The use of automation and digital technologies in wood manufacturing is expected to reduce production costs by up to 30% by 2030. These technologies can help optimize production processes, reduce waste, and increase efficiency. (Source: McKinsey & Company)
The implementation of lean manufacturing principles in wood manufacturing can lead to a 20-30% reduction in production costs. This can be achieved by optimizing production processes, reducing waste, and improving efficiency. (Source: IndustryWeek)
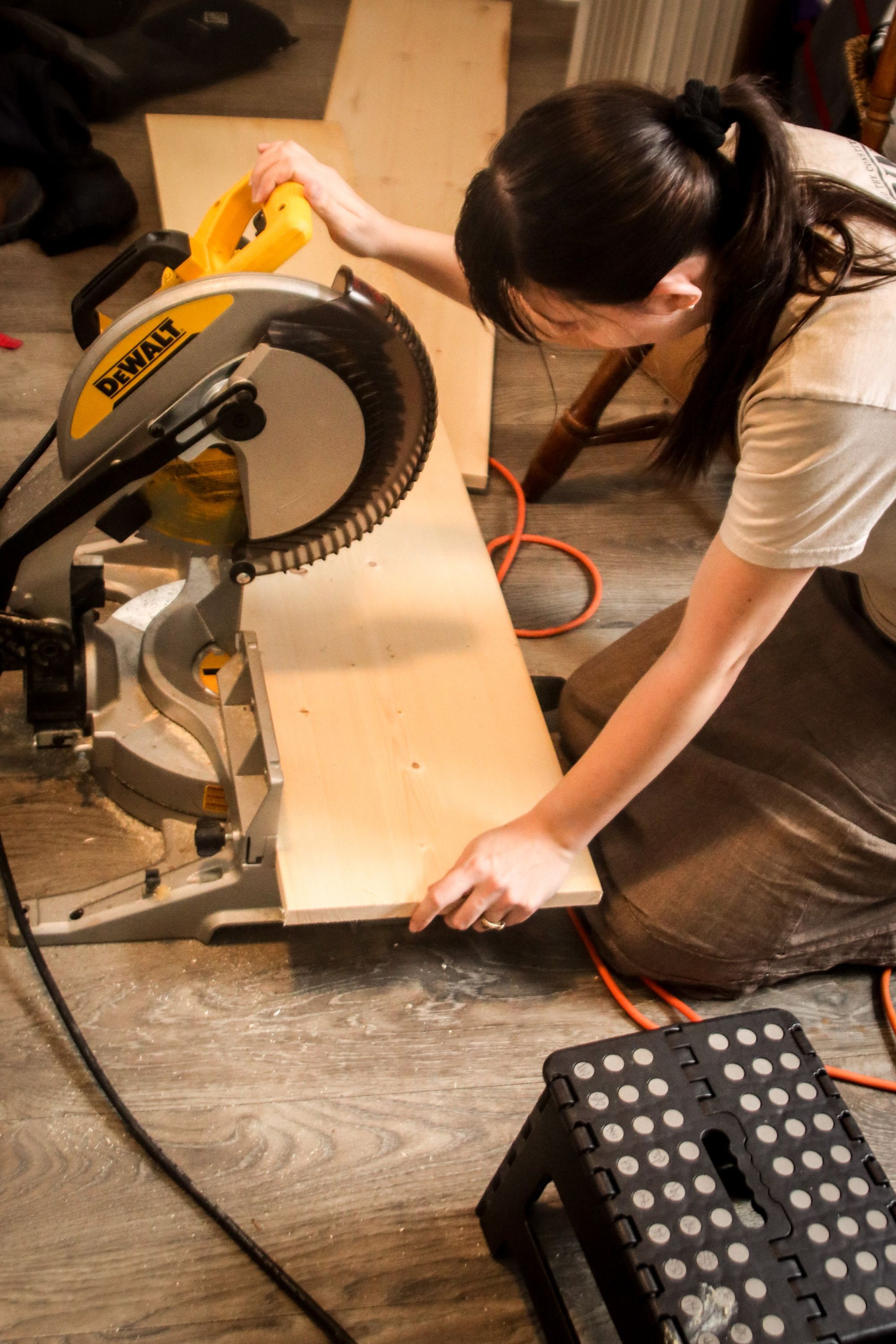
The use of sustainable materials and practices in wood manufacturing can help reduce costs by up to 15%. This can be achieved by minimizing waste, reducing energy consumption, and optimizing transportation. (Source: Accenture)
The adoption of energy-efficient practices in wood manufacturing can lead to a 10-15% reduction in energy costs. This can be achieved by using energy-efficient equipment, optimizing production processes, and reducing energy consumption in buildings. (Source: US Department of Energy)
All of these statistics highlight the different strategies that can be implemented to reduce the cost of wood manufacturing.
Considering that the global wood products market size is expected to grow from $661.8 billion in 2020 to $797.7 billion in 2025, at a compound annual growth rate (CAGR) of 3.8% due to increasing demand for wood products in construction, furniture, and packaging industries, as well as growing awareness of sustainability practices in wood manufacturing.(Source: MarketsandMarkets)
It is thus important, as well as more profitable, to reduce the cost of wood manufacturing.
This article will be your complete guide to reducing the cost of wood manufacturing by covering the following topics:
- What is Wood Manufacturing?
- What is Leading to the Rising Costs of Wood Manufacturing?
- What are Some Cost Reduction Challenges in Wood Manufacturing?
- Strategies to Reduce the Cost of Wood Manufacturing
- Importance of Reducing the Cost of Wood Manufacturing
- What are Some Sustainable Practices that can Help Reduce the Cost of Wood Manufacturing?
- How will the Implementation of MRP Systems Help in Reducing the Cost of Wood Manufacturing?
- How can Deskera Help You with Wood Manufacturing?
- Key Takeaways
- Related Articles
What is Wood Manufacturing?
Wood manufacturing is the process of transforming raw wood materials into finished products that can be used in various applications. This process typically involves several stages, including logging, sawing, planing, and shaping, and may also include additional processes such as drying, laminating, and finishing.
Wood manufacturing can produce a wide range of products, from simple wooden boards and planks to complex furniture, cabinetry, and architectural elements. It is an important industry in many parts of the world and plays a significant role in the global economy.
In addition to traditional woodworking techniques, modern wood manufacturing often incorporates advanced technologies such as computer-controlled cutting and machining, robotics, and digital design and fabrication tools. These technologies allow for greater precision, efficiency, and customization in the production process.
What is Leading to the Rising Costs of Wood Manufacturing?
There are several factors contributing to the rising costs of wood manufacturing:
- Increased demand: The demand for wood products has risen in recent years due to factors such as population growth, urbanization, and increased construction activity. This has led to higher prices for raw materials, including lumber and other wood products.
- Supply chain disruptions: Uncertain circumstances like the COVID-19 pandemic have disrupted supply chains globally, including those in the wood manufacturing industry. Delays and shortages in raw materials, transportation, and labor have caused prices to increase.
- Tariffs and trade disputes: Tariffs and trade disputes between countries have resulted in higher prices for imported wood products and materials, such as Canadian softwood lumber.
- Environmental regulations: Stricter environmental regulations in some countries have led to higher costs for sustainable sourcing and production of wood products, such as certification and compliance with forest management standards.
- Labor costs: Labor costs have increased in some regions due to factors such as higher minimum wages, labor shortages, and increased competition for skilled workers.
All of these factors contribute to the rising costs of wood manufacturing, making it more challenging for companies to remain competitive in the industry.
What are Some Cost Reduction Challenges in Wood Manufacturing?
There are several cost reduction challenges in wood manufacturing, including:
- Maintaining quality: Cost reduction efforts should not compromise product quality. Maintaining high-quality products is important for customer satisfaction, reputation, and repeat business.
- Fluctuating demand: Wood manufacturing companies may face fluctuating demand due to seasonal variations, economic conditions, or changes in customer preferences. This can make it difficult to plan production schedules, manage inventory, and optimize production processes.
- Managing external factors: External factors such as tariffs, trade regulations, and raw material prices can affect the cost of wood manufacturing. Companies may need to adapt their production processes, sourcing strategies, or pricing models in response to these factors.
- Balancing short-term and long-term goals: Cost reduction efforts should not compromise the long-term sustainability and growth of the company. Companies need to balance short-term cost reduction goals with long-term investment in research and development, employee training, and sustainable practices.
- Finding skilled labor: Wood manufacturing companies may face challenges in finding skilled labor due to a shortage of qualified workers, competition from other industries, or changing skill requirements. This can affect productivity, product quality, and production costs.
Overall, cost reduction efforts in wood manufacturing should be balanced with the need to maintain product quality, adapt to external factors, and invest in long-term sustainability and growth.
Strategies to Reduce the Cost of Wood Manufacturing
There are several strategies that can be implemented to reduce the cost of wood manufacturing:
Use Efficient Production Methods
Using efficient production methods can help to reduce costs associated with labor and improve productivity in wood manufacturing. Here are some ways to achieve this:
- Optimize production schedules: Scheduling production processes efficiently can help to reduce idle time and improve throughput. This can be done by using production planning software, analyzing production data, and implementing a system of standardized work procedures.
- Implement automation and robotics: Automation and robotics can help to reduce labor costs and increase productivity by performing repetitive tasks quickly and accurately. This can include using robots for material handling, CNC machines for cutting and shaping wood, and automated assembly lines.
- Invest in equipment that is energy-efficient and requires minimal maintenance: Investing in equipment that is energy-efficient and requires minimal maintenance can help to reduce energy costs and minimize downtime associated with repairs. This includes using energy-efficient motors, pumps, and lighting systems.
- Use a flexible manufacturing system: Using a flexible manufacturing system can help to reduce costs associated with changing production runs and enable more efficient use of resources. This can include using equipment that can be reconfigured quickly and easily, using computer-controlled machinery, and implementing just-in-time manufacturing.
- Implement a quality control program: Implementing a quality control program can help to reduce costs associated with rework and improve customer satisfaction. This includes implementing a system of standard operating procedures, using statistical process control methods, and providing employee training on quality control principles.
- Use efficient material handling systems: Efficient material handling systems can help to reduce labor costs and minimize damage to materials. This includes using conveyors, forklifts, and automated guided vehicles to move materials quickly and safely.
By implementing these efficient production methods, wood manufacturers can reduce labor costs, improve productivity, and increase their competitiveness in the industry.
Use Sustainable and Renewable Materials
Using sustainable and renewable materials can help to reduce costs associated with raw materials, improve the environmental performance of the company, and enhance its brand reputation. Here are some ways to achieve this:
- Use FSC-certified wood products: Using wood products certified by the Forest Stewardship Council (FSC) can help to ensure that the wood comes from responsibly managed forests. This can help to reduce the risk of legal and reputational problems associated with illegal logging and improve the sustainability of the wood supply.
- Use recycled materials: Using recycled wood or wood-based materials can help to reduce costs associated with raw materials and minimize waste. This can include using recycled pallets or using wood waste as a feedstock for other products, such as composite wood products.
- Explore alternative materials: Exploring alternative materials such as bamboo, agricultural residues, or other biomaterials can help to reduce costs associated with raw materials and improve the environmental performance of the company. For example, bamboo is a fast-growing and renewable resource that can be used as a substitute for wood in many applications.
- Implement a closed-loop system: Implementing a closed-loop system can help to minimize waste and reduce the need for raw materials. This includes using waste from production processes as feedstock for other products, such as using sawdust, as a fuel source for energy generation.
- Use local sourcing: Sourcing materials locally can help to reduce transportation costs and minimize the environmental impact of the supply chain. This includes working with local suppliers to source wood or other materials that are sustainably produced.
By using sustainable and renewable materials, wood manufacturers can reduce costs associated with raw materials, improve the environmental performance of the company, and enhance their brand reputation with consumers who are increasingly concerned about sustainability. This will help you in improving customer retention, customer loyalty, and net revenue of your company.
Optimize Supply Chain Management
There are several ways to optimize supply chain management to reduce the cost of wood manufacturing:
- Improve inventory management: By closely monitoring the inventory levels of raw materials and finished goods, you can avoid stockpiling excess materials or products, which can lead to increased storage costs and waste.
- Streamline transportation: Analyze the shipping routes and modes of transportation used to transport raw materials and finished products. Consider consolidating shipments, using more efficient transportation methods, and negotiating better rates with carriers to reduce transportation costs.
- Implement lean manufacturing principles: Lean manufacturing principles can help you identify and eliminate waste in the production process. By reducing waste, you can reduce production costs and improve efficiency.
- Develop strong supplier relationships: Building strong relationships with suppliers can help you negotiate better pricing and terms for raw materials. It can also help ensure a consistent supply of high-quality materials.
- Implement technology: Consider implementing technology such as inventory management software, transportation management software, and automated production systems. These tools can help you track and manage your supply chain more efficiently, reducing costs and increasing efficiency.
- Use data analysis: By analyzing data on production, inventory, transportation, and supplier performance, you can identify areas where costs can be reduced, and efficiency can be improved. Use this data to make informed decisions and continuously optimize your supply chain management.
Overall, optimizing supply chain management requires a holistic approach that considers all aspects of the supply chain, from raw materials sourcing to finished product delivery.
By implementing the strategies outlined above, you can reduce costs, improve efficiency, and ultimately increase profitability in wood manufacturing.
Reduce Waste
Reducing waste is an effective way to reduce the cost of wood manufacturing. Here are some strategies to consider:
- Implement lean manufacturing principles: Lean manufacturing principles focus on identifying and eliminating waste in the production process. By minimizing waste, you can reduce production costs and improve efficiency. For example, you can reduce overproduction, overprocessing, and defects.
- Optimize raw material usage: Evaluate the use of raw materials in the production process. Look for ways to minimize waste, such as using computerized cutting machines or optimizing the size and shape of the pieces being cut.
- Use recycled materials: Consider using recycled materials in your production process. Using recycled materials reduces the amount of waste generated and can help lower production costs.
- Train employees: Train employees on best practices for reducing waste. For example, teach them how to properly handle and store materials to avoid damage or spoilage.
- Implement waste reduction programs: Implement programs that encourage waste reduction, such as recycling or composting programs. By reducing waste, you can lower disposal costs and even generate revenue from recycled materials.
- Monitor and measure waste: Track and measure the amount of waste generated in your production process. Use this data to identify areas where waste can be reduced and to monitor the effectiveness of your waste reduction strategies.
By implementing these strategies, you can significantly reduce waste and lower the cost of wood manufacturing.
Implement Energy Efficient Practices
Implementing energy-efficient practices can help reduce the cost of wood manufacturing while also reducing the environmental impact of the operation. Here are some strategies to consider:
- Conduct an energy audit: An energy audit can help identify areas where energy is being wasted and opportunities for energy efficiency. The audit will provide a detailed analysis of energy usage and help prioritize areas for improvement.
- Upgrade lighting: Replace inefficient lighting with energy-efficient LED bulbs. LED lighting uses significantly less energy and lasts longer than traditional lighting, reducing maintenance costs.
- Optimize equipment: Optimize the use of equipment such as compressors, pumps, and motors to reduce energy consumption. Regular maintenance and tuning of equipment can help optimize performance and reduce energy waste.
- Improve insulation: Properly insulate buildings and equipment to reduce energy waste from heating and cooling. Insulation will also help maintain a consistent temperature inside the building, reducing the need for heating and cooling.
- Use renewable energy sources: Consider using renewable energy sources such as solar, wind, or geothermal energy to power the operation. Investing in renewable energy can reduce energy costs over the long term and reduce reliance on non-renewable energy sources.
- Implement energy-efficient processes: Identify areas of the production process where energy is being wasted and implement energy-efficient practices. For example, optimizing the drying process can significantly reduce energy consumption.
By implementing these strategies, you can significantly reduce energy costs and improve the sustainability of your wood manufacturing operation.
Use Digital Technologies
Digital technologies can help reduce the cost of wood manufacturing by increasing efficiency and optimizing production processes. Here are some strategies to consider:
- Implement automation: Automated systems can help streamline production processes and reduce labor costs. For example, you can use automated saws or sorting systems to increase efficiency and reduce waste.
- Use computer-aided design (CAD): CAD software can help optimize the use of raw materials, reduce waste, and improve product quality. CAD can also help speed up the design process and reduce design errors.
- Implement a manufacturing execution system (MES): MES software can help manage the production process, from raw materials to finished products. The system can help optimize production, reduce waste, and improve quality control.
- Use sensors and monitoring systems: Sensors and monitoring systems can help track the performance of equipment and identify issues before they become costly problems. For example, sensors can detect when equipment needs maintenance or when a machine is about to fail.
- Implement a digital supply chain: A digital supply chain can help optimize the flow of materials and products, reduce lead times, and improve inventory management. A digital supply chain can also help reduce transportation costs by optimizing shipping routes.
- Use virtual reality (VR) and augmented reality (AR): VR and AR can be used to simulate production processes, train employees, and optimize the use of equipment. For example, AR can be used to provide real-time instructions to operators, reducing the need for training and improving production efficiency.
By implementing these strategies, you can improve the efficiency of your wood manufacturing operation, reduce costs, and improve quality control.
Implement Lean Manufacturing Principles
Implementing lean manufacturing principles can help reduce the cost of wood manufacturing by eliminating waste, improving efficiency, and optimizing processes. Here are some strategies to consider:
- Identify and eliminate waste: Identify all forms of waste in the production process, including overproduction, overprocessing, waiting, defects, excess inventory, unnecessary motion, and underutilized talent. Once identified, eliminate or reduce waste through the implementation of lean manufacturing techniques.
- Improve flow: Streamline the production process by improving flow. Minimize delays, bottlenecks, and downtime. Reduce setup times, batch sizes, and changeovers to improve flow and increase production efficiency.
- Standardize work: Establish standard work procedures to ensure consistency and quality. Document procedures and train employees on how to follow them. This will help reduce variability and improve product quality.
- Empower employees: Empower employees to identify and solve problems. Provide them with the tools, training, and resources needed to improve processes and reduce waste. Encourage continuous improvement through regular feedback and communication.
- Implement a pull system: Implement a pull system to control inventory levels and reduce waste. This system ensures that production is only initiated when there is a demand for the product, which reduces the risk of overproduction.
- Continuously improve: Continuously evaluate the production process to identify areas for improvement. Use data and feedback to make informed decisions and implement changes as needed. Encourage a culture of continuous improvement to ensure that the process is always improving.
By implementing lean manufacturing principles, you can significantly reduce the cost of wood manufacturing while improving quality and efficiency.
Invest in Employee Training
Investing in employee training can help reduce the cost of wood manufacturing by improving efficiency, reducing errors, and increasing productivity. Here are some strategies to consider:
- Cross-train employees: Cross-training employees in different areas of the production process can improve flexibility and reduce downtime. This will ensure that production can continue even if an employee is absent, and it will improve the overall efficiency of the operation.
- Train employees on new technologies: Training employees on new technologies can help increase efficiency and reduce errors. For example, training employees on computer-aided design (CAD) software can improve design accuracy and reduce waste.
- Provide safety training: Safety training is essential for preventing accidents and reducing the cost of workplace injuries. Employees should be trained on proper safety procedures and the correct use of protective equipment.
- Provide ongoing training: Provide ongoing training to keep employees up-to-date with new technologies and best practices. This will ensure that employees are continuously improving and that the operation is staying competitive.
- Train employees on problem-solving: Train employees on problem-solving techniques to empower them to identify and solve problems on their own. This will improve the overall efficiency of the operation and reduce the risk of errors and waste.
- Encourage a culture of learning: Encourage a culture of learning by providing opportunities for employees to attend training courses, conferences, and workshops. This will foster a culture of continuous improvement and help keep the operation competitive.
By investing in employee training, you can improve the efficiency of your wood manufacturing operation, reduce errors, and increase productivity.
Implement Sustainable Practices
Implementing sustainable practices can help reduce the cost of wood manufacturing by reducing waste, increasing efficiency, and improving product quality. Here are some strategies to consider:
- Use sustainable materials: Use sustainable and responsibly-sourced materials, such as FSC-certified wood, to reduce the environmental impact of the manufacturing process. This can also help improve the reputation of the company and attract environmentally-conscious customers.
- Reduce waste: Implement waste reduction strategies, such as recycling, composting, and reusing materials, to reduce the amount of waste produced during the manufacturing process. This can help reduce waste disposal costs and improve the environmental impact of the operation.
- Use energy-efficient equipment: Use energy-efficient equipment and processes to reduce energy consumption and lower energy costs. This can include upgrading lighting systems, optimizing HVAC systems, and using energy-efficient machinery.
- Optimize transportation: Optimize transportation by using fuel-efficient vehicles, optimizing delivery routes, and reducing transportation distances. This can help reduce transportation costs and lower the carbon footprint of the operation.
- Implement water conservation practices: Implement water conservation practices, such as collecting and reusing rainwater or installing low-flow fixtures, to reduce water consumption and lower water bills.
- Encourage a culture of sustainability: Encourage employees to embrace sustainable practices by promoting environmental awareness and providing training on sustainability initiatives. This can also help improve the reputation of the company and attract environmentally-conscious customers.
By implementing sustainable practices, you can reduce the cost of wood manufacturing while improving the environmental impact of the operation. Additionally, adopting sustainable practices can improve the reputation of the company and attract environmentally-conscious customers.
Using Alternative Materials
Using alternative materials is a potential cost-reduction strategy for wood manufacturing companies. The cost of wood is affected by factors such as supply and demand, transportation costs, and environmental regulations, which can cause price fluctuations and impact profit margins.
By using alternative materials, companies can potentially reduce their reliance on wood and mitigate the impact of these cost factors.
Some alternative materials that wood manufacturing companies can consider include:
- Engineered wood products: These products are made from wood fibers, chips, or veneers bonded together with adhesives to form composite materials. They offer similar properties to solid wood but can be less expensive and more sustainable.
- Bamboo: Bamboo is a fast-growing plant that can be used as an alternative to wood. It has similar properties to wood, including strength and durability, but grows much faster than trees and is, therefore, more sustainable.
- Agricultural residues: Agricultural residues such as straws, husks, and stalks can be used to produce composite materials that can be used as a substitute for wood.
- Recycled materials: Recycled materials such as plastic, rubber, and glass can be used to produce composite materials that can be used as a substitute for wood.
- Natural fibers: Natural fibers such as hemp, flax, and jute can be used to produce composite materials that can be used as a substitute for wood.
While using alternative materials can help reduce the cost of wood manufacturing, it is important to consider factors such as availability, quality, and sustainability.
Companies should conduct a thorough analysis of the costs and benefits of using alternative materials and ensure that they meet industry standards and regulations.
Importance of Reducing the Cost of Wood Manufacturing
Reducing the cost of wood manufacturing is important for several reasons:
- Competitive advantage: In today's competitive business environment, it is essential to keep costs low to remain competitive. By reducing the cost of wood manufacturing, companies can offer more competitive pricing to their customers, which can help them gain a competitive advantage over their competitors.
- Increased profitability: Reducing the cost of wood manufacturing can help increase profitability by improving profit margins. By reducing costs, companies can increase their profits without having to increase their prices, which can help them remain competitive in the market.
- Improved efficiency: By implementing cost reduction strategies, companies can improve their efficiency, which can help them produce products faster and with fewer errors. This can result in increased productivity, improved product quality, and faster delivery times.
- Sustainable practices: Reducing the cost of wood manufacturing can also lead to the adoption of more sustainable practices. By reducing waste, conserving resources, and using energy-efficient equipment, companies can reduce their environmental impact and contribute to a more sustainable future.
- Employee satisfaction: By reducing costs, companies can also invest more in their employees, such as by offering better wages, benefits, and training opportunities. This can help improve employee satisfaction, which can lead to increased productivity, higher quality work, and a lower employee turnover rate.
Overall, reducing the cost of wood manufacturing is important for improving profitability, competitiveness, efficiency, sustainability, and employee satisfaction.
What are Some Sustainable Practices that can Help Reduce the Cost of Wood Manufacturing?
There are several sustainable practices that can help reduce the cost of wood manufacturing, including:
- Using sustainable materials: Using sustainably-sourced wood and other materials can help reduce the cost of wood manufacturing by reducing waste, minimizing legal liabilities, and attracting environmentally-conscious customers.
- Reducing waste: Implementing waste reduction measures such as recycling, reusing materials, and minimizing scrap can help reduce the cost of wood manufacturing by reducing the need to purchase new materials and minimizing disposal costs.
- Using energy-efficient equipment: Using energy-efficient equipment such as energy-efficient lighting and HVAC systems and using machines with energy-saving features can help reduce energy consumption and lower energy costs.
- Optimizing transportation: Optimizing transportation by using fuel-efficient vehicles, consolidating shipments, and reducing unnecessary trips can help reduce transportation costs and carbon emissions.
- Encouraging a culture of sustainability: Encouraging employees to adopt sustainable practices such as turning off lights when leaving a room, using reusable water bottles, and reducing paper usage can help reduce the cost of wood manufacturing by reducing energy consumption and waste.
Overall, adopting sustainable practices can help reduce the cost of wood manufacturing by reducing waste, minimizing legal liabilities, attracting environmentally-conscious customers, reducing energy consumption, lowering transportation costs, and improving efficiency.
How will the Implementation of MRP Systems Help in Reducing the Cost of Wood Manufacturing?
The implementation of Material Requirements Planning (MRP) systems can help in reducing the cost of wood manufacturing in several ways:
- Improved inventory management: MRP systems can help companies optimize their inventory levels by tracking usage, lead times, and reorder points. By having the right amount of inventory on hand, companies can reduce inventory carrying costs, minimize waste, and avoid stockouts.
- Reduced material waste: MRP systems can help minimize material waste by calculating the exact amount of material needed for each production order. This can help reduce scrap and overproduction, resulting in lower material costs.
- Improved scheduling: MRP systems can help optimize production schedules by considering the availability of materials, equipment, and labor. This can help reduce idle time, improve throughput, and increase efficiency.
- Reduced lead times: MRP systems can help reduce lead times by providing accurate delivery dates for raw materials and finished goods. This can help improve customer satisfaction and reduce the cost of expedited shipping.
- Increased accuracy: MRP systems can help improve the accuracy of production planning and forecasting, resulting in fewer errors and less rework. This can help reduce labor costs and improve product quality.
Overall, the implementation of MRP systems can help wood manufacturing companies reduce costs by improving inventory management, reducing material waste, improving scheduling, reducing lead times, and increasing accuracy. This can lead to increased efficiency, productivity, and profitability.
How can Deskera Help You with Wood Manufacturing?
Deskera is a material requirements planning (MRP) software solution that can help wood manufacturing companies manage their operations more efficiently and effectively. Some ways Deskera can help include:
- Supply chain management: Deskera MRP can help wood manufacturing companies optimize their supply chain management by tracking inventory levels, managing suppliers, and streamlining procurement processes.
- Manufacturing operations: Deskera MRP can help wood manufacturing companies manage their manufacturing operations by optimizing production schedules, tracking work orders, and monitoring production costs.
- Financial management: Deskera Books can help wood manufacturing companies manage their finances by automating accounting processes, generating financial reports, and managing cash flow.
- Sales and customer management: Deskera CRM can help wood manufacturing companies manage their sales and customer relationships by tracking customer interactions, managing leads and opportunities, and providing customer support.
- Project management: Deskera MRP can help wood manufacturing companies manage their projects by tracking tasks, managing resources, and monitoring project timelines and budgets.
Key Takeaways
Reducing the cost of wood manufacturing is a key priority for companies in the industry, as it can help improve competitiveness, profitability, and sustainability.
Wood manufacturing companies face a range of cost challenges, such as fluctuating demand, raw material prices, and labor shortages, which can impact their profitability and growth prospects.
To overcome these challenges, companies are adopting a range of cost-reduction strategies, such as:
- Use efficient production methods: Implementing efficient production methods can help to reduce labor costs and improve productivity. This includes optimizing production schedules, using automation and robotics to reduce labor costs, and investing in equipment that is energy-efficient and requires minimal maintenance.
- Use sustainable and renewable materials: Sourcing materials from sustainable and renewable sources can help to reduce the cost of raw materials and improve the environmental performance of the company. This includes using FSC-certified wood products, using recycled materials, and exploring alternative materials such as bamboo or agricultural residues.
- Optimize supply chain management: Optimizing supply chain management can help to reduce costs associated with transportation, inventory management, and procurement. This includes working closely with suppliers to negotiate better prices, reducing lead times, and implementing just-in-time inventory systems.
- Reduce waste: Reducing waste can help to reduce disposal costs and minimize the use of raw materials. This includes implementing waste reduction and recycling programs, using waste as a source of energy, and optimizing production processes to reduce waste.
- Implement energy-efficient practices: Implementing energy-efficient practices can help to reduce energy costs and improve the environmental performance of the company. This includes using energy-efficient equipment, implementing lighting and HVAC systems that reduce energy consumption, and optimizing production processes to minimize energy use.
- Use digital technologies: Using digital technologies such as CAD/CAM software, CNC machines, and 3D printing can help to reduce costs associated with design, prototyping, and production. These technologies can also help to improve accuracy, efficiency, and customization.
- Implement lean manufacturing principles: Implementing lean manufacturing principles can help to reduce waste, improve efficiency, and increase productivity. This includes implementing continuous improvement programs, streamlining production processes, and eliminating non-value-added activities.
- Invest in employee training: Investing in employee training can help to improve productivity, reduce errors, and increase employee engagement. This includes providing training in safety, quality control, and job-specific skills.
- Implement sustainable practices: Implementing sustainable practices can help to improve the environmental and social performance of the company. This includes implementing sustainable sourcing policies, reducing carbon emissions, and engaging in responsible forest management practices.
- Use alternative materials: Consider using alternative materials that can replace or supplement traditional wood products. For example, using engineered wood products, such as laminated veneer lumber or oriented strand board, can reduce the cost of raw materials while still providing the necessary strength and durability.
By implementing these strategies, wood manufacturers can reduce their costs and improve their competitiveness in the industry while also improving their environmental and social performance.
Overall, Deskera can provide wood manufacturing companies with a comprehensive MRP solution that can help them streamline their operations, reduce costs, and improve efficiency and profitability.
Related Articles
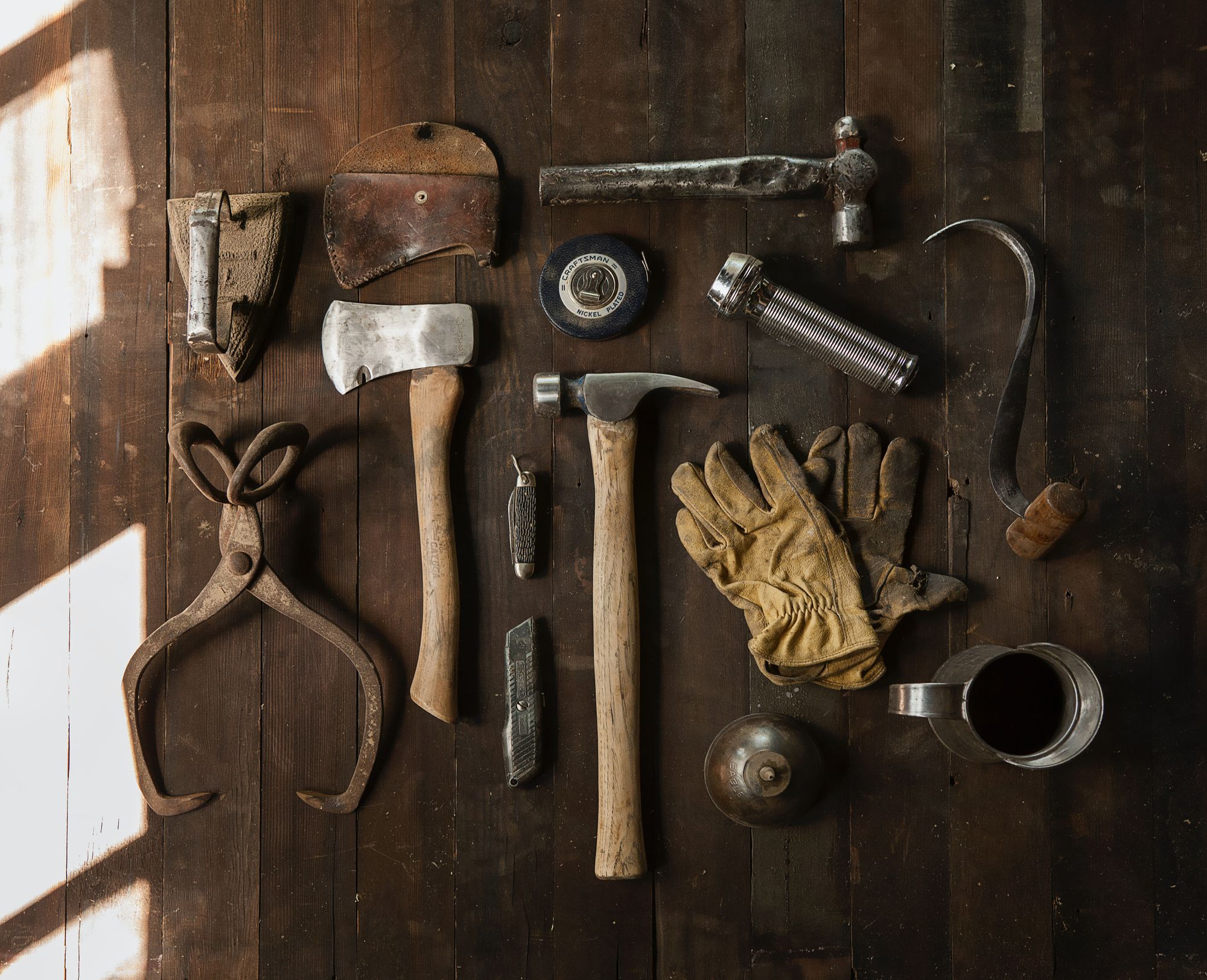
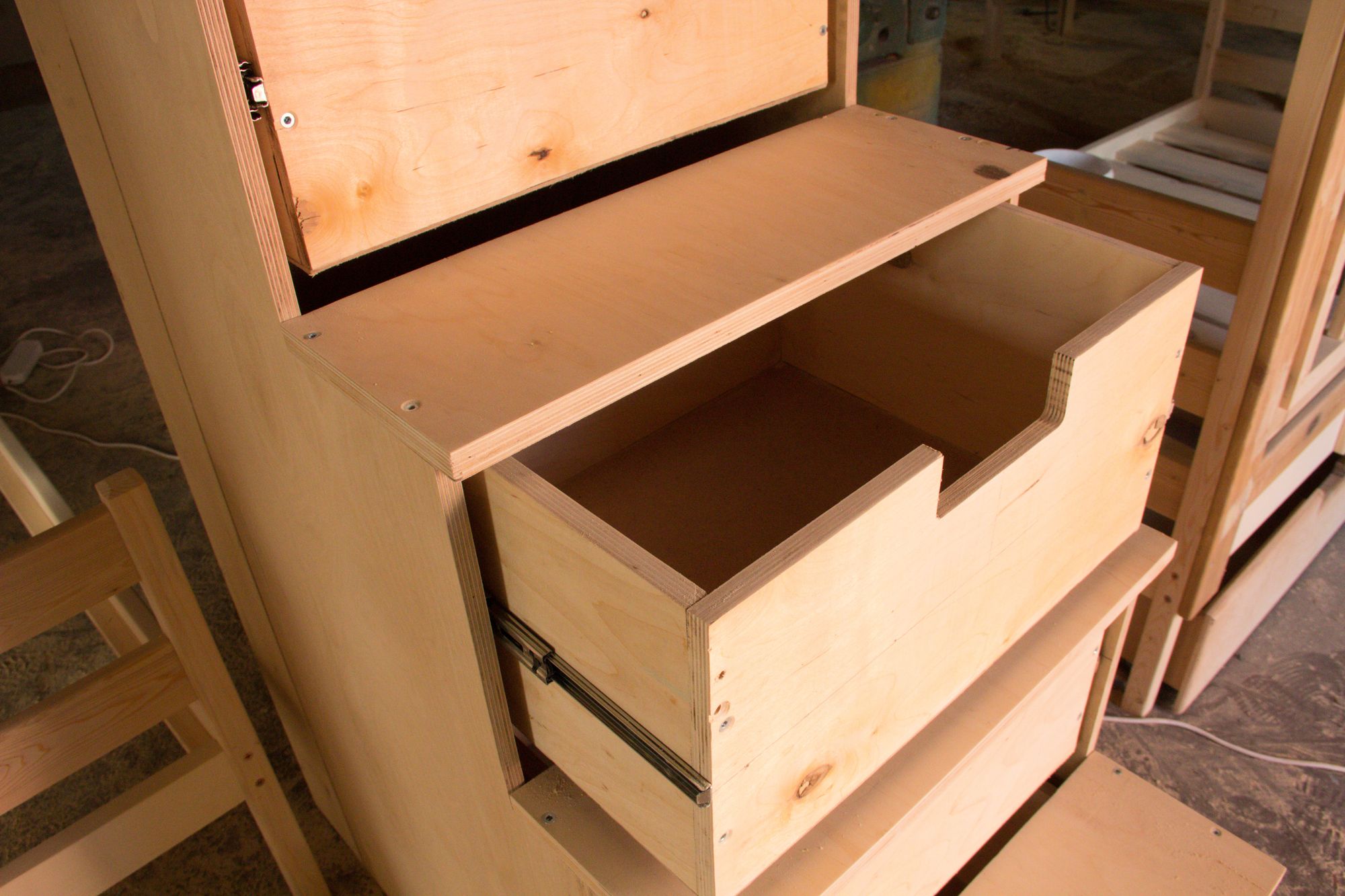
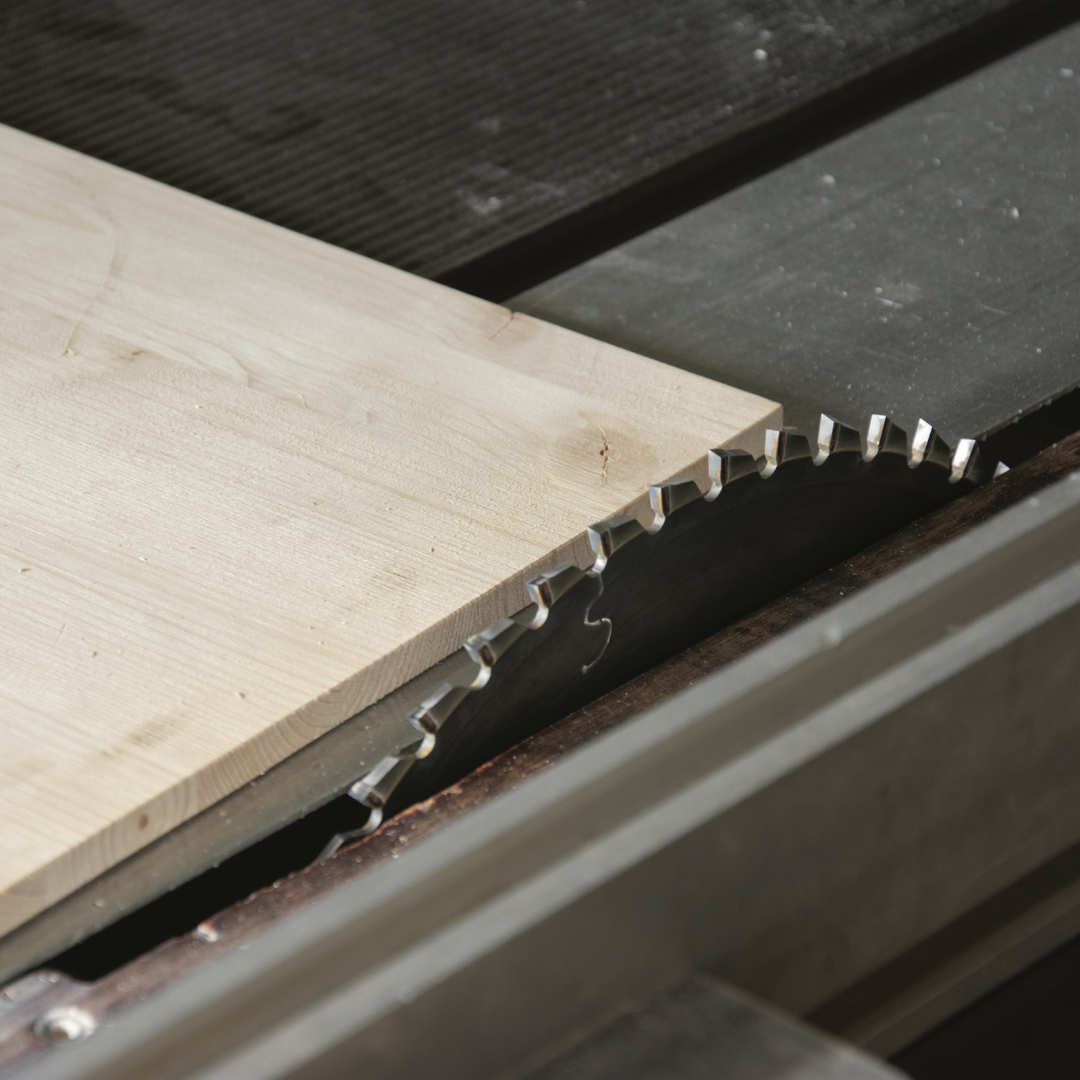
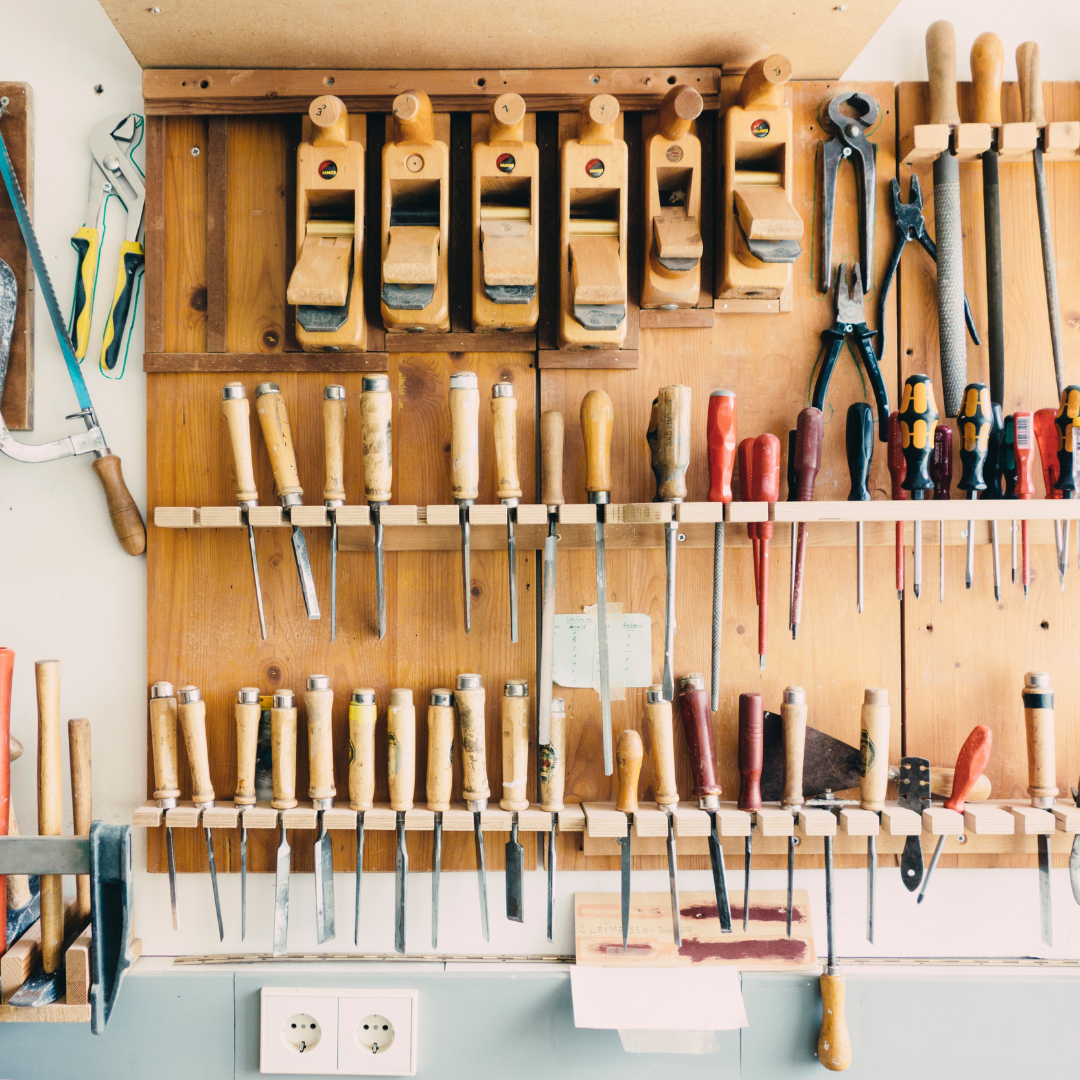