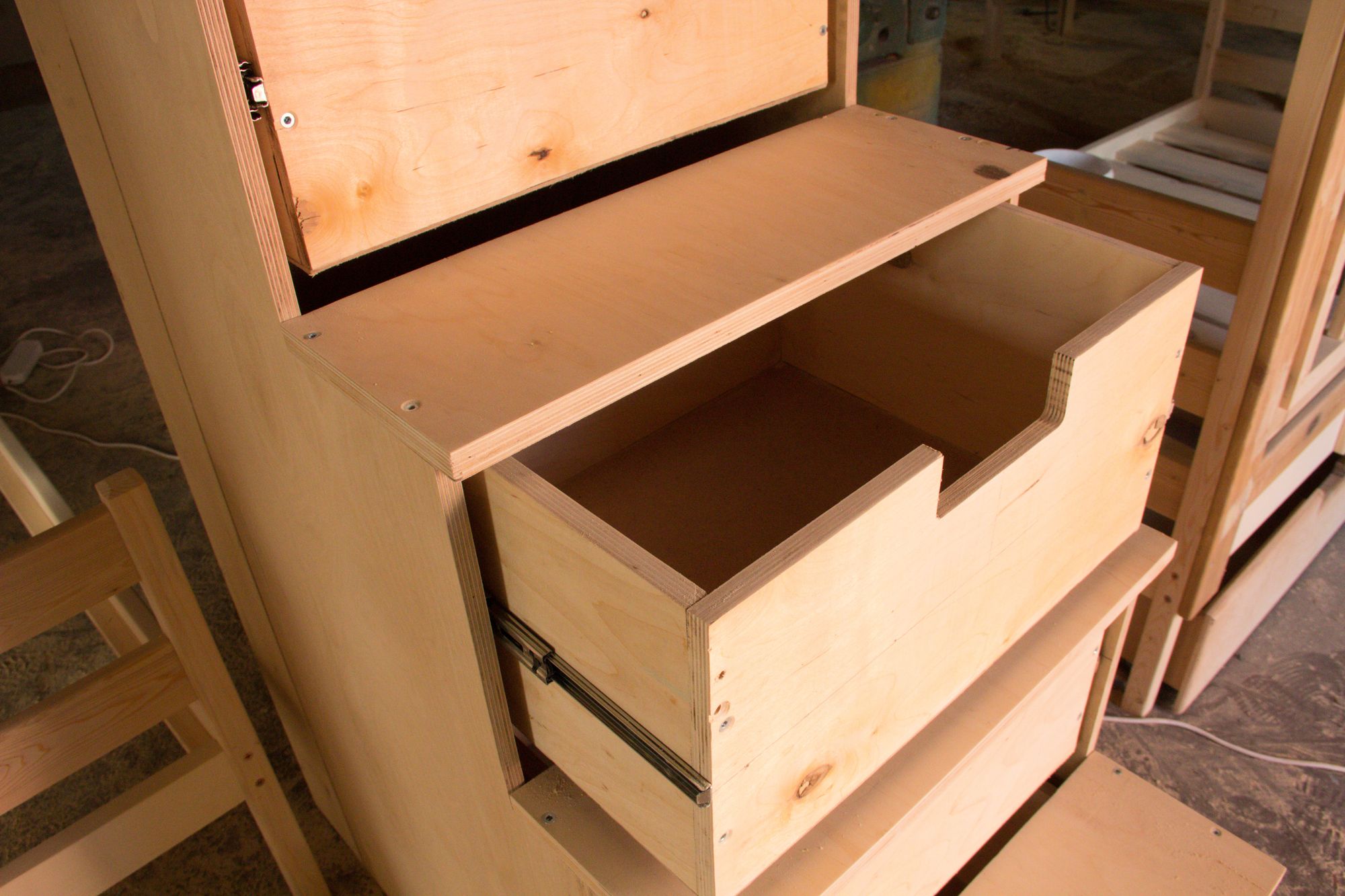
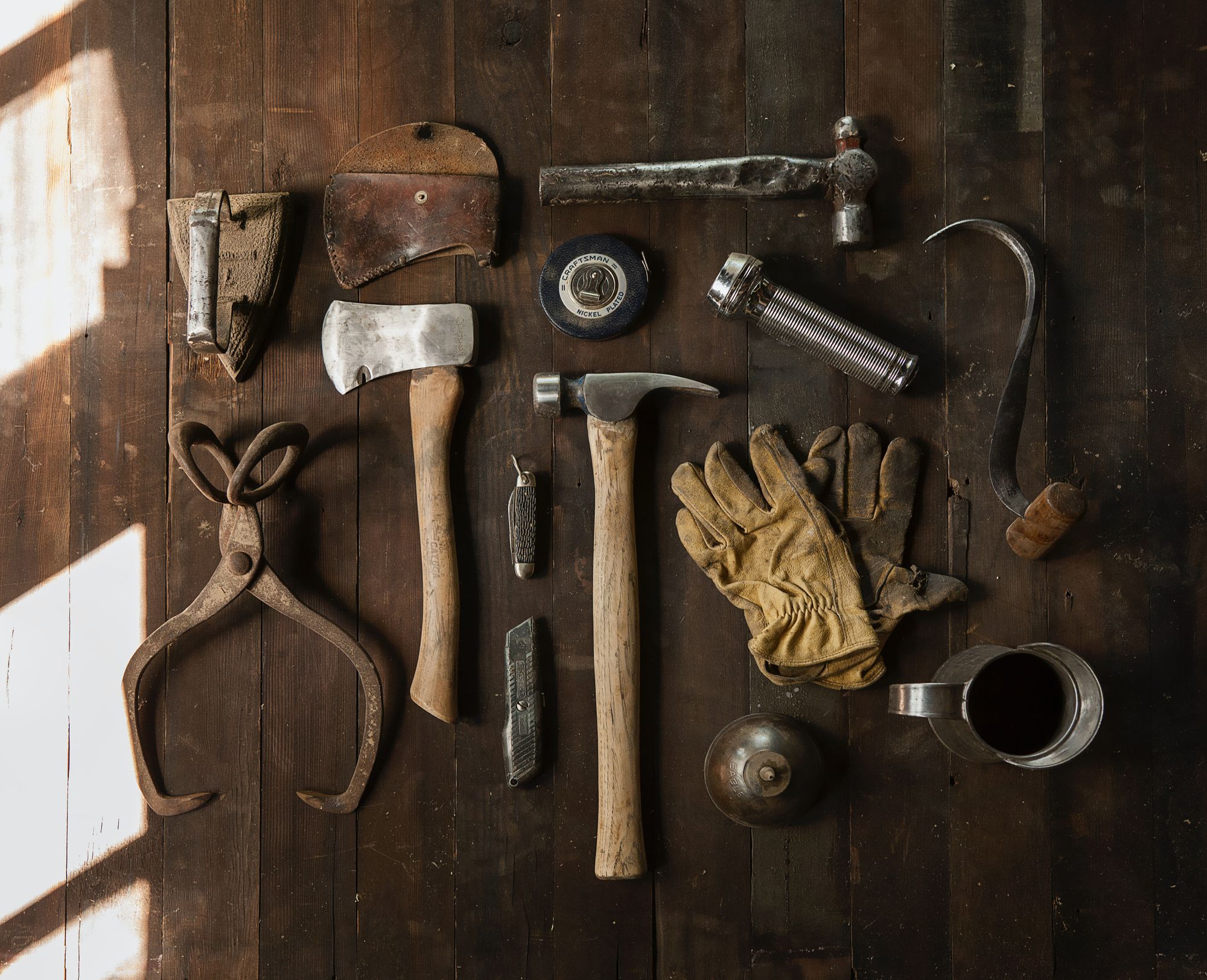