Furniture production has a significant impact on the environment due to the use of natural resources and the creation of waste. With the global focus on sustainability, it is essential for furniture companies to adopt strategies that reduce waste and maximize efficiency in their production processes.
According to the Environmental Protection Agency (EPA), in 2018, furniture and furnishings accounted for 9.7 million tons (4.1%) of the total municipal solid waste (MSW) generated in the United States.
By doing so, companies can not only reduce their environmental impact but also improve their bottom line. This topic explores various strategies that furniture companies can use to achieve this goal, including Design for Manufacturing and Assembly (DFMA), Lean Manufacturing, effective materials management, and recycling/upcycling.
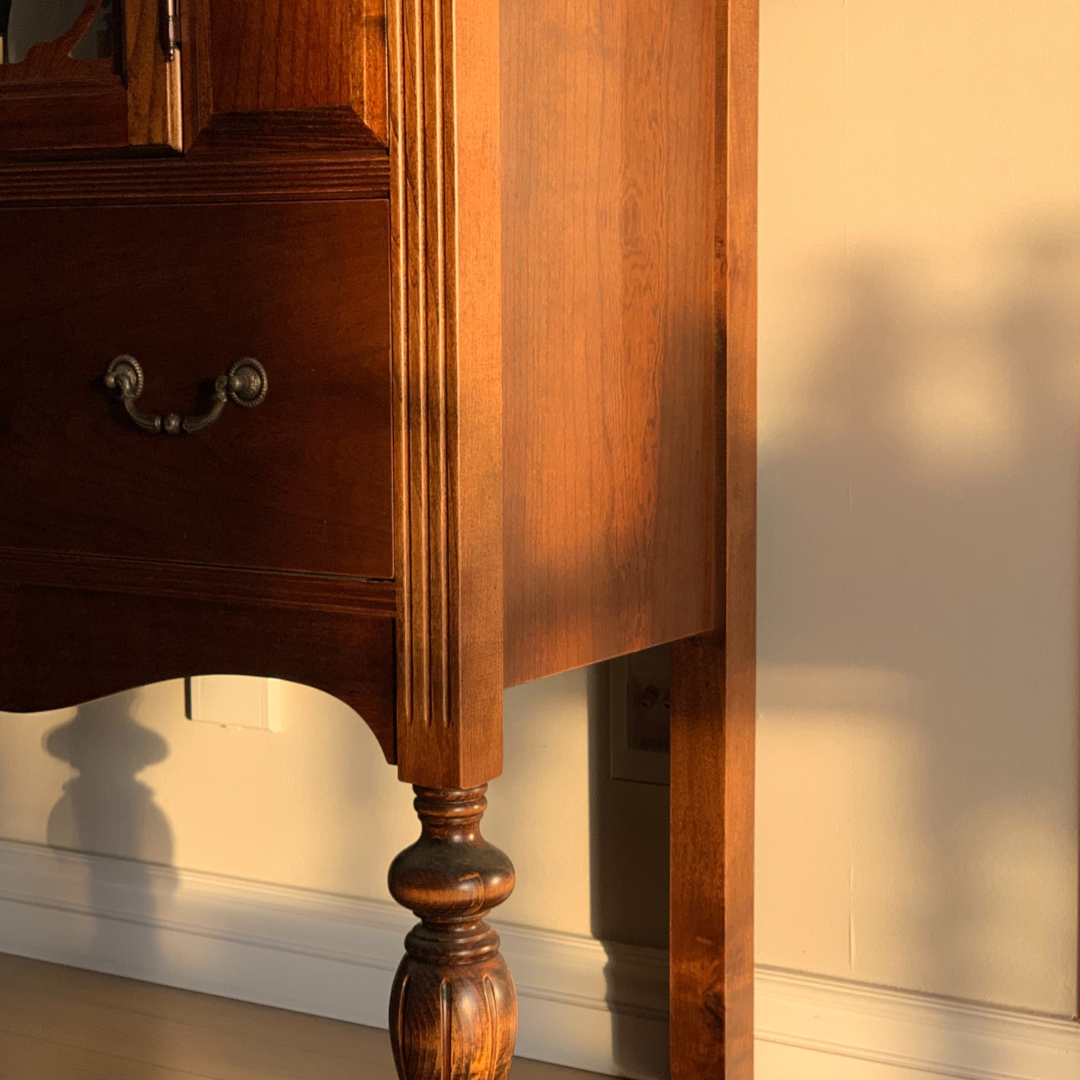
By incorporating these strategies, furniture companies can reduce their waste, optimize their production processes, and create high-quality, sustainable furniture products that meet consumer demands.
Ultimately, this topic highlights the importance of environmentally responsible practices in furniture production and encourages furniture companies to take action towards a more sustainable future.
- Significance of Reducing Waste and Maximizing Efficiency in Furniture Production
- Design for Manufacturing and Assembly (DFMA)
- Lean Manufacturing
- Materials Management
- Recycling and Upcycling
- Typical Challenges in Reducing Waste in Furniture Production
- MRP and ERP Systems for Reducing Waste and Maximizing Efficiency in Furniture Production
- How can Deskera Help You?
- Key Takeaways
- Related Articles
Significance of Reducing Waste and Maximizing Efficiency in Furniture Production
Reducing waste and maximizing efficiency in furniture production is crucial in today's world where environmental sustainability is becoming increasingly important. Furniture production is known to consume natural resources, generate waste, and contribute to climate change.
By adopting sustainable practices that minimize waste and optimize production processes, furniture companies can significantly reduce their environmental impact while also improving their profitability and competitiveness. In this section, we will discuss the significance of reducing waste and maximizing efficiency in furniture production.
We will explore the benefits of implementing sustainable practices such as Design for Manufacturing and Assembly (DFMA), Lean Manufacturing, effective materials management, and recycling/upcycling. We will also highlight the importance of corporate responsibility and meeting consumer demand for sustainable products.
Reducing waste and maximizing efficiency in furniture production is significant for several reasons:
- Environmental sustainability: Furniture production consumes natural resources and generates waste, contributing to environmental degradation. By reducing waste and maximizing efficiency, furniture companies can minimize their environmental impact, conserve resources, and help mitigate climate change.
- Cost savings: By reducing waste and optimizing their production processes, furniture companies can save on costs related to materials, labor, and energy. This can improve their profitability and competitiveness in the market.
- Consumer demand: As consumers become more environmentally conscious, they are increasingly demanding sustainable products. Furniture companies that prioritize reducing waste and maximizing efficiency can meet this demand and attract environmentally conscious consumers.
- Corporate responsibility: Reducing waste and maximizing efficiency is a key component of corporate responsibility. Furniture companies have a responsibility to operate sustainably and minimize their impact on the environment.
Overall, reducing waste and maximizing efficiency in furniture production is significant for the environment, the economy, consumer demand, and corporate responsibility. By adopting sustainable practices, furniture companies can create high-quality products while minimizing their impact on the environment.
Design for Manufacturing and Assembly (DFMA)
In furniture production, DFMA can be used to reduce waste and improve efficiency by designing products that are easier and more cost-effective to produce.
DFMA considers factors such as material selection, part reduction, and assembly processes, with the goal of creating products that are easier to assemble, require fewer parts, and generate less waste. By implementing DFMA principles in furniture design, companies can improve their production processes, reduce costs, and create more sustainable products.
In this section, we will explore how DFMA can be applied in furniture design to reduce waste and improve efficiency, and provide examples of furniture designs that incorporate DFMA principles.
Explanation of DFMA Principles
Design for Manufacturing and Assembly (DFMA) is a set of principles and practices used to optimize product design for ease of manufacturing and assembly. DFMA principles are designed to minimize waste and improve efficiency by reducing the number of parts in a product, simplifying assembly processes, and reducing the time and cost of production.
The following are the key DFMA principles:
- Simplify design: By simplifying the design of a product, the number of parts required can be reduced, which minimizes waste and improves efficiency.
- Standardize parts: Standardizing parts reduces the number of unique parts required and simplifies the manufacturing and assembly process.
- Minimize assembly steps: By minimizing the number of assembly steps required, the time and cost of production can be reduced.
- Optimize assembly sequence: By optimizing the sequence of assembly steps, the time and effort required for assembly can be minimized.
- Design for ease of handling: Designing products for ease of handling reduces the risk of damage during production and assembly, minimizing waste and reducing costs.
By implementing these DFMA principles in furniture design, companies can reduce waste, minimize their environmental impact, and improve the efficiency of their production processes.
By creating more sustainable products that are easier and more cost-effective to produce, furniture companies can meet consumer demand for environmentally responsible products while also improving their profitability and competitiveness in the market.
How DFMA can be Applied in Furniture Design to Reduce Waste and Improve Efficiency
DFMA can be applied in furniture design to reduce waste and improve efficiency in several ways:
- Material selection: DFMA principles encourage designers to consider the availability and cost of materials, as well as their environmental impact. By selecting materials that are readily available and easy to work with, designers can minimize waste and reduce the time and cost of production.
- Part reduction: DFMA principles encourage designers to reduce the number of parts required in a product. This reduces the amount of waste generated during production, simplifies assembly, and reduces the time and cost of production.
- Standardization: By standardizing parts and components, designers can reduce the number of unique parts required in a product. This simplifies the manufacturing and assembly process, reduces the time and cost of production, and minimizes waste.
- Modular design: DFMA principles encourage designers to create modular designs that can be assembled quickly and easily. This simplifies the assembly process, reduces the time and cost of production, and makes it easier to repair and replace parts.
- Design for recyclability: DFMA principles encourage designers to consider the end-of-life disposal of their products. By designing products that can be easily disassembled and recycled or reused, designers can reduce waste and minimize the environmental impact of their products.
By adopting these principles, furniture companies can create more sustainable products that meet consumer demand for environmentally responsible products while also improving their profitability and competitiveness in the market.
Examples of Furniture Designs that Incorporate DFMA Principles
There are numerous examples of furniture designs that incorporate DFMA principles, including:
- Flat-pack furniture: Flat-pack furniture, such as IKEA's products, are designed to be easily assembled by the end consumer using a minimal number of parts. The designs are optimized for efficient manufacturing, transportation, and assembly.
- Modular furniture: Modular furniture, such as office cubicles or shelving units, are designed to be easily assembled and disassembled, allowing for customization and flexibility. The modular design also allows for easy repair and replacement of parts.
- Multi-functional furniture: Multi-functional furniture, such as sofa beds or storage ottomans, are designed to serve multiple purposes, reducing the need for additional furniture pieces. The designs are optimized for ease of assembly and disassembly, as well as material and part reduction.
- CNC cut furniture: Computer numerical control (CNC) cut furniture, such as the designs by Michael Iannone, are made from flat sheets of wood or other materials that are cut using a CNC machine. The designs are optimized for efficient material use and minimal waste, as well as ease of assembly.
- Recyclable furniture: Furniture designs, such as the Cradle to Cradle certified chairs by Herman Miller, are designed for recyclability at the end of their life cycle. The designs are optimized for easy disassembly and reuse of materials.
These furniture designs incorporate DFMA principles to reduce waste, minimize environmental impact, and improve the efficiency of production and assembly processes.
By adopting DFMA principles in furniture design, companies can create more sustainable products that meet consumer demand for environmentally responsible products while also improving their profitability and competitiveness in the market.
Lean Manufacturing
Lean manufacturing is a production method that focuses on minimizing waste and maximizing efficiency in the manufacturing process. It involves eliminating non-value-added activities, reducing inventory, and optimizing production flows to create products more efficiently and cost-effectively.
In this section, we will explore how lean manufacturing can be applied to furniture production to reduce waste, improve efficiency, and increase profitability.
Explanation of Lean Manufacturing Principles
Lean manufacturing is based on several principles that aim to reduce waste and improve efficiency in the production process. The five core principles of lean manufacturing are:
- Value: Define value from the customer's perspective and focus on delivering products that meet or exceed their expectations.
- Value stream: Identify the value stream or the sequence of steps required to deliver the product to the customer. Eliminate non-value-added steps and focus on optimizing the flow of the remaining value-added steps.
- Flow: Optimize the flow of the value stream by removing any barriers, bottlenecks, or delays. This involves creating a smooth and continuous flow of work and materials through the production process.
- Pull: Produce products only when they are needed by the customer. This involves creating a pull system where production is triggered by customer demand, rather than by a forecast or a production schedule.
- Perfection: Continuously improve the production process by eliminating waste, improving quality, and optimizing efficiency. This involves creating a culture of continuous improvement and involving all employees in the process.
By applying these principles, lean manufacturing aims to create a production process that is efficient, flexible, and responsive to customer demand. This, in turn, leads to reduced waste, increased productivity, improved quality, and increased profitability.
How Lean Manufacturing can be Applied in Furniture Production to Reduce Waste and Improve Efficiency
Lean manufacturing principles can be applied in furniture production to reduce waste and improve efficiency in several ways, including:
- Eliminating waste: Lean manufacturing aims to eliminate waste in all its forms, including overproduction, excess inventory, unnecessary motion, waiting, overprocessing, defects, and unused talent. In furniture production, this can be achieved by optimizing the production flow, reducing setup times, minimizing inventory, and eliminating non-value-added activities.
- Continuous improvement: Lean manufacturing encourages continuous improvement of the production process through the involvement of all employees. By empowering employees to identify and solve problems, furniture manufacturers can improve quality, reduce waste, and increase efficiency.
- Just-in-time production: JIT manufacturing advocates for producing products only when they are needed by the customer. This involves creating a pull system where production is triggered by customer demand, rather than by a forecast or a production schedule. In furniture production, this can be achieved by designing furniture that can be produced quickly and easily, without the need for excess inventory.
- Standardization: Lean manufacturing promotes standardization of processes and procedures to minimize variation and improve efficiency. In furniture production, this can be achieved by standardizing the size, shape, and components of furniture, as well as by creating standard work instructions for each production process.
- Kaizen events: Kaizen events are short-term improvement projects that focus on a specific area of the production process. By involving employees in Kaizen events, furniture manufacturers can identify and implement improvements quickly and effectively.
By applying lean manufacturing principles, furniture manufacturers can reduce waste, improve efficiency, and increase profitability. This can be achieved through the creation of a culture of continuous improvement, the involvement of all employees in the improvement process, and the adoption of lean manufacturing tools and techniques.
Examples of Lean Manufacturing Techniques that can be Used in Furniture Production
Here are some examples of Lean Manufacturing techniques that can be used in furniture production:
- 5S: A visual management technique that involves organizing the workspace to reduce waste and improve efficiency. The 5S's stand for sort, set in order, shine, standardize, and sustain.
- Kanban: A pull system that uses visual signals to control the flow of materials and products through the production process. In furniture production, Kanban can be used to ensure that only the necessary amount of inventory is produced.
- Value Stream Mapping: A technique used to analyze and optimize the flow of materials and information through the production process. By identifying and eliminating non-value-added activities, furniture manufacturers can reduce waste and improve efficiency.
- Single-Minute Exchange of Die (SMED): A technique used to reduce setup times and improve efficiency. In furniture production, SMED can be used to reduce the time it takes to changeover production from one product to another.
- Poka-yoke: A mistake-proofing technique that involves designing the production process to prevent errors and defects from occurring. In furniture production, Poka-yoke can be used to prevent assembly errors and improve quality.
By using these Lean Manufacturing techniques, furniture manufacturers can reduce waste, improve efficiency, and increase profitability. They can also improve product quality, reduce lead times, and enhance customer satisfaction.
Materials Management
Efficient materials management is a critical component of reducing waste and maximizing efficiency in furniture production. This involves managing the flow of materials from the supplier to the production floor, optimizing inventory levels, and reducing waste throughout the materials management process.
In this section, we will explore some of the key principles of materials management and how they can be applied in furniture production to improve efficiency and reduce waste.
Importance of Materials Management in Reducing Waste and Improving Efficiency
Materials management plays a crucial role in reducing waste and improving efficiency in furniture production. By effectively managing the flow of materials from suppliers to the production line, furniture companies can minimize waste, reduce costs, and optimize production processes.
One important aspect of materials management is inventory control. Keeping inventory levels optimized can help reduce waste by minimizing the amount of excess materials and supplies that are sitting unused in storage.
Just-in-time inventory management is one technique that can be used to ensure that materials are ordered and delivered only when they are needed for production.
Waste reduction programs can also be implemented as part of materials management. These programs can help identify areas where waste is being generated and take steps to reduce it. For example, materials that would otherwise be discarded as waste can be recycled or repurposed, reducing the amount of material that is sent to landfills.
Effective materials management can also lead to improved efficiency in production processes. By ensuring that materials are available when needed and that production is running smoothly, furniture companies can minimize downtime and increase productivity.
This can result in lower costs and higher profits, as well as improved customer satisfaction due to faster delivery times and higher quality products. Overall, effective materials management is an essential component of any strategy to reduce waste and improve efficiency in furniture production.
Strategies for Effective Materials Management in Furniture Production
Here are some effective strategies for materials management in furniture production:
- Just-in-time (JIT) inventory: JIT is a system of inventory management that involves producing and receiving goods just in time to meet customer demand. This system helps to reduce inventory levels, minimize storage costs, and reduce waste associated with excess inventory.
- Kanban system: A Kanban system uses visual signals to manage the flow of materials and products through the production process. This system can help to reduce inventory levels and improve production efficiency.
- Material Requirements Planning (MRP): MRP is a computer-based inventory management system that helps to ensure that the right materials are available when they are needed for production. This system helps to reduce waste associated with excess inventory and shortages.
- Waste reduction programs: Furniture manufacturers can implement waste reduction programs to identify and eliminate waste throughout the materials management process. These programs can help to reduce waste associated with excess inventory, scrap, rework, and disposal.
- Supplier collaboration: Collaboration with suppliers can help furniture manufacturers to optimize the flow of materials and reduce waste throughout the supply chain. By working closely with suppliers to manage inventory levels, furniture manufacturers can reduce the costs associated with excess inventory and improve supplier performance.
By implementing these materials management strategies, furniture manufacturers can improve production efficiency, reduce waste, and minimize costs associated with inventory and waste management. These strategies can help furniture manufacturers to achieve leaner, more efficient production processes and enhance their competitive position in the market.
Examples of furniture companies that have successfully implemented materials management strategies
Here are some examples of furniture companies that have successfully implemented materials management strategies:
- IKEA: IKEA is a Swedish furniture manufacturer that is known for its efficient materials management practices. The company uses a just-in-time inventory system to reduce inventory levels and minimize storage costs. IKEA also collaborates closely with suppliers to optimize the flow of materials and reduce waste throughout the supply chain.
- Herman Miller: Herman Miller is an American furniture manufacturer that has implemented a waste reduction program to minimize waste associated with excess inventory, scrap, and rework. The company has also implemented a Kanban system to manage the flow of materials and products through the production process.
- Steelcase: Steelcase is another American furniture manufacturer that has implemented a just-in-time inventory system to reduce inventory levels and minimize storage costs. The company also uses a computer-based material requirements planning (MRP) system to ensure that the right materials are available when they are needed for production.
- HON Furniture: HON Furniture is an American furniture manufacturer that has implemented a supplier collaboration program to optimize the flow of materials and reduce waste throughout the supply chain. The company also uses a Kanban system to manage the flow of materials and products through the production process.
These furniture companies have successfully implemented materials management strategies to reduce waste and improve efficiency in their production processes. By optimizing the flow of materials, minimizing inventory levels, and reducing waste throughout the materials management process, these companies have achieved significant cost savings and enhanced their competitive position in the market.
Recycling and Upcycling
Recycling and upcycling are important strategies for reducing waste and promoting sustainability in furniture production. By repurposing materials and minimizing the use of virgin resources, furniture manufacturers can reduce their environmental impact and enhance their social responsibility.
In this section, we will explore how furniture manufacturers can incorporate recycling and upcycling principles into their production processes to reduce waste and promote sustainability.
Benefits of Recycling and Upcycling in Furniture Production
Recycling and upcycling offer several benefits for furniture production, including:
- Environmental sustainability: By recycling and upcycling materials, furniture manufacturers can reduce the demand for virgin resources and minimize the environmental impact associated with resource extraction and processing.
- Cost savings: Recycling and upcycling can help furniture manufacturers to reduce their material costs and minimize waste disposal expenses.
- Social responsibility: By incorporating recycling and upcycling principles into their production processes, furniture manufacturers can demonstrate their commitment to sustainability and environmental stewardship.
- Increased customer appeal: Consumers are increasingly interested in sustainable and eco-friendly products. Furniture manufacturers that incorporate recycling and upcycling principles into their production processes can enhance their appeal to environmentally conscious consumers.
- Creative design opportunities: Upcycling materials can inspire creative and unique furniture designs that stand out in the market and appeal to consumers looking for one-of-a-kind pieces.
Overall, recycling and upcycling can offer numerous benefits for furniture manufacturers, including cost savings, environmental sustainability, social responsibility, increased customer appeal, and creative design opportunities.
How Furniture Companies can Incorporate Recycling and Upcycling into their Production Processes
Furniture companies can incorporate recycling and upcycling into their production processes in several ways, including:
- Material selection: Furniture manufacturers can choose materials that are easily recyclable or upcyclable, such as wood, metal, glass, and plastic. By selecting materials that can be easily repurposed, furniture companies can minimize waste and promote sustainability.
- Design for disassembly: Furniture designers can incorporate design features that make it easy to disassemble furniture at the end of its life. This allows materials to be easily separated and recycled or upcycled.
- Material recovery: Furniture manufacturers can implement a process for recovering materials from products at the end of their life. This can involve disassembling the product and separating materials for recycling or upcycling.
- Upcycling and repurposing: Furniture companies can repurpose materials and components from old products to create new designs. For example, an old wooden door can be transformed into a unique coffee table or a metal frame can be used to create a new chair.
- Waste reduction: Furniture manufacturers can implement waste reduction programs to minimize the amount of waste generated during the production process. This can involve recycling or upcycling waste materials, such as sawdust or scrap wood, to create new products or components.
Examples of Furniture Companies that have Successfully Implemented Recycling and Upcycling Strategies
There are several furniture companies that have successfully implemented recycling and upcycling strategies in their production processes. Here are a few examples:
- Herman Miller: Herman Miller is a furniture company that has a strong commitment to sustainability. The company incorporates recycling and upcycling principles into its production processes and has implemented a program for recycling and reusing materials. For example, Herman Miller recycles its used office chairs and uses the materials to create new products.
- Emeco: Emeco is a furniture company that produces chairs made from recycled aluminum. The company uses 80% recycled aluminum in its production processes and has implemented a program for recycling its products at the end of their life.
- Loll Designs: Loll Designs is a furniture company that produces outdoor furniture made from recycled plastic. The company uses recycled plastic from milk jugs to create its products and has implemented a program for recycling its products at the end of their life.
- Uhuru Design: Uhuru Design is a furniture company that specializes in upcycling materials to create unique designs. The company has created a line of furniture made from reclaimed materials, such as salvaged wood and discarded metal.
Overall, these furniture companies demonstrate that recycling and upcycling can be successfully incorporated into production processes to reduce waste, promote sustainability, and enhance environmental and social responsibility.
Typical Challenges in Reducing Waste in Furniture Production
Reducing waste in furniture production can be a challenging task due to various factors, such as:
Complex supply chains: The furniture industry often involves complex supply chains that can make it difficult to track materials and products throughout the production process. This can make it challenging to identify and address waste at each stage of the production process.
Material selection: Furniture manufacturers often use a wide range of materials, and some of these materials may be difficult to recycle or upcycle. Choosing materials that are easily repurposed can be a challenge.
Design constraints: Furniture designers may face constraints in creating designs that are easily disassembled or that incorporate recycled or upcycled materials. Meeting aesthetic and functional requirements can be challenging while also reducing waste.
Cost considerations: Implementing waste reduction strategies, such as recycling and upcycling, can come with additional costs. For example, using recycled or upcycled materials may be more expensive than using new materials. Manufacturers may also face costs associated with implementing new waste reduction programs.
Consumer behavior: Consumer behavior can impact the amount of waste generated in furniture production. For example, consumers may be more likely to dispose of furniture rather than repair or refurbish it, leading to more waste.
Overcoming these challenges requires a collaborative effort from stakeholders in the furniture industry, including manufacturers, designers, suppliers, and consumers. By working together to address these challenges, the furniture industry can make significant strides in reducing waste and promoting sustainability.
MRP and ERP Systems for Reducing Waste and Maximizing Efficiency in Furniture Production
MRP (Material Requirements Planning) and ERP (Enterprise Resource Planning) systems are software tools that help manufacturers manage their production processes, including materials, inventory, and production schedules. Both MRP and ERP systems can play an important role in reducing waste and maximizing efficiency in furniture production.
MRP systems focus primarily on managing materials and inventory levels. These systems use data from production schedules, inventory levels, and sales forecasts to determine the materials needed for production.
MRP systems help manufacturers to minimize waste by ensuring that they have the right amount of materials at the right time. This can reduce the risk of over-ordering materials, which can lead to excess inventory and waste.
ERP systems are more comprehensive and cover a broader range of business functions, including production, inventory, sales, accounting, and human resources. ERP systems provide a centralized platform for managing all aspects of a business, allowing manufacturers to streamline their operations and improve efficiency.
ERP systems can help manufacturers to minimize waste by providing real-time data on inventory levels, production schedules, and sales orders. This enables manufacturers to adjust production schedules and inventory levels as needed, reducing the risk of excess inventory and waste.
Important features of MRP and ERP systems that can assist in reducing waste and maximizing efficiency in furniture production include:
- Inventory management: Both MRP and ERP systems provide tools for managing inventory levels, including real-time inventory tracking and automatic inventory replenishment. This can help manufacturers to minimize waste by ensuring that they have the right amount of inventory on hand at all times.
- Production scheduling: MRP and ERP systems can help manufacturers to optimize their production schedules, ensuring that production runs smoothly and efficiently. This can help to minimize waste by reducing downtime and ensuring that products are produced on time.
- Material tracking: MRP systems provide tools for tracking materials throughout the production process, from raw materials to finished products. This can help manufacturers to identify potential bottlenecks and optimize their production processes.
- Real-time data: Both MRP and ERP systems provide real-time data on production schedules, inventory levels, and sales orders. This enables manufacturers to adjust their production schedules and inventory levels as needed, reducing the risk of excess inventory and waste.
In summary, MRP and ERP systems can play an important role in reducing waste and maximizing efficiency in furniture production. By providing tools for managing inventory levels, production schedules, and material tracking, manufacturers can streamline their operations and reduce waste.
How can Deskera Help You?
Deskera ERP and MRP systems help you to keep your business units organized. The system's primary functions are as follows:
- Keep track of your raw materials and final items inventories
- Control production schedules and routings
- Keep a bill of materials
- Produce thorough reports
- Make your own dashboards
Deskera's integrated financial planning tools enable investors to better plan and track their investments. It can assist investors in making faster and more accurate decisions.
Deskera Books allows you to better manage your accounts and finances. Maintain good accounting practices by automating tasks like billing, invoicing, and payment processing.
Deskera CRM is a powerful solution that manages your sales and helps you close deals quickly. It not only enables you to perform critical tasks like lead generation via email, but it also gives you a comprehensive view of your sales funnel.
Deskera People is a straightforward tool for centralizing your human resource management functions.
Key Takeaways
- Design for Manufacturing and Assembly (DFMA) principles can be applied in furniture design to reduce waste and improve efficiency.
- Lean Manufacturing principles can be used in furniture production to reduce waste and improve efficiency by minimizing non-value adding activities and optimizing production processes.
- Effective materials management strategies, such as just-in-time inventory and waste reduction programs, can help furniture companies reduce waste and improve efficiency.
- Recycling and upcycling can provide numerous benefits to furniture production, including reducing waste, decreasing environmental impact, and increasing customer appeal.
- MRP and ERP systems can assist furniture companies in reducing waste and maximizing efficiency by providing tools for managing inventory levels, production schedules, and material tracking.
- Furniture companies that successfully implement these strategies and principles can benefit from reduced costs, increased productivity, and improved environmental sustainability.
Related Articles
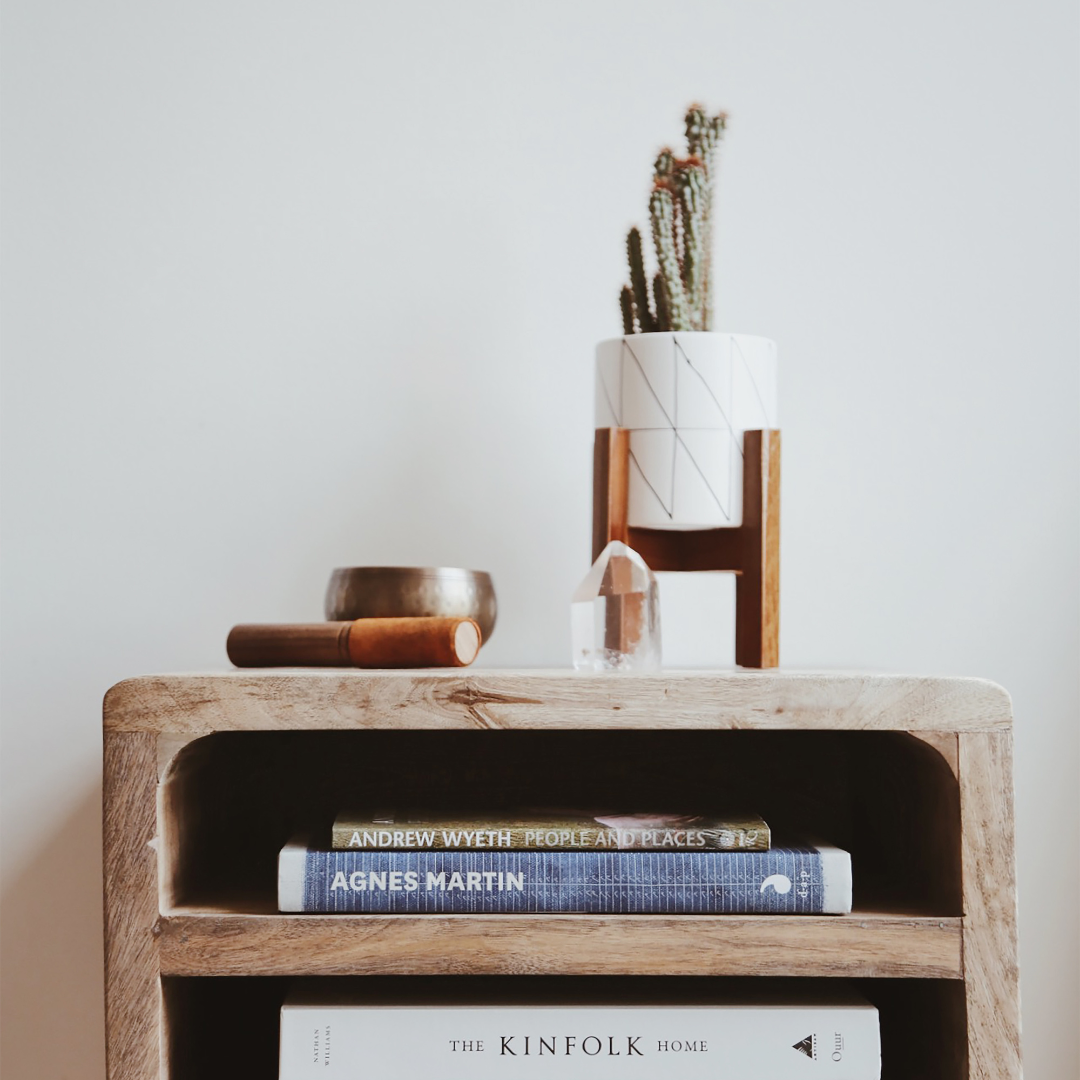
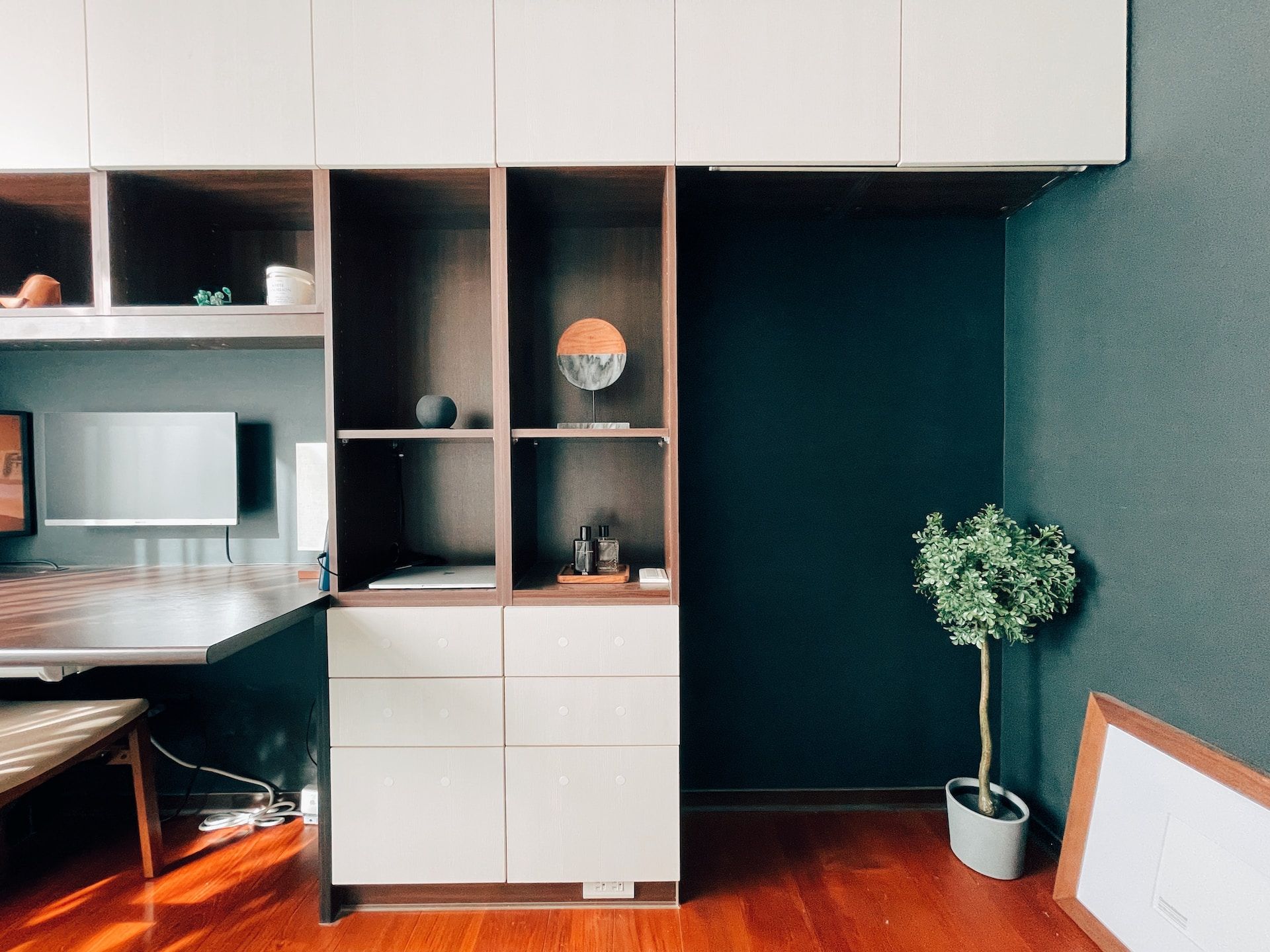
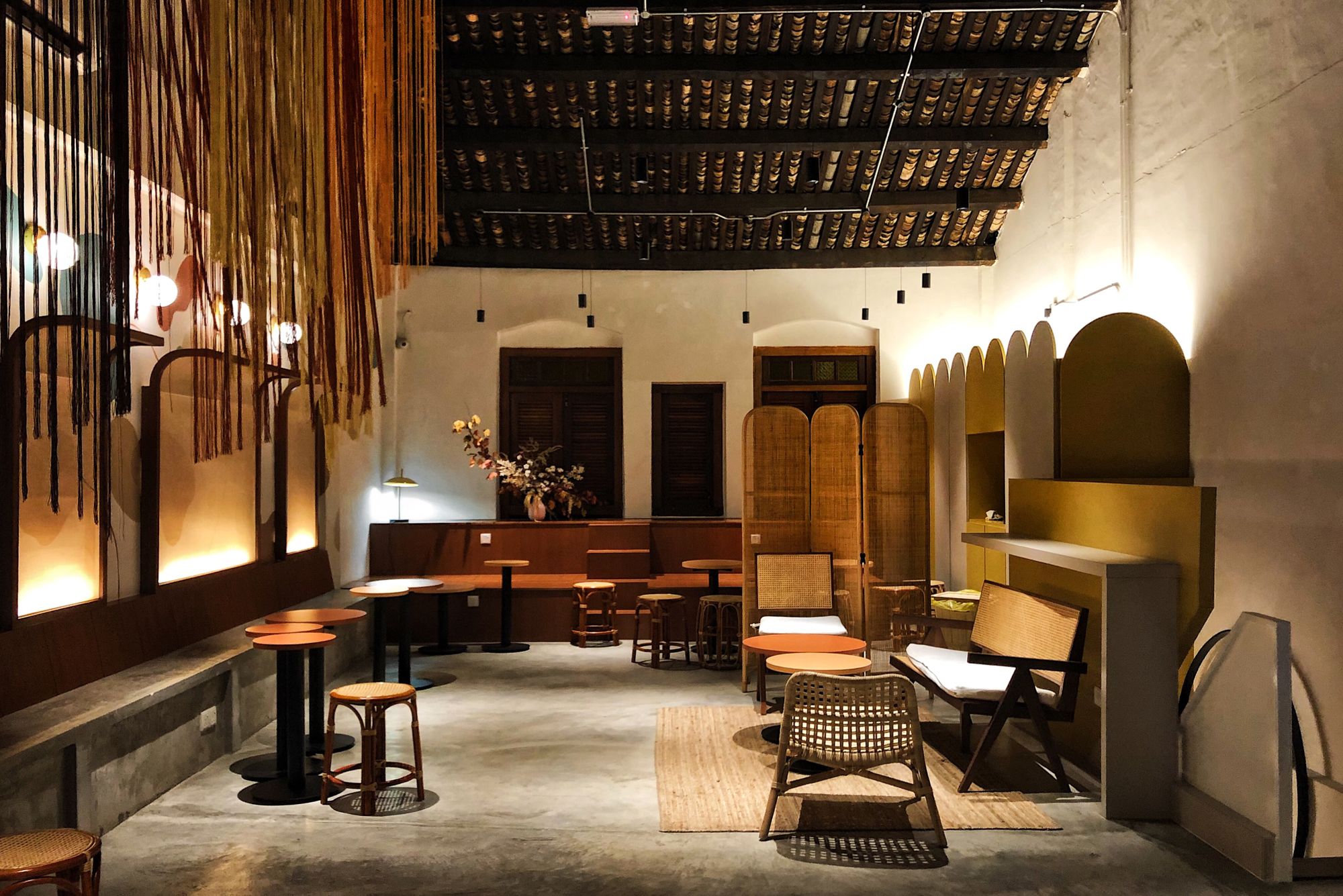