Are you a business owner trying to understand the impact of accurate production scheduling on your business’s profit margins? If yes, then you are on the right page.
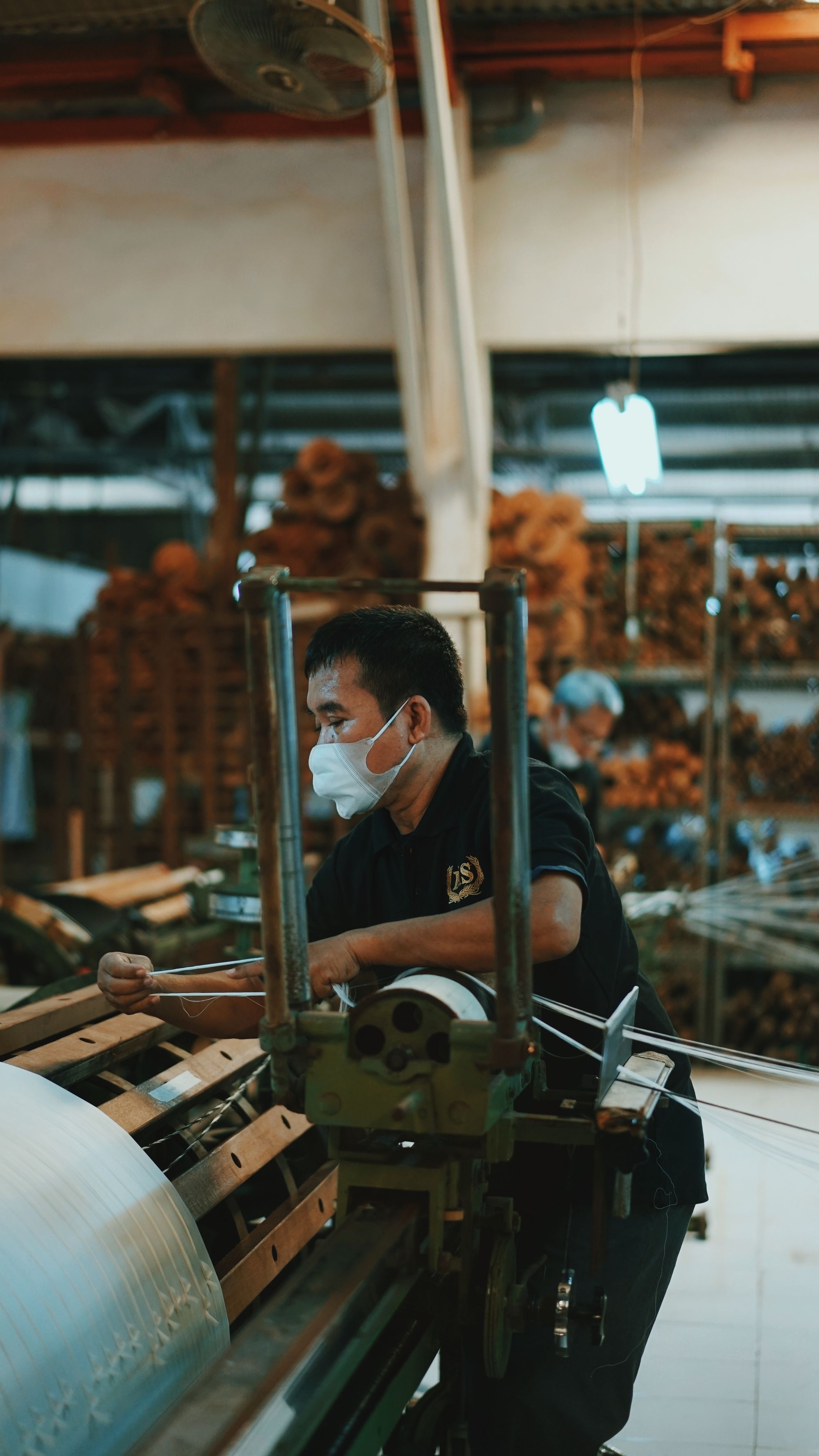
Accurate production scheduling plays a pivotal role in shaping the operational efficiency and financial performance of manufacturing and production-centric businesses. An effective production schedule ensures that resources are optimally utilized, production costs are minimized, and customer demands are met with precision.
However, the true measure of success lies in how accurate production scheduling directly impacts a company's profit margins. The ability to produce and deliver products efficiently and on time can significantly influence cost savings, customer satisfaction, revenue generation, and ultimately, the bottom line.
By comprehensively examining the multifaceted relationship between accurate production scheduling and profit margins, organizations can make informed strategic choices that drive profitability, bolster competitiveness, and establish a foundation for sustained success in a dynamic and ever-evolving marketplace.
Through the lens of accurate production scheduling, we unravel the factors that propel companies toward achieving their financial goals and embracing a future of optimized production processes and increased profitability.
In this article, we delve into the various aspects of measuring the impact of accurate production scheduling on profit margins.
The topics covered in this article are:
- What is Production Scheduling?
- All About Profit Margins
- What is Accurate Production Scheduling?
- Impact of Accurate Production Scheduling on Profit Margins
- How to Measure the Impact of Accurate Production Scheduling on Profit Margins?
- How Can Deskera Help You with Production Scheduling?
- Key Takeaways
- Related Articles
What is Production Scheduling?
Production scheduling is a critical process in manufacturing that involves planning, organizing, and optimizing the production of goods or services to meet customer demand efficiently.
It ensures that resources, such as labor, materials, and equipment, are utilized optimally to achieve maximum productivity and minimize production costs. Effective production scheduling helps companies deliver products on time, avoid excessive inventory, and improve overall operational efficiency.
Here's an overview of key aspects of production scheduling:
1.Objectives of Production Scheduling:
- Meeting customer demand: The primary goal of production scheduling is to ensure that customer orders are fulfilled on time and in the required quantities.
- Resource optimization: Production scheduling aims to allocate resources efficiently to minimize costs and maximize productivity.
- Inventory management: Scheduling production helps in maintaining optimal inventory levels to avoid overstocking or stockouts.
- Minimizing lead times: By optimizing production schedules, companies can reduce lead times, improving responsiveness to customer demands.
- Enhancing flexibility: Production scheduling allows companies to adapt quickly to changes in demand or production constraints.
2. Factors Considered in Production Scheduling:
- Customer demand: Production schedules are driven by customer orders and demand forecasts.
- Production capacity: Companies assess their production capacity to determine the feasibility of meeting demand within specific timelines.
- Resource availability: Scheduling considers the availability of labor, materials, and equipment needed for production.
- Lead times: The time required to procure materials, perform setups, and complete production runs influences scheduling decisions.
- Production constraints: Factors like machine availability, production sequencing, and shift schedules are considered in the scheduling process.
- Cost considerations: Production scheduling aims to minimize production costs, including labor, materials, and setup expenses.
3. Types of Production Scheduling:
- Forward Scheduling: Production starts as soon as materials and resources are available, working towards the delivery date.
- Backward Scheduling: Production begins at a specified delivery date, working backward to determine the start date and resource requirements.
- Infinite Scheduling: Production is scheduled without considering capacity constraints, suitable for processes with no resource limitations.
- Finite Scheduling: Scheduling that considers capacity constraints, ensuring resources are not overbooked or overloaded.
4. Production Scheduling Tools and Techniques:
- Production Planning Software: Advanced software solutions facilitate efficient production scheduling, resource allocation, and real-time monitoring.
- Kanban Systems: A lean production approach that uses visual cards or signals to control the flow of materials and maintain production balance.
- Just-In-Time (JIT) Manufacturing: A method that schedules production to meet customer demand precisely, reducing inventory costs and lead times.
- Material Requirements Planning (MRP): A system that plans production based on demand forecasts and the bill of materials.
- Advanced Planning and Scheduling (APS): Software that uses algorithms to optimize production schedules considering multiple variables and constraints.
In conclusion, production scheduling is a crucial process that enables manufacturing companies to operate efficiently, meet customer demands, optimize resources, and maintain a competitive advantage in the market. Accurate and well-organized production scheduling plays a pivotal role in driving business success and maximizing profitability.
All About Profit Margins
Profit margins are a fundamental financial metric that assesses a company's profitability and efficiency. It indicates the percentage of revenue that remains as profit after deducting all costs and expenses associated with generating that revenue. Profit margins are essential for understanding a company's financial health and its ability to generate profit from its operations.
Here's an overview of key aspects of profit margins:
1.Gross Profit Margin:
- Gross profit margin measures the profitability of a company's core business activities, excluding indirect costs such as administrative and selling expenses.
- It is calculated as (Gross Profit / Total Revenue) x 100.
- Gross profit is the revenue remaining after deducting the cost of goods sold (COGS).
2. Operating Profit Margin:
- The operating profit margin reflects a company's operating efficiency, including all direct and indirect costs related to its normal business operations.
- It is calculated as (Operating Profit / Total Revenue) x 100.
- Operating profit includes all operating expenses, such as COGS, selling expenses, administrative expenses, and research and development costs.
3. Net Profit Margin:
- Net profit margin is the most comprehensive profitability metric, representing the percentage of revenue that remains as profit after all expenses, taxes, and interest payments.
- It is calculated as (Net Profit / Total Revenue) x 100.
- Net profit includes all expenses, taxes, interest, and other non-operating income and expenses.
4. Importance of Profit Margins:
- Financial Health: Profit margins are a critical indicator of a company's financial health and long-term sustainability.
- Comparisons: Profit margins allow for comparisons between different companies or industries, helping investors and stakeholders assess relative profitability.
- Performance Measurement: Monitoring changes in profit margins over time helps evaluate a company's performance and efficiency.
- Investment Decision Making: Profit margins influence investment decisions as investors seek companies with strong and consistent profitability.
- Growth and Expansion: Higher profit margins provide companies with more resources for growth, research, and expansion.
5. Factors Affecting Profit Margins:
- Pricing Strategy: The pricing of products or services can impact profit margins.
- Cost Management: Effective cost control measures can improve profit margins.
- Sales Volume: Higher sales volume can boost overall profits.
- Efficiency: Improved operational efficiency leads to higher margins.
- Market Conditions: External factors like competition and economic conditions influence profit margins.
6. Limitations of Profit Margins:
- Industry Differences: Profit margins vary across industries, making direct comparisons challenging.
- Non-Operating Items: Non-operating items can distort profit margins, such as one-time gains or losses.
- Manipulation: Companies may use accounting practices to manipulate reported profit margins.
In conclusion, profit margins are crucial metrics for assessing a company's profitability, financial health, and efficiency. Understanding different types of profit margins and their implications helps investors, stakeholders, and management make informed decisions and evaluate the overall performance of a business.
What is Accurate Production Scheduling?
Accurate production scheduling is a systematic and data-driven approach to planning and organizing production activities in a way that optimizes resources, minimizes costs, and meets customer demands efficiently.
It involves creating detailed production plans that take into account various factors, such as demand forecasts, production capacity, resource availability, lead times, and production constraints.
The main goal of accurate production scheduling is to ensure that products are manufactured at the right time, in the right quantities, and with the right resources, while maintaining high-quality standards.
Key characteristics of accurate production scheduling include:
- Demand Forecasting: Accurate production scheduling starts with reliable demand forecasting. Companies use historical data, market trends, and customer behavior analysis to predict future demand more accurately. This helps in planning production runs that align closely with customer orders and anticipated demand.
- Resource Optimization: Production scheduling aims to allocate resources, such as labor, materials, and equipment, efficiently. By matching resource availability with production needs, companies can maximize productivity and minimize production costs.
- Real-Time Monitoring: Advanced production scheduling systems often include real-time monitoring capabilities. This allows companies to track the progress of production runs, identify potential issues or delays, and make timely adjustments to ensure smooth operations.
- Flexibility and Adaptability: Accurate production scheduling takes into account the dynamic nature of business environments. It allows companies to adjust production plans quickly in response to changing market conditions, customer demands, or unforeseen disruptions.
- Minimizing Idle Time: Production schedules aim to minimize idle time between production runs or tasks. This reduces downtime and ensures that equipment and resources are utilized optimally.
- Just-In-Time (JIT) Principles: Accurate production scheduling often incorporates JIT principles, where production is closely aligned with customer demand. JIT practices help companies avoid excessive inventory, reduce carrying costs, and improve responsiveness to market changes.
- Contingency Planning: Accurate production scheduling involves contingency planning to address potential disruptions or delays. Having alternative plans in place ensures that companies can respond effectively to unexpected events.
- Integration with Supply Chain: Production scheduling is not limited to a company's internal operations. It also involves coordination with suppliers and logistics partners to ensure smooth supply chain operations.
- Focus on Quality: Accurate production scheduling aims to maintain product quality and consistency. It allows sufficient time for quality checks and ensures that production schedules do not compromise on product standards.
- Continuous Improvement: Companies that practice accurate production scheduling often seek opportunities for continuous improvement. They analyze production data, identify areas for optimization, and implement changes to enhance efficiency and effectiveness.
In summary, accurate production scheduling is a critical process that enables manufacturing companies to operate efficiently, meet customer demands, optimize resources, and maintain a competitive advantage in the market. It involves careful planning, data analysis, and proactive decision-making to achieve optimal results in production operations.
Impact of Accurate Production Scheduling on Profit Margins
Accurate production scheduling can have a significant impact on profit margins for manufacturing companies. It plays a crucial role in optimizing resources, minimizing downtime, and maximizing productivity.
Here are some key ways in which accurate production scheduling can affect profit margins:
Reduced Production Costs
Reduced production costs focuses on how accurate production scheduling can help manufacturing companies lower their overall production expenses. Let's delve deeper into the key aspects of this point:
- Efficient Resource Allocation: Accurate production scheduling allows companies to plan and allocate resources more effectively. This includes labor, raw materials, energy, and other inputs required for production. By having a precise understanding of the production requirements and timelines, manufacturers can avoid overstaffing or underutilization of resources, reducing associated labor costs.
- Minimized Wastage: When production is scheduled accurately, there is less chance of producing more than what is required (overproduction). Overproduction can lead to excess inventory and increase holding costs. Additionally, when production runs are better planned, there is less likelihood of errors, reworks, or defects, leading to reduced scrap and material wastage.
- Optimal Batch Sizing: Accurate production scheduling allows manufacturers to determine the most appropriate batch sizes for production runs. By optimizing batch sizes, companies can achieve economies of scale and reduce setup costs, resulting in lower production costs per unit.
- Reduced Setup Times: Efficient scheduling enables manufacturers to sequence production runs in a way that minimizes setup times between different product batches. Quick changeovers between products or production processes lead to less downtime and increased productivity.
- Just-In-Time (JIT) Manufacturing: Accurate production scheduling aligns well with JIT principles, where materials and components are delivered just when they are needed for production. This approach helps in reducing inventory carrying costs, as companies only hold the necessary materials, reducing storage and handling expenses.
- Energy and Equipment Optimization: Proper scheduling ensures that machines and equipment are utilized optimally. By avoiding unnecessary idle time and running equipment at their peak efficiency, energy consumption is minimized, resulting in lower utility costs.
- Streamlined Production Flow: Accurate scheduling optimizes the flow of production, eliminating bottlenecks and reducing wait times between production stages. This results in a smoother production process, which in turn reduces delays and inefficiencies that can increase costs.
- Data-Driven Decision Making: Advanced production scheduling tools use historical data and real-time information to optimize production plans. By making data-driven decisions, companies can identify cost-saving opportunities and improve overall production efficiency.
- Continuous Improvement: Accurate production scheduling is an iterative process that allows companies to continuously improve their operations. By monitoring performance metrics and analyzing scheduling data, manufacturers can identify areas for improvement and implement cost-saving measures.
- Supplier Coordination: Accurate scheduling enables better coordination with suppliers, ensuring that materials and components are available precisely when needed. This minimizes delays in the supply chain and avoids expedited shipping costs or production disruptions due to material shortages.
By addressing these aspects and incorporating accurate production scheduling practices, manufacturing companies can effectively reduce their production costs, leading to improved profit margins and a more competitive position in the market.
Minimized Inventory Costs
It emphasizes on how accurate production scheduling can help manufacturing companies reduce their inventory holding costs. Efficient inventory management is crucial as excessive inventory can tie up valuable capital, lead to increased storage expenses, and pose the risk of obsolescence.
Here's a more detailed explanation of how minimized inventory costs are achieved through accurate production scheduling:
- Demand Forecasting: Accurate production scheduling starts with reliable demand forecasting. By analyzing historical data, market trends, and customer behavior, companies can predict demand more accurately. This ensures that production is aligned with expected sales, reducing the need for excessive inventory.
- Just-In-Time (JIT) Inventory: JIT principles are often incorporated into accurate production scheduling. Instead of stockpiling large quantities of raw materials or finished goods, companies keep inventory levels lean by receiving materials and producing goods just in time for customer demand. This approach reduces carrying costs and the risk of inventory obsolescence.
- Safety Stock Optimization: Safety stock is the buffer inventory held to account for unexpected fluctuations in demand or supply chain disruptions. Accurate production scheduling helps in optimizing safety stock levels by factoring in variability in demand and lead times. This ensures that safety stock is minimized without compromising on customer service levels.
- Reduced Carrying Costs: Carrying costs include expenses related to warehousing, handling, insurance, and depreciation of inventory. Accurate production scheduling minimizes the time inventory spends in storage, leading to lower carrying costs overall.
- Lower Holding Expenses: By avoiding overproduction and optimizing inventory levels, companies can reduce the need for additional storage space. This helps in saving on rental or infrastructure costs associated with warehousing.
- Inventory Turnover Improvement: Accurate production scheduling facilitates higher inventory turnover rates. Higher turnover means that inventory is sold and replenished more frequently, leading to a faster conversion of inventory into revenue and reduced carrying costs.
- Avoidance of Obsolete Inventory: Overproduction or inaccurate demand forecasting can lead to the accumulation of obsolete inventory that cannot be sold. Accurate production scheduling minimizes overproduction, reducing the risk of obsolete stock and potential losses associated with disposing of such inventory.
- Lower Working Capital Requirements: Leaner inventory levels through accurate production scheduling mean that less working capital is tied up in inventory. This releases cash that can be used for other critical business needs, such as investment in new technologies, marketing, or debt reduction.
- Improved Inventory Tracking: Accurate production scheduling often involves the use of advanced inventory tracking systems. This helps companies have real-time visibility into their inventory levels, allowing them to make informed decisions about production and purchasing to avoid stockouts or excess inventory.
- Enhanced Supplier Relationships: Better production scheduling enables companies to communicate their inventory needs more effectively to suppliers. This fosters stronger partnerships and may lead to more favorable terms, such as discounts for bulk orders or reduced lead times, further optimizing inventory costs.
By focusing on minimizing inventory costs through accurate production scheduling, manufacturing companies can streamline their operations, improve financial performance, and maintain a competitive edge in the market.
Improved Equipment Utilization
It highlights how accurate production scheduling can lead to better use of machinery and equipment in manufacturing processes. Efficient equipment utilization is crucial for maximizing productivity and reducing operational costs.
Here's a more detailed explanation of how improved equipment utilization is achieved through accurate production scheduling:
- Reduced Downtime: Accurate production scheduling helps in planning production runs more efficiently, minimizing the idle time between different product batches. This reduced downtime ensures that machines and equipment are operational for a larger portion of the production schedule, increasing overall productivity.
- Optimized Workflows: Proper scheduling enables companies to sequence production tasks in a way that minimizes the time spent on changeovers and setups. This streamlined workflow ensures that equipment is used more effectively and reduces time wasted during transitions between different products or production processes.
- Balancing Workloads: Accurate production scheduling ensures that workloads are balanced across different machines and workstations. It helps avoid bottlenecks and prevents situations where some equipment is overutilized while others remain underutilized.
- Preventive Maintenance Planning: Through production scheduling, companies can proactively plan maintenance and equipment servicing during planned downtime. Regular maintenance ensures that machinery operates at peak efficiency and minimizes unexpected breakdowns, preventing prolonged unplanned downtimes that can impact production schedules.
- Efficient Job Sequencing: Scheduling production jobs in a logical sequence based on equipment requirements and product characteristics can help in optimizing equipment utilization. This may involve grouping similar products together, taking into account material compatibility, and reducing setup times between successive jobs.
- Eliminating Overtime: With accurate production scheduling, companies can better match production output with demand, reducing the need for overtime to meet customer orders. This not only improves equipment utilization but also helps control labor costs.
- Avoiding Overproduction: Overproduction can tie up equipment and inventory unnecessarily. Accurate production scheduling ensures that production quantities align closely with demand, preventing excessive use of equipment and associated costs.
- Real-Time Monitoring: Advanced production scheduling systems often include real-time monitoring of equipment performance. This provides insights into machine efficiency, identifying potential bottlenecks, and helping operators and managers make data-driven decisions to enhance equipment utilization.
- Flexibility and Adaptability: Accurate production scheduling allows companies to adjust production plans quickly in response to changing demands or unexpected disruptions. This flexibility ensures that equipment is utilized efficiently even under varying conditions.
- Improved Overall Efficiency: When equipment is utilized optimally, overall production efficiency improves, leading to higher output levels without additional capital investments. This translates to increased revenue potential and improved profit margins.
By incorporating accurate production scheduling practices, manufacturing companies can make the most of their machinery and equipment, reducing downtime, improving efficiency, and enhancing overall productivity. This contributes to cost savings, better resource utilization, and a competitive advantage in the market.
Better Customer Satisfaction
It emphasizes how accurate production scheduling can positively impact customer satisfaction levels. Satisfied customers are more likely to remain loyal to a brand, place repeat orders, and recommend the company to others, which ultimately leads to increased sales and revenue.
Here's a more detailed explanation of how accurate production scheduling contributes to better customer satisfaction:
- On-Time Deliveries: Accurate production scheduling ensures that products are manufactured and delivered to customers on time. Meeting delivery deadlines is crucial for building trust and credibility with customers. When customers receive their orders promptly, they are more likely to view the company as reliable and dependable.
- Reduced Lead Times: Efficient production scheduling can help reduce lead times from order placement to delivery. Shorter lead times meet customer demands for faster service and can be a competitive advantage, especially in industries with high customer expectations for rapid fulfillment.
- Consistent Product Availability: By aligning production schedules with demand forecasts, companies can maintain consistent product availability. Customers appreciate having access to products whenever they need them, which fosters loyalty and reduces the risk of losing customers to competitors.
- Customization and Personalization: Accurate production scheduling allows companies to handle custom orders and personalized products effectively. This capability enhances the customer experience by meeting individual preferences and requirements.
- Fewer Backorders: Accurate production scheduling helps prevent situations where products are out of stock, resulting in backorders. Customers dislike waiting for products that are not immediately available, and backorders can lead to frustration and lost sales opportunities.
- Enhanced Order Accuracy: Efficient production scheduling reduces the likelihood of errors in order processing. When customers receive the correct products in the right quantities, it enhances their satisfaction and reduces the need for returns and exchanges.
- Responsiveness to Demand Surges: During periods of high demand, accurate production scheduling allows companies to scale up production appropriately. Meeting increased demand promptly demonstrates a commitment to customer satisfaction and can help retain customers during peak times.
- Quality Assurance: Proper production scheduling ensures that adequate time and resources are allocated to each production run. This attention to detail enhances quality control measures, resulting in higher-quality products that meet or exceed customer expectations.
- Effective Communication: Accurate production scheduling facilitates better communication with customers. Companies can provide accurate and up-to-date information regarding order status, delivery times, and any potential delays, keeping customers informed and engaged.
- Continuous Improvement: By using production scheduling data and customer feedback, companies can identify areas for improvement and implement changes to enhance the customer experience continually. Customers value companies that actively seek feedback and make efforts to improve their services.
Overall, accurate production scheduling plays a vital role in meeting customer expectations and providing a positive experience throughout the entire order fulfillment process. By consistently delivering on time, offering customization options, maintaining product availability, and focusing on quality, companies can build strong customer relationships, foster loyalty, and drive business growth.
Enhanced Planning and Decision Making
It highlights how accurate production scheduling can empower manufacturing companies with better planning and decision-making capabilities. By having access to precise production schedules and data-driven insights, companies can make informed choices that lead to more efficient operations and improved overall performance.
Here's a more detailed explanation of how enhanced planning and decision-making are achieved through accurate production scheduling:
- Resource Allocation: Accurate production scheduling provides a clear picture of production requirements and timelines. This enables companies to allocate resources, including labor, materials, and equipment, more effectively. Proper resource planning ensures that the right resources are available when needed, avoiding shortages and overstaffing.
- Capacity Planning: By understanding production schedules and demands, companies can assess their production capacity accurately. This allows them to identify potential bottlenecks and plan for capacity expansions or upgrades when necessary to meet future demands.
- Forecasting and Demand Planning: Accurate production scheduling involves detailed demand forecasting and demand planning. Companies can use historical data, market trends, and customer insights to predict demand more accurately, allowing for better production planning to meet future customer needs.
- Inventory Management: Production scheduling helps in optimizing inventory levels. By analyzing demand forecasts and lead times, companies can maintain lean inventory levels, reducing carrying costs while ensuring sufficient stock to meet customer demands.
- Cost Analysis: Accurate production scheduling facilitates cost analysis by providing data on production expenses, labor costs, and resource utilization. Companies can evaluate the cost-effectiveness of different production plans and make data-driven decisions to minimize costs.
- Production Efficiency: With proper production scheduling, companies can identify inefficiencies in their production processes. Analyzing production data helps in finding areas that require improvement, allowing for continuous process optimization.
- New Product Introductions: When introducing new products, accurate production scheduling is crucial to ensure a smooth launch. Companies can plan production runs, assess resource requirements, and align marketing and sales efforts to meet customer demand.
- Risk Management: Scheduling production accurately allows companies to identify potential risks in advance. By assessing production schedules and potential constraints, companies can plan for contingencies and mitigate risks effectively.
- Strategic Investments: Accurate production scheduling provides insights into the capacity and efficiency of existing production assets. This data helps in making informed decisions regarding investments in new equipment or technology upgrades.
- Adaptability to Market Changes: Companies with accurate production scheduling are more adaptable to market fluctuations and changes in customer demand. They can adjust production plans quickly to seize opportunities or address challenges as they arise.
By leveraging accurate production scheduling, manufacturing companies can gain a competitive edge by making well-informed decisions that optimize resources, reduce costs, and enhance overall efficiency. It enables them to align production with demand, respond to changing market conditions, and drive long-term success in their industry.
Reduced Overtime and Rush Orders
It highlights how accurate production scheduling can help manufacturing companies avoid excessive overtime and rush orders, which can be costly and impact productivity and employee morale. Here's a more detailed explanation of how accurate production scheduling contributes to reducing overtime and rush orders:
- Optimal Resource Planning: Accurate production scheduling allows companies to plan production runs more efficiently. By matching production schedules with demand forecasts, companies can avoid situations where additional work hours are required to meet customer orders.
- Balanced Workloads: Effective scheduling helps in distributing workloads evenly, preventing situations where certain shifts or departments are consistently overloaded while others are underutilized. This balanced approach reduces the need for overtime to compensate for uneven work distribution.
- Eliminating Production Bottlenecks: Accurate production scheduling helps in identifying potential bottlenecks in the production process. By addressing these bottlenecks proactively, companies can avoid delays that might lead to overtime to meet production deadlines.
- Improved Equipment Utilization: As mentioned earlier, accurate production scheduling leads to better equipment utilization, minimizing the need for extended production hours to achieve required output levels.
- Strategic Shift Planning: With accurate production scheduling, companies can plan and optimize employee work schedules more effectively. This can help reduce overtime costs and increase workforce productivity.
- Preventing Stockouts: Proper scheduling ensures that production runs are aligned with demand forecasts. By avoiding stockouts, rush orders are less likely to occur, reducing the need for expedited production and shipping, which can be costly.
- Efficient Order Fulfillment: Accurate production scheduling enables companies to plan production runs based on customer orders and demand forecasts. This approach allows for timely and efficient order fulfillment without the need for last-minute rushes.
- Lean Production Practices: Implementing accurate production scheduling often goes hand-in-hand with adopting lean production principles. Lean manufacturing aims to eliminate waste and improve efficiency, which can significantly reduce the need for overtime and rush orders.
- Realistic Lead Time Commitments: By having a clear view of production schedules and capacity, companies can provide customers with realistic lead time commitments. Avoiding overpromising and setting achievable delivery times reduces the risk of rush orders due to unmet expectations.
- Employee Satisfaction: Reduced overtime and rush orders contribute to a healthier work-life balance for employees. By providing more predictable work schedules, employees can have a better quality of life and increased job satisfaction, which positively impacts productivity and reduces employee turnover.
In summary, accurate production scheduling enables companies to plan and execute production runs more efficiently, leading to reduced overtime, better workforce planning, and a smoother production process.
By avoiding rush orders and excessive overtime, manufacturing companies can improve cost-effectiveness, employee morale, and overall operational performance.
Lower Penalty Costs
It emphasizes how accurate production scheduling can help manufacturing companies avoid or reduce penalty costs associated with late deliveries or non-compliance with contractual obligations. Meeting delivery deadlines is crucial for maintaining strong business relationships and avoiding financial penalties.
Here's a more detailed explanation of how accurate production scheduling contributes to lower penalty costs:
- Timely Deliveries: Accurate production scheduling ensures that production runs are planned and executed in a way that meets customer delivery deadlines and contractual agreements. Delivering products on time reduces the risk of incurring penalties for late deliveries.
- Contractual Compliance: Many contracts with customers or suppliers include specific terms regarding delivery schedules, lead times, or performance requirements. By adhering to these contractual obligations through proper scheduling, companies can avoid penalties for non-compliance.
- Buffer Time Planning: Accurate production scheduling often involves incorporating buffer time into production plans. This buffer accounts for unforeseen delays and uncertainties in the production process, reducing the risk of missing delivery deadlines and incurring penalties.
- Real-Time Monitoring: Advanced production scheduling tools may include real-time monitoring capabilities. This allows companies to track the progress of production runs and identify potential delays early on, enabling them to take corrective actions to avoid penalties.
- Supply Chain Coordination: Accurate production scheduling extends beyond a company's internal operations and includes coordination with suppliers and logistics partners. By ensuring smooth supply chain coordination, companies can avoid disruptions that might lead to late deliveries and subsequent penalties.
- Contingency Planning: Accurate production scheduling involves contingency planning for unforeseen events that could impact production timelines. By having alternative plans in place, companies can minimize the risk of delays and penalties if unexpected issues arise.
- Improved Communication: Efficient production scheduling fosters better communication between different departments and stakeholders involved in the production process. This improved communication helps in addressing potential roadblocks promptly and ensuring that everyone is aligned with the delivery schedule.
- Proactive Issue Resolution: With accurate production scheduling, companies can proactively identify and address potential issues that could lead to delays. By resolving problems early on, companies can mitigate the risk of penalties resulting from late deliveries.
- Reputation Management: Meeting delivery deadlines consistently enhances a company's reputation for reliability and professionalism. A strong reputation can lead to better business opportunities and fewer penalties related to contractual non-compliance.
- Customer Satisfaction: On-time deliveries are essential for customer satisfaction. Satisfied customers are less likely to impose penalties for late deliveries and are more inclined to maintain long-term partnerships with reliable suppliers.
In conclusion, accurate production scheduling plays a crucial role in helping manufacturing companies avoid or minimize penalty costs associated with late deliveries and contractual non-compliance.
By delivering products on time, adhering to contractual obligations, and implementing effective contingency planning, companies can protect their bottom line and maintain positive relationships with customers and partners.
Increased Flexibility and Adaptability
It underscores how accurate production scheduling can enhance a manufacturing company's ability to respond to changing market conditions, customer demands, and unforeseen disruptions. Flexibility and adaptability are crucial in modern business environments, where market dynamics can shift rapidly.
Here's a more detailed explanation of how accurate production scheduling contributes to increased flexibility and adaptability:
- Rapid Response to Market Changes: Accurate production scheduling allows companies to adjust their production plans quickly in response to changes in market demand, new product opportunities, or shifts in consumer preferences. This agility enables companies to capitalize on emerging opportunities and stay ahead of competitors.
- Efficient Resource Reallocation: With accurate production scheduling, companies can identify underutilized resources and redirect them to more profitable products or customer orders. This flexibility helps optimize resource allocation, leading to improved efficiency and cost-effectiveness.
- Customization and Personalization: Modern consumers often demand customized or personalized products. Accurate production scheduling allows companies to incorporate customization into their manufacturing processes efficiently, offering tailored products to meet specific customer needs.
- Seasonal Demand Variations: Many industries experience seasonal fluctuations in demand. Accurate production scheduling helps companies anticipate and prepare for these variations, ensuring that they have the capacity to meet peak demand periods without incurring excessive costs during low-demand periods.
- New Product Introductions: Introducing new products requires adaptability in the production process. Accurate production scheduling enables companies to plan and execute the launch of new products efficiently, ensuring a smooth transition into production.
- Supply Chain Disruptions: Unforeseen disruptions in the supply chain can impact production schedules. Accurate production scheduling allows companies to quickly adjust production plans and source materials from alternative suppliers to mitigate the effects of disruptions.
- Continuous Process Improvement: With accurate production scheduling, companies can analyze production data and identify opportunities for improvement. The ability to make data-driven decisions enhances the company's adaptability by implementing changes that optimize efficiency and productivity.
- Real-Time Monitoring and Decision Making: Advanced production scheduling systems often include real-time monitoring capabilities. This enables companies to monitor production progress and respond swiftly to any deviations from the plan, facilitating real-time decision-making.
- Lean Manufacturing Practices: Accurate production scheduling is often aligned with lean manufacturing principles, which focus on eliminating waste and improving efficiency. Adopting lean practices enhances a company's adaptability by streamlining processes and reducing lead times.
- Product Mix Adjustments: Companies may need to adjust their product mix based on changing market demand or economic conditions. Accurate production scheduling allows for easy transitions between different product lines to meet evolving customer preferences.
In conclusion, accurate production scheduling equips manufacturing companies with the flexibility and adaptability needed to thrive in dynamic business environments.
By quickly responding to market changes, efficiently reallocating resources, and implementing continuous improvements, companies can stay competitive and deliver value to their customers while maintaining operational efficiency and profitability.
Competitive Advantage
It emphasizes how accurate production scheduling can provide manufacturing companies with a distinct edge over their competitors in the market. A well-executed production scheduling strategy can enhance efficiency, responsiveness, and customer satisfaction, which contribute to gaining a competitive edge.
Here's a more detailed explanation of how accurate production scheduling leads to a competitive advantage:
- Improved Efficiency: Accurate production scheduling optimizes production processes, reduces downtime, and minimizes wastage, leading to increased overall efficiency. Companies that can produce more output with fewer resources have a cost advantage, allowing them to offer competitive prices to customers.
- Faster Time-to-Market: Efficient production scheduling enables quicker response times, allowing companies to bring products to market faster. This agility helps capitalize on emerging trends and meet customer demands promptly, gaining an edge over slower competitors.
- Customization and Personalization: With accurate production scheduling, companies can efficiently handle customization and personalization requests from customers. The ability to offer tailored products sets them apart from competitors with limited customization capabilities.
- On-Time Deliveries: Meeting delivery deadlines consistently through accurate production scheduling enhances customer satisfaction. Companies that reliably deliver products on time are more likely to attract and retain customers compared to those with a history of late deliveries.
- Adaptability to Market Changes: Accurate production scheduling allows companies to adapt quickly to changing market conditions, consumer preferences, and demand fluctuations. This adaptability enables them to stay ahead of competitors that may struggle to adjust their operations promptly.
- Better Resource Utilization: Efficient production scheduling ensures that resources are utilized optimally, minimizing wastage and unnecessary costs. Competitors with less streamlined processes may incur higher expenses, giving the more efficient company a competitive advantage.
- Lean Manufacturing: Companies adopting accurate production scheduling often implement lean manufacturing principles. Lean practices focus on eliminating waste and increasing value-added activities, enhancing competitiveness by reducing costs and lead times.
- Stronger Supplier Relationships: Accurate production scheduling involves better coordination with suppliers, fostering stronger partnerships. Favorable relationships with suppliers can lead to preferential terms, reduced lead times, and better pricing, providing a competitive edge.
- Enhanced Customer Satisfaction: Accurate production scheduling leads to improved customer satisfaction due to on-time deliveries, product quality, and flexibility in meeting customer demands. Satisfied customers are more likely to remain loyal and recommend the company to others.
- Continuous Improvement: Companies utilizing accurate production scheduling are more likely to embrace continuous improvement initiatives. By constantly seeking ways to enhance efficiency and quality, they can maintain a competitive edge over competitors with stagnant processes.
In conclusion, accurate production scheduling is a powerful tool that enables manufacturing companies to gain a competitive advantage in the market.
By leveraging the efficiency, adaptability, customer satisfaction, and continuous improvement, companies can differentiate themselves from their competitors and position themselves as industry leaders, driving business growth and long-term success.
Improved Cash Flow
It highlights how accurate production scheduling can positively impact a manufacturing company's cash flow, which is essential for maintaining financial stability and supporting business operations.
Accurate production scheduling can lead to smoother production cycles, reduced inventory costs, and more predictable revenue streams, all of which contribute to better cash flow management.
Here's a more detailed explanation of how improved cash flow is achieved through accurate production scheduling:
- Reduced Inventory Carrying Costs: Accurate production scheduling helps companies maintain optimal inventory levels. By avoiding excessive inventory, businesses can reduce inventory carrying costs, including storage, insurance, and handling expenses. Lower inventory costs free up cash that can be used for other business needs.
- Faster Inventory Turnover: Accurate production scheduling aligns production with actual demand, ensuring that inventory is sold and replenished more quickly. Faster inventory turnover means cash is tied up for shorter periods, allowing companies to reinvest the capital in other areas of the business.
- Just-In-Time (JIT) Inventory: Accurate production scheduling often involves implementing JIT inventory practices. JIT principles minimize the amount of inventory held in stock, freeing up cash that would otherwise be invested in maintaining excess inventory.
- Timely Invoicing and Payments: With accurate production scheduling, companies can deliver products on time, leading to timely invoicing and payments. Improved cash flow occurs when customers pay promptly for delivered goods, reducing the need for extended credit terms.
- Reduced Downtime Costs: Efficient production scheduling minimizes downtime and idle time for machinery and equipment. This reduction in downtime translates to increased productivity, generating more revenue and cash flow for the company.
- Better Credit Management: Accurate production scheduling enables companies to manage their production cycles and payment terms more effectively. This, in turn, allows businesses to negotiate favorable credit terms with suppliers and manage payment schedules to optimize cash flow.
- Improved Financial Planning: With accurate production scheduling, companies can forecast production-related cash flows more accurately. This enables better financial planning, ensuring that cash reserves are available to meet operational needs, capital expenditures, and debt obligations.
- Effective Resource Utilization: By optimizing resource allocation and avoiding overproduction, accurate production scheduling helps reduce unnecessary expenses, freeing up cash for more strategic investments.
- Cash Flow Forecasting: Accurate production scheduling provides a clearer picture of production timelines and customer demands. This data can be used to create more accurate cash flow forecasts, assisting in better cash flow management and planning for future financial needs.
- Opportunity for Investments: Improved cash flow gives companies the financial capacity to invest in growth opportunities, research, and development, new technologies, or expanding into new markets. Having surplus cash allows companies to pursue strategic initiatives that drive long-term success.
In conclusion, accurate production scheduling plays a vital role in improving a manufacturing company's cash flow management. By reducing inventory carrying costs, increasing inventory turnover, facilitating timely invoicing and payments, and optimizing resource utilization, accurate production scheduling contributes to a healthier cash flow position, supporting business stability and growth.
How to Measure the Impact of Accurate Production Scheduling on Profit Margins?
Measuring the impact of accurate production scheduling on profit margins requires a comprehensive analysis of various financial and operational metrics. Here are the key steps to measure this impact:
Data Collection
Data Collection emphasizes the importance of gathering relevant and accurate data to measure the impact of accurate production scheduling on profit margins.
Data collection is the foundation of any analysis and evaluation process, providing the necessary information for assessing the effectiveness of production scheduling practices.
Here's a more detailed explanation of data collection in this context:
- Production Scheduling Data: Collect data related to the production schedules, including production dates, start and end times of each task, allocated resources (labor and equipment), and planned production quantities. This data provides insights into how production runs are organized and whether they are aligned with demand.
- Financial Performance Data: Gather financial data, including revenue, cost of goods sold (COGS), operating expenses, and net profit. This information helps determine the overall profitability of the company and the financial impact of production scheduling changes.
- Inventory Data: Access data on inventory levels, both raw materials and finished goods. Analyze the changes in inventory levels before and after accurate production scheduling implementation to assess the impact on inventory management and carrying costs.
- Sales Data: Collect sales data, including sales volumes, customer orders, and order fulfillment status. This data helps determine whether accurate production scheduling leads to increased sales and customer satisfaction.
- Customer Satisfaction Metrics: Gather customer feedback and satisfaction scores to evaluate how accurate production scheduling affects customer experiences. Feedback from customers can highlight improvements in product availability, on-time deliveries, and overall service quality.
- Employee Productivity Data: Collect data on employee productivity, including production output per employee, idle time, and the number of setups or changeovers required. This data allows for an assessment of how production scheduling influences employee efficiency and resource utilization.
- Quality Control Data: Access quality control data, such as defect rates and rework percentages, to assess the impact of production scheduling on product quality. Efficient production scheduling should allow sufficient time for quality checks and reduce the likelihood of defects and rework.
- Lead Time Data: Analyze lead time data to understand the impact of accurate production scheduling on order-to-delivery times. A reduction in lead times can lead to improved customer satisfaction and increased repeat business.
- Supplier Performance Data: Collect data on supplier performance, including lead times for raw materials and supplier reliability. Improved production scheduling may enhance relationships with suppliers and reduce lead times for materials, positively impacting production efficiency.
- Historical Data: Analyze historical data on production scheduling and financial performance to establish baseline metrics. Comparing current data with historical data helps identify trends and improvements resulting from accurate production scheduling implementation.
- Real-Time Monitoring Data: If the company utilizes real-time monitoring tools or software for production scheduling, collect relevant data from these systems. Real-time monitoring data provides insights into current production progress and any deviations from the planned schedule.
In conclusion, data collection is a crucial step in measuring the impact of accurate production scheduling on profit margins.
The gathered data forms the basis for analysis and evaluation, enabling companies to make data-driven decisions to optimize their production processes and enhance financial performance.
Accurate and comprehensive data collection ensures that the evaluation process is robust and provides actionable insights to drive continuous improvement.
Establish Baseline Metrics
It refers to the process of defining and recording key performance indicators (KPIs) and other relevant metrics before implementing accurate production scheduling practices.
These baseline metrics serve as a benchmark for comparison and help measure the impact of the changes made to production scheduling on various aspects of a company's performance.
Here's a more detailed explanation of establishing baseline metrics:
- Identify Key Performance Indicators (KPIs): Determine the most relevant KPIs that will be used to assess the impact of accurate production scheduling. Common KPIs may include gross profit margin, operating profit margin, net profit margin, inventory turnover ratio, on-time delivery rate, customer satisfaction scores, lead times, and employee productivity metrics.
- Historical Data Collection: Gather historical data for the identified KPIs and metrics over a significant period before implementing the changes. This data could span several months or years, depending on the nature of the industry and business.
- Data Accuracy and Consistency: Ensure that the historical data collected is accurate, consistent, and recorded in a standardized manner. Any data discrepancies or anomalies should be addressed before establishing the baseline metrics.
- Financial Performance Metrics: Record financial metrics such as revenue, COGS, operating expenses, and net profit for the period under consideration. These financial indicators provide a clear picture of the company's profitability and efficiency before accurate production scheduling implementation.
- Inventory Metrics: Document inventory-related metrics, including inventory levels, turnover rates, and carrying costs. Understanding inventory metrics is essential for assessing the impact of production scheduling on inventory management.
- Delivery Metrics: Measure on-time delivery rates and lead times for customer orders. These metrics indicate how well the company meets customer expectations in terms of order fulfillment.
- Customer Satisfaction Metrics: Collect customer feedback and satisfaction scores to establish baseline customer satisfaction levels. This data provides insights into how customers perceive the company's product availability and delivery performance.
- Employee Productivity Metrics: Record employee productivity metrics, such as production output per employee and downtime. These metrics help assess the efficiency of production operations and resource utilization.
- Quality Control Metrics: Document quality control data, such as defect rates and rework percentages. This data provides insights into the quality of products before implementing accurate production scheduling changes.
- Data Visualization: Visualize the collected data using charts, graphs, or dashboards. Data visualization makes it easier to identify trends and patterns and facilitates communication of the baseline metrics to stakeholders.
- Document Findings: Summarize and document the baseline metrics and key findings. Clearly outline the current performance levels for each KPI and relevant metric to serve as a reference for comparison after implementing accurate production scheduling.
By establishing baseline metrics, companies create a starting point for measuring the effectiveness of accurate production scheduling changes.
Comparing the data collected before and after implementation enables companies to identify improvements, areas for further optimization, and the overall impact on profit margins and operational efficiency.
Having reliable baseline metrics ensures that the evaluation process is robust and provides valuable insights into the success of the production scheduling improvements.
Identify Key Performance Indicators (KPIs)
It refers to the process of selecting and defining the most important metrics that will be used to measure the impact of accurate production scheduling on various aspects of a company's performance. KPIs are critical performance metrics that align with the company's strategic goals and provide insights into its success and efficiency.
Here's a more detailed explanation of identifying key performance indicators:
- Relevance to Objectives: KPIs should directly align with the company's objectives and goals related to production scheduling. For example, if the primary goal is to improve on-time delivery, an on-time delivery rate KPI would be relevant.
- Quantifiable and Measurable: KPIs must be quantifiable and measurable, meaning they can be expressed in numerical terms and tracked over time. This allows for objective evaluation of progress and performance.
- Specific and Clear: Each KPI should be specific and clearly defined, leaving no room for ambiguity in its interpretation. This ensures that everyone in the organization understands the metric's meaning and purpose.
- Timeliness: KPIs should be updated and available in a timely manner to enable real-time or periodic assessment of performance. This helps in identifying issues promptly and making necessary adjustments.
- Balance: It is important to strike a balance in the selection of KPIs to ensure they cover different aspects of production scheduling and overall business performance. A combination of financial, operational, customer-focused, and employee-related KPIs provides a comprehensive view.
- Industry Standards: Consider industry-specific KPIs and benchmarks to gain insights into how the company compares to competitors or best practices within the industry.
- Alignment with Stakeholders: KPIs should be relevant and meaningful to various stakeholders, including management, employees, customers, and investors. Stakeholder buy-in is crucial for the success of KPI monitoring and performance improvement initiatives.
Examples of KPIs relevant to the impact of accurate production scheduling on profit margins and overall performance include:
- Gross Profit Margin: Indicates the profitability of core business activities by measuring revenue minus the cost of goods sold.
- On-Time Delivery Rate: Measures the percentage of customer orders delivered on or before the promised delivery date.
- Inventory Turnover Ratio: Evaluate the efficiency of inventory management by dividing the cost of goods sold by the average inventory value.
- Employee Productivity: Assesses the output per employee or labor cost per unit produced to measure workforce efficiency.
- Customer Satisfaction Scores: Gauges customer satisfaction through surveys or feedback to understand how well the company meets customer expectations.
- Lead Times: Measures the time taken from order placement to order delivery to assess the efficiency of the production process.
- Operating Profit Margin: Reflects the efficiency of a company's overall operations by measuring operating profit as a percentage of total revenue.
By identifying and monitoring these KPIs, companies can gain valuable insights into the impact of accurate production scheduling on various aspects of their business performance. Regularly tracking these metrics enables companies to make data-driven decisions, optimize their production processes, and drive continuous improvement in their operations.
Analyze Profit Margins
It involves examining the different components of profit margins before and after the implementation of accurate production scheduling. Analyzing profit margins provides valuable insights into the financial impact of production scheduling changes on a company's profitability and operational efficiency.
Here's a more detailed explanation of how to analyze profit margins:
- Calculate Different Profit Margins: Calculate various profit margins, including gross profit margin, operating profit margin, and net profit margin. Each margin provides a different perspective on the company's profitability and cost structure.
- Gross Profit Margin: This measures the profitability of a company's core business activities by deducting the cost of goods sold (COGS) from revenue. The formula is (Gross Profit / Total Revenue) x 100.
- Operating Profit Margin: This assesses the efficiency of a company's operations by including all operating expenses in addition to COGS. The formula is (Operating Profit / Total Revenue) x 100.
- Net Profit Margin: This is the most comprehensive profitability metric, taking into account all expenses, taxes, and interest payments. The formula is (Net Profit / Total Revenue) x 100.
- Compare Baseline Metrics: Compare the profit margins calculated before implementing accurate production scheduling (baseline metrics) with the profit margins after the changes have been implemented. Identify any significant changes in profit margins.
- Identify Factors Impacting Profit Margins: Analyze the factors that contributed to changes in profit margins. Consider factors such as changes in production costs, improvements in resource utilization, reductions in inventory carrying costs, and changes in sales volume or revenue.
- Cost Savings Analysis: Assess the impact of accurate production scheduling on production costs. Compare the costs incurred before and after implementation, including labor costs, material costs, setup costs, and other production-related expenses.
- Inventory Management: Analyze the effect of accurate production scheduling on inventory levels. Determine if there was a reduction in excess inventory or if inventory turnover improved, leading to cost savings.
- Revenue Impact: Investigate the impact of accurate production scheduling on revenue generation. Evaluate whether on-time deliveries and improved customer satisfaction led to increased sales or repeat business.
- Time Savings: Quantify the time saved in production due to better planning and scheduling. Reduced setup times, minimized idle time, and streamlined production processes contribute to increased productivity and cost savings.
- Return on Investment (ROI): Conduct a return on investment analysis to evaluate the financial benefits gained from implementing accurate production scheduling. Compare the cost of implementing new systems or software with the financial gains resulting from increased profit margins.
- Consider Long-Term Impact: Take into account the long-term effects of accurate production scheduling on profit margins. Some benefits may take time to materialize fully, such as improved supplier relationships, reduced lead times, and enhanced market reputation.
- Continuous Improvement: Use the analysis to identify areas for further optimization and continuous improvement in production scheduling and overall business operations. Iterate and refine the scheduling practices based on the insights gained.
By analyzing profit margins and understanding the factors that influenced changes, companies can make informed decisions to optimize production scheduling strategies and improve overall financial performance.
Continuous monitoring and analysis of profit margins help ensure that production scheduling practices remain effective and aligned with the company's financial goals and objectives.
Cost Savings Analysis
It involves assessing the impact of accurate production scheduling on production costs and identifying potential cost savings resulting from improved efficiency and resource utilization. Analyzing cost savings is crucial in understanding the financial benefits of accurate production scheduling and its contribution to overall profitability.
Here's a more detailed explanation of how to conduct a cost-savings analysis:
- Cost Components: Identify the different cost components involved in the production process. These may include labor costs, material costs, setup costs, overhead expenses, and any other production-related expenses.
- Baseline Cost Data: Gather historical data on production costs before implementing accurate production scheduling. This baseline data serves as a reference point for comparison.
- Post-Implementation Cost Data: After implementing accurate production scheduling, collect data on production costs during the same time period. Ensure that data collection methods and categorization are consistent with the baseline data.
- Comparison of Cost Data: Compare the production costs before and after implementing accurate production scheduling. Calculate the percentage change in each cost component to determine the cost savings.
- Labor Costs: Analyze the impact of production scheduling on labor costs. Determine if resource optimization and improved workflow reduced overtime hours or idle time, leading to lower labor expenses.
- Material Costs: Assess the effect of accurate production scheduling on material costs. Consider whether reduced lead times, better inventory management, or optimized production runs resulted in lower material expenses.
- Setup Costs: Evaluate the impact of accurate production scheduling on setup costs. Determine if more efficient scheduling and sequencing of production runs led to reduced setup times and associated expenses.
- Inventory Carrying Costs: Analyze the impact of accurate production scheduling on inventory levels. Determine if optimized production schedules led to lower inventory holding costs.
- Reduction in Downtime: Measure the reduction in downtime resulting from accurate production scheduling. Reduced downtime leads to increased production efficiency and cost savings.
- Maintenance Costs: Assess whether accurate production scheduling contributed to lower maintenance costs by reducing wear and tear on machinery and equipment.
- Improved Resource Utilization: Analyze the impact of accurate production scheduling on resource utilization. Determine if resources such as labor, equipment, and materials were used more efficiently, resulting in cost savings.
- Cost-Saving Initiatives: Consider any cost-saving initiatives or process improvements that were implemented as part of accurate production scheduling. Evaluate the financial impact of these initiatives on overall cost savings.
- ROI Analysis: Conduct a return on investment (ROI) analysis to quantify the financial benefits gained from implementing accurate production scheduling. Compare the cost of implementing new systems or software with the realized cost savings.
- Long-Term Cost Savings: Consider the long-term effects of accurate production scheduling on cost savings. Some benefits may take time to fully materialize, and ongoing monitoring is necessary to capture the cumulative impact.
By conducting a comprehensive cost-savings analysis, companies can quantify the financial benefits of accurate production scheduling and identify areas where further improvements can be made.
This analysis provides valuable insights into the efficiency and effectiveness of production scheduling practices and helps in making data-driven decisions to optimize production processes and enhance overall profitability.
Inventory Management
Inventory Management focuses on assessing the impact of accurate production scheduling on inventory levels and optimizing inventory management practices. Inventory management plays a crucial role in controlling costs and ensuring a smooth production process.
Analyzing the effects of accurate production scheduling on inventory can reveal opportunities for reducing carrying costs and improving overall operational efficiency.
Here's a more detailed explanation of inventory management analysis:
- Inventory Levels Before Implementation: Gather historical data on inventory levels before implementing accurate production scheduling. This data provides a baseline for comparison and helps understand the company's previous inventory management practices.
- Inventory Turnover Ratio: Calculate the inventory turnover ratio, which is the number of times inventory is sold and replenished within a specific period. A higher turnover ratio indicates more efficient inventory management.
- Carrying Costs: Assess the carrying costs associated with inventory, including storage, insurance, obsolescence, and handling expenses. Identify the financial impact of carrying excess inventory.
- Stockouts and Backorders: Analyze the occurrence of stockouts (when inventory is depleted) and backorders (when customers order out-of-stock items). These incidents may be indicators of inadequate or inaccurate production scheduling.
- Impact of Accurate Production Scheduling: After implementing accurate production scheduling, track changes in inventory levels, turnover ratio, and stockouts or backorders. Determine if there are improvements in these inventory management metrics.
- Optimal Inventory Levels: Assess whether accurate production scheduling has helped maintain optimal inventory levels. Balancing inventory levels to meet customer demand while avoiding excessive stock can lead to cost savings.
- Just-In-Time (JIT) Principles: Evaluate the application of JIT principles in inventory management, where production is aligned with customer demand. JIT can help minimize excess inventory and carrying costs.
- Inventory Carrying Cost Reduction: Calculate the reduction in inventory carrying costs resulting from more efficient production scheduling and improved inventory management practices.
- Safety Stock Analysis: Analyze safety stock levels to ensure buffer inventory is appropriately managed. Accurate production scheduling should consider lead times and demand variability to optimize safety stock levels.
- Supply Chain Coordination: Consider how accurate production scheduling impacts coordination with suppliers to ensure timely deliveries of raw materials, minimizing inventory stockouts.
- Slow-Moving or Obsolete Inventory: Evaluate if accurate production scheduling helps reduce the occurrence of slow-moving or obsolete inventory, which can lead to significant losses.
- Inventory Forecast Accuracy: Assess the accuracy of inventory forecasting after implementing accurate production scheduling. Improved forecasting can lead to better inventory management and cost savings.
- Cost of Expedited Shipments: Determine if accurate production scheduling has reduced the need for expedited shipments to manage inventory shortages, resulting in cost savings.
- Customer Order Fulfillment: Analyze the impact of accurate production scheduling on order fulfillment rates. Improvements in production scheduling can lead to better customer satisfaction and reduced lead times.
By analyzing inventory management metrics before and after implementing accurate production scheduling, companies can identify areas for improvement, optimize inventory levels, and reduce carrying costs.
Improved inventory management leads to better resource utilization, reduced waste, and increased overall operational efficiency. These benefits contribute to higher profit margins and a more competitive position in the market.
On-Time Delivery Performance
On-Time Delivery Performance focuses on evaluating the impact of accurate production scheduling on the company's ability to deliver products to customers on or before the promised delivery dates.
On-time delivery is a critical aspect of customer satisfaction and plays a significant role in maintaining strong customer relationships. Analyzing on-time delivery performance provides insights into the efficiency of production scheduling and its impact on customer service.
Here's a more detailed explanation of this analysis:
- On-Time Delivery Metrics: Define the metrics that will be used to measure on-time delivery performance. Common metrics include the percentage of orders delivered on time, average delivery lead time, and the number of late deliveries.
- Baseline On-Time Delivery Data: Gather historical data on on-time delivery rates before implementing accurate production scheduling. This baseline data serves as a reference point for comparison.
- Post-Implementation On-Time Delivery Data: After implementing accurate production scheduling, collect data on on-time delivery rates during the same time period. Ensure that data collection methods and categorization are consistent with the baseline data.
- Comparison of On-Time Delivery Rates: Compare the on-time delivery rates before and after implementing accurate production scheduling. Calculate the percentage change in on-time delivery to determine improvements.
- Customer Satisfaction: Correlate changes in on-time delivery performance with customer satisfaction metrics. High on-time delivery rates often lead to increased customer satisfaction and loyalty.
- Root Cause Analysis: If there were any improvements in on-time delivery, conduct a root cause analysis to identify the factors contributing to the positive change. These factors may include better production scheduling, reduced lead times, or improved resource utilization.
- Impact on Customer Retention: Assess whether improved on-time delivery performance has positively affected customer retention rates. Satisfied customers are more likely to become repeat customers and refer others to the company.
- Cost of Expedited Deliveries: Analyze the cost of expedited deliveries or rush orders made to meet customer demands due to poor scheduling. Accurate production scheduling should reduce the need for expensive expedited shipments.
- Impact on Sales: Consider the impact of improved on-time delivery on sales performance. Timely deliveries can lead to increased sales and revenue, as customers are more likely to place repeat orders.
- Customer Feedback: Gather feedback from customers regarding their perception of the company's on-time delivery performance. Customer feedback can highlight specific areas for improvement.
- Benchmarking: Compare the company's on-time delivery performance with industry benchmarks or competitors' performance. This provides context and helps identify opportunities for further improvement.
- Supply Chain Coordination: Assess how accurate production scheduling impacts supply chain coordination with suppliers and logistics partners. Effective coordination ensures timely availability of raw materials and timely deliveries to customers.
- Order Processing Efficiency: Analyze the impact of accurate production scheduling on order processing efficiency. A more streamlined production process can lead to faster order processing and shorter lead times.
By analyzing on-time delivery performance, companies can gauge the effectiveness of their production scheduling strategies and their ability to meet customer expectations.
Improvements in on-time delivery rates positively influence customer satisfaction, loyalty, and overall business performance.
Additionally, it helps identify areas for further optimization and ensures that the company remains competitive in the market.
Customer Satisfaction
Customer Satisfaction focuses on evaluating the impact of accurate production scheduling on customer satisfaction levels.
Customer satisfaction is a critical factor in business success, as satisfied customers are more likely to become repeat customers, provide positive referrals, and contribute to the company's long-term profitability.
Analyzing customer satisfaction in relation to accurate production scheduling provides valuable insights into how efficient production processes can positively influence customer experiences.
Here's a more detailed explanation of this analysis:
- Customer Feedback: Gather feedback from customers through surveys, interviews, or other means to gauge their satisfaction with product availability, delivery times, and overall service levels. Customer feedback is a direct measure of how well the company meets customer expectations.
- Customer Satisfaction Scores: Use customer satisfaction scores and ratings to quantify the level of satisfaction. These scores can be collected through post-purchase surveys or other feedback mechanisms.
- Comparison with Baseline Data: Compare customer satisfaction scores or feedback data before and after implementing accurate production scheduling. This comparison helps assess the impact of the changes on customer satisfaction.
- On-Time Delivery: Analyze the relationship between on-time delivery performance and customer satisfaction. Timely deliveries often contribute to higher customer satisfaction.
- Order Accuracy: Assess the accuracy of orders fulfilled after implementing accurate production scheduling. Fewer errors in order processing can positively impact customer satisfaction.
- Communication and Transparency: Evaluate whether accurate production scheduling has improved communication and transparency with customers regarding order status, lead times, and potential delays.
- Impact on Customer Retention: Measure the impact of improved customer satisfaction on customer retention rates. Satisfied customers are more likely to remain loyal to the company.
- Customer Complaints: Analyze the frequency and nature of customer complaints related to production delays, product availability, or order fulfillment. Fewer complaints may indicate improved satisfaction.
- Repeat Business: Assess whether improved customer satisfaction has led to an increase in repeat business. Satisfied customers are more likely to make repeat purchases.
- Referral Rate: Analyze the rate at which satisfied customers refer others to the company. Positive referrals can contribute to the company's growth and acquisition of new customers.
- Benchmarking: Compare the company's customer satisfaction levels with industry benchmarks or competitors' performance. Benchmarking provides insights into the company's relative position in the market.
- Employee Engagement: Assess the relationship between employee engagement and customer satisfaction. Engaged and motivated employees are more likely to deliver better customer service.
- Continuous Improvement: Use customer feedback and satisfaction data to identify areas for continuous improvement. Implement changes based on customer feedback to enhance satisfaction levels further.
By analyzing customer satisfaction data in the context of accurate production scheduling, companies can better understand the impact of production efficiency on customer experiences.
Satisfied customers contribute to a positive brand reputation, increased customer loyalty, and ultimately higher profit margins through repeat business and positive word-of-mouth referrals.
Ensuring a customer-centric approach to production scheduling can lead to sustainable business growth and a competitive advantage in the market.
Time Savings
Time Savings focuses on assessing the amount of time saved in the production process as a result of accurate production scheduling.
Time savings are a crucial benefit of efficient production scheduling, as they directly impact productivity, resource utilization, and overall operational efficiency.
Analyzing time savings provides insights into the effectiveness of production scheduling changes and their contribution to improved business performance.
Here's a more detailed explanation of this analysis:
- Time Tracking: Implement a system to track the time spent on different production tasks and processes before and after accurate production scheduling is implemented. This data will be used to quantify time savings.
- Baseline Time Data: Gather historical data on production times and timelines before implementing accurate production scheduling. This baseline data serves as a reference point for comparison.
- Post-Implementation Time Data: After implementing accurate production scheduling, collect data on production times during the same time period. Ensure that data collection methods and categorization are consistent with the baseline data.
- Comparison of Time Data: Compare the production times before and after implementing accurate production scheduling. Calculate the percentage change in time for each production task or process to determine the time savings.
- Reduction in Setup Times: Assess whether accurate production scheduling has led to reduced setup times for production runs. Optimized scheduling can streamline setup processes and reduce downtime.
- Minimization of Idle Time: Analyze the impact of accurate production scheduling on minimizing idle time between production tasks or runs. Reduced idle time leads to increased resource utilization and productivity.
- Impact on Lead Times: Evaluate the effect of accurate production scheduling on lead times for order fulfillment. Shorter lead times indicate more efficient production processes.
- Resource Utilization Efficiency: Measure the efficiency of resource utilization after implementing accurate production scheduling. Optimized scheduling should ensure that resources such as labor, equipment, and materials are used effectively.
- Impact on Production Cycle Time: Calculate the reduction in production cycle time resulting from accurate production scheduling. A shorter production cycle time indicates improved efficiency.
- Real-Time Monitoring: If real-time monitoring tools or software are used for production scheduling, use the data from these systems to track and quantify time savings.
- Impact on Employee Productivity: Assess the impact of accurate production scheduling on employee productivity. A more efficient production process can lead to increased productivity and output per employee.
- Cost Savings Analysis: Analyze the cost savings resulting from time savings. Reduced production time can lead to lower labor costs, lower overhead costs, and increase overall operational efficiency.
- Continuous Improvement: Identify areas for further optimization and continuous improvement in production scheduling to achieve additional time savings.
By analyzing time savings resulting from accurate production scheduling, companies can measure the efficiency and effectiveness of the production process.
Time savings contribute to improved resource utilization, reduced downtime, and increased productivity, leading to better profitability and competitiveness in the market.
The data obtained from this analysis can be used to make data-driven decisions and further enhance production scheduling strategies to achieve even greater time savings.
Return on Investment (ROI) Analysis
Return on Investment (ROI) Analysis, focuses on quantifying the financial benefits gained from implementing accurate production scheduling. ROI analysis assesses the profitability and cost-effectiveness of the changes made to production scheduling by comparing the financial gains with the investment made to implement those changes.
Here's a more detailed explanation of conducting an ROI analysis:
- Investment Cost: Determine the total investment cost incurred to implement accurate production scheduling. This may include costs associated with purchasing and implementing new software, training employees, hiring consultants, and any other expenses related to the implementation.
- Financial Benefits: Identify the financial benefits resulting from accurate production scheduling. These benefits can include cost savings, increased sales, reduced downtime, improved resource utilization, and other efficiency gains.
- Cost Savings: Calculate the cost savings achieved through accurate production scheduling. This involves analyzing the reduction in production costs, inventory carrying costs, overtime expenses, and other operational cost savings.
- Revenue Increase: Evaluate any revenue increase resulting from improved on-time delivery, increased customer satisfaction, and the potential for higher repeat business.
- Quantify Time Savings: Quantify the time savings achieved through optimized production scheduling. Calculate the reduction in production cycle time and the associated labor cost savings.
- Tangible and Intangible Benefits: Consider both tangible and intangible benefits in the ROI analysis. Tangible benefits are quantifiable and directly impact the bottom line (e.g., cost savings), while intangible benefits may not have a direct monetary value but still contribute to the company's overall success (e.g., improved customer satisfaction).
- Timeframe: Determine the timeframe over which the ROI analysis will be conducted. Depending on the nature of the investment, the timeframe may vary (e.g., short-term, medium-term, or long-term ROI analysis).
- ROI Calculation: To calculate ROI, use the following formula: ROI = (Net Financial Benefits / Investment Cost) x 100
- Net Financial Benefits = Total financial benefits - Investment Cost
- Consideration of Risks: Assess any potential risks associated with implementing accurate production scheduling. Evaluate the likelihood of risks occurring and their potential impact on the ROI.
- Sensitivity Analysis: Perform sensitivity analysis to understand how changes in key assumptions, such as cost savings or revenue increases, may affect the ROI.
- Benchmarking: Compare the ROI with industry benchmarks or the expected ROI for similar investments. This provides context and helps gauge the success of the implementation.
- Communication of Findings: Present the findings of the ROI analysis to stakeholders, such as management and investors, to gain support and alignment for future investments.
- Continuous Improvement: Use the ROI analysis as a basis for continuous improvement. Based on the results, identify areas for further optimization and fine-tuning of production scheduling strategies.
By conducting an ROI analysis, companies can objectively assess the financial impact of accurate production scheduling and determine if the investment in implementing these changes is justified.
Positive ROI indicates that the changes have been cost-effective and have contributed to increased profitability and overall business success. The analysis also helps in making informed decisions for future investments in production scheduling and other operational improvements.
Employee Productivity
Employee Productivity focuses on evaluating the impact of accurate production scheduling on employee productivity. Employee productivity is a critical factor in achieving operational efficiency and meeting production targets.
Analyzing employee productivity in the context of production scheduling changes provides insights into how the new scheduling practices have affected workforce performance.
Here's a more detailed explanation of this analysis:
- Define Employee Productivity Metrics: Identify key metrics to measure employee productivity, such as output per employee, units produced per hour, or production output compared to standard time.
- Baseline Productivity Data: Gather historical data on employee productivity before implementing accurate production scheduling. This baseline data serves as a reference point for comparison.
- Post-Implementation Productivity Data: After implementing accurate production scheduling, collect data on employee productivity during the same time period. Ensure that data collection methods and categorization are consistent with the baseline data.
- Comparison of Productivity Data: Compare employee productivity levels before and after implementing accurate production scheduling. Calculate the percentage change in productivity to determine improvements.
- Resource Utilization: Assess how accurate production scheduling has impacted resource utilization, including labor. Determine if resource allocation has improved and if there is less idle time or downtime.
- Training and Skill Development: Consider the impact of any training or skill development initiatives introduced alongside production scheduling changes. Skilled and trained employees are more likely to be productive.
- Employee Feedback: Gather feedback from employees regarding the impact of production scheduling changes on their work. Employee insights can provide valuable qualitative data to complement the quantitative analysis.
- Employee Engagement: Analyze the relationship between production scheduling changes and employee engagement. Engaged employees are generally more productive and motivated.
- Reduction in Overtime: Assess whether accurate production scheduling has reduced the need for overtime work. A reduction in overtime hours can indicate improved production efficiency.
- Employee Satisfaction: Evaluate the impact of production scheduling changes on employee satisfaction. Satisfied employees are more likely to be productive and committed to their work.
- Cross-Training: Consider the impact of cross-training employees to handle multiple tasks and roles. Cross-training can enhance workforce flexibility and overall productivity.
- Safety and Ergonomics: Assess whether production scheduling changes have had any impact on workplace safety and ergonomics. A safer work environment can lead to higher productivity and reduced absenteeism.
- Continuous Improvement: Use the analysis to identify areas for further optimization and continuous improvement in employee productivity and production scheduling.
By analyzing employee productivity in the context of production scheduling changes, companies can understand how scheduling improvements impact workforce efficiency. Productive employees contribute to higher production output, reduced costs, and improved overall business performance.
The insights gained from this analysis can help in making data-driven decisions to further optimize production scheduling strategies and enhance workforce productivity.
Additionally, it ensures that the company maintains a motivated and engaged workforce, leading to a competitive advantage in the market.
Long-Term Impact
Long-Term Impact focuses on assessing the lasting effects of accurate production scheduling over an extended period. Analyzing the long-term impact helps companies understand how production scheduling changes influence various aspects of the business beyond the initial implementation phase. It provides insights into the sustainability of the improvements and the continuous benefits gained over time.
Here's a more detailed explanation of considering the long-term impact:
- Long-Term Data Collection: Collect data over an extended period, typically beyond the immediate post-implementation phase. Long-term data provides a more comprehensive view of the effects of accurate production scheduling.
- Tracking Performance Trends: Analyze trends in key performance indicators (KPIs), such as profit margins, on-time delivery rates, customer satisfaction scores, and employee productivity, over the long term. Identify patterns and changes in performance.
- Stability of Improvements: Evaluate the stability of improvements achieved through accurate production scheduling. Determine if the benefits have been sustained over time or if there have been fluctuations.
- Customer Loyalty: Assess the impact of improved on-time delivery and customer satisfaction on customer loyalty over the long term. Loyal customers contribute to sustainable revenue growth.
- Employee Retention and Engagement: Measure employee retention rates and engagement levels over time. Determine if a positive work environment resulting from improved production scheduling leads to long-term employee satisfaction.
- Supplier Relationships: Evaluate how accurate production scheduling has influenced supplier relationships. Strong, long-term relationships with suppliers can lead to more reliable and timely deliveries of raw materials.
- Market Reputation: Consider how accurate production scheduling has contributed to the company's reputation in the market. A positive reputation can attract new customers and business opportunities.
- Adaptability to Market Changes: Analyze how accurate production scheduling has helped the company adapt to changes in customer demand, market trends, and industry dynamics over time.
- Continuous Improvement Initiatives: Assess the company's efforts to continuously improve production scheduling strategies over the long term. Evaluate how feedback and data are used to drive ongoing optimization.
- Return on Investment (ROI) Sustainment: Determine if the initial ROI achieved from implementing accurate production scheduling has been maintained or improved over time.
- Industry Comparisons: Benchmark the company's long-term performance against industry competitors. Understanding how the company's production scheduling practices compare to industry best practices is crucial for sustained success.
- Organizational Learning: Consider how lessons learned from the initial implementation have been integrated into the organization's culture and processes to support continuous improvement.
By evaluating the long-term impact of accurate production scheduling, companies can ensure that the improvements are sustainable and continue to contribute to the company's success over time.
This analysis helps in making strategic decisions, setting long-term goals, and allocating resources to maintain and enhance the positive effects of production scheduling changes.
It also reinforces the importance of continuous improvement and adaptability in a dynamic business environment, positioning the company for long-term competitiveness and growth.
How Can Deskera Help You with Production Scheduling?
Deskera MRP is an integrated software solution designed to help businesses manage their manufacturing processes, including production scheduling.
Here's how Deskera MRP can assist you with production scheduling:
- Resource Planning: Deskera MRP enables you to efficiently plan and allocate resources for your production schedule. You can define the availability and capacity of your resources, such as labor, machinery, and equipment, and schedule tasks accordingly. This helps in optimizing resource utilization and balancing workloads.
- Production Order Management: With Deskera MRP, you can easily create and manage production orders. You can define the bill of materials (BOM) and set up routing for each order, specifying the sequence of operations and dependencies. This allows you to schedule and track the progress of production orders, ensuring timely execution.
- Real-Time Visibility: Deskera MRP provides real-time visibility into your production schedule. You can monitor the status of production orders, track work in progress (WIP), and identify bottlenecks or potential delays. This visibility enables you to make informed decisions and take proactive actions to optimize your production scheduling.
- Capacity Planning: Deskera MRP helps you plan and manage production capacity effectively. You can evaluate resource availability, track utilization rates, and forecast capacity requirements based on production demand. This enables you to align your capacity with the production schedule and avoid overloading resources or creating bottlenecks.
- Demand Planning and Forecasting: Deskera MRP incorporates demand planning and forecasting capabilities. By analyzing historical data and market trends, you can accurately forecast future demand. This information can be used to adjust production schedules, allocate resources, and ensure that you meet customer requirements on time.
- Collaboration and Communication: Deskera MRP facilitates collaboration and communication among stakeholders involved in production scheduling. You can share real-time updates, task assignments, and production-related information with your team members, suppliers, and other relevant parties. This streamlines communication reduces errors, and enhances coordination.
- Reporting and Analytics: Deskera MRP provides robust reporting and analytics features. You can generate various reports related to production scheduling, such as resource utilization, lead times, production efficiency, and capacity analysis. These insights help in monitoring performance, identifying areas for improvement, and making data-driven decisions.
Key Takeaways
Accurate production scheduling stands as a fundamental pillar in the quest for improved profit margins and long-term business success. The key ways in which accurate production scheduling can affect profit margins are:
- Reduced Production Costs: Accurate scheduling helps in better planning and allocation of resources, such as labor, materials, and machinery. This leads to reduced wastage, minimized setup times, and improved overall efficiency, all of which contribute to lower production costs.
- Minimized Inventory Costs: By scheduling production accurately, companies can avoid overproduction and excessive inventory holding costs. Having the right amount of inventory at the right time ensures that capital is not tied up unnecessarily in stockpiles, reducing carrying costs and potential obsolescence.
- Improved Equipment Utilization: Accurate scheduling helps in maximizing the utilization of machinery and equipment. Minimizing downtime and idle time for machines means more products can be manufactured in a given timeframe, increasing overall output without incurring additional capital expenses.
- Better Customer Satisfaction: Timely and accurate production scheduling leads to on-time deliveries, which enhances customer satisfaction. Satisfied customers are more likely to place repeat orders and recommend the company to others, resulting in increased sales and long-term profitability.
- Enhanced Planning and Decision Making: Accurate production scheduling provides management with a clear picture of production timelines and resource requirements. This helps in making informed decisions regarding expansion, investment in new equipment, or hiring additional staff, ensuring that resources are utilized optimally to maximize profits.
- Reduced Overtime and Rush Orders: When production is scheduled accurately, the need for last-minute overtime and rush orders decreases. These rush expenses can be costly and can eat into profit margins, so avoiding them through better planning is financially advantageous.
- Lower Penalty Costs: For companies operating under contracts or agreements with penalties for late deliveries, accurate production scheduling can help avoid or reduce penalty costs, further contributing to improved profit margins.
- Increased Flexibility and Adaptability: Accurate production scheduling allows companies to respond more effectively to changing market demands and unforeseen disruptions. It enables them to adjust production plans quickly, optimize resources, and minimize losses during turbulent times.
- Competitive Advantage: Having an efficient production scheduling process can provide a competitive edge in the market. Companies that can consistently deliver products on time and at lower costs are more likely to attract and retain customers, outperform competitors, and secure a larger market share.
- Improved Cash Flow: Better production scheduling leads to smoother production cycles and more predictable cash flow. This predictability allows for more effective financial planning, reducing the risk of cash flow shortages that could hinder operations or require costly external financing.
In conclusion, accurate production scheduling is a critical factor in improving profit margins for manufacturing companies. By reducing production costs, inventory costs, and downtime while enhancing customer satisfaction and overall efficiency, businesses can achieve sustainable growth and higher profitability.
The crucial steps to measure the impact of accurate production scheduling on profit margins are:
- Data Collection: Gather relevant data related to production scheduling, financial performance, and operational efficiency. This data may include production schedules, sales data, revenue, cost of goods sold (COGS), operating expenses, inventory levels, and customer satisfaction metrics.
- Establish Baseline Metrics: Before implementing accurate production scheduling practices, establish baseline metrics for profit margins and other relevant performance indicators. This will serve as a reference point for comparison after the changes are implemented.
- Identify Key Performance Indicators (KPIs): Determine the KPIs that will be used to measure the impact of accurate production scheduling on profit margins. Key KPIs may include gross profit margin, operating profit margin, net profit margin, inventory turnover ratio, on-time delivery rate, and customer satisfaction scores.
- Analyze Profit Margins: Compare profit margins before and after the implementation of accurate production scheduling. Calculate the percentage change in each profit margin metric to understand the impact.
- Cost Savings Analysis: Assess the impact of accurate production scheduling on production costs, such as labor, materials, and overhead expenses. Identify cost savings resulting from improved resource utilization, reduced downtime, and more efficient workflows.
- Inventory Management: Analyze the effect of accurate production scheduling on inventory levels and carrying costs. Measure the reduction in excess inventory and associated holding costs.
- On-Time Delivery Performance: Measure the improvement in on-time delivery performance after implementing accurate production scheduling. On-time deliveries can lead to better customer satisfaction and repeat business.
- Customer Satisfaction: Collect feedback from customers to gauge their satisfaction with product availability, delivery times, and overall service levels. Improved customer satisfaction may lead to higher customer retention and increased sales.
- Time Savings: Quantify the time saved in production due to better planning and scheduling. Reduced setup times and minimized idle time contribute to increased productivity and cost savings.
- Return on Investment (ROI) Analysis: Calculate the return on investment resulting from the implementation of accurate production scheduling. Compare the cost of implementing new systems or software with the financial benefits gained from increased profit margins.
- Employee Productivity: Assess the impact of accurate production scheduling on employee productivity. Engage with employees to gather feedback on how the new scheduling practices have affected their work and efficiency.
- Long-Term Impact: Consider the long-term effects of accurate production scheduling on profit margins. Some benefits may take time to materialize fully, such as improved supplier relationships, reduced lead times, and enhanced market reputation.
By conducting a thorough analysis of these metrics and comparing the data before and after implementing accurate production scheduling practices, you can quantitatively measure the impact on profit margins and overall financial performance.
This evaluation will provide insights into the effectiveness of the new scheduling strategies and help in making informed decisions to further enhance profitability and competitiveness.
Overall, Deskera MRP serves as a comprehensive solution for managing production scheduling. It helps streamline your manufacturing processes, optimize resource utilization, improve visibility, and enhance overall efficiency. By leveraging its features, you can effectively plan and execute your production schedule while minimizing bottlenecks and ensuring timely order fulfillment.
Related Articles
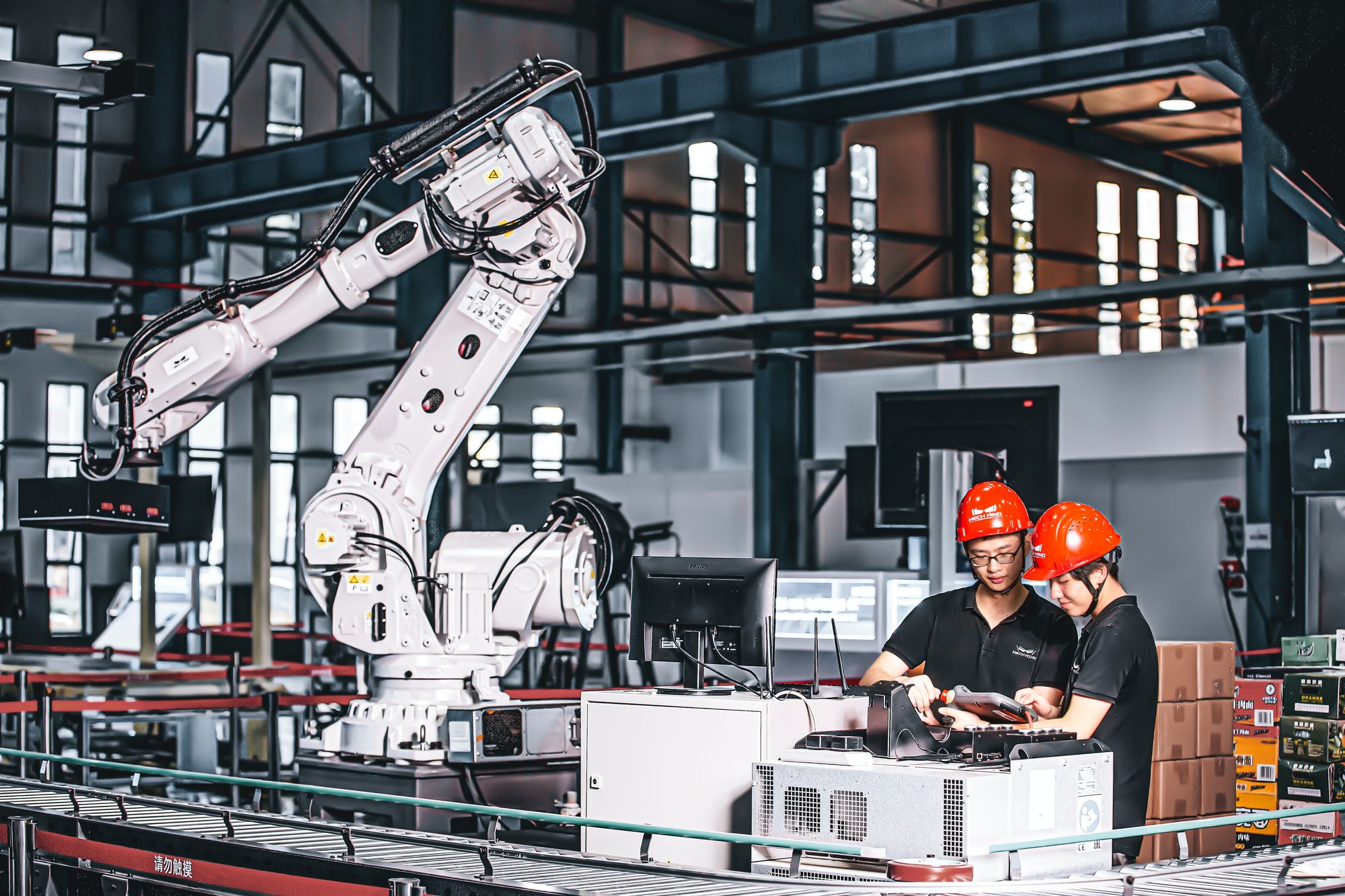
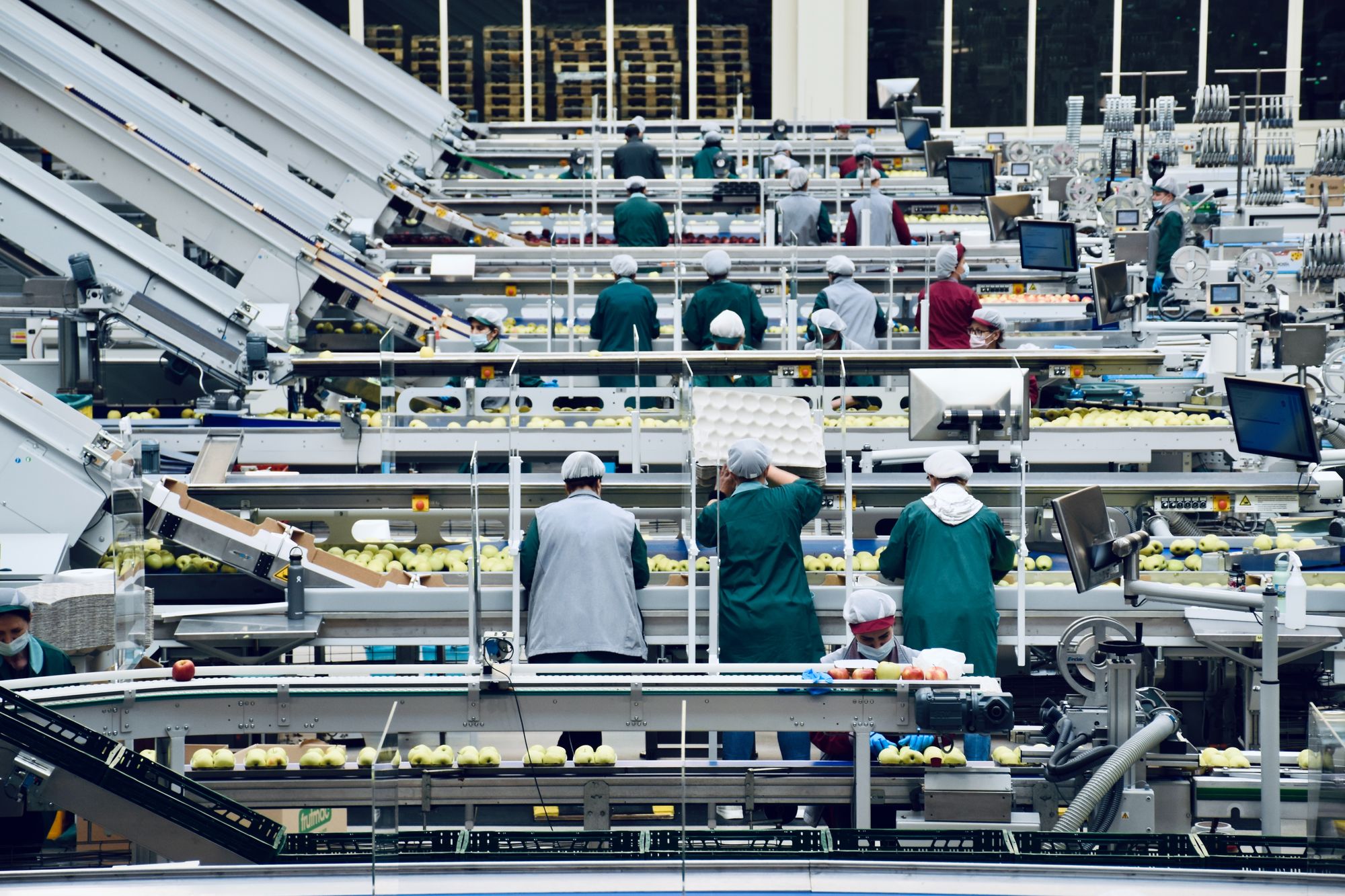
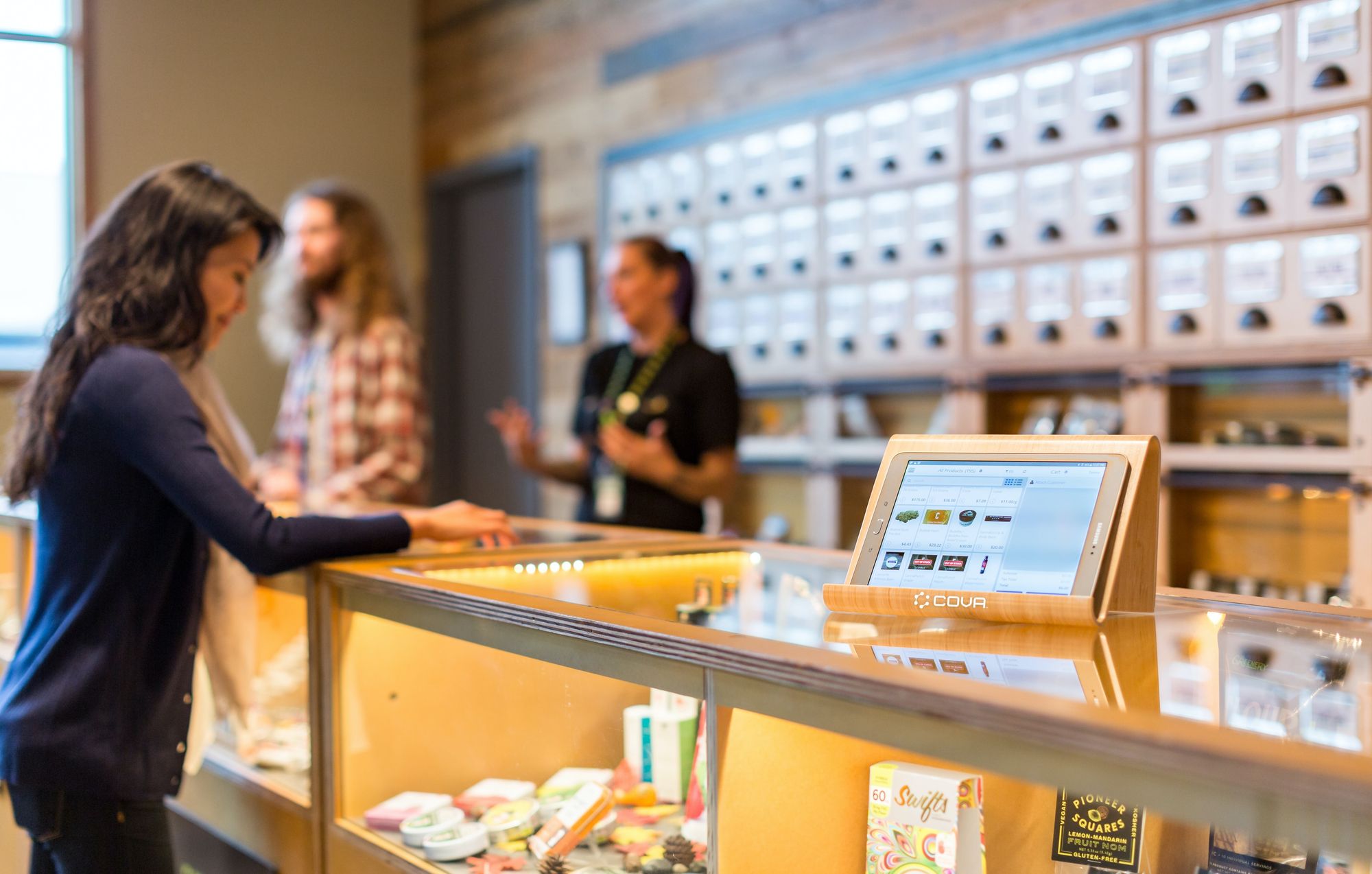
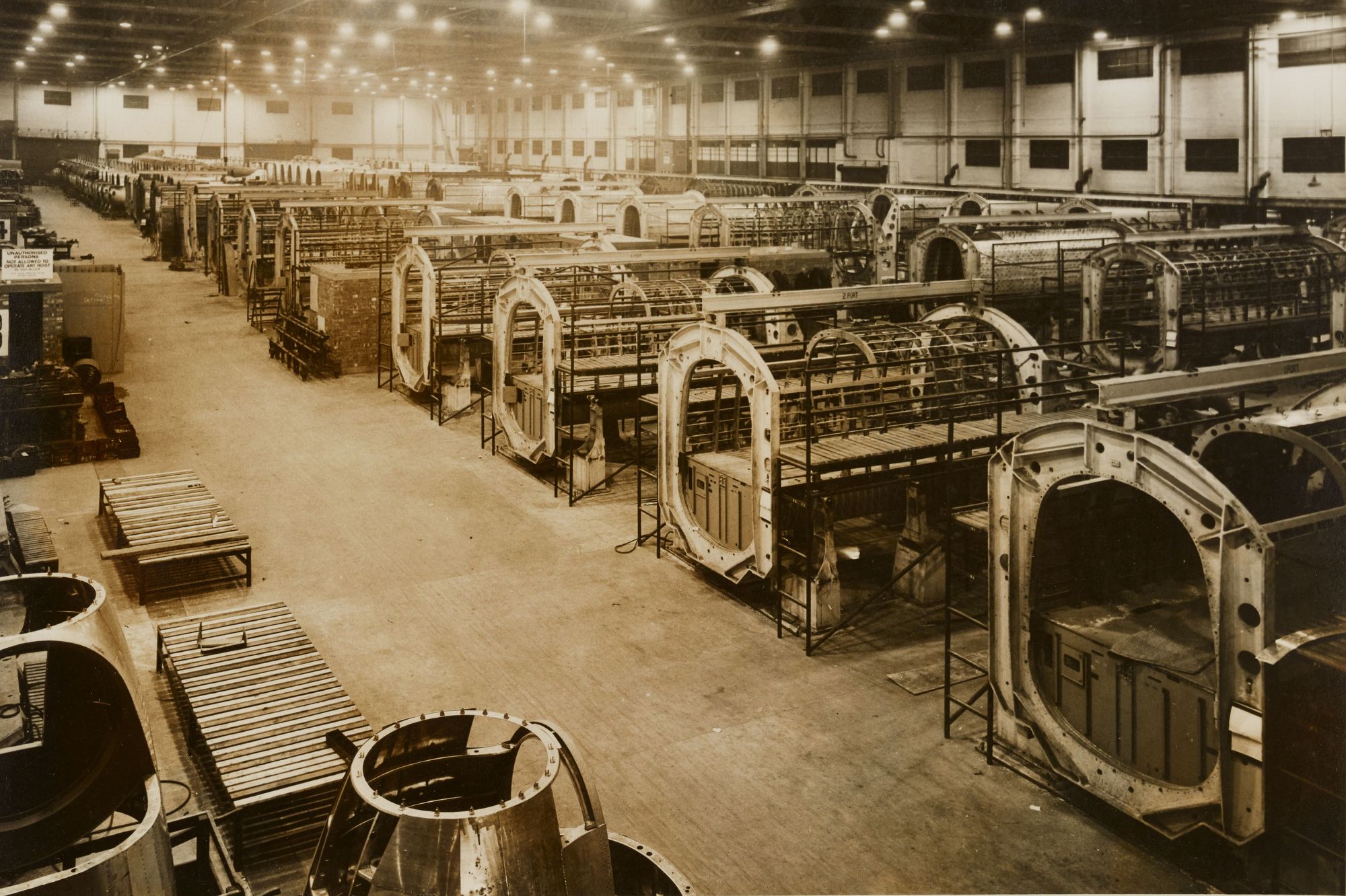
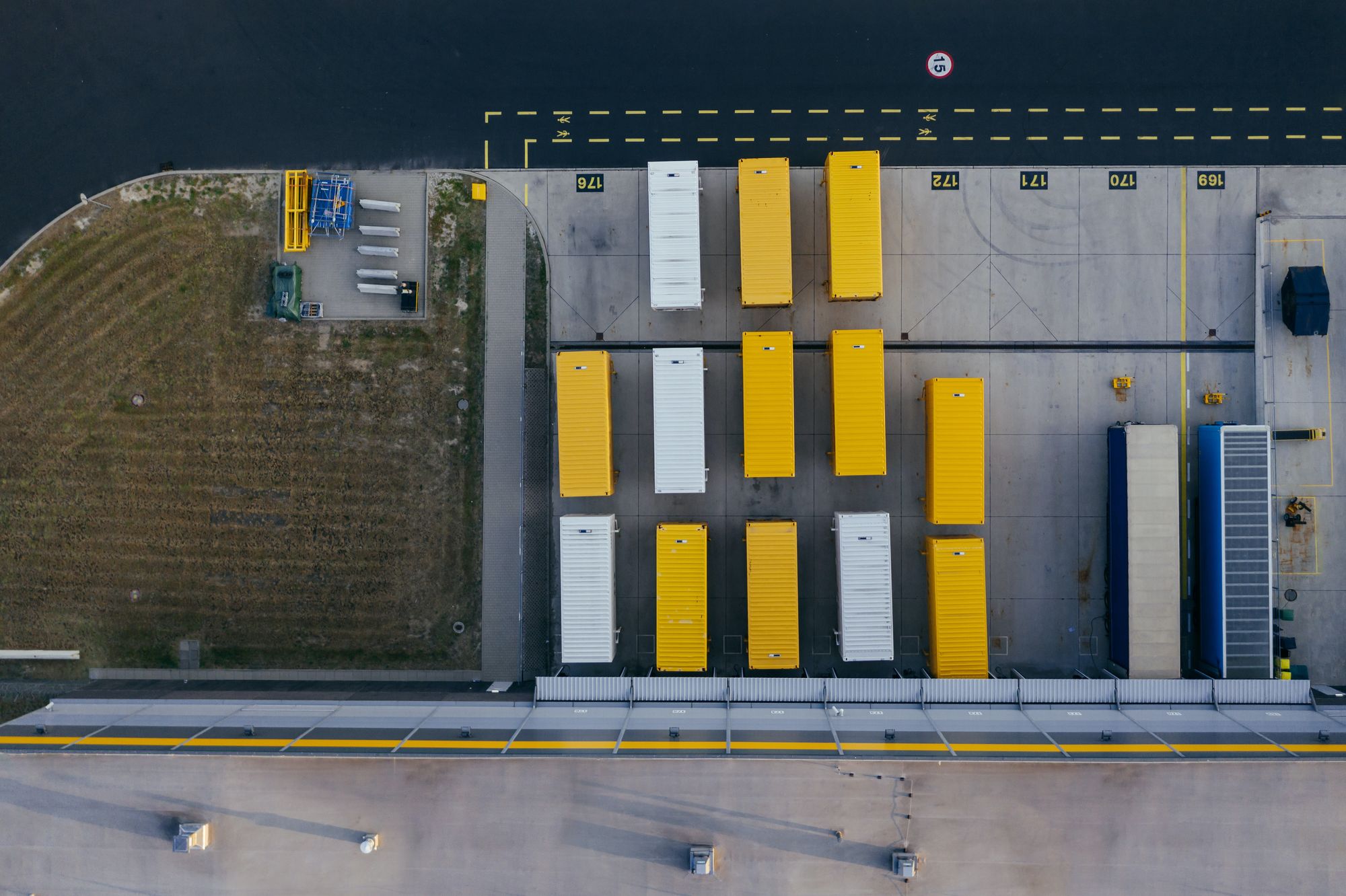
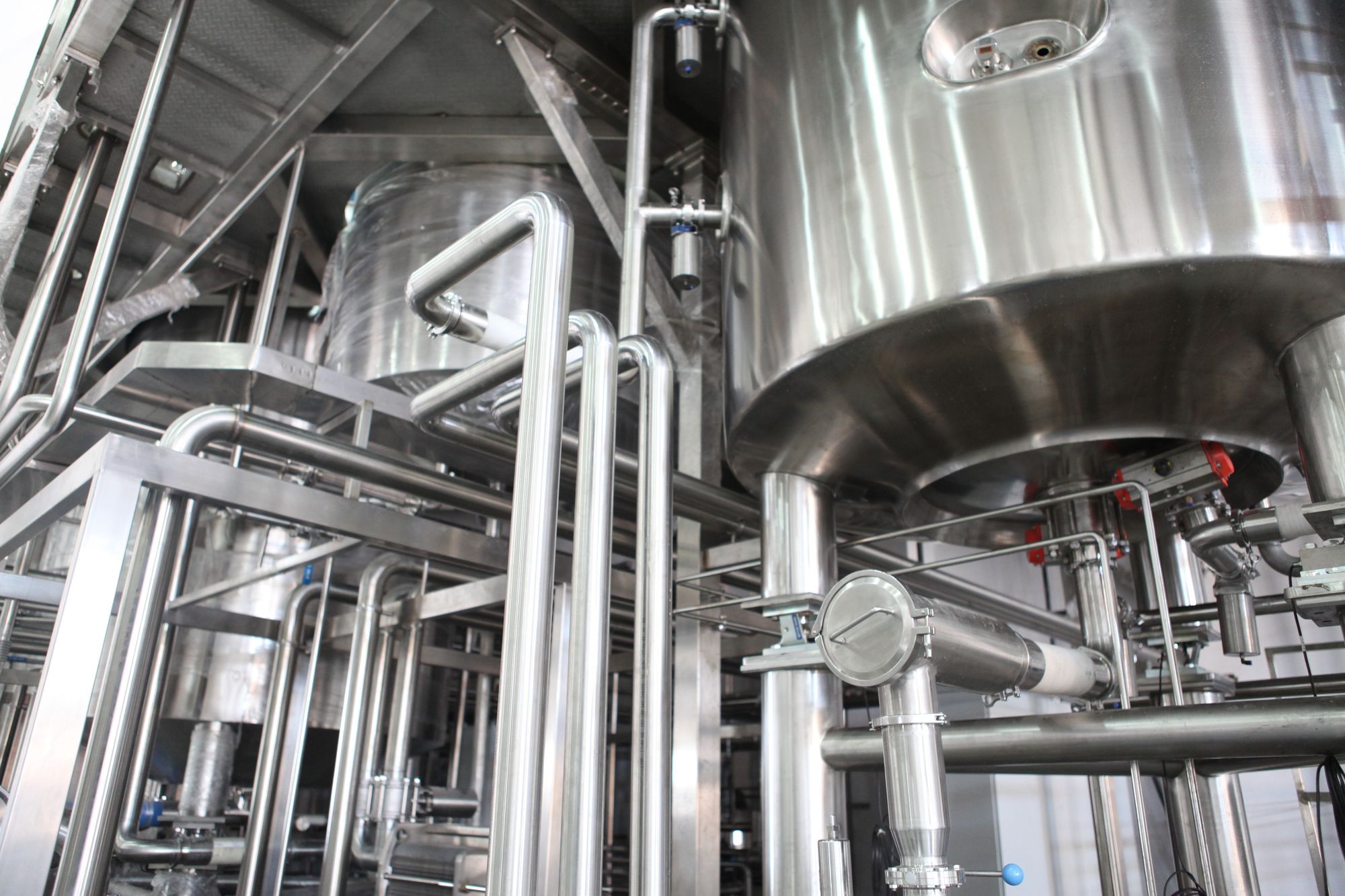