For manufacturers, having a well-thought-out manufacturing control plan is essential. It ensures a competent production planning and management.
Manufacturing control is a critical component of any successful production system. It requires careful planning and efficient processes to ensure that quality standards are met, costs are minimized, and deadlines are met. With the right strategies in place, companies can increase productivity, reduce costs, and improve customer satisfaction.
The manufacturing industry is rapidly evolving, making it increasingly difficult for companies to stay ahead of the competition. To stay competitive, manufacturers must have a comprehensive control system in place to ensure efficiency and accuracy in the production process.
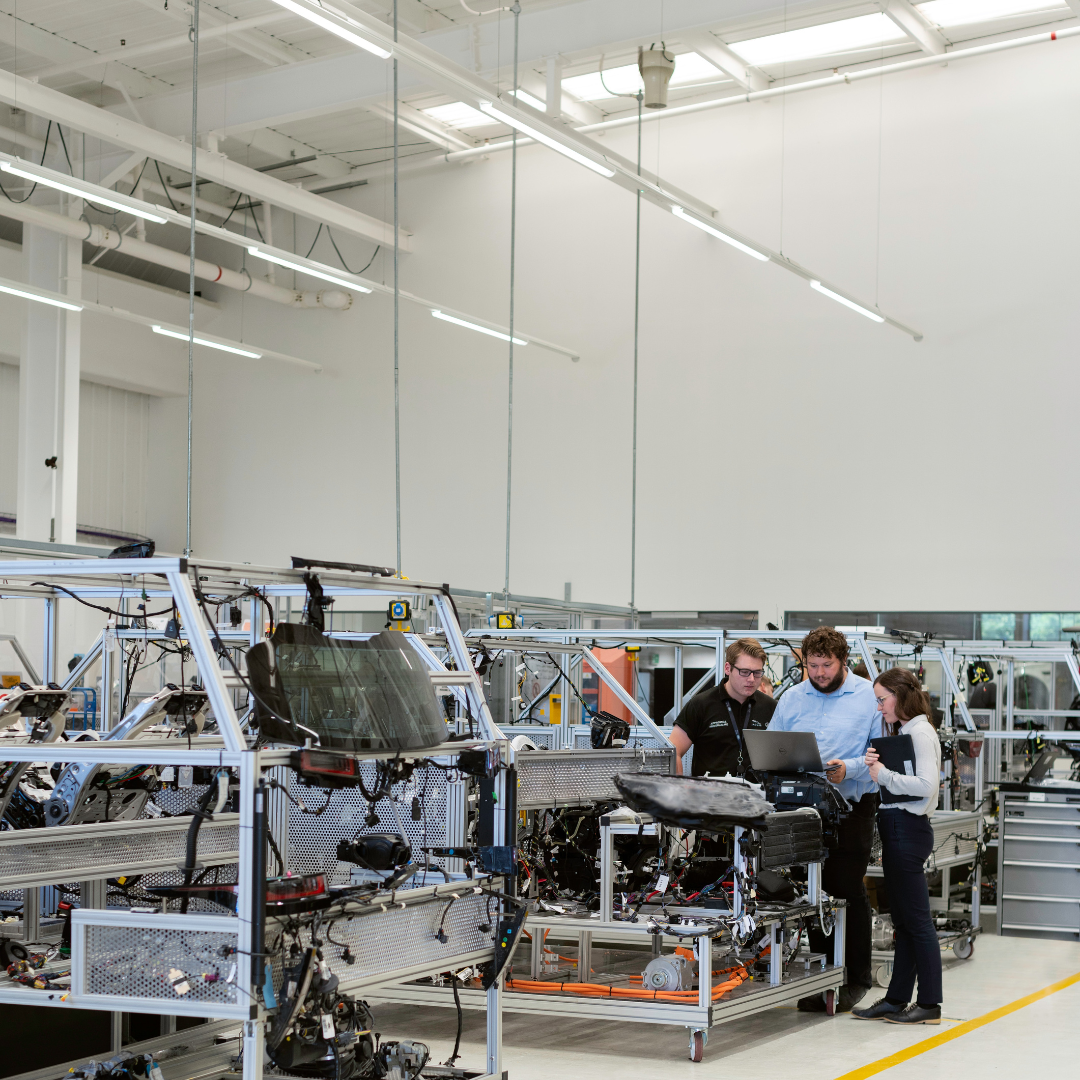
A well-designed control system can help manufacturers identify and resolve issues quickly, reduce costs, and provide better customer service. By leveraging the right tools and processes, manufacturers can create a control system that allows them to stay on top of their production operations.
This article will discuss the essential components of an effective manufacturing control system and how to implement them in your organization.
- What is Manufacturing Control?
- What is Manufacturing Control Plan?
- Benefits of Creating a Plan to Optimize Output
- Developing a Manufacturing Control Plan
- Implementing the Manufacturing Control Plan
- How can the MRP system Benefit Manufacturing Control Plan?
- Conclusion
- How can Deskera Help You?
- Key Takeaways
- Related Articles
What is Manufacturing Control?
Manufacturing control is the process of overseeing and managing the manufacturing of goods. It involves developing procedures that ensure quality and consistency across the production process. Furthermore, it involves monitoring and adjusting the process to ensure that products meet desired specifications and customer requirements.
It includes both hardware and software components for tracking, supervising, and enhancing production. The goal of manufacturing process control is to produce products that satisfy or exceed quality requirements while minimizing waste and increasing efficiency.
Manufacturers rely on various sensors, controllers, actuators, and other devices that collect data about the manufacturing process to accomplish this. This information is then analyzed in order to identify trends and issues that can be addressed in order to improve quality and efficiency.
Manufacturing control also involves tracking production costs, managing inventory, and ensuring the efficient use of resources.
4 Elements of the Manufacturing Process
The following components form the four parts of a manufacturing procedure:
- Inputs
- Controlled variables
- Uncontrolled variables
- Outputs
Inputs
Inputs in a manufacturing control plan are the resources, information, and instructions needed to complete a product or service. This includes raw materials, labor, capital, and other resources necessary for production. Additionally, the plan may include instructions for quality control and safety measures.
Controlled Variables
Controlled variables in a manufacturing control plan are the elements of a process that are kept consistent and unchanged in order to ensure the quality and consistency of the product. This includes things like temperature, pressure, humidity, and other factors that have an effect on the production process.
Uncontrolled Variables
Uncontrolled variables are factors that are not directly managed by a manufacturing control plan. These variables are outside of the plan's control, and they can have a significant impact on the outcome of the manufacturing process. Examples of uncontrolled variables include the availability of raw materials, the weather, the cost of energy, and the cost of labor.
Outputs
Outputs in a manufacturing control plan refer to the output specifications that are required to be achieved when producing a product. This typically includes the quality, quantity, and cost of the product. The control plan also outlines the necessary steps and processes that must be followed to achieve the desired output.
What is Manufacturing Control Plan?
A Manufacturing Control Plan (MCP) is a document that highlights the specific steps, processes, and requirements for manufacturing a product. It is used to ensure that the product is manufactured to meet the customer’s requirements, conforms to the relevant standards, and is produced in a safe, efficient, and cost-effective manner.
It also outlines the quality control checks and tests that will be performed to ensure the product is of high quality. The MCP is typically created by the manufacturing team and approved by the customer.
The smooth operation of the manufacturing process and compliance with all quality requirements can be ensured with the help of a well-designed control plan, which offers a clear and concise road map. Manufacturers can avoid potential issues and respond quickly if one does arise by summarizing the necessary steps.
Benefits of Creating a Control Plan to Optimize Output
There are various benefits to creating a control plan.
- Enhanced productivity: A control plan can help optimize output by setting performance targets and monitoring progress. Thus, allowing for more efficient use of resources and the realization of greater productivity.
- Improved quality: A control plan can also help ensure quality is consistently maintained. Thereby, reducing the likelihood of costly defects and increasing customer satisfaction.
- Reduced costs: By reducing waste and optimizing performance, a control plan can help reduce costs associated with production and operations.
- Enhanced competitiveness: A control plan can help a business stay competitive in the marketplace by ensuring it adheres to industry standards and practices.
- Increased flexibility: By allowing for faster responses to changing market conditions, a control plan can help a business remain agile and competitive.
- Improved communication: By providing a clear roadmap for operations, a control plan can ensure that all team members are working towards the same goals and objectives.
Developing a Manufacturing Control Plan
This section discusses the steps required in developing a manufacturing control plan. Let’s check them here:
A. Identifying Key Outputs
This is a step to developing a manufacturing control plan that involves determining what needs to be produced and in what quantity to meet the goals of the plan. This includes the product specifications, quality standards, and production deadlines that need to be completed.
It also involves considering the resources that are available for production and the potential for any bottlenecks that could cause delays. Having a clear understanding of these outputs will help to ensure that the plan is effective and efficient.
B. Establishing Objectives
This is a step that aids in developing a manufacturing control plan. It involves setting production goals and determining the criteria that should be met in order to reach those goals.
This includes determining the desired output and quality levels of the product, as well as defining the timeline for achieving the goals. Additionally, the objectives should be measurable, achievable, and realistic. This step is the basis for the rest of the plan and provides a framework for the development of the other components.
C. Assessing Resources
This step involves analyzing the resources and capabilities that the organization has access to. It includes personnel, equipment, facilities, and materials. This assessment helps the organization identify and understand the strengths and weaknesses of its resources and capabilities.
This information is then used to determine the most effective and efficient ways to achieve the goals of the manufacturing control plan.
D. Establishing Deadlines
Establishing deadlines to develop a manufacturing control plan involves setting a timeline for each step of the manufacturing process. Deadlines for each step should be realistic and attainable and should be clearly communicated to all relevant stakeholders.
This timeline should include enough flexibility to account for unexpected delays, such as the need to rework components or delays in the delivery of materials, while still allowing the overall manufacturing process to remain on track.
Implementing the Manufacturing Control Plan
The manufacturing control plan is a vital tool for organizations to ensure that the manufacturing process is efficient, cost effective and meets the required standards. It provides a framework to ensure that all activities related to the manufacturing process are properly planned and managed.
The steps for implementing the manufacturing control plan are as follows:
Establish Objectives
Being the first step, it involves setting goals for the plan and determining what needs to be accomplished. It also identifies the resources and tools needed to meet these objectives.
The objectives should be realistic and achievable and should be based on the organization’s overall goals. Develop measurable objectives and goals for the manufacturing control plan. Define the desired outcomes that will be achieved by the plan and the timeframe in which they should be achieved.
The objectives should also be measurable, so that progress can be assessed and monitored. Additionally, the objectives should be clearly communicated to all stakeholders to ensure that everyone is working towards the same goals.
Gather Data
Data gathering is a vital step in the process of implementing a manufacturing control plan. This involves collecting information from different sources, such as customer feedback, market research, and other industry sources. This helps to gain insights into the current state of the manufacturing process.
This data can then be used to make informed decisions regarding the best ways to improve the efficiency and effectiveness of the manufacturing process. Gathering data can also help identify areas of potential risk and areas that require further investigation.
By gathering data, it is possible to make informed decisions about the best course of action to take when implementing a manufacturing control plan.
Analyze Data
Analyze the data to identify areas of improvement. Identify the root causes of any issues in the manufacturing process and develop strategies to address them.
It involves looking at the data that is collected closely and evaluating it to determine how well it works for the implementation.
Develop Plan
Here, you must develop a detailed plan that outlines the steps needed to meet the objectives.
It involves creating a detailed plan that outlines the specific actions, resources, and timeline necessary to execute the plan.
This plan should include the steps required to implement the manufacturing control plan, the responsible parties, the timeline, and the resources needed. The plan should also provide details on how the plan will be monitored and evaluated to ensure that it is being implemented effectively. Also, specify the roles and responsibilities of each team member.
Set up Quality Control Procedures
Quality control procedures involve setting up a system that requires quality checks at each stage of production, from raw materials to finished products. This system should include inspections, measurements, testing, and other methods to ensure that the product meets the necessary criteria.
It should also involve corrective measures when necessary, to ensure that any products that do not meet the specified standards are identified and rectified. Quality control procedures should be documented and updated regularly in order to ensure that they remain effective.
Implement Plan
While you begin to implement your plan, training the employees and team members is essential. Provide the necessary resources to ensure the successful execution of the plan.
Once implemented, it is also vital to monitor the process and make adjustments as needed. Fine-tune your processes based on the initial requirements set for accomplishing.
Evaluate Results and Improve
Evaluate the results of the plan and identify areas for improvement. Use this feedback to refine and improve the manufacturing control plan.
How can the MRP system Benefit the Manufacturing Control plan?
A Manufacturing Control Plan (MCP) is an important document used by manufacturers to ensure that their products meet quality standards, meet customer requirements, and adhere to safety regulations. It details the process of manufacturing and the steps that need to be taken in order to produce a quality product.
An MRP system (Material Requirements Planning) can streamline the process of creating and implementing MCP. By using an MRP system, manufacturers can have all of the information they need to put together their MCP in one place.
Besides these, the MRP systems can help achieve the following:
- Track inventory levels
- Track order history
- Production schedules
- Provide real-time updates on the status of inventory and production
This makes it easier for manufacturers to plan ahead and anticipate any potential issues that may arise in the production process.
MRP systems can be used to monitor and control the production process. MRP systems can automatically adjust production schedules based on changes in inventory levels and customer demand. This helps to ensure that the production process is running efficiently and that products are being produced on time.
Conclusion
Manufacturing control can influence output by establishing and maintaining standards of quality, quantity, and cost associated with a product or service.
By implementing strategies such as developing an effective control system, cost tracking, and testing and validating processes, businesses can ensure that their production cycle runs smoothly and efficiently.
Proper use of the manufacturing control plan can help in improving the product quality and reducing costs. It helps in streamlining processes, increasing efficiency and ensuring customer satisfaction. The manufacturing control plan also provides a platform for evaluating the performance of the organization and its employees.
In conclusion, effective manufacturing control is key to a successful production process, and by implementing the right strategies, businesses can ensure that their production cycle runs efficiently and yields the desired results.
How can Deskera Help You?
Deskera MRP enables you to keep a close eye on the manufacturing process. The solution assists you in staying on top of your game and maintaining your company's competitive edge, from the bill of materials to the production planning features.

Deskera ERP and MRP system can help you:
- Manage production plans
- Maintain Bill of Materials
- Generate detailed reports
- Create a custom dashboard
Deskera Books is a tool for maintaining good accounting practices. Accounting software automates tasks like billing, invoicing, expenses, and payments.
Deskera CRM is a platform that helps you increase sales and close deals more quickly. It enables critical functions such as email lead generation, landing pages for lead generation, and excellent customer service.
Deskera People is a simple payroll automation software. From hiring, onboarding, and managing employee benefits and bonuses to leave and attendance management, the tool speeds up payroll processing.
Key Takeaways
- Manufacturing control is the process of overseeing and managing the production of goods.
- It involves developing procedures that ensure quality and consistency across the production process.
- Inputs, controlled variables, uncontrolled variables, and outputs are the 4 parts of the manufacturing process.
- A Manufacturing Control Plan (MCP) is a document that highlights the specific steps, processes, and requirements for manufacturing a product.
- It is used to ensure that the product is manufactured to meet the customer’s requirements, conforms to the relevant standards, and is produced in a safe, efficient, and cost-effective manner.
- Enhanced productivity, improved quality, and reduced costs are some of the benefits of creating a control plan.
- Developing a control plan involves steps including identifying key outputs, establishing goals, and assessing resources.
- Gathering and analyzing data marks the beginning of the implementation process of the control plan.
- An MRP system (Material Requirements Planning) can streamline the process of creating and implementing MCP. By using an MRP system, manufacturers can have all of the information they need to put together their MCP in one place.
Related Articles
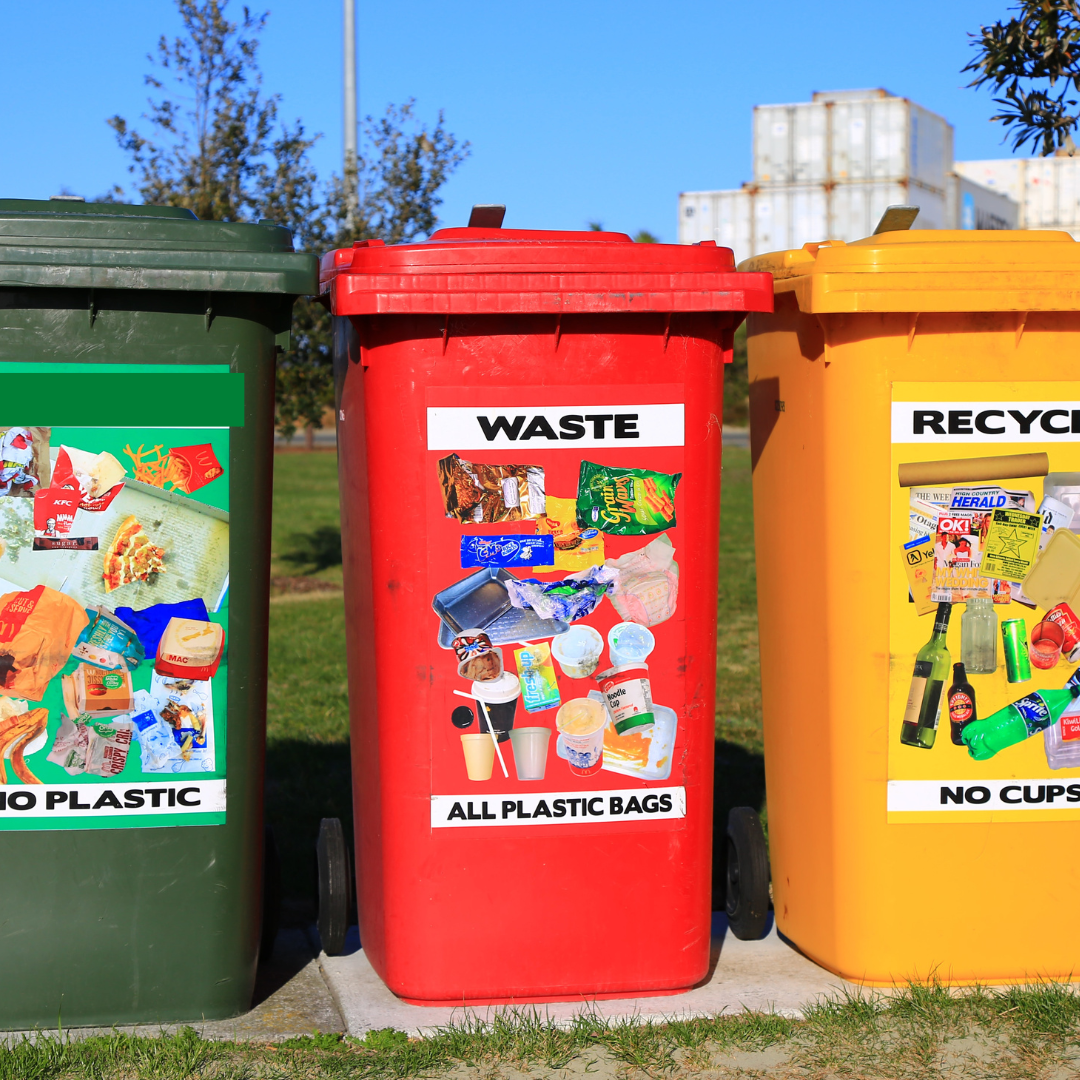
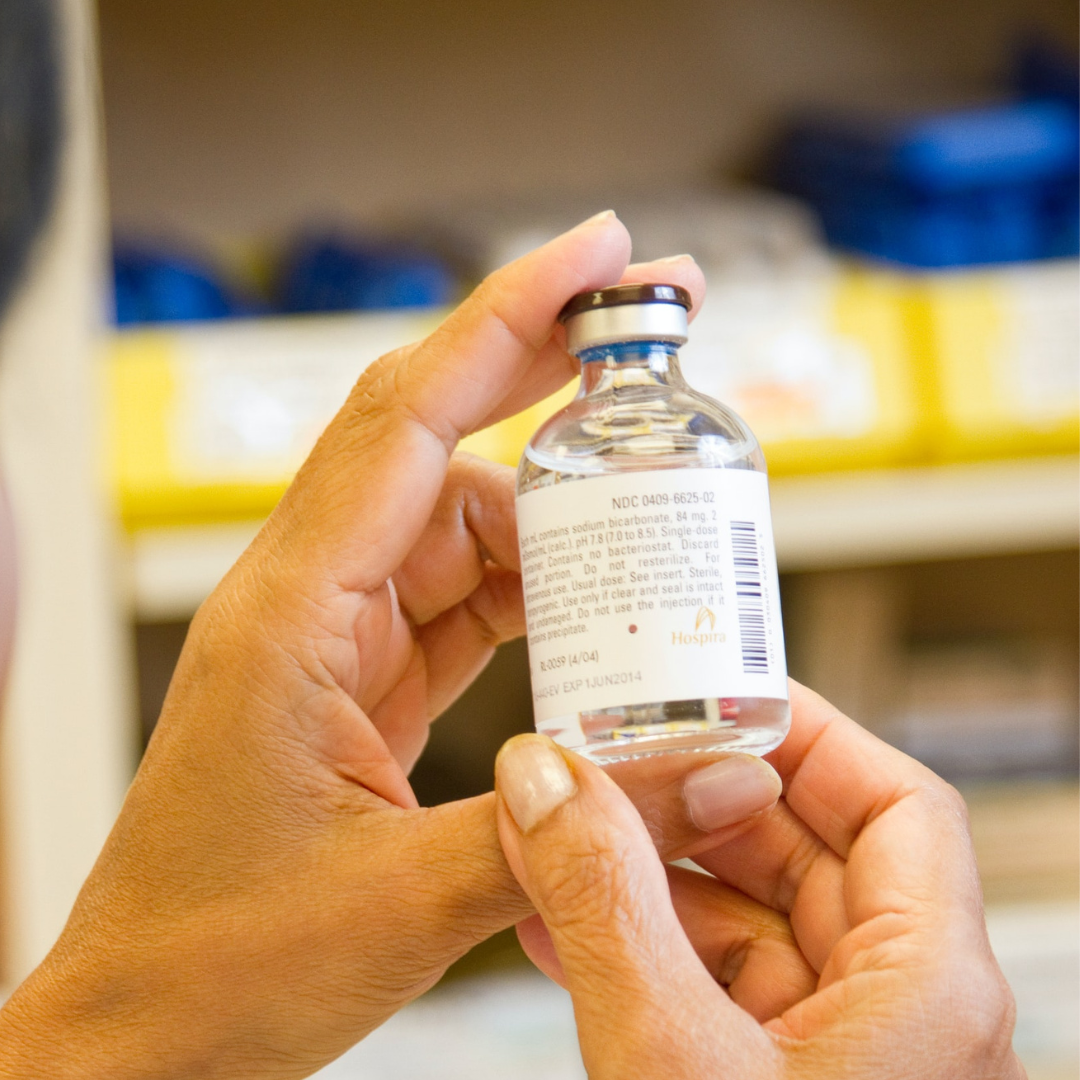
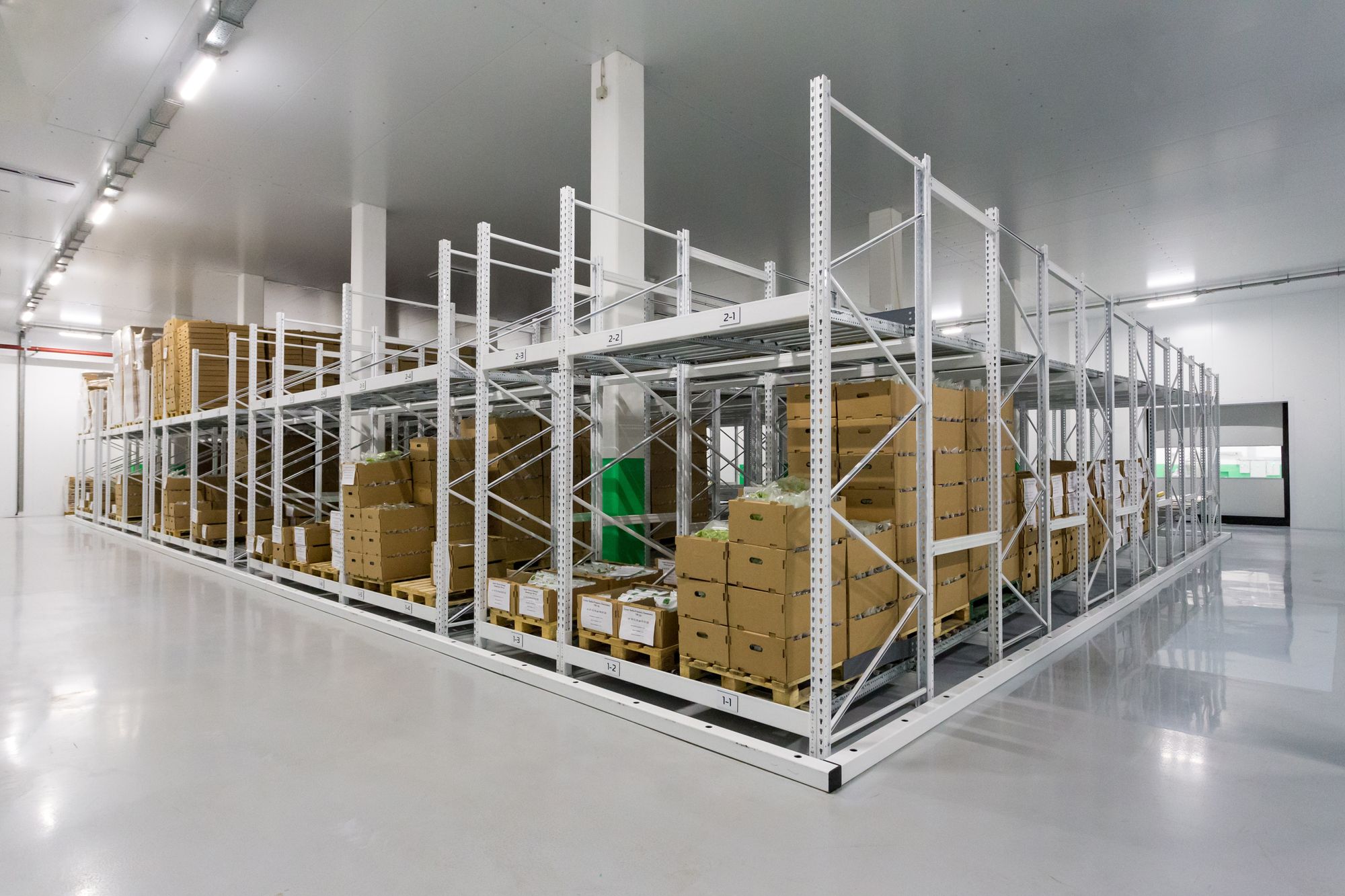
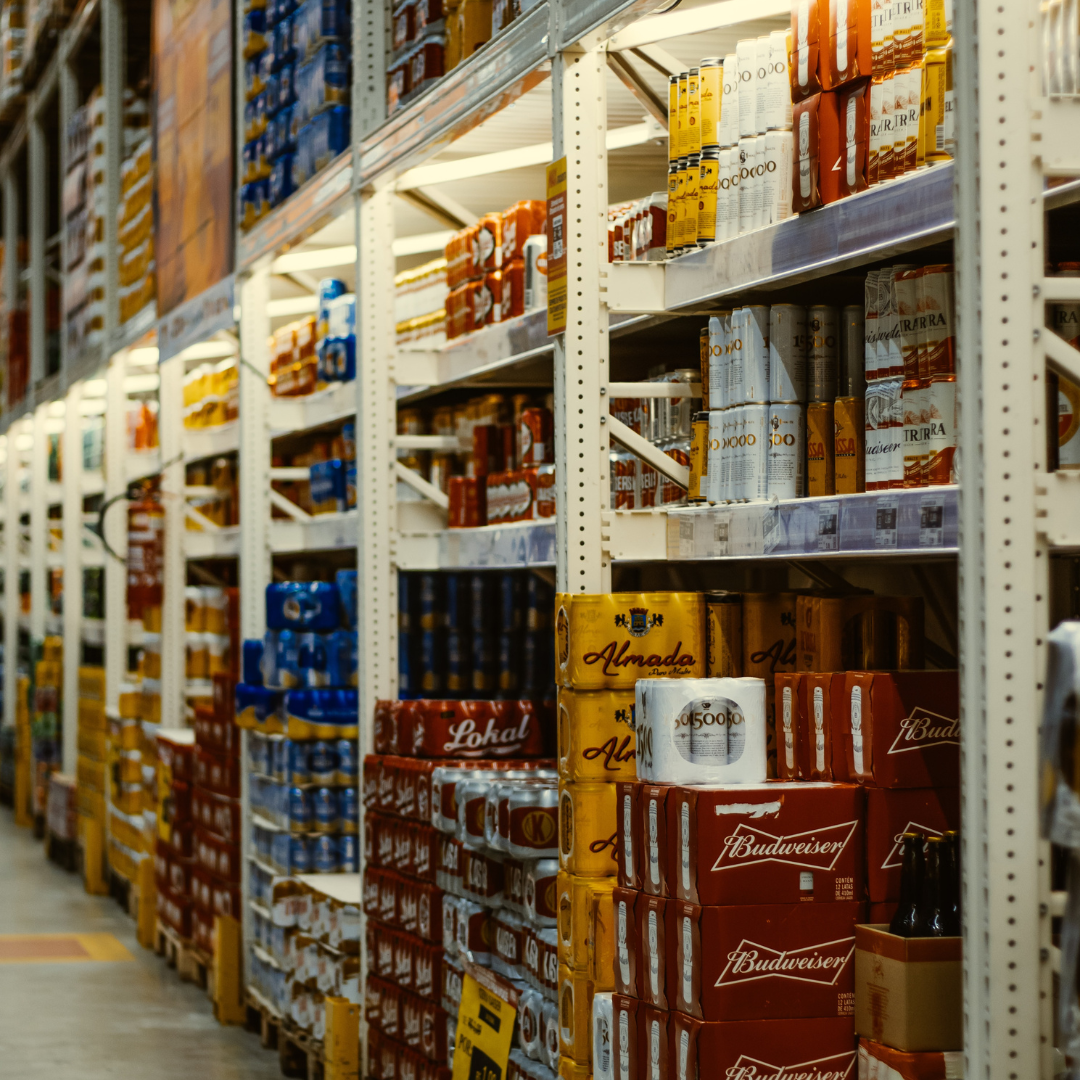