Are you a business owner looking to reduce lead time through production scheduling? If yes, then you are on the right page.
In today's fast-paced and highly competitive business landscape, reducing lead time has become a crucial goal for companies seeking to enhance their operational efficiency and gain a competitive edge. Lead time refers to the time taken from receiving a customer order to delivering the finished product. Shortening lead time is not only beneficial for meeting customer demands promptly but also for optimizing resource utilization and minimizing production costs.
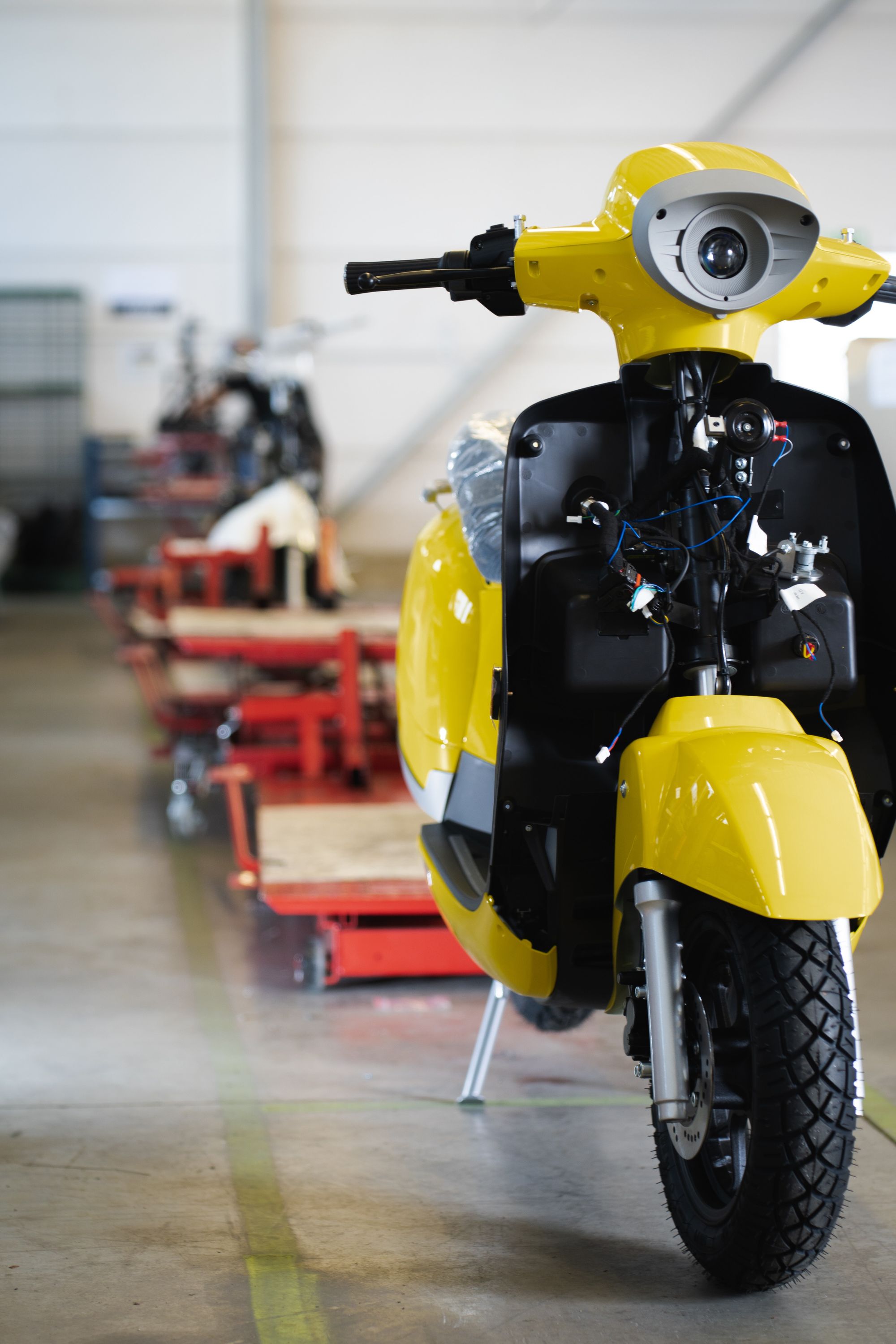
One of the most powerful tools that companies can employ to achieve shorter lead times is production scheduling. Production scheduling is the strategic planning and organization of production activities, tasks, and resources to optimize the flow of work and ensure that production processes run smoothly and efficiently.
This article explores the power of production scheduling in reducing lead time, focusing on the various ways it contributes to improved operational performance and customer satisfaction.
The topics covered in this article are:
- What is Lead Time?
- What is Production Scheduling?
- Importance of Reducing Lead Time
- Importance of Production Scheduling
- The Power of Production Scheduling in Reducing Lead Time
- Does Production Scheduling Prioritize High-Priority Orders During Peak Demand Periods?
- Can Production Scheduling Enhance On-Time Delivery Performance?
- Is Production Scheduling Suitable for Both Small and Large-Scale Manufacturing Businesses?
- Can Production Scheduling Accommodate Varying Batch Sizes Efficiently?
- Can Production Scheduling Help Reduce Variability in Lead Times?
- What Role Does Technology Play in Production Scheduling for Lead Time Reduction?
- How Can Deskera Help You with Production Scheduling?
- Key Takeaways
- Related Articles
What is Lead Time?
Lead time refers to the amount of time it takes to complete a process or task from its initiation to its completion. It is commonly used in various industries and contexts, including manufacturing, supply chain management, project management, and service delivery.
In manufacturing: Lead time refers to the time it takes for raw materials to be converted into finished goods. It includes the time taken for processing, assembly and any other steps in the production process.
In supply chain management: Lead time represents the time it takes for an order to be placed and fulfilled, including order processing, production, transportation, and delivery to the end customer.
In project management: Lead time refers to the time needed to complete a specific task or project activity. It helps project managers plan and schedule tasks efficiently.
In-service delivery: Lead time indicates the time taken to fulfill a service request, from the customer's initial contact to the delivery of the service.
Lead time is an essential metric for businesses to monitor and optimize, as it directly impacts their ability to meet customer demands, manage inventory levels, plan production schedules, and deliver products or services on time. Reducing lead time can lead to increased efficiency, better customer satisfaction, and improved overall performance.
What is Production Scheduling?
Production scheduling is the process of planning and organizing the production activities within a manufacturing facility or production system. It involves determining the sequence of operations, allocating resources, and setting timelines to ensure the efficient and timely production of goods.
The main objectives of production scheduling are:
- Meeting customer demand: Production scheduling aims to fulfill customer orders and demands in a timely manner, ensuring that products are available when needed.
- Optimizing resources: It involves the effective allocation of labor, machinery, materials, and other resources to achieve maximum efficiency and minimize production costs.
- Minimizing lead times: Efficient scheduling helps reduce the time it takes to convert raw materials into finished products, thereby shortening the lead time.
- Minimizing inventory levels: By streamlining the production process, scheduling aims to minimize excess inventory and reduce carrying costs.
- Balancing production lines: In situations where multiple products are manufactured on the same production line, scheduling ensures a balanced allocation of resources to prevent bottlenecks and optimize throughput.
- Adapting to changes: Production schedules must be flexible to accommodate changes in demand, supply, or unexpected events that can affect the production process.
The production scheduling process typically involves the following steps:
- Demand forecasting: Analyzing historical data and market trends to estimate future demand for products.
- Order management: Managing customer orders and understanding their priorities.
- Capacity planning: Assessing the available resources and their capacity to determine what can be produced within a given timeframe.
- Sequencing: Deciding the order in which different production tasks or jobs will be executed.
- Scheduling: Setting specific start and end times for each production task or job.
- Monitoring and control: Keeping track of production progress and making adjustments as necessary to maintain the schedule.
Production scheduling is a critical aspect of efficient manufacturing operations as it ensures that resources are utilized effectively, production runs smoothly, and customer orders are fulfilled promptly. Modern manufacturing often uses software systems to aid in complex production scheduling processes and optimize production efficiency.
Importance of Reducing Lead Time
Reducing lead time is of paramount importance for businesses across various industries. It offers numerous benefits that positively impact the overall efficiency, customer satisfaction, and competitiveness of a company.
Here are some key reasons why reducing lead time is crucial:
- Improved Customer Satisfaction: Shorter lead times mean faster delivery of products or services to customers. This translates to quicker order fulfillment and reduced waiting times, leading to higher customer satisfaction and customer loyalty.
- Increased Responsiveness: Reduced lead time allows a company to respond swiftly to changes in customer demands, market trends, and emerging opportunities. Being able to adapt quickly can give a competitive edge in dynamic markets.
- Lower Inventory Costs: Shorter lead times mean businesses can operate with lower inventory levels while still meeting customer demands. This reduces carrying costs, the risk of overstocking, and the need for expensive warehousing.
- Enhanced Flexibility: With reduced lead times, a company can adjust production schedules and respond to unexpected events or disruptions more effectively, minimizing the impact on operations.
- Faster Innovation and Time-to-Market: Shorter lead times enable companies to bring new products and innovations to the market more quickly, gaining a first-mover advantage and capturing market share ahead of competitors.
- Increased Productivity and Efficiency: Streamlining processes to reduce lead times often leads to improved operational efficiency, optimized resource allocation, and a reduction in unnecessary delays.
- Better Cash Flow: Quicker turnaround times from production to sales lead to faster revenue generation, which, in turn, improves cash flow and financial stability.
- Higher Competitiveness: A company with shorter lead times can be more agile, responsive, and efficient, making it more competitive in the market and attracting more customers.
- Improved Supplier Relationships: Reducing lead times can positively impact relationships with suppliers, as they can better plan their production and deliveries, leading to more reliable partnerships.
- Reduced Risk: Long lead times may result in uncertainty and higher risks, such as demand fluctuations, obsolescence, and changes in market conditions. Shortening lead times mitigates these risks.
Overall, reducing lead time is a strategic approach to optimize business operations and enhance customer satisfaction. It requires careful planning, efficient processes, and often the adoption of modern technologies to streamline and accelerate production cycles, supply chains, and service delivery.
Businesses that effectively reduce lead times can gain a competitive advantage and position themselves for long-term success in their respective markets.
Importance of Production Scheduling
Production scheduling is a critical aspect of manufacturing and production processes, and its importance cannot be overstated.
Here are some key reasons why production scheduling is crucial for businesses:
- Optimal Resource Utilization: Production scheduling ensures that resources such as labor, machinery, equipment, and materials are allocated efficiently. It helps avoid overloading certain resources while others remain underutilized, leading to cost savings and increased productivity.
- Meeting Customer Demand: Effective production scheduling ensures that customer orders and demands are met on time. It helps avoid delays in production and delivery, leading to higher customer satisfaction and customer retention.
- Reduced Lead Times: By streamlining the production process and minimizing wait times between different stages, production scheduling helps in reducing overall lead times. This, in turn, allows businesses to respond more quickly to changing market demands and remain competitive.
- Inventory Management: A well-executed production schedule helps in maintaining optimal inventory levels. It prevents excess inventory buildup, reduces carrying costs, and minimizes the risk of stockouts.
- Improved Production Planning: Production scheduling allows for better production planning and coordination of production activities. It enables companies to anticipate potential bottlenecks or constraints and proactively address them.
- Enhanced Efficiency: With a clear production schedule, employees know their tasks and timelines, leading to improved workflow and efficiency in the production process.
- Cost Reduction: Effective production scheduling can lead to cost savings through better resource allocation, reduced overtime, minimized setup times, and improved process efficiency.
- Better Quality Control: With production scheduling, companies can allocate time for quality control checks and inspections, ensuring that products meet the required standards before reaching customers.
- Flexibility and Adaptability: A well-designed production schedule allows for adjustments and reallocation of resources when unexpected events or changes in demand occur. It enhances the company's ability to respond to dynamic market conditions.
- Competitive Advantage: Efficient production scheduling can provide a competitive edge by allowing businesses to produce more, at a lower cost, and with quicker turnaround times than competitors.
- Improved Decision-Making: A production schedule provides a clear roadmap for managers to make informed decisions related to production, resource allocation, and customer commitments.
- Better Workforce Management: Scheduling helps companies manage their workforce effectively by ensuring the right number of skilled workers are available at the right time.
Overall, production scheduling plays a vital role in optimizing production processes, reducing costs, meeting customer demands, and enhancing overall efficiency. It allows businesses to operate smoothly and proactively, which is crucial in today's fast-paced and competitive market environments.
The Power of Production Scheduling in Reducing Lead Time
Production scheduling plays a pivotal role in reducing lead time and can significantly impact a company's operational efficiency and competitiveness.
Here's how production scheduling contributes to lead time reduction:
Efficient Resource Allocation
Efficient resource allocation in production scheduling involves the strategic planning and distribution of various resources, including labor, machinery, equipment, and materials, to ensure their optimal utilization and minimize wastage.
This aspect of production scheduling directly impacts lead time reduction by eliminating idle time, reducing setup times, and maintaining a smooth flow of production processes.
Here's a more detailed explanation of how efficient resource allocation contributes to shorter lead times:
- Minimizing Idle Time: Idle time refers to the periods when resources are not actively engaged in productive tasks. Inefficient resource allocation can lead to excessive idle time, causing delays and increasing lead times. Production scheduling identifies the required resources for each task and ensures they are available when needed. By minimizing idle time, production processes run smoothly, and lead times are shortened.
- Optimizing Machine and Equipment Usage: Proper production scheduling takes into account the capacity and capabilities of different machines and equipment. By strategically scheduling tasks on appropriate machinery, companies can maximize their utilization and throughput. This reduces waiting time for machine availability and enhances overall production efficiency, contributing to shorter lead times.
- Balancing Workloads: Production scheduling ensures that workloads are balanced across resources and production lines. When workloads are evenly distributed, no single resource becomes a bottleneck, which would otherwise slow down the entire production process. This balance prevents unnecessary delays and reduces lead times.
- Reducing Changeover Time: In settings where different products or batches are produced on the same machines or production lines, changeover time can be a significant source of downtime. Efficient production scheduling aims to minimize changeover time by grouping similar tasks together or sequencing tasks strategically. This approach helps to reduce setup time and keeps production lines running smoothly, ultimately leading to shorter lead times.
- Prioritizing Critical Tasks: Production scheduling allows managers to prioritize critical tasks or orders with tight deadlines. By ensuring that essential tasks are given the necessary resources and attention, businesses can meet urgent customer demands promptly and reduce lead times for time-sensitive orders.
- Minimizing Material Shortages: Effective production scheduling considers the availability of raw materials and components required for production. By coordinating with suppliers and integrating supply chain information, companies can avoid material shortages and production delays caused by material unavailability, thus reducing lead times.
- Real-Time Resource Tracking: Modern production scheduling systems often provide real-time tracking and monitoring of resource usage. This allows managers to spot any deviations from the schedule promptly and take corrective actions to keep production on track. Early intervention prevents delays and helps maintain shorter lead times.
In conclusion, efficient resource allocation through production scheduling is crucial for streamlining production processes, optimizing resource utilization, and reducing lead times. By ensuring that the right resources are available at the right time and place, businesses can improve their operational efficiency, meet customer demands more effectively, and gain a competitive advantage in the market.
Minimizing Setup and Changeover Times
Minimizing setup and changeover times is a crucial aspect of production scheduling that directly impacts the overall efficiency and productivity of a manufacturing process.
Setup time refers to the time required to prepare a machine, equipment, or production line for a new task or product, while changeover time specifically refers to the time it takes to transition from one product or production run to another. Both setup and changeover times can result in significant downtime if not managed effectively.
Here's a more detailed explanation of how minimizing setup and changeover times contributes to shorter lead times:
- Reduced Downtime: Long setup and changeover times can lead to significant downtime between production runs, which in turn increases the overall lead time for a product. By minimizing these times, production scheduling aims to keep the equipment and production lines running more consistently, reducing idle time and optimizing production capacity.
- Sequential and Parallel Processing: Production scheduling carefully plans the order in which different tasks or products are produced. By organizing tasks to be processed in sequence or in parallel, setup and changeover times can be optimized. Sequential processing minimizes changeovers by producing similar products consecutively, while parallel processing allows different products to be produced simultaneously, reducing overall downtime.
- Standardization and Simplification: Standardizing and simplifying setup procedures can significantly reduce the time required for changeovers. For instance, using quick-change tooling or standardized equipment setups allows for faster transitions between different tasks, thus minimizing changeover times.
- Smaller Batch Sizes: Production scheduling can help determine the ideal batch size for each production run. Smaller batch sizes mean more frequent changeovers, but they also reduce the amount of work-in-progress (WIP) inventory and the risk of overproduction. This approach supports a more responsive and flexible production process.
- Elimination of Non-Value-Adding Activities: Production scheduling identifies and eliminates non-value-adding activities during setup and changeover processes. By focusing only on essential steps and eliminating waste, the time required for setup and changeovers is reduced, contributing to shorter lead times.
- Training and Skill Development: Properly trained and skilled operators can perform setups and changeovers more efficiently. Production scheduling takes into account operator skill levels and ensures that tasks are assigned to the most capable individuals, improving the speed and effectiveness of these processes.
- Continuous Improvement and Kaizen: Production scheduling is not a one-time activity but an ongoing process of improvement. Companies can use principles like Kaizen (continuous improvement) to regularly analyze setup and changeover times, identify areas for enhancement, and implement changes that further reduce lead times.
- Integration with Maintenance: Regular maintenance and equipment upkeep is vital to reducing downtime during setup and changeovers. Production scheduling can integrate maintenance activities to ensure that machines and equipment are in optimal condition, reducing the risk of breakdowns and unplanned downtime.
By minimizing setup and changeover times, production scheduling helps increase production efficiency, reduce lead times, and enhance a company's ability to respond quickly to changing customer demands.
It promotes a more agile and responsive production process, ultimately leading to improved customer satisfaction and a competitive edge in the market.
Streamlined Production Flow
Streamlined production flow is a critical aspect of production scheduling that focuses on optimizing the sequence of production tasks and minimizing delays between different stages of the manufacturing process. The goal is to create a smooth and efficient flow of work that reduces lead times and enhances overall production efficiency.
Here's a more detailed explanation of how streamlined production flow contributes to shorter lead times:
- Process Mapping and Analysis: Production scheduling begins with a thorough process mapping and analysis of the entire production workflow. This involves breaking down the production process into individual steps and identifying potential bottlenecks, inefficiencies, and areas for improvement.
- Elimination of Waste: One of the key principles of streamlining production flow is to eliminate waste, as defined by Lean Manufacturing principles. Waste can take various forms, including overproduction, excessive waiting time, unnecessary transportation, and excess inventory. By identifying and eliminating waste, production scheduling aims to create a leaner and more efficient production process.
- Optimal Task Sequencing: Based on the process analysis, production scheduling determines the most optimal sequence for performing production tasks. Tasks are sequenced in a way that minimizes wait times between different stages, ensuring a smoother flow of work and reducing lead times.
- Kanban and Just-in-Time (JIT) Production: Production scheduling may incorporate Kanban systems and Just-in-Time (JIT) production principles. Kanban systems use visual signals to manage inventory and trigger production tasks only when necessary, reducing inventory levels and improving production flow. JIT production focuses on producing only what is needed, precisely when it is needed, which minimizes waste and optimizes production efficiency.
- Pull Production System: A pull production system, another concept derived from Lean Manufacturing, ensures that production is initiated based on actual customer demand. This approach avoids overproduction and reduces the risk of accumulating excess inventory, leading to a smoother production flow and shorter lead times.
- Balancing Production Workloads: Production scheduling strives to balance workloads across different production stages and resources. When workloads are balanced, no single stage becomes a bottleneck that slows down the entire production process. Balanced workloads help maintain a steady production flow and reduce lead times.
- Capacity and Resource Planning: Production scheduling considers the capacity and availability of resources such as labor, machinery, and equipment. By aligning production tasks with resource capacities, companies can avoid resource constraints and ensure a continuous and streamlined flow of production.
- Continuous Improvement: Streamlined production flow is not a one-time achievement but an ongoing process of continuous improvement. Production scheduling facilitates the identification of opportunities for improvement and encourages the implementation of changes that lead to even greater efficiency and shorter lead times over time.
By focusing on a streamlined production flow, production scheduling contributes to reducing delays, eliminating waste, optimizing resources, and enhancing the overall efficiency of the production process. This, in turn, leads to shorter lead times, increased customer satisfaction, and improved competitiveness in the market.
Real-Time Monitoring and Adjustment
Real-time monitoring and adjustment in production scheduling refer to the ability to track and analyze production activities as they occur and make timely adjustments to ensure that production stays on track and meets the desired goals.
This dynamic approach allows companies to respond quickly to changes, identify potential issues, and optimize production processes in real time.
Here's a more detailed explanation of how real-time monitoring and adjustment contribute to shorter lead times:
- Immediate Issue Identification: Real-time monitoring enables managers to identify issues or deviations from the production schedule as soon as they arise. This could include unexpected machine breakdowns, material shortages, or any other disruptions. Identifying problems early allows for faster resolution, reducing downtime and minimizing the impact on lead times.
- Data-Driven Decision Making: Real-time monitoring provides access to live data and performance metrics, allowing managers to make informed decisions based on up-to-date information. Data-driven decision-making helps optimize production schedules, allocate resources effectively, and maintain efficient production flow, all of which contribute to shorter lead times.
- Proactive Problem Solving: With real-time monitoring, potential bottlenecks or inefficiencies can be identified proactively. Managers can take corrective actions before these issues escalate, preventing delays and ensuring a smooth production process.
- Continuous Performance Evaluation: Real-time monitoring allows for continuous evaluation of production performance against the planned schedule. This ongoing assessment helps identify trends and patterns, enabling companies to implement continuous improvement initiatives to further reduce lead times.
- Resource Allocation Optimization: By tracking resource usage in real time, production scheduling can optimize resource allocation. It helps ensure that resources are being used efficiently, avoids overloading certain resources, and maintains a balanced production flow, ultimately reducing lead times.
- Adaptation to Demand Fluctuations: Real-time monitoring enables companies to respond quickly to changes in customer demand. As demand fluctuates, production schedules can be adjusted in real-time to prioritize critical orders and avoid backlogs, thereby minimizing lead times for urgent customer requests.
- Integration with IoT and Automation: Real-time monitoring often involves the integration of Internet of Things (IoT) devices and automation systems on the production floor. These technologies provide real-time data on machine performance, product quality, and other essential parameters. By utilizing IoT and automation, companies can quickly detect anomalies, make necessary adjustments, and maintain a streamlined production flow.
- Collaboration and Communication: Real-time monitoring fosters better collaboration and communication among different teams and departments involved in the production process. It enables swift communication of critical information, ensuring that everyone is aware of any changes or issues that may impact production schedules.
By leveraging real-time monitoring and adjustment, production scheduling becomes a dynamic and responsive process. It empowers companies to proactively manage their production operations, address challenges promptly, and optimize resource usage to achieve shorter lead times, improved efficiency, and enhanced customer satisfaction.
Effective Order Sequencing
Effective order sequencing in production scheduling refers to the strategic arrangement of customer orders or production tasks in a sequence that maximizes efficiency, minimizes setup times, and optimizes resource utilization. By carefully planning the order in which different orders or tasks are executed, companies can reduce lead times and improve overall production performance.
Here's a more detailed explanation of how effective order sequencing contributes to shorter lead times:
- Similar Product Grouping: Production scheduling groups similar or related products together in a sequence. By producing similar products consecutively, changeover times between production runs are minimized, as the setup and preparation for the next task are often similar or even identical. This reduces downtime and optimizes resource utilization.
- Prioritization of High-Priority Orders: Effective order sequencing takes into account the priority of different customer orders or production tasks. High-priority orders are given precedence and scheduled to be completed first. This ensures that urgent customer demands are met promptly, reducing lead times for critical orders.
- Minimization of Waiting Time: Order sequencing aims to minimize waiting times between different production stages. By scheduling tasks in a logical and timely manner, work flows smoothly from one stage to the next without unnecessary delays, ultimately shortening lead times.
- Demand Forecasting: Production scheduling considers demand forecasting data to predict customer orders in advance. By anticipating demand trends, companies can optimize order sequencing to handle expected order volumes more efficiently, avoiding last-minute rush and potential delays.
- Batch Size Optimization: Order sequencing is closely tied to batch size optimization. Smaller batch sizes allow for more frequent changeovers but also reduce work-in-progress (WIP) inventory, decrease lead times, and provide greater flexibility in meeting changing customer demands.
- Reduced Setup Time Impact: Efficient order sequencing minimizes the impact of setup times on overall production performance. By organizing tasks strategically, the setup time between different orders is effectively absorbed into the production schedule, ensuring a more continuous and streamlined flow of work.
- Effective Use of Critical Resources: Some resources or equipment may have limited availability or may be critical for specific tasks. Production scheduling ensures that these critical resources are utilized efficiently and that tasks requiring these resources are sequenced accordingly, reducing the risk of delays and resource constraints.
- Agility and Adaptability: An effective order sequencing strategy considers the need for flexibility and adaptability in production. As customer demands change or unexpected events occur, production schedules can be adjusted promptly to accommodate these changes without compromising lead times.
- Integration with Supply Chain: Production scheduling can be integrated with supply chain management systems, enabling a more holistic approach to order sequencing. By considering supply chain factors, such as raw material availability and transportation lead times, companies can further optimize order sequencing and reduce overall lead times.
By carefully planning and sequencing customer orders and production tasks, production scheduling optimizes the utilization of resources, reduces downtime, and ensures a more efficient production process. This ultimately leads to shorter lead times, improved customer satisfaction, and increased competitiveness in the market.
Improved Workforce Efficiency
Improving workforce efficiency is a crucial aspect of production scheduling that focuses on optimizing the productivity and performance of the workforce involved in the production process. A more efficient workforce translates to quicker task completion, reduced idle time, and overall improved production output, leading to shorter lead times.
Here's a more detailed explanation of how improving workforce efficiency contributes to reducing lead times:
- Task Assignment and Workload Balancing: Production scheduling ensures that tasks are assigned to the most appropriate workers based on their skills and expertise. By matching the right people to the right tasks, employees can perform their duties more effectively, reducing errors and minimizing the time required to complete each task.
- Reduced Waiting Time: By streamlining production processes and coordinating tasks, production scheduling minimizes waiting time for workers. When employees have clear instructions and can proceed with their assigned tasks promptly, waiting periods are reduced, leading to a smoother workflow and shorter lead times.
- Standardized Work Procedures: Production scheduling may involve the implementation of standardized work procedures. Standardization provides clear guidelines and instructions for workers, ensuring consistent and efficient execution of tasks, which in turn improves productivity and reduces lead times.
- Training and Skill Development: Investing in workforce training and skill development enhances employees' capabilities and confidence in performing their tasks. A well-trained workforce is more efficient, makes fewer mistakes, and requires less supervision, contributing to improved overall production efficiency and shorter lead times.
- Incentives and Motivation: Production scheduling can align incentives and performance goals with lead time reduction objectives. By incentivizing workers to achieve productivity targets and meet production schedules, motivation, and engagement increase, leading to a more efficient and focused workforce.
- Minimizing Unplanned Absences: Production scheduling helps anticipate production demands and plan workforce availability accordingly. By aligning work shifts and vacation schedules, companies can minimize unplanned absences, ensuring a consistent and uninterrupted production process.
- Employee Empowerment: Production scheduling that involves input from the workforce fosters a sense of ownership and empowerment among employees. When workers are involved in decision-making and process improvement initiatives, they are more likely to take ownership of their tasks and contribute to a more efficient production process.
- Continuous Improvement Culture: Production scheduling promotes a culture of continuous improvement. By regularly analyzing performance data and seeking input from workers, companies can identify areas for improvement and implement changes that optimize workforce efficiency and reduce lead times over time.
- Clear Communication: Effective production scheduling includes clear communication of production schedules, goals, and expectations to the workforce. When employees have a clear understanding of the production plan, they can align their efforts and work collaboratively to achieve the desired outcomes, ultimately leading to shorter lead times.
By focusing on improving workforce efficiency, production scheduling creates a more productive, engaged, and effective workforce. This, in turn, leads to reduced lead times, increased productivity, and improved overall performance, positioning the company for greater success and competitiveness in the market.
Faster Response to Changes in Demand
Faster response to changes in demand is a crucial capability that effective production scheduling provides to companies. It involves the ability to adapt quickly and efficiently to fluctuations in customer demand, market trends, or unforeseen events. A company's agility in responding to these changes can significantly impact lead times and overall customer satisfaction.
Here's a more detailed explanation of how a faster response to changes in demand contributes to lead time reduction:
- Real-Time Data and Insights: Production scheduling relies on real-time data and performance metrics. This up-to-date information enables companies to closely monitor customer demand patterns and market trends, allowing them to detect changes early and respond promptly.
- Flexible Production Plans: A well-designed production schedule includes flexibility to adjust production plans rapidly. Companies can resequence tasks, prioritize critical orders, and allocate resources based on the latest demand information, ensuring a more efficient and adaptable production process.
- Dynamic Inventory Management: Faster response to changes in demand allows companies to adjust their inventory management strategies accordingly. By aligning production levels with actual demand, they can avoid excessive stockpiling or stockouts, leading to reduced lead times.
- Quick Order Processing: Production scheduling ensures that customer orders are processed promptly. With a faster response to incoming orders, companies can initiate production activities sooner, minimizing the time between order placement and delivery.
- Supply Chain Collaboration: Effective production scheduling involves close collaboration with suppliers and other stakeholders in the supply chain. By maintaining open communication channels, companies can respond rapidly to changes in material availability or transportation issues, mitigating potential delays.
- Optimized Resource Allocation: In response to changes in demand, production scheduling can optimize the allocation of resources, including labor and machinery. Allocating resources based on demand fluctuations ensures that production remains aligned with actual requirements, preventing unnecessary downtime and bottlenecks.
- Accurate Demand Forecasting: Production scheduling incorporates accurate demand forecasting to anticipate future customer requirements. By having a clearer picture of anticipated demand, companies can plan ahead and prepare for fluctuations in production volumes more effectively.
- Adaptable Production Processes: A faster response to changes in demand requires adaptable production processes. Companies can adopt lean manufacturing principles, implement quick changeover techniques, and embrace flexible manufacturing technologies to adjust production quickly to new demand scenarios.
- Minimized Lead Time Variability: Faster response to changes in demand helps minimize lead time variability. By reducing the time taken to process orders and deliver products, companies can provide a more consistent and reliable experience to customers.
- Customer Satisfaction: Ultimately, a faster response to changes in demand leads to better customer satisfaction. When companies can fulfill customer needs promptly and efficiently, customers are more likely to be satisfied and loyal, leading to repeat business and positive word-of-mouth referrals.
In conclusion, a faster response to changes in demand is a crucial aspect of production scheduling that enables companies to stay agile, adaptive, and customer-focused.
By adjusting production plans, optimizing resources, and collaborating effectively with the supply chain, companies can reduce lead times and enhance overall operational efficiency, ultimately leading to a competitive advantage in the market.
Smoother Supply Chain Integration
Smoother supply chain integration is a critical aspect of production scheduling that involves seamless coordination and collaboration with suppliers, vendors, and other partners within the supply chain.
It aims to optimize the flow of materials, information, and resources throughout the supply chain, leading to improved production efficiency and reduced lead times.
Here's a more detailed explanation of how smoother supply chain integration contributes to shorter lead times:
- Real-Time Communication: Effective production scheduling requires real-time communication and data exchange with suppliers. By having timely information on material availability, transportation schedules, and potential delays, companies can make informed decisions and adjust production plans accordingly.
- Timely Material Procurement: Smoother supply chain integration ensures that raw materials and components are procured in a timely manner. By aligning material deliveries with production schedules, companies can avoid stockouts and reduce waiting times for essential materials, leading to shorter lead times.
- Collaborative Production Planning: Production scheduling involves collaborative production planning with suppliers. By sharing production forecasts and demand information, suppliers can plan their own production and inventory levels, ensuring a more synchronized and efficient supply chain.
- Supplier Performance Monitoring: Smoother supply chain integration enables companies to monitor supplier performance more effectively. By tracking key performance indicators (KPIs) such as delivery reliability and lead times, companies can identify areas for improvement and build more reliable supplier partnerships.
- Integrated Inventory Management: Production scheduling that integrates with the supply chain allows for better visibility into inventory levels at various stages of the supply chain. This visibility helps optimize inventory management, avoiding excess stockpiling and ensuring adequate stock levels to meet customer demands.
- Just-in-Time (JIT) Delivery: JIT delivery is a concept closely associated with smoother supply chain integration. By implementing JIT principles, companies can receive materials and components just in time for production, reducing the need for large buffer inventories and minimizing lead times.
- Mitigation of Supply Disruptions: Smoother supply chain integration enables companies to quickly identify and address potential supply disruptions. By proactively managing risks and implementing contingency plans, companies can minimize the impact of supply disruptions on production schedules and lead times.
- Agility in Supply Chain Adjustments: When demand patterns change, production scheduling that is well-integrated with the supply chain allows for swift adjustments. Companies can work closely with suppliers to modify material orders and delivery schedules, ensuring a more responsive and adaptive production process.
- Improved Order Fulfillment: Smoother supply chain integration supports improved order fulfillment capabilities. With better coordination between production schedules and supplier deliveries, companies can fulfill customer orders more efficiently and meet promised delivery dates, leading to shorter lead times.
- Collaborative Problem-Solving: In cases of unexpected supply chain challenges, smooth integration fosters collaborative problem-solving. By working together with suppliers to find solutions, companies can overcome obstacles and maintain a consistent production flow, reducing delays and minimizing lead times.
In summary, smoother supply chain integration is a key enabler of efficient production scheduling. By fostering collaboration, optimizing inventory, improving communication, and adapting to changes in the supply chain, companies can achieve shorter lead times, enhance customer satisfaction, and strengthen their competitive position in the market.
Reduced Rework and Errors
Reduced rework and errors are a critical aspect of production scheduling that focuses on identifying and addressing potential issues early in the production process to minimize the need for rework or corrections.
By implementing measures to prevent errors and ensuring quality control throughout the production process, companies can significantly reduce lead times and improve overall production efficiency.
Here's a more detailed explanation of how reducing rework and errors contributes to shorter lead times:
- Standardized Work Procedures: Production scheduling involves the implementation of standardized work procedures that provide clear guidelines for each task. When workers follow consistent and standardized processes, the likelihood of errors and variations decreases, leading to higher-quality output and reduced rework.
- Training and Skill Development: Investing in workforce training and skill development ensures that employees have the necessary knowledge and expertise to perform their tasks accurately. Skilled workers are less likely to make errors, leading to a reduction in rework and a smoother production process.
- Quality Control Checks: Production scheduling includes provisions for quality control checks at various stages of the production process. These checks help identify defects or errors early on, allowing for immediate corrective action and preventing the need for rework later in the process.
- Real-Time Monitoring: Real-time monitoring of production activities allows managers to identify deviations from quality standards promptly. This enables timely intervention to address any issues, preventing the propagation of errors and avoiding the need for extensive rework.
- Root Cause Analysis: When errors occur, production scheduling incorporates root cause analysis to identify the underlying factors contributing to the problem. By addressing the root causes, companies can implement preventive measures to avoid similar errors in the future, leading to improved efficiency and reduced rework.
- Effective Communication: Clear and effective communication between different teams and departments involved in the production process is essential to avoid misunderstandings and errors. Production scheduling ensures that communication channels are established, promoting better coordination and accuracy.
- Risk Management: Production scheduling involves risk management strategies to identify potential sources of errors and defects. By proactively managing risks, companies can take preventive measures and minimize the occurrence of errors, leading to shorter lead times.
- Continuous Improvement Culture: Production scheduling fosters a culture of continuous improvement, encouraging employees to provide feedback and suggestions for process enhancements. By continuously refining processes based on feedback, companies can reduce errors and optimize production efficiency over time.
- Automation and Technology: Integration of automation and advanced technology in the production process can significantly reduce human errors. Production scheduling incorporates the use of technology to automate repetitive tasks, ensuring higher accuracy and consistency in output.
- Supplier Quality Management: Smoother supply chain integration, as mentioned earlier, includes supplier quality management. By working closely with suppliers to ensure the quality of incoming materials and components, companies can minimize errors caused by poor-quality inputs.
In conclusion, reducing rework and errors through effective production scheduling leads to higher-quality output, reduced lead times, and improved overall production efficiency.
By implementing preventive measures, emphasizing quality control, and fostering a culture of continuous improvement, companies can enhance customer satisfaction and gain a competitive advantage in the market.
Continuous Improvement
Continuous improvement is a fundamental principle of production scheduling that emphasizes the ongoing effort to identify and implement enhancements in all aspects of the production process.
It involves regularly evaluating performance, identifying areas for improvement, and making incremental changes to optimize efficiency and reduce lead times.
Continuous improvement is not a one-time event but a continual and iterative process that helps companies stay competitive and adapt to changing market demands.
Here's a more detailed explanation of how continuous improvement contributes to shorter lead times:
- Data-Driven Analysis: Continuous improvement relies on data-driven analysis of production performance. Key performance indicators (KPIs) are monitored regularly to measure productivity, lead times, quality, and other critical metrics. This data provides insights into areas that need improvement and guides decision-making.
- Root Cause Analysis: When issues or inefficiencies arise, continuous improvement involves conducting root cause analysis to identify the underlying reasons behind the problems. By addressing root causes, companies can implement more effective solutions to prevent recurrence.
- Kaizen Philosophy: Continuous improvement draws on the Kaizen philosophy, which emphasizes making small, incremental changes to achieve continuous and sustainable improvements. These small improvements add up over time and lead to significant gains in production efficiency and shorter lead times.
- Employee Involvement: Continuous improvement encourages employee involvement and empowerment. By seeking input from the workforce, companies can tap into the collective knowledge and experience of their employees, leading to innovative ideas and practical solutions for improvement.
- Benchmarking: Continuous improvement involves benchmarking performance against industry best practices or internal standards. By comparing performance to benchmarks, companies can identify performance gaps and set realistic improvement targets.
- Experimentation and Pilot Projects: Continuous improvement encourages experimentation and pilot projects to test new ideas and process changes on a smaller scale before implementing them company-wide. This approach reduces the risk of disruptions and allows for fine-tuning before full implementation.
- Process Optimization: Continuous improvement focuses on optimizing processes at every stage of the production cycle. This includes identifying bottlenecks, eliminating waste, improving workflow, and enhancing resource utilization, all of which contribute to reduced lead times.
- Technology Adoption: Embracing new technologies and process innovations is an essential aspect of continuous improvement. By adopting advanced technologies, companies can automate repetitive tasks, enhance data analysis, and achieve higher levels of efficiency.
- Feedback Loop: Continuous improvement establishes a feedback loop where insights and lessons learned from previous improvements inform future initiatives. This iterative process allows for ongoing refinements and ensures that improvements are sustained over time.
- Performance Review and Recognition: Continuous improvement includes recognition and celebration of achievements. Recognizing employees' contributions to process improvements motivates them to continue seeking innovative solutions and actively participating in the improvement process.
In summary, continuous improvement is a dynamic and integral part of production scheduling that drives companies to strive for excellence in their production processes.
By continuously identifying opportunities for improvement, implementing changes, and refining strategies based on data and feedback, companies can achieve shorter lead times, greater operational efficiency, and a competitive edge in the market.
Does Production Scheduling Prioritize High-Priority Orders During Peak Demand Periods?
Yes, production scheduling prioritizes high-priority orders during peak demand periods. When customer demands surge or during periods of increased urgency, production scheduling ensures that high-priority orders receive preferential treatment to meet delivery deadlines and maintain customer satisfaction.
Prioritizing high-priority orders during peak demand periods is a key strategy to optimize resource utilization and reduce lead times.
Here's how production scheduling achieves this:
- Order Prioritization: Production scheduling involves assigning priority levels to different customer orders based on their urgency and importance. High-priority orders are identified and treated as top priorities in the production schedule.
- Dynamic Scheduling: During peak demand periods, production schedules are adjusted dynamically to accommodate high-priority orders. This may involve reallocating resources, expediting production processes, or resequencing tasks to ensure timely completion of critical orders.
- Resource Allocation: Production scheduling optimizes resource allocation to support high-priority orders. Resources such as machines, skilled labor, and materials are strategically assigned to expedite the production of urgent orders.
- Shorter Lead Times: Prioritizing high-priority orders translates into shorter lead times for these specific orders. Production scheduling ensures that the necessary resources are available and that the production process operates at maximum efficiency to meet tight delivery schedules.
- Minimized Waiting Times: By prioritizing high-priority orders, production scheduling reduces waiting times and idle periods in the production process. This minimizes delays and ensures a smooth and continuous production flow.
- Real-Time Monitoring: Production scheduling involves real-time monitoring of production activities. This enables managers to identify potential delays or issues that may affect high-priority orders and allows for immediate adjustments to maintain timely production.
- Collaboration with Sales and Customer Service: Production scheduling involves close collaboration with sales and customer service teams. This ensures that production schedules align with the latest customer demands and any changes in order priorities during peak demand periods.
- Contingency Planning: During peak demand periods, production scheduling incorporates contingency planning to address unexpected events or disruptions. This proactive approach helps mitigate risks and ensures that high-priority orders are completed on time.
- Effective Communication: Efficient communication among production teams, managers, and stakeholders is essential during peak demand periods. Production scheduling ensures that everyone is aware of the high-priority orders and the urgency of meeting delivery commitments.
In conclusion, production scheduling places a significant emphasis on prioritizing high-priority orders during peak demand periods. By dynamically adjusting schedules, optimizing resource allocation, and expediting production processes, production scheduling helps companies meet customer expectations, reduce lead times, and maintain a competitive edge in the market during critical business periods.
Can Production Scheduling Enhance On-Time Delivery Performance?
Yes, production scheduling can significantly enhance on-time delivery performance. On-time delivery refers to the ability of a company to fulfill customer orders and deliver products within the promised time frame.
Production scheduling plays a pivotal role in achieving on-time delivery by optimizing production processes, resource allocation, and coordination with the supply chain.
Here's how production scheduling enhances on-time delivery performance:
- Efficient Production Planning: Production scheduling creates well-structured and optimized production plans. By sequencing tasks and managing resources effectively, ensures that production processes run smoothly and minimize lead times, leading to on-time completion of orders.
- Real-Time Monitoring and Adjustments: With real-time monitoring, production scheduling enables managers to track progress and identify potential delays or bottlenecks promptly. This allows for timely adjustments to the production schedule to ensure on-time delivery.
- Sequencing of High-Priority Orders: Production scheduling prioritizes high-priority orders and schedules them for immediate production. By aligning production schedules with customer demands, companies can meet urgent delivery requirements and achieve on-time delivery.
- Supply Chain Coordination: Production scheduling involves coordination with suppliers to ensure timely material deliveries. By synchronizing production with the supply chain, companies can avoid delays caused by material shortages and maintain on-time delivery performance.
- Reduced Lead Times: Through optimization of production processes, resource utilization, and workflow, production scheduling helps reduce lead times. Shorter lead times enable companies to complete production faster, leading to improved on-time delivery performance.
- Contingency Planning: Production scheduling includes contingency planning to address unforeseen events or disruptions that may impact production. Having backup plans in place helps companies mitigate risks and maintain on-time delivery even in challenging situations.
- Effective Communication and Collaboration: Production scheduling promotes effective communication and collaboration among teams involved in the production process. Clear communication ensures that everyone is aware of production schedules and delivery commitments, facilitating on-time performance.
- Customer-Centric Focus: By aligning production schedules with customer demands, production scheduling ensures a customer-centric approach. Meeting delivery deadlines becomes a top priority, enhancing customer satisfaction and loyalty.
- Lean and Continuous Improvement Initiatives: Production scheduling incorporates lean manufacturing principles and continuous improvement initiatives. By eliminating waste, optimizing processes, and enhancing efficiency, on-time delivery performance is enhanced.
- Meeting Peak Demand Periods: During peak demand periods, production scheduling adjusts schedules to handle increased production requirements. By optimizing resource allocation and planning for higher production volumes, companies can fulfill orders on time.
In conclusion, production scheduling plays a vital role in enhancing on-time delivery performance. By optimizing production processes, managing resources efficiently, and coordinating with the supply chain, production scheduling ensures that orders are completed and delivered on time, leading to improved customer satisfaction, loyalty, and a competitive edge in the market.
Is Production Scheduling Suitable for Both Small and Large-Scale Manufacturing Businesses?
Yes, production scheduling is suitable for both small and large-scale manufacturing businesses. It is a versatile and fundamental practice that can be tailored to the specific needs and scale of any manufacturing operation.
Whether a company produces small batches of custom-made products or operates on a large-scale mass production model, production scheduling plays a critical role in optimizing efficiency, reducing lead times, and enhancing overall operational performance.
Here's how production scheduling is relevant and beneficial for both small and large-scale manufacturing businesses:
For Small-Scale Manufacturing Businesses:
- Resource Optimization: Production scheduling helps small-scale manufacturers make the most of limited resources, such as machinery, labor, and materials. By efficiently allocating resources, these businesses can increase productivity and reduce production costs.
- Flexible Production Planning: Small-scale manufacturers often face frequent changes in customer demands and product specifications. Production scheduling allows for flexible production planning, enabling companies to adapt quickly to varying order sizes and product requirements.
- Shorter Lead Times: With production scheduling, small-scale manufacturers can streamline their production processes and reduce lead times. This enhances customer satisfaction and competitiveness in the market.
- Improved Order Fulfillment: By aligning production schedules with customer orders, small-scale manufacturers can ensure timely order fulfillment, leading to satisfied customers and repeat business.
- Lower Inventory Costs: Production scheduling helps small businesses maintain optimal inventory levels, preventing excess stockpiling and minimizing storage costs.
For Large-Scale Manufacturing Businesses:
- Efficient Resource Utilization: Large-scale manufacturers handle a higher volume of production, making resource optimization crucial. Production scheduling maximizes the efficiency of production lines, ensuring that resources are used effectively.
- Complex Production Sequencing: Large-scale manufacturers often deal with intricate production sequences involving multiple products and assembly lines. Production scheduling optimizes these sequences to reduce downtime and improve overall production flow.
- Continuous Improvement: With large-scale operations, even small efficiency gains can have significant impacts. Production scheduling fosters a culture of continuous improvement, leading to incremental enhancements and higher overall productivity.
- Synchronized Supply Chain: As large-scale manufacturers often have extensive supply chains, production scheduling helps synchronize production with suppliers, ensuring timely material deliveries and avoiding production delays.
- Economies of Scale: Production scheduling allows large-scale manufacturers to leverage economies of scale more effectively, optimizing production volume to achieve cost efficiencies.
In conclusion, production scheduling is a valuable tool for both small and large-scale manufacturing businesses. It adapts to the unique requirements of each operation, helping companies of all sizes optimize their production processes, reduce lead times, and enhance operational efficiency.
Whether producing custom-made products or mass-produced items, the implementation of production scheduling can lead to increased competitiveness, improved customer satisfaction, and better overall business performance.
Can Production Scheduling Accommodate Varying Batch Sizes Efficiently?
Yes, production scheduling can accommodate varying batch sizes efficiently. The flexibility to handle different batch sizes is a crucial aspect of production scheduling, especially in industries where customer demands can vary significantly or in make-to-order manufacturing scenarios.
Here's how production scheduling accommodates varying batch sizes efficiently:
- Dynamic Resource Allocation: Production scheduling optimizes the allocation of resources based on the batch size requirements. Depending on the batch size, the scheduling algorithm adjusts the assignment of machines, labor, and materials to ensure efficient utilization without overburdening resources.
- Batch-Level Planning: Production scheduling considers the specific requirements of each batch when creating production plans. For larger batches, longer production runs might be more feasible, while smaller batches may require more frequent changeovers to accommodate varying product specifications.
- Sequencing Flexibility: Production scheduling allows for flexible sequencing of tasks based on batch sizes. Smaller batches can be prioritized to minimize lead times and meet urgent customer demands, while larger batches can be scheduled for optimization of resource utilization.
- Minimizing Changeover Times: For industries where frequent changeovers are necessary due to varying batch sizes, production scheduling aims to minimize changeover times. Techniques such as quick changeover methodologies and efficient setup procedures are employed to reduce downtime between production runs.
- Lean Manufacturing Principles: Production scheduling often incorporates lean manufacturing principles, such as one-piece flow or small batch production, to optimize production efficiency and reduce work-in-progress (WIP) inventory for varying batch sizes.
- Just-in-Time (JIT) Principles: JIT principles are integrated into production scheduling to match production with customer demand. Smaller batches, in line with JIT principles, enable companies to produce what is needed when it is needed, reducing excess inventory and lead times.
- Resource Capacity Planning: Production scheduling considers the available capacity of resources, such as machines and labor, to ensure that the scheduled batch sizes align with the capabilities of the production system. This prevents resource overload and avoids production delays.
- Advanced Planning and Scheduling Software: The use of advanced planning and scheduling software allows companies to model and simulate different batch scenarios. This enables them to identify the most efficient and cost-effective ways to produce varying batch sizes.
- Order Sequencing: Production scheduling optimizes the sequencing of customer orders with varying batch sizes to minimize setup and changeover times. Similar orders may be grouped together to reduce downtime between production runs.
In summary, production scheduling is designed to be adaptable and can efficiently accommodate varying batch sizes. By leveraging dynamic resource allocation, sequencing flexibility, lean manufacturing principles, and advanced planning software, companies can optimize their production processes and reduce lead times, regardless of the batch size requirements.
Can Production Scheduling Help Reduce Variability in Lead Times?
Yes, production scheduling can help reduce variability in lead times. Variability in lead times refers to the inconsistency or fluctuations in the time taken to complete a production process or fulfill customer orders. Production scheduling addresses various factors that contribute to lead time variability, leading to more consistent and predictable lead times.
Here's how production scheduling achieves this:
- Optimized Resource Allocation: Production scheduling ensures efficient allocation of resources, such as machines, labor, and materials, based on production requirements and capacities. This optimization minimizes resource-related bottlenecks and reduces variations in lead times caused by resource constraints.
- Sequencing and Prioritization: By sequencing tasks and prioritizing orders effectively, production scheduling minimizes waiting times and prioritizes critical orders. This reduces the impact of order delays on lead times and ensures a smoother production flow.
- Streamlined Production Flow: Production scheduling aims to streamline the production process, eliminating non-value-added activities and reducing production inefficiencies. This results in a more consistent and predictable workflow, reducing variations in lead times.
- Real-Time Monitoring and Adjustment: With real-time monitoring of production activities, production scheduling allows for swift adjustments to address issues as they arise. By resolving problems promptly, lead time variability is minimized.
- Continuous Improvement Culture: Production scheduling fosters a culture of continuous improvement, encouraging companies to identify and address the root causes of lead time variability. Ongoing improvements lead to a more stable and predictable production process.
- Accurate Demand Forecasting: Production scheduling incorporates accurate demand forecasting, helping companies anticipate customer requirements. Better predictions of demand lead to more precise production planning and reduced lead time fluctuations.
- Supplier Collaboration: Smoother supply chain integration, facilitated by production scheduling, enables companies to collaborate closely with suppliers. This collaboration ensures timely material deliveries, minimizing variations in lead times due to supply chain disruptions.
- Lean Principles and Waste Reduction: Production scheduling often incorporates lean manufacturing principles, which aim to reduce waste and inefficiencies in the production process. By eliminating waste, companies can achieve more consistent and predictable lead times.
- Standardization of Processes: Standardizing production processes and work procedures helps maintain consistency in output and reduces lead time variability resulting from inconsistent work practices.
- Reduction of Rework and Errors: Production scheduling focuses on reducing errors and rework through quality control measures. By preventing defects and rework, companies can maintain more stable lead times.
In conclusion, production scheduling plays a significant role in reducing variability in lead times.
By optimizing resource allocation, streamlining production flow, implementing continuous improvements, and maintaining accurate demand forecasts, production scheduling creates a more stable and predictable production process, resulting in consistent and reliable lead times.
Ultimately, this contributes to improved customer satisfaction and a competitive advantage in the market.
What Role Does Technology Play in Production Scheduling for Lead Time Reduction?
Technology plays a crucial role in production scheduling for lead time reduction. It empowers companies to optimize their production processes, enhance operational efficiency, and respond swiftly to changing demands.
Here are some key roles that technology plays in production scheduling for lead time reduction:
- Real-Time Data and Monitoring: Technology enables the collection and analysis of real-time data on production activities, machine performance, and resource utilization. This data provides valuable insights for better decision-making and enables managers to monitor production progress in real-time, identifying potential bottlenecks or inefficiencies promptly.
- Advanced Planning and Scheduling (APS) Software: APS software solutions use algorithms and optimization techniques to create efficient production schedules. These tools consider various factors, such as production capacity, material availability, and order priorities, to generate optimized schedules that minimize lead times.
- Automation and Robotics: Automation and robotics streamline repetitive tasks, reducing human intervention and potential errors. By automating certain production processes, companies can achieve faster and more consistent task completion, contributing to shorter lead times.
- Internet of Things (IoT) Devices: IoT devices integrated into production equipment provide real-time data on machine performance, health, and maintenance needs. Predictive maintenance through IoT technology helps prevent unexpected breakdowns, minimizing downtime and lead time delays.
- Simulation and Digital Twin Technology: Simulation tools and digital twins allow companies to model and test different production scenarios virtually. By simulating various production schedules and processes, companies can identify the most efficient and effective strategies for lead time reduction.
- Supply Chain Integration: Technology facilitates seamless integration with suppliers, enabling real-time communication and data exchange. With improved supply chain visibility, companies can optimize material procurement, reduce inventory levels, and respond swiftly to supply chain disruptions, all of which contribute to shorter lead times.
- Cloud-Based Collaboration: Cloud-based platforms enable real-time collaboration among production teams, regardless of their physical locations. Teams can share production schedules, track progress, and coordinate tasks more efficiently, leading to streamlined production flow and reduced lead times.
- Artificial Intelligence (AI) and Machine Learning: AI and machine learning algorithms analyze historical production data to identify patterns and trends. By leveraging AI insights, companies can make data-driven decisions to optimize production processes, reduce errors, and further shorten lead times.
- Demand Forecasting and Predictive Analytics: Advanced forecasting tools use historical data and market trends to predict future demand accurately. Accurate demand forecasting helps companies plan production more effectively, avoiding overproduction or stockouts and reducing lead times.
- Mobile and Communication Technologies: Mobile apps and communication tools facilitate real-time communication among teams and stakeholders. Instant communication helps resolve production issues quickly and facilitates smooth coordination, leading to faster response times and reduced lead times.
In conclusion, technology plays a transformative role in production scheduling for lead time reduction. By leveraging real-time data, automation, predictive capabilities, and advanced planning software, companies can optimize their production processes, minimize delays, and achieve shorter lead times, ultimately enhancing customer satisfaction and competitive advantage in the market.
How Can Deskera Help You with Production Scheduling?
Deskera MRP is an integrated software solution designed to help businesses manage their manufacturing processes, including production scheduling.
Here's how Deskera MRP can assist you with production scheduling:
- Resource Planning: Deskera MRP enables you to efficiently plan and allocate resources for your production schedule. You can define the availability and capacity of your resources, such as labor, machinery, and equipment, and schedule tasks accordingly. This helps in optimizing resource utilization and balancing workloads.
- Production Order Management: With Deskera MRP, you can easily create and manage production orders. You can define the bill of materials (BOM) and set up routing for each order, specifying the sequence of operations and dependencies. This allows you to schedule and track the progress of production orders, ensuring timely execution.
- Real-Time Visibility: Deskera MRP provides real-time visibility into your production schedule. You can monitor the status of production orders, track work in progress (WIP), and identify bottlenecks or potential delays. This visibility enables you to make informed decisions and take proactive actions to optimize your production scheduling.
- Capacity Planning: Deskera MRP helps you plan and manage production capacity effectively. You can evaluate resource availability, track utilization rates, and forecast capacity requirements based on production demand. This enables you to align your capacity with the production schedule and avoid overloading resources or creating bottlenecks.
- Demand Planning and Forecasting: Deskera MRP incorporates demand planning and forecasting capabilities. By analyzing historical data and market trends, you can accurately forecast future demand. This information can be used to adjust production schedules, allocate resources, and ensure that you meet customer requirements on time.
- Collaboration and Communication: Deskera MRP facilitates collaboration and communication among stakeholders involved in production scheduling. You can share real-time updates, task assignments, and production-related information with your team members, suppliers, and other relevant parties. This streamlines communication reduces errors, and enhances coordination.
- Reporting and Analytics: Deskera MRP provides robust reporting and analytics features. You can generate various reports related to production scheduling, such as resource utilization, lead times, production efficiency, and capacity analysis. These insights help in monitoring performance, identifying areas for improvement, and making data-driven decisions.
Key Takeaways
Production scheduling plays a pivotal role in reducing lead times and enhancing overall operational efficiency for businesses. The ways in which production scheduling helps in reducing lead time are:
- Efficient Resource Allocation: Production scheduling helps allocate resources, such as labor, machines, and materials, optimally. By ensuring that the right resources are available at the right time, it minimizes idle time and reduces delays between production stages, leading to shorter lead times.
- Minimizing Setup and Changeover Times: Scheduling allows for careful planning of production runs to minimize setup and changeover times between different products or batches. Quick transitions between tasks reduce downtime and increase production throughput, ultimately reducing lead time.
- Streamlined Production Flow: A well-designed production schedule sequences tasks logically and eliminates unnecessary waiting periods. This smooth flow of production processes ensures that work moves efficiently through the system, decreasing overall lead time.
- Real-Time Monitoring and Adjustment: Production schedules can be monitored in real-time, allowing managers to identify potential bottlenecks or delays early on. This proactive approach enables timely adjustments to avoid lead time disruptions.
- Effective Order Sequencing: By prioritizing and sequencing customer orders based on deadlines and requirements, production scheduling ensures that critical orders are processed first. This way, lead times for high-priority orders are minimized.
- Improved Workforce Efficiency: Scheduling provides clarity to workers about their tasks and deadlines, reducing idle time and promoting better time management. This, in turn, leads to increased workforce productivity and shorter lead times.
- Faster Response to Changes in Demand: With production scheduling in place, businesses can adjust their production plans more quickly when demand fluctuates. This agility helps prevent delays and shortages, contributing to reduced lead times.
- Smoother Supply Chain Integration: Production schedules can be integrated with suppliers' schedules, enabling timely delivery of raw materials and components. A well-coordinated supply chain ensures smoother production processes and shorter lead times.
- Reduced Rework and Errors: Accurate production scheduling minimizes the likelihood of errors and rework, which can cause delays and increase lead times. When tasks are carefully planned, mistakes are less likely to occur, leading to quicker production cycles.
- Continuous Improvement: Production scheduling provides valuable data for analyzing production performance. By identifying inefficiencies and areas for improvement, companies can continuously refine their processes to further reduce lead times over time.
In the dynamic and competitive business environment, the power of production scheduling becomes evident as companies strive to stay agile, responsive, and customer-focused. Embracing production scheduling as a fundamental practice empowers businesses to meet customer demands promptly, optimize resource usage, and gain a competitive edge in the market.
In conclusion, production scheduling is a potent tool that unlocks the potential for companies to achieve shorter lead times, increased productivity, and sustained success. By integrating production scheduling into their operations, businesses can create a more efficient and streamlined production process, ultimately resulting in enhanced customer satisfaction and business growth.
Overall, Deskera MRP serves as a comprehensive solution for managing production scheduling. It helps streamline your manufacturing processes, optimize resource utilization, improve visibility, and enhance overall efficiency. By leveraging its features, you can effectively plan and execute your production schedule while minimizing bottlenecks and ensuring timely order fulfillment.
Related Articles
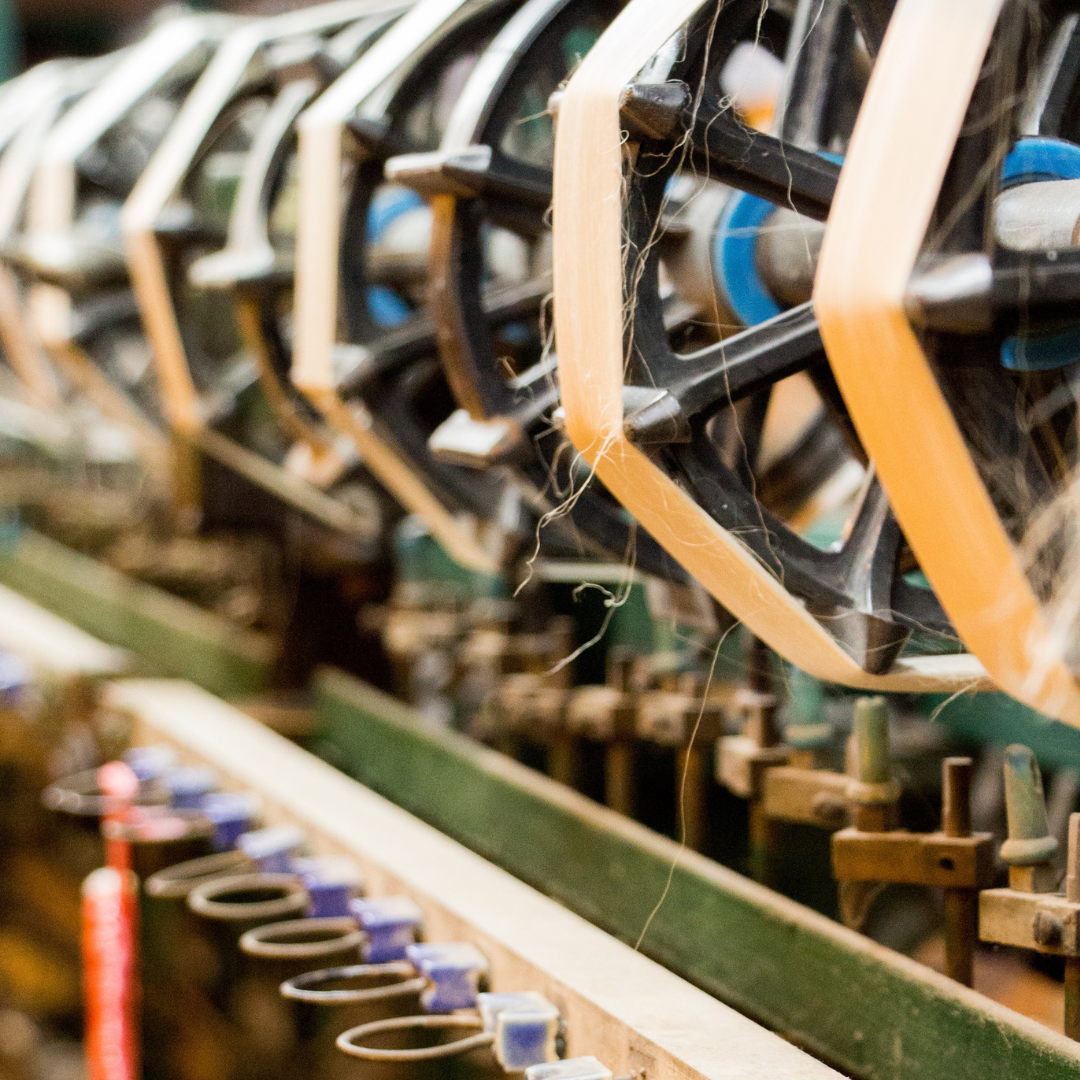
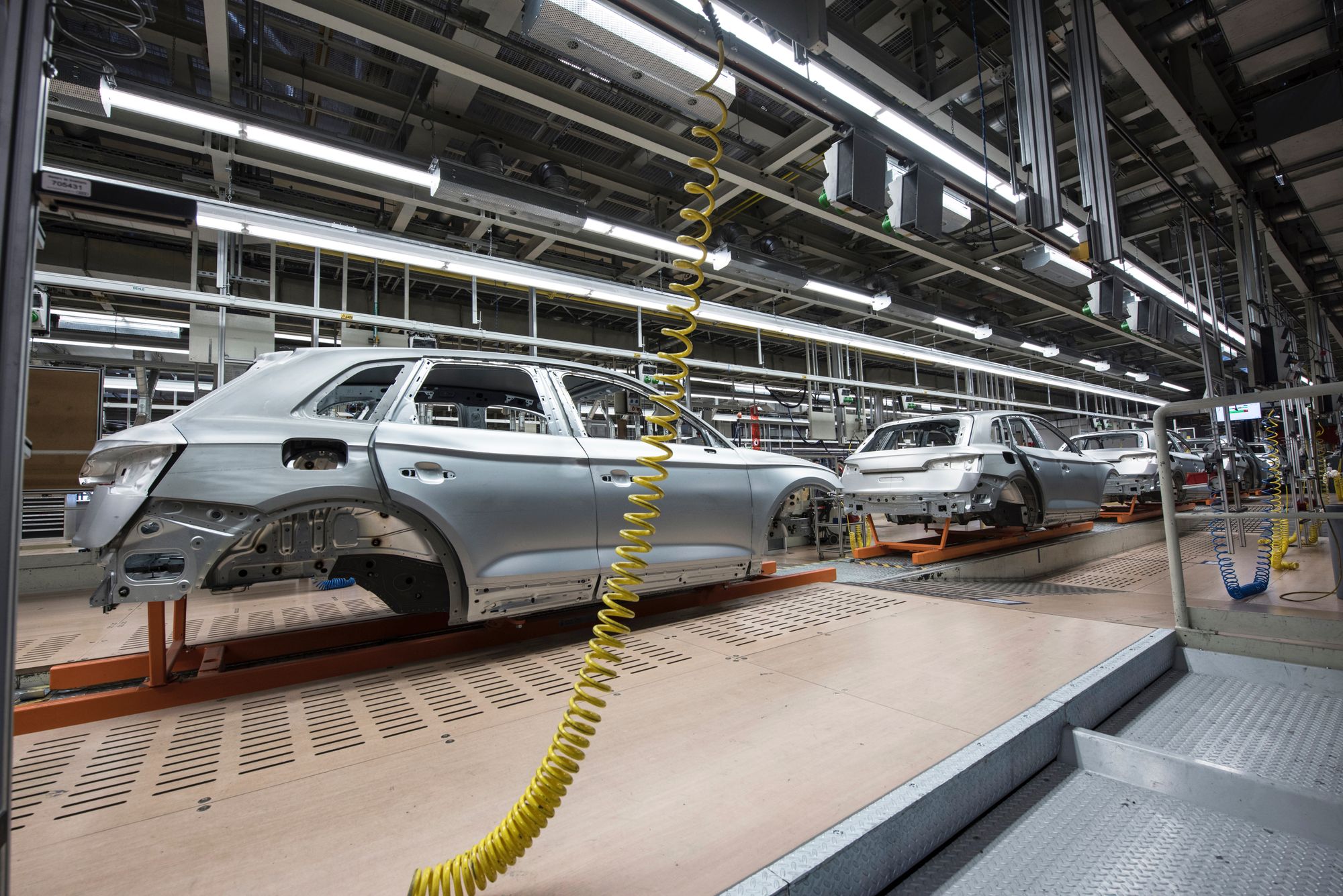
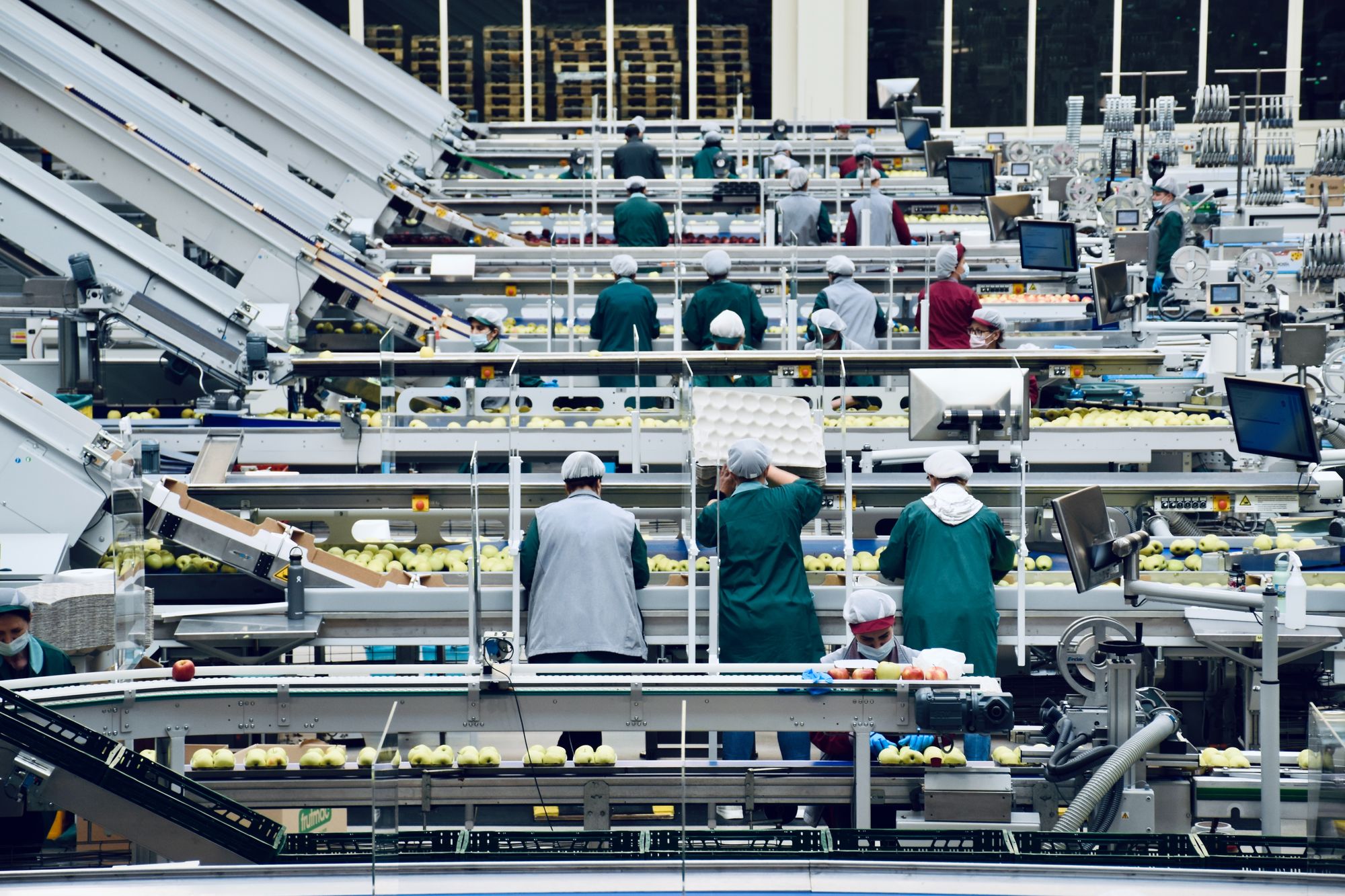
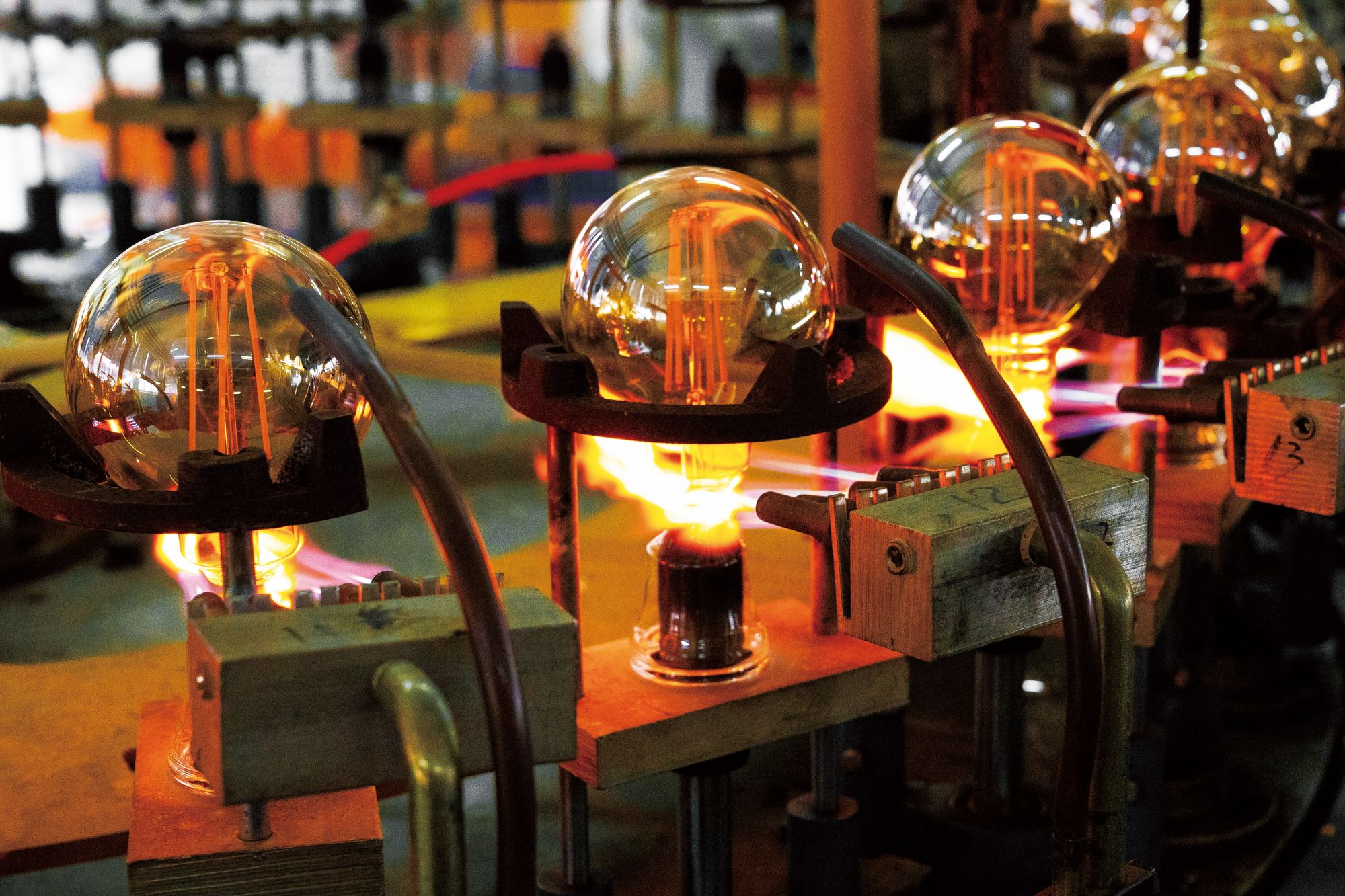
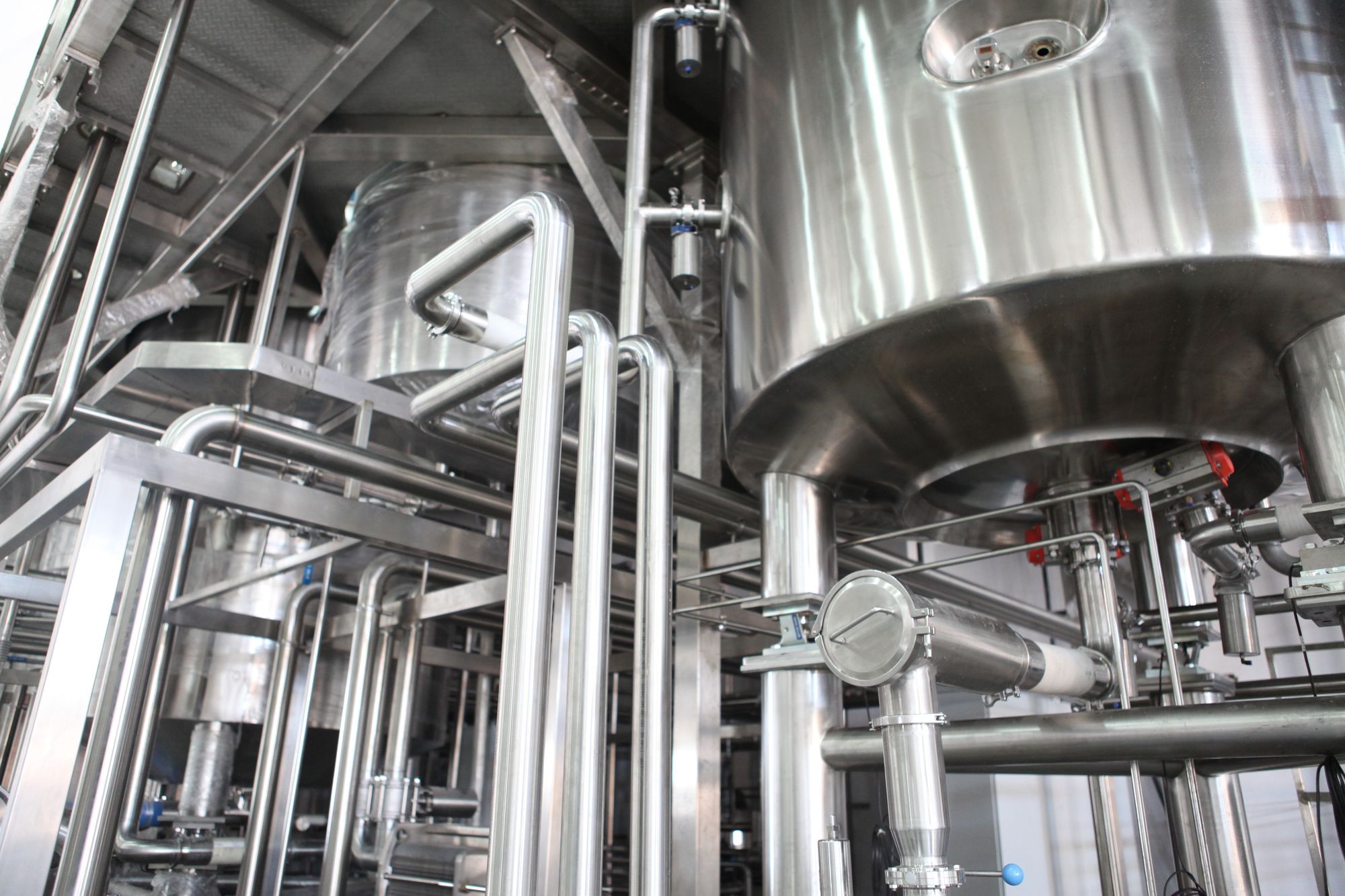
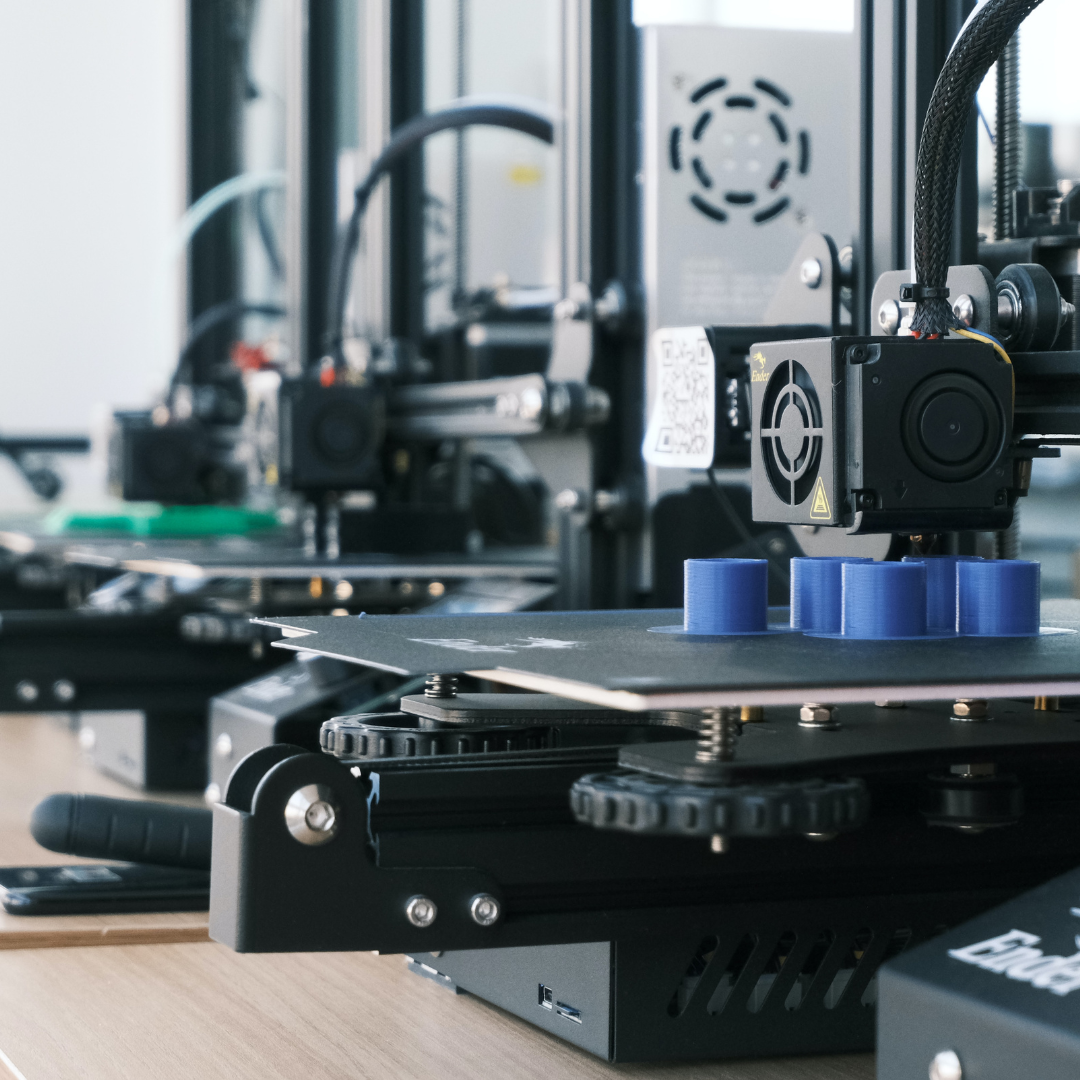