Plastic injection molding is a manufacturing process used to produce a wide range of plastic parts and components. It involves melting plastic pellets and injecting them into a mold cavity, where they are cooled and solidified to form the desired shape.
The process begins with the selection of the appropriate plastic material, which is typically chosen based on its physical properties, such as strength, stiffness, and heat resistance. The plastic pellets are then fed into a heated barrel, where they are melted and mixed with other additives, such as colorants or reinforcing fibers.
The molten plastic is then injected under high pressure into a mold cavity, which is typically made of steel and has the desired shape of the final part. The mold is held closed under pressure until the plastic has solidified and cooled sufficiently to be ejected from the mold.
The injection molding process can be used to produce a wide range of plastic parts, from small, intricate components to large, complex structures. It is a highly efficient and repeatable process, making it ideal for high-volume production of plastic parts.
In this article, we will explore the benefits of plastic injection molding for manufacturing in detail:
- Cost-effectiveness
- High precision and accuracy
- Wide range of materials
- Fast cycle times
- Design flexibility
- Low scrap rates
- Repeatable and consistent results
- Reduced labor costs
- Reduced post-processing requirements
- Environmental benefits
- Ability to incorporate specific features
- How can Deskera Help You?
- Conclusion
- Related Articles
Cost-effectiveness
Cost-effectiveness is one of the primary advantages of plastic injection molding for manufacturing. Although the initial investment in tooling and molds can be expensive, the per-unit cost of producing plastic parts decreases significantly as production volume increases.
This is because the cost of tooling and molds is spread over a larger number of parts, reducing the per-unit cost. Additionally, injection molding can be highly automated, reducing labor costs and increasing production efficiency.
Another factor that contributes to the cost-effectiveness of injection molding is the low scrap rate. The process is highly controlled, and material usage is optimized, resulting in minimal waste material. This can reduce material costs and disposal costs.
Finally, injection molding allows for the production of highly precise and accurate parts, reducing the need for post-processing, such as trimming or sanding. This can save time and labor costs, further contributing to the cost-effectiveness of the process.
The cost-effectiveness of injection molding makes it an ideal method for high-volume manufacturing applications, where the initial investment in tooling and molds can be amortized over a large number of parts, resulting in significant cost savings.
High precision and accuracy
High precision and accuracy are among the key advantages of plastic injection molding for manufacturing. The process is highly controlled, allowing for tight tolerances and consistent quality from one part to the next.
The molds used in injection molding can be designed to achieve precise and complex geometries, allowing for the production of highly precise and accurate parts. The molds can also be designed to incorporate features such as threads, undercuts, and inserts, further increasing the precision and accuracy of the parts produced.
Additionally, injection molding machines can operate at high speeds, allowing for rapid production of large volumes of parts with consistent quality. This makes it an ideal method for high-volume manufacturing applications where precision and accuracy are critical.
The high precision and accuracy of plastic injection molding make it a popular method for producing complex, high-quality plastic parts that require precise tolerances and consistent quality.
Wide range of materials
Another advantage of plastic injection molding for manufacturing is the wide range of materials that can be used in the process. Injection molding can accommodate a wide range of plastic materials, including thermoplastics, thermosets, and elastomers, which offer a variety of physical and chemical properties.
Different materials can be chosen based on the specific requirements of the application. For example, if a part requires high strength and stiffness, a reinforced thermoplastic such as nylon or polycarbonate may be chosen. If a part requires high heat resistance, a thermoset material such as phenolic or epoxy may be chosen.
In addition, the choice of material can affect the manufacturing process itself. For example, some materials may require higher injection pressure or longer cooling times, which can affect the cycle time and cost of production.
Overall, the wide range of materials that can be used in plastic injection molding makes it a versatile and flexible method for producing plastic parts that can meet a wide range of requirements.
Fast cycle times
Fast cycle times are another advantage of plastic injection molding for manufacturing. Injection molding machines can operate at high speeds, allowing for rapid production of large volumes of parts.
The cycle time for injection molding typically includes four stages: clamping, injection, cooling, and ejection. The cooling stage can be the most time-consuming, as the part must be allowed to cool and solidify before it can be ejected from the mold. However, the cooling time can be reduced by using cooling channels within the mold or by using a mold with better heat transfer properties.
Fast cycle times are particularly beneficial for high-volume manufacturing applications, where a large number of parts must be produced quickly and efficiently. This can result in faster time-to-market, increased productivity, and lower per-unit costs.
The fast cycle times of plastic injection molding make it an efficient method for producing large volumes of plastic parts with consistent quality and precision.
Design flexibility
Design flexibility is another key advantage of plastic injection molding for manufacturing. The process allows for a high degree of design freedom and flexibility, enabling the production of complex and intricate parts with precise geometries.
Injection molding allows for the creation of parts with a wide range of shapes, sizes, and configurations. The molds used in the process can be designed to incorporate features such as undercuts, internal threads, and intricate surface textures, which can be difficult or impossible to produce using other manufacturing methods.
Additionally, injection molding allows for the production of multi-component parts or assemblies in a single operation, further increasing design flexibility. This can result in a reduction in assembly time and costs, as well as improved part performance and functionality.
The flexibility of injection molding also allows for design changes to be easily incorporated into the production process. Molds can be modified or replaced to accommodate design changes, allowing for rapid iteration and improvement of the part design.
The design flexibility of plastic injection molding makes it a popular method for producing complex, high-quality plastic parts that require precise geometries and intricate features. The ability to produce parts with a high degree of design freedom and flexibility allows for the creation of innovative and customized products that meet the specific needs of customers.
Low scrap rates
Low scrap rates are another advantage of plastic injection molding for manufacturing. The process is highly controlled, and material usage is optimized, resulting in minimal waste material.
During the injection molding process, the material is melted and injected into the mold, filling all the cavities and creating the desired part. The process is highly automated, which ensures consistency and accuracy from one part to the next.
The optimization of material usage in injection molding helps to minimize scrap rates. The molds are designed to ensure that the material is distributed evenly and that there are no air pockets or other defects in the part. This helps to ensure that the parts are produced with a high level of accuracy and precision.
In addition, the process allows for the use of regrind, which is the recycled material from previous runs. This can help to reduce material waste and lower production costs
.
The low scrap rates of plastic injection molding make it an efficient method for producing high-quality plastic parts with minimal waste material. The process allows for the optimization of material usage, ensuring that the parts produced are of consistent quality and accuracy, while minimizing the amount of material that goes to waste.
Repeatable and consistent results
Repeatable and consistent results are another key advantage of plastic injection molding for manufacturing. The process is highly controlled and automated, which helps to ensure that the parts produced are of consistent quality and accuracy.
The injection molding process involves several stages, including clamping, injection, cooling, and ejection. Each stage is precisely controlled, allowing for consistent and repeatable results from one part to the next
.
The molds used in injection molding are designed to ensure that the material is distributed evenly, and that there are no air pockets or other defects in the part. This helps to ensure that the parts produced are of consistent quality and accuracy.
Additionally, injection molding machines are highly automated, with the ability to monitor and adjust the process parameters in real-time. This allows for rapid adjustments to be made to the process, ensuring that the parts produced are of consistent quality and accuracy.
The repeatable and consistent results of plastic injection molding make it an efficient method for producing high-quality plastic parts. The highly controlled and automated nature of the process ensures that the parts produced are of consistent quality and accuracy, with minimal variation from one part to the next. This helps to reduce the need for post-processing and inspection, further reducing the overall production time and cost.
Reduced labor costs
Reduced labor costs are another advantage of plastic injection molding for manufacturing. The process is highly automated, with minimal labor required to operate the machines and produce the parts.
Injection molding machines are highly automated and require minimal manual labor to operate. Once the molds have been set up, the process can run without the need for human intervention, except for periodic quality checks and maintenance.
The highly automated nature of the process also helps to reduce the need for post-processing and inspection. The parts produced by injection molding are typically of consistent quality and accuracy, with minimal variation from one part to the next. This helps to reduce the need for manual inspection and sorting, further reducing labor costs.
Additionally, injection molding allows for the production of large volumes of parts in a relatively short amount of time. This helps to increase productivity and reduce the overall labor cost per part.
The reduced labor costs of plastic injection molding make it an efficient method for producing high-quality plastic parts. The highly automated nature of the process reduces the need for manual labor and post-processing, while allowing for the production of large volumes of parts in a short amount of time. This helps to reduce the overall cost of production, making injection molding a cost-effective solution for many manufacturing applications.
Reduced post-processing requirements
Reduced post-processing requirements are another advantage of plastic injection molding for manufacturing. The process produces parts that are typically of high quality and accuracy, with minimal variation from one part to the next, reducing the need for extensive post-processing.
Injection molding allows for the production of parts with precise geometries and intricate features, without the need for extensive machining or finishing operations. The molds used in the process are designed to create parts with smooth surfaces and precise dimensions, minimizing the need for post-processing operations such as sanding, polishing, or painting.
Additionally, injection molding can produce parts with a wide range of surface finishes, including textured, matte, and glossy finishes. This eliminates the need for additional surface treatment or finishing operations.
The reduced post-processing requirements of injection molding not only reduce the overall production time but also help to lower production costs. By eliminating the need for additional finishing operations, injection molding can help to reduce the cost of labor and materials, making it a cost-effective solution for many manufacturing applications.
The reduced post-processing requirements of plastic injection molding make it an efficient method for producing high-quality plastic parts. The process produces parts with precise geometries and a wide range of surface finishes, reducing the need for additional finishing operations and minimizing the overall production time and cost.
Environmental benefits
There are several environmental benefits of plastic injection molding for manufacturing.
First, injection molding can help to reduce material waste. The process is highly controlled, with material usage optimized to minimize waste. Additionally, the molds used in injection molding are designed to create parts with minimal material usage, reducing the amount of waste generated.
Second, injection molding can help to reduce energy consumption. The process uses less energy compared to other manufacturing methods, such as machining or casting. Additionally, some injection molding machines are designed to be energy-efficient, reducing the overall energy consumption of the process.
Third, injection molding can be used with a wide range of recyclable materials, such as polypropylene, polystyrene, and PET. These materials can be recycled and reused, reducing the need for virgin materials and lowering the overall environmental impact of the manufacturing process.
Finally, injection molding can help to reduce transportation emissions. The process can be used to produce parts on-site, reducing the need for transportation of finished parts and raw materials.
The environmental benefits of plastic injection molding make it an efficient and sustainable method for manufacturing high-quality plastic parts. The process minimizes material waste, reduces energy consumption, promotes the use of recyclable materials, and can help to reduce transportation emissions.
Ability to incorporate specific features
One of the key advantages of plastic injection molding for manufacturing is the ability to incorporate features such as threads, hinges, and inserts directly into the part during the molding process. This is known as "molded-in features."
Molded-in features are created by designing the mold with the desired feature built-in. This allows for the creation of parts with integrated components, reducing the need for additional assembly steps and improving part performance.
For example, molded-in threads can be created directly in the part during the molding process, eliminating the need for post-molding operations such as tapping or ultrasonic welding. Similarly, molded-in hinges can create a more reliable and durable hinge compared to other methods of attachment.
Injection molding also allows for the incorporation of inserts directly into the part during the molding process. Inserts are pre-fabricated metal or plastic components that are placed in the mold before the plastic material is injected. The plastic material flows around the insert, creating a secure and reliable attachment.
The ability to incorporate features such as threads, hinges, and inserts directly into the part during the molding process improves the quality and reliability of the final product. It also reduces the need for additional assembly steps, lowering production costs and improving efficiency.
The ability to incorporate molded-in features is a major advantage of plastic injection molding for manufacturing. It allows for the creation of parts with integrated components, improving part performance and reducing assembly time and costs.
How can Deskera Help You?
Deskera's integrated financial planning tools allow investors to better plan their investments and track their progress. It can help investors make decisions faster and more accurately.
Deskera Books can assist you in automating your accounting and mitigating business risks. Deskera makes it easier to create invoices by automating many other procedures, reducing your team's administrative workload.
Deskera also offers a suite of integrated applications to help businesses manage their financials, inventory, and operations. Furthermore, other business aspects such as HR (Deskera People), CRM (Deskera CRM), and ERP are provided by Deskera. These could be crucial and can help short sellers keep track of their businesses and make better decisions.
Conclusion
Here are the main points of the benefits of plastic injection molding for manufacturing:
- Cost-effective for high volume production runs
- High efficiency and fast production rates
- High precision and accuracy in product design and manufacturing
- Versatile in terms of material options and product design
- Low waste and scrap production
- Consistent quality and repeatability in product manufacturing
- Environmentally friendly with the use of recycled materials and reduced waste
- Ability to create complex shapes and designs
- Low labor costs and automation options for increased efficiency
- Flexibility in production runs and customization options
Overall, plastic injection molding offers numerous benefits for manufacturing in terms of cost-effectiveness, efficiency, precision, versatility, sustainability, and design flexibility.
Related Articles
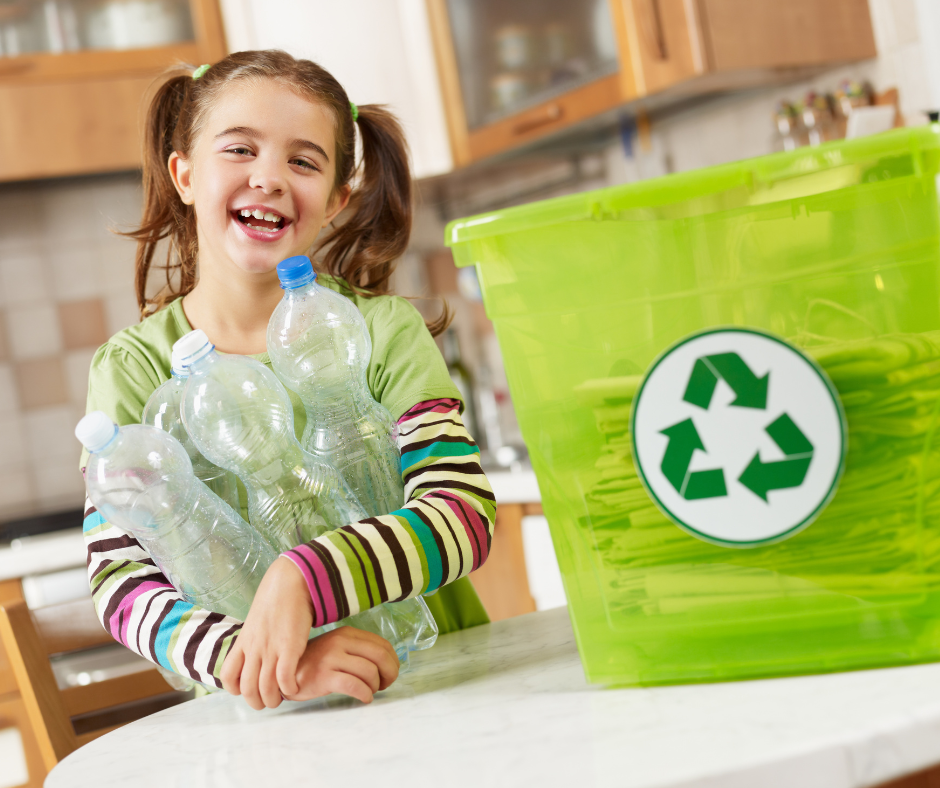
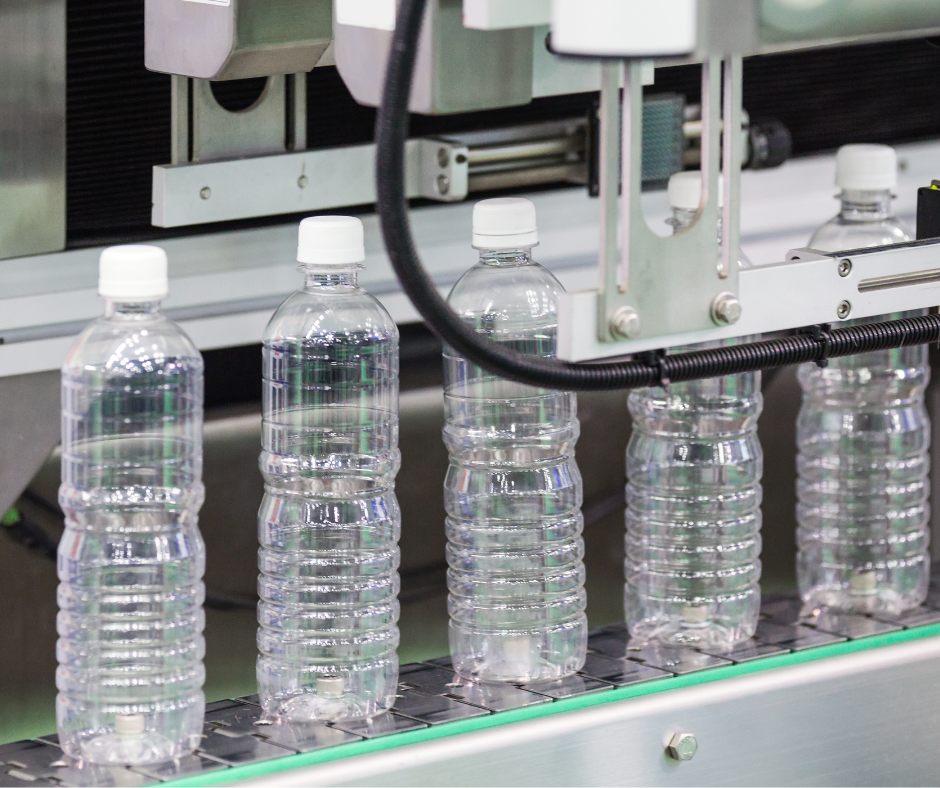
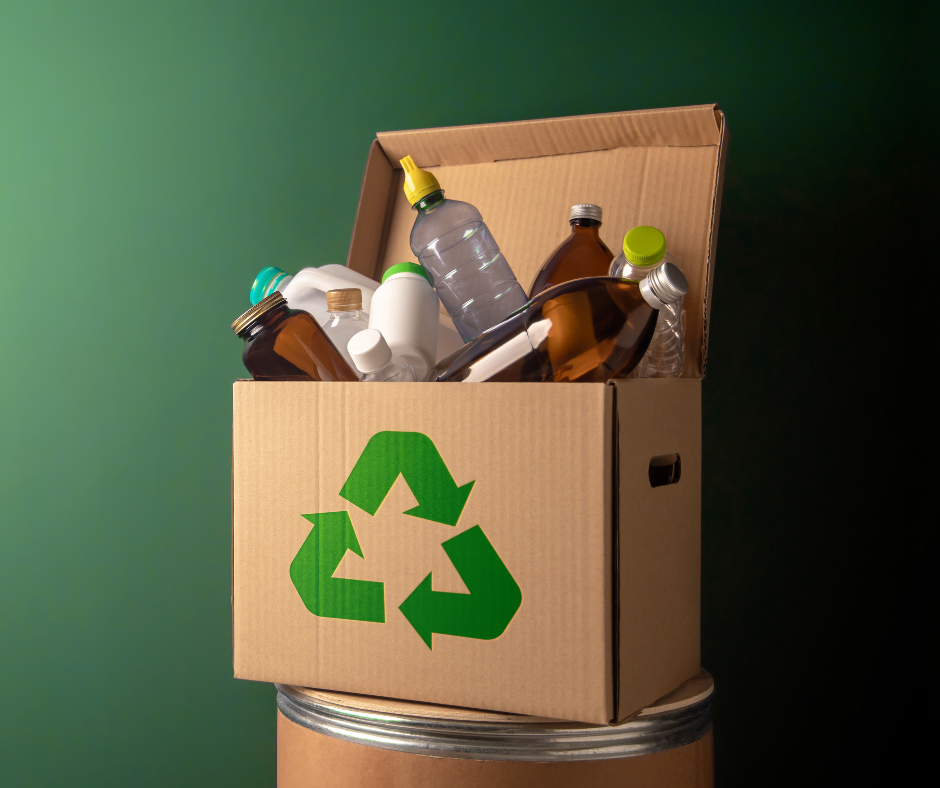