Manufacturing production scheduling can be a challenging task for companies of all sizes. Finding the optimal balance between the available resources and customer demand is crucial to ensure efficient operations and customer satisfaction.
Production scheduling can make or break a company's success in today's fast-paced business world, where delivery times are becoming increasingly important. According to a recent National Association of Manufacturers (NAM) survey, nearly 72% of manufacturing companies believe that production scheduling is one of the most critical factors affecting their operations.
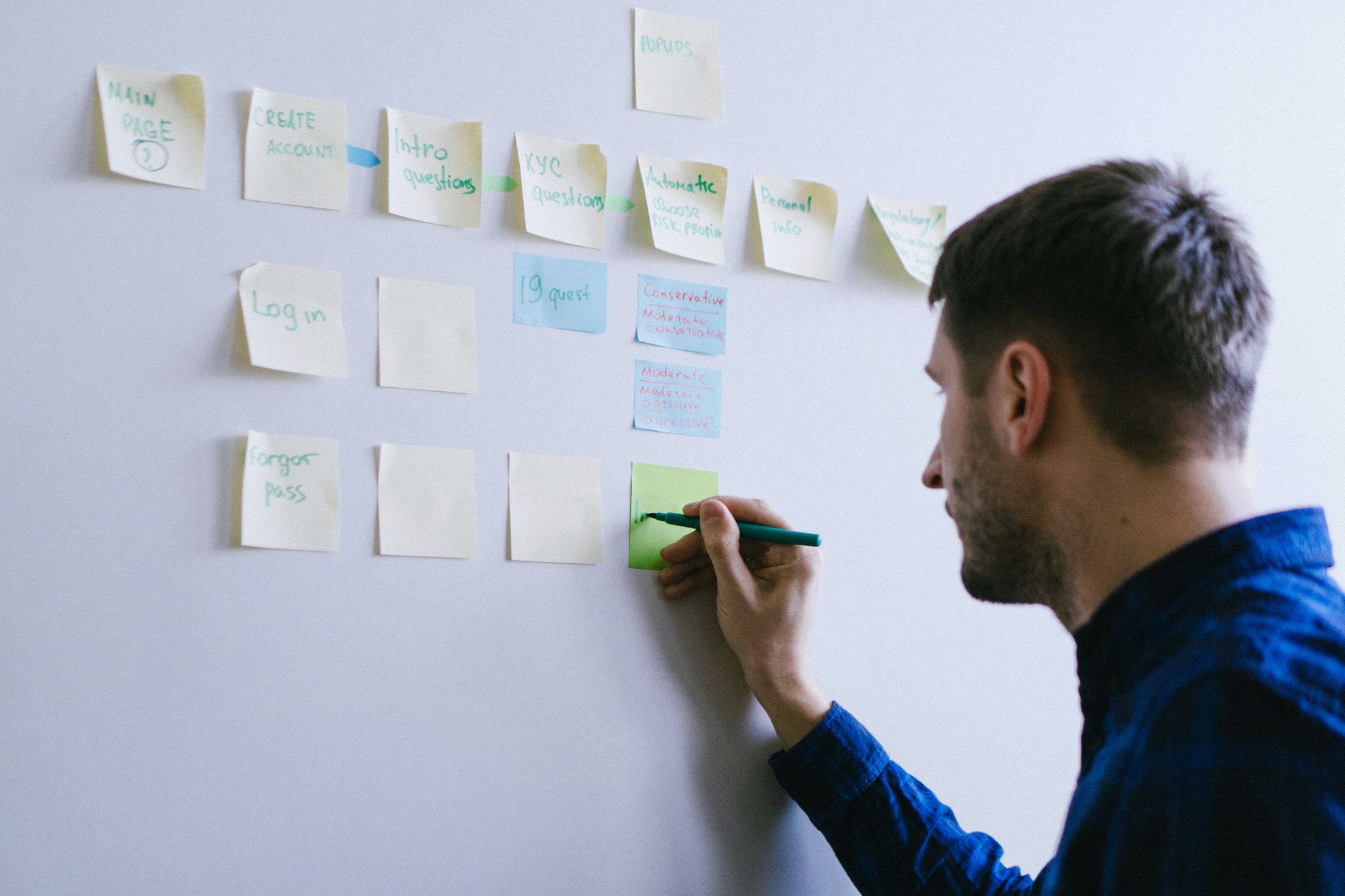
In this article, we will explore how to optimize your manufacturing production scheduling for greater efficiency. We will discuss the latest trends and best practices in the industry, including the use of advanced software systems, predictive analytics, and real-time data analysis.
By implementing these strategies, manufacturers can improve their production schedules, reduce lead times, and increase overall efficiency. So, let's dive into the details and discover how to streamline your manufacturing production scheduling process.
Here's what we shall cover in this post:
- What Is Manufacturing Production Scheduling?
- Understanding the Importance of Accurate Forecasting
- The Impact of Production Scheduling on Inventory Management
- Best Practices for Scheduling Complex Manufacturing Operations
- The Role of Technology in Production Scheduling
- Advantages of Implementing Automated Scheduling Systems
- Common Challenges and Pitfalls of Production Scheduling
- Tips for Improving Communication and Collaboration Among Teams
- Cross-Training and Flexibility in Scheduling
- Conclusion
- Key Takeaways
What Is Manufacturing Production Scheduling?
Manufacturing production scheduling refers to the process of planning and coordinating the production of goods in a manufacturing environment. It involves developing a detailed production plan that outlines the quantity and timing of each production task and the resources required to complete each task.
- The ultimate goal of production scheduling is to ensure that production runs as efficiently as possible while meeting customer demands and controlling costs.
- A production schedule typically includes a list of tasks that must be completed, as well as the timing of each task and the resources required to complete it. This may include information on materials, equipment, and personnel needed to complete each task.
- Manufacturing production scheduling can be a complex process, and it requires close collaboration between different departments within an organization, including production, engineering, purchasing, and logistics.
- Effective production scheduling can provide a number of benefits to manufacturers. It can help to increase productivity and efficiency by reducing downtime, minimizing inventory levels, and ensuring that resources are used effectively.
- It can also help to improve quality control and reduce the risk of defects or other issues that could impact the performance or reliability of the finished product. Effective production scheduling can help manufacturers improve their bottom line by reducing costs, improving customer satisfaction, and driving growth and profitability.
Benefits of Optimizing Manufacturing Production Scheduling
Optimizing manufacturing production scheduling can significantly benefit a company, from improved efficiency to increased profitability.
- Improved Efficiency: Optimizing production scheduling can help to reduce production time and increase productivity, resulting in improved efficiency. By scheduling production more effectively, manufacturers can reduce wait times and bottlenecks, ensure that machines are fully utilized, and reduce idle time. This means that more products can be produced in less time, which can help to increase output and reduce costs.
- Increased Profitability: By improving efficiency, manufacturers can also increase profitability. By reducing production time and increasing productivity, manufacturers can produce more products in less time, reducing costs and increasing revenue. In addition, optimized production scheduling can minimize downtime, which can also help to reduce costs and increase profitability.
- Improved Customer Satisfaction: Optimizing production scheduling can also help to improve customer satisfaction. Manufacturers can meet customer demand more effectively by ensuring that products are delivered on time and in the desired quantities. This can help build customer loyalty and improve the company's overall reputation.
- Improved Quality: Optimizing production scheduling can also help enhance product quality. By reducing wait times and bottlenecks, manufacturers can reduce the risk of defects and improve the consistency of their products. This can help to improve customer satisfaction and reduce the risk of returns and warranty claims.
- Better Resource Utilization: Optimized production scheduling can help manufacturers to make better use of their resources, including machines, labor, and raw materials. By scheduling production more effectively, manufacturers can ensure that their resources are being used efficiently, which can help to reduce waste and increase profitability.
- Enhanced Flexibility: Optimizing production scheduling can also help to improve flexibility. By scheduling production more effectively, manufacturers can be more responsive to changes in customer demand, supply chain disruptions, and other factors that may impact production. This can help improve the manufacturing process's agility and reduce the risk of delays and other issues.
By implementing effective scheduling strategies and utilizing tools like production scheduling software, manufacturers can achieve these benefits and position themselves for success in a competitive market.
Understanding the Importance of Accurate Forecasting
Accurate forecasting is critical to any successful business operation, especially in industries where demand for products or services can fluctuate rapidly.
Improves Inventory Management
Accurate forecasting helps companies to manage their inventory levels better, ensuring they have enough stock to meet demand without holding too much inventory that can become obsolete or incur additional storage costs.
Enables Better Financial Planning
Accurate forecasting also allows companies to plan their finances more effectively. By predicting future sales and demand, businesses can better allocate resources, budget for expenses, and invest in new opportunities.
Increases Operational Efficiency
Accurate forecasting also helps companies to optimize their production processes, reducing the likelihood of overproduction, waste, and unnecessary labor costs.
Enhances Customer Service
By accurately forecasting demand, companies can ensure that they have enough products or services to meet customer needs, improving customer satisfaction and loyalty.
Facilitates Strategic Planning
Accurate forecasting also allows companies to plan for the future, identifying opportunities for growth, expansion, and diversification.
Reduces Risk
Finally, accurate forecasting can help companies to minimize risk by allowing them to anticipate and prepare for potential market fluctuations or changes in customer demand.
By allowing companies to manage inventory levels better, plan finances, optimize production processes, enhance customer service, facilitate strategic planning, and reduce risk, accurate forecasting can provide significant benefits to a company and help it to achieve long-term success.
The Impact of Production Scheduling on Inventory Management
Inventory management is a critical function in any manufacturing organization and is closely tied to production scheduling. Production scheduling determines when and how much of each product should be manufactured, and this information is used to manage inventory levels.
There are several ways in which production scheduling can impact inventory management.
- Minimizing Inventory Costs: One of the primary benefits of effective production scheduling is the ability to reduce inventory costs. This is accomplished by scheduling production to match customer demand, reducing the need for excess inventory. By producing only what is needed, manufacturers can reduce carrying costs and avoid the risk of overstocking.
- Preventing Stockouts: Production scheduling also plays a critical role in avoiding stockouts. When production is scheduled accurately, manufacturers can ensure that they have enough inventory to meet customer demand. This helps to prevent stockouts, which can be costly in terms of lost sales and customer dissatisfaction.
- Reducing Lead Times: Production scheduling can also help to reduce lead times. By scheduling production more efficiently, manufacturers can reduce the time it takes to produce and deliver products. This can be particularly important in industries with short product lifecycles or rapidly changing customer demands.
- Improving Customer Service: Effective production scheduling can also help to improve customer service. Manufacturers can enhance customer satisfaction and loyalty by ensuring that products are delivered on time and in the correct quantities. This can lead to increased sales and repeat business.
- Optimizing Production Processes: Finally, production scheduling can help to optimize production processes. Manufacturers can make changes by analyzing production schedules and identifying bottlenecks to improve efficiency and reduce waste. This can lead to cost savings and increased productivity.
As such, manufacturers need to invest in production scheduling tools and techniques that can help them achieve these benefits.
Balancing Capacity and Demand
Balancing capacity and demand is a critical factor in manufacturing production scheduling. Manufacturers must ensure that they have enough capacity to meet customer demand while not overproducing and creating excess inventory.
Here are some key points to consider when balancing capacity and demand in production scheduling:
Accurately forecast demand: The first step in balancing capacity and demand is accurately forecasting customer demand. This can be a challenging task, but it is essential to ensure that you have enough capacity to meet customer needs without overproducing.
Several forecasting methods can help manufacturers estimate future demand, including time-series analysis, regression analysis, and market research.
Understand your production capacity: Once you understand customer demand, evaluating your capacity is essential. This includes assessing the capacity of individual machines, production lines, and overall plant capacity.
This information can help you determine if you have enough capacity to meet demand and identify potential bottlenecks that may limit your production capacity.
Consider different production scheduling strategies: Once you understand customer demand and capacity, you can start to develop a production scheduling strategy that balances capacity and demand.
One approach is to use a chase strategy, where production levels are adjusted to match demand. Another approach is to use a level strategy, where production levels are kept constant, and inventory is used to meet fluctuations in demand.
Use technology to optimize production scheduling: Technology can play a crucial role in optimizing production scheduling and balancing capacity and demand.
Advanced planning and scheduling (APS) software can help manufacturers create optimized production schedules that take into account production capacity, customer demand, and other factors. This can help manufacturers reduce lead times, improve on-time delivery rates, and reduce inventory levels.
Continuously monitor and adjust production schedules: Balancing capacity and demand is an ongoing process, and manufacturers must continuously monitor and adjust their production schedules as demand and capacity change.
By monitoring key performance indicators (KPIs) such as on-time delivery rates, lead times, and inventory levels, manufacturers can quickly identify potential issues and make adjustments to their production schedules to ensure they are meeting customer demand while maintaining optimal inventory levels.
Accurately forecasting demand, understanding production capacity, considering different production scheduling strategies, using technology to optimize production scheduling, and continuously monitoring and adjusting production schedules can help manufacturers achieve optimal inventory levels, reduce lead times, and improve on-time delivery rates.
Strategies for Managing Lead Times
Lead time management is a crucial element in production scheduling. It refers to the time required to manufacture a product from when an order is placed to when it is delivered.
Managing lead times effectively ensures on-time delivery, reduced inventory costs, and improved customer satisfaction.
- Implement a Just-In-Time (JIT) system: JIT is a lean manufacturing strategy focusing on producing goods just in time for customer demand. It eliminates unnecessary inventory by relying on a demand-pull system. The JIT system allows manufacturers to produce only what they need when they need it, thus reducing lead times.
- Reduce setup times: Setup time refers to the time required to set up a machine or equipment to produce a specific product. Setting setup times can reduce lead times by enabling the manufacturer to produce products quickly and efficiently.
- Optimize production processes: Optimizing production processes involves identifying and eliminating bottlenecks that can cause delays in production. This can be achieved by streamlining processes, using efficient machinery, and improving employee training.
- Implement a supply chain management system: It can help manufacturers manage their production schedules by providing real-time data on inventory levels, production processes, and customer demand. This information can be used to adjust production schedules and reduce lead times.
- Implement an Enterprise Resource Planning (ERP) system: ERP is a software system that integrates various business processes such as inventory management, production planning, and customer relationship management. An ERP system can help manufacturers manage their production schedules more efficiently by providing real-time data on inventory levels, production processes, and customer demand.
- Use advanced scheduling tools: Advanced scheduling tools such as computer-aided manufacturing (CAM) and computer-aided design (CAD) can help manufacturers manage their production schedules more efficiently. These tools can help identify bottlenecks and optimize production processes, thereby reducing lead times.
- Use data analytics: Data analytics can help manufacturers analyze production data and identify areas for improvement. By using data analytics, manufacturers can identify bottlenecks, optimize production processes, and reduce lead times.
By managing lead times effectively, manufacturers can reduce inventory costs, improve customer satisfaction, and achieve on-time delivery.
Best Practices for Scheduling Complex Manufacturing Operations
Manufacturing operations can be complex, involving multiple processes and factors that need to be taken into account for efficient and effective production. Scheduling these operations is a critical task that requires careful planning, coordination, and execution.
Start with a clear understanding of the production process: Before creating a production schedule, it's essential to have a clear understanding of the manufacturing process.
This involves knowing the sequence of operations, the time required for each operation, and any dependencies or constraints that may affect the schedule. A detailed understanding of the process makes creating an efficient production schedule that accounts for all the necessary factors easier.
Use scheduling software: Using scheduling software can help streamline the scheduling process and ensure accuracy. Scheduling software can help in generating a production schedule that accounts for all constraints, such as capacity, labor, and materials availability.
These tools can also be used to optimize the schedule, allowing for more efficient production and reducing lead times.
Implement a real-time monitoring system: A real-time monitoring system can provide visibility into the production process, allowing for better management of production schedules.
Real-time monitoring systems can track production performance, equipment status, and inventory levels. This data can be used to adjust schedules in real time, allowing for quick responses to unexpected events or changes in demand.
Optimize production based on demand: Understanding demand patterns can help in optimizing production schedules. By analyzing historical demand data, manufacturers can forecast future demand and adjust production schedules accordingly. This can help avoid overproduction, reduce inventory levels, and improve customer satisfaction.
Collaborate with suppliers: Working closely with suppliers can help in improving scheduling accuracy and efficiency. Manufacturers can plan production schedules by clearly understanding supplier lead times and availability. Collaborating with suppliers can also help in identifying potential bottlenecks in the supply chain, allowing for proactive measures to be taken to avoid production delays.
Implement a continuous improvement program: A continuous improvement program can help identify areas for improvement in the production scheduling process. This involves regularly reviewing production schedules, identifying areas for improvement, and implementing changes to improve efficiency and accuracy.
By implementing a continuous improvement program, manufacturers can ensure that their production schedules are always optimized for maximum efficiency.
By starting with a clear understanding of the production process, using scheduling software, implementing real-time monitoring systems, optimizing production based on demand, collaborating with suppliers, and implementing a continuous improvement program, manufacturers can create a scheduling process that is efficient, accurate, and flexible enough to meet changing demands.
Considerations for Scheduling Multi-Site Manufacturing Operations
Multi-site manufacturing operations require careful coordination and planning to ensure that production runs smoothly across all locations.
When scheduling such operations, several factors must be taken into consideration, including the production capacity of each site, the transportation of materials and finished products between sites, and the availability of skilled labor.
Here are some critical considerations for scheduling multi-site manufacturing operations:
Capacity Planning: It is essential to evaluate the production capacity of each site and ensure that it aligns with the demand for the products. Sites should be able to handle the expected volume of work to avoid backlogs or delays. Production schedules should be adjusted based on the capacity of each site, and it may be necessary to shift some workloads between sites to maintain optimal output levels.
Material Management: In multi-site manufacturing, the movement of raw materials and finished products between sites is essential. Developing a comprehensive transportation plan is important to ensure timely deliveries and avoid bottlenecks. This plan should include details on the routes to be used, the frequency of shipments, and the expected transit times.
Skilled Labor Availability: Different sites may have different levels of skilled labor availability. When scheduling multi-site manufacturing operations, it is essential to take into account the availability of skilled workers at each site. The schedules should be planned in such a way that the workload is distributed evenly across all sites, taking into account the skill level of the workers.
Contingency Planning: Despite careful planning and execution, unexpected events can still occur during multi-site manufacturing operations. It is important to have contingency plans in place to address any issues that may arise. These plans should include steps for managing disruptions in transportation, changes in demand, or any other unexpected event that may impact the production schedule.
Technology and Software: Advanced technology and software can help streamline the scheduling process for multi-site manufacturing operations. Several software solutions can help manage the scheduling process, track production progress, and provide real-time visibility into production status across all sites. These tools can be particularly useful in large, complex operations where keeping track of all the moving parts may be difficult.
Lean Manufacturing Principles: Applying lean manufacturing principles can help optimize multi-site manufacturing operations. This includes identifying and eliminating waste, reducing inventory levels, and improving overall efficiency. By implementing these principles, manufacturers can improve their production schedules and reduce the time and resources needed to produce high-quality products.
The Role of Technology in Production Scheduling
In recent years, advances in technology have greatly improved the accuracy and efficiency of production scheduling, allowing manufacturers to balance capacity and demand better, reduce lead times, and increase productivity. Here are some key ways technology is changing the production scheduling landscape:
Automation
Automated scheduling tools allow manufacturers to quickly and accurately schedule production runs based on real-time data, such as inventory levels, machine availability, and order volumes. This reduces the time and effort required to create and update schedules manually, freeing up resources for other critical tasks.
Integration
Integrating scheduling software with other manufacturing systems, such as ERP and MES, allows manufacturers to better manage the entire production process from end to end. This helps ensure that schedules align with other key factors, such as material availability, labor requirements, and machine maintenance needs.
Real-time Tracking
Real-time tracking of production performance allows manufacturers to quickly identify and respond to issues that arise during the production process, such as machine breakdowns or unexpected order changes. This helps to minimize downtime and delays, ensuring that schedules remain on track.
Predictive Analytics
Predictive analytics tools can analyze historical data to identify patterns and trends in production performance, helping manufacturers to predict future demand and optimize schedules accordingly. This helps to ensure that capacity is aligned with demand, reducing the risk of overproduction or stockouts.
Mobile Access
Mobile access to scheduling software allows production managers to stay connected and make changes to schedules in real time, even when they are away from the factory floor. This improves flexibility and responsiveness, helping to ensure that schedules remain on track even in the face of unexpected events.
Overall, technology plays an increasingly important role in production scheduling, helping manufacturers optimize schedules, reduce lead times, and increase productivity. As technology continues to advance, we can expect to see even more innovative solutions emerge that further streamline and improve this critical aspect of manufacturing operations.
Advantages of Implementing Automated Scheduling Systems
Automated scheduling systems are becoming increasingly popular in the manufacturing industry due to the benefits they provide.
- Reduced errors and improved accuracy: Automated scheduling systems use algorithms to optimize schedules, reducing the likelihood of human error. This leads to improved accuracy in the production schedule, reducing the likelihood of delays, backlogs, and other problems.
- Increased productivity: By using automated scheduling systems, manufacturers can ensure that production resources are being used to their full potential, leading to increased productivity. The software can take into account all available resources and allocate them efficiently, reducing downtime and increasing output.
- Better visibility into the production process: Automated scheduling systems provide real-time data on the production process, allowing managers to make informed decisions about the allocation of resources. This leads to better coordination between departments and improved overall efficiency.
- Faster decision-making: With automated scheduling systems, managers can quickly and easily identify issues and make decisions in real time. The software can highlight areas that require attention, allowing managers to take swift action and prevent problems from escalating.
- Improved customer satisfaction: By using automated scheduling systems, manufacturers can ensure that orders are completed on time and to the required quality standards. This leads to improved customer satisfaction and repeat business.
- Reduced costs: Automated scheduling systems can help manufacturers to reduce costs by optimizing the use of resources, reducing the need for overtime, and improving the efficiency of the production process. This can lead to significant cost savings over time.
- Scalability: Automated scheduling systems can be easily scaled up or down depending on the needs of the business. This means that manufacturers can quickly adapt to changes in demand or production capacity without having to invest in additional resources.
- Integration with other systems: Automated scheduling systems can be integrated with other software systems, such as ERP and MES systems, to provide a seamless production process. This leads to improved communication and coordination between departments, further improving efficiency.
From improved accuracy and increased productivity to better visibility into the production process and reduced costs, these systems can help to optimize the production process and improve overall efficiency.
Common Challenges and Pitfalls of Production Scheduling
Despite its importance, production scheduling is not always an easy task. It comes with a host of challenges that can lead to delays, inefficiencies, and cost overruns.
Unexpected Changes in Demand: One of the most significant challenges in production scheduling is unexpected changes in demand. A sudden spike in demand can put a strain on resources, leading to delays and missed deadlines. On the other hand, a sudden drop in demand can result in excess inventory and wasted resources.
Manufacturers must have robust forecasting and demand planning systems to overcome this challenge.
Limited Capacity: Capacity constraints are another common challenge in production scheduling. Manufacturers must carefully balance demand with their available capacity to avoid overloading their resources. Failure to manage capacity can result in bottlenecks, delays, and decreased efficiency.
To address this challenge, manufacturers can invest in technology that allows them to monitor capacity utilization in real time and adjust their schedules accordingly.
Machine Breakdowns: Machine breakdowns can also pose a significant challenge to production schedules. A single breakdown can cause delays in the entire production process, leading to missed deadlines and unhappy customers.
To minimize the impact of machine breakdowns, manufacturers should invest in preventative maintenance programs and have backup equipment available.
Lack of Visibility: A lack of visibility into the production process can also hinder effective scheduling. Manufacturers may struggle to identify inefficiencies and bottlenecks without real-time data and analytics.
To overcome this challenge, manufacturers can invest in software solutions providing real-time visibility into the production process.
Poor Communication: Effective communication is critical to successful production scheduling. However, poor communication between different departments and teams can lead to misunderstandings and delays. To address this challenge, manufacturers should establish clear lines of communication and ensure that all stakeholders are on the same page.
Inefficient Processes: Inefficient processes can also hinder effective production scheduling. Manufacturers must constantly evaluate their processes to identify areas for improvement and optimization. Streamlining processes can increase efficiency, reduce lead times, and improve scheduling accuracy.
Human Error: Finally, human error can also pose a significant challenge to production scheduling. Errors in data entry or scheduling can lead to missed deadlines and delays in the production process. To minimize the impact of human error, manufacturers can invest in automated scheduling systems that reduce the need for manual data entry.
Manufacturers must navigate a host of challenges, from unexpected changes in demand to limited capacity and machine breakdowns. However, by investing in technology, streamlining processes, and establishing clear communication, manufacturers can overcome these challenges and achieve effective production scheduling.
Tips for Improving Communication and Collaboration Among Teams
Effective communication and collaboration among teams are crucial for achieving business goals and ensuring the success of any project. Whether working remotely or in a physical office space, teams must work together and share information effectively to achieve their objectives. Here are some tips for improving communication and collaboration among teams:
- Define Roles and Responsibilities: Establish clear roles and responsibilities for team members to avoid confusion and misunderstandings. Everyone on the team should clearly understand what is expected of them and what they are responsible for.
- Use Collaboration Tools: Utilize collaboration tools such as project management software, instant messaging, and video conferencing to facilitate communication and collaboration among team members. These tools allow teams to share files, chat in real time, and hold virtual meetings from anywhere in the world.
- Foster Open Communication: Encourage open communication among team members by creating a safe space where everyone can share their thoughts, ideas, and concerns. Create an environment where team members feel comfortable speaking up and asking questions.
- Set Realistic Goals: Set realistic goals and expectations for the team. Make sure everyone is on the same page and understands what is expected of them. Avoid setting unrealistic deadlines or goals that are unattainable.
- Provide Regular Feedback: Provide regular feedback to team members to help them improve their performance and achieve their goals. Encourage two-way feedback so that team members can also provide feedback to their colleagues.
- Build Trust: Building trust is essential for effective communication and collaboration. Encourage team members to get to know each other and foster a sense of community within the team. Encourage transparency and honesty among team members.
- Embrace Diversity: Embrace diversity and encourage different perspectives within the team. Encourage team members to share their unique perspectives and experiences to help the team achieve its objectives.
- Address Conflicts Promptly: Address conflicts promptly to prevent them from escalating and negatively impacting team morale. Encourage team members to discuss any conflicts or issues openly and honestly and work together to find a resolution.
- Celebrate Achievements: Celebrate team achievements and milestones to recognize the hard work and effort put in by team members. Celebrating achievements helps to boost team morale and encourages team members to continue working towards their goals.
Metrics for Measuring Scheduling Performance and Success
Effective scheduling is critical for any organization to achieve optimal production performance. Measuring the success of scheduling processes requires the use of specific metrics that provide insight into the efficiency and effectiveness of the scheduling process.
These metrics help identify areas for improvement and provide a basis for evaluating the impact of process changes.
On-time Delivery
One of the most critical metrics for measuring scheduling success is on-time delivery. This metric measures the percentage of orders that are delivered on or before the scheduled date. It is a critical measure of customer satisfaction and indicates the scheduling process's effectiveness.
- Importance of On-time delivery: On-time delivery is crucial for maintaining customer satisfaction and loyalty. Failing to deliver products on time can result in customer dissatisfaction, increased costs due to rework or penalties, and, ultimately, loss of business.
- Calculation of On-time Delivery: To calculate the on-time delivery metric, divide the total number of products delivered on or before the promised delivery date by the total number of products ordered, then multiply the result by 100 to get a percentage.
To measure on-time delivery accurately, organizations need to establish clear criteria and metrics:
Define the Delivery Timeframe: Organizations must define the timeframe within which an order or project is considered on time. This could be a specific date, a range of dates, or a specified number of days from the order placement or project initiation.
Track Delivery Performance: Organizations need to track delivery performance by monitoring the actual delivery dates and comparing them to the promised delivery dates. This data allows them to calculate the on-time delivery percentage.
Set Performance Targets: Organizations should establish performance targets for on-time delivery. These targets can be based on industry standards, customer expectations, or internal goals. Setting targets helps organizations identify areas for improvement and benchmark their performance against competitors or industry best practices.
Monitor Root Causes: Organizations should analyze the root causes of delivery delays to identify recurring issues and implement corrective actions. This could involve evaluating internal processes, assessing supplier performance, or identifying bottlenecks in the supply chain. By addressing these root causes, organizations can improve their on-time delivery performance.
- Factors affecting On-time delivery: Factors that can impact on-time delivery include inaccurate forecasting, poor production scheduling, supply chain disruptions, delays in material or component delivery, and transportation issues.
- Impact of On-time delivery: Achieving high levels of on-time delivery can lead to increased customer satisfaction, repeat business, and positive word-of-mouth recommendations. On the other hand, poor on-time delivery performance can lead to negative customer experiences, lost business, and damage to the company's reputation.
- Benchmarks for On-time Delivery: Benchmarking can help companies compare their on-time delivery performance against industry standards and competitors. The on-time delivery benchmark can vary by industry and product type, but generally, a 95% or higher rate is considered good performance.
- Continuous improvement of On-time delivery: Continuous improvement initiatives can help companies improve their on-time delivery performance. This can involve implementing new technology, improving production scheduling processes, optimizing logistics and transportation, and working closely with suppliers and customers to manage lead times.
Lead Time
Lead time is the time it takes to complete a production order from start to finish. Reducing lead time is important because it can increase production capacity and help the organization meet customer demand. Measuring lead time provides a basis for identifying areas for improvement and evaluating the effectiveness of process changes.
- Importance: Lead time is a critical metric for manufacturing companies as it affects the company's competitiveness, customer satisfaction, and profitability. A shorter lead time means faster delivery, which leads to increased customer satisfaction and repeat business. Moreover, it allows companies to be more responsive to customer demand, reduce inventory levels, and increase productivity.
- Factors Affecting Lead Time: The lead time is influenced by various factors such as the complexity of the manufacturing process, availability of raw materials, capacity utilization, workforce skills, equipment reliability, and transportation time.
- Calculation: Lead time can be calculated in different ways, depending on the company's manufacturing process and customer requirements. A simple formula to calculate lead time is the sum of manufacturing, inspection, and transportation time. However, some companies may include other factors such as order processing, material procurement, and waiting times.
- Measuring and Monitoring: Measuring and monitoring lead time is essential to ensure that the manufacturing process runs efficiently and meets customer expectations. Companies can use various tools and techniques, such as value stream mapping, process flow analysis, and statistical process control, to measure and monitor lead time.
Schedule Adherence
Schedule adherence is the degree to which actual production matches the scheduled plan. This metric provides insight into the ability of the organization to execute the schedule and indicates the level of variability in the production process.
Importance of Schedule Adherence: Schedule adherence is essential for several reasons. Firstly, it ensures that the production process is optimized for maximum efficiency, which can lead to increased productivity and profitability.
Secondly, it helps to ensure that customer orders are delivered on time, which is critical for maintaining customer satisfaction and loyalty.
Thirdly, it enables production managers to identify bottlenecks and other inefficiencies in the manufacturing process, allowing them to make changes to improve productivity and profitability.
Measuring Schedule Adherence: Schedule adherence is typically measured using a simple formula. The formula involves calculating the percentage of completed production activities that were completed as planned.
For example, if the production team was scheduled to complete 100 activities in a given period and only completed 90 activities as planned, the schedule adherence would be 90%. Measuring schedule adherence is important in monitoring and controlling the manufacturing process.
To measure schedule adherence accurately, organizations need to establish clear criteria and metrics:
Define the Schedule: Organizations must define the planned schedule, including the start and end dates for tasks, activities, projects, or service delivery. The schedule should include milestones, deadlines, or specific timeframes for each activity.
Track Adherence: Organizations need to track schedule adherence by comparing the actual completion dates of tasks or activities with the planned schedule. This data allows them to calculate the schedule adherence percentage.
Set Performance Targets: Organizations should establish performance targets for schedule adherence. These targets can be based on industry standards, customer expectations, or internal goals. Setting targets helps organizations measure their performance, identify areas for improvement, and drive continuous improvement efforts.
Monitor Deviations: It is crucial to monitor deviations from the planned schedule. Deviations can include tasks or activities that are completed earlier or later than scheduled. By monitoring deviations, organizations can identify patterns, assess the impact of deviations on overall schedule adherence, and take corrective actions.
Factors Affecting Schedule Adherence: Several factors can affect schedule adherence, including equipment breakdowns, material shortages, unexpected demand fluctuations, and employee absenteeism.
Production managers must identify and address these factors to ensure that the manufacturing process runs smoothly and that customer orders are delivered on time.
Strategies for Improving Schedule Adherence: Manufacturing facilities must implement effective strategies to improve schedule adherence. Some strategies that can be used include regular maintenance and repair of equipment to prevent breakdowns, ensuring adequate inventory levels to prevent material shortages, and implementing a flexible workforce to handle unexpected demand fluctuations.
Another effective strategy is to establish clear communication channels between different departments within the manufacturing facility to ensure that everyone is working towards the same production goals.
Production Efficiency
Production efficiency measures the ratio of actual production output to the planned production output. It is an indication of the effectiveness of the scheduling process in maximizing production capacity.
- Importance: Production efficiency is essential for measuring the effectiveness of the manufacturing process. It provides insight into how well the organization is utilizing its resources and helps identify areas where improvements can be made. A high production efficiency indicates that the organization is efficient in its use of resources, minimizing costs and maximizing profits.
- Factors affecting production efficiency: Various factors can affect production efficiency, including equipment downtime, labor availability, material shortages, and quality issues. Identifying and addressing these factors to improve production efficiency is essential.
- Benefits: Improving production efficiency can lead to various benefits for the organization, such as increased productivity, reduced costs, improved quality, and better customer satisfaction. Higher production efficiency can also help the company remain competitive in the market and achieve better profits.
- Methods of improving production efficiency: There are various ways to improve production efficiency, such as optimizing the manufacturing process, reducing downtime, improving quality control, implementing automation, and enhancing workforce skills. The organization should identify the areas that need improvement and take steps to improve production efficiency.
Resource Utilization
Resource utilization measures the degree to which resources such as labor, equipment, and materials are utilized in the production process. It is an essential metric for identifying areas of waste and inefficiency and improving overall production performance.
Importance of resource utilization: Measuring resource utilization is essential for optimizing production scheduling, as it allows managers to identify areas of inefficiency and take corrective action.
By maximizing the use of resources, manufacturers can increase productivity, reduce costs, and improve overall profitability.
How to measure resource utilization: Resource utilization can be measured using a variety of methods, such as calculating the percentage of time resources are being used, analyzing machine downtime, or tracking the number of products produced per unit of time.
The key is finding a measurement that accurately reflects how efficiently resources are utilized.
To measure resource utilization accurately, organizations need to establish clear criteria and metrics:
Define Resource Categories: Organizations must define the categories of resources to be measured, such as equipment, manpower, facilities, or materials. Each resource category may have specific metrics and measurement parameters.
Track Resource Usage: Organizations need to track the usage of resources by collecting data on the actual time or effort spent on productive activities. This data allows them to calculate the resource utilization percentage.
Set Performance Targets: Organizations should establish performance targets for resource utilization. These targets can be based on industry benchmarks, best practices, or internal goals. Setting targets helps organizations measure their performance, identify areas for improvement, and drive continuous improvement efforts.
Monitor and Analyze Variability: It is important to monitor and analyze the variability of resource utilization. Variability can indicate fluctuations in resource demand, inefficient workflows, or resource bottlenecks. By identifying the sources of variability, organizations can implement strategies to reduce variability and improve resource utilization consistency.
Factors that impact resource utilization: Several factors can affect resource utilization, including production planning, machine breakdowns, personnel availability, and raw material shortages. Manufacturers can improve resource utilization and overall scheduling performance by identifying these factors and taking proactive steps to address them.
Benefits of optimizing resource utilization: Optimizing resource utilization can significantly impact a manufacturer's bottom line. By reducing downtime and improving efficiency, manufacturers can increase production output, improve product quality, and reduce waste.
Additionally, manufacturers can reduce their environmental impact by utilizing resources more effectively and creating a more sustainable production process.
Inventory Levels
Inventory levels are an essential indicator of the effectiveness of the scheduling process. High inventory levels can indicate poor scheduling performance, while low inventory levels can indicate inadequate capacity to meet demand.
Measuring inventory levels provides insight into the effectiveness of the scheduling process in meeting customer demand while minimizing inventory costs.
Importance of Monitoring Inventory Levels: Maintaining appropriate inventory levels is vital for a manufacturing company. Excess inventory can lead to increased storage and handling costs, while insufficient inventory can cause delays and production shutdowns. It is essential to have the right amount of inventory to meet customer demand and avoid stockouts or delays in production.
Metrics Used to Measure Inventory Levels: Several metrics can be used to measure inventory levels, including:
- Raw Material Inventory: This metric measures the amount of raw material that a company has in stock. Monitoring raw material inventory levels is essential to ensure the company can meet its production needs.
- Work-in-Progress Inventory: This metric measures the amount of work-in-progress items that a company has in stock. Work-in-progress items are partially completed products that are waiting to be finished. Monitoring this inventory level is essential to ensure production is running efficiently.
- Finished Goods Inventory: This metric measures the amount of finished products that a company has in stock. Monitoring finished goods inventory levels is essential to ensure the company can meet customer demand.
Optimal Inventory Levels: Determining optimal inventory levels is crucial to production schedules. Companies must strike a balance between having enough inventory to meet demand and not overstocking. This can be achieved by using techniques such as just-in-time (JIT) inventory management or lean manufacturing. These techniques aim to minimize inventory levels while ensuring that enough inventory is available to meet production needs.
Changeover Time
Changeover time is the time it takes to switch production from one product to another. Reducing changeover time is important because it can increase production flexibility and help the organization meet changing customer demand.
Measuring change over time provides a basis for identifying areas for improvement and evaluating the effectiveness of process changes.
To measure changeover time accurately, organizations need to establish clear criteria and metrics:
Define Changeover Process: Organizations must define the changeover process and its boundaries. This includes identifying the specific tasks and activities involved in the changeover, as well as the start and end points of the process. A well-defined changeover process ensures consistency in measurement and enables effective analysis.
Track Changeover Duration: Organizations need to track the actual time taken to complete a changeover. This can be done using time-tracking tools, stopwatch measurements, or automated data collection systems. It is important to capture accurate and reliable data to calculate changeover time accurately.
Calculate Changeover Time: Changeover time is calculated as the difference between the end time of the previous production run and the start time of the subsequent production run. This provides a clear measurement of the time dedicated to changeover activities.
Set Performance Targets: Organizations should establish performance targets for changeover time. These targets can be based on industry benchmarks, best practices, or internal goals. Setting targets helps organizations measure their performance, identify areas for improvement, and drive continuous improvement efforts.
Importance: Reducing changeover time can help manufacturers to increase their production capacity, reduce inventory levels, and respond quickly to changing customer demands. This metric can also help identify process improvement opportunities and cost savings.
Factors affecting change over time: The length of the changeover time is influenced by several factors, including the complexity of the production process, the type of equipment and machinery used, the number of products being produced, and the skill level of the operators.
Techniques for reducing changeover time: There are several techniques that manufacturers can use to reduce changeover time, such as single-minute exchange of die (SMED), which involves separating internal and external setup activities and performing them concurrently, and using quick-change tooling to minimize the time required to switch equipment.
Monitoring and measuring change over time: Manufacturers can use various methods to measure and monitor change over time, such as using stopwatches or electronic timers to record the time taken for each step of the changeover process and tracking change over time as part of overall equipment effectiveness (OEE) calculations.
Benefits of reducing changeover time: By reducing changeover time, manufacturers can increase their production flexibility, respond more quickly to changing customer demands, reduce inventory levels, and improve overall equipment effectiveness. This can result in increased profitability and competitive advantage in the marketplace.
Challenges and considerations: While reducing changeover time can provide significant benefits, it may also require substantial investments in equipment, training, and process improvement.
It is important to carefully evaluate the costs and benefits of any changeover time reduction initiatives and to involve all stakeholders in the decision-making process. Additionally, manufacturers should consider the impact of changeover time on other metrics, such as production efficiency and on-time delivery.
Downtime
Downtime is the time when equipment is not in operation. Reducing downtime is essential because it can increase production capacity and minimize production costs. Measuring downtime provides insight into the effectiveness of the scheduling process in minimizing production disruptions and maximizing equipment utilization.
Factors Contributing to Downtime:
Several factors contribute to downtime in manufacturing operations. These factors include machine breakdowns, maintenance activities, changeovers, and production planning errors.
Machine breakdowns can occur due to various reasons, such as wear and tear, poor maintenance, and operator errors. Maintenance activities like repairs and upgrades can also contribute to downtime.
Changeovers involving switching from one product or process to another can cause significant downtime if not properly planned and executed. Production planning errors, such as inaccurate forecasting and scheduling, can also lead to extended downtime.
Strategies to Minimize Downtime:
Reducing downtime is crucial to maximize production efficiency and profitability. Here are some strategies to minimize downtime in manufacturing operations:
- Preventive Maintenance: Regular maintenance activities can help prevent machine breakdowns and reduce the frequency and duration of downtime. Preventive maintenance involves regular inspection, cleaning, and repairs of machines and equipment.
- Predictive Maintenance: Predictive maintenance uses data and analytics to predict and prevent machine breakdowns before they occur. It involves monitoring machines and equipment in real-time to detect potential issues and perform maintenance activities before they lead to downtime.
- Changeover Optimization: Optimizing changeovers involves streamlining and standardizing the process to reduce the time and resources required to switch from one product or process to another. This can include using quick-changeover tools and techniques, improving team communication and collaboration, and reducing setup times.
- Production Planning and Scheduling: Accurate forecasting and scheduling can minimize downtime by ensuring that machines and resources are available when needed. It involves optimizing production schedules to balance demand and capacity, minimizing changeovers, and reducing idle time.
- Operator Training and Support: Well-trained and supported operators can help prevent machine breakdowns and reduce the duration of downtime. It involves providing operators with the necessary skills, knowledge, and resources to operate machines and equipment efficiently and safely.
Cycle Time
Cycle time is the time it takes to complete one cycle of production. Measuring cycle time provides insight into the effectiveness of the scheduling process in optimizing production efficiency and reducing lead time.
Importance of Cycle Time: Cycle time is a critical metric for manufacturing operations, as it provides insight into process efficiency and productivity. A low cycle time means that a product can be produced quickly, which can help companies meet customer demand and reduce inventory costs.
On the other hand, a high cycle time indicates that there are bottlenecks in the production process that need to be addressed.
Role of Cycle Time in Production Scheduling: Cycle time is an important consideration when creating production schedules, as it helps determine the number of units that can be produced within a given time frame.
By optimizing cycle time, companies can increase production efficiency and reduce costs. Production schedules that consider cycle time can help companies meet customer demand while avoiding overproduction and inventory waste.
Factors Affecting Cycle Time: Several factors can affect cycle time, including equipment performance, raw material quality, and worker productivity. By identifying the factors that impact cycle time, companies can make targeted improvements to increase productivity and efficiency.
How to Improve Cycle Time: There are several strategies that companies can use to improve cycle time, including implementing lean manufacturing practices, investing in automation technology, and optimizing workflow processes. Companies can increase productivity and profitability by continuously monitoring and improving cycle time.
Measuring Cycle Time: To measure cycle time accurately, it is essential to track production time for each unit of product. This can be done using specialized software tools or manual data collection. Once data is collected, it can be analyzed to identify process improvement and optimization opportunities.
Quality
Quality is an essential factor in the success of any production process. Measuring quality provides insight into the effectiveness of the scheduling process in producing high-quality products that meet customer specifications and minimize rework.
These metrics help companies identify defects, improve processes, and ensure that products meet the desired specifications.
Defect rate: The defect rate is the percentage of defective products that are produced during manufacturing operations. Defective products are those that do not meet the required specifications or have some other issue that makes them unfit for use.
The defect rate is a critical quality metric because it directly affects customer satisfaction and brand reputation. Higher defect rates lead to more product returns, lower customer satisfaction, and decreased brand reputation.
Calculate the Defect Rate: The defect rate is calculated by dividing the number of defects by the total number of units or occurrences and multiplying the result by 100 to obtain a percentage. The formula for calculating the defect rate is as follows:
Defect Rate = (Number of Defects / Total Number of Units) × 100
First Pass Yield (FPY): First pass yield (FPY) is the percentage of products that meet the required specifications on the first attempt. FPY is a critical quality metric because it indicates the effectiveness of the manufacturing process.
A higher FPY demonstrates that the manufacturing process is efficient and that the products meet the required specifications. A lower FPY indicates that the manufacturing process is ineffective and the products require multiple attempts to meet the required specifications. A low FPY can result in increased costs and decreased customer satisfaction.
To calculate FPY accurately, organizations need to follow a systematic approach:
Define Defects and Acceptance Criteria: Organizations should define and document what constitutes a defect and establish clear acceptance criteria. Defects may include physical defects, performance issues, deviations from specifications, or any other factors that impact product or service quality. Clear acceptance criteria enable consistent evaluation of outputs and facilitate accurate FPY calculation.
Collect Data: Organizations need to collect relevant data on the number of defect-free units produced or services delivered and the total number of units produced or delivered. This data can be obtained through inspections, quality control checks, customer feedback, or other reliable sources.
Calculate First Pass Yield (FPY): FPY is calculated by dividing the number of defect-free units by the total number of units and multiplying the result by 100 to obtain a percentage. The formula for calculating FPY is as follows:
FPY = (Number of Defect-free Units / Total Number of Units) × 100
Customer satisfaction: Customer satisfaction is a metric that measures the degree to which customers are satisfied with the products or services they receive. Customer satisfaction is a critical quality metric because it indicates whether the products meet the customer's needs and expectations.
Companies that prioritize customer satisfaction can increase customer loyalty and generate repeat business. Customer satisfaction can be measured through surveys, feedback forms, or online reviews.
Mean time to repair (MTTR): Mean time to repair (MTTR) is the average time it takes to repair a failed product or machine. MTTR is a critical quality metric because it indicates the reliability of the products or machines.
A higher MTTR suggests that the products or machines are less reliable and require more maintenance. A lower MTTR suggests that the products or machines are more reliable and require less maintenance.
To calculate MTTR accurately, organizations need to follow a systematic approach:
Define Repair Instances: Organizations should clearly define what constitutes a repair instance. It could be a single equipment failure event or a set of related failures that require repair.
Record Repair Data: Organizations need to maintain detailed records of repair incidents, including the time the failure occurred, the time it took to resolve the issue, and any additional relevant information. This data can be obtained through maintenance logs, work orders, or other tracking systems.
Calculate Mean Time to Repair (MTTR): MTTR is calculated by summing up the total repair time for all instances and dividing it by the number of repair incidents. The formula for calculating MTTR is as follows:
MTTR = Total Repair Time / Number of Repair Instances
Mean time between failures (MTBF): Mean time between failures (MTBF) is the average time it takes for a product or machine to fail. MTBF is a critical quality metric because it indicates the reliability of the products or machines.
A higher MTBF suggests that the products or machines are more reliable and require less maintenance. A lower MTBF indicates that the products or machines are less reliable and require more maintenance.
To calculate MTBF accurately, organizations need to follow a systematic approach:
Define Failure Instances: Organizations should clearly define what constitutes a failure instance. It could be a complete breakdown, malfunction, or any other event that leads to a loss of functionality or performance.
Record Failure Data: Organizations need to collect data on the occurrence of failures, including the time when the failure happened and any other relevant information. This data can be obtained through equipment logs, maintenance records, or other monitoring systems.
Calculate Mean Time Between Failures (MTBF): MTBF is calculated by dividing the total operating time by the number of failures. The formula for calculating MTBF is as follows:
MTBF = Total Operating Time / Number of Failures
Scrap rate: The scrap rate is the percentage of raw materials or components that are discarded during manufacturing operations. The scrap rate is a critical quality metric because it indicates the efficiency of the manufacturing process.
A higher scrap rate demonstrates that manufacturing is less efficient and wastes more resources. A lower scrap rate suggests that manufacturing is more efficient and wastes fewer resources.
Calculate Scrap Rate: Scrap rate is calculated by dividing the total weight or quantity of scrap by the total weight or quantity of products manufactured and multiplying by 100. The formula for calculating scrap rate is as follows:
Scrap Rate = (Total Scrap / Total Production) * 100
Overall Equipment Effectiveness (OEE): Overall Equipment Effectiveness (OEE) is a metric that measures the efficiency and effectiveness of manufacturing equipment. OEE takes into account three factors: availability, performance, and quality. Availability refers to the amount of time that equipment is available for production.
Performance refers to the speed at which the equipment operates. Quality refers to the percentage of products that meet the required specifications. OEE is a critical quality metric because it indicates the effectiveness of the manufacturing equipment.
To calculate OEE accurately, organizations need to follow a systematic approach:
Define OEE Components: Organizations should clearly define the components of OEE (availability, performance, and quality) and determine how each component will be measured and calculated.
Collect Data: Organizations need to collect data on equipment availability, performance, and quality. This data can be obtained through equipment logs, production records, maintenance records, and quality control systems.
Calculate OEE: OEE is calculated by multiplying the availability, performance, and quality percentages. The formula for calculating OEE is as follows:
OEE = Availability% x Performance% x Quality%
These metrics help identify areas for improvement and provide a basis for evaluating the impact of process changes. By monitoring these metrics and continuously improving the scheduling process, organizations can achieve optimal production performance and meet customer demand while minimizing costs.
Continuous Improvement and Feedback Loops
Feedback loops, or the ongoing collection and analysis of data related to production scheduling, are a vital component of continuous improvement. Here are some points to consider regarding continuous improvement and feedback loops in production scheduling:
- Importance of feedback loops: Feedback loops provide critical information about the effectiveness of scheduling processes and enable organizations to make data-driven decisions about improvements. They help identify inefficiencies, bottlenecks, and other issues that may impact performance.
- Identifying areas for improvement: To improve production scheduling processes, it is essential to identify the areas that require improvement. This can be done through data analysis, including the examination of historical data on production times, cycle times, and other vital metrics.
- Root cause analysis: Once areas for improvement have been identified, it is essential to conduct a root cause analysis to determine the underlying reasons for performance issues. This may involve examining data, conducting interviews with stakeholders, and other methods.
- Implementing changes: After identifying areas for improvement and determining the root causes of issues, the next step is to implement changes to improve scheduling processes. This may involve introducing new technology, revising workflows, or other changes.
- Monitoring performance: To ensure that improvements are effective, it is essential to monitor performance over time. This involves ongoing data collection and analysis and regular reviews of key metrics related to production schedules.
- Making adjustments: Continuous improvement is an ongoing process, and organizations must be prepared to make adjustments as necessary. This may involve revising workflows, changing technology, or other changes to optimize scheduling performance.
- Building a culture of continuous improvement: Finally, creating a culture of continuous improvement within the organization is essential. This involves encouraging feedback, promoting collaboration, and fostering a commitment to ongoing optimization and refinement of production scheduling processes.
Cross-Training and Flexibility in Scheduling
Here are some key points to consider when it comes to cross-training and flexibility in production scheduling:
Cross-Training and Job Rotation
Cross-training refers to the practice of training employees to perform multiple tasks or roles within a company. Job rotation involves moving employees from one job to another, providing them with a broader range of experience and skills. Cross-training and job rotation are essential for developing a flexible workforce that can adapt to demand, and production needs changes.
Flexibility in Scheduling
Flexibility in scheduling involves quickly adjusting production schedules based on changing demand, disruptions, or other factors. This can include shifting production resources from one task to another, adjusting production volumes, or modifying production schedules to accommodate unexpected events.
The key is to have a flexible production schedule that allows for adjustments to be made quickly and efficiently.
Benefits of Cross-Training and Flexibility
There are several benefits to cross-training and flexibility in production scheduling. For one, it allows companies to respond quickly to changes in demand, minimizing the impact of unexpected disruptions or changes in the marketplace. Additionally, cross-training and job rotation can help employees develop new skills, making them more valuable to the company and increasing their job satisfaction. Finally, a flexible production schedule can help companies reduce costs by maximizing production efficiency and minimizing waste.
Challenges to Cross-Training and Flexibility
While cross-training and flexibility are essential for any production scheduling strategy, there are also challenges to implementing these practices. For example, finding the time and resources to train employees on multiple tasks or roles can be difficult.
Additionally, employees may resist change or hesitate to take on new responsibilities. Finally, companies may need to invest in new equipment or technology to support a more flexible production schedule.
Tips for Successful Cross-Training and Flexibility
Companies should take a few key steps to implement cross-training and flexibility in production scheduling successfully. First, they should identify areas where cross-training would be most beneficial, such as areas with high turnover or where skills are in short supply.
Second, they should communicate the benefits of cross-training and flexibility to employees, highlighting the opportunities for skill development and increased job satisfaction. Finally, they should invest in the resources necessary to support a more flexible production schedule, such as technology or additional training programs.
How can Deskera Help You?
Deskera MRP allows you to closely monitor the manufacturing process. From the bill of materials to the production planning features, the solution helps you stay on top of your game and keep your company's competitive edge.
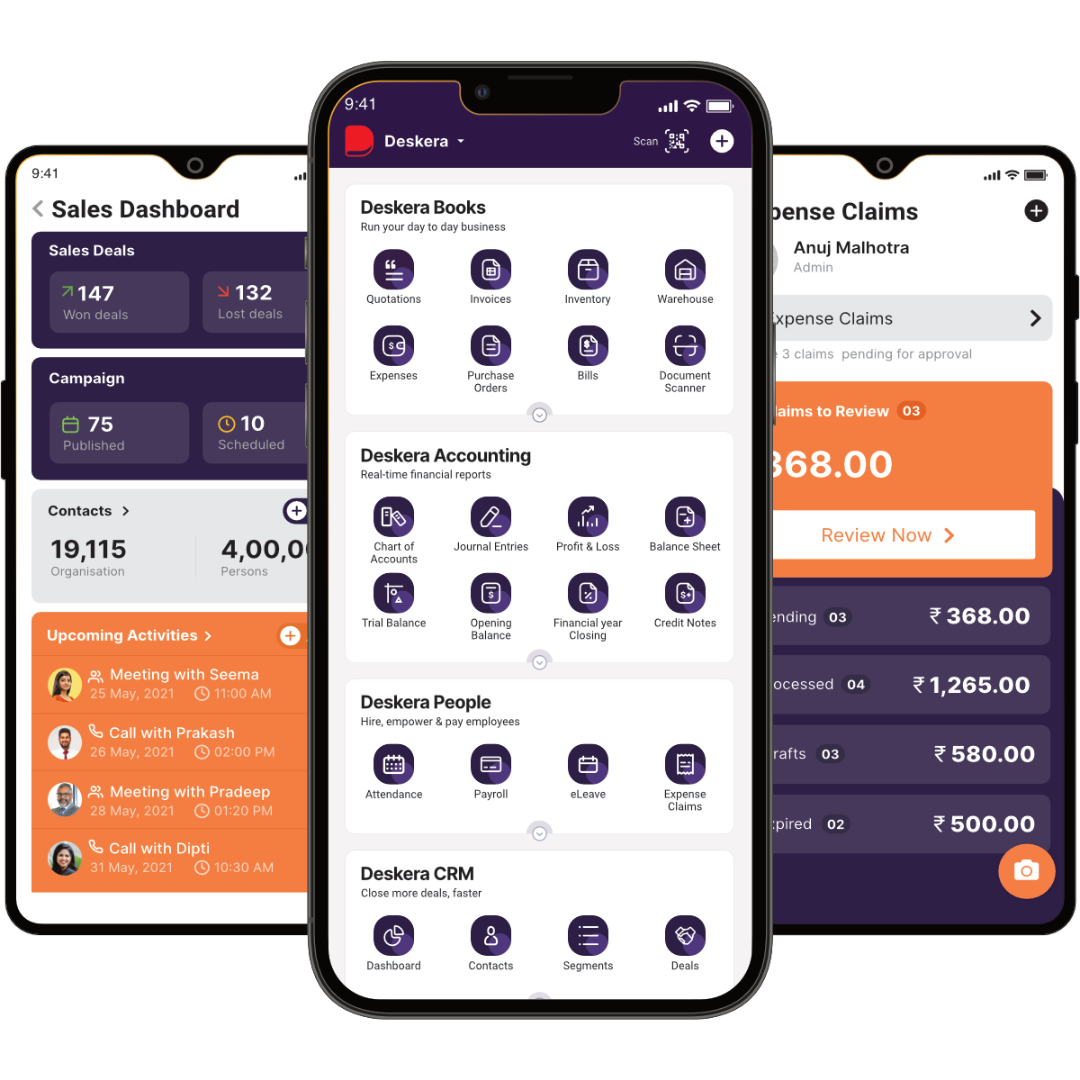
Deskera ERP and MRP system can help you:
- Manage production plans
- Maintain Bill of Materials
- Generate detailed reports
- Create a custom dashboard
Deskera ERP is a comprehensive system that allows you to maintain inventory, manage suppliers, and track supply chain activity in real-time, as well as streamline a variety of other corporate operations.
Deskera Books enables you to manage your accounts and finances more effectively. Maintain sound accounting practices by automating accounting operations such as billing, invoicing, and payment processing.
Deskera CRM is a strong solution that manages your sales and assists you in closing agreements quickly. It not only allows you to do critical duties such as lead generation via email, but it also provides you with a comprehensive view of your sales funnel.
Deskera People is a simple tool for taking control of your human resource management functions. The technology not only speeds up payroll processing but also allows you to manage all other activities such as overtime, benefits, bonuses, training programs, and much more. This is your chance to grow your business, increase earnings, and improve the efficiency of the entire production process.
Conclusion
Optimizing manufacturing production scheduling is essential to ensure greater efficiency, reduce lead times, minimize inventory levels, and improve on-time delivery performance. An optimized production schedule ensures that the right amount of resources are allocated to the right jobs at the right time, and it can help manufacturers remain competitive in a global market.
Manufacturers can optimize production scheduling by investing in advanced scheduling software, collaborating closely with suppliers, and streamlining manufacturing processes. An optimized production schedule requires a balance between minimizing production time and reducing costs while meeting customer demand.
By using data analytics and predictive modeling, manufacturers can identify production bottlenecks, optimize production capacity, and improve production planning accuracy. Collaboration with suppliers can reduce lead times and inventory levels, reducing costs and improving customer satisfaction.
Streamlining manufacturing processes through continuous improvement initiatives and lean manufacturing techniques can optimize production scheduling by reducing waste, improving quality, and increasing efficiency. By focusing on improving processes, manufacturers can reduce cycle times, increase throughput, and ultimately achieve greater efficiency.
Key Takeaways
- Manufacturing production scheduling plays a critical role in ensuring that operations are executed efficiently, on time, and at a lower cost.
- Scheduling in a manufacturing plant involves sequencing and allocating tasks, resources, and time to achieve optimal results.
- The optimization of production scheduling requires a comprehensive understanding of the manufacturing processes, capacity, demand, and constraints.
- Efficient scheduling can lead to better customer satisfaction, increased productivity, reduced lead times, and cost savings.
- Adopting an automated scheduling system can help manufacturers gain real-time insights into the production process, improve communication and decision-making, and reduce scheduling errors.
- The use of predictive analytics can help manufacturers anticipate production issues and optimize schedules to prevent delays and minimize downtime.
- Collaboration and communication between various departments are crucial in achieving an effective production scheduling system.
- The use of visual aids such as Gantt charts, calendars, and dashboards can help manufacturers monitor and track the progress of their production schedule and identify potential bottlenecks.
- Lean manufacturing principles can help reduce waste and improve the efficiency of the production scheduling process.
- The development of a contingency plan can help manufacturers prepare for unexpected events that could affect their production schedules.
Related Articles
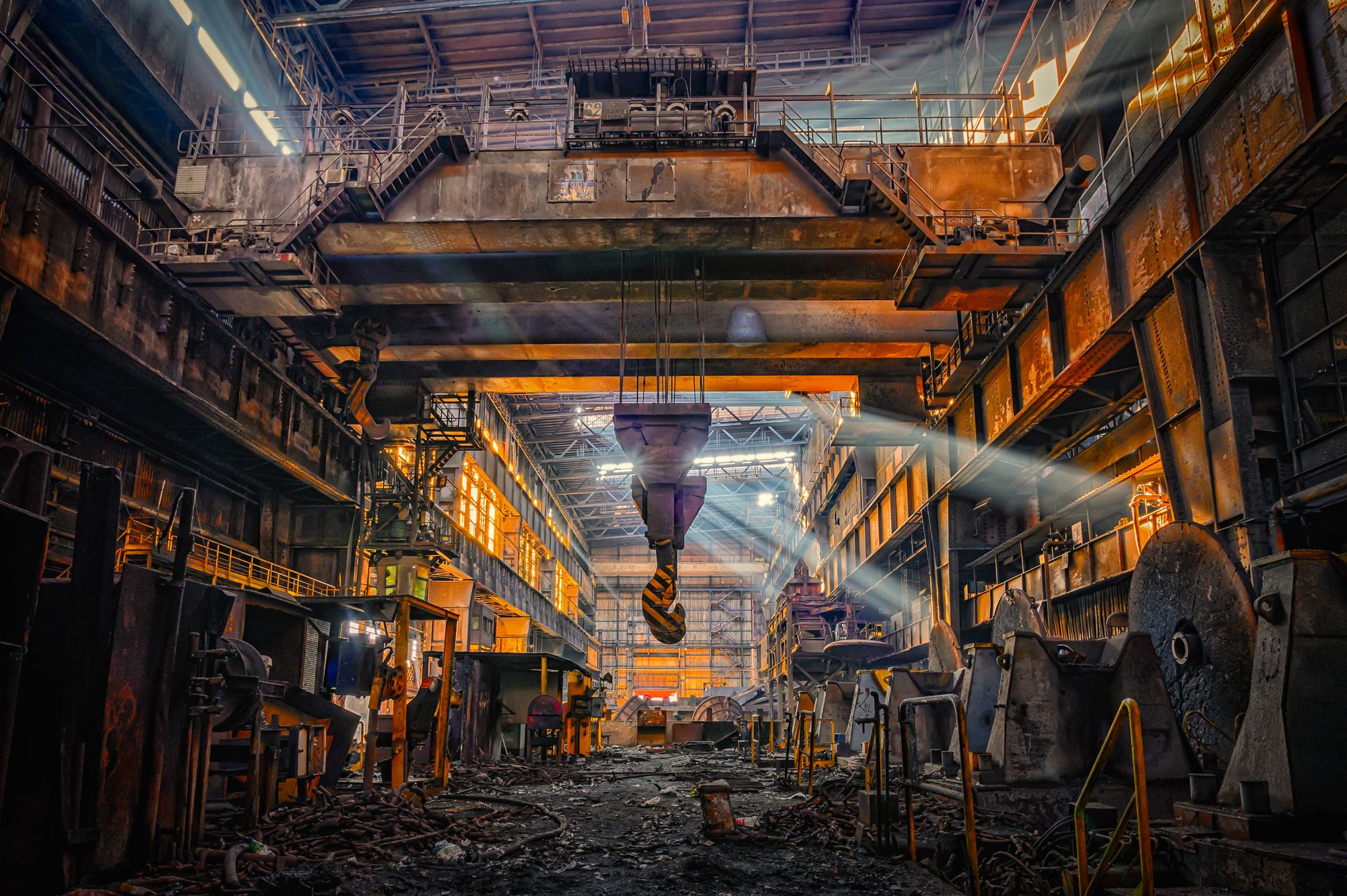
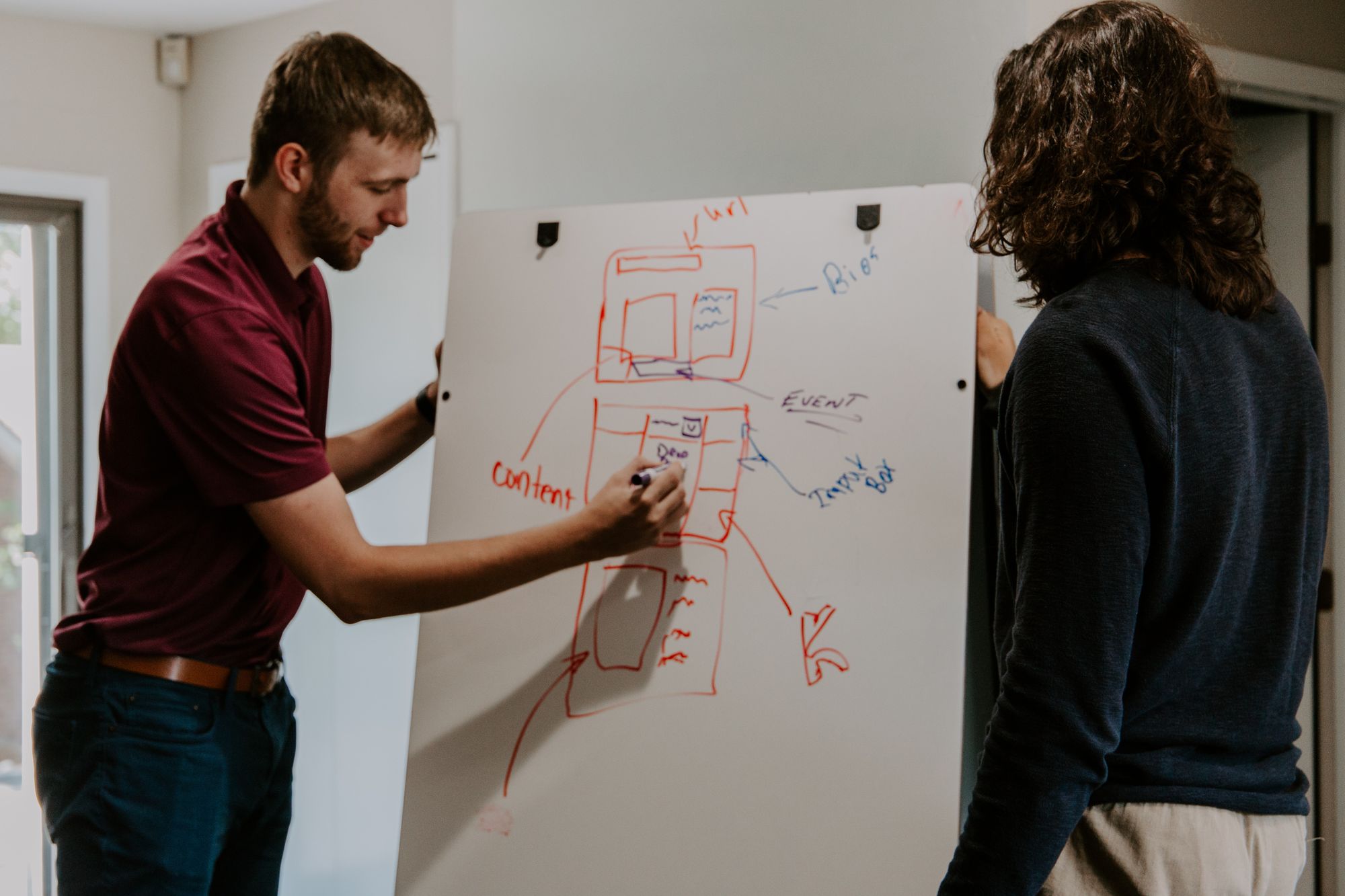
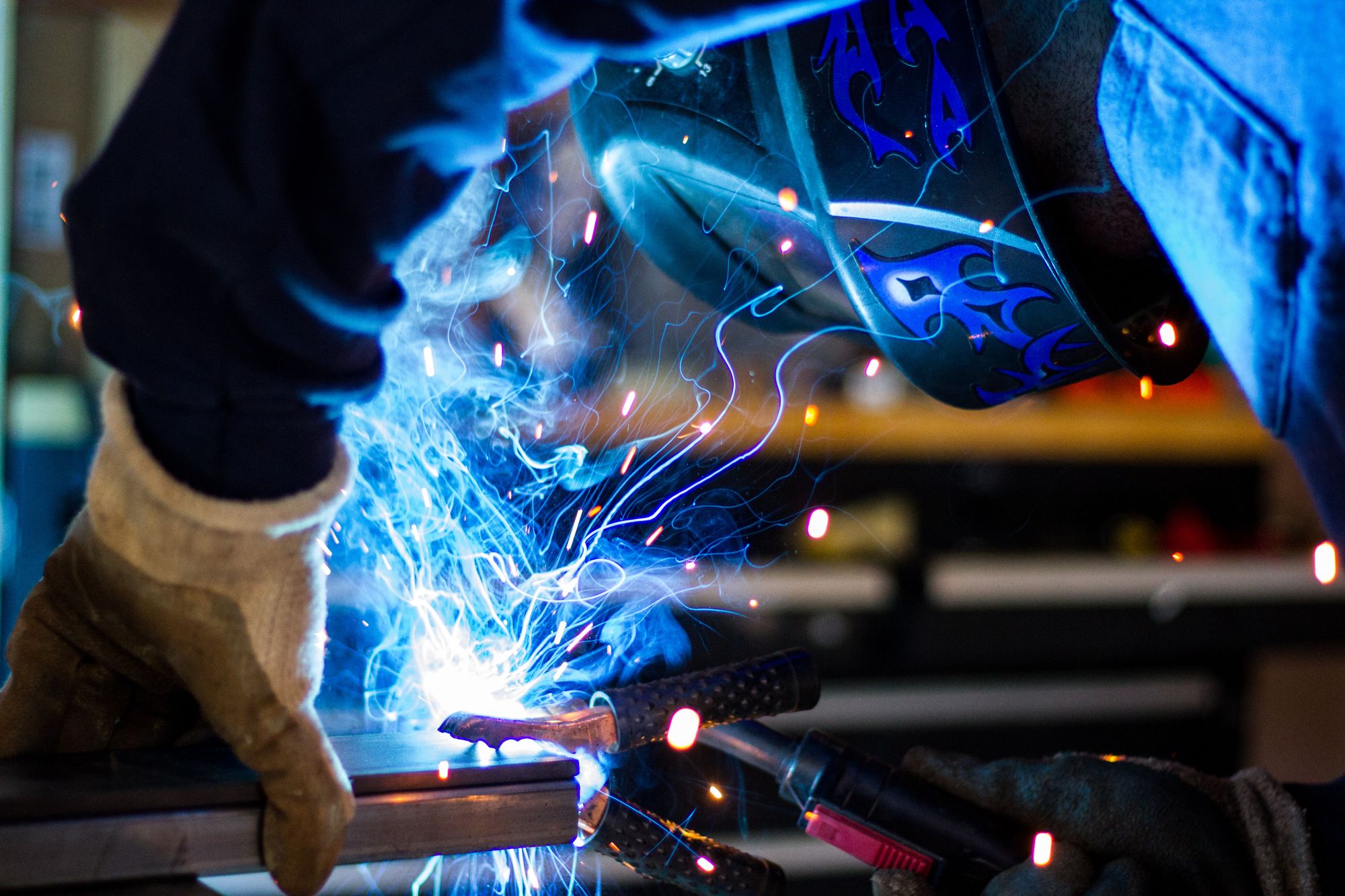
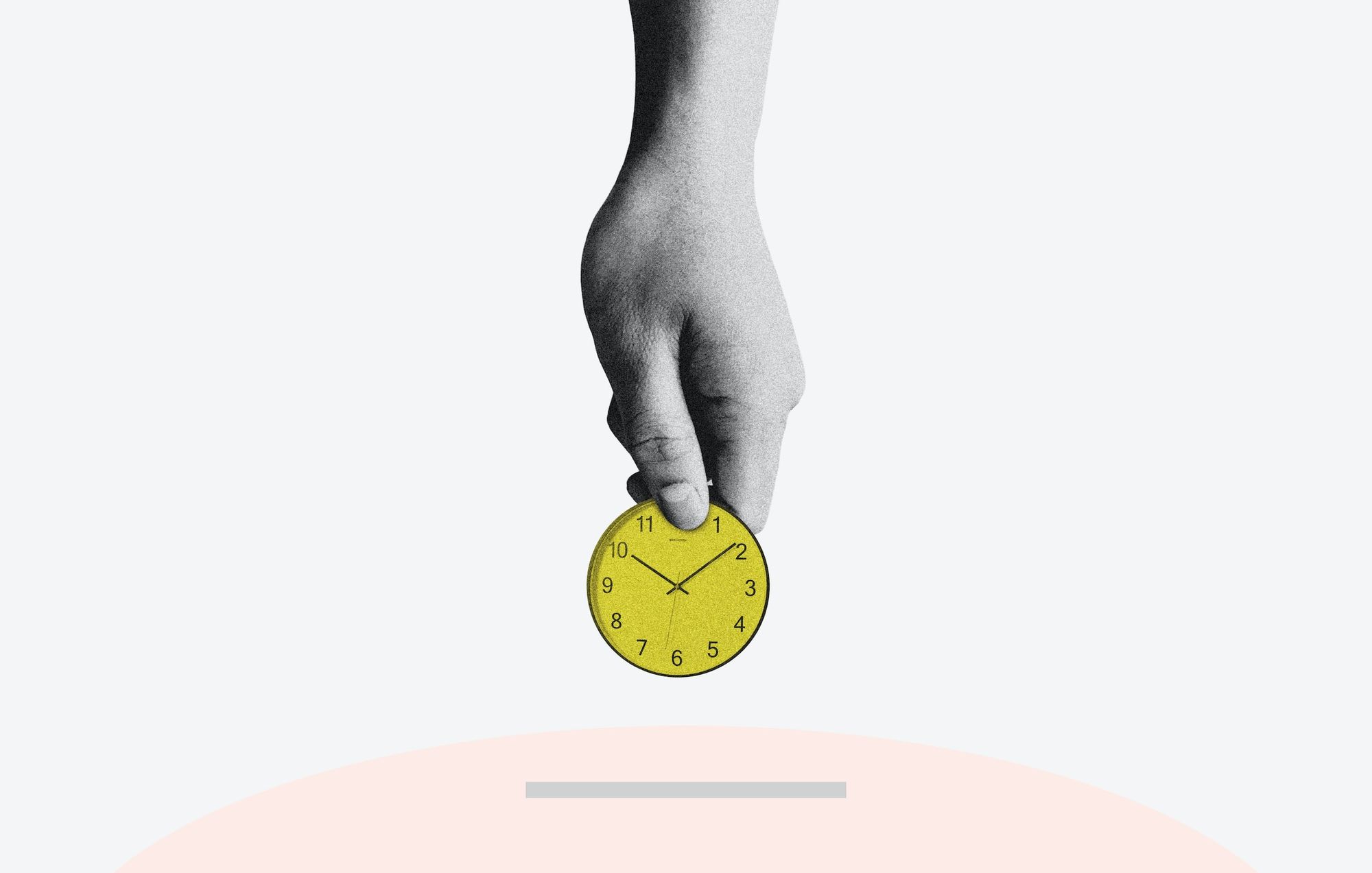