Plastics are ubiquitous in our daily lives and have revolutionized modern manufacturing. From packaging and consumer goods to transportation and construction, plastics offer unique properties such as durability, flexibility, and lightweight that make them ideal for a wide range of applications.
However, not all plastics are created equal, and the manufacturing process used to produce them can significantly impact their properties and applications.
Understanding the different types of plastic and manufacturing processes is essential for making informed decisions about their use and disposal. This article provides an overview of the most common types of plastic and manufacturing processes, their advantages and disadvantages, and their applications.
It also explores sustainability and environmental concerns associated with plastic manufacturing and waste management, as well as emerging trends in eco-friendly plastics and recycling.
To stay competitive and sustainable, manufacturers are increasingly turning to ERP.AI to automate workflows, optimize resource use, and gain real-time visibility across the entire production lifecycle.
Meaning of Plastic Manufacturing
Plastics manufacturing is the process of creating plastic products by transforming raw plastic materials into finished products. It involves several stages of production, from designing and engineering the product, to molding, shaping, and assembling it. The raw materials used in plastic manufacturing typically include polymers, resins, and additives.
The process of plastics manufacturing varies depending on the type of plastic being used and the intended product. The most common types of plastic used in manufacturing include thermoplastics, thermosetting plastics, elastomers, and biodegradable plastics. Each type of plastic has its own unique properties and requires specific manufacturing processes to achieve the desired product.
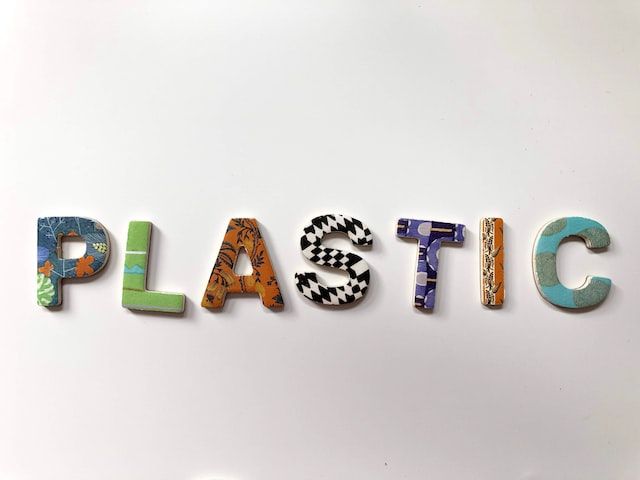
Plastics manufacturing also involves a variety of manufacturing processes, including injection molding, blow molding, extrusion, rotational molding, and thermoforming. These processes vary in complexity and are chosen based on the type of plastic being used and the desired product specifications.
The use of plastics in manufacturing has become increasingly important in modern society due to its versatility, durability, and cost-effectiveness. Plastics can be used in a wide range of products, from packaging materials to medical devices to automotive components.
However, plastic manufacturing also poses significant environmental challenges, such as plastic waste and pollution. To address these challenges, the industry is working to develop more sustainable and eco-friendly manufacturing practices, such as recycling and upcycling, and the use of biodegradable plastics.
Importance of Plastics in our Daily Lives
Plastics are an essential part of our daily lives and are used in countless products that we rely on. Here are some of the reasons why plastics are important:
Durability:
Plastics are durable and long-lasting, which makes them ideal for use in products that need to withstand wear and tear, such as car parts, construction materials, and packaging.
Versatility:
Plastics can be molded and shaped into a wide range of products, from everyday items like water bottles and food containers to specialized products like medical devices and electronic components.
Lightweight:
Plastics are lightweight, which makes them ideal for use in products that need to be easily transportable, such as packaging materials.
Cost-effective:
Plastics are often less expensive than alternative materials, making them an affordable choice for many products.
Safety:
Plastics are safe and hygienic, making them ideal for use in products that come into contact with food, such as food packaging and kitchenware.
Sustainability:
Plastics can be recycled and reused, which makes them a more sustainable choice than single-use materials like paper and cardboard.
Overall, plastics play an important role in our daily lives and have many benefits that make them essential for a wide range of products. However, it's important to address the environmental challenges associated with plastic use and work towards more sustainable manufacturing and disposal practices.
Different Types of Plastic Manufacturing
There are four main types of plastic used in manufacturing, each with its own unique properties and manufacturing processes. These types of plastics are:
Thermoplastics:
Thermoplastics are a type of plastic that can be melted and re-molded repeatedly without undergoing significant chemical changes. Examples of thermoplastics include polyethylene, polypropylene, polystyrene, and PVC.
The manufacturing process for thermoplastics involves melting the plastic material and injecting it into a mold, which is then cooled to solidify the product.
Thermosetting Plastics:
Thermosetting plastics are a type of plastic that undergoes a chemical change when heated and cannot be re-melted or re-molded. Examples of thermosetting plastics include epoxy, phenolic, and melamine.
Further, the manufacturing process for thermosetting plastics involves heating the plastic material in a mold until it undergoes a chemical reaction and hardens.
Biodegradable Plastics:
Biodegradable plastics are a type of plastic that can be broken down by natural processes over time. Examples of biodegradable plastics include polylactic acid (PLA) and polyhydroxyalkanoates (PHA).
The manufacturing process for biodegradable plastics is similar to that of traditional plastics, but the materials used are biodegradable and compostable.
Elastomers:
Elastomers are a type of plastic that can stretch and return to their original shape. Examples of elastomers include rubber, silicone, and polyurethane. The manufacturing process for elastomers involves mixing the plastic material with a curing agent and then heating and molding the mixture into the desired shape.
Each type of plastic requires specific manufacturing processes to achieve the desired product, and there are several manufacturing processes used in plastics manufacturing, including injection molding, blow molding, extrusion, rotational molding, and thermoforming.
Furthermore, the choice of manufacturing process depends on the type of plastic being used and the desired product specifications.
Plastic Manufacturing Process
There are several manufacturing processes used in plastics manufacturing, each with its own advantages and limitations. The most common manufacturing processes for plastics include:
Injection Molding:
Injection molding is a process used for thermoplastics and thermosetting plastics. The process involves melting the plastic material and injecting it into a mold under high pressure.
Further, the mold is then cooled, and the plastic part is ejected from the mold. Injection molding is ideal for producing large quantities of identical parts with high precision and low waste.
Blow Molding:
Blow molding is a process used for creating hollow plastic parts, such as bottles and containers. The process involves melting the plastic material and blowing it into a mold, where it takes on the shape of the mold. The mold is then cooled, and the plastic part is removed from the mold. Blow molding is a cost-effective process for producing large quantities of hollow plastic parts.
Extrusion:
Extrusion is a process used for creating long continuous pieces of plastic with a consistent cross-section. The process involves melting the plastic material and forcing it through a die, which shapes the plastic into a specific shape. Extrusion is ideal for creating plastic tubing, pipes, and sheets.
Rotational Molding:
Rotational molding is a process used for creating large, hollow plastic parts, such as tanks and playground equipment. The process involves heating a mold and rotating it around two perpendicular axes.
Further, the plastic material is then introduced into the mold, where it melts and adheres to the mold's surface. The mold is then cooled, and the plastic part is removed from the mold.
Thermoforming:
Thermoforming is a process used for creating thin, shallow plastic parts, such as packaging trays and lids. The process involves heating a sheet of plastic until it becomes pliable, then forming it over a mold using vacuum pressure or mechanical force. The plastic part is then cooled and removed from the mold.
Let’s study each of them in detail:
(A) Injection Molding
Injection molding is a manufacturing process used to create parts from both thermoplastics and thermosetting plastics. The process involves several steps, which include:
- Material Selection:
The first step in injection molding is selecting the appropriate plastic material for the product being produced. The plastic material is typically supplied in the form of pellets, which are loaded into the injection molding machine's hopper.
- Melting and Injection:
The plastic pellets are then melted in the machine's barrel and forced into the mold cavity through a screw or ram under high pressure. The mold is typically made up of two halves that are clamped together during the injection process.
- Cooling and Solidification:
Once the plastic has been injected into the mold, it is allowed to cool and solidify in the mold cavity. The cooling time is determined by the thickness of the plastic part, the material being used, and the temperature of the mold.
- Ejection:
Once the plastic part has solidified, the mold is opened, and the part is ejected from the mold using ejector pins.
- Post-Processing:
After ejection, the part may require additional post-processing, such as trimming excess plastic or adding finishing touches.
Injection molding is a versatile process that can be used to produce complex shapes and geometries with high precision and consistency.
Moreover, the process can be automated for efficient production, making it ideal for producing large quantities of identical parts. However, the initial cost of tooling can be high, and the process may not be suitable for producing large, bulky parts.
Advantages and Disadvantages of Injection Molding
Injection molding is a widely used manufacturing process for producing plastic parts. Like any manufacturing process, it has its advantages and disadvantages. Here are some of the pros and cons of injection molding:
Advantages:
- High Precision and Consistency: Injection molding can produce highly precise and consistent parts with minimal variations between individual parts.
- Efficiency: The process can be automated, making it highly efficient for producing large quantities of identical parts.
- Versatility: Injection molding can be used to produce a wide range of shapes and geometries, from small intricate parts to larger, more complex parts.
- Cost-effective: Injection molding can be a cost-effective manufacturing process, especially for high-volume production runs.
Disadvantages:
- High Initial Cost: The initial cost of tooling and equipment for injection molding can be high, making it less feasible for small-scale production runs.
- Limited Material Selection: Injection molding is best suited for producing parts from thermoplastics and thermosetting plastics, limiting the choice of materials that can be used.
- Long Lead Times: Designing and creating molds for injection molding can be a time-consuming process, resulting in longer lead times for product development and production.
- Limited Part Size: Injection molding may not be suitable for producing large, bulky parts due to limitations in mold size and machine capacity.
Applications of Injection Molding
Following, we've discussed some crucial applications of rotational molding. Some common applications of injection molding include:
- Packaging: Injection molding is often used to produce plastic packaging for a variety of products, including food, beverages, cosmetics, and household cleaning products. The process can produce custom shapes and sizes that meet specific packaging requirements.
- Automotive: Injection molding is commonly used in the automotive industry to produce components such as interior trims, dashboards, and bumpers. The process offers design flexibility and cost-effectiveness for large production runs.
- Medical Devices: Injection molding is used to produce medical device components such as syringes, vials, and connectors. The process can produce custom shapes and sizes that meet specific requirements for sterilization and functionality.
- Consumer Goods: Injection molding is used to produce a variety of consumer goods, including toys, kitchenware, and electronic housings. The process can produce custom shapes and sizes with specific color and texture requirements.
- Electronics: Injection molding is used to produce a variety of electronic components, including cases, covers, and housings for phones, computers, and other devices. The process can produce custom shapes and sizes with specific features such as screw bosses and snap fits.
- Aerospace: Injection molding is used to produce lightweight components for aircraft, such as ducting and air distribution systems. The process offers design flexibility and cost-effectiveness for large production runs.
(B) Blow Molding
Blow molding is a manufacturing process used to create hollow plastic parts, such as bottles, containers, and tanks. The process involves several steps, which include:
- Material Selection:
The first step in blow molding is selecting the appropriate plastic material for the product being produced. The plastic material is typically supplied in the form of pellets, which are loaded into the blow molding machine's hopper.
- Extrusion and Parison Formation:
The plastic pellets are melted in the machine's extruder and then extruded as a hollow tube called a parison. The size and shape of the parison are determined by the shape of the mold.
- Blow Molding:
The parison is then placed in a mold cavity, which is then closed and clamped shut. Compressed air is blown into the parison, causing it to expand and conform to the shape of the mold. The plastic is cooled and solidified in the mold.
- Ejection:
Once the plastic part has solidified, the mold is opened, and the part is ejected from the mold using ejector pins.
- Trimming and Finishing:
After ejection, the part may require additional trimming to remove excess plastic or any flash that may have formed during the blow molding process. The part may also require additional finishing touches, such as printing or labeling.
Blow molding is a versatile process that can be used to produce a wide range of shapes and sizes of hollow plastic parts. The process can be automated for efficient production, making it ideal for producing large quantities of identical parts. However, the process may not be suitable for producing solid parts or parts with complex geometries.
Advantages and Disadvantages of Blow Molding
Blow molding is a widely used manufacturing process for producing hollow plastic parts, such as bottles, containers, and tanks. Like any manufacturing process, it has its advantages and disadvantages. Here are some of the pros and cons of blow molding:
Advantages:
- Versatility: Blow molding can be used to produce a wide range of shapes and sizes of hollow plastic parts.
- Efficiency: The process can be automated, making it highly efficient for producing large quantities of identical parts.
- Strength and Durability: Blow-molded parts are generally strong, durable, and resistant to impact and environmental factors.
- Cost-effective: Blow molding can be a cost-effective manufacturing process, especially for high-volume production runs.
Disadvantages:
- Limited Material Selection: Blow molding is best suited for producing parts from certain types of plastic materials, limiting the choice of materials that can be used.
- Limited Part Design: The process may not be suitable for producing parts with complex geometries or thick walls.
- Long Lead Times: Designing and creating molds for blow molding can be a time-consuming process, resulting in longer lead times for product development and production.
- Additional Post-Processing: Blow-molded parts may require additional post-processing, such as trimming and finishing, which can add to the overall cost of production.
Applications of Blow Molding
Blow molding has a wide range of applications across many industries due to its versatility and ability to produce complex shapes. Some common applications of blow molding include:
- Packaging: Blow molding is often used to produce plastic bottles, containers, and jars for a variety of products, including food, beverages, cosmetics, and household cleaning products. The process can produce custom shapes and sizes that meet specific packaging requirements.
- Automotive: Blow molding is commonly used in the automotive industry to produce components such as fuel tanks, air ducts, and intake manifolds. The process offers design flexibility and cost-effectiveness for large production runs.
- Medical Devices: Blow molding is used to produce medical device components such as IV bags, fluid containers, and respiratory therapy devices. The process can produce custom shapes and sizes that meet specific requirements for sterilization and functionality.
- Consumer Goods: Blow molding is used to produce a variety of consumer goods, including toys, sporting goods, and outdoor equipment. The process can produce custom shapes and sizes with specific color and texture requirements.
- Industrial: Blow molding is used to produce industrial components such as drums, tanks, and containers for chemicals, oils, and other fluids. The process can produce large-scale products with high durability and strength.
- Aerospace: Blow molding is used to produce lightweight components for aircraft, such as ducting and air distribution systems. The process offers design flexibility and cost-effectiveness for large production runs.
(C) Extrusion
Extrusion is a manufacturing process used to create plastic products with a constant cross-section, such as pipes, tubes, and sheeting. The process involves several steps, which include:
Material Selection:
The first step in extrusion is selecting the appropriate plastic material for the product being produced. The plastic material is typically supplied in the form of pellets or powder, which are loaded into the extruder's hopper.
Melting and Mixing:
The plastic material is melted and mixed in the extruder's barrel using a combination of heat and mechanical action. The molten plastic is then forced through a die, which shapes the plastic into a continuous profile.
Cooling and Sizing:
As the plastic exits the die, it is cooled using a cooling bath or air stream to solidify the plastic. The plastic may also be sized or shaped using additional equipment, such as pullers or cutters.
Co-Extrusion (Optional):
In some cases, multiple layers of plastic may be extruded simultaneously using a co-extrusion process. This allows for the creation of products with different properties or colors.
Finishing:
Once the extruded product has been cooled and sized, it may require additional finishing touches, such as printing, cutting, or punching.
With a uniform cross-section, a variety of plastic goods can be made using the flexible method of extrusion. The method is perfect for generating several similar parts in big quantities since it can be automated for effective production. The method might not work well for creating complex geometries or designs that call for different wall thicknesses.
Advantages and Disadvantages of Extrusion
Extrusion is a widely used manufacturing process for producing plastic products with a constant cross-section, such as pipes, tubes, and sheeting. Like any manufacturing process, it has its advantages and disadvantages. Here are some of the pros and cons of extrusion:
Advantages:
- Versatility: Extrusion can be used to produce a wide range of plastic products with a consistent cross-section.
- Efficiency: The process can be automated, making it highly efficient for producing large quantities of identical parts.
- Strength and Durability: Extruded products are generally strong, durable, and resistant to impact and environmental factors.
- Cost-effective: Extrusion can be a cost-effective manufacturing process, especially for high-volume production runs.
Disadvantages:
- Limited Design Capabilities: Extrusion is best suited for producing products with a constant cross-section, limiting the ability to create complex geometries or shapes with varying wall thicknesses.
- High Setup Costs: Designing and creating extrusion dies can be a costly process, resulting in higher setup costs compared to other manufacturing processes.
- Limited Material Selection: Extrusion is best suited for producing products from certain types of plastic materials, limiting the choice of materials that can be used.
- Poor Surface Finish: Extruded products may have a rough or uneven surface finish, which may require additional finishing processes.
Applications of Extrusion
Following, we've discussed some crucial applications of rotational molding. Following are a few of the frequent uses for extrusion:
- Pipes and Tubing: Extrusion is widely used to produce pipes and tubing for various applications, such as plumbing, irrigation, and medical devices.
- Packaging: Extrusion is used to produce plastic films and sheets for packaging applications, such as bags, pouches, and food containers.
- Construction: Extruded plastic profiles are used in construction applications, such as window frames, doors, and siding.
- Automotive: Extruded plastic parts are used in automotive applications, such as seals, gaskets, and interior trim.
- Electrical: Extruded plastic parts are used in electrical applications, such as cable insulation and conduit.
- Medical: Extrusion is used to produce medical devices, such as catheters and tubing for blood transfusion.
- Consumer Goods: Extrusion is used to produce a wide range of consumer goods, such as toys, sporting equipment, and household items.
(D) Rotational Molding
Rotational molding is a manufacturing process used to produce hollow plastic products with complex shapes and geometries. The process involves several steps, which include:
- Mold Preparation:
The first step in rotational molding is preparing the mold. The mold is typically made of aluminum or steel and consists of two or more parts that fit together to form a hollow cavity.
- Material Loading:
The plastic material, usually in the form of powder or pellets, is loaded into the mold cavity.
- Heating:
The mold is heated in an oven or a furnace, and it rotates simultaneously on two perpendicular axes. The heat melts the plastic, and the rotation of the mold ensures that the melted plastic coats the inside of the mold cavity evenly.
- Cooling:
After the plastic has coated the inside of the mold cavity, the mold is removed from the oven and cooled using fans or water. The cooling process solidifies the plastic and allows it to maintain its shape.
- Part Ejection:
Once the plastic has cooled and solidified, the mold is opened, and the part is ejected. The process is then repeated for the production of additional parts.
Moreover, rotational molding is a important manufacturing process that can be used to produce a wide range of hollow plastic products with complex shapes and geometries.
It is ideal for producing large parts with a relatively low production volume. It is also cost-effective and can produce high-quality parts with consistent wall thicknesses. However, it may not be suitable for producing parts with high precision or for producing small parts.
Advantages and Disadvantages of Rotational Molding
Rotational molding is a manufacturing process that has several advantages and disadvantages, including:
Advantages:
- Flexible: Rotational molding can be used to produce hollow plastic products with complex shapes and geometries, making it a versatile manufacturing process.
- Robust: The products produced through rotational molding are durable and can withstand impact and other environmental factors.
- Cost-effective: Rotational molding can be a cost-effective manufacturing process, especially for producing large, low-volume parts.
- Consistent Wall Thickness: The process ensures that the wall thickness of the product is consistent throughout, ensuring that the product's strength is uniform.
Disadvantages:
- Limited Precision: Rotational molding may not be suitable for producing parts with high precision or tight tolerances.
- Limited Material Selection: Rotational molding is best suited for producing parts from certain types of plastic materials, limiting the choice of materials that can be used.
- Long Cycle Time: The process can have a long cycle time, making it less suitable for high-volume production runs.
- Limited Surface Finish: The surface finish of the products produced through rotational molding may not be as smooth as those produced through other manufacturing processes, requiring additional finishing processes.
Applications of Rotational Molding
Following, we've discussed some crucial applications of rotational molding. Let's discuss:
- Playground Equipment: Rotational molding is used to produce playground equipment, such as slides, tunnels, and climbing structures. These products are durable, lightweight, and resistant to weather and UV radiation.
- Automotive Parts: Rotational molding is used to produce automotive parts, such as gas tanks, air ducts, and dashboards. These parts are lightweight, strong, and resistant to impact and environmental factors.
- Outdoor Furniture: Rotational molding is used to produce outdoor furniture, such as chairs, tables, and benches. These products are durable, lightweight, and resistant to weather and UV radiation.
- Medical Products: Rotational molding is used to produce medical products, such as hospital beds, wheelchair components, and prosthetic devices. These products can be produced in complex shapes and geometries that are difficult to achieve with other manufacturing processes.
- Sports Equipment: Rotational molding is used to produce sports equipment, such as kayaks, canoes, and helmets. These products are lightweight, strong, and resistant to impact and environmental factors.
(E) Thermoforming
Thermoforming is a manufacturing process that involves heating a thermoplastic sheet until it becomes pliable, then forming it over a mold, and finally cooling it to create a three-dimensional shape. The process can be broken down into the following steps:
- Sheet Preparation: A thermoplastic sheet, typically made of materials such as polystyrene, PVC, or PET, is loaded onto the thermoforming machine. The sheet is then heated to a temperature where it becomes pliable and can be molded.
- Mold Preparation: The mold for the desired product is created and installed onto the thermoforming machine. The mold can be made from materials such as aluminum, steel, or wood, and is typically created using CNC machining.
- Forming: Once the thermoplastic sheet is heated and pliable, it is then pulled over the mold by vacuum, pressure, or a combination of both. The sheet is then pressed onto the mold to create the desired shape. After forming, the excess plastic is trimmed away from the product.
- Cooling: The formed product is then cooled to its final shape, typically using either air- or water-cooling methods. Once cooled, the product is ejected from the mold.
- Finishing: The finished product may require additional finishing processes, such as trimming or drilling, to achieve the desired final appearance and functionality.
Thermoforming can be used to produce a variety of products, covering from packaging materials, food containers, automotive components, to medical devices. Moreover, the process is known for its speed, efficiency, and cost-effectiveness, making it a popular choice for producing large quantities of low-cost products.
Advantages and Disadvantages of Thermoforming
Thermoforming offers several advantages and disadvantages, which are important to consider when choosing the appropriate manufacturing process for a specific application.
Advantages:
Cost-Effective: Thermoforming is a cost-effective manufacturing process, especially for producing large quantities of parts. The process requires less initial investment in tooling compared to other manufacturing processes such as injection molding.
Flexible: Thermoforming is a versatile process that can be used to produce a wide range of products with different sizes, shapes, and thicknesses. The process can be used with a variety of materials, including polystyrene, PVC, PET, and polypropylene.
Short Lead Time: Thermoforming offers fast production times, as the process is typically quicker than other manufacturing processes like injection molding. This makes it a popular choice for projects with tight deadlines.
Customizable: Thermoforming offers a high degree of design flexibility, as it can produce complex shapes and features with relative ease. Customization of colors, textures, and finishes can also be done with relative ease.
Reduced Waste: Thermoforming has low scrap rates, and the process can use recycled materials, which is an eco-friendly alternative to other manufacturing processes.
Disadvantages:
- Limited Material Choice: Thermoforming is limited to using thermoplastics, which can be a disadvantage if a specific application requires different materials like metals, ceramics, or composites.
- Limited Precision: Thermoforming may not be suitable for applications that require high precision, as the process is subject to some degree of variability due to material shrinkage and warping.
- Limited Robustness: Thermoformed products may not be as durable as other manufacturing processes. Thermoformed products are more prone to cracking, chipping, and fading.
- Tooling Costs: Thermoforming requires a considerable initial investment in tooling, which can be a disadvantage for small production runs.
- Limited Design Features: Thermoforming has some limitations on the design features of products compared to other manufacturing processes, such as injection molding.
Applications of Thermoforming
Thermoforming has a wide range of applications across many industries due to its versatility and cost-effectiveness. Some common applications of thermoforming include:
- Packaging: Thermoforming is often used to produce packaging for a variety of products, including food, medical devices, and consumer goods. The process can produce custom shapes and sizes that protect products during shipping and handling.
- Automotive: Thermoforming is commonly used in the automotive industry to produce interior components such as door panels, instrument panels, and trim parts. The process offers design flexibility and cost-effectiveness for large production runs.
- Medical Devices: Thermoforming is used to produce medical device components such as trays, housings, and covers. The process can produce custom shapes and sizes that meet specific requirements for sterilization and functionality.
- Consumer Goods: Thermoforming is used to produce a variety of consumer goods, including toys, displays, and electronic enclosures. The process can produce custom shapes and sizes with specific color and texture requirements.
- Aerospace: Thermoforming is used to produce lightweight interior components for aircraft, such as overhead bins and seat components. The process offers design flexibility and cost-effectiveness for large production runs.
- Building and Construction: Thermoforming is used to produce building and construction components such as wall panels, window frames, and roofing materials. The process can produce custom shapes and sizes that meet specific design requirements.
Sustainability and Environmental Concerns
Plastics manufacturing processes have come under scrutiny due to their impact on the environment, particularly with regard to plastic waste and pollution.
As a result, there has been a growing interest in sustainability and reducing the environmental impact of plastic production. Many manufacturers are exploring ways to reduce waste and use more environmentally friendly materials, such as bioplastics, which are made from renewable resources and can biodegrade.
Additionally, there are efforts to improve recycling technologies and increase the use of recycled materials in manufacturing.
Moreover, there is a need to balance the benefits of plastics manufacturing with the environmental concerns, and many companies are working towards more sustainable practices in the industry.
Plastic Waste Management
Plastic waste management is the process of reducing, reusing, and recycling plastic products to minimize their environmental impact. Plastic waste can cause significant harm to the environment, including pollution of the air, water, and soil, as well as harm to wildlife and marine ecosystems.
One of the most effective ways to manage plastic waste is to reduce the amount of plastic used in the first place. This can be achieved through measures such as using reusable bags and containers, choosing products with less packaging, and avoiding single-use plastics like straws and utensils.
For the plastic that is still produced and used, recycling is a key component of waste management. Plastic recycling involves the collection, sorting, cleaning, and processing of plastic waste into new products.
Furthermore, this can help to reduce the amount of plastic that ends up in landfills or pollutes the environment. However, there are challenges with plastic recycling, including the cost and complexity of the process, and the fact that not all types of plastic are recyclable.
Another approach to plastic waste management is to develop new technologies and methods for the disposal of plastic waste. This includes techniques such as pyrolysis, which involves heating plastic waste to convert it into fuel or other chemicals, and biodegradation, which involves using microorganisms to break down plastic waste.
Ultimately, effective plastic waste management requires a combination of strategies, including reducing plastic use, increasing recycling rates, and developing new technologies for disposal. By implementing these measures, we can help to reduce the impact of plastic waste on the environment and create a more sustainable future.
Biodegradable and Eco-Friendly Plastics
Biodegradable and eco-friendly plastics are types of plastic that are designed to break down naturally in the environment, without causing harm or pollution. These plastics are typically made from renewable resources, such as plant-based materials like corn starch, potato starch, or sugarcane, rather than from fossil fuels.
Biodegradable plastics are designed to decompose through natural processes, such as exposure to sunlight, moisture, and microorganisms, into water, carbon dioxide, and organic matter. This makes them a more sustainable alternative to traditional plastics, which can persist in the environment for hundreds of years.
Eco-friendly plastics are designed to have a lower environmental impact throughout their lifecycle, from production to disposal. This can include using renewable energy sources, reducing greenhouse gas emissions, and promoting sustainable practices in the supply chain.
However, there are some challenges with biodegradable and eco-friendly plastics. For example, some biodegradable plastics require specific environmental conditions, such as high temperatures or humidity, to break down, which may not be present in all environments. Additionally, there are concerns about the impact of these plastics on food safety and the potential for them to contaminate recycling streams.
Moreover, biodegradable and eco-friendly plastics have the potential to help reduce the environmental impact of plastic production and use. However, there is a need for continued research and development to improve their effectiveness and ensure that they are a viable solution for addressing plastic waste and pollution.
Recycling and Upcycling
Recycling and upcycling are two approaches to managing waste and reducing the environmental impact of human activities.
Recycling involves taking waste materials, such as plastic, paper, glass, or metal, and processing them into new products. The process typically involves collecting and sorting the waste, cleaning and preparing it for processing, and then using it as raw material for new products.
Furthermore, recycling can help to reduce the amount of waste sent to landfills, conserve natural resources, and reduce the energy required for manufacturing new products.
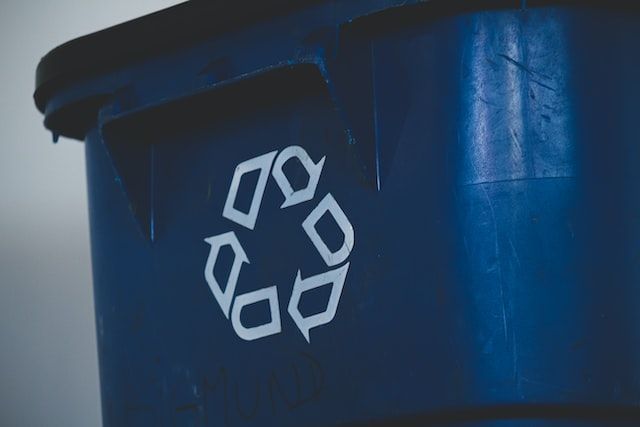
Upcycling, on the other hand, involves taking waste materials and transforming them into new products with a higher value or quality than the original. This can involve creative uses of materials, such as turning old clothing into a quilt or repurposing shipping containers into homes or offices.
Furthermore, upcycling can help to reduce waste and promote sustainability by extending the life of materials and reducing the need for new production.
Both recycling and upcycling have benefits and challenges. Recycling requires significant resources and energy to collect and process waste, and not all materials are easily recyclable.
Upcycling can require creativity and specialized skills and may not be a scalable solution for managing large volumes of waste. However, both approaches can help to promote a circular economy, where waste is minimized, resources are conserved, and materials are reused in innovative ways.
Overall, recycling and upcycling are important tools for managing waste and promoting sustainability. By finding new uses for materials and reducing the need for new production, we can reduce the environmental impact of our activities and create a more sustainable future.
Future of Plastic Manufacturing
The future of plastic manufacturing is likely to be shaped by several factors, including advancements in technology, sustainability concerns, and changing consumer preferences. Here are some potential trends and developments that could shape the future of plastic manufacturing in more detail:
Sustainable Materials:
As consumers and regulators continue to demand more sustainable products, the plastic manufacturing industry is likely to shift towards using more eco-friendly materials. This could include biodegradable plastics, recycled plastics, or plant-based plastics that can be produced without relying on fossil fuels.
Advances in material science and manufacturing techniques are likely to drive this shift, as companies work to develop materials that are both sustainable and cost-effective.
Additive Manufacturing:
Additive manufacturing, or 3D printing, has the potential to revolutionize the plastic manufacturing industry by enabling the production of complex parts with greater precision and efficiency. This could allow manufacturers to create customized products on demand, reducing waste and increasing production flexibility.
Digitalization:
As with many other industries, digitalization is likely to play a major role in the future of plastic manufacturing. This could involve the use of digital tools to design, simulate, and optimize manufacturing processes, as well as to monitor and control production in real-time.
Digital technologies could also be used to improve supply chain management, allowing companies to better track and optimize the flow of materials and products.
Circular Economy:
The concept of a circular economy, where waste is minimized and materials are continually reused or recycled, is likely to become more important in the plastic manufacturing industry. This could involve developing closed-loop supply chains, where materials are collected, recycled, and reused within the same production process.
In addition, advances in recycling technologies could enable the production of high-quality recycled plastics, reducing the need for virgin materials.
Regulations:
As concerns about plastic pollution continue to grow, governments and regulatory bodies are likely to introduce more stringent regulations on the use and disposal of plastics. This could include bans on certain types of plastics or packaging, as well as regulations on the production and disposal of plastic waste.
Companies that are able to adapt to these regulations and develop sustainable products and production processes are likely to be more successful in the long term.
How AI Is Revolutionizing Manufacturing
AI platforms help manufacturers automate repetitive tasks, streamline factory workflows, and reduce production time through intelligent process optimization. Predictive maintenance solutions anticipate equipment failures before they happen.
AI also supports workforce planning by aligning scheduling with real-time demand, and even assists in generative design, accelerating product development. By integrating AI across operations, manufacturers can cut costs, innovate faster, and bring products to market with greater speed and precision.
Frequently Asked Questions (FAQs) Associated with Plastic Manufacturing
Following, we’ve discussed some crucial frequently asked questions (FAQs) linked with plastics manufacturing. Let’s discuss:
Que 1: What are the most common types of plastic used in manufacturing?
Ans: The most common types of plastic used in manufacturing are polyethylene (PE), polypropylene (PP), polystyrene (PS), polyvinyl chloride (PVC), and polyethylene terephthalate (PET).
Que 2: What is the most common plastic manufacturing process?
Ans: Injection molding is the most common plastic manufacturing process.
Que 3: What is the difference between biodegradable and non-biodegradable plastics?
Ans: Biodegradable plastics are designed to break down naturally in the environment, while non-biodegradable plastics do not.
Que 4: How can I recycle plastic products?
Ans: Plastic products can be recycled by sorting them according to their recycling codes and placing them in recycling bins. They can also be taken to recycling centers or picked up by recycling services.
Que 5: Are biodegradable plastics a sustainable solution to plastic waste?
Ans: Biodegradable plastics have the potential to reduce the environmental impact of plastic waste, but their effectiveness depends on specific environmental conditions and their impact on recycling streams is still being studied.
Que 6: How can I reduce my plastic waste?
Ans: You can reduce your plastic waste by using reusable products, avoiding single-use plastics, recycling, and choosing products made from sustainable materials.
Que 7: What are the environmental impacts of plastic manufacturing?
Ans: The environmental impacts of plastic manufacturing include greenhouse gas emissions, water pollution, and negative impacts on wildlife and ecosystems.
Que 8: What is the circular economy and how does it relate to plastic manufacturing?
Ans: The circular economy is a model of production and consumption where waste is minimized, resources are conserved, and materials are reused in innovative ways. Plastic manufacturing can be part of a circular economy by using recycled materials and designing products for durability and recyclability.
Wrapping Up
In conclusion, plastics are an integral part of our daily lives, and plastic manufacturing processes play a crucial role in their production. Each manufacturing process has its advantages and disadvantages, and their applications vary according to the characteristics of the plastic produced.
However, the environmental impact of plastic waste cannot be ignored, and it is crucial to address sustainability concerns through proper waste management, recycling, and the development of biodegradable and eco-friendly plastics.
As the world seeks to transition to a circular economy, plastic manufacturing processes must evolve to minimize waste, conserve resources, and reuse materials in innovative ways.
Overall, the future of plastics manufacturing lies in sustainable practices that balance the needs of society, the economy, and the environment.
How Deskera Can Assist You?
Deskera's integrated financial planning tools allow investors to better plan their investments and track their progress. It can help investors make decisions faster and more accurately.
Deskera Books enables you to manage your accounts and finances more effectively. Maintain sound accounting practices by automating accounting operations such as billing, invoicing, and payment processing.
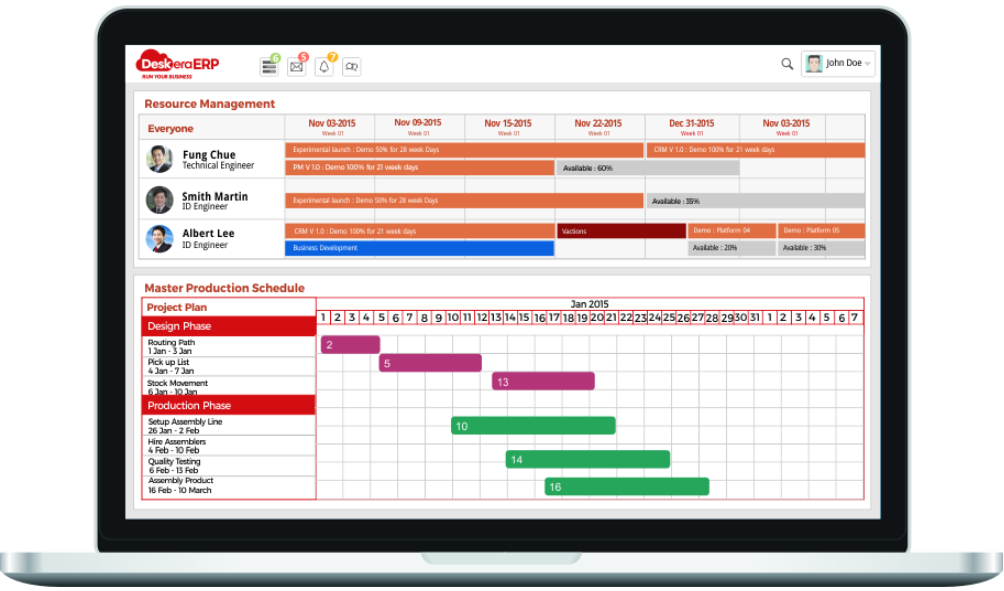
Deskera CRM is a strong solution that manages your sales and assists you in closing agreements quickly. It not only allows you to do critical duties such as lead generation via email, but it also provides you with a comprehensive view of your sales funnel.
Deskera People is a simple tool for taking control of your human resource management functions. The technology not only speeds up payroll processing but also allows you to manage all other activities such as overtime, benefits, bonuses, training programs, and much more. This is your chance to grow your business, increase earnings, and improve the efficiency of the entire production process.
Final Takeaways
We've arrived at the last section of this guide. Let's have a look at some of the most important points to remember:
- Plastics manufacturing is the process of creating plastic products by transforming raw plastic materials into finished products. It involves several stages of production, from designing and engineering the product, to molding, shaping, and assembling it.
- Biodegradable plastics are a type of plastic that can be broken down by natural processes over time. Examples of biodegradable plastics include polylactic acid (PLA) and polyhydroxyalkanoates (PHA).
- The first step in injection molding is selecting the appropriate plastic material for the product being produced. The plastic material is typically supplied in the form of pellets, which are loaded into the injection molding machine's hopper.
- Blow molding is often used to produce plastic bottles, containers, and jars for a variety of products, including food, beverages, cosmetics, and household cleaning products. The process can produce custom shapes and sizes that meet specific packaging requirements.
- Thermoforming can be used to produce a variety of products, including packaging materials, food containers, automotive components, and medical devices. The process is known for its speed, efficiency, and cost-effectiveness, making it a popular choice for producing large quantities of low-cost products.
- Plastic waste management is the process of reducing, reusing, and recycling plastic products to minimize their environmental impact. Plastic waste can cause significant harm to the environment, including pollution of the air, water, and soil, as well as harm to wildlife and marine ecosystems.
- Recycling involves taking waste materials, such as plastic, paper, glass, or metal, and processing them into new products. The process typically involves collecting and sorting the waste, cleaning and preparing it for processing, and then using it as raw material for new products. It can help to reduce the amount of waste sent to landfills, conserve natural resources, and reduce the energy required for manufacturing new products.
Related Articles
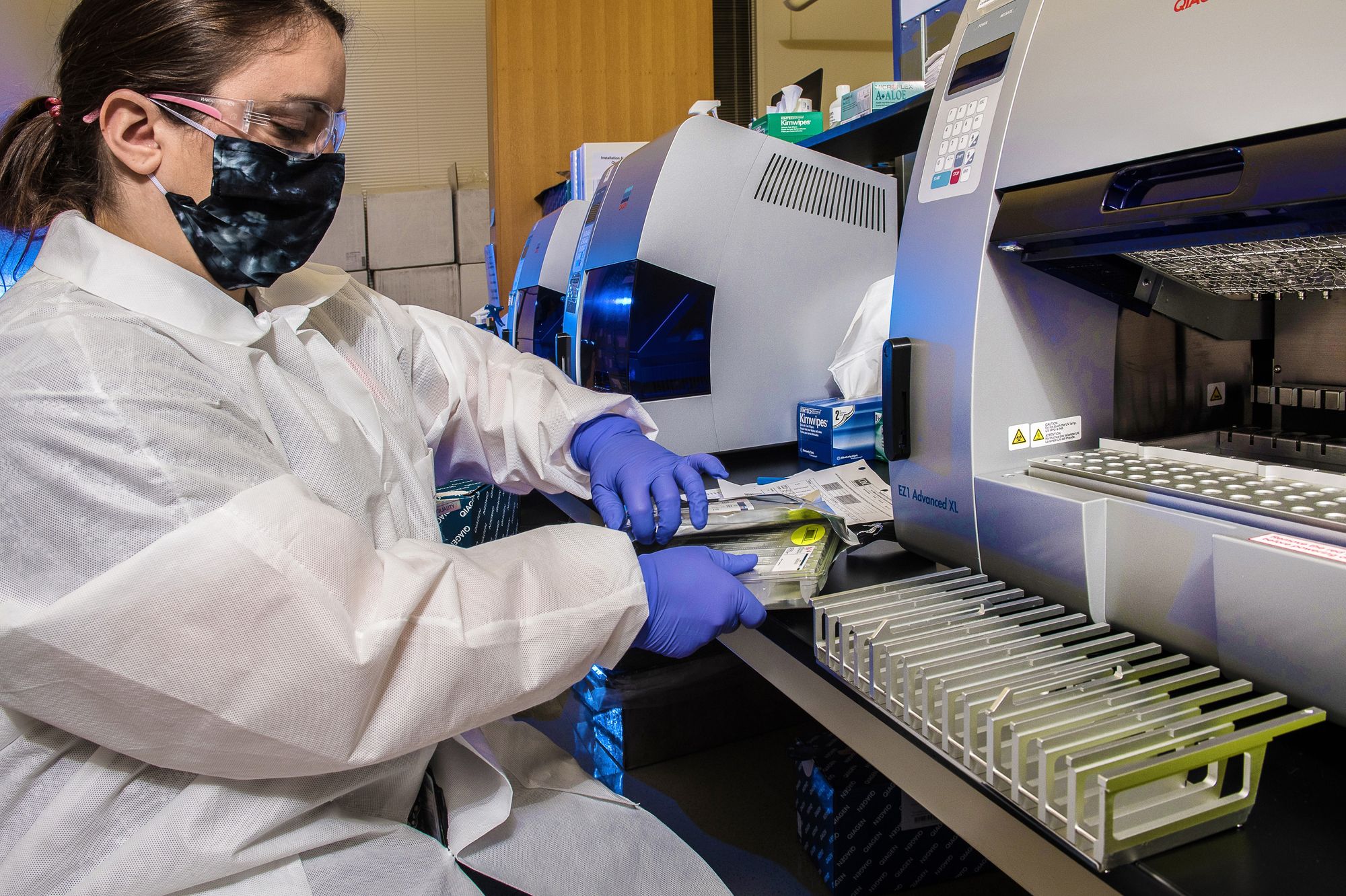
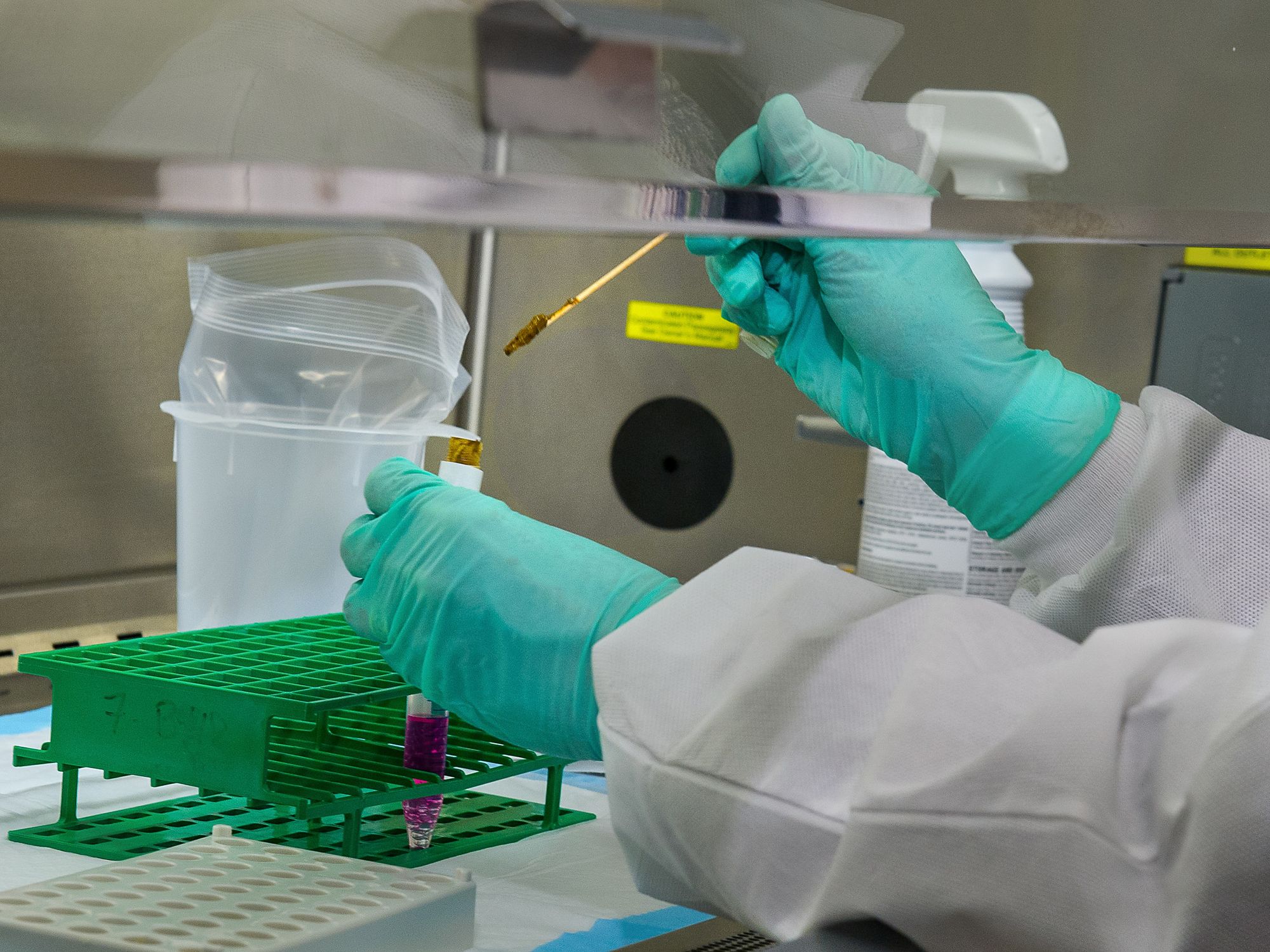
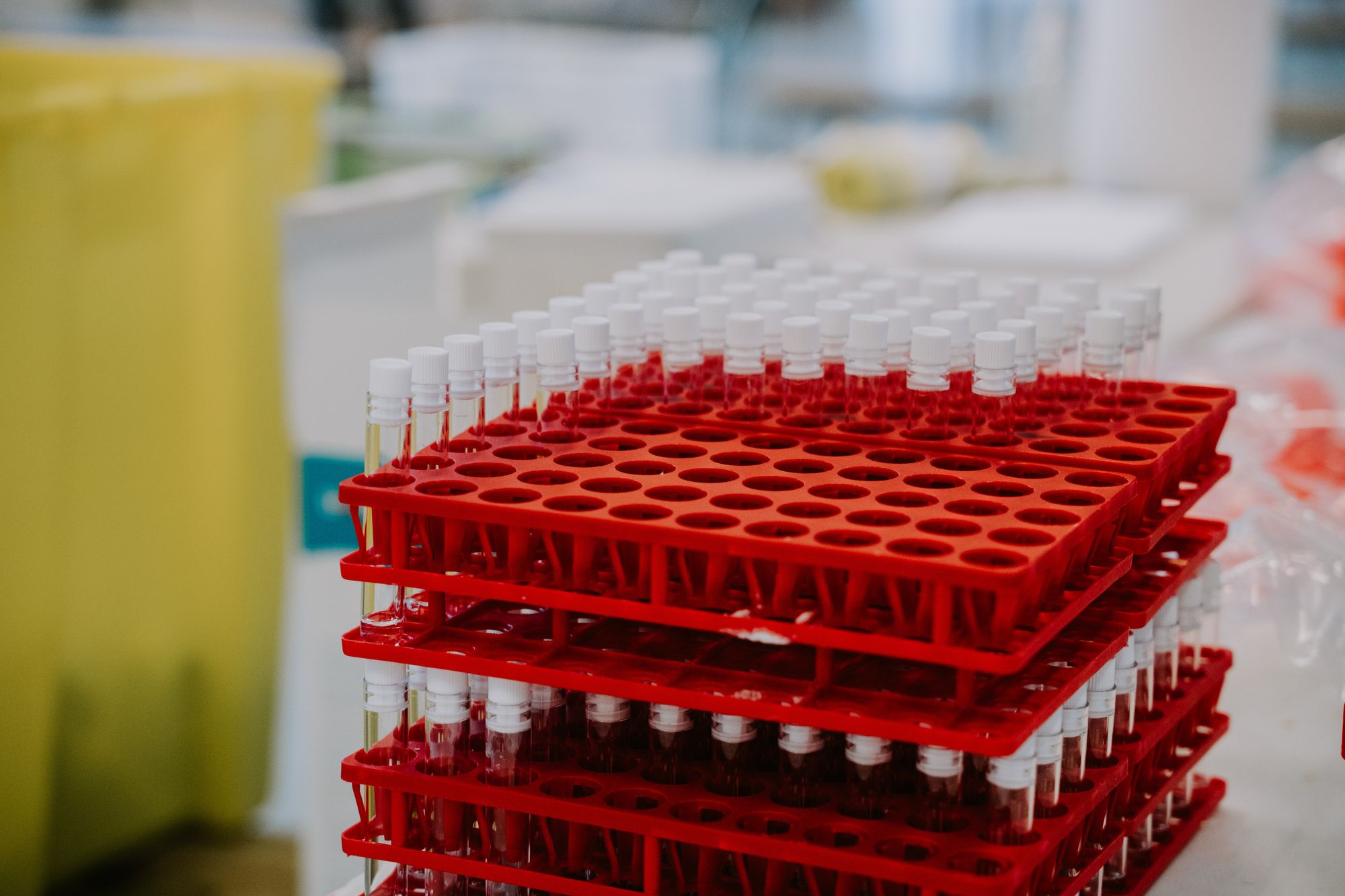
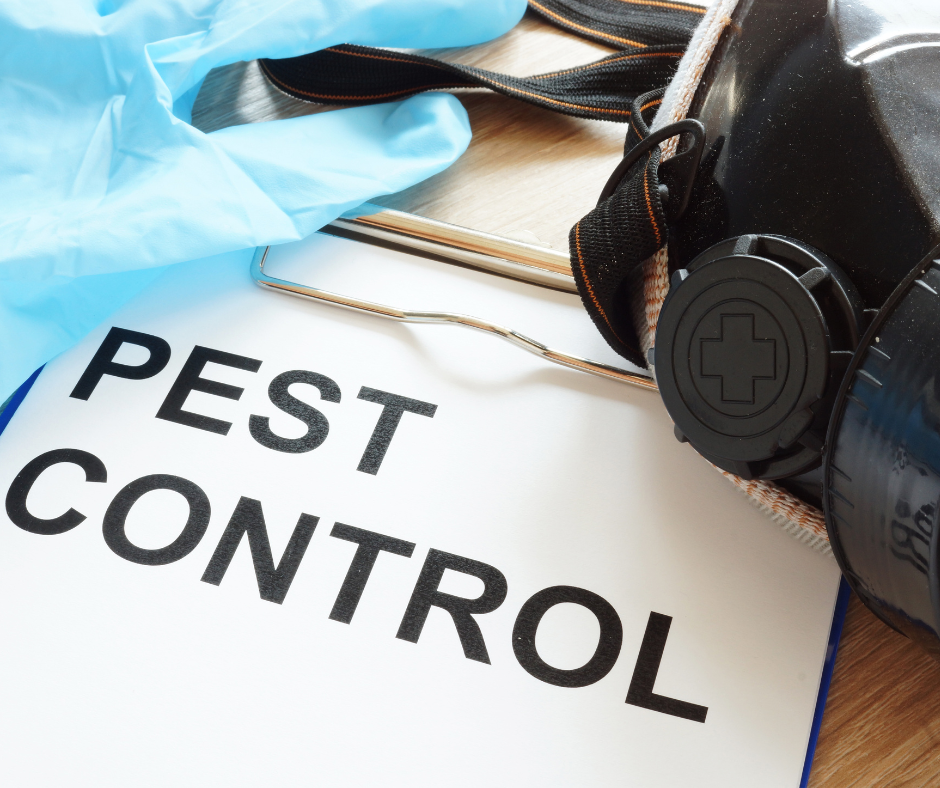
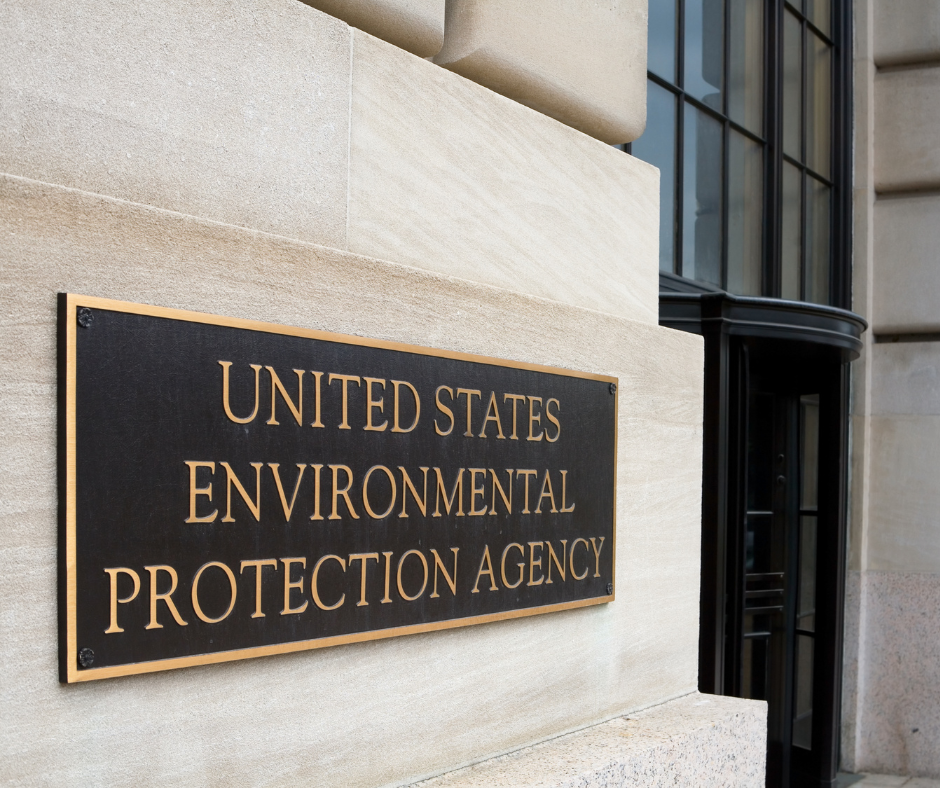