Are you a part of the industrial machinery equipment industry? Are you looking for ways to ensure the success of your supply chain? If your answer to these questions is yes, then you are on the right page.
In the dynamic realm of industrial machinery equipment manufacturing, the orchestration of a seamless supply chain is not just a necessity; it's the lifeline of success.
As global markets evolve, customer expectations rise, and technological advancements reshape industry standards, companies in this sector must continually adapt and innovate to maintain their competitive edge. Amidst this landscape of change and complexity, industrial machinery equipment ERP emerges as a beacon of efficiency and optimization.
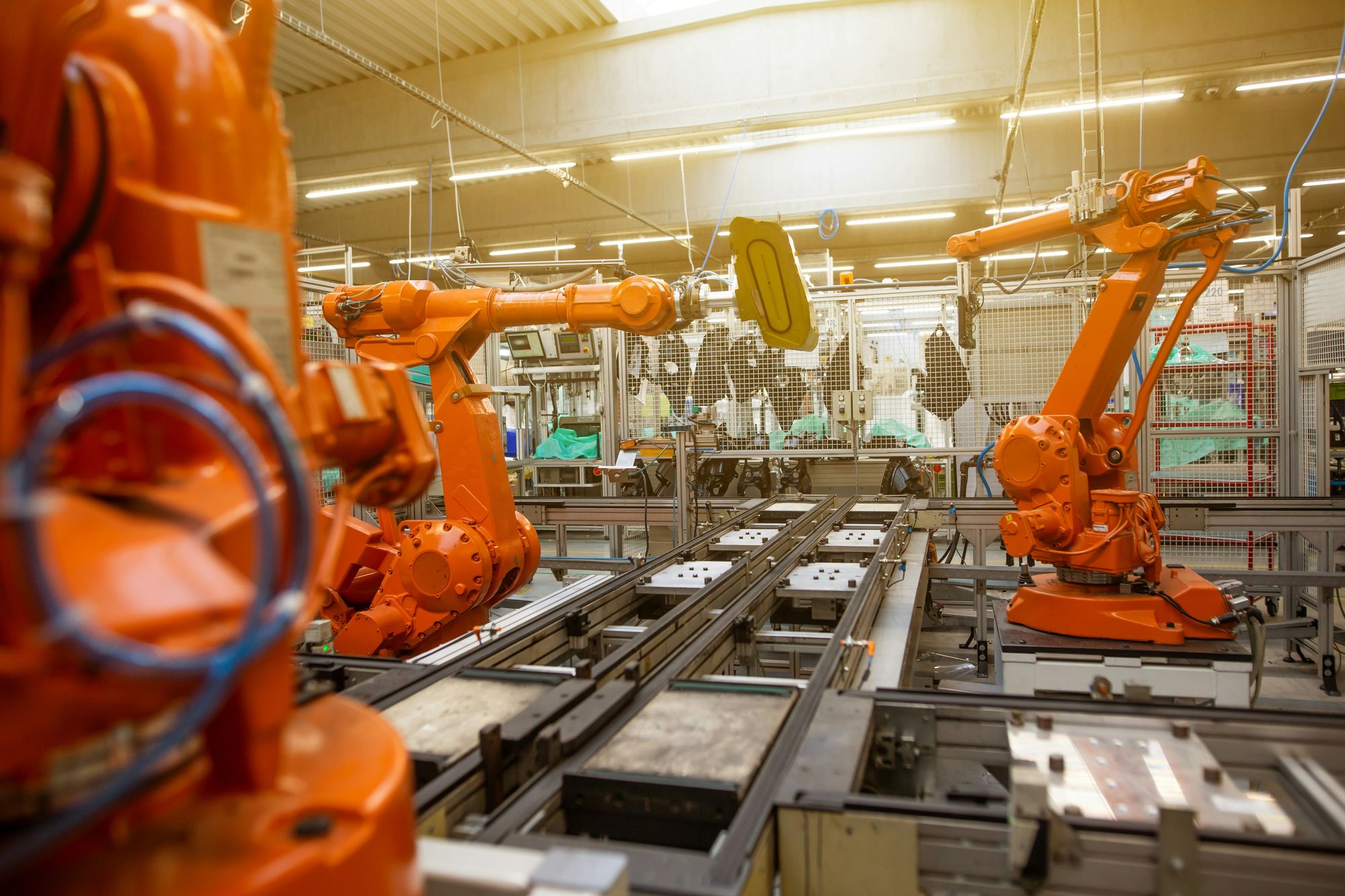
In this article, we will delve into the crucial aspects where manufacturing ERP systems tailored for industrial machinery equipment manufacturing make a significant impact. From procurement optimization to streamlined production planning, from efficient inventory management to enhanced quality control, each step plays a pivotal role in ensuring supply chain excellence.
To help you get a better understanding of how industrial machinery equipment ERP will help you with supply chain success, the topics covered in this article are:
- What is the Industrial Machinery Equipment Industry?
- What is Industrial Machinery Equipment ERP?
- Importance of Supply Chain Success in the Industrial Machinery Equipment Industry
- 12 Steps to Supply Chain Success with Industrial Machinery Equipment ERP
- How can Deskera as an Industrial Machinery Equipment ERP Help in Achieving Supply Chain Success?
- Key Takeaways
- Related Articles
What is the Industrial Machinery Equipment Industry?
The industrial machinery equipment industry encompasses a broad range of businesses involved in the design, manufacture, distribution, and maintenance of machinery and equipment used in various industrial applications.
This sector plays a fundamental role in supporting other industries by providing the tools, machinery, and equipment necessary for manufacturing, construction, agriculture, transportation, and infrastructure development.
The industrial machinery equipment industry includes a diverse array of products, ranging from heavy machinery and equipment used in manufacturing and construction to specialized machinery for agricultural, mining, and energy production purposes.
Some common examples of machinery and equipment within this industry include:
- Machine Tools: Equipment used for shaping, cutting, drilling, and forming materials, including lathes, milling machines, drills, and CNC machining centers.
- Material Handling Equipment: Machinery used for the movement, storage, and transportation of materials and products within manufacturing facilities, warehouses, and distribution centers. Examples include forklifts, conveyors, cranes, and palletizers.
- Construction Machinery: Equipment used in construction projects for excavation, earthmoving, paving, and building. This category includes bulldozers, excavators, cranes, loaders, and concrete mixers.
- Heavy Equipment: Large machinery used in various industries for tasks such as lifting, digging, hauling, and material handling. Examples include dump trucks, loaders, bulldozers, and excavators.
- Industrial Automation and Robotics: Automated systems and robotic equipment used for manufacturing processes, assembly, and material handling tasks. This includes robotic arms, automated guided vehicles (AGVs), and industrial robots.
- Manufacturing Machinery: Equipment used in manufacturing processes for producing goods, such as injection molding machines, packaging machinery, metalworking equipment, and textile machinery.
- Agricultural Machinery: Machinery used in agriculture for planting, harvesting, irrigation, and processing crops. This includes tractors, combines, harvesters, seeders, and irrigation systems.
- Mining Equipment: Machinery used in mining operations for extraction, transportation, and processing of minerals and ores. Examples include drills, crushers, loaders, and mineral processing equipment.
- Energy Equipment: Machinery used in energy production and distribution, including power generation equipment, turbines, pumps, compressors, and renewable energy systems.
- Commercial and Industrial Vehicles: Vehicles and equipment used for transportation and logistics, such as trucks, trailers, buses, and industrial vehicles.
Overall, the industrial machinery equipment industry plays a vital role in driving economic growth, supporting infrastructure development, and enabling manufacturing and production processes across various sectors.
This industry continuously evolves with advancements in technology, automation, and sustainability practices to meet the changing needs of global markets.
What is Industrial Machinery Equipment ERP?
Industrial Machinery Equipment ERP refers to an Enterprise Resource Planning (ERP) system specifically designed to meet the unique needs and challenges of the industrial machinery equipment industry.
This specialized ERP software provides comprehensive solutions for managing and optimizing various aspects of operations within industrial machinery and equipment manufacturing companies.
Industrial machinery equipment ERP solutions offer a wide range of functionalities tailored to the specific requirements of this industry, including:
- Production Management: Industrial machinery equipment ERP systems facilitate efficient production planning, scheduling, and execution. They provide tools for managing work orders, routings, bill of materials (BOM), and capacity planning to optimize production processes and ensure on-time delivery of products.
- Inventory Management: These MRP software systems include advanced inventory management features to track and control inventory levels of raw materials, components, and finished goods. They support inventory optimization techniques such as just-in-time (JIT) inventory, lot tracking, and serial number tracking to minimize carrying costs and optimize stock levels.
- Supply Chain Management: Industrial machinery equipment ERP solutions streamline supply chain processes by integrating procurement, supplier management, and logistics. They facilitate collaboration with suppliers, optimize procurement workflows, and ensure timely delivery of materials to support production schedules.
- Engineering Change Management: Manufacturing ERP systems for industrial machinery equipment includes engineering change management functionalities to manage product configurations, revisions, and engineering changes effectively. They enable manufacturers to track and control changes to product designs, specifications, and documentation throughout the product lifecycle.
- Service Management: These industrial machinery ERP systems support after-sales service operations, including field service management, warranty management, and service contract management. They enable manufacturers to schedule service appointments, dispatch technicians, and manage spare parts inventory to ensure timely resolution of customer issues and maximize equipment uptime.
- Quality Management: Industrial machinery equipment ERP solutions include quality management features to ensure product quality and compliance with industry standards. They support quality control processes, inspections, non-conformance management, and corrective and preventive actions (CAPA) to maintain high-quality standards and minimize defects.
- Financial Management: Manufacturing software systems for industrial machinery equipment provide robust financial management functionalities, including accounting, budgeting, and financial reporting. They enable manufacturers to track costs, revenues, and profitability across projects, departments, and business units.
- Customer Relationship Management (CRM): These manufacturing ERP solutions integrate CRM functionalities to manage customer relationships, sales orders, and inquiries. They enable manufacturers to track customer interactions, manage sales pipelines, and provide personalized service to customers.
- Business Intelligence and Analytics: Industrial machinery equipment ERP systems include business intelligence (BI) and analytics tools to analyze data and generate insights for decision-making. They provide dashboards, reports, and key performance indicators (KPIs) to monitor performance, identify trends, and drive continuous improvement.
- Integration and Scalability: These MRP software systems offer seamless integration with other enterprise systems, such as PLM (Product Lifecycle Management), MES (Manufacturing Execution Systems), and SCM (Supply Chain Management) solutions. They are scalable to accommodate the growing needs of manufacturing companies as they expand and evolve.
Overall, industrial machinery equipment ERP solutions play a critical role in optimizing operations, enhancing productivity, and driving growth within the industrial machinery and equipment manufacturing sector.
They enable manufacturers to streamline processes, improve efficiency, and maintain a competitive edge in today's dynamic and demanding business environment.
Importance of Supply Chain Success in the Industrial Machinery Equipment Industry
The importance of supply chain success in the industrial machinery equipment industry cannot be overstated, as it directly impacts various aspects of business operations, competitiveness, and customer satisfaction.
Here are some key reasons why supply chain success is crucial in this sector:
- Efficient Operations: A well-functioning supply chain ensures the efficient flow of materials, components, and finished products throughout the manufacturing process. It helps streamline production processes, minimize waste, and optimize resource utilization, leading to improved operational efficiency.
- Cost Control: Supply chain success enables manufacturers to control costs effectively by optimizing procurement, inventory management, and production processes. By minimizing overhead costs, reducing lead times, and optimizing transportation, manufacturers can maintain competitive pricing and improve profitability.
- Quality Assurance: A robust supply chain ensures the availability of high-quality materials and components for manufacturing industrial machinery equipment. By implementing stringent quality control measures and collaborating with reliable suppliers, manufacturers can maintain product quality standards and meet customer expectations for performance and reliability.
- On-Time Delivery: Timely delivery of machinery equipment is essential to meet customer demand and maintain customer satisfaction. A well-managed supply chain ensures on-time delivery of products by minimizing lead times, optimizing production schedules, and coordinating logistics effectively.
- Customer Satisfaction: Supply chain success directly impacts customer satisfaction by ensuring product availability, timely delivery, and consistent quality. Satisfied customers are more likely to repeat purchases, provide positive customer feedback, and recommend the manufacturer to others, driving business growth and profitability.
- Competitive Advantage: An efficient and agile supply chain can provide a significant competitive advantage in the industrial machinery equipment industry. Manufacturers that can deliver high-quality products quickly and cost-effectively are better positioned to compete in the market and win new business opportunities.
- Innovation and Flexibility: A responsive supply chain enables manufacturers to adapt quickly to changing market conditions, customer preferences, and industry trends. It facilitates innovation by enabling manufacturers to introduce new products, technologies, and features to meet evolving customer needs and stay ahead of competitors.
- Risk Management: A resilient supply chain helps mitigate risks associated with disruptions such as raw material shortages, production delays, or supply chain disruptions. By diversifying suppliers, implementing contingency plans, and maintaining adequate inventory buffers, manufacturers can minimize the impact of unforeseen events on operations and ensure business continuity.
- Regulatory Compliance: Compliance with regulatory requirements and industry standards is essential in the industrial machinery equipment sector. A well-managed supply chain ensures compliance by sourcing materials from reputable suppliers, adhering to quality and safety standards, and maintaining proper documentation and traceability.
- Sustainability: Supply chain success is increasingly linked to sustainability goals such as reducing carbon emissions, minimizing waste, and promoting ethical sourcing practices. Manufacturers that prioritize sustainability in their supply chain operations can enhance their brand reputation, attract environmentally conscious customers, and contribute to a more sustainable future.
In summary, supply chain success is critical for manufacturers in the industrial machinery equipment industry to achieve operational excellence, control costs, maintain quality standards, satisfy customer expectations, gain a competitive edge, manage risks, ensure regulatory compliance, promote innovation, and drive sustainability.
By investing in supply chain optimization and collaboration, manufacturers can position themselves for long-term success in a dynamic and competitive market environment.
12 Steps to Supply Chain Success with Industrial Machinery Equipment ERP
Implementing an industrial machinery equipment ERP system offers numerous benefits for optimizing supply chain management in the industry.
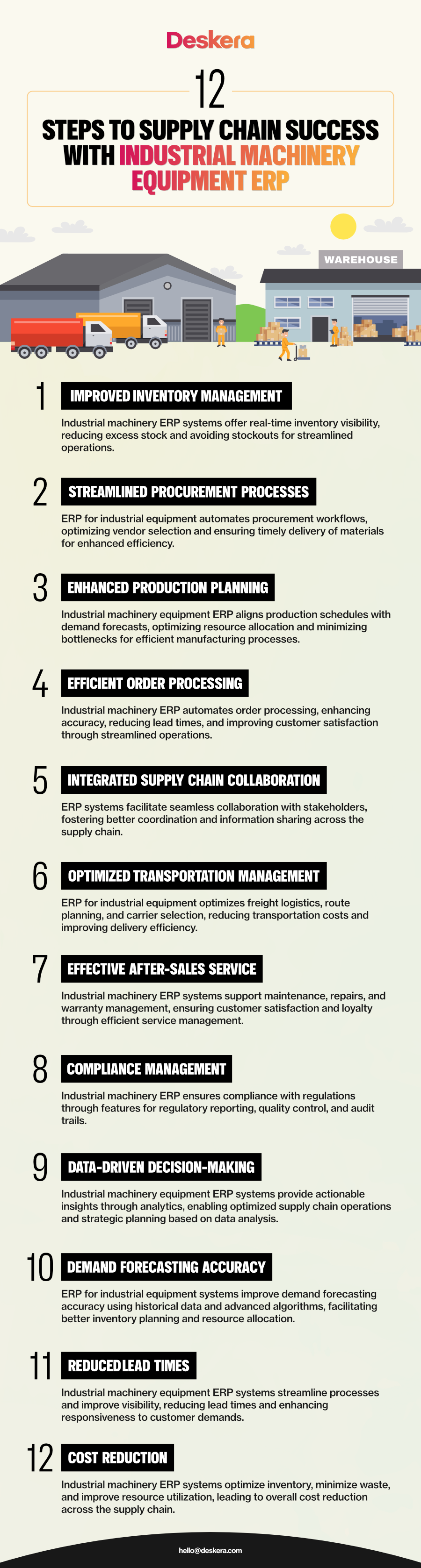
Here are 12 ways it helps:
Improved Inventory Management
Improved inventory management is a critical aspect of supply chain success in the industrial machinery equipment sector, and leveraging industrial machinery equipment ERP solutions can significantly enhance this aspect.
Manufacturing software for industrial equipment incorporates robust features and functionalities tailored specifically to the needs of this industry.
Here's how an industrial machinery equipment ERP system optimizes inventory management:
- Real-Time Visibility: Industrial machinery equipment ERP systems provide real-time visibility into inventory levels across multiple locations, warehouses, and production facilities. This visibility allows manufacturers to accurately track the movement of raw materials, work-in-progress (WIP), and finished goods.
- Inventory Optimization: With the help of manufacturing software, organizations can implement advanced inventory optimization techniques. These include setting optimal reorder points, safety stock levels, and economic order quantities (EOQ) based on demand forecasts, lead times, and production schedules.
- Demand Forecasting Integration: Manufacturing ERP systems integrate with demand forecasting modules to predict future inventory requirements accurately. By analyzing historical data, market trends, and customer demand patterns, manufacturers can align inventory levels with anticipated demand, minimizing excess inventory and stockouts.
- Automated Replenishment: MRP software for industrial equipment automates the replenishment process by triggering purchase orders or production orders when inventory levels fall below predefined thresholds. This automation ensures the timely replenishment of critical components and materials, preventing production disruptions and delays.
- Serial and Lot Tracking: Many industrial machinery equipment ERP solutions offer robust serial and lot tracking capabilities. Manufacturers can trace the movement of individual components or batches throughout the supply chain, enabling accurate recall management, quality control, and compliance with regulatory requirements.
- Integrated Supply Chain: Industrial machinery equipment ERP systems facilitate seamless integration with suppliers, distributors, and logistics partners. This integration enables real-time collaboration, electronic data interchange (EDI), and automated order processing, streamlining the flow of materials and reducing lead times.
- Warehouse Management: Manufacturing ERP includes warehouse management functionalities to optimize inventory storage, picking, and packing processes. By implementing efficient warehouse layouts, inventory tracking systems, and barcode scanning technologies, manufacturers can improve inventory accuracy and operational efficiency.
- MRP Software Integration: Industrial machinery ERP systems often include Material Requirements Planning (MRP) software modules. MRP software helps manufacturers plan and schedule production activities based on inventory levels, production capacity, and demand forecasts, ensuring optimal resource utilization and minimizing excess inventory.
- Quality Control: Quality control features integrated into manufacturing software systems enable manufacturers to monitor the quality of incoming materials, in-process inventory, and finished goods. By identifying and addressing quality issues early in the production process, manufacturers can minimize inventory rework, scrap, and returns.
- Inventory Valuation: Industrial machinery equipment ERP systems provide accurate inventory valuation methods, such as first-in-first-out (FIFO) or weighted average cost. Accurate inventory valuation ensures compliance with accounting standards, enables precise financial reporting, and supports strategic decision-making.
In summary, industrial machinery equipment ERP systems play a crucial role in optimizing inventory management processes within the manufacturing supply chain.
By providing real-time visibility, demand forecasting integration, automated replenishment, and robust inventory tracking capabilities, these solutions help manufacturers minimize costs, improve efficiency, and enhance customer satisfaction.
Streamlined Procurement Processes
Streamlined procurement processes are vital for supply chain success in the industrial machinery equipment sector, and industrial machinery equipment ERP solutions play a crucial role in achieving this optimization.
With features specifically tailored for this industry, such as those found in ERP for industrial equipment, manufacturers can significantly enhance their procurement operations.
Here's how industrial machinery equipment ERP facilitates streamlined procurement processes:
- Centralized Procurement Management: Industrial machinery equipment ERP systems centralize procurement activities, allowing manufacturers to manage sourcing, purchasing, and vendor management from a single platform. This centralized approach improves visibility and control over procurement processes.
- Automated Purchase Order Generation: Manufacturing ERP automates the generation of purchase orders based on predefined triggers such as inventory levels, reorder points, or production requirements. This automation eliminates manual intervention, reduces processing time, and ensures timely procurement of materials and components.
- Vendor Management: Industrial machinery ERP systems include vendor management functionalities to streamline interactions with suppliers. Manufacturers can maintain comprehensive vendor databases, track vendor performance metrics, and evaluate supplier quality and reliability.
- RFQ Management: ERP for industrial equipment enables efficient management of requests for quotation (RFQs) by standardizing the RFQ creation process, automating supplier communication, and facilitating bid comparison and analysis. This streamlines the supplier selection process and ensures competitive pricing.
- Contract Management: Manufacturing ERP systems incorporate contract management capabilities to streamline contract negotiation, execution, and compliance. Manufacturers can maintain contract repositories, track contract terms and conditions, and automate contract renewal processes.
- Integrated Supplier Collaboration: MRP software facilitates seamless collaboration with suppliers through integrated communication channels. Manufacturers can exchange documents, specifications, and purchase orders electronically, reducing manual errors and communication delays.
- Budgeting and Cost Control: Manufacturing software includes budgeting and cost control features to monitor procurement expenditures and ensure adherence to budgetary constraints. Manufacturers can set spending limits, track purchase commitments, and analyze procurement costs in real-time.
- Compliance Management: Manufacturing ERP systems help ensure compliance with regulatory requirements and internal policies governing procurement activities. By incorporating compliance checks, audit trails, and approval workflows, manufacturers can mitigate risks and maintain regulatory compliance.
- Supplier Performance Evaluation: Industrial machinery equipment ERP enables manufacturers to evaluate supplier performance based on predefined key performance indicators (KPIs) such as delivery reliability, product quality, and responsiveness. This data-driven approach facilitates supplier performance improvement and informed decision-making.
- Inventory Reconciliation: Industrial machinery ERP facilitates seamless reconciliation of inventory receipts with purchase orders, invoices, and packing slips. Manufacturers can reconcile inventory discrepancies promptly, reducing inventory inaccuracies and ensuring data integrity.
In summary, industrial machinery equipment ERP systems streamline procurement processes by centralizing procurement management, automating purchase order generation, enhancing vendor management, and facilitating collaboration with suppliers.
By optimizing these processes, manufacturers can reduce procurement cycle times, control costs, and enhance supply chain efficiency.
Enhanced Production Planning
Enhanced production planning is a key factor in achieving supply chain success within the industrial machinery equipment sector, and leveraging industrial machinery equipment ERP solutions is instrumental in achieving this optimization.
Industrial machinery equipment ERP offers tailored features to support efficient production planning processes.
Here's how Industrial Machinery Equipment ERP facilitates enhanced production planning:
- Demand Forecasting Integration: Industrial machinery equipment ERP systems integrate advanced demand forecasting functionalities. By analyzing historical data, market trends, and customer demand patterns, manufacturers can accurately predict future demand for their machinery equipment products.
- MRP Software Integration: Manufacturing ERP includes material requirements planning (MRP) software modules to support production planning activities. MRP software calculates material requirements based on production schedules, inventory levels, and demand forecasts, enabling manufacturers to plan production activities effectively.
- Resource Optimization: Industrial machinery equipment ERP systems optimize the allocation of resources, including labor, equipment, and materials, to support production planning objectives. By balancing resource capacities with production demands, manufacturers can maximize efficiency and minimize production bottlenecks.
- Real-Time Production Scheduling: ERP for industrial equipment provides real-time production scheduling capabilities, allowing manufacturers to create detailed production schedules based on demand forecasts, resource availability, and production constraints. This enables efficient utilization of production capacity and minimizes idle time.
- Capacity Planning: Manufacturing ERP systems incorporate capacity planning functionalities to assess production capacity against demand forecasts and identify potential capacity constraints. Manufacturers can adjust production schedules and resource allocations to optimize capacity utilization and meet customer demand effectively.
- Work Order Management: Manufacturing software facilitates streamlined work order management processes. Manufacturers can create, prioritize, and track work orders for production activities, ensuring timely execution and adherence to production schedules.
- Production Cost Estimation: MRP software includes production cost estimation features to assess the cost of manufacturing machinery equipment products. Manufacturers can analyze production costs, including labor, materials, overhead, and setup costs, to determine product profitability and set competitive pricing strategies.
- Quality Management Integration: Industrial machinery ERP systems integrate quality management functionalities to ensure product quality throughout the production process. Manufacturers can implement quality control measures, track non-conformances, and enforce quality standards to minimize rework and scrap.
- Supply Chain Collaboration: Manufacturing ERP facilitates collaboration with suppliers, subcontractors, and partners involved in the production process. Manufacturers can exchange production-related information, such as material availability and lead times, to optimize production planning and scheduling.
- Continuous Improvement: ERP for industrial equipment supports continuous improvement initiatives by providing insights into production performance and efficiency. Manufacturers can analyze production data, identify areas for improvement, and implement corrective actions to enhance production planning processes over time.
In summary, industrial machinery equipment ERP systems play a crucial role in enhancing production planning processes by integrating demand forecasting, MRP software, resource optimization, real-time scheduling, capacity planning, and quality management functionalities.
By leveraging these capabilities, manufacturers can improve production efficiency, reduce lead times, and meet customer demand effectively within the industrial machinery equipment sector.
Efficient Order Processing
Efficient order processing is essential for achieving supply chain success in the industrial machinery equipment sector, and industrial machinery equipment ERP solutions play a crucial role in streamlining this aspect of operations. Industrial machinery equipment ERP offers specialized features to optimize order processing workflows.
Here's how industrial machinery equipment ERP facilitates efficient order processing:
- Automated Order Entry: Industrial machinery ERP systems automate the order entry process, allowing sales representatives to input customer orders directly into the ERP system. This automation reduces manual errors and speeds up order processing times.
- Order Validation: ERP for Industrial Equipment includes order validation functionalities to ensure the accuracy and completeness of incoming orders. The system performs checks against predefined criteria, such as product availability, pricing, and credit limits, to validate orders before processing.
- Real-Time Inventory Availability: Manufacturing ERP provides real-time visibility into inventory levels, enabling sales representatives to check product availability instantly during order entry. This ensures that customers receive accurate information about product availability and delivery lead times.
- Order Tracking: MRP software systems enable order tracking throughout the order fulfillment process. Sales representatives, customers, and other stakeholders can track the status of orders in real-time, from order entry to shipment and delivery, improving transparency and customer satisfaction.
- Automated Order Routing: ERP for industrial equipment automates the routing of orders to the appropriate departments or production facilities for processing. This automation ensures that orders are routed efficiently, based on factors such as product type, production capacity, and geographic location.
- Integrated Sales and Production Planning: Manufacturing ERP integrates sales order processing with production planning activities to ensure alignment between customer demand and production schedules. Orders are scheduled based on production capacity, lead times, and resource availability, minimizing delays and maximizing efficiency.
- Order Fulfillment Optimization: Manufacturing software systems optimize order fulfillment processes by prioritizing orders based on predefined criteria, such as customer priority, order value, and delivery deadlines. This ensures that high-priority orders are processed and shipped promptly, enhancing customer satisfaction.
- Automated Invoicing and Billing: ERP for industrial equipment automates the generation of invoices and billing statements upon order completion. This automation reduces manual effort, minimizes errors, and accelerates the invoicing process, improving cash flow and financial visibility.
- Customer Relationship Management Integration: Manufacturing ERP integrates with customer relationship management (CRM) systems to provide a comprehensive view of customer interactions and order history. Sales representatives can access customer data, preferences, and order history directly from the ERP system, facilitating personalized customer service.
- Order Modification and Cancellation: Industrial machinery equipment ERP systems allow sales representatives to modify or cancel orders as needed, even after they have been processed. This flexibility ensures responsiveness to customer requests and changes, enhancing customer satisfaction and customer loyalty.
In summary, industrial machinery equipment ERP systems streamline order processing by automating order entry, validation, routing, tracking, and fulfillment.
By integrating sales and production planning activities, optimizing order prioritization, and providing seamless integration with CRM systems, manufacturing ERP helps manufacturers enhance efficiency, accuracy, and customer satisfaction in order processing workflows.
Integrated Supply Chain Collaboration
Integrated supply chain collaboration is crucial for achieving success in the industrial machinery equipment sector, and leveraging industrial machinery equipment ERP solutions is essential for facilitating seamless collaboration across the supply chain. ERP for industrial equipment offers specialized features to enhance collaboration among suppliers, customers, and other stakeholders.
Here's how industrial machinery equipment ERP facilitates integrated supply chain collaboration:
- Supplier Integration: Manufacturing software systems integrate seamlessly with supplier systems, enabling electronic data interchange (EDI) and automated communication channels. Suppliers can receive purchase orders, submit invoices, and provide shipment notifications directly through the ERP system, reducing manual effort and errors.
- Vendor Portal: Manufacturing ERP includes vendor portals that allow suppliers to access relevant information, such as purchase orders, delivery schedules, and quality requirements. This self-service portal enables suppliers to collaborate effectively with manufacturers, track order status, and respond to inquiries in real time.
- Collaborative Forecasting: MRP software facilitates collaborative demand forecasting between manufacturers and suppliers. Manufacturers can share demand forecasts, production schedules, and inventory requirements with suppliers, enabling suppliers to plan production and raw material procurement accordingly.
- Integrated Procurement: Industrial machinery equipment ERP systems streamline procurement processes by integrating procurement activities with supplier collaboration. Manufacturers can send RFQs, negotiate contracts, and place purchase orders directly within the ERP system, ensuring seamless communication and transaction processing.
- Electronic Data Interchange (EDI): ERP for industrial equipment supports EDI standards for electronic data exchange with suppliers and customers. EDI enables the automated exchange of documents such as purchase orders, invoices, and shipping notices, reducing paper-based processes and improving data accuracy.
- Customer Collaboration: Industrial machinery equipment ERP systems facilitate collaboration with customers through integrated communication channels. Manufacturers can receive orders, provide order status updates, and address customer inquiries directly within the ERP system, enhancing customer satisfaction and loyalty.
- Supply Chain Visibility: Manufacturing software provides real-time visibility into supply chain activities, allowing manufacturers to track the movement of materials, components, and finished goods across the supply chain. This visibility enables proactive decision-making, risk management, and performance monitoring.
- Quality Collaboration: ERP for industrial equipment supports collaborative quality management processes between manufacturers and suppliers. Manufacturers can share quality requirements, inspection criteria, and non-conformance reports with suppliers, facilitating continuous improvement and compliance with quality standards.
- Logistics Collaboration: Industrial machinery ERP systems facilitate collaboration with logistics partners, such as carriers and freight forwarders. Manufacturers can coordinate shipment schedules, track deliveries, and manage transportation costs directly within the manufacturing ERP system, ensuring on-time delivery and cost efficiency.
- Collaborative Product Development: Manufacturing ERP supports collaborative product development processes by enabling cross-functional collaboration among design, engineering, and manufacturing teams. Manufacturers can share product specifications, design revisions, and prototype feedback within the MRP software system, accelerating time-to-market and improving product quality.
In summary, industrial machinery equipment ERP systems play a critical role in facilitating integrated supply chain collaboration by integrating supplier and customer interactions, enabling collaborative forecasting, supporting EDI standards, and providing visibility into supply chain activities.
By leveraging these capabilities, manufacturers can enhance collaboration, improve responsiveness, and achieve supply chain success within the industrial machinery equipment sector.
Optimized Transportation Management
Optimized transportation management is essential for achieving supply chain success in the industrial machinery equipment sector, and industrial machinery equipment ERP solutions play a crucial role in streamlining transportation operations. ERP for industrial equipment offers specialized features to optimize transportation management processes.
Here's how industrial machinery equipment ERP facilitates optimized transportation management:
- Carrier Selection: Industrial machinery equipment ERP systems facilitate the selection of carriers based on predefined criteria such as cost, transit time, and service quality. Manufacturers can compare carrier rates, track records, and availability directly within the ERP system, enabling informed decision-making.
- Route Optimization: Manufacturing software includes route optimization functionalities to optimize delivery routes and minimize transportation costs. Manufacturers can consider factors such as distance, traffic conditions, and delivery windows to plan efficient delivery routes, reducing fuel consumption and transit times.
- Freight Consolidation: MRP software systems support freight consolidation strategies to optimize transportation costs. Manufacturers can consolidate multiple shipments into larger, more cost-effective loads, leveraging economies of scale and reducing overall transportation expenses.
- Load Planning: Manufacturing ERP facilitates load planning by optimizing the allocation of products and orders to vehicles. Manufacturers can maximize load capacity, minimize empty space, and ensure efficient utilization of transportation assets, reducing transportation costs per unit.
- Transportation Management System (TMS) Integration: ERP for industrial equipment integrates with Transportation Management Systems (TMS) to streamline transportation planning and execution. Manufacturers can access TMS functionalities such as load tendering, carrier communication, and shipment tracking directly within the ERP system, ensuring seamless coordination and visibility across transportation operations.
- Freight Rate Management: Industrial machinery equipment ERP systems include freight rate management features to manage carrier contracts, rates, and tariffs. Manufacturers can negotiate favorable freight rates, track rate changes, and analyze transportation costs to optimize carrier selection and routing decisions.
- Delivery Scheduling: MRP software enables efficient delivery scheduling by considering customer preferences, delivery windows, and route optimization constraints. Manufacturers can schedule deliveries based on customer availability and preferences, ensuring on-time delivery and customer satisfaction.
- Cross-Docking: Industrial machinery equipment ERP systems support cross-docking operations to minimize inventory holding costs and streamline order fulfillment processes. Manufacturers can transfer products directly from inbound to outbound vehicles, reducing handling and storage costs and accelerating order cycle times.
- Visibility and Tracking: Manufacturing ERP provides real-time visibility into transportation activities, allowing manufacturers to track shipments, monitor delivery status, and proactively address any issues or delays. This visibility enables better communication with customers and suppliers, enhancing overall supply chain efficiency.
- Performance Analytics: MRP software systems offer transportation performance analytics to evaluate carrier performance, monitor key performance indicators (KPIs), and identify opportunities for improvement. Manufacturers can analyze transportation costs, transit times, and service levels to optimize transportation management strategies over time.
In summary, industrial machinery equipment ERP systems play a critical role in optimizing transportation management processes by facilitating carrier selection, route optimization, freight consolidation, load planning, and integration with Transportation Management Systems (TMS).
By leveraging these capabilities, manufacturers can reduce transportation costs, improve delivery reliability, and enhance overall supply chain efficiency within the industrial machinery equipment sector.
Effective After-Sales Service
Effective after-sales service is a critical component of achieving supply chain success in the industrial machinery equipment sector, and industrial machinery equipment ERP solutions play a crucial role in facilitating this aspect of operations. ERP for industrial equipment offers specialized features to support efficient after-sales service processes.
Here's how industrial machinery equipment ERP facilitates effective after-sales service:
- Service Management Module: Industrial machinery ERP systems include dedicated service management modules to support after-sales service activities. These modules enable manufacturers to manage service requests, track service orders, and schedule service technicians efficiently.
- Service Contract Management: Manufacturing software includes service contract management functionalities to manage service agreements, warranties, and maintenance contracts. Manufacturers can track contract terms, renewal dates, and service entitlements, ensuring compliance with service commitments.
- Field Service Management: MRP software systems facilitate field service management by optimizing the deployment of service technicians and resources. Manufacturers can schedule service appointments, assign tasks, and manage service routes effectively, maximizing technician productivity and customer satisfaction.
- Spare Parts Inventory Management: Manufacturing ERP includes spare parts inventory management features to ensure the availability of spare parts for after-sales service activities. Manufacturers can track spare parts inventory levels, reorder points, and lead times, minimizing downtime and ensuring timely repairs.
- Service Request Tracking: ERP for industrial equipment enables manufacturers to track service requests from initiation to resolution. Manufacturers can capture customer service requests, assign service technicians, and monitor service progress in real time, ensuring prompt resolution and customer satisfaction.
- Remote Diagnostics and Monitoring: Industrial machinery equipment ERP systems support remote diagnostics and monitoring capabilities for proactive maintenance and troubleshooting. Manufacturers can remotely monitor equipment performance, diagnose issues, and schedule preventive maintenance activities, minimizing equipment downtime and service costs.
- Service Performance Analytics: Manufacturing ERP provides service performance analytics to evaluate the effectiveness of after-sales service operations. Manufacturers can analyze key performance indicators (KPIs) such as response times, resolution rates, and customer satisfaction scores to identify areas for improvement and drive continuous service excellence.
- Customer Portal: Manufacturing software systems include customer portals that allow customers to submit service requests, track service status, and access self-service resources. This self-service portal enhances customer engagement and satisfaction by providing transparency and convenience in after-sales service interactions.
- Integration with CRM Systems: MRP software integrates with CRM systems to provide a comprehensive view of customer interactions and service history. Manufacturers can access customer data, preferences, and service history directly within the ERP system, enabling personalized service and support.
- Knowledge Base Management: Industrial machinery equipment ERP systems include knowledge base management functionalities to capture and share service knowledge and best practices. Manufacturers can create, organize, and disseminate service manuals, troubleshooting guides, and instructional videos to support service technicians and enhance service quality.
In summary, industrial machinery equipment ERP systems play a critical role in facilitating effective after-sales service by providing service management modules, service contract management, field service management, spare parts inventory management, service request tracking, remote diagnostics, service performance analytics, customer portals, integration with CRM systems, and knowledge base management functionalities.
By leveraging these capabilities, manufacturers can enhance customer satisfaction, maximize equipment uptime, and drive service excellence within the industrial machinery equipment sector.
Compliance Management
Compliance management is a critical aspect of achieving supply chain success in the industrial machinery equipment sector, and industrial machinery equipment ERP solutions play a crucial role in ensuring regulatory compliance and adherence to industry standards. ERP for industrial equipment offers specialized features to support compliance management processes.
Here's how industrial machinery equipment ERP facilitates compliance management:
- Regulatory Compliance Tracking: Industrial machinery equipment ERP systems track regulatory requirements and compliance standards relevant to the industry, such as safety regulations, environmental regulations, and product certifications. Manufacturers can maintain compliance checklists, track regulatory changes, and ensure adherence to applicable regulations.
- Audit Trails: ERP for industrial equipment includes audit trail functionalities to track and record changes made to critical data and transactions within the system. Manufacturers can maintain an audit trail of user activities, system configurations, and data modifications to support regulatory audits and compliance verification.
- Document Management: Manufacturing ERP systems facilitate document management and version control for compliance-related documents, such as compliance certificates, test reports, and regulatory filings. Manufacturers can organize and maintain compliance documents centrally within the ERP system, ensuring accessibility and accuracy.
- Quality Control and Assurance: MRP software incorporates quality control and assurance features to ensure product quality and compliance with regulatory standards. Manufacturers can define quality control processes, conduct inspections, and manage non-conformance events to address quality issues and maintain compliance.
- Risk Management: Manufacturing software systems support risk management processes to identify, assess, and mitigate compliance risks across the supply chain. Manufacturers can analyze potential risks related to regulatory non-compliance, supply chain disruptions, and operational failures, and implement risk mitigation strategies accordingly.
- Compliance Reporting: ERP for industrial equipment includes compliance reporting capabilities to generate regulatory reports and documentation required for regulatory submissions and audits. Manufacturers can automate the generation of compliance reports, ensuring accuracy and timeliness in regulatory reporting.
- Supplier Compliance Monitoring: Industrial machinery equipment ERP systems facilitate supplier compliance monitoring by assessing and managing supplier compliance with regulatory requirements and contractual obligations. Manufacturers can track supplier performance metrics, conduct supplier audits, and enforce compliance standards throughout the supply chain.
- Employee Training and Certification Management: Manufacturing ERP includes features for managing employee training and certification requirements related to compliance. Manufacturers can track employee training records, certifications, and competency levels to ensure that employees are adequately trained and qualified to perform their roles in compliance with regulatory requirements.
- Change Management: Industrial machinery ERP systems support change management processes to manage changes to compliance-related policies, procedures, and regulations. Manufacturers can document, evaluate, and implement changes systematically, ensuring compliance with updated regulations and standards.
- Integration with Regulatory Databases: Manufacturing software integrates with external regulatory databases and repositories to access regulatory information, updates, and resources. Manufacturers can stay informed about changes to regulations and standards relevant to the industry and adjust their compliance management processes accordingly.
In summary, industrial machinery equipment ERP systems play a critical role in facilitating compliance management by tracking regulatory requirements, maintaining audit trails, managing compliance documents, ensuring quality control, managing risks, generating compliance reports, monitoring supplier compliance, managing employee training, facilitating change management, and integrating with regulatory databases.
By leveraging these capabilities, manufacturers can ensure regulatory compliance, mitigate compliance risks, and maintain operational excellence within the industrial machinery equipment sector.
Data-Driven Decision-Making
Data-driven decision-making is crucial for achieving supply chain success in the industrial machinery equipment sector, and industrial machinery equipment ERP solutions play a pivotal role in facilitating this approach. Industrial machinery ERP offers specialized features to enable data-driven decision-making processes.
Here's how industrial machinery equipment ERP facilitates data-driven decision-making:
- Real-Time Data Analytics: Manufacturing ERP systems provide real-time access to operational data from various sources within the supply chain. Manufacturers can analyze data on inventory levels, production performance, sales trends, and supplier performance in real time to make informed decisions promptly.
- Advanced Reporting Tools: Manufacturing software includes advanced reporting tools that enable manufacturers to generate customized reports and dashboards to visualize key performance indicators (KPIs) and metrics relevant to supply chain operations. These reports provide insights into areas such as inventory turnover ratio, production efficiency, and order fulfillment rates.
- Predictive Analytics: MRP software systems leverage predictive analytics algorithms to forecast future trends and outcomes based on historical data and statistical models. Manufacturers can use predictive analytics to anticipate demand fluctuations, identify potential supply chain disruptions, and optimize production planning and inventory management strategies proactively.
- Demand Forecasting: Manufacturing ERP incorporates demand forecasting functionalities to predict future demand for industrial machinery equipment products accurately. Manufacturers can analyze historical sales data, market trends, and customer behavior to forecast demand with a high degree of accuracy, enabling optimal inventory planning and production scheduling.
- Inventory Optimization: Industrial machinery ERP systems use data-driven algorithms to optimize inventory levels and reduce carrying costs while ensuring product availability. By analyzing demand patterns, lead times, and supply chain constraints, manufacturers can implement inventory optimization strategies such as just-in-time (JIT) inventory management and ABC analysis.
- Supplier Performance Analysis: Manufacturing software enables manufacturers to evaluate supplier performance based on data-driven metrics such as on-time delivery, quality performance, and cost-effectiveness. Manufacturers can use supplier performance analysis to identify top-performing suppliers, negotiate better terms, and mitigate risks associated with underperforming suppliers.
- Cost Analysis: MRP software systems enable manufacturers to conduct cost analysis across various aspects of the supply chain, including production, procurement, transportation, and inventory management. By analyzing cost drivers and cost structures, manufacturers can identify cost-saving opportunities, optimize spending, and improve profitability.
- Scenario Planning: Manufacturing ERP supports scenario planning capabilities that allow manufacturers to simulate different scenarios and assess the potential impact on supply chain performance. Manufacturers can evaluate scenarios such as changes in demand, disruptions in supply, or fluctuations in raw material prices to develop contingency plans and mitigate risks.
- Root Cause Analysis: Industrial machinery equipment ERP systems facilitate root cause analysis by providing data-driven insights into the underlying factors contributing to supply chain issues or performance gaps. Manufacturers can identify the root causes of problems such as production delays, quality defects, or inventory shortages and implement corrective actions to address them effectively.
- Continuous Improvement: ERP for industrial equipment supports a culture of continuous improvement by providing data-driven feedback and performance metrics. Manufacturers can monitor KPIs, track progress toward goals, and identify opportunities for process optimization and innovation to drive continuous improvement initiatives within the supply chain.
In summary, industrial machinery equipment ERP systems play a critical role in enabling data-driven decision-making by providing real-time data analytics, advanced reporting tools, predictive analytics, demand forecasting, inventory optimization, supplier performance analysis, cost analysis, scenario planning, root cause analysis, and support for continuous improvement initiatives.
By leveraging these capabilities, manufacturers can make informed decisions, optimize supply chain performance, and achieve supply chain success within the industrial machinery equipment sector.
Demand Forecasting Accuracy
Demand forecasting accuracy is essential for achieving supply chain success in the industrial machinery equipment sector, and industrial machinery equipment ERP solutions play a vital role in improving forecasting accuracy. ERP for industrial equipment offers specialized features to enhance demand forecasting processes.
Here's how industrial machinery equipment ERP contributes to demand forecasting accuracy:
- Historical Data Analysis: Industrial machinery ERP systems analyze historical sales data, production trends, and market demand patterns to identify historical demand patterns. By examining past performance, manufacturers can identify trends, seasonality, and patterns that influence future demand.
- Statistical Forecasting Models: ERP for industrial equipment leverages statistical forecasting models, such as time series analysis, moving averages, and exponential smoothing, to forecast future demand based on historical data. These models consider factors such as trend, seasonality, and cyclical variations to generate accurate demand forecasts.
- Machine Learning Algorithms: Industrial machinery equipment ERP systems employ machine learning algorithms to improve demand forecasting accuracy by analyzing large datasets and identifying complex patterns and correlations. Machine learning algorithms can adapt and learn from new data, enhancing the accuracy of demand forecasts over time.
- Demand Sensing: Manufacturing ERP incorporates demand sensing capabilities to capture real-time demand signals from various sources, such as point-of-sale data, customer orders, and market intelligence. By integrating real-time demand data into the forecasting process, manufacturers can improve the accuracy of demand forecasts and respond quickly to changes in customer demand.
- Collaborative Forecasting: Manufacturing software systems facilitate collaborative demand forecasting by involving key stakeholders, such as sales teams, marketing teams, and customers, in the forecasting process. Collaborative forecasting enables manufacturers to incorporate valuable insights and domain knowledge from multiple sources, leading to more accurate demand forecasts.
- Integration with External Data Sources: MRP software integrates with external data sources, such as market research reports, economic indicators, and industry trends, to enrich demand forecasting models with external factors that may influence demand. By incorporating external data sources, manufacturers can improve the accuracy and robustness of demand forecasts.
- Promotion and Marketing Analysis: Industrial machinery ERP systems analyze the impact of promotions, marketing campaigns, and other external events on demand patterns. By evaluating the effectiveness of promotions and marketing activities, manufacturers can adjust demand forecasts accordingly to account for anticipated changes in demand.
- Customer Segmentation: Manufacturing ERP facilitates customer segmentation based on factors such as geographic location, industry vertical, and purchase history. By segmenting customers, manufacturers can develop more targeted demand forecasts tailored to specific customer segments, improving forecast accuracy.
- Forecast Accuracy Metrics: Industrial machinery equipment ERP systems track forecast accuracy metrics, such as mean absolute percentage error (MAPE) and forecast bias, to evaluate the performance of demand forecasting models. By analyzing forecast accuracy metrics, manufacturers can identify areas for improvement and refine forecasting models to enhance accuracy.
- Continuous Improvement: ERP for industrial equipment supports continuous improvement initiatives by providing feedback mechanisms and performance monitoring capabilities. Manufacturers can monitor forecast accuracy over time, identify forecasting errors and discrepancies, and implement corrective actions to improve forecast accuracy continually.
In summary, industrial machinery equipment ERP systems play a crucial role in improving demand forecasting accuracy by leveraging historical data analysis, statistical forecasting models, machine learning algorithms, demand sensing, collaborative forecasting, integration with external data sources, promotion and marketing analysis, customer segmentation, forecast accuracy metrics, and support for continuous improvement initiatives.
By leveraging these capabilities, manufacturers can enhance forecast accuracy, optimize inventory management, and achieve supply chain success within the industrial machinery equipment sector.
Reduced Lead Times
Reducing lead times is crucial for achieving supply chain success in the industrial machinery equipment sector, and industrial machinery equipment ERP solutions play a pivotal role in streamlining operations to achieve this objective. Manufacturing ERP offers specialized features to optimize processes and minimize lead times.
Here's how industrial machinery equipment ERP contributes to reducing lead times:
- Real-Time Production Planning: Industrial machinery equipment ERP systems enable real-time production planning by integrating production schedules, resource availability, and customer demand data. Manufacturers can adjust production schedules dynamically to respond to changes in demand, minimizing lead times and ensuring timely order fulfillment.
- Optimized Inventory Management: ERP for industrial equipment facilitates optimized inventory management by aligning inventory levels with demand forecasts and production schedules. By maintaining optimal inventory levels, manufacturers can reduce lead times for raw materials and components procurement, minimizing production delays.
- Demand Forecasting Integration: Industrial Machinery ERP integrates demand forecasting functionalities to predict future demand for machinery equipment products accurately. By forecasting demand with precision, manufacturers can plan production schedules more effectively, reducing lead times and improving responsiveness to customer demand.
- Supplier Collaboration: Manufacturing ERP facilitates collaboration with suppliers to streamline procurement processes and reduce lead times for raw materials and components. Manufacturers can communicate production requirements, share demand forecasts, and collaborate on inventory management strategies to optimize supply chain efficiency.
- Automated Order Processing: MRP software systems automate order processing workflows, from order entry to production scheduling and fulfillment. By automating manual tasks and eliminating bottlenecks in the order processing cycle, manufacturers can reduce lead times and improve order turnaround times.
- Production Efficiency Improvement: Manufacturing software supports continuous improvement initiatives to enhance production efficiency and reduce lead times. Manufacturers can identify inefficiencies in production processes, implement process improvements, and optimize resource utilization to accelerate production cycles.
- Supply Chain Visibility: Industrial machinery equipment ERP provides real-time visibility into supply chain activities, enabling manufacturers to track the movement of materials, monitor production progress, and identify potential delays. By enhancing supply chain visibility, manufacturers can proactively address issues and minimize lead times.
- Just-in-Time (JIT) Manufacturing: Manufacturing ERP supports Just-in-Time (JIT) manufacturing principles by synchronizing production schedules with customer demand. Manufacturers can produce machinery equipment products in response to specific customer orders, minimizing inventory holding costs and lead times associated with excess inventory.
- Integrated Quality Management: MRP software integrates quality management functionalities to ensure product quality and minimize rework and scrap. By maintaining high-quality standards throughout the production process, manufacturers can reduce lead times associated with quality-related issues and ensure timely delivery of defect-free products.
- Performance Analytics: Manufacturing software systems provide performance analytics tools to monitor key performance indicators (KPIs) related to lead times, production efficiency, and supply chain performance. By analyzing performance metrics, manufacturers can identify areas for improvement and implement strategies to further reduce lead times over time.
In summary, industrial machinery equipment ERP systems play a crucial role in reducing lead times by enabling real-time production planning, optimizing inventory management, integrating demand forecasting, facilitating supplier collaboration, automating order processing, improving production efficiency, enhancing supply chain visibility, implementing JIT manufacturing principles, integrating quality management, and providing performance analytics capabilities.
By leveraging these capabilities, manufacturers can minimize lead times, improve customer satisfaction, and achieve supply chain success within the industrial machinery equipment sector.
Cost Reduction
Cost reduction is a critical aspect of achieving supply chain success in the industrial machinery equipment sector, and industrial machinery equipment ERP solutions play a pivotal role in optimizing costs throughout the supply chain. Manufacturing ERP offers specialized features to identify cost-saving opportunities and streamline operations.
Here's how industrial machinery equipment ERP contributes to cost reduction:
- Optimized Procurement Processes: Industrial machinery ERP systems streamline procurement processes by automating supplier selection, purchase order generation, and invoice processing. By leveraging economies of scale and negotiating favorable terms with suppliers, manufacturers can reduce procurement costs and optimize spending on raw materials and components.
- Inventory Optimization: ERP for industrial equipment facilitates inventory optimization by aligning inventory levels with demand forecasts and production schedules. By maintaining optimal inventory levels, manufacturers can minimize carrying costs, reduce inventory holding costs, and avoid excess inventory write-offs, resulting in significant cost savings.
- Production Efficiency Improvement: MRP software supports continuous improvement initiatives to enhance production efficiency and reduce manufacturing costs. By identifying inefficiencies in production processes, optimizing resource utilization, and implementing lean manufacturing principles, manufacturers can minimize waste, improve productivity, and lower production costs.
- Supply Chain Collaboration: Manufacturing ERP facilitates collaboration with suppliers, subcontractors, and partners to optimize supply chain efficiency and reduce costs. By sharing production forecasts, coordinating logistics, and implementing vendor-managed inventory (VMI) programs, manufacturers can reduce lead times, minimize transportation costs, and optimize inventory holding costs.
- Energy Management: Manufacturing software systems include energy management functionalities to monitor and optimize energy consumption across manufacturing operations. By identifying energy-intensive processes, implementing energy-saving measures, and optimizing equipment utilization, manufacturers can reduce energy costs and improve sustainability.
- Maintenance Management: ERP for industrial equipment integrates maintenance management functionalities to optimize equipment maintenance schedules and reduce downtime. By implementing preventive maintenance programs, monitoring equipment health, and scheduling maintenance activities based on equipment usage and performance data, manufacturers can minimize unplanned downtime and reduce maintenance costs.
- Quality Management Integration: Industrial machinery equipment ERP systems integrate quality management functionalities to ensure product quality and minimize costs associated with quality-related issues. By implementing robust quality control measures, conducting inspections, and addressing non-conformances promptly, manufacturers can reduce rework, scrap, and warranty costs.
- Transportation Optimization: Manufacturing software facilitates transportation optimization by optimizing shipment consolidation, route planning, and carrier selection. By leveraging transportation management functionalities, manufacturers can minimize transportation costs, reduce freight expenses, and improve delivery efficiency.
- Labor Optimization: Industrial machinery ERP systems optimize labor utilization by aligning production schedules with workforce availability and skill levels. By implementing workforce management functionalities, manufacturers can minimize labor costs, improve productivity, and maximize efficiency across manufacturing operations.
- Cost Analysis and Reporting: MRP software provides cost analysis and reporting tools to monitor and analyze costs across various aspects of the supply chain. By generating cost reports, analyzing cost drivers, and identifying cost-saving opportunities, manufacturers can implement cost-reduction initiatives and improve profitability.
In summary, industrial machinery equipment ERP systems play a crucial role in cost reduction by optimizing procurement processes, inventory management, production efficiency, supply chain collaboration, energy management, maintenance management, quality management, transportation optimization, labor utilization, and cost analysis.
By leveraging these capabilities, manufacturers can identify cost-saving opportunities, streamline operations, and achieve supply chain success within the industrial machinery equipment sector.
How can Deskera as an Industrial Machinery Equipment ERP Help in Achieving Supply Chain Success?
Deskera, as an industrial machinery equipment ERP, can significantly contribute to supply chain success in several ways:
- Streamlined Procurement Processes: Deskera ERP streamlines procurement processes by automating supplier management, purchase order generation, and invoice processing. This ensures efficient procurement of raw materials and components, reducing lead times and ensuring timely availability of materials for production.
- Inventory Optimization: Deskera ERP helps optimize inventory levels by providing real-time visibility into inventory levels, demand forecasts, and production schedules. This enables manufacturers to maintain optimal inventory levels, minimize excess inventory, and avoid stockouts, leading to improved inventory turnover and reduced carrying costs.
- Production Planning and Scheduling: Deskera ERP facilitates efficient production planning and scheduling by integrating production workflows, resource allocation, and capacity planning. Manufacturers can optimize production schedules, balance workloads, and ensure on-time delivery of products to meet customer demand.
- Quality Management: Deskera ERP includes robust quality management functionalities to ensure product quality and compliance with industry standards. It supports quality control processes, inspections, and non-conformance management, enabling manufacturers to maintain high-quality standards and minimize defects.
- Service Management: Deskera ERP supports after-sales service operations, including field service management, warranty management, and service contract management. It enables manufacturers to schedule service appointments, dispatch technicians, and manage spare parts inventory, ensuring timely resolution of customer issues and maximizing equipment uptime.
- Demand Forecasting: Deskera ERP provides demand forecasting capabilities to predict future demand for machinery equipment products accurately. By analyzing historical sales data, market trends, and customer behavior, manufacturers can forecast demand with precision, optimize inventory levels, and improve production planning.
- Financial Management: Deskera ERP includes robust financial management functionalities, including accounting, budgeting, and financial reporting. It enables manufacturers to track costs, revenues, and profitability across projects, departments, and business units, supporting informed decision-making and financial analysis.
- Business Intelligence and Analytics: Deskera ERP offers business intelligence (BI) and analytics tools to analyze data and generate insights for decision-making. It provides dashboards, reports, and key performance indicators (KPIs) to monitor supply chain performance, identify trends, and drive continuous improvement initiatives.
Key Takeaways
The 12 steps to supply chain success with industrial machinery equipment ERP represent a holistic approach to optimizing operations, enhancing efficiency, and driving growth in the industrial machinery equipment manufacturing sector.
These 12 steps are:
- Improved Inventory Management: Manufacturing ERP systems provide real-time visibility into inventory levels, enabling better control over stock levels, reducing excess inventory, and minimizing stockouts.
- Streamlined Procurement Processes: By automating procurement workflows, MRP software systems streamline the purchasing process, optimize vendor selection, and ensure timely delivery of raw materials and components.
- Enhanced Production Planning: Manufacturing software systems facilitate efficient production planning by aligning production schedules with demand forecasts, optimizing resource allocation, and minimizing production bottlenecks.
- Efficient Order Processing: Manufacturing ERP systems automate order processing tasks, from order entry to fulfillment, improving order accuracy, reducing lead times, and enhancing customer satisfaction.
- Integrated Supply Chain Collaboration: ERP systems enable seamless collaboration with suppliers, customers, and other stakeholders through integrated communication channels, fostering better coordination and information sharing.
- Optimized Transportation Management: MRP software systems incorporate transportation management modules to optimize freight logistics, route planning, and carrier selection, reducing transportation costs and improving delivery efficiency.
- Effective After-Sales Service: Industrial machinery equipment ERP systems include service management functionalities to support after-sales service activities such as maintenance, repairs, and warranty management, ensuring customer satisfaction and loyalty.
- Compliance Management: Industrial machinery ERP systems help ensure compliance with industry regulations and standards by incorporating features for regulatory reporting, quality control, and documentation management.
- Data-Driven Decision-Making: ERP for industrial equipment systems provides actionable insights through advanced analytics and reporting capabilities, enabling data-driven decision-making to optimize supply chain operations and strategic planning.
- Demand Forecasting Accuracy: Manufacturing ERP systems leverage historical data and advanced forecasting algorithms to improve demand forecasting accuracy, enabling better inventory planning and resource allocation.
- Reduced Lead Times: By streamlining processes and improving visibility across the supply chain, MRP software systems help reduce lead times, from order placement to delivery, enhancing responsiveness to customer demands.
- Cost Reduction: Overall, industrial machinery equipment ERP systems help reduce costs across the supply chain by optimizing inventory levels, minimizing waste, improving resource utilization, and enhancing operational efficiency.
By leveraging the capabilities of manufacturing ERP solutions tailored to their specific needs, manufacturers can overcome challenges, seize opportunities, and achieve supply chain excellence.
Overall, Deskera industrial machinery equipment ERP plays a crucial role in optimizing supply chain processes, enhancing productivity, and driving growth within the industrial machinery equipment sector.
By leveraging its comprehensive features and functionalities, manufacturers can streamline operations, improve efficiency, and maintain a competitive edge in today's dynamic business environment.
Related Articles
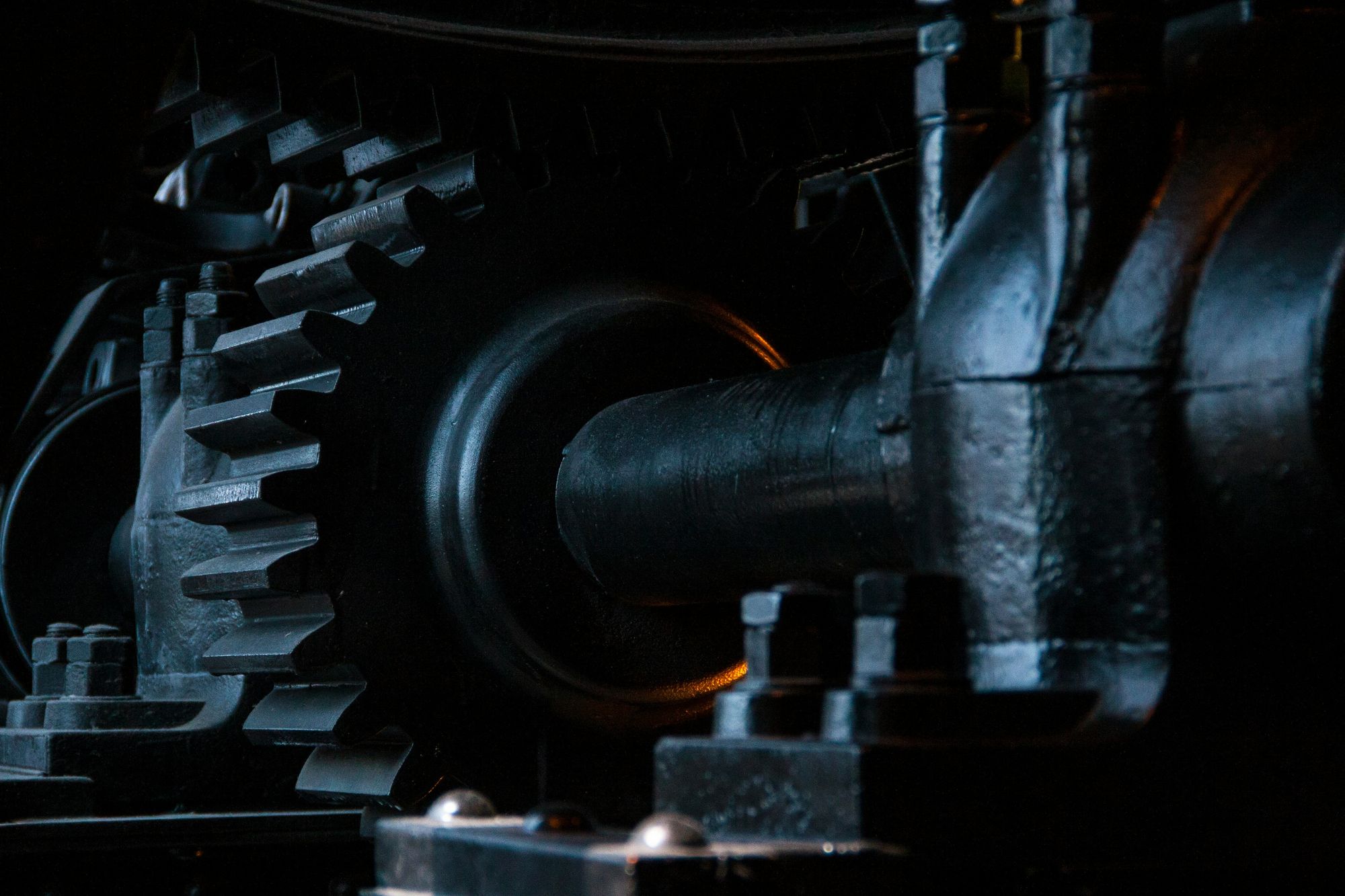
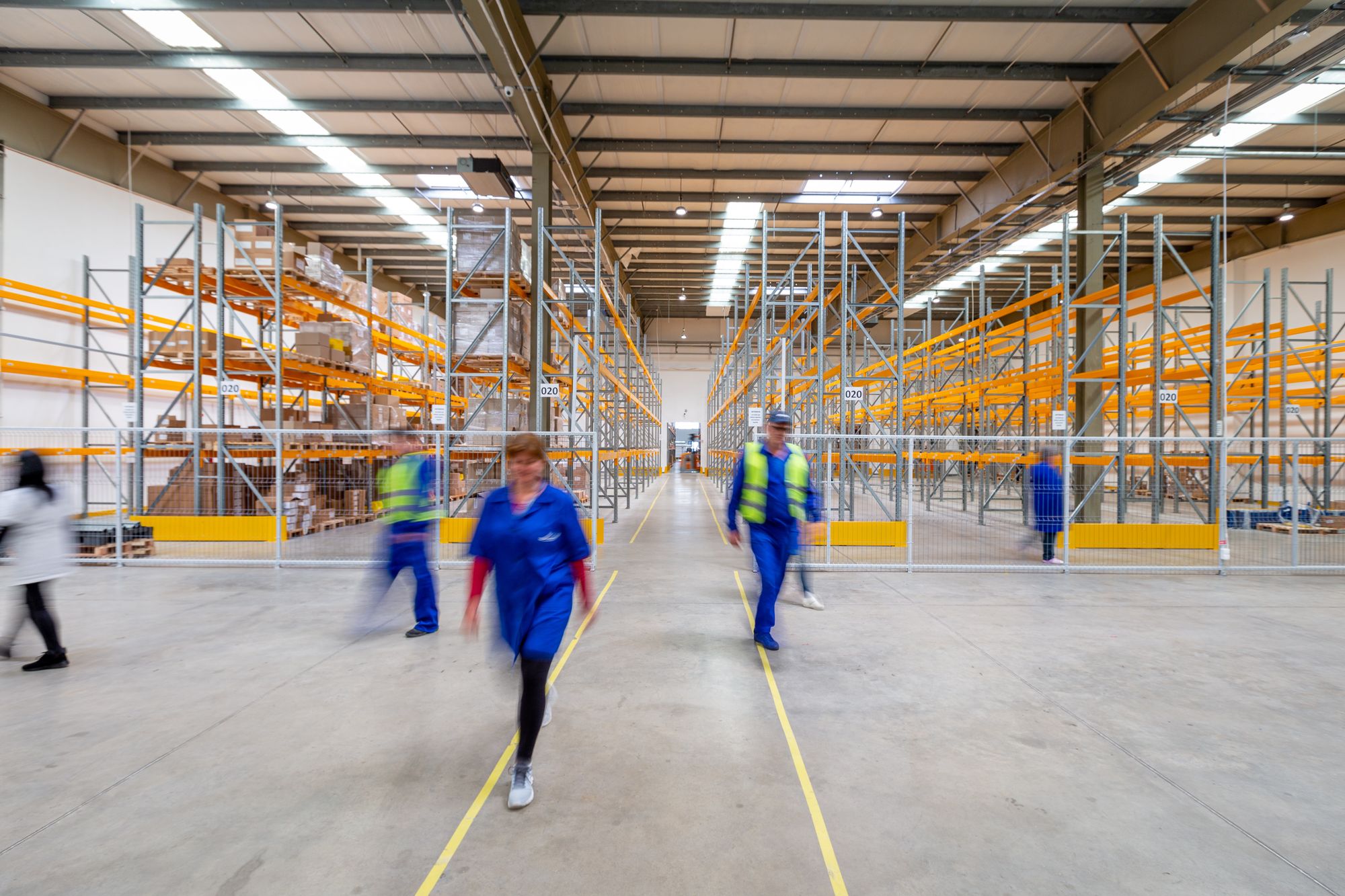

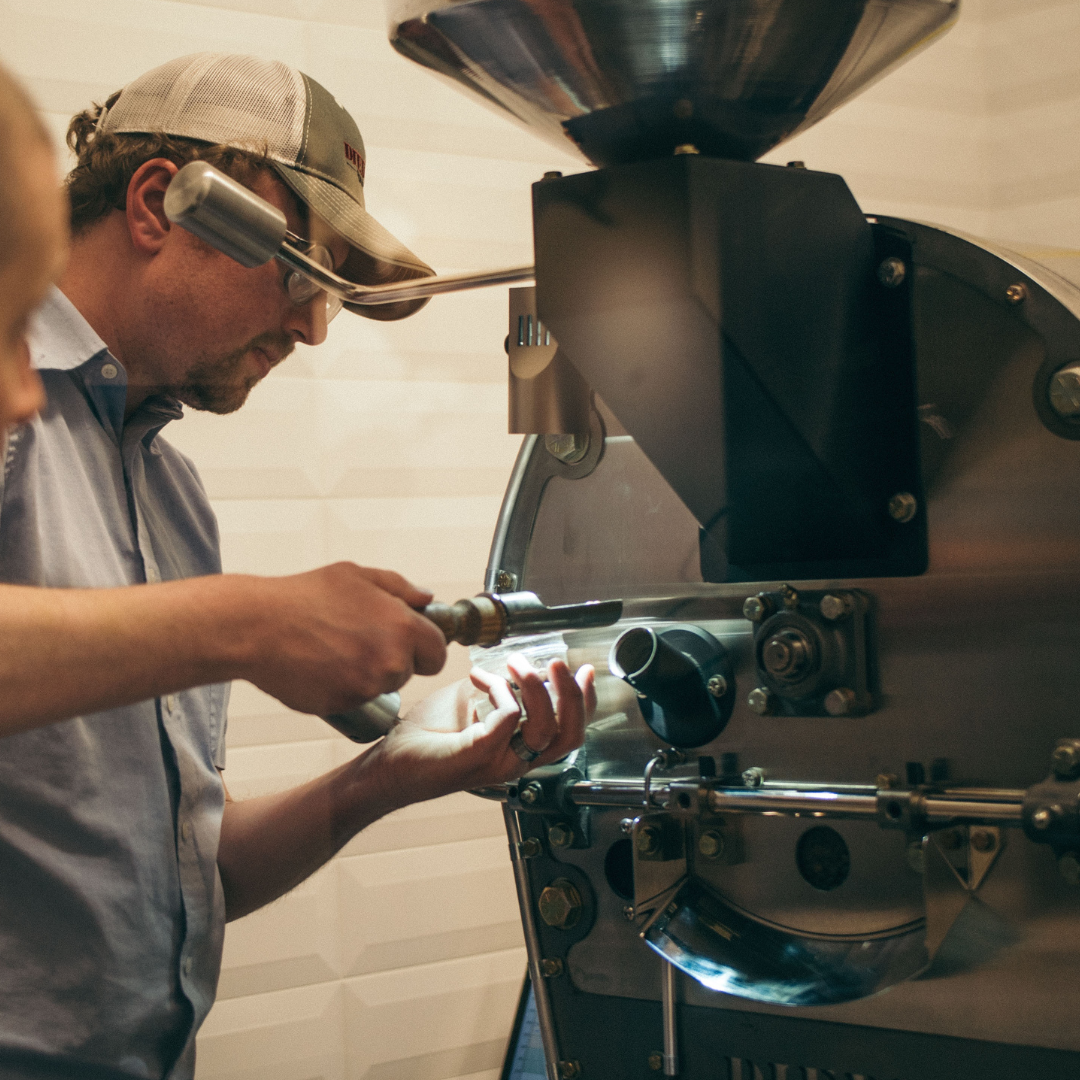
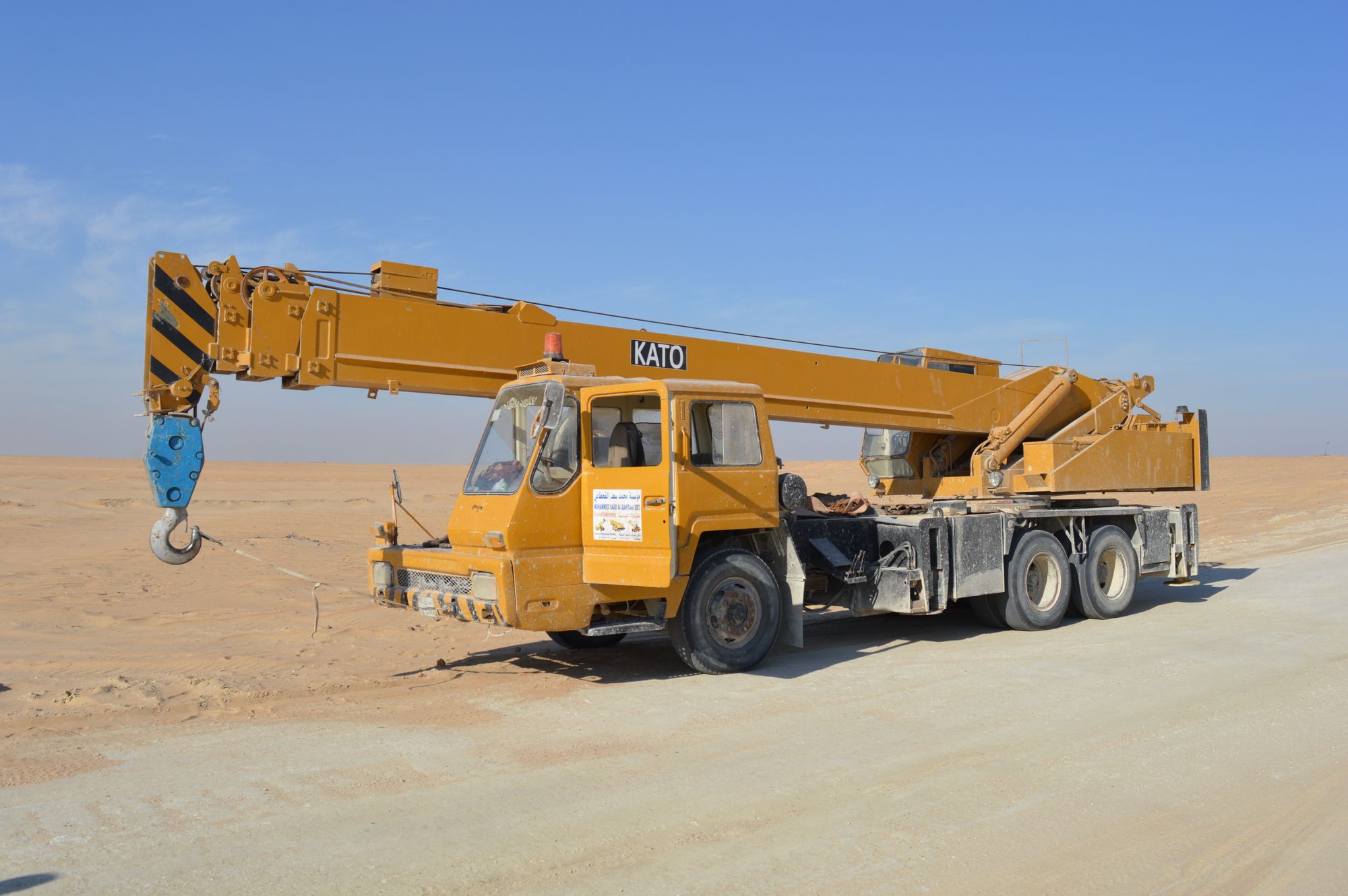
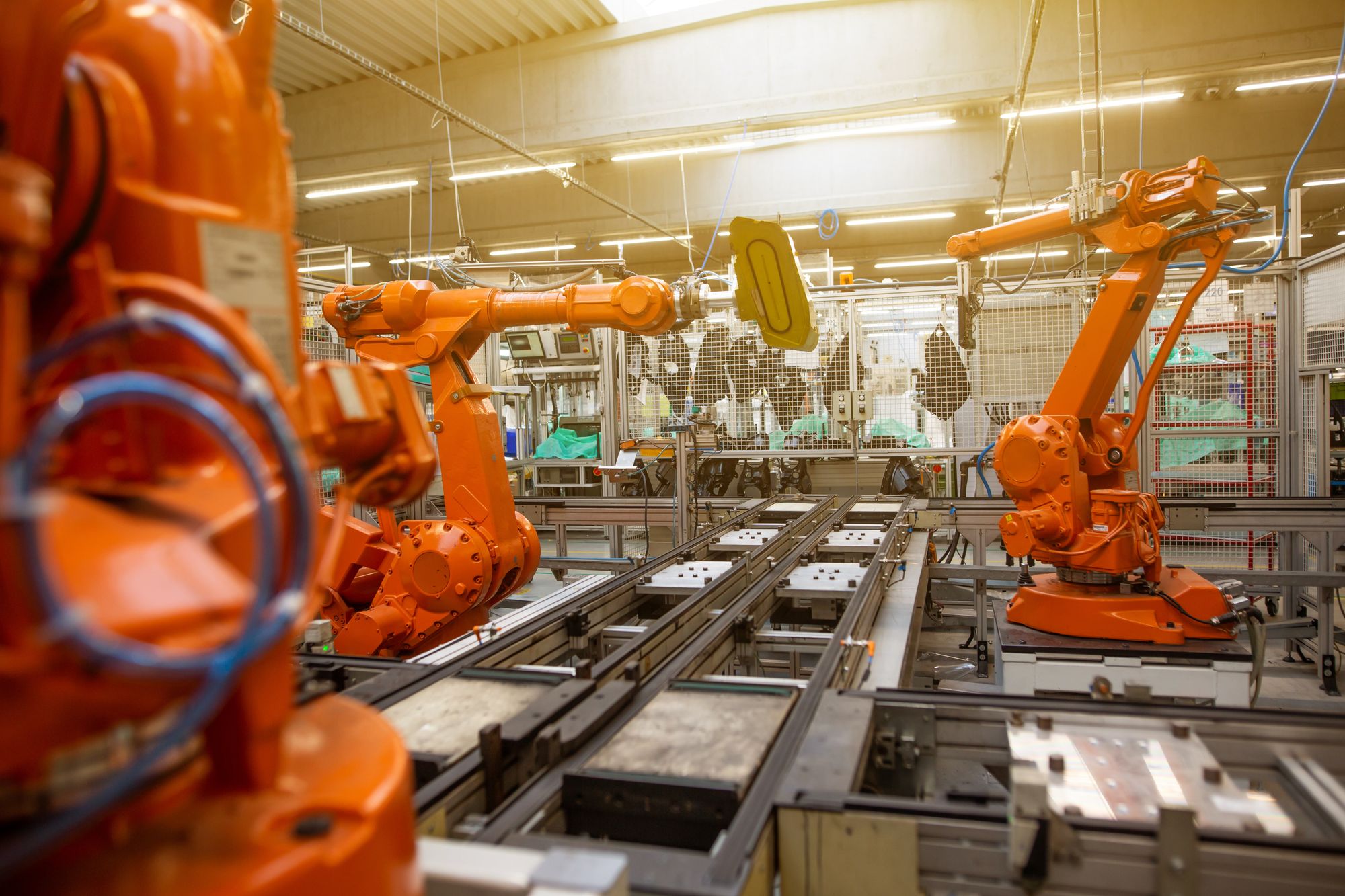