Plastic manufacturing is a complex process that involves the use of many different types of materials. In order to make sure that the final product is of high quality, it is essential that all the steps in the manufacturing process are conducted correctly.
In this article, we’ve discussed some of the key aspects of quality control in plastics manufacturing. Let’s take a look at the table of content below:
- Meaning of Quality Control in Plastic Manufacturing
- Types of Plastic Manufacturing Processes
- Reasons to Employ a Plastics Quality Control Test
- Key Quality Control Measures in Plastic Manufacturing
- Common Quality Control Issues, Prevention & Correction
- Regulatory Requirements
- Manufacturers' Quality Control Measures
- Frequently Asked Questions (FAQs) Associated with Quality Control in Plastic Manufacturing
- How Deskera Can Assist You?
Let's get started!
Meaning of Quality Control in Plastic Manufacturing
Quality control in plastic manufacturing refers to the process of monitoring and inspecting various stages of the manufacturing process to ensure that the final plastic products meet certain standards of quality.
It includes checking for defects, such as surface imperfections, warping, dimensional accuracy, and other potential issues that can impact the performance, durability, and safety of the product.
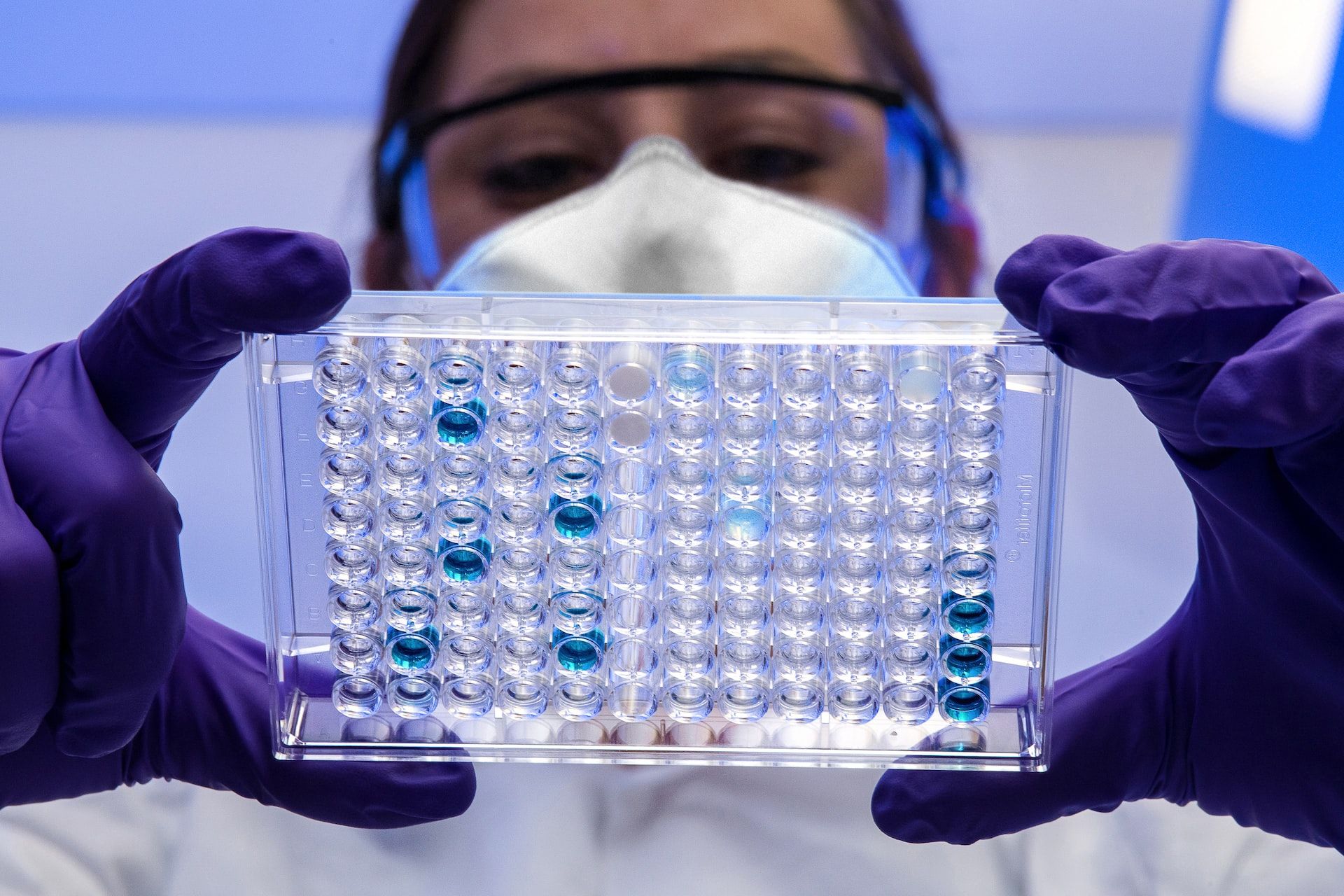
The goal of quality control is to ensure that the plastic products manufactured meet the customer's specifications and expectations, while also complying with regulatory requirements and safety standards.
This involves implementing a range of quality control measures, including statistical process control, visual inspection, mechanical testing, and other techniques to ensure that the products meet the desired level of quality.
Types of Plastic Manufacturing Processes
There are several types of plastic manufacturing processes, including:
- Injection Molding: Injection molding is a popular process for producing plastic parts in high volumes. In this process, plastic is melted and injected into a mold to create the desired shape.
- Blow Molding: Blow molding is used to create hollow plastic parts, such as bottles and containers. In this process, a molten tube of plastic is inflated into a mold to create the desired shape.
- Extrusion: Extrusion is a continuous process used to create plastic products with a consistent cross-section. In this process, plastic is melted and pushed through a die to create a specific shape.
- Thermoforming: Thermoforming is used to create plastic products with a complex shape or design. In this process, a heated sheet of plastic is formed over a mold to create the desired shape.
- Rotational Molding: Rotational molding is used to create large, hollow plastic products, such as tanks and playground equipment. In this process, plastic is heated and rotated inside a mold to create the desired shape.
- Compression Molding: Compression molding is used to create large, flat plastic parts, such as automotive parts and appliance panels. In this process, plastic is placed in a mold and compressed under high pressure and heat to create the desired shape.
- Transfer Molding: Transfer molding is similar to compression molding but involves placing the plastic material in a heated chamber and then transferring it into a mold cavity to create the desired shape. This process is often used for creating small, precision parts.
Reasons to Employ a Plastics Quality Control Test
Following, we've discussed crucial five reasons why using a quality control test for plastics is important:
Ensuring Product Quality:
Quality control tests can help to ensure that plastic products meet the required specifications and are free from defects. This can improve product quality and consistency, which can lead to increased customer satisfaction and repeat business.
Reducing Waste:
Quality control tests can help to identify defects early in the manufacturing process, allowing manufacturers to correct the issue before producing large quantities of defective parts. This can reduce waste and save time and money.
Improving Efficiency:
By monitoring the manufacturing process and identifying areas where improvements can be made, quality control tests can help to improve efficiency and reduce production time and costs.
Meeting Regulatory Requirements:
Many industries have regulatory requirements for plastic products, such as food contact regulations set by the FDA. Quality control tests can help to ensure that products meet these requirements and comply with applicable regulations.
Maintaining Brand Reputation:
Poor product quality can damage a company's reputation and negatively impact its bottom line. By using quality control tests to ensure product quality and consistency, manufacturers can protect their brand reputation and maintain customer trust.
Key Quality Control Measures in Plastic Manufacturing
Plastic manufacturing requires strict quality control measures to ensure that the final product meets the required standards. Below are the key quality control measures commonly used in plastic manufacturing, how they work, what types of defects they can detect, and practical examples of how they are implemented:
Statistical Process Control (SPC): SPC is a method used to monitor and control the manufacturing process by collecting data on process parameters and analyzing them statistically. SPC can detect process variations and trends that may affect product quality.
For example, if the temperature or pressure during the injection molding process varies, it can result in defects such as warpage, sink marks, or voids. SPC can detect these variations and trends and enable corrective actions to be taken before the defects become significant.
Practical Example: In injection molding, the process parameters such as temperature, pressure, and cycle time are monitored, and a control chart is created to analyze the data. The chart helps identify any variations and trends and helps determine whether the process is within the acceptable limits.
Visual Inspection:
Visual inspection involves visually examining the finished product to identify any surface defects, such as cracks, scratches, or color variations. Visual inspection can detect defects that affect the product's appearance, which can be critical for products that are highly visible or marketed based on their appearance.
Practical Example: In plastic extrusion, the extruded product is visually inspected to identify any surface defects such as bubbles or scratches that may affect its appearance or performance.
Mechanical Testing:
Mechanical testing involves subjecting the finished product to mechanical stresses to assess its strength, durability, and performance. Mechanical testing can detect defects such as brittleness, stress cracking, or deformation under load.
Practical Example: In plastic pipe manufacturing, the finished product is tested to ensure it can withstand the specified pressure without failure. This test involves subjecting the pipe to internal pressure and measuring any deformation or failure.
All in all, statistical process control, visual inspection, and mechanical testing are some of the key quality control measures used in plastic manufacturing. These measures detect defects such as variations in process parameters, surface defects, and mechanical failures. Implementing these measures in practice involves monitoring process parameters, visually inspecting finished products, and subjecting them to mechanical testing to ensure they meet the required standards.
Common Quality Control Issues, Prevention & Correction
Plastic manufacturing involves several steps, and quality control issues can arise at any stage, resulting in defects that affect the product's quality and performance.
Below are some of the most common quality control issues that can occur in plastic manufacturing, how they are caused, and how they can be prevented or corrected:
Warping:
Warping is a common quality control issue that occurs when the plastic part bends or twists out of shape during the cooling process. Warping can be caused by uneven cooling or cooling too quickly.
Prevention: To prevent warping, it is essential to maintain consistent cooling across the plastic part. This can be achieved by adjusting the cooling rate and using mold design that minimizes uneven cooling.
Correction: Warped parts can be corrected by applying heat to the affected area and then reshaping the part back into its original shape.
Sink Marks:
Sink marks are depressions or dents on the surface of a plastic part that occur due to uneven cooling or poor mold design. Sink marks can affect the product's appearance and performance.
Prevention: To prevent sink marks, it is essential to maintain consistent cooling across the part and use mold designs that minimize the chances of uneven cooling.
Correction: Sink marks can be corrected by sanding or filling the affected area to restore the part's surface.
Flashing:
Flashing is the excess material that protrudes from the part's surface due to poor mold design or excess pressure during the injection molding process. Flashing can affect the part's appearance and performance.
Prevention: To prevent flashing, it is essential to optimize the injection molding process and use mold designs that prevent excess material from leaking out of the part's surface.
Correction: Flashing can be corrected by trimming or sanding the excess material from the part's surface.
Tips for identifying and addressing quality control issues before they affect product quality:
- Monitor process parameters: Regular monitoring of process parameters such as temperature, pressure, and cycle time can help identify any variations or trends that may affect product quality.
- Conduct regular inspections: Regular visual inspections of finished parts can help identify surface defects that may affect the product's appearance or performance.
- Use statistical process control: Statistical process control can help identify process variations and trends that may affect product quality.
Have a Quality Management System: Having a quality management system that includes regular audits and corrective action plans can help identify and address quality control issues before they affect product quality.
Overall, warping, sink marks, and flashing are some of the most common quality control issues that can occur in plastic manufacturing. These issues can be prevented by optimizing the manufacturing process and mold design and correcting them by applying heat, sanding, or trimming.
Regular monitoring of process parameters, visual inspections, statistical process control, and implementing a quality management system can help identify and address quality control issues before they affect product quality.
Regulatory Requirements
Plastic manufacturers must adhere to various regulatory requirements to ensure the safety and quality of their products. These requirements may vary depending on the type of plastic, its intended use, and the geographic location where it is being sold.
Below are some of the key regulations and standards that apply to plastic products:
FDA Food Contact Regulations:
The Food and Drug Administration (FDA) regulates plastic materials that come into contact with food to ensure they are safe for use. The FDA sets specific requirements for food contact substances and requires manufacturers to obtain clearance before marketing a product.
RoHS:
The Restriction of Hazardous Substances (RoHS) Directive regulates the use of certain hazardous substances in electrical and electronic equipment, including plastic components.
REACH:
The Registration, Evaluation, Authorization, and Restriction of Chemicals (REACH) Regulation is a European Union regulation that aims to ensure the safe use of chemicals in products, including plastic materials.
ISO 9001:
ISO 9001 is a quality management system standard that sets requirements for a company's quality management system. It helps ensure that products and services meet customer and regulatory requirements.
Compliance with these regulations and standards is crucial for plastic manufacturers to ensure the safety and quality of their products.
Noncompliance can result in legal and financial consequences, such as fines, product recalls, and loss of reputation. Furthermore, noncompliance can also lead to safety issues and harm to consumers, which can have severe implications for a company's reputation and bottom line.
Eventually, plastic manufacturers must adhere to various regulatory requirements to ensure the safety and quality of their products. Some of the key regulations and standards that apply to plastic products include FDA Food Contact Regulations, RoHS, REACH, and ISO 9001. Compliance with these regulations and standards is essential to maintain product safety and quality, avoid legal and financial consequences, and protect a company's reputation and bottom line.
Manufacturers' Quality Control Measures
Establishing tolerances for set-points is a critical part of quality control for plastic manufacturers. Tolerances are the allowable deviation from a set value or specification.
By establishing tolerances for mathematical parameters like fill speed, pack time, and pressure, manufacturers can ensure that the manufacturing process is consistent and produces parts that meet the required specifications.
Modern machinery has made it easier for manufacturers to establish and monitor tolerances for set-points.
For example, computer numerical control (CNC) machines can be programmed with precise set-points for various manufacturing parameters.
The machines can then monitor these parameters during the manufacturing process and make adjustments in real-time to ensure that the parts are within the specified tolerances.
In addition to monitoring set-points, manufacturers may also use statistical process control (SPC) to monitor the entire manufacturing process and identify any trends or patterns that indicate that the process is not operating within the specified tolerances.
SPC allows manufacturers to collect and analyze data on various aspects of the manufacturing process, such as the quality of raw materials, the temperature and pressure of the molding machine, and the dimensions of the finished product.
By analyzing this data, manufacturers can identify areas where the process is not operating within the specified tolerances and make adjustments to improve the process and minimize defects.
By establishing tolerances for set-points and using modern machinery and statistical process control, plastic manufacturers can minimize defects and ensure that their products meet the required specifications. This can improve product quality and consistency, reduce waste, and ultimately lead to increased customer satisfaction.
Frequently Asked Questions (FAQs) Associated with Quality Control in Plastic Manufacturing
Following, we’ve discussed some crucial frequently asked questions linked with quality control in plastic manufacturing. Let’s learn:
Que 1: What types of plastics can be used for manufacturing?
Ans: There are many different types of plastics that can be used for manufacturing, including polyethylene, polypropylene, polystyrene, PVC, PET, and many others. The choice of plastic depends on the desired properties of the finished product, such as strength, stiffness, heat resistance, and chemical resistance.
Que 2: What is injection molding?
Ans: Injection molding is a manufacturing process in which molten plastic is injected into a mold cavity to form a solid part. The process involves heating the plastic to its melting point, injecting it into the mold, and then cooling and solidifying it. Injection molding is commonly used for producing high-volume parts with complex shapes.
Que 3: What is the role of quality control in plastic manufacturing?
Ans: The role of quality control in plastic manufacturing is to ensure that the finished products meet the required specifications and are free from defects. Quality control measures can include monitoring the manufacturing process, performing visual inspections, conducting mechanical testing, and establishing tolerances for set-points.
Que 4: What are some common defects that can occur in plastic manufacturing?
Ans: Common defects in plastic manufacturing include warping, sink marks, flash, and voids. These defects can be caused by factors such as improper molding conditions, poor design, or incorrect material selection.
Que 5: What are some regulatory requirements that plastic manufacturers must adhere to?
Ans: Plastic manufacturers must adhere to a variety of regulatory requirements to ensure product safety and quality. These requirements can include food contact regulations (such as those set by the FDA), environmental regulations, and quality management standards (such as ISO 9001).
Que 6: How can plastic manufacturers minimize defects and ensure product quality?
Ans: Plastic manufacturers can minimize defects and ensure product quality by implementing quality control measures such as statistical process control, visual inspection, and mechanical testing.
They can also establish tolerances for set-points and use modern machinery to monitor and adjust the manufacturing process in real-time. By following these best practices, manufacturers can produce high-quality products that meet the required specifications and customer expectations.
How Deskera Can Assist You?
Deskera's integrated financial planning tools allow investors to better plan their investments and track their progress. It can help investors make decisions faster and more accurately.
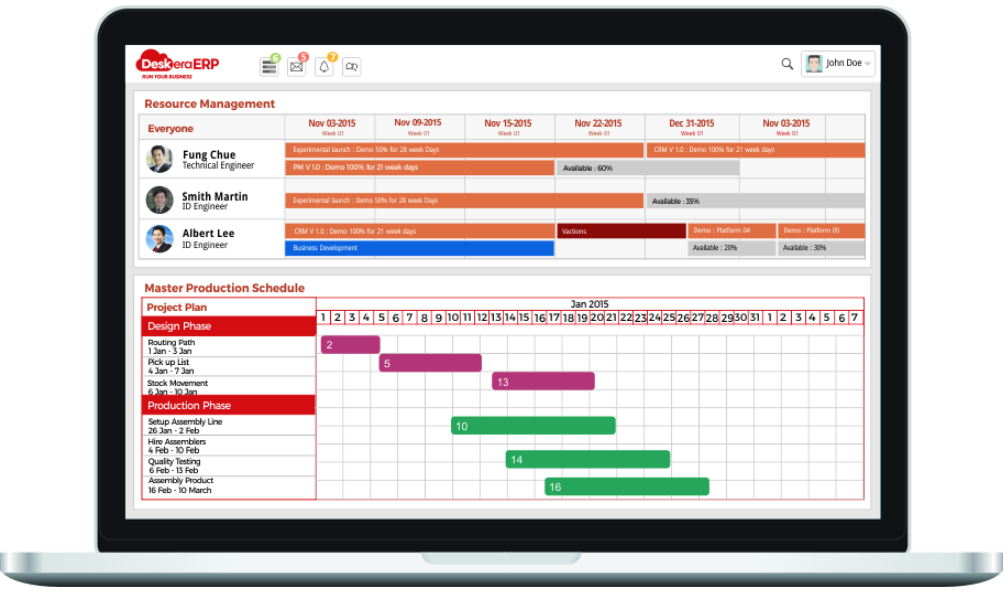
Deskera Books enables you to manage your accounts and finances more effectively. Maintain sound accounting practices by automating accounting operations such as billing, invoicing, and payment processing.
Deskera CRM is a strong solution that manages your sales and assists you in closing agreements quickly. It not only allows you to do critical duties such as lead generation via email, but it also provides you with a comprehensive view of your sales funnel.
Deskera People is a simple tool for taking control of your human resource management functions. The technology not only speeds up payroll processing but also allows you to manage all other activities such as overtime, benefits, bonuses, training programs, and much more. This is your chance to grow your business, increase earnings, and improve the efficiency of the entire production process.
Final Takeaways
We've arrived at the last section of this guide. Let's have a look at some of the most important points to remember:
- Quality control in plastic manufacturing refers to the process of monitoring and inspecting various stages of the manufacturing process to ensure that the final plastic products meet certain standards of quality.
- Reducing waste: Quality control tests can help to identify defects early in the manufacturing process, allowing manufacturers to correct the issue before producing large quantities of defective parts. This can reduce waste and save time and money.
- Maintaining brand reputation: Poor product quality can damage a company's reputation and negatively impact its bottom line. By using quality control tests to ensure product quality and consistency, manufacturers can protect their brand reputation and maintain customer trust.
- SPC is a method used to monitor and control the manufacturing process by collecting data on process parameters and analyzing them statistically. SPC can detect process variations and trends that may affect product quality.
- Visual inspection involves visually examining the finished product to identify any surface defects, such as cracks, scratches, or color variations. Visual inspection can detect defects that affect the product's appearance, which can be critical for products that are highly visible or marketed based on their appearance.
- The Food and Drug Administration (FDA) regulates plastic materials that come into contact with food to ensure they are safe for use. The FDA sets specific requirements for food contact substances and requires manufacturers to obtain clearance before marketing a product.
Related Articles
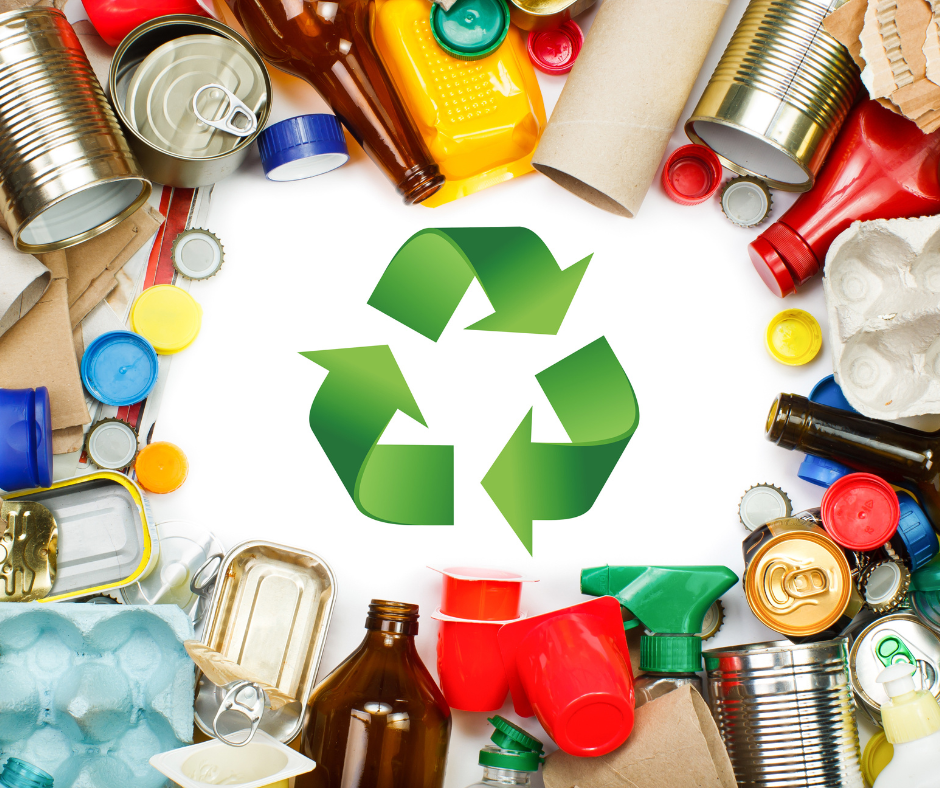

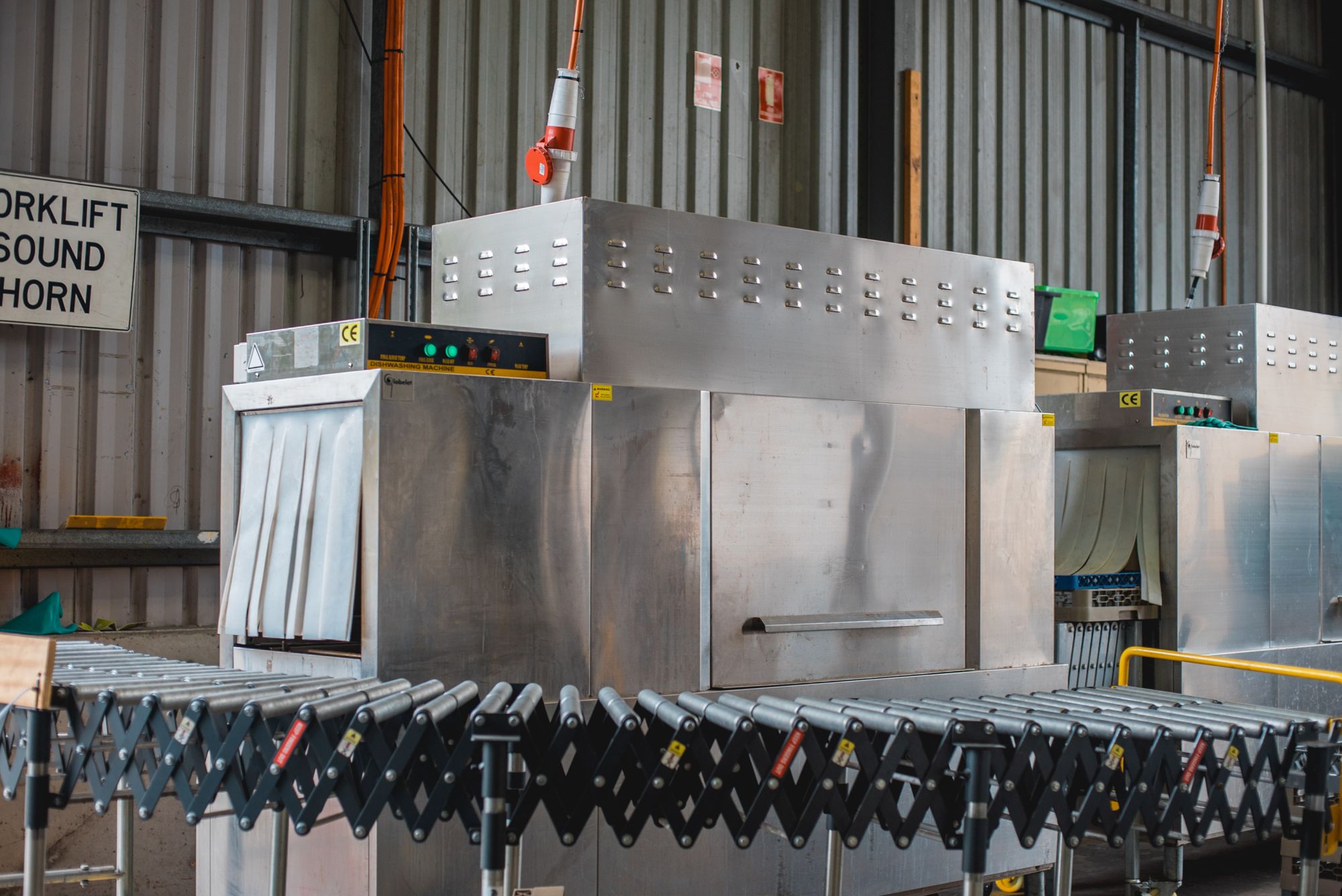
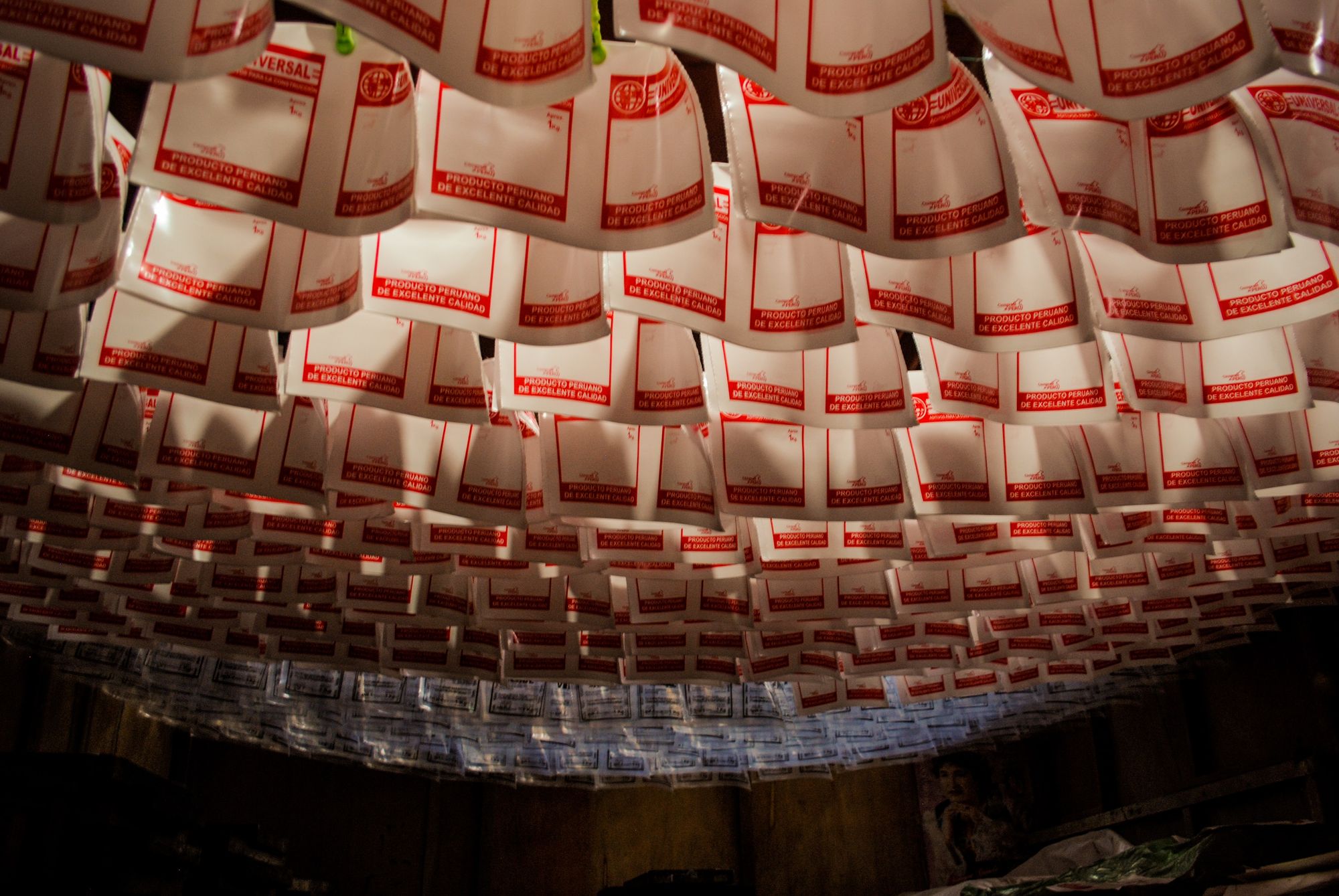
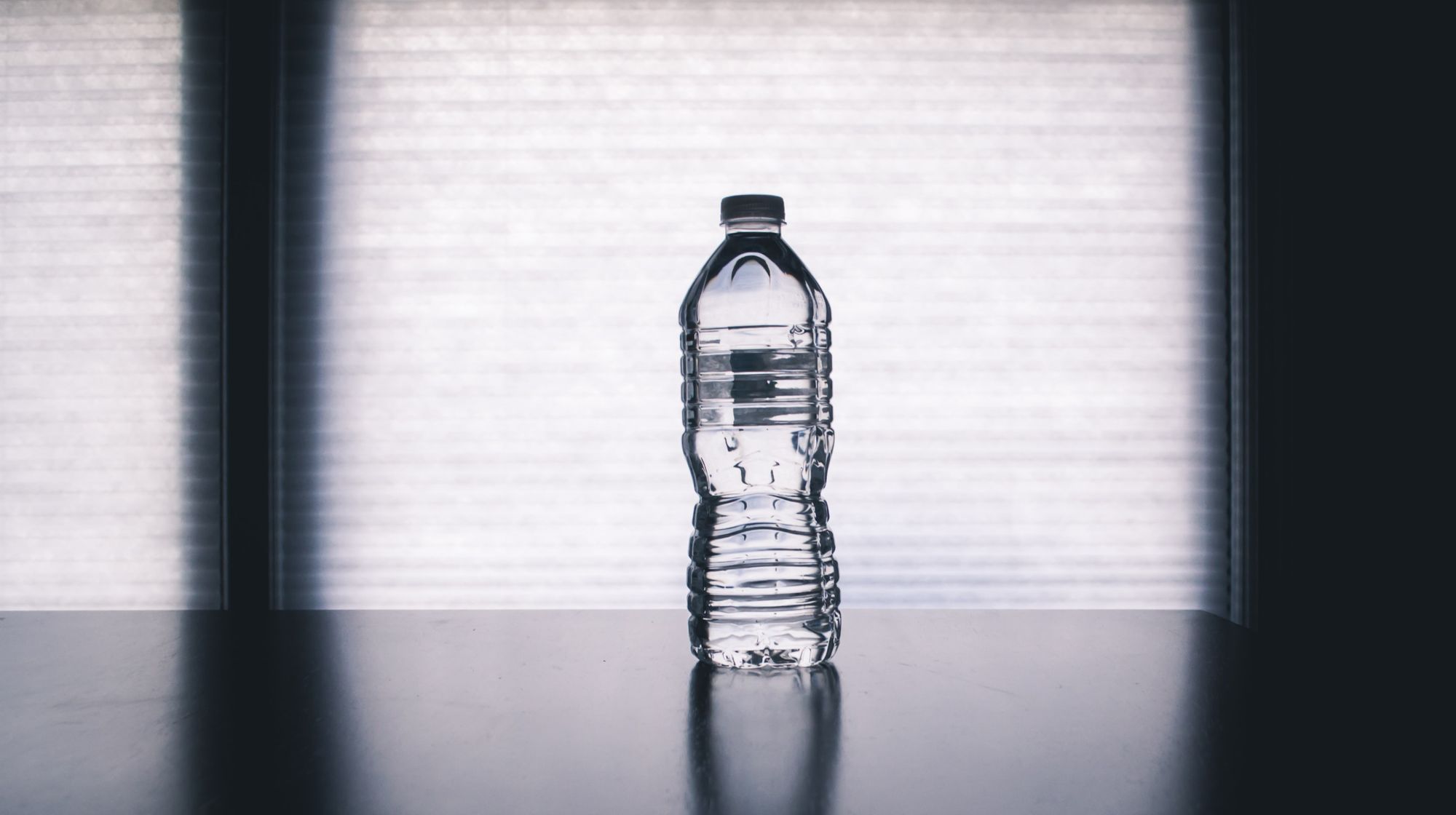