According to the Food and Agriculture Organization (FAO), global paper production reached 419 million metric tons in 2020, which is an increase of 0.8% from 2019. The paper industry is a major employer, with an estimated 1.5 million people employed in the industry in Europe alone, according to CEPI.
Paper manufacturing is a significant industry that plays an important role in many sectors of the global economy. However, the industry faces challenges related to environmental sustainability and energy efficiency, and is working to address these challenges through innovation and sustainable practices.
Paper is one of the world's most widely used and versatile materials, with applications ranging from packaging and printing to construction and hygiene. The paper manufacturing process involves a series of complex steps, including pulping, screening, cleaning, refining, and papermaking, which require the use of various chemicals and additives to enhance the properties of paper and ensure its quality. This article will provide an in-depth discussion of the role of additives in paper manufacturing.
- Types of Additives Used in Paper Manufacturing
- Fillers
- Retention Aids
- Sizing Agents
- Wet Strength Agents
- Dry Strength Agents
- Defoamers
- Dyes and Pigments
- Benefits of Using Additives in Paper Manufacturing
- Challenges and Limitations of Using Additives in Paper Manufacturing
- How can Deskera Help You?
- Conclusion
- Related Articles
Types of Additives Used in Paper Manufacturing
Several additives are used in paper manufacturing, each of which serves a specific purpose. Some of the most commonly used additives include fillers, retention aids, sizing agents, wet strength agents, dry strength agents, defoamers, and dyes and pigments.
Fillers
Fillers are a type of additive used in paper manufacturing to improve the optical and mechanical properties of paper while reducing production costs. Fillers are typically inorganic materials such as clay, calcium carbonate, and titanium dioxide. They are added to the paper pulp during the manufacturing process to fill the spaces between the fibers and increase the paper's bulkiness.
The use of fillers in paper manufacturing offers several benefits, including:
- Improved optical properties: Fillers can increase the brightness, opacity, and whiteness of paper, making it more visually appealing.
- Increased bulkiness: Fillers can increase the bulkiness of paper, making it feel thicker and more substantial.
- Reduced production costs: Fillers are less expensive than cellulose fibers, so their use can reduce the cost of paper production.
- Enhanced printability: The addition of fillers can improve the surface characteristics of paper, making it more receptive to ink and improving the quality of printed images.
- Reduced environmental impact: The use of fillers can reduce the environmental impact of paper production by reducing the amount of cellulose fibers needed, thus conserving natural resources and reducing waste.
However, the use of fillers also has some limitations and challenges. For example, excessive use of fillers can negatively impact the strength and durability of paper. More reliance on fillers can also result in reduced paper quality and increased wear and tear on papermaking equipment. Additionally, the type and quality of the filler used can affect the properties of the paper, so careful selection and testing is necessary to ensure the desired results.
Fillers are an essential type of additive used in paper manufacturing to improve paper's optical and mechanical properties while reducing production costs. Their use offers several benefits, including improved optical properties, increased bulkiness, reduced production costs, enhanced printability, and reduced environmental impact. However, using fillers also has limitations and challenges that must be carefully considered and managed to ensure high-quality paper products.
Retention Aids
Retention aids are an additive used in paper manufacturing to improve the retention of fibers and fillers in the paper pulp, thus reducing the amount of material lost during the papermaking process. Using retention aids can also improve paper's strength, surface properties, and printability.
Retention aids work by increasing the attraction between the fibers and fillers in the pulp and by improving the drainage and dewatering of the pulp on the paper machine. This helps reduce the amount of fiber and fill lost in the process, resulting in increased paper strength and improved paper quality.
Retention aids can be classified into several categories, including:
- Natural polymers: These are derived from natural sources such as starch, guar gum, and cellulose. They are typically non-toxic, biodegradable, and renewable, making them environmentally friendly options.
- Synthetic polymers: These are synthetic substances such as polyacrylamide, polyethylene oxide, and polyvinyl alcohol. They are often used in combination with natural polymers to enhance their performance.
- Inorganic compounds: These are compounds such as bentonite, clay, and silica. They are often used as fillers, but they can also act as retention aids by improving the drainage and retention of pulp on the paper machine.
The use of retention aids offers several benefits, including:
- Improved paper quality: Retention aids can improve the uniformity, surface properties, and printability of paper, resulting in higher-quality products.
- Increased production efficiency: Retention aids can improve the dewatering and drainage of the pulp on the paper machine, reducing production time and energy consumption.
- Reduced environmental impact: Using retention aids can reduce the amount of fiber and filler lost during the papermaking process, resulting in less waste and reduced environmental impact.
However, the use of retention aids also has some limitations and challenges. For example, overuse of retention aids can negatively impact the strength and durability of paper. Additionally, some retention aids may be costly or difficult to source, and their effectiveness may vary depending on the type of pulp and paper being produced.
Retention aids are an important type of additive used in paper manufacturing to improve the retention of fibers and fillers in the paper pulp, resulting in higher quality products, increased production efficiency, and reduced environmental impact. The use of retention aids offers several benefits, but their use must be carefully managed to ensure high-quality paper products and efficient and cost-effective production processes.
Sizing Agents
Sizing agents are an additive used in paper manufacturing to improve the paper's resistance to water absorption and prevent ink from bleeding or feathering on the paper surface. Sizing agents are typically added to the paper pulp during manufacturing to improve the paper's printability and durability.
Sizing agents can be classified into two main categories: internal sizing agents and surface sizing agents.
Internal sizing agents are added to the paper pulp during manufacturing and are designed to react with the cellulose fibers to create a water-resistant barrier. Internal sizing agents can be further classified as either acidic or alkaline, depending on the pH of the pulp. Acidic sizing agents are typically used in acidic pulps, such as those used in newsprint production. In contrast, alkaline sizing agents are used in alkaline pulps, such as those used in producing high-quality printing and writing papers.
Surface sizing agents are applied to the paper's surface after it has been formed and dried. Surface sizing agents are typically used on papers that require a high degree of water resistance or ink holdout, such as coated papers used for printing and packaging applications.
The use of sizing agents offers several benefits, including:
- Improved water resistance: Sizing agents can improve the paper's resistance to water absorption, reducing the risk of paper degradation and improving the paper's durability.
- Enhanced printability: Sizing agents can prevent ink from bleeding or feathering on the paper surface, resulting in sharper and more defined printed images.
- Improved surface properties: Sizing agents can improve paper's surface smoothness and uniformity, resulting in higher-quality products.
- Reduced paper consumption: Using sizing agents can reduce the amount of paper needed for a given task, resulting in cost savings and reduced environmental impact.
However, the use of sizing agents also has some limitations and challenges. Overuse of sizing agents can negatively impact the strength and durability of paper, and the type and quality of the sizing agent used can affect the properties of the paper. Additionally, some sizing agents may be costly or difficult to source, and their effectiveness may vary depending on the type of pulp and paper being produced.
Sizing agents are an important type of additive used in paper manufacturing to improve the paper's water resistance, printability, and surface properties. Sizing agents offer several benefits, but their use must be carefully managed to ensure high-quality paper products and efficient and cost-effective production processes.
Wet Strength Agents
Wet strength agents are a type of additive used in paper manufacturing to improve the paper's strength and durability when wet. Wet strength agents are typically added to the paper pulp during manufacturing to improve the paper's resistance to water and other fluids.
Wet strength agents work by crosslinking the cellulose fibers in the paper, creating a strong, water-resistant network. There are several types of wet strength agents, including:
- Melamine-formaldehyde: This is a synthetic wet-strength agent that is commonly used in the production of tissue and towel paper products. It is effective at low concentrations and provides good wet strength without sacrificing paper softness.
- Polyamide-epichlorohydrin: This is a natural wet-strength agent often used to produce high-quality printing and writing papers. It is effective at higher concentrations than melamine-formaldehyde and can provide greater wet strength.
- Glyoxylated polyacrylamide: This is a synthetic wet-strength agent often used to produce packaging papers. It is effective at low concentrations and can provide good wet strength and water resistance.
The use of wet strength agents offers several benefits, including:
- Improved paper durability: Wet strength agents can improve the paper's resistance to water and other fluids, reducing the risk of paper degradation and improving the paper's durability.
- Enhanced product performance: Using wet strength agents can improve the performance of paper products, particularly those exposed to moisture or fluids.
- Expanded product applications: The use of wet strength agents can extend the range of product applications for paper, allowing it to be used in new and innovative ways.
However, using wet strength agents also has some limitations and challenges. Overuse of wet strength agents can negatively impact the paper's softness and flexibility, and the type and quality of the wet strength agent used can affect the properties of the paper. Additionally, some wet-strength agents may be costly or difficult to source, and their effectiveness may vary depending on the pulp and paper produced.
Wet strength agents are an important type of additive used in paper manufacturing to improve the paper's strength and durability when wet. Wet strength agents offer several benefits, but their use must be carefully managed to ensure high-quality paper products and efficient and cost-effective production processes.
Dry Strength Agents
Dry strength agents are a type of additive used in paper manufacturing to improve the paper's strength and durability when dry. Dry strength agents are typically added to the paper pulp during the manufacturing process to improve the paper's internal bonding strength.
Dry strength agents work by increasing the internal bonding forces between the cellulose fibers in the paper. There are several types of dry strength agents, including:
- Cationic starch: This is a natural dry strength agent that is commonly used in the production of printing and writing papers. It is effective at low concentrations and can improve paper strength and stiffness.
- Polyacrylamide: This is a synthetic dry strength agent that is often used in the production of packaging papers. It can improve the paper's tensile strength, burst strength, and tear resistance.
- Carboxymethyl cellulose: This modified cellulose derivative used as a dry strength agent in the production of tissue and towel paper products. It can improve the paper's wet and dry strength, as well as its softness and absorbency.
The use of dry strength agents offers several benefits, including:
- Improved paper strength: Dry strength agents can improve the paper's tensile strength, tear resistance, and internal bonding strength, resulting in a stronger and more durable product.
- Increased paper quality: Using dry strength agents can improve the quality of paper products, particularly those that require high strength and durability.
- Reduced production costs: Using dry strength agents can reduce the amount of pulp needed to produce a given amount of paper, resulting in cost savings and reduced environmental impact.
However, the use of dry-strength agents also has some limitations and challenges. Overuse of dry strength agents can negatively impact the paper's flexibility and stiffness, and the type and quality of the dry strength agent used can affect the properties of the paper. Additionally, some dry-strength agents may be costly or difficult to source, and their effectiveness may vary depending on the pulp and paper produced.
Dry strength agents are an important type of additive used in paper manufacturing to improve the paper's strength and durability when dry. Dry strength agents offer several benefits, but their use must be carefully managed to ensure high-quality paper products and efficient and cost-effective production processes.
Defoamers
Defoamers are additives used in the paper manufacturing process to control or eliminate foam. Foam can be a problem in the papermaking process because it can interfere with equipment operation and reduce production efficiency.
Defoamers work by breaking down foam and preventing its formation. They are typically added to the paper pulp during the manufacturing process, and they can be classified into two main categories: silicone-based and non-silicone-based defoamers.
Silicone-based defoamers are the paper industry's most commonly used type of defoamer. They effectively reduce foam in both the pulp and papermaking processes and are typically added directly to the pulp.
Non-silicone-based defoamers are less commonly used and are typically added to the process water rather than the pulp. They are typically used when silicone-based defoamers are not suitable due to process or product requirements.
The use of defoamers offers several benefits, including:
- Improved production efficiency: Defoamers can help reduce foam-related downtime, increasing production efficiency.
- Improved product quality: Using defoamers can help prevent foam-related defects in the paper, resulting in higher-quality products.
- Reduced chemical usage: Defoamers can help to reduce the amount of chemicals needed to control foam, resulting in cost savings and reduced environmental impact.
However, the use of defoamers also has some limitations and challenges. Overuse of defoamers can negatively impact the paper's strength and other properties, and the type and quality of the defoamer used can affect the properties of the paper. Additionally, defoamers can be costly and may require specialized handling and storage.
Defoamers are an important type of additive used in paper manufacturing to control or eliminate foam. Defoamers offer several benefits, but their use must be carefully managed to ensure high-quality paper products and efficient and cost-effective production processes.
Dyes and Pigments
Dyes and pigments are additives used in paper manufacturing to impart color to the paper. The choice of dye or pigment depends on the desired color and the paper's properties.
Dyes are soluble substances that are typically used to color pulp fibers. They are added to the pulp during manufacturing and absorbed by the fibers, resulting in a uniform color throughout the paper.
On the other hand, pigments are insoluble particles that are added to the paper surface after forming. Pigments can be added to the paper coating or applied as a surface treatment to achieve the desired color and appearance.
The use of dyes and pigments offers several benefits, including:
- Increased product appeal: Using dyes and pigments can enhance the appearance of paper products, making them more visually appealing to consumers.
- Enhanced printing quality: Dyes and pigments can improve the printability of paper products by providing a more uniform surface for ink to adhere to.
- Customization: The use of dyes and pigments allows for customization of paper products to meet specific customer requirements.
However, the use of dyes and pigments also has some limitations and challenges. The quality and stability of the color can be affected by the type of dye or pigment used, the manufacturing process, and the storage conditions. Additionally, some dyes and pigments can be costly or difficult to source, and their use can increase the environmental impact of paper production.
Dyes and pigments are important additives used in paper manufacturing to impart color and enhance the appearance of paper products. The use of dyes and pigments offers several benefits, but their use must be carefully managed to ensure high-quality paper products and efficient and cost-effective production processes.
Benefits of Using Additives in Paper Manufacturing
Additives play a critical role in paper manufacturing, as they can enhance the properties of paper and ensure its quality. Some of the benefits of using additives in paper manufacturing include:
- Improved optical properties: Fillers can improve the brightness, opacity, and whiteness of paper, while dyes and pigments can add color and vibrancy.
- Increased strength and stiffness: Wet strength agents, dry strength agents, and fillers can improve the strength and stiffness of paper, making it more durable and resistant to stress.
- Enhanced printability: Sizing agents can improve the ink receptivity of paper, making it easier to print on and improving the quality of printed images.
- Reduced production cost: Fillers can reduce the cost of paper production by replacing some of the more expensive fibers with less expensive materials. Retention aids can reduce fiber and filler loss, saving money on raw materials.
- Improved environmental performance: Additives can improve the environmental performance of paper by reducing the amount of raw materials required, increasing the efficiency of the papermaking process, and improving the recyclability and biodegradability of paper.
Challenges and Limitations of Using Additives in Paper Manufacturing
While additives offer many benefits to the paper manufacturing process, they also pose several challenges and limitations. Some of the challenges and limitations of using additives in paper manufacturing include:
- Cost: Some additives can be expensive, increasing the cost of paper production.
- Compatibility: Additives may not be compatible with other papermaking chemicals, resulting in reduced effectiveness or even harm to the papermaking process.
- Environmental impact: Some additives can have a negative environmental impact, such as fillers that may not be biodegradable or sizing agents that may contain harmful chemicals.
- Health and safety concerns: Some additives, such as formaldehyde-based resins, can pose health and safety risks to workers in the paper manufacturing industry.
- Quality control: Additives can affect the properties of paper in unpredictable ways, making it difficult to ensure consistent quality and performance.
- Regulatory requirements: Some additives may be subject to regulatory requirements, such as restrictions on the use of certain chemicals or limits on the amount of additives that can be used in paper products.
How can Deskera Help You?
Deskera's integrated financial planning tools allow investors to better plan their investments and track their progress. It can help investors make decisions faster and more accurately.
Deskera Books can assist you in automating your accounting and mitigating business risks. Deskera makes it easier to create invoices by automating many other procedures, reducing your team's administrative workload.
Deskera also offers a suite of integrated applications to help businesses manage their financials, inventory, and operations. Furthermore, other business aspects such as HR (Deskera People), CRM (Deskera CRM), and ERP are provided by Deskera. These could be crucial and can help short sellers keep track of their businesses and make better decisions.
Conclusion
Additives play a critical role in the manufacturing of paper products, as they can enhance the properties and performance of paper and ensure its quality. The choice of additives depends on a variety of factors, including the desired properties of the paper, the raw materials used, and the production process. While additives offer many benefits, they also pose several challenges and limitations, such as cost, compatibility, environmental impact, health and safety concerns, quality control, and regulatory requirements. Paper manufacturers must carefully consider these factors when choosing and using additives in order to ensure that they produce high-quality paper products that meet the needs of their customers while minimizing their impact on the environment and ensuring the health and safety of their workers.
Related Articles
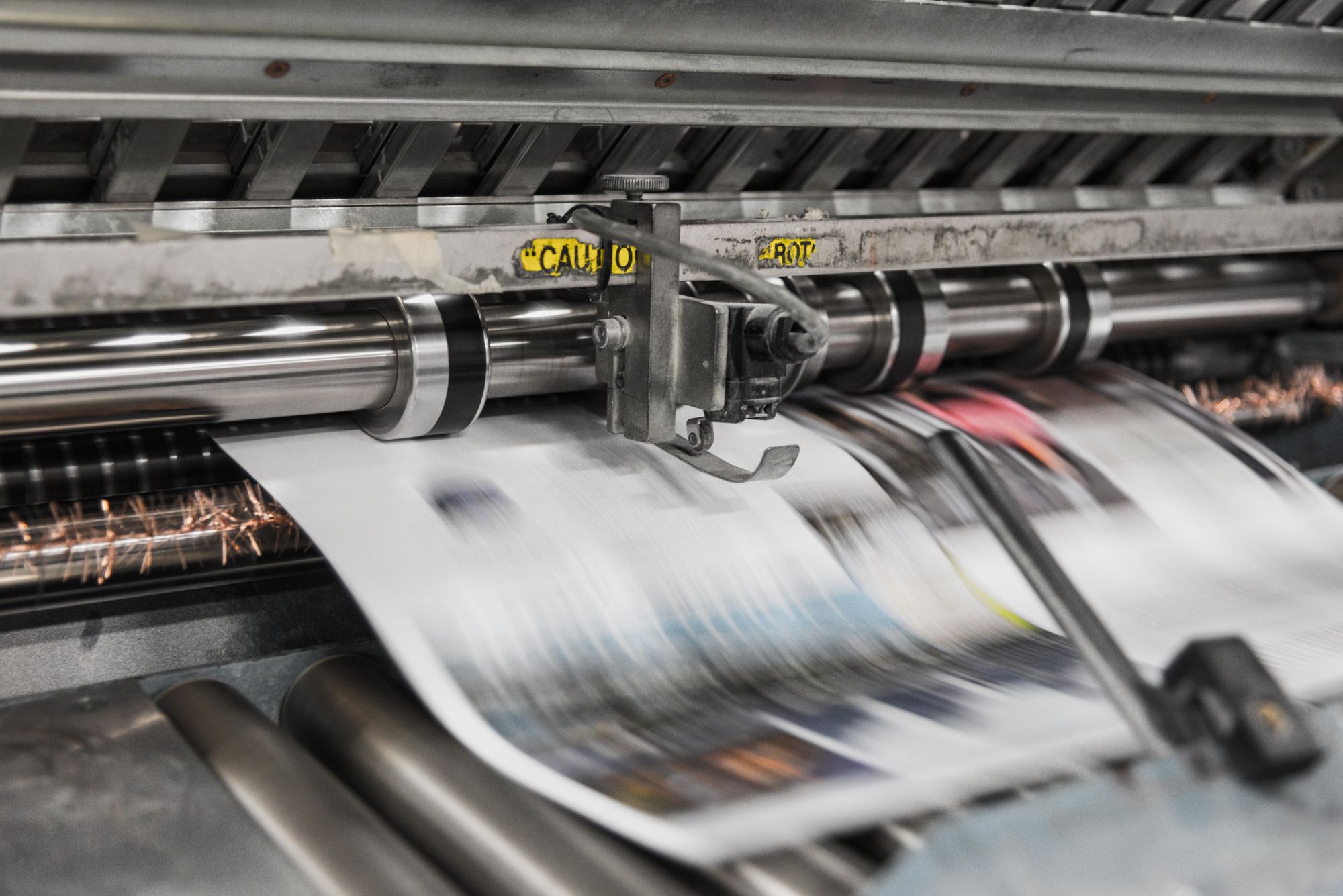
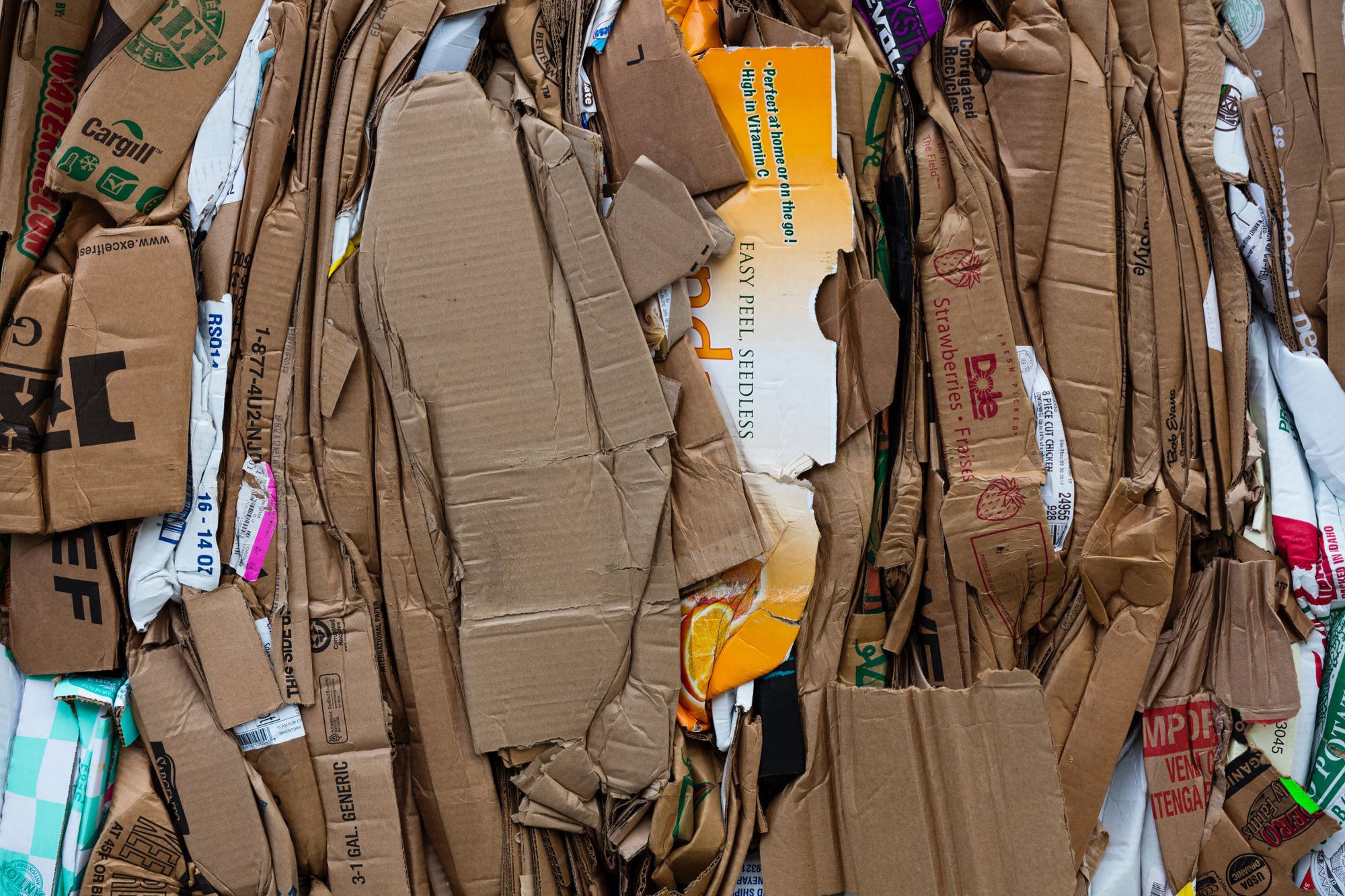
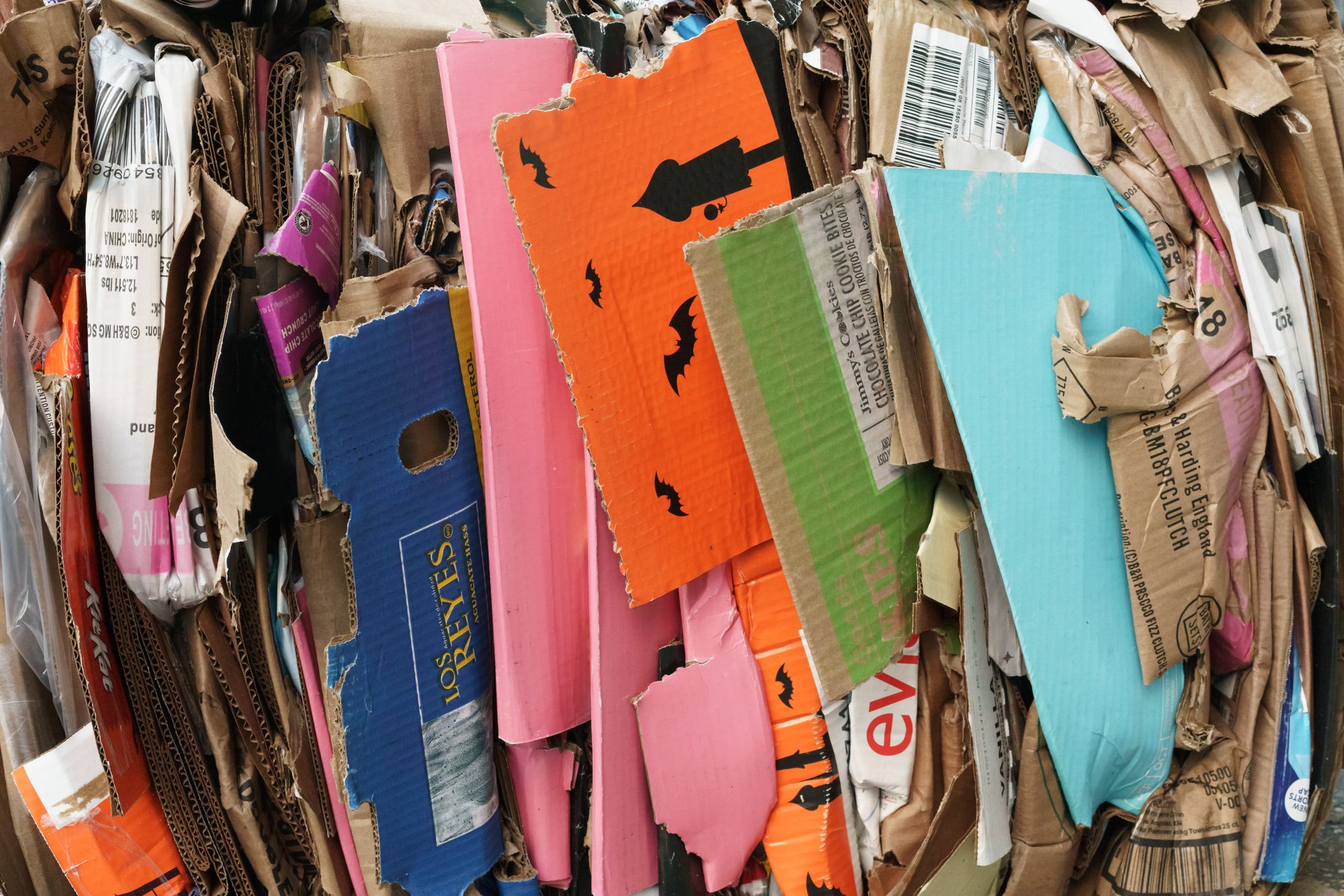