Have you ever wondered why some businesses struggle with excess inventory while others face stockouts? The answer often lies in their manufacturing strategy—whether they follow a push or pull approach. These two production models define how companies manage demand, inventory, and production planning, directly impacting efficiency and profitability.
Push manufacturing relies on demand forecasts to produce goods in advance, ensuring stock availability but risking overproduction. In contrast, pull manufacturing is demand-driven, producing only what is required, minimizing waste but risking delays if demand surges unexpectedly. Choosing the right approach depends on factors like market predictability, operational flexibility, and supply chain responsiveness.
This is where Deskera manufacturing ERP plays a crucial role. By integrating real-time demand forecasting, automated inventory management, and seamless production planning, Deskera manufacturing ERP helps businesses optimize both push and pull manufacturing models. Whether a company needs better stock control or faster production response, Deskera manufacturing ERP ensures smoother operations with data-driven decision-making.
Understanding push vs. pull manufacturing is essential for companies aiming to balance efficiency and customer satisfaction. In this article, we’ll explore the key differences, benefits, and challenges of each model, helping you determine which approach best suits your business.
What is Push Manufacturing?
Push manufacturing is a production strategy that relies on forecasted demand rather than real-time customer orders. In this approach, manufacturers produce goods in advance based on sales projections, ensuring that products are available for immediate distribution.
The goal is to optimize production efficiency, reduce per-unit costs, and maintain a steady supply in the market. However, inaccurate forecasts can lead to overproduction, excessive inventory, and higher storage costs.
Key Characteristics of Push Manufacturing
- Forecast-Based Production – Companies use demand predictions to determine the quantity and type of products to manufacture.
- High Inventory Levels – Large quantities of finished goods are stored in warehouses to meet future demand.
- Longer Lead Times – Since production is completed before customer orders, there may be delays if adjustments are needed.
- Higher Costs – Maintaining large inventories increases storage, logistics, and potential waste costs.
- Emphasis on Sales & Marketing – Businesses must actively promote products to drive demand and avoid excess inventory.
Industries and Products That Use Push Manufacturing
Push manufacturing is ideal for industries with stable and predictable demand, where mass production offers cost advantages. Common examples include:
- Fast-moving consumer goods (FMCG) – Packaged foods, personal care products, and cleaning supplies.
- Clothing & Textiles – Seasonal fashion collections produced ahead of time.
- Pharmaceuticals – Medications manufactured in advance based on regulatory approvals and demand forecasts.
- Electronics & Automotive – Large-scale production of smartphones, laptops, and cars based on projected sales.
- Construction Materials – Cement, steel, and lumber stockpiled for future building projects.
A Classic Example: Ford’s Model T
One of the most famous applications of push manufacturing was Henry Ford’s Model T production in the early 20th century. By standardizing the assembly line, Ford could mass-produce vehicles at lower costs and push them into the market efficiently. However, limited customization options (such as the Model T being available only in black for over a decade) highlighted the downside of a strict push system.
Push manufacturing remains a powerful strategy for businesses that benefit from economies of scale. However, in fast-changing markets, companies often integrate pull-based elements to enhance flexibility and reduce inventory risks.
What is Pull Manufacturing?
Pull manufacturing is a production strategy where products are created based on actual customer demand rather than forecasted estimates. In this system, production is initiated only when an order is placed, minimizing inventory levels and reducing waste.
Pull manufacturing aligns closely with lean manufacturing principles and often incorporates Just-in-Time (JIT) techniques to ensure efficient resource utilization.
This approach contrasts with push manufacturing, where goods are produced in anticipation of future demand, leading to potential overproduction and excess inventory.
Key Characteristics of Pull Manufacturing
- Demand-Driven Production
- Products are manufactured only when there is a confirmed customer order.
- Reduces the risk of overproduction and obsolete inventory.
- Low Inventory Levels
- Companies maintain minimal stock, relying on JIT replenishment.
- Reduces storage costs and improves cash flow.
- Increased Flexibility
- Enables rapid adaptation to changes in customer demand.
- Ideal for industries with short product lifecycles or customized orders.
- Shorter Lead Times
- Streamlines the supply chain to fulfill orders quickly.
- Reduces delays and enhances customer satisfaction.
- Waste Reduction
- Eliminates unnecessary production and excess raw material usage.
- Supports sustainable and cost-efficient manufacturing.
- Improved Quality Control
- Focuses on producing high-quality goods tailored to specific customer needs.
- Reduces defects and waste associated with mass production.
Industries and Products Best Suited for Pull Manufacturing
Pull manufacturing is ideal for industries that require flexibility, customization, and responsiveness to market trends. Some examples include:
- Customized or Made-to-Order Products – Furniture, personalized gifts, and custom apparel.
- High-Tech and Electronics – Smartphones, computer components, and innovative gadgets.
- Food and Beverage – Restaurants and food service providers preparing fresh meals.
- Healthcare – Medical devices, custom prosthetics, and pharmaceuticals tailored to patient needs.
- Printing and Publishing – Print-on-demand services for books, packaging, and marketing materials.
By implementing a pull manufacturing system, businesses can minimize waste, optimize efficiency, and enhance customer satisfaction through demand-driven production.
Toyota Production System (TPS) – A Benchmark in Pull Manufacturing
Toyota revolutionized the automotive industry with its Just-in-Time (JIT) manufacturing, a core principle of pull manufacturing. Instead of producing vehicles based on forecasts, Toyota builds cars only when there is customer demand.
How Toyota’s Pull Manufacturing Works:
- Customer Orders Trigger Production
Toyota doesn’t mass-produce cars in advance. Instead, each vehicle is assembled only after a customer places an order.
- Minimal Inventory Stock
Raw materials and components are ordered only when needed to fulfill existing customer orders, reducing excess stock and storage costs.
- Kanban System for Workflow Efficiency
Toyota uses a Kanban system, where production is signaled only when the next stage in the supply chain requires parts, ensuring a smooth flow without overproduction.
- Just-in-Time Delivery from Suppliers
Parts arrive at assembly plants precisely when needed, minimizing holding costs and waste.
Push Manufacturing vs. Pull Manufacturing
Push and pull manufacturing are two distinct production strategies that determine how products are manufactured, stocked, and delivered to customers.
Which System is Better?
- Push Manufacturing is best for standardized products with predictable demand, such as FMCG (fast-moving consumer goods), pharmaceuticals, and consumer electronics.
- Pull Manufacturing is ideal for industries with fluctuating demand, customization needs, or high-cost inventory, such as automobiles, fashion, healthcare, and food services.
Many companies today combine both approaches, using a hybrid push-pull system to optimize inventory management and production efficiency.
Pros and Cons of Push Manufacturing
Push manufacturing operates on a make-to-stock (MTS) basis, where goods are produced in anticipation of future demand. While it offers advantages in efficiency and lead time reduction, it also has drawbacks related to inventory management and demand forecasting.
Pros of Push Manufacturing
- Lower Lead Times for Customers
- Since products are pre-manufactured and stocked, customers can receive their orders quickly.
- Ideal for businesses where speed is a competitive advantage (e.g., FMCG, retail).
- Economies of Scale
- Large production runs reduce per-unit costs due to bulk purchasing and efficient use of resources.
- Helps lower manufacturing costs and increase profit margins.
- Efficient Resource Utilization
- Enables manufacturers to plan production schedules, workforce allocation, and material procurement efficiently.
- Reduces downtime and improves factory productivity.
- Stable Supply Chain Operations
- Since production is planned ahead of time, suppliers and logistics partners can work with predictable schedules.
- Helps avoid frequent production disruptions.
- Better for Standardized Products
- Works well for industries with predictable demand and limited customization, such as consumer electronics, packaged foods, and household products.
Cons of Push Manufacturing
- High Risk of Overproduction
- Forecasting errors can lead to excess inventory, resulting in higher storage costs and potential product obsolescence.
- Particularly problematic for industries with short product life cycles (e.g., fashion, technology).
- Higher Inventory Holding Costs
- Requires significant warehouse space and resources to store unsold products.
- Adds costs related to inventory management, insurance, and potential depreciation.
- Less Flexibility to Market Changes
- If customer demand shifts, manufacturers may be left with excess or outdated stock.
- Harder to adapt to sudden market trends, customization requests, or supply chain disruptions.
- Potential Waste and Losses
- Unsold inventory may lead to waste, especially for perishable goods (e.g., food, pharmaceuticals).
- Companies may need to discount or discard excess stock, reducing profitability.
- Dependency on Accurate Forecasting
- Requires sophisticated demand forecasting models to predict market trends accurately.
- Forecasting errors can lead to stock shortages (underproduction) or excess stock (overproduction).
Is Push Manufacturing Right for Your Business?
- Best for businesses with stable and predictable demand (e.g., FMCG, pharmaceuticals, automotive, consumer electronics).
- Risky for industries with rapidly changing trends or high customization needs (e.g., fashion, high-tech gadgets).
Many companies combine push and pull strategies to balance efficiency and flexibility, using a hybrid push-pull system to optimize production and inventory management.
Pros and Cons of Pull Manufacturing
Pull manufacturing follows a make-to-order (MTO) or just-in-time (JIT) approach, where production is triggered by actual customer demand rather than forecasts. While it offers advantages like reduced waste and inventory costs, it also comes with challenges related to supply chain responsiveness and lead times.
Pros of Pull Manufacturing
- Minimized Inventory Costs
- Since products are made only when there is demand, companies avoid excessive inventory storage costs.
- Reduces risks of stock obsolescence and depreciation.
- Less Waste and Overproduction
- Avoids producing excess goods that might not sell, leading to more efficient resource usage.
- Aligns with lean manufacturing principles to reduce waste in production.
- Greater Flexibility to Market Changes
- Businesses can quickly adjust production to match demand fluctuations.
- Ideal for industries where customization or frequent product updates are common (e.g., fashion, high-tech, automotive).
- Improved Product Quality
- Since products are manufactured in response to specific customer needs, there is a greater focus on quality control.
- Helps prevent defects and reduces the need for rework or unsold defective products.
- Better Cash Flow Management
- Companies do not need to invest heavily in raw materials and inventory upfront.
- Revenue is more directly tied to sales, improving financial efficiency.
Cons of Pull Manufacturing
- Longer Lead Times for Customers
- Since production starts after an order is placed, customers may have to wait longer to receive their products.
- Not ideal for businesses where quick delivery is a priority (e.g., retail, FMCG).
- Supply Chain Vulnerability
- Pull systems rely heavily on suppliers delivering raw materials on time.
- Any delays in the supply chain can disrupt production and impact customer satisfaction.
- Higher Production Costs for Small Batches
- Economies of scale are harder to achieve because production occurs in smaller, on-demand batches.
- May lead to higher per-unit costs compared to push manufacturing, especially if demand fluctuates unpredictably.
- Requires Advanced Coordination and Technology
- Pull systems require strong coordination between suppliers, production teams, and logistics.
- Many businesses must invest in real-time data tracking, AI-driven demand forecasting, and automation to make pull manufacturing efficient.
- Risk of Stockouts During Demand Surges
- If demand suddenly spikes, production may struggle to keep up, leading to delays or missed sales opportunities.
- Businesses need a small safety stock to balance efficiency with demand fluctuations.
Is Pull Manufacturing Right for Your Business?
- Best for businesses with unpredictable demand, high customization needs, or short product life cycles (e.g., luxury goods, high-tech, automotive).
- Risky for industries where quick delivery is essential or raw material supply chains are unreliable (e.g., fast-moving consumer goods).
Many companies use a hybrid push-pull system to combine efficiency with responsiveness, optimizing production and inventory management.
Benefits of Using a Hybrid Push-Pull Manufacturing System
A hybrid push-pull manufacturing system combines the strengths of both push and pull strategies, optimizing production, inventory, and supply chain efficiency.
By leveraging push for predictable demand and pull for customized or uncertain demand, businesses can balance efficiency, cost savings, and responsiveness. This approach is particularly useful in industries with fluctuating demand, complex product lines, or long lead times.
1. Enhanced Flexibility in Production
- A hybrid system allows businesses to adjust production strategies based on product types and demand patterns.
- Push manufacturing can be used for high-demand, low-variability products, while pull manufacturing is ideal for customized or unpredictable items.
- This flexibility ensures better responsiveness to market shifts and customer needs, improving overall agility.
2. Improved Inventory Management
- Push manufacturing ensures a steady supply of high-demand products, reducing the risk of stockouts.
- Pull manufacturing minimizes excess inventory for low-demand or customized items, reducing storage costs and preventing waste.
- The hybrid approach allows for a balanced inventory, optimizing stock levels while maintaining availability.
3. Better Supply Chain Efficiency
- The system enables efficient use of resources by aligning production with demand.
- Bulk production (push) lowers per-unit costs for standardized products, while on-demand production (pull) reduces waste for customized items.
- A responsive supply chain ensures smoother material flow, reducing bottlenecks and lead times.
4. Cost Savings
- By blending economies of scale (push) with on-demand efficiency (pull), businesses can optimize costs.
- Push systems lower production costs through mass production.
- Pull systems reduce overproduction and unnecessary storage expenses.
- The hybrid model strikes a cost-effective balance, reducing financial risks from excessive stock or last-minute production.
5. Increased Customer Satisfaction
- Customers benefit from faster fulfillment of standard products (push) and customization options for specific needs (pull).
- Shorter lead times for made-to-order items and readily available stock for high-demand products improve customer experience.
- A flexible production approach ensures businesses can quickly respond to customer preferences.
6. Risk Mitigation
- The hybrid model diversifies risks, reducing the downsides of each individual system.
- Push systems ensure supply readiness for stable-demand items.
- Pull systems prevent excessive stock buildup for unpredictable items.
- This reduces financial losses from overproduction or lost sales due to stockouts.
7. Scalability and Responsiveness
- The hybrid approach scales efficiently, adjusting the push-pull balance based on:
- Seasonal demand fluctuations
- Market trends
- New product introductions
- Businesses can quickly adapt to unexpected demand shifts or supply chain disruptions.
A hybrid push-pull manufacturing system enables businesses to maximize efficiency, reduce costs, and improve customer satisfaction while remaining agile in a changing market.
By integrating predictive production (push) with demand-driven responsiveness (pull), companies can achieve a resilient, cost-effective, and customer-centric manufacturing strategy.
Factors to Consider When Choosing Between Push and Pull Manufacturing
Selecting between push and pull manufacturing depends on various factors, including demand predictability, production costs, inventory management, and customer expectations.
Below are key considerations to help businesses decide the best approach:
1. Demand Predictability
- Push Manufacturing: Suitable for businesses with stable and predictable demand, as production is based on forecasts.
- Pull Manufacturing: Ideal for industries with uncertain or fluctuating demand, where production is triggered by actual orders.
Key Question: Can your business accurately predict future demand?
2. Inventory Management
- Push Manufacturing: Requires high inventory levels, leading to increased storage costs but ensuring product availability.
- Pull Manufacturing: Operates with minimal inventory, reducing holding costs but risking stockouts if demand surges.
Key Question: Do you have the capacity and capital to store large inventories?
3. Lead Time Requirements
- Push Manufacturing: Ensures products are ready for immediate delivery, reducing customer wait times.
- Pull Manufacturing: Requires longer lead times, as production starts only after an order is placed.
Key Question: How quickly do your customers expect to receive products?
4. Production Costs
- Push Manufacturing: Benefits from economies of scale, as mass production reduces per-unit costs.
- Pull Manufacturing: Minimizes waste but may result in higher production costs per unit due to smaller batch sizes.
Key Question: Does your business benefit more from large-scale production or just-in-time efficiency?
5. Product Customization
- Push Manufacturing: Best for standardized products, where consistency and volume are more important than customization.
- Pull Manufacturing: Allows for high customization, making it ideal for industries like fashion, automotive, and electronics.
Key Question: Does your product require high levels of customization?
6. Risk Management
- Push Manufacturing: Carries the risk of overproduction, obsolete stock, and market shifts leading to financial losses.
- Pull Manufacturing: Reduces inventory risk but can face delays and supply chain disruptions if demand spikes unexpectedly.
Key Question: Which is riskier for your business—excess inventory or delayed order fulfillment?
7. Supply Chain Stability
- Push Manufacturing: Works well when suppliers are reliable and can handle large orders efficiently.
- Pull Manufacturing: Requires a flexible and responsive supply chain to produce goods on demand.
Key Question: Can your suppliers support a just-in-time production model?
8. Industry and Market Conditions
- Push Manufacturing: Common in industries like FMCG, pharmaceuticals, and automobiles, where demand is steady.
- Pull Manufacturing: Suited for highly competitive markets where customer preferences change rapidly (e.g., fashion, tech gadgets).
Key Question: Does your industry favor stable production or demand-driven flexibility?
Choosing between push and pull manufacturing depends on your business model, customer expectations, production capabilities, and risk tolerance. Many companies adopt a hybrid push-pull system, combining the efficiency of push with the flexibility of pull to optimize operations.
How Deskera ERP and MRP Support Both Push and Pull Manufacturing
Deskera ERP and MRP systems provide comprehensive tools to help manufacturers effectively manage push, pull, and hybrid manufacturing strategies. Whether your business relies on demand forecasts or real-time customer orders, Deskera offers automation, real-time tracking, and data-driven decision-making to optimize production efficiency.
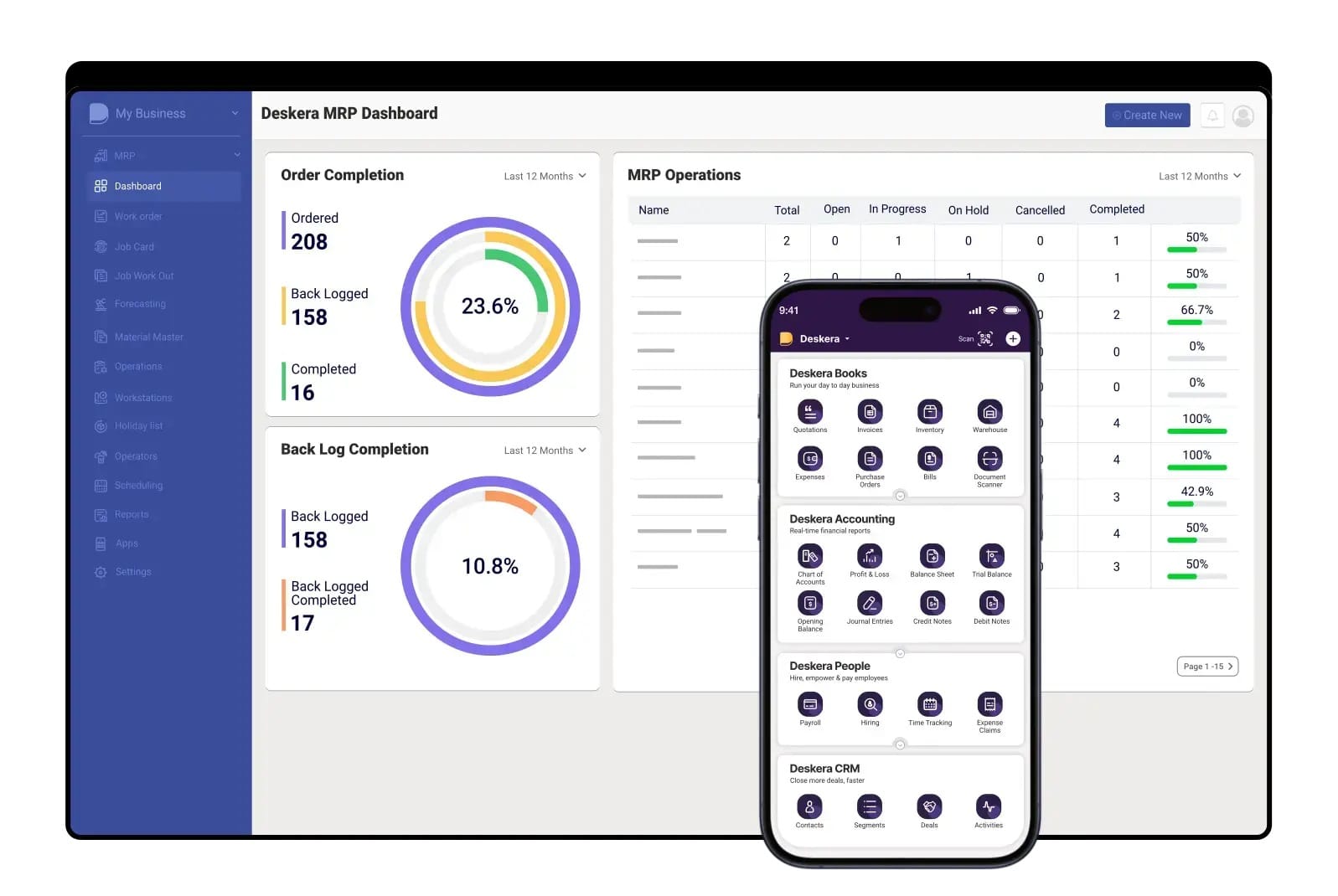
1. Streamlining Push Manufacturing with Deskera
- Demand Forecasting & Production Planning: Deskera MRP helps businesses plan production based on historical data and predictive analytics, ensuring the right amount of stock is available.
- Inventory Optimization: With real-time inventory tracking, businesses can manage stock levels efficiently, preventing overstocking or stockouts.
- Bulk Order Management: Deskera ERP enables batch production scheduling, helping manufacturers take advantage of economies of scale.
- Supplier & Procurement Automation: Automate purchase orders and material planning, ensuring raw materials are always available for large-scale production.
2. Enhancing Pull Manufacturing with Deskera
- Just-in-Time (JIT) Inventory Control: Deskera MRP minimizes inventory waste by ensuring materials are procured and used only when needed for production.
- Order-Driven Production: The system integrates real-time sales data, allowing businesses to initiate manufacturing only when customer orders are received.
- Agile Supply Chain Management: Deskera ERP enhances supplier coordination and lead time tracking, ensuring quick replenishment and reduced delays.
- Shop Floor Execution & Work Order Management: Monitor work orders, track progress, and adjust schedules based on demand fluctuations.
3. Supporting a Hybrid Push-Pull Approach
For businesses leveraging a hybrid push-pull model, Deskera provides:
- Production Scheduling & Resource Allocation: Balance bulk production (push) while maintaining the ability to produce on-demand (pull).
- Safety Stock & Buffer Management: Maintain optimal stock levels to ensure customer demand is met without overproduction.
- AI-Driven Insights: Use Deskera’s AI-powered analytics to adjust manufacturing strategies dynamically based on market conditions.
Why Choose Deskera for Push and Pull Manufacturing?
Deskera ERP and MRP help manufacturers achieve cost efficiency, waste reduction, and improved responsiveness to customer demand. Whether your business follows a push, pull, or hybrid model, Deskera provides the tools needed to maintain seamless operations and continuous growth.
Key Takeaways
- Push manufacturing is driven by demand forecasts, while pull manufacturing is based on actual customer demand. Each approach has its advantages depending on industry needs.
- Toyota’s Just-in-Time (JIT) system exemplifies pull manufacturing, reducing waste and improving efficiency by producing only what is needed, when it is needed.
- Ford’s mass production model demonstrates push manufacturing, where high-volume production anticipates market demand, ensuring product availability.
- Push manufacturing allows economies of scale and predictable production schedules but can lead to excess inventory and high storage costs.
- Pull manufacturing minimizes waste and storage costs but requires a highly responsive supply chain to avoid stockouts and production delays.
- Combining push and pull strategies helps manufacturers balance efficiency and responsiveness, reducing waste while ensuring timely product availability.
- Businesses must evaluate demand predictability, inventory costs, production lead times, and supply chain agility to determine the best manufacturing strategy.
- Deskera’s ERP and MRP systems enhance both push and pull manufacturing by optimizing production planning, inventory control, and supply chain efficiency through automation and real-time data insights.
Related Articles
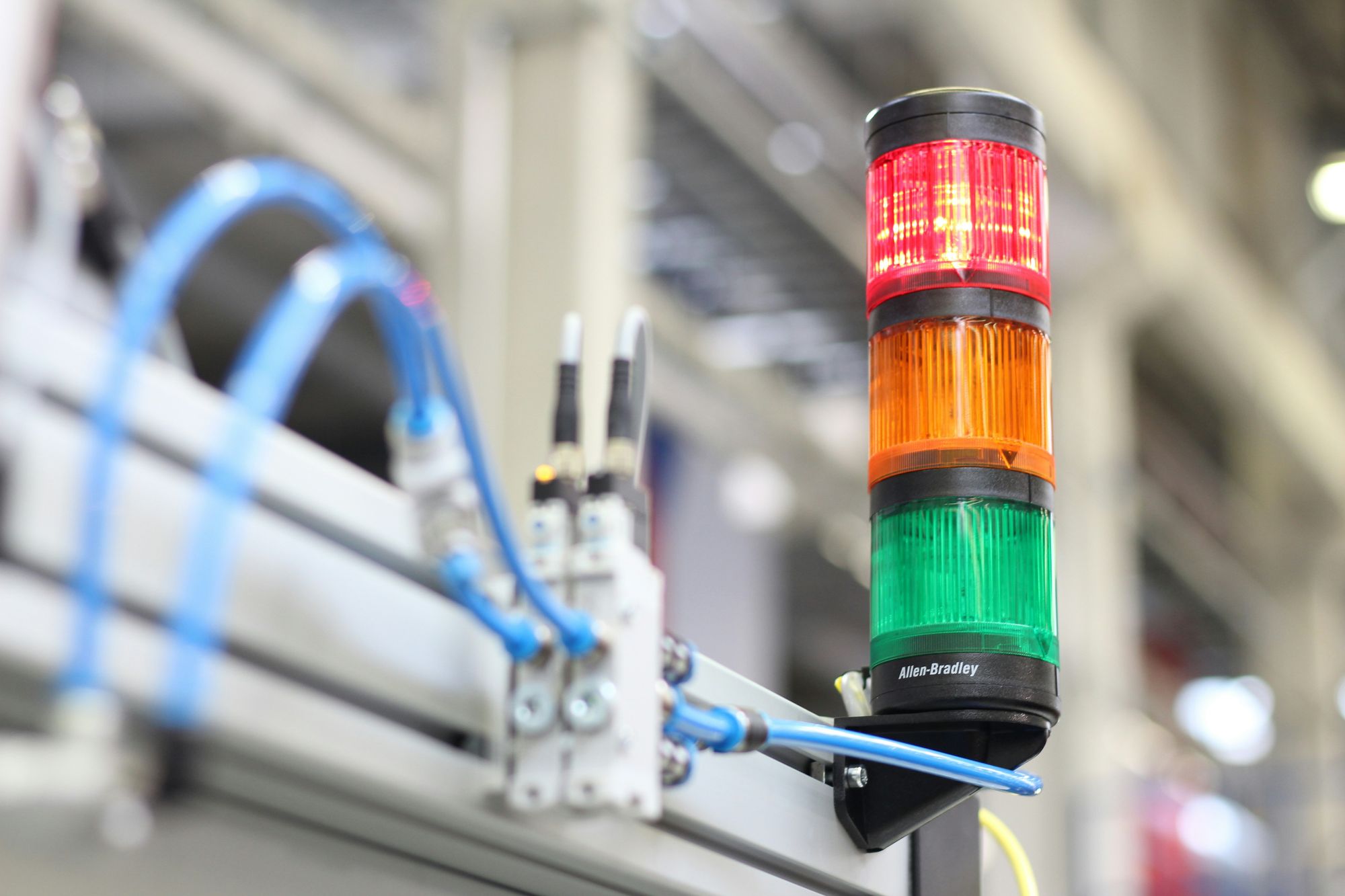
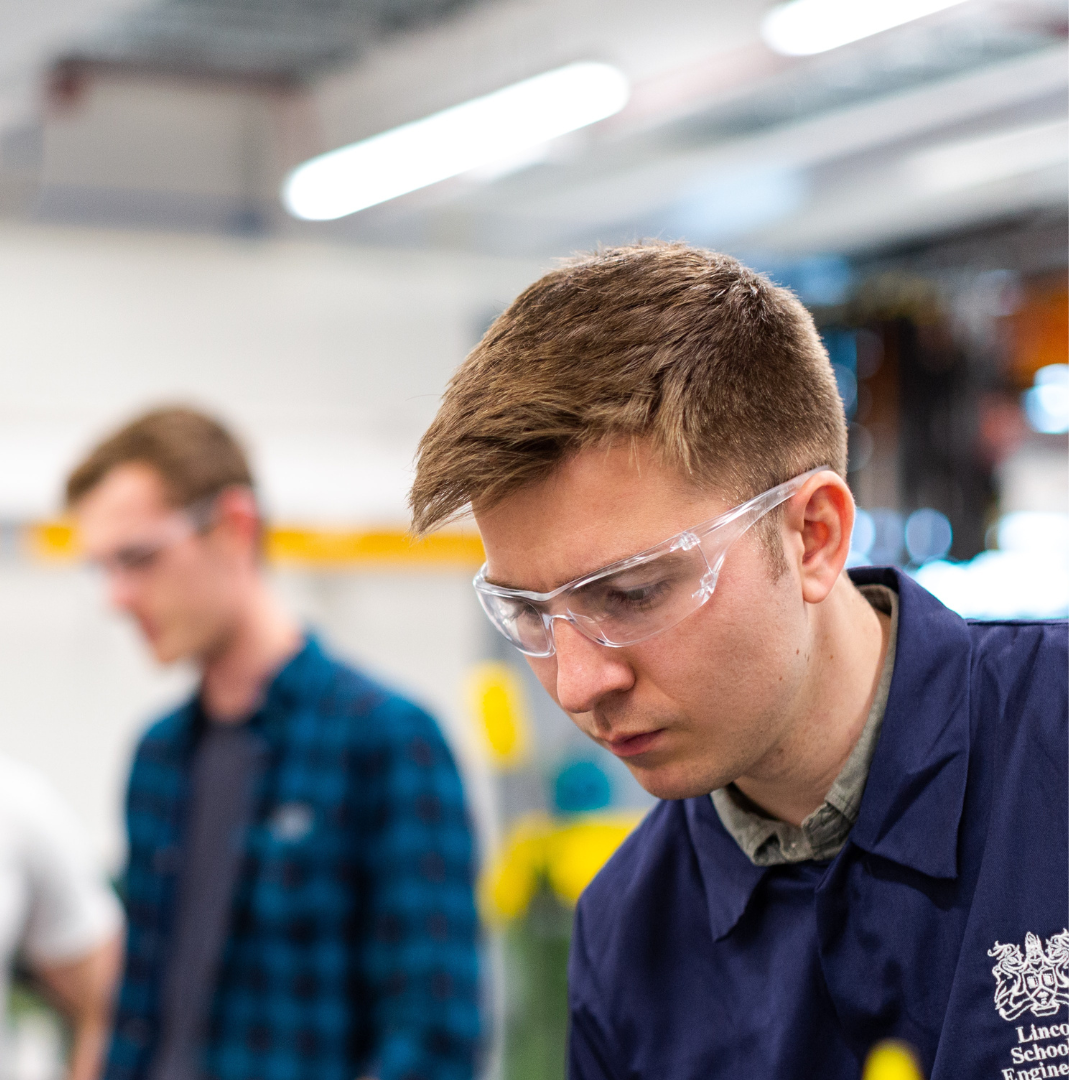
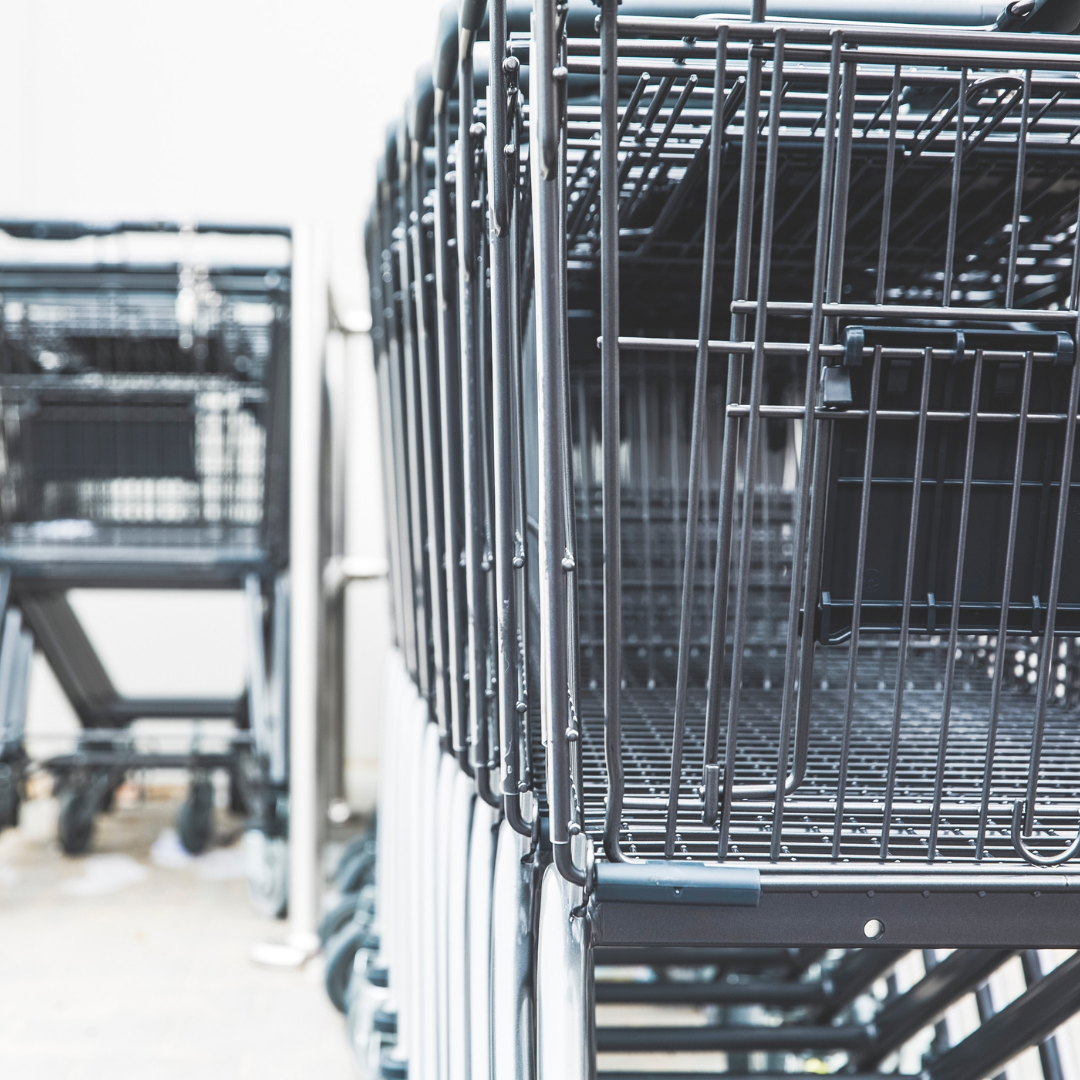
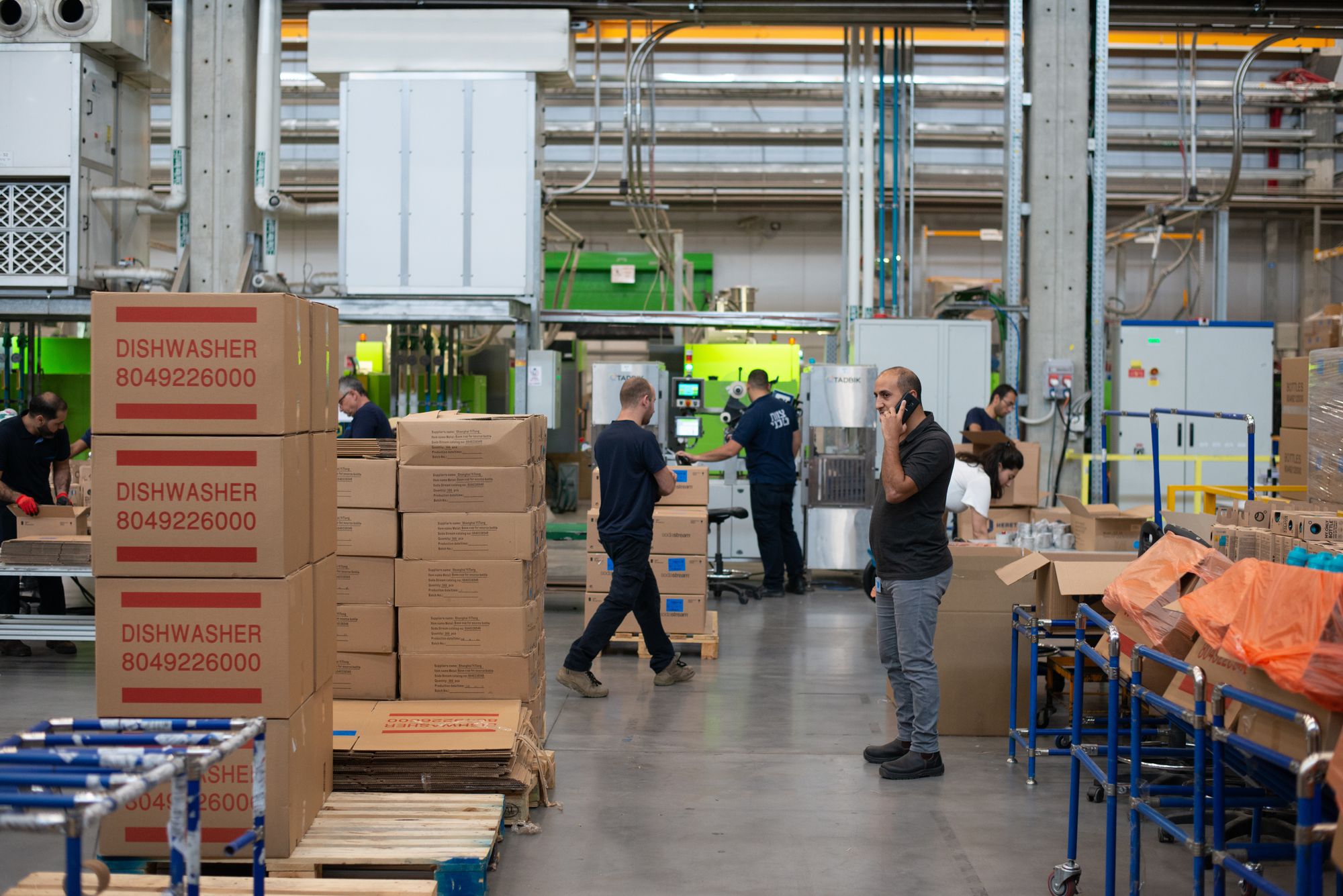
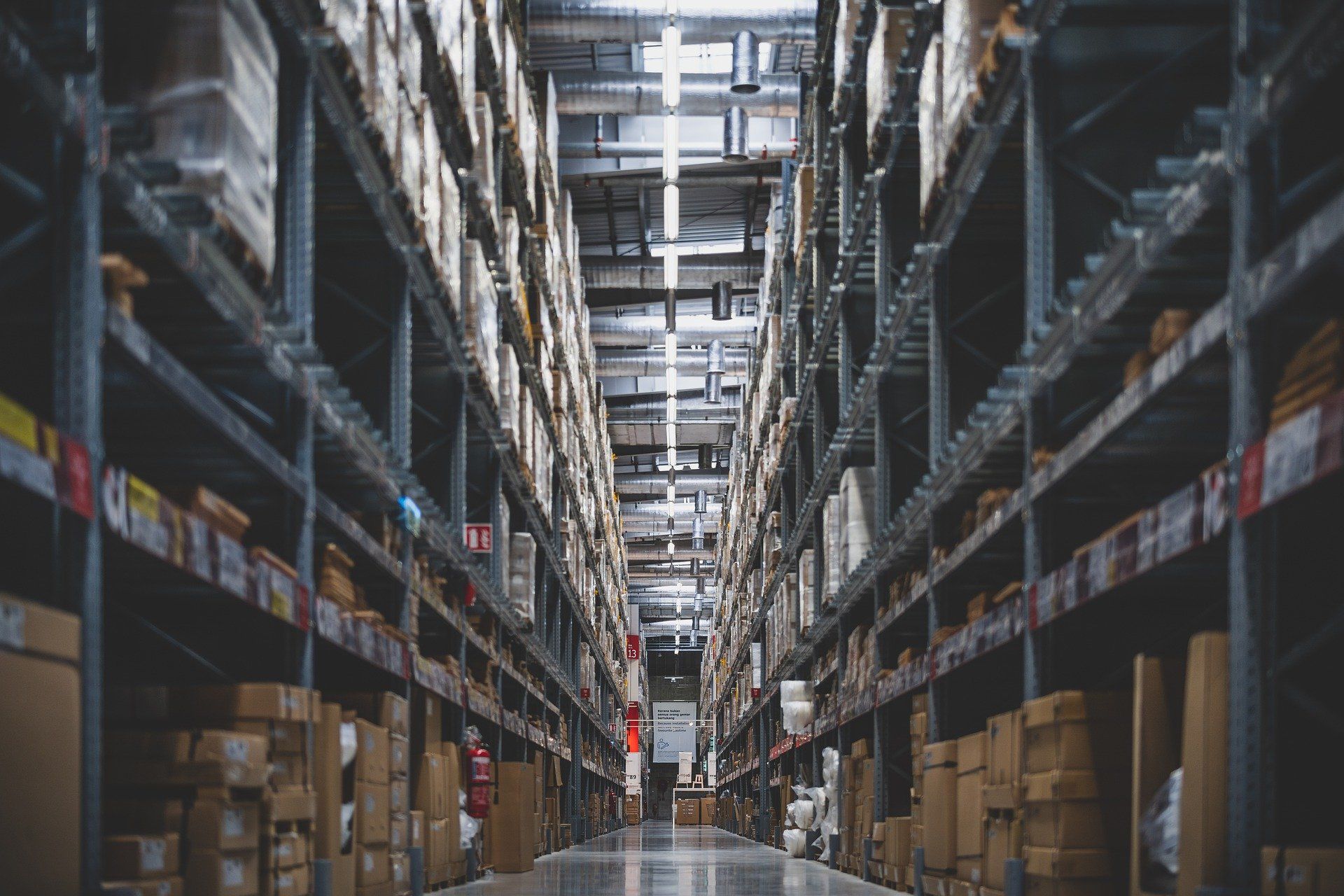
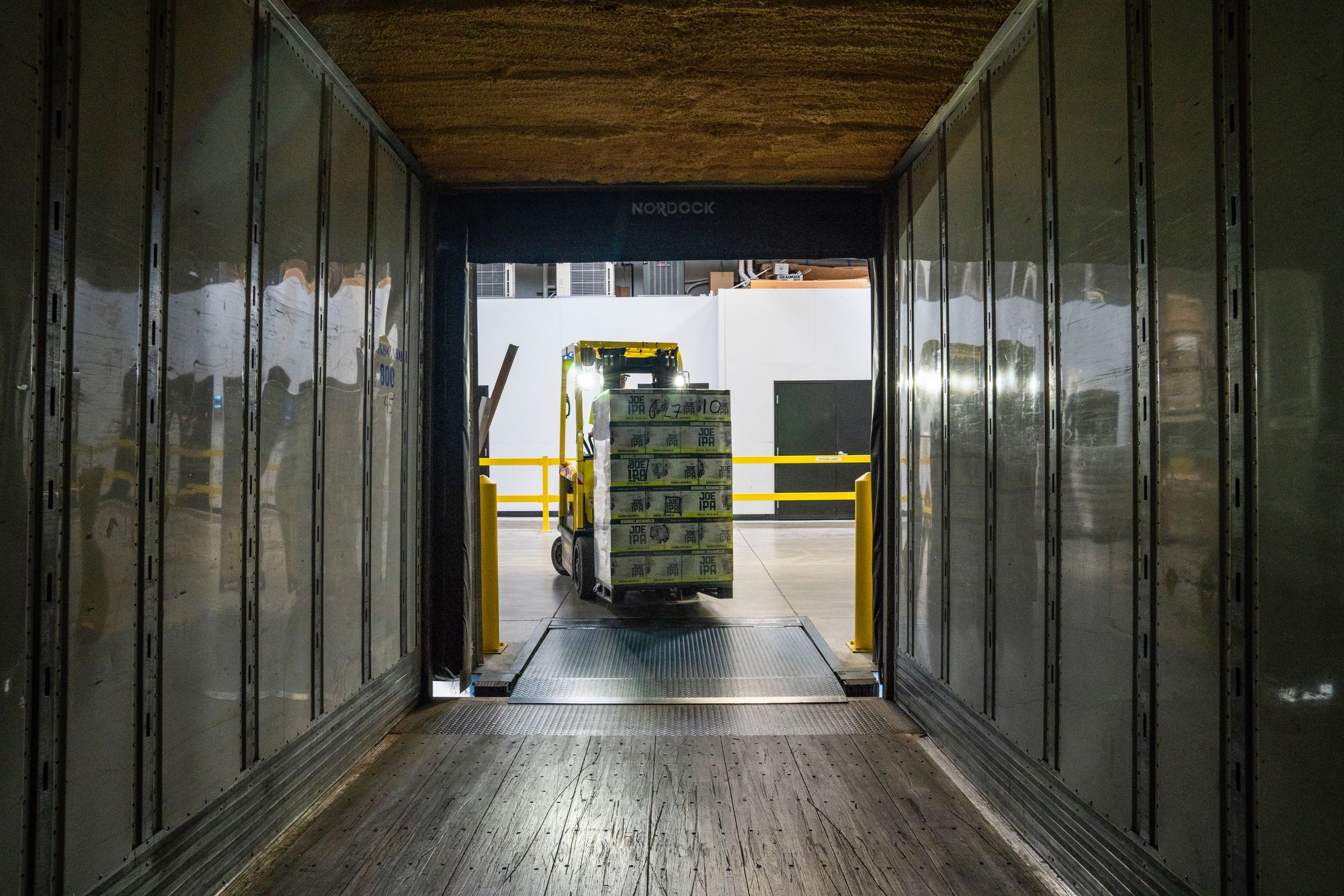