Plastic manufacturing is an essential industry that affects almost every aspect of our daily lives, from the packaging of our food to the construction of our cars. In 2023, the United States is expected to produce over 107 million metric tons of plastic, highlighting the vast scale of the industry.
With such a significant impact on the economy and our daily lives, it is essential to have a comprehensive understanding of plastic manufacturing.
As the demand for plastic products continues to grow, it is crucial to understand the manufacturing process, the types of plastic materials available, and the environmental impact of plastic production and disposal.
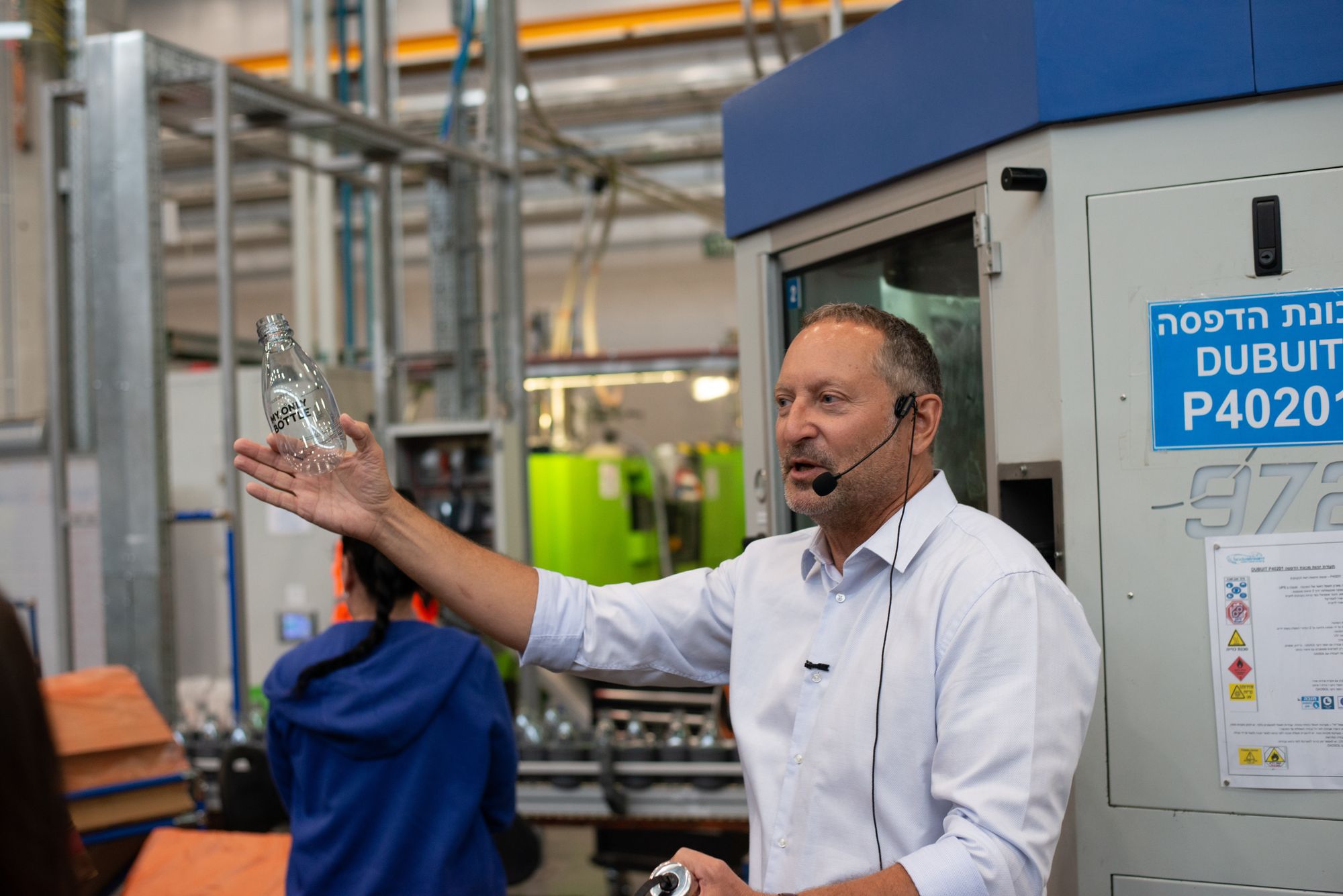
This comprehensive guide on plastic manufacturing aims to provide readers with a comprehensive overview of the industry, from the raw materials used in plastic production to the different processing techniques and applications of plastics.
Whether you are a seasoned industry professional or simply interested in learning more about this ubiquitous material, this guide will serve as a valuable resource for understanding the world of plastic manufacturing.
Here's what we shall cover in this post:
- Overview of the Plastic Manufacturing Industry
- Understanding the Various Types of Plastics Used in Manufacturing
- Essential Steps in the Plastic Manufacturing Process
- Key Considerations for Choosing the Right Plastic Manufacturing Method
- Benefits and Drawbacks of Plastic Manufacturing
- Environmental Impacts of Plastic Manufacturing
- Advances in Sustainable Plastic Manufacturing
- Best Practices for Recycling Plastic Waste
- Future Trends and Innovations in Plastic Manufacturing
- Conclusion
- Key Takeaways
Overview of the Plastic Manufacturing Industry
Plastic manufacturing is one of the largest industries in the world, and it plays a critical role in the global economy. Plastic products are used in a wide range of industries, including packaging, automotive, construction, electronics, and healthcare.
History of Plastic Manufacturing
Plastic manufacturing has been around for over a century, with the first synthetic plastic being invented in 1907. The industry experienced significant growth during World War II, as plastics were used to replace traditional materials like metal and glass.
Since then, the industry has continued to grow and evolve, with new materials and manufacturing processes being developed regularly.
Key Players in the Industry
A few large players, including Dow Chemical, ExxonMobil, and BASF, dominate the plastic manufacturing industry. These companies are involved in all aspects of the plastic manufacturing process, from raw material production to product design and distribution.
There are also many smaller companies in the industry, particularly in the area of plastic recycling and sustainability.
Understanding the Various Types of Plastics Used in Manufacturing
Plastic is a versatile and widely used material in the manufacturing industry. There are many different types of plastics used in manufacturing, each with its own unique properties and characteristics.
This section will provide an overview of the various types of plastics used in manufacturing, including their properties, common applications, and recycling considerations.
Polyethylene (PE):
Polyethylene is a common type of plastic used in manufacturing. It is a lightweight and flexible material that is resistant to moisture, chemicals, and UV radiation. It is commonly used in the production of plastic bags, packaging materials, and pipes.
Polyethylene is recyclable and can be used to make new products such as trash bags, plastic lumber, and playground equipment.
Polypropylene (PP):
Polypropylene is a strong and durable plastic that is resistant to heat, moisture, and chemicals. It is commonly used in the production of food packaging, automotive parts, and household items.
Polypropylene is recyclable and can be used to make new products such as garden furniture, storage containers, and automotive parts.
Polyvinyl Chloride (PVC):
Polyvinyl Chloride is a versatile plastic used in various applications, including construction, automotive, and medical industries. It is resistant to fire, chemicals, and UV radiation.
PVC is recyclable, but recycling can be challenging due to the presence of additives and contaminants.
Polystyrene (PS):
Polystyrene is a lightweight and rigid plastic commonly used to produce packaging materials, disposable cups and plates, and insulation. It is recyclable, but recycling rates are low due to the low demand for recycled polystyrene.
Polyethylene Terephthalate (PET):
Polyethylene Terephthalate is a strong and lightweight plastic commonly used in producing plastic bottles, food packaging, and textiles. It is recyclable and can be used to make new products such as carpeting, clothing, and automotive parts.
Acrylonitrile Butadiene Styrene (ABS):
Acrylonitrile Butadiene Styrene is a tough and durable plastic commonly used in producing automotive parts, toys, and electronic housings. It is recyclable and can be used to make new products such as computer housings, automotive parts, and plastic lumber.
Polycarbonate (PC):
Polycarbonate is a strong and lightweight plastic commonly used in producing eyeglass lenses, medical devices, and electronic components. It is recyclable and can be used to make new products such as automotive parts, electrical components, and safety glasses.
Essential Steps in the Plastic Manufacturing Process
Raw Material Preparation
The first step in the plastic manufacturing process is the preparation of raw materials. Plastic products can be made from a variety of materials, including polyethylene, polypropylene, and PVC.
The raw materials are typically in the form of pellets or powders and are mixed with additives such as colorants, stabilizers, and fillers to enhance their properties.
Melting and Mixing
Once the raw materials are prepared, they are fed into an extruder machine. The extruder melts and mixes the raw materials and additives together to form a homogeneous mixture. The mixture is then forced through a die to form the desired shape.
Molding
After the plastic material has been extruded, it is cooled and cut into the desired shape. The process of shaping the plastic material is called molding. There are several different types of molding, including injection molding, blow molding, and compression molding.
Each molding type has unique advantages and disadvantages, and manufacturers choose the most appropriate method for their particular application.
Finishing
Once the plastic product has been molded, it is subjected to finishing processes to enhance its appearance and functionality. Finishing processes may include trimming, polishing, painting, and printing.
These processes are essential to producing a high-quality plastic product that meets the required specifications.
Quality Control
Quality control is an essential step in the plastic manufacturing process. Manufacturers must ensure that their products meet the required specifications and are free from defects.
Quality control measures may include visual inspection, testing, and certification. Manufacturers may also use statistical process control methods to monitor and improve their production processes.
Packaging and Shipping
After the plastic products have passed quality control, they are packaged and shipped to customers. Packaging is an integral part of manufacturing as it protects the products during transportation and storage.
Manufacturers must also comply with regulations regarding the labeling and disposal of plastic products.
Key Considerations for Choosing the Right Plastic Manufacturing Method
Choosing the right plastic manufacturing method is crucial for producing high-quality plastic products that meet the required specifications. Several different plastic manufacturing methods are available, each with unique advantages and disadvantages.
This section will discuss the key considerations for choosing the right plastic manufacturing method.
Production Volume:
The production volume is one of the most important considerations when choosing a plastic manufacturing method. Some manufacturing methods are more suited to large-scale production, while others are better suited to small-scale production.
Injection molding, for example, is a highly efficient method that is well-suited to large-scale production, while 3D printing is better suited to small-scale production.
Material Selection:
Another important consideration when choosing a plastic manufacturing method is the type of material that will be used. Different manufacturing methods are better suited for different kinds of materials.
Injection molding, for example, is well-suited to materials such as thermoplastics and thermosetting plastics, while blow molding is better suited to materials such as polyethylene and polypropylene.
The complexity of the Design:
The complexity of the design is another important consideration when choosing a plastic manufacturing method. Some manufacturing methods are better suited to simple designs, while others are better suited to more complex designs.
Injection molding, for example, is well-suited to complex designs with intricate details, while blow molding is better suited to simpler designs.
Cost:
Cost is another important consideration when choosing a plastic manufacturing method. Some manufacturing methods are more expensive than others, and the cost can vary depending on the production volume, material selection, and complexity of the design.
Injection molding, for example, is a more expensive method than blow molding, but it is also more efficient and produces higher-quality products.
Time-to-Market:
The time-to-market is another crucial consideration when choosing a plastic manufacturing method. Some methods are faster than others, and the time-to-market can be influenced by factors such as tooling lead times and production volume.
Injection molding, for example, has a longer lead time for tooling but is faster in producing products once the tooling is complete.
Sustainability:
Sustainability is an essential consideration for many manufacturers today. Some plastic manufacturing methods are more environmentally sustainable than others. Manufacturers should consider factors such as energy consumption, waste generation, and material recyclability when choosing a plastic manufacturing method.
Benefits and Drawbacks of Plastic Manufacturing
Benefits
Versatility
One of the primary benefits of plastic manufacturing is the versatility of plastics. Plastics can be molded into a wide range of shapes and sizes, making them ideal for a wide range of applications.
Durability
Plastics are highly durable and resistant to wear and tear, making them ideal for use in products that need to withstand harsh environments or frequent use.
Cost-Effective
Plastic manufacturing is often more cost-effective than other materials manufacturing processes, making it an attractive option for manufacturers looking to reduce costs.
Lightweight
Plastics are typically much lighter than other materials, making them ideal for use in applications where weight is a concern, such as in the automotive and aerospace industries.
Recyclable
Many types of plastic are recyclable, which can help to reduce waste and minimize the environmental impact of plastic manufacturing.
Drawbacks
Environmental Impact
Plastic manufacturing has a significant environmental impact, with plastics being a major contributor to ocean pollution and landfills.
Health Concerns
There are concerns about the potential health risks of certain plastics, such as bisphenol A (BPA), which has been linked to various health problems, including cancer and reproductive issues.
Non-Biodegradable
Many types of plastic are non-biodegradable, which means they can persist in the environment for hundreds of years, contributing to pollution and environmental damage.
Limited Lifespan
While plastics are durable, they have a limited lifespan and can degrade over time, particularly when exposed to sunlight or heat.
Energy Intensive
Plastic manufacturing is an energy-intensive process, with the production of plastics requiring significant amounts of energy and producing greenhouse gas emissions.
Environmental Impacts of Plastic Manufacturing
While plastic manufacturing offers numerous benefits, there are also significant environmental impacts associated with plastic production, use, and disposal. In this section, we will discuss the environmental effects of plastic manufacturing.
- Greenhouse Gas Emissions: The production of plastics requires significant amounts of energy, primarily from fossil fuels, which contributes to greenhouse gas emissions and climate change.
- Air Pollution: Plastic manufacturing processes, such as extrusion and injection molding, can release harmful air pollutants, including volatile organic compounds (VOCs) and particulate matter.
- Water Pollution: Plastic manufacturing also contributes to water pollution, with some plastics manufacturing processes releasing toxic chemicals into waterways, such as phthalates, bisphenol A (BPA), and dioxins.
- Landfill Waste: Plastic manufacturing results in a significant amount of waste, much of which ends up in landfills, where it can persist for hundreds of years without breaking down.
- Marine Pollution: Plastics are a significant contributor to marine pollution, with an estimated 8 million metric tons of plastic entering the oceans each year, harming marine life and ecosystems.
- Microplastics: The breakdown of larger plastic items into smaller particles, known as microplastics, has become a significant environmental concern, with microplastics found in oceans, soil, and even drinking water.
- Wildlife Harm: Plastic pollution can harm wildlife through ingestion or entanglement, leading to injury or death.
- Resource Depletion: The production of plastics requires significant amounts of non-renewable resources, such as oil and gas, which can lead to resource depletion and environmental damage associated with resource extraction.
Advances in Sustainable Plastic Manufacturing
The manufacturing of plastics has been associated with numerous environmental problems, including greenhouse gas emissions, water pollution, and waste management issues.
As a result, there has been an increasing focus on developing sustainable plastic manufacturing methods. In this section, we will discuss advances in sustainable plastic manufacturing.
Bioplastics:
Bioplastics are plastics derived from renewable biomass sources such as corn starch, sugarcane, and potato starch. Unlike traditional plastics, which are derived from petroleum, bioplastics can be produced using renewable resources, reducing the environmental impact of plastic production.
Recycled Plastics:
The use of recycled plastics is an effective way to reduce the environmental impact of plastic manufacturing. By using recycled plastic, manufacturers can reduce the amount of plastic waste that ends up in landfills and oceans.
Biodegradable Plastics:
Biodegradable plastics are designed to break down quickly in the environment, reducing the amount of plastic waste that persists in the environment. These plastics can be made from a variety of materials, including plant-based materials and traditional petroleum-based plastics that are modified to break down more quickly.
Sustainable Manufacturing Processes:
The manufacturing process itself can have a significant impact on the environmental footprint of plastic production.
Advances in sustainable manufacturing processes include using renewable energy sources, such as solar and wind power, and using closed-loop systems that recycle waste materials and reduce the amount of raw materials needed.
Life Cycle Assessments:
A life cycle assessment (LCA) is a method used to assess the environmental impact of a product throughout its life cycle, from production to disposal. The use of LCAs in plastic manufacturing can help identify areas where environmental improvements can be made, such as reducing energy use or incorporating more sustainable materials.
Circular Economy:
The circular economy is a concept that aims to minimize waste and maximize resource efficiency by keeping materials in use for as long as possible.
In the context of plastic manufacturing, the circular economy involves designing products to be reused, repaired, or recycled and creating closed-loop systems that minimize waste and pollution.
Collaborative Efforts:
Advances in sustainable plastic manufacturing require collaboration between manufacturers, policymakers, and consumers. Policymakers can promote sustainable manufacturing practices through regulations and incentives, while consumers can support sustainable products and disposal practices.
Best Practices for Recycling Plastic Waste
Plastic waste is a major environmental problem, as it takes hundreds of years to decompose and can harm wildlife and ecosystems. Recycling plastic waste is one way to mitigate these negative impacts. Here are some best practices for recycling plastic waste:
- Separate plastic waste from other materials: Plastic waste should be separated from other waste materials, such as paper, glass, and metal. This ensures that the plastic can be processed separately and reduces contamination of different materials.
- Follow local recycling guidelines: Different regions have different guidelines for what types of plastic can be recycled and how they should be prepared for recycling. It is important to follow local guidelines to ensure that plastic can be recycled effectively.
- Clean and dry plastic waste: Plastic waste should be cleaned and dried before it is recycled. This removes any contaminants that may hinder the recycling process and ensures that the recycled plastic is of high quality.
- Consider using a recycling service: Some cities offer recycling services for plastic waste. These services can collect plastic waste from homes or businesses and ensure that it is recycled properly.
- Support companies that use recycled plastic: By purchasing products made from recycled plastic, consumers can help create demand for recycled materials and support the growth of the recycling industry.
- Reduce plastic use: The best way to reduce the environmental impact of plastic waste is to reduce the amount of plastic that is used in the first place. Consumers can reduce their plastic use by using reusable bags, bottles, and containers.
- Educate others: Educating others about the importance of recycling plastic waste and the best practices for doing so can help create a culture of sustainability and reduce the amount of plastic waste that ends up in landfills or oceans.
Future Trends and Innovations in Plastic Manufacturing
Plastic manufacturing has come a long way since its inception, with significant advancements in technology and processes leading to increased efficiency and sustainability. Here are some future trends and innovations in plastic manufacturing:
- 3D Printing: 3D printing has already revolutionized manufacturing and is expected to do the same for plastic manufacturing. This technology allows for more complex designs and customization, reducing waste and improving efficiency.
- Automation: Automation is becoming increasingly popular in plastic manufacturing, as it can improve efficiency and reduce labor costs. Robots can perform tasks such as injection molding, trimming, and packaging faster and more accurately than humans.
- Sustainable Packaging: The demand for sustainable packaging is increasing, and plastic manufacturers are exploring new materials and designs to meet this demand. This includes biodegradable plastics, reusable packaging, and compostable materials.
- Recycling Innovations: Innovations in recycling technology are making it possible to recycle more types of plastic and reduce waste. This includes advancements in chemical recycling, which can break down plastics into their chemical components for reuse.
- Nanotechnology: Nanotechnology is being used to improve the properties of plastic materials, such as making them stronger, more heat-resistant, and more flexible. This technology also has the potential to make plastic manufacturing more sustainable by reducing energy consumption and waste.
- Blockchain: Blockchain technology can be used to create a transparent and secure supply chain for plastic manufacturing. This can improve traceability and accountability, ensuring that plastic waste is managed correctly and recycled.
How Deskera Can Assist You?
Deskera MRP allows you to closely monitor the manufacturing process. From the bill of materials to the production planning features, the solution helps you stay on top of your game and keep your company's competitive edge.
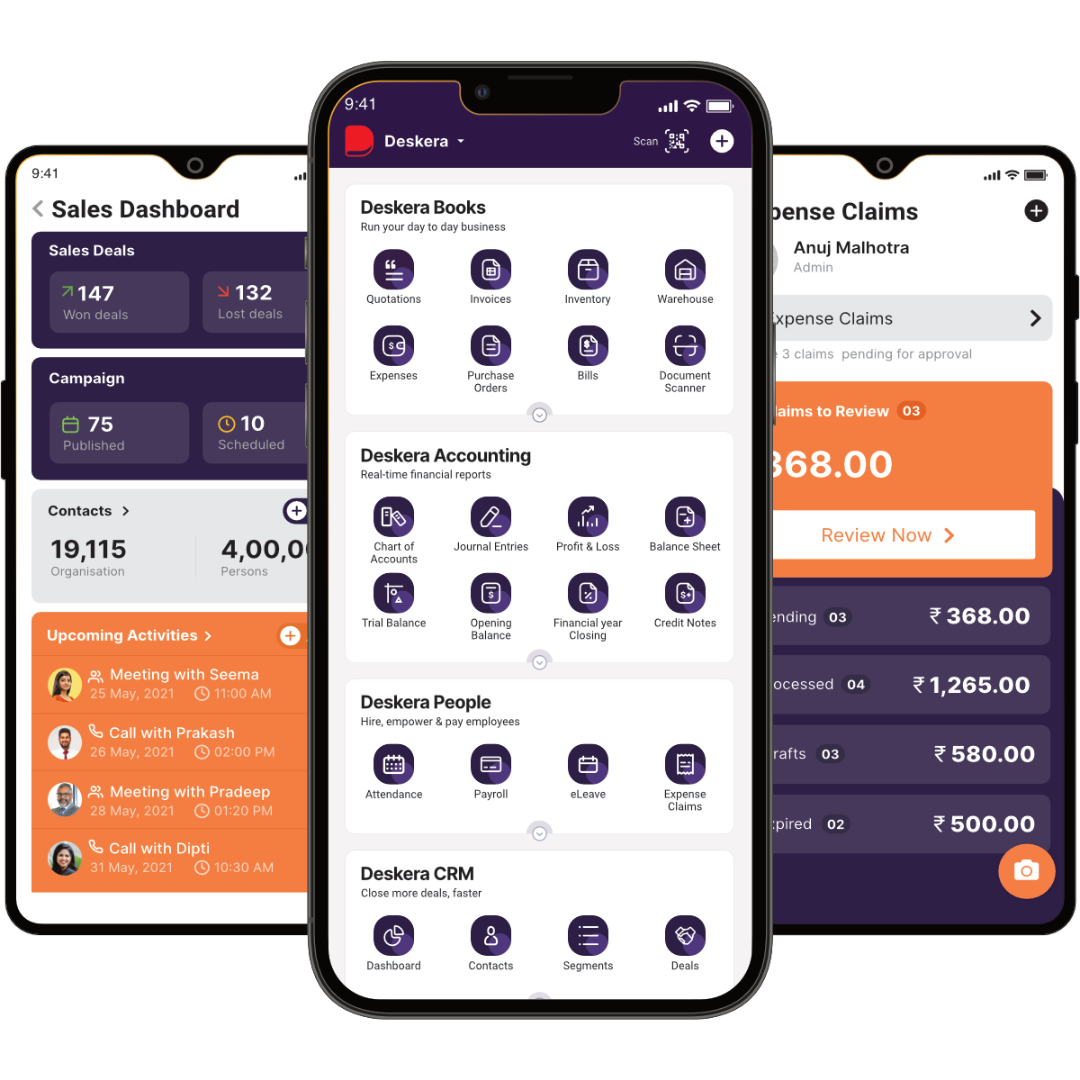
Deskera ERP and MRP system can help you:
- Manage production plans
- Maintain Bill of Materials
- Generate detailed reports
- Create a custom dashboard
Deskera ERP is a comprehensive system that allows you to maintain inventory, manage suppliers, and track supply chain activity in real-time, as well as streamline a variety of other corporate operations.
Deskera Books enables you to manage your accounts and finances more effectively. Maintain sound accounting practices by automating accounting operations such as billing, invoicing, and payment processing.
Deskera CRM is a strong solution that manages your sales and assists you in closing agreements quickly. It not only allows you to do critical duties such as lead generation via email, but it also provides you with a comprehensive view of your sales funnel.
Deskera People is a simple tool for taking control of your human resource management functions. The technology not only speeds up payroll processing but also allows you to manage all other activities such as overtime, benefits, bonuses, training programs, and much more. This is your chance to grow your business, increase earnings, and improve the efficiency of the entire production process.
Conclusion
Plastic manufacturing is a vast and complex process that requires careful consideration of various factors such as raw materials, equipment, and production techniques. It has revolutionized various industries and is essential to our daily lives.
However, with the increasing awareness of the harmful impact of plastic on the environment, it is crucial to adopt sustainable manufacturing practices and promote the use of biodegradable alternatives.
Additionally, safety should always be a top priority in plastic manufacturing to prevent accidents and ensure the health and well-being of workers. This comprehensive guide highlights the key aspects of plastic manufacturing and provides insights into the best practices for sustainable and safe production.
By implementing these strategies, the plastic manufacturing industry can continue to thrive while minimizing its environmental impact and contributing to a safer and healthier world.
Key Takeaways
- Plastic manufacturing involves a complex process of melting, shaping, cooling, and finishing plastic materials into various products.
- Raw materials used in plastic manufacturing include petroleum, natural gas, and coal, which are processed to form plastic pellets or resin.
- The plastic manufacturing process can be categorized into four main types: injection molding, blow molding, extrusion, and thermoforming.
- Injection molding is the most common type of plastic manufacturing, and it involves the use of molds to shape molten plastic into desired products.
- Blow molding is used to manufacture hollow plastic products such as bottles, and it involves the use of compressed air to inflate a hot plastic tube in a mold.
- Extrusion is used to manufacture plastic products such as pipes, sheets, and films. It involves using an extruder to melt and shape plastic materials into a continuous stream.
- Thermoforming is used to manufacture plastic products such as trays, cups, and containers, and it involves the use of heat and pressure to shape plastic sheets into desired forms.
- Plastic manufacturing has many advantages, including low production costs, versatility, durability, and recyclability.
Related Articles
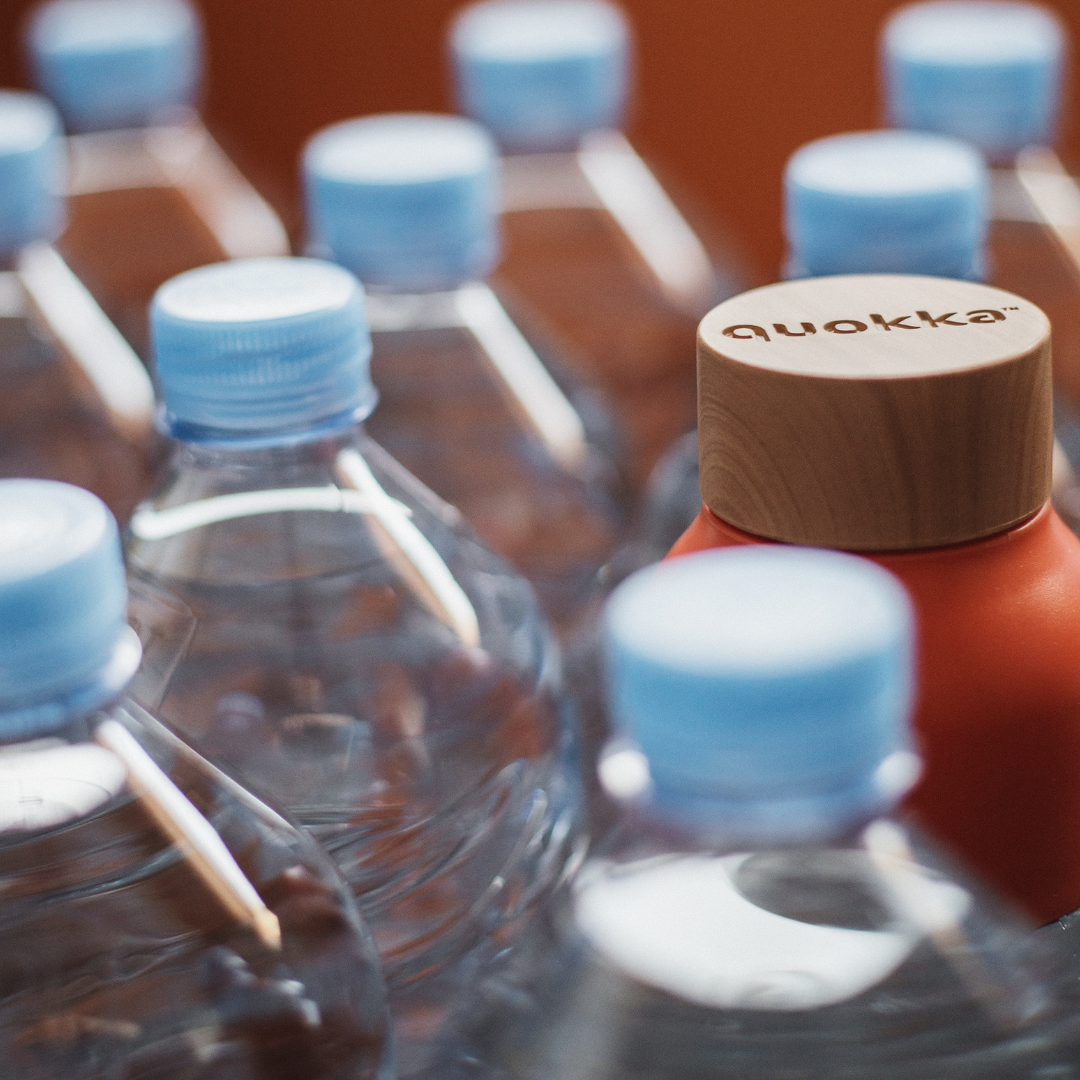
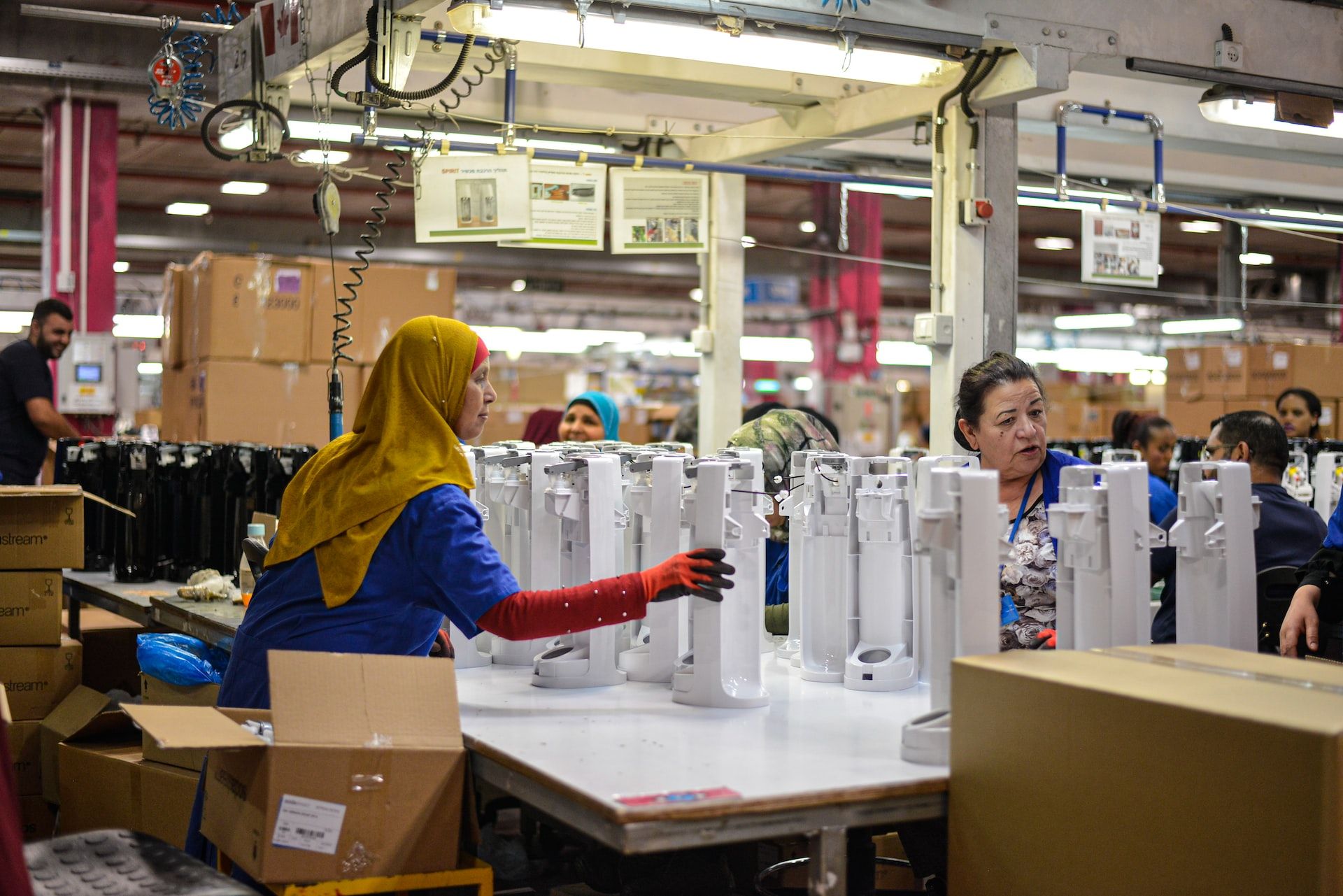
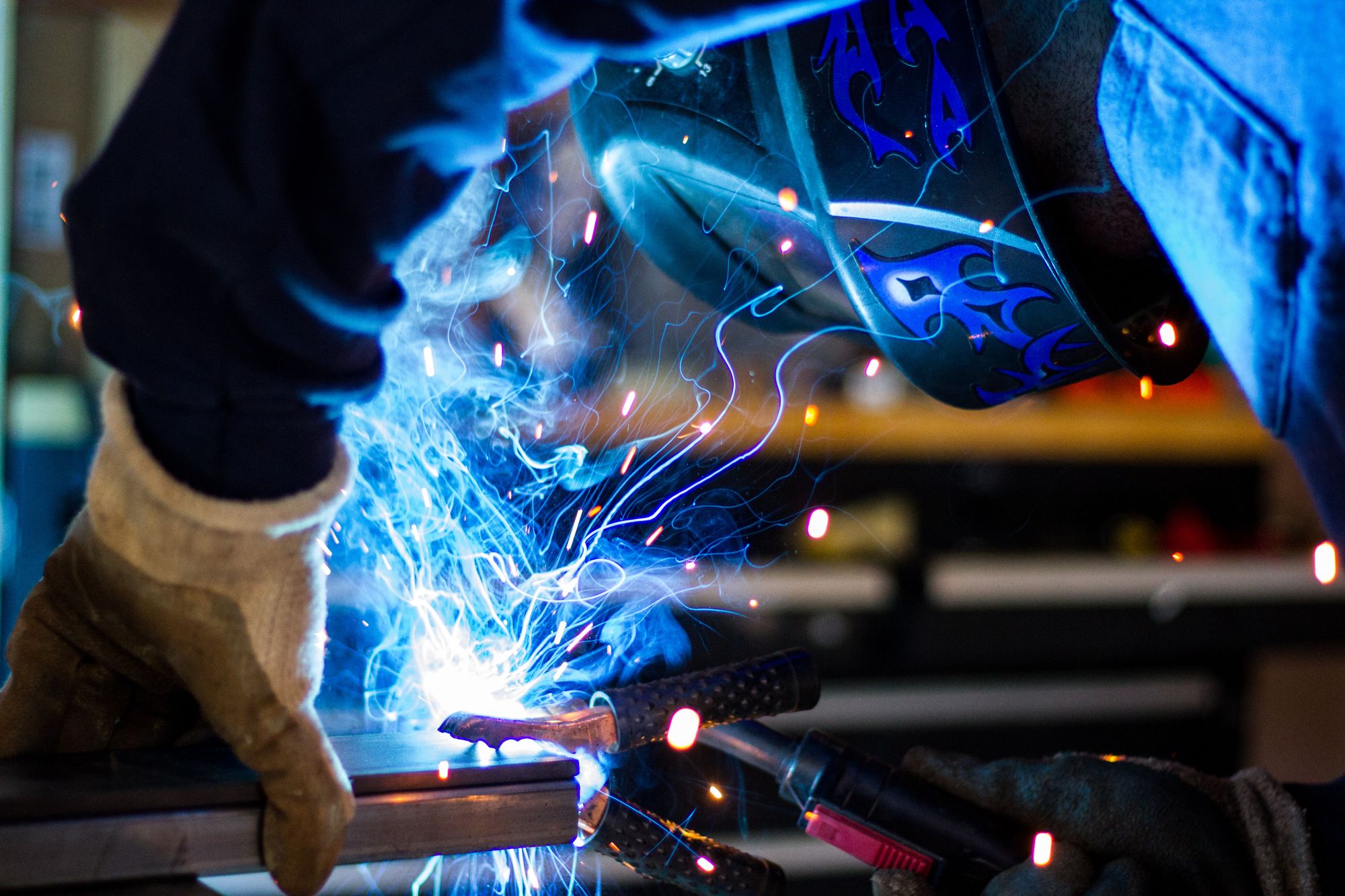
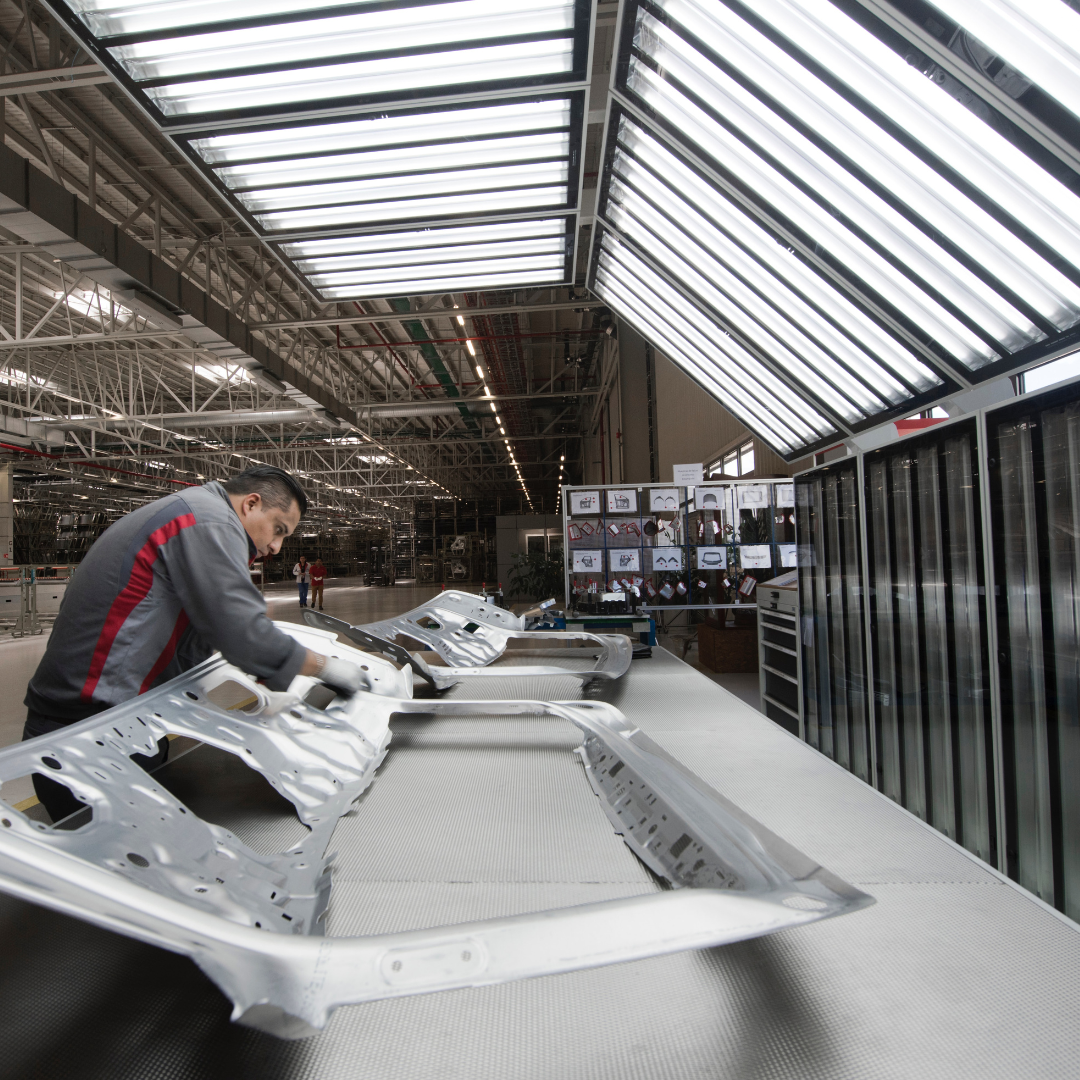