The manufacturing industry has never been more focused on efficiency than it is today. This is especially true in North America, where higher business costs put many manufacturers at a competitive disadvantage compared to global counterparts in China, India, and Indonesia.
How can North American manufacturers increase productivity while reducing waste to remain competitive in the global market?
Many people believe that the answer lies in a set of principles and practices known as lean manufacturing. In this article, we will explore more about:
- What is Lean Manufacturing?
- Advantages of Lean Manufacturing in Chemical Manufacturing
- Disadvantages of Lean Manufacturing in Chemical Manufacturing
- How can Deskera Help You?
- Conclusion
What is Lean Manufacturing?
Lean manufacturing is an approach to production that focuses on minimizing waste, improving efficiency, and maximizing customer value. It is a systematic and continuous improvement methodology emphasizing the importance of reducing waste and increasing efficiency in all aspects of production, including design, supply chain, production, and delivery.
Lean manufacturing is often associated with the Toyota Production System, which was developed in Japan in the 1940s and 1950s. The system was designed to improve production efficiency and reduce waste while also improving quality and increasing flexibility.
Some of the key principles of lean manufacturing include:
- Identifying and eliminating waste: Lean manufacturing seeks to identify and eliminate any unnecessary steps in the production process that do not add value for the customer. Examples of waste include excess inventory, overproduction, waiting time, unnecessary motion, and defects.
- Continuous improvement: Lean manufacturing is a continuous improvement process that involves regularly evaluating and refining the production process to improve efficiency and quality.
- Pull production: In a lean manufacturing system, production is based on customer demand, rather than forecasts or estimates. This helps to minimize waste and excess inventory.
- Flexibility: Lean manufacturing systems are designed to be flexible and adaptable to changing customer needs and production requirements.
- Empowering workers: Lean manufacturing involves empowering workers to identify and solve problems in the production process. This helps to improve efficiency and quality while also increasing employee engagement and satisfaction.
Lean manufacturing is a customer-focused approach to production that seeks to eliminate waste and maximize efficiency while also improving quality and flexibility. It is a continuous improvement process that requires ongoing evaluation and refinement to ensure the production process is as efficient and effective as possible.
Adopting a lean manufacturing approach in chemical manufacturing can have a number of advantages and disadvantages, both for the company and for its stakeholders. In this essay, we will explore the advantages and disadvantages of adopting a lean manufacturing approach in chemical manufacturing in detail.
Advantages of Lean Manufacturing in Chemical Manufacturing
Here are some of the advantages of lean manufacturing in chemical manufacturing:
Increased Efficiency
One of the primary advantages of adopting a lean manufacturing approach in chemical manufacturing is increased efficiency. Lean manufacturing techniques focus on identifying and eliminating waste, optimizing production processes, and streamlining operations. By implementing these principles, companies can improve the speed and efficiency of their production processes, resulting in faster turnaround times, reduced lead times, and improved on-time delivery.
In addition, lean manufacturing techniques can help reduce the amount of time and effort required to perform routine tasks, freeing up resources to focus on more strategic initiatives. This can lead to increased productivity and higher levels of output, without requiring additional resources or increasing the risk of errors.
Improved Quality
Another advantage of adopting a lean manufacturing approach in chemical manufacturing is improved quality. Lean manufacturing principles emphasize the importance of identifying and eliminating sources of defects and errors in production processes. By doing so, companies can produce higher-quality products that are less likely to be returned or recalled.
In addition, by focusing on quality at every stage of the production process, companies can reduce the risk of errors and defects, resulting in a higher degree of consistency and reliability in their products. This can improve customer satisfaction and help build a reputation for quality and reliability.
Reduced Costs
Lean manufacturing techniques can help reduce the cost of production in chemical manufacturing. By identifying and eliminating waste, companies can reduce the amount of time and resources required to produce a given product. This can lead to lower production costs, reduced inventory costs, and improved profitability.
In addition, lean manufacturing techniques can help companies reduce the cost of quality by identifying and eliminating sources of defects and errors. Companies can save money and improve their bottom line by reducing the number of returns, recalls, and other quality issues.
Increased Flexibility
Adopting a lean manufacturing approach can make it easier for chemical manufacturers to respond to changes in demand and adjust production schedules accordingly. By streamlining production processes and reducing the amount of time and effort required to produce a given product, companies can become more agile and responsive to changes in the market.
In addition, by implementing lean manufacturing principles, companies can improve their ability to predict and respond to changes in demand, reducing the risk of overproduction or underproduction.
Improved Safety
Lean manufacturing techniques emphasize the importance of safety, both for workers and for the environment. By identifying and eliminating sources of waste and inefficiency, companies can reduce the risk of accidents and environmental incidents. In addition, by focusing on quality at every stage of the production process, companies can reduce the risk of defects and errors that could lead to safety or environmental issues.
In the long run, this can help reduce the risk of accidents and environmental incidents, reducing the potential liability for the company and improving its reputation.
Enhanced Sustainability
Finally, adopting a lean manufacturing approach can help chemical manufacturers reduce their environmental impact. By reducing waste, using fewer resources, and producing fewer emissions, companies can improve their sustainability and reduce their environmental footprint. This can improve the company's reputation with stakeholders and help position it as a leader in sustainable manufacturing practices.
Disadvantages of Lean Manufacturing in Chemical Manufacturing
Here are some of the disadvantages of lean manufacturing in chemical manufacturing:
Increased Upfront Costs
Adopting a lean manufacturing approach can require significant upfront investment. This may include the cost of new equipment, the cost of training and retraining employees, and the cost of implementing new processes and procedures. In addition, the transition to lean manufacturing may require changes to the company's supply chain or other aspects of its operations, which can also be costly.
While these costs can be offset by the long-term benefits of lean manufacturing, such as increased efficiency, improved quality, and reduced costs, it may take some time for these benefits to be realized. This means that companies may need to be prepared to make a significant investment in order to implement lean manufacturing successfully.
Resistance to Change
Another potential disadvantage of adopting a lean manufacturing approach in chemical manufacturing is resistance to change. Many employees may be resistant to new processes or procedures, mainly if they have worked the same way for a long time. This can make it difficult to implement lean manufacturing successfully and can slow down the transition process.
In addition, stakeholders outside the company, such as suppliers or customers, may also be resistant to changes in the company's operations. This can make it more difficult for the company to implement new processes or procedures and can slow down the adoption of lean manufacturing principles.
Difficulties in Implementation
Implementing a lean manufacturing approach can be challenging, particularly in complex manufacturing environments like chemical manufacturing. This is because there may be a large number of variables to consider, such as raw materials, production processes, and quality control measures.
In addition, implementing lean manufacturing principles may require changes to the company's supply chain or other aspects of its operations. This can be challenging to coordinate and may require significant effort and resources to implement successfully.
Risk of Over-Optimization
One of the risks of adopting a lean manufacturing approach is over-optimization. This can occur when companies become so focused on eliminating waste and streamlining processes that they neglect other important aspects of their operations, such as quality control or environmental sustainability.
This can lead to a situation where the company is producing products more efficiently, but at the cost of quality or environmental sustainability. This can be particularly problematic in industries like chemical manufacturing, where quality and environmental considerations are particularly important.
Potential Job Losses
Implementing a lean manufacturing approach can result in job losses, particularly if the company is able to produce the same amount of output with fewer employees. This can be particularly challenging for employees who have been working in the company for a long time and may not have the skills or training to transition to new roles.
In addition, job losses can have a negative impact on the local community, particularly if the company is a major employer in the area. This can lead to a decline in economic activity and a negative impact on the quality of life for residents.
How can Deskera Help You?
Deskera's integrated financial planning tools allow investors to better plan their investments and track their progress. It can help investors make decisions faster and more accurately.
Deskera Books can assist you in automating your accounting and mitigating business risks. Deskera makes it easier to create invoices by automating many other procedures, reducing your team's administrative workload.
Deskera also offers a suite of integrated applications to help businesses manage their financials, inventory, and operations. Furthermore, other business aspects such as HR (Deskera People), CRM (Deskera CRM), and ERP are provided by Deskera. These could be crucial and can help short sellers keep track of their businesses and make better decisions.
Conclusion
Adopting a lean manufacturing approach in chemical manufacturing can have a number of advantages and disadvantages. While lean manufacturing can improve efficiency, quality, and sustainability, it can also be costly to implement and may be met with resistance from employees and stakeholders. In addition, lean manufacturing can be challenging to implement successfully, particularly in complex manufacturing environments like chemical manufacturing.
Ultimately, the decision to adopt a lean manufacturing approach will depend on the specific circumstances of the company and its stakeholders. Companies considering a transition to lean manufacturing should carefully weigh the advantages and disadvantages and develop a comprehensive plan for implementation that takes into account the needs and concerns of all stakeholders.
Related Articles
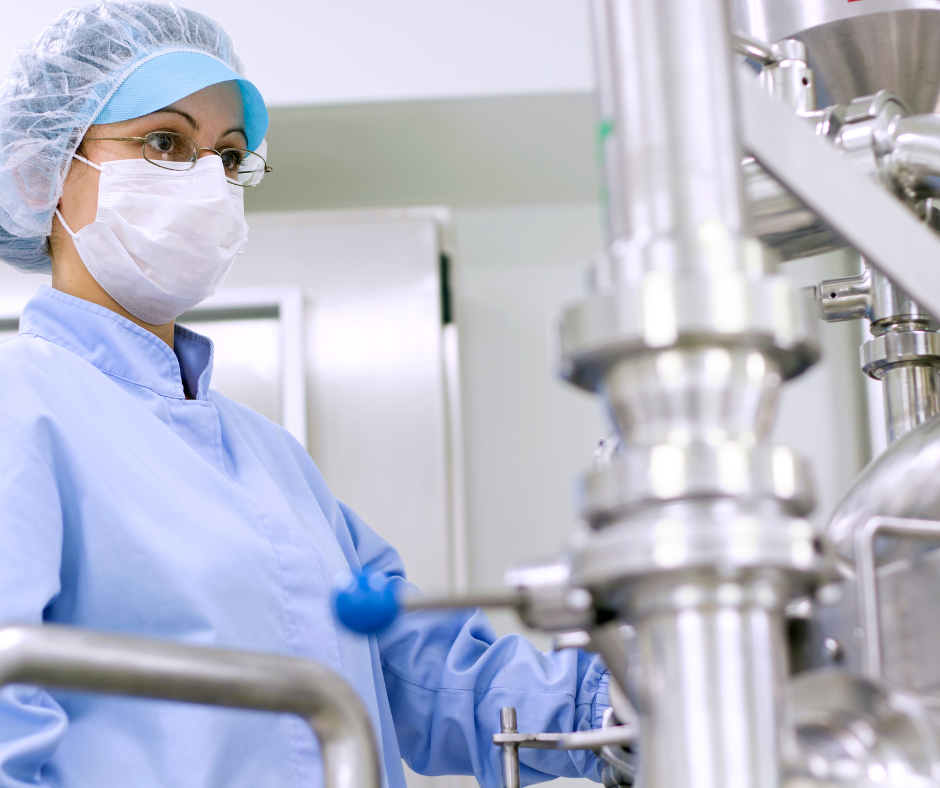
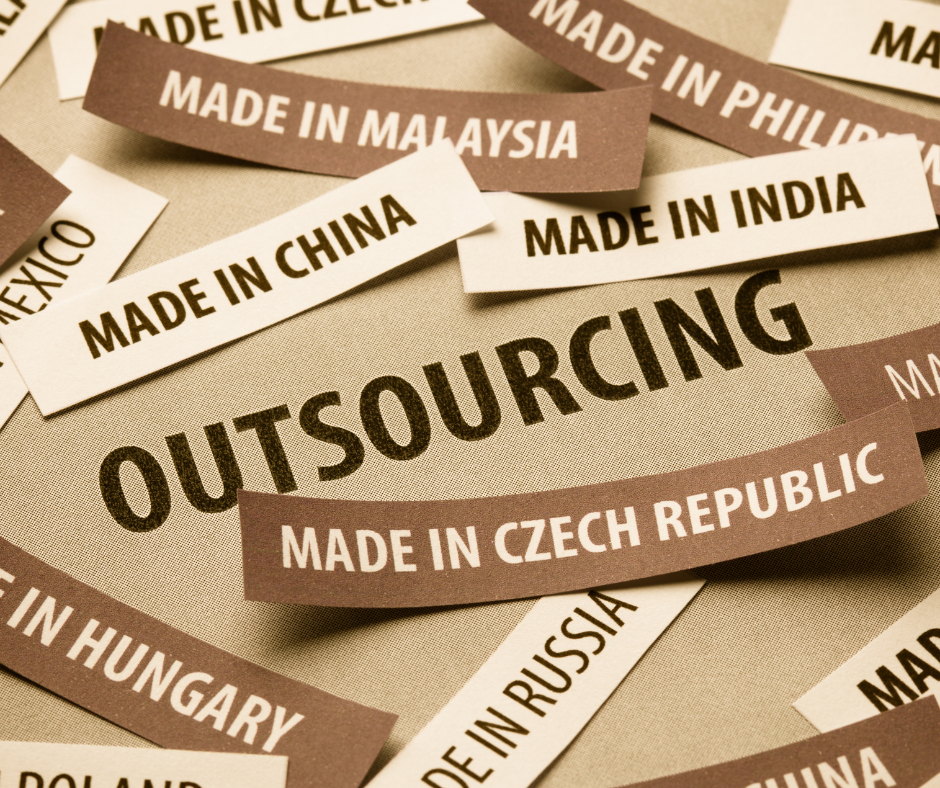
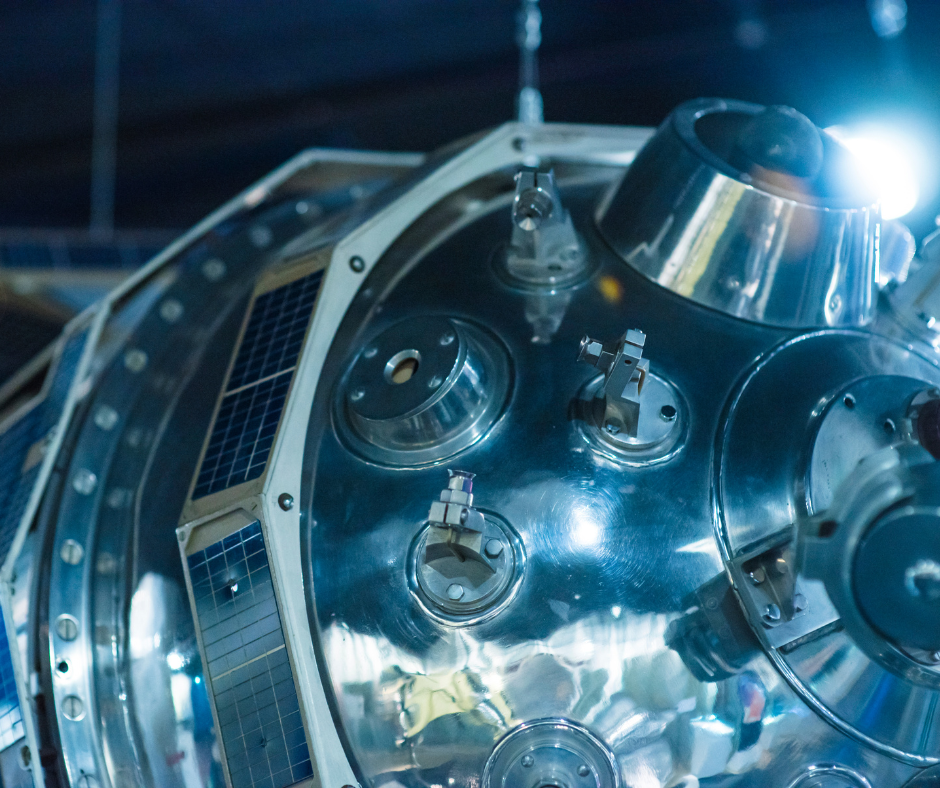
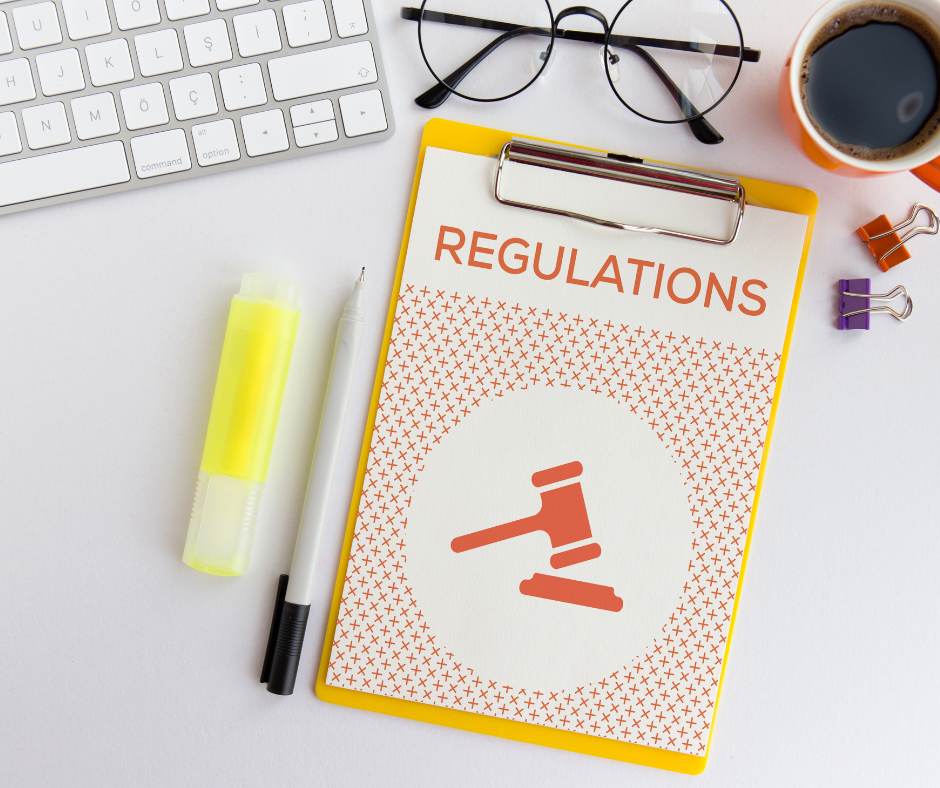