The global food manufacturing industry is one of the most significant contributors to the economy, employing millions of people and providing food to billions worldwide. However, the cost of producing food is a significant challenge for manufacturers, and reducing these costs has become a crucial goal for companies operating in this industry.
While maintaining food quality and safety standards, manufacturers must find ways to cut costs without compromising on the quality of the food they produce.
Reducing the cost of food manufacturing is essential because it can make food more affordable for consumers, increase profits for manufacturers, and improve the industry's competitiveness. With the increasing demand for food, manufacturers are under pressure to produce more while keeping costs low, making cost reduction strategies even more critical.
In today's world, where sustainability and efficiency are critical, manufacturers are exploring innovative ways to reduce their manufacturing costs. This includes adopting cost-effective production techniques, optimizing the supply chain, reducing energy consumption, and investing in technology and automation.
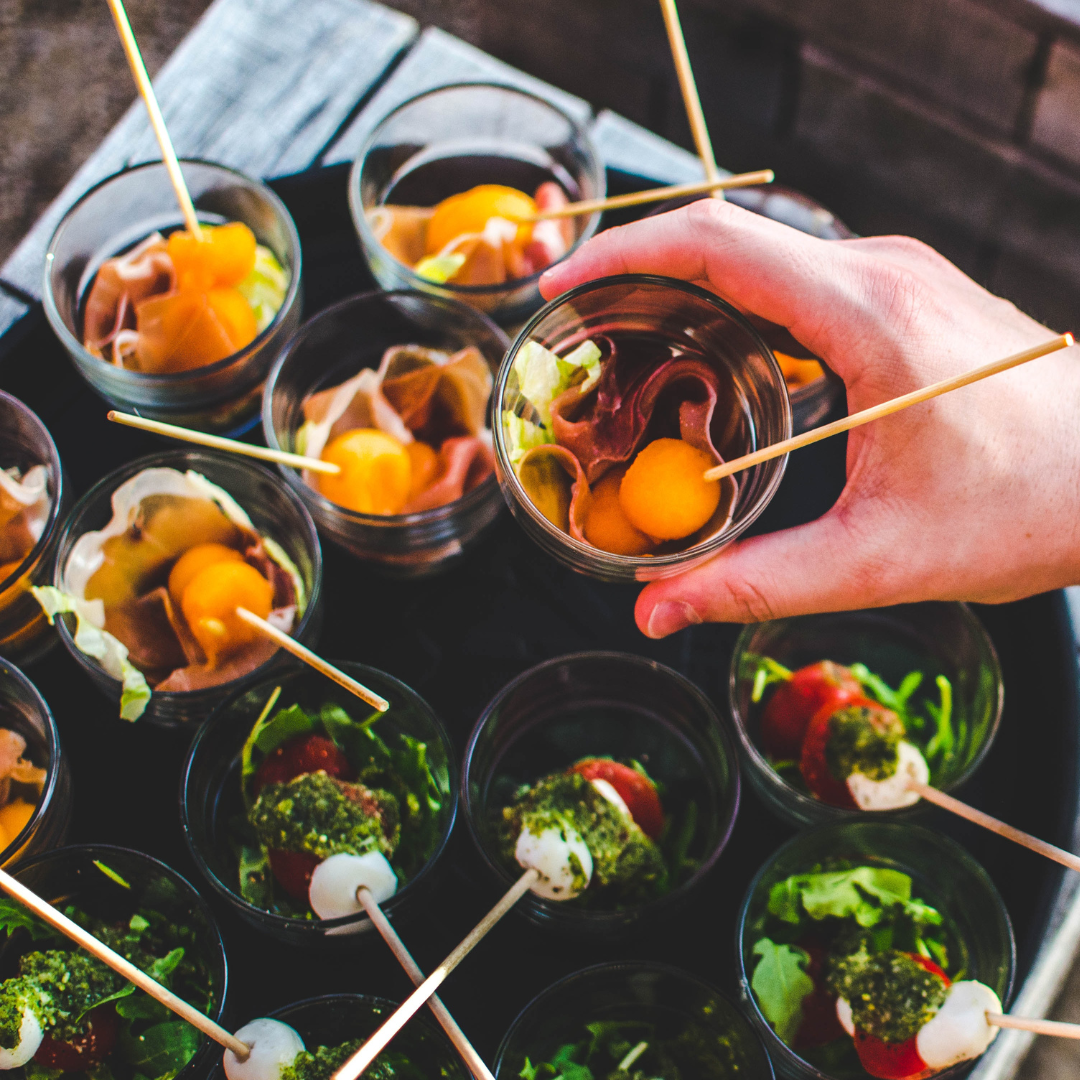
In this article, we will explore some of the most effective strategies that manufacturers can use to reduce their food production costs. We will examine the various cost drivers in the industry and discuss practical solutions that companies can adopt to achieve significant cost savings.
By implementing these strategies, food manufacturers can improve their bottom line and ensure that they can continue to provide high-quality food to consumers at an affordable price.
- Importance of Cost Reduction in the Food Manufacturing Industry
- Analyzing the Cost Structure of Food Manufacturing
- Areas Where the Most Significant Cost Savings can be Achieved
- Impact of Raw Material Prices, Labor Costs, Energy Costs, and Equipment Maintenance Costs on the Overall Cost Structure
- Adopting Cost-Effective Production Techniques
- Optimizing the Supply Chain to Reduce Costs
- Reducing Energy Consumption to Reduce Production Costs
- Improving Inventory Management to Reduce Costs
- Employee Training and Development to Reduce Cost of Food Manufacturing
- How can MRP and ERP systems Assist in Reducing Costs in Food Manufacturing?
- How can Deskera Help You?
- Key Takeaways
- Related Articles
Importance of Cost Reduction in the Food Manufacturing Industry
Cost reduction is essential in the food manufacturing industry because it can impact the bottom line of companies, increase profitability, and enhance competitiveness. The cost of manufacturing food can significantly impact a company's profit margins, which is why reducing these costs is crucial. By reducing costs, companies can offer competitive prices to consumers, which can increase demand and sales volume.
Additionally, cost reduction can enable companies to invest in research and development, improving their products' quality, and ensuring that they remain relevant in the market. Cost reduction can also help manufacturers remain competitive in the face of rising costs of raw materials, labor, and energy. With increased competition and pressure to maintain high-quality standards, cost reduction has become a vital strategy for survival in the industry.
Furthermore, reducing costs can lead to more sustainable practices, which is increasingly important in today's environmentally conscious society. By reducing waste and energy consumption, companies can reduce their carbon footprint and contribute to a more sustainable future. Sustainable practices can also enhance a company's reputation, attracting environmentally conscious consumers and boosting sales.
In summary, cost reduction is crucial in the food manufacturing industry because it can increase profitability, enhance competitiveness, enable investment in research and development, and promote sustainability. Companies that implement effective cost reduction strategies can achieve significant cost savings, improve their bottom line, and ensure that they remain competitive in the market.
Analyzing the Cost Structure of Food Manufacturing
Analyzing the cost structure of food manufacturing is an essential step in identifying areas where cost savings can be achieved. The main cost drivers in food manufacturing include raw materials, labor, energy, and equipment maintenance costs.
Raw materials costs are a significant cost driver in food manufacturing, and fluctuations in these costs can significantly impact a company's profit margins. To reduce these costs, manufacturers can explore alternative suppliers, negotiate prices, and optimize their raw material inventory management to reduce waste.
Labor costs are also a significant expense in food manufacturing, and reducing these costs can be challenging due to the industry's labor-intensive nature. Manufacturers can explore automation and lean manufacturing techniques to reduce labor costs while maintaining quality standards. Additionally, optimizing scheduling and improving employee training can help reduce labor costs.
Energy costs are another significant expense in food manufacturing, and reducing these costs can be achieved through various energy-saving initiatives. Manufacturers can invest in renewable energy sources, such as solar or wind power, and upgrade to energy-efficient equipment. Additionally, implementing best practices in equipment maintenance can help reduce energy consumption.
Equipment maintenance costs are also a significant cost driver in food manufacturing. To reduce these costs, companies can implement preventative maintenance programs to ensure equipment is in good working order and reduce the risk of breakdowns. Regular maintenance can also help extend the lifespan of equipment, reducing the need for costly repairs or replacements.
In conclusion, analyzing the cost structure of food manufacturing is critical in identifying areas where cost savings can be achieved. By understanding the main cost drivers in the industry, manufacturers can implement effective cost reduction strategies, such as optimizing raw materials, labor, energy, and equipment maintenance costs.
By reducing costs, manufacturers can improve their bottom line and remain competitive in the industry.
Areas where the Most Significant Cost Savings Can Be Achieved
In food manufacturing, there are several areas where significant cost savings can be achieved. By identifying these areas and implementing effective cost reduction strategies, manufacturers can improve their profitability and competitiveness.
Here are some of the main areas where the most significant cost savings can be achieved:
- Raw materials: Raw materials are a significant cost driver in food manufacturing. By optimizing inventory management and negotiating prices with suppliers, manufacturers can achieve significant cost savings. Additionally, by exploring alternative suppliers and reducing waste, companies can reduce their raw material costs.
- Labor: Labor costs are another significant expense in food manufacturing, and reducing these costs can be achieved through automation, lean manufacturing techniques, and optimizing scheduling. Additionally, improving employee training can lead to more efficient and productive workers, reducing the need for additional staff.
- Energy: Energy costs are a significant expense in food manufacturing, and implementing energy-saving initiatives can lead to significant cost savings. By investing in renewable energy sources, upgrading to energy-efficient equipment, and implementing best practices in equipment maintenance, manufacturers can reduce their energy consumption and costs.
- Packaging: Packaging costs can be a significant expense in food manufacturing. By exploring alternative packaging materials and reducing waste, companies can achieve significant cost savings. Additionally, by optimizing packaging design and size, manufacturers can reduce transportation costs, leading to further cost savings.
- Supply chain: Optimizing the supply chain can lead to significant cost savings in food manufacturing. By reducing transportation costs, optimizing inventory levels, and streamlining logistics, manufacturers can reduce their overall costs.
There are several areas where significant cost savings can be achieved in food manufacturing. By implementing effective cost reduction strategies in these areas, manufacturers can improve their profitability and competitiveness in the industry.
Impact of Raw Material Prices, Labor Costs, Energy Costs, and Equipment Maintenance Costs on the Overall Cost Structure
Raw material prices, labor costs, energy costs, and equipment maintenance costs are significant drivers of the overall cost structure in food manufacturing. Let's take a closer look at how each of these cost drivers can impact the overall cost structure.
- Raw material prices: Raw materials are one of the most significant cost drivers in food manufacturing. Fluctuations in raw material prices can have a significant impact on a company's profitability. When raw material prices increase, manufacturers may need to pass these costs onto consumers or absorb the additional costs, reducing their profit margins. Alternatively, manufacturers can explore alternative suppliers, negotiate prices, and optimize inventory management to reduce their raw material costs.
- Labor costs: In this labor-intensive industry, reducing labor costs while maintaining quality standards can be a challenging task. When labor costs increase, manufacturers may need to reduce their workforce or automate processes to reduce labor costs. Additionally, optimizing scheduling and improving employee training can help reduce labor costs.
- Energy costs: Energy costs are another significant cost driver in food manufacturing. The industry relies heavily on energy for food processing and packaging, making energy-saving initiatives critical to reducing costs. When energy costs increase, manufacturers may need to explore renewable energy sources, upgrade to energy-efficient equipment, or implement best practices in equipment maintenance to reduce energy consumption and costs.
- Equipment maintenance costs: Equipment maintenance costs are another significant cost driver in food manufacturing. When equipment breaks down, manufacturers may need to replace or repair it, incurring additional costs. Preventative maintenance programs can help reduce equipment maintenance costs by ensuring that equipment is in good working order and reducing the risk of breakdowns. Regular maintenance can also help extend the lifespan of equipment, reducing the need for costly repairs or replacements.
By understanding these cost drivers and implementing effective cost reduction strategies, manufacturers can improve their profitability and remain competitive in the industry.
Adopting Cost-Effective Production Techniques
Adopting cost-effective production techniques is crucial in food manufacturing to achieve significant cost savings and improve overall profitability. Here are some production techniques that can help reduce costs:
- Lean manufacturing: Lean manufacturing is a production technique that aims to reduce waste and improve efficiency. By eliminating non-value-added activities and streamlining processes, manufacturers can reduce costs and increase productivity. Implementing lean manufacturing techniques can help reduce labor costs, raw material costs, and energy costs.
- Automation: Automation involves the use of machines and robotics to perform repetitive tasks, reducing the need for human labor. Automation can significantly reduce labor costs and improve efficiency, leading to faster production times and increased output.
- Just-in-time (JIT) manufacturing: JIT manufacturing is a production technique that involves producing goods only when they are needed, reducing inventory levels and the associated costs. JIT manufacturing can also help reduce waste and improve efficiency by eliminating excess inventory and reducing the risk of product obsolescence.
- Continuous Improvement: Continuous improvement involves continually reviewing and optimizing production processes to improve efficiency and reduce costs. This technique can help identify areas for improvement, such as reducing downtime, improving quality control, and reducing waste.
- Outsourcing: Outsourcing involves using external suppliers or contractors to perform certain tasks, such as packaging or transportation. Outsourcing can help reduce labor and equipment costs, as well as reduce the need for capital investment in equipment and facilities.
Thus, adopting cost-effective production techniques is essential in food manufacturing to remain competitive in the industry. By implementing lean manufacturing, automation, JIT manufacturing, continuous improvement, and outsourcing, manufacturers can significantly reduce costs and improve their profitability. It is crucial to assess each technique's benefits and potential drawbacks and implement them appropriately to achieve the desired results.
Optimize the Production Process, Reduce Waste, and Improve Efficiency
Optimizing the food production process, reducing waste, and improving efficiency is critical to achieving cost savings and maintaining competitiveness in the food manufacturing industry. Here are some strategies that can help optimize the food production process and reduce waste:
- Standardize processes: Standardizing production processes can help reduce variability, improve quality control, and reduce waste. By establishing clear procedures for each task and training employees on these procedures, manufacturers can ensure that each product meets the same high-quality standards, reducing waste and improving efficiency.
- Implement quality control measures: Implementing quality control measures can help identify and prevent defects in products, reducing waste and improving overall product quality. Regular testing and inspection can help identify issues early on and ensure that products meet customer requirements.
- Reduce changeover time: Reducing changeover time between production runs can help increase production capacity and reduce waste. By optimizing the changeover process and minimizing downtime between runs, manufacturers can increase their output and reduce the need for excess inventory.
- Implement inventory management techniques: Implementing inventory management techniques can help reduce waste and improve efficiency. By maintaining optimal inventory levels and using just-in-time techniques, manufacturers can reduce waste and lower storage costs.
- Monitor equipment performance: Monitoring equipment performance can help identify issues early on and prevent breakdowns, reducing downtime and improving efficiency. Regular maintenance and equipment inspections can help ensure that equipment is functioning optimally and reduce the need for costly repairs or replacements.
- Reduce packaging waste: Reducing packaging waste can help reduce costs and improve sustainability. By using eco-friendly packaging materials and optimizing packaging design, manufacturers can reduce the amount of waste generated and improve their environmental impact.
Thus, optimizing the food production process, reducing waste, and improving efficiency are crucial to achieving cost savings and maintaining competitiveness in the food manufacturing industry.
By standardizing processes, implementing quality control measures, reducing changeover time, implementing inventory management techniques, monitoring equipment performance, and reducing packaging waste, manufacturers can significantly reduce costs and improve their profitability.
Examples of Companies that Have Successfully Implemented these Techniques and Achieved Cost Savings
Several food manufacturing companies have successfully implemented cost-saving techniques to improve their production processes and increase profitability. Here are some examples:
- Nestle: Nestle has implemented lean manufacturing techniques to reduce waste and increase efficiency in their production processes. They have also optimized their inventory management and implemented just-in-time techniques to reduce inventory levels and storage costs.
- PepsiCo: PepsiCo has invested in automation and robotics to reduce labor costs and improve efficiency in their production processes. They have also implemented a continuous improvement program to identify and eliminate inefficiencies in their operations.
- Tyson Foods: Tyson Foods has implemented a data-driven approach to improve their production processes and reduce waste. By collecting and analyzing data on production performance and quality control, they have been able to identify areas for improvement and optimize their operations.
- Kellogg Company: Kellogg Company has implemented a sustainability program to reduce waste and improve their environmental impact. They have reduced packaging waste by using eco-friendly materials and optimized their transportation and distribution processes to reduce fuel consumption and emissions.
By adopting strategies such as lean manufacturing, automation, data-driven analysis, and sustainability programs, these companies have been able to remain competitive in the industry and achieve long-term success.
Optimizing the Supply Chain to Reduce Costs
Optimizing the supply chain is a critical method for reducing the cost of food manufacturing. The supply chain encompasses all the processes involved in the production and delivery of a product, from the sourcing of raw materials to the delivery of the finished product to the end customer. By optimizing the supply chain, food manufacturers can reduce costs, improve efficiency, and increase profitability.
Here are some ways in which optimizing the supply chain can reduce the cost of food manufacturing:
- Efficient sourcing of raw materials: By sourcing raw materials from reliable suppliers who offer competitive prices and quality products, manufacturers can reduce the cost of materials and ensure the quality of the final product.
- Streamlined logistics: Optimizing logistics processes, such as transportation and warehousing, can reduce the time and cost of moving products throughout the supply chain. This can help reduce inventory holding costs and minimize the risk of waste due to spoilage or expiration.
- Improved forecasting and planning: Effective forecasting and planning can help manufacturers anticipate demand, optimize production schedules, and reduce inventory holding costs. By predicting demand more accurately, manufacturers can reduce the risk of overproduction or stockouts, which can lead to waste and increased costs.
- Collaboration with suppliers and customers: Collaboration with suppliers and customers can help reduce costs and improve efficiency throughout the supply chain. By working together to streamline processes, manufacturers can reduce lead times, improve product quality, and increase customer satisfaction.
- Automation and technology: Automation and technology can help manufacturers optimize their supply chain processes, reducing costs and improving efficiency. For example, implementing a supply chain management system can help manufacturers track inventory levels, optimize production schedules, and reduce waste.
By efficiently sourcing raw materials, streamlining logistics, improving forecasting and planning, collaborating with suppliers and customers, and leveraging automation and technology, food manufacturers can reduce costs, improve efficiency, and increase profitability.
Use of Technology and Data Analytics to Improve Supply Chain Efficiency and Reduce Costs
Technology and data analytics have become increasingly important in improving supply chain efficiency and reducing costs in the food manufacturing industry. Here are some ways in which technology and data analytics are being used to optimize the supply chain:
- Internet of Things (IoT): IoT devices, such as sensors and smart tags, can be used to track products throughout the supply chain. This can help manufacturers optimize production schedules, reduce waste, and improve the accuracy of inventory management.
- Big Data Analytics: Data analytics can be used to analyze large amounts of data from multiple sources, including social media, weather reports, and customer feedback. This can help manufacturers identify patterns, optimize logistics processes, and make data-driven decisions.
- Artificial Intelligence (AI): AI can be used to optimize supply chain processes, including forecasting demand, identifying potential disruptions, and optimizing transportation routes. This can help manufacturers reduce costs, improve efficiency, and increase customer satisfaction.
- Blockchain: Blockchain technology can be used to improve transparency and traceability throughout the supply chain. This can help manufacturers improve quality control, reduce the risk of fraud, and improve supply chain security.
- Cloud Computing: Cloud computing can be used to store and analyze supply chain data in real-time, providing manufacturers with valuable insights into their operations. This can help manufacturers optimize their production processes, reduce waste, and improve efficiency.
Technology and data analytics are becoming increasingly important in improving supply chain efficiency and reducing costs in the food manufacturing industry. By leveraging IoT, big data analytics, AI, blockchain, and cloud computing, manufacturers can optimize their production processes, improve the accuracy of inventory management, reduce waste, and increase customer satisfaction.
Reducing Energy Consumption to Reduce Production Costs
Reducing energy consumption is an effective method for reducing the cost of food manufacturing. Energy is a significant cost factor for food manufacturers, as it is required for heating, cooling, refrigeration, and other processes. Here are some ways in which food manufacturers can reduce their energy consumption:
- Energy-efficient equipment: Food manufacturers can reduce energy consumption by using energy-efficient equipment, such as refrigeration units, ovens, and boilers. These types of equipment are designed to use less energy while still providing the same level of performance.
- Energy management systems: Energy management systems can be used to monitor and control energy usage throughout the manufacturing process. These systems can automatically adjust energy usage based on demand, which can help reduce energy waste.
- Lighting: Upgrading to LED lighting can significantly reduce energy consumption in food manufacturing facilities. LED lighting is more energy-efficient than traditional lighting and lasts longer, which reduces maintenance costs.
- Insulation: Proper insulation of equipment and buildings can help reduce energy consumption by preventing heat loss or gain. This can be achieved through the use of insulation materials, such as foam insulation or spray foam.
- Renewable energy sources: Food manufacturers can also reduce energy costs by using renewable energy sources, such as solar or wind power. While the initial investment in these types of energy sources can be high, the long-term cost savings can be significant.
These measures also have the added benefit of reducing greenhouse gas emissions, which can help food manufacturers meet sustainability goals and reduce their environmental impact.
How Companies Can Reduce Energy Consumption Through the Use of Renewable Energy Sources and Improved Maintenance Practices
Food companies can reduce energy consumption and associated costs by implementing several strategies, such as using renewable energy sources, energy-efficient equipment, and improved maintenance practices. Here's a closer look at each of these strategies:
- Renewable energy sources: Using renewable energy sources such as solar or wind power can significantly reduce energy costs. Food companies can install solar panels or wind turbines to generate electricity, or they can purchase renewable energy credits from utilities to offset their energy use. By reducing reliance on traditional energy sources, food companies can also reduce their carbon footprint and improve their sustainability.
- Improved maintenance practices: Regular maintenance of equipment can also help reduce energy consumption. Food companies can implement a preventative maintenance program that includes cleaning and tuning equipment, replacing worn or damaged parts, and checking for leaks. This can help improve equipment efficiency and reduce energy waste.
Companies can also improve their sustainability and reduce their carbon footprint, which can help them meet their environmental goals and expectations of stakeholders. In addition, energy-saving measures can enhance a company's reputation, attract customers who value sustainability, and reduce exposure to energy price fluctuations.
Examples of Companies that Have Successfully Reduced Energy Consumption and Achieved Cost Savings
There are several examples of food companies that have successfully reduced energy consumption and achieved cost savings by implementing energy-saving measures. Here are some notable examples:
- General Mills: General Mills, a leading food company, has set a goal to reduce its greenhouse gas emissions by 28% by 2025. To achieve this goal, the company has implemented several energy-saving measures, such as using renewable energy sources, improving energy efficiency in its facilities, and reducing waste. General Mills has also installed energy-efficient lighting and equipment, resulting in an annual cost savings of over $7 million.
- Nestle: Nestle, one of the largest food companies in the world, has set a goal to use 100% renewable electricity in its factories and warehouses by 2025. To achieve this goal, the company has installed solar panels and wind turbines at its facilities, reducing its reliance on traditional energy sources. In addition, Nestle has implemented energy-efficient technologies and processes, resulting in a 34% reduction in energy consumption since 2005.
- PepsiCo: PepsiCo, a leading food and beverage company, has set a goal to reduce its greenhouse gas emissions by 20% by 2030. To achieve this goal, the company has implemented several energy-saving measures, such as using renewable energy sources, improving energy efficiency in its facilities, and reducing waste. PepsiCo has also invested in energy-efficient lighting, equipment, and packaging, resulting in an annual cost savings of over $200 million.
- Kellogg's: Kellogg's, a global food company, has set a goal to reduce its energy use by 15% per metric ton of food produced by 2020. To achieve this goal, the company has implemented several energy-saving measures, such as using renewable energy sources, improving energy efficiency in its facilities, and reducing waste. Kellogg's has also invested in energy-efficient lighting and equipment, resulting in an annual cost savings of over $1 million.
These examples demonstrate that food companies can reduce energy consumption and associated costs by implementing energy-saving measures such as using renewable energy sources, improving energy efficiency, and reducing waste. These measures not only result in cost savings but also help food companies meet their environmental goals and expectations of stakeholders.
Improving Inventory Management to Reduce Costs
Improving inventory management is an effective way to reduce costs in food manufacturing. Efficient inventory management ensures that the right amount of inventory is available at the right time to meet customer demand, while also minimizing inventory holding costs, spoilage, and waste.
One strategy for improving inventory management is to implement just-in-time (JIT) inventory systems. JIT inventory systems involve ordering materials and supplies only as they are needed for production, rather than stockpiling them in advance. This helps to reduce the costs associated with holding excess inventory, such as storage, handling, and obsolescence.
Another strategy for improving inventory management is to use data analytics to forecast demand and optimize inventory levels. By analyzing historical sales data, production schedules, and other factors, food manufacturers can predict future demand and adjust inventory levels accordingly. This helps to ensure that inventory levels are optimized to meet customer demand while minimizing the risk of stockouts and excess inventory.
Implementing effective inventory tracking and management systems is also essential for improving inventory management. Using barcode or RFID tracking systems can help to ensure accurate inventory counts and reduce the risk of inventory discrepancies. Additionally, implementing automated inventory tracking and management systems can help to reduce the time and labor required to manage inventory.
By implementing JIT inventory systems, using data analytics to forecast demand, and implementing effective inventory tracking and management systems, food manufacturers can minimize inventory holding costs, reduce spoilage and waste, and ensure that the right amount of inventory is available at the right time to meet customer demand.
Employee Training and Development to Reduce Cost of Food Manufacturing
Employee training and development is an important strategy for reducing costs in food manufacturing. Well-trained and motivated employees can improve productivity, reduce waste, and ensure that processes are performed efficiently and effectively.
One way to implement employee training and development programs is through continuous improvement programs such as Lean Six Sigma. These programs provide employees with the tools and techniques to identify inefficiencies and implement process improvements. By implementing these programs, employees can reduce waste and improve process efficiency, ultimately leading to cost savings.
Providing ongoing training to employees can also help to reduce costs. For example, training employees on the proper use of equipment can reduce maintenance costs and increase equipment lifespan. Similarly, providing training on food safety and quality can reduce the risk of contamination and product recalls, which can be costly.
Cross-training employees is another effective way to reduce costs in food manufacturing. Cross-training employees to perform multiple tasks can increase flexibility in production, allowing manufacturers to adjust to changes in demand without having to hire additional staff. This can result in labor cost savings while ensuring that production is not affected by changes in demand.
Finally, investing in employee development can improve employee morale and retention, reducing the costs associated with turnover and training new employees. Providing opportunities for professional growth and career advancement can help employees feel valued and engaged, leading to increased productivity and lower turnover rates.
In conclusion, employee training and development is an effective way to reduce costs in food manufacturing. By implementing continuous improvement programs, providing ongoing training, cross-training employees, and investing in employee development, food manufacturers can improve productivity, reduce waste, and improve efficiency, ultimately leading to cost savings.
How can MRP and ERP systems Assist in Reducing Costs in Food Manufacturing?
Material Requirements Planning (MRP) and Enterprise Resource Planning (ERP) systems can assist in reducing costs in food manufacturing in several ways:
- Inventory Management: MRP and ERP systems can help food manufacturers optimize their inventory levels and avoid overstocking or understocking. This can reduce the cost of holding excess inventory and minimize the risk of stockouts, which can disrupt production and increase costs.
- Production Planning: MRP and ERP systems can help food manufacturers plan their production schedules more efficiently, ensuring that they produce the right amount of products at the right time. This can reduce the need for overtime or rushed production, which can increase costs.
- Cost Tracking: MRP and ERP systems can help food manufacturers track the costs associated with each stage of the production process, from raw materials to finished products. This can help identify areas where costs can be reduced, such as optimizing raw material usage or reducing waste.
- Supply Chain Management: MRP and ERP systems can help food manufacturers manage their supply chain more effectively, from procurement to delivery. This can help minimize lead times, reduce transportation costs, and optimize supplier relationships.
- Real-Time Data: MRP and ERP systems can provide real-time data on production, inventory levels, and supply chain activities. This can help food manufacturers make more informed decisions, improve efficiency, and reduce costs.
Overall, MRP and ERP systems can help food manufacturers improve their operations, reduce costs, and increase profitability by providing better visibility and control over their production processes, inventory levels, and supply chain activities.
How can Deskera Help You?
Deskera ERP and MRP systems help you to keep your business units organized. The system's primary functions are as follows:
- Keep track of your raw materials and final items inventories
- Control production schedules and routings
- Keep a bill of materials
- Produce thorough reports
- Make your own dashboards
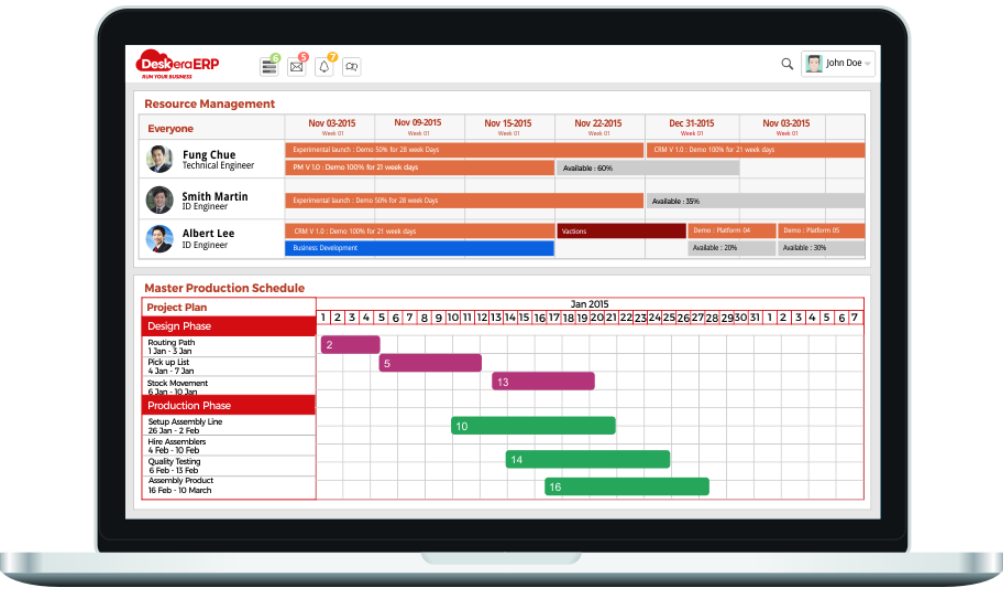
Deskera's integrated financial planning tools enable investors to better plan and track their investments. It can assist investors in making faster and more accurate decisions.
Deskera Books allows you to better manage your accounts and finances. Maintain good accounting practices by automating tasks like billing, invoicing, and payment processing.
Deskera CRM is a powerful solution that manages your sales and helps you close deals quickly. It not only enables you to perform critical tasks like lead generation via email, but it also gives you a comprehensive view of your sales funnel.
Deskera People is a straightforward tool for centralizing your human resource management functions.
Key Takeaways
- Analyzing the cost structure of food manufacturing is essential to identify areas where cost savings can be achieved.
- Raw material prices, labor costs, energy costs, and equipment maintenance costs significantly impact the overall cost structure of food manufacturing.
- Adopting cost-effective production techniques such as lean manufacturing, automation, and process optimization can help reduce costs.
- Improving supply chain efficiency through technology and data analytics can reduce costs by minimizing waste and improving delivery times.
- Renewable energy sources, energy-efficient equipment, and improved maintenance practices can help reduce energy consumption and associated costs.
- Reducing waste through process optimization, supply chain efficiency, and sustainable packaging can significantly reduce costs.
- Investing in employee training and development can improve productivity and reduce labor costs.
- Collaborating with suppliers and customers can help reduce costs and improve efficiency.
- Outsourcing non-core functions can help reduce costs and improve focus on core competencies.
- Implementing continuous improvement processes such as Six Sigma and Kaizen can help identify and eliminate waste, reducing costs.
- Regularly reviewing and renegotiating supplier contracts can help reduce costs.
- Improving inventory management can help reduce costs associated with storage, spoilage, and waste.
- Investing in research and development to identify new cost-saving opportunities can help food manufacturers stay competitive.
- Leveraging technology such as the Internet of Things (IoT) and Artificial Intelligence (AI) can help reduce costs and improve efficiency.
- Regularly benchmarking against industry peers and best practices can help identify opportunities for cost savings and continuous improvement.
Related Articles
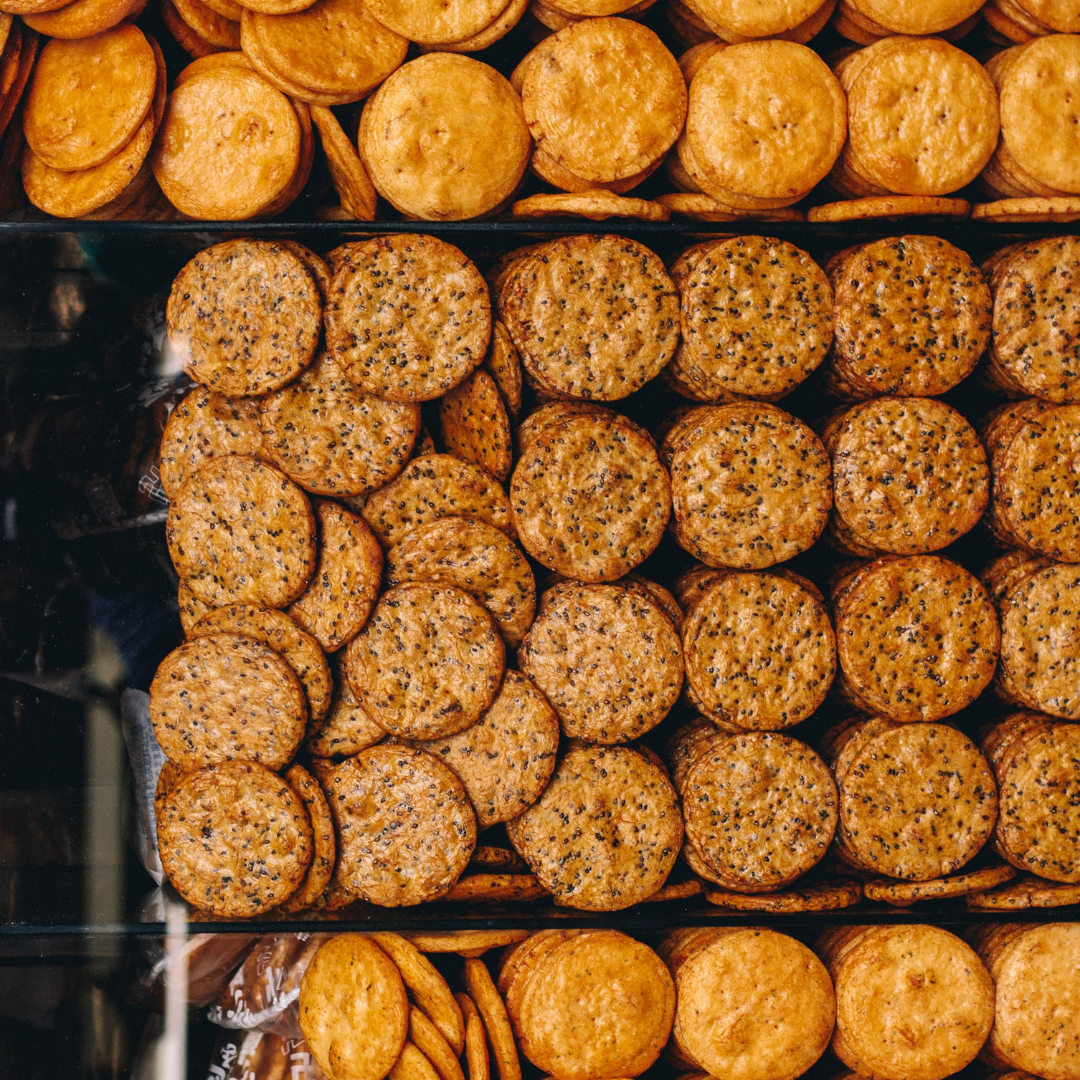
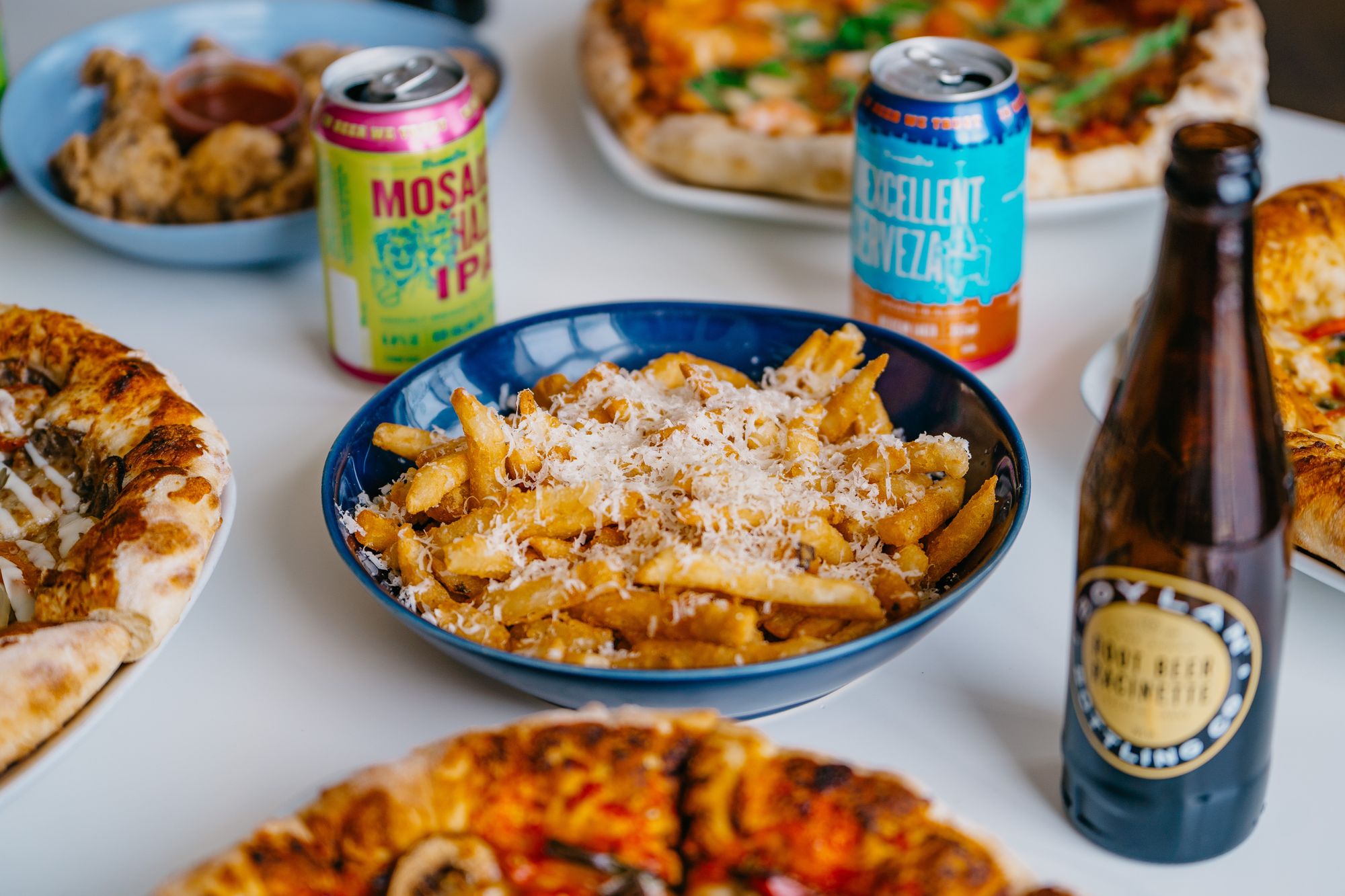
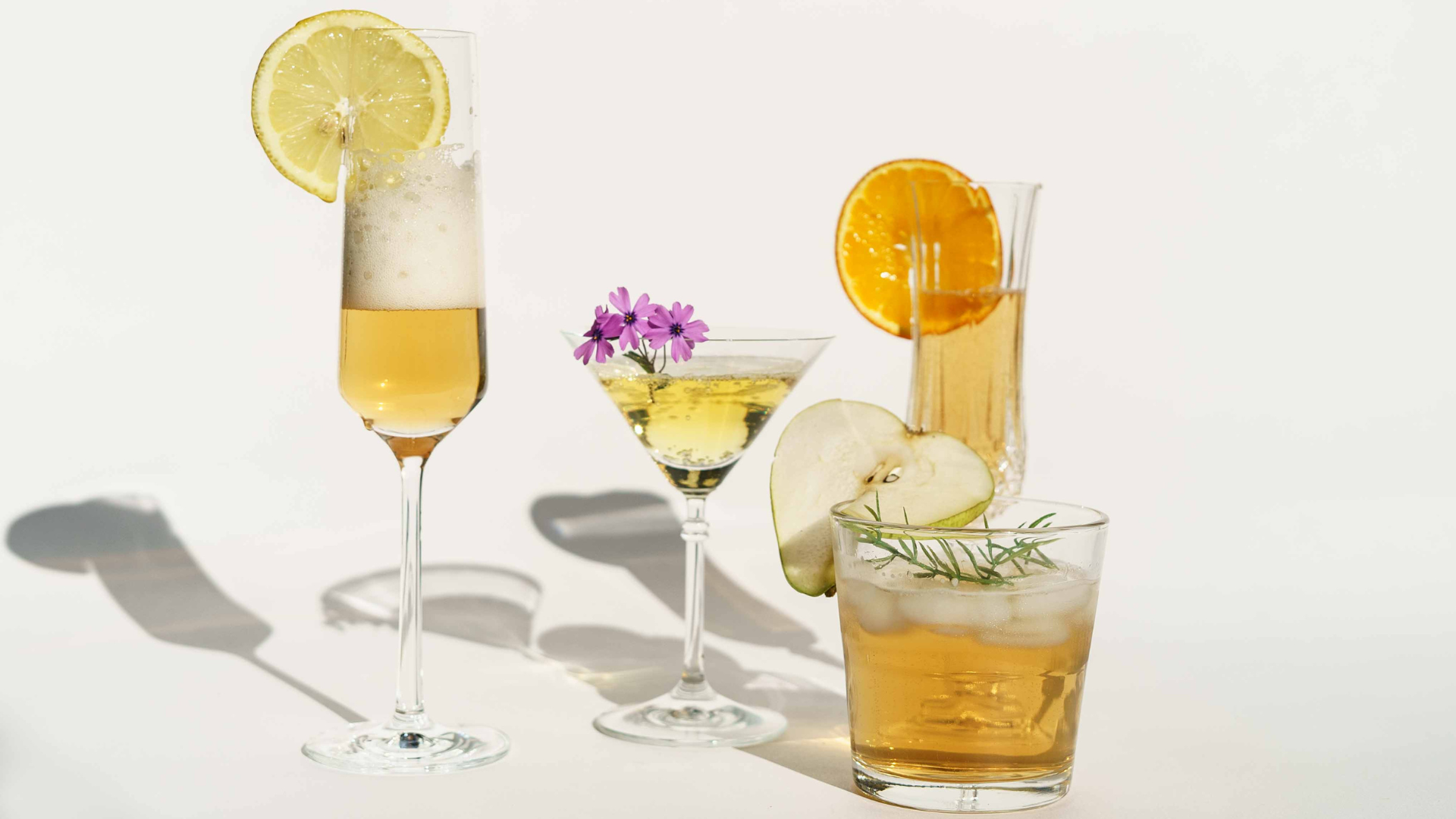