How well does plastic manufacturing work? Is it effective at reducing environmental impact? Are the benefits worth the costs?
Plastic is versatile and durable. It has many applications, such as packaging, clothing, toys, furniture and more. Plastics can have a large environmental impact if they are not produced correctly. When plastics are made properly, they can have a smaller environmental impact.
There are several ways to measure the effectiveness of plastic manufacturing. In this guide, we’ll cover everything associated with measuring effectiveness of plastic manufacturing. Let’s take a look at the table of content:
- Importance of Measuring Effectiveness in Plastic Manufacturing
- 1. KPI for Plastic Manufacturing
- 2. Factors Affecting Effectiveness in Plastic Manufacturing
- 3. Implementing a Measurement System
- 4. Tools and Software Available for Tracking and Analyzing KPIs
- 5. Benchmarking and Continuous Improvement
- 6. Case Studies
- Wrapping Up
- How Deskera Can Assist You?
Let's get started!
Importance of Measuring Effectiveness in Plastic Manufacturing
Plastic manufacturing is a highly competitive and constantly evolving industry, and measuring effectiveness is crucial for businesses that want to remain competitive and profitable.
Measuring effectiveness involves tracking key performance indicators (KPIs) and benchmarking against industry standards to identify areas for improvement and make data-driven decisions.
One of the main benefits of measuring effectiveness is that it helps businesses optimize their operations and reduce waste. By tracking KPIs such as production volume, waste reduction, and quality control, businesses can identify inefficiencies in their processes and make adjustments to improve their bottom line.
For example, measuring the amount of plastic waste generated during production can help businesses identify opportunities to reduce waste and save money on raw materials.
Measuring effectiveness also helps businesses meet customer demands and comply with industry regulations. With increasing concerns over environmental sustainability, customers are looking for businesses that prioritize sustainable manufacturing practices.
Furthermore, measuring KPIs such as energy consumption and carbon emissions can help businesses reduce their environmental footprint and meet industry standards for sustainability.
Furthermore, measuring effectiveness helps businesses make data-driven decisions and set realistic goals for growth. By benchmarking against industry standards and analyzing their KPIs, businesses can identify areas for improvement and set achievable targets for growth. This allows businesses to make informed decisions about investments in new technologies and equipment that can improve efficiency and competitiveness.
Finally, measuring effectiveness helps businesses stay competitive in a rapidly evolving industry. As new technologies and materials emerge, businesses must be able to adapt quickly and efficiently to remain competitive. Measuring effectiveness can help businesses identify opportunities for innovation and stay ahead of the curve in terms of new products, processes, and materials.
In summary, measuring effectiveness is crucial for businesses in the plastic manufacturing industry that want to remain competitive and profitable. By tracking KPIs, benchmarking against industry standards, and making data-driven decisions, businesses can optimize their operations, reduce waste, meet customer demands, comply with industry regulations, set realistic goals for growth, and stay competitive in a rapidly evolving industry.
1. KPI for Plastic Manufacturing
Key Performance Indicators (KPIs) are measurements that are used to track and assess the performance of a business or organization. In the context of plastic manufacturing, KPIs are used to measure the effectiveness of manufacturing processes and identify areas for improvement.
Some common KPIs for plastic manufacturing include production volume, quality control, energy consumption, and waste reduction.
By tracking these KPIs, businesses can make data-driven decisions to optimize their operations, reduce waste, and meet customer demands. KPIs are a vital tool for businesses in the plastic manufacturing industry to stay competitive and profitable.
KPIs for Plastic Manufacturing
KPIs for plastic manufacturing are measurements used to assess the performance of manufacturing processes in terms of quality, efficiency, and profitability. These KPIs vary depending on the goals and objectives of the business, but some common KPIs include:
Production Volume: This KPI measures the number of plastic products produced within a specific time frame. It is a crucial metric for measuring the efficiency of production processes and identifying opportunities for increasing output.
Quality Control: This KPI measures the quality of the finished product by tracking defects, errors, and customer complaints. It helps businesses identify areas for improvement in the production process and ensure customer satisfaction.
Energy Consumption: This KPI measures the amount of energy used in the manufacturing process. By tracking energy consumption, businesses can identify opportunities for reducing energy usage and increasing efficiency.
Waste Reduction: This KPI measures the amount of waste generated during the manufacturing process. It is important for businesses to track this metric as it helps identify areas where waste can be reduced, leading to cost savings and increased sustainability.
Machine Utilization: This KPI measures the amount of time machines are utilized during the manufacturing process. By tracking machine utilization, businesses can identify opportunities for increasing productivity and reducing downtime.
Overall, KPIs are important for measuring the effectiveness of plastic manufacturing processes and identifying opportunities for improvement. By tracking these metrics, businesses can make data-driven decisions to optimize their operations and stay competitive in the industry.
Example of KPIs Used in Plastic Manufacturing
Here are some examples of KPIs commonly used in plastic manufacturing:
Total Unit Cost: Total unit cost is one of the key performance indicators (KPIs) that can be used to measure the effectiveness of plastic manufacturing. This KPI measures the total cost of producing a single unit of plastic product, including direct costs such as raw materials, labor, and overhead costs such as equipment maintenance and utilities.
By tracking total unit cost, plastic manufacturers can identify areas where costs can be reduced, such as optimizing production processes, reducing waste, and increasing efficiency. This KPI can also help manufacturers make informed decisions about pricing and profitability.
In addition to total unit cost, other KPIs such as production volume, waste reduction, and quality control can also be used to measure the effectiveness of plastic manufacturing. By tracking these KPIs and continuously improving processes, plastic manufacturers can achieve significant improvements in their operations and contribute to a more sustainable future.
Production Volume: This KPI measures the number of plastic products produced in a specific time period, such as daily, weekly, or monthly. The production volume is important for measuring the efficiency of manufacturing processes and identifying opportunities for increasing output.
Waste Reduction: This KPI measures the amount of waste generated during the manufacturing process, such as scrap or defective products. Waste reduction is crucial for improving sustainability, reducing costs, and improving overall efficiency.
Quality Control: This KPI measures the quality of the finished product by tracking defects, errors, and customer complaints. Quality control is important for ensuring customer satisfaction and maintaining a good reputation in the industry.
Downtime: This KPI measures the amount of time machines or equipment are not operational due to maintenance, repairs, or other issues. Downtime is a crucial metric for measuring efficiency and identifying opportunities for improving machine utilization and productivity.
Energy Consumption: This KPI measures the amount of energy used in the manufacturing process. By tracking energy consumption, businesses can identify opportunities for reducing energy usage and increasing efficiency.
Customer Satisfaction: This KPI measures customer satisfaction with the finished product. It is important for businesses to track this metric as it helps identify areas for improvement in the production process and ensures customer loyalty.
Furthermore, these KPIs are crucial for measuring the effectiveness of plastic manufacturing processes and identifying opportunities for improvement. By tracking these metrics, businesses can optimize their operations, reduce waste, improve quality, and increase profitability.
2. Factors Affecting Effectiveness in Plastic Manufacturing
The effectiveness of plastic manufacturing processes can be affected by a variety of factors.
Some of the key factors include the quality of raw materials, the efficiency of production processes, the skills and experience of the workforce, the quality of machinery and equipment, and the effectiveness of quality control measures.
External factors such as economic conditions, government regulations, and competition in the industry can also have an impact on the effectiveness of plastic manufacturing.
By understanding these factors and identifying areas for improvement, businesses can optimize their operations, reduce waste, improve quality, and increase profitability.
Factors that Affect Effectiveness
There are several factors that can impact the effectiveness of plastic manufacturing processes. Some of the key factors include:
Raw Materials: The quality of raw materials used in plastic manufacturing can have a significant impact on the finished product's quality and consistency. Poor-quality raw materials can lead to defects, errors, and customer complaints, resulting in additional costs and lost productivity.
Machinery and Equipment: The efficiency and reliability of machinery and equipment used in plastic manufacturing are essential for achieving high production volumes and maintaining consistent quality. Frequent breakdowns or malfunctions can result in downtime, lost productivity, and additional costs.
Labor: The skills, experience, and training of the workforce can significantly impact the effectiveness of plastic manufacturing. A highly skilled and experienced workforce can identify and solve problems quickly, maintain machinery and equipment, and optimize production processes.
Quality Control: The effectiveness of quality control measures is essential for ensuring that the finished product meets customer expectations and industry standards. Ineffective quality control can lead to defective products, increased waste, and additional costs.
External Factors: Economic conditions, government regulations, and competition in the industry can also impact the effectiveness of plastic manufacturing processes. For example, changes in raw material prices, tariffs, or regulations can affect production costs and profitability.
By understanding these factors and implementing measures to address them, businesses can optimize their operations and improve the effectiveness of plastic manufacturing processes. This can result in increased productivity, improved quality, and reduced costs, ultimately leading to increased profitability and competitiveness in the industry.
How these Factors Can be Optimized for Better Effectiveness?
Optimizing the factors that impact the effectiveness of plastic manufacturing can help businesses improve their production processes and achieve better results. Here are some ways to optimize these factors:
Raw Materials: Businesses can optimize raw materials by working closely with suppliers to ensure consistent quality, testing materials before use, and using only approved materials. Investing in high-quality materials may initially be more expensive, but it can result in better consistency, fewer defects, and less waste in the long run.
Machinery and Equipment: To optimize machinery and equipment, businesses can invest in regular maintenance and repairs, upgrade outdated equipment, and train employees to use the equipment effectively. This can help reduce downtime, increase productivity, and improve the quality of the finished product.
Labor: Businesses can optimize labor by investing in training and development programs, hiring skilled and experienced workers, and providing a safe and positive work environment. This can help increase employee satisfaction, reduce turnover, and improve the quality and efficiency of the manufacturing process.
Quality Control: To optimize quality control, businesses can implement testing and inspection procedures at various stages of the production process, invest in quality control equipment, and regularly review and update quality control protocols. This can help identify and address issues early on, reducing waste and improving the quality of the finished product.
External Factors: Businesses can optimize their response to external factors by keeping up-to-date with industry trends and regulations, building strong relationships with suppliers and customers, and maintaining financial flexibility. This can help businesses adapt to changes in the market and maintain competitiveness.
Overall, optimizing these factors can help businesses improve the effectiveness of plastic manufacturing processes, reduce waste, improve quality, and increase profitability. By continuously reviewing and improving their processes, businesses can stay competitive and meet the evolving needs of their customers.
3. Implementing a Measurement System
Implementing a measurement system is essential for measuring the effectiveness of plastic manufacturing processes.
A measurement system provides a framework for collecting, analyzing, and interpreting data related to key performance indicators (KPIs) such as production volume, waste reduction, and quality control.
By implementing a measurement system, businesses can identify areas for improvement, set targets, and track progress toward achieving their goals. It is important to ensure that the measurement system is designed to capture relevant data accurately and efficiently, and that the data is analyzed and interpreted to drive continuous improvement.
Additionally, businesses should communicate the measurement system and its results to employees to create a culture of accountability and continuous improvement.
Steps Involved in Implementing a Measurement System
Implementing a measurement system in plastic manufacturing involves several key steps, including:
Identify Key Performance Indicators (KPIs): The first step in implementing a measurement system is to identify the KPIs that are most relevant to the business's goals and objectives. This may include production volume, waste reduction, quality control, and other metrics that are important to the business's success.
Establish Targets: Once the KPIs have been identified, it is important to establish targets that will help the business achieve its goals. These targets should be specific, measurable, achievable, relevant, and time-bound (SMART).
Develop a Data Collection Plan: A data collection plan outlines how data will be collected, when it will be collected, and who will be responsible for collecting it. This may involve installing sensors on production equipment, collecting data manually, or using software to automate data collection.
Implement Data Collection: Once the data collection plan has been developed, it is important to implement it effectively. This may involve training employees on how to collect data, installing sensors and software, and regularly reviewing data to ensure accuracy.
Analyze and Interpret Data: The data collected should be analyzed and interpreted regularly to identify trends, patterns, and areas for improvement. This may involve creating graphs, charts, and reports to visualize the data and communicate it to relevant stakeholders.
Take Action: Based on the analysis and interpretation of the data, businesses should take action to improve performance in areas where KPIs are not meeting targets. This may involve process improvements, equipment upgrades, employee training, or other interventions.
Communicate Results: It is important to communicate the results of the measurement system to employees and other stakeholders to create a culture of accountability and continuous improvement. This may involve regular meetings to review progress, sharing data visualizations, and recognizing employees for their contributions to improving performance.
Overall, implementing a measurement system is a crucial step for businesses looking to improve the effectiveness of their plastic manufacturing processes. By following these steps, businesses can collect and analyze data effectively, identify areas for improvement, and take action to achieve their goals.
4. Tools and Software Available for Tracking and Analyzing KPIs
There are several tools and software available for tracking and analyzing KPIs in plastic manufacturing, including:
Manufacturing Execution Systems (MES): MES software is designed to help businesses manage their manufacturing processes and track performance in real-time. MES software can collect data from various sources, such as production equipment and manual data entry, and provide real-time visibility into production performance. MES systems can help track KPIs such as production volume, cycle times, and waste reduction.
Enterprise Resource Planning (ERP) Systems: ERP software is designed to help businesses manage their entire operation, from finance and accounting to supply chain and production. ERP software can help track KPIs such as inventory levels, material usage, and production costs.
Business Intelligence (BI) Tools: BI tools are designed to help businesses analyze and interpret data to make better decisions. BI tools can help track KPIs such as defect rates, customer satisfaction, and on-time delivery. These tools can help visualize data in dashboards, reports, and charts, making it easier for decision-makers to identify trends and patterns.
Statistical Process Control (SPC) Software: SPC software is designed to help businesses monitor and control their manufacturing processes by tracking key quality metrics such as defect rates and variation. SPC software can help identify when a process is out of control, allowing businesses to take corrective action before defects occur.
Data Analytics Software: Data analytics software can help businesses analyze large amounts of data to identify patterns and trends. Data analytics software can help track KPIs such as production volume, inventory levels, and customer satisfaction. These tools can help identify areas for improvement and support data-driven decision-making.
Overall, there are many tools and software available to help businesses track and analyze KPIs in plastic manufacturing. It is important to choose tools that are tailored to the business's specific needs and goals, and that provide accurate and actionable insights into performance.
5. Benchmarking and Continuous Improvement
Benchmarking and continuous improvement are two important aspects of measuring effectiveness in plastic manufacturing.
Benchmarking involves comparing a business's performance against industry standards or best practices to identify areas for improvement. By benchmarking against competitors or similar businesses, a business can identify gaps in its performance and implement strategies to close those gaps.
Continuous improvement involves regularly reviewing and improving processes to enhance performance and achieve business goals. This may involve using data analytics to identify areas for improvement, implementing process improvements, and regularly reviewing performance against KPIs.
By benchmarking and implementing continuous improvement strategies, businesses can stay competitive and improve their effectiveness in plastic manufacturing. These strategies can help businesses identify areas for improvement, optimize their processes, and achieve their goals over time.
Importance of Benchmarking and Continuous Improvement in Measuring Effectiveness
Benchmarking and continuous improvement are critical components of measuring effectiveness in plastic manufacturing as they provide businesses with valuable insights into their performance and help them identify areas for improvement.
Benchmarking against industry standards or best practices helps businesses to identify gaps in their performance compared to their competitors or other businesses in the same industry.
By analyzing the differences in performance, businesses can develop a better understanding of where they stand in the market and identify opportunities for improvement.
Benchmarking can also help businesses to set realistic goals and targets for their KPIs, which can be tracked over time to measure effectiveness.
Continuous improvement is equally important as it allows businesses to continually enhance their performance and achieve their goals.
Regularly reviewing and improving processes helps to optimize performance, improve efficiency, and reduce costs. It also helps businesses to identify and address potential issues before they become major problems, reducing the risk of product defects, downtime, and waste.
By implementing benchmarking and continuous improvement strategies, businesses can continuously measure their effectiveness and identify opportunities for improvement. This can help them stay competitive, achieve their business objectives, and maintain high levels of customer satisfaction.
How Benchmarking can Help Identify Areas for Improvement and Establish Industry Standards?
Benchmarking is an effective way for businesses to identify areas for improvement and establish industry standards.
By comparing their performance against other businesses in the same industry, businesses can gain insights into their strengths and weaknesses and identify areas where they may be falling behind the competition.
Benchmarking helps businesses to establish industry standards by identifying best practices that are being used by leading companies in the industry. This information can then be used to set goals and targets for KPIs that align with industry standards.
For example, a plastic manufacturing company may benchmark its production cycle time against that of industry leaders and set a goal to reduce cycle time to match or beat the industry standard.
Benchmarking can also help businesses identify areas for improvement by highlighting performance gaps or areas where they may be underperforming compared to the competition.
This information can be used to develop strategies to close these gaps and improve performance. For example, a plastic manufacturing company may benchmark its defect rate against the industry standard and identify that its defect rate is higher. This may prompt the company to implement quality control measures to reduce defects and improve product quality.
Overall, benchmarking is a powerful tool for identifying areas for improvement and establishing industry standards. By analyzing the performance of other businesses in the same industry, companies can gain valuable insights into their own performance, set realistic goals and targets, and develop strategies to improve performance and achieve their business objectives.
6. Case Studies
Case studies that illustrate the successful implementation of measurement systems in plastic manufacturing
Case Study 1: Toyota Motor Corporation
Toyota Motor Corporation is a global leader in automotive manufacturing and has implemented a robust measurement system to optimize its plastic manufacturing processes. The company uses a range of KPIs, including production volume, defect rate, and cycle time, to measure the effectiveness of its manufacturing processes. Toyota's measurement system is designed to identify areas for improvement and drive continuous improvement across its operations.
As a result of its measurement system, Toyota has been able to achieve significant improvements in its plastic manufacturing processes, including reducing production cycle times and defect rates. By regularly analyzing data and identifying areas for improvement, Toyota has been able to optimize its operations and maintain high levels of quality in its plastic products.
Case Study 2: PepsiCo
PepsiCo, a leading food and beverage company, has implemented a comprehensive measurement system to optimize its plastic packaging manufacturing processes. The company uses KPIs such as material efficiency, waste reduction, and energy consumption to measure the effectiveness of its operations.
PepsiCo has been able to achieve significant improvements in its plastic packaging manufacturing processes as a result of its measurement system. By analyzing data and identifying areas for improvement, the company has been able to reduce waste and improve the sustainability of its operations. This has enabled PepsiCo to improve its brand reputation and achieve cost savings in its plastic manufacturing processes.
Case Study 3: HP Inc.
HP Inc., a leading technology company, has implemented a measurement system to optimize its plastic manufacturing processes for its printers and other products. The company uses KPIs such as material usage, recycling rates, and energy consumption to measure the effectiveness of its operations.
HP Inc. has been able to achieve significant improvements in its plastic manufacturing processes as a result of its measurement system. By analyzing data and identifying areas for improvement, the company has been able to reduce material usage and improve the sustainability of its operations. This has enabled HP Inc. to meet its sustainability goals and achieve cost savings in its plastic manufacturing processes.
Overall, these case studies illustrate the successful implementation of measurement systems in plastic manufacturing. By using KPIs to measure the effectiveness of their operations, companies are able to identify areas for improvement and optimize their processes for improved efficiency and sustainability.
Analysis of the Results Achieved and the Lessons Learned
The case studies presented show that implementing a measurement system in plastic manufacturing can lead to significant improvements in efficiency, quality, and sustainability. All three companies - Toyota, PepsiCo, and HP Inc. - were able to achieve improvements in their manufacturing processes as a result of their measurement systems.
For example, Toyota was able to reduce production cycle times and defect rates, while PepsiCo and HP Inc. were able to improve their sustainability and reduce waste in their plastic manufacturing processes. These improvements not only lead to cost savings but also improve the reputation of the companies and contribute to their sustainability goals.
The case studies also demonstrate that implementing a measurement system requires a commitment to continuous improvement and a willingness to embrace change. In each case, the companies had to analyze data, identify areas for improvement, and implement changes to their operations. This required a culture of innovation and a willingness to invest in new technology and processes.
Another lesson learned from these case studies is the importance of selecting the right KPIs for measuring effectiveness. The companies in these case studies selected KPIs that were relevant to their specific operations and goals. For example, Toyota's KPIs focused on cycle times and defect rates, while PepsiCo and HP Inc. focused on waste reduction and sustainability.
Finally, the case studies highlight the importance of benchmarking and learning from other companies in the industry. By comparing their performance to that of other companies, the companies in these case studies were able to identify areas for improvement and establish industry standards.
In conclusion, the results achieved by the companies in these case studies demonstrate that implementing a measurement system can lead to significant improvements in plastic manufacturing processes.
However, it requires a commitment to continuous improvement, a willingness to embrace change, and the selection of the right KPIs for measuring effectiveness.
By learning from these case studies, other companies in the plastic manufacturing industry can implement their own measurement systems and achieve similar improvements in their operations.
Wrapping Up
In conclusion, measuring the effectiveness of plastic manufacturing is crucial for improving operational efficiency, reducing waste, and achieving sustainability goals.
Key performance indicators (KPIs) such as production volume, waste reduction, and quality control can be used to track and analyze performance in plastic manufacturing. Factors such as raw materials, machinery, and labor also play a significant role in determining effectiveness, and optimizing these factors can lead to better results.
Implementing a measurement system requires a commitment to continuous improvement and the selection of the right KPIs for the specific operation and goals. There are various tools and software available to track and analyze KPIs, and benchmarking can help identify areas for improvement and establish industry standards.
Case studies demonstrate that implementing a measurement system can lead to significant improvements in plastic manufacturing processes. However, it requires a culture of innovation, a willingness to invest in new technology and processes, and a commitment to learning from other companies in the industry.
In summary, measuring effectiveness in plastic manufacturing is crucial for achieving operational efficiency, reducing waste, and contributing to sustainability goals. By implementing a measurement system and continuously improving processes, companies in the plastic manufacturing industry can achieve significant improvements in their operations and contribute to a more sustainable future.
How Deskera Can Assist You?
Deskera's integrated financial planning tools allow investors to better plan their investments and track their progress. It can help investors make decisions faster and more accurately.
Deskera Books enables you to manage your accounts and finances more effectively. Maintain sound accounting practices by automating accounting operations such as billing, invoicing, and payment processing.
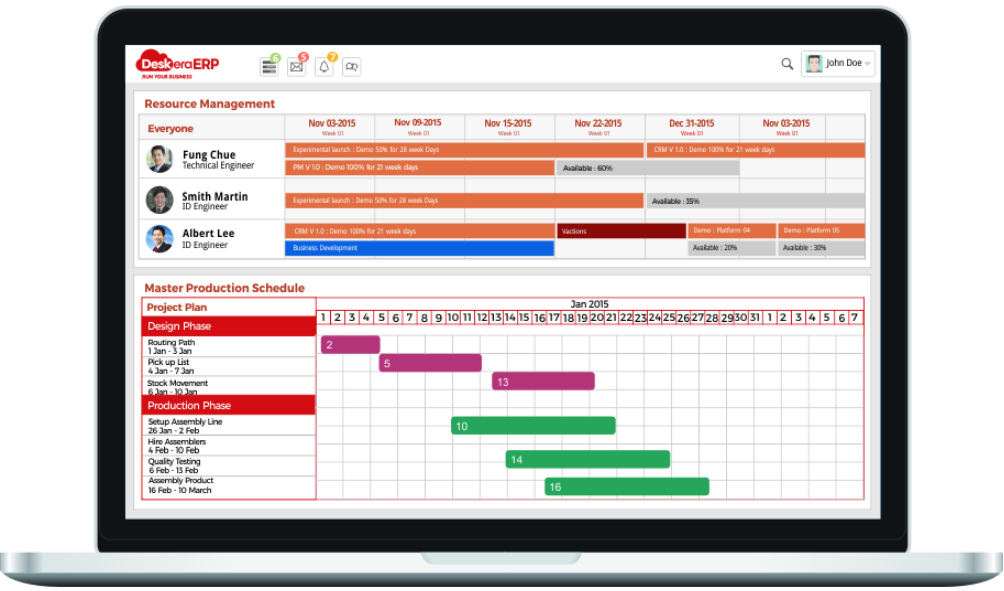
Deskera CRM is a strong solution that manages your sales and assists you in closing agreements quickly. It not only allows you to do critical duties such as lead generation via email, but it also provides you with a comprehensive view of your sales funnel.
Deskera People is a simple tool for taking control of your human resource management functions. The technology not only speeds up payroll processing but also allows you to manage all other activities such as overtime, benefits, bonuses, training programs, and much more. This is your chance to grow your business, increase earnings, and improve the efficiency of the entire production process.
Final Takeaways
We've arrived at the last section of this guide. Let's have a look at some of the most important points to remember:
- Measuring effectiveness involves tracking key performance indicators (KPIs) and benchmarking against industry standards to identify areas for improvement and make data-driven decisions. One of the main benefits of measuring effectiveness is that it helps businesses optimize their operations and reduce waste.
- By benchmarking against industry standards and analyzing their KPIs, businesses can identify areas for improvement and set achievable targets for growth. This allows businesses to make informed decisions about investments in new technologies and equipment that can improve efficiency and competitiveness.
- Key Performance Indicators (KPIs) are measurements that are used to track and assess the performance of a business or organization. In the context of plastic manufacturing, KPIs are used to measure the effectiveness of manufacturing processes and identify areas for improvement.
- Total unit cost is one of the key performance indicators (KPIs) that can be used to measure the effectiveness of plastic manufacturing. This KPI measures the total cost of producing a single unit of plastic product, including direct costs such as raw materials, labor, and overhead costs such as equipment maintenance and utilities.
- The efficiency and reliability of machinery and equipment used in plastic manufacturing are essential for achieving high production volumes and maintaining consistent quality. Frequent breakdowns or malfunctions can result in downtime, lost productivity, and additional costs.
- It is important to communicate the results of the measurement system to employees and other stakeholders to create a culture of accountability and continuous improvement. This may involve regular meetings to review progress, sharing data visualizations, and recognizing employees for their contributions to improving performance.
- MES software is designed to help businesses manage their manufacturing processes and track performance in real-time. MES software can collect data from various sources, such as production equipment and manual data entry, and provide real-time visibility into production performance. MES systems can help track KPIs such as production volume, cycle times, and waste reduction.
- SPC software is designed to help businesses monitor and control their manufacturing processes by tracking key quality metrics such as defect rates and variation. SPC software can help identify when a process is out of control, allowing businesses to take corrective action before defects occur.
Related Article
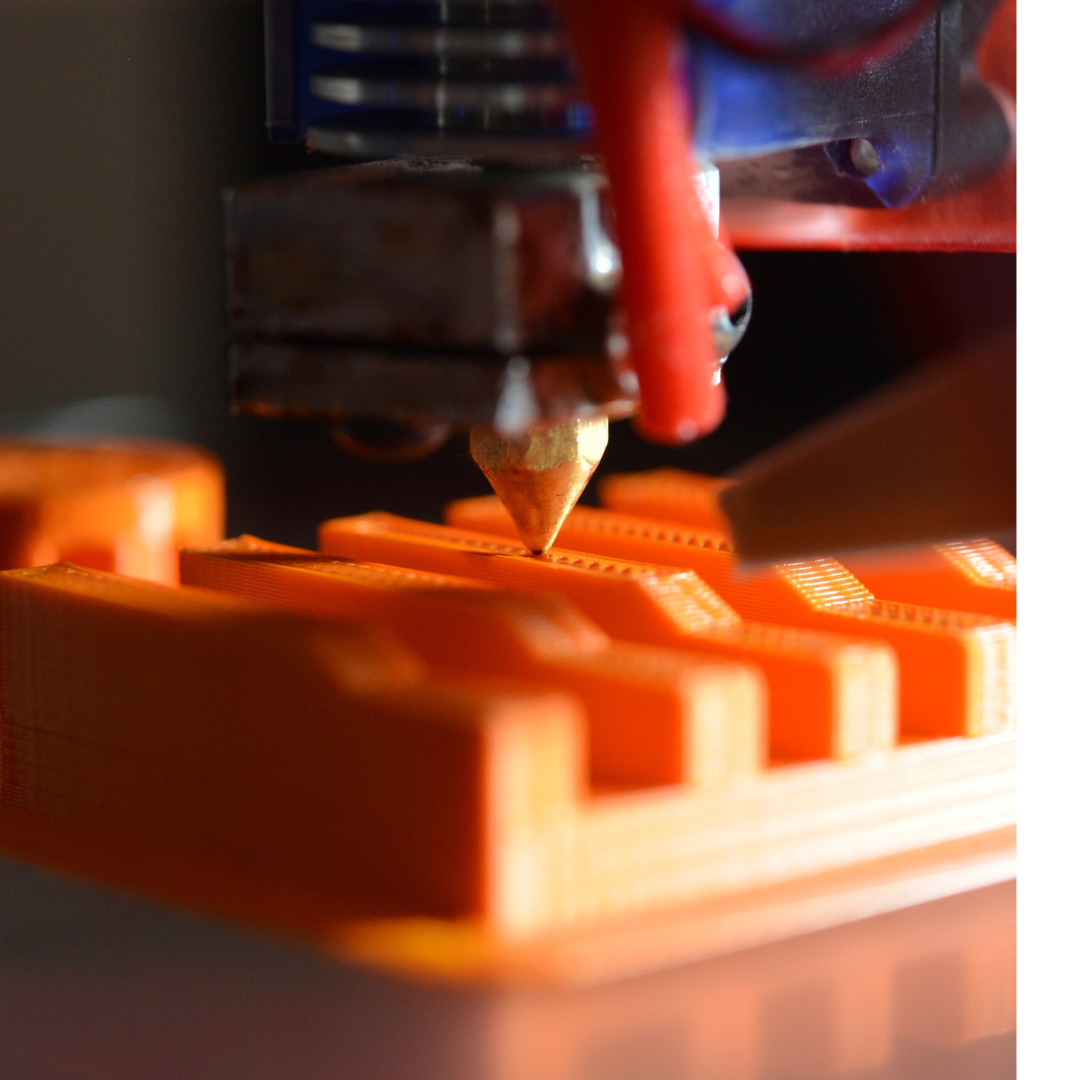
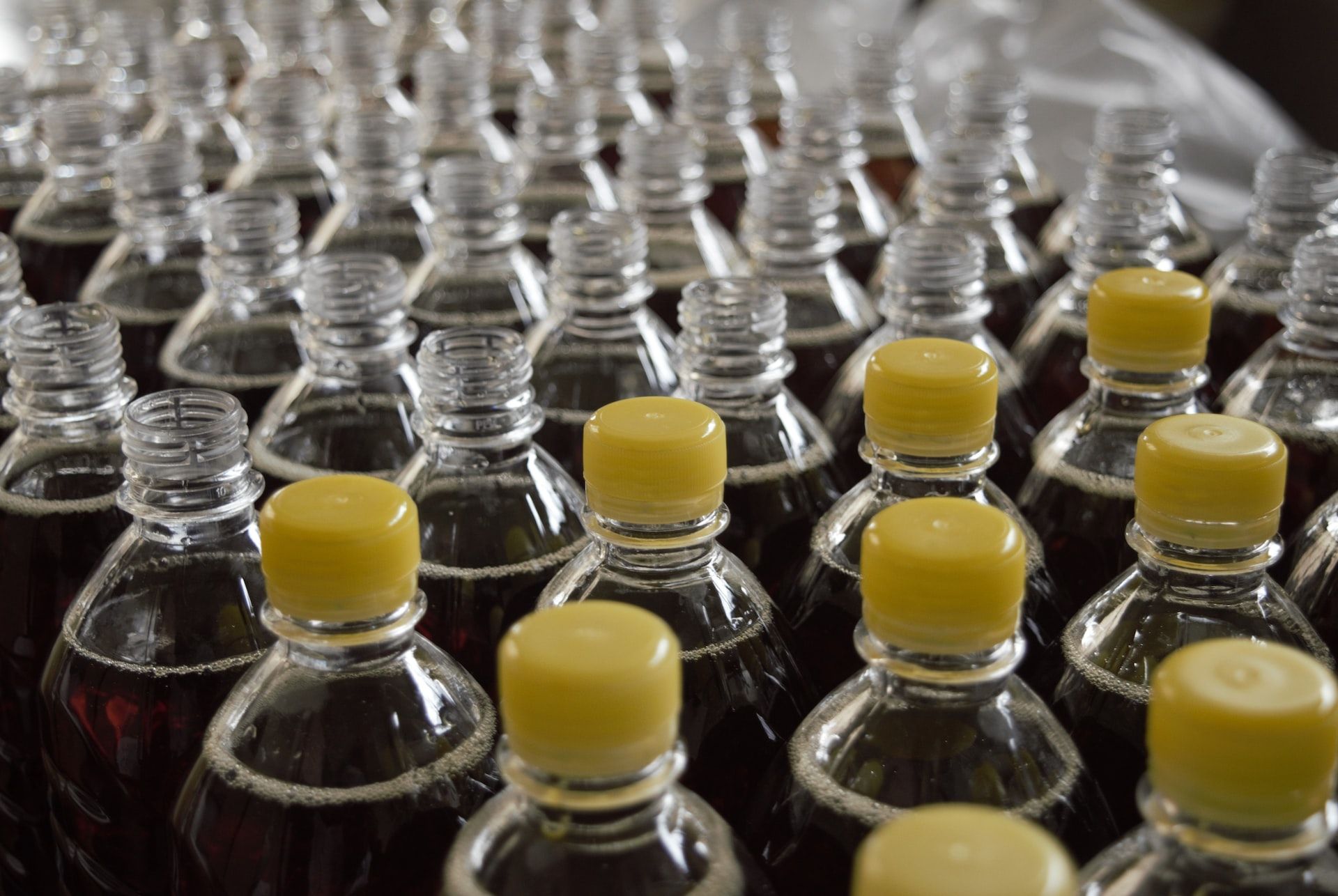

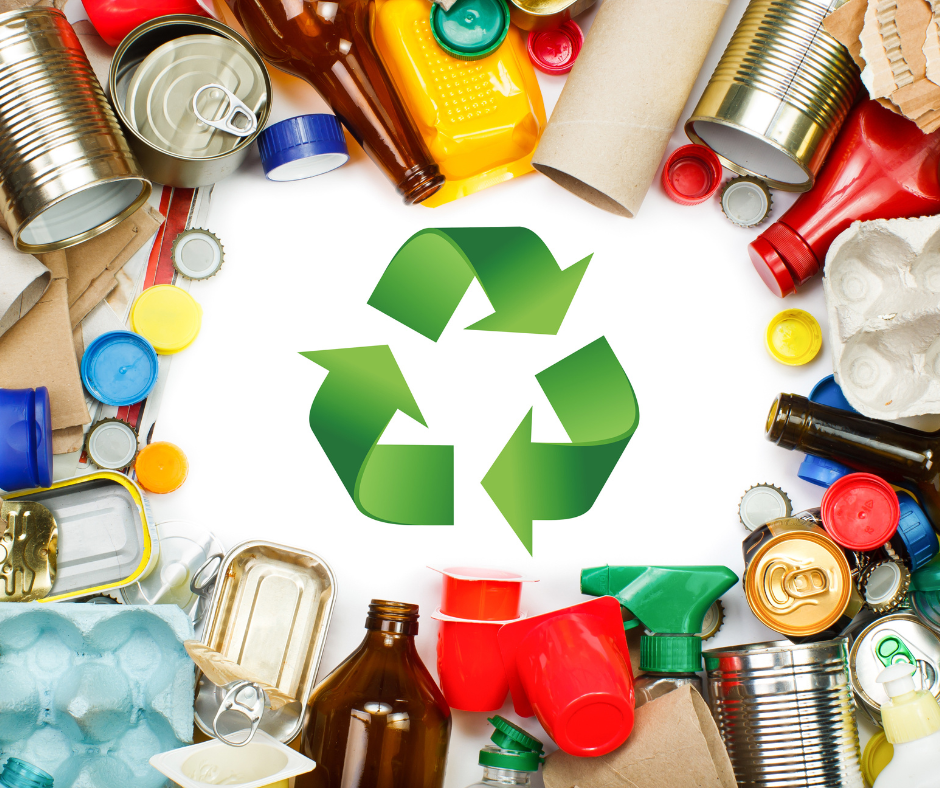
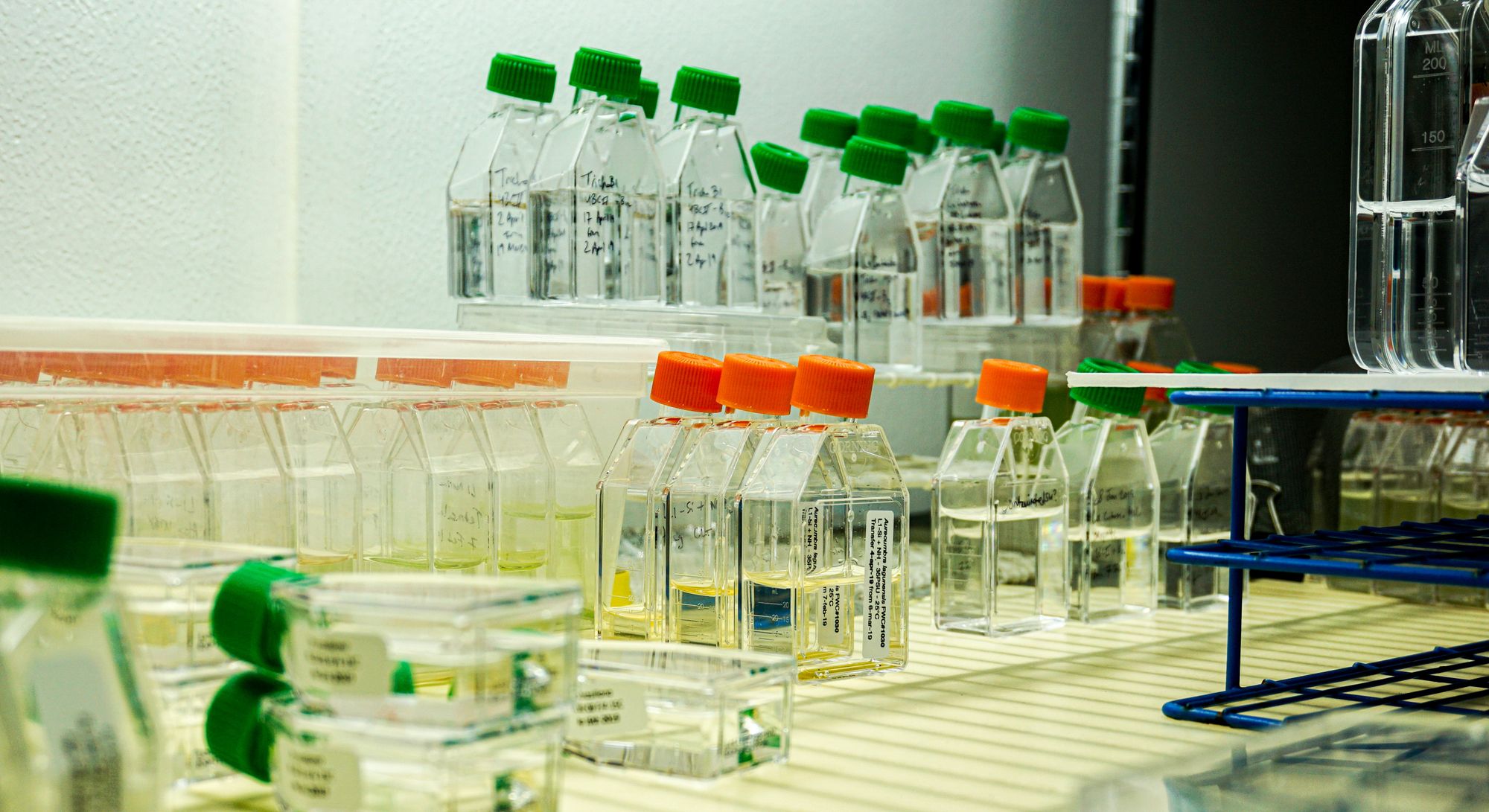