Have you ever wondered why certain problems keep recurring in your business despite repeated efforts to fix them? The answer lies in addressing not just the symptoms but the root causes.
Root Cause Analysis (RCA) is a systematic approach to uncovering the fundamental reasons behind problems, allowing businesses to implement solutions that prevent them from reoccurring. Whether it’s streamlining operations or improving product quality, mastering RCA is a vital skill for sustainable problem-solving.
RCA goes beyond quick fixes by focusing on the "why" behind every issue. It empowers businesses to ask critical questions, analyze processes, and find solutions that are both effective and lasting.
This approach not only resolves current challenges but also strengthens your organization’s ability to prevent future issues, fostering continuous improvement and operational excellence. From manufacturing to customer service, RCA is a versatile tool that delivers measurable results.
Deskera ERP can be a game-changer when it comes to implementing RCA in your business. With features like real-time data analysis, automated reporting, and process monitoring, Deskera ERP enables businesses to pinpoint root causes efficiently.
Its user-friendly dashboards and AI-driven insights provide a clear view of operations, making it easier to identify trends, spot bottlenecks, and act on findings. By integrating RCA into your workflows through Deskera, you can drive smarter decisions and long-term growth.
In this blog, we’ll guide you through the essentials of Root Cause Analysis, from its methodologies to its applications in modern businesses. Let’s explore how RCA can transform the way you address challenges and set the foundation for a culture of continuous improvement.
What is Root Cause Analysis?
Root Cause Analysis (RCA) is a systematic process aimed at identifying the fundamental causes of problems, issues, or incidents within an organization. Rather than focusing on immediate symptoms, RCA digs deeper to uncover the underlying factors responsible for the problem. By addressing these root causes, organizations can implement long-term solutions that prevent recurrence, enhance operational efficiency, and foster a proactive problem-solving culture.
Unlike reactive approaches that focus on "putting out fires," RCA prioritizes prevention and sustainability. It relies on a combination of principles, methodologies, and techniques to trace problems to their origins. Common tools such as the 5 Whys, Fishbone Diagram, and Fault Tree Analysis help organizations analyze the causal factors behind events, revealing where systems, processes, or procedures may have failed.
RCA is applicable across industries and scenarios, whether it's investigating machinery failure in manufacturing, analyzing service disruptions in IT systems, or addressing safety incidents in healthcare. It connects seemingly isolated events into a meaningful sequence, helping organizations understand the "how," "why," and "when" of the problem. For example, an RCA might explain why a manufacturing machine repeatedly breaks down or why a web application experiences downtime.
By uncovering the true source of an issue, RCA enables organizations to identify corrective actions and implement solutions that ensure long-term improvement. This proactive approach makes RCA an essential component of quality management, reducing operational disruptions and improving overall business outcomes.
Core Principles of Root Cause Analysis
Root Cause Analysis (RCA) is most effective when guided by a set of core principles that ensure a thorough and actionable approach to problem-solving. These principles form the foundation of a successful RCA process, enabling organizations to uncover and address the true causes of issues.
Focus on Root Causes, Not Just Symptoms
RCA prioritizes identifying the underlying reasons for a problem rather than addressing surface-level symptoms. While treating symptoms may provide short-term relief, only by resolving the root causes can organizations prevent the issue from recurring and ensure long-term stability.
Emphasize "How" and "Why," Not "Who"
Effective RCA shifts the focus away from assigning blame to individuals and instead emphasizes understanding how and why a problem occurred. This fosters a culture of learning and improvement rather than fear or defensiveness, encouraging collaborative problem-solving.
Base Findings on Concrete Cause-and-Effect Evidence
A systematic and methodical approach is essential for RCA. Analysts should rely on verifiable cause-and-effect evidence to support their conclusions. This ensures that the identified root causes are accurate and actionable.
Acknowledge the Possibility of Multiple Root Causes
Many problems arise from a combination of factors rather than a single cause. RCA recognizes this complexity, ensuring that all contributing factors are thoroughly explored and addressed.
Develop Actionable Solutions
RCA is not just about identifying root causes; it also aims to create informed and practical solutions to eliminate or mitigate them. This includes considering preventive measures to avoid recurrence and sharing insights to replicate successful outcomes elsewhere.
Take a Holistic and Preventive Approach
RCA encourages a comprehensive analysis that considers the broader context of the problem. By looking at processes, systems, and environments, RCA helps identify preventive measures that improve organizational efficiency and reduce future risks.
By adhering to these principles, RCA not only resolves specific issues but also drives continuous improvement, creating a more resilient and proactive organizational framework.
Key Steps in Root Cause Analysis
Root Cause Analysis isn’t just about fixing problems; it’s about creating a culture that actively seeks out inefficiencies, learns from mistakes, and strives for continuous improvement.
By following these insights, you not only address the immediate issue but also pave the way for a more resilient, adaptable, and innovative organization. Make RCA a part of your company’s DNA, and it will yield lasting improvements that positively impact all facets of the business.
1. Define the Problem with Precision
A successful RCA begins with a crystal-clear understanding of the problem at hand. Problems can often be perceived differently by various stakeholders, so it’s crucial to align on a common definition. Instead of focusing on abstract issues like “low productivity,” refine the problem to be specific and measurable, such as “increased production downtime due to machine failures.”
By defining the problem with clarity, you create a roadmap for your RCA and ensure that every team member is on the same page. Engage with key stakeholders to explore their perspectives and ensure the problem is accurately scoped.
Insight: Consider incorporating Key Performance Indicators (KPIs) or benchmarks that allow you to quantify the issue and measure the effectiveness of future solutions.
2. Collect Data: The Backbone of Your Analysis
Data collection forms the foundation of a robust RCA. Both qualitative insights and quantitative data are crucial in understanding the full scope of the problem. Go beyond simply gathering data — ensure that you are collecting evidence that answers the right questions. Track historical performance data, observe patterns, and interview key individuals who are most affected by the issue.
Insight: Leverage advanced analytics or business intelligence tools to aggregate data from various sources. This allows you to spot trends and hidden correlations that could point to the root cause. Additionally, employing tools like sentiment analysis (in case of employee issues) can add nuance to the data you collect.
3. Identify Causal Factors: Connecting the Dots
Once you have a comprehensive set of data, begin identifying potential causal factors. These are the conditions or events that contribute to the problem but are not necessarily the root causes. Often, these factors are interconnected, and understanding their relationships helps you avoid superficial conclusions.
Insight: Use frameworks like the Fishbone Diagram (Ishikawa) or Failure Mode and Effects Analysis (FMEA) to visually map out causal factors. This method helps break down complex issues into manageable categories and can highlight systemic problems that may otherwise be overlooked.
4. Sequence Causal Factors: Chronology is Key
Next, map out the sequence of events leading to the problem using flow charts or timeline diagrams. This helps visualize how different causal factors are interrelated over time. Recognizing patterns and sequences will allow you to pinpoint exactly where things went wrong, offering deeper insight into the failure points.
Insight: Think of this as a narrative. Each causal factor represents a chapter in a story — understanding the order and context is crucial to uncovering the "plot twist" that led to the current situation. Tools like process maps or value stream maps are particularly useful in identifying process inefficiencies.
5. Identify the Root Cause(s): Getting to the Core
Now, it’s time to dig deeper and ask, "What is the fundamental cause?" This step involves systematically ruling out less significant factors and focusing on the underlying issue. Keep an open mind during this phase — often, the root cause may not be immediately obvious, and multiple layers may need to be peeled back.
Insight: Don’t just rely on surface-level conclusions. The 5 Whys technique encourages iterative questioning until the actual issue is found. Additionally, consider conducting Impact Analysis to evaluate how each potential cause will affect the organization long-term, helping prioritize the most critical issues.
6. Develop and Implement Solutions: From Insight to Action
Once the root cause(s) are identified, the next step is developing solutions. The solutions should not just address the symptoms but eliminate the root causes entirely. Create detailed action plans, outline necessary resources, and assign ownership. Keep in mind that implementing change requires a structured approach, considering potential roadblocks, resource limitations, and stakeholder buy-in.
Insight: Solutions should be SMART — Specific, Measurable, Achievable, Relevant, and Time-bound. Furthermore, consider employing Lean or Six Sigma methodologies to improve processes systematically. Additionally, solutions should not be a "one-size-fits-all" approach — tailor the corrective actions to different departments, teams, or systems to ensure maximum impact.
7. Monitor and Evaluate: Continuous Improvement
Implementing solutions is just one part of the equation; the real test is in evaluating their effectiveness over time. Constant monitoring and periodic evaluations will ensure that the problem doesn’t reoccur. Establish feedback loops where team members can report progress and new challenges, allowing you to make real-time adjustments to the action plan.
Insight: Use Kaizen (continuous improvement) principles to instill a culture where problem-solving is an ongoing, iterative process. Implement regular reviews (weekly or monthly) and track KPIs to measure the long-term impact of your solutions. This will ensure that your improvements not only stick but also adapt to evolving business conditions.
8. Foster Organizational Learning and Knowledge Sharing
Root cause analysis should not be a one-time effort. It should serve as a learning process for the entire organization. After resolving the issue, take the time to document the findings, solutions, and any lessons learned during the process. This knowledge should be shared across teams to prevent similar problems from emerging elsewhere in the organization.
Insight: Create a knowledge base or repository where RCA findings are stored for future reference. This can include templates, case studies, and best practices to guide teams through future problem-solving processes. Encourage cross-functional collaboration so that RCA insights are disseminated throughout the organization.
9. Align Root Cause Analysis with Strategic Goals
Lastly, align your RCA efforts with your broader organizational strategy. If you are solving operational problems, ensure the solutions also support long-term goals such as customer satisfaction, profitability, and sustainability. By keeping the bigger picture in mind, you ensure that the corrective actions you take today will contribute to the organization’s vision for tomorrow.
Insight: Consider integrating RCA into your strategic planning framework. Use it to inform decision-making around process optimization, resource allocation, and risk management. This ensures RCA becomes not just a reactive tool but a proactive part of your organizational strategy.
When to Perform a Root Cause Analysis
Root Cause Analysis (RCA) is a powerful tool for identifying and addressing the underlying causes of issues within an organization. Knowing when to perform an RCA is critical to ensure that time, resources, and effort are invested effectively. Here are some key situations where performing an RCA is essential:
1. Recurring Problems
If an issue or problem keeps reappearing despite efforts to fix it, it’s a clear sign that the solution has only addressed the symptoms, not the root cause. Performing an RCA will help identify the fundamental cause, ensuring a permanent resolution.
Example: If machinery breakdowns occur repeatedly despite maintenance, an RCA can help pinpoint whether the issue is related to training, equipment quality, or process inefficiencies.
2. Decreased Performance or Productivity
When there is a noticeable drop in performance, efficiency, or productivity — whether in sales, manufacturing, customer service, or any other department — an RCA should be initiated. Understanding why key metrics have shifted can help address any gaps or obstacles hindering performance.
Example: A factory sees a sudden drop in production output. An RCA would help determine whether it's due to machine malfunctions, staffing issues, or process inefficiencies.
3. Unexpected Failures or Accidents
In the event of a failure, accident, or safety incident, an RCA is crucial to uncover the contributing factors. This helps organizations prevent future occurrences by addressing not just the immediate cause but any underlying systemic issues.
Example: A safety breach in the workplace requires an RCA to assess whether it was caused by human error, equipment failure, or a failure to follow safety protocols.
4. Quality Issues or Customer Complaints
When customers report consistent quality issues or dissatisfaction, it’s time to investigate the root causes. RCA helps businesses uncover issues in production processes, supplier quality, or customer service that might be leading to these complaints.
Example: A company receives multiple complaints about defects in their product packaging. An RCA could reveal whether the problem lies in the design, materials, or manufacturing process.
5. Significant Changes or Disruptions
When introducing new processes, systems, or technologies, performance disruptions may arise. An RCA helps ensure these transitions happen smoothly by identifying early signs of issues and allowing proactive adjustments.
Example: After implementing new software, employees face frequent issues with system downtime. An RCA would help uncover whether the issue is with the software, employee training, or integration with existing systems.
6. Underperformance of New Initiatives
If a new project, product, or initiative fails to meet expectations, an RCA helps determine why it did not succeed. This enables teams to adjust strategies and avoid repeating the same mistakes.
Example: A new marketing campaign underperforms in terms of engagement. RCA would help identify whether the problem lies in targeting, content strategy, or campaign execution.
7. Compliance and Regulatory Issues
In highly regulated industries, an RCA is essential when compliance is at risk or regulations are violated. By identifying the root cause of non-compliance, organizations can take corrective action and avoid future legal or regulatory issues.
Example: A company faces a penalty for failing to meet environmental standards. RCA could determine whether the root cause is a process lapse, employee negligence, or inadequate equipment.
8. Cost Overruns or Budget Issues
When projects consistently exceed their budgets or timelines, an RCA can uncover why this is happening and identify inefficiencies, poor planning, or hidden costs.
Example: A construction project consistently exceeds its budget. An RCA might uncover issues like mismanagement of resources, delays in procurement, or unforeseen operational hurdles.
Root Cause Analysis Methodologies
Root cause analysis (RCA) is a systematic process used to identify the underlying causes of problems or issues within an organization. While all RCAs follow similar steps, various methodologies can be used to collect data and uncover the root cause effectively. Often, organizations choose a specific method and complement it with tools such as templates or specialized software to facilitate the process.
5 Whys
The 5 Whys technique is based on the principle that asking "Why?" repeatedly helps uncover the root cause of an issue. By questioning the problem at hand, problem solvers are encouraged to dig deeper rather than making assumptions. While three questions may suffice for some cases, more complex problems may require dozens of inquiries. The goal of this method is to continue asking questions until the true cause is identified.
Failure Mode and Effects Analysis (FMEA)
FMEA is a comprehensive approach that systematically identifies potential failures within a system or process and evaluates the impact of each failure. This method is similar to risk analysis, where all possible failure points are considered, and preventive actions are taken to address the most critical root causes likely to lead to problems.
Pareto Chart
Pareto charts combine bar charts and line graphs to highlight the frequency of different root causes. By displaying causes in descending order of occurrence, organizations can focus on addressing the most frequent issues first. The chart’s structure helps teams identify and target the most impactful causes, ultimately providing the greatest benefit to the business.
Impact Analysis
Impact analysis assesses both the positive and negative outcomes of potential root causes, helping organizations understand how each issue affects operations. This method provides a broader view of consequences, guiding the team to focus on solutions that offer the most significant benefits.
Change Analysis
Change analysis is useful when there has been a significant shift in a process or system’s performance. This method involves reviewing how factors such as personnel, data, infrastructure, or information may have evolved over time, helping to pinpoint the factors that caused the change in performance.
Event Analysis
Often employed for investigating major incidents, event analysis focuses on tracing the sequence of events that led to a single, significant problem, such as an accident or disaster. The process involves gathering evidence quickly and thoroughly to reconstruct the event timeline, which then aids in identifying both direct and contributing causes.
Causal Factor Tree Analysis
Causal factor tree analysis visually displays the various actions, decisions, or events that contributed to a problem using a tree diagram. This method helps organizations map out the causal chain leading to an issue, enabling a clearer understanding of the problem’s origins.
Ishikawa Diagram
Also known as the Fishbone diagram, the Ishikawa diagram is a visual representation of cause-and-effect relationships. It categorizes potential causes into various subgroups, making it easier to analyze the various contributing factors surrounding an issue.
DMAIC
DMAIC stands for Define, Measure, Analyze, Improve, and Control. This methodology is data-driven and is often used within the Six Sigma framework to improve processes. It provides a structured approach to solving problems by first defining the issue, measuring its impact, analyzing the root cause, implementing improvements, and controlling the new processes to maintain efficiency.
Kepner-Tregoe’s Root Cause Analysis
This RCA methodology follows a four-step problem-solving process, starting with a situation analysis, followed by problem analysis, solution analysis, and concluding with a potential problem analysis. This systematic approach helps organizations make informed decisions based on thorough analysis.
Fault Tree Analysis (FTA)
FTA uses logic diagrams to represent the relationships between different causes and their effects, helping organizations visualize how various factors contribute to a problem. This method allows teams to map out causal relationships in a structured manner using Boolean logic.
Barrier Analysis
Barrier analysis emphasizes the importance of protective measures to prevent issues. This RCA methodology examines the absence of proper barriers that could have prevented a problem and recommends solutions to implement barriers that will prevent similar issues from recurring. It is frequently used in risk management to enhance safety and operational stability.
Benefits of Mastering Root Cause Analysis (RCA)
Root Cause Analysis (RCA) is more than just a problem-solving tool; it is a comprehensive approach that drives continuous improvement, boosts productivity, and minimizes risks. By mastering RCA, organizations can achieve long-term success across various aspects of their operations.
Below are the key benefits of incorporating RCA into your business processes:
1. Continuous Improvement
RCA is an iterative process designed not only to resolve immediate issues but also to enhance overall system performance over time. By addressing the root cause, organizations can avoid recurring problems and foster a culture of continuous improvement. This empowers teams to refine processes, optimize operations, and stay adaptable to changing circumstances.
Benefit: RCA helps create long-term improvements in quality, efficiency, and responsiveness, driving progress across the entire organization.
2. Increased Productivity
When issues are left unresolved or inadequately addressed, they can lead to downtime, delays, and inefficiencies. RCA directly targets the source of these issues, preventing disruptions that affect employee focus and morale. By eliminating recurring problems, employees can redirect their efforts towards more critical tasks, improving overall productivity.
Benefit: A reduction in operational bottlenecks and downtime means employees have more bandwidth to focus on strategic activities that enhance business growth.
3. Reduced Costs
Unaddressed problems often lead to repeated repairs, increased maintenance costs, and wasted resources. For instance, recurring equipment breakdowns, software malfunctions, or workflow inefficiencies can incur significant expenses. RCA identifies the root cause, eliminating the need for frequent fixes, resulting in long-term cost savings.
Benefit: By addressing issues at their source, businesses can avoid the ongoing costs of repeated troubleshooting and repairs, improving financial efficiency.
4. Better Defect Detection
Product defects and service quality issues often stem from underlying operational problems that are overlooked. RCA helps detect these issues early, enabling businesses to address them before they negatively impact the end product or customer experience. Early intervention protects the company from costly product recalls, reputational damage, and lost revenue.
Benefit: Proactively tackling defects ensures high-quality products and services, preserving brand reputation and customer trust.
5. Reduced Risks
RCA is essential for mitigating risks related to safety, compliance, and operational failure. Identifying and correcting root causes of safety hazards, equipment malfunctions, or system failures leads to safer working environments and fewer risks to employees and the business.
Benefit: A more secure work environment helps to avoid accidents, regulatory fines, and the negative impact on employee well-being.
6. Optimization of Systems and Processes
RCA not only helps identify failures but also provides valuable insights into how systems and processes can be optimized. This continuous refinement of operations ensures that businesses remain competitive and efficient. Over time, businesses can scale their processes to meet the demands of growth.
Benefit: By improving system design and operation, organizations can unlock better performance, adaptability, and scalability.
7. Prevention of Recurring Issues
One of the most significant advantages of RCA is its ability to prevent the same or similar problems from reoccurring. Once the root cause is identified and corrected, organizations can implement strategies to avoid future incidents, ensuring long-term stability and reliability.
Benefit: Reducing recurring issues results in more reliable operations and saves time and resources, leading to smoother daily workflows.
8. Improved Customer Service and Client Satisfaction
Addressing root causes enables businesses to respond to customer issues more efficiently and thoroughly. By solving problems at the source, companies can deliver better customer service, leading to increased satisfaction and customer loyalty.
Benefit: Customers benefit from timely and effective resolutions, enhancing their overall experience and strengthening customer relationships.
9. Enhanced In-House Communication and Collaboration
RCA encourages cross-functional teams to work together in identifying and solving problems. This collaboration fosters better communication, a shared understanding of underlying systems, and a team-oriented approach to problem-solving.
Benefit: Strengthened team communication and collaboration lead to improved organizational cohesion and collective problem-solving capabilities.
10. Better Documentation and Knowledge Management
Effective RCA is often accompanied by thorough documentation that records how issues were identified, analyzed, and solved. This knowledge can be leveraged in future projects or operations to prevent similar problems, improving organizational learning and knowledge retention.
Benefit: Documenting RCA processes ensures that valuable lessons are not lost and can be applied to future projects, reducing the learning curve for new challenges.
11. Process Improvement and Team Development
Through RCA, organizations can identify inefficiencies in processes, gaps in training, and opportunities for further development. This insight allows teams to refine their workflows and helps managers identify training needs to ensure that teams have the skills required to address challenges effectively.
Benefit: RCA drives process improvement while simultaneously enhancing the capabilities of your team, making them more adaptable and resourceful.
Challenges in Implementing Root Cause Analysis (RCA)
While Root Cause Analysis (RCA) is a powerful tool for resolving issues and improving business operations, its implementation is not always straightforward. Various obstacles can hinder the effective application of RCA, making it important for organizations to address these challenges proactively.
Here are some of the key challenges faced when implementing RCA and potential strategies for overcoming them:
1. Lack of Expertise and Training
One of the most significant barriers to successfully implementing RCA is the lack of skilled personnel who are well-versed in the methodology. RCA requires a deep understanding of the underlying issues, as well as proficiency in analytical tools and techniques. Without proper training, teams may struggle to conduct effective root cause analyses, leading to incorrect conclusions or incomplete solutions.
Solution: Invest in training and skill development for employees, ensuring that key personnel are proficient in RCA techniques. Bringing in external experts to guide the process can also provide valuable insights.
2. Insufficient Data and Information
RCA relies heavily on accurate, comprehensive data to identify the true cause of issues. Without access to detailed records or relevant metrics, teams may end up speculating about the root cause, leading to ineffective solutions. Inadequate data collection methods, poorly maintained records, or siloed information systems can make it difficult to conduct a thorough RCA.
Solution: Ensure that data collection processes are standardized and that relevant information is easily accessible across the organization. Implement systems for continuous monitoring to gather data in real time, helping to inform RCA efforts.
3. Resistance to Change
Implementing RCA often uncovers underlying issues with existing processes or practices that may require significant changes. Employees, managers, or even leadership teams may resist these changes due to concerns about disruption, fear of failure, or reluctance to adopt new methods. Resistance to change can slow down the RCA process or prevent it from being fully implemented.
Solution: Engage stakeholders early in the process to build support for RCA. Clearly communicate the benefits of RCA, both in terms of operational improvements and long-term cost savings. Providing ongoing support and education can help ease resistance.
4. Overlooking the Human Element
RCA often focuses on technical or process-related issues, but the human factor—such as employee behavior, communication, and decision-making—can also play a significant role in problem occurrences. Ignoring the human element in RCA may lead to incomplete analyses and solutions that fail to address the true root cause of an issue.
Solution: Incorporate a holistic approach to RCA that considers both technical and human factors. Involve employees at all levels in the RCA process to better understand the role that behavior, communication, and decision-making play in the challenges faced.
5. Time and Resource Constraints
Root cause analysis can be time-consuming and resource-intensive, particularly when dealing with complex problems. Teams may struggle to allocate sufficient time and resources to conduct a thorough RCA, especially when there are pressing deadlines or competing priorities. Inadequate planning for RCA can lead to rushed or incomplete analyses.
Solution: Plan RCA activities as part of a structured problem-solving process and allocate sufficient time and resources. By integrating RCA into day-to-day operations, organizations can balance urgent tasks with the need for thorough analysis.
6. Misidentifying Symptoms as Root Causes
One of the key challenges of RCA is distinguishing between symptoms and the actual root cause of an issue. It's easy to become fixated on the immediate, visible problem rather than digging deeper to uncover the underlying causes. This can lead to quick fixes that don’t address the true source of the issue, resulting in recurring problems.
Solution: Emphasize a systematic approach to RCA that involves asking probing questions and continually digging deeper until the true root cause is identified. Use the "5 Whys" technique or Fishbone Diagram to challenge assumptions and thoroughly investigate the problem.
7. Lack of Follow-Through and Accountability
After identifying the root cause, it's essential to take corrective action and follow through with implementation. However, organizations sometimes fail to fully implement solutions, either due to a lack of accountability or because the root cause analysis itself was insufficient. Without proper follow-through, RCA can become a futile exercise.
Solution: Assign clear ownership and accountability for implementing solutions. Regularly monitor progress and ensure that changes are being carried out effectively. Make sure that any corrective actions are tracked and reviewed for effectiveness.
8. Scope Creep and Complexity
In some cases, RCA can become too broad or complicated, leading teams to investigate too many potential causes or layers of issues. This “scope creep” can make the process overly complex and divert focus away from the most pressing problem. A lack of clear objectives or understanding of what needs to be solved can lead to paralysis by analysis.
Solution: Define the scope of the RCA upfront and maintain focus on solving the most critical issues. Ensure that the analysis remains targeted and avoid diving into unrelated problems that may not significantly impact the overall system.
9. Inadequate Communication Across Teams
RCA requires collaboration and communication across multiple departments or teams to identify and address root causes. Poor communication, lack of coordination, or siloed operations can hinder the RCA process, leading to incomplete or inaccurate findings.
Solution: Foster a culture of open communication and cross-functional collaboration. Encourage teams from different departments to contribute insights and work together to solve the problem. Regular check-ins and collaborative platforms can help ensure seamless communication.
10. Failure to Monitor and Adjust Solutions
Even after corrective actions are implemented, it’s crucial to monitor their effectiveness and adjust the approach as needed. If RCA solutions aren’t continuously evaluated or updated, organizations may revert to old practices or encounter new issues that were not initially anticipated.
Solution: Establish metrics and KPIs to monitor the success of corrective actions over time. Regularly review and refine processes based on new data or feedback, ensuring that the solutions remain effective and relevant.
Best Practices for Effective Root Cause Analysis (RCA)
To maximize the effectiveness of Root Cause Analysis (RCA), organizations must adopt best practices that ensure thoroughness, accuracy, and sustainable solutions. The following best practices will guide you through the RCA process, helping you resolve issues efficiently and continuously improve your processes.
1. Define the Problem Clearly
Before diving into the analysis, it’s crucial to have a clear understanding of the problem you're trying to solve. A poorly defined issue can lead to ineffective RCA efforts. Ensure that the problem is articulated in measurable terms, and be specific about what occurred, when, and how.
Best Practice: Use the SMART (Specific, Measurable, Achievable, Relevant, Time-bound) criteria to define the problem statement. This helps narrow down the focus and sets the foundation for the analysis.
2. Use a Structured Approach
A structured approach helps keep the analysis systematic and comprehensive. Relying on a standard methodology ensures that every critical step is addressed and prevents overlooking key details.
Best Practice: Adopt proven RCA tools like the 5 Whys, Fishbone Diagram (Ishikawa), or Fault Tree Analysis. These methods guide the team in exploring causes methodically and can lead to more accurate findings.
3. Involve Cross-Functional Teams
RCA is more effective when a diverse group of individuals from different departments collaborate. The involvement of people from various perspectives ensures that the analysis is not limited to a single viewpoint and that all potential causes are considered.
Best Practice: Form a team with representatives from operations, quality control, engineering, IT, and other relevant departments. Encourage input from employees who are directly involved with the processes or equipment under review.
4. Ask the Right Questions
The root cause is often hidden beneath layers of symptoms, so it’s important to ask probing questions to explore all possibilities. Use open-ended questions and apply techniques like the 5 Whys to drill deeper into each layer of the issue.
Best Practice: Ask questions such as, “Why did this happen?” followed by additional “Why” questions to uncover the root cause. Ensure that the questions are data-driven and avoid jumping to conclusions prematurely.
5. Collect and Analyze Data
Effective RCA relies on accurate and comprehensive data. Without sufficient evidence, conclusions can be skewed, leading to incorrect assumptions. Therefore, it's crucial to gather data from multiple sources to support the analysis.
Best Practice: Use quantitative and qualitative data, including historical performance metrics, production records, maintenance logs, and employee feedback. Analyze patterns to identify correlations and underlying issues.
6. Consider All Potential Causes
A common mistake in RCA is narrowing down the potential causes too early in the process. To truly identify the root cause, all possibilities must be explored thoroughly, including human errors, process inefficiencies, equipment failures, and environmental factors.
Best Practice: Conduct a comprehensive brainstorming session with the RCA team to consider all potential contributing factors. Use the Fishbone Diagram to categorize causes into areas like people, process, environment, materials, machinery, and management.
7. Focus on the System, Not Just the Symptoms
Root Cause Analysis aims to uncover systemic issues, not just address symptoms. It's important to look at how the broader system works, as recurring problems often stem from deeper issues within processes, workflows, or culture.
Best Practice: Don’t just fix the immediate problem. Once the root cause is identified, look for ways to improve the system to prevent similar issues from recurring. This may involve process redesign or updating SOPs (Standard Operating Procedures).
8. Document the Process and Findings
Documentation is key to the success of RCA. Properly documenting both the process and the conclusions provides transparency, helps track progress, and allows the team to revisit the findings if similar issues arise in the future.
Best Practice: Create a detailed RCA report that includes the problem statement, analysis tools used, identified root causes, corrective actions taken, and timelines. Keep a record of lessons learned for future reference.
9. Implement Corrective Actions and Solutions
Once the root cause is identified, it's essential to take corrective action to resolve the issue and prevent it from happening again. The corrective measures should address the root cause rather than just alleviate the symptoms.
Best Practice: Develop a corrective action plan with clear steps, responsible parties, and deadlines. Ensure that the solutions are practical, feasible, and aligned with the organization’s goals.
10. Monitor and Review the Results
After implementing corrective actions, it’s crucial to monitor the results to ensure that the problem is truly resolved. This helps verify the effectiveness of the solutions and allows for adjustments if needed.
Best Practice: Set up monitoring mechanisms, such as KPIs (Key Performance Indicators), to track the progress of implemented solutions. Periodically review the performance and adjust the action plan if the issue reoccurs or if there are new developments.
11. Promote a Culture of Continuous Improvement
RCA should not be a one-time activity. For RCA to deliver long-term benefits, organizations must create a culture of continuous improvement. By making RCA a regular part of the problem-solving process, teams can preemptively identify and address potential issues before they escalate.
Best Practice: Encourage employees at all levels to participate in RCA initiatives and share insights. Regularly schedule RCA reviews and process audits to foster a mindset of ongoing improvement.
How Deskera ERP Can Help with Root Cause Analysis
Root Cause Analysis (RCA) is a critical practice for identifying and addressing the underlying causes of issues within business operations. Deskera ERP offers a range of features that can significantly aid in performing effective RCA by providing the tools, data, and insights necessary for comprehensive analysis and resolution.
Here’s how Deskera ERP can enhance your root cause analysis efforts:
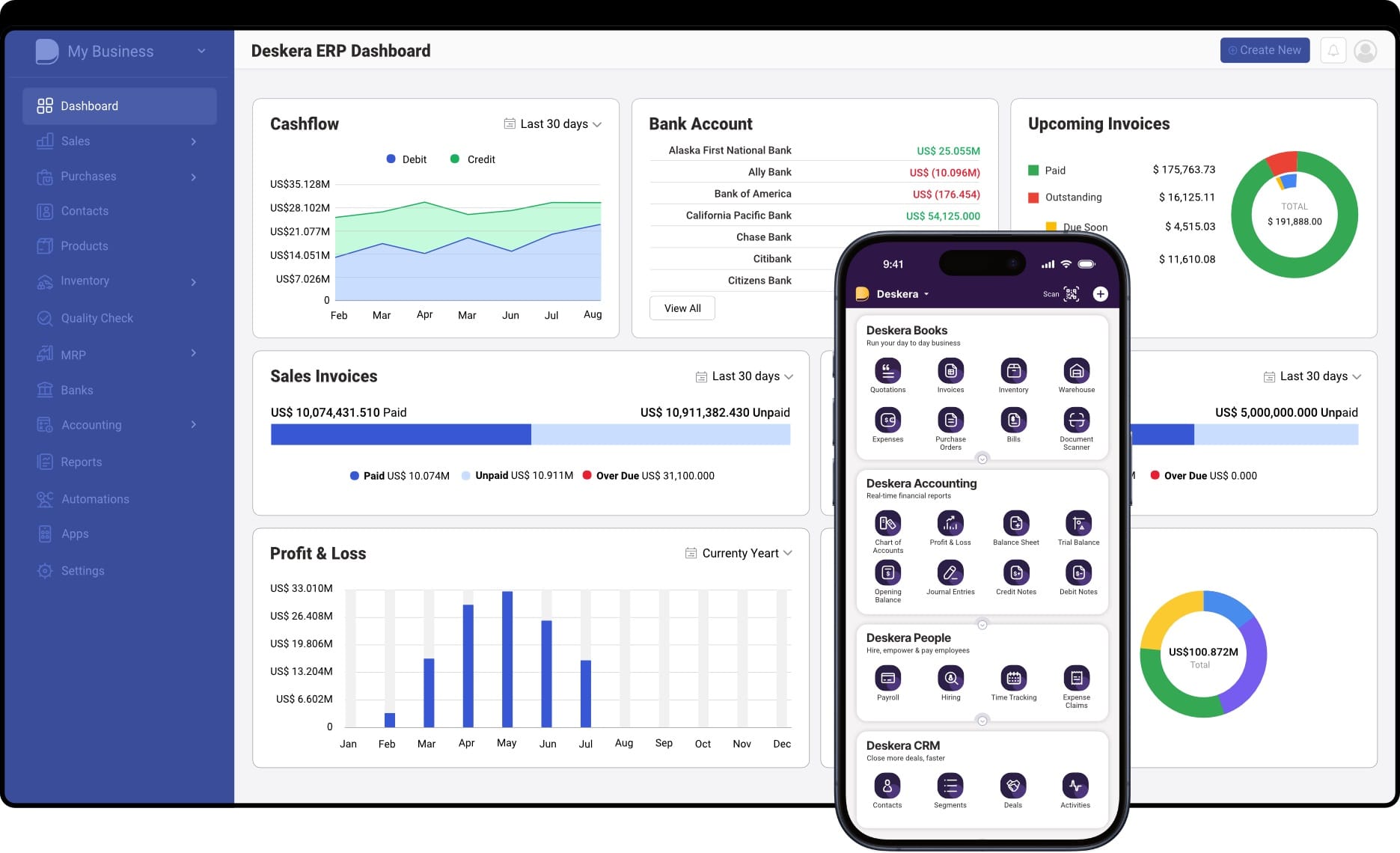
1. Centralized Data for Accurate Insights
Deskera ERP integrates various business functions such as inventory, finance, HR, and manufacturing into one centralized platform. This consolidation of data enables businesses to access accurate, real-time information across all departments, which is crucial for performing effective RCA.
Benefit: With all relevant data in one place, you can quickly identify patterns, correlations, and discrepancies that might indicate the root cause of issues, such as supply chain disruptions or production delays.
2. Comprehensive Reporting and Analytics
Deskera ERP offers powerful reporting and analytics tools that allow users to generate detailed reports and analyze data trends. The ability to track key metrics across various functions—such as production rates, inventory levels, and employee performance—helps pinpoint inefficiencies or performance gaps.
Benefit: By utilizing Deskera’s analytics tools, you can easily track historical performance and analyze deviations, which can be essential for uncovering the underlying causes of recurring problems, such as inventory stockouts or delays in production.
3. Real-Time Monitoring of Key Performance Indicators (KPIs)
Deskera ERP includes customizable dashboards that provide real-time monitoring of critical KPIs related to your operations. These KPIs could include production timelines, quality control metrics, and delivery schedules, which are vital when analyzing problems in workflows or systems.
Benefit: Deskera’s real-time monitoring capabilities allow you to quickly detect anomalies in performance, helping identify potential root causes before they escalate. You can also track the effectiveness of implemented corrective actions to ensure that the root cause is resolved.
4. Supply Chain Transparency and Traceability
Deskera ERP’s supply chain management features provide full visibility and traceability of materials, orders, and shipments. This transparency is key when investigating issues such as delays or quality control failures in the supply chain.
Benefit: With Deskera’s supply chain tools, you can trace every aspect of your procurement, production, and delivery processes. This helps identify if root causes are arising from suppliers, production inefficiencies, or shipping delays, allowing you to take swift corrective actions.
5. Automated Workflows and Alerts
Deskera ERP allows businesses to automate workflows, ensuring that tasks are completed on time and according to predefined processes. Additionally, its alert systems notify users of any deviations from expected performance.
Benefit: The ability to automate workflows and receive alerts enables businesses to quickly respond to irregularities and analyze whether these deviations are symptomatic of larger, systemic issues. Automated processes help streamline the RCA process by ensuring that nothing is overlooked.
6. Collaboration and Communication Tools
Deskera ERP fosters better collaboration by providing integrated communication tools. Teams across departments can share data, reports, and insights directly within the platform, facilitating smoother cross-functional collaboration during the RCA process.
Benefit: RCA is most effective when diverse perspectives are considered. Deskera ERP’s collaboration tools make it easier for teams to discuss issues, share observations, and contribute to the root cause analysis, ensuring a more comprehensive evaluation of the problem.
Key Takeaways
- Root Cause Analysis (RCA) is an essential problem-solving approach that goes beyond symptoms to identify and address the fundamental issues driving problems in organizations.
- RCA enables organizations to prevent recurring problems by focusing on root causes, leading to enhanced efficiency, reduced risks, and sustainable solutions.
- RCA involves a clear and systematic process, starting with problem identification, data collection, root cause identification, analysis, and the implementation of corrective actions.
- Various RCA methodologies, such as 5 Whys, FMEA, and Ishikawa diagrams, provide structured approaches tailored to different problem-solving needs.
- RCA should be performed when recurring issues arise, critical system failures occur, or when there is a need to improve processes proactively.
- Mastering RCA leads to continuous improvement, reduced costs, increased productivity, better defect detection, enhanced safety, and optimized systems and processes.
- Common challenges include lack of training, insufficient data, resistance to change, and focusing on symptoms rather than root causes, which can hinder the effectiveness of RCA.
- Successful RCA requires assembling a diverse team, using structured tools like fishbone diagrams, fostering open communication, and focusing on systemic changes rather than quick fixes.
- Deskera ERP supports RCA by providing centralized data, real-time monitoring, advanced reporting, and collaboration tools that streamline problem-solving and ensure long-term solutions.
Related Articles
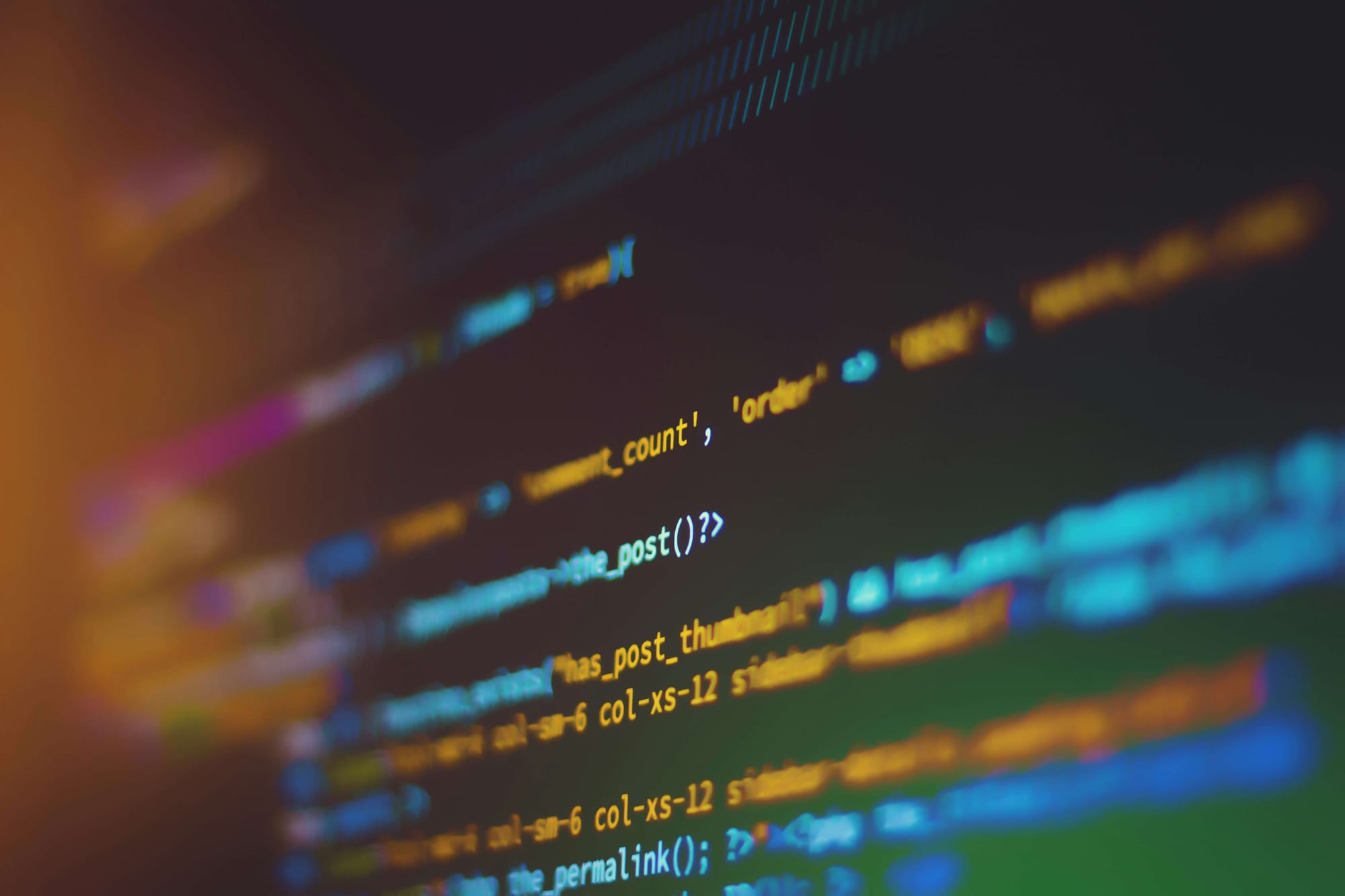
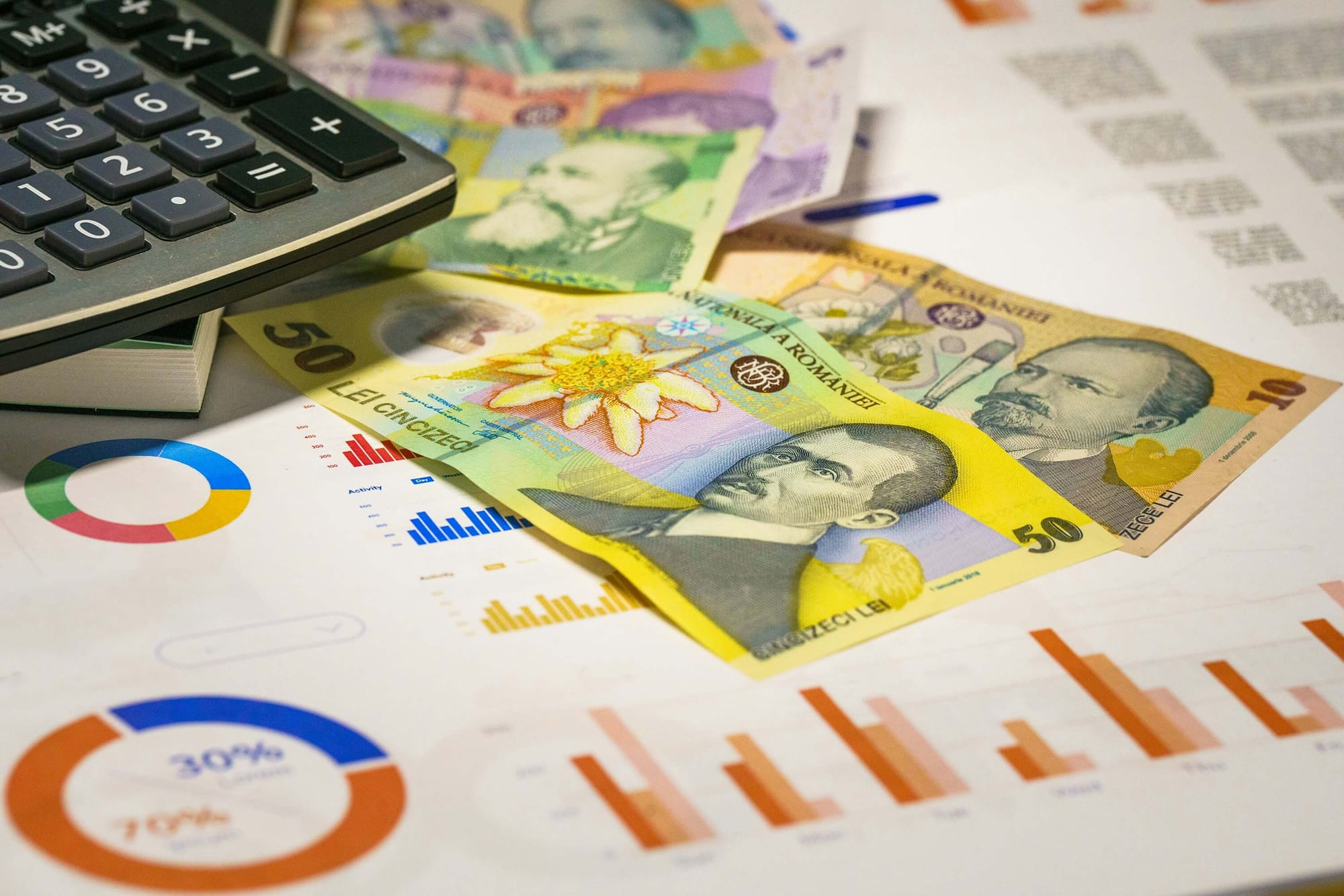
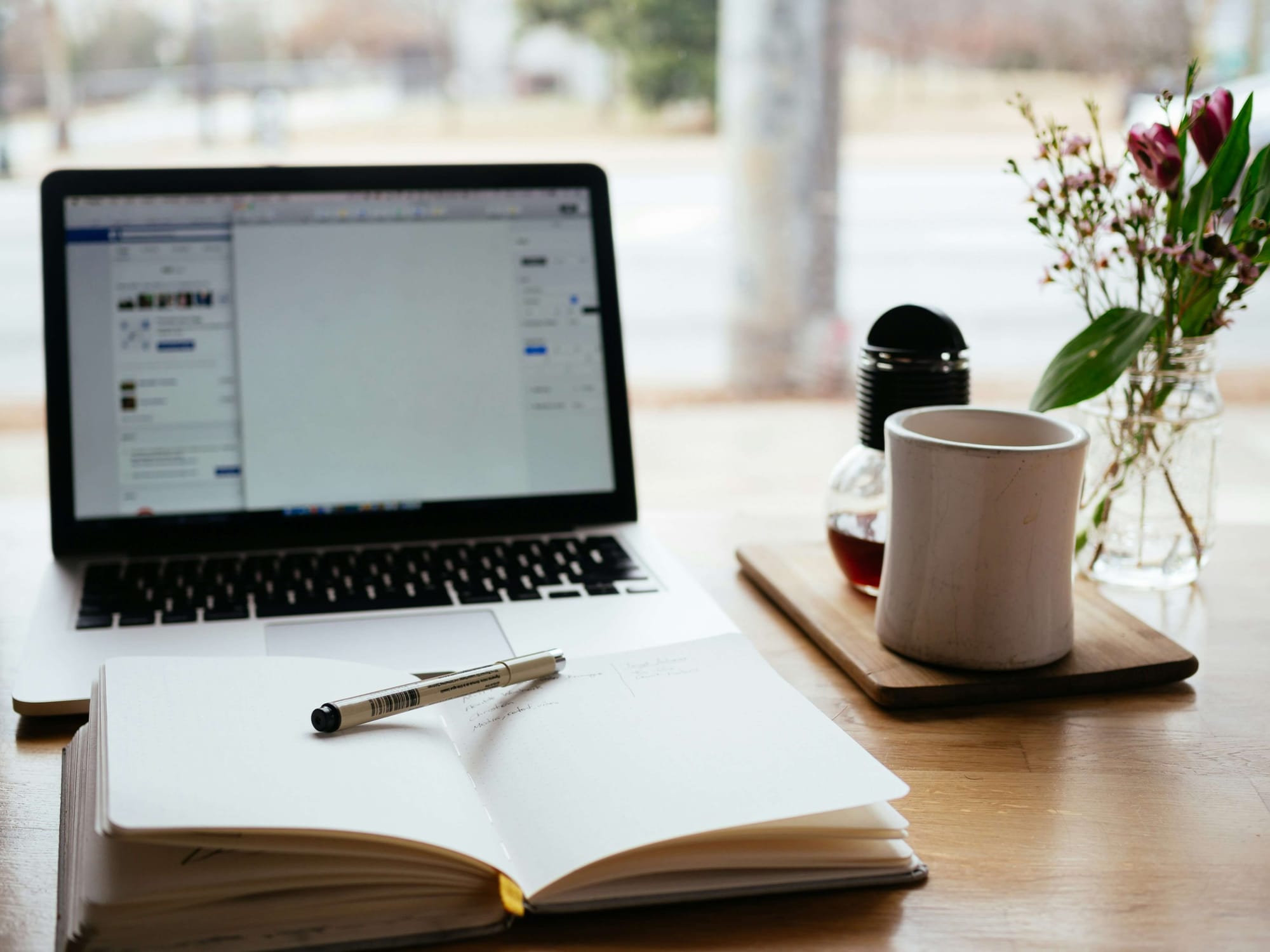
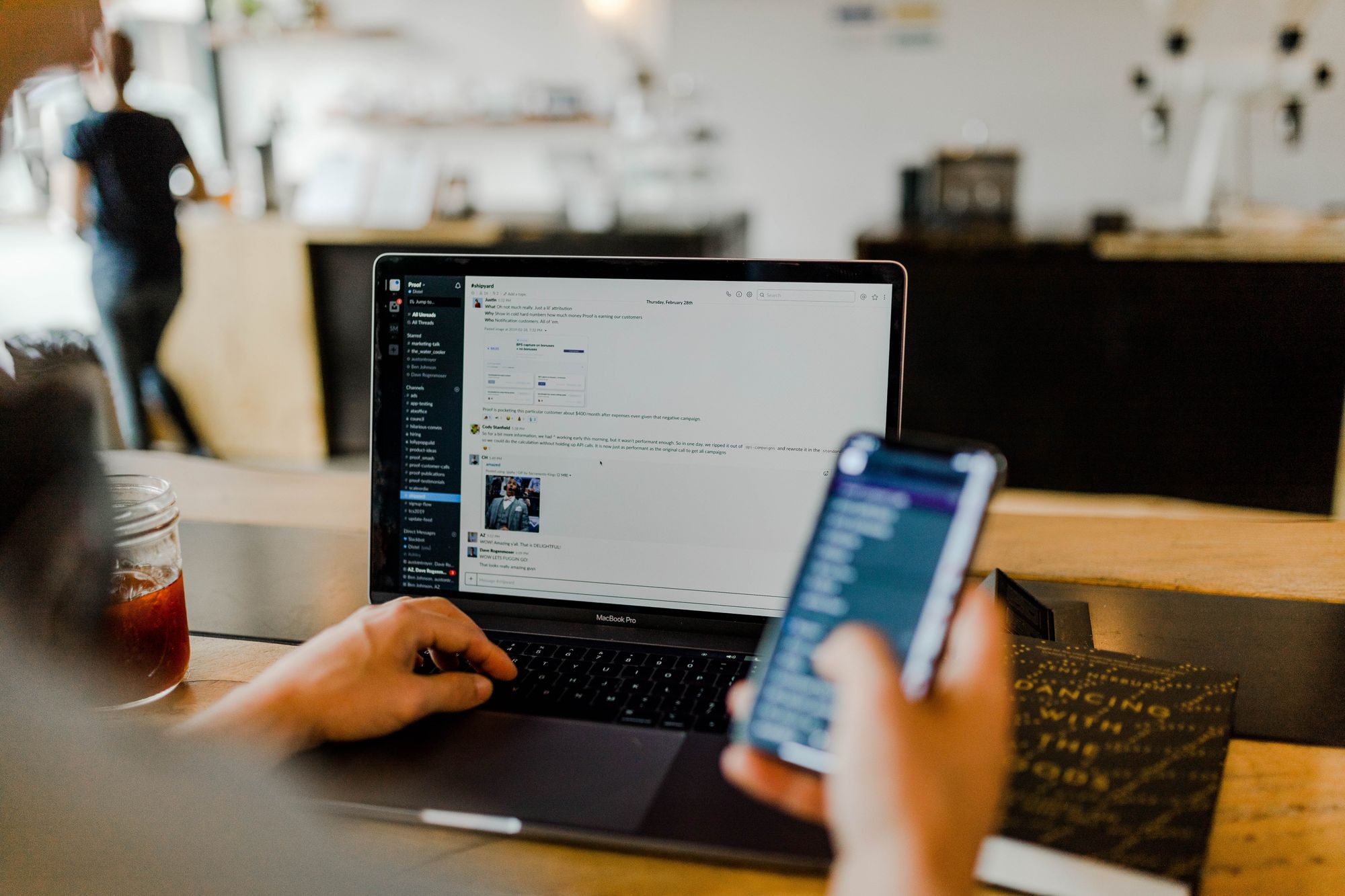
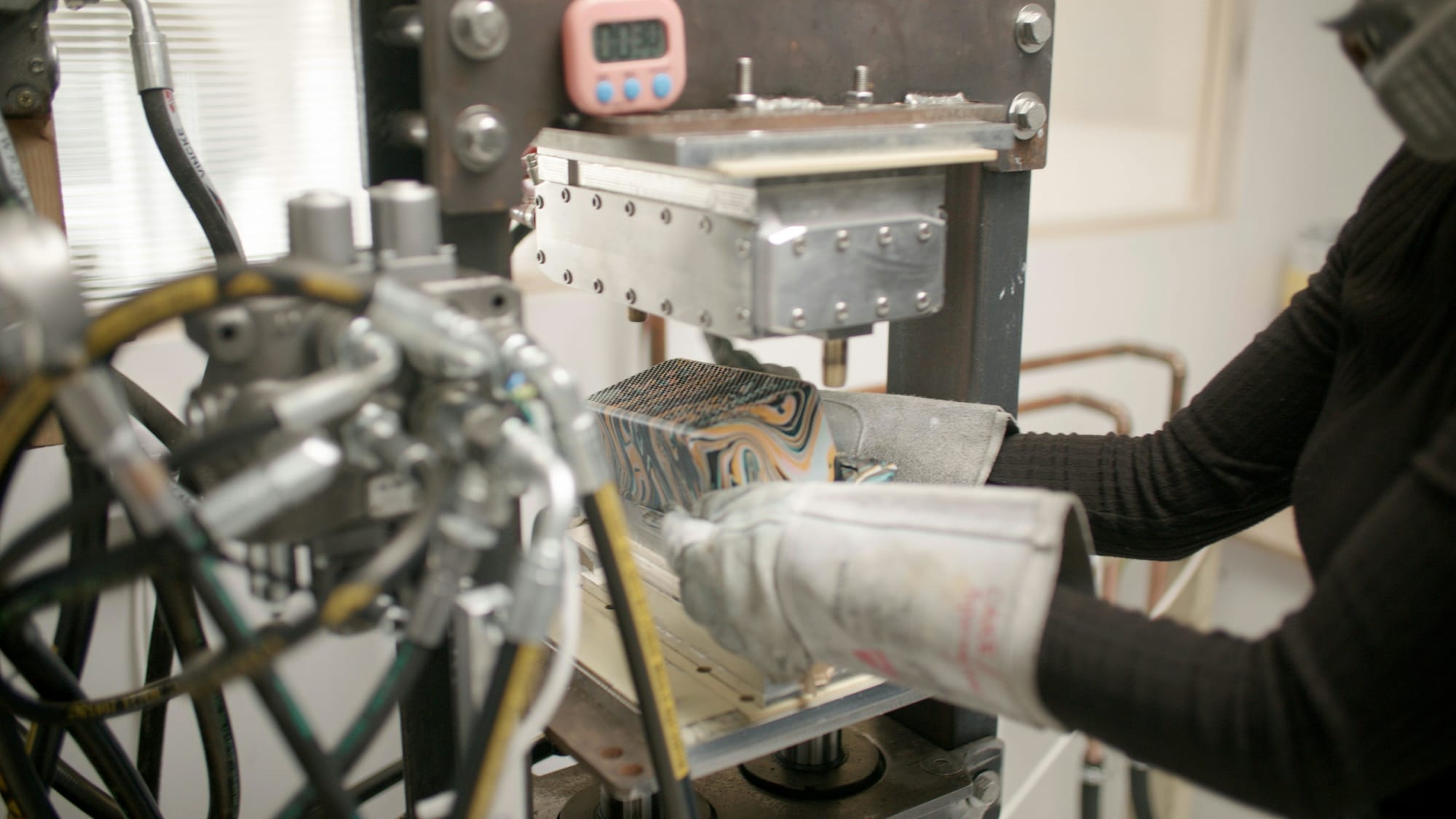
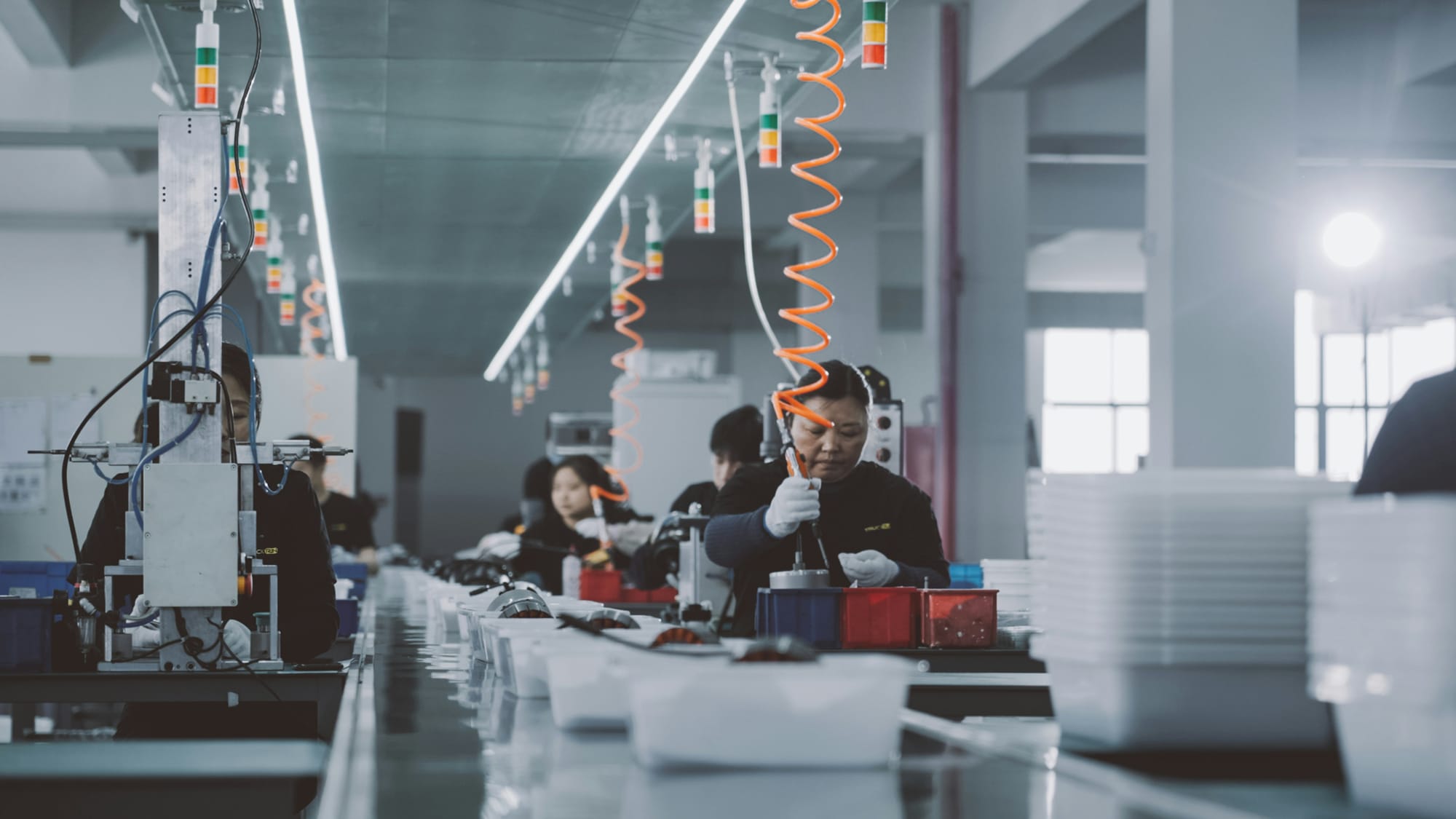