In a survey conducted by Industry Week, 91% of manufacturers said that quality control was the most important factor in maintaining customer satisfaction. According to a report by MarketsandMarkets, the global market for paper testing, inspection, and certification is projected to reach $11.9 billion by 2025, driven by the growing demand for high-quality paper products.
These statistics highlight the importance of quality control in paper production and its positive impact on product quality, customer satisfaction, and environmental sustainability.
Ensuring quality control in paper production is essential to meet customer expectations, maintain production efficiency, and minimize waste. Quality control involves taking measures to ensure that the paper produced meets the required standards and specifications.
This article will discuss various strategies that paper manufacturers can implement to ensure quality control in paper production:
- Why is Quality Control Essential in Paper Production?
- Key Strategies For Achieving Quality Control In Paper Production
- Testing and Sampling
- Process Control
- Training and Education
- Quality Assurance Programs
- Inspection and Testing Equipment
- Traceability
- How can Deskera Help You?
- Key Takeaways
- Related Articles
Why is Quality Control Essential in Paper Production?
Quality control is important in paper production for several reasons, including:
- Meeting customer requirements: Customers expect paper products to meet specific requirements, such as strength, thickness, and brightness. Quality control ensures that the paper produced meets these requirements consistently.
- Reducing waste: Producing paper that does not meet the required specifications can result in waste, as the paper may need to be discarded or recycled. Quality control can help identify any issues early on, reducing waste and improving production efficiency.
- Improving product quality: Quality control helps ensure that the paper produced is of high quality, which can lead to improved customer satisfaction and increased sales.
- Compliance with regulations: Paper manufacturers must comply with various regulations related to product quality and safety. Quality control helps ensure that the paper produced meets these regulations and standards.
- Protecting brand reputation: Producing high-quality paper consistently helps protect the brand reputation of the manufacturer. Customers are more likely to trust and continue to purchase from a manufacturer that consistently produces high-quality paper.
In summary, quality control is essential in paper production to ensure that the paper produced meets customer requirements, reduces waste, improves product quality, complies with regulations, and protects brand reputation.
Key Strategies For Achieving Quality Control In Paper Production
Ensuring quality control in paper production is crucial to meet customer expectations, maintain production efficiency, and minimize waste. Here are some key strategies for achieving quality control in paper production:
Testing and Sampling
Testing and sampling are critical components of quality control in paper production. Regular testing and sampling of the paper throughout the production process can help identify and address any issues early on, ensuring that the final product meets the required specifications and standards.
There are several tests that paper manufacturers can conduct to ensure that the paper produced meets the required specifications. These include:
- Strength Tests: These tests determine how much force is required to tear the paper or how much weight the paper can hold. Tensile strength, tear strength, and burst strength are all common tests used to evaluate paper strength.
- Porosity Tests: These tests determine how easily ink can pass through the paper. Porosity testers measure the amount of air that can pass through a specified area of paper in a given amount of time.
- Smoothness Tests: These tests determine the paper's finish. Air leak testers or Sheffield smoothness testers are commonly used to measure the smoothness of the paper surface.
- Thickness Tests: These tests measure the thickness of the paper to ensure that it is consistent and meets the required specifications.
In addition to these tests, paper manufacturers also use sampling to ensure quality control. Sampling involves selecting a portion of the paper produced and analyzing it to ensure that it meets the required specifications. Paper manufacturers may use different sampling methods, such as random sampling or systematic sampling, depending on their requirements.
Regular testing and sampling help paper manufacturers identify any quality issues early on, allowing them to make necessary adjustments to the production process before it is too late. This can prevent the production of substandard paper and reduce waste, ultimately leading to a more efficient and profitable production process.
Process Control
Process control is another critical component of quality control in paper production. Process control involves monitoring and controlling the paper production process to ensure that the paper meets the required specifications and standards.
There are several process control methods that paper manufacturers can use to ensure quality control. These include:
- Process monitoring: This involves monitoring the paper production process for any variations or deviations from the standard operating procedures. Process monitoring can be done through regular visual inspections, automated sensors, or other monitoring systems.
- Statistical process control: This involves using statistical tools to analyze and monitor the paper production process. Statistical process control can help identify trends and patterns in the data, allowing manufacturers to make necessary adjustments to the process before it produces substandard paper.
- Feedback control: This involves using feedback from the paper produced to adjust the production process. Feedback control can be done through regular testing and sampling of the paper, as well as through customer feedback and complaints.
By implementing process control methods, paper manufacturers can ensure that the paper produced meets the required specifications and standards. Process control methods can help identify any issues early on, allowing manufacturers to make necessary adjustments to the process before it produces substandard paper. This can prevent the production of substandard paper, reduce waste, and improve the overall efficiency of the paper production process.
Training and Education
Training and education are essential components of quality control in paper production. Properly trained employees are critical to maintaining consistent product quality and identifying potential quality issues early on.
There are several areas where training and education can be beneficial in paper production. These include:
- Machine operation: Proper training on how to operate paper production machines is essential to ensuring that the machines are used correctly and that the paper produced meets the required specifications.
- Quality control procedures: Employees involved in the quality control process should be trained on the various tests and sampling methods used in paper production, as well as the required specifications and standards.
- Safety: Proper training on safety procedures is essential to ensure that employees are safe while working in the paper production facility.
- Environmental awareness: Training on environmental regulations and best practices can help employees reduce waste and operate the paper production process in an environmentally responsible manner.
Paper manufacturers can ensure that their employees are knowledgeable and competent in their roles by providing proper training and education. This can improve product quality, reduce waste, and improve production efficiency. Additionally, well-trained employees are more likely to identify potential quality issues early on, leading to quicker resolution of any issues that arise.
Quality Assurance Programs
Quality assurance programs are another critical component of quality control in paper production. Quality assurance programs provide a structured approach to ensuring that the paper produced meets the required specifications and standards.
There are several elements that a quality assurance program should include:
- Standard operating procedures: A quality assurance program should include detailed standard operating procedures (SOPs) that outline the steps required to produce paper that meets the required specifications and standards.
- Documentation: A quality assurance program should require proper documentation of all steps in the paper production process, including testing and sampling results. This documentation can help identify any issues early on and ensure that the paper produced meets the required specifications.
- Auditing: A quality assurance program should include regular auditing to ensure that the paper production process is being followed correctly and that the paper produced meets the required specifications and standards.
- Continuous improvement: A quality assurance program should also include a process for continuous improvement, where any issues identified are addressed and improvements are made to the paper production process.
By implementing a quality assurance program, paper manufacturers can ensure that the paper produced meets the required specifications and standards consistently. A quality assurance program can help identify any issues early on, reducing waste and improving production efficiency. Additionally, a quality assurance program can help build customer trust in the paper produced, leading to improved customer satisfaction and increased sales.
Inspection and Testing Equipment
Inspection and testing equipment is a critical component of quality control in paper production. Proper inspection and testing equipment can help ensure that the paper produced meets the required specifications and standards consistently.
There are several types of inspection and testing equipment that paper manufacturers may use, including:
- Basis weight scale: A basis weight scale is used to measure the weight of a sheet of paper. This measurement is critical to ensuring that the paper produced meets the required basis weight specifications.
- Caliper gauge: A caliper gauge is used to measure the thickness of a sheet of paper. This measurement is critical to ensuring that the paper produced meets the required thickness specifications.
- Tensile tester: A tensile tester is used to measure the strength of a sheet of paper. This measurement is critical to ensuring that the paper produced meets the required strength specifications.
- Brightness meter: A brightness meter is used to measure the brightness of a sheet of paper. This measurement is critical to ensuring that the paper produced meets the required brightness specifications.
- Moisture meter: A moisture meter is used to measure the moisture content of a sheet of paper. This measurement ensures the paper meets the required moisture content specifications.
By using proper inspection and testing equipment, paper manufacturers can ensure that the paper produced meets the required specifications and standards consistently. This can improve product quality, reduce waste, and increase production efficiency. Additionally, proper inspection and testing equipment can help identify any issues early on, allowing for quick resolution and preventing the production of substandard paper.
Traceability
Traceability is an essential aspect of quality control in paper production. Traceability refers to the ability to track the production process and raw materials used to produce a particular batch of paper. This tracking allows manufacturers to identify any issues that may arise during production and take corrective action quickly.
There are several elements to establishing traceability in paper production, including:
- Record keeping: Paper manufacturers must maintain accurate records of all raw materials used in production, including the source, quantity, and quality of each material.
- Lot tracking: Manufacturers must be able to track each batch of paper produced to its corresponding raw materials, production process, and testing and inspection results.
- Barcode and labeling: Barcode and labeling systems can help track raw materials and finished products through the production process.
- Supplier quality management: Manufacturers must ensure that their suppliers meet the required quality standards and are able to provide traceability information for their raw materials.
By establishing traceability in paper production, manufacturers can quickly identify any issues that may arise during production, such as quality issues or contamination. This can reduce waste, improve product quality, and increase production efficiency. Additionally, traceability can help build customer trust in the paper produced, leading to improved customer satisfaction and increased sales.
How can Deskera Help You?
Deskera's integrated financial planning tools allow investors to better plan their investments and track their progress. It can help investors make decisions faster and more accurately.
Deskera Books can assist you in automating your accounting and mitigating business risks. Deskera makes it easier to create invoices by automating many other procedures, reducing your team's administrative workload.
Deskera also offers a suite of integrated applications to help businesses manage their financials, inventory, and operations. Furthermore, other business aspects such as HR (Deskera People), CRM (Deskera CRM), and ERP are provided by Deskera. These could be crucial and can help short sellers keep track of their businesses and make better decisions.
Key Takeaways
Here's a summary of ensuring quality control in paper production in bullet points:
- Establish clear specifications for raw materials, production processes, and finished products.
- Use quality control tools like statistical process control (SPC) and Six Sigma.
- Perform regular inspections and testing throughout the production process.
- Train employees on quality control procedures and the importance of consistent quality.
- Implement corrective actions immediately when quality issues are identified.
Related Articles
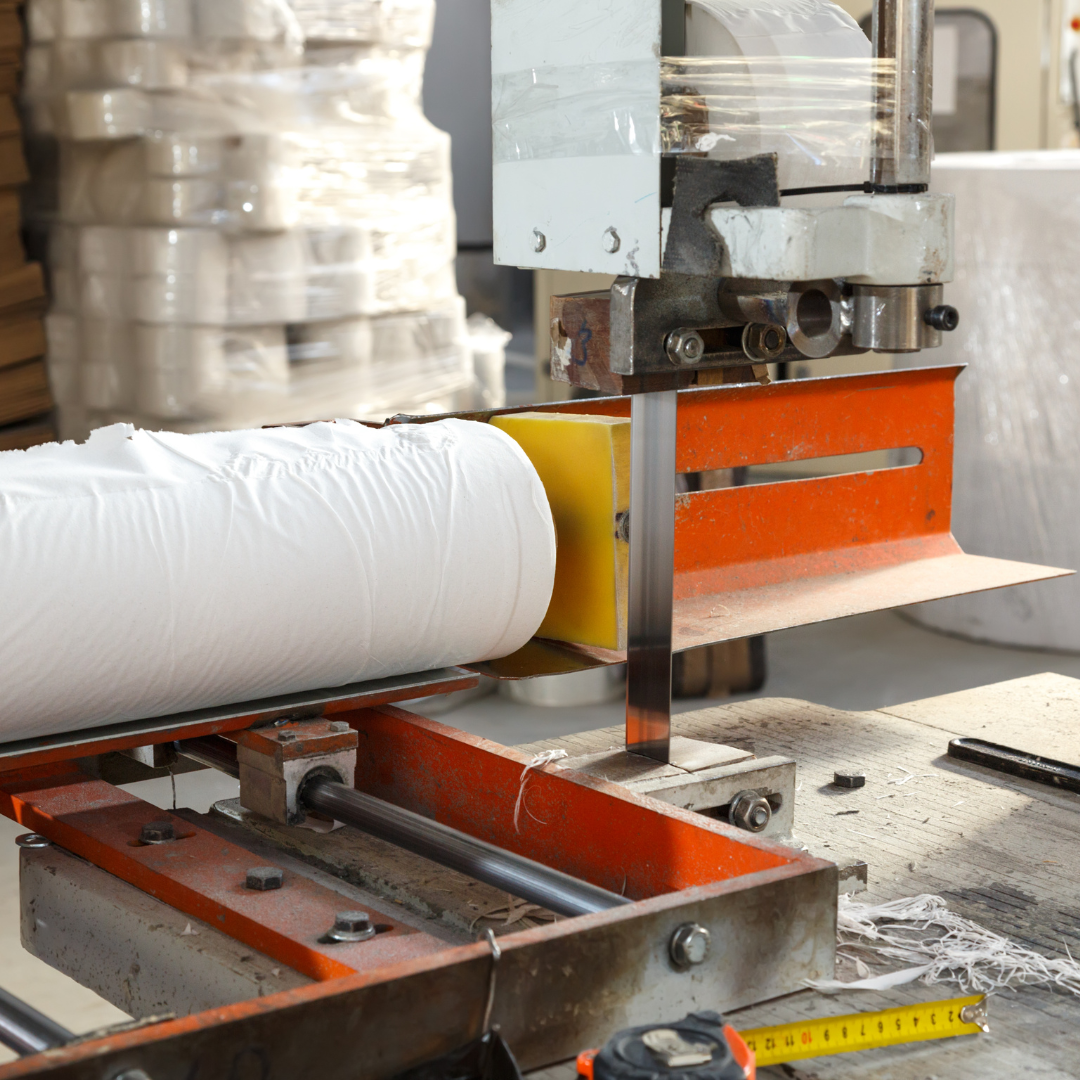
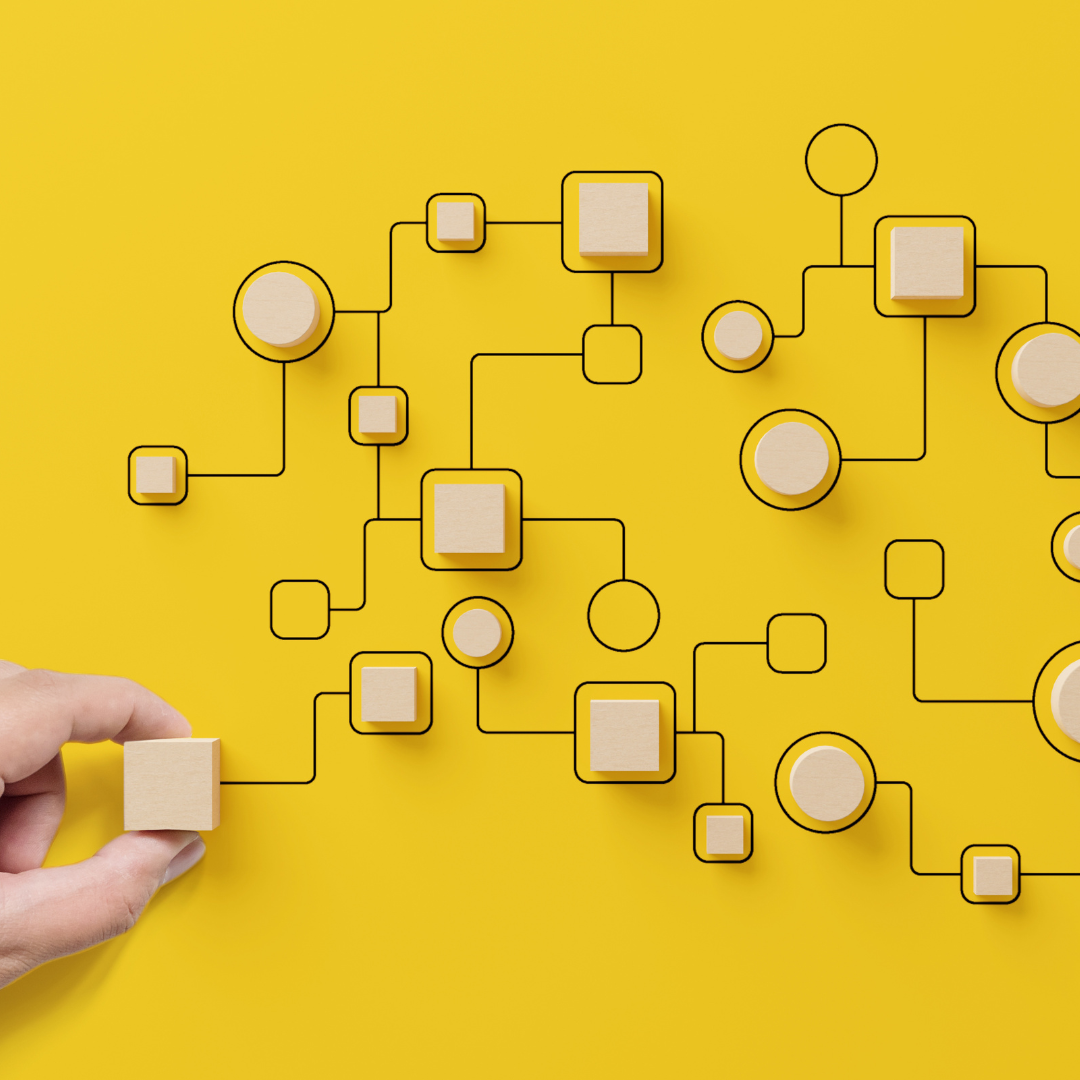
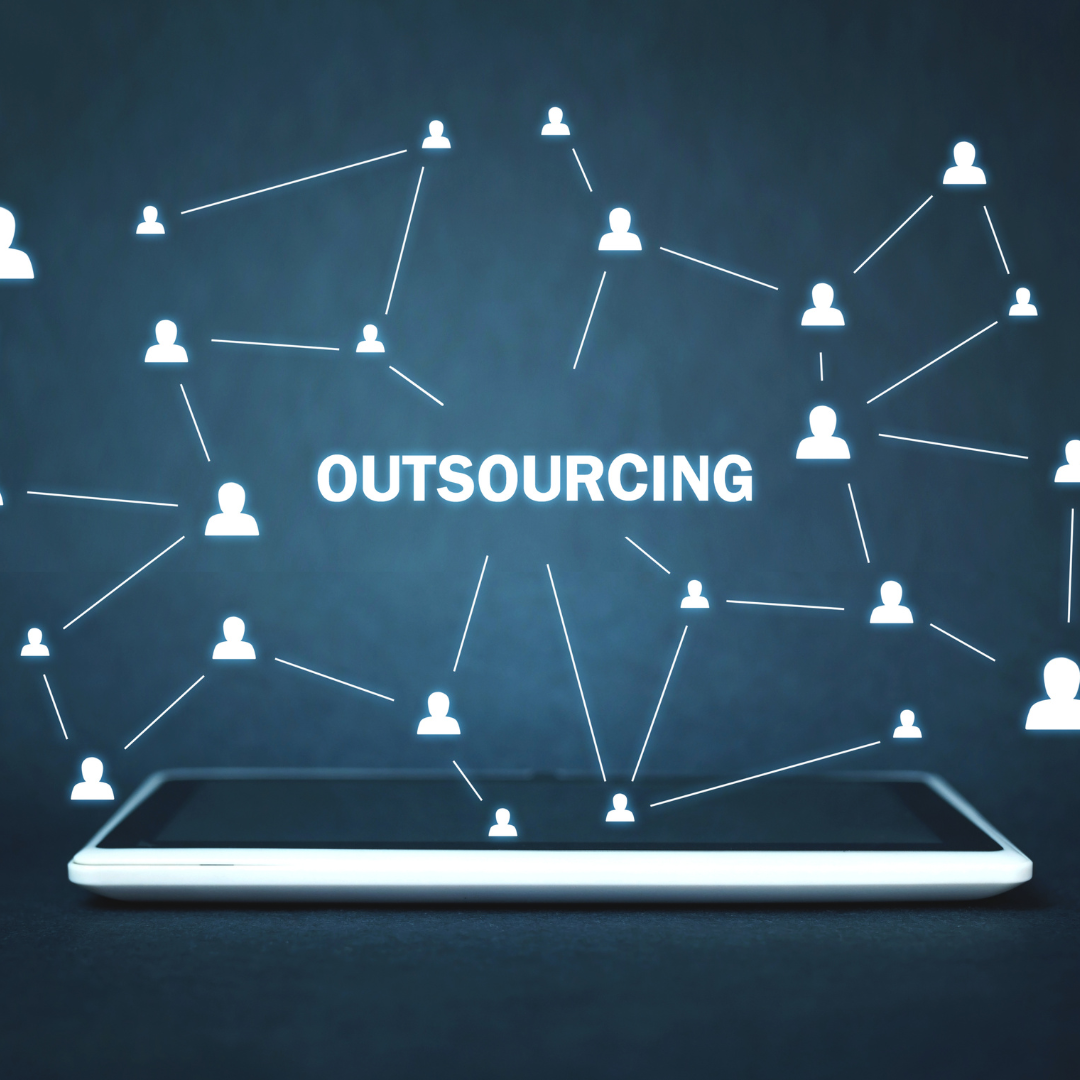
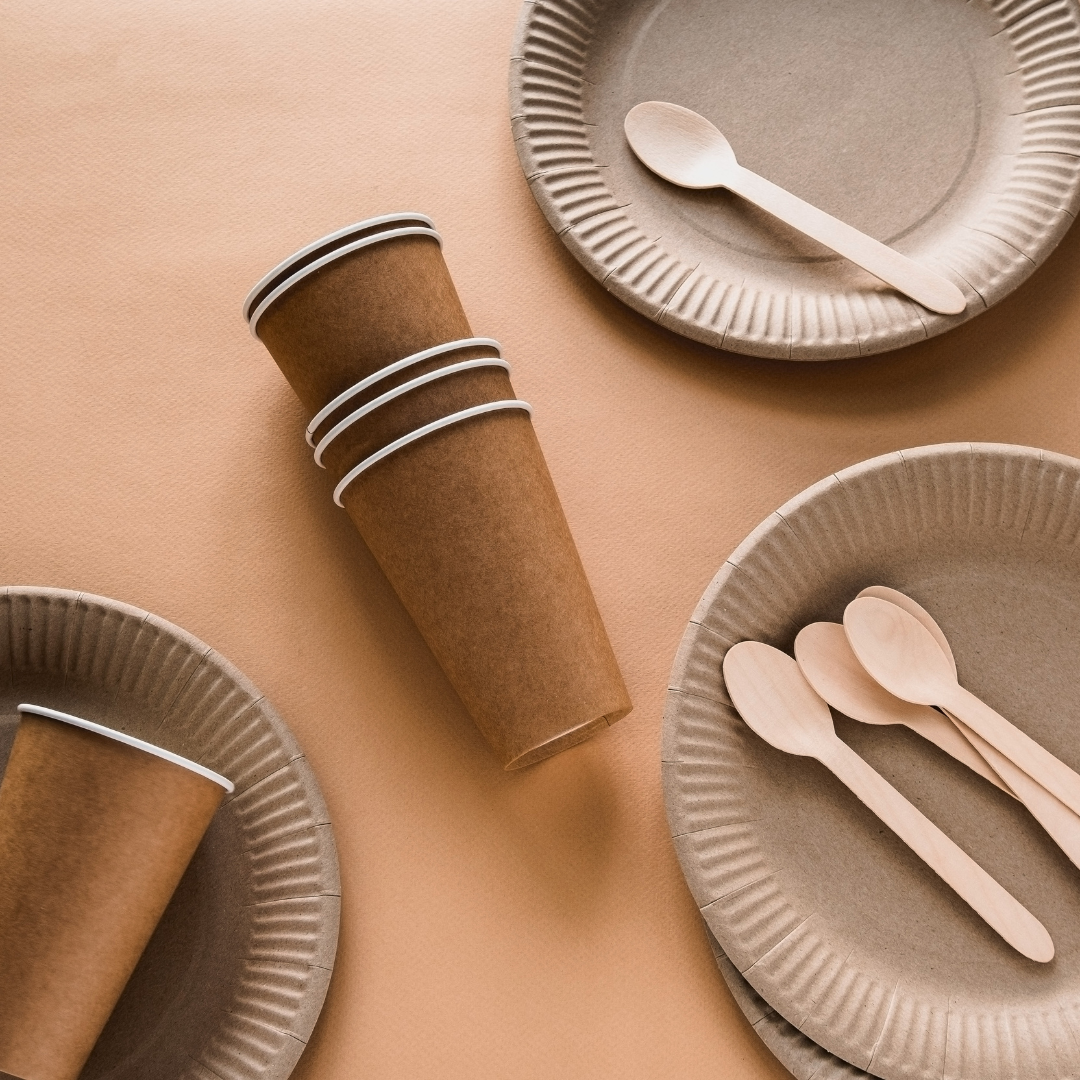