In today's dynamic manufacturing landscape, where customer demands are constantly evolving, having an efficient production planning process is crucial for success. From accurately forecasting demand to seamless execution, streamlining the manufacturing production planning process can significantly enhance operational efficiency, reduce costs, and improve customer satisfaction.
According to a recent survey conducted by industry experts, over 70% of manufacturing companies struggle with production planning challenges, leading to delays, excess inventory, and missed opportunities. However, implementing effective strategies and leveraging advanced technologies can address these issues and drive positive outcomes.
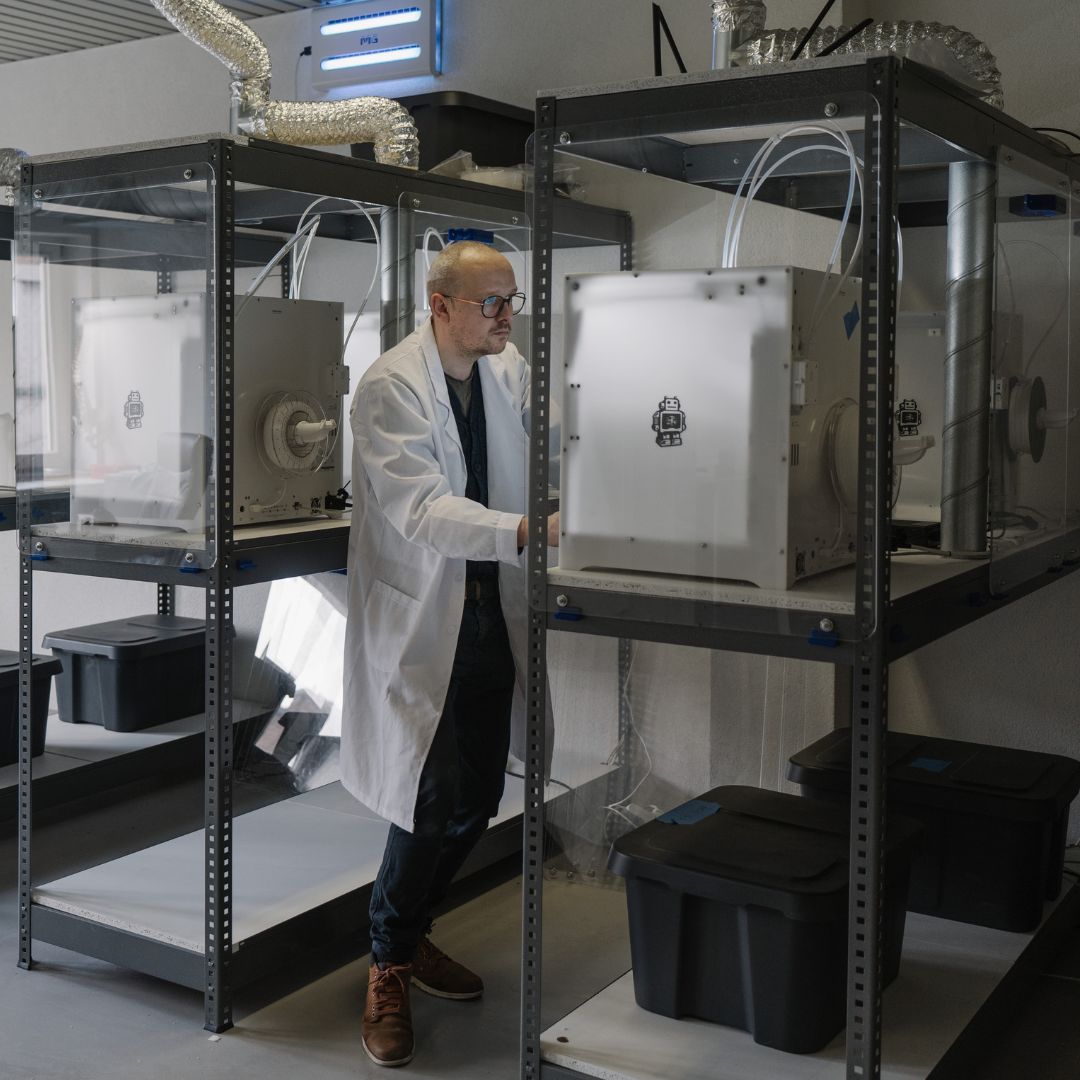
This article will delve into the key steps involved in streamlining the production planning process, offering valuable insights, techniques, and best practices. Additionally, real-world case studies and success stories will demonstrate the transformative impact of optimized production planning.
So, let's explore how your manufacturing business can go from forecasting to execution with streamlined production planning.
- Importance of Efficient Manufacturing Production Planning Process
- Understanding the Manufacturing Production Planning Process
- Improving Forecasting for Accurate Planning
- Aligning Demand and Supply
- Streamlining Production Planning and Scheduling
- Enhancing Execution and Monitoring
- Continuous Improvement and Optimization
- Overcoming Implementation Challenges
- Case Studies and Success Stories
- Conclusion
- How can Deskera Help You?
- Key Takeaways
- Related Articles
Importance of Efficient Manufacturing Production Planning Process
An efficient manufacturing production planning process holds paramount importance in today's competitive business landscape. It serves as the backbone of a well-organized and productive manufacturing operation. The benefits of streamlining this process are numerous and directly impact the overall success and profitability of a company.
Firstly, an efficient production planning process ensures optimal utilization of resources, including labor, materials, and equipment. By accurately forecasting demand and aligning it with production capabilities, manufacturers can avoid overproduction or underutilization, leading to cost savings and improved profitability.
Secondly, streamlined production planning enables timely delivery of products to customers. By effectively managing lead times, production schedules, and inventory levels, companies can meet customer expectations and enhance customer satisfaction, thereby fostering strong relationships and repeat business.
Furthermore, an optimized production planning process reduces waste, eliminates bottlenecks, and minimizes production downtime. It allows for effective inventory management, preventing excessive stockpiling or shortages, and improving cash flow.
Lastly, a well-structured production planning process enables manufacturers to respond swiftly to market fluctuations, demand changes, and unforeseen disruptions. It promotes agility and adaptability, empowering companies to stay competitive in a rapidly evolving business environment.
Overall, an efficient manufacturing production planning process not only enhances operational efficiency but also positively impacts customer satisfaction, profitability, and business resilience. It serves as a key driver for success in the manufacturing industry.
Understanding the Manufacturing Production Planning Process
The production planning process is a systematic approach employed by manufacturing companies to efficiently manage and coordinate the various activities involved in transforming raw materials into finished products.
A. Components of the production planning process
It encompasses several interconnected components, including:
- Demand Forecasting: This involves analyzing historical data, market trends, and customer insights to estimate future demand for products. Accurate demand forecasting is crucial for aligning production levels with customer requirements.
- Capacity Planning: Capacity planning focuses on determining the optimal utilization of resources, such as labor, equipment, and facilities, to meet production demands. It involves evaluating current capabilities, identifying constraints, and planning resource allocation accordingly.
- Material Planning: Material planning involves determining the quantity and timing of raw materials and components needed for production. It includes tasks such as inventory management, supplier coordination, and procurement planning to ensure a smooth flow of materials throughout the production process.
- Routing and Scheduling: Routing entails defining the sequence of operations and production steps required to transform raw materials into finished goods. Scheduling involves assigning timeframes and resources to each operation, ensuring that production activities are properly sequenced and coordinated.
- Production Monitoring and Control: This component involves real-time monitoring of production activities to ensure adherence to schedules, quality standards, and productivity goals. It includes tracking progress, identifying bottlenecks, and implementing corrective measures to maintain efficiency.
B. Key Challenges and Pain Points:
The manufacturing production planning process is not without its challenges and pain points. Some common challenges include:
- Demand Variability: Fluctuations in customer demand can make accurate forecasting and capacity planning difficult. Unexpected changes in demand patterns can lead to overproduction or stockouts, impacting profitability and customer satisfaction.
- Supply Chain Complexity: Managing a complex supply chain with multiple suppliers, long lead times, and potential disruptions poses challenges in material planning and coordination. Lack of visibility and communication issues can result in delays and production bottlenecks.
- Resource Constraints: Limited availability of skilled labor, machinery, or production facilities can hinder production planning. Balancing resource utilization and capacity optimization becomes crucial to meet demand while minimizing costs.
- Production Synchronization: Coordinating multiple production processes, especially in multi-stage or multi-site manufacturing, requires efficient routing and scheduling. Achieving synchronization among different departments and processes can be challenging.
- Information and Communication: Inadequate information sharing, poor communication, and data silos can impede the flow of information across various stages of production planning. Lack of integration among systems and departments can lead to errors, delays, and inefficiencies.
Addressing these challenges requires the implementation of robust planning systems, accurate data analysis, improved collaboration among stakeholders, and the adoption of advanced technologies such as enterprise resource planning (ERP) systems and manufacturing execution systems (MES).
Improving Forecasting for Accurate Planning
Accurate forecasting is a crucial element in the manufacturing production planning process, as it lays the foundation for effective resource allocation, inventory management, and production scheduling.
In this section, we delve into the importance of precise forecasting and explore various techniques and tools that can enhance the accuracy of demand predictions. By leveraging historical data, demand forecasting methods, and collaborative approaches, manufacturers can gain valuable insights to optimize their production planning process.
This section aims to provide valuable insights and practical strategies for improving forecasting accuracy, ultimately enabling manufacturers to align their production levels with customer demands and achieve greater operational efficiency.
A. Importance of accurate forecasting
Accurate forecasting plays a pivotal role in the manufacturing production planning process for several reasons:
- Demand Alignment: Accurate forecasting enables manufacturers to align their production levels with customer demand. By understanding future demand patterns, companies can avoid underproduction or overproduction, ensuring that they have the right amount of products available when customers need them. This leads to improved customer satisfaction and helps prevent lost sales opportunities.
- Efficient Resource Allocation: Precise forecasting allows manufacturers to allocate their resources effectively. By having a clear understanding of future demand, they can optimize labor, equipment, and raw material utilization. This minimizes wastage, reduces costs, and improves overall operational efficiency.
- Inventory Management: Accurate forecasting aids in efficient inventory management. By predicting demand accurately, manufacturers can maintain optimal inventory levels, avoiding excessive stockpiling or shortages. This helps in reducing carrying costs, preventing obsolescence, and ensuring a smooth flow of materials through the production process.
- Production Planning and Scheduling: Reliable forecasting provides a solid foundation for production planning and scheduling activities. It enables manufacturers to create realistic production plans, allocate resources efficiently, and establish realistic timelines. This helps in streamlining operations, reducing bottlenecks, and improving overall productivity.
- Supply Chain Optimization: Accurate forecasting extends beyond the manufacturing facility and positively impacts the entire supply chain. By sharing demand forecasts with suppliers, manufacturers can collaborate effectively and enhance supply chain coordination. This leads to improved lead times, reduced stockouts, and better supplier relationships.
It ultimately contributes to increased customer satisfaction, reduced costs, and improved competitiveness in the marketplace.
B. Techniques and tools for effective forecasting
Techniques and Tools for Effective Forecasting:
- Historical Data Analysis: Historical data analysis involves examining past sales data, market trends, and other relevant historical information to identify patterns and trends. By analyzing historical data, manufacturers can gain insights into seasonal fluctuations, market trends, and other factors that influence demand. This data serves as a basis for making informed forecasts and improving accuracy.
- Demand Forecasting Methods: Various demand forecasting methods can be employed to predict future demand. These methods include:
a. Time Series Analysis: This method involves analyzing historical data to identify trends, seasonality, and other patterns. Techniques such as moving averages, exponential smoothing, and trend analysis are used to forecast future demand based on historical patterns.
b. Market Research and Surveys: Market research and surveys involve collecting data through customer surveys, interviews, and market analysis to gather insights on customer preferences, buying behavior, and market trends. This qualitative data can be used to complement quantitative forecasting methods.
c. Statistical Modeling: Statistical modeling techniques, such as regression analysis and correlation analysis, can be employed to identify relationships between demand and various factors, such as price, promotional activities, and economic indicators. These models help in quantifying the impact of these factors on demand and making accurate forecasts.
d. Machine Learning and Artificial Intelligence: Advanced technologies like machine learning and artificial intelligence are increasingly being used for demand forecasting. These algorithms can analyze large volumes of data, identify patterns, and make accurate predictions based on complex models and algorithms. - Collaborative Forecasting: Collaborative forecasting involves involving key stakeholders, such as sales teams, marketing teams, and suppliers, in the forecasting process. By leveraging the collective knowledge and expertise of various departments, manufacturers can gain a more comprehensive understanding of demand drivers and potential challenges. Collaborative forecasting improves accuracy by incorporating insights from different perspectives and aligning expectations among stakeholders.
To support these techniques, manufacturers can leverage various tools and software for effective forecasting. These tools range from basic spreadsheet software like Microsoft Excel to more advanced forecasting software and integrated enterprise resource planning (ERP) systems.
These tools help in data analysis, model building, and visualization, enabling manufacturers to make more accurate and informed forecasts.
Aligning Demand and Supply
Efficiently balancing customer demand with production capabilities is essential for optimizing inventory levels, reducing costs, and ensuring timely delivery of products. This section delves into the strategies and approaches that manufacturers can employ to achieve a seamless alignment between demand and supply.
By implementing techniques such as just-in-time (JIT) manufacturing and vendor-managed inventory (VMI), companies can enhance their production planning process and establish a robust foundation for efficient operations.
Through a comprehensive examination of demand-supply synchronization, this section aims to provide valuable insights and practical guidance for manufacturers seeking to streamline their production planning process and improve overall business performance.
A. Balancing demand and supply
Balancing demand and supply is a critical aspect of the manufacturing production planning process. It involves aligning customer demand with production capabilities to ensure optimal utilization of resources, minimize inventory costs, and meet customer expectations. Here are key considerations and strategies for achieving this balance:
- Accurate Demand Forecasting: Accurate demand forecasting serves as the foundation for balancing demand and supply. By analyzing historical data, market trends, and customer insights, manufacturers can estimate future demand more accurately. This enables them to plan production levels, inventory levels, and resource allocation accordingly.
- Flexible Production Capacity: Having a flexible production capacity helps manufacturers respond to changes in demand quickly. By designing production processes that can be easily scaled up or down, manufacturers can adjust their production capabilities based on demand fluctuations. This flexibility reduces the risk of overproduction or underutilization of resources.
- Collaborative Planning: Collaboration among various departments, such as sales, marketing, and operations, is crucial for aligning demand and supply. Regular communication and information sharing enable a better understanding of customer requirements, market dynamics, and production constraints. This collaborative approach helps in achieving consensus on production plans and ensures that they are aligned with demand forecasts.
- Agile Inventory Management: Effective inventory management plays a vital role in balancing demand and supply. By implementing strategies such as just-in-time (JIT) manufacturing and vendor-managed inventory (VMI), manufacturers can reduce inventory holding costs and minimize the risk of stockouts or excess inventory. JIT manufacturing focuses on producing goods only when there is a specific demand, while VMI involves suppliers monitoring and managing inventory levels on behalf of the manufacturer.
- Demand-Supply Optimization Tools: Leveraging advanced planning and optimization tools can enhance the ability to balance demand and supply effectively. These tools consider various factors such as lead times, production capacities, and customer demand variability to optimize production plans and resource allocation. Enterprise resource planning (ERP) systems and advanced planning and scheduling (APS) software are examples of tools that aid in demand-supply optimization.
This alignment contributes to improved customer satisfaction, reduced costs, and increased competitiveness in the market.
B. Optimizing inventory levels
Optimizing inventory levels is a crucial aspect of the manufacturing production planning process. It involves finding the right balance between having enough inventory to meet customer demand while minimizing carrying costs and the risk of obsolescence. Here are key considerations and strategies for optimizing inventory levels:
- Demand Forecasting and Planning: Accurate demand forecasting is essential for optimizing inventory levels. By analyzing historical data, market trends, and customer insights, manufacturers can forecast demand more precisely. This enables them to plan their inventory levels accordingly, ensuring that they have sufficient stock to meet customer demand without excessive overstocking.
- Safety Stock and Lead Time Management: Incorporating safety stock into inventory planning helps buffer against demand variability and unforeseen disruptions in the supply chain. By considering factors such as lead times, production variability, and supplier reliability, manufacturers can determine the appropriate level of safety stock to maintain. Efficient lead time management, including reducing lead times where possible, also helps in optimizing inventory levels and responsiveness to customer demands.
- Just-in-Time (JIT) and Lean Principles: Implementing JIT manufacturing and Lean principles can aid in optimizing inventory levels. JIT focuses on producing goods only when there is specific demand, reducing the need for excessive inventory. Lean principles, such as reducing waste and improving process efficiency, contribute to leaner inventory levels by minimizing work-in-progress inventory and eliminating non-value-added activities.
- Supplier Collaboration and Vendor-Managed Inventory (VMI): Collaborating closely with suppliers and implementing VMI can optimize inventory levels. VMI involves suppliers monitoring and managing inventory levels on behalf of the manufacturer. By sharing real-time inventory data and collaborating with suppliers, manufacturers can ensure a steady flow of materials, reduce stockouts, and avoid excessive inventory buildup.
- Inventory Management Systems and Technology: Leveraging inventory management systems and technology can improve inventory control and optimization. These systems enable real-time tracking of inventory levels, facilitate demand-supply synchronization, and automate replenishment processes. Advanced technologies such as barcode scanning, RFID tagging, and automated inventory control systems enhance accuracy and efficiency in inventory management.
By optimizing inventory levels, manufacturers can reduce carrying costs, minimize the risk of obsolescence, and improve cash flow. Effective inventory optimization ensures that products are available when customers need them, enhancing customer satisfaction and competitiveness in the marketplace.
C. Strategies for demand and supply synchronization
Demand and supply synchronization is crucial for efficient production planning. Here are two key strategies for achieving synchronization:
- Just-in-Time (JIT) Manufacturing: JIT is a production strategy that aims to minimize inventory levels by producing goods only when there is specific demand. With JIT manufacturing, manufacturers receive raw materials and components just in time for production, eliminating the need for excess inventory. This strategy helps reduce carrying costs, minimize waste, and improve overall efficiency in the production process. JIT relies on accurate demand forecasting, streamlined production processes, and strong supplier relationships to ensure timely delivery of materials.
- Vendor-Managed Inventory (VMI): VMI is a collaborative approach between manufacturers and suppliers that involves the supplier monitoring and managing inventory levels on behalf of the manufacturer. In VMI, the supplier has real-time access to the manufacturer's inventory data and takes responsibility for replenishing stock based on agreed-upon inventory levels or consumption patterns. This strategy allows manufacturers to focus on core production activities while suppliers take charge of inventory management. VMI improves supply chain visibility, reduces stockouts, and enhances overall supply chain efficiency.
By implementing JIT manufacturing and VMI, manufacturers can achieve closer alignment between customer demand and supply capabilities. These strategies contribute to reduced inventory carrying costs, improved responsiveness to customer needs, enhanced supply chain coordination, and increased overall operational efficiency.
Streamlining Production Planning and Scheduling
Creating a production plan is a crucial step in streamlining production planning and scheduling. It involves developing a detailed roadmap that outlines the sequence of production activities, resource requirements, and timelines.
Here are key considerations in creating an effective production plan:
Demand Forecasting: The production plan should be aligned with accurate demand forecasts to ensure the right quantity of products is produced to meet customer demand. Demand forecasts serve as the basis for determining production volumes and scheduling.
Capacity Assessment: Assessing the available production capacity is essential to determine the feasibility of meeting demand. Factors such as equipment availability, labor resources, and production lead times are considered to ensure that the production plan is feasible and achievable within the available resources.
Production Sequence: The production plan should define the order in which production activities are to be carried out. It outlines the steps involved in transforming raw materials into finished goods, taking into account factors such as production time, dependencies between tasks, and the availability of inputs.
Resource Allocation: The production plan includes resource allocation, determining the quantity of materials, labor, and equipment required at each stage of production. Effective resource allocation ensures optimal utilization of resources, minimizing bottlenecks and idle time.
Contingency Planning: Anticipating and planning for contingencies, such as machine breakdowns, supplier delays, or changes in demand, is important in creating a robust production plan. Including contingency measures helps mitigate risks and maintain smooth operations.
B. Factors Influencing Production Planning Decisions:
Several factors influence production planning decisions. Manufacturers need to consider these factors to make informed decisions that maximize efficiency and productivity. Here are some key factors to consider:
Demand Variability: Fluctuations in customer demand can significantly impact production planning decisions. Manufacturers must analyze historical demand patterns, market trends, and customer preferences to anticipate demand variability accurately. Balancing demand variability with production capacity is essential to avoid stockouts or excessive inventory levels.
Lead Time: Lead time, including procurement lead time and production lead time, affects production planning decisions. Longer lead times may necessitate adjustments in the production schedule to ensure the timely availability of materials and meet customer deadlines.
Production Costs: Production costs, including labor, raw materials, equipment maintenance, and energy consumption, influence production planning decisions. Balancing cost considerations with production volume is crucial to optimize profitability.
Capacity Constraints: Available production capacity, including labor and equipment availability, influences production planning decisions. Manufacturers must assess capacity constraints and optimize resource allocation to maximize production output.
Production Efficiency and Quality: Maximizing production efficiency and maintaining high-quality standards are important considerations in production planning decisions. Balancing productivity goals with quality requirements helps ensure customer satisfaction and minimize rework or product recalls.
By considering these factors, manufacturers can make informed production planning decisions that maximize resource utilization, meet customer demands, and achieve operational efficiency. Streamlining production planning and scheduling involves finding the optimal balance among these factors to optimize productivity and meet business objectives.
C. Tools and software for production planning and scheduling
Efficient production planning and scheduling are facilitated by the use of specialized tools and software. Here are two key technologies used in production planning and scheduling:
Enterprise Resource Planning (ERP) Systems:
ERP systems are comprehensive software solutions that integrate various aspects of a company's operations, including production planning and scheduling. They provide a centralized platform for managing and coordinating different functions, such as inventory management, procurement, manufacturing, and sales.
Key features of ERP systems for production planning and scheduling include:
- Demand forecasting: ERP systems often include modules or functionalities for demand forecasting, enabling manufacturers to make accurate predictions and align production accordingly.
- Resource management: ERP systems help optimize resource allocation by providing real-time visibility into inventory levels, production capacity, and labor availability. This allows for efficient scheduling of resources to meet demand.
- Production scheduling: ERP systems offer tools for creating and managing production schedules, considering factors such as order prioritization, lead times, and resource availability. These tools facilitate efficient coordination of production activities.
- Inventory control: ERP systems provide inventory management capabilities, allowing manufacturers to track inventory levels, manage stockouts, and optimize inventory replenishment to meet demand while minimizing carrying costs.
Advanced Planning and Scheduling (APS) Systems:
APS systems are specialized software solutions designed to enhance production planning and scheduling. They utilize advanced algorithms and optimization techniques to generate optimized production schedules, considering multiple variables and constraints.
Key features of APS systems include:
- Capacity planning: APS systems help identify and optimize production capacity based on available resources and demand requirements. They consider factors such as machine capabilities, labor availability, and production constraints to generate feasible schedules.
- Real-time scheduling: APS systems offer real-time scheduling capabilities, enabling manufacturers to respond quickly to changing demand or production disruptions. These systems provide visibility into the current production status and allow for dynamic adjustments to schedules.
- What-if analysis: APS systems allow manufacturers to perform "what-if" scenarios to evaluate the impact of different variables on production schedules. This helps in assessing the feasibility of alternative scenarios and making informed decisions.
- Optimization algorithms: APS systems employ advanced algorithms to optimize production schedules based on predefined objectives, such as minimizing makespan, reducing changeover times, or maximizing resource utilization. These algorithms consider various constraints and variables to generate optimal schedules.
By leveraging ERP systems and APS systems, manufacturers can streamline production planning and scheduling, optimize resource utilization, improve on-time delivery, and enhance overall operational efficiency. These tools provide a comprehensive and data-driven approach to managing production processes and ensure efficient coordination among various departments.
Enhancing Execution and Monitoring
Enhancing execution and monitoring is essential for effective production planning. It involves translating production plans into action, implementing real-time monitoring and control mechanisms, and using key performance indicators (KPIs) to measure and improve production efficiency.
A. Translating Plans into Action:
Translating plans into action involves effectively communicating the production plan to the workforce and ensuring its implementation. This includes assigning tasks, providing clear instructions, and establishing accountability. Effective communication and coordination across different teams and departments are vital to ensure smooth execution of the production plan.
B. Real-time Monitoring and Control:
Real-time monitoring and control enable manufacturers to track the progress of production activities and make necessary adjustments in real-time. By using technologies such as sensors, IoT devices, and automation systems, manufacturers can collect data on production parameters, equipment performance, and quality metrics. Real-time monitoring helps identify deviations from the plan and allows for proactive interventions to address issues promptly.
C. Key Performance Indicators (KPIs) for Production Efficiency:
Key performance indicators (KPIs) provide measurable metrics to assess production efficiency and performance. KPIs can include metrics such as overall equipment efficiency (OEE), production cycle time, scrap and rework rates, and on-time delivery. Monitoring KPIs enables manufacturers to identify areas for improvement, track progress towards production goals, and drive continuous improvement efforts.
By enhancing execution and monitoring, manufacturers can ensure that production plans are effectively implemented, deviations are addressed promptly, and performance is continuously monitored and improved. This leads to increased operational efficiency, reduced costs, and enhanced customer satisfaction.
Continuous Improvement and Optimization
Continuous improvement and optimization are crucial elements in the manufacturing production planning process. They involve ongoing efforts to enhance operational efficiency, eliminate waste, and achieve higher levels of productivity and quality.
A. Importance of Continuous Improvement:
Continuous improvement is vital for staying competitive in the market and meeting evolving customer demands. It fosters a culture of innovation and drives efficiency gains by identifying and eliminating inefficiencies, reducing costs, and improving overall business performance.
B. Lean Manufacturing Principles:
Lean manufacturing principles focus on minimizing waste and maximizing value-added activities. It involves techniques such as value stream mapping, 5S methodology, and just-in-time (JIT) production. Lean principles optimize processes, reduce lead times, improve resource utilization, and enhance overall operational efficiency.
C. Six Sigma Methodologies:
Six Sigma methodologies aim to reduce defects and variations in processes, leading to improved quality and customer satisfaction. It employs statistical analysis and data-driven approaches to identify root causes of problems and implement effective solutions. Six Sigma methodologies, such as DMAIC (Define, Measure, Analyze, Improve, Control), provide a structured framework for problem-solving and process optimization.
By embracing continuous improvement, implementing lean manufacturing principles, and utilizing Six Sigma methodologies, manufacturers can streamline operations, reduce waste, enhance quality, and achieve optimal efficiency. These approaches foster a culture of innovation and excellence, enabling organizations to continuously adapt and improve their production planning processes.
Overcoming Implementation Challenges
Implementing changes in the manufacturing production planning process can pose various challenges. Overcoming these challenges is crucial to ensure the successful implementation and adoption of new practices. Here are key areas to focus on:
A. Change Management and Employee Engagement:
Change management plays a vital role in overcoming implementation challenges. It involves effectively communicating the reasons for change, addressing employee concerns, and involving employees in the decision-making process. Engaging employees through training programs, workshops, and regular communication fosters ownership, reduces resistance, and increases acceptance of new processes.
B. Integration with Other Business Functions:
Successful implementation requires integration with other business functions, such as procurement, inventory management, and sales. Collaboration and communication among different departments are essential to align processes, share information, and streamline operations. Breaking down silos and fostering cross-functional collaboration enhances efficiency and ensures a seamless flow of information throughout the organization.
C. Overcoming Resistance to Change:
Resistance to change is a common challenge during implementation. It can stem from fear of the unknown, concerns about job security, or a lack of understanding about the benefits of the changes. Overcoming resistance requires clear communication about the purpose and advantages of the new processes, addressing individual concerns, and providing support and training to build confidence and competence.
Additionally, involving key stakeholders from the beginning, conducting pilot projects to showcase the benefits, and recognizing and rewarding successful implementation efforts can help overcome resistance and promote a positive change culture.
By addressing these implementation challenges, organizations can successfully adopt new production planning practices, enhance efficiency, and drive continuous improvement. Overcoming challenges requires a comprehensive approach that focuses on people, processes, and effective communication throughout the implementation journey.
Case Studies and Success Stories
Case studies and success stories provide valuable insights into real-world examples of organizations that have successfully streamlined their manufacturing production planning processes.
By exploring these real-life examples, organizations can understand the challenges faced, the approaches taken, and the tangible benefits achieved.
A. Examples of companies that streamlined their production planning process
- Toyota: Toyota is renowned for its efficient production planning and execution, exemplified by its Toyota Production System (TPS). By implementing lean manufacturing principles and just-in-time production, Toyota has successfully streamlined its production planning process. The company focuses on waste reduction, continuous improvement, and a highly synchronized production system, enabling it to achieve high levels of efficiency, quality, and customer satisfaction.
- Apple: Apple has established a reputation for its effective production planning and supply chain management. The company utilizes demand forecasting techniques, collaborative planning with suppliers, and advanced production scheduling to ensure timely delivery of its products. By aligning production with demand and maintaining a responsive supply chain, Apple optimizes its production planning process and minimizes inventory levels while meeting customer expectations.
- Amazon: As a global e-commerce giant, Amazon has mastered the art of efficient production planning and fulfillment. Through advanced forecasting algorithms, real-time inventory management, and strategically located fulfillment centers, Amazon streamlines its production planning process to meet customer demands swiftly and accurately. The company's emphasis on data-driven decision-making and process optimization contributes to its exceptional efficiency and ability to handle high volumes of orders.
- Procter & Gamble (P&G): P&G has implemented innovative production planning strategies to optimize its manufacturing processes. The company utilizes collaborative forecasting and demand sensing techniques to gather real-time data on customer demand and adjust production plans accordingly. P&G also emphasizes supply chain integration and works closely with suppliers to ensure efficient procurement and inventory management, enhancing its production planning effectiveness.
These companies serve as prime examples of organizations that have successfully streamlined their production planning processes. These examples demonstrate the potential benefits and insights that can be gained by adopting effective production planning strategies.
B. Lessons learned and best practices
- Accurate Demand Forecasting: Effective production planning starts with accurate demand forecasting. Companies should invest in robust forecasting techniques and data analysis to understand customer demand patterns and anticipate future trends. This helps in aligning production plans with market demands, reducing inventory holding costs, and improving customer satisfaction.
- Collaborative Planning and Communication: Collaboration among different departments and stakeholders is crucial for successful production planning. Effective communication and information sharing ensure that all teams are aligned with the production goals and have a clear understanding of their roles and responsibilities. Regular meetings, cross-functional collaboration, and feedback loops facilitate seamless coordination and decision-making.
- Flexibility and Agility: Production planning should account for dynamic market conditions and unforeseen disruptions. Building flexibility into the planning process enables quick adjustments to production schedules, resource allocation, and inventory management. Agile methodologies and real-time data monitoring help organizations respond rapidly to changing customer demands and market fluctuations.
- Technology Integration: Leveraging advanced technology and software solutions enhances production planning efficiency. Integrated systems, such as Enterprise Resource Planning (ERP) and Advanced Planning and Scheduling (APS) software, enable real-time data visibility, automated workflows, and optimization algorithms. This integration improves accuracy, reduces manual errors, and streamlines production processes.
- Continuous Improvement and Learning: Organizations should foster a culture of continuous improvement by encouraging employees to identify and address bottlenecks, waste, and inefficiencies in the production planning process. Learning from past experiences, conducting root cause analyses, and implementing corrective actions contribute to ongoing optimization and operational excellence.
- Key Performance Indicators (KPIs): Establishing relevant KPIs allows organizations to measure and track production planning performance. KPIs such as on-time delivery, production cycle time, inventory turnover, and resource utilization provide insights into the effectiveness of production planning efforts. Regular monitoring of KPIs helps identify areas for improvement and guides decision-making.
Conclusion
In conclusion, streamlining the manufacturing production planning process is essential for organizations to achieve operational efficiency, cost-effectiveness, and customer satisfaction. From accurate forecasting to execution, every step in the production planning process plays a critical role in optimizing resources, minimizing waste, and meeting customer demands.
By implementing best practices and leveraging advanced tools and technologies, companies can overcome challenges and drive continuous improvement. Accurate demand forecasting, collaborative planning, and effective communication are key factors that contribute to successful production planning. Integrating technology, such as ERP and APS systems, enables real-time data visibility, automation, and optimization.
Lessons learned from successful companies highlight the importance of flexibility, agility, and continuous improvement. Adapting to dynamic market conditions and fostering a culture of learning and innovation are essential for staying competitive and meeting evolving customer expectations.
By monitoring key performance indicators, organizations can measure the effectiveness of their production planning efforts and identify areas for improvement. Regular evaluation and adjustment of strategies based on data-driven insights contribute to ongoing optimization and operational excellence.
In summary, by embracing the principles of accurate forecasting, efficient execution, continuous improvement, and technological integration, organizations can streamline their manufacturing production planning process, drive efficiency gains, and achieve sustainable success in today's competitive market.
How can Deskera Help You?
Deskera ERP and MRP systems help you to keep your business units organized. The system's primary functions are as follows:
- Keep track of your raw materials and final items inventories
- Control production schedules and routings
- Keep a bill of materials
- Produce thorough reports
- Make your own dashboards
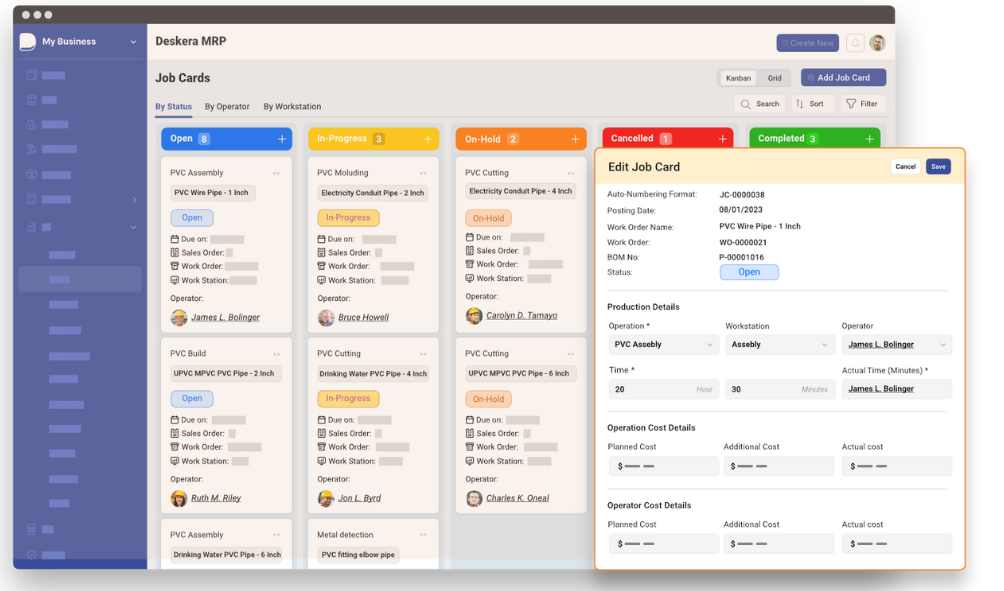
Deskera's integrated financial planning tools enable investors to better plan and track their investments. It can assist investors in making faster and more accurate decisions.
Deskera Books allows you to better manage your accounts and finances. Maintain good accounting practices by automating tasks like billing, invoicing, and payment processing.
Deskera CRM is a powerful solution that manages your sales and helps you close deals quickly. It not only enables you to perform critical tasks like lead generation via email, but it also gives you a comprehensive view of your sales funnel.
Deskera People is a straightforward tool for centralizing your human resource management functions.
Key Takeaways
- Accurate demand forecasting is crucial for effective production planning, allowing organizations to align their resources with customer demands.
- Collaborative planning and communication among different departments and stakeholders enhance coordination and ensure a shared understanding of production goals.
- Flexibility and agility in production planning enable organizations to respond swiftly to market fluctuations and unexpected disruptions.
- Technology integration, such as ERP and APS systems, improves efficiency by providing real-time data visibility, automation, and optimization.
- Continuous improvement and learning are essential for driving operational excellence in production planning processes.
- Key performance indicators (KPIs) help measure and track production planning performance, enabling organizations to identify areas for improvement.
- Lean manufacturing principles, such as waste reduction and just-in-time production, contribute to streamlined production planning.
- Six Sigma methodologies aid in reducing process variations and improving quality in production planning.
- Change management and employee engagement play a crucial role in overcoming resistance and ensuring successful implementation of new production planning practices.
- Case studies and success stories provide valuable insights and inspiration for organizations seeking to streamline their production planning processes, showcasing best practices and lessons learned from real-world examples.
Related Articles
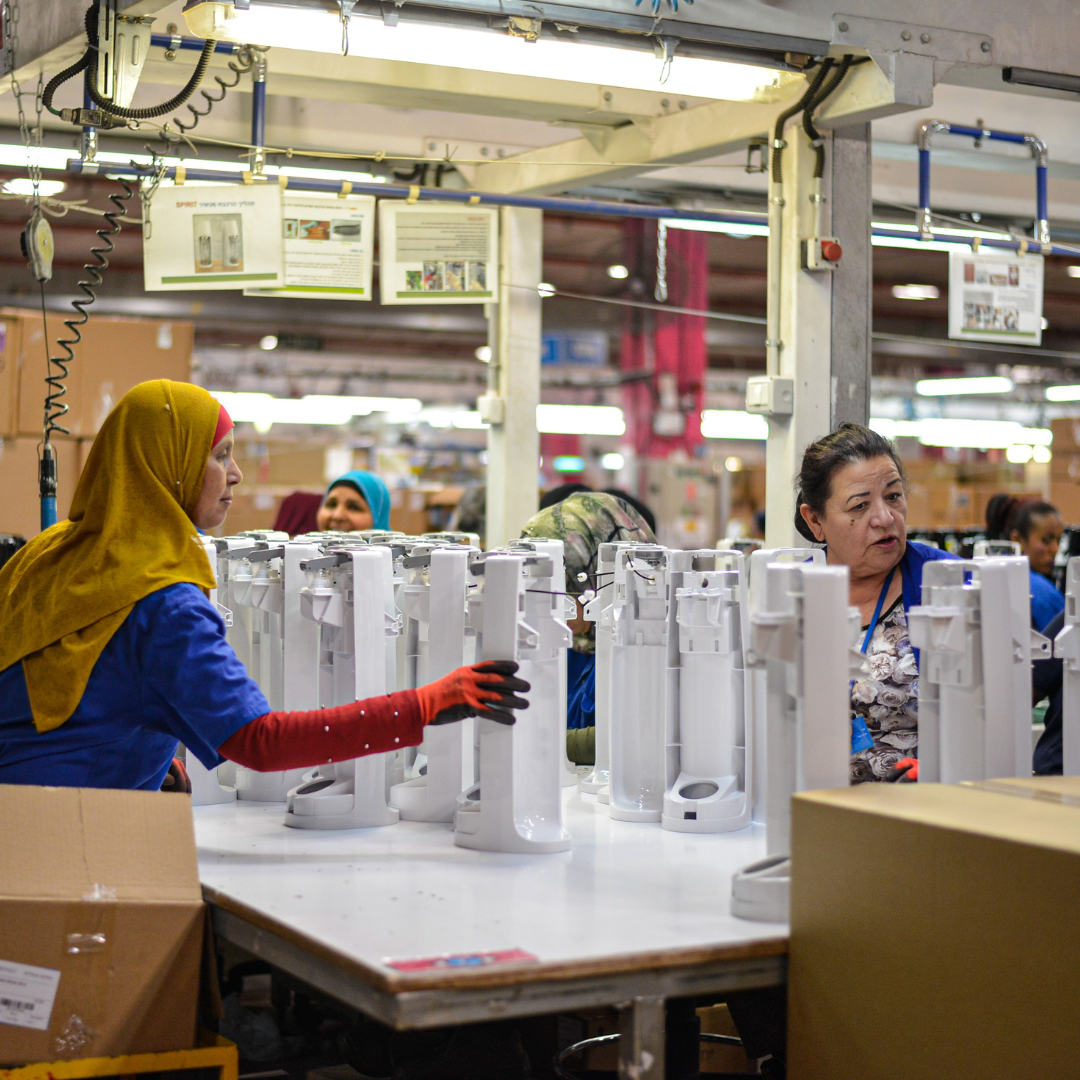
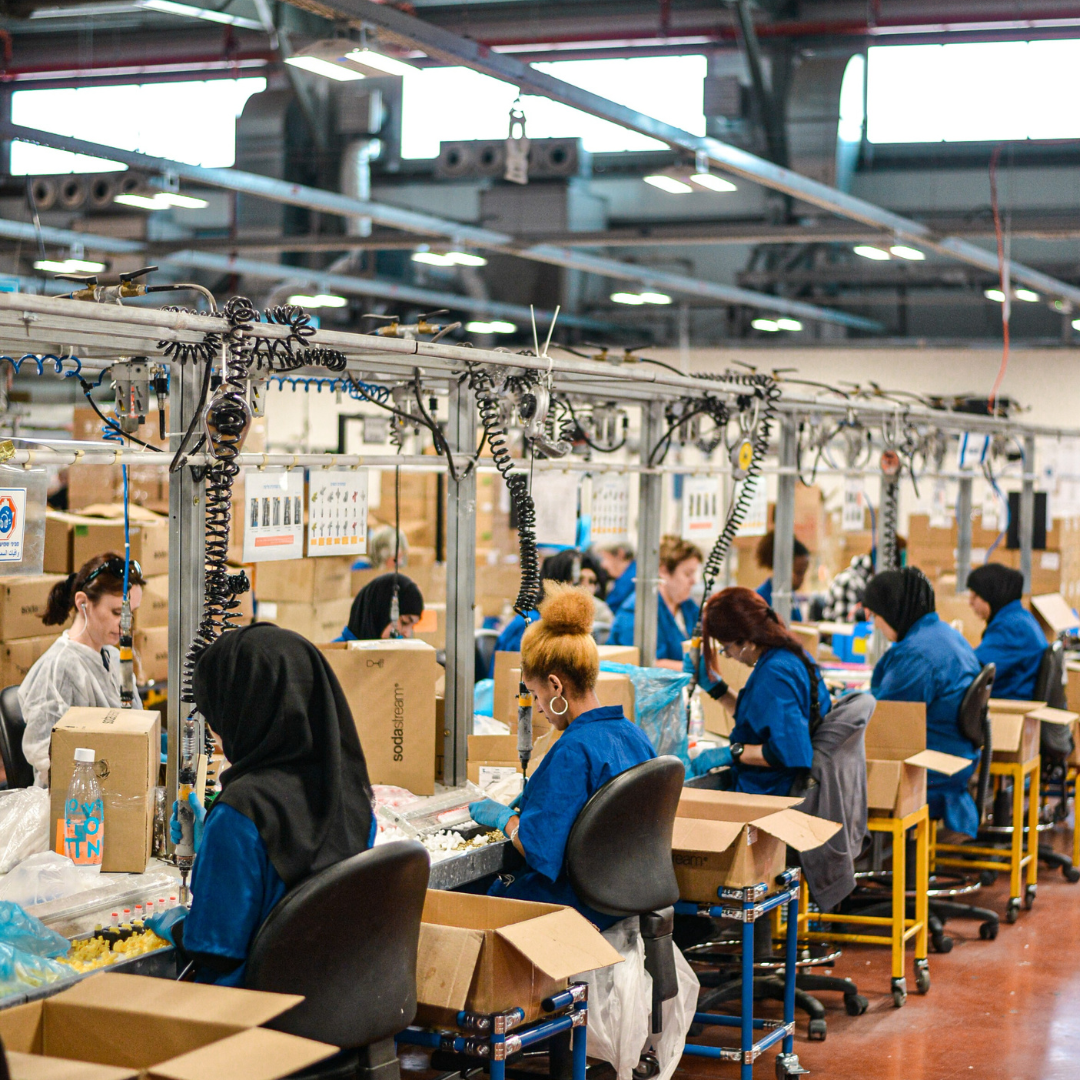
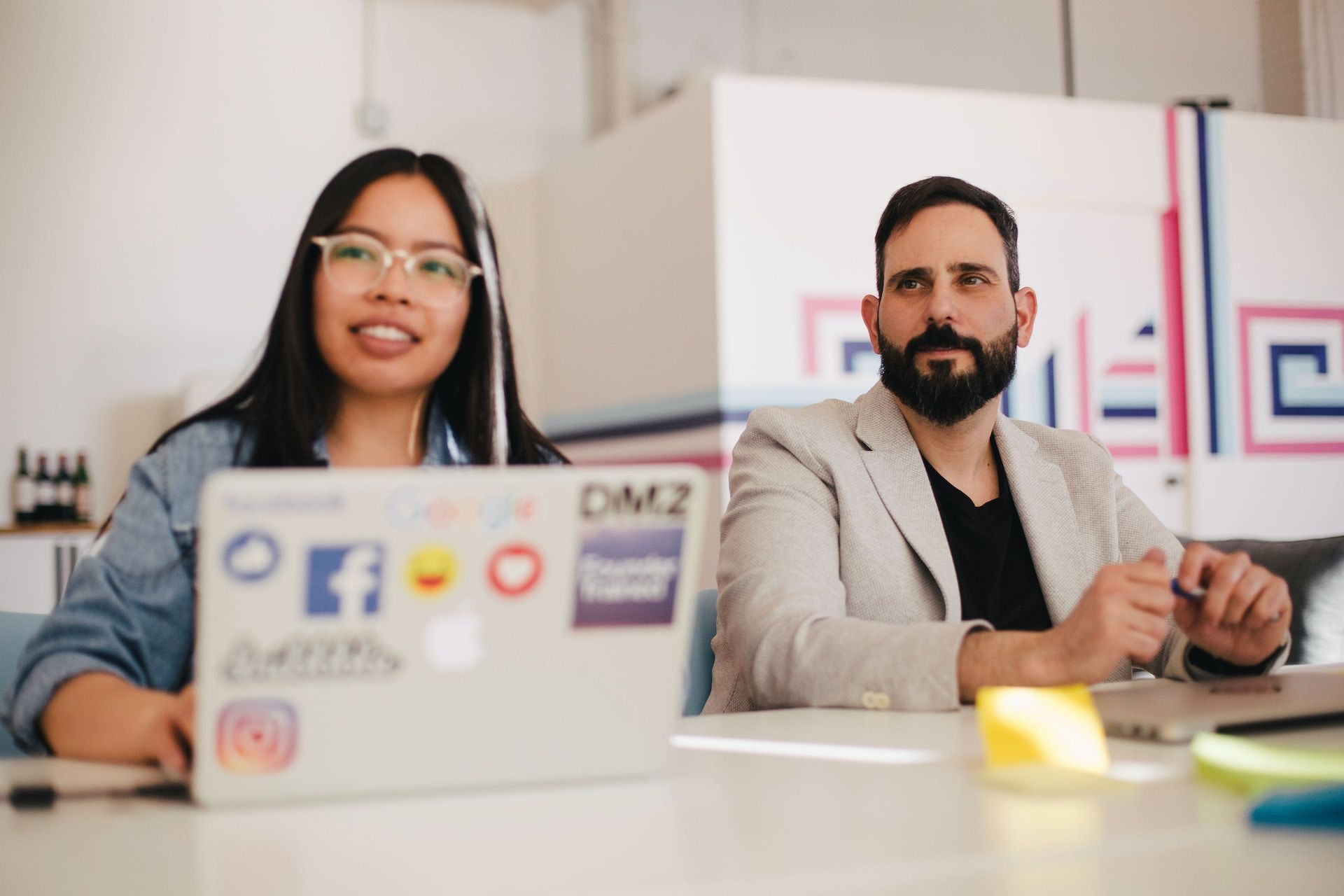
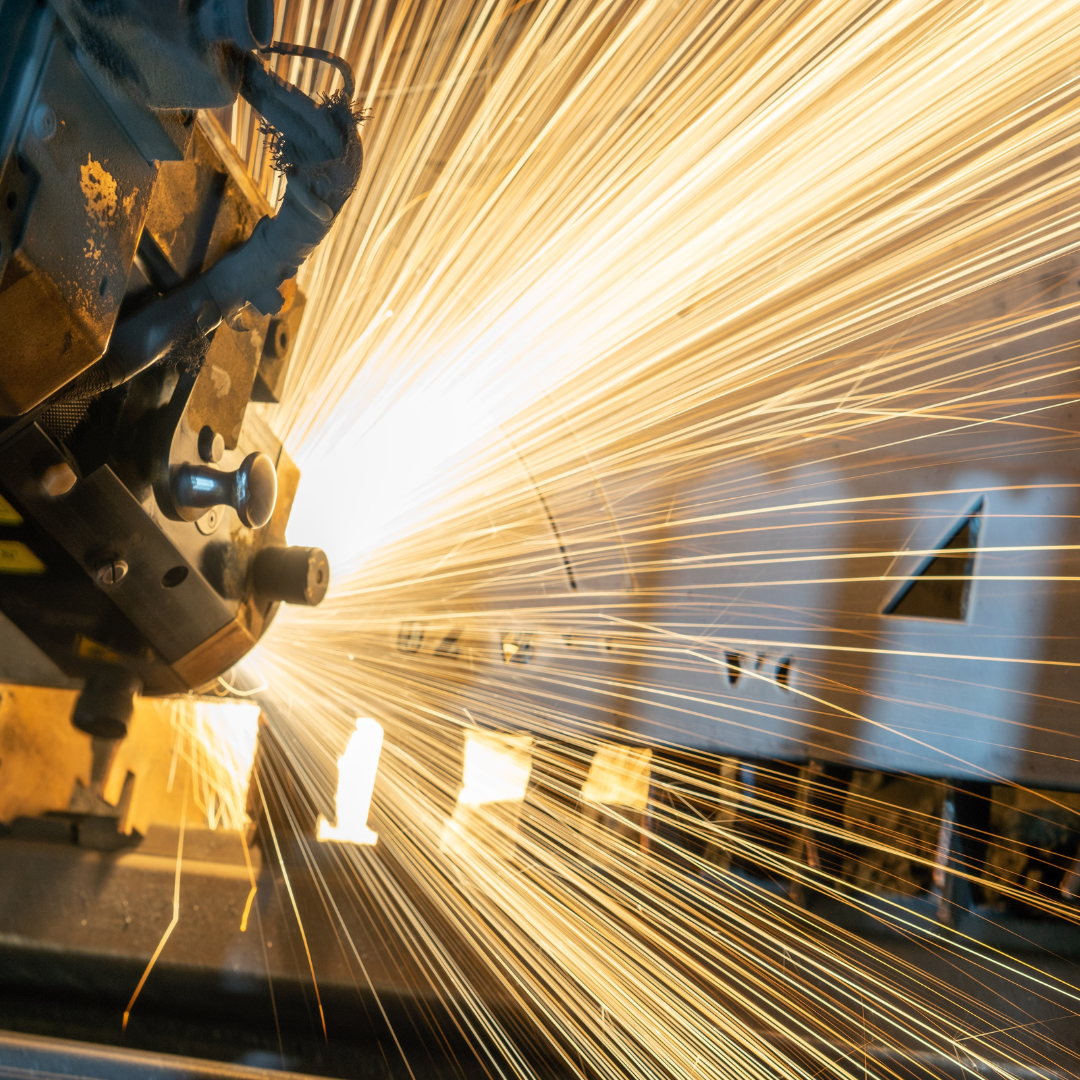