Manufacturing operations inherently consume resources and generate waste, but this doesn't have to be at the expense of the environment.
Recent data from the National Association of Manufacturers (NAM) highlights that nearly 75% of US manufacturers are actively pursuing sustainable practices to reduce their environmental footprint, underscoring the shift towards sustainable cost management for improved profitability and reputation.
Sustainable cost management is the practice of managing costs in a way that minimizes environmental impact and ensures long-term profitability. It is a win-win approach that can help manufacturers reduce their environmental footprint, improve their bottom line, and gain a competitive edge.
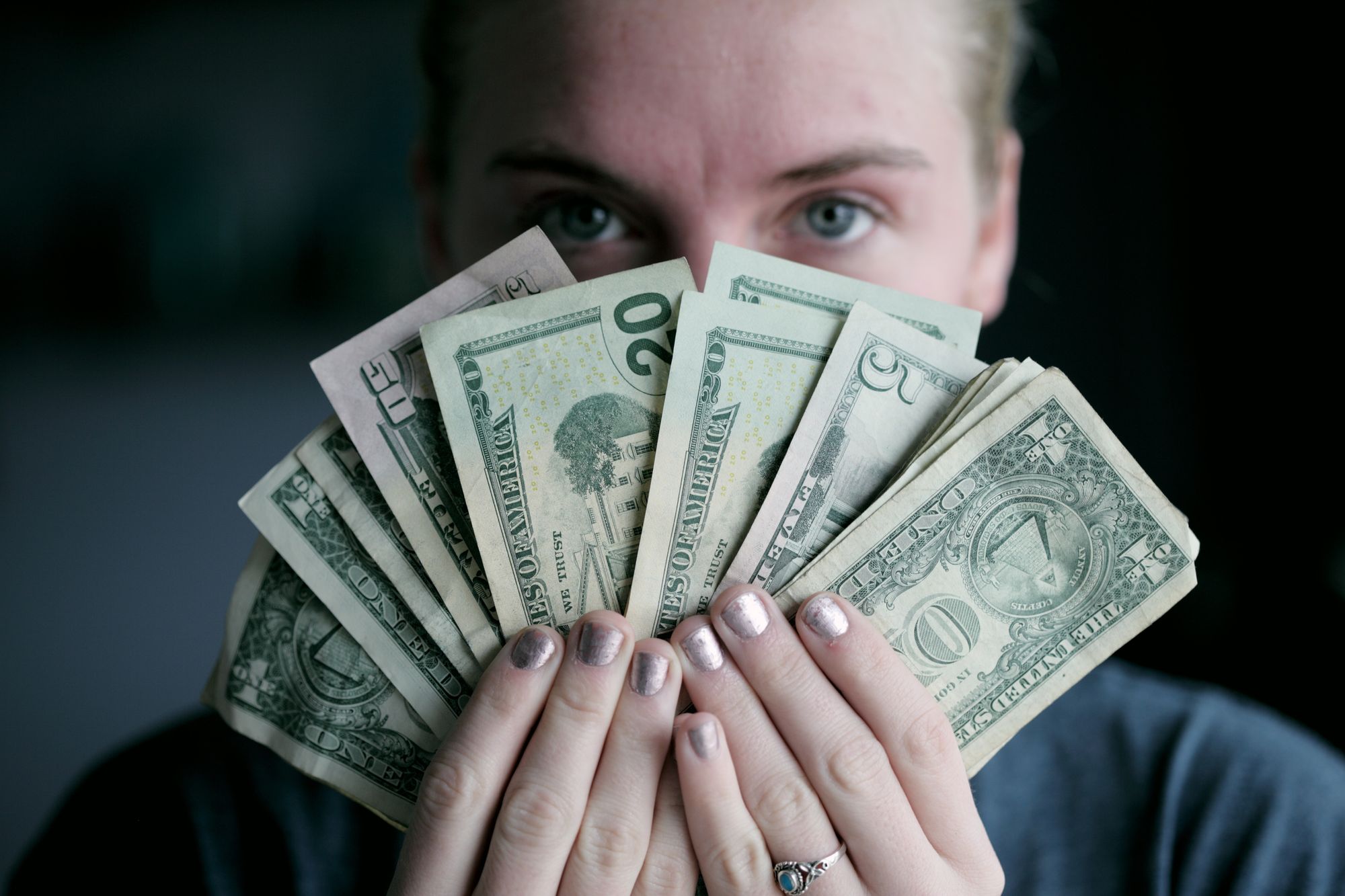
Gone are the days when profitability was synonymous with mere financial gains. In this era of heightened social consciousness, resource scarcity, and regulatory scrutiny, manufacturers find themselves at a pivotal juncture – one where the pursuit of profit must be intricately interwoven with sustainable practices.
In the United States, the manufacturing sector is responsible for a significant amount of environmental pollution. According to the Environmental Protection Agency (EPA), manufacturing accounts for 24% of all greenhouse gas emissions in the United States. It also accounts for 20% of water pollution and 17% of waste generation.
This article delves into various facets of sustainable cost management, offering insights into tools, strategies, and real-world examples.
By the time you conclude this article, it is our goal that you'll be armed with a comprehensive understanding of how sustainable practices can not only enhance your financial bottom line but also contribute to a more resilient, responsible, and prosperous future for both your manufacturing enterprise and the global community as a whole.
Here is all that we shall discover in this post:
- Introduction to Sustainable Cost Management
- Linking Cost Management to Long-Term Profitability
- Identifying Cost Drivers in Manufacturing Processes
- Leveraging Technology for Cost Monitoring and Analysis
- Collaboration and Communication in Cost Management
- Compliance and Regulatory Alignment in Cost Control
- Measuring Success: Key Performance Indicators (KPIs)
- Future Trends: Innovations in Sustainable Cost Management
- How Can Deskera Help You?
- Conclusion
- Key Takeaways
Introduction to Sustainable Cost Management
Sustainable cost management is a strategic approach that aims to achieve a harmonious balance between economic viability, social responsibility, and environmental stewardship within an organization's operations.
In an era characterized by heightened awareness of climate change, resource scarcity, and ethical business practices, sustainable cost management has emerged as a critical tool for businesses to not only enhance their financial performance but also contribute positively to society and the environment.
Foundations of Sustainable Cost Management:
At its core, sustainable cost management encompasses two intertwined objectives: achieving economic efficiency and maintaining environmental and social integrity. It is based on the understanding that businesses operate within complex ecosystems and interdependent systems that require a holistic approach to decision-making.
This approach challenges the traditional notion of cost management solely focused on reducing immediate financial outlays, instead promoting the optimization of overall value by incorporating broader considerations.
Principles of Sustainable Cost Management
The following are the key principles that underpin sustainable cost management:
- Lifecycle Thinking:
One of the foundational principles of sustainable cost management is adopting a lifecycle perspective. This involves considering the entire lifecycle of a product, process, or service, from raw material extraction and production to distribution, use, and eventual disposal.
Traditional cost management often focuses solely on the upfront costs of production, neglecting the downstream impacts and costs associated with a product's lifecycle. Lifecycle thinking encourages businesses to identify inefficiencies, waste generation, and environmental impacts at every stage, enabling them to make more informed decisions.
By taking a holistic view of a product's lifecycle, organizations can uncover opportunities for resource optimization, waste reduction, and emissions mitigation.
For example, a company producing consumer electronics can adopt design principles that prioritize easy repairability and recyclability, thereby extending the lifespan of products and reducing electronic waste. This not only aligns with environmental goals but also offers cost savings through reduced waste disposal fees and more efficient use of resources.
- Total Cost Assessment:
Traditional cost management often focuses solely on direct financial costs, overlooking indirect costs associated with environmental and social impacts. Sustainable cost management emphasizes the importance of conducting a comprehensive assessment of the total cost of ownership.
This includes not only upfront production costs but also costs related to environmental compliance, waste management, regulatory fines, employee health and safety, and reputation management.
For instance, a manufacturing facility might be tempted to cut costs by disregarding environmental regulations and emitting pollutants into the air or water. However, the long-term consequences of fines, litigation, public backlash, and potential health issues among employees and communities can significantly outweigh the short-term cost savings.
By factoring in these hidden costs, sustainable cost management guides organizations toward more responsible decisions that align with both economic and environmental goals.
- Materiality and Stakeholder Engagement:
Sustainable cost management recognizes that not all environmental and social issues are equally significant to every organization. Materiality assessment involves identifying the most relevant issues that could impact an organization's performance and reputation.
This requires engagement with stakeholders, including employees, customers, investors, regulators, and communities. Engaging with stakeholders helps identify the concerns that matter most to them and allows organizations to prioritize their efforts accordingly.
By engaging with stakeholders, organizations gain insights into issues such as climate change, supply chain ethics, labor practices, and community impacts. Addressing these issues proactively demonstrates a commitment to responsible practices, reduces reputational risks, and fosters positive relationships with stakeholders.
For instance, a food company sourcing ingredients from environmentally sensitive areas might engage with local communities and conservation organizations to ensure sustainable practices that protect ecosystems and support the well-being of communities.
- Innovation and Collaboration:
Sustainable cost management encourages businesses to foster a culture of innovation and collaboration to develop solutions that simultaneously enhance economic and environmental performance.
Innovation can lead to the development of new technologies, products, and processes that drive efficiency gains and environmental benefits. Collaborating with partners, suppliers, research institutions, and even competitors can open up opportunities for shared learning and problem-solving.
For instance, the automotive industry has witnessed collaboration between manufacturers to develop electric vehicle technologies and charging infrastructure.
This collaborative effort not only responds to environmental concerns but also positions the companies involved as leaders in an evolving market. Innovation and collaboration can yield competitive advantages, enhance market positioning, and stimulate industry-wide progress toward sustainability.
- Performance Measurement and Reporting:
A crucial principle of sustainable cost management is the establishment of robust measurement and reporting systems. Organizations need to track and quantify their environmental and social impacts using standardized metrics. This allows for informed decision-making, the identification of areas for improvement, and the transparent communication of performance to stakeholders.
By accurately measuring and reporting progress, organizations can showcase their commitment to sustainability, build trust with stakeholders, and attract investors and customers who value responsible practices. For instance, a company might track and report reductions in greenhouse gas emissions, water usage, and waste generation, demonstrating a meaningful contribution to environmental goals.
Linking Cost Management to Long-Term Profitability
At first glance, cost management and long-term profitability may seem like two distinct aspects of business operations. However, a closer examination reveals a symbiotic relationship between the two.
Cost management encompasses a range of strategies aimed at optimizing resource allocation, reducing waste, and improving operational efficiency. When executed strategically, these practices have the potential to significantly influence a company's long-term profitability.
Cost management is not just about cost reduction; it's about optimizing the allocation of resources to achieve sustainable competitive advantages. Sustainable cost management is the integration of these practices with a broader focus on environmental and social responsibility, aligning an organization's operations with the principles of corporate sustainability.
Strategic Cost Management for Long-Term Profitability:
Effective cost management strategies go beyond short-term cost-cutting. They involve a strategic and holistic approach that considers the interplay between financial, environmental, and social factors. Here are key strategic approaches that link cost management to long-term profitability:
- Process Efficiency and Innovation:
Enhancing process efficiency through innovation is a cornerstone of sustainable cost management. This involves identifying areas of inefficiency, waste generation, and resource underutilization within an organization's operations. By embracing innovative technologies, lean practices, and streamlined workflows, companies can reduce costs while maintaining or improving product quality.
For example, a manufacturing company might invest in advanced automation and robotics to optimize production processes. While the upfront investment might be substantial, the long-term benefits in terms of reduced labor costs, increased production speed, and minimized errors can lead to substantial gains in profitability over time.
- Lifecycle Cost Analysis:
Considering the entire lifecycle of products or services is a critical aspect of sustainable cost management. This approach involves assessing not only the direct costs of production but also the costs associated with raw material extraction, manufacturing, distribution, use, and eventual disposal. By analyzing the total cost of ownership, organizations can identify opportunities to minimize costs and environmental impacts throughout a product's entire lifecycle.
For instance, a company that produces packaging materials can explore using recycled materials to reduce raw material costs, energy consumption, and waste generation. While the immediate cost might be slightly higher, the long-term benefits in terms of reduced resource depletion and waste management expenses can lead to enhanced profitability.
- Supply Chain Optimization:
The supply chain plays a pivotal role in cost management and long-term profitability. Organizations can optimize their supply chain by engaging in responsible sourcing, building strong relationships with suppliers, and promoting ethical practices. A well-managed supply chain minimizes disruptions, reduces lead times, and enhances inventory management, ultimately leading to cost savings and improved customer satisfaction.
For instance, a retail company can collaborate closely with its suppliers to ensure just-in-time inventory management. This approach reduces excess inventory costs, minimizes storage expenses, and enhances the overall efficiency of the supply chain, positively impacting long-term profitability.
- Risk Management and Resilience:
Sustainable cost management extends to risk management and building organizational resilience. Companies that proactively address environmental, social, and regulatory risks are better prepared to navigate uncertainties and maintain long-term profitability.
Identifying potential risks and developing mitigation strategies can prevent costly disruptions and reputation damage.
For example, an energy company might diversify its energy sources to reduce dependence on fossil fuels, thereby mitigating the financial risks associated with fluctuating oil prices and regulatory changes aimed at reducing carbon emissions. This strategic approach not only aligns with environmental goals but also safeguards profitability in the face of market volatility.
Benefits of Sustainable Cost Management in Manufacturing
As the global business landscape evolves, manufacturers are increasingly recognizing that responsible cost management not only enhances operational efficiency and profitability but also contributes to environmental sustainability.
Enhanced Operational Efficiency:
Sustainable cost management in manufacturing begins with a comprehensive evaluation of processes and resource utilization. This assessment often reveals opportunities for increased operational efficiency. By identifying and addressing inefficiencies, manufacturers can reduce waste, minimize energy consumption, optimize production workflows, and streamline supply chain operations.
For example, Lean manufacturing principles, which aim to eliminate waste and improve processes, can be applied to reduce excessive inventory levels, shorten production lead times, and enhance overall production flow.
This results in reduced carrying costs minimized resource consumption, and improved responsiveness to market demand. Sustainable cost management encourages manufacturers to continuously seek improvements in their operations, fostering a culture of continuous improvement and efficiency.
Cost Reduction and Long-Term Savings:
One of the primary advantages of sustainable cost management in manufacturing is the potential for significant cost reduction. As manufacturers adopt more efficient processes and technologies, they can achieve direct cost savings by optimizing resource use, reducing waste disposal costs, and lowering energy consumption. These immediate cost savings contribute to improved short-term profitability.
Moreover, sustainable cost management focuses on long-term value by considering the lifecycle costs of products. While adopting environmentally friendly technologies or materials may entail higher initial costs, their longer lifespan, and reduced maintenance needs can lead to substantial savings over the product's lifetime.
For instance, energy-efficient machinery may have a higher upfront cost but lower energy consumption, resulting in reduced operational costs and enhanced profitability over time.
Competitive Advantage and Market Differentiation:
Manufacturers that embrace sustainable cost management gain a competitive edge in a rapidly evolving marketplace. Consumers, investors, and regulators are increasingly valuing environmentally responsible practices. By incorporating sustainability into their operations, manufacturers can differentiate themselves from competitors and appeal to environmentally conscious consumers and investors.
Companies that actively promote their commitment to sustainability often attract a dedicated customer base willing to pay a premium for products with reduced environmental impact. Additionally, as sustainability becomes a more significant factor in supplier selection, manufacturers with strong sustainable practices are better positioned to secure partnerships with like-minded businesses.
Innovation and Technological Advancements:
The pursuit of sustainable cost management encourages manufacturers to explore innovative technologies and practices. As they seek to reduce their environmental footprint and resource consumption, manufacturers often invest in research and development to develop new solutions and processes. This drive for innovation can lead to breakthroughs in product design, manufacturing techniques, and operational efficiency.
For instance, the automotive industry has witnessed a shift toward electric and hybrid vehicles driven by sustainability concerns. Manufacturers investing in electric vehicle technology not only address environmental concerns but also position themselves as leaders in a growing market segment. These innovations not only benefit the manufacturer's bottom line but also contribute to broader societal and environmental goals.
Environmental Stewardship and Reputation Enhancement:
Sustainable cost management aligns manufacturing practices with environmental stewardship. By adopting responsible waste management, pollution reduction measures, and energy-efficient technologies, manufacturers can significantly minimize their ecological footprint. This commitment to environmental responsibility resonates with stakeholders and the broader public, enhancing the company's reputation and brand value.
Manufacturers that actively promote their sustainable initiatives bolster their reputation as socially responsible entities. Such positive perceptions can lead to increased customer loyalty, employee engagement, and favorable relationships with regulatory authorities. Moreover, a strong reputation for sustainability can attract environmentally conscious investors and partners, further contributing to the company's overall profitability.
Regulatory Compliance and Risk Mitigation:
Regulatory frameworks are increasingly focusing on environmental and social responsibilities, with stricter regulations aimed at reducing environmental impacts and promoting sustainable practices. Manufacturers that proactively adopt sustainable cost management practices are better positioned to comply with these regulations, minimizing the risk of fines, penalties, and legal challenges.
In addition to regulatory compliance, sustainable cost management also enhances risk mitigation. Manufacturers that consider potential environmental and social risks associated with their operations can implement preventive measures to mitigate these risks.
For example, by addressing supply chain vulnerabilities or potential environmental hazards, manufacturers can prevent costly disruptions to their operations and protect their profitability.
Employee Engagement and Productivity:
Employees are increasingly drawn to companies that demonstrate a commitment to sustainability. Manufacturers that prioritize sustainable cost management often create a positive work environment that aligns with employees' values. This commitment to responsible practices fosters employee engagement and morale, leading to higher productivity and reduced turnover rates.
Moreover, manufacturers can leverage sustainable initiatives to attract and retain top talent. Professionals who are passionate about sustainability and corporate social responsibility are more likely to be drawn to companies that share these values. This influx of skilled and motivated employees can contribute to enhanced operational efficiency and innovation.
Adaptability in a Changing Landscape:
The manufacturing sector is not immune to the evolving challenges of climate change, resource scarcity, and social inequality. Sustainable cost management equips manufacturers with the tools to adapt to these challenges by fostering a culture of flexibility and innovation. Manufacturers that integrate sustainable practices into their operations are better prepared to navigate changing regulations, consumer preferences, and market dynamics.
Identifying Cost Drivers in Manufacturing Processes
Cost drivers are the factors that significantly influence the overall expenses incurred during the production process. By identifying and analyzing these drivers, manufacturers can make informed decisions to allocate resources effectively, reduce waste, and enhance the bottom line.
Cost drivers can be broadly categorized into two types: variable and fixed. Understanding these categories is essential for devising appropriate strategies to manage their impact on manufacturing processes.
a. Variable Cost Drivers:
Variable cost drivers are directly proportional to the level of production. As production volume increases or decreases, these costs fluctuate accordingly. Examples of variable cost drivers include raw materials, direct labor, energy consumption, and packaging materials.
For instance, in a manufacturing process that produces automobiles, the cost of raw materials such as steel, rubber, and plastic would be a variable cost driver. As the production volume increases, the consumption of these materials rises, leading to higher costs. Identifying and understanding variable cost drivers is essential for businesses to manage and control their costs effectively. Here are some common variable cost drivers:
- Labor Costs: Labor costs are a significant variable expense for many businesses. As production increases, the need for labor also increases. The number of employees, the hours worked, and any overtime can directly impact variable labor costs. Additionally, wages and benefits provided to employees are variable costs.
- Raw Materials and Supplies: Businesses that produce physical goods often experience variable costs associated with raw materials and supplies. The quantity of materials required to produce a given quantity of goods directly affects variable costs. Changes in the cost of raw materials can also impact variable costs.
- Utilities and Energy: Energy consumption, including electricity, water, and heating/cooling, can be a significant variable cost for many businesses. Higher production levels typically require more energy usage, leading to increased variable costs in this category.
- Manufacturing Costs: Businesses engaged in manufacturing incur variable costs related to processes such as machining, assembly, and packaging. The more units produced, the more variable costs associated with these manufacturing processes.
- Distribution and Transportation Costs: Companies that transport goods to customers or retailers may experience variable costs related to shipping, transportation, and distribution. The distance traveled, shipping volume and mode of transportation can all influence these costs.
- Direct Labor Costs: Direct labor costs pertain specifically to the workforce directly involved in the production process. As production increases, the need for direct labor, including operators and technicians, increases as well.
- Commissions and Bonuses: For businesses with sales teams, variable costs may include sales commissions and bonuses. These costs are directly tied to sales performance and can vary based on the volume of products or services sold.
- Packaging Costs: The cost of packaging materials and supplies, such as boxes, labels, and packaging inserts, can vary based on production volume. Higher production levels may require more packaging materials, resulting in higher variable costs.
- Outsourced Services: Businesses often outsource certain services, such as customer support or maintenance. The cost of these services can vary based on usage or volume, leading to variable costs.
- Machine Maintenance and Repairs: In manufacturing or production environments, maintenance and repair costs for machinery and equipment can be variable. Higher production levels may lead to more wear and tear on equipment, requiring more frequent maintenance and repairs.
- Marketing and Advertising Costs: Variable costs related to marketing and advertising efforts can increase as a business promotes its products or services more aggressively to capture larger market shares.
- Sales Incentives and Discounts: Variable costs can also include incentives and discounts offered to customers or distributors based on the volume of products purchased.
- Per-Unit Royalties or Licensing Fees: In industries where products are produced under licenses or franchises, the variable cost structure may include per-unit royalties or licensing fees that increase with higher production.
- Waste and Scrap Costs: In manufacturing, the volume of waste or scrap generated can vary based on production levels. Managing waste and minimizing scrap is essential to control variable costs.
- Maintenance and Repairs for Facilities: For businesses with physical facilities, maintenance and repair costs can vary based on the level of activity and usage. Higher production may lead to more wear and tear on facilities, resulting in increased variable costs.
b. Fixed Cost Drivers:
Fixed cost drivers remain relatively constant regardless of changes in production volume. They include costs associated with facilities, equipment, rent, and administrative overhead. Fixed cost drivers are often incurred to maintain the infrastructure and operational capacity required for manufacturing processes.
In the context of the automobile manufacturing example, the lease payment for the production facility, machinery depreciation, and administrative salaries would be examples of fixed-cost drivers. These costs remain relatively stable, even if production volumes vary. Here are some common fixed-cost drivers:
- Rent and Lease Expenses: The cost of renting or leasing facilities, office space, manufacturing plants, or equipment represents a significant fixed cost for many businesses. The terms of the lease, such as monthly rent or annual payments, determine the fixed nature of this cost.
- Salaries and Wages for Permanent Staff: Fixed costs include the salaries and wages of permanent employees who are typically on a fixed pay scale. These costs remain constant regardless of variations in production or business activity.
- Depreciation and Amortization: Depreciation is the allocation of the cost of long-term assets over their useful life, while amortization refers to the same process for intangible assets. These non-cash expenses represent fixed costs because they do not change based on production levels.
- Insurance Premiums: Business insurance premiums, such as property insurance and liability insurance, are typically fixed costs. The premium amount remains stable over a given period regardless of the business's operational activity.
- Loan Interest Payments: The interest paid on loans, whether they are for equipment purchases, real estate, or other business needs, is a fixed cost as long as the interest rate remains constant.
- Annual Licenses and Memberships: Certain licenses, permits, or memberships have fixed annual fees that businesses need to pay regardless of their level of activity.
- Subscription Services: Fixed costs can include subscription services like software licenses, cloud services, and online platforms, where the subscription fees are predetermined and unchanging.
- Salaries of Upper Management: The salaries of top executives and upper management are typically considered fixed costs, as they are predetermined and unaffected by short-term changes in business activity.
- Property Taxes: Property taxes on owned facilities are typically fixed costs, although they can vary based on changes in property value and local tax rates.
- Utilities for Fixed Facilities: If a business has facilities with fixed operational hours, such as office spaces or manufacturing plants, the utilities' fixed costs, like rent, remain constant.
- Lease Payments: Payments for long-term leases on equipment, vehicles, or other assets are typically fixed costs, as they are contracted at a specific amount for a predetermined period.
- Annual Software Maintenance Fees: Many businesses pay annual maintenance fees for software licenses, ensuring access to updates and support. These fees are fixed costs that remain constant over the contract period.
- Subscription-Based Services: Businesses that rely on subscription-based services, such as security systems, internet services, and communication tools, incur fixed costs for these services.
- Marketing and Advertising Retainers: Some businesses engage marketing agencies or consultants on a retainer basis, where a fixed monthly fee is paid for ongoing services.
- Property Leases: Leases for office space, retail locations, or manufacturing facilities typically involve fixed monthly payments regardless of the business's operational activity.
Methods of Identifying Cost Drivers:
Identifying cost drivers requires a thorough analysis of manufacturing processes, resource utilization, and operational data. Several methods can be employed to uncover these drivers:
a. Cost Allocation Analysis:
This method involves breaking down the overall costs of a manufacturing process into specific cost categories. By attributing costs to different aspects of production, organizations can identify which cost categories have the most substantial impact on the total expenses.
Key Concepts in Cost Allocation:
- Direct Costs vs. Indirect Costs: Direct costs are expenses that can be traced directly to a specific cost object, such as a product or project. Indirect costs, also known as overhead costs, are not easily attributable to a single cost object and need to be allocated among multiple objects.
- Cost Object: A cost object is the item, activity, or entity for which costs are being allocated. It could be a product, a department, a project, or any other defined entity within the organization.
- Cost Driver: A cost driver is a variable that influences the amount of cost incurred. It serves as the basis for allocating costs. Cost drivers can be factors like time, usage, square footage, or any metric that correlates with the incurrence of costs.
Methods of Cost Allocation:
- Direct Allocation: When costs can be directly traced to a single cost object, they are allocated directly. For example, if a machine is used solely for producing a particular product, the costs of that machine are directly allocated to the product.
- Step Method: In cases where some costs can be directly attributed, but others require further allocation, the step method is used. Costs are allocated in multiple steps, starting with direct allocation and then moving on to more complex allocations.
- Cost Pools and Allocation Bases: Cost pools group similar costs together, and an allocation base is chosen to distribute those costs. For instance, if overhead costs include rent, utilities, and maintenance, square footage or the number of employees could be used as an allocation base to distribute these costs among departments.
- Reciprocal Allocation: In situations where costs are shared among multiple departments or entities, reciprocal allocation considers the interdependence of the entities and allocates costs accordingly.
b. Activity-Based Costing (ABC):
ABC is a methodology that allocates costs to specific activities within the production process. This approach provides a more accurate understanding of how resources are consumed during each activity, helping to identify the activities that are the primary drivers of costs.
For example, in a furniture manufacturing process, ABC might reveal that the process of assembly requires a significant amount of labor and time, making it a key cost driver. This insight can lead to strategies for streamlining the assembly process.
Key Concepts in Activity-Based Costing (ABC):
- Activities: Activities are specific tasks or processes within an organization that consume resources and incur costs. Activities can be related to production, administrative tasks, distribution, customer service, etc.
- Cost Pools: Cost pools are categories that group similar costs related to specific activities. Each cost pool represents a different type of activity within the organization.
- Cost Drivers: Cost drivers are factors that influence the consumption of resources and the occurrence of activities. They are used to determine the extent of resources consumed by each activity.
Steps in Implementing Activity-Based Costing:
- Identify Activities: Identify all the activities performed within the organization. These activities can be both value-added (directly contributing to product/service quality) and non-value-added (essential for the organization but not directly contributing to product/service quality).
- Determine Cost Drivers: For each activity, determine the most appropriate cost driver. A cost driver should have a logical connection to the consumption of resources for that activity.
- Assign Costs to Activities: Accumulate the costs associated with each activity. This includes direct costs (easily traced to activities) and indirect costs (allocated to activities based on predetermined drivers).
- Allocate Costs to Cost Objects: Once costs are assigned to activities, allocate those costs to specific cost objects (products, services, projects, departments) using the cost driver information.
- Calculate Activity Rates: Calculate an activity rate for each activity by dividing the total cost of the activity by the total units of the cost driver consumed. This rate is used to allocate costs to cost objects.
- Allocate Costs to Cost Objects: Multiply the activity rate by the number of cost driver units consumed by each cost object to allocate costs accurately.
c. Historical Data Analysis:
Analyzing historical data, such as past production runs or financial records, can provide insights into cost patterns. By comparing data from different periods, organizations can identify trends and variations in cost drivers.
Key Concepts in Historical Data Analysis:
- Data Collection: Historical data analysis begins with the collection of relevant data from various sources. This data can be quantitative (numeric) or qualitative (descriptive) and is often obtained from records, databases, surveys, or archives.
- Data Cleaning: Raw data may contain errors, inconsistencies, or missing values. Data cleaning involves identifying and rectifying these issues to ensure the accuracy and reliability of the analysis.
- Exploratory Data Analysis (EDA): EDA involves summarizing and visualizing data to understand its characteristics, distributions, and potential relationships between variables.
- Statistical Analysis: Statistical techniques are applied to historical data to identify patterns, trends, correlations, and other insights. Common statistical methods include regression analysis, time series analysis, hypothesis testing, and clustering.
- Pattern Recognition: Historical data analysis aims to recognize meaningful patterns that have occurred over time. These patterns can be used to understand behavior or make predictions.
- Prediction and Forecasting: By analyzing historical data, predictive models can be developed to forecast future outcomes based on observed patterns and relationships.
d. Sensitivity Analysis:
Sensitivity analysis involves assessing how changes in specific variables impact overall costs. Manufacturers can simulate scenarios where different variables (such as raw material prices, energy costs, or labor rates) vary and observe their effect on total expenses.
For instance, by analyzing how fluctuations in energy prices affect production costs, manufacturers can prepare for potential cost increases and explore energy-efficient alternatives.
Key Concepts in Sensitivity Analysis:
- Variables of Interest: In cost analysis, variables of interest are the factors that can influence costs. These could include production volume, material costs, labor rates, exchange rates, interest rates, demand fluctuations, etc.
- Base Case: The base case represents the initial assumptions or conditions for the cost analysis. It serves as a reference point against which variations in the variables are compared.
- Scenario Analysis: Sensitivity analysis often involves creating scenarios by adjusting specific variables to observe their impact on costs. Each scenario represents a different combination of variable values.
- Range of Variation: Sensitivity analysis typically examines a range of possible values for the variables. This range can be predetermined based on historical data, expert opinions, or simulations.
- Impact Assessment: The goal of sensitivity analysis is to assess how changes in the variables impact the cost outcomes. This is usually measured in terms of percentages or absolute changes.
e. Benchmarking:
Comparing the performance of a manufacturing process with industry benchmarks can help identify cost drivers. This approach provides context by highlighting areas where an organization's costs are higher than the industry average.
Types of Benchmarking in Cost Management:
- Competitive Benchmarking: Involves comparing costs and performance metrics with direct competitors within the same industry. This type of benchmarking helps organizations understand how they stand against similar players in the market.
- Functional Benchmarking: Focuses on comparing processes and practices with organizations that perform similar functions, regardless of industry. It aims to identify cross-industry best practices that can be adapted to improve cost management.
- Internal Benchmarking: Compares different departments, units, or divisions within the same organization. It helps identify variations in cost efficiency and encourages knowledge sharing and improvement within the organization.
- Strategic Benchmarking: Involves benchmarking against organizations that are recognized as leaders in certain areas, even if they are not direct competitors. This type of benchmarking aims to emulate strategies and practices that have contributed to their success.
Strategies for Managing Cost Drivers:
Once cost drivers are identified, manufacturers can implement strategies to manage their impact effectively:
- Process Optimization:
Efficiency improvements in manufacturing processes can mitigate the impact of cost drivers. Lean manufacturing principles, Six Sigma methodologies, and process reengineering can help identify areas for optimization, leading to reduced waste, shorter cycle times, and enhanced resource utilization.
- Supplier Collaboration:
Collaborating with suppliers can lead to cost reductions in areas such as raw materials and components. Negotiating favorable terms, exploring bulk purchasing options, and seeking alternatives with better pricing can all contribute to managing cost drivers.
- Technology Adoption:
Investing in advanced technologies, such as automation, robotics, and data analytics, can reduce labor costs, enhance accuracy, and improve overall process efficiency. Technological advancements can mitigate the impact of labor-related cost drivers.
- Energy Efficiency Measures:
Energy consumption is often a significant cost driver in manufacturing. Implementing energy-efficient technologies, optimizing equipment usage, and adopting renewable energy sources can lead to substantial cost savings over time.
- Employee Training and Development:
Investing in employee training can lead to increased productivity and reduced errors, mitigating the impact of labor-related cost drivers. Skilled and well-trained employees are more efficient and contribute to higher overall operational excellence.
- Maintenance and Equipment Upkeep:
Proper maintenance of equipment and machinery reduces downtime and extends its lifespan. Preventive maintenance practices can prevent unexpected breakdowns and repair costs, which are common fixed-cost drivers.
- Supplier Diversification:
Depending heavily on a single supplier can make manufacturers vulnerable to fluctuations in raw material prices or availability. Diversifying suppliers can provide greater flexibility in managing cost drivers related to raw materials.
Optimizing Resource Allocation for Efficiency and Savings
The judicious allocation of resources, both financial and non-financial, can lead to streamlined processes, improved productivity, and ultimately, increased profitability.
Resource allocation involves the distribution of various assets, including financial resources, human capital, time, and technology, to different aspects of a business's operations. The goal is to ensure that resources are utilized most efficiently and effectively to achieve organizational objectives. Efficient resource allocation not only enhances productivity but also contributes to sustainable cost management, a critical consideration for businesses aiming to maintain their competitive edge.
- Strategic Alignment and Priority Setting
To optimize resource allocation, a business must first establish a clear strategic direction. This involves defining the company's mission, vision, and long-term goals. With strategic alignment in place, it becomes easier to prioritize resource allocation based on the initiatives that directly support the overarching objectives.
Identifying high-priority projects and core activities enables businesses to allocate resources where they can generate the most value. This strategic approach prevents the scattering of resources across various projects without a clear focus, ensuring that efforts are concentrated on initiatives that drive growth and efficiency.
- Data-Driven Decision-Making
Data plays a pivotal role in optimizing resource allocation. Businesses should gather and analyze relevant data to make informed decisions about resource allocation. This includes financial data, performance metrics, market trends, and customer insights. By understanding where resources are most needed and where they can have the greatest impact, businesses can allocate them more effectively.
Data-driven decision-making enables businesses to identify bottlenecks, inefficiencies, and areas of potential savings. For example, analyzing production data can reveal where process improvements are needed, leading to cost reductions and enhanced productivity. Similarly, analyzing customer data can guide marketing efforts, ensuring that resources are allocated to the most promising market segments.
- Cost-Benefit Analysis
Cost-benefit analysis is a powerful tool for evaluating the potential returns of different resource allocation decisions. It involves comparing the costs associated with a particular initiative or project to the expected benefits it will generate. By quantifying both costs and benefits, businesses can prioritize projects that offer the highest return on investment.
When applying cost-benefit analysis, businesses should consider not only financial costs and benefits but also non-financial factors. For instance, a project might have intangible benefits like improved brand reputation or enhanced customer loyalty. Including these factors in the analysis provides a more comprehensive picture of the potential impact of resource allocation decisions.
- Agile Resource Management
In today's dynamic business environment, agility is crucial for effective resource allocation. Agile resource management involves the ability to quickly adapt and reallocate resources in response to changing market conditions, customer demands, or internal factors. This flexibility allows businesses to seize opportunities and mitigate risks more effectively.
Implementing agile resource management requires clear communication and collaboration across departments. Cross-functional teams can assess resource needs, prioritize projects, and allocate resources based on real-time insights. This approach ensures that resources are allocated to initiatives that align with current market trends and customer preferences.
- Lean and Six Sigma Principles
Lean and Six Sigma methodologies focus on eliminating waste, reducing defects, and improving process efficiency. These principles can be applied to resource allocation by identifying and eliminating activities that do not contribute value to the final product or service. By streamlining processes and reducing inefficiencies, businesses can optimize the use of their resources.
For example, the concept of "just-in-time" resource allocation from lean management emphasizes delivering resources precisely when and where they are needed, reducing excess inventory and associated carrying costs. Six Sigma's data-driven approach can help identify areas where resources are being wasted due to defects or errors, leading to improved resource utilization and cost savings.
- Technology and Automation
Advancements in technology offer opportunities to optimize resource allocation through automation and digitalization. Automation can streamline repetitive tasks, allowing human resources to be allocated to more strategic and value-added activities.
Additionally, digital tools such as project management software, resource planning systems, and predictive analytics platforms enable businesses to allocate resources more efficiently and accurately.
Automated resource allocation systems can take into account factors such as employee skill sets, project timelines, and budget constraints. These systems can help ensure that the right resources are allocated to the right projects at the right time, minimizing delays and cost overruns.
Leveraging Technology for Cost Monitoring and Analysis
Technology has revolutionized the way businesses operate and manage their finances. Traditional methods of cost monitoring and analysis often relied on manual processes, spreadsheets, and retrospective reporting.
However, with the advent of advanced digital solutions, companies can now access real-time data, conduct complex analyses, and make proactive decisions to optimize their cost structures.
Digital Tools for Real-Time Data Collection
One of the fundamental shifts brought about by technology is the ability to collect and access real-time data. Digital tools such as Enterprise Resource Planning (ERP) systems, expense management software, and cloud-based platforms enable businesses to capture expenses as they occur, providing an accurate and up-to-date view of their financial situation.
ERP systems integrate various functions of a business, including finance, procurement, and operations, into a single platform. This integration facilitates seamless data sharing and eliminates the need for manual data entry across different systems. Additionally, expense management software allows employees to submit expenses digitally, streamlining the approval process and reducing the risk of errors.
Data Analytics for In-Depth Insights
The vast amount of data generated by businesses can be transformed into valuable insights using data analytics tools. These tools allow companies to uncover patterns, trends, and anomalies within their expenses, leading to more informed decision-making.
Advanced data analytics techniques, such as predictive and prescriptive analytics, enable businesses to anticipate cost fluctuations and identify potential cost-saving opportunities. For instance, predictive analytics can help predict demand fluctuations, allowing companies to adjust their production schedules and inventory levels accordingly, minimizing wastage and reducing costs.
Cost Classification and Categorization
Technology aids in accurate cost classification and categorization, ensuring that expenses are properly allocated to relevant cost centers and projects. This is particularly valuable in complex organizations with multiple departments and initiatives.
Automation can assist in categorizing expenses based on predefined rules and criteria. For example, machine learning algorithms can analyze historical data to automatically assign expenses to specific categories, reducing manual effort and errors. This not only improves the accuracy of cost allocation but also provides a clearer picture of where resources are being utilized.
Visualization Tools for Enhanced Understanding
Visual representations of cost data can greatly enhance understanding and decision-making. Data visualization tools, such as dashboards and interactive graphs, transform complex financial information into easily digestible formats.
These tools allow stakeholders to explore cost trends, compare different cost categories, and identify outliers. For instance, a manufacturing company can use a dashboard to track the cost of raw materials over time, helping them identify potential fluctuations that could impact their profitability. Visualization tools provide a clear overview of the financial landscape, enabling quicker and more informed responses.
Benchmarking and Competitive Analysis
Technology also facilitates benchmarking and competitive analysis by providing access to industry-wide data and performance metrics. With the availability of market insights, businesses can compare their cost structures to industry averages and identify areas where they may be over- or under-performing.
Benchmarking can uncover cost-saving opportunities by highlighting areas where expenses are significantly higher than industry standards. This could lead to investigations into inefficient processes or supplier relationships. Additionally, competitive analysis can inform decisions about pricing strategies, allowing businesses to position themselves effectively within their market.
Scenario Modeling and Sensitivity Analysis
Technology empowers businesses to simulate various scenarios and assess the potential impact of different decisions on costs. Scenario modeling involves creating hypothetical situations and evaluating how changes in variables, such as production volume or input costs, would affect overall costs.
Sensitivity analysis, a subset of scenario modeling, examines the sensitivity of outcomes to changes in specific variables. For instance, a retail company could use sensitivity analysis to understand how fluctuations in exchange rates might impact the cost of imported goods. These tools provide a forward-looking perspective, helping businesses prepare for different cost-related contingencies.
Automation and Process Optimization
Automation is a game-changer in cost monitoring and analysis. Routine tasks, such as data entry, reconciliation, and reporting, can be automated, freeing up valuable human resources for more strategic activities.
Robotic Process Automation (RPA) can handle repetitive tasks with high accuracy and speed. For example, RPA can extract cost data from invoices and automatically update expense records in the ERP system. This reduces the likelihood of manual errors and ensures that cost information is consistently accurate.
Balancing Quality and Cost Considerations
Quality and cost are two key pillars that underpin business success. Quality signifies the level of excellence, reliability, and satisfaction a product or service delivers to customers. On the other hand, cost represents the expenditure of resources required to produce, deliver, and support that product or service.
These two aspects are inherently interconnected, as the pursuit of high quality often incurs higher costs, while cost-cutting measures can potentially compromise quality.
Understanding the Quality-Cost Trade-off
The quality-cost trade-off is a central concept in business strategy that underscores the tension between delivering exceptional quality and controlling costs. When businesses focus on improving quality, they often invest in better materials, advanced technology, and skilled labor, all of which contribute to higher costs. Conversely, cost-cutting measures, such as reducing resources or outsourcing, may lead to a decline in quality if not carefully managed.
Striking the right balance between quality and cost necessitates a nuanced approach that considers both short-term and long-term implications. Short-term cost savings achieved by sacrificing quality can lead to longer-term repercussions, including customer dissatisfaction, reduced brand reputation, and increased expenses due to corrective actions.
Defining Quality Metrics and Standards
To achieve a harmonious balance between quality and cost, organizations must define clear quality metrics and standards. These benchmarks serve as guiding principles for decision-making across the entire value chain, from product development to customer service.
Businesses should collaborate with their stakeholders, including customers, suppliers, and employees, to establish quality expectations. Defining quality standards ensures that all parties involved understand the level of excellence required and allows for more informed discussions about the trade-offs between quality and cost.
- Customer-Centric Approach
Quality, ultimately, is determined by customer perception and satisfaction. Businesses that prioritize a customer-centric approach often find a successful balance between quality and cost. By closely listening to customer feedback, organizations can identify areas where quality improvements are necessary and allocate resources more effectively.
Customer feedback loops, surveys, and focus groups provide valuable insights into which aspects of a product or service matter most to customers. This information can guide resource allocation decisions, ensuring that investments are directed towards enhancing the aspects of quality that align with customer expectations.
- Total Quality Management (TQM) Principles
Total Quality Management (TQM) is a comprehensive framework that emphasizes continuous improvement in all areas of a business. TQM principles advocate for involving employees at all levels, fostering a culture of quality, and minimizing waste in processes. These principles can help organizations achieve better quality outcomes while maintaining cost efficiencies.
TQM encourages organizations to adopt a systematic approach to identifying and addressing quality issues. By streamlining processes, eliminating defects, and continuously seeking ways to enhance quality, businesses can avoid the costs associated with rework, defects, and customer complaints.
- Lean Principles and Process Optimization
Lean principles focus on eliminating waste and maximizing efficiency throughout the value chain. Lean methodologies help businesses identify and eliminate activities that do not add value, thus contributing to cost reduction while maintaining or improving quality.
Applying lean principles involves analyzing processes to identify bottlenecks, redundancies, and inefficiencies. By streamlining workflows, businesses can achieve cost savings without compromising quality. For example, the implementation of just-in-time inventory practices can minimize excess inventory costs while ensuring that materials are available when needed.
Supplier Collaboration and Strategic Partnerships
Suppliers play a crucial role in the quality-cost equation. Collaborating closely with suppliers and forging strategic partnerships can lead to mutual benefits in terms of quality improvements and cost optimization.
When businesses work closely with suppliers, they can negotiate favorable terms, leverage economies of scale, and receive early insights into industry trends. Suppliers who align with the organization's quality standards can provide consistent, high-quality inputs, reducing the likelihood of defects and quality-related costs down the line.
Collaboration and Communication in Cost Management
Collaboration refers to the process of individuals or teams working together to achieve common goals. In cost management, collaboration involves different stakeholders coming together to share insights, ideas, and expertise, fostering a holistic approach to managing costs. The significance of collaboration in cost management can be understood through the following points:
- Cross-functional Expertise: Effective cost management requires input from various departments such as finance, operations, procurement, and project management. Collaboration allows experts from these different fields to pool their knowledge and perspectives, leading to well-rounded cost management strategies.
- Enhanced Decision-making: When diverse perspectives are considered, the decision-making process becomes more informed and robust. Collaborative discussions help in identifying potential cost-saving opportunities and addressing potential risks, leading to better decisions that balance short-term cost reductions with long-term sustainability.
- Innovative Solutions: Collaborative environments often foster creativity and innovation. When individuals with different backgrounds collaborate, they can brainstorm innovative ways to optimize costs without compromising quality or customer satisfaction.
- Shared Accountability: Collaboration promotes a sense of shared ownership among stakeholders. When individuals work together on cost management, they are more likely to take ownership of cost-related outcomes, leading to better adherence to budgetary constraints.
- Timely Problem Solving: Cost overruns and deviations from budgets can occur due to unforeseen circumstances. Collaborative teams can quickly respond to these challenges, brainstorming and implementing solutions promptly.
The Role of Communication in Cost Management: Effective communication is a cornerstone of successful cost management. It involves the clear and accurate exchange of information among stakeholders at all levels. The impact of communication on cost management is highlighted by the following points:
- Transparency: Transparent communication ensures that all stakeholders have a clear understanding of project goals, budgetary constraints, and cost-saving initiatives. This reduces misunderstandings and minimizes the likelihood of unexpected cost overruns.
- Budget Alignment: Clear communication of budgetary allocations and expectations helps teams align their activities with financial constraints. This prevents activities that could lead to unnecessary costs or misallocation of resources.
- Progress Tracking: Regular communication about the progress of cost management initiatives allows teams to track their achievements against predetermined targets. If deviations occur, timely communication enables quick corrective actions.
- Risk Management: Effective communication helps in identifying potential risks that could impact cost management. By sharing insights about emerging risks, stakeholders can collectively develop strategies to mitigate these threats and their associated costs.
- Stakeholder Engagement: Engaging stakeholders through transparent communication builds their trust and commitment. When stakeholders understand the rationale behind cost management decisions, they are more likely to support and actively participate in cost-saving efforts.
- Feedback Loops: Communication channels provide a means for stakeholders to provide feedback on cost management strategies. This feedback loop allows for continuous improvement and refinement of cost management processes.
Collaboration and Communication Tools and Strategies in Cost Management: To leverage the benefits of collaboration and communication in cost management, organizations can adopt various tools and strategies:
- Project Management Software: Utilizing project management tools that facilitate collaboration, communication, and resource allocation enhances visibility into cost-related activities. Tools like Asana, Trello, and Microsoft Project allow teams to track progress and communicate effectively.
- Cost Management Software: Specialized cost management software helps in tracking expenses, monitoring budget adherence, and generating cost-related reports. Tools like QuickBooks enable accurate financial management.
- Regular Meetings and Workshops: Scheduled meetings and workshops provide platforms for cross-functional teams to discuss cost management strategies, share updates, and brainstorm solutions. Regular communication through these sessions ensures everyone is aligned with cost-saving goals.
- Open Communication Channels: Organizations should establish open channels of communication, both formal and informal, to encourage the free flow of information. This can include email updates, instant messaging platforms, and regular status reports.
- Data Visualization Tools: Using data visualization tools like Tableau or Power BI can help in presenting complex cost-related information in a visual format, making it easier for stakeholders to understand and analyze.
- Change Management: Implementing effective communication strategies during changes in cost management processes or tools is crucial. Properly communicating the reasons for change, benefits, and training resources can enhance adoption and minimize disruptions.
Tracking Environmental Impact in Cost Assessments
The incorporation of environmental impact tracking in cost assessments acknowledges the interconnectedness of economic activities and their effects on the natural world. This integration holds several key benefits:
- Holistic Decision-Making: Factoring in environmental impact ensures a comprehensive evaluation of costs. Decision-makers can make informed choices that align with both economic and environmental objectives, leading to more balanced and responsible outcomes.
- Risk Mitigation: Environmental risks, such as regulatory changes, resource scarcity, and reputational damage, can significantly affect the long-term costs of a project. By including environmental impact assessments, organizations can identify and address potential risks in advance.
- Long-Term Sustainability: By considering environmental impacts, organizations shift their focus from short-term financial gains to long-term sustainability. This approach is essential for maintaining business resilience and adapting to changing environmental conditions.
- Stakeholder Engagement: Many stakeholders, including customers, investors, and regulatory bodies, increasingly expect organizations to demonstrate their commitment to sustainability. Integrating environmental impact assessments into cost evaluations showcases responsible practices and enhances stakeholder trust.
- Innovation and Efficiency: Environmental considerations can drive innovation by encouraging the development of eco-friendly technologies and processes. Such innovations often lead to increased efficiency, reduced costs, and competitive advantage.
Challenges in Tracking Environmental Impact in Cost Assessments: While the benefits are significant, several challenges must be addressed to effectively track environmental impact in cost assessments:
- Complexity of Interactions: Environmental impacts are intricate and interconnected. Activities in one area can lead to cascading effects in others, making it challenging to accurately predict the full scope of consequences.
- Data Availability and Quality: Reliable and comprehensive data on environmental impacts can be challenging to obtain. Accurate assessment requires data on emissions, resource consumption, waste generation, and more, which may not always be readily available.
- Methodological Variability: Different methodologies exist for assessing environmental impacts, such as Life Cycle Assessment (LCA) and carbon footprint analysis. Choosing the most appropriate method for a specific context can be complex and may lead to inconsistent results.
- Monetary Valuation of Environmental Impacts: Assigning monetary values to environmental impacts (such as carbon pricing) is subject to debate and can be controversial. Deciding on appropriate valuation methods requires careful consideration.
- Trade-offs and Conflicting Goals: In some cases, pursuing environmentally friendly options may initially result in higher costs. Balancing these trade-offs while striving for sustainability can be challenging.
Methodologies for Integrating Environmental Impact into Cost Assessments: Several methodologies are available for integrating environmental impact assessments into cost evaluations:
- Life Cycle Assessment (LCA): LCA is a widely used methodology that assesses the environmental impacts of a product, process, or activity across its entire lifecycle. It considers resource extraction, production, transportation, use, and disposal. LCA provides a holistic view of environmental impacts and helps identify hotspots for improvement.
- Carbon Footprint Analysis: This methodology focuses specifically on measuring the greenhouse gas emissions associated with a product or process. It helps organizations understand their carbon emissions and develop strategies for emission reduction.
- Environmental Input-Output Analysis: This approach analyzes the direct and indirect impacts of economic activities on the environment. It considers how different sectors of the economy are interconnected and how changes in one sector can affect others.
- Eco-Efficiency Analysis: Eco-efficiency involves evaluating the relationship between the environmental impact of an activity and the economic value it generates. It aims to identify ways to achieve more output with less input and fewer environmental resources.
Tools for Integrating Environmental Impact into Cost Assessments: Several tools can facilitate the integration of environmental impact considerations into cost assessments:
- Sustainability Software: Dedicated software platforms, such as SimaPro and GaBi, provide tools for conducting life cycle assessments, carbon footprint analyses, and other environmental impact assessments. These platforms streamline data collection, analysis, and reporting.
- Environmental Management Systems (EMS): EMS software, such as ISO 14001-compliant systems, helps organizations monitor and manage their environmental performance. These systems provide a structured approach to tracking and reducing environmental impacts.
- Carbon Accounting Tools: Carbon accounting software assists organizations in calculating and reporting their carbon emissions. These tools often provide features for scenario analysis, helping organizations explore emissions reduction strategies.
- Triple Bottom Line Accounting Software: Some accounting software solutions incorporate the triple bottom line framework, which includes financial, social, and environmental considerations. These tools help organizations evaluate the broader impacts of their activities.
- Supply Chain Management Software: Many organizations' environmental impacts extend beyond their immediate operations to their supply chains. Supply chain management software can help track and manage environmental impacts throughout the value chain.
Compliance and Regulatory Alignment in Cost Control
Compliance refers to the act of adhering to laws, regulations, industry standards, and internal policies that govern various aspects of business conduct. While cost control focuses on managing expenses and optimizing resources, it must be carried out within the boundaries set by compliance and regulatory frameworks.
Compliance refers to the adherence of an organization to laws, regulations, standards, and internal policies that govern its operations. It encompasses various aspects, including financial reporting, data protection, workplace safety, environmental regulations, consumer protection, and more. Compliance ensures that organizations operate within legal boundaries, uphold ethical standards, and mitigate the risks associated with non-compliance.
Regulatory Alignment involves aligning an organization's practices and processes with relevant regulations, standards, and guidelines. It requires a proactive approach to understanding and adhering to regulatory requirements that impact the organization's industry, sector, or geographic location.
The Risks of Non-Compliance in Cost Control:
Non-compliance in cost control can lead to a range of adverse consequences:
- Legal Consequences: Violating laws and regulations can result in legal actions, fines, penalties, and even criminal charges for the organization and its leadership.
- Reputational Damage: Non-compliance tarnishes an organization's reputation, leading to a loss of stakeholder trust, decreased customer loyalty, and negative media coverage.
- Operational Disruptions: Legal actions and regulatory investigations can disrupt business operations, impacting productivity, supply chains, and customer relationships.
- Financial Impact: Fines, penalties, legal fees, and potential compensation to affected parties can lead to significant financial losses.
- Loss of Competitive Advantage: Organizations with a reputation for ethical conduct and compliance enjoy a competitive advantage over non-compliant competitors.
Strategies for Achieving Compliance and Regulatory Alignment in Cost Control:
To overcome the challenges and achieve alignment between compliance and cost control, organizations can implement several strategies:
- Compliance-Centric Culture: Foster a culture that prioritizes compliance and ethical behavior throughout the organization. Leadership commitment, training programs, and regular communication are key.
- Cross-Functional Collaboration: Establish collaboration between compliance, legal, finance, and other relevant departments to ensure alignment in decision-making.
- Risk Assessment: Conduct thorough risk assessments to identify compliance risks associated with cost control measures. This helps prioritize areas that require special attention.
- Regulatory Intelligence: Stay updated on industry-specific regulations and changes in the regulatory landscape. Regularly review compliance requirements to ensure accurate understanding.
- Compliance Audits: Regularly conduct compliance audits to identify gaps and address non-compliance issues promptly. Audits help organizations identify areas where cost control measures might conflict with regulations.
- Clear Policies and Procedures: Develop clear and comprehensive policies and procedures that guide cost control efforts while ensuring compliance. These documents should be accessible to all employees.
Managing Supply Chain Costs for Sustainability
Supply chain costs encompass a wide array of expenses incurred throughout the process of sourcing, producing, and distributing goods and services. These costs are influenced by factors such as raw material prices, transportation expenses, inventory holding costs, and labor wages.
However, the traditional approach to supply chain cost management often fails to account for the broader impact of these operations on the environment, society, and long-term business viability.
Sustainability, on the other hand, involves the integration of economic, environmental, and social considerations into business strategies. It aims to minimize negative impacts on the environment, promote social responsibility, and ensure the long-term success of organizations.
Challenges in Managing Supply Chain Costs for Sustainability:
Several challenges are inherent in aligning supply chain costs with sustainability objectives:
- Lack of Visibility and Transparency: Many supply chains span multiple geographies and involve numerous suppliers, making it challenging to gain visibility into the environmental and social practices at each stage. This lack of transparency hinders efforts to assess the true costs and impacts of the supply chain.
- The complexity of Metrics: Measuring sustainability performance involves a complex interplay of economic, environmental, and social indicators. Developing meaningful metrics that capture these dimensions accurately can be daunting.
- Short-Term Focus: Organizations often prioritize short-term financial gains over long-term sustainability goals. This focus can lead to decisions that sacrifice sustainability for immediate cost savings.
- Supplier Engagement: Suppliers might not share the same level of commitment to sustainability. Convincing suppliers to adopt sustainable practices can be challenging, particularly if it entails higher costs.
Strategies for Managing Supply Chain Costs for Sustainability
- Lean and Efficient Operations: Embracing lean principles can lead to reduced waste and increased efficiency within supply chain operations. Techniques such as Just-in-Time (JIT) inventory management and Six Sigma can optimize resource utilization, thereby minimizing costs and environmental impacts.
- Reverse Logistics and Circular Economy: Implementing effective reverse logistics processes can recover value from products at the end of their lifecycle, reducing disposal costs and promoting a circular economy. Remanufacturing, refurbishing, and recycling initiatives can extend the life of products and reduce the need for new resource extraction.
- Technology and Data Analytics: Leveraging advanced technologies such as the Internet of Things (IoT), blockchain, and data analytics can provide real-time visibility into supply chain operations. This data-driven approach enables informed decision-making, enhances risk management, and identifies opportunities for cost savings and sustainability improvements.
Measuring Success: Key Performance Indicators (KPIs)
Effective cost management is a critical aspect of business operations, as it directly impacts profitability, competitiveness, and sustainability. To gauge the success of cost management initiatives, organizations rely on Key Performance Indicators (KPIs) – quantifiable metrics that provide insights into various aspects of cost control and efficiency.
By tracking these KPIs, businesses can assess their progress, identify areas for improvement, and make informed decisions to optimize their cost management strategies.
- Cost of Goods Sold (COGS)
The COGS KPI evaluates the direct costs incurred in producing goods or services. It encompasses expenses such as raw materials, labor, and manufacturing overhead. Monitoring COGS helps businesses assess the efficiency of their production processes and identify trends in cost fluctuations that could impact profitability.
- Gross Profit Margin
Gross profit margin is the ratio of gross profit (revenue minus COGS) to total revenue, expressed as a percentage. This KPI measures the proportion of revenue that remains after accounting for direct production costs. A higher gross profit margin indicates better cost management and pricing strategies.
- Operating Expense Ratio
The operating expense ratio calculates operating expenses (such as salaries, rent, utilities, and marketing) as a percentage of total revenue. This KPI provides insights into how efficiently a company is managing its non-production costs. A lower operating expense ratio indicates effective cost control.
- Earnings Before Interest and Taxes (EBIT)
EBIT represents a company's operating earnings before accounting for interest and taxes. It showcases the business's ability to generate profits from its core operations. Tracking EBIT helps assess cost management's impact on operating income and profitability.
- EBITDA (Earnings Before Interest, Taxes, Depreciation, and Amortization)
EBITDA further adds back depreciation and amortization to EBIT. It provides a clearer view of a company's operational performance by excluding non-cash expenses. EBITDA is particularly useful when comparing organizations with varying capital structures.
- Return on Investment (ROI)
ROI measures the profitability of an investment relative to its cost. It helps evaluate the efficiency of capital allocation and whether investments in cost management initiatives are yielding desired returns.
- Cost Variance
Cost variance assesses the difference between expected costs and actual costs. By tracking this KPI, businesses can identify cost overruns or savings deviations and take corrective actions as needed.
- Inventory Turnover
Inventory turnover calculates how many times a company's inventory is sold and replaced within a given period. A higher inventory turnover indicates efficient inventory management, reducing holding costs and potential waste.
- Accounts Payable Turnover
Accounts payable turnover gauges how quickly a company pays off its suppliers. A higher turnover suggests efficient management of payables and potential negotiation leverage for favorable terms.
- Cost Per Unit or Service
Calculating the cost per unit or service helps assess the efficiency of production or service delivery. Lowering the cost per unit while maintaining quality indicates successful cost management.
- Cost Savings
Tracking cost savings resulting from specific initiatives, such as process optimization or supplier negotiations, quantifies the impact of cost management efforts. This KPI encourages a proactive approach to cost reduction.
- Sustainability Metrics
Incorporating sustainability metrics, such as carbon emissions reduction or water usage efficiency, into cost management KPIs showcases the alignment between cost control and environmental responsibility.
Training and Empowering Employees in Cost Management
Training and empowering employees in cost management can have a significant impact on overall operational efficiency, profitability, and the successful implementation of cost-saving initiatives.
Importance of Employee Training in Cost Management
- Enhanced Awareness: Many employees may not fully understand how their roles and actions impact the organization's overall costs. Training helps raise awareness about cost implications and encourages a more mindful approach to resource utilization.
- Ownership and Accountability: When employees understand the financial implications of their decisions, they are more likely to take ownership of their tasks and be accountable for cost-efficient outcomes.
- Informed Decision-Making: Well-informed employees are better equipped to make decisions that align with cost-saving goals. Training provides them with the knowledge and tools needed to evaluate options and choose the most financially responsible course of action.
- Empowerment and Engagement: When employees are empowered with the knowledge to identify cost-saving opportunities, they feel more engaged in their roles and contribute actively to the organization's success.
Strategies for Employee Training and Empowerment
- Tailored Training Programs: Develop training programs that cater to the specific needs of different departments and roles. For instance, sales teams can be trained in negotiation techniques to secure better terms with suppliers, while production teams can focus on lean manufacturing principles.
- Real-Life Case Studies: Incorporate real-life case studies that demonstrate how cost management initiatives have led to tangible benefits for the organization. These examples make the training more relatable and inspire employees to think creatively.
- Cross-Functional Workshops: Organize workshops that bring together employees from various departments to brainstorm cost-saving ideas collaboratively. Cross-functional collaboration often leads to innovative solutions that wouldn't be apparent within individual silos.
- Financial Literacy Training: Provide basic financial literacy training to employees who do not have a background in finance. This training can cover concepts like budgeting, cost analysis, and reading financial statements.
Future Trends: Innovations in Sustainable Cost Management
Organizations are increasingly recognizing that integrating sustainability into their cost management strategies not only mitigates risks but also offers opportunities for innovation and competitive advantage. In the coming years, several trends and innovations are likely to shape the field of sustainable cost management.
Circular Economy Integration
The concept of the circular economy emphasizes reducing waste, reusing materials, and recycling products at the end of their lifecycle. In the future, businesses will place greater emphasis on designing products and processes that minimize waste and maximize the recovery of valuable resources.
By adopting circular economy principles, companies can reduce raw material costs, decrease environmental impact, and create new revenue streams through product refurbishment and recycling.
Advanced-Data Analytics and AI
Data analytics and artificial intelligence (AI) will play a pivotal role in sustainable cost management. Businesses will leverage these technologies to gather real-time data from various sources along the supply chain, enabling better demand forecasting, optimized inventory management, and enhanced risk assessment.
AI-powered algorithms can identify cost-saving opportunities and recommend efficient resource allocation strategies, leading to significant operational efficiencies.
Blockchain for Supply Chain Transparency
Blockchain technology enhances supply chain transparency by creating an immutable and traceable record of transactions. This can ensure the authenticity and origin of products, reduce the risk of fraud, and enable more accurate tracking of resources and materials.
Enhanced transparency also facilitates the identification of inefficiencies and waste within the supply chain.
Renewable Energy Adoption
As the cost of renewable energy technologies continues to decline, more businesses will invest in generating their energy from renewable sources such as solar, wind, and hydropower. By reducing reliance on traditional energy sources, organizations can cut energy costs, lower carbon emissions, and improve their sustainability profiles.
Green Product Innovation
Consumers are increasingly demanding environmentally friendly products. Businesses will invest in research and development to create innovative products with lower environmental footprints. Green product innovation can lead to reduced production costs, enhanced market competitiveness, and improved brand reputation.
Carbon Pricing and Emission Reduction Initiatives
With a growing emphasis on addressing climate change, carbon pricing mechanisms and emissions reduction initiatives will become more prevalent. Businesses will need to factor carbon-related costs into their operations and supply chains. Implementing emission reduction strategies can lead to cost savings, regulatory compliance, and positive public perception.
Collaborative Sustainability Networks
Collaborative networks will emerge to address shared sustainability challenges. Industry alliances, consortiums, and platforms will facilitate the exchange of best practices, data, and solutions. These networks can accelerate innovation, reduce duplication of efforts, and create economies of scale in sustainable cost management.
Impact Measurement and Reporting
Organizations will focus on quantifying the positive environmental and social impacts of their cost management strategies. Measuring and reporting these impacts, such as reduced carbon emissions or improved community well-being, can enhance brand credibility and attract socially conscious consumers and investors.
How Can Deskera Help You?
Deskera ERP and MRP systems help you to keep your business units organized. The system's primary functions are as follows:
- Keep track of your raw materials and final items inventories
- Control production schedules and routings
- Keep a bill of materials
- Produce thorough reports
- Make your own dashboards
Deskera ERP offers a range of tools and features that can help businesses effectively manage their costs across various operational processes. From budgeting and expense tracking to cost allocation and analysis, Deskera ERP provides comprehensive solutions for cost management. Here's how Deskera ERP can help in cost management:
- Budgeting and Forecasting: Deskera ERP allows businesses to create, monitor, and manage budgets for different departments, projects, or activities. This helps in setting spending limits, predicting costs, and tracking actual expenses against budgeted amounts.
- Expense Tracking: The system enables businesses to track expenses in real time, including purchases, employee reimbursements, travel expenses, and more. This ensures accurate expense recording and visibility.
- Cost Allocation: Deskera ERP supports the allocation of costs to specific projects, products, or departments. This helps in understanding the true cost of different activities and aids in decision-making.
- Purchase Order Management: The system streamlines purchase order creation, approval, and tracking, ensuring that purchases are made within budget and approved channels.
Deskera Books enables you to manage your accounts and finances more effectively. Maintain sound accounting practices by automating accounting operations such as billing, invoicing, and payment processing.
Deskera CRM is a strong solution that manages your sales and assists you in closing agreements quickly. It not only allows you to do critical duties such as lead generation via email, but it also provides you with a comprehensive view of your sales funnel.
Deskera People is a simple tool for taking control of your human resource management functions. The technology not only speeds up payroll processing but also allows you to manage all other activities such as overtime, benefits, bonuses, training programs, and much more.
Conclusion
Sustainable cost management is a fundamental pillar that manufacturers must embrace to navigate the complexities of the modern business landscape and ensure long-term profitability. Throughout this article, we have delved into the intricacies, benefits, and challenges associated with adopting sustainable cost management practices.
Manufacturers operate in an environment characterized by constant change, from technological advancements to evolving consumer preferences. As such, the implementation of sustainable cost management practices is not just a strategic choice but a necessity for survival and growth. By diligently managing costs across all aspects of their operations, manufacturers can safeguard profitability in the face of unpredictable market dynamics.
The benefits of sustainable cost management extend beyond financial gains. A leaner, more efficient operation is inherently more resilient, better equipped to weather economic downturns or disruptions in the supply chain.
Sustainable cost management is not a fleeting trend but a paradigm shift that manufacturers must embrace to secure their profitability and long-term viability. By adopting holistic, forward-thinking approaches that consider environmental, social, and economic impacts, manufacturers can achieve a balanced equation where financial gains coexist with responsible business practices.
As the manufacturing landscape continues to evolve, sustainable cost management remains an essential tool that propels manufacturers toward profitability, resilience, and success in a rapidly changing world.
Key Takeaways
- Sustainable cost management is not just a choice; it's a strategic imperative for manufacturers aiming to thrive in a dynamic and competitive market.
- It involves more than just cutting costs. It's a holistic approach that encompasses efficient resource allocation, waste reduction, and environmentally responsible practices.
- Sustainable cost management builds operational resilience, enabling manufacturers to navigate economic uncertainties and disruptions more effectively.
- Embracing sustainable practices demonstrates a commitment to environmental responsibility, aligning with growing consumer demands for ethical business practices.
- While short-term cost-cutting is important, sustainable cost management takes a long-term perspective, balancing immediate gains with lasting benefits.
- It encourages innovation as manufacturers seek creative ways to optimize processes, reduce waste, and enhance efficiency.
- Sustainable practices don't just save the environment; they directly impact the bottom line through reduced expenses and increased operational efficiency.
- Collaborating with suppliers and partners who share sustainability goals can lead to mutual cost savings and efficiency improvements.
- The integration of digital technologies like IoT and advanced analytics empowers manufacturers with real-time insights for better decision-making.
- Sustainable cost management fosters employee engagement as workers are often more motivated to contribute to environmentally conscious initiatives.
Related Articles
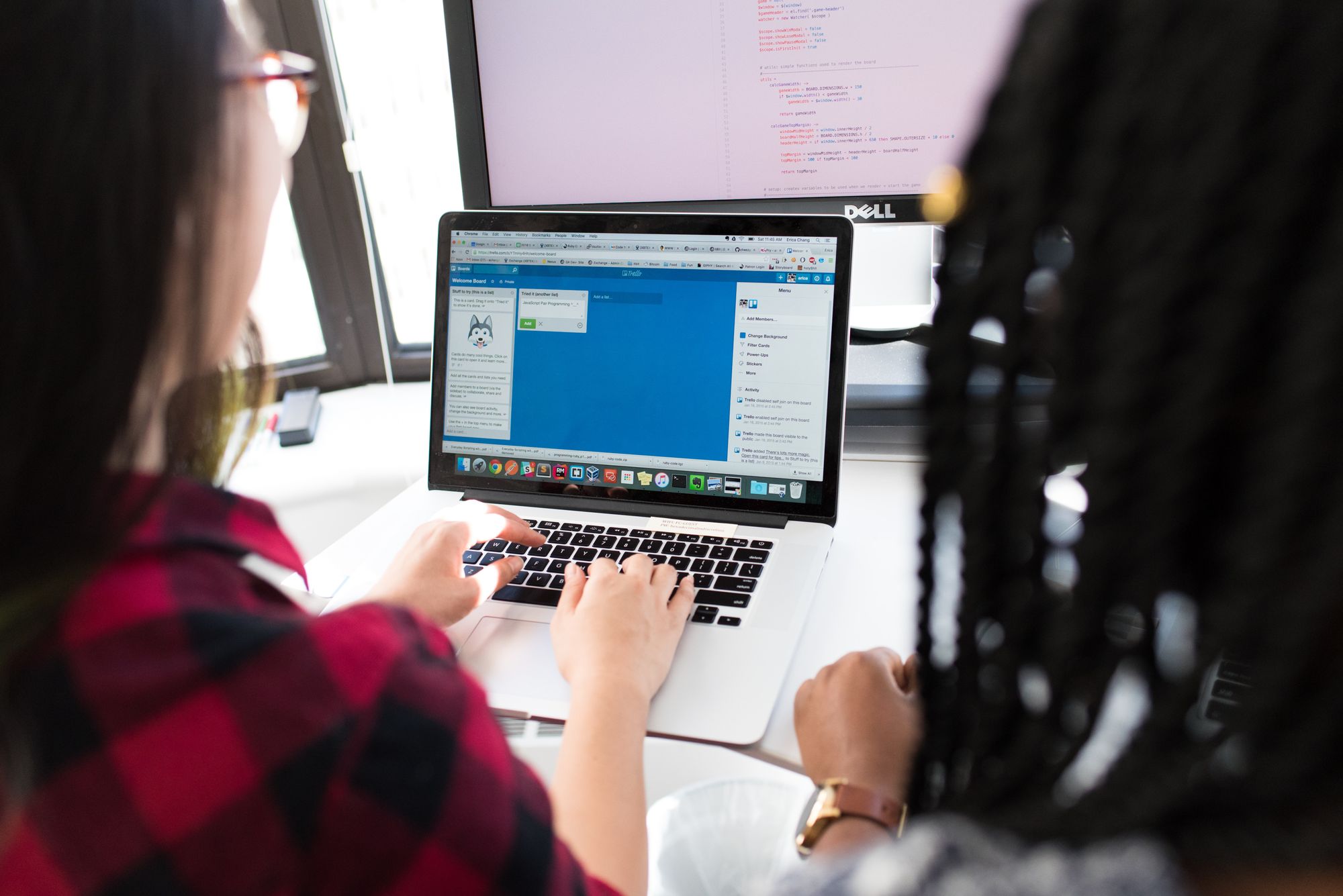
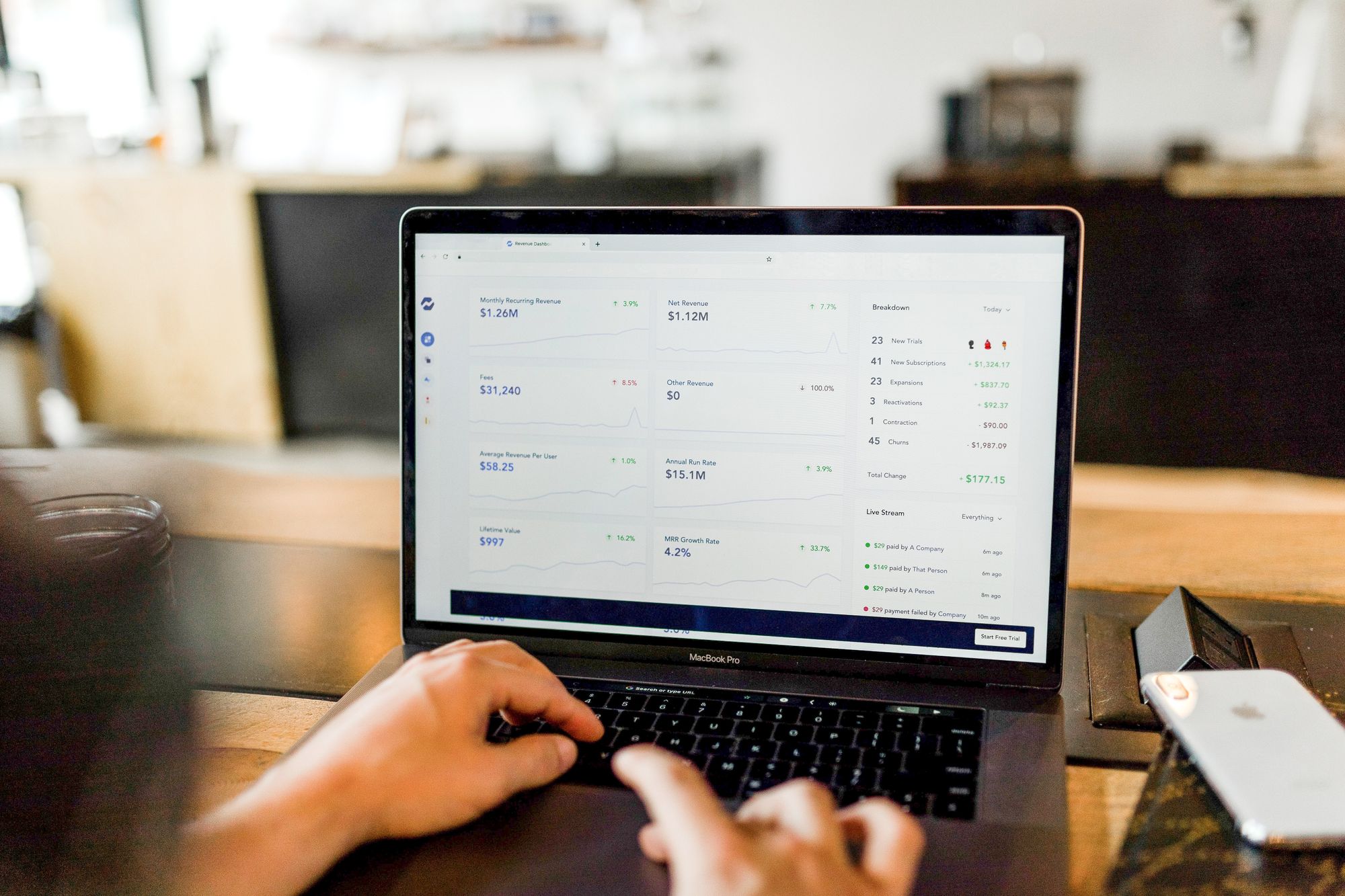
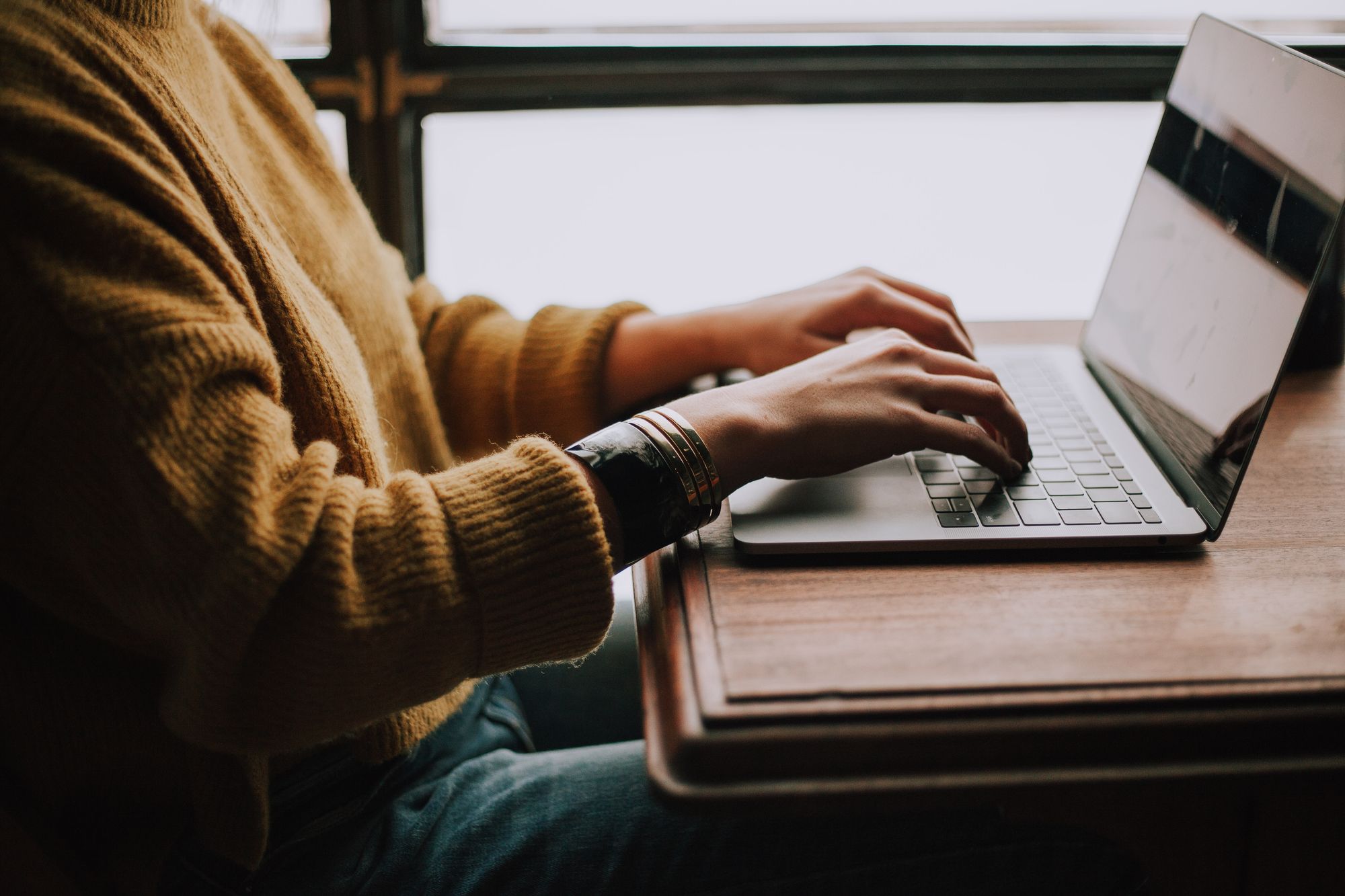
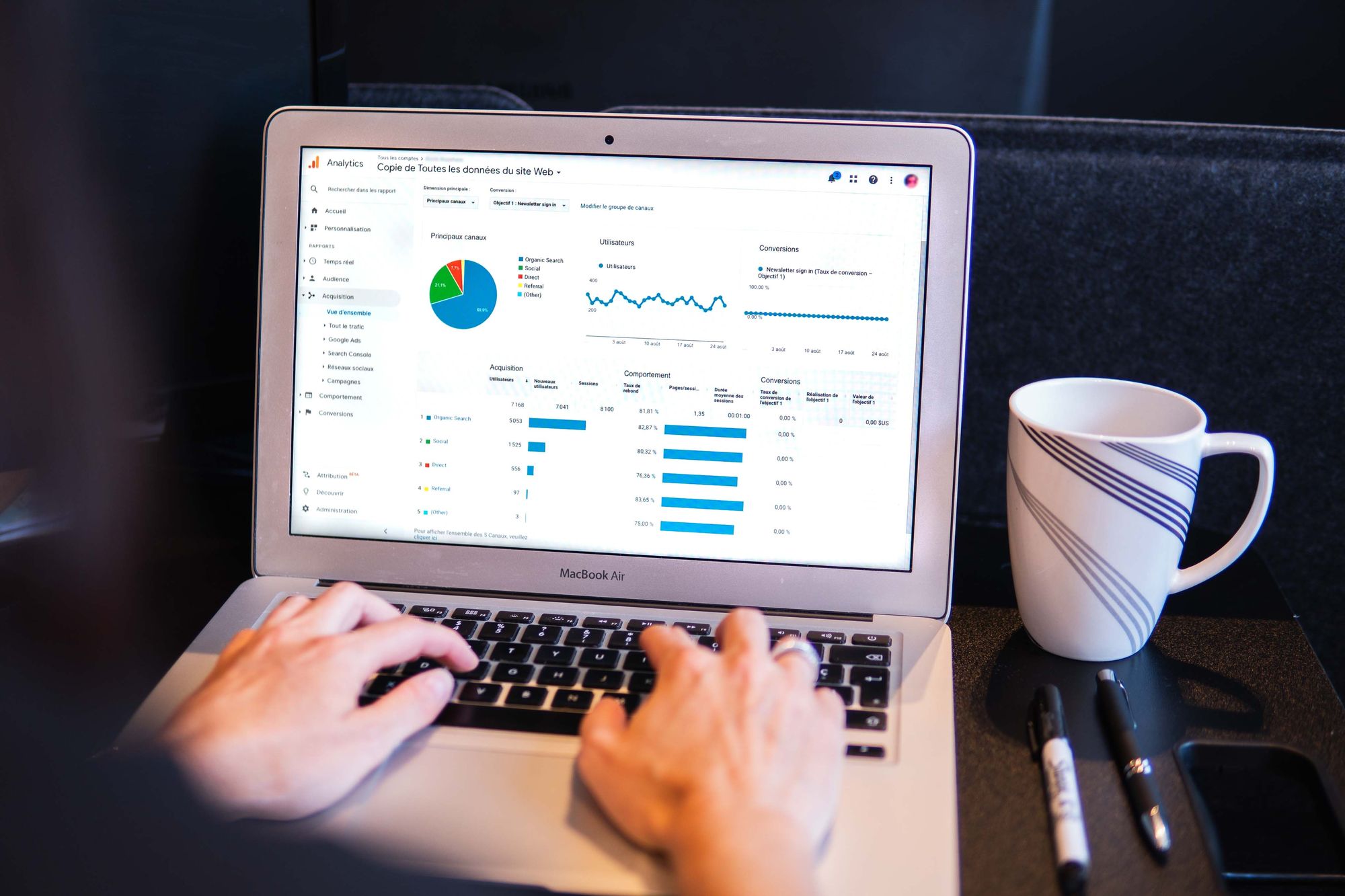