The global digital manufacturing software market, valued at $6.9 billion in 2022, is projected to skyrocket to $33.7 billion by 2032, with a remarkable compound annual growth rate (CAGR) of 17.4% from 2023 to 2032 (Source: Allied Market Research). This surge underscores the critical role manufacturing software plays in the industry, particularly for small businesses aiming to enhance their operational efficiency and competitiveness.
For small businesses, manufacturing software is more than just a tool—it's a lifeline. These solutions help streamline production processes, manage inventory, and optimize resources, but small businesses often face challenges such as limited budgets, lack of technical expertise, and integration issues with existing systems. Navigating these challenges requires a clear understanding of what manufacturing software can offer and how to select the right solution.
This article aims to guide small businesses through the process of choosing the best manufacturing software. We will explore the essential features to look for, review top software options, and provide practical advice to help you make an informed decision.
Among the notable solutions available, Deskera ERP stands out with its comprehensive suite of tools designed specifically for small businesses. Deskera ERP offers robust features for inventory management, production planning, and financial tracking, all integrated into a user-friendly platform that helps streamline operations and drive growth.
What is Manufacturing Software?
Manufacturing software for small businesses encompasses a range of digital tools designed to streamline and optimize production processes. The primary purpose of this software is to enhance operational efficiency by automating routine tasks, improving accuracy, and providing real-time insights into various aspects of manufacturing.
Whether it's managing inventory, scheduling production runs, or handling financials, manufacturing software integrates these functions into a cohesive system, ultimately helping businesses save time and reduce costs.
Types of Manufacturing Software
There are several key types of manufacturing software tailored to different aspects of the production process:
- ERP Software for Small Manufacturing Business: Enterprise Resource Planning (ERP) software integrates various business functions, including manufacturing, finance, and human resources, into a single unified system. This type of software provides a comprehensive view of business operations, facilitating better decision-making and coordination across departments.
- MRP Software: Material Requirements Planning (MRP) software focuses on managing inventory levels, production schedules, and material procurement. It helps ensure that the right materials are available at the right time, minimizing production delays and reducing excess inventory.
- MES Software: Manufacturing Execution Systems (MES) are designed to manage and monitor work in progress on the shop floor. MES software provides real-time data on production processes, helping to optimize workflows and maintain product quality.
- Manufacturing Scheduling Software for Small Business: This software specifically addresses the scheduling needs of small businesses, allowing them to plan and coordinate production runs efficiently. It helps in balancing production schedules with resource availability, leading to improved productivity.
- Accounting Software for Manufacturing Small Business: This type of software integrates financial management with manufacturing operations. It tracks expenses, manages budgets, and generates financial reports, providing valuable insights into the cost of production and overall financial health.
How Manufacturing Software Benefits Small Businesses
The best manufacturing software for small businesses offers several advantages:
- Enhanced Efficiency: By automating routine tasks and integrating various functions, manufacturing software reduces manual work and minimizes errors. This leads to faster production cycles and more efficient operations.
- Streamlined Operations: Manufacturing software automates and integrates various business processes, from inventory management to production scheduling and financial reporting. This streamlining reduces manual tasks, minimizes errors, and ensures that all departments are aligned, leading to more efficient operations.
- Improved Inventory Management: Manufacturing inventory software helps small businesses maintain optimal inventory levels, reducing the risk of stockouts or overstocking. It provides real-time visibility into inventory status, facilitating better inventory control and planning.
- Better Production Planning: Manufacturing scheduling software enables businesses to plan production runs more effectively. It helps in aligning production schedules with demand, ensuring that resources are utilized efficiently and deadlines are met.
- Integrated Financial Management: ERP solutions for manufacturing that include accounting features allow businesses to track production costs, manage budgets, and generate financial reports. This integration provides a clear picture of financial performance and helps in making informed decisions.
- Scalability: As businesses grow, manufacturing software can scale to accommodate increased production volumes and complexity. ERP for manufacturing systems, in particular, offer scalability and flexibility to support business expansion.
- Data-Driven Decision Making: Manufacturing software offers robust reporting and analytics capabilities, enabling businesses to generate detailed reports and gain insights into various aspects of their operations. Data-driven decision-making helps identify trends, uncover inefficiencies, and guide strategic planning, ultimately leading to better business outcomes.
- Enhanced Customer Satisfaction: By optimizing production processes, ensuring timely delivery, and maintaining high product quality, manufacturing software helps improve customer satisfaction. Satisfied customers are more likely to become repeat buyers and recommend the business to others, driving growth and profitability.
- Compliance and Risk Management: Manufacturing software helps businesses comply with industry regulations and standards by maintaining accurate records and providing audit trails. It also enhances risk management by identifying potential issues early and implementing preventive measures to mitigate them.
Overall, implementing manufacturing software can significantly enhance the operational capabilities of small businesses, enabling them to compete more effectively in the market and achieve long-term success.
Key Features to Look for in the Manufacturing Software
The key features to look for in the manufacturing software for small businesses are:
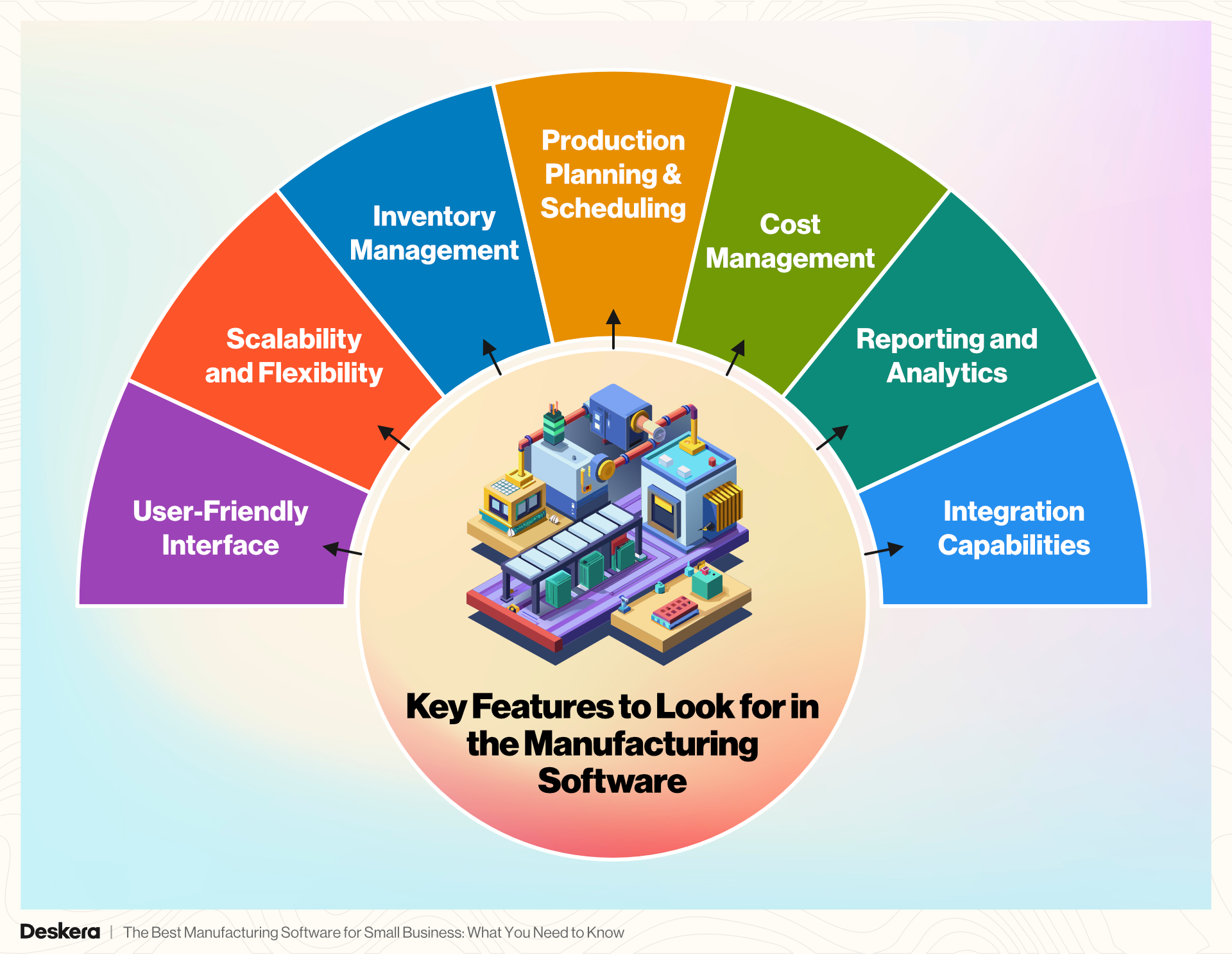
User-Friendly Interface
A user-friendly interface is crucial for manufacturing software for small businesses, as it ensures that employees can quickly learn and efficiently use the system.
Ease of use reduces the time and cost associated with training, allowing staff to focus on productive tasks. Intuitive interfaces often feature clear navigation menus, visual dashboards, and drag-and-drop functionalities.
For instance, ERP software for small manufacturing businesses with a streamlined design can simplify complex processes such as inventory management and production scheduling, making it easier for users to access and interpret critical data without extensive technical knowledge.
Scalability and Flexibility
Scalability and flexibility are essential attributes for any manufacturing software, particularly ERP solutions for manufacturing. As small businesses grow and their production needs evolve, scalable software can accommodate increased workloads and more complex operations.
Flexible systems offer customization options, allowing businesses to tailor the software to their specific requirements. For example, a manufacturing scheduling software for small businesses that scales with company growth can add modules for new product lines or expanded facilities.
Customizable ERP for manufacturing enables businesses to adapt workflows, reports, and functionalities to their unique processes, ensuring that the software remains relevant as the business expands.
Inventory Management
Effective inventory management is a cornerstone of successful manufacturing operations. Manufacturing inventory software provides real-time tracking and updates on stock levels, helping businesses avoid overstocking or stockouts.
Integration with other systems, such as accounting software for manufacturing small businesses, ensures seamless data flow and accurate financial reporting.
This integration allows for better demand forecasting, more efficient reordering processes, and improved cash flow management.
By utilizing real-time data, small businesses can maintain optimal inventory levels, reduce holding costs, and enhance overall supply chain efficiency.
Production Planning and Scheduling
Production planning and scheduling are critical for meeting customer demands and optimizing resource utilization.
Manufacturing software for small businesses often includes tools that help create and adjust production schedules based on real-time data.
These tools assist in forecasting demand, allocating resources efficiently, and identifying potential bottlenecks.
For instance, ERP software for small manufacturing businesses with advanced scheduling capabilities can synchronize production runs with inventory levels and workforce availability.
This ensures that production processes are streamlined, deadlines are met, and operational efficiency is maximized.
Cost Management
Cost management is vital for maintaining profitability and financial health. Manufacturing software helps track and control production costs by monitoring expenses related to materials, labor, and overhead.
Budgeting and financial reporting features within ERP solutions for manufacturing provide detailed insights into cost structures and enable businesses to make informed financial decisions.
By analyzing cost data, small businesses can identify areas for cost reduction, optimize resource allocation, and improve overall financial performance.
Effective cost management ensures that manufacturing operations remain within budget and contributes to sustainable business growth.
Reporting and Analytics
Data-driven decisions are essential for staying competitive in the manufacturing industry. Manufacturing software offers robust reporting and analytics features that provide valuable insights into various aspects of operations.
These tools generate reports on production performance, inventory levels, financial metrics, and more. Analytics capabilities enable businesses to identify trends, measure key performance indicators (KPIs), and make strategic adjustments.
For example, ERP for manufacturing systems with advanced analytics can help small businesses forecast demand, optimize production schedules, and improve resource utilization.
Access to comprehensive and accurate data empowers businesses to make informed decisions and drive continuous improvement.
Integration Capabilities
Integration capabilities are critical for ensuring that manufacturing software works seamlessly with other business systems.
Compatibility with accounting software, customer relationship management (CRM) systems, and other tools allows for efficient data sharing and process automation.
APIs and third-party integrations enable businesses to connect their manufacturing software with external applications, enhancing functionality and streamlining workflows.
For instance, integrating manufacturing software for small businesses with CRM systems can improve customer order management and communication.
These integration capabilities ensure that all business functions are aligned, reducing redundancies and improving overall efficiency.
Top Manufacturing Software for Small Business
The top 5 manufacturing software for small businesses are:
Deskera ERP
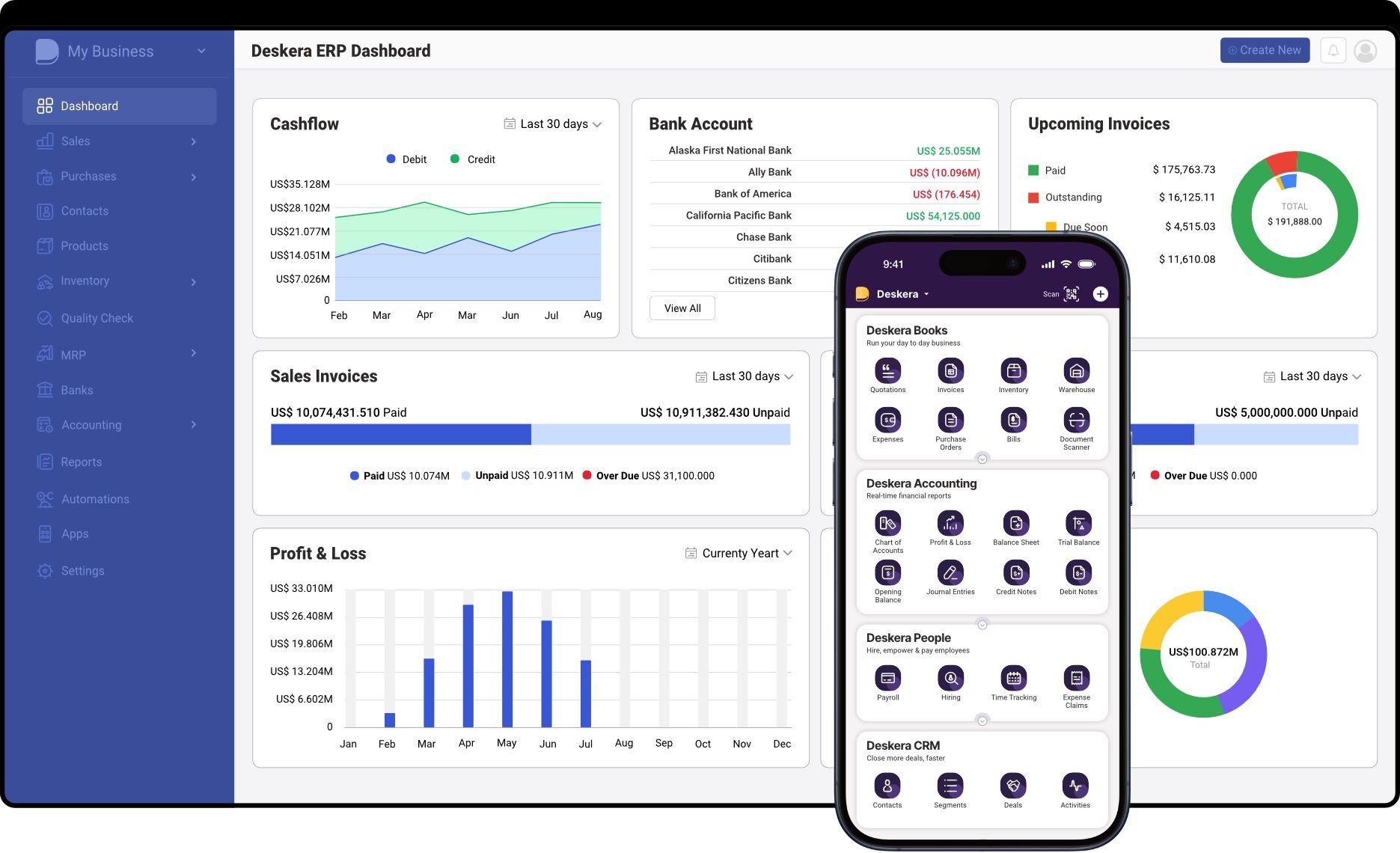
Deskera ERP is a comprehensive solution designed for small businesses, offering an integrated platform for managing inventory, production, and financials. Known for its user-friendly interface and robust features, Deskera ERP helps streamline operations and improve efficiency.
Key Features
Inventory Management: Real-time tracking and updates provide a clear view of stock levels, helping businesses avoid overstocking or stockouts. Deskera ERP integrates seamlessly with other systems, allowing for efficient inventory control and accurate forecasting.
Production Planning: Advanced scheduling tools enable businesses to create and adjust production schedules based on real-time data, ensuring optimal resource utilization and timely order fulfillment. The software helps identify potential bottlenecks and streamline production processes.
Financial Integration: Deskera ERP includes comprehensive accounting software for manufacturing small businesses. It tracks expenses, manages budgets, and generates financial reports, offering a clear picture of financial health and supporting informed decision-making.
Reporting and Analytics: The platform provides robust reporting and analytics capabilities, offering valuable insights into various aspects of operations. Users can generate custom reports on production performance, inventory levels, and financial metrics, aiding strategic planning and continuous improvement.
Scalability: Deskera ERP is designed to adapt to business growth. The software's customizable options allow businesses to add new modules and features as their needs evolve, ensuring the system remains relevant and effective.
Mobile Accessibility: Enables you to manage and access critical business data and processes on-the-go, enhancing flexibility and responsiveness.
AI-Assistant David: Automates routine tasks, assists in navigating through the ERP software, and provides real-time insights to support informed decision-making.
Robust Security Measures: Ensures robust security to safeguard your data against cyber threats and unauthorized access, ensuring peace of mind for your business operations.
Pros and Cons
Pros: Easy to use, affordable, comprehensive feature set.
Cons: No features for document management
Katana
Katana is a modern manufacturing software designed specifically for small businesses. It offers an intuitive and visual interface, making it easy for users to manage production and inventory efficiently.
Key Features
User-Friendly Interface: Intuitive design for easy navigation.
Inventory Management: Real-time updates and tracking.
Production Planning: Visual tools for effective scheduling.
Integration Capabilities: Compatible with various third-party applications.
Cost Management: Tracking and controlling production costs.
Pros and Cons
Pros: Easy to use, affordable, excellent for visual management.
Cons: Limited advanced features compared to larger ERP systems.
Acumatica
Acumatica is a cloud-based ERP solution that offers a flexible, scalable, and user-friendly platform for small businesses. It integrates various business functions, including manufacturing, financials, and customer management, providing a comprehensive solution that grows with your business.
Key Features
- ERP Solutions for Manufacturing: Integrates production, inventory, and financial management for streamlined operations.
- Manufacturing Scheduling Software for Small Business: Advanced scheduling tools help optimize production processes and resource allocation.
- Inventory Management: Real-time inventory tracking and management to avoid stockouts and overstocking.
- Financial Management: Comprehensive budgeting, financial reporting, and expense tracking.
- Integration Capabilities: Seamless integration with other business software, such as CRM and eCommerce platforms.
- Scalability and Flexibility: Easily add modules and features as the business grows, ensuring the system remains relevant.
Pros and Cons
- Pros: User-friendly, highly scalable, flexible pricing, strong integration capabilities.
- Cons: Initial setup can be complex, customization may require technical expertise.
Odoo
Odoo is an open-source ERP system that offers a wide array of modules tailored to various business needs, including manufacturing, inventory, and accounting. Its affordability and extensive customization options make it a popular choice for small businesses.
Key Features
- Manufacturing Software for Small Business: Comprehensive tools for managing manufacturing processes from planning to execution.
- ERP Software for Small Manufacturing Business: Modules for production, inventory, and financial management.
- Inventory Management: Real-time updates and tracking, integration with sales and procurement.
- Production Planning and Scheduling: Tools for optimizing production schedules, resource allocation, and capacity planning.
- Cost Management: Features for tracking production costs, budgeting, and financial reporting.
- Integration Capabilities: Compatible with various third-party applications through APIs and built-in connectors.
Pros and Cons
- Pros: Affordable, highly customizable, extensive module options, strong community support.
- Cons: Customization can be complex and time-consuming, may require technical expertise for setup and maintenance.
Fishbowl
Fishbowl is specifically designed for inventory management and manufacturing for small to medium-sized businesses. It integrates seamlessly with QuickBooks, making it an excellent choice for businesses needing robust inventory and manufacturing capabilities without the complexity of larger ERP systems.
Key Features
- Manufacturing Inventory Software: Efficient inventory management with real-time tracking and updates.
- Manufacturing Scheduling Software for Small Business: Tools for creating and managing production schedules to optimize resource use.
- Integration with QuickBooks: Seamless financial integration for streamlined accounting and inventory processes.
- Cost Management: Features for tracking production costs and generating detailed financial reports.
- Reporting and Analytics: Data-driven insights into inventory levels, production performance, and financial health.
- User-Friendly Interface: Intuitive design that simplifies inventory and manufacturing management.
Pros and Cons
- Pros: Easy integration with QuickBooks, user-friendly interface, affordable, strong inventory management features.
- Cons: Limited advanced ERP features compared to larger systems, primarily focused on inventory and manufacturing.
How to Choose the Right Manufacturing Software
To choose the right manufacturing software, you must follow these steps:
Assessing Your Business Needs and Goals
Before selecting manufacturing software for small business, it's crucial to assess your specific needs and goals. Determine the core functionalities required, such as inventory management, production planning, or accounting integration.
For instance, ERP software for small manufacturing businesses might be essential if you need a comprehensive solution that integrates various business processes.
Clearly defining your objectives, such as improving efficiency or scaling operations, will help you narrow down the options.
Understanding your needs ensures that the chosen software aligns with your business strategies and supports long-term growth.
Budget Considerations
Budget is a key factor in choosing the best manufacturing software for small business. Software costs can vary widely, from affordable solutions to high-end systems.
It's important to consider not only the initial purchase price but also ongoing expenses such as subscription fees, maintenance, and training costs.
Some software providers offer scalable pricing plans that grow with your business, making ERP solutions for manufacturing more accessible to small businesses.
Carefully evaluate the total cost of ownership and ensure the software provides a good return on investment by enhancing operational efficiency and productivity.
Evaluating Software Providers
Evaluating software providers involves looking beyond the product itself to assess the level of support and service offered.
Reliable customer support is essential, especially during the implementation phase and for troubleshooting issues.
Check if the provider offers regular software updates to keep the system current with industry standards and technological advancements.
Reviews of manufacturing software for small business often highlight the importance of responsive and knowledgeable support teams.
Additionally, consider the provider’s reputation and experience in the industry, as well-established companies are more likely to offer robust and reliable solutions.
Trial Periods and Demonstrations
Taking advantage of trial periods and demonstrations is a practical way to assess manufacturing software for small businesses.
Many providers offer free trials or demo versions of their software, allowing you to test its functionality and user interface.
This hands-on experience can help you determine if the software meets your operational needs and is user-friendly for your team.
During the trial, focus on key features such as inventory management, manufacturing scheduling software for small business, and integration capabilities.
A thorough evaluation during the trial period can prevent costly mistakes and ensure the software is a good fit.
Reading User Reviews and Testimonials
User reviews and testimonials provide valuable insights into the performance and reliability of manufacturing software.
Reading reviews from other small businesses can highlight common benefits and potential drawbacks of specific software options.
Look for feedback on features such as ERP for manufacturing, ease of use, customer support, and overall satisfaction. Reviews often reveal practical experiences that can help you make an informed decision.
Additionally, testimonials from reputable sources or industry experts can validate the effectiveness of the software.
Incorporating this feedback into your decision-making process ensures that you choose a solution that is well-regarded and proven in real-world applications.
Implementation and Best Practices
Successfully implementing manufacturing software for small businesses requires a strategic approach and adherence to best practices.
This section provides essential steps to ensure a smooth transition, effective staff training, ongoing maintenance, and methods for measuring success and return on investment.
Steps for a Smooth Implementation Process
Implementing manufacturing software for small businesses requires careful planning and execution. Start by defining a clear implementation strategy, including setting realistic timelines and milestones.
Involve key stakeholders from different departments to ensure that all business needs are addressed. Conduct a thorough system setup, including data migration, configuration of features, and integration with existing systems such as accounting software for manufacturing small businesses.
Regularly communicate progress and address any issues promptly. Testing the software in a controlled environment before full deployment helps identify and resolve potential problems, ensuring a smooth transition and minimal disruption to operations.
Training and Onboarding for Staff
Effective training and onboarding are essential for maximizing the benefits of manufacturing software for small businesses. Develop a comprehensive training program that covers all aspects of the software, from basic navigation to advanced features like ERP for manufacturing.
Utilize various training methods, including hands-on sessions, tutorials, and user manuals, to cater to different learning styles. Encourage staff to ask questions and provide feedback to improve the training process.
Regular training updates and refresher courses help keep employees proficient as new features are introduced. A well-trained team ensures efficient use of the software, leading to improved productivity and accuracy.
Ongoing Maintenance and Support
Ongoing maintenance and support are crucial for the long-term success of any manufacturing software. Regular software updates and patches ensure that the system remains secure and performs optimally.
Establish a support system that includes access to customer service for troubleshooting issues and answering questions.
Some ERP solutions for manufacturing offer dedicated support teams that provide assistance with complex problems. Scheduled maintenance checks help identify and resolve potential issues before they impact operations.
Keeping the software updated and maintaining open communication with the support team ensures that the system continues to meet your business needs effectively.
Measuring Success and ROI
Measuring success and return on investment (ROI) is essential to evaluate the effectiveness of manufacturing software for small businesses.
Start by defining key performance indicators (KPIs) that align with your business goals, such as improved production efficiency, reduced inventory costs, or enhanced financial reporting.
Use the reporting and analytics features of the software to track these metrics over time. Compare pre-implementation and post-implementation data to assess the software’s impact on your operations.
Regularly reviewing these metrics helps identify areas for further improvement and ensures that the software continues to deliver value. Demonstrating a positive ROI validates the investment and supports future technology initiatives.
Key Takeaways
Choosing the best manufacturing software for small businesses is crucial for enhancing efficiency, accuracy, and overall competitiveness.
Definition and Purpose: Manufacturing software integrates various business processes, automating tasks to enhance efficiency and accuracy.
Types of Manufacturing Software: ERP, MRP, MES are the main types, each catering to specific aspects of manufacturing operations.
Benefits for Small Businesses: Improves inventory management, production planning, financial management, and overall operational efficiency.
The key features to look for in the manufacturing software are:
User-Friendly Interface: Essential for ease of use and quick adoption.
Scalability and Flexibility: Ability to grow with your business and adapt to changing needs.
Inventory Management: Real-time tracking and seamless integration with other systems.
Production Planning and Scheduling: Tools for optimizing schedules and resource planning.
Cost Management: Features for tracking production costs and budgeting.
Reporting and Analytics: Crucial for data-driven decision-making.
Integration Capabilities: Compatibility with other software like accounting and CRM.
To choose the right manufacturing software,
Assess Business Needs and Goals: Understand your specific requirements and objectives.
Budget Considerations: Ensure the software fits within your financial constraints.
Evaluate Software Providers: Look for good customer support, regular updates, and reliable performance.
Trial Periods and Demonstrations: Test the software before committing.
Read User Reviews and Testimonials: Gain insights from other users’ experiences.
The manufacturing software implementation and best practices are:
Steps for Smooth Implementation: Clear strategy, stakeholder involvement, thorough setup, and regular communication.
Training and Onboarding for Staff: Comprehensive training programs and regular updates.
Ongoing Maintenance and Support: Regular updates, dedicated support, and scheduled maintenance.
Measuring Success and ROI: Define KPIs, track metrics, and compare pre- and post-implementation data.
Deskera ERP is one of the leading manufacturing software for small businesses. It offers powerful features such as inventory management, production planning, financial integration, mobile accessibility, AI-assistant David, and robust security measures.
Related Articles
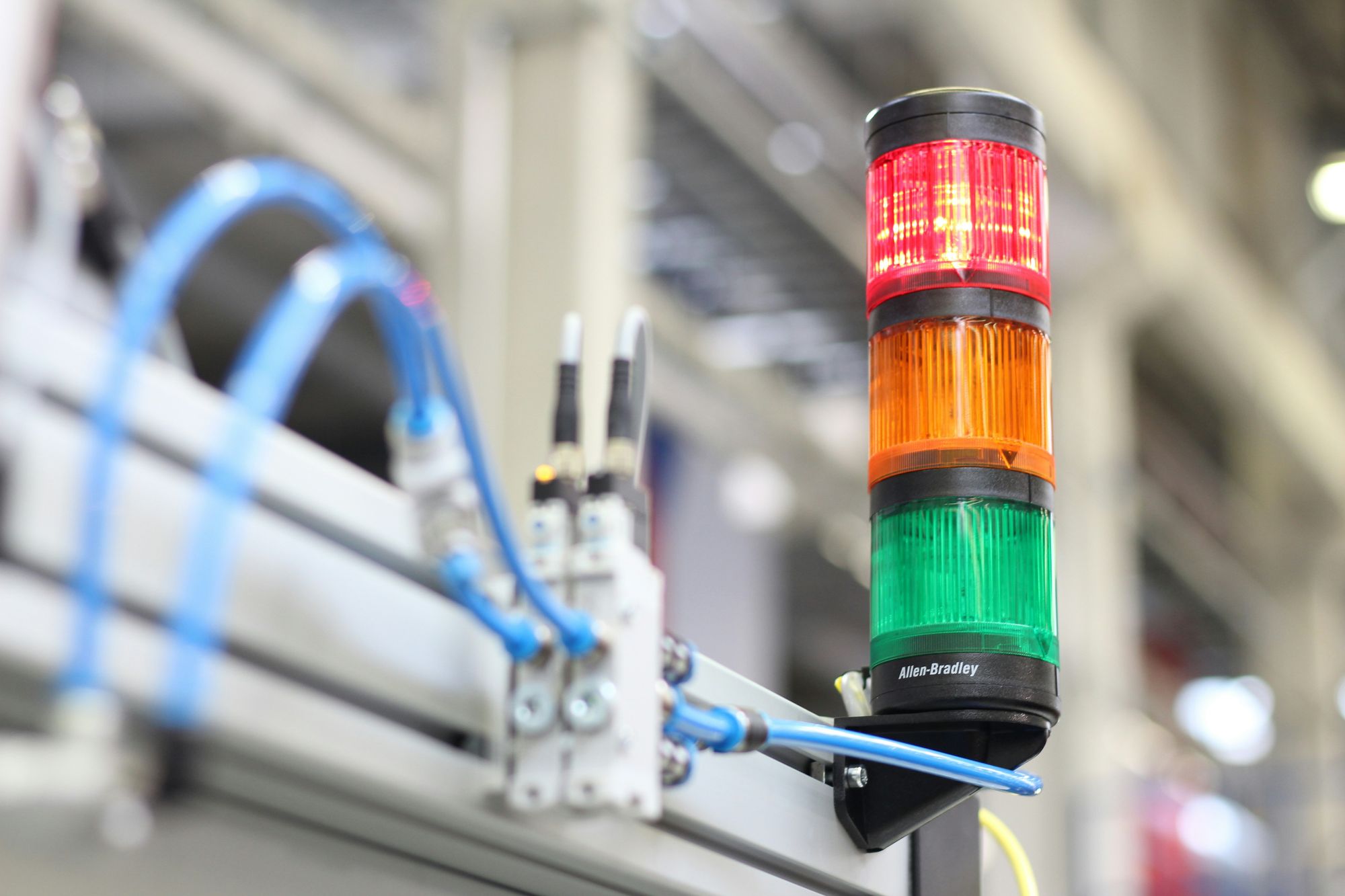
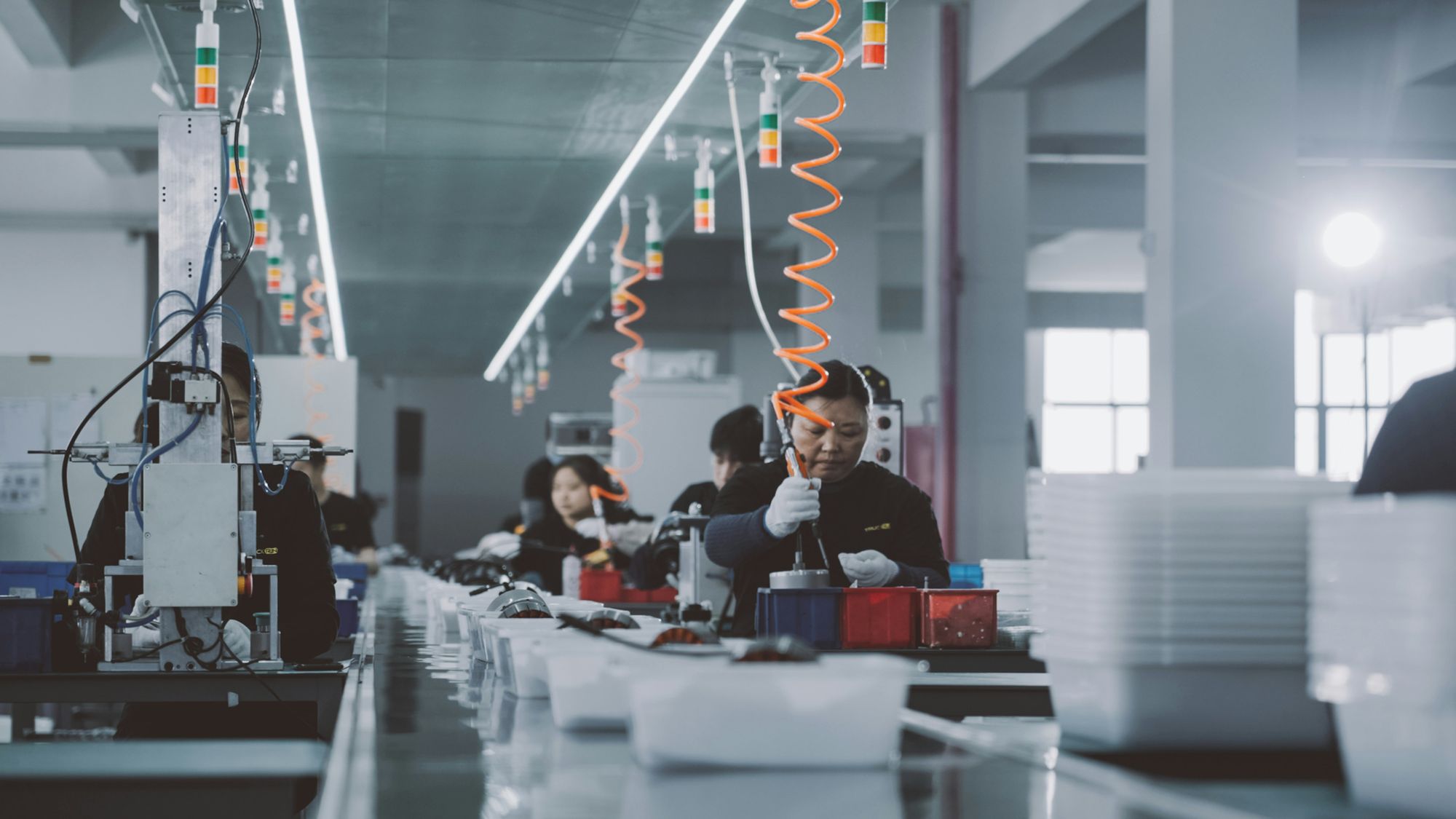
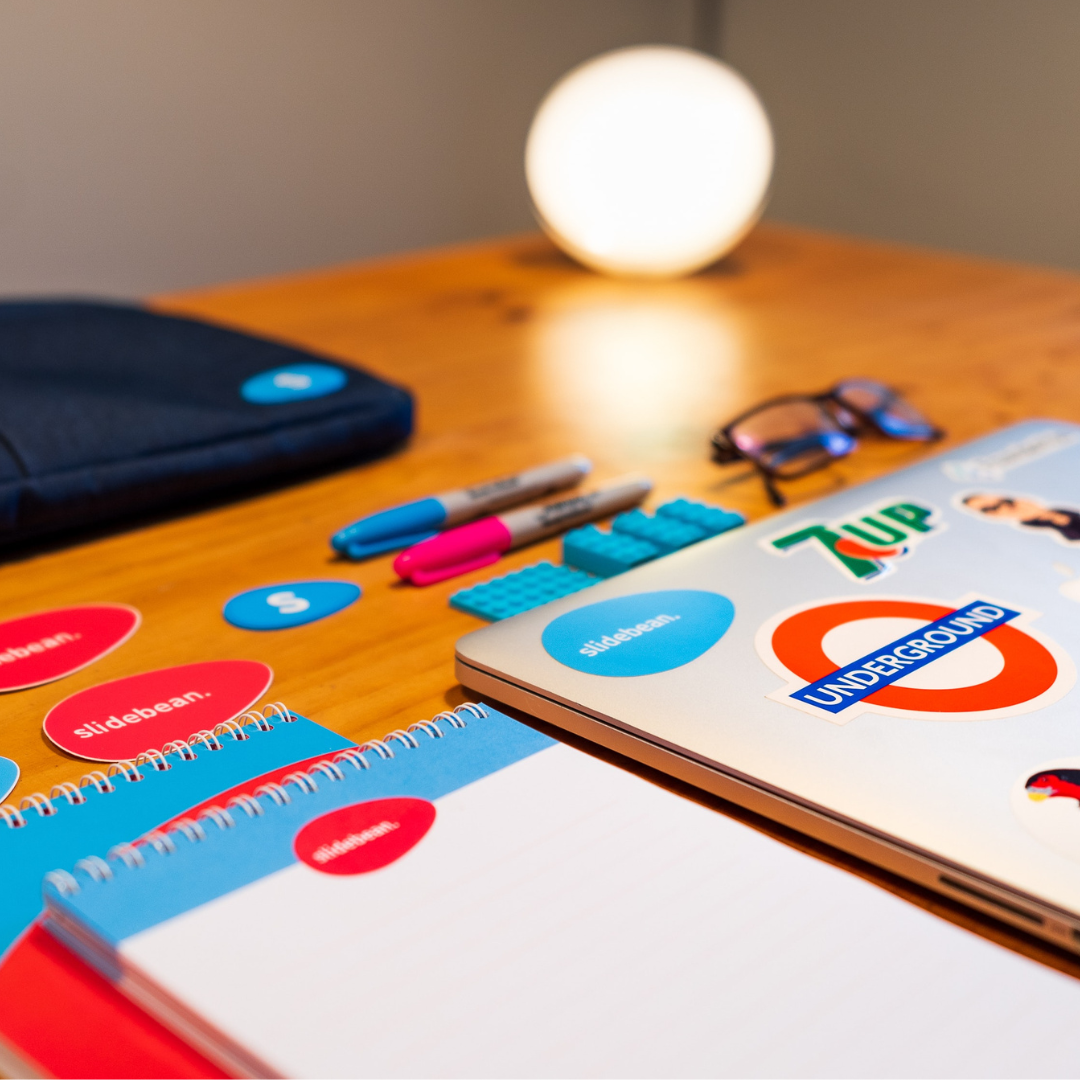
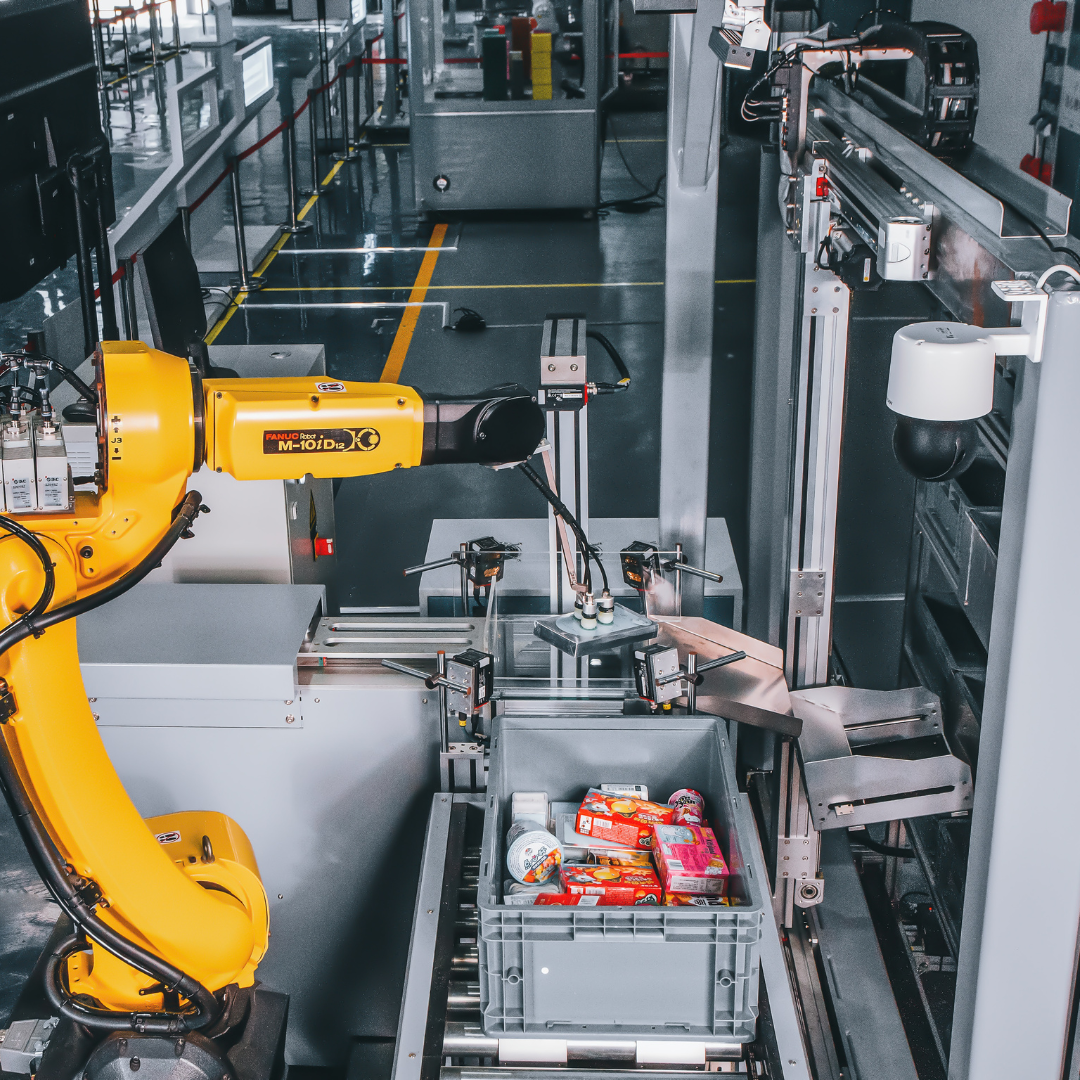
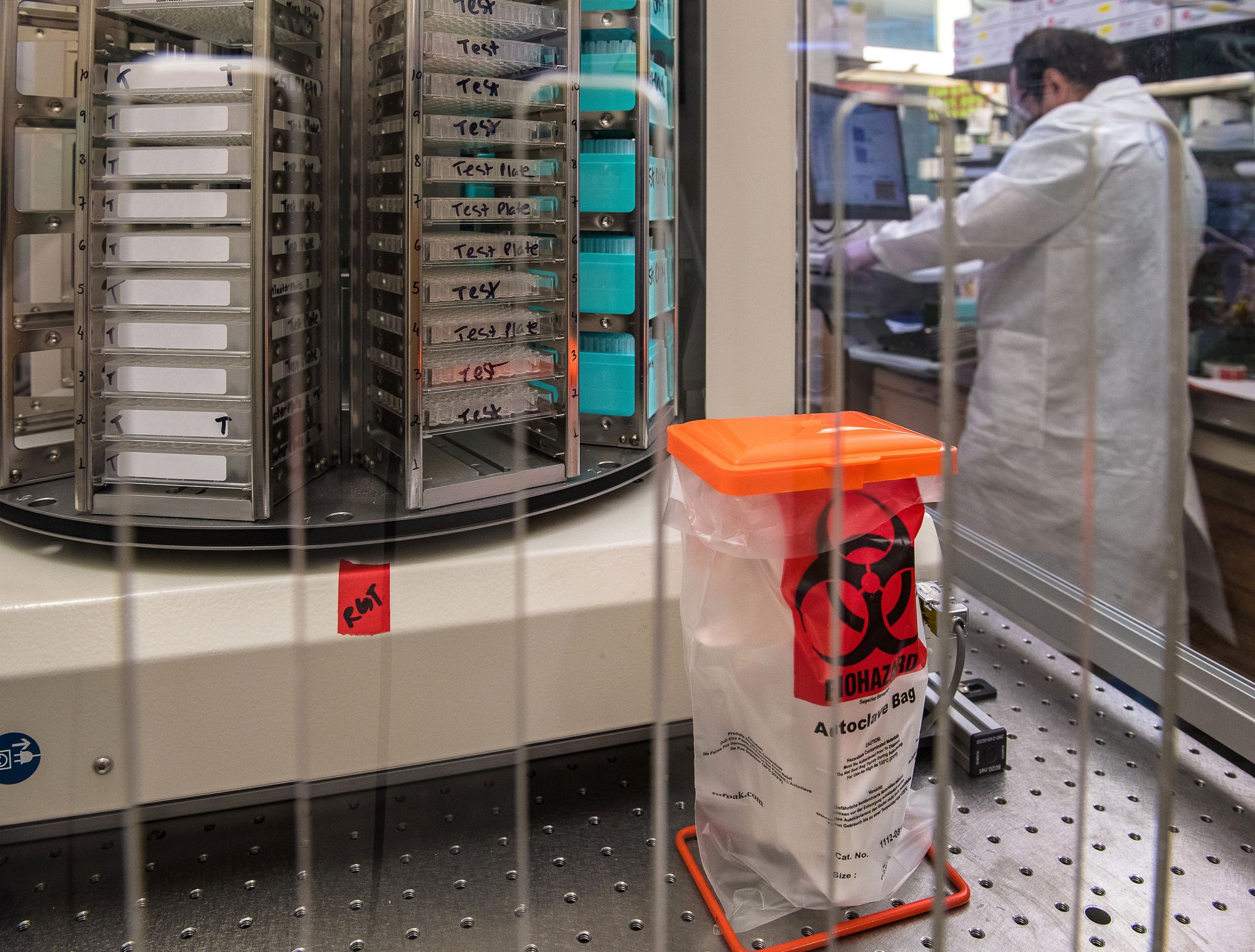
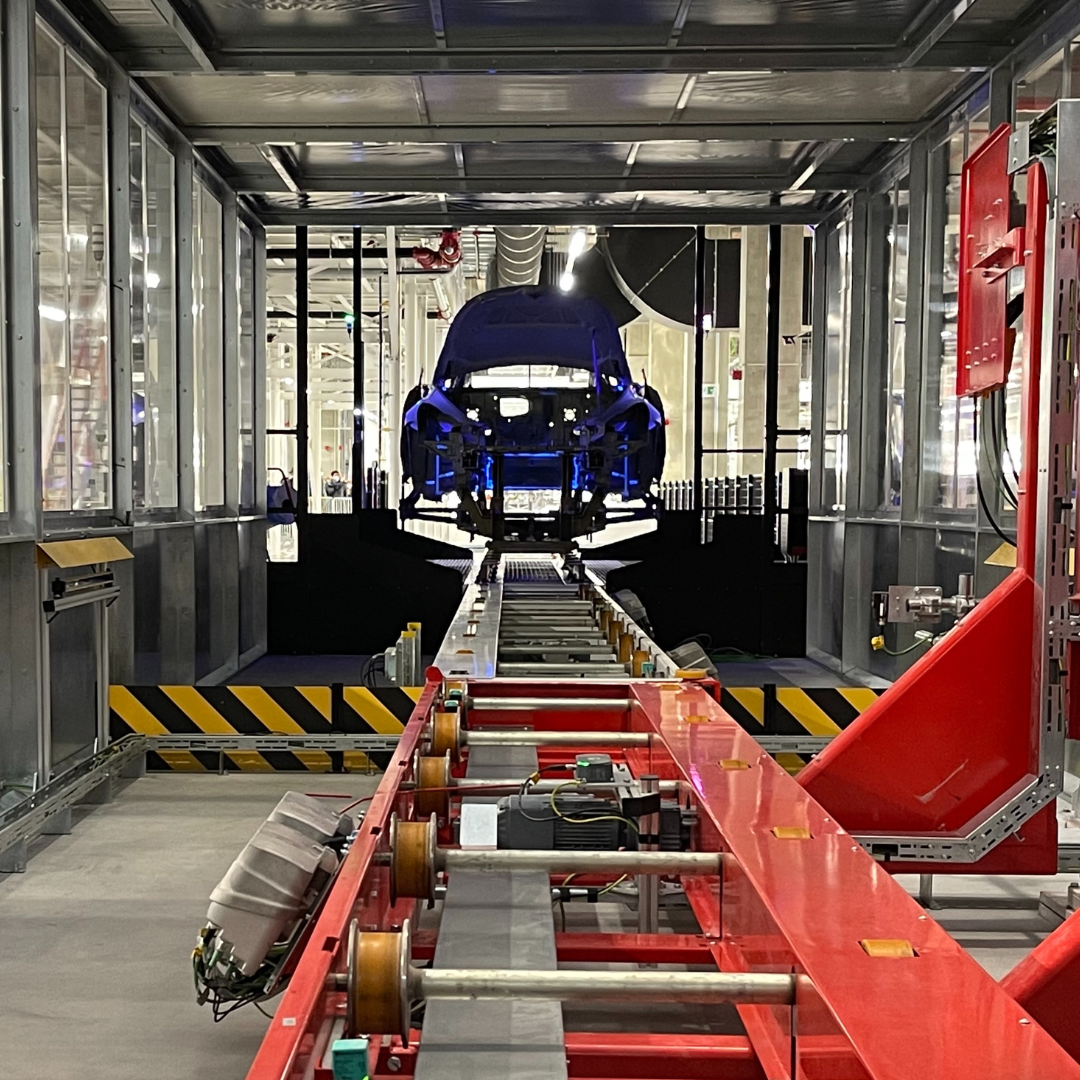