One of the factors supporting the company's success in achieving its goals is the ability to meet demand and provide satisfaction to customers. The Rough Cut Capacity Planning (RCPP) method is a method that can show a comparison between the actual capacity available and the capacity needed.
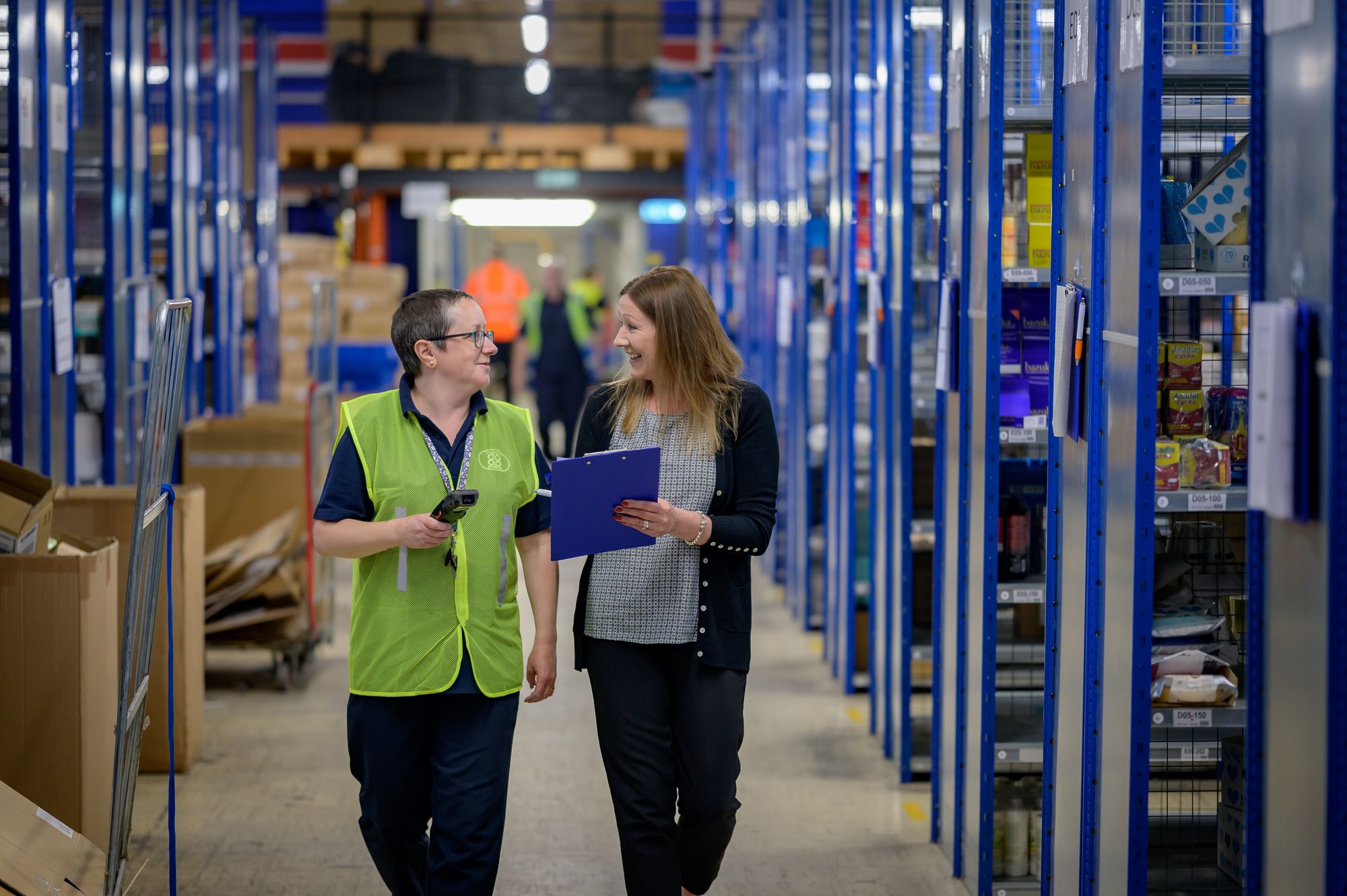
Isn’t this something that your organization must have too? Worry not because you are about to learn everything you need to know about rough-cut capacity planning. So, let’s get started!
This article covers the following:
- What is capacity planning?
- What are the types of capacity planning?
- What is rough cut capacity planning?
- What is the objective of rough-cut capacity planning?
- What are the levels of calculating rough-cut capacity planning?
- What are the three methods of rough-cut capacity planning?
- What are the benefits of rough-cut capacity planning?
- What is the downside of rough-cut capacity planning?
- When should you use rough-cut capacity planning?
- What is the difference between MPS and RCCP?
- How can Deskera assist you?
What is Capacity Planning?
Organizations utilize a capacity planning method to determine their production capacity to adapt to their products' shifting demands. In the context of capacity planning, a design capacity is an organization's maximum capability to finish a specific amount of work in a specific time.
Capacity planning is the process of balancing available resources to meet project capacity requirements or customer demand. The amount of work that can be finished in a specific length of time is referred to as capacity in project management and production.
The capacity planning process is essential in areas of project management expertise, for example,
- Resource management
- Time management
- Team management
- Work Management.
Production capacity, strategy planning, and project planning go hand in hand. Planning is the task of scheduling the team members so that the work gets completed on time.
Capacity management is not a set procedure. Because every company is distinct and demand keeps fluctuating, project managers can employ various capacity planning methodologies to respond to different conditions.
Issues in Capacity Planning
Here are some common issues of capacity planning that you must be aware of:
Data Collection
Capacity planning involves combining data from multiple sources, including internal groups such as sales, manufacturing, and finance, as well as external information about market trends.
Not all of this information may be easy to obtain. That can make it difficult to quickly build a consolidated, up-to-date view of current capacity use and determine how much capacity the company needs.
Data Quality
Data combined from multiple sources can be of inconsistent quality and in a variety of different formats. Some data may contain errors, especially if it’s been collected manually. Other information may be out of date.
Calculation Accuracy
Capacity planning can involve complex calculations that factor in materials, people, equipment, market demand forecasts, and more. Accuracy is essential to ensure the company doesn’t underestimate or overestimate the capacity it needs to meet demand. But it’s easy to make errors, especially if data is drawn from many sources and the calculations are performed manually using spreadsheets.
Collaboration
There are so many people involved in capacity planning, both internal and external, that it can be challenging to keep everyone in sync. Production teams may not be kept up to date with information about new projects and sales that affect the amount of capacity the company needs. Further adding to the challenge: Some information may need to be communicated externally to suppliers and customers.
What are the Types of Capacity Planning?
There are two types of capacity planning, long-term capacity planning and short-term capacity planning:
Long-Term Capacity Planning
In the big picture, long-term capacity planning relates to creating strategic plans for all of your main production lines. Plans developed for specific sites, technology, and the applicability of your production methods to other goods are all included in these long-term capacity plans.
Planning for future capacity is not a given. Eventually, if you find that short-term capacity plans are ineffective, it might change. When introducing a new shift pattern into your production line, which, regrettably, doesn't boost productivity long-term capacity planning would be conducted.
If you are unable to subcontract work, changing your routing manufacturer can be your best option. A long-term capacity plan to increase productivity can include redesigning the route through your factory.
Short-Term Capacity Planning
You might consider any current plans that are being carried out as part of your short-term capacity planning. Issues with short-term capacity planning include items like:
-Scheduling and planning for production
-Shift work
-Relative capacity balance
Your short-term capacity planning may cover a period of time that ranges from a few days to six months. Short-term capacity planning aims to efficiently and economically handle unanticipated demand spikes and dips.
Offering overtime to your employees is an illustration of short-term capacity planning and is a frequently used example. Since you won't have to: Overtime is a flexible and affordable solution to high demand.
What is Rough-Cut Capacity Planning?
A tool for long-term plan capacity planning is rough-cut capacity planning (RCCP/RCP). It is used to negotiate modifications to the master schedule and/or the available capacity, as well as to balance the necessary and available capacity.
Based on your RCCP analysis, adjustments can be made to either the anticipated production or the available capacity. Without completely delving into the specifics of resource management, the goal of RCCP is to gain a broad understanding of demand and capacity.
It also lists your capacity requirements to meet your training production schedule.
A more accurate estimate is determined later through capacity requirements planning (CRP) after the MPS has been used for material requirements planning (MRP).
What is the Objective of Rough-Cut Capacity Planning?
Traditionally, the general goal in RCCP is to balance the total available capacity i.e., the manufacturing capability of a production facility, with the total required capacity demanded by the MPS.
What is meant by “balance” is that an attempt is made to match the required capacity with the available capacity. Insufficient available capacity of a production facility would obviously result in an inability to fulfill the MPS.
In this case, the user may decide either to increase available capacity or, if possible, to adjust the MPS to reduce the required capacity. Excess available capacity would waste resources.
In this case, the user may decide to decrease the available capacity or adjust the MPS to increase the required capacity. Before considering known RCCP approaches, it is helpful to review basic manufacturing terminology.
When a batch of items is to be processed, the processing is typically governed by a “work order.” As is known in the art, a work order (also referred to as a “job” or a “lot”) describes a set of operations (e.g., cutting, sanding, painting) that is to be performed to process a particular item.
For instance, processing may comprise the steps necessary for generating a product from raw materials or components. A work order typically includes a due date, i.e., a time by which completion of the work order is needed.
A “work center” is a set of one or more machines having similar capabilities on which a particular operation can be completed. For example, in a semiconductor backend assembly environment, a “Wire Bond” work center may contain multiple wire bonders which come from different equipment manufacturers. Yet, they are all generally capable of completing the wire bonding operation.
The terms “work center” and “operation” are sometimes used interchangeably. The term “items” and the term “products” may be used interchangeably herein to refer to units to be processed.
What are the Levels of Calculating of Rough-Cut Capacity Planning?
There are two levels of calculating rough cut capacity planning, routing based rough-cut capacity planning and rate-based rough-cut capacity planning.
Routing-Based RCCP
Routing-based rough cut capacity planning shows your resource availability. For this, you’re going to look into the required and available capacity in hours per week per resource.
Required Hours Calculation
Calculates the required hours for each resource by taking each master schedule entry for a bill of resource item, and multiplying the master schedule quantity by the total hours on each bill of resource requirement that references the resource.
- Calculates the required date for each resource by offsetting the master schedule date by the setback days defined on the bill of resource requirement. Since capacity assumes infinite capacity, all the required hours for the resource are allocated to the required date.
- Buckets the required hours into weekly buckets.
Available Hours Calculation
Routing-based RCCP calculates available hours for a resource using the resource availability information you define in Bills of Material. You can define resources, departments, shifts, and shift calendars.
Having defined your departments, resources, and shifts, you can assign shifts to resources and resources to departments. Routing-based RCCP calculates available hours for a resource by summing the available hours for each shift that uses the resource using the following formula:
available hours = capacity units x shift hours per
day x shift days per week x efficiency x utilization
In case of 24hrs of resources:
available hours = capacity units x 24 hours per day x
workdays per week x efficiency x utilization
Capacity units represents the number of resource units available to a department. Shift hours per day and shift days per week reflect the availability times you specify for each shift. Workdays per week reflect the number of workdays in the week based on the workday calendar
Load Ratio
Routing-based RCCP calculates capacity load ratio for each resource by dividing the total required hours per week by the total available hours per week, using the following formula:
capacity load ratio = required hours / available hours
Rate-Based RCCP
This is where you measure your rough cut capacity by production lines. For this, you’ll need to figure out your required and available capacity per week per production line.
So, to quickly summarize, your rough-cut capacity planning will look into how much you need to produce, how much you can produce, and how you can find a balance between the two.
Required Rate Calculation
Rate-based RCCP uses bills of resources to determine rate-based capacity requirements.
Maximum Hourly Rate
Maximum hourly rate represents the maximum production rate for a production line across all assemblies.
Rate-based RCCP:
- Calculates the required rate for each line by taking each master schedule entry for a bill of resource item, and using the repetitive schedule allocation process to allocate the master schedule rate across individual production lines.
- Calculates the required date for each rate by offsetting the master schedule end date by the setback days defined on the bill of resource requirement. Since capacity assumes infinite capacity, all of the required rate for the production line is allocated to the required date.
- Buckets the required rates into weekly buckets.
Various Rough-Cut Capacity Planning Methods
#1 Capacity Planning Using Overall Factors (CPOF)
Future capacity requirements are calculated using previous data using capacity planning utilising overall factors (CPOF). This straightforward method examines workstation data, MPS, and production time.
Analysis of Production Capacity Planning and Control in Pt. Krakatau Wajatama using Rough Cut Capacity Planning (RCCP), a research study from the steel sector, states that "CPOF calculates work capacity at each work station in each MPS period."
#2 Bill of Labour
The bill-of-labor (BOLA) or bill-of-capacity approach to capacity planning estimates how many hours are required at each workstation to create a finished good.
The researchers advise multi-product enterprises to employ the bill-of-labor strategy. The BOLA method establishes a clear connection between the quantities in the MPS and the number of hours required to generate a unique final product at each workstation.
#3 Resource Profile Approach
The resource profile approach looks at the time it takes to complete each activity while also including lead time. This approach is more accurate because it goes beyond the workstation hours to consider resource lead times.
What are the Benefits of Rough-Cut Capacity Planning?
Here are some big benefits of rough-cut capacity planning that you don't want to miss out on, so let's take a look.
Easy Project Management
You can quickly identify which work should start first and which job you can start later because of rough-cut capacity planning. Hence you and your team make sure about your work priority. In this way, it improves your project management.
Effortless Resource Management
You can get a clear idea of the resources available and the working hours required for each process in each workstation. Hence you can quickly identify the more or less workload and adjust the capacity by increasing or decreasing the shifts and increasing the number of workstations.
Reduced Lead Time
Rough-cut capacity planning helps the manufacturer find out the issues in the manufacturing process and allows him to address the problem immediately. Hence it reduces the manufacturing lead time.
Cost Efficient
Knowing your team’s capacity can forecast how you can take on many training projects in a given period. That helps to bring down costs by reducing the waste on the training team.
Recognize Room for Improvement
It allows you to check out the training demand depending on the available resources like working hours, budget, and skills.
Better Planning
When aligning L&D to overall business objectives, capacity planning allows you to assess training demand against the supply of available resources. Those resources consist of the following:
- Employee working hours
- Budget
- Skills
It also helps to make sure your training team is supporting the organization in meeting strategic objectives.
Expect Less Stockouts
Stock-outs occur when you fail to meet customer demand. It’s no secret that customers don’t like to wait, and you being “out” of a product or service will only push them onto the next business that can meet their demand.
Thankfully, one benefit of capacity planning is that you can reduce stock-outs and even avoid them altogether. Throughout your planning process, you’ll see how the market and demand fluctuate, making you better able to predict supply and demand changes. ‘
Boost Delivery Capacity
Today’s customers want their products immediately. Quick turnaround times for deliveries can spell success for a business, while slower delivery times can lose business.
Capacity planning is a great way to gauge your delivery capacity so that you know you have the workers available to deliver your products as soon as they’re purchased, making you a contender among the market competition.
Reduced Waste
Rough-Cut Capacity Planning allows manufacturers to plan properly so that they are not wasting raw materials or products. A production manager will have a better understanding of how much product should be produced, so there is less waste in the process.
Moreover, it facilitates better planning by telling managers when training projects can be executed with minimal impact on productivity. Overall, RCCP helps eliminate waste in the production process.
It also helps identify periods where training projects are not necessary, so resources are preserved during those times to avoid interruptions or delays.
Improved Efficiency
Lastly, RCCP can boost efficiency by improving resource management. Since RCCP clearly lists available capacity planning and resources, the production demand planning process is flexible.
This can also help production managers quickly locate and resolve problem areas. As a result, the manufacturing process runs more efficiently with a decrease in lead times.
Availability of Resources and Goods
Another notable benefit of capacity planning is ensuring future availability. Before you sign a new contract or send another proposal to a potential client, capacity planning helps you know for sure that you have the workforce and resources needed to take care of your new customers, projects, and more.
Labour and Plant Availability
RCCP also allows you to identify potential upcoming labor and plant issues. Skills matrices are helpful for working out if you have the people you need to run all aspects of your production line.
Companies can get into trouble when two key players take time off at the same time, and nobody else in the firm has the skills to take their place. This can also raise the question of whether cross-training within the skills matrix is required to mitigate the situation in the future.
RCCP is also helpful for determining whether the change over time for machines is worth it. Suppose, for instance, you are a pie brand, and you make two products: a standard meat and potato and a premium version.
Ideally, after finishing the value run, you’d like to adjust your production line to create packaging that reflects the premium line. However, RCCP might tell you that the costs of doing so outweigh the benefits.
For instance, switching to premium pie production might actually cost you more money than it will generate. So the profitable decision might be to sell premium products in regular packaging to retailers at your cost.
Space Availability
Lastly, RCCP comes in handy when planning space. For instance, you might notice that you have the potential to make a large number of sales in the coming months. Perhaps consumer tastes are changing, and a spike in demand is imminent.
RCCP can help by showing you whether you have shelving space to store all the additional goods in your warehouse. You might need to rent temporary storage or decide if it’s worth investing capital in a brand-new distribution center.
You can also use it for scenario planning. For instance, you can see what might happen to your space availability if you change your stocking strategy temporarily.
What is the Downside of Rough-Cut Capacity Planning?
Every coin has two sides; similarly, like the many benefits of rough-cut planning, there are also a few disadvantages that you must also make a note of. Let’s take a look!
Time Consuming
This depends on the size of the organization. And luckily, nowadays, you have many different planning tools available. So you can speed up and simplify project planning and capacity planning.
Updating the Schedules on Time
Project managers and planners must consider updating the schedule as a standard part of their tasks. So it is important that the planning takes place structurally and that the planning is kept up to date.
Quality of Data
RCCP depends on data, and much of that data collection requires manual gathering and reconciliation. This results in more time spent finding the data you need than analyzing it.
One way to overcome this obstacle is to export data from the appropriate sources and consolidate it into a single solution that allows for dynamic updates. This single source of truth provides a solitary access point to up-to-date information.
Need for Accurate Calculation
RCCP relies on several calculations that depend on accurate data. Any inaccurate data or calculation error risks creating problems with the entire RCCP process. To reduce the risk of error, maintain all calculations, data, and analytics in a single location.
Weak Communication
RCCP touches all areas of an organization. Geographical and functional separation adds to the complexity of capacity planning. To overcome any communication issues, choose a single location for planning. This allows for data and analysis transparency, confirmation of data integrity, and cross-departmental conversations.
When Should You Use Rough-Cut Capacity Planning?
RCCP is an ideal approach to scheduling where:
- The route can’t fully describe the production processes of a product entered into the system due to the complexity of defining each task in the process – e.g., typically in the case of a prototype or new fabrication
- The routes don’t contain enough information on the order of the tasks in the manufacturing processes and the implications of these – e.g., there is no interop time in the route to move material from one operation to the next.
In the above scenarios, the following actions need to be undertaken so the rough-cut capacity planner can understand what time values are attached to each task.
- Recording the expected time for each process in a job in its route records
- On the assumption that each component in the assembly has a linear production route, the RCCP then works out, from the delivery date of the works order, the last start date of each operation
- If the product is an assembly as opposed to a flat item, the RCCP starts from the final assembly, works out the start date of its works order, goes to the next level and does the same, and so on through the whole bill of materials (BOM)
- For that complete job, one ends up with a number of operations across every level of the BOM, each with their own last-start dates
- If an item in a job does not have a linear route, but the planner still records the time for each operation, one can intervene and manually override the start dates
- A lead time can also be used to calculate the start dates of the works order within a BOM
What is the Difference Between Rough-Cut Capacity Planning and Capacity Requirement Planning?
The process of determining a company's available production capacity and whether it can reach its production objectives is known as Capacity Requirement Planning (CRP).
The CRP technique evaluates the business's anticipated manufacturing schedule first. In order to determine if the current capacity can successfully satisfy the current production schedule, capacity needs planning to compare this schedule to the company's real production capabilities.
RCCP is to be used in the initial planning stages for master production schedules while on the other hand, while CRP is to be used as a near-final capacity check on the master schedule. This helps you achieve more accurate information as compared to RCCP.
Organizations are finding it harder and harder to predict demand as data and information proliferate. Rough-cut capacity planning has become popular among organizations as a result of its effectiveness in helping them meet client orders on time without compromising quality or going over budget.
Making sure there are no production bottlenecks in place before they can help prevent future expansion in addition to addressing immediate needs. RCCP in manufacturing provides a methodology that combines these two aspects with cost-effective tools for optimizing productivity levels across your organization’s operations.
Although the rough-cut capacity planning approach has a number of benefits and drawbacks, it is regarded as a secure starting point. To make it better, you can always go for an all-in-one ERP solution like Deskera. Let’s find out how Deskera can assist you.
How Can Deskera Assist You?
Enterprise Resource Planning (ERP) solution helps businesses create effective capacity plans based on analysis of production capacity. One such ERP solution is Deskera ERP.
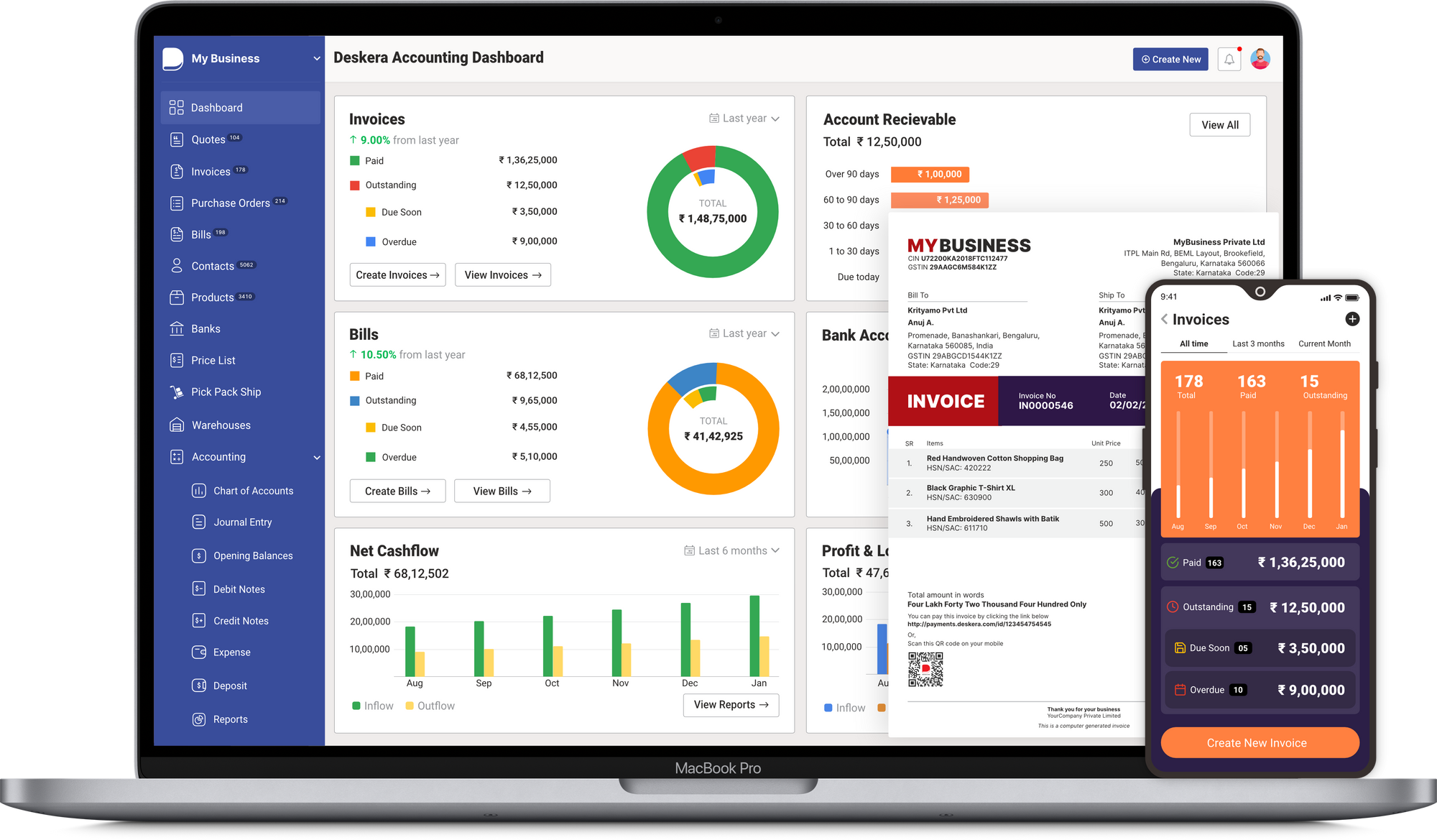
It generates reports necessary for both short- and long-term capacity planning, helping to predict future needs based on the data available. Find out more about how Deskera can make your business easy to run by taking a free trial.
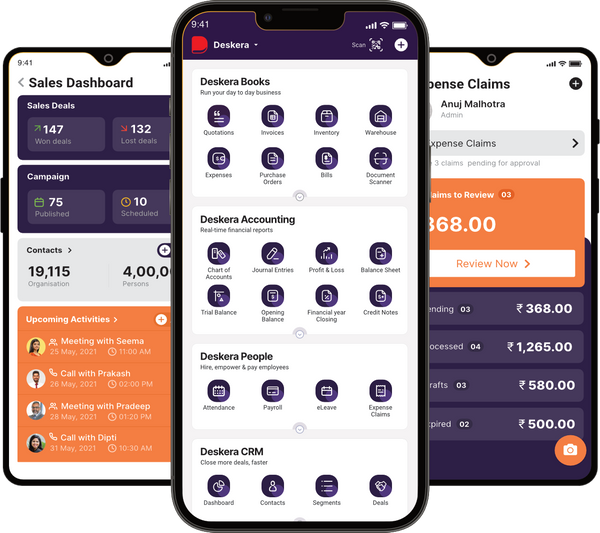
Key Takeaways
- Capacity planning is the process of balancing available resources to meet project capacity requirements or customer demand.
- Long-term capacity planning relates to creating strategic plans for all of your main production lines.
- You might consider any current plans that are being carried out as part of your short-term capacity planning.
- A tool for long-term plan capacity planning is rough-cut capacity planning (RCCP/RCP).
- The general goal of RCCP is to balance the total available capacity.
- RCCP is to be used in the initial planning stages for master production schedules while the other hand, while CRP is to be used as a near-final capacity check on the master schedule
- Enterprise Resource Planning (ERP) solution helps businesses create effective capacity plans based on analysis of production capacity.
Related Articles:
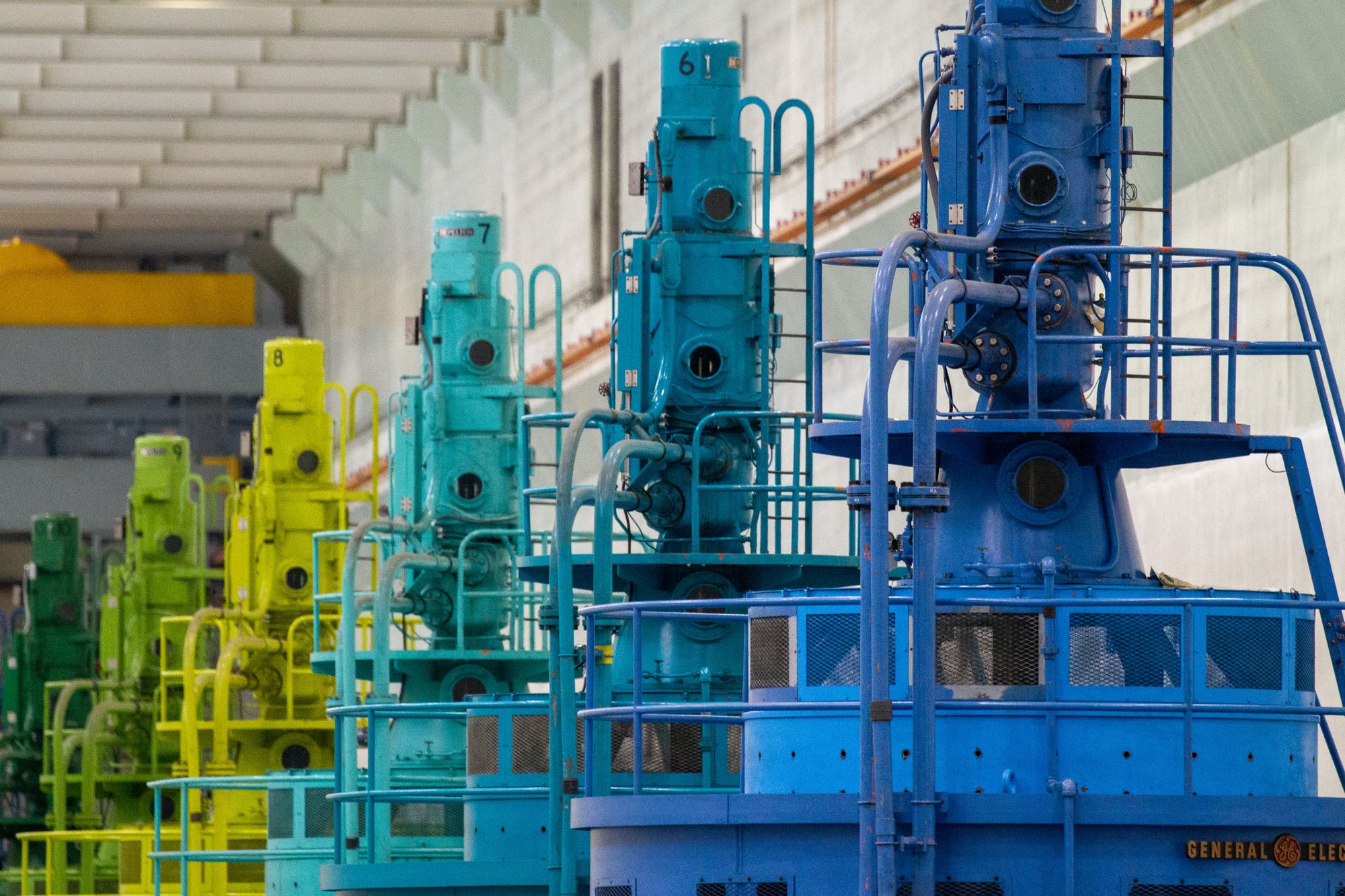
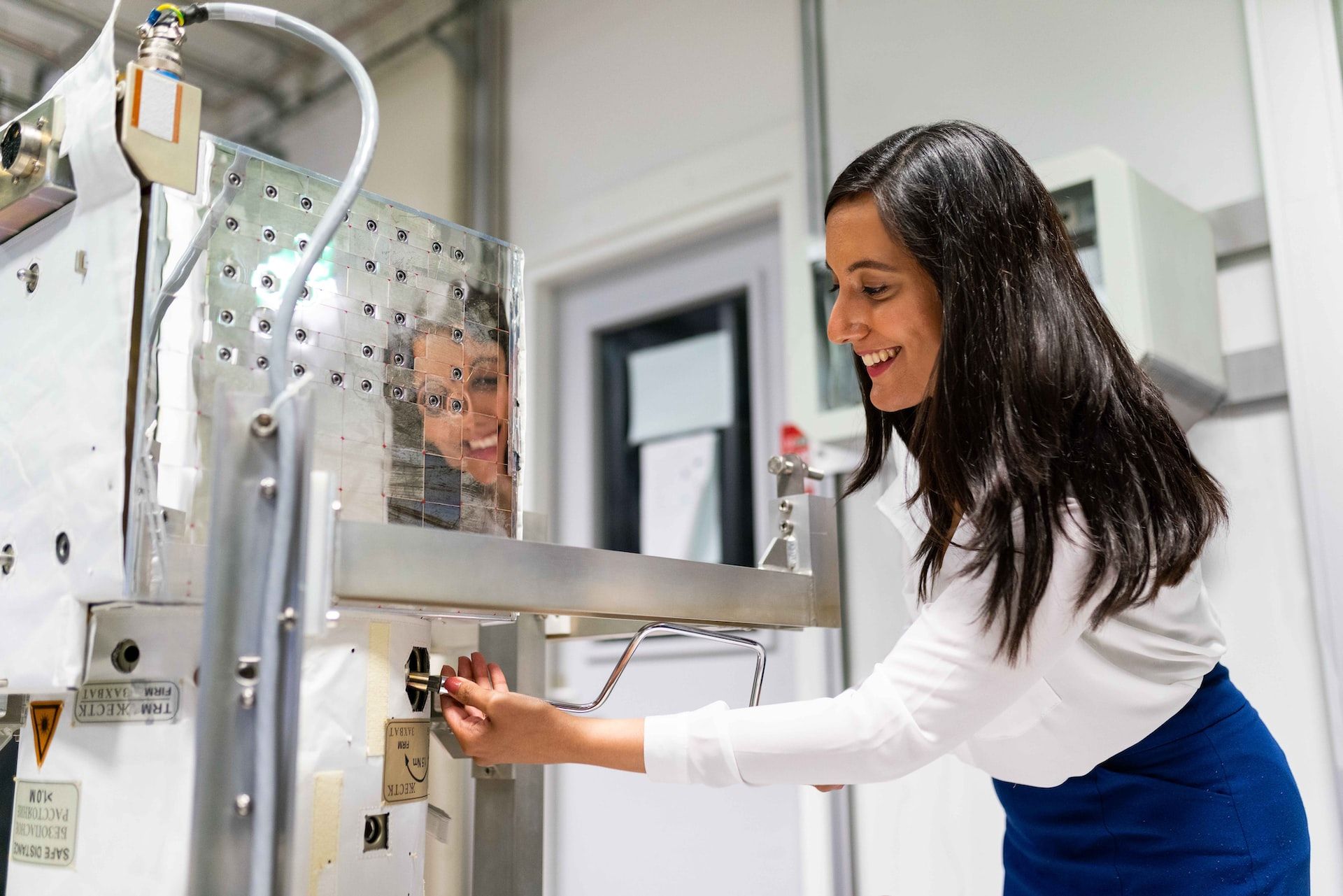
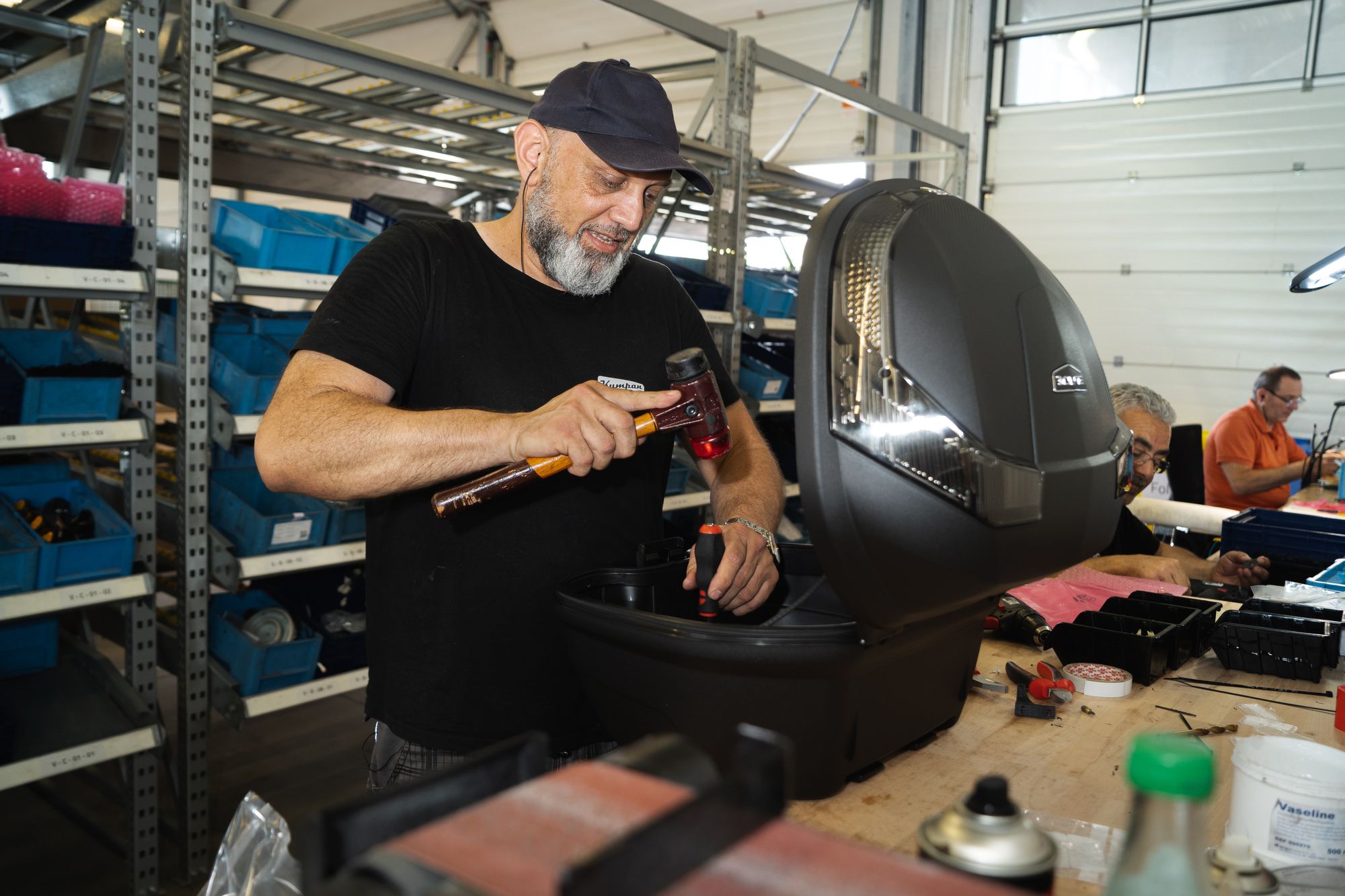
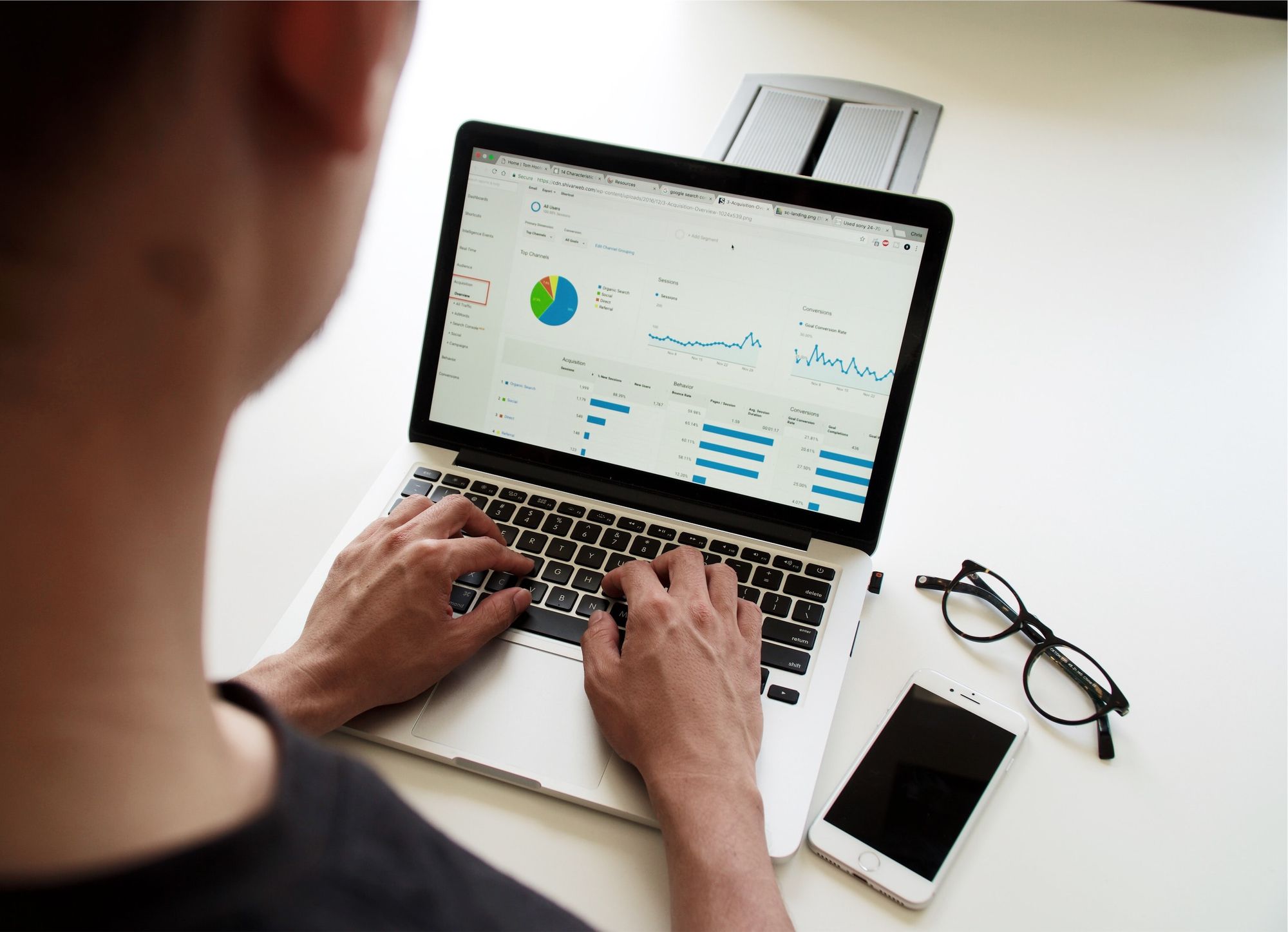