Effective inventory control plays a pivotal role in the success and sustainable growth of manufacturing companies. It empowers executives to optimize resources, reduce costs, and enhance operational efficiency while ensuring customer satisfaction.
In today's increasingly competitive and environmentally conscious business landscape, manufacturing executives must embrace inventory control strategies that align with sustainability goals.
According to a recent study by the Council of Supply Chain Management Professionals, approximately 7.4% of a company's revenue is tied up in inventory on average. Furthermore, inefficient inventory management can result in increased carrying costs, wastage, and missed sales opportunities. Hence, manufacturing executives need to take proactive measures to optimize inventory control and drive sustainable growth.
This article explores how manufacturing executives can optimize inventory control for sustainable growth. It will delve into the key elements of effective inventory control, the role of executives in driving optimization efforts, and strategies for minimizing excess inventory while maximizing supply chain efficiency.
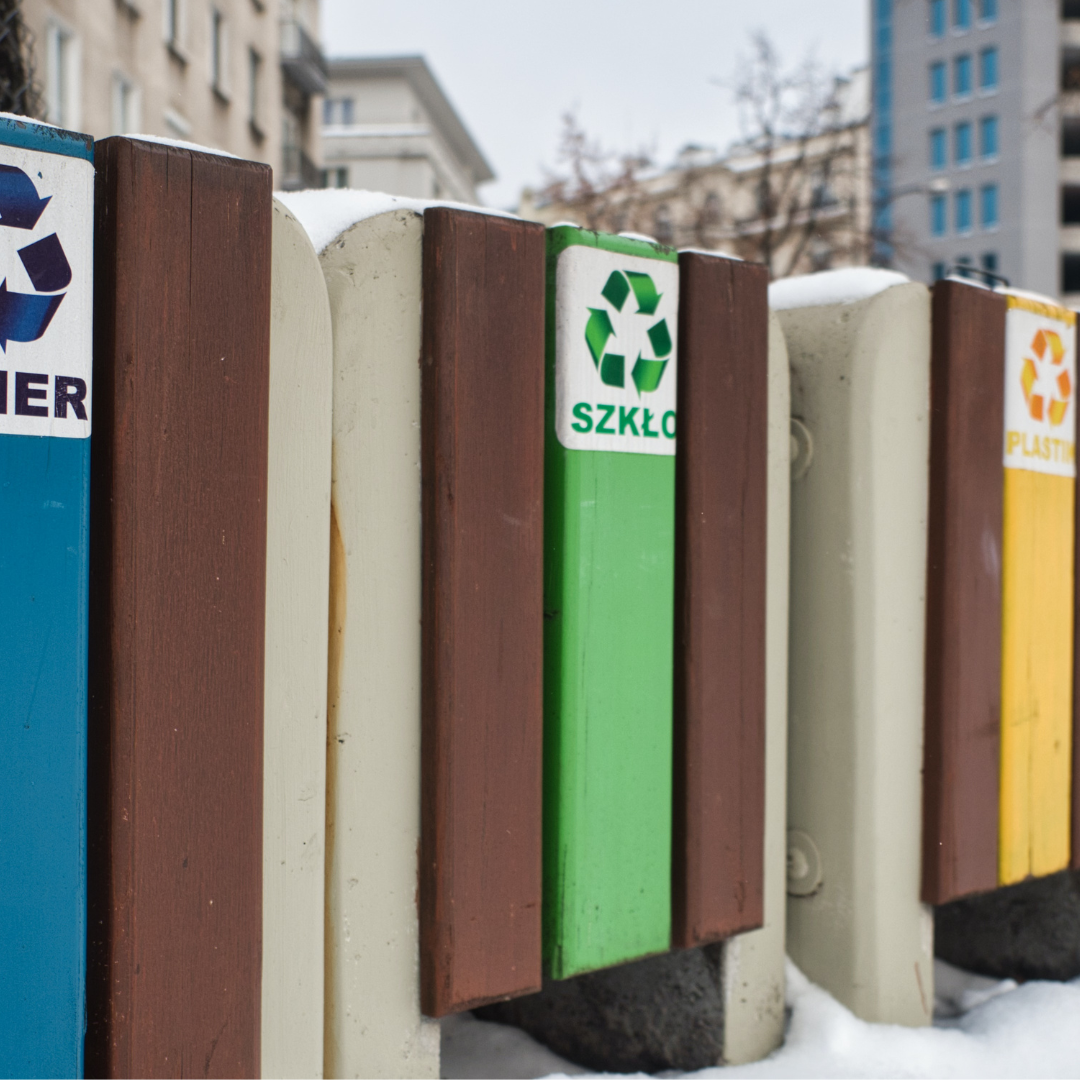
Additionally, it will highlight the importance of technology adoption, data-driven decision-making, and collaboration in achieving inventory control excellence. By implementing these practices, manufacturing executives can unlock significant operational benefits, reduce environmental impact, and position their organizations for long-term success.
Here is a list of topics we shall cover in this post:
- Importance of Inventory Control for Manufacturing Executives
- Need for Sustainable Growth in the Manufacturing Sector
- Understanding Inventory Control
- The Role of Manufacturing Executives in Inventory Control
- Optimizing Inventory Control for Sustainable Growth
- Overcoming Challenges in Inventory Control Optimization
- Case Studies and Best Practices
- Prioritizing Inventory Control for Sustainable Growth
- Future Outlook and Emerging Trends in Inventory Control
- Conclusion
- How can Deskera Help You?
- Key Takeaways
- Related Articles
Importance of Inventory Control for Manufacturing Executives
Inventory control is of paramount importance for manufacturing executives as it directly impacts the overall success and profitability of their organizations. By effectively managing inventory, manufacturing executives can optimize resources, minimize costs, enhance customer satisfaction, and drive sustainable growth.
One key reason why inventory control is crucial is the financial aspect. Inventory ties up a significant portion of a company's capital, and inefficient inventory management can lead to increased carrying costs, obsolescence, and wastage. By implementing robust inventory control measures, manufacturing executives can minimize excess inventory, improve cash flow, and free up capital for other critical business activities.
Moreover, inventory control plays a vital role in meeting customer demands and ensuring high service levels. By accurately forecasting demand and optimizing inventory levels, manufacturing executives can prevent stockouts and backorders, thus enhancing customer satisfaction and loyalty. This, in turn, leads to repeat business and positive word-of-mouth recommendations.
Inventory control also contributes to operational efficiency. By categorizing and classifying inventory based on demand patterns, executives can identify fast-moving and slow-moving items, allowing for better production planning and order management. This optimization helps streamline manufacturing processes, reduce lead times, minimize waste, and improve overall productivity.
Additionally, effective inventory control aligns with sustainability goals. By minimizing excess inventory and optimizing supply chain operations, manufacturing executives can reduce their organization's environmental impact. This includes reducing waste, energy consumption, and carbon emissions associated with manufacturing and storage processes.
Inventory control is a critical function for manufacturing executives as it directly influences financial performance, customer satisfaction, operational efficiency, and sustainability. By implementing robust inventory control strategies, manufacturing executives can achieve optimal inventory levels, enhance cash flow, meet customer demands, and drive sustainable growth in today's competitive business landscape.
Need for Sustainable Growth in the Manufacturing Sector
The manufacturing sector plays a significant role in global economic development, but it also has a substantial impact on the environment and society. The need for sustainable growth in the manufacturing sector arises from various interconnected factors.
- Environmental Impact: Manufacturing processes often consume vast amounts of energy and natural resources while generating substantial waste and emissions. Unsustainable manufacturing practices contribute to climate change, pollution, and resource depletion. To mitigate these negative impacts, the manufacturing sector must transition towards sustainable practices that minimize environmental harm.
- Regulatory Compliance: Governments around the world are implementing stricter environmental regulations and standards. Non-compliance can result in fines, penalties, and reputational damage. To ensure long-term viability, manufacturing companies must adopt sustainable practices that align with regulatory requirements and promote environmental stewardship.
- Resource Efficiency: Sustainable growth in the manufacturing sector requires optimizing the use of resources. This includes minimizing waste generation, reducing energy consumption, and maximizing the utilization of raw materials. By adopting resource-efficient practices, manufacturers can reduce costs, enhance operational efficiency, and contribute to a more circular economy.
- Consumer Expectations: Modern consumers are increasingly conscious of sustainability and prefer products that are ethically produced and environmentally friendly. Manufacturers that prioritize sustainable practices gain a competitive edge by meeting consumer demands and building trust. Sustainable growth allows manufacturers to tap into new market segments, enhance brand reputation, and foster customer loyalty.
- Supply Chain Resilience: Sustainability is closely linked to supply chain resilience. As climate change and resource scarcity pose risks to the availability and affordability of raw materials, manufacturers need to ensure a resilient supply chain. This involves diversifying sourcing, reducing dependence on limited resources, and fostering partnerships with sustainable suppliers.
- Social Responsibility: Manufacturing companies have a social responsibility to their employees, local communities, and society as a whole. Sustainable growth includes considerations such as fair labor practices, worker safety, community engagement, and supporting social initiatives. By incorporating social responsibility into their operations, manufacturers can enhance their reputation and attract and retain top talent.
By integrating sustainability into their strategies, manufacturing companies can not only reduce their environmental footprint but also achieve long-term profitability, competitiveness, and resilience in a rapidly evolving global landscape.
Understanding Inventory Control
Inventory control is a vital aspect of efficient and successful operations for manufacturing executives. By effectively managing inventory, executives can optimize resources, reduce costs, and enhance customer satisfaction.
This section delves into the fundamental principles and key elements of inventory control, providing a comprehensive understanding of its scope and importance. From demand forecasting and planning to inventory tracking and optimization techniques, manufacturing executives will gain valuable insights into how to achieve optimal inventory control.
By mastering the intricacies of inventory control, executives can make informed decisions, streamline operations, and drive sustainable growth for their organizations.
A. Definition and scope of inventory control
Inventory control refers to the strategic management and supervision of a company's inventory levels to ensure efficient operations, minimize costs, and meet customer demands. It involves maintaining the right balance of inventory, neither excessive nor insufficient, to support production and fulfill customer orders effectively.
The scope of inventory control encompasses various aspects, including:
- Inventory Classification and Categorization: This involves categorizing inventory based on factors such as demand patterns, value, and criticality. It helps prioritize inventory management efforts, allocate resources effectively, and identify fast-moving and slow-moving items.
- Demand Forecasting and Planning: Accurate forecasting of customer demand is crucial for inventory control. It involves analyzing historical data, market trends, and customer insights to anticipate future demand levels. By forecasting demand, manufacturing executives can align production schedules, optimize inventory levels, and avoid stockouts or excess inventory.
- Efficient Order Management: Effective order management is integral to inventory control. It involves efficiently processing and fulfilling customer orders, coordinating with suppliers, and optimizing order quantities to minimize inventory carrying costs and lead times.
- Inventory Tracking and Monitoring: Real-time tracking and monitoring of inventory enable manufacturing executives to have visibility into stock levels, location, and movement. It helps prevent stockouts, identify potential bottlenecks, and ensure inventory accuracy.
- Inventory Optimization Techniques: Inventory optimization involves using various strategies and techniques to achieve optimal inventory levels. This may include implementing just-in-time (JIT) manufacturing, adopting demand-driven production models, leveraging technology solutions, and applying data analytics for inventory decision-making.
Understanding the definition and scope of inventory control provides manufacturing executives with a foundation for implementing effective inventory management strategies. By comprehending the various components and considerations involved, executives can optimize inventory levels, minimize costs, enhance operational efficiency, and meet customer demands consistently.
B. Key elements of effective inventory control
Effective inventory control relies on several key elements that enable manufacturing executives to optimize resources, reduce costs, and improve operational efficiency. This section delves into the essential components of successful inventory control, providing insights into the strategies and practices that drive inventory management excellence.
From demand forecasting and planning to inventory classification and optimization techniques, manufacturing executives will gain a comprehensive understanding of the crucial elements necessary for achieving optimal inventory control.
Demand Forecasting and Planning: Accurate demand forecasting involves analyzing historical data, market trends, and customer insights to anticipate future demand levels. By aligning production schedules and inventory levels with projected demand, manufacturing executives can optimize resource allocation, reduce stockouts, and avoid excess inventory.
Inventory Classification and Categorization: Categorizing inventory based on demand patterns, value, and criticality helps prioritize management efforts. Fast-moving items require closer monitoring and higher stock levels, while slow-moving items may warrant adjustments in procurement strategies. Classification enables efficient allocation of resources, identification of obsolete stock, and effective inventory replenishment strategies.
Efficient Order Management: Efficient order management involves streamlining the processes associated with customer orders. This includes order processing, coordination with suppliers, and optimization of order quantities. By minimizing lead times and carrying costs, executives can improve customer satisfaction, reduce inventory holding, and enhance operational efficiency.
Inventory Tracking and Monitoring: Real-time tracking and monitoring of inventory provide visibility into stock levels, location, and movement. This enables executives to prevent stockouts, identify potential bottlenecks, and ensure accurate inventory records. Monitoring also facilitates timely reordering, inventory accuracy, and effective management of stock in different locations or channels.
Inventory Optimization Techniques: Inventory optimization techniques involve employing strategies to achieve optimal inventory levels. This includes implementing just-in-time (JIT) manufacturing, adopting demand-driven production models, leveraging technology solutions, and utilizing data analytics to make informed inventory decisions.
These techniques help minimize carrying costs, reduce waste, and improve overall supply chain efficiency.
The Role of Manufacturing Executives in Inventory Control
Manufacturing executives play a pivotal role in driving effective inventory control within their organizations. Their leadership, strategic planning, and decision-making abilities significantly impact the optimization of inventory levels, resource allocation, and overall operational efficiency.
This section explores the critical responsibilities and contributions of manufacturing executives in inventory control. From setting strategic objectives to collaborating with cross-functional teams and aligning inventory control with sustainability goals, executives have the power to shape and implement strategies that drive success.
A. Leadership and strategic planning
Leadership and strategic planning are fundamental aspects of the manufacturing executive's role in inventory control. Effective leadership sets the vision, direction, and priorities for inventory management initiatives within the organization. It involves guiding the team, establishing clear goals, and fostering a culture of excellence and continuous improvement.
Manufacturing executives must develop strategic plans that align inventory control with broader organizational objectives. This includes setting inventory turnover targets, optimizing working capital, and balancing customer service levels. They must also ensure that inventory control strategies are integrated into the overall business strategy and align with the organization's financial and operational goals.
Leadership in inventory control requires executives to inspire and empower their teams. They must encourage collaboration, promote cross-functional communication, and foster a culture of accountability. By providing guidance, resources, and support, executives can enable their teams to implement effective inventory control practices and drive continuous improvement.
Strategic planning entails evaluating market trends, customer demands, and internal capabilities to determine the optimal inventory levels and replenishment strategies. It involves analyzing data, conducting risk assessments, and making informed decisions regarding inventory investments, production schedules, and supplier relationships.
Manufacturing executives must also stay updated on industry trends, emerging technologies, and best practices in inventory control. By actively seeking knowledge and fostering a learning mindset, executives can make informed decisions, anticipate market changes, and drive innovation in inventory management.
In summary, effective leadership and strategic planning are critical for manufacturing executives in inventory control. By providing vision, direction, and support, executives can shape the inventory management strategy, foster a culture of excellence, and drive the organization towards optimal inventory control and sustainable growth.
B. Collaboration with cross-functional teams
Collaboration with cross-functional teams is a crucial aspect of the manufacturing executive's role in inventory control. Effective inventory management requires coordination and cooperation among various departments and stakeholders within the organization. By fostering collaboration, executives can optimize processes, enhance communication, and drive continuous improvement throughout the supply chain.
Manufacturing executives must establish strong working relationships with teams such as procurement, production, sales, finance, and logistics. Collaborating with these teams ensures that inventory control strategies are aligned with the broader organizational goals and objectives. It allows for a holistic approach to inventory management that considers factors such as production capacity, sales forecasts, financial constraints, and customer demands.
Cross-functional collaboration enables better demand forecasting and planning. By actively engaging sales and marketing teams, executives can gather market insights, customer feedback, and sales forecasts that provide valuable inputs for inventory planning. Collaborative demand planning helps align production schedules, optimize inventory levels, and reduce the risk of stockouts or excess inventory.
Collaboration with procurement teams is vital in inventory control. By working closely with procurement, executives can optimize supplier relationships, ensure timely and cost-effective replenishment, and mitigate supply chain risks. Collaborative efforts can involve sharing demand forecasts, supplier performance metrics, and jointly identifying opportunities for cost savings or process improvements.
Furthermore, collaboration with finance teams is essential to ensure that inventory control strategies align with financial objectives. Executives need to work closely with finance departments to monitor inventory costs, analyze inventory turnover ratios, and optimize working capital. Collaborative financial analysis can help identify areas of improvement, cost-saving opportunities, and ensure that inventory management practices align with profitability goals.
Effective cross-functional collaboration also involves regular communication, sharing of information, and establishing efficient workflows. By breaking down silos and fostering open communication channels, executives can facilitate timely decision-making, problem-solving, and the implementation of inventory control initiatives.
In summary, collaboration with cross-functional teams is vital for manufacturing executives in inventory control. By fostering strong relationships, promoting open communication, and leveraging the expertise of different departments, executives can drive synergistic efforts, optimize processes, and achieve optimal inventory control across the organization.
C. Alignment with sustainability goals
Manufacturing executives have a critical role to play in aligning inventory control practices with sustainability goals. As the global focus on environmental and social responsibility grows, integrating sustainable practices into inventory management becomes increasingly important for long-term success.
By aligning inventory control with sustainability goals, manufacturing executives can reduce environmental impact, enhance brand reputation, and contribute to a more sustainable future.
One aspect of aligning inventory control with sustainability is reducing waste. Executives can implement strategies such as lean manufacturing, just-in-time (JIT) production, and waste reduction initiatives to minimize excess inventory, reduce material waste, and optimize resource usage.
By avoiding overproduction and closely monitoring inventory levels, executives can contribute to a more circular and resource-efficient economy.
Another key consideration is selecting sustainable suppliers. Executives can collaborate with procurement teams to evaluate supplier practices, such as ethical sourcing, responsible manufacturing processes, and adherence to environmental standards. By partnering with sustainable suppliers, manufacturing executives can ensure that the entire supply chain aligns with sustainability goals.
Moreover, executives can leverage technology and data analytics to improve sustainability in inventory control. Implementing inventory management systems and using real-time data can enhance accuracy in demand forecasting, leading to optimized inventory levels and reduced waste.
Additionally, technology solutions can enable efficient transportation planning, route optimization, and carbon footprint tracking, contributing to overall supply chain sustainability.
Manufacturing executives can also promote product lifecycle management, considering sustainability aspects from design to disposal. By encouraging the development of eco-friendly products, implementing recycling or take-back programs, and exploring sustainable packaging options, executives can reduce the environmental impact associated with their products and their associated inventory.
Furthermore, executives can educate and engage employees in sustainability initiatives. By fostering a culture of sustainability and providing training on responsible inventory management practices, executives can empower employees to contribute to environmental and social responsibility goals.
By aligning inventory control with sustainability goals, manufacturing executives can demonstrate corporate social responsibility, attract eco-conscious customers, and enhance their brand reputation. It also positions the organization for long-term success by mitigating environmental risks, complying with regulations, and capitalizing on emerging market opportunities driven by sustainability.
D. Technology adoption and automation
Manufacturing executives play a pivotal role in driving technology adoption and automation in inventory control. The integration of advanced technologies can revolutionize inventory management processes, enhance efficiency, and improve decision-making. By leveraging technology and automation, executives can optimize inventory control, streamline operations, and achieve sustainable growth.
One key aspect of technology adoption is implementing inventory management systems. These systems enable real-time tracking of inventory levels, automate order processing, and provide valuable insights through data analytics. By centralizing inventory data and automating routine tasks, executives can make informed decisions, reduce manual errors, and improve overall inventory accuracy.
Manufacturing executives can also leverage automated demand forecasting and planning tools. These tools use historical data, market trends, and algorithms to generate accurate demand forecasts, optimize inventory levels, and align production schedules. By adopting automated forecasting solutions, executives can enhance accuracy, responsiveness, and agility in meeting customer demands while minimizing inventory carrying costs.
Furthermore, technology-enabled automation can streamline order management processes. Executives can implement electronic data interchange (EDI) systems, barcode scanning, and automated order fulfillment processes to reduce lead times, eliminate manual errors, and enhance order accuracy. Automation not only improves operational efficiency but also enhances customer satisfaction by ensuring timely and error-free order processing.
Manufacturing executives can also explore the benefits of technology-driven optimization techniques. This includes implementing advanced inventory optimization algorithms that consider factors like demand variability, lead times, and cost constraints to determine optimal order quantities and reorder points. By leveraging these tools, executives can reduce excess inventory, minimize stockouts, and achieve better resource utilization.
In addition, emerging technologies such as Internet of Things (IoT) and RFID (Radio Frequency Identification) can enable real-time inventory tracking and monitoring. By deploying sensors and RFID tags, executives can gain visibility into inventory movements, location accuracy, and automate inventory reconciliation processes. This promotes proactive decision-making, reduces stock discrepancies, and enables effective supply chain management.
Manufacturing executives need to foster a culture of technological innovation and provide the necessary resources and training to employees. By encouraging collaboration with IT departments and embracing continuous improvement, executives can drive technology adoption, maximize the benefits of automation, and ensure a smooth transition to digital inventory management processes.
In summary, technology adoption and automation are key areas of focus for manufacturing executives in inventory control. Technology adoption enhances decision-making, improves operational performance, and paves the way for future growth and competitiveness in the manufacturing sector.
Optimizing Inventory Control for Sustainable Growth
Achieving sustainable growth is a priority for manufacturing executives, and optimizing inventory control plays a pivotal role in this pursuit. This section delves into strategies and best practices that enable executives to optimize inventory control for sustainable growth.
From embracing lean principles and adopting advanced technologies to fostering a culture of continuous improvement, executives will gain valuable insights into how to drive efficiency, reduce waste, and align inventory management practices with sustainability goals.
A. Minimizing excess inventory
Here are some ways in which manufacturers can minimize inventory.
Just-in-Time (JIT) Manufacturing:
Just-in-Time (JIT) manufacturing is a strategy aimed at minimizing excess inventory by producing goods or components in response to specific customer demand. With JIT, manufacturing executives closely synchronize production with customer orders, ensuring that products are produced only when needed. By adopting JIT principles, manufacturing executives can achieve several benefits in minimizing excess inventory:
- Reduced carrying costs: JIT manufacturing minimizes the need for storing excessive inventory, resulting in lower carrying costs such as storage space, insurance, and inventory holding expenses.
- Improved cash flow: By reducing excess inventory, JIT manufacturing enables manufacturing executives to free up capital that would otherwise be tied up in inventory. This improves cash flow and provides more financial flexibility for the organization.
- Enhanced responsiveness: JIT manufacturing allows for quicker response to changes in customer demand. By producing goods closer to the time of actual demand, manufacturing executives can better align inventory levels with real-time customer requirements, minimizing the risk of excess inventory.
Demand-Driven Production:
Demand-driven production focuses on aligning production levels with actual customer demand, reducing the need for excessive inventory. Manufacturing executives leverage demand forecasting, market insights, and real-time data to drive production decisions.
Key benefits of demand-driven production in minimizing excess inventory include:
- Improved customer satisfaction: By producing goods based on actual customer demand, manufacturing executives can ensure that inventory levels match customer requirements, minimizing stockouts and improving customer satisfaction.
- Reduced waste: Demand-driven production enables manufacturing executives to avoid overproduction, reducing the risk of obsolete or unused inventory. This minimizes waste and promotes a more sustainable approach to inventory control.
- Flexibility and adaptability: By closely monitoring customer demand, manufacturing executives can quickly adjust production levels to meet changing market needs. This agility reduces the likelihood of excess inventory due to inaccurate demand forecasts.
In summary, both JIT manufacturing and demand-driven production strategies contribute to minimizing excess inventory. These strategies optimize inventory levels and support sustainable growth in the manufacturing sector.
B. Enhancing supply chain visibility and collaboration
Enhancing supply chain visibility and collaboration is a critical aspect of optimizing inventory control for sustainable growth. Manufacturing executives recognize that a transparent and collaborative supply chain enables efficient inventory management, reduces lead times, and improves overall operational performance.
By fostering visibility and collaboration, executives can gain insights into the entire supply chain, and identify potential bottlenecks.
Supply Chain Visibility:
Supply chain visibility refers to the ability to track and monitor inventory, materials, and information as they flow through the supply chain. Enhanced visibility provides manufacturing executives with real-time data and insights into inventory levels, demand patterns, production status, and logistics.
Benefits of supply chain visibility in optimizing inventory control include:
- Proactive inventory management: By monitoring inventory levels, lead times, and supplier performance, executives can proactively identify potential shortages or excesses and take appropriate actions to prevent stockouts or inventory buildup.
- Efficient risk management: Enhanced visibility enables executives to identify potential risks, such as supply disruptions or quality issues, and implement contingency plans to mitigate their impact on inventory control.
- Improved collaboration with suppliers: Visibility facilitates collaboration with suppliers, allowing for better coordination, information sharing, and alignment of inventory management strategies. This collaboration can lead to improved supplier performance, reduced lead times, and optimized inventory levels.
Collaboration in the Supply Chain:
Collaboration among supply chain partners is vital for optimizing inventory control. Manufacturing executives should foster collaboration and establish strong relationships with suppliers, distributors, and logistics providers. Key benefits of collaboration in inventory control include:
- Demand collaboration: By actively engaging with customers and sharing demand forecasts, executives can align production schedules, optimize inventory levels, and reduce the risk of stockouts or excess inventory.
- Supplier collaboration: Collaboration with suppliers helps streamline procurement processes, improve order fulfillment, and enhance supply chain responsiveness. Executives can work closely with suppliers to share information, negotiate favorable terms, and implement vendor-managed inventory (VMI) programs.
- Data sharing and integration: Collaboration facilitates the sharing and integration of data across the supply chain, enabling real-time visibility into inventory levels, production schedules, and transportation status. This data integration supports accurate demand planning and proactive inventory management.
- Joint improvement initiatives: Executives can collaborate with supply chain partners to identify areas for improvement, such as reducing lead times, optimizing order quantities, or implementing lean practices. Joint improvement initiatives drive efficiency, reduce costs, and enhance overall supply chain performance.
Through improved visibility, executives can gain insights into the supply chain, enabling accurate demand forecasting, proactive inventory management, and efficient risk mitigation. Collaboration fosters effective communication, data sharing, and joint improvement initiatives, and enhancing overall supply chain performance.
C. Implementing data-driven inventory management
Data-driven inventory management is a strategic approach that leverages advanced analytics and real-time monitoring to optimize inventory levels, reduce costs, and improve operational efficiency.
Manufacturing executives can harness the power of data to make informed decisions, accurately forecast demand, and proactively manage inventory. This approach enables executives to align inventory levels with customer demands, minimize stockouts, and avoid excess inventory.
The two key components of implementing data-driven inventory management are inventory analytics and forecasting, as well as real-time monitoring and reporting.
Inventory Analytics and Forecasting:
Inventory analytics involves the use of statistical models and algorithms to analyze historical data, market trends, and other relevant factors to generate accurate demand forecasts and optimize inventory levels. Key benefits of inventory analytics and forecasting include:
- Optimal inventory planning: Through inventory analytics, executives can identify optimal order quantities, reorder points, and safety stock levels. This ensures that inventory levels are aligned with customer demand while minimizing carrying costs and inventory obsolescence.
- Efficient supply chain management: With accurate demand forecasting, executives can collaborate with suppliers and logistics providers to optimize lead times, transportation routes, and overall supply chain efficiency. This leads to improved customer satisfaction, reduced costs, and enhanced operational performance.
Real-time Monitoring and Reporting:
Real-time monitoring and reporting involve the use of technology solutions and automated systems to capture and analyze inventory data in real-time. This enables executives to have up-to-date visibility into inventory levels, demand patterns, and other key performance indicators. Benefits of real-time monitoring and reporting in inventory management include:
- Proactive decision-making: With real-time data, executives can quickly identify inventory discrepancies, monitor stock levels, and address potential issues before they escalate. This allows for proactive decision-making to optimize inventory levels and respond to changing customer demands promptly.
- Timely replenishment: Real-time monitoring enables executives to track inventory levels and automatically trigger replenishment orders when inventory reaches predefined thresholds. This minimizes the risk of stockouts and ensures continuous availability of products to customers.
- Performance tracking and optimization: Real-time reporting provides executives with key performance metrics, such as inventory turnover ratio, fill rate, and order cycle time. These insights enable continuous improvement and optimization of inventory management processes.
Real-time monitoring and reporting enable executives to have up-to-date visibility into inventory performance, facilitating proactive decision-making and efficient supply chain management. Adopting a data-driven approach enhances operational efficiency, reduces costs, and contributes to sustainable growth in the manufacturing sector.
D. Leveraging technology solutions
In the quest for optimizing inventory control, manufacturing executives can harness the power of technology solutions to drive efficiency, accuracy, and sustainable growth.
This section explores three key technology solutions: inventory management software, RFID and IoT applications, and artificial intelligence (AI) and machine learning (ML) algorithms. By leveraging these technologies, executives can transform their inventory control practices and unlock numerous benefits.
Inventory Management Software:
Inventory management software offers a comprehensive platform to streamline and automate inventory-related tasks. This technology solution provides executives with advanced features such as real-time inventory tracking, demand forecasting, order management, and reporting and analytics.
By implementing inventory management software, executives can:
- Centralize inventory data and enhance visibility: The software consolidates inventory information in one place, enabling executives to have real-time visibility into inventory levels, locations, and movements across multiple warehouses or locations.
- Improve inventory accuracy and control: With automated data capture and barcode scanning capabilities, inventory management software minimizes manual errors and enhances inventory accuracy. Executives can track stock levels, conduct cycle counts, and perform accurate inventory reconciliations.
- Optimize demand planning and inventory replenishment: By leveraging demand forecasting modules, executives can generate accurate demand forecasts based on historical data, market trends, and customer insights. This empowers them to optimize inventory levels, align production schedules, and avoid stockouts or excess inventory.
- Streamline order processing and fulfillment: Inventory management software automates order processing, reducing manual intervention and improving order accuracy. Executives can streamline workflows, manage customer orders efficiently, and improve overall order fulfillment processes.
RFID and IoT Applications:
RFID and IoT technologies provide real-time tracking, monitoring, and data capture capabilities, revolutionizing inventory control practices. By leveraging RFID tags, sensors, and connectivity, manufacturing executives can:
- Enhance real-time inventory visibility: RFID tags and IoT sensors attached to inventory items enable executives to track their location, movement, and condition in real-time. This improves inventory visibility and enables proactive decision-making.
- Automate data capture and reduce manual efforts: RFID and IoT applications automate data capture, eliminating the need for manual inventory counts. This saves time, reduces errors, and ensures accurate and up-to-date inventory information.
- Improve supply chain efficiency: With RFID and IoT technologies, executives can monitor inventory levels, transportation, and logistics in real-time. This enhances supply chain visibility, optimizes inventory replenishment, and enables efficient order fulfillment.
- Enhance traceability and quality control: RFID and IoT solutions enable executives to track the movement of inventory throughout the supply chain, ensuring traceability and facilitating effective quality control processes.
Artificial Intelligence and Machine Learning:
Artificial intelligence and machine learning algorithms bring advanced analytical capabilities to inventory control, empowering executives to make data-driven decisions and optimize inventory levels. By leveraging AI and ML, executives can:
- Accurately forecast demand: AI and ML algorithms analyze historical sales data, market trends, and external factors to generate accurate demand forecasts. This enables executives to plan inventory levels effectively, reduce stockouts, and improve customer satisfaction.
- Optimize inventory planning and replenishment: AI and ML algorithms analyze various factors such as demand patterns, lead times, and supplier performance to determine optimal order quantities, reorder points, and safety stock levels. This ensures optimal inventory levels while minimizing carrying costs and the risk of excess inventory.
- Enhance decision-making with predictive insights: AI and ML algorithms can analyze large volumes of data to provide executives with predictive insights. These insights help in identifying potential inventory issues, optimizing supply chain processes, and making proactive decisions to avoid disruptions.
- Enable continuous improvement: AI and ML algorithms can monitor and analyze inventory performance, identify trends, and suggest optimization strategies. This enables executives to continuously improve their inventory control practices and drive operational excellence
Overcoming Challenges in Inventory Control Optimization
While optimizing inventory control is crucial for sustainable growth, manufacturing executives often encounter various challenges along the way. This section explores the common challenges faced in inventory control optimization and discusses strategies to overcome them.
By addressing these challenges head-on, executives can navigate the complexities of inventory management and achieve efficient and sustainable inventory control processes.
A. Balancing inventory costs and customer service levels
Balancing inventory costs and customer service levels is a crucial challenge faced by manufacturing executives in their pursuit of optimal inventory control. On one hand, maintaining excessive inventory levels can lead to increased carrying costs, tie up valuable resources, and risk obsolescence.
On the other hand, insufficient inventory can result in stockouts, missed sales opportunities, and dissatisfied customers. Achieving the delicate balance requires careful consideration of factors such as lead times, demand variability, production capabilities, and customer service requirements.
To address this challenge, manufacturing executives can implement several strategies. Accurate demand forecasting and planning play a pivotal role in estimating customer demand and aligning inventory levels accordingly. By leveraging historical data, market trends, and customer insights, executives can minimize the risk of overstocking or stockouts.
Additionally, employing inventory optimization techniques such as economic order quantity (EOQ), safety stock analysis, and ABC analysis helps identify the appropriate inventory levels for different products. This ensures that high-demand items are adequately stocked while reducing inventory levels for low-demand or slow-moving items.
Effective collaboration with suppliers is also crucial in managing inventory costs and customer service levels. Building strong relationships, sharing demand forecasts, and implementing vendor-managed inventory (VMI) programs can optimize replenishment lead times and reduce the need for excessive safety stock.
Embracing lean principles, such as just-in-time (JIT) manufacturing and lean production, can further minimize excess inventory by synchronizing production with customer demand. Executives can implement efficient production and delivery systems that reduce lead times and improve responsiveness.
Monitoring inventory performance metrics, such as inventory turnover ratio, fill rate, and stockout rate, provides valuable insights into the effectiveness of inventory control strategies. By implementing key performance indicators (KPIs) and regularly evaluating inventory performance, executives can make data-driven decisions for continuous improvement.
B. Dealing with supply chain disruptions
Supply chain disruptions pose significant challenges to inventory control for manufacturing executives. Unexpected events such as natural disasters, geopolitical issues, supplier bankruptcies, transportation disruptions, and pandemics can disrupt the flow of materials and impact production schedules, leading to inventory imbalances.
Managing these disruptions requires proactive strategies and agile approaches to mitigate risks and maintain optimal inventory levels.
To effectively deal with supply chain disruptions, manufacturing executives can implement the following strategies:
Risk assessment and contingency planning: Conducting thorough risk assessments allows executives to identify potential vulnerabilities in the supply chain. By understanding the critical dependencies and potential risks, they can develop contingency plans to mitigate disruptions. This includes identifying alternative suppliers, diversifying sourcing strategies, and implementing business continuity plans.
Supplier relationship management: Cultivating strong relationships with suppliers is crucial in times of disruption. Regular communication and collaboration help executives stay informed about potential issues and proactively address them. Developing partnerships based on trust and transparency enables swift decision-making and facilitates effective problem-solving during disruptions.
Inventory buffer and safety stock: Maintaining a strategic inventory buffer and safety stock can provide a cushion during supply chain disruptions. By strategically placing safety stock at critical points in the supply chain, executives can mitigate the impact of disruptions and ensure continuity of operations. However, balancing the cost of holding additional inventory with the potential risks is essential to avoid excess inventory.
Supply chain visibility and technology adoption: Enhancing supply chain visibility through technology solutions enables executives to monitor the flow of materials, identify bottlenecks, and anticipate disruptions. Implementing supply chain management software, real-time tracking systems, and data analytics tools provides valuable insights and empowers executives to make proactive decisions.
Collaborative planning and coordination: Collaborating with cross-functional teams, suppliers, and customers is vital during supply chain disruptions. Executives can leverage collaborative planning processes, such as Sales and Operations Planning (S&OP), to align demand forecasts, production capacities, and inventory levels across the supply chain. By fostering collaboration, executives can optimize decision-making and minimize the impact of disruptions.
Agility and flexibility: Building agile supply chain capabilities allows executives to respond quickly to disruptions and adapt their inventory control strategies. This includes having flexible production capabilities, maintaining a diversified supplier base, and implementing responsive inventory management practices such as dynamic safety stock adjustment and expedited order fulfillment.
Proactive risk management, strong supplier relationships, strategic inventory planning, supply chain visibility, collaboration, and agility form the foundation for resilient inventory control practices in the face of disruptions.
C. Addressing environmental sustainability concerns
As organizations increasingly focus on reducing their carbon footprint and operating in an environmentally responsible manner, inventory control plays a crucial role in achieving sustainability goals. By implementing strategies that prioritize environmental sustainability, manufacturing executives can contribute to a greener future while optimizing their inventory management practices.
To effectively address environmental sustainability concerns in inventory control, manufacturing executives can adopt the following approaches:
Sustainable sourcing and supplier management: Executives can prioritize suppliers that adhere to sustainable practices and have environmentally friendly processes. This includes sourcing materials from renewable or recycled sources, engaging with suppliers who prioritize sustainability, and monitoring supplier compliance with environmental standards. By partnering with sustainable suppliers, executives can ensure the eco-friendly sourcing of raw materials and components.
Efficient inventory management: Optimizing inventory levels and reducing excess stock can lead to significant environmental benefits. Executives can implement lean inventory practices, such as just-in-time (JIT) manufacturing, to minimize waste, energy consumption, and greenhouse gas emissions.
Product lifecycle management: Considering the entire lifecycle of products is essential for environmental sustainability. Executives can adopt strategies that extend product lifespans, encourage repair and refurbishment, and promote recycling and responsible disposal practices.
By designing products with recyclable materials and facilitating their end-of-life treatment, manufacturing executives can reduce waste and environmental impact.
Packaging optimization: Reducing packaging waste is another vital aspect of environmental sustainability. Executives can explore eco-friendly packaging alternatives, such as using recyclable or biodegradable materials and minimizing excessive packaging. By optimizing packaging design and minimizing material usage, manufacturers can decrease waste generation and transportation-related carbon emissions.
Energy efficiency and renewable energy adoption: Manufacturing operations consume significant amounts of energy. Executives can prioritize energy efficiency measures, such as implementing energy-saving technologies, optimizing equipment utilization, and improving facility insulation.
Additionally, embracing renewable energy sources, such as solar or wind power, can significantly reduce the environmental impact of manufacturing operations.
Continuous improvement and measurement: Executives should establish environmental performance metrics and regularly monitor progress towards sustainability goals. By tracking key indicators like energy consumption, waste generation, and carbon emissions, executives can identify areas for improvement.
They can also implement targeted initiatives to drive environmental sustainability in their inventory control practices.
D. Managing change and resistance within the organization
Implementing inventory control optimization initiatives often requires significant organizational change, which can be met with resistance from employees and other stakeholders. Managing this change effectively is essential for successful implementation and long-term sustainability.
Manufacturing executives must proactively address resistance, engage employees, and create a supportive environment for change. By doing so, they can foster a culture of continuous improvement and maximize the benefits of optimized inventory control.
To effectively manage change and resistance within the organization, manufacturing executives can employ the following strategies:
Clear communication: Transparent and timely communication is crucial in managing change. Executives should clearly articulate the reasons behind the inventory control optimization initiatives, the benefits it brings, and the expected impact on employees and processes. Regular updates, town hall meetings, and open forums provide opportunities for dialogue and address concerns.
Stakeholder involvement: Involving key stakeholders, such as employees, department heads, and cross-functional teams, in the decision-making process helps gain their buy-in and ownership of the changes. By including their perspectives, insights, and suggestions, executives can increase engagement and reduce resistance.
Training and support: Providing comprehensive training and support is vital for ensuring that employees have the necessary skills and knowledge to adapt to the changes. Executives should offer training programs, workshops, and resources that help employees understand new processes, technologies, and tools related to inventory control optimization.
Ongoing support and coaching during the transition period can help employees overcome challenges and build confidence.
Change champions and influencers: Identifying change champions within the organization can significantly aid in managing resistance. These individuals, who are enthusiastic about the changes and believe in their benefits, can act as advocates and influencers, addressing concerns and encouraging others to embrace the changes. Their influence can help build momentum and create a positive change culture.
Addressing concerns and feedback: Executives should actively listen to employee concerns, address them promptly, and provide transparent feedback. It is essential to create channels for employees to express their opinions, ask questions, and provide feedback on the implementation of inventory control optimization initiatives. By acknowledging concerns and addressing them thoughtfully, executives can build trust and reduce resistance.
Celebrating successes and recognizing achievements: Recognizing and celebrating successes along the way is crucial in maintaining motivation and sustaining momentum. Executives should acknowledge individual and team achievements, highlighting the positive impacts of the changes on the organization and its stakeholders. This reinforces the benefits of the optimized inventory control and encourages continued engagement.
Clear communication, stakeholder involvement, training and support, change champions, addressing concerns and feedback, and celebrating successes are key strategies that foster a culture of change acceptance and drive sustainable implementation.
Ultimately, a supportive environment for change paves the way for improved efficiency, enhanced profitability, and long-term success in inventory control optimization.
Case Studies and Best Practices
This section highlights the transformative impact of optimized inventory control practices in manufacturing companies. By implementing strategies such as just-in-time production, agile replenishment, these companies have achieved improved efficiency, cost savings, customer satisfaction, and market competitiveness.
Toyota: Toyota is known for its successful implementation of the just-in-time (JIT) inventory control system. By closely aligning production with customer demand, Toyota has minimized excess inventory and achieved significant cost savings. This approach has allowed them to reduce lead times, improve efficiency, and maintain a high level of customer satisfaction. Toyota's success with optimized inventory control has been a key factor in their ability to compete in the global automotive market.
Zara: Zara, a fast-fashion retailer, has revolutionized the fashion industry with its agile inventory control practices. By leveraging real-time sales data and rapid replenishment, Zara keeps inventory levels low while ensuring products are readily available to customers. This strategy enables them to respond quickly to changing fashion trends and reduce the risk of unsold inventory. Zara's inventory control practices have contributed to their remarkable success, making them one of the world's leading fashion retailers.
Amazon: Amazon's success can be attributed in part to its sophisticated inventory control systems. Through advanced data analytics and forecasting algorithms, Amazon optimizes inventory levels across its vast network of fulfillment centers. By strategically positioning inventory and leveraging efficient order management systems, Amazon ensures fast and reliable delivery to customers while minimizing excess stock. This streamlined approach has allowed them to rapidly scale their operations and become a dominant force in the e-commerce industry.
Dell: Dell revolutionized the computer manufacturing industry by implementing a build-to-order model. Rather than building computers in advance, Dell waits for customer orders before assembling and shipping the products. This approach significantly reduces inventory costs and eliminates the need for excessive stock. By closely aligning production with demand, Dell has achieved remarkable efficiency and responsiveness, leading to increased customer satisfaction and market competitiveness.
Procter & Gamble (P&G): P&G implemented a collaborative forecasting and planning system called Collaborative Planning, Forecasting, and Replenishment (CPFR). This system allows P&G to collaborate with retailers, sharing real-time sales data and demand forecasts. This optimized inventory control has strengthened their relationships with retailers and facilitated mutual success in the consumer goods industry.
These examples serve as inspiration for other manufacturing companies seeking to optimize their inventory control and drive sustainable growth.
Prioritizing Inventory Control for Sustainable Growth
Manufacturing executives play a pivotal role in driving sustainable growth through effective inventory control practices. To ensure long-term success and contribute to a greener future, it is crucial for executives to prioritize and optimize inventory control with sustainability in mind.
Here is what manufacturing executives must look forward to:
- Embrace a sustainability mindset: Recognize the importance of environmental sustainability and its impact on business success. Understand that optimizing inventory control practices can reduce waste, conserve resources, minimize environmental impact, and improve operational efficiency.
- Set clear sustainability goals: Establish specific, measurable, achievable, relevant, and time-bound (SMART) sustainability goals for inventory control. These goals may include reducing waste, minimizing carbon emissions, optimizing energy usage, and promoting sustainable sourcing and manufacturing practices.
- Integrate sustainability into inventory control strategies: Integrate sustainable practices into inventory control strategies and decision-making processes. This includes adopting lean manufacturing principles, implementing just-in-time production, optimizing packaging to reduce waste, and prioritizing eco-friendly suppliers.
- Invest in technology and data analytics: Leverage technology solutions and data analytics to enhance inventory control practices. Implement inventory management software, real-time monitoring systems, and predictive analytics tools to optimize inventory levels, reduce waste, and improve demand forecasting accuracy.
- Foster cross-functional collaboration: Encourage collaboration among different departments, including supply chain, operations, sales, and sustainability teams. Foster open communication, knowledge sharing, and coordination to align inventory control efforts with sustainability initiatives.
- Empower employees: Engage and empower employees at all levels to contribute to sustainable inventory control practices. Provide training and education on sustainability principles, encourage innovation and continuous improvement, and recognize and reward environmentally responsible behaviors.
- Measure and monitor progress: Establish key performance indicators (KPIs) to measure progress towards sustainability goals. Regularly track and report on sustainability metrics related to inventory control, such as waste reduction, energy efficiency, and carbon footprint. Use this data to drive continuous improvement and communicate the positive impact of sustainable inventory control practices.
By prioritizing inventory control for sustainable growth, manufacturing executives can not only drive operational efficiency and cost savings but also contribute to a more sustainable future. Let us commit to optimizing inventory control practices with sustainability at the forefront, creating a positive impact on the environment, society, and long-term business success.
Future outlook and emerging trends in inventory control
The future of inventory control is poised for exciting advancements and emerging trends that will revolutionize the way manufacturing companies manage their inventory. Here are some key future outlooks and emerging trends in inventory control:
Artificial Intelligence (AI) and Machine Learning: AI and machine learning technologies are increasingly being applied to inventory control processes. These advanced technologies can analyze vast amounts of data, identify patterns, and make accurate demand forecasts. AI-powered inventory control systems can optimize inventory levels, reduce stockouts, and enhance supply chain efficiency.
Internet of Things (IoT) and Real-time Monitoring: IoT devices and sensors embedded in inventory assets can provide real-time data on inventory levels, location, and condition. This enables companies to have comprehensive visibility into their inventory throughout the supply chain. Real-time monitoring allows for proactive inventory management, faster response to changes, and better decision-making.
Blockchain Technology: Blockchain technology offers enhanced transparency, security, and traceability in supply chain operations. By leveraging blockchain, manufacturers can track the movement of inventory, verify authenticity, and ensure compliance with sustainability and ethical standards. This technology has the potential to streamline inventory control processes, reduce fraud, and enhance trust among supply chain partners.
Robotics and Automation: Robotics and automation are transforming inventory management operations. Autonomous robots can handle repetitive tasks such as picking, packing, and organizing inventory, improving accuracy and efficiency. Automated systems can also optimize inventory replenishment, minimize stockouts, and enhance order fulfillment processes.
Predictive Analytics and Demand Sensing: Predictive analytics techniques combined with demand sensing capabilities allow companies to anticipate customer demand more accurately. By analyzing various data sources, including social media trends, weather patterns, and economic indicators, companies can proactively adjust inventory levels and optimize production schedules to meet changing demand patterns.
Sustainable Inventory Control: The focus on sustainability will continue to shape inventory control practices in the future. Manufacturers will increasingly prioritize eco-friendly sourcing, circular economy principles, and waste reduction strategies. Sustainable inventory control practices will not only reduce environmental impact but also drive cost savings and enhance brand reputation.
Collaborative Supply Chain Networks: Collaboration among supply chain partners will become more critical for effective inventory control. Collaborative platforms and networks will enable real-time information sharing, demand planning, and inventory optimization across the supply chain. By working together, companies can achieve better visibility, reduce excess inventory, and respond faster to customer needs.
3D Printing: The advent of 3D printing technology has the potential to disrupt traditional inventory control practices. With 3D printing, manufacturers can produce on-demand and customizable products, reducing the need for large inventories. This technology offers the opportunity for localized production, faster time-to-market, and reduced waste.
As these future outlooks and emerging trends unfold, manufacturing companies that embrace and adapt to these advancements in inventory control will gain a competitive edge.
Conclusion
Manufacturing executives play a pivotal role in driving this optimization process. They need to understand the importance of inventory control for sustainable growth, set clear goals aligned with sustainability principles, and integrate these goals into their overall business strategies. Collaboration with cross-functional teams, alignment with sustainability goals, technology adoption, and effective leadership are essential elements in this journey.
The implementation of just-in-time manufacturing, demand-driven production, data-driven inventory management, and technology solutions such as inventory management software, RFID, IoT applications, and AI-driven analytics are key enablers of optimized inventory control. These practices enhance supply chain visibility, streamline processes, and improve decision-making accuracy.
Overcoming challenges such as balancing inventory costs and customer service levels, managing supply chain disruptions, addressing sustainability concerns, and managing change and resistance within the organization are critical for long-term success.
Looking ahead, the future of inventory control promises exciting advancements, including AI and machine learning, IoT and real-time monitoring, blockchain technology, robotics and automation, predictive analytics, and collaborative supply chain networks. Embracing these emerging trends will further enhance inventory control practices, improve efficiency, and drive sustainable growth.
Manufacturing executives must seize the opportunity to prioritize inventory control for sustainable growth.
How can Deskera Help You?
Deskera ERP and MRP systems help you to keep your business units organized. The system's primary functions are as follows:
- Keep track of your raw materials and final items inventories
- Control production schedules and routings
- Keep a bill of materials
- Produce thorough reports
- Make your own dashboards
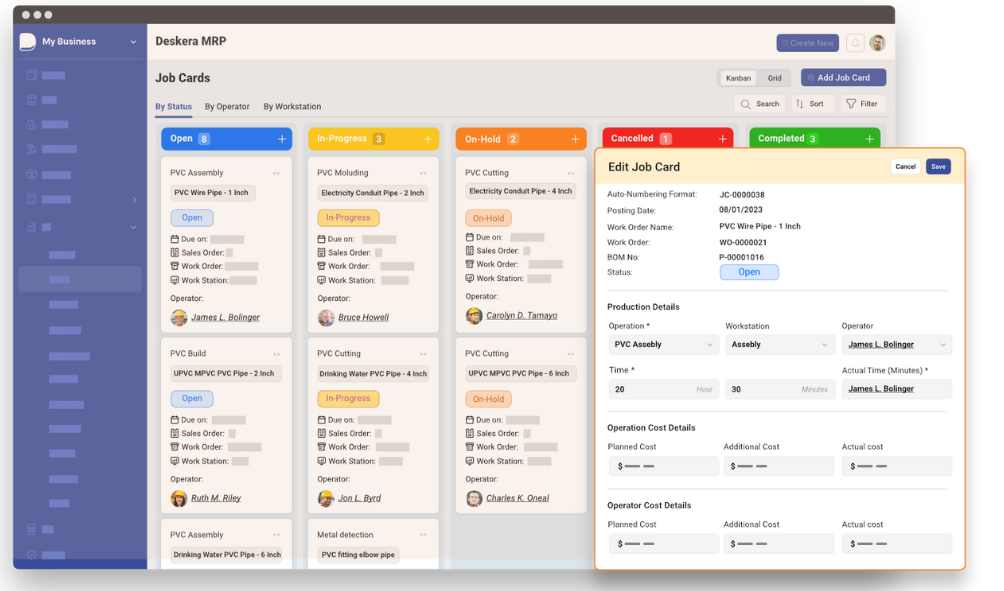
Deskera's integrated financial planning tools enable investors to better plan and track their investments. It can assist investors in making faster and more accurate decisions.
Deskera Books allows you to better manage your accounts and finances. Maintain good accounting practices by automating tasks like billing, invoicing, and payment processing.
Deskera CRM is a powerful solution that manages your sales and helps you close deals quickly. It not only enables you to perform critical tasks like lead generation via email, but it also gives you a comprehensive view of your sales funnel.
Deskera People is a straightforward tool for centralizing your human resource management functions.
Key Takeaways
- Optimizing inventory control is essential for manufacturing executives to achieve sustainable growth in today's competitive business landscape.
- Effective inventory control practices can reduce costs, enhance operational efficiency, improve customer satisfaction, and contribute to a greener future.
- Manufacturing executives play a crucial role in driving the optimization process by setting clear sustainability goals and integrating them into overall business strategies.
- Collaboration with cross-functional teams and alignment with sustainability goals are key elements in achieving optimized inventory control.
- Technology adoption, such as inventory management software, RFID, IoT applications, and AI-driven analytics, enables enhanced inventory control and supply chain visibility.
- Just-in-time manufacturing and demand-driven production strategies minimize excess inventory and improve responsiveness to customer demand.
- Data-driven inventory management, including inventory analytics and forecasting, enhances decision-making accuracy and efficiency.
- Real-time monitoring and reporting allows for proactive inventory management and timely response to changes in demand or supply.
- Leveraging technology solutions, such as inventory management software, RFID, IoT applications, and AI-driven analytics, streamlines inventory control processes and improves efficiency.
- Overcoming challenges such as balancing inventory costs and customer service levels, managing supply chain disruptions, addressing sustainability concerns, and managing change within the organization is crucial for long-term success.
Related Articles
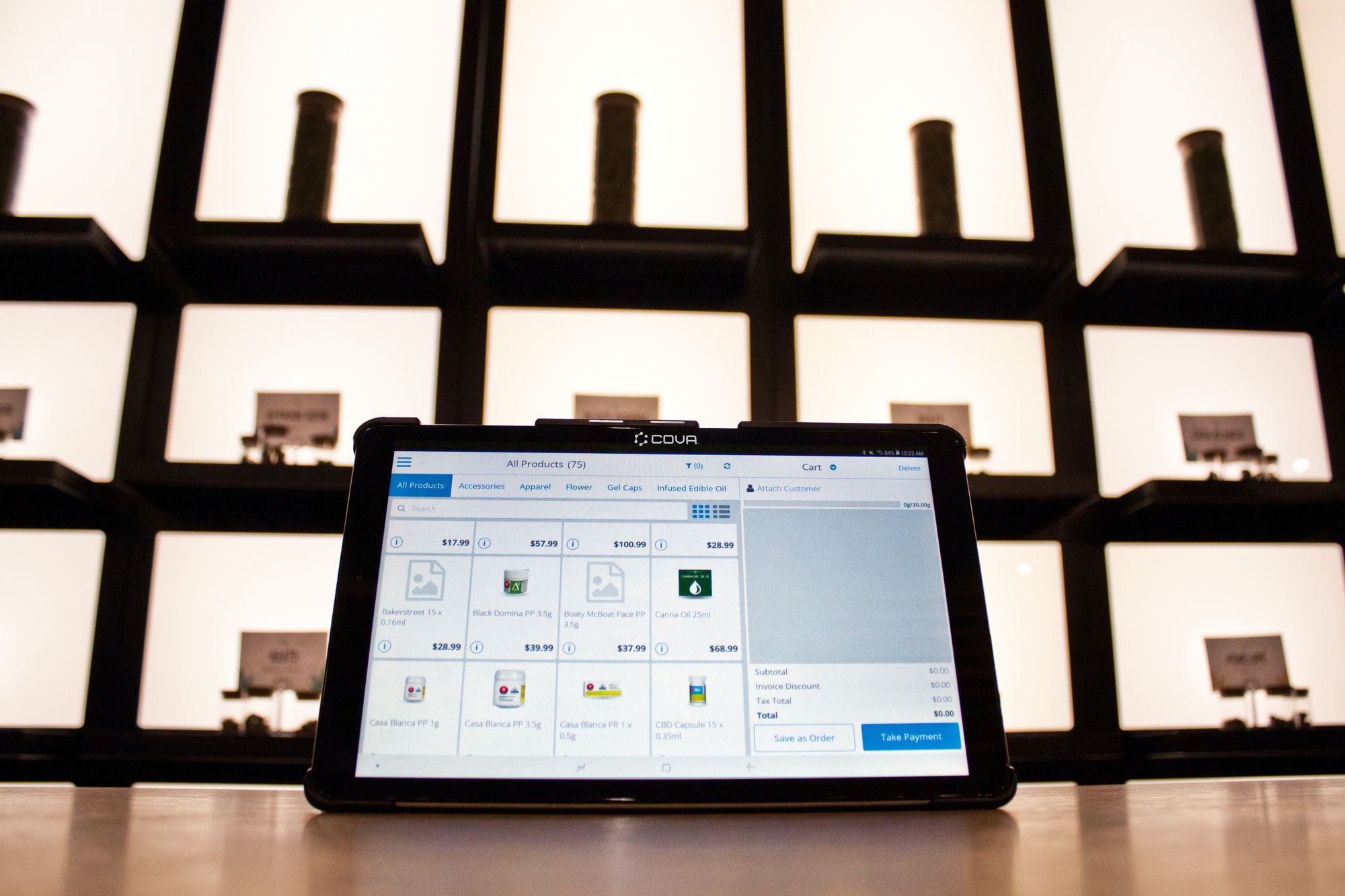
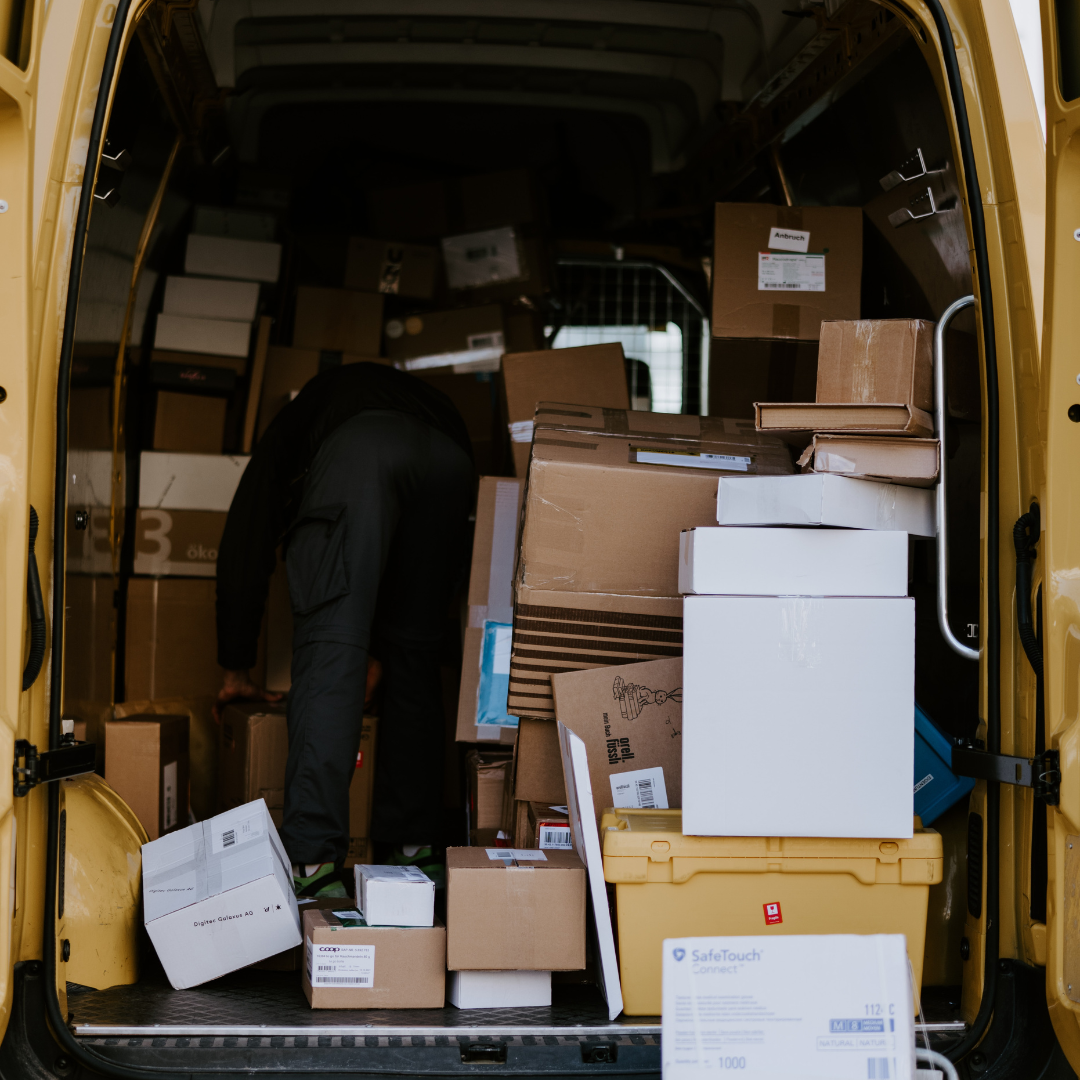
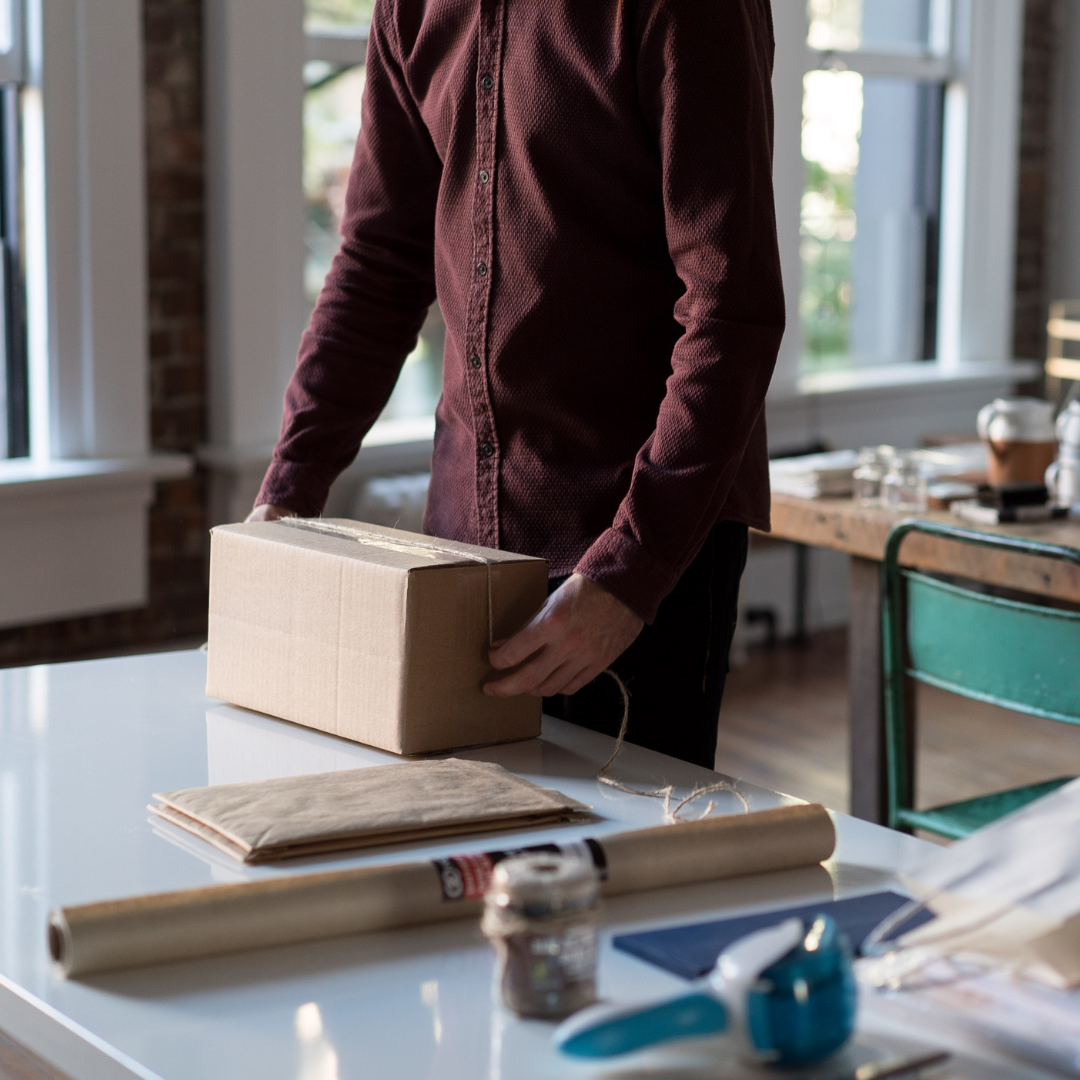
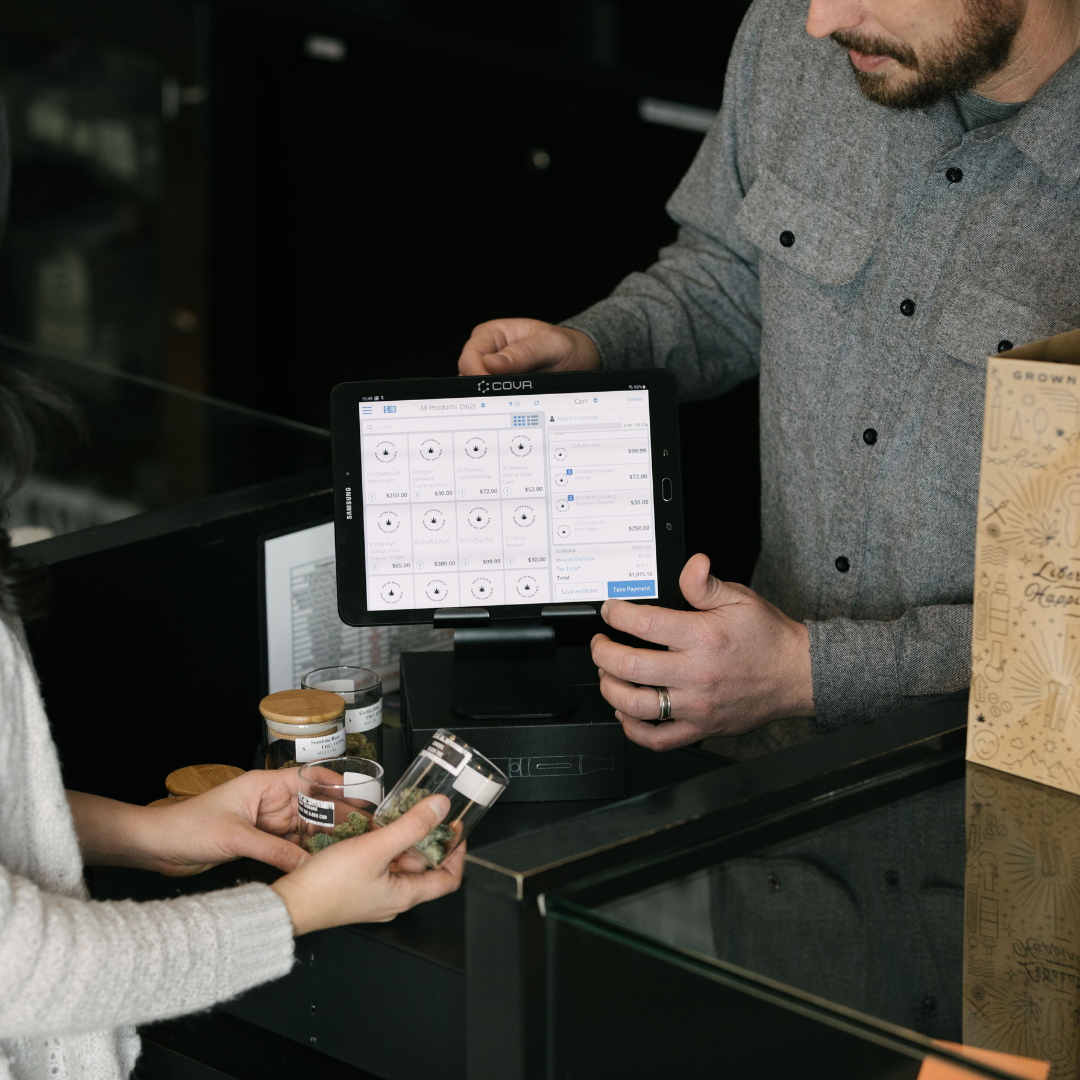