Did you know that manufacturing companies are the biggest users of ERP software, accounting for 47% of businesses seeking to implement it? This statistic highlights how critical efficient management has become in the manufacturing sector, where the complexity of production processes requires advanced solutions.
Manufacturing management software plays a pivotal role in streamlining these operations. By automating tasks such as production planning, inventory control, and quality management, it enables manufacturers to optimize efficiency, reduce waste, and improve output.
In today’s competitive market, businesses that adopt this technology gain a significant advantage by ensuring smoother workflows and real-time decision-making.
To stay competitive, companies need this software not only to boost operational efficiency but also to cut costs and adapt to changing demands quickly. Without it, manual processes become overwhelming and errors inevitable, leading to reduced productivity and profitability.
Deskera manufacturing ERP offers a comprehensive solution to these challenges. It combines production planning, inventory management, and demand forecasting in one platform.
With AI-driven insights and real-time tracking, Deskera manufacturing ERP helps manufacturers optimize resources, reduce lead times, and enhance overall production efficiency, making it an ideal choice for modern manufacturing environments.
What is Manufacturing Management Software?
Manufacturing management software is a digital solution designed to streamline and optimize the complex processes involved in manufacturing operations. This type of software provides businesses with the tools they need to plan, execute, and monitor production activities efficiently.
It integrates various functions such as production scheduling, inventory management, quality control, and supply chain coordination, enabling manufacturers to have real-time visibility into their operations.
There are different types of manufacturing management software, including ERP (Enterprise Resource Planning), MRP (Material Requirements Planning), and MES (Manufacturing Execution System). Each offers unique functionalities tailored to different aspects of the manufacturing process.
For instance, ERP focuses on integrating all business functions, while MRP handles inventory and material planning, and MES ensures production execution and quality control on the shop floor.
At its core, manufacturing management software is designed to enhance operational efficiency, reduce production costs, and improve product quality. By automating routine tasks and providing real-time data on every stage of the production cycle, it helps businesses make informed decisions, adapt to changes quickly, and meet customer demands effectively.
Key Features of Manufacturing Management Software
Manufacturing management software offers a wide range of features designed to streamline and optimize production processes. These features ensure that every aspect of manufacturing, from inventory to quality control, is managed effectively.
Below are some key features that make this software indispensable for businesses:
1. Production Planning and Scheduling
Effective production planning and scheduling is crucial to meeting deadlines and maximizing resources. Manufacturing management software allows manufacturers to automate production schedules, ensuring efficient use of machinery, materials, and labor. This reduces downtime and enhances productivity by aligning production with customer demand.
2. Inventory Management
Manufacturing inventory management software provides real-time tracking of raw materials and finished products. This feature ensures that manufacturers can monitor inventory levels, reduce stock shortages, and avoid overstocking, leading to better cash flow management and optimized storage space.
3. Quality Control
A robust quality management software for manufacturing ensures that every product meets set standards before leaving the production line. With automated inspections, defect tracking, and reporting, manufacturers can ensure consistent product quality while reducing the chances of costly recalls or returns.
4. Supply Chain Management
Managing suppliers and procurement processes is another critical aspect of manufacturing. Manufacturing operations management software helps streamline supply chain activities by tracking vendor performance, managing purchase orders, and monitoring lead times. This ensures seamless coordination between suppliers and production teams, reducing delays and improving overall efficiency.
5. Financial and Cost Management
Manufacturing ERP systems often come with integrated financial modules, enabling companies to monitor production costs, track labor expenses, and manage overall budgets. By integrating financial data with production metrics, businesses can make better-informed decisions that drive profitability.
6. Project Management
For companies that handle complex manufacturing projects, manufacturing project management software is essential. This feature allows businesses to track project progress, allocate resources, and manage timelines, ensuring that projects stay on track and within budget.
7. Compliance and Reporting
Staying compliant with industry regulations is crucial for manufacturers. Manufacturing process management software provides built-in compliance features and reporting tools that help ensure adherence to standards such as ISO or OSHA. This reduces the risk of penalties and keeps operations in line with legal requirements.
8. Customization and Scalability
The best manufacturing software for small businesses offers customization options that allow it to adapt to unique business needs. Additionally, scalable solutions ensure that the software grows with the company, providing flexibility as production demands increase.
9. Cost-Effective Solutions
For businesses seeking affordable solutions, there are several low-cost manufacturing ERP software options that provide essential features without breaking the bank. Some companies may even opt for manufacturing management software free versions, ideal for startups or small-scale operations.
10. Cloud-Based Access and Mobility
Many modern ERP for manufacturing industry systems offer cloud-based platforms, allowing manufacturers to access their data remotely and manage operations from anywhere. This enhances collaboration across teams and ensures real-time access to critical information, even in decentralized or global operations.
Incorporating these features into any best ERP software for manufacturing ensures businesses can streamline processes, maintain high-quality standards, and stay competitive in the dynamic manufacturing landscape.
Key Benefits of Manufacturing Management Software
Implementing manufacturing management software can transform production operations by enhancing efficiency, improving decision-making, and reducing costs.
Below are some of the key benefits that manufacturers can expect when using these systems:
1. Increased Operational Efficiency
Manufacturing management software automates various manual tasks such as production planning, scheduling, and inventory management, reducing the risk of human errors and increasing overall efficiency.
By integrating data across departments, the software helps optimize resource allocation, minimize downtime, and ensure smooth workflows throughout the manufacturing process.
2. Real-Time Visibility and Data-Driven Decision Making
With manufacturing ERP, manufacturers gain real-time access to crucial data on production, inventory, and supply chain activities.
This visibility enables decision-makers to monitor performance, identify bottlenecks, and quickly address issues before they escalate. By leveraging data analytics, manufacturers can make informed decisions that improve output and profitability.
3. Cost Reduction
Manufacturing inventory management software helps businesses track raw materials, finished goods, and inventory levels, reducing excess stock and preventing costly stockouts.
This not only improves cash flow but also helps optimize storage space. Moreover, automated production scheduling and resource management lead to more efficient use of labor and machinery, which cuts down on operational costs.
4. Improved Product Quality
Using quality management software for manufacturing, manufacturers can ensure consistent product quality by automating inspections, tracking defects, and maintaining compliance with industry standards.
This results in fewer returns, reduced waste, and increased customer satisfaction. By integrating quality control processes into the manufacturing system, businesses can maintain high standards without compromising efficiency.
5. Enhanced Supply Chain Management
Manufacturing management software allows seamless coordination with suppliers by automating procurement, tracking vendor performance, and managing orders.
This integration ensures timely delivery of materials, minimizes supply chain disruptions, and improves relationships with key vendors.
As a result, manufacturers can reduce lead times and respond more effectively to customer demands.
6. Scalability and Flexibility
For growing businesses, using scalable manufacturing ERP solutions or low-cost manufacturing ERP software ensures that the software can grow along with the company.
Whether expanding production lines or entering new markets, the system’s flexibility allows manufacturers to adapt their processes quickly without significant disruptions.
7. Improved Collaboration
By integrating all business functions—from production and inventory to finance and sales—manufacturing management software fosters better communication and collaboration between departments.
This integrated approach ensures that everyone has access to the same data, which enhances team coordination and reduces miscommunication.
8. Regulatory Compliance and Reporting
Many ERP for manufacturing industry systems come with built-in compliance features that help businesses adhere to industry regulations such as ISO standards or OSHA requirements.
Additionally, robust reporting capabilities allow manufacturers to generate custom reports for audits, performance tracking, and decision-making, ensuring smooth compliance management.
9. Customer Satisfaction
Manufacturing management software enhances product quality, reduces production delays, and optimizes delivery schedules, all of which contribute to improved customer satisfaction.
By ensuring that orders are fulfilled on time and meet quality standards, businesses can build stronger relationships with clients and maintain a positive reputation in the market.
10. Lower Total Cost of Ownership
For smaller businesses, opting for the best manufacturing software for small businesses can provide immediate benefits without a significant upfront investment.
Even for larger enterprises, the cost savings from increased efficiency, reduced waste, and better resource management outweigh the initial costs of implementing the software.
Incorporating the right manufacturing project management software and other related solutions can revolutionize operations and enable manufacturers to stay competitive, cost-effective, and customer-focused.
Common Challenges in Manufacturing Without Software
Running a manufacturing operation without the aid of manufacturing management software presents numerous challenges that can hinder productivity, increase costs, and compromise product quality.
Below are some of the most common challenges manufacturers face when they rely on manual or outdated processes:
1. Inefficient Production Planning
Without automated manufacturing project management software, businesses often struggle with production planning and scheduling. Managing resources, labor, and machinery manually can lead to inefficient use of assets, delays, and inconsistent production output. This results in missed deadlines and unfulfilled customer orders, impacting both revenue and reputation.
2. Poor Inventory Management
One of the biggest issues in manufacturing without software is ineffective inventory management. Manufacturing inventory management software tracks raw materials, work-in-progress, and finished goods in real time. Without it, manufacturers risk stockouts, overstocking, and material shortages, which can lead to production delays or excessive storage costs.
3. Limited Visibility and Data Accuracy
Manual systems often lack real-time visibility into production processes, leading to poor decision-making. Without the data integration provided by manufacturing ERP, businesses are forced to rely on fragmented or outdated information, making it harder to identify inefficiencies, track performance, or forecast demand accurately.
4. Inconsistent Product Quality
Ensuring consistent product quality is a significant challenge without quality management software for manufacturing. Manual quality control processes are prone to errors, and any defects or compliance issues may go unnoticed until after production, leading to costly recalls or product returns. Inconsistent quality can also damage a company’s reputation and strain customer relationships.
5. Increased Operational Costs
Manufacturers that don't use manufacturing process management software often face higher operational costs due to inefficient use of resources and labor.
Manual tracking of production workflows, combined with errors in resource allocation, can result in wasted time, excess inventory, and overuse of materials—all of which increase costs unnecessarily.
6. Supply Chain Disruptions
Managing procurement, vendor relationships, and inventory levels manually can lead to frequent supply chain disruptions. Without manufacturing operations management software, manufacturers often face issues like late deliveries, unfulfilled orders, or poor coordination with suppliers, all of which can slow down production and affect customer satisfaction.
7. Difficulty in Scaling Operations
Growing manufacturing businesses need flexibility and scalability to accommodate increased production demands. Without the right ERP for manufacturing industry, scaling operations becomes difficult, as manual processes are time-consuming and prone to errors. This lack of scalability can prevent businesses from expanding efficiently and responding quickly to market demands.
8. Compliance and Regulatory Challenges
Meeting industry regulations and standards can be a time-consuming process without the automated features of manufacturing management software. Without integrated compliance tracking, businesses risk falling short of regulatory requirements, leading to penalties, legal issues, or loss of certification.
9. Poor Collaboration Across Departments
In the absence of an integrated system like manufacturing ERP, communication between departments—such as production, inventory, and sales—becomes siloed. This lack of collaboration can lead to miscommunication, delays, and bottlenecks, hindering the overall productivity and efficiency of the manufacturing process.
10. Inability to Optimize Costs and Resources
Without the visibility provided by low-cost manufacturing ERP software, it is challenging to optimize costs and resource allocation. This can result in excessive labor costs, wasted materials, and higher production expenses, all of which impact a company’s profitability.
These challenges highlight the importance of investing in manufacturing management software. By automating critical processes, businesses can avoid common pitfalls, improve operational efficiency, and remain competitive in today’s fast-paced market.
How to Choose the Right Manufacturing Management Software
Selecting the right manufacturing management software is crucial for enhancing operational efficiency and achieving business goals. With numerous options available, it’s essential to choose a solution that aligns with your specific needs and objectives.
Here’s a step-by-step guide to help you make an informed decision:
1. Assess Your Needs and Objectives
Start by evaluating your current manufacturing processes and identifying areas where software could add the most value. Consider factors such as:
- Production Planning: Do you need advanced scheduling and resource management?
- Inventory Control: Are you looking for real-time inventory tracking and automated reordering?
- Quality Management: Do you require robust quality control features?
Understanding your specific needs will help you choose a solution that offers the right set of features.
2. Consider Software Features and Functionality
Compare the features offered by different software solutions to ensure they meet your requirements. Key features to look for include:
- Production Scheduling: Automated scheduling and resource allocation.
- Inventory Management: Real-time tracking of materials and finished goods.
- Quality Control: Tools for monitoring and managing product quality.
- Reporting and Analytics: Comprehensive reporting capabilities for data-driven decision-making.
Opt for solutions that offer comprehensive functionality relevant to your manufacturing processes, such as manufacturing process management software.
3. Evaluate Integration Capabilities
Ensure that the software integrates seamlessly with your existing systems, such as accounting software, CRM, or supply chain management tools. Integration capabilities are essential for maintaining data consistency and streamlining operations. Look for solutions that offer:
- ERP Integration: Compatibility with ERP for manufacturing industry systems.
- Data Syncing: Automatic data transfer between systems to reduce manual input.
Integration helps ensure that your manufacturing management software works cohesively with other business functions, enhancing overall efficiency.
4. Consider Scalability and Flexibility
Choose software that can grow with your business. Scalability is important for adapting to increased production demands or expanding operations. Look for:
- Customization Options: Ability to tailor the software to your specific needs.
- Modular Design: Options to add or remove features as your business evolves.
The best ERP software for manufacturing are scalable solutions that will allow you to adjust functionalities based on your growth.
5. Evaluate Cost and ROI
Assess the total cost of ownership, including initial setup, licensing fees, and ongoing maintenance costs. Consider both short-term and long-term expenses to ensure the software provides a good return on investment. Options include:
- Free Solutions: Manufacturing management software free versions for small-scale operations.
- Cost-Effective Choices: Best ERP for manufacturing industry solutions that offer competitive pricing.
Calculate potential savings from increased efficiency and reduced operational costs to determine the software’s ROI.
6. Check Vendor Reputation and Support
Research the software vendor’s reputation and support services. Look for:
- Customer Reviews: Feedback from other users to gauge satisfaction and reliability.
- Support Services: Availability of customer support, training resources, and software updates.
A reputable vendor with strong support services ensures that you can resolve issues quickly and make the most of your manufacturing management software.
7. Conduct a Trial or Demo
Before making a final decision, request a trial or demo of the software. This allows you to:
- Test Functionality: Evaluate how well the software meets your needs in a real-world scenario.
- Assess Usability: Determine if the interface is user-friendly and intuitive.
A trial or demo can provide valuable insights into how the software performs and whether it aligns with your manufacturing processes.
8. Consider Industry-Specific Needs
Some manufacturing sectors have unique requirements. Ensure the software you choose caters to industry-specific needs, such as:
- Compliance Requirements: Adherence to industry standards and regulations.
- Specialized Features: Custom features relevant to your manufacturing type.
Selecting software designed for your industry ensures it addresses specific challenges and compliance needs.
By following these steps and carefully evaluating your options, you can choose the right manufacturing management software that enhances your operational efficiency, supports growth, and improves overall business performance.
Top Manufacturing Management Software Options in 2024
In 2024, several manufacturing management software solutions stand out for their comprehensive features, scalability, and ability to address the diverse needs of manufacturing businesses. Here’s a brief overview of some of the leading options, including their key features, pricing, and target industries:
1. Deskera Manufacturing ERP
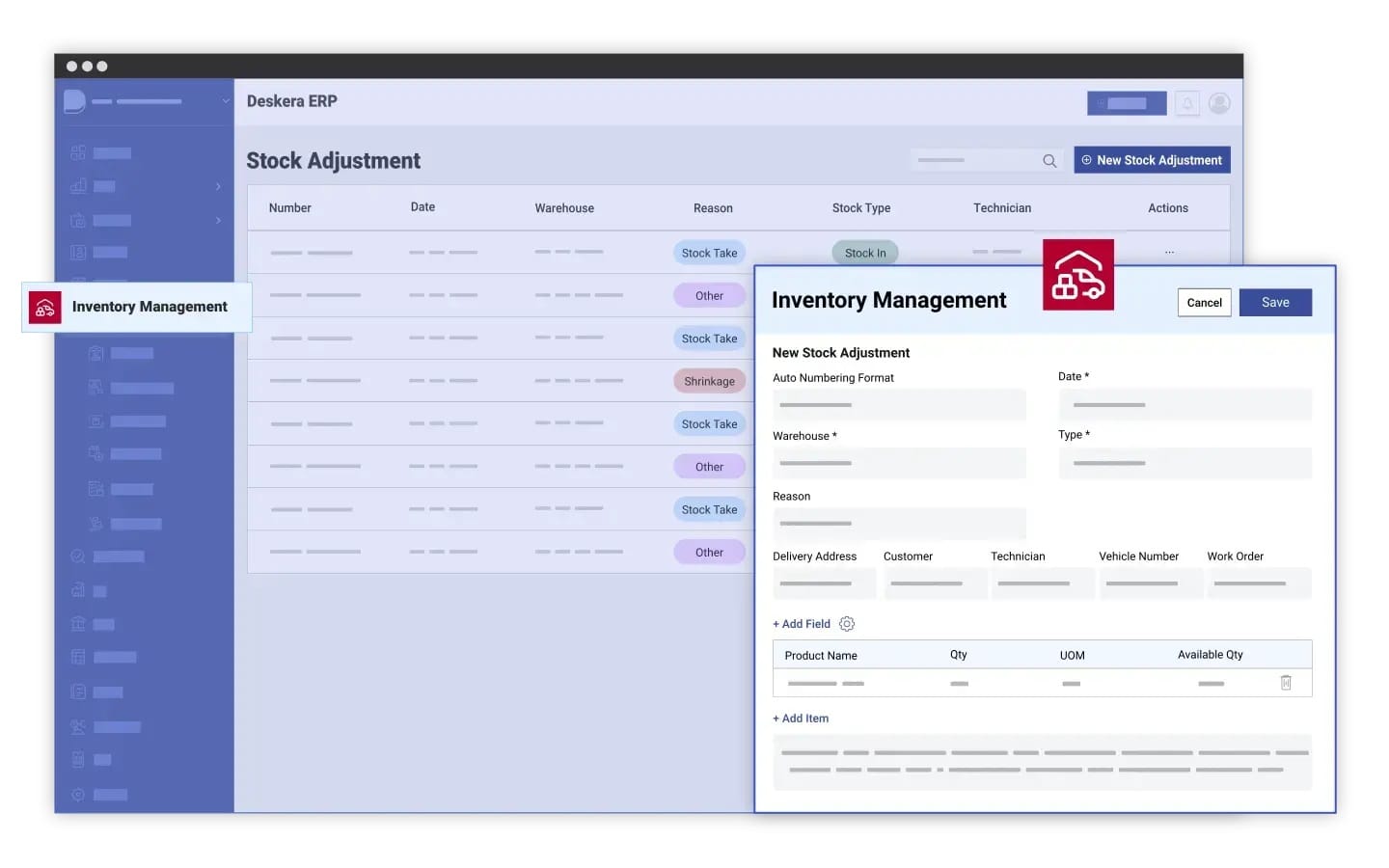
Overview: Deskera offers a robust manufacturing ERP solution that integrates various business functions into a single platform. It’s designed to streamline production processes, manage inventory, and enhance overall efficiency. With advanced features and an AI assistant, Deskera is well-suited for businesses looking to optimize their operations comprehensively.
Key Features:
- Production Planning: Automated scheduling and resource allocation to optimize production workflows.
- Inventory Management: Real-time tracking of raw materials, work-in-progress, and finished goods to minimize stockouts and excess inventory.
- Quality Control: Built-in quality management tools to ensure consistent product quality and compliance with industry standards.
- Demand Forecasting: Advanced analytics and machine learning algorithms to predict future demand and adjust production schedules accordingly.
- AI Assistant - David: Deskera’s AI Assistant, David, offers smart insights, automated data entry, and predictive analytics to enhance decision-making and operational efficiency.
- Reporting and Analytics: Comprehensive reporting tools for monitoring performance, generating financial reports, and analyzing key business metrics.
- Mobile Access: Mobile-friendly interface for managing operations on the go, including access to production schedules, inventory levels, and real-time alerts.
Pricing: Deskera provides tiered pricing based on the size of the organization and the features required. It offers both standard and customized plans, making it suitable for small to medium-sized businesses. Pricing details are available upon request.
Target Industries: Deskera caters to a range of industries, including manufacturing, distribution, and retail. It’s particularly beneficial for companies looking for an all-in-one solution that scales with their growth and incorporates advanced features like AI-driven insights.
2. Katana
Overview: Katana is known for its user-friendly interface and powerful manufacturing inventory management software capabilities. It’s designed to help small to medium-sized manufacturers manage production and inventory efficiently.
Key Features:
- Real-Time Inventory Tracking: Updates inventory levels in real time.
- Production Scheduling: Simplified scheduling and order management.
- Integration: Seamless integration with eCommerce platforms and accounting software.
- Reporting: Detailed reports on sales, inventory, and production.
Pricing: Katana offers several pricing tiers, starting from an affordable basic plan to more advanced options with additional features. Pricing varies depending on the number of users and additional functionalities required.
Target Industries: Katana is ideal for small to mid-sized manufacturers across various sectors, including consumer goods, electronics, and apparel. It’s especially useful for businesses looking to streamline inventory and production processes.
3. Fishbowl Manufacturing
Overview: Fishbowl Manufacturing provides a comprehensive manufacturing operations management software solution that integrates with QuickBooks. It’s designed for businesses that need advanced inventory and manufacturing management capabilities.
Key Features:
- Inventory Management: Advanced features for tracking inventory levels, orders, and shipments.
- Production Management: Tools for managing work orders, bills of materials, and production schedules.
- Integration: Integrates seamlessly with QuickBooks for financial management.
- Reporting: Customizable reporting and analytics for better decision-making.
Pricing: Fishbowl Manufacturing offers a range of pricing plans based on the number of users and features required. Pricing is available upon request, with options for both on-premises and cloud-based solutions.
Target Industries: Fishbowl is suitable for various manufacturing sectors, including electronics, automotive, and consumer products. It’s especially beneficial for companies already using QuickBooks for their accounting needs.
4. JobBOSS
Overview: JobBOSS is a flexible manufacturing project management software designed to help job shops and custom manufacturers manage their operations efficiently. It focuses on job tracking and production management.
Key Features:
- Job Tracking: Real-time tracking of job status, costs, and timelines.
- Production Scheduling: Tools for managing production schedules and resource allocation.
- Inventory Control: Comprehensive inventory management and purchasing features.
- Reporting: Detailed reports on job performance, costs, and profitability.
Pricing: JobBOSS offers customizable pricing based on the specific needs of the business. Pricing information is available through direct consultation with the vendor.
Target Industries: JobBOSS is particularly suited for job shops, custom manufacturers, and companies with complex production needs. It’s beneficial for businesses that require detailed job tracking and project management.
These manufacturing management software options offer a range of features and pricing structures to meet the needs of different industries and business sizes. By selecting the right solution, manufacturers can enhance efficiency, streamline operations, and improve overall performance.
Future Trends in Manufacturing Management Software
As manufacturing continues to evolve, so do the technologies and tools that support it. The landscape of manufacturing management software is rapidly changing, driven by advancements in technology and shifting industry needs. Here are some key trends shaping the future of manufacturing management software:
1. Integration of Artificial Intelligence and Machine Learning
Overview: Artificial Intelligence (AI) and Machine Learning (ML) are becoming integral to manufacturing ERP systems. These technologies enhance predictive analytics, automate routine tasks, and optimize production processes.
Key Developments:
- Predictive Maintenance: AI-driven algorithms can predict equipment failures before they occur, reducing downtime and maintenance costs.
- Enhanced Quality Control: Machine learning models analyze production data to identify and rectify quality issues in real time.
- Smart Automation: AI-powered systems adjust production schedules and resource allocation dynamically based on real-time data and forecasts.
Impact: The integration of AI and ML improves operational efficiency, reduces manual intervention, and enhances decision-making capabilities in manufacturing operations management software.
2. Growth of Cloud-Based Solutions
Overview: Cloud-based manufacturing management software continues to gain popularity due to its flexibility, scalability, and cost-effectiveness. Cloud solutions offer businesses the ability to access their systems and data from anywhere, facilitating remote management and collaboration.
Key Developments:
- Scalability: Cloud-based platforms easily scale with business growth, accommodating increased data volumes and user requirements.
- Real-Time Access: Cloud solutions provide real-time access to data and analytics, enhancing responsiveness and agility.
- Cost Efficiency: Reduced upfront costs and pay-as-you-go pricing models make cloud solutions accessible for businesses of all sizes.
Impact: Cloud-based manufacturing ERP systems provide greater flexibility and accessibility, allowing businesses to adapt quickly to changing market conditions and operational needs.
3. Enhanced Cybersecurity Measures
Overview: As manufacturing systems become more interconnected, cybersecurity becomes increasingly critical. Protecting sensitive data and ensuring the integrity of manufacturing processes are top priorities.
Key Developments:
- Advanced Threat Detection: Enhanced cybersecurity solutions use AI and machine learning to detect and respond to potential threats in real time.
- Data Encryption: Robust encryption methods safeguard data both in transit and at rest.
- Compliance: Software solutions incorporate features to ensure compliance with industry standards and regulations, such as GDPR and CCPA.
Impact: Improved cybersecurity measures protect against data breaches and cyberattacks, ensuring the safety and reliability of manufacturing management software.
4. Increased Focus on Sustainability and Green Manufacturing
Overview: Sustainability is becoming a key focus in manufacturing, driven by regulatory pressures and consumer demand. Manufacturing management software is evolving to support green manufacturing initiatives and reduce environmental impact.
Key Developments:
- Energy Management: Software tools track and optimize energy usage, reducing consumption and costs.
- Waste Reduction: Advanced analytics identify opportunities for reducing waste and improving resource utilization.
- Sustainability Reporting: Integrated reporting features provide insights into environmental impact and support compliance with sustainability standards.
Impact: By supporting green manufacturing practices, manufacturing management software helps businesses meet environmental goals, improve efficiency, and enhance their corporate social responsibility profile.
5. Adoption of Industry 4.0 Technologies
Overview: Industry 4.0 technologies, including the Internet of Things (IoT), digital twins, and advanced robotics, are transforming manufacturing processes. These technologies are increasingly integrated into manufacturing project management software to enhance automation and data visibility.
Key Developments:
- IoT Integration: IoT devices provide real-time data on equipment performance and production metrics, enabling better monitoring and control.
- Digital Twins: Virtual models of physical assets allow for simulation and analysis, improving design and operational efficiency.
- Advanced Robotics: Collaborative robots (cobots) and automated systems enhance precision and productivity on the factory floor.
Impact: The adoption of Industry 4.0 technologies leads to smarter, more efficient manufacturing operations, driving innovation and competitiveness in the industry.
6. Customizable and Modular Solutions
Overview: Manufacturers are increasingly seeking customizable and modular manufacturing management software solutions that can be tailored to their specific needs. This approach allows businesses to select and integrate features that best align with their unique processes.
Key Developments:
- Modular Architecture: Software solutions offer modular components that can be added or removed based on business requirements.
- Customization Options: Flexible configuration options allow businesses to tailor the software to their specific workflows and processes.
- Integration Capabilities: Enhanced integration features support seamless connections with other business systems and tools.
Impact: Customizable and modular software solutions provide greater flexibility and adaptability, enabling businesses to implement solutions that fit their precise needs and scale as they grow.
These trends highlight the dynamic evolution of manufacturing management software and its increasing alignment with technological advancements and industry demands. By staying informed about these developments, manufacturers can leverage cutting-edge solutions to drive efficiency, innovation, and competitive advantage.
The Role of Manufacturing Management Software in Industry 4.0
Industry 4.0, also known as the Fourth Industrial Revolution, represents a transformative shift in manufacturing through the integration of advanced technologies such as the Internet of Things (IoT), artificial intelligence (AI), and automation.
Manufacturing management software plays a pivotal role in facilitating this revolution, enabling businesses to harness these technologies for improved efficiency, flexibility, and competitiveness. Here’s how manufacturing management software supports Industry 4.0:
1. Integration with IoT Devices
Overview: The Internet of Things (IoT) involves connecting physical devices and machinery to the internet, enabling them to collect and exchange data. Manufacturing management software integrates with IoT devices to provide real-time insights into production processes.
Key Benefits:
- Real-Time Monitoring: IoT sensors track equipment performance, environmental conditions, and production metrics, providing real-time data to the software.
- Predictive Maintenance: By analyzing data from IoT devices, the software can predict equipment failures and schedule maintenance before issues arise, reducing downtime.
- Enhanced Visibility: Provides a comprehensive view of the entire production process, helping to identify bottlenecks and optimize workflows.
Impact: Integration with IoT devices enhances operational visibility and efficiency, leading to more informed decision-making and proactive management.
2. Leveraging AI and Machine Learning
Overview: Artificial Intelligence (AI) and Machine Learning (ML) are integral to Industry 4.0, offering advanced analytics and automation capabilities. Manufacturing management software incorporates AI and ML to optimize various aspects of manufacturing.
Key Benefits:
- Predictive Analytics: AI algorithms analyze historical data to forecast demand, optimize inventory levels, and improve production scheduling.
- Quality Control: Machine learning models detect patterns and anomalies in production data, enhancing quality control and reducing defects.
- Automated Decision-Making: AI-driven systems automate routine tasks and decision-making processes, increasing efficiency and reducing human error.
Impact: AI and ML integration empowers manufacturers to leverage data for strategic decision-making, improve quality, and enhance operational efficiency.
3. Utilizing Digital Twins
Overview: Digital twins are virtual replicas of physical assets or processes. Manufacturing management software uses digital twins to simulate and analyze production systems in a virtual environment.
Key Benefits:
- Simulation and Optimization: Digital twins allow manufacturers to simulate various scenarios and test changes in a risk-free environment, optimizing production processes.
- Real-Time Data Integration: Digital twins integrate real-time data from IoT devices, providing a dynamic view of physical assets and processes.
- Enhanced Design and Testing: Manufacturers can test new designs and processes virtually, reducing time and costs associated with physical prototyping.
Impact: Digital twins enhance design, testing, and optimization capabilities, leading to more efficient and innovative manufacturing processes.
4. Facilitating Smart Automation
Overview: Smart automation involves the use of advanced robotics and automated systems to perform complex tasks with minimal human intervention. Manufacturing management software supports smart automation by coordinating and optimizing these systems.
Key Benefits:
- Flexible Manufacturing: Automated systems can quickly adapt to changes in production schedules and product specifications, enabling flexible manufacturing.
- Increased Precision: Robotics and automated systems perform tasks with high precision, reducing errors and improving product quality.
- Efficient Resource Utilization: Automation optimizes resource allocation and reduces waste, leading to more efficient production processes.
Impact: Smart automation enhances manufacturing flexibility, precision, and efficiency, driving innovation and competitiveness.
5. Enhancing Data Analytics and Reporting
Overview: Data analytics and reporting are crucial for understanding and optimizing manufacturing operations. Manufacturing management software provides advanced analytics and reporting capabilities to support data-driven decision-making.
Key Benefits:
- Comprehensive Reporting: Advanced reporting tools offer insights into production performance, quality metrics, and operational efficiency.
- Data-Driven Insights: Analytics tools analyze large volumes of data to identify trends, forecast demand, and optimize inventory management.
- Real-Time Dashboards: Real-time dashboards provide up-to-date information on key performance indicators, enabling timely decision-making.
Impact: Enhanced data analytics and reporting capabilities enable manufacturers to make informed decisions, optimize operations, and drive continuous improvement.
6. Supporting Cybersecurity and Data Protection
Overview: With the increased connectivity of Industry 4.0 technologies, cybersecurity becomes a critical concern. Manufacturing management software incorporates advanced security measures to protect data and ensure system integrity.
Key Benefits:
- Advanced Threat Detection: AI and machine learning technologies detect and respond to potential security threats in real time.
- Data Encryption: Robust encryption methods safeguard sensitive data both in transit and at rest.
- Compliance: Software solutions include features to ensure compliance with industry regulations and data protection standards.
Impact: Strong cybersecurity measures protect against data breaches and cyberattacks, ensuring the reliability and security of manufacturing operations.
7. Enabling Seamless Integration Across Systems
Overview: Industry 4.0 requires seamless integration between various systems and technologies. Manufacturing management software facilitates integration across different platforms and applications.
Key Benefits:
- Interoperability: Software solutions integrate with ERP systems, IoT devices, and other business applications, providing a unified view of operations.
- Data Synchronization: Ensures consistent and accurate data across all systems, improving coordination and efficiency.
- Streamlined Processes: Integration reduces manual data entry and improves process automation.
Impact: Seamless integration enhances operational efficiency and ensures that all systems work together harmoniously, supporting the goals of Industry 4.0.
Manufacturing management software is at the heart of Industry 4.0, enabling manufacturers to leverage advanced technologies for enhanced efficiency, flexibility, and competitiveness.
By integrating with IoT devices, utilizing AI and machine learning, supporting digital twins, facilitating smart automation, enhancing data analytics, ensuring cybersecurity, and enabling system integration, these software solutions drive the future of manufacturing. Embracing these capabilities will help manufacturers stay ahead in a rapidly evolving industry landscape.
Ensuring Data Security and Compliance with Manufacturing Management Software
In an era where data breaches and regulatory requirements are increasingly stringent, ensuring data security and compliance is paramount for manufacturers using manufacturing management software. This software not only streamlines production processes but also handles vast amounts of sensitive data.
Here’s how businesses can ensure data security and compliance with their manufacturing management software:
1. Implementing Robust Cybersecurity Measures
Overview: Cybersecurity is crucial for protecting sensitive data from unauthorized access and cyberattacks. Effective cybersecurity measures within manufacturing management software safeguard against potential threats and vulnerabilities.
Key Strategies:
- Advanced Threat Detection: Utilize AI and machine learning algorithms to identify and respond to potential security threats in real time.
- Regular Security Updates: Ensure that the software is updated regularly with the latest security patches and updates to protect against known vulnerabilities.
- Multi-Factor Authentication (MFA): Implement MFA to add an extra layer of security by requiring additional verification steps for user access.
Impact: Robust cybersecurity measures protect against data breaches, ensuring the integrity and confidentiality of manufacturing data.
2. Ensuring Data Encryption
Overview: Data encryption is essential for securing sensitive information both in transit and at rest. Manufacturing management software should include encryption protocols to protect data from unauthorized access.
Key Strategies:
- Data Encryption in Transit: Use secure protocols such as TLS (Transport Layer Security) to encrypt data transmitted over networks.
- Data Encryption at Rest: Encrypt stored data using strong encryption algorithms to protect it from unauthorized access.
- End-to-End Encryption: Ensure that all data exchanges between systems, users, and devices are encrypted to maintain data security throughout its lifecycle.
Impact: Encryption protects sensitive data from being intercepted or accessed by unauthorized parties, maintaining data confidentiality and security.
3. Adhering to Regulatory Compliance
Overview: Compliance with industry regulations and data protection laws is critical for avoiding legal issues and maintaining customer trust. Manufacturing management software should support compliance with relevant regulations.
Key Strategies:
- GDPR Compliance: Ensure that the software adheres to the General Data Protection Regulation (GDPR) by implementing data protection measures, such as data minimization and user consent management.
- HIPAA Compliance: For manufacturers in the healthcare sector, ensure compliance with the Health Insurance Portability and Accountability Act (HIPAA) by protecting patient data and maintaining confidentiality.
- Industry-Specific Standards: Comply with industry-specific standards such as ISO 9001 for quality management and ISO 27001 for information security management.
Impact: Adhering to regulatory compliance helps avoid legal penalties and enhances the trust of customers and stakeholders by ensuring that data protection standards are met.
4. Implementing Access Controls
Overview: Access controls manage who can access and modify data within the manufacturing management software. Properly configured access controls prevent unauthorized users from accessing sensitive information.
Key Strategies:
- Role-Based Access Control (RBAC): Implement RBAC to assign permissions based on user roles, ensuring that individuals only have access to the data necessary for their job functions.
- User Authentication: Require strong passwords and authentication methods to verify user identities before granting access.
- Access Monitoring: Regularly review and audit user access logs to detect and address any unauthorized access attempts.
Impact: Effective access controls ensure that only authorized personnel can access sensitive data, reducing the risk of data breaches and unauthorized modifications.
5. Conducting Regular Security Audits
Overview: Regular security audits are essential for identifying potential vulnerabilities and ensuring that data security measures are effective. Manufacturing management software should undergo periodic audits to assess its security posture.
Key Strategies:
- Vulnerability Assessments: Perform regular vulnerability assessments to identify and address potential security weaknesses.
- Penetration Testing: Conduct penetration testing to simulate cyberattacks and evaluate the software’s defenses against potential threats.
- Compliance Audits: Regularly review compliance with data protection regulations and industry standards to ensure ongoing adherence.
Impact: Regular security audits help identify and mitigate potential security issues, ensuring that the software remains secure and compliant with regulations.
6. Implementing Data Backup and Recovery Solutions
Overview: Data backup and recovery solutions ensure that critical data can be restored in the event of a loss or corruption. Manufacturing management software should include robust backup and recovery mechanisms.
Key Strategies:
- Automated Backups: Schedule regular automated backups to ensure that data is consistently backed up without manual intervention.
- Backup Encryption: Encrypt backup data to protect it from unauthorized access.
- Disaster Recovery Plan: Develop and test a disaster recovery plan to quickly restore data and resume operations in the event of a system failure or data loss.
Impact: Effective data backup and recovery solutions ensure data integrity and availability, minimizing the impact of data loss or corruption on manufacturing operations.
7. Training and Awareness Programs
Overview: Employee training and awareness programs are critical for maintaining data security and compliance. Ensuring that staff members understand data protection practices and regulatory requirements is essential.
Key Strategies:
- Security Training: Provide regular training on cybersecurity best practices, including recognizing phishing attempts and safe data handling procedures.
- Compliance Education: Educate employees about regulatory requirements and their role in maintaining compliance.
- Ongoing Awareness: Implement ongoing awareness programs to keep employees informed about evolving security threats and best practices.
Impact: Training and awareness programs empower employees to follow best practices and contribute to maintaining data security and compliance.
Ensuring data security and compliance with manufacturing management software involves implementing robust cybersecurity measures, data encryption, adherence to regulatory standards, access controls, regular security audits, data backup and recovery solutions, and comprehensive training programs.
By addressing these aspects, manufacturers can protect sensitive data, meet regulatory requirements, and maintain the integrity of their operations. As the industry continues to evolve, staying vigilant and proactive in these areas will be crucial for safeguarding data and ensuring compliance.
Training and Implementation Strategies for Manufacturing Management Software
Implementing manufacturing management software effectively is crucial for maximizing its benefits and ensuring a smooth transition. Training and implementation strategies play a vital role in achieving successful adoption and integration.
Here’s a comprehensive guide to training and implementing manufacturing management software:
1. Develop a Clear Implementation Plan
Overview: A well-structured implementation plan outlines the steps needed to integrate the manufacturing management software into your existing operations. This plan should cover timelines, resource allocation, and key milestones.
Key Components:
- Project Scope: Define the objectives and scope of the implementation, including which features of the software will be utilized.
- Timeline: Establish a timeline for the implementation process, including key milestones and deadlines.
- Resource Allocation: Identify the resources needed, including personnel, budget, and technology.
Impact: A clear implementation plan ensures that all stakeholders are aligned and that the integration process is organized and efficient.
2. Conduct a Needs Assessment
Overview: Before implementation, assess your organization’s needs to ensure that the manufacturing management software aligns with your specific requirements.
Key Components:
- Current Processes: Review current manufacturing processes and identify areas for improvement.
- Software Requirements: Determine the features and capabilities required to address your needs.
- Stakeholder Input: Gather input from key stakeholders to understand their requirements and expectations.
Impact: A needs assessment helps tailor the software implementation to meet your organization’s specific needs and objectives.
3. Select a Project Team
Overview: A dedicated project team is essential for managing the implementation process and ensuring successful adoption of the manufacturing management software.
Key Roles:
- Project Manager: Oversees the implementation process, coordinates tasks, and ensures deadlines are met.
- IT Specialists: Handle technical aspects of the software installation and integration.
- Process Experts: Provide insights into existing processes and help configure the software to meet operational needs.
- End Users: Represent the departments that will use the software, providing feedback and testing functionality.
Impact: A well-chosen project team ensures that the implementation process is managed effectively and that all aspects of the software are addressed.
4. Develop a Comprehensive Training Program
Overview: Training is critical for ensuring that employees understand how to use the manufacturing management software effectively. A comprehensive training program should cover all aspects of the software and address the needs of different user groups.
Key Components:
- Training Materials: Create user guides, manuals, and online resources that provide detailed instructions on using the software.
- Training Sessions: Conduct hands-on training sessions, workshops, and webinars to familiarize users with the software’s features and functions.
- Ongoing Support: Offer continuous support and refresher training to address any issues and keep users updated on new features.
Impact: Effective training ensures that employees are confident in using the software and can leverage its full capabilities to improve manufacturing processes.
5. Configure and Customize the Software
Overview: Configuring and customizing the manufacturing management software to fit your organization’s specific needs is essential for optimal performance and usability.
Key Steps:
- System Configuration: Set up the software according to your organization’s processes, including configuring modules, workflows, and user roles.
- Customization: Tailor the software’s features and interfaces to align with your unique requirements and preferences.
- Integration: Integrate the software with existing systems, such as ERP or inventory management systems, to ensure seamless data flow and functionality.
Impact: Proper configuration and customization ensure that the software aligns with your business processes and integrates effectively with other systems.
6. Conduct Pilot Testing
Overview: Pilot testing involves running the manufacturing management software in a controlled environment to identify and address any issues before full-scale implementation.
Key Steps:
- Test Scenarios: Develop test scenarios that simulate real-world manufacturing processes and tasks.
- User Feedback: Collect feedback from pilot users to identify any issues or areas for improvement.
- Adjustments: Make necessary adjustments based on feedback and test results to optimize the software’s performance.
Impact: Pilot testing helps identify potential problems and ensures that the software is ready for full-scale deployment, minimizing disruptions and issues.
7. Monitor and Evaluate Performance
Overview: After implementation, ongoing monitoring and evaluation are crucial for assessing the effectiveness of the manufacturing management software and making continuous improvements.
Key Components:
- Performance Metrics: Define key performance indicators (KPIs) to measure the software’s impact on manufacturing processes, such as production efficiency, inventory accuracy, and quality control.
- User Feedback: Regularly collect feedback from users to identify any challenges or areas for improvement.
- Continuous Improvement: Use performance data and feedback to make iterative improvements to the software and its usage.
Impact: Monitoring and evaluating performance ensure that the software continues to meet your organization’s needs and provides opportunities for ongoing optimization.
8. Ensure Change Management
Overview: Effective change management is essential for overcoming resistance and ensuring a smooth transition to the new manufacturing management software.
Key Strategies:
- Communication: Keep stakeholders informed about the benefits and changes associated with the software implementation.
- Support Systems: Provide support systems, such as help desks and user forums, to assist employees with the transition.
- Change Champions: Identify and support change champions within the organization who can advocate for the software and assist their peers.
Impact: Effective change management helps to address resistance, build support, and ensure a successful adoption of the software.
Key Takeaways
- Manufacturing management software is crucial for modern manufacturing operations, offering benefits such as improved efficiency, cost-effectiveness, and competitive advantage. Companies must leverage this software to streamline processes and stay ahead in a rapidly evolving industry.
- Manufacturing management software integrates various functions of manufacturing operations, from inventory management to production scheduling. It plays a vital role in coordinating and optimizing processes to ensure seamless and efficient manufacturing workflows.
- Essential features of manufacturing management software include real-time inventory tracking, production scheduling, quality control, and data analytics. These features enable manufacturers to manage operations effectively, enhance productivity, and maintain high-quality standards.
- Manufacturing management software offers numerous benefits, including increased operational efficiency, cost reduction, improved decision-making, and enhanced quality control. By automating and integrating processes, it helps manufacturers achieve better results and stay competitive.
- Operating without manufacturing management software can lead to challenges such as inefficient processes, data inaccuracies, and difficulty in scaling operations. These challenges can hinder productivity and growth, highlighting the need for effective software solutions.
- Selecting the right manufacturing management software involves assessing your specific needs, evaluating software features, and considering factors like scalability, cost, and user-friendliness. A well-chosen software solution will align with your business requirements and support long-term success.
- Popular manufacturing management software options in 2024, such as Deskera, Katana, Fishbowl Manufacturing, and JobBOSS, offer various features and pricing models to suit different industries and business sizes. Evaluating these options can help you find the best fit for your organization.
- Future trends in manufacturing management software include advancements in AI and machine learning, increased automation, and greater integration with Industry 4.0 technologies. Staying abreast of these trends will help manufacturers adapt and thrive in a dynamic landscape.
- Manufacturing management software is integral to Industry 4.0, enabling smart manufacturing through data integration, IoT, and advanced analytics. It supports the transition to more intelligent, connected, and automated manufacturing processes.
- Ensuring data security and compliance involves implementing robust cybersecurity measures, data encryption, and adhering to regulatory standards. Protecting sensitive data and maintaining compliance are critical for safeguarding manufacturing operations and avoiding legal issues.
- Successful implementation of manufacturing management software requires a clear plan, thorough training, and effective change management. Proper preparation and support ensure a smooth transition and maximize the software’s benefits.
- Deskera Manufacturing ERP stands out for its comprehensive features tailored to enhance various aspects of manufacturing management, including real-time inventory tracking, production planning, and quality control. Its AI-powered assistant, David, offers advanced data analytics and predictive insights, helping businesses make informed decisions and optimize their operations effectively.
Related Articles
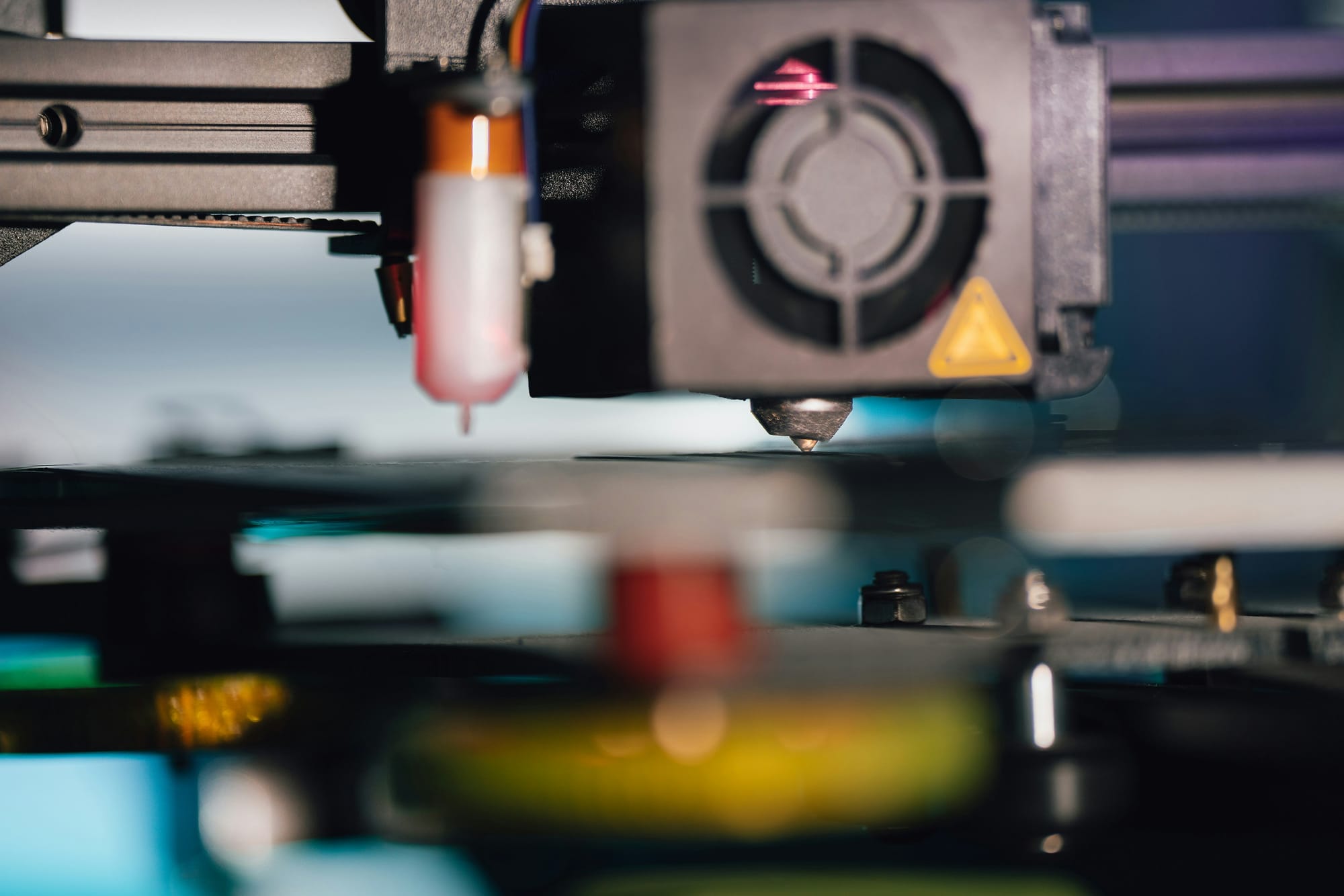
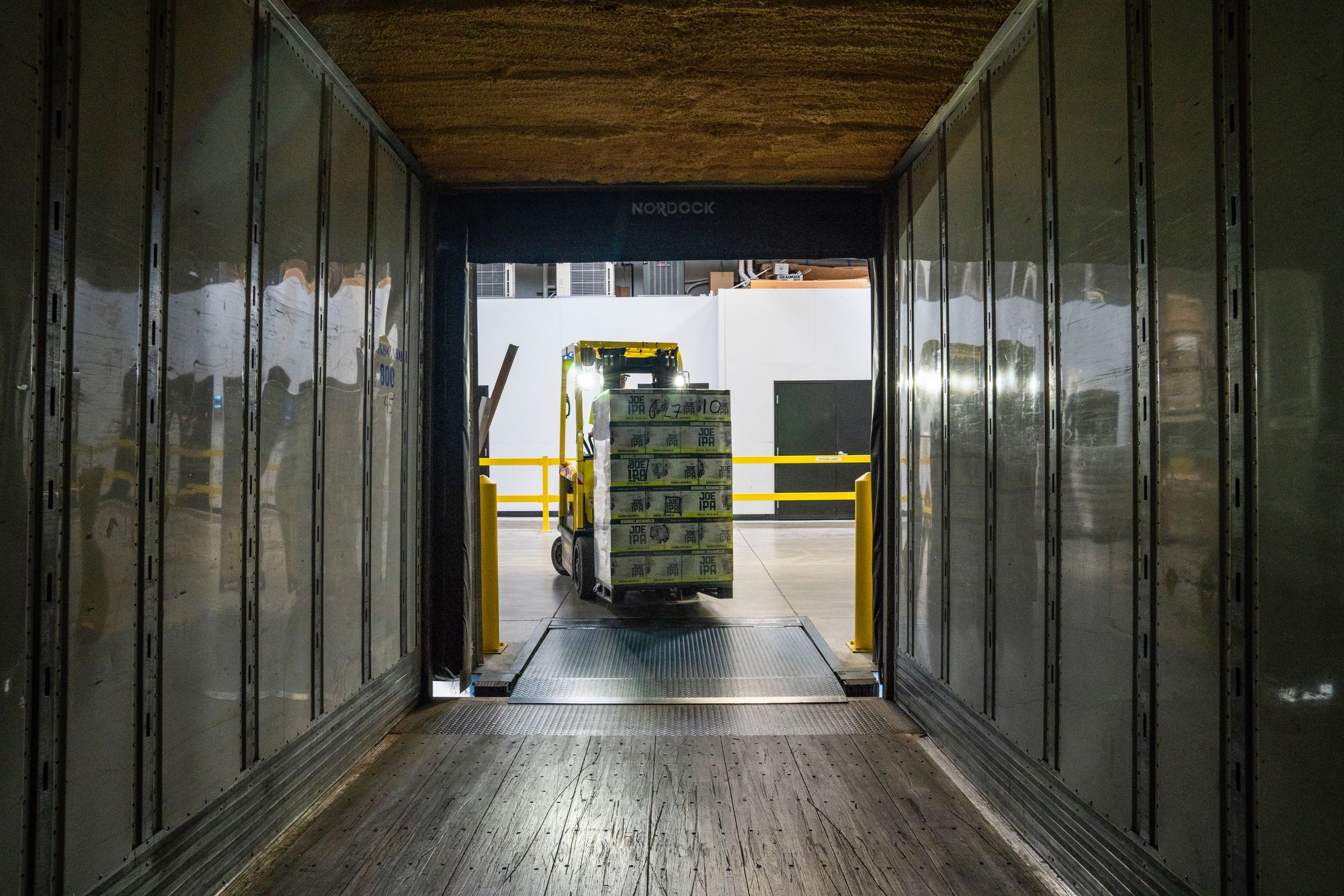
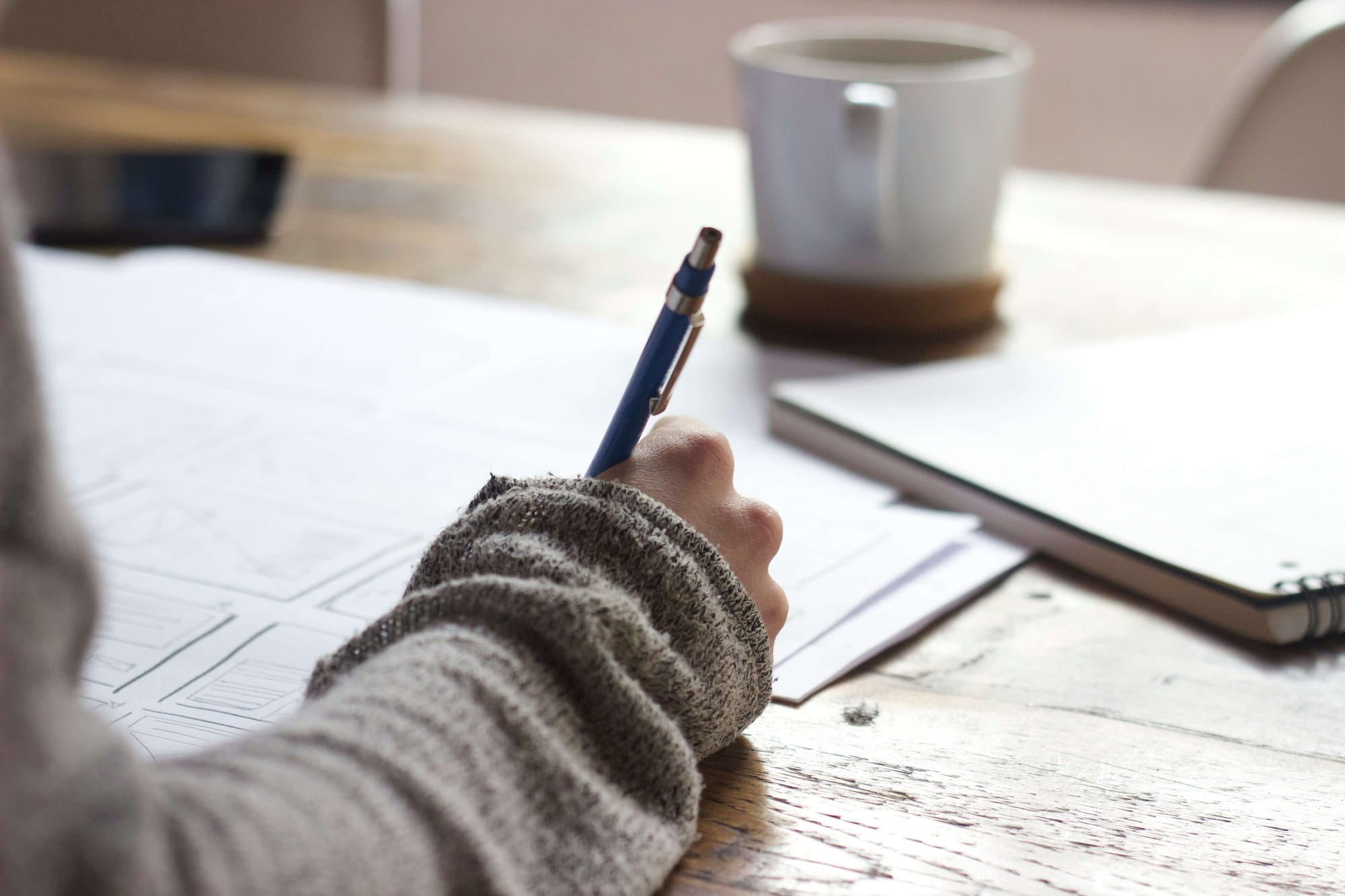
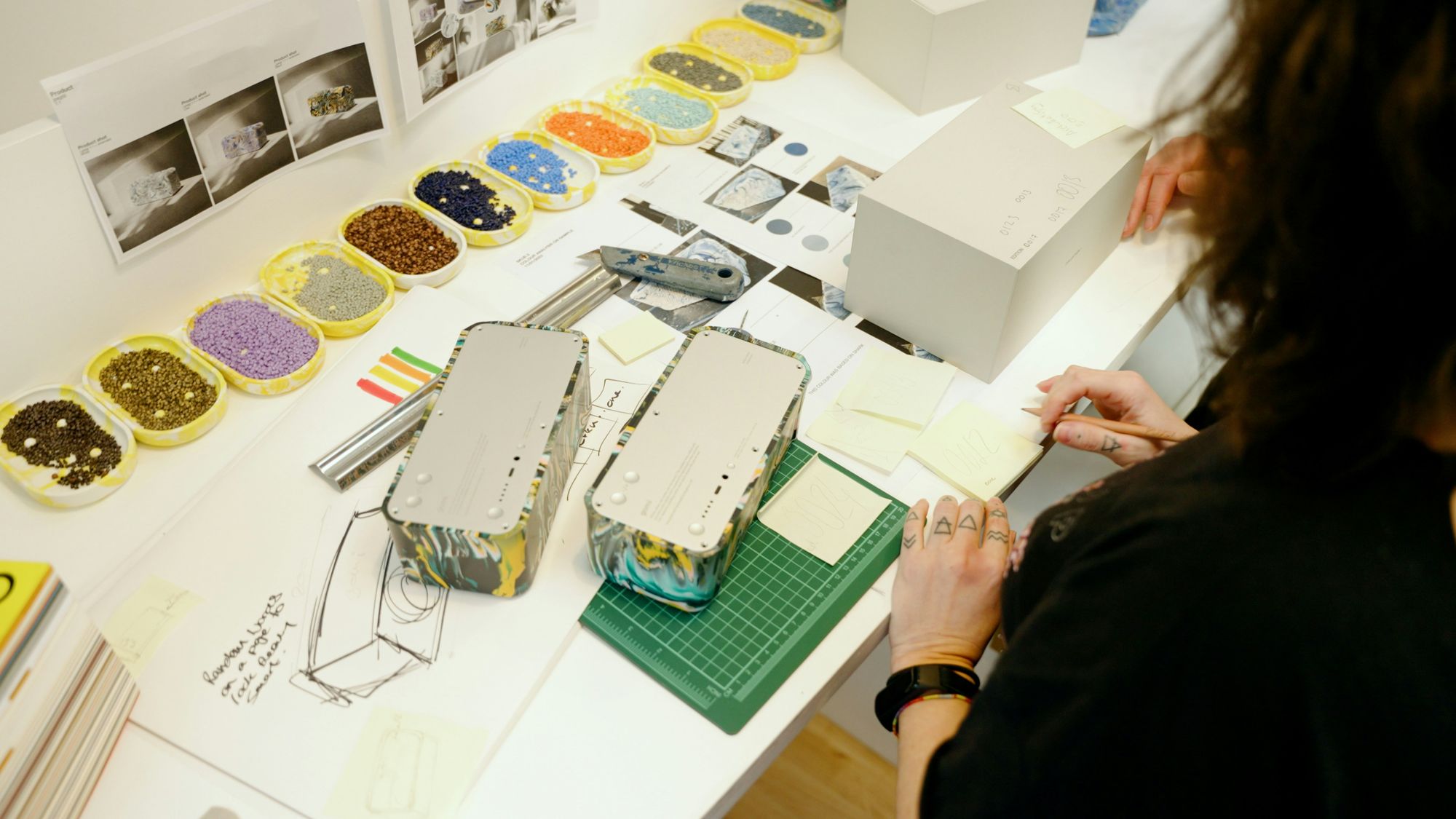
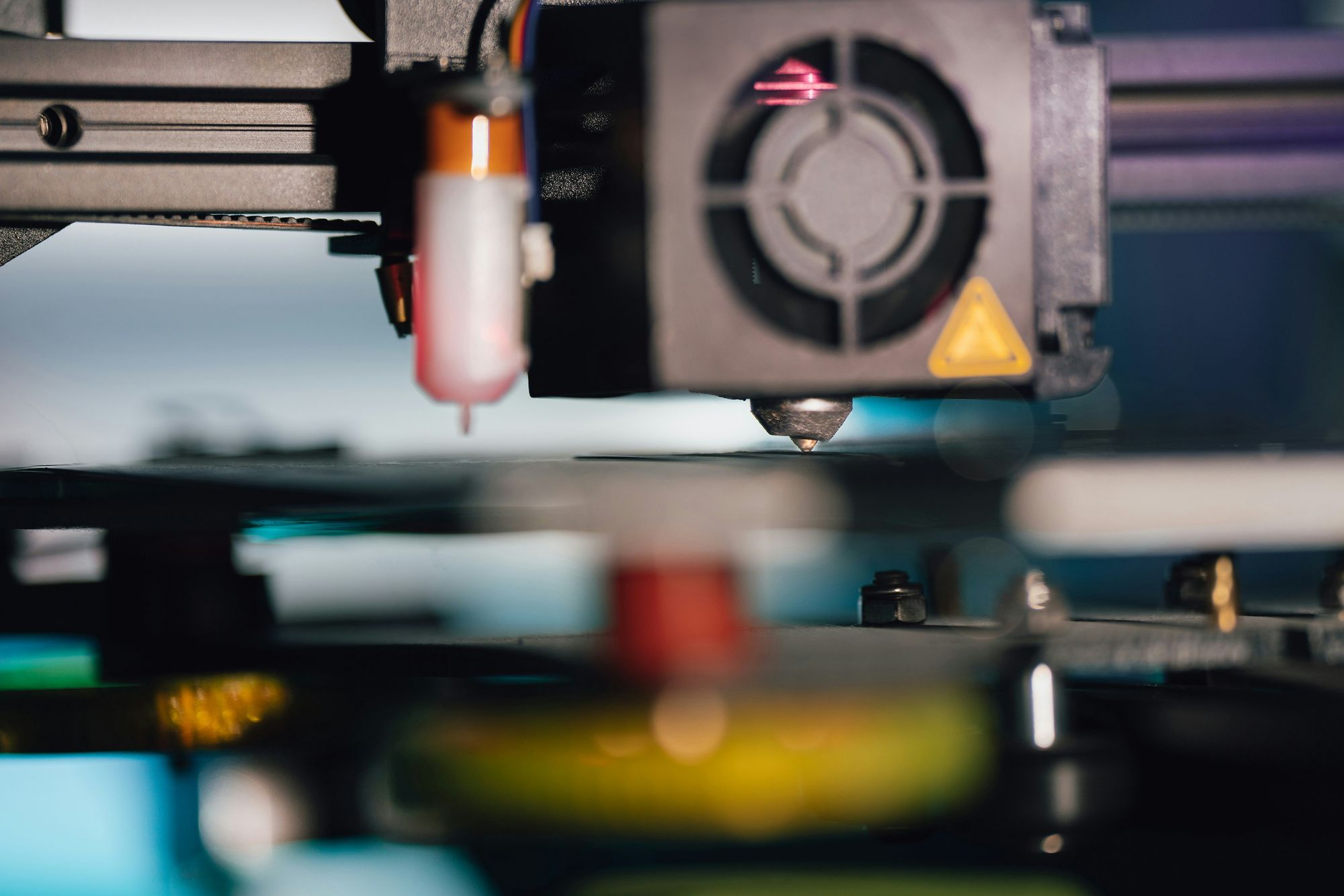
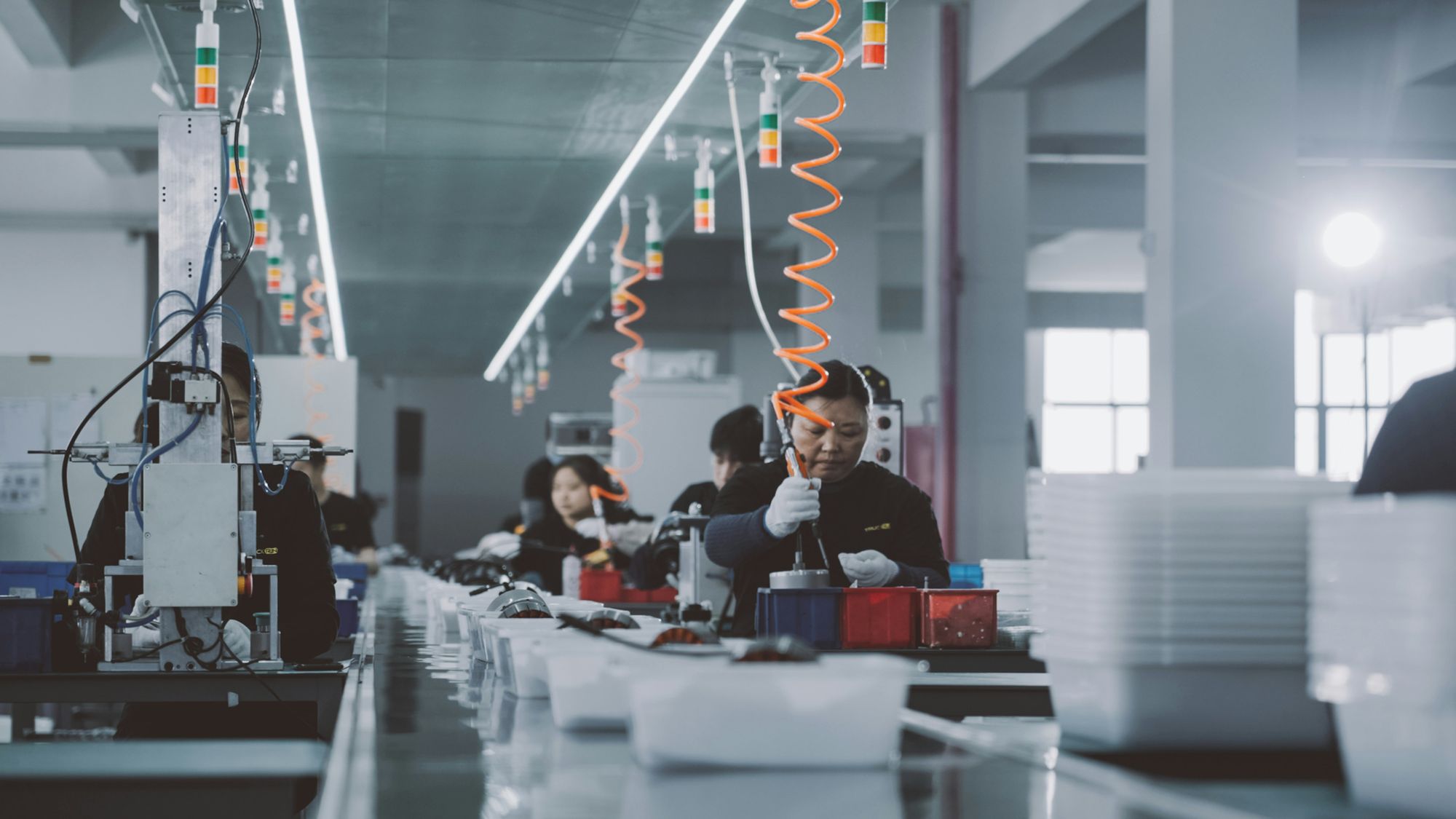