Predictive maintenance (PdM) is revolutionizing how businesses manage their assets and equipment. With industries increasingly shifting towards data-driven maintenance strategies, PdM is rapidly gaining traction as a key enabler of operational efficiency.
In fact, according to Grand View Research, the global predictive maintenance market is expected to skyrocket to $60.13 billion by 2030, underscoring the growing demand for smart, proactive maintenance solutions. This shift is driven by advancements in IoT, artificial intelligence, and machine learning, allowing businesses to predict equipment failures before they occur.
A 2024 global survey of 1,165 maintenance, repair, and operations (MRO) professionals from industries like manufacturing, retail, and hospitality highlights PdM’s increasing adoption.
The survey revealed that nearly one-third of companies actively use predictive maintenance, making it the third most popular maintenance strategy after preventive maintenance and the run-to-failure approach. This widespread adoption reflects the industry’s recognition of PdM’s ability to minimize downtime, reduce costs, and improve asset reliability.
Beyond its popularity, the financial and operational benefits of PdM are undeniable. According to the Deloitte Analytics Institute, predictive maintenance can lower maintenance costs by up to 25% while boosting uptime by 10–20%.
By leveraging real-time equipment monitoring and predictive analytics, businesses can shift from reactive to proactive maintenance, preventing costly breakdowns and optimizing resource allocation. This strategic shift not only enhances productivity but also extends the lifespan of critical assets.
For businesses looking to integrate predictive maintenance into their operations seamlessly, Deskera ERP provides a robust solution. With advanced analytics, real-time monitoring, and automated workflows, Deskera ERP helps organizations track equipment performance, predict failures, and optimize maintenance schedules.
By combining ERP capabilities with predictive maintenance, companies can enhance operational efficiency, reduce maintenance costs, and ensure business continuity.
What is Predictive Maintenance?
Predictive maintenance (PdM), also known as condition-based maintenance, is a proactive maintenance strategy that leverages real-time data and advanced analytics to predict equipment failures before they happen.
It involves continuously monitoring asset performance using Internet of Things (IoT) sensors, machine learning (ML) algorithms, and data analytics to detect operational anomalies. By identifying potential issues early, businesses can schedule maintenance only when necessary, reducing unplanned downtime and optimizing asset utilization.
At the core of predictive maintenance is condition monitoring, where machines are equipped with sensors that track vital parameters such as vibration, temperature, and pressure. These insights help businesses assess an asset’s health in real-time and forecast potential failures.
Predictive maintenance aims to minimize maintenance costs, extend asset lifecycles, and ensure equipment reliability while avoiding unnecessary preventive maintenance expenses. This strategic approach reduces overall maintenance efforts while keeping operations running smoothly.
A key advantage of PdM is its ability to optimize maintenance schedules. Instead of following fixed maintenance intervals, businesses can rely on historical performance data and AI-driven insights to determine exactly when maintenance is needed.
According to Deloitte Analytics Institute, predictive maintenance can lower maintenance costs by up to 25% and increase uptime by 10–20%. This makes it an invaluable tool for industries where unplanned failures lead to costly disruptions, such as manufacturing, logistics, and utilities.
With ERP solutions like Deskera, businesses can seamlessly integrate predictive maintenance into their operations. Deskera ERP enables organizations to track equipment performance in real time, automate maintenance workflows, and utilize predictive insights to prevent unexpected failures. By combining ERP capabilities with predictive maintenance, companies can improve asset efficiency, reduce costs, and ensure seamless business operations.
Predictive Maintenance vs. Preventive Maintenance
Both predictive maintenance (PdM) and preventive maintenance (PM) aim to increase equipment reliability and reduce downtime, but they follow different approaches.
1. Definition & Approach
- Predictive Maintenance (PdM): A data-driven, proactive approach that uses real-time monitoring, sensors, and analytics to predict equipment failures before they happen. Maintenance is only performed when needed.
- Preventive Maintenance (PM): A scheduled, proactive approach where maintenance tasks are carried out at fixed intervals based on time or usage, regardless of the asset’s actual condition.
2. Maintenance Scheduling
- PdM: Maintenance is performed only when necessary, based on real-time data and predictive analytics.
- PM: Maintenance is performed at predetermined intervals, whether or not the equipment actually needs it.
3. Data Utilization
- PdM: Uses IoT-enabled sensors and technologies like vibration analysis, temperature monitoring, and machine learning to assess equipment health.
- PM: Relies on historical performance and manufacturer recommendations without real-time monitoring.
4. Cost Efficiency
- PdM: Higher upfront investment in sensors, software, and training but cost-effective in the long run by reducing unnecessary maintenance and downtime.
- PM: Lower initial investment, but maintenance is performed regardless of need, leading to higher long-term costs due to unnecessary repairs and downtime.
5. Downtime Considerations
- PdM: Maintenance occurs without unexpected downtime because faults are detected before they escalate.
- PM: Can cause planned downtime since maintenance occurs at set intervals, even if no issues exist.
6. Suitability for Industries
- PdM: Ideal for industries where equipment failure has high safety, operational, or financial risks, such as aviation, energy, and manufacturing.
- PM: More suitable for smaller operations or less critical assets where precise failure prediction isn't essential, such as office HVAC systems or fleet vehicles.
Choosing the Right Maintenance Strategy
The choice between predictive and preventive maintenance depends on factors like:
- Asset criticality – Does failure lead to significant costs or safety risks?
- Operational impact – Can downtime be planned, or must it be avoided entirely?
- Budget & technology readiness – Can the business invest in IoT sensors and analytics?
While preventive maintenance is simpler to implement, predictive maintenance optimizes costs and asset lifespan by avoiding unnecessary repairs and reducing equipment downtime.
Companies looking for long-term efficiency and reliability often combine both strategies—using predictive maintenance for critical assets and preventive maintenance for lower-risk equipment.
How Predictive Maintenance Works
Predictive maintenance is a proactive approach that uses sensor technology, artificial intelligence (AI), and machine learning (ML) to detect early signs of equipment failure.
It helps businesses reduce downtime, lower maintenance costs, and improve asset reliability. The process involves multiple stages, each playing a crucial role in predicting and preventing breakdowns.
1. Equipment Selection and Sensor Installation
Not all assets require predictive maintenance. Companies prioritize high-value equipment or machinery prone to frequent failures. Sensors are installed on critical components to continuously monitor operational parameters such as:
- Vibration (detects misalignment or bearing wear)
- Temperature (identifies overheating risks)
- Pressure (monitors fluid or gas flow)
- Acoustic signals (detects abnormal noise patterns)
Proper sensor placement and calibration are essential to ensure accurate data collection.
2. Data Collection and Transmission
Once installed, the sensors gather real-time data on equipment performance. The data is then transmitted to a centralized system via:
- IoT networks for seamless real-time connectivity
- Cloud-based enterprise asset management (EAM) or CMMS systems for storage and accessibility
This enables businesses to monitor asset health remotely and detect anomalies early.
3. Data Processing and Analysis
Raw sensor data is cleaned and processed to remove anomalies. Advanced analytics and ML models analyze this data to identify patterns and predict failures. Key processes include:
- Data cleansing to eliminate noise and errors
- Statistical modeling to compare historical and real-time data
- AI-driven pattern recognition to detect subtle deviations in equipment behavior
These insights enable maintenance teams to identify potential problems before they escalate.
4. Predictive Modeling
Using AI and ML, predictive models are trained to forecast equipment failures based on historical trends and real-time sensor data. These models continuously learn and refine their accuracy over time, helping businesses:
- Anticipate component wear and failure
- Optimize maintenance schedules
- Reduce unnecessary inspections and repairs
For instance, vibration sensors on a conveyor belt can predict bearing failures before they cause production halts.
5. Alert Generation and Maintenance Planning
When predictive models detect potential failures, they generate alerts for maintenance teams. These alerts help organizations:
- Schedule just-in-time maintenance to prevent unexpected downtime
- Allocate resources efficiently, reducing unnecessary repairs
- Prioritize maintenance based on asset criticality
For example, in aviation, sensors on aircraft engines detect unusual vibrations and trigger maintenance scheduling before a serious issue occurs.
6. Maintenance Execution
Technicians act on predictive alerts by performing necessary repairs or adjustments. This step involves:
- Assigning skilled personnel based on the nature of the issue
- Ensuring the availability of spare parts and tools
- Conducting repairs during scheduled downtimes to minimize disruptions
A well-executed predictive maintenance strategy ensures businesses prevent costly breakdowns.
7. Performance Analysis and Model Refinement
To improve accuracy, businesses continuously evaluate predictive models based on real-world maintenance outcomes. This involves:
- Comparing predicted failures with actual equipment performance
- Fine-tuning AI and ML models for better accuracy
- Adjusting sensor thresholds to reduce false alarms
For example, if a predictive model is generating too many alerts for minor issues, its sensitivity can be adjusted to focus only on critical failures.
Key Technologies in Predictive Maintenance
Predictive maintenance relies on an ecosystem of interconnected technologies, including:
- IoT Sensors – Capture real-time data on equipment performance
- Industrial IoT (IIoT) Networks – Transmit sensor data securely
- Predictive Analytics & Machine Learning (ML) – Identify trends and failure patterns
- Artificial Intelligence (AI) – Enhance data-driven decision-making
- ERP Software – Integrates maintenance insights with supply chain, inventory, and workforce planning
- CMMS & EAM Systems – Manage maintenance tasks and optimize asset management
Predictive maintenance not only minimizes downtime and reduces costs but also enhances operational efficiency by ensuring businesses stay ahead of equipment failures.
By leveraging ERP software, companies can seamlessly integrate predictive maintenance insights with overall business processes, making maintenance more strategic and cost-effective.
When Should You Use Predictive Maintenance?
With multiple maintenance strategies available, it’s important to know when predictive maintenance makes the most sense. Before implementing a predictive maintenance program, businesses must ensure they have:
- Sufficient data to train and refine predictive models.
- Technological capability to leverage IoT sensors, AI, ML, and data analytics.
- Expertise to implement and manage predictive maintenance systems effectively.
- Operational flexibility to adjust or pause equipment usage for maintenance.
If these conditions are met, predictive maintenance is ideal in the following scenarios:
1. Protecting Critical Equipment
Predictive maintenance is most beneficial for assets that are mission-critical to operations, such as turbine generators in power plants or manufacturing robots in automotive production. By detecting early signs of failure, businesses can prevent costly breakdowns and ensure smooth operations.
2. Identifying Failure Patterns
Industries that require constant monitoring of failure patterns—such as aviation and heavy machinery—can benefit significantly. For example, airlines use predictive maintenance to analyze engine performance data, identifying wear patterns and replacing parts before failures disrupt operations.
3. Reducing the Cost of Downtime
Companies with continuous manufacturing or high-demand production schedules rely on predictive maintenance to prevent disruptions. In power generation plants, for example, vibration analysis detects turbine anomalies early, preventing costly unplanned shutdowns.
4. Lowering Maintenance Costs
Predictive maintenance helps businesses focus resources on assets that truly need attention rather than performing unnecessary routine maintenance. For example, fleet management companies analyze vehicle performance data to determine optimal maintenance intervals, reducing both costs and downtime.
5. Ensuring Regulatory and Safety Compliance
Industries such as transportation, energy, and healthcare have strict compliance and safety requirements. Predictive maintenance helps address potential equipment issues before they pose safety risks or result in regulatory violations.
For instance, oil analysis in transportation can detect engine contaminants that may lead to emissions noncompliance, helping companies avoid penalties.
By implementing predictive maintenance in these scenarios, businesses can improve asset reliability, reduce costs, and enhance operational efficiency while maintaining regulatory compliance.
Technologies and Methods of Predictive Maintenance
Predictive maintenance employs various advanced technologies and methodologies to monitor equipment health, detect early signs of failure, and optimize maintenance schedules. Each method offers unique benefits suited for different types of machinery and operating conditions.
1. Vibration Analysis
Vibration analysis is a cornerstone of predictive maintenance, used primarily for high-speed rotating equipment such as turbines and motors. It detects misalignments, unbalanced components, or worn bearings by analyzing vibration patterns. Specialized sensors and analytics software help identify abnormal vibrations early, allowing for scheduled maintenance without disrupting production.
2. Motor Circuit Analysis
This technique evaluates the condition of electric motors by analyzing their electrical signatures. It helps detect insulation wear, power quality issues, and rotor imbalances. By identifying potential motor failures early, it prevents costly downtime and repairs.
3. Oil Analysis
Oil analysis is crucial for machinery that relies on lubrication, such as turbines, compressors, and hydraulic systems. It detects contaminants, viscosity changes, and chemical imbalances that indicate wear or overheating. Regular oil sampling and laboratory analysis ensure optimal performance and prevent failures.
4. Thermography (Infrared Analysis)
Also known as thermal imaging, thermography uses infrared cameras to detect heat variations in machinery. Hotspots in electrical systems, mechanical components, or insulation indicate defects like friction, blockages, or faulty circuits. This non-intrusive method allows maintenance teams to detect and address issues before they lead to failures.
5. Acoustic Monitoring
Acoustic monitoring identifies unusual noises—such as grinding, hissing, or banging—that may indicate bearing wear, misalignment, or lubrication issues. It is often performed in real-time using specialized sensors and microphones, which analyze sound patterns to distinguish between normal and abnormal operations.
6. Ultrasonic Analysis
A more advanced form of acoustic monitoring, ultrasonic analysis uses high-frequency sound waves to detect mechanical and electrical issues. It is particularly useful for identifying leaks in pressurized systems, monitoring bearing wear, and diagnosing gear misalignment. This precise and non-intrusive technique enhances reliability and efficiency.
7. Emissions Testing
Machinery that involves combustion, such as boilers and engines, undergoes emissions testing to measure pollutants like carbon dioxide, nitrogen oxides, and sulfur oxides. This method ensures compliance with environmental regulations, improves fuel efficiency, and helps detect faults in combustion systems.
8. Infrared Analysis
While similar to thermography, infrared analysis includes both emitted and reflected infrared energy to assess a system’s condition. It provides deeper insights into electrical and mechanical systems, enabling more accurate predictions of potential failures.
By integrating these predictive maintenance technologies, organizations can enhance equipment reliability, reduce downtime, and optimize maintenance costs. Each method plays a crucial role in a proactive maintenance strategy, ensuring operational efficiency and longevity of machinery.
Benefits of Predictive Maintenance
Predictive maintenance (PdM) offers significant advantages by proactively identifying potential equipment failures and optimizing maintenance schedules. This results in cost savings, increased efficiency, and improved operational reliability. Here are the key benefits:
1. Reduced Maintenance Costs
Predictive maintenance minimizes unnecessary repairs and reduces maintenance-related expenses. By identifying potential failures early, organizations can avoid costly emergency repairs, reduce labor costs, and optimize spare parts usage.
2. Fewer Machine Failures
Continuous monitoring and predictive analytics help detect early warning signs of equipment degradation. Over time, this leads to fewer unexpected failures, ensuring smoother operations and increased reliability.
3. Reduced Downtime
Predictive maintenance helps schedule repairs before failures occur, minimizing unplanned downtime. With early detection, faulty components can be replaced in a timely manner, keeping operations running efficiently.
4. Optimized Spare Parts Management
Instead of stockpiling spare parts in anticipation of breakdowns, predictive maintenance enables organizations to maintain just-in-time inventory, reducing capital investment in unused parts and preventing material waste.
5. Increased Equipment Lifespan
Addressing minor issues before they escalate helps extend the operational life of machinery. Condition-based monitoring prevents excessive wear and tear, ensuring long-term asset performance.
6. Estimation of Mean Time Between Failures (MTBF)
Predictive maintenance allows businesses to calculate MTBF, helping determine the optimal replacement time for equipment. This prevents excessive repair costs and ensures a better return on investment.
7. Increased Production Efficiency
With fewer machine failures and reduced downtime, businesses can maintain consistent production levels. Condition-based maintenance ensures that manufacturing and industrial processes operate at peak efficiency.
8. Enhanced Workplace Safety
By detecting potential hazards, such as overheating or mechanical failures, predictive maintenance prevents dangerous accidents. Organizations implementing PdM programs often see reduced workplace injuries and improved compliance with safety regulations.
9. Improved Repair Verification
PdM helps verify the success of maintenance actions. By using techniques such as vibration analysis, maintenance teams can assess whether a repair has fully resolved an issue or if further intervention is needed.
10. Increased Profitability
By improving asset performance, reducing downtime, and minimizing maintenance costs, predictive maintenance directly contributes to higher revenue and profitability. The cost savings from proactive maintenance outweigh the investment in monitoring technologies.
11. Strategic Asset Management
Predictive analytics allow businesses to forecast equipment failures, optimize maintenance schedules, and allocate resources efficiently. This leads to a more structured and proactive maintenance strategy.
12. Environmental Benefits
Predictive maintenance helps organizations reduce energy consumption by ensuring that equipment operates efficiently. Additionally, lower material waste and fewer emergency repairs contribute to sustainability efforts.
By integrating predictive maintenance into their operations, organizations can enhance efficiency, maximize asset lifespan, and achieve significant cost savings while ensuring long-term operational success.
Drawbacks of Predictive Maintenance (PdM)
While predictive maintenance (PdM) offers substantial benefits, including reduced downtime and cost savings, its implementation comes with significant challenges. Below are the key drawbacks of predictive maintenance in greater detail:
1. High Initial Costs and Investment
- Implementing PdM requires substantial financial investment in sensors, IoT infrastructure, cloud storage, and predictive analytics software.
- Many companies also need to upgrade or replace outdated machinery to integrate with predictive systems.
- Costs associated with purchasing and configuring a Computerized Maintenance Management System (CMMS) or Enterprise Asset Management (EAM) software can be high.
- Smaller businesses may find the upfront costs prohibitive, making it difficult to justify the return on investment (ROI) in the short term.
2. Workforce Training and Skill Gaps
- Employees must be trained in using new PdM tools, interpreting analytics, and understanding machine learning-based insights.
- Maintenance teams traditionally trained for preventive or reactive maintenance may struggle to adapt to a data-driven approach.
- Companies may need to hire specialists such as data scientists, IoT engineers, and reliability analysts, which adds to operational expenses.
- The learning curve for PdM software can be steep, requiring long-term training investments.
3. Complexity of Implementation and System Integration
- PdM requires integrating different technologies such as IoT sensors, cloud computing, machine learning algorithms, and AI-driven analytics.
- Compatibility issues can arise when integrating predictive systems with legacy equipment or outdated IT infrastructure.
- Initial setup and calibration of sensors, as well as fine-tuning of predictive models, can take months or even years before full operational efficiency is achieved.
- System failures or inaccurate predictions due to incorrect integration can lead to mistrust among maintenance teams.
4. High Data Dependency and Quality Issues
- Predictive models rely on extensive historical and real-time data to generate accurate failure predictions.
- Poor sensor placement, faulty sensors, or insufficient data sensitivity can result in misleading insights.
- Data silos, where different departments store data separately, can limit predictive accuracy and hinder maintenance efficiency.
- If an asset lacks sufficient failure history, predictive models may be unreliable, leading to either over-maintenance or unexpected breakdowns.
5. Over-Reliance on Predictive Models and Technology
- Predictive maintenance systems are not foolproof—algorithms may fail to detect failures due to unexpected external factors (e.g., environmental conditions, operator errors).
- A strong dependency on automated systems can cause maintenance teams to overlook manual inspections and operator intuition.
- False positives can lead to unnecessary maintenance, increasing downtime and costs, while false negatives may cause unexpected equipment failures.
- Sensor drift (gradual inaccuracy of sensors over time) can lead to incorrect data interpretation if not regularly recalibrated.
6. Difficulty in Assessing Criticality and Cost-Benefit Analysis
- Not all assets are suitable for PdM. For example, low-cost machinery with inexpensive and easily replaceable parts may be better maintained using traditional methods.
- Determining which assets justify the high cost of predictive maintenance requires thorough failure mode and effects analysis (FMEA), which itself demands time and resources.
- Without proper assessment, companies risk investing in PdM for assets that do not provide significant ROI.
7. Regulatory, Compliance, and Legal Challenges
- Many industries, such as aerospace, pharmaceuticals, and food manufacturing, have strict regulatory requirements that mandate scheduled preventive maintenance.
- Regulatory bodies may not fully accept AI-driven maintenance schedules, requiring organizations to follow traditional approaches.
- Compliance with data protection regulations (e.g., GDPR, HIPAA) can be a challenge, especially when using cloud-based predictive analytics systems.
8. Maintenance of Predictive Systems Themselves
- PdM tools require continuous updates, recalibration, and maintenance to ensure data accuracy.
- Predictive models must be refined regularly as new failure patterns emerge, requiring additional data analysis efforts.
- AI-driven systems may need periodic retraining with fresh data to maintain their accuracy, adding to operational costs.
- Software glitches, hardware malfunctions, and network issues can disrupt PdM effectiveness, leading to unexpected breakdowns.
9. False Alarms and Alert Fatigue
- PdM systems can sometimes generate excessive alerts, many of which may be false positives, leading to unnecessary interventions.
- Frequent false alarms may result in "alert fatigue," where maintenance teams begin to ignore or delay responses to alerts, increasing failure risks.
- Tuning alert thresholds to the right level without missing actual failures is a continuous challenge.
10. Operational Disruptions During Implementation
- Installing and configuring PdM sensors often requires temporarily shutting down machinery, which can disrupt production.
- Equipment modifications to support predictive analytics may interfere with ongoing processes.
- Employees may resist PdM adoption due to fear of job displacement or unfamiliarity with data-driven decision-making.
11. Challenges with New Equipment Integration
- As organizations expand or upgrade machinery, integrating new assets into the existing predictive maintenance framework can be complex.
- Each new asset may require customized sensors, unique data collection models, and individual calibration, which adds complexity and cost.
- Ensuring uniformity in data collection across different equipment types can be a significant challenge.
12. Long Payback Period
- The return on investment (ROI) for PdM is not immediate—it can take years before businesses realize significant cost savings.
- In some industries, downtime reduction alone may not justify the high implementation costs.
- Companies that expect quick financial gains from PdM may be disappointed if they do not achieve immediate efficiency improvements.
Predictive maintenance presents a transformative approach to asset management, but its challenges must not be overlooked. High initial investment, workforce training, data dependency, and technological complexities make it difficult for every organization to implement effectively.
Future Trends of Predictive Maintenance
Predictive maintenance (PdM) has evolved significantly, driven by technological advancements and the increasing need for real-time asset monitoring. Initially, condition-based maintenance emerged as an improvement over traditional reactive and preventive approaches. However, the lack of integration between business systems hindered the widespread adoption of PdM.
Today, IoT sensors, AI, and big data technologies are transforming PdM, making it more accurate and accessible. The pandemic accelerated digital transformation, pushing companies to integrate predictive maintenance into their operations. Additionally, the rising costs of unplanned downtime—estimated to be around 11% of turnover for Fortune Global 500 companies—is fueling its adoption.
Here are some key technological advancements shaping the future of predictive maintenance:
1. Automated Robotic Inspection
Industries such as oil and gas, utilities, and manufacturing are deploying autonomous robotic systems to monitor equipment in remote or hazardous locations.
- AI-powered robots act as mobile sensors, collecting and transmitting data to computerized maintenance management systems (CMMS).
- These robotic inspections improve efficiency and reduce maintenance costs by enabling continuous monitoring without human intervention.
2. Augmented Reality (AR) and Virtual Reality (VR) for Maintenance
Immersive technologies like AR and VR are transforming asset inspections and repairs.
- AR can overlay real-time sensor data onto physical equipment, allowing technicians to detect faults faster.
- VR simulations help in training maintenance teams by providing realistic repair scenarios.
- Both technologies enhance accuracy, reduce human errors, and improve safety in maintenance operations.
3. Digital Twins for Predictive Analytics
Digital twins create virtual models of physical assets, simulating real-world operating conditions.
- By integrating IoT data and AI, digital twins can predict failure scenarios and test maintenance strategies.
- This technology reduces unexpected breakdowns and improves asset lifespan by allowing organizations to refine their PdM models in a risk-free environment.
4. IoT-Enabled Predictive Maintenance in EAM/CMMS Systems
Modern Enterprise Asset Management (EAM) and CMMS solutions now come equipped with IoT-powered predictive maintenance capabilities.
- Sensors provide real-time condition monitoring, triggering automated alerts for potential failures.
- Businesses can optimize maintenance scheduling, reduce downtime, and lower repair costs.
- PdM is now integrated into broader enterprise applications, creating a connected maintenance ecosystem.
5. Predictive Maintenance-as-a-Service (PdMaaS)
Cloud-based Predictive Maintenance-as-a-Service is making PdM more accessible and cost-effective for businesses of all sizes.
- Companies can outsource PdM to specialized service providers, avoiding the need for large upfront investments.
- PdMaaS solutions are scalable, require minimal training, and deliver faster ROI compared to on-premise deployments.
- Tailored PdMaaS models ensure flexibility and customization for different industries.
How Deskera ERP Helps with Predictive Maintenance
Deskera ERP provides a comprehensive suite of tools that can enhance predictive maintenance (PdM) by integrating real-time data, automation, and AI-driven analytics into asset management.
Here’s how Deskera ERP can support PdM initiatives:
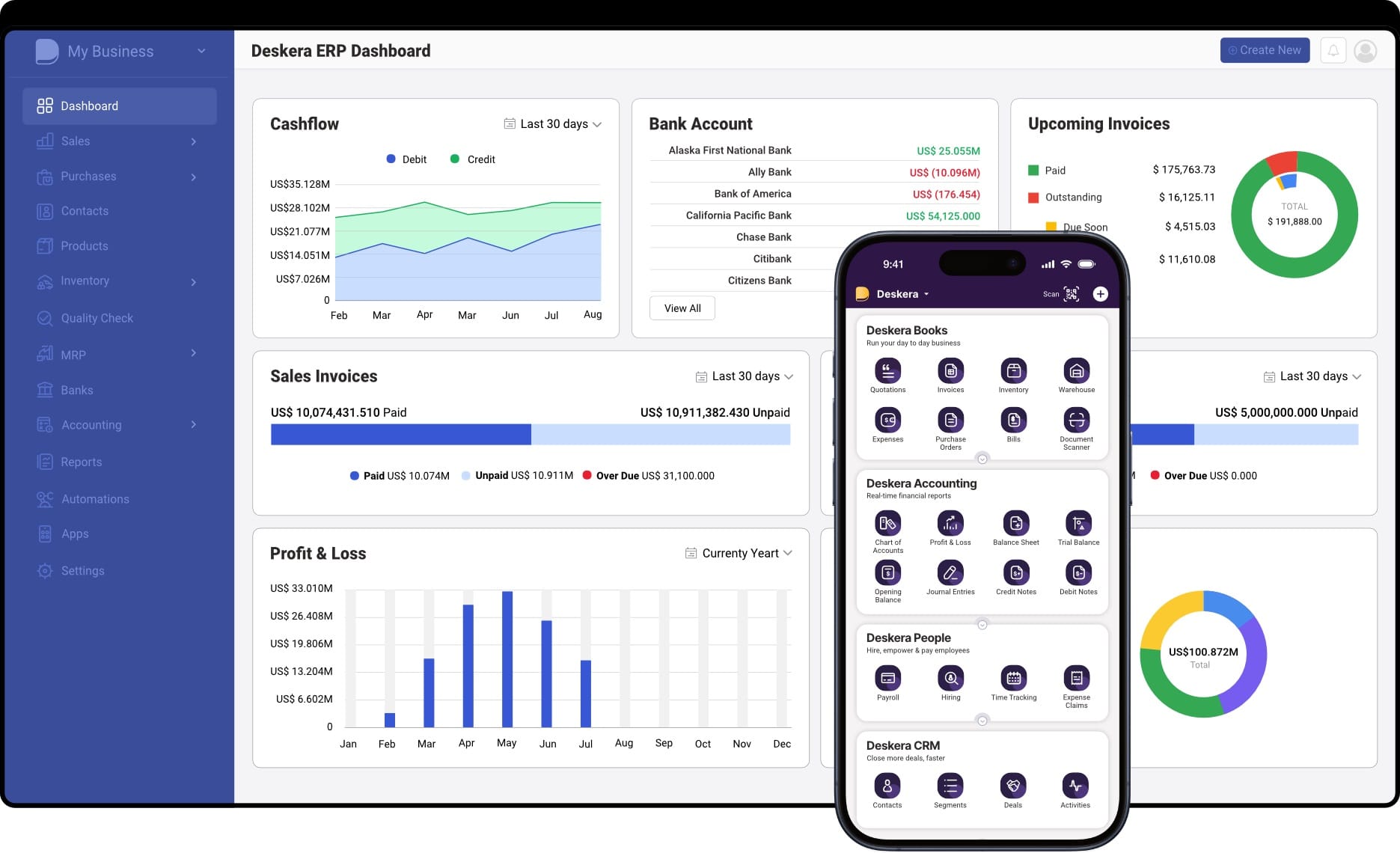
1. Centralized Asset Management
- Deskera ERP offers a single platform to track and manage all assets, ensuring that maintenance schedules, repair history, and performance data are easily accessible.
- Businesses can gain better visibility into equipment conditions and prioritize maintenance tasks accordingly.
2. Real-Time Data Collection & IoT Integration
- Deskera ERP can integrate with IoT sensors to monitor real-time asset performance.
- The system analyzes historical and real-time data to identify early warning signs of potential failures.
- Alerts and notifications ensure timely maintenance actions, reducing unexpected downtime.
3. Automated Work Order Management
- Predictive analytics in Deskera ERP automatically generates work orders when maintenance is required.
- The system ensures that the right resources, spare parts, and technicians are assigned efficiently.
- This reduces manual intervention, speeds up repairs, and prevents costly disruptions.
4. AI-Driven Predictive Analytics
- Deskera ERP leverages machine learning and AI algorithms to analyze equipment performance patterns.
- It predicts potential failures and recommends preventive actions before issues escalate.
- This helps businesses optimize maintenance schedules and avoid unnecessary servicing costs.
5. Inventory & Spare Parts Optimization
- Deskera ERP ensures that the right spare parts are always available by tracking inventory levels and automating restocking.
- This eliminates delays caused by unavailable parts and improves overall maintenance efficiency.
6. Compliance & Reporting
- The system helps businesses maintain regulatory compliance by automating audit trails, tracking maintenance logs, and generating compliance reports.
- Predictive maintenance insights allow companies to meet industry safety and maintenance standards seamlessly.
Why Choose Deskera ERP for Predictive Maintenance?
- Cloud-based & Scalable: Deskera ERP is a flexible, cloud-based solution that can be scaled to suit businesses of all sizes.
- Mobile Accessibility: Managers can monitor maintenance KPIs, approve work orders, and track asset health from anywhere.
- Seamless Integration: The system can integrate with CMMS, IoT platforms, and other enterprise applications for a connected maintenance strategy.
By leveraging Deskera ERP for predictive maintenance, businesses can reduce downtime, improve asset longevity, and enhance overall operational efficiency.
Key Takeaways
- Predictive maintenance leverages data, IoT sensors, and AI-driven analytics to anticipate equipment failures before they occur, reducing unplanned downtime and maintenance costs.
- PdM relies on real-time monitoring, historical data analysis, and predictive algorithms to assess asset health, helping businesses schedule maintenance only when necessary.
- Technologies like IoT, machine learning, digital twins, cloud computing, and automated robotic inspections enhance predictive maintenance by improving accuracy and efficiency.
- PdM increases asset lifespan, minimizes costly breakdowns, improves operational efficiency, and enhances workplace safety by addressing potential failures in advance.
- High initial costs, complex data integration, workforce training requirements, and reliance on accurate data make implementation challenging, especially for small businesses.
- Companies can mitigate challenges by starting with pilot projects, leveraging ERP software for data integration, investing in employee training, and ensuring proper sensor calibration.
- ERP solutions like Deskera ERP streamline PdM by centralizing asset management, automating work orders, optimizing inventory for spare parts, and ensuring compliance with industry regulations.
- Emerging trends like AI-driven predictive analytics, predictive maintenance-as-a-service, AR/VR for inspections, and advanced robotic monitoring will further revolutionize maintenance strategies.
Related Articles
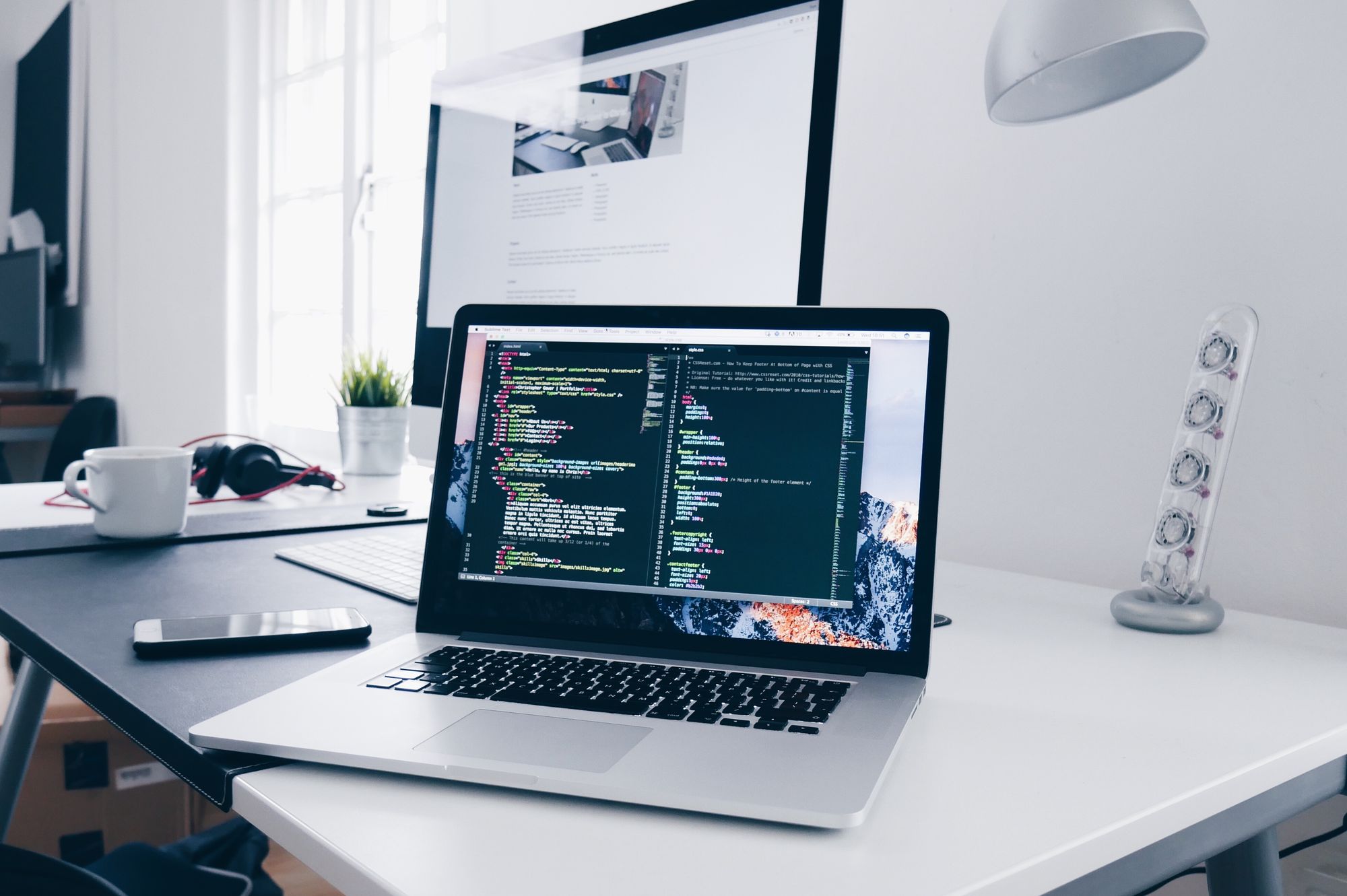
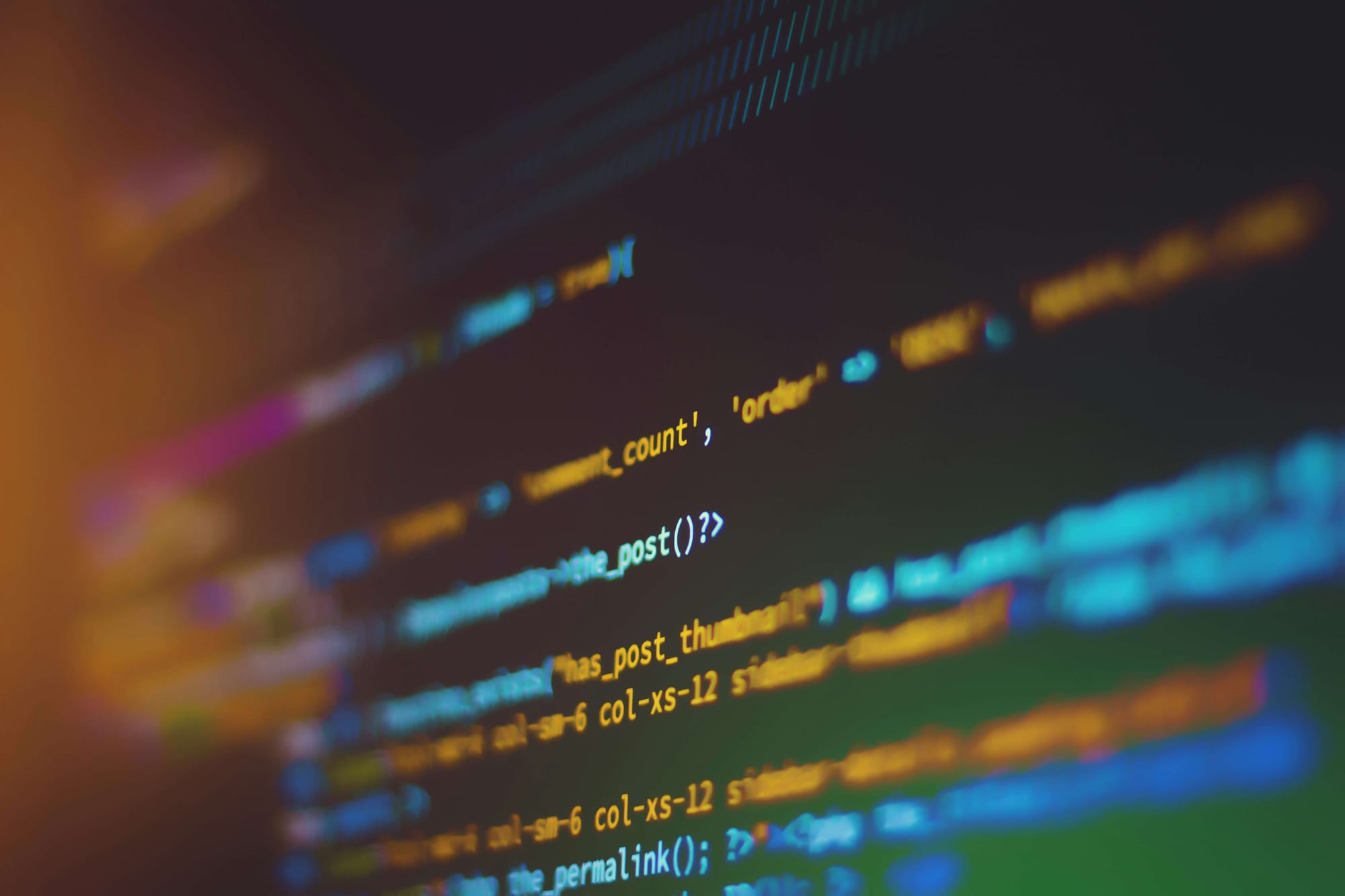
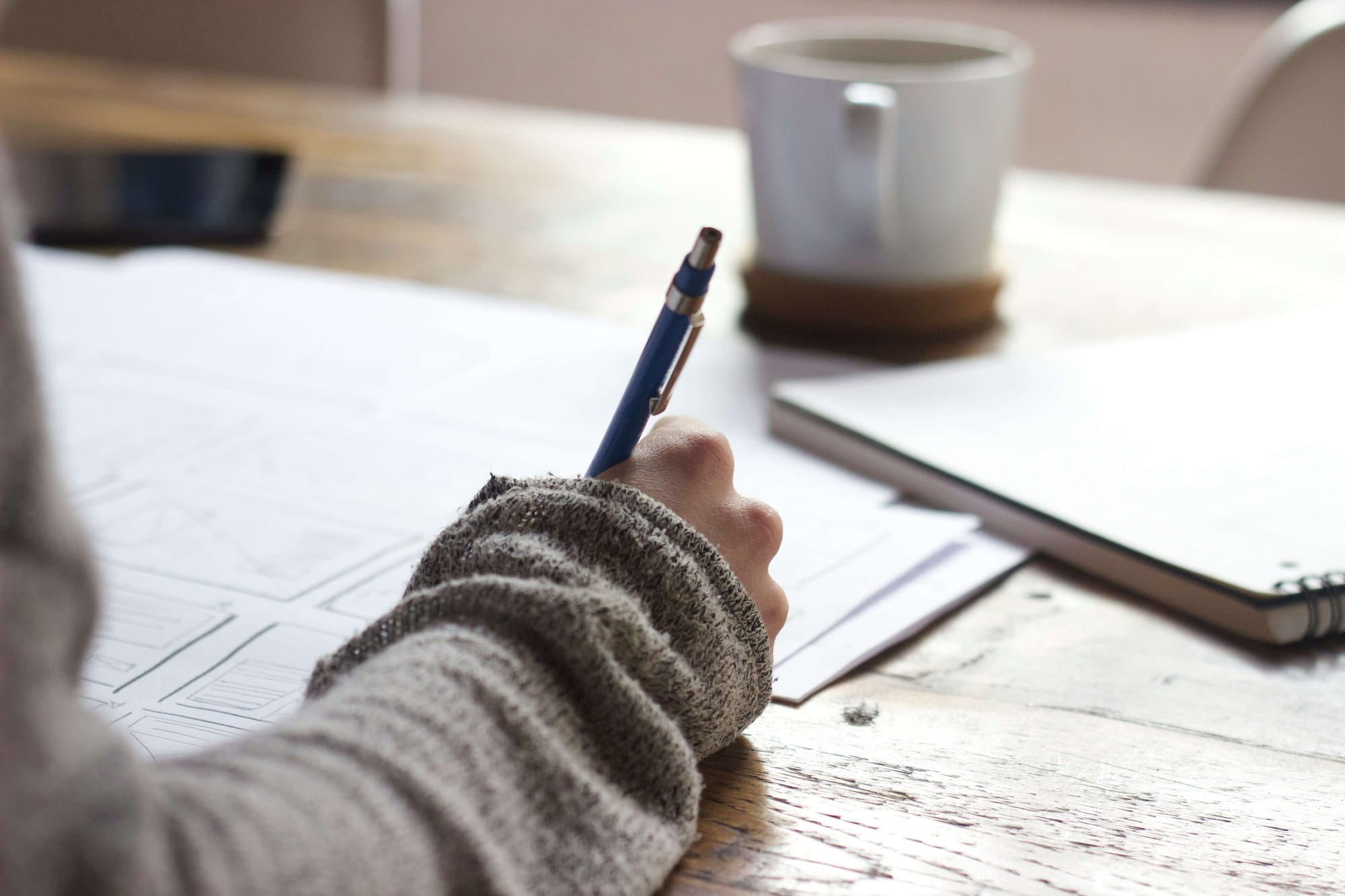
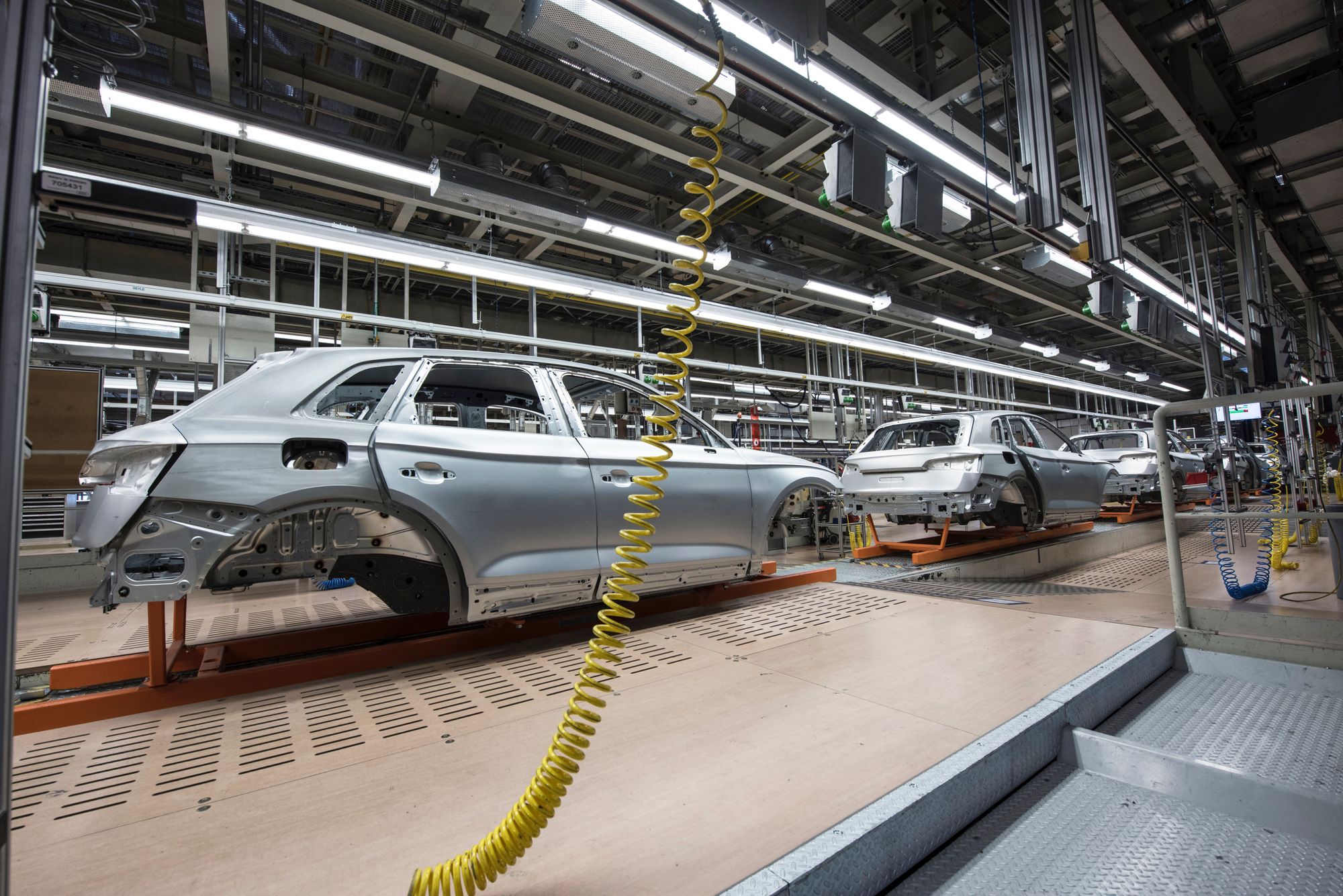
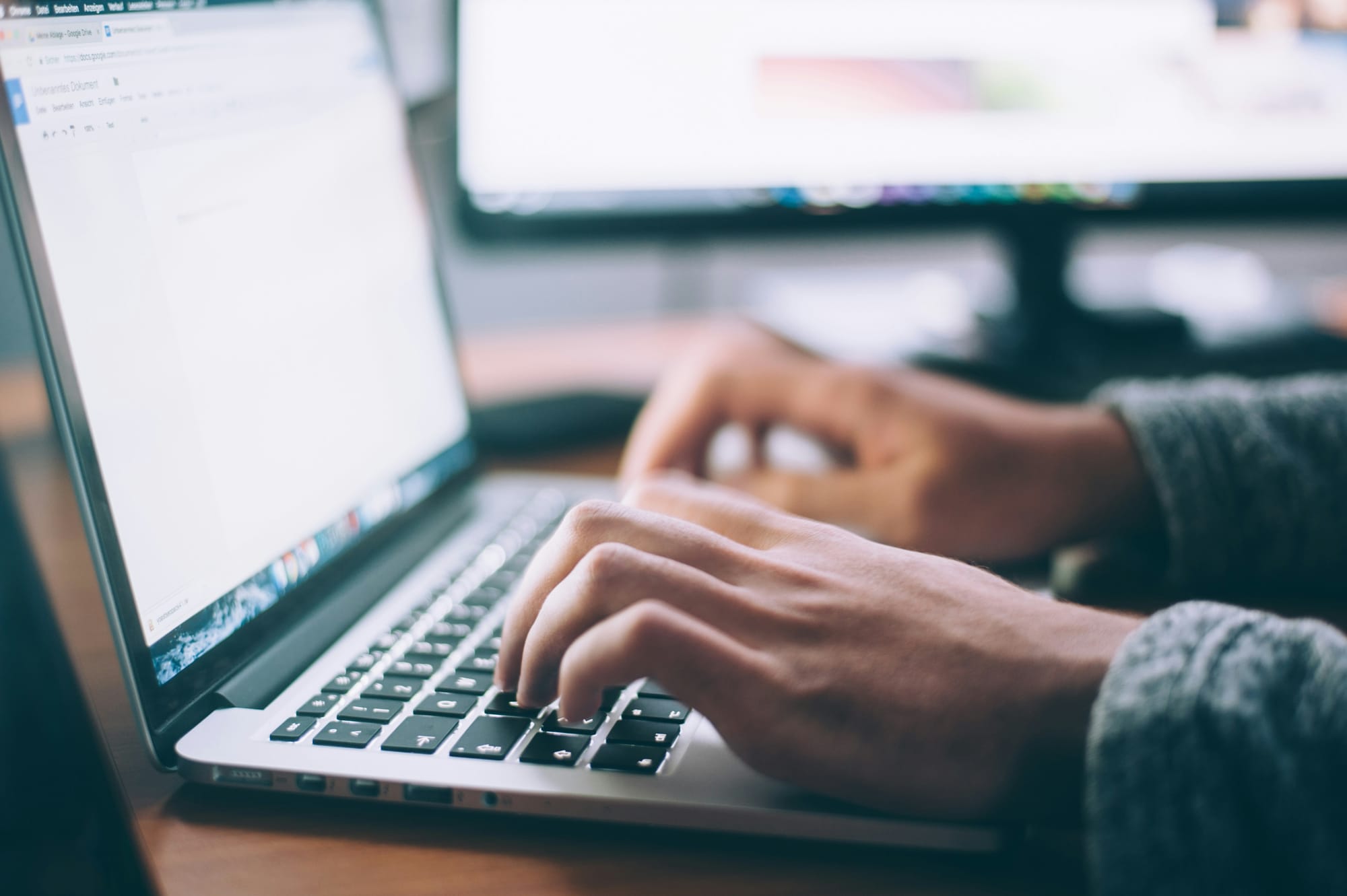
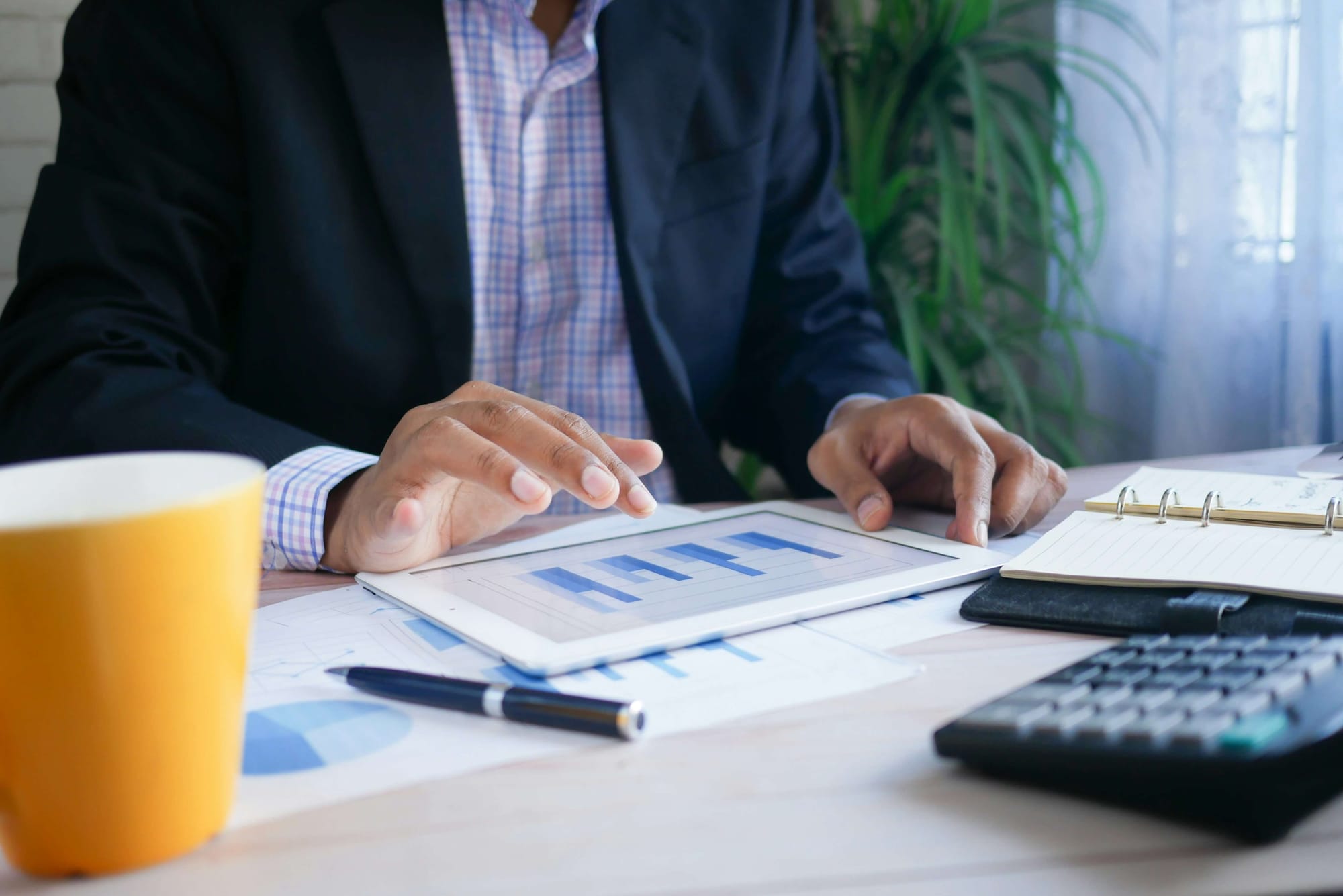