The plastics's invasion of the planet is a reality. Just think about it, the island of floating plastic debris in the Pacific Ocean now covers 1.6 million km. The moment has arrived for every one of us to act if we want to save the earth.
Plastics are clearly causing the planet major problems, and we can change this by taking action. Our lives now revolve almost exclusively around plastic.
It's everywhere: product packaging, cosmetic chemicals, textiles, mobile phones, etc. You might even be chewing gum right now that contains it! Because of its pervasiveness, many people would find it challenging to give it up altogether. So, reducing the use of plastics necessitates a change in habits and a shift in perspective.
From both an environmental point of view as well as a commercial standpoint, the plastic manufacturing process has to be reviewed continuously. This is why reducing waste and maximizing efficiency in plastic production is crucial.
In this article, we will look more into:
- Why is Reducing Waste and Maximizing Efficiency in Plastic Production Important?
- Strategies to Reduce Waste and Maximize Efficiency in Plastic Production
- Material Selection
- Lean Manufacturing
- Process Optimization
- Automation
- Recycling
- Energy Efficiency
- Supplier Partnerships
- Training and Education
- Continuous Improvement
- How can Deskera Help You?
- Conclusion
- Related Articles
Why is Reducing Waste and Maximizing Efficiency in Plastic Production Important?
Reducing waste and maximizing efficiency in plastic production is important for several reasons:
- Environmental impact: Plastic waste is a major contributor to environmental pollution, including marine litter and landfills. By reducing waste, less plastic ends up in the environment and ecosystems, protecting wildlife and preventing harm to the natural world.
- Resource conservation: Plastic production requires significant amounts of fossil fuels, energy, and other resources like water. By maximizing efficiency, fewer resources are needed to produce the same amount of plastic, reducing the strain on natural resources and energy systems.
- Economic benefits: Reducing waste and maximizing efficiency can also save plastic manufacturers' costs. By minimizing waste and using resources more efficiently, companies can reduce their operational costs and increase profitability.
- Sustainability: As consumers and businesses become more environmentally conscious, there is a growing demand for sustainable products and practices. Reducing waste and maximizing efficiency in plastic production can help companies meet this demand and improve their reputation as socially responsible and sustainable businesses.
Reducing waste and maximizing efficiency in plastic production is important for protecting the environment, conserving resources, achieving cost savings, and promoting sustainability.
Strategies to Reduce Waste and Maximize Efficiency in Plastic Production
Here are some strategies that can be employed to reduce waste and maximize efficiency in plastic production :
Material Selection
Material selection is a critical factor in reducing waste and maximizing efficiency in plastic production. By choosing raw materials that can be easily recycled or reused, companies can reduce waste and improve the sustainability of their production processes. Here are some tips for material selection:
- Choose recyclable materials: Select materials that are easily recyclable and have a high recycling rate. For example, polyethylene terephthalate (PET) is a commonly used plastic that can be easily recycled.
- Select biodegradable materials: Consider using biodegradable materials that can break down over time and reduce environmental impact.
- Choose materials with a longer lifespan: Select materials that are durable and have a longer lifespan, reducing the need for replacement.
- Consider post-consumer recycled content: Choose materials that contain post-consumer recycled content to reduce waste and increase sustainability.
- Avoid hazardous materials: Avoid materials that contain hazardous chemicals or are difficult to dispose of.
By selecting materials that are easy to recycle or biodegradable, companies can reduce the environmental impact of their production processes. Choosing materials with a longer lifespan and post-consumer recycled content can also reduce waste and improve sustainability.
Lean Manufacturing
Lean manufacturing is a methodology that focuses on reducing waste, increasing efficiency, and optimizing production processes. The goal of lean manufacturing is to eliminate any activities that do not add value to the production process, and to continually improve the processes over time. Here are some key principles of lean manufacturing:
- Value: Define value from the customer's perspective and focus on delivering that value.
- Value Stream Mapping: Map out the entire production process to identify waste and inefficiencies.
- Flow: Eliminate bottlenecks and interruptions in the production process to improve flow.
- Pull: Use a pull system to produce products only when they are needed, reducing inventory and waste.
- Perfection: Continuously strive for perfection by making small, incremental improvements to the production process.
By implementing lean manufacturing principles, companies can reduce waste and optimize production processes, leading to increased efficiency, reduced costs, and improved quality. Lean manufacturing can also help companies identify improvement areas and foster a continuous improvement culture.
Process Optimization
Process optimization is the act of analyzing and improving production processes to increase efficiency, reduce waste, and improve quality. The goal is to identify and eliminate any activities that do not add value to the production process, and to improve the operations over time continually. Here are some steps that companies can take to optimize their production processes:
- Map out the process: Map out the entire production process to identify areas of waste and inefficiency.
- Analyze the process: Analyze the process to identify bottlenecks, unnecessary steps, and other sources of waste.
- Set goals: Set goals for improving the process, such as reducing cycle time, increasing throughput, or improving quality.
- Implement changes: Implement changes to the process to eliminate waste and improve efficiency.
- Monitor performance: Monitor the performance of the process to track progress towards goals and identify areas for further improvement.
- Continuously improve: Continuously improve the process by making small, incremental changes over time.
Companies can reduce waste, increase efficiency, and improve quality by optimizing production processes. This can lead to cost savings, improved customer satisfaction, and a competitive advantage in the marketplace.
Automation
Automation refers to the use of technology and machinery to perform tasks and processes without human intervention. In the context of plastic production, automation can be used to increase efficiency, reduce labor costs, and improve product quality. Here are some examples of how automation can be used in plastic production:
- Injection molding: Automated injection molding machines can be used to produce plastic parts quickly and consistently, with minimal human intervention.
- Material handling: Automated material handling systems can be used to transport raw materials, finished products, and waste materials throughout the production facility, reducing the need for manual labor.
- Quality control: Automated quality control systems can be used to inspect and test plastic products for defects and ensure they meet specifications.
- Assembly: Automated assembly systems can be used to assemble plastic parts into finished products, reducing labor costs and improving efficiency.
- Packaging: Automated packaging systems can be used to package plastic products quickly and efficiently, reducing the need for manual labor.
Companies can increase efficiency, reduce labor costs, and improve product quality by implementing automation in plastic production processes. However, automation also requires significant upfront investment and may require retraining of workers.
Recycling
Recycling is the process of converting waste materials into new products, typically to prevent the waste of potentially useful materials and reduce the consumption of raw materials. In the context of plastic production, recycling can help reduce waste and conserve natural resources. Here are some examples of how recycling can be used in plastic production:
- Recycled plastic pellets: Recycled plastic pellets can be used as a raw material in producing new plastic products, reducing the need for virgin materials.
- Post-consumer recycled content: Plastic products can be made with post-consumer recycled content, which is plastic that has been recovered and processed from consumer waste.
- Closed-loop recycling: In a closed-loop recycling system, plastic products are collected and recycled into new products at the end of their useful life, reducing waste and conserving resources.
- Energy recovery: Some plastics that cannot be recycled can be used as a source of energy through incineration or other methods.
By incorporating recycling into plastic production processes, companies can reduce waste, conserve resources, and demonstrate their commitment to sustainability. However, recycling also requires infrastructure for collection and processing, and there may be limitations on the types of plastics that can be recycled effectively.
Energy Efficiency
Energy efficiency refers to using less energy to perform the same task or achieve the same output level. In the context of plastic production, energy efficiency can help reduce energy consumption, lower costs, and reduce greenhouse gas emissions. Here are some examples of how energy efficiency can be improved in plastic production:
- Lighting and HVAC systems: Upgrading lighting and HVAC systems to more energy-efficient technologies can reduce energy consumption in the production facility.
- Equipment efficiency: Upgrading production equipment to more energy-efficient models can reduce energy consumption during the production process.
- Process optimization: Optimizing production processes to reduce energy consumption and waste can lead to significant energy savings.
- Renewable energy: Installing renewable energy sources such as solar or wind power can provide clean energy and reduce reliance on fossil fuels.
By improving energy efficiency in plastic production processes, companies can lower costs, reduce their environmental impact, and improve their reputation with environmentally conscious consumers. However, improving energy efficiency may require upfront investments in new equipment or infrastructure, and there may be limitations on the types of energy-saving measures that can be implemented in some production facilities.
Supplier Partnerships
Supplier partnerships refer to the collaboration between companies and their suppliers to improve efficiency, quality, and sustainability in the supply chain. In the context of plastic production, supplier partnerships can help streamline processes, reduce waste, and improve the environmental performance of the supply chain. Here are some examples of how supplier partnerships can be used in plastic production:
- Collaboration on product design: Companies can work with their suppliers to develop more sustainable, efficient, and cost-effective products.
- Just-in-time delivery: Suppliers can work with companies to provide materials and components on a just-in-time basis, reducing inventory costs and waste.
- Waste reduction and recycling: Suppliers can work with companies to reduce waste and increase recycling in the supply chain, leading to cost savings and environmental benefits.
- Supplier assessment and selection: Companies can assess and select suppliers based on their environmental and social performance, incentivizing suppliers to improve their sustainability practices.
By working closely with their suppliers, companies can improve their plastic production processes' efficiency, quality, and sustainability. However, supplier partnerships require trust, communication, and cooperation between companies and their suppliers and may require significant investment in supplier assessment and development.
Training and Education
Training and education are important aspects of reducing waste and maximizing efficiency in plastic production. Here are some examples of how training and education can help improve the performance of plastic production processes:
- Employee training: Training employees on best practices for plastic production processes, including waste reduction and energy efficiency, can improve performance and reduce waste.
- Continuous improvement programs: Implementing continuous improvement programs that encourage employees to identify and solve problems can help identify opportunities for waste reduction and efficiency improvements.
- Environmental and sustainability training: Providing training on environmental and sustainability issues can increase employee awareness and help drive changes in behavior and practices.
- Industry certification programs: Participation in industry certification programs, such as ISO 14001 for environmental management, can provide a framework for improving sustainability performance and reducing waste.
By investing in employee training and education and participating in industry certification programs, companies can improve their performance in plastic production processes, reduce waste, and improve their environmental performance. However, training and education require significant investment in time and resources and may require effective changes in company culture and practices.
Continuous Improvement
Continuous improvement is a philosophy and process that aims to constantly improve a business or organization's performance. It involves identifying areas for improvement, developing strategies to address them, and implementing changes to improve processes, products, and services. In the context of plastic production, continuous improvement can help reduce waste, improve efficiency, and enhance sustainability performance. Here are some examples of how continuous improvement can be applied in plastic production processes:
- Process optimization: Continuously monitoring and analyzing plastic production processes can help identify areas for improvement, such as reducing waste, improving energy efficiency, or increasing production rates.
- Lean manufacturing: Implementing lean manufacturing principles, such as just-in-time delivery, kanban systems, and value stream mapping, can help identify waste in production processes and develop strategies to eliminate it.
- Employee involvement: Encouraging employee involvement in identifying areas for improvement and implementing changes can help drive continuous improvement efforts and improve engagement and morale.
- Benchmarking: Comparing the performance of plastic production processes against industry benchmarks or best practices can help identify areas for improvement and develop strategies to address them.
By implementing continuous improvement programs, companies can identify opportunities to reduce waste, improve efficiency, and enhance sustainability performance in plastic production processes. However, continuous improvement requires commitment from management and employees, and may require significant investment in time and resources to be effective.
In keeping with the environmental pressures, companies constantly need to improve the manufacturing process, which is where ERP software can play a significant role.
How can Deskera Help You?
Deskera's integrated financial planning tools allow investors to better plan their investments and track their progress. It can help investors make decisions faster and more accurately.
Deskera Books can assist you in automating your accounting and mitigating business risks. Deskera makes it easier to create invoices by automating many other procedures, reducing your team's administrative workload.
Deskera also offers a suite of integrated applications to help businesses manage their financials, inventory, and operations. Furthermore, other business aspects such as HR (Deskera People), CRM (Deskera CRM), and ERP are provided by Deskera. These could be crucial and can help short sellers keep track of their businesses and make better decisions.
Conclusion
Here are some strategies that can be employed:
- Material selection: Choose raw materials that can be easily recycled or reused.
- Lean manufacturing: Implement lean manufacturing principles to reduce waste and optimize efficiency.
- Process optimization: Analyze production processes to identify areas of waste and inefficiency, then implement process improvements.
- Automation: Implement automation to reduce human error and increase production speed.
- Recycling: Implement recycling programs to reduce waste and reuse materials.
- Energy efficiency: Implement energy-efficient equipment and processes to reduce energy consumption.
- Supplier partnerships: Work with suppliers to reduce waste and increase efficiency throughout the supply chain.
- Training and education: Provide training and education to employees to improve their skills and reduce errors.
- Continuous improvement: Foster a culture of continuous improvement to identify and address inefficiencies over time.
Related Articles
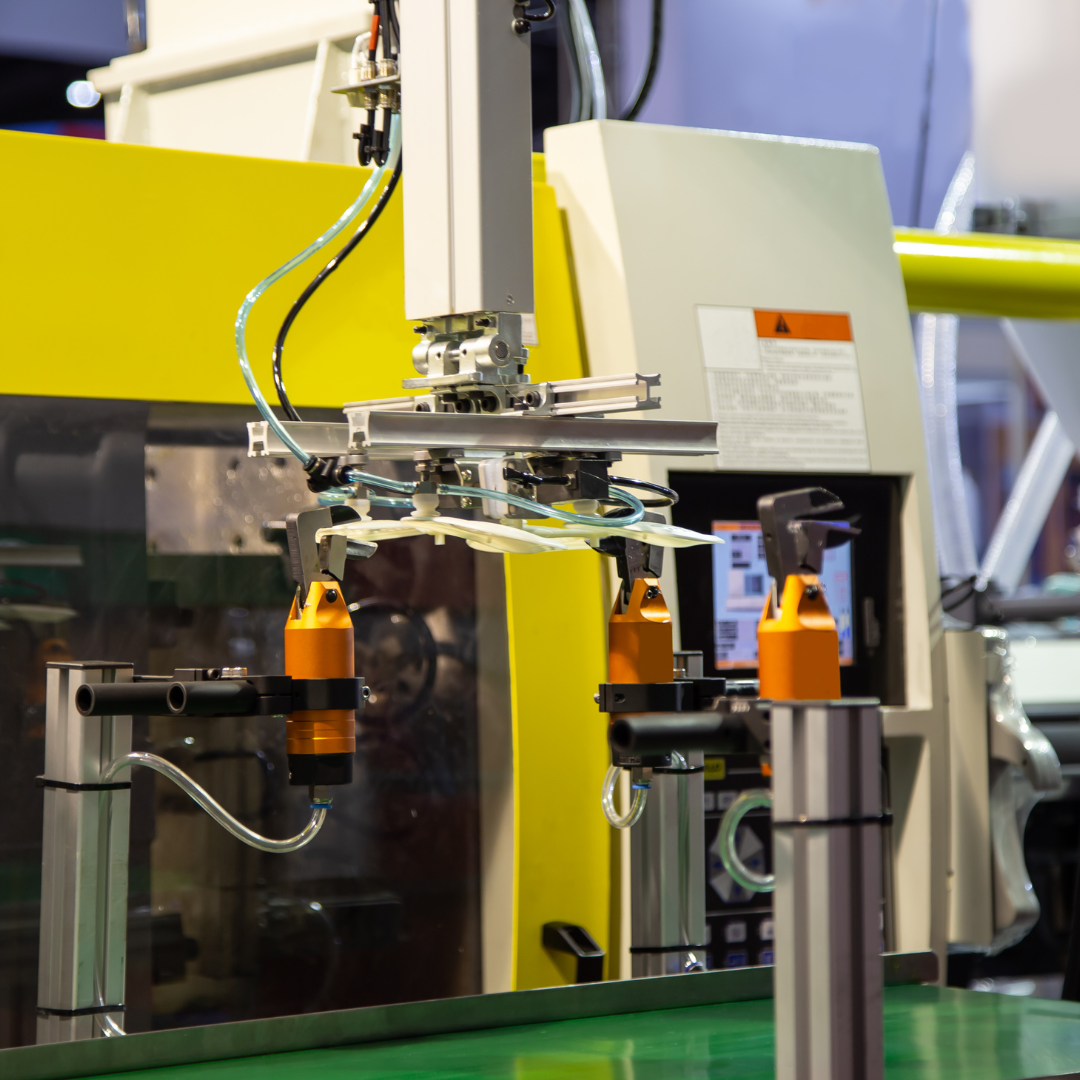
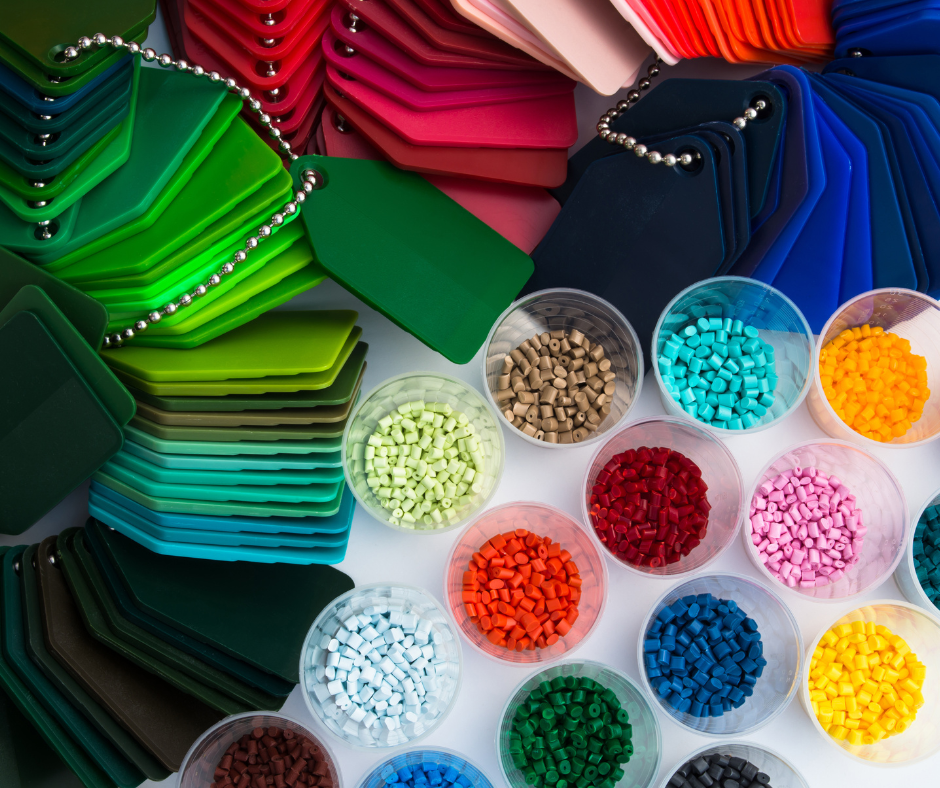
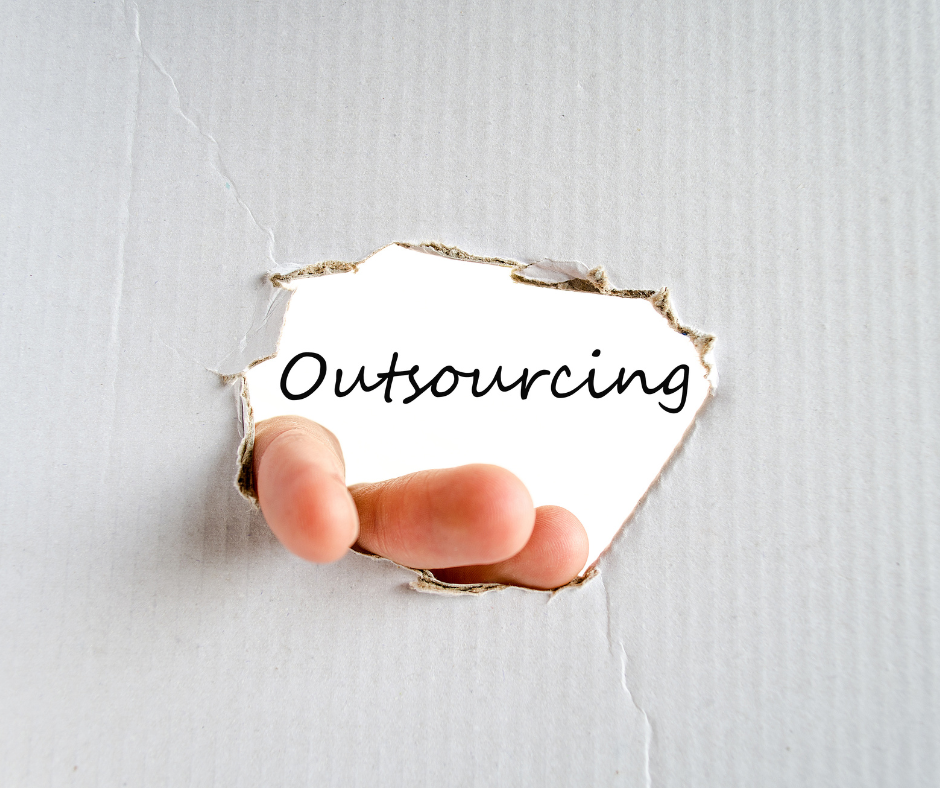