Are you ready to embark on a manufacturing journey where your production schedule is fine-tuned with real-time data? Imagine a world where you can effortlessly navigate the complexities of production scheduling, optimize resources, and easily meet customer demands.
Well, that world is within reach, thanks to the power of real-time data in manufacturing.
Gone are the days of relying on outdated and static information. With real-time data, manufacturers can access up-to-the-minute insights into their production processes, inventory levels, machine performance, and customer demands.
Imagine a scenario where you can monitor machine efficiency in real-time, identify bottlenecks before they become critical, and adjust your production schedule accordingly. Real-time data enables you to do just that. By integrating smart sensors, Internet of Things (IoT) devices, and advanced analytics tools, manufacturers can gather data in real time, gaining a comprehensive view of their operations.
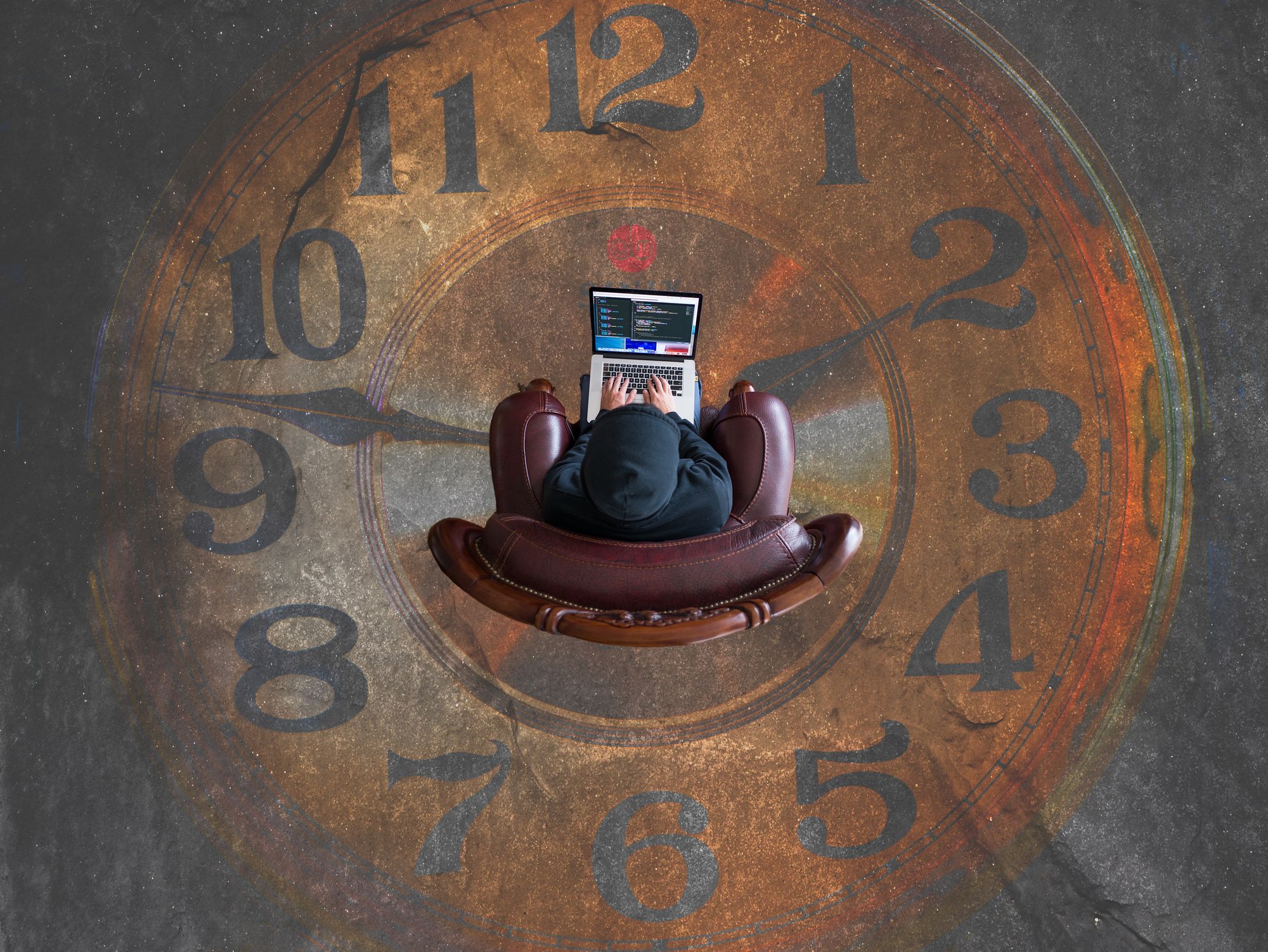
According to a recent National Association of Manufacturers survey, 77% of manufacturers agree that real-time data and analytics are crucial for driving operational efficiency and reducing costs. Furthermore, research from McKinsey & Company indicates that manufacturers who leverage real-time data to drive decision-making can improve their productivity by up to 30%.
In this article, we will explore the world of real-time manufacturing data and its role in successful production scheduling.
We will discuss the latest trends, technologies, and best practices for harnessing the power of real-time data. From implementing data collection systems to leveraging advanced analytics tools, we will provide actionable insights to help you unlock the full potential of real-time data in your manufacturing operations.
So, get ready to embark on an exciting journey into the world of real-time data and witness how it can revolutionize your manufacturing production scheduling.
Here's what we shall cover in this post:
- Introduction to Real-Time Data in Manufacturing Scheduling
- Key Metrics to Monitor in Real-Time for Scheduling Optimization
- Using Real-Time Data for Demand Forecasting
- Integration of Real-Time Data With Scheduling Software
- Future Trends: Real-Time Data Advancements in Manufacturing Scheduling
- How Can Deskera Help You?
- Conclusion
- Key Takeaways
Introduction to Real-Time Data in Manufacturing Scheduling
Real-time data in manufacturing scheduling refers to continuously updated information that allows for instant analysis and decision-making. It provides up-to-date insights into various aspects of the production process.
- Real-time data plays a crucial role in enabling agile decision-making and optimizing production schedules. It is obtained from sources such as machine sensors, IoT devices, production monitoring systems, and supply chain integration.
- Real-time data offers several benefits, including enhanced decision-making, improved efficiency, minimized downtime, and agile response to changes. It also supports quality control efforts and enables continuous improvement initiatives.
- However, utilizing real-time data requires addressing challenges such as data integration, accuracy, security, and analysis capabilities.
- By leveraging real-time data effectively, manufacturers can make data-driven decisions, improve operational efficiency, and meet customer demands more efficiently.
Enhancing Scheduling Accuracy With Real-Time Data
Real-time data plays a crucial role in enhancing scheduling accuracy in manufacturing operations. Providing up-to-the-minute information allows for better decision-making and optimization of production schedules.
Here are some key points on how real-time data enhances scheduling accuracy:
- Immediate Visibility: Real-time data provides immediate visibility into various aspects of the production process, including machine status, inventory levels, and production progress. This enables schedulers to have a real-time understanding of the current situation on the shop floor.
- Timely Adjustments: With real-time data, schedulers can make timely adjustments to the production schedule based on actual conditions. They can identify bottlenecks, monitor work-in-progress, and allocate resources efficiently to ensure smooth production flow.
- Demand-Supply Alignment: Real-time data helps in aligning production schedules with customer demand and supply chain dynamics. By monitoring customer orders, inventory levels, and production capacity in real time, schedulers can adjust production schedules to meet changing demands and minimize stockouts or excess inventory.
- Improved Forecasting: Real-time data provides valuable insights for forecasting future demand and production requirements. By analyzing historical data, market trends, and customer behavior in real time, schedulers can make more accurate forecasts, reducing the risk of underproduction or overproduction.
- Minimized Downtime: Real-time data allows for proactive maintenance and reduces downtime. By monitoring equipment performance and receiving real-time alerts for potential issues, schedulers can plan preventive maintenance activities, ensuring optimal equipment availability and minimizing unplanned production interruptions.
- Agile Response to Changes: Real-time data enables schedulers to respond quickly to unexpected changes, such as equipment breakdowns, supply chain disruptions, or order cancellations. They can swiftly adjust the production schedule, reassign resources, and prioritize tasks based on real-time information, minimizing the impact on overall productivity.
- Data-Driven Decision Making: Real-time data empowers schedulers to make data-driven decisions. By analyzing real-time information on machine performance, production metrics, and resource availability, they can optimize production schedules, improve efficiency, and allocate resources effectively.
- Continuous Improvement: Real-time data supports continuous improvement efforts in scheduling. By capturing real-time performance data and analyzing it for patterns and opportunities, schedulers can identify areas for improvement, implement process changes, and track the impact of these improvements on scheduling accuracy over time.
Incorporating real-time data into the scheduling process enables manufacturers to optimize their operations, improve customer satisfaction, and stay competitive in today's dynamic business environment.
Key Metrics to Monitor in Real-Time for Scheduling Optimization
Monitoring key metrics in real time is essential for scheduling optimization in manufacturing operations. By keeping a close eye on these metrics, schedulers can make informed decisions, identify areas for improvement, and optimize production schedules to enhance efficiency and productivity.
Here are some key metrics to monitor in real time for scheduling optimization:
Machine Utilization
Machine utilization measures the percentage of time that a machine is actively producing output. By monitoring machine utilization in real time, schedulers can identify underutilized or overutilized machines and make adjustments to optimize production capacity and balance workloads.
Identifying Bottlenecks:
- Machine utilization can help identify bottlenecks in the production process.
- By analyzing machine utilization rates, schedulers can pinpoint machines that are operating at or near full capacity, causing delays and inefficiencies.
- This information allows for proactive planning and allocation of resources to optimize production flow.
Maximizing Production Capacity:
- Monitoring machine utilization enables schedulers to optimize production capacity.
- By identifying underutilized machines, production downtime can be minimized, and additional production orders can be scheduled to maximize the use of available resources.
- This improves overall production efficiency and reduces idle time.
Scheduling Optimization:
- Machine utilization data plays a crucial role in scheduling optimization.
- By analyzing historical machine utilization patterns, schedulers can make informed decisions about the allocation of jobs to machines.
- This ensures balanced workloads and minimizes idle time, leading to improved productivity and on-time delivery.
Maintenance and Downtime Planning:
- Machine utilization metrics help in planning maintenance activities and reducing unplanned downtime.
- By analyzing utilization rates, schedulers can schedule preventive maintenance during periods of low machine utilization to minimize production disruptions.
- This proactive approach reduces costly breakdowns and improves overall equipment effectiveness.
Production Cycle Time
Production cycle time measures the time it takes to complete a product from start to finish. Monitoring production cycle time in real time helps schedulers identify bottlenecks, delays, or inefficiencies in the production process.
Addressing these issues promptly can reduce cycle time and improve overall productivity.
- Shorter production cycle times indicate higher productivity, reduced lead times, and increased customer satisfaction.
- Longer production cycle times can highlight bottlenecks, inefficiencies, and areas where process improvements are needed.
- Effective management of production cycle time helps manufacturers meet customer demands, minimize inventory costs, and improve overall operational performance.
- Optimizing production cycle times can lead to increased throughput, reduced work-in-progress inventory, and improved on-time delivery performance.
- Production cycle time is influenced by various factors such as equipment availability, labor efficiency, material availability, and process reliability.
- Manufacturers can drive continuous improvement initiatives by setting targets and continuously monitoring production cycle times, and enhancing their competitiveness.
- Advanced scheduling techniques and real-time data integration can further optimize production cycle times by enabling dynamic scheduling and efficient resource allocation.
Work-in-Progress (WIP)
WIP refers to the number of products or tasks that are currently in progress but not yet completed. Real-time monitoring of WIP allows schedulers to track the flow of work on the shop floor, identify areas of congestion, and take corrective actions to maintain a balanced and efficient production flow.
- Monitoring WIP levels helps manufacturers understand the balance between production capacity and customer demand and make informed decisions regarding resource allocation and scheduling.
- High WIP levels can indicate overproduction, excessive inventory, and potential delays in fulfilling customer orders.
- Low WIP levels may suggest an underutilization of resources or inefficient production processes.
- Manufacturers can reduce lead times, improve cash flow, and enhance overall operational efficiency by optimizing WIP levels.
- Effective WIP management requires accurate demand forecasting, efficient production planning, and real-time visibility into the production floor.
- Lean manufacturing principles, such as just-in-time (JIT) production and pull-based schedules, aim to minimize WIP levels and eliminate waste in the production process.
- Implementing and integrating WIP tracking systems with scheduling software can provide real-time visibility into WIP levels, enabling proactive decision-making and continuous improvement efforts.
On-Time Delivery
On-time delivery measures the percentage of orders or shipments that are delivered to customers on time. Real-time monitoring of on-time delivery helps schedulers track performance against delivery targets and identify any potential delays or bottlenecks that could impact customer satisfaction.
It enables them to take proactive measures to ensure timely delivery.
- Meeting delivery deadlines is crucial for maintaining customer satisfaction, building trust, and gaining a competitive advantage.
- Late deliveries can result in customer dissatisfaction, order cancellations, and company reputation damage.
- On-Time Delivery is influenced by various factors, including production cycle time, inventory management, supplier reliability, transportation logistics, and order processing efficiency.
- Effective scheduling and production planning are essential for ensuring manufacturing operations align with customer demand and lead times.
- Real-time visibility into the production floor, inventory levels, and order status is crucial for tracking progress and identifying potential delays.
- Continuous monitoring and analysis of On-Time Delivery performance help identify areas for improvement and drive operational excellence.
- Implementing advanced scheduling tools, such as advanced planning and scheduling (APS) software, can optimize production schedules, minimize lead times, and enhance On-Time Delivery performance.
Inventory Levels
Monitoring inventory levels in real time is crucial for scheduling optimization. It allows schedulers to track raw material availability, work-in-progress inventory, and finished goods inventory.
By having real-time visibility into inventory levels, schedulers can make informed decisions about production quantities, replenishment, and resource allocation to avoid stockouts or excessive inventory.
- Optimal inventory levels are essential for meeting customer demands while minimizing carrying costs and stockouts.
- High inventory levels can tie up working capital, lead to storage issues, and increase the risk of obsolescence.
- Low inventory levels can result in production disruptions, delayed order fulfillment, and missed sales opportunities.
- Maintaining the right balance of inventory is crucial for streamlining production processes and ensuring smooth operations.
- Accurate demand forecasting, lead time analysis, and production planning are key factors in determining optimal inventory levels.
- Real-time visibility into inventory levels is vital for scheduling decisions, such as prioritizing production orders and managing reordering points.
- Just-in-Time (JIT) and lean manufacturing principles aim to minimize inventory levels by synchronizing production with customer demand.
- Advanced inventory management techniques, such as ABC analysis, safety stock optimization, and vendor-managed inventory (VMI), can help improve inventory levels and overall scheduling efficiency.
Production Efficiency
Production efficiency measures the ratio of actual output to the planned output. Real-time monitoring of production efficiency helps schedulers identify production losses, such as downtime, setup time, or quality issues.
By addressing these inefficiencies in real time, schedulers can optimize production processes, improve efficiency, and maximize output.
- Tracking production efficiency helps identify areas for improvement and optimize scheduling to enhance overall productivity.
- Factors that impact production efficiency include equipment reliability, maintenance practices, workforce skills, production planning, and coordination across different stages of the manufacturing process.
- Real-time monitoring and data collection enable the measurement of production efficiency, allowing timely adjustments and interventions.
- Lean manufacturing principles, such as continuous improvement and waste reduction, aim to enhance production efficiency by eliminating non-value-added activities and optimizing workflows.
- Key performance indicators (KPIs) like Overall Equipment Efficiency (OEE), cycle time, and scrap rates are commonly used to quantify production efficiency.
- By focusing on improving production efficiency, manufacturers can achieve higher output, reduced costs, improved customer satisfaction, and a competitive advantage in the market.
Employee Productivity
Employee productivity measures the output achieved per unit of labor input. Real-time monitoring of employee productivity allows schedulers to track individual or team performance, identify areas for improvement, and allocate resources effectively. It helps ensure that labor resources are utilized efficiently to meet production targets.
- High employee productivity indicates optimal skills, knowledge, and time utilization, resulting in increased output and improved overall performance.
- Low employee productivity may be indicative of various factors, such as inadequate training, inefficient work processes, lack of motivation, or suboptimal scheduling practices.
- Tracking employee productivity helps identify opportunities for improvement, optimize scheduling, and enhance the overall efficiency of manufacturing operations.
- Factors that impact employee productivity include workforce skills, training, motivation, workload management, communication, and collaboration.
- Scheduling practices considering employee capabilities, workload balance, and task prioritization contribute to higher productivity.
- Real-time monitoring of employee activities and performance can provide insights into productivity levels and enable timely interventions or adjustments.
- Employee productivity can be measured using key performance indicators (KPIs) such as output per hour, labor utilization, efficiency ratios, or specific productivity metrics tailored to the manufacturing processes.
- By focusing on improving employee productivity, manufacturers can achieve higher output, reduced costs, improved quality, and better overall competitiveness in the market.
Equipment Performance
Monitoring equipment performance in real time provides insights into the reliability and effectiveness of production machinery. Key metrics to monitor include equipment uptime, downtime, maintenance requirements, and performance indicators such as OEE (Overall Equipment Effectiveness).
Real-time equipment performance data helps schedulers plan maintenance activities, reduce downtime, and optimize equipment utilization.
- Monitoring equipment performance helps identify potential issues, schedule maintenance activities, optimize equipment usage, and ensure smooth production operations.
- Factors that influence equipment performance include equipment reliability, maintenance practices, calibration, availability of spare parts, and operator training.
- Scheduling practices considering equipment capabilities, maintenance schedules, and downtime for preventive or corrective maintenance contribute to higher performance levels.
- Real-time monitoring of equipment parameters, such as speed, efficiency, and failure rates, provides valuable data for assessing and improving equipment performance.
- Key performance indicators (KPIs) used to measure equipment performance include OEE, uptime percentage, mean time between failures (MTBF), mean time to repair (MTTR), and production output per hour.
- By focusing on optimizing equipment performance, manufacturers can enhance production efficiency, minimize downtime, reduce costs, and improve overall manufacturing effectiveness.
Quality Metrics
Real-time monitoring of quality metrics, such as first-pass yield, rework, and scrap rates, is vital for optimizing scheduling. It enables schedulers to identify quality issues as they occur, take corrective actions, and prevent the production of defective products. By maintaining high-quality standards in real-time, schedulers can avoid disruptions and ensure customer satisfaction.
Here are some key points about quality metrics as a metric in manufacturing scheduling:
Defect Rate:
- The defect rate measures the number of defective units or parts in a given production batch or timeframe.
- It helps identify areas of improvement and guides corrective actions to reduce defects and improve product quality.
- It is calculated by dividing the number of defective units by the total number of units produced and multiplying by 100 to get the percentage.
- Monitoring the defect rate helps identify areas of improvement and take corrective actions to reduce defects and enhance product quality.
- It allows manufacturers to identify the root causes of defects, implement preventive measures, and continuously improve their manufacturing processes.
- Monitoring the defect rate helps identify areas of improvement and take corrective actions to reduce defects and enhance product quality.
- It allows manufacturers to identify the root causes of defects, implement preventive measures, and continuously improve their manufacturing processes.
First Pass Yield (FPY):
- FPY represents the percentage of products that meet quality standards without the need for rework or repair during the initial production run.
- It reflects the effectiveness of the manufacturing process in producing high-quality products and minimizing waste.
- Monitoring the FPY provides valuable insights into the efficiency and effectiveness of the manufacturing process.
- It helps identify areas of improvement, optimize resource allocation, and reduce rework, scrap, and overall production costs.
- Higher FPY translates to increased productivity and throughput as more products pass through the manufacturing process successfully on the first attempt.
- It allows manufacturers to produce a higher volume of defect-free products within a given timeframe.
- FPY serves as a key performance indicator for continuous improvement efforts within manufacturing organizations.
- It provides a benchmark for setting improvement goals, measuring progress, and implementing initiatives to enhance the quality and efficiency of the production process.
Customer Complaints:
- Tracking customer complaints provides valuable insights into product quality and customer satisfaction.
- Monitoring and addressing customer complaints help identify recurring issues, improve product quality, and enhance customer experience.
- Customer complaints can provide valuable insights into the design and development stage of new products.
- By analyzing the complaints, manufacturers can identify design flaws, functionality issues, or gaps in meeting customer requirements, allowing them to make necessary modifications.
- Customer complaints can also shed light on the performance of suppliers and subcontractors involved in the manufacturing process.
- Manufacturers can assess the impact of supplier-related issues on customer satisfaction and take appropriate actions, such as finding alternative suppliers or implementing stricter quality control measures.
- By implementing preventive actions, such as process improvements, training programs, or quality control measures, manufacturers can proactively reduce the occurrence of customer complaints and associated disruptions.
Scrap and Rework Rates:
- Scrap rate measures the percentage of materials or components discarded due to defects or non-conformance.
- The rework rate reflects the percentage of products that require rework or additional processing to meet quality standards.
- Monitoring and reducing scrap and rework rates minimize waste, improve efficiency, and enhance overall product quality.
- Comparing scrap and rework rates with industry benchmarks and best practices helps manufacturers assess their performance and identify areas for improvement.
- It enables them to learn from other successful companies and implement strategies to reduce waste and improve overall manufacturing efficiency.
- Scrap and rework rates contribute to the cost of poor quality, which includes the costs associated with defects, rework, customer complaints, and warranty claims.
- By minimizing scrap and rework, manufacturers can reduce the cost of poor quality and improve their bottom line.
- Scrap and rework rates can provide insights into the performance of suppliers and subcontractors involved in the manufacturing process.
- High rates may indicate issues with the quality of supplied materials or components, prompting manufacturers to evaluate and improve supplier partnerships.
Return Material Authorization (RMA) Rate:
- RMA rate measures the number of products returned by customers due to quality issues or defects.
- Tracking the RMA rate helps identify root causes, implement corrective actions, and improve product quality and customer satisfaction.
- Scrap and rework rates are indicators of the effectiveness of quality control measures in place.
- High rates suggest a need for process improvements, better training, or enhanced quality assurance techniques to minimize defects.
- Analyzing scrap and rework rates helps identify the root causes behind the defects or non-conformance issues.
- By conducting root cause analysis, manufacturers can address the underlying issues and implement preventive measures to reduce future waste.
- Scrap and rework rates can provide insights into the performance of suppliers and subcontractors involved in the manufacturing process.
Quality Control Checkpoints:
- Implementing quality control checkpoints at various stages of the production process ensures that quality standards are met.
- These checkpoints include inspections, tests, and quality control measures to identify and address any deviations from desired quality.
- Quality control checkpoints facilitate documentation and traceability of quality-related information.
- By recording inspection results, test data, and other quality metrics at checkpoints, manufacturers can establish a comprehensive quality record for each product, enhancing traceability and accountability.
- Quality control checkpoints contribute to improved customer satisfaction.
- By maintaining stringent quality control measures, manufacturers can deliver products that meet or exceed customer expectations, leading to higher customer satisfaction and brand loyalty.
- Quality control checkpoints enable continuous monitoring of quality throughout the manufacturing process.
- Manufacturers can establish a system of regular inspections and tests at checkpoints to monitor the quality of products at different stages, ensuring consistency and reliability.
Supplier Quality Metrics:
- Monitoring supplier quality metrics, such as on-time delivery, material conformance, and supplier defect rates, helps ensure the quality of incoming materials and components.
- Collaboration with suppliers to improve their quality metrics contributes to overall product quality.
- Quality certifications, such as ISO 9001, are important supplier quality metrics that indicate a supplier's commitment to maintaining quality management systems.
- Suppliers with relevant certifications demonstrate their adherence to quality standards and best practices.
- SCARs are metrics that measure the number of corrective action requests issued to suppliers due to quality issues.
- It reflects the supplier's responsiveness and effectiveness in addressing and resolving quality problems.
Process Capability Indices:
- Process capability indices, such as Cp and Cpk, measure the capability of a manufacturing process to consistently produce products within specified quality limits.
- Cpk is a commonly used process capability index that measures the ability of a process to produce items within the specified tolerance limits.
- It takes into account both the centering of the process and the spread of the data to determine if the process is capable of meeting customer requirements.
- These indices provide insights into process stability, variation, and the ability to meet quality requirements.
- PCIs evaluate the variation in the manufacturing process, which is crucial for maintaining consistent product quality.
- Lower process variation results in higher process capability, indicating that the process is better controlled and capable of producing products within tighter tolerances.
- PCIs consider the target values specified for critical quality characteristics.
- By comparing the actual process performance to the target values, manufacturers can determine if the process can consistently meet the desired quality standards.
Energy Consumption
Monitoring energy consumption in real-time allows schedulers to identify energy-intensive processes or equipment and optimize energy usage. By tracking energy consumption metrics, such as electricity, water, or gas usage, schedulers can implement energy-saving measures, reduce costs, and minimize the environmental impact of manufacturing operations.
- Implementing energy monitoring systems enables real-time tracking and analysis of energy consumption.
- These systems provide valuable data on energy usage patterns, peak demand periods, and areas where energy efficiency can be improved.
- Energy consumption metrics should be regularly monitored and analyzed to identify trends, patterns, and areas for improvement.
- Manufacturers can use the insights gained from these metrics to implement continuous improvement strategies that enhance energy efficiency and reduce energy waste over time.
- Energy consumption metrics play a role in complying with energy-related regulations and standards.
- By monitoring and reporting energy consumption, manufacturers can ensure compliance with energy efficiency regulations and demonstrate their commitment to environmental responsibility.
Using Real-Time Data for Demand Forecasting
Demand forecasting is critical to effective supply chain management and production planning. Businesses can optimize inventory levels, production schedules, and resource allocation by accurately predicting customer demand.
Real-time data has emerged as a valuable tool for demand forecasting, providing up-to-date insights into market trends, customer behavior, and external factors that impact demand. Here are some key points on using real-time data for demand forecasting:
Market Trends: Real-time data allows businesses to monitor and analyze market trends in real-time, such as changes in consumer preferences, emerging product trends, or shifts in market dynamics.
By capturing and analyzing this data, businesses can identify patterns, anticipate market changes, and adjust their demand forecasts accordingly.
- Understanding market trends specific to your industry is crucial for accurate demand forecasting in scheduling.
- Analyze industry reports, market research, and trade publications to identify key trends that can impact demand for your products or services.
- Stay updated on evolving consumer behavior, preferences, and purchasing patterns.
- Monitor changes in consumer demographics, lifestyles, and buying habits to anticipate shifts in demand.
- Consider macroeconomic factors such as GDP growth, inflation, interest, and employment levels.
- Economic indicators provide insights into the overall market conditions and can influence demand for goods and services.
- Keep an eye on technological advancements that can impact consumer preferences and create new market opportunities.
- Understand how emerging technologies can affect demand for your products and consider their integration into your forecasting models.
- Stay informed about regulatory changes and compliance requirements that can impact demand.
- Changes in regulations, standards, or industry-specific guidelines can affect the demand for certain products or services.
Customer Behavior: Real-time data provides valuable insights into customer behavior, including purchasing patterns, buying preferences, and seasonality. By analyzing customer data in real time, businesses can understand customer demand drivers and make accurate forecasts based on actual customer behavior.
- Analyze customer purchase history to understand buying patterns, frequency, and seasonality.
- Identify recurring orders, trends, and fluctuations in demand to forecast future customer behavior.
- Segment customers based on demographic, psychographic, and behavioral characteristics.
- Understand different customer segments' unique needs, preferences, and purchasing behaviors to tailor demand forecasting accordingly.
- Conduct customer surveys and collect feedback to gain insights into their preferences, satisfaction levels, and future purchase intentions.
- Use survey data to identify patterns and make more accurate demand forecasts.
- Monitor social media platforms to understand customer sentiments, discussions, and emerging trends.
- Social media listening provides real-time insights into customer preferences, needs, and concerns that can influence demand.
External Factors: Real-time data helps businesses incorporate external factors that impact demand into their forecasting models. These factors may include economic indicators, weather conditions, social media sentiment, or competitor activities. By monitoring real-time data on these external factors, businesses can adjust their demand forecasts to account for potential impacts on customer demand.
- Monitor macroeconomic indicators such as GDP growth, inflation rates, and consumer confidence levels.
- Changes in economic conditions can impact customer purchasing power and overall demand for products.
- Account for seasonal fluctuations in demand due to holidays, weather conditions, and cultural events.
- Adjust production schedules to align with expected changes in customer demand during specific seasons.
Point-of-Sale Data: Real-time point-of-sale data provides businesses with immediate visibility into actual sales and customer purchasing patterns. By integrating this data into demand forecasting models, businesses can make accurate predictions based on real-time sales data rather than relying solely on historical data.
- Analyze sales transactions recorded at the point of sale to capture real-time data on product purchases.
- POS data provides valuable insights into customer buying behavior, including product preferences and purchase patterns.
- Track sales volume and revenue generated at different points of sale to understand demand trends.
- Identify peak sales periods, low-demand periods, and seasonal variations to optimize production scheduling.
- Evaluate individual product performance by analyzing POS data, including sales quantities and customer feedback.
- Identify top-selling products, slow-moving items, and product performance trends to adjust production plans accordingly.
- Utilize POS data to segment customers based on purchasing behavior, demographics, or other relevant criteria.
- Understand the preferences of different customer segments to tailor production schedules and meet their specific needs.
Social Media Monitoring: Social media platforms generate vast amounts of real-time data that can provide insights into customer sentiment, preferences, and emerging trends. By monitoring social media conversations and trends, businesses can capture valuable insights and incorporate them into their demand forecasting processes.
- Monitor social media platforms to analyze customer sentiments and opinions about your brand and products.
- Identify positive and negative feedback that can influence future demand and adjust production schedules accordingly.
- Track social media conversations and trending topics related to your industry or products.
- Identify emerging trends, preferences, and viral content that can impact demand and incorporate them into demand forecasting models.
- Monitor social media influencers and their impact on consumer behavior.
- Identify influential individuals who can drive demand for your products and collaborate with them to enhance brand visibility and sales.
- Assess the response to product launches, marketing campaigns, or promotions through social media monitoring.
- Gauge customer interest and engagement levels to forecast demand accurately and plan production schedules accordingly.
Web Analytics: Real-time web analytics data provides information about website traffic, customer browsing behavior, and online purchasing patterns. By leveraging web analytics data, businesses can gain insights into customer interest and demand patterns and adjust their forecasts accordingly.
- Analyze website traffic patterns and visitor behavior to gain insights into customer preferences and interests.
- Identify peak traffic periods and correlate them with demand fluctuations to adjust production schedules accordingly.
- Monitor conversion rates, i.e., the percentage of website visitors who take desired actions (e.g., making a purchase).
- Analyze conversion rates to understand customer buying behavior and forecast demand for specific products or services.
- Track the user journey on your website, from initial engagement to conversion.
- Identify key touchpoints, pages, or actions that lead to higher conversions and optimize production schedules accordingly.
- Evaluate the performance of individual product pages on your website.
- Monitor page views, time spent, and bounce rates to understand customer interest in specific products and forecast demand accordingly.
- Analyze the search terms and keywords that drive traffic to your website.
- Identify popular search queries related to your products or industry and incorporate them into demand forecasting models.
Supply Chain Visibility: Real-time data from the supply chain, such as supplier performance, inventory levels, and production capacities, enables businesses to assess potential bottlenecks or constraints that could impact demand fulfillment. By integrating this supply chain data into demand forecasting, businesses can optimize inventory management and production planning to meet customer demand.
- Supply chain visibility enables companies to respond quickly to demand variations and fluctuations.
- Organizations can adjust their schedules and operations by continuously monitoring customer demand signals, inventory levels, and production capacity. This agility helps in preventing stockouts, reducing excess inventory, and maintaining customer satisfaction.
- Supply chain visibility enhances the resilience of the entire supply chain network. By having clear visibility into the demand forecast, companies can proactively identify potential disruptions or bottlenecks in the supply chain and take preventive measures.
- This can involve alternative sourcing strategies, capacity adjustments, or contingency plans to ensure uninterrupted supply and minimize the impact of uncertainties.
Machine Learning and AI: Real-time data combined with advanced analytics techniques, such as machine learning and artificial intelligence, enables businesses to develop more accurate and dynamic demand forecasting models. These models can analyze vast amounts of real-time data, identify patterns, and continuously improve forecasting accuracy.
- Machine Learning algorithms can analyze large volumes of historical data, including sales records, customer behavior, market trends, and external factors, to identify patterns and relationships.
- By recognizing complex patterns, ML models can make accurate predictions about future demand, enabling better scheduling decisions.
- Machine Learning models can outperform traditional forecasting methods by leveraging advanced algorithms and statistical techniques.
- These models can learn from historical data and adjust their predictions based on changing patterns, resulting in more accurate demand forecasts. This accuracy helps in optimizing production schedules, inventory levels, and resource allocation.
- Machine Learning enables organizations to monitor demand in real time by analyzing data from multiple sources, such as point-of-sale systems, online transactions, social media, and supply chain sensors.
- This real-time visibility allows businesses to detect demand variations promptly and adjust scheduling decisions accordingly, minimizing the risk of stockouts or overstocks.
Collaboration and Data Sharing: Real-time data facilitates collaboration and data sharing among various stakeholders in the supply chain, including suppliers, distributors, and retailers. By sharing real-time data, businesses can improve demand visibility, enhance collaboration, and make more informed forecasting decisions.
- Collaboration and data sharing enables multiple stakeholders, such as suppliers, manufacturers, distributors, and retailers, to contribute and share their data related to demand forecasting.
- By pooling together diverse data sources, businesses can obtain a comprehensive view of the market, customer trends, and supply chain dynamics, leading to more accurate demand forecasts.
- When stakeholders collaborate and share their data, it allows for a more accurate demand forecasting process. Each participant can contribute their unique insights and expertise, resulting in a holistic understanding of demand patterns.
- This collaborative approach helps in minimizing individual biases, enhancing data quality, and improve the overall accuracy of demand forecasts.
- Collaboration and data sharing facilitate greater visibility across the supply chain. By sharing information on inventory levels, production capacities, lead times, and customer demand signals, stakeholders can gain real-time insights into the status of the entire supply chain.
- This visibility helps in identifying potential bottlenecks, aligning schedules, and making informed decisions to optimize operations.
Leveraging IoT Devices for Real-Time Data Collection
In today's interconnected world, the Internet of Things (IoT) has revolutionized the way businesses collect and analyze data. IoT devices, equipped with sensors and connectivity capabilities, enable real-time data collection and analysis across various industries.
When it comes to scheduling, leveraging IoT devices for real-time data collection offers numerous benefits in terms of efficiency, accuracy, and decision-making. Here are some key points on leveraging IoT devices for real-time data collection:
Sensor-Based Data Collection: IoT devices are equipped with sensors that can collect and transmit data in real time. These sensors can capture various types of data, such as temperature, humidity, pressure, motion, and location. By deploying IoT devices with relevant sensors, businesses can collect real-time data from their operations and assets.
- Sensors capture data in real time, providing instant visibility into the status and performance of different elements in the supply chain.
- This includes information on inventory levels, production rates, equipment utilization, transportation conditions, and environmental factors. Real-time visibility enables timely decision-making, allowing for efficient scheduling adjustments based on current conditions.
- Sensors can monitor the condition and performance of equipment or assets involved in the supply chain. For example, temperature sensors can monitor the temperature of perishable goods during transportation, while vibration sensors can detect irregularities in machinery.
- By monitoring the health and condition of assets, businesses can proactively schedule maintenance activities, optimize asset utilization, and prevent costly breakdowns or delays.
Seamless Connectivity: IoT devices are designed to be connected to the internet, enabling seamless data transmission to centralized systems or cloud platforms.
This connectivity allows businesses to access real-time data from remote locations, making it easier to monitor operations and make informed decisions regardless of geographical constraints.
- Seamless connectivity enables the instantaneous exchange of information and data between different stakeholders involved in the scheduling process. This includes suppliers, manufacturers, distributors, retailers, logistics providers, and even customers.
- Real-time information sharing allows for immediate updates on inventory levels, production status, transportation conditions, and other relevant data, enabling accurate and timely scheduling decisions.
- Seamless connectivity promotes collaboration and coordination among different parties involved in the scheduling process. By providing a platform for real-time communication, stakeholders can work together to align schedules, resolve conflicts, and make joint decisions.
- Seamless connectivity allows for the integration of various systems and technologies involved in scheduling. This includes Enterprise Resource Planning (ERP) systems, Manufacturing Execution Systems (MES), Warehouse Management Systems (WMS), and Transportation Management Systems (TMS), among others.
- Integrated systems ensure a seamless flow of information across different stages of the supply chain, enabling end-to-end visibility and streamlining scheduling processes.
Remote Monitoring and Control: IoT devices can be remotely monitored and controlled, allowing businesses to track and manage operations from anywhere. This remote accessibility enables real-time monitoring of production processes, equipment performance, and other relevant parameters, facilitating prompt decision-making and proactive scheduling adjustments.
Predictive Maintenance: IoT devices can monitor the condition of machinery and equipment in real time, providing insights into potential failures or maintenance needs. This data can be used for predictive maintenance strategies, scheduling maintenance activities at optimal times to avoid unplanned downtime and optimize production schedules.
Data Analytics and Insights: IoT devices generate vast amounts of data that can be analyzed to gain valuable insights. By leveraging advanced analytics techniques, businesses can uncover patterns, trends, and correlations within the data, leading to more informed scheduling decisions and continuous improvement of production processes.
Seamless Integration with Scheduling Systems: IoT devices can seamlessly integrate with existing scheduling systems, feeding real-time data directly into the scheduling software. This integration enables the scheduling system to make intelligent decisions based on the most current information, optimizing resource allocation, reducing lead times, and improving overall scheduling accuracy.
Real-Time Notifications and Alerts: IoT devices can trigger real-time notifications and alerts based on predefined thresholds or events. This functionality allows businesses to receive instant notifications about critical situations, such as equipment malfunctions or production delays, enabling prompt action and adjustment of schedules to minimize disruptions.
Integration of Real-Time Data With Scheduling Software
Here are key points on the integration of real-time data with scheduling software:
Real-Time Data Capture: The integration of real-time data with scheduling software enables businesses to capture data from various sources in real time. This includes data from IoT devices, sensors, production equipment, and other relevant systems.
Real-time data capture ensures that scheduling decisions are based on the most up-to-date information, allowing for better accuracy and responsiveness.
Seamless Data Transfer: Scheduling software that integrates real-time data enables the seamless transfer of information from data sources to the scheduling system. This eliminates the need for manual data entry and minimizes the risk of errors or delays in updating the schedule.
It also ensures that all stakeholders have access to the latest information and can make informed decisions accordingly.
Dynamic Scheduling: The integration of real-time data with scheduling software allows for dynamic scheduling. Real-time data on machine availability, production rates, inventory levels, and other relevant parameters can be continuously monitored and used to adjust schedules in real time.
This flexibility helps optimize resource allocation, minimize downtime, and adapt to changing production demands or unforeseen events.
Improved Visibility: Integration of real-time data provides enhanced visibility into the production process. Managers and stakeholders can access real-time dashboards or reports that display key performance indicators, production metrics, and scheduling information.
This visibility enables better monitoring of operations, identification of bottlenecks, and proactive decision-making to keep production on track.
Enhanced Collaboration: Real-time data integration fosters collaboration among different departments and stakeholders involved in scheduling. With access to real-time information, teams can communicate and coordinate effectively, ensuring that everyone is aligned and working towards the same goals.
This collaboration leads to better coordination of resources, reduced lead times, and improved overall efficiency.
Real-Time Data Visualization for Better Scheduling Insights
In the realm of manufacturing and production scheduling, real-time data visualization plays a crucial role in providing actionable insights for improved decision-making and optimization.
By presenting data in a visually appealing and intuitive manner, real-time data visualization allows businesses to understand complex information quickly and make informed scheduling decisions. Here are key points on the benefits of real-time data visualization for better scheduling insights:
Improved Data Understanding: Real-time data visualization transforms raw data into visually engaging charts, graphs, and dashboards, making it easier for users to understand and interpret complex information.
Enhanced Decision-Making: Real-time data visualization empowers schedulers to make faster and more accurate decisions. By presenting real-time data in an interactive and dynamic manner, visualizations enable schedulers to identify bottlenecks, resource constraints, or deviations from the schedule promptly.
This helps them take immediate action, allocate resources efficiently, and make necessary adjustments to meet production targets.
Real-Time Performance Monitoring: Real-time data visualization provides real-time monitoring of key performance indicators (KPIs) and production metrics.
Through dynamic dashboards and visual representations, schedulers can track production progress, machine utilization, cycle times, and other relevant metrics. This real-time visibility allows for proactive scheduling decisions to optimize production efficiency.
Early Issue Detection: Real-time data visualization enables schedulers to identify issues or anomalies as they occur. By visualizing real-time data, any deviations from expected performance or production targets can be detected early on. This allows for timely intervention, preventing potential disruptions, and ensuring smooth scheduling and production processes.
Interactive What-If Analysis: Real-time data visualization tools often offer interactive features such as "what-if" analysis. This functionality allows schedulers to simulate different scenarios and assess the potential impact of scheduling decisions on production outcomes.
By visually exploring various options and their consequences, schedulers can make informed decisions and choose the best scheduling strategy for optimal results.
Historical and Real-Time Data Integration: Real-time data visualization tools often enable the integration of historical and real-time data. By combining these two types of data, schedulers gain a comprehensive view of production performance over time.
This integration allows for trend analysis, performance benchmarking, and the identification of long-term scheduling patterns for continuous improvement.
Mobile Accessibility: Many real-time data visualization tools offer mobile accessibility, allowing schedulers to access visualizations and insights on the go. With mobile compatibility, schedulers can monitor production data and make informed decisions from anywhere, ensuring timely responses to scheduling challenges and maintaining efficient operations.
Challenges and Considerations in Using Real-Time Data for Scheduling
Using real-time data for scheduling in manufacturing brings numerous benefits, but it also presents certain challenges and considerations. Understanding these challenges and addressing them appropriately is essential to ensure the successful implementation and utilization of real-time data for scheduling purposes.
Here are key points highlighting the challenges and considerations in using real-time data for scheduling:
- Data Accuracy and Quality: Real-time data is only valuable if it is accurate and of high quality. Inaccurate or unreliable data can lead to incorrect scheduling decisions and negatively impact overall production efficiency. Ensuring data accuracy and quality requires robust data collection processes, validation mechanisms, and data cleansing techniques.
- Data Integration and Compatibility: Integrating real-time data from various sources and systems can be challenging, especially when dealing with different data formats and communication protocols. Compatibility issues may arise, requiring appropriate data integration strategies, such as using standardized data formats or employing data integration platforms.
- Data Volume and Velocity: Real-time data in manufacturing environments can be vast and generated at high velocities. Managing and processing such large volumes of data in real time can strain existing infrastructure and systems. Adequate computational power, storage capacity, and data processing capabilities are necessary to handle the volume and velocity of real-time data.
- Data Security and Privacy: Real-time data often contains sensitive information about production processes, equipment, and personnel. Ensuring data security and privacy is crucial to protect intellectual property, preventing unauthorized access, and complying with data protection regulations. Implementing robust cybersecurity measures, encryption techniques, and access controls is essential to safeguard real-time data.
- Real-Time Decision-Making: Utilizing real-time data for scheduling requires the ability to make fast and informed decisions. Schedulers and operators must have the necessary skills, training, and tools to analyze real-time data and act upon it promptly. This may involve providing training on data analysis techniques, implementing decision-support systems, or establishing clear protocols for real-time decision-making.
- System Reliability and Resilience: Relying on real-time data for scheduling means that the underlying systems and infrastructure must be highly reliable and resilient. Any disruptions in data collection, transmission, or processing can significantly impact scheduling accuracy and performance. Implementing redundancy measures, backup systems, and robust data infrastructure is crucial to ensure the continuous availability of real-time data.
- Scalability and Future-Proofing: As manufacturing operations evolve and expand, the scalability and future-proofing of real-time data systems become important considerations. The chosen technologies and infrastructure should have the capacity to handle increasing data volumes, support additional data sources, and accommodate future growth without compromising performance or scalability.
- Change Management and Adoption: Implementing real-time data for scheduling may require changes in processes, workflows, and organizational culture. Ensuring the smooth adoption of real-time data systems requires effective change management strategies, stakeholder buy-in, and training programs to equip employees with the necessary skills and knowledge to utilize real-time data effectively.
By addressing these challenges and considerations, manufacturers can harness the power of real-time data to optimize scheduling, enhance operational efficiency, and gain a competitive edge in the dynamic manufacturing landscape.
Security and Privacy Concerns in Real-Time Data-Driven Scheduling
Real-time data-driven scheduling in manufacturing offers significant benefits, but it also raises concerns regarding security and privacy. The nature of real-time data and its collection, storage, and transmission can expose manufacturers to potential vulnerabilities and risks.
Understanding and addressing these security and privacy concerns is crucial to ensure the protection of sensitive information and maintain the trust of customers and stakeholders.
Here are key points highlighting the security and privacy concerns in real-time data-driven scheduling:
Data Breaches: Real-time data contains valuable information about production processes, equipment, and personnel. Any unauthorized access or data breach can result in the exposure of sensitive information, trade secrets, or customer data. Implementing robust cybersecurity measures, such as encryption, firewalls, and access controls, is essential to protect against data breaches.
- Data breaches involve unauthorized access to sensitive or confidential information. Hackers or malicious actors exploit vulnerabilities in systems, networks, or applications to gain unauthorized entry and access data that they should not have.
- Data breaches can result in the loss or theft of valuable data. This includes personal information (such as names, addresses, Social Security numbers), financial data (credit card details, bank account numbers), intellectual property, or trade secrets. The stolen data can be misused for various criminal activities.
- Data breaches can lead to significant financial losses for organizations. They incur costs associated with investigating the breach, implementing security measures, notifying affected individuals, providing identity theft protection services, and potential legal fines or settlements. Additionally, organizations may experience a loss of customers and business opportunities due to reputational damage.
- Data breaches can severely damage the reputation of organizations. When customer data is compromised, trust in the organization's ability to protect personal information is eroded. Reputational damage can result in a loss of customers, diminished brand value, and negative media attention.
- Data breaches often trigger legal and regulatory consequences. Organizations may face legal liabilities, lawsuits, or regulatory fines for failing to protect customer data adequately. Compliance with data protection and privacy regulations, such as the General Data Protection Regulation (GDPR) or the California Consumer Privacy Act (CCPA), becomes critical.
Data Integrity: Real-time data integrity ensures that the data remains accurate, complete, and unaltered throughout its lifecycle. Any unauthorized modifications or tampering with real-time data can lead to incorrect scheduling decisions and compromised production processes. Employing data integrity checks, digital signatures, and audit trails helps maintain the trustworthiness of real-time data.
- Data integrity ensures that data is accurate, reliable, and free from errors, inconsistencies, or corruption. It provides a trustworthy foundation for decision-making and analysis.
- Data integrity maintains consistency and cohesion by ensuring that data remains synchronized and aligned across different systems, databases, or applications.
- Data integrity measures prevent unauthorized modifications, deletions, or alterations to data, ensuring that only authorized personnel can make changes.
- Data integrity involves implementing validation and verification processes to ensure the accuracy, completeness, and validity of data, preventing the entry of invalid or inconsistent information.
- Data integrity measures are closely linked to data security practices. Robust security controls and encryption techniques protect data from unauthorized access, ensuring its integrity throughout its lifecycle.
Insider Threats: Internal employees or contractors with access to real-time data can pose security risks. Deliberate or unintentional actions by insiders, such as data theft, unauthorized access, or accidental data leaks, can compromise the security and privacy of real-time data. Implementing strong access controls, user authentication mechanisms, and regular employee training on data security protocols mitigates insider threats.
- Insider threats arise when individuals with authorized access to systems and data intentionally misuse their privileges for personal gain, revenge, or harm to the organization. Their actions may include theft, sabotage, or unauthorized disclosure of sensitive information.
- Insider threats can also emerge from accidental or negligent behavior by employees. This includes mistakenly sharing sensitive data, falling victim to phishing attacks, or failing to adhere to security protocols, thereby inadvertently causing harm or compromising the organization's security.
- Insiders possess knowledge of the organization's systems, processes, and sensitive data, as well as the necessary access privileges. This insider knowledge makes it easier for them to exploit vulnerabilities and bypass security controls, increasing the potential impact of their actions.
- Insider threats can have a higher potential for causing significant damage compared to external threats. Insiders already have authorized access, reducing the need to bypass external security measures. They can carry out their actions undetected, resulting in longer exposure times and greater access to critical systems and data.
- Organizations grant employees and trusted individuals certain privileges and access rights to perform their duties effectively. However, these privileges can be misused, intentionally or unintentionally, resulting in insider threats. Balancing trust and privilege with appropriate security controls is crucial to mitigate this risk.
Third-Party Risks: Manufacturing operations often rely on third-party vendors, suppliers, or service providers who may have access to real-time data. Ensuring the security and privacy practices of these third parties is essential to prevent data breaches or unauthorized data sharing. Establishing clear data protection agreements, conducting due diligence on third-party security measures, and monitoring their compliance helps mitigate third-party risks.
- Engaging with third parties expands an organization's attack surface, as it introduces additional entry points for potential security breaches. Weaknesses in the third party's security practices or infrastructure can be exploited by malicious actors to gain unauthorized access to the organization's systems or data.
- Organizations often have limited control over the security measures and practices of third parties. This lack of control increases the risk of security incidents, as the organization is reliant on the third party's ability to implement and maintain effective security controls.
- Third-party risks can result in data breaches, leading to the compromise of sensitive information. When organizations share data with third parties, there is a potential for unauthorized access, theft, or accidental exposure of the data, which can result in reputational damage, regulatory penalties, and legal consequences.
- Organizations may face compliance challenges when working with third parties. They need to ensure that the third party complies with relevant regulations and industry standards, such as data protection laws or cybersecurity requirements. Non-compliance by third parties can expose the organization to regulatory scrutiny and legal liabilities.
Regulatory Compliance: Real-time data-driven scheduling may involve the processing and storage of personal or sensitive information subject to data protection regulations.
Manufacturers must comply with applicable privacy laws and regulations, such as the General Data Protection Regulation (GDPR) or industry-specific regulations. Understanding the legal requirements, implementing privacy safeguards, and obtaining necessary consents or permissions are critical for regulatory compliance.
Data Retention and Destruction: Real-time data may be stored for varying periods based on operational requirements. Establishing appropriate data retention policies ensures that data is retained only for as long as necessary and securely destroyed when no longer needed.
Clear guidelines on data retention, archiving, and secure data disposal help minimize the risks associated with long-term data storage.
- Data retention and destruction practices are crucial for ensuring compliance with legal and regulatory requirements. Different laws and regulations, such as the General Data Protection Regulation (GDPR) or industry-specific regulations, prescribe specific guidelines for data retention periods and proper data destruction methods.
- Retaining data beyond its required retention period can increase data liability risks. Storing unnecessary data exposes organizations to potential breaches, unauthorized access, or data misuse. Proper data retention and destruction practices help minimize data liability and associated risks.
- Data retention and destruction enable storage optimization by regularly removing obsolete, redundant, or trivial data. By eliminating unnecessary data, organizations can free up storage space, reduce costs associated with data storage, and enhance overall data management efficiency.
- Proper data retention and destruction practices help protect individual privacy. Retaining personal data for longer than necessary increases the risk of unauthorized access, data breaches, or misuse. Timely and secure data destruction ensures that personal information is not retained longer than required, promoting privacy protection.
Data Transmission and Interception: Real-time data is transmitted between various systems, devices, and stakeholders. During transmission, there is a risk of interception or unauthorized access, especially if encryption or secure communication protocols are not implemented.
Employing secure data transmission protocols, such as Transport Layer Security (TLS), protects real-time data during transit.
Data Anonymization and Aggregation: In certain cases, sharing real-time data for collaborative purposes or analysis may be required. Anonymizing or aggregating the data before sharing helps protect the privacy of individuals or organizations.
Implementing anonymization techniques, removing personally identifiable information, or aggregating data at a higher level ensures data privacy while still providing valuable insights.
Addressing these security and privacy concerns in real-time data-driven scheduling is vital for manufacturers to safeguard sensitive information, maintain customer trust, and comply with legal and regulatory obligations.
Future Trends: Real-Time Data Advancements in Manufacturing Scheduling
The field of manufacturing scheduling is evolving rapidly with advancements in real-time data technologies. These advancements are transforming the way manufacturing processes are planned, executed, and optimized.
Here are key points highlighting the future trends and advancements in real-time data for manufacturing scheduling:
Internet of Things (IoT) Integration
The integration of IoT devices in manufacturing processes allows for real-time data collection from various sources, such as sensors, machines, and production systems. This enables the continuous monitoring of production parameters, machine performance, and environmental conditions, providing valuable data for scheduling optimization.
- IoT integration in manufacturing scheduling enables real-time monitoring of machines, equipment, and production processes.
- Connected sensors and devices capture data on various parameters such as temperature, humidity, machine performance, and product quality, providing valuable insights for scheduling optimization.
- IoT integration provides enhanced visibility and transparency across the manufacturing process.
- Real-time data on machine status, inventory levels, and production progress can be collected and shared across the organization, enabling better decision-making and effective scheduling adjustments.
Artificial Intelligence (AI) and Machine Learning (ML)
AI and ML technologies are being applied to real-time data in manufacturing scheduling to predict production outcomes, identify patterns, and optimize scheduling decisions.
These technologies can analyze large volumes of real-time data and learn from historical patterns to make accurate predictions and recommendations for scheduling optimization.
- AI and ML enable adaptive scheduling in manufacturing. These technologies can continuously monitor real-time data, such as machine performance, material availability, and workforce capacity, and dynamically adjust schedules in response to changing conditions.
- Adaptive scheduling helps optimize production plans in real time and improves agility in response to unforeseen events or disruptions.
- Demand Forecasting: AI and ML algorithms can analyze historical sales data, market trends, and external factors to accurately forecast demand.
- By incorporating demand forecasting into manufacturing scheduling, organizations can align production capacity and resources with expected customer demand, minimizing inventory costs and reducing lead times.
Edge Computing
Edge computing brings computational power closer to the data source, enabling real-time data processing and analysis at the edge of the network. This reduces latency and allows for faster decision-making based on real-time data, making it ideal for time-sensitive manufacturing scheduling decisions.
- Edge computing in manufacturing scheduling reduces network congestion by processing data locally instead of sending it to a centralized cloud or data center.
- This approach reduces the burden on the network infrastructure and ensures that critical scheduling decisions can be made even in environments with limited or intermittent connectivity.
- Edge computing offers enhanced security for manufacturing scheduling.
- By processing sensitive data locally, it minimizes the need to transmit critical information over external networks, reducing the risk of data breaches or unauthorized access. This localized approach enhances data privacy and protects sensitive scheduling information.
Advanced Analytics and Visualization
Advancements in analytics and visualization tools enable manufacturing schedulers to gain deeper insights from real-time data. Advanced analytics techniques, such as predictive analytics and prescriptive analytics, can identify trends, detect anomalies, and provide recommendations for optimizing schedules based on real-time data.
Cloud-Based Solutions
Cloud computing offers a scalable and flexible infrastructure for real-time data storage, processing, and analysis. Cloud-based solutions provide easy access to real-time data from anywhere, facilitating collaboration and enabling organizations to leverage the power of real-time data for scheduling optimization.
Digital Twins: Digital twins are virtual representations of physical manufacturing assets and processes. By integrating real-time data from sensors and other sources, digital twins enable organizations to simulate and optimize manufacturing scheduling in a virtual environment, minimizing risks and maximizing efficiency.
- Digital twins create virtual representations of physical manufacturing systems, including machines, equipment, and processes.
- In manufacturing scheduling, digital twins provide a detailed and accurate model of the production environment, allowing schedulers to simulate and optimize schedules in a virtual setting before implementing them in the real world.
- Digital twins allow for what-if analysis in manufacturing scheduling. Schedulers can simulate various scenarios and evaluate the impact of different scheduling decisions on key performance indicators such as production throughput, resource utilization, or customer delivery times.
- This capability enables schedulers to make informed decisions based on a comprehensive understanding of potential outcomes.
Integration with Supply Chain Networks
Real-time data advancements in manufacturing scheduling are driving closer integration with supply chain networks. By sharing real-time data across suppliers, manufacturers, and customers, organizations can achieve better synchronization, demand visibility, and collaboration, resulting in more efficient scheduling across the entire supply chain.
How Can Deskera Help You?
Deskera MRP allows you to closely monitor the manufacturing process. From the bill of materials to the production planning features, the solution helps you stay on top of your game and keep your company's competitive edge.
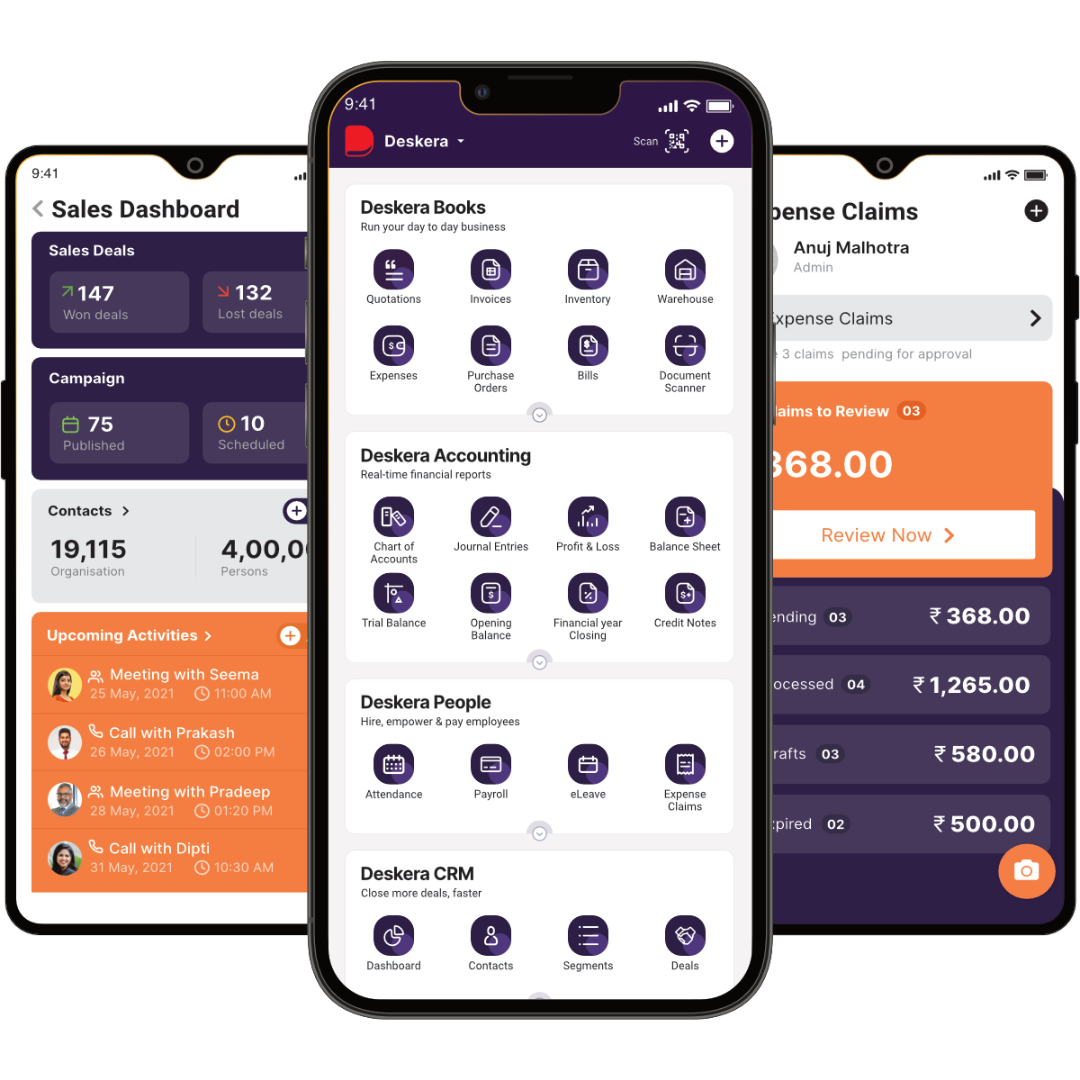
Deskera ERP and MRP system can help you:
- Manage production plans
- Maintain Bill of Materials
- Generate detailed reports
- Create a custom dashboard
Deskera ERP is a comprehensive system that allows you to maintain inventory, manage suppliers, and track supply chain activity in real-time, as well as streamline a variety of other corporate operations.
Deskera Books enables you to manage your accounts and finances more effectively. Maintain sound accounting practices by automating accounting operations such as billing, invoicing, and payment processing.
Deskera CRM is a strong solution that manages your sales and assists you in closing agreements quickly. It not only allows you to do critical duties such as lead generation via email, but it also provides you with a comprehensive view of your sales funnel.
Deskera People is a simple tool for taking control of your human resource management functions. The technology not only speeds up payroll processing but also allows you to manage all other activities such as overtime, benefits, bonuses, training programs, and much more. This is your chance to grow your business, increase earnings, and improve the efficiency of the entire production process.
Conclusion
Real-time data plays a crucial role in successful manufacturing production scheduling. It provides manufacturers with accurate and up-to-date information about various aspects of the production process, enabling them to make informed decisions and optimize scheduling for improved efficiency and productivity.
Real-time data allows manufacturers to monitor production activities in real time, track inventory levels, analyze machine performance, and assess overall production performance. By leveraging real-time data, manufacturers can identify bottlenecks, optimize resource allocation, minimize downtime, and respond quickly to changes in demand or production constraints.
Furthermore, real-time data enables manufacturers to implement predictive analytics and machine learning algorithms for more accurate forecasting and planning.
By analyzing historical and real-time data, manufacturers can identify patterns and trends, forecast demand more accurately, and optimize production schedules accordingly.
Moreover, real-time data facilitates the adoption of advanced technologies such as the Internet of Things (IoT), which enables the integration of sensors and devices throughout the production process. IoT sensors can collect and transmit real-time data on machine performance, energy consumption, quality parameters, and other relevant metrics.
Key Takeaways
- Real-time data enables manufacturers to monitor production activities in real time, track inventory levels, analyze machine performance, and assess overall production performance.
- By leveraging real-time data, manufacturers can identify bottlenecks, optimize resource allocation, minimize downtime, and respond quickly to changes in demand or production constraints.
- Real-time data facilitates proactive decision-making by providing manufacturers with timely information on machine performance, material availability, and workforce capacity.
- Improved communication and collaboration among different departments and stakeholders are facilitated by real-time data, enabling faster decision-making and problem-solving.
- Real-time data allows manufacturers to implement predictive analytics and machine learning algorithms for more accurate forecasting and planning.
- Real-time data enhances visibility into the manufacturing process, enabling manufacturers to identify inefficiencies, bottlenecks, and areas for improvement.
- Manufacturers can leverage real-time data to track and monitor key performance indicators (KPIs) and measure their performance against predefined goals.
- Real-time data enables manufacturers to identify patterns and trends, forecast demand accurately, optimizes production scheduling, and avoid overproduction or stockouts.
- The integration of real-time data with advanced technologies such as the Internet of Things (IoT) allows for better equipment monitoring, anomaly detection, and optimized maintenance activities.
- Robust data collection systems, secure networks, data storage, and processing capabilities are essential for effectively leveraging real-time data in production scheduling.
Related Articles
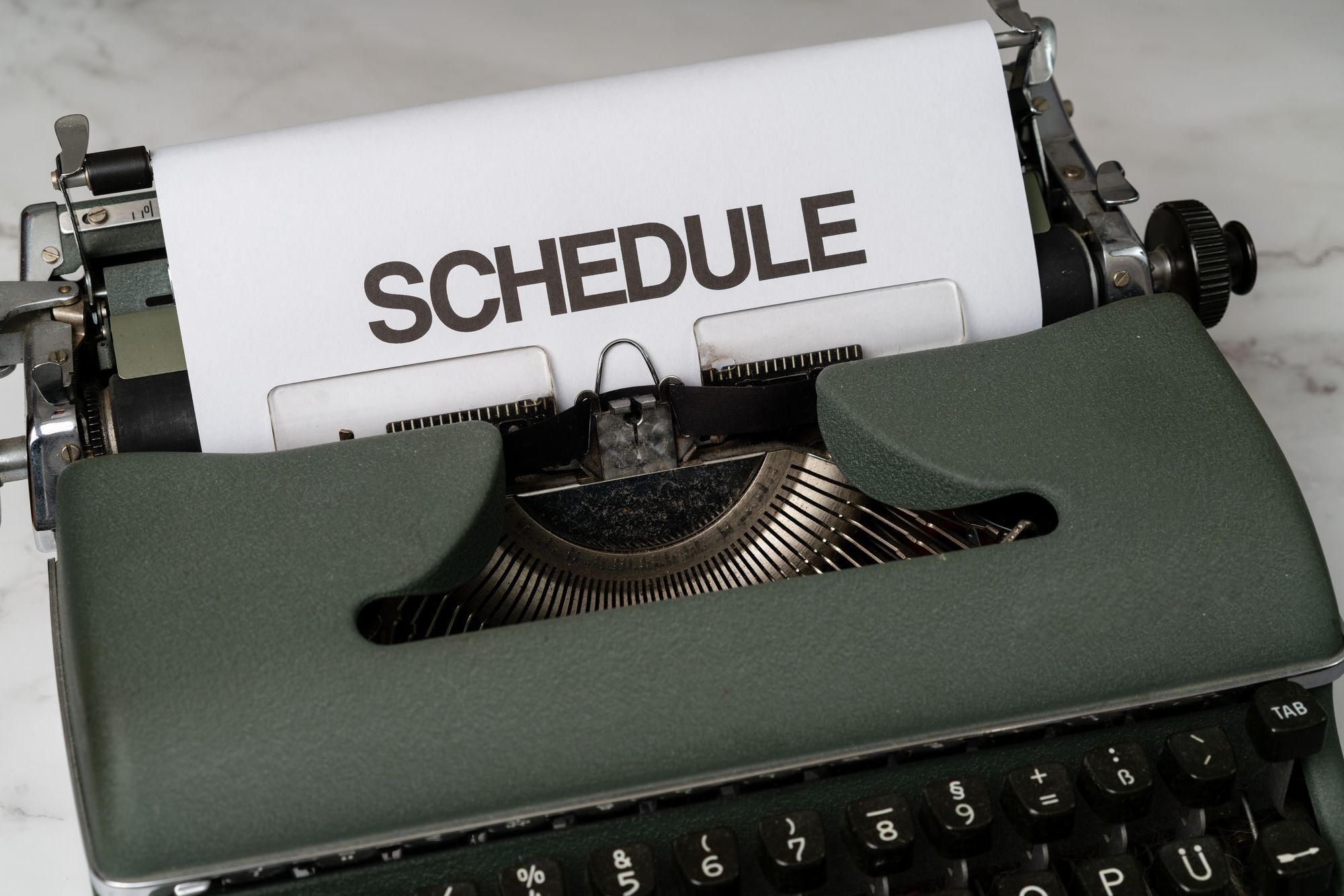
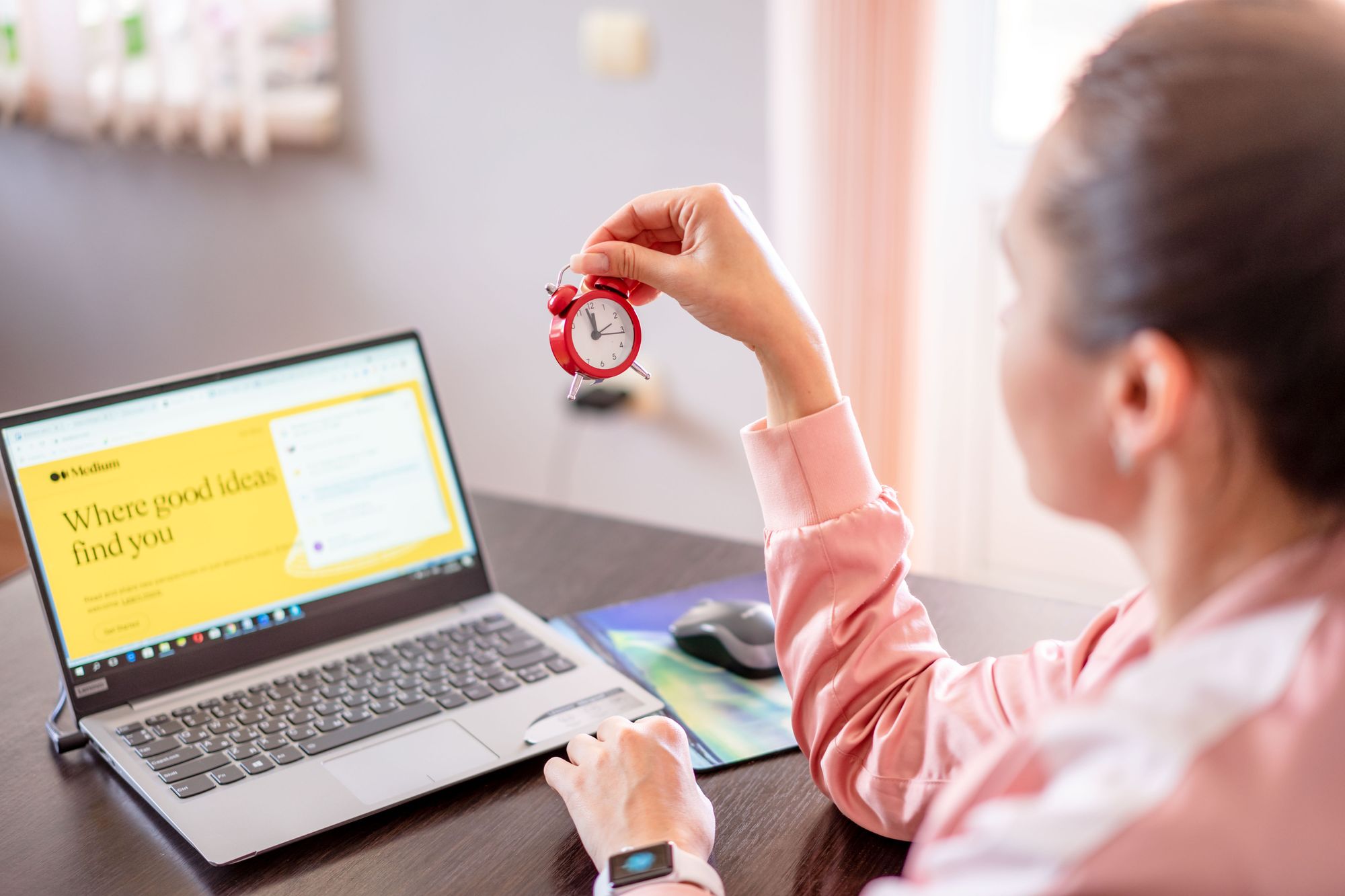
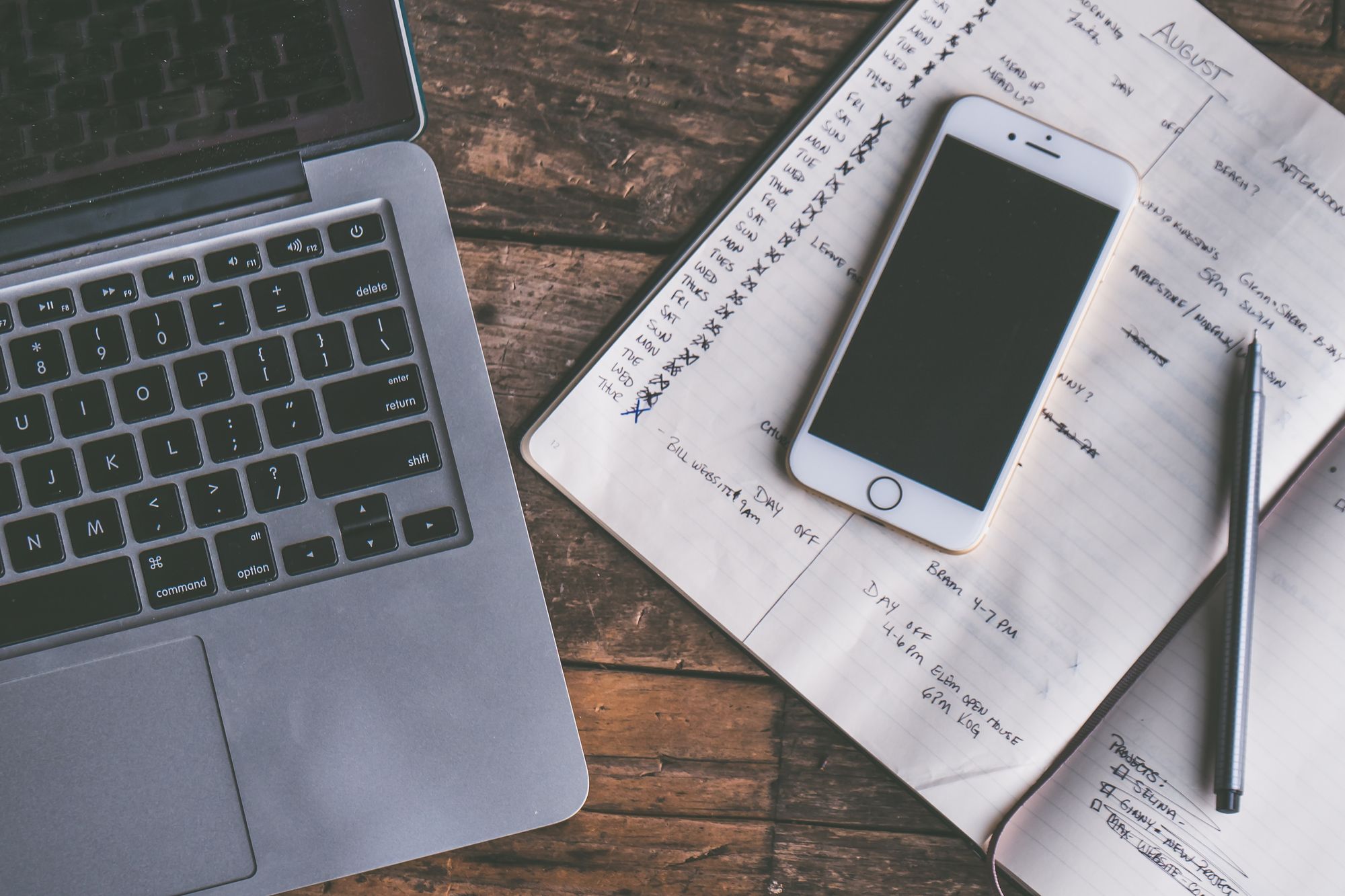
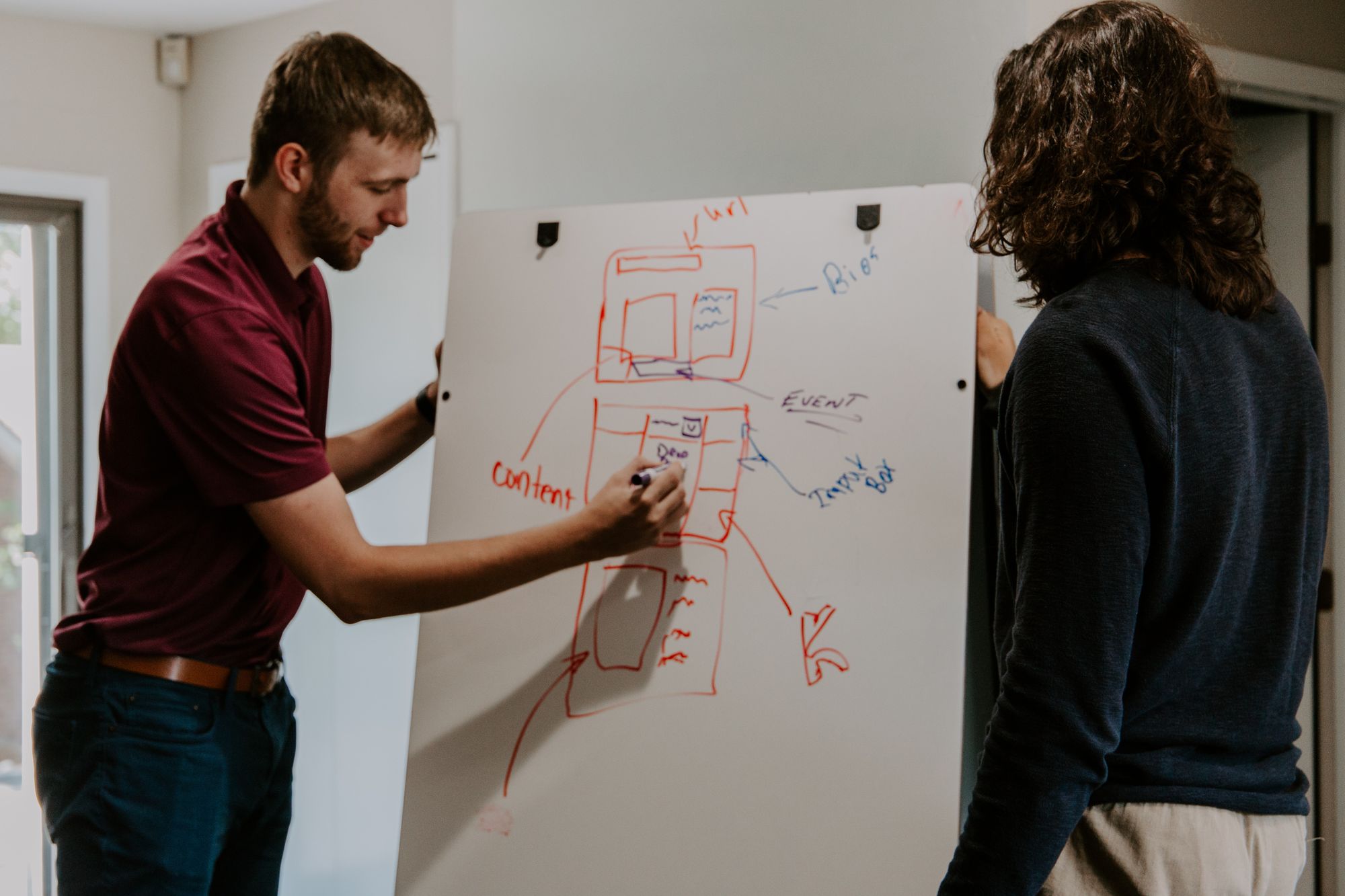