According to a recent report by ResearchAndMarkets, the global market for paper and pulp processing equipment was valued at $8.7 billion in 2020 and is expected to reach $12.2 billion by 2026, growing at a CAGR of 5.2% from 2021 to 2026.
Paper manufacturing techniques vary in their processes, materials, and equipment used, and each has its own set of advantages and disadvantages. Understanding the pros and cons of different paper manufacturing techniques is essential for selecting the best method for producing specific paper products.
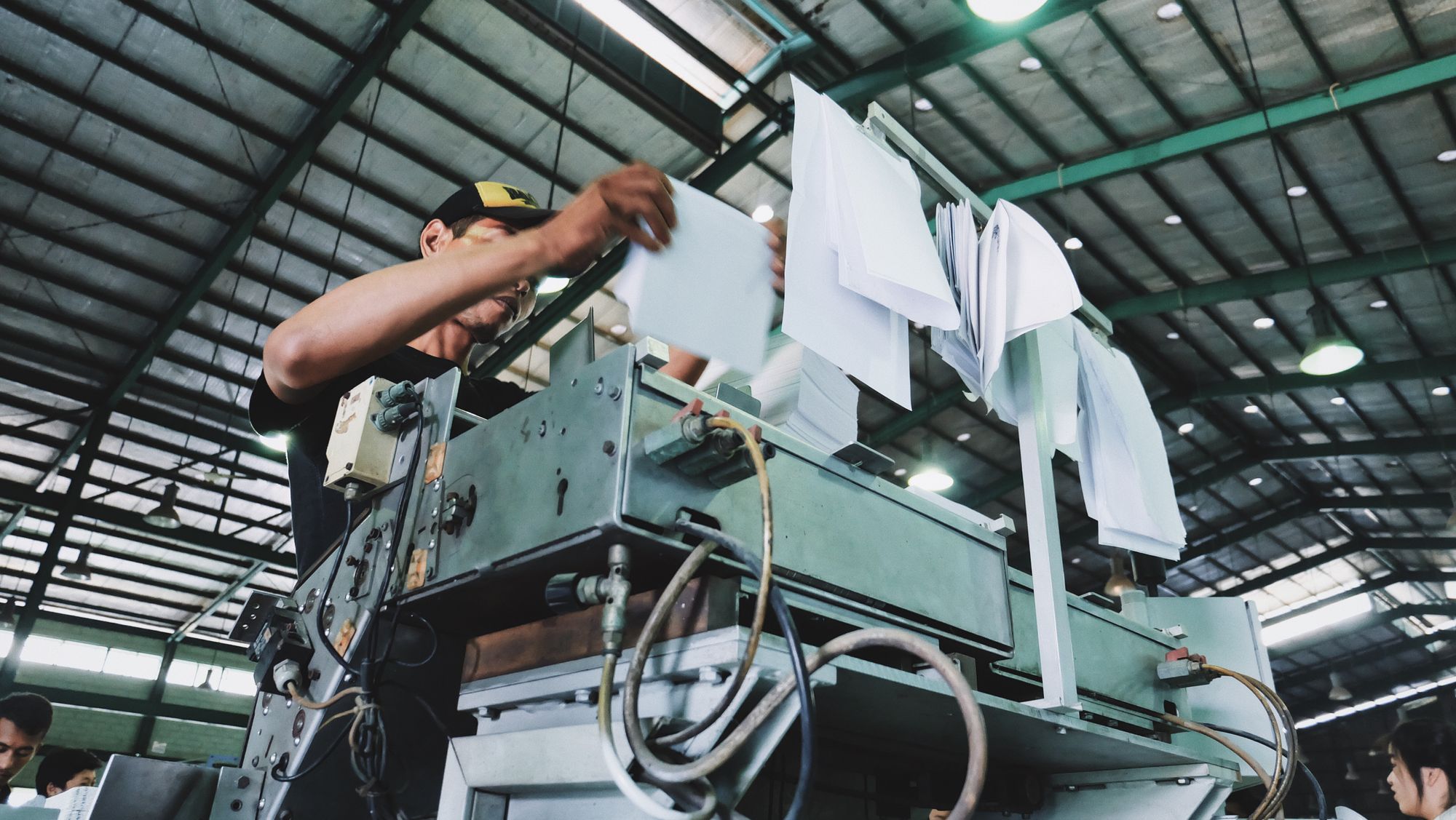
Mechanical pulping, chemical pulping, and recycled paper are common techniques used in paper manufacturing. However, these are not the only paper manufacturing techniques. There are several more to be understood and taken into account.
Each of these paper manufacturing techniques has its own set of pros and cons. Some of the advantages of these techniques include improved paper quality, increased efficiency, and reduced costs. However, these techniques can also have disadvantages, such as environmental concerns, higher costs, and reduced product performance.
By understanding the pros and cons of different paper manufacturing techniques, manufacturers can make informed decisions about which technique to use based on the specific requirements of their products, their budget, and their environmental goals.
This article will be your guide to the pros and cons of different paper manufacturing techniques by covering the following topics:
- All About Paper Manufacturing Techniques
- The Pros and Cons of Different Paper Manufacturing Techniques
- Upcoming Trends in Paper Manufacturing Techniques
- Factors for Determining the Most Suitable Paper Manufacturing Technique for Your Business
- How can Deskera Help You with Paper Manufacturing?
- Key Takeaways
- Related Articles
All About Paper Manufacturing Techniques
Paper manufacturing techniques involve a series of processes that convert raw materials into finished paper products. The techniques used vary depending on the type of paper being produced, but they generally follow the same basic steps.
- Raw Material Preparation: The first step in paper manufacturing is the preparation of raw materials. This can include harvesting trees for wood pulp, collecting recycled paper, or preparing cotton or other fibers.
- Pulping: Once the raw materials are collected, they are pulped. This process breaks down the fibers into a slurry that is ready for processing.
- Cleaning: After pulping, the slurry is cleaned to remove any contaminants or impurities, such as dirt or bark.
- Refining: The slurry is then refined to create a consistent texture and to improve the strength of the paper.
- Additives: Various additives, such as sizing agents or fillers, may be added to the slurry to improve the properties of the paper.
- Forming: The slurry is then formed into sheets or rolls using a variety of methods, including Fourdrinier machines, cylinder machines, or twin-wire formers.
- Pressing: The formed sheets or rolls are then pressed to remove excess water and improve the density of the paper.
- Drying: The paper is then dried using heated rollers or by passing it through a series of dryers.
- Finishing: The finished paper may undergo additional treatments, such as calendaring or coating, to improve its properties and appearance.
Modern paper manufacturing techniques have become highly automated and efficient, with sophisticated machinery and computerized controls that monitor and optimize the entire process. This has allowed paper mills to produce large volumes of high-quality paper with minimal waste and environmental impact.
However, paper manufacturing still has some environmental challenges, such as the use of chemicals and the generation of wastewater and solid waste. Many paper mills have implemented sustainability practices, such as using recycled materials and reducing water and energy consumption, to minimize their environmental impact.
The Pros and Cons of Different Paper Manufacturing Techniques
The pros and cons of different paper manufacturing techniques are as follows:
Mechanical Pulping
Mechanical pulping is a paper-making process that involves physically grinding wood chips into pulp. Here are some of the pros and cons of mechanical pulping:
Pros:
- High yield: Mechanical pulping has a high yield, which means that it can produce a large amount of pulp from a given amount of wood chips. This makes it a cost-effective method of paper-making.
- Good for certain types of paper: Mechanical pulp is well-suited for producing newsprint, as well as other low-quality papers that don't require a high degree of strength or durability.
- Energy efficiency: Mechanical pulping requires less energy than other pulping methods, such as chemical pulping, because it relies on physical grinding rather than chemical reactions.
Cons:
- Reduced paper strength: Mechanical pulping can result in reduced paper strength, which can make the paper more prone to tearing or breaking. This is because the process breaks down the fibers in the wood, resulting in shorter, weaker fibers.
- Reduced paper quality: Mechanical pulping can also result in a lower-quality paper with a more uneven surface and reduced brightness.
- Environmental concerns: The grinding process used in mechanical pulping can generate a lot of heat and noise and can also produce large amounts of wastewater. Additionally, the use of wood chips from trees that are not sustainably harvested can contribute to deforestation and other environmental issues.
Chemical Pulping
Chemical pulping is a paper-making process that involves the use of chemicals to break down the lignin in wood chips, separating the cellulose fibers to create pulp. Here are some of the pros and cons of chemical pulping:
Pros:
- Stronger paper: Chemical pulping typically produces stronger paper than mechanical pulping due to the longer, stronger cellulose fibers that result from the process.
- Better paper quality: Chemical pulping can also produce higher-quality paper with a smoother surface and better brightness, making it suitable for a wider range of applications.
- More sustainable: Chemical pulping can be done with sustainably harvested wood, reducing the environmental impact of paper production.
Cons:
- Higher cost: Chemical pulping requires more energy and resources than mechanical pulping, making it more expensive.
- Chemical waste: The chemicals used in the process can be hazardous to human health and the environment, and the waste produced can be difficult and expensive to dispose of properly.
- Lower yield: Chemical pulping typically results in a lower yield than mechanical pulping, meaning that it produces less pulp from a given amount of wood chips. This can increase the cost of production and contribute to deforestation if not done sustainably.
Kraft Process
The Kraft process is a widely used paper manufacturing technique that involves the use of strong alkaline chemicals such as sodium hydroxide and sodium sulfide to break down wood fibers. Here are some pros and cons of the Kraft process:
Pros:
- Strong and durable paper: The Kraft process produces strong, durable paper with high resistance to tearing and bursting. The pulp produced by this process is suitable for a wide range of paper products.
- High yield: The Kraft process has a high yield, meaning that it produces more pulp per unit of wood compared to other pulping techniques.
- Suitable for different types of wood: The Kraft process can be used with a variety of wood species, including softwood and hardwood.
- Reduced environmental impact: The Kraft process has a lower environmental impact than other pulping techniques because it uses fewer chemicals and produces less waste.
Cons:
- High energy consumption: The Kraft process is an energy-intensive process that requires a significant amount of energy to operate. This can result in high energy costs and greenhouse gas emissions.
- Large amounts of chemicals: The Kraft process requires large amounts of strong alkaline chemicals such as sodium hydroxide and sodium sulfide. This can result in high chemical costs and environmental concerns associated with the disposal of chemicals.
- Limited versatility: The Kraft process is primarily used for producing strong, durable paper products such as paper bags, corrugated boxes, and packaging materials. It may not be suitable for producing fine paper products such as writing paper or tissue paper.
- High initial cost: The Kraft process requires a significant amount of capital investment to set up a pulping facility. This can make it difficult for small-scale paper manufacturers to adopt this technique.
Sulfite Process
The sulfite process is a chemical pulping technique that involves the use of sulfurous acid to break down wood fibers. Here are some pros and cons of the sulfite process:
Pros:
- High-quality paper: The sulfite process produces high-quality paper with a high degree of brightness and a fine texture. It is often used for producing fine paper products such as writing paper, tissue paper, and high-end printing paper.
- Versatility: The sulfite process can be used with a variety of wood species, including softwood and hardwood.
- Reduced environmental impact: The sulfite process produces less waste and has a lower environmental impact than the Kraft process because it uses fewer chemicals.
Cons:
- High skill requirement: The sulfite process requires a higher level of skill and expertise to operate compared to other pulping techniques. This can result in higher labor costs and training expenses.
- High energy consumption: The sulfite process is an energy-intensive process that requires a significant amount of energy to operate. This can result in high energy costs and greenhouse gas emissions.
- High chemical cost: The sulfite process requires the use of expensive chemicals such as sulfur dioxide, which can result in high chemical costs.
- Limited production capacity: The sulfite process has a lower production capacity compared to other pulping techniques. This can result in longer processing times and higher production costs.
Recycled Paper
Recycled paper is paper made from paper that has already been used and discarded. Here are some of the pros and cons of recycled paper in paper manufacturing:
Pros:
- Reduced environmental impact: Recycling paper reduces the need for harvesting virgin trees and reduces the amount of waste sent to landfills, which can help to reduce greenhouse gas emissions and other environmental impacts.
- Energy efficient: Making paper from recycled fibers requires less energy than making paper from virgin fibers, as the fibers have already been processed and do not require as much processing to make into pulp.
- Cost-effective: Using recycled fibers can be cost-effective, as it reduces the need for virgin pulp and can be less expensive than other sources of fiber.
Cons:
- Reduced paper quality: Recycled paper fibers are typically shorter and weaker than virgin fibers, which can result in lower-quality paper with reduced strength and durability.
- Limited availability: The availability of recycled fibers can be limited, particularly for certain grades and types of paper, which can make it difficult for some manufacturers to use recycled fibers.
- Contamination: Recycled paper can be contaminated with ink, dirt, and other materials, which can affect the quality of the paper and require additional processing steps to remove.
Fourdrinier Paper-making
Fourdrinier paper-making is a process used to make paper from pulp. It involves passing a sheet of pulp through a series of rollers and screens, which drains and presses the water out of the pulp and leaves a sheet of paper behind.
The sheet of paper is then dried and finished to create the desired texture and finish. This process was invented by French industrialists in 1806 and is still the most common method of paper-making today.
Some of the pros and cons of Fourdrinier paper-making are:
Pros:
- High production speed: Fourdrinier paper-making can produce paper at a very high speed, which makes it suitable for producing large quantities of paper.
- Large paper machines: Fourdrinier paper machines can produce paper in very large widths and lengths, making them suitable for producing a wide range of paper products.
- Good quality: Fourdrinier paper-making can produce high-quality paper with consistent thickness and good surface smoothness.
- Versatility: Fourdrinier paper-making can be used to produce a wide range of paper grades, including printing papers, writing papers, and packaging papers.
- Cost-effective: Fourdrinier paper-making is a cost-effective method of producing paper, especially for high-volume production.
Cons:
- High energy consumption: Fourdrinier paper-making requires a lot of energy to operate, which can increase production costs.
- Water pollution: Fourdrinier paper-making generates a lot of wastewater, which can be a source of water pollution if not treated properly.
- Fiber damage: The mechanical action of Fourdrinier paper-making can damage the fibers in the pulp, reducing the strength and quality of the resulting paper.
- Capital-intensive: Fourdrinier paper machines are expensive to purchase and maintain, making them a significant investment for paper manufacturers.
- Limited flexibility: Fourdrinier paper-making is less flexible than other paper manufacturing techniques, as it requires specialized equipment and infrastructure.
Cylinder Mould Paper-making
Cylinder mould paper-making is a paper-making process that uses a cylindrical mould, which rotates partially submerged in a vat of pulp slurry to form a paper web. The process was developed in France in the early 19th century and was the first machine-made paper process.
The process creates a paper with a unique surface texture and is often used for art papers, watermark paper, and luxury papers.
Here are some of the pros and cons of cylinder mould paper-making:
Pros:
- High paper quality: Cylinder mould paper-making produces high-quality paper with excellent strength, smoothness, and printability.
- Fiber preservation: Cylinder mould paper-making preserves the length and strength of the fibers in the pulp, resulting in the stronger and more durable paper.
- Versatility: Cylinder mould paper-making can produce a wide range of paper grades, including printing papers, writing papers, and specialty papers.
- Eco-friendly: Cylinder mould paper-making generates less wastewater and produces less air pollution than other paper manufacturing techniques.
- Flexibility: Cylinder mould paper-making is more flexible than Fourdrinier paper-making, as it can produce a wider range of paper weights and textures.
Cons:
- Slow production speed: Cylinder mould paper-making is slower than Fourdrinier paper-making, which can increase production costs and limit the production volume.
- Higher cost: Cylinder mould paper-making is generally more expensive than Fourdrinier paper-making, as it requires more specialized equipment and skilled labor.
- Limited paper width: Cylinder mould paper-making is limited in the width of paper that can be produced, which can limit the range of paper products that can be produced.
- Limited scalability: Cylinder mould paper-making is not as easily scalable as Fourdrinier paper-making, which can limit its usefulness for large-scale paper production.
- More frequent maintenance: Cylinder mould paper-making requires more frequent maintenance than Fourdrinier paper-making, which can increase production costs and reduce efficiency.
Twin Wire Paper Making
Twin-wire paper making is a technique used in paper manufacturing where a pulp suspension is simultaneously drained and dewatered using two parallel wires or screens. Here are some pros and cons of this technique:
Pros:
- High-speed production: Twin wire paper making is a high-speed paper manufacturing technique that can produce paper at a faster rate than other traditional paper-making methods.
- Consistent quality: The twin wire paper-making technique produces paper with uniform thickness and texture, resulting in a consistent quality product.
- Reduced energy consumption: This technique requires less energy and has a lower environmental impact compared to other paper manufacturing techniques.
- Reduced water usage: The twin wire paper-making technique uses less water than other paper-making techniques, leading to water conservation.
Cons:
- Initial cost: The initial cost of setting up a twin-wire paper-making facility can be expensive, making it difficult for small-scale paper manufacturers to adopt this technique.
- Maintenance cost: The maintenance cost for the twin wire paper-making technique is higher than other traditional paper-making methods.
- Limited paper types: Twin wire paper making is mainly used for producing printing and writing papers. It may not be suitable for other types of paper products.
- Production limitations: The production capacity of twin wire paper making is limited due to the width of the twin wire machine.
Specialty Paper
Specialty paper is a paper manufacturing technique that involves creating paper products for specific, specialized uses. Here are some of the pros and cons of specialty paper as a paper manufacturing technique:
Pros:
- Higher value: Specialty paper products are often more valuable than standard paper products due to their specialized uses and properties.
- Unique properties: Specialty paper products can have unique properties, such as water resistance, fire resistance, or antimicrobial properties, which can make them well-suited for certain applications.
- Increased revenue: Specialty paper products can create new revenue streams for paper manufacturers, as they often command higher prices than standard paper products.
- Greater durability: Specialty paper products are often designed to be more durable than standard paper products, allowing them to withstand harsh environmental conditions or repeated use.
Cons:
- Higher cost: Specialty paper products can be more expensive to produce than standard paper products due to the additional processing and materials required to create the specialized properties.
- Limited availability: Specialty paper products may be produced in smaller quantities and may be less readily available than standard paper products, which can make them more difficult or expensive to obtain.
- Limited applications: Specialty paper products are often designed for specific, specialized uses, which can limit their versatility and applicability to other uses. Additionally, the specialized properties of some specialty paper products may not be necessary or useful for all applications, which can limit their usefulness.
Coated Paper
Coated paper is a paper manufacturing technique that involves applying a coating of chemicals or materials to one or both sides of the paper. Here are some of the pros and cons of coated paper as a paper manufacturing technique:
Pros:
- Improved print quality: Coated paper produces a smoother, more uniform surface that allows for better ink absorption and improved print quality.
- Enhanced appearance: Coated paper can have a glossier or matte appearance, which can make it more visually appealing for certain applications.
- Greater durability: Coated paper can be more durable than uncoated paper, with better resistance to water, tearing, and wrinkling.
- Better aesthetics: Coated paper can have a more polished, professional appearance than uncoated paper, which can make it well-suited for certain applications, such as high-end catalogs or magazines.
Cons:
- Higher cost: Coated paper can be more expensive to produce than uncoated paper due to the additional processing and materials required to apply the coating.
- Limited recycling potential: Coated paper can be difficult to recycle, as the coating can interfere with the paper fibers and cause contamination.
- Environmental concerns: The chemicals used in coating paper can have environmental impacts if not handled and disposed of properly, potentially leading to water and air pollution.
- Limited applications: Coated paper may not be suitable for all applications, such as writing or printing with certain types of ink or printing methods. Additionally, the coating can sometimes cause problems with adhesion or finishing processes, such as folding or gluing.
Tissue Paper-making
Tissue paper making is a paper manufacturing technique that produces lightweight, highly absorbent, and soft paper products. Here are some potential pros and cons of tissue paper making as a paper manufacturing technique:
Pros:
- High production efficiency: Tissue paper making is a highly automated process that allows for large-scale production with minimal labor requirements.
- Low raw material usage: Tissue paper-making requires less fiber than other paper-making processes, which reduces the amount of raw material required.
- Low energy consumption: Tissue paper-making uses less energy than other paper-making processes, as the paper does not need to be dried to the same extent.
- Versatility: Tissue paper can be used for a wide range of products, including facial tissues, toilet paper, and paper towels, making it a versatile paper product.
- Softness and absorbency: Tissue paper is known for its softness and absorbency, making it ideal for use in personal hygiene products.
Cons:
- Chemical use: Tissue paper making may require the use of chemicals such as bleach to achieve the desired brightness or color, which can be harmful to the environment if not managed properly.
- Water usage: Tissue paper making requires a significant amount of water, which can be a strain on water resources if not managed properly.
- Short lifespan: Tissue paper products are typically used once and then disposed of, leading to a short lifespan and contributing to waste and environmental pollution.
- Lower strength: Tissue paper products are typically less durable and have lower strength compared to other paper products, which can limit their use in certain applications.
- Limited recyclability: Due to their short fibers and the chemicals used in their production, tissue paper products may not be easily recyclable, which can contribute to waste and environmental pollution.
Deinking
Deinking is a paper manufacturing technique that involves removing ink and other contaminants from recycled paper to produce a clean pulp for use in new paper products. Here are some of the pros and cons of deinking as a paper manufacturing technique:
Pros:
- Increased use of recycled paper: Deinking allows for the production of high-quality recycled paper products, which reduces the need for virgin fibers and the associated environmental impacts of harvesting and processing trees.
- Improved quality: Deinking can improve the quality of recycled paper products by removing contaminants that can affect the strength and appearance of the paper.
- Cost-effective: Using deinked pulp can be cost-effective, as it reduces the need for virgin pulp and can be less expensive than other sources of fiber.
Cons:
- High energy use: Deinking can be an energy-intensive process, requiring significant amounts of water, chemicals, and electricity to remove ink and other contaminants from recycled paper.
- Limited effectiveness: Deinking may not be effective at removing all types of contaminants from recycled paper, which can limit the quality of the resulting pulp and paper products.
- Chemical waste: Deinking can produce chemical waste, such as sludge, which can be difficult and expensive to dispose of safely. Additionally, some of the chemicals used in deinking, such as peroxide or chlorine, can be harmful to human health and the environment if not handled properly.
Bleaching
Bleaching is a paper manufacturing technique that involves treating pulp with chemicals to remove impurities and create a brighter, whiter paper product. Here are some of the pros and cons of bleaching as a paper manufacturing technique:
Pros:
- Improved paper quality: Bleaching can improve the brightness and whiteness of paper products, resulting in a higher quality and more visually appealing product.
- Increased versatility: Bleaching can make a paper more suitable for a wider range of applications, including printing and writing, as well as specialty uses such as tissue and packaging.
- Improved pulp yield: Bleaching can increase the yield of usable pulp from a given amount of wood or other fiber, resulting in more efficient use of resources.
Cons:
- Environmental concerns: The chemicals used in bleaching, such as chlorine, can have environmental impacts if not handled and disposed of properly, potentially leading to water and air pollution.
- Energy consumption: Bleaching can be an energy-intensive process, requiring significant amounts of electricity and water to achieve the desired level of brightness and whiteness.
- Cost: Bleaching can be expensive due to the additional processing and chemicals required, which can increase the cost of the final paper product.
Calendering
Calendering is a paper manufacturing technique that involves passing the paper through rollers to create a smooth, uniform surface. Here are some of the pros and cons of calendering as a paper manufacturing technique:
Pros:
- Improved paper surface: Calendering can create a smooth, uniform surface on paper, which can improve its printability and appearance.
- Increased durability: Calendering can make the paper more resistant to wear and tear, as well as water and other liquids.
- Versatility: Calendering can be used on a wide range of paper grades and types, including printing and writing paper, as well as specialty paper products.
Cons:
- Reduced bulk: Calendering can reduce the thickness and bulk of the paper, which can affect its weight, opacity, and stiffness.
- Higher cost: Calendering can be more expensive than other paper manufacturing techniques due to the additional processing and equipment required.
- Environmental concerns: Calendering can be an energy-intensive process, requiring significant amounts of electricity and potentially leading to increased carbon emissions. Additionally, the rollers used in calendering can wear down over time, creating waste that must be disposed of properly.
Drying
Drying is a critical step in the paper manufacturing process, as it removes the water from the wet pulp to create a finished paper product. Here are some of the pros and cons of drying as a paper manufacturing technique:
Pros:
- Increased efficiency: Efficient drying methods can help to reduce the amount of time and energy required to produce a finished paper product.
- Improved paper quality: Proper drying techniques can help to ensure a uniform paper product with the desired moisture content, resulting in a higher quality product.
- Reduced transportation costs: Drying can reduce the weight and volume of paper products, which can help to reduce transportation costs.
Cons:
- Energy consumption: Drying can be an energy-intensive process, requiring significant amounts of heat and electricity to remove the water from the pulp.
- Environmental concerns: The energy required for drying can contribute to carbon emissions and other environmental impacts if not managed properly.
- Potential for damage: Improper drying techniques can lead to defects in the finished paper product, such as warping or curling, which can reduce its value and usability.
Converting
Converting is a paper manufacturing technique that involves transforming large rolls or sheets of paper into finished products, such as envelopes, labels, and packaging. Here are some of the pros and cons of converting as a paper manufacturing technique:
Pros:
- Customization: Converting allows for a high degree of customization, as paper can be cut, folded, and printed to meet specific customer needs and requirements.
- Efficiency: Converting can improve efficiency by reducing waste and optimizing the use of raw materials.
- Flexibility: Converting can be used to produce a wide range of paper products, from simple envelopes to complex packaging solutions.
Cons:
- Cost: Converting can be a costly process, requiring specialized equipment and skilled labor.
- Quality concerns: Improper converting techniques can lead to defects in the finished product, such as misaligned printing or inconsistent folding, which can reduce its value and usability.
- Environmental concerns: The waste generated during the converting process can contribute to environmental issues if not properly managed and disposed of. Additionally, the use of inks, adhesives, and other materials in converting can have environmental impacts if not managed properly.
Upcoming Trends in Paper Manufacturing Techniques
The paper manufacturing industry is continually evolving, driven by advancements in technology, changing consumer preferences, and sustainability concerns. Here are some upcoming trends in paper manufacturing techniques:
- Digitalization and automation: The paper industry is adopting digital and automated systems to improve efficiency, reduce costs, and minimize errors. Machine learning and artificial intelligence are being used to optimize processes, reduce downtime, and improve product quality.
- Sustainable practices: Sustainability is a key concern in the paper industry, and many companies are adopting eco-friendly practices. This includes using renewable energy sources, reducing water consumption, and using recycled materials.
- Use of alternative fibers: As sustainability becomes increasingly important, there is a growing interest in using alternative fibers for paper production. This includes agricultural waste, such as straw and sugarcane bagasse, as well as recycled textiles and synthetic fibers.
- Smart packaging: With the rise of e-commerce and online shopping, there is a growing demand for smart packaging solutions. These can include active and intelligent packaging that can monitor and report on the condition of products during shipping and storage.
- Customization and personalization: Consumers are increasingly looking for unique and personalized products, and the paper industry is responding by offering customized printing and design services.
Overall, the paper manufacturing industry is constantly adapting to changing market demands and technological advancements. The trends outlined above are just a few examples of how the industry is evolving to meet the needs of customers while also addressing environmental concerns.
Factors for Determining the Most Suitable Paper Manufacturing Technique for Your Business
There are several factors that can determine the most suitable paper manufacturing technique for a business. These factors include:
- Type of paper product: The type of paper product that a business intends to produce can determine the most suitable paper manufacturing technique. For instance, some paper products, such as tissue paper and newsprint, may require a different manufacturing process compared to premium paper products, such as printing paper and specialty paper.
- Required production volume: The required production volume can also determine the most suitable manufacturing technique. Some techniques are more suitable for high-volume production, while others are better suited for lower volumes.
- Cost considerations: The cost of production can also be a factor in determining the most suitable manufacturing technique. Some techniques may require more expensive equipment or raw materials, which can increase the cost of production.
- Environmental considerations: Environmental concerns can also play a role in determining the most suitable manufacturing technique. Some techniques may have a higher environmental impact than others, and a business may prioritize using techniques that are more sustainable and environmentally friendly.
- Quality requirements: The quality requirements of the paper product can also be a factor in determining the most suitable manufacturing technique. Some techniques may be better suited for producing high-quality paper products than others.
Overall, it is important for a business to consider these and other relevant factors when selecting a paper manufacturing technique that is best suited for their needs.
How can Deskera Help You with Paper Manufacturing?
Deskera MRP can help paper manufacturing companies in a variety of ways:
- Material Requirements Planning (MRP): Deskera's MRP software can help paper manufacturers plan their production schedules, manage inventory levels, and track raw materials and finished products. This can help paper manufacturers optimize their production processes and reduce waste.
- Sales and Customer Relationship Management (CRM): Deskera's CRM software can help paper manufacturers manage their sales pipelines, track customer interactions, and generate sales forecasts. This can help paper manufacturers improve their customer engagement and increase sales.
- Accounting and Finance Management: Deskera's accounting and finance management software, i.e., Deskera Books, can help paper manufacturers manage their financial transactions, generate financial reports, and track expenses. This can help paper manufacturers streamline their financial processes and improve their financial performance.
- Human Resource Management (HRM): Deskera People can help paper manufacturers manage their employee data, track attendance and leave, and process payroll. This can help paper manufacturers manage their workforce more efficiently and effectively.
- Business Intelligence (BI): Deskera is a BI software that can help paper manufacturers analyze their data, generate insights, and make informed business decisions. This can help paper manufacturers improve their operational efficiency and drive growth.
Key Takeaways
There are several paper manufacturing techniques available, each with its own set of pros and cons. The choice of technique depends on the desired end product, the cost, and the environmental impact.
The different paper manufacturing techniques whose pros and cons you must consider are:
- Mechanical pulping
- Chemical pulping
- Kraft process
- Sulfite process
- Recycled paper
- Fourdrinier paper-making
- Cylinder mould paper-making
- Twin-wire paper-making
- Specialty paper
- Coated paper
- Tissue paper-making
- Deinking
- Bleaching
- Calendering
- Drying
- Converting
The several factors that you must consider in addition to the pros and cons of the different paper manufacturing techniques to decide the most suitable technique for your business are:
- Type of paper product
- Required production volume
- Cost considerations
- Environmental considerations
- Quality requirements
Overall, Deskera can help paper manufacturers improve productivity, reduce costs, and ensure efficient operations by providing a unified view of the entire production process.
Related Articles
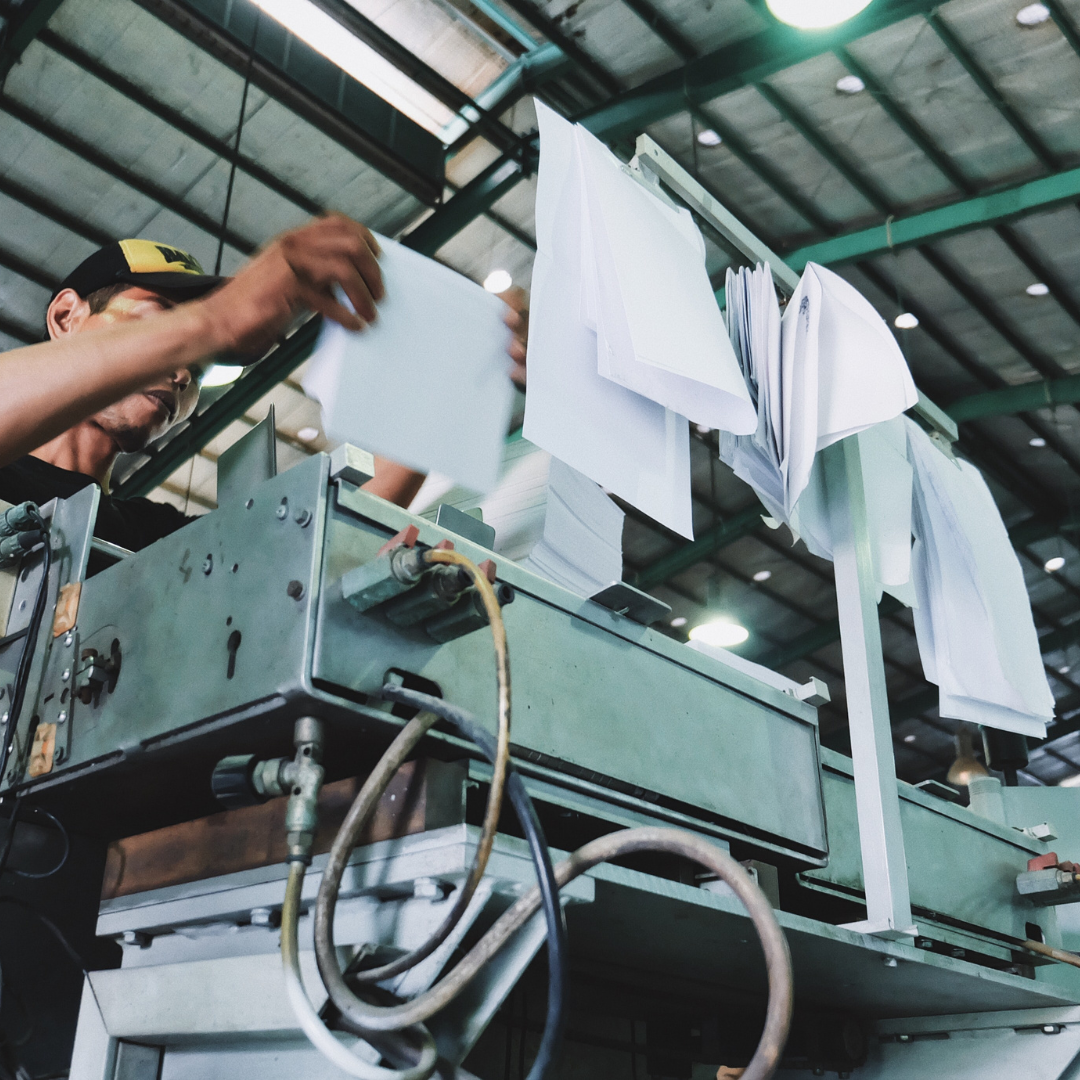
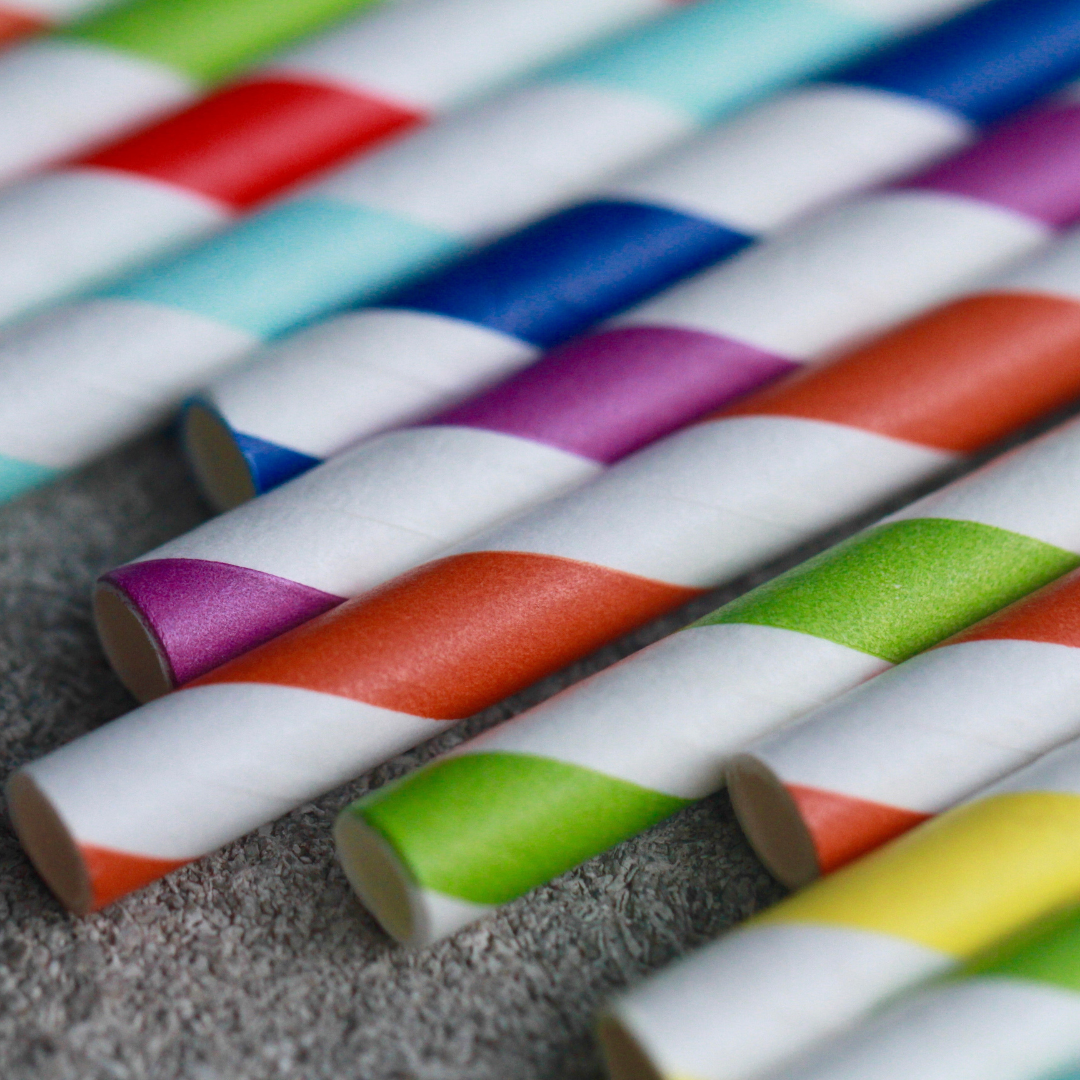
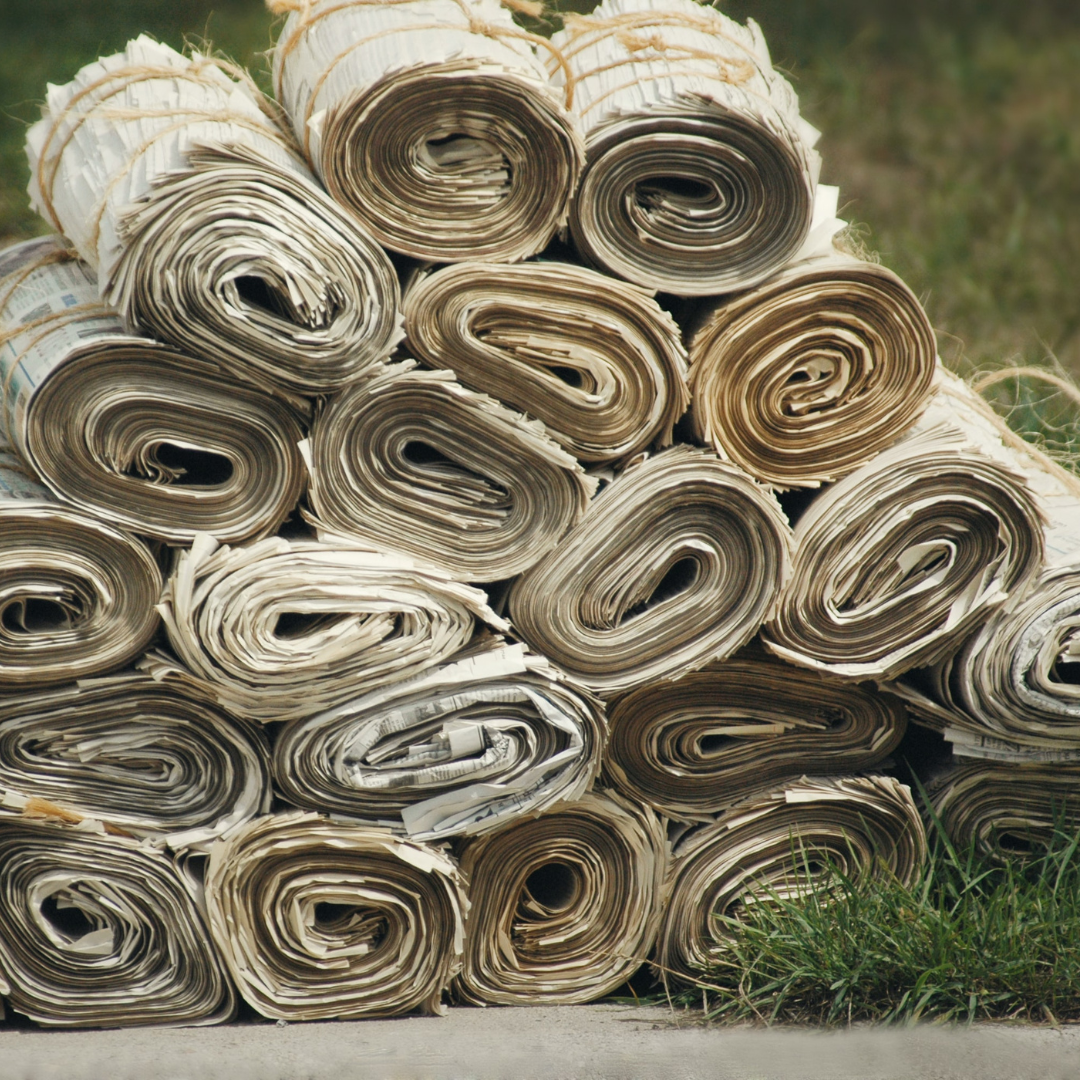
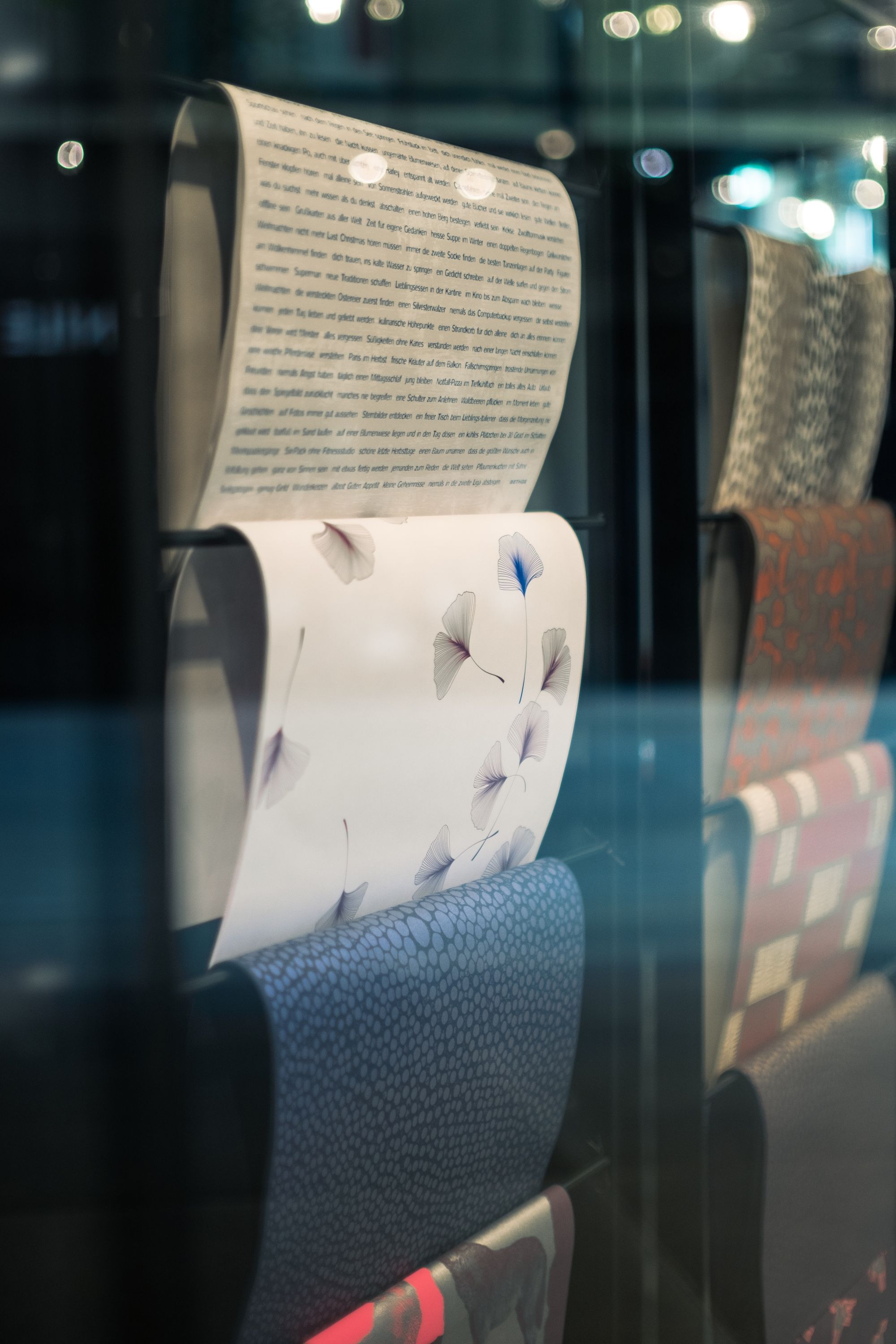
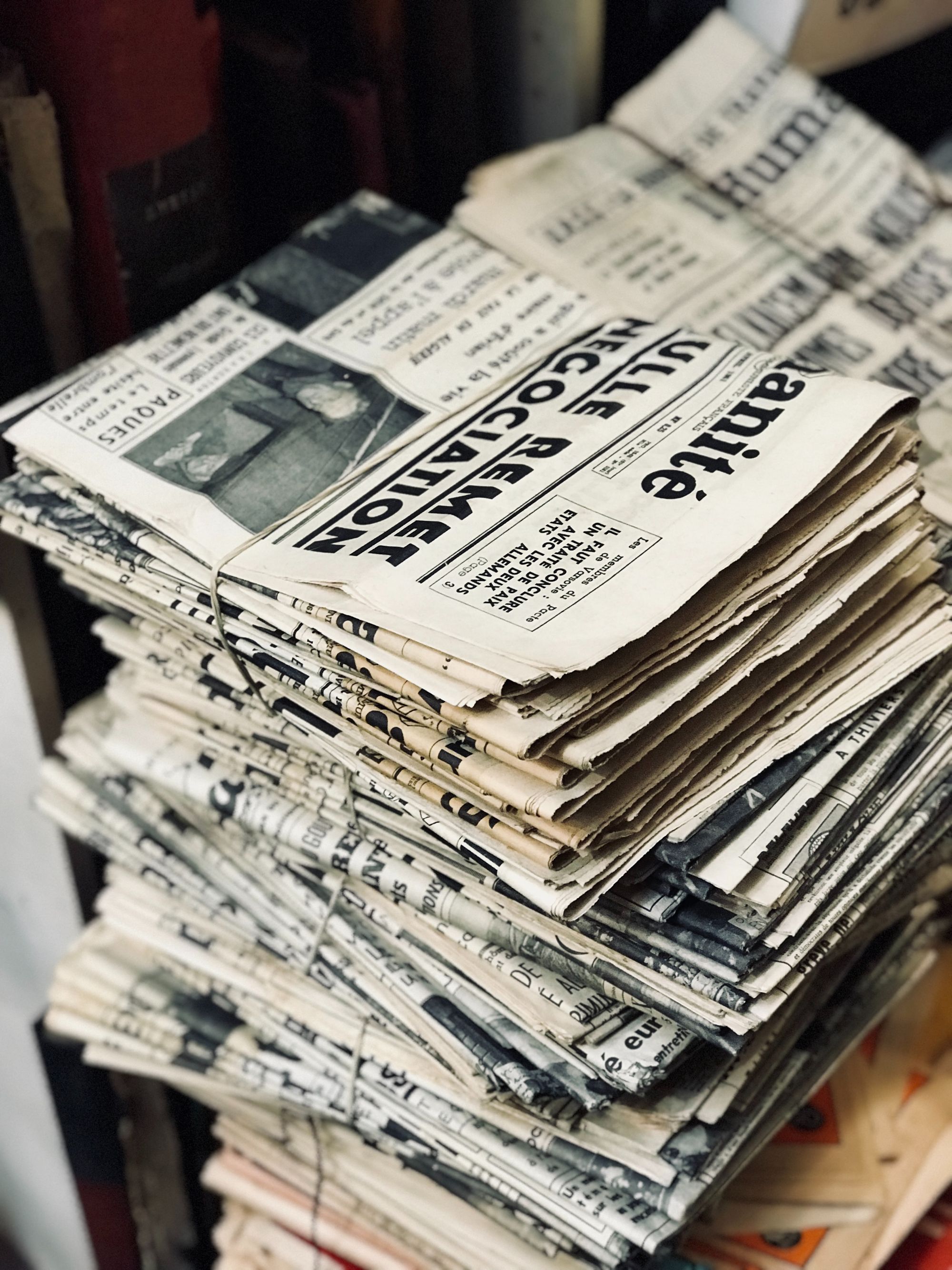
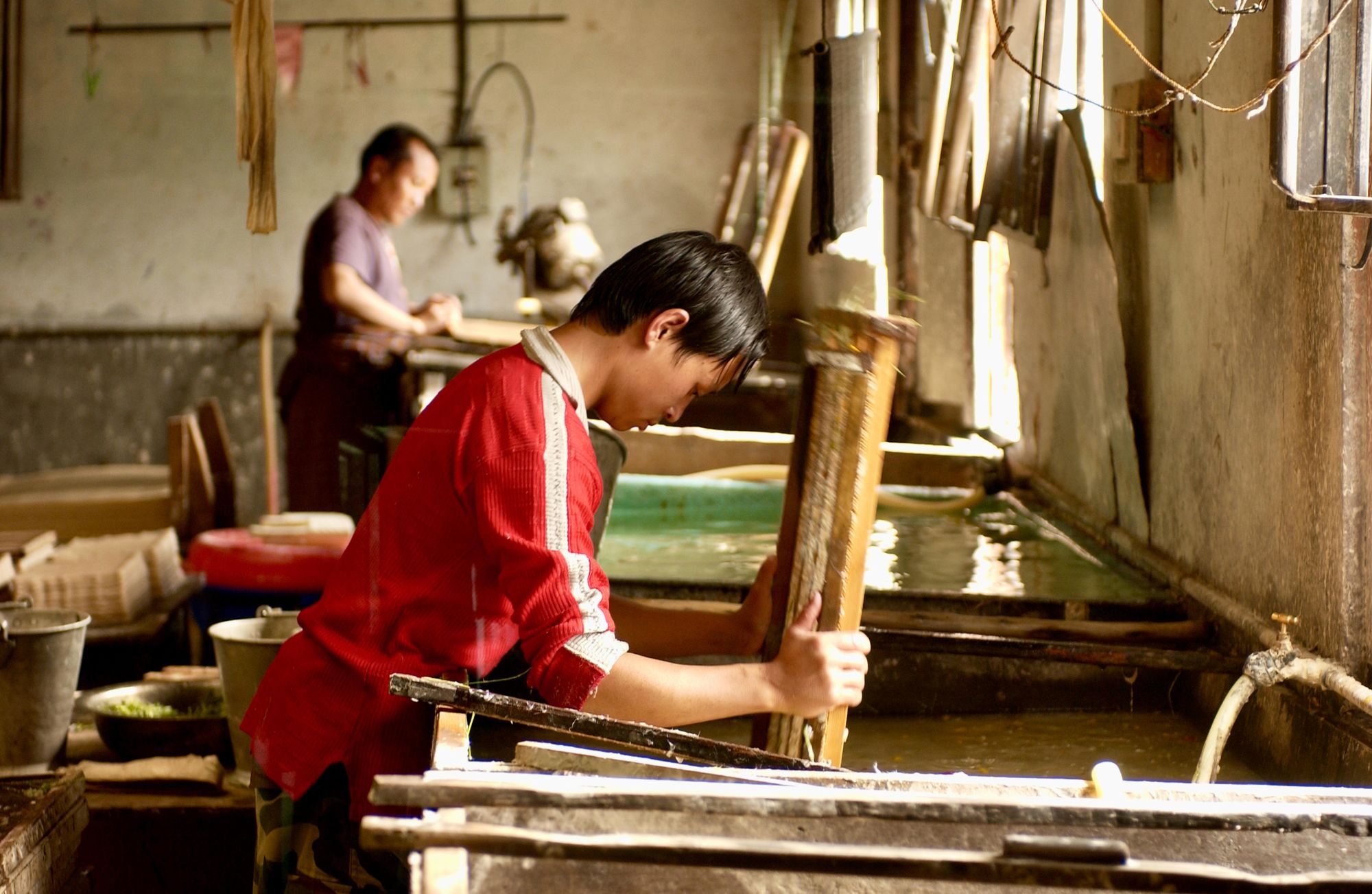