In 2020, manufacturing operations faced a number of challenges due to the COVID-19 pandemic, including supply chain disruptions, labor shortages, and decreased demand. Furthermore, according to a survey conducted by the National Association of Manufacturers, the top three challenges facing manufacturers in 2020 were: workforce availability, supply chain disruptions, and operating costs.
Manufacturing is a critical component of the global economy and presents many challenges to businesses. Companies must navigate a complex landscape of regulatory compliance, cost containment, and quality assurance. They must also keep up with rapidly changing technology, emerging markets, and new customer demands.
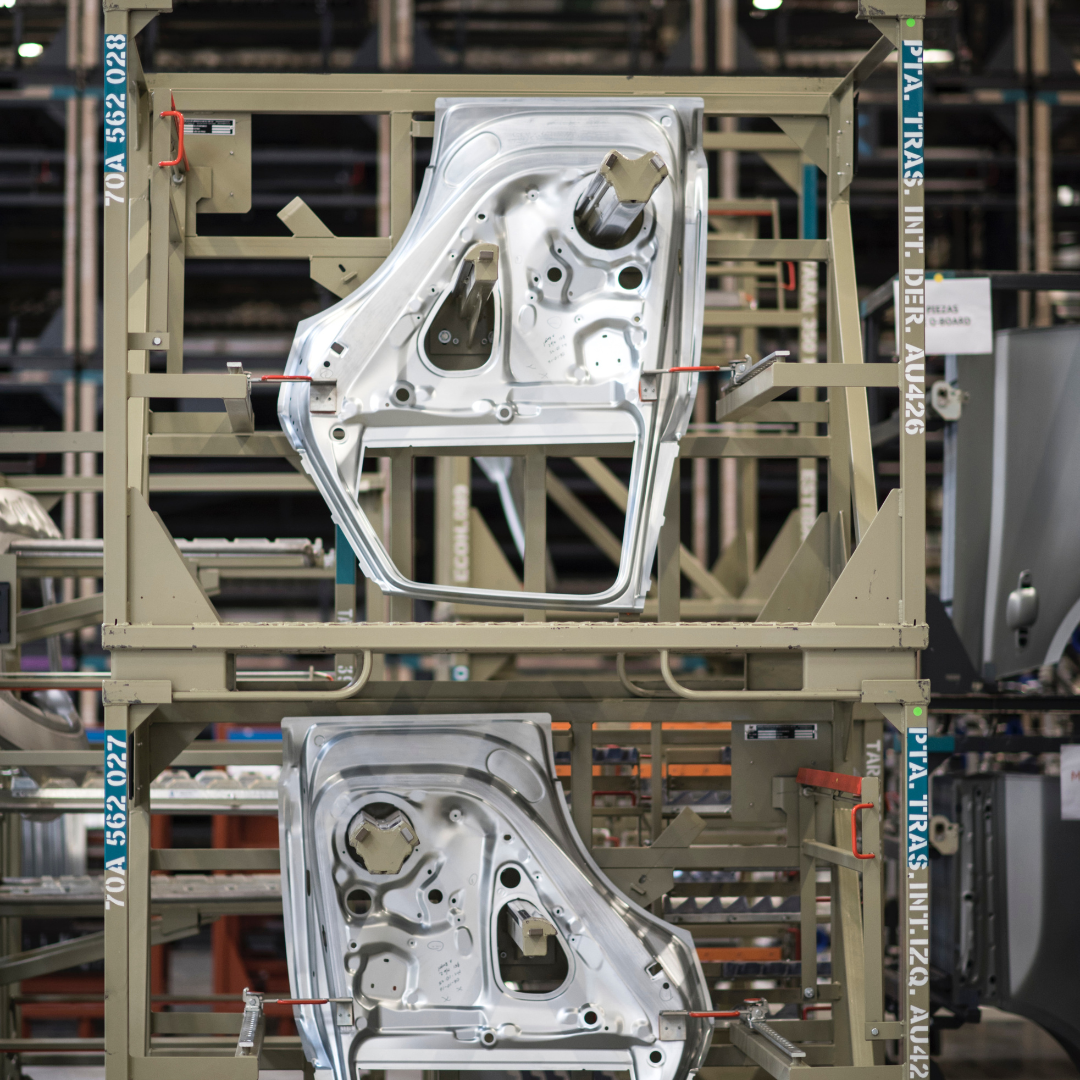
This article will explore some of the most common manufacturing challenges and discuss strategies for overcoming them.
- Definition of Manufacturing Challenges
- Overview of the Manufacturing Industry
- Types of Manufacturing Challenges
- Economic Challenges
- Regulatory Challenges
- Technological Challenges
- The Impact of Manufacturing Challenges
- How do Manufacturing Challenges Affect Businesses?
- 5 Effects of Manufacturing Challenges on Consumers
- Strategies for Overcoming Manufacturing Challenges
- Cost Reduction Strategies
- Improved Processes
- Automation
- Summary of Manufacturing Challenges
- Conclusion
- How can Deskera Help You?
- Key Takeaways
- Related Articles
Definition of Manufacturing Challenges
Manufacturing challenges refer to any issues or difficulties encountered during the production of goods or services. These issues may include long lead times, high costs, insufficient resources, outdated technology, inadequate facilities, or inefficient processes.
Manufacturing challenges can arise from various sources, such as supplier problems, customer demands, or changing market conditions. It is important for organizations to identify and address these challenges to ensure the successful production of goods and services.
Overview of the Manufacturing Industry
Manufacturing is an integral part of the global economy and is responsible for the production of a vast array of products. These range from basic necessities such as food, clothing, and shelter to luxuries such as electronics and automobiles.
As such, it plays a major role in economic and social development, creating employment opportunities, producing goods for export, and providing the resources needed for a thriving market. Manufacturing is often seen as a key driver of economic growth, and many countries rely heavily on it to boost their economies.
The global manufacturing industry is a large and complex sector with a wide range of sub-industries and activities. It can be broadly divided into three main categories: primary, secondary, and tertiary manufacturing.
- Primary manufacturing involves the production of raw materials such as steel, glass, timber, and plastics.
- Secondary manufacturing involves the transformation of these materials into usable products.
- Tertiary manufacturing involves the final assembly of the products and their packaging for sale.
The global manufacturing industry has seen significant growth over recent years. In 2018, global manufacturing output was estimated to be worth $11.14 trillion, up from $9.99 trillion in 2017 and $8.93 trillion in 2016. This growth has been driven by a number of factors, including technological advances, increased global trade, and the emergence of new markets.
The largest manufacturing countries in the world are the United States, China, Japan, Germany, South Korea, and India. These countries account for the majority of the world’s manufacturing output, with China alone accounting for nearly a quarter (24.5%) of the world’s total manufacturing output in 2018. The United States is the second largest manufacturer, accounting for 15.4% of the world’s total manufacturing output in 2018.
Technology has played a major role in the growth of the manufacturing industry. Automation, robotics, and 3D printing have enabled manufacturers to reduce costs, increase efficiency and improve product quality. In addition, the internet has allowed manufacturers to access new markets and customers, while the use of Big Data has enabled them to gain insights into customer preferences and trends in order to better predict demand and develop new products.
The global manufacturing industry is also increasingly reliant on global supply chains. Many companies are relying on overseas suppliers to produce components of their products, while others are outsourcing production to countries with lower labor costs. This has enabled them to reduce costs and increase their competitiveness.
Types of Manufacturing Challenges
There are several types of manufacturing challenges, including cost-related issues, quality control issues, and supply chain challenges. Cost-related challenges include rising material costs, labor costs, and energy costs.
Quality control issues include maintaining consistent product quality, meeting customer specifications, and implementing quality assurance standards. Supply chain challenges include managing lead times, maintaining inventory levels, and dealing with supply chain disruptions.
Additionally, manufacturers must also contend with environmental issues, such as environmental regulations, waste management, and sustainability initiatives.
Finally, manufacturers must also remain competitive in a global marketplace, as well as keep up with technological advancements. This includes investing in new equipment and processes, implementing automation, and researching new ways to improve product design and production.
Let’s look at some of the common challenges here:
- Capacity Planning Challenges: Capacity planning is the process of determining the production capacity needed by an organization to meet changing demands for its products. It involves forecasting demand, analyzing capacity, and making decisions about investments in equipment, facilities, and personnel.
- Quality Control Challenges: Quality control is the process of ensuring that products and services meet certain standards of quality. Quality control systems are designed to detect defects and prevent them from being released into the marketplace.
- Cost Reduction Challenges: Cost reduction is the process of identifying and eliminating unnecessary costs in order to increase profits. Cost reduction initiatives can include streamlining production processes, reducing waste, and outsourcing certain activities.
- Supply Chain Management Challenges: Supply chain management is the process of managing and coordinating the flow of materials and information between suppliers, manufacturers, distributors, and customers. It includes activities such as inventory management, order fulfillment, and transportation.
- Automation Challenges: Automation is the use of technology to automate processes and reduce labor costs. Automation can involve complex systems, such as robotics, or simpler processes, such as automated production lines.
Economic Challenges
There are multiple economic challenges that manufacturing faces today. Let’s check them here.
- Rising labor costs: As wages and benefits rise, manufacturing companies must find ways to manage the increasing costs of labor. This can be a challenge for companies that rely heavily on manual labor.
- Global competition: Manufacturers are increasingly facing competition from countries with cheaper labor costs, such as China and India. This can put pressure on prices and profits and make it difficult for companies to remain competitive.
- Increasing material costs: The cost of raw materials can be volatile, making it difficult to budget accurately and plan for production.
- Technology adoption: Companies must continually invest in new technology to remain competitive, which can be expensive.
- Supply chain complexity: With global competition, manufacturers must be able to manage increasingly complex supply chains. They must have the ability to source materials from multiple countries and manage the logistics of shipping and customs.
Regulatory Challenges
Regulatory challenges in manufacturing can include the following:
- Ensuring compliance with environmental regulations, such as hazardous waste disposal, air and water pollution control, and energy efficiency.
- Meeting stringent safety standards and protocols, such as OSHA regulations and other applicable standards.
- Adhering to quality control standards, such as ISO 9000 and other industry-specific certifications.
- Ensuring compliance with labor laws, such as minimum wage, overtime, and employee classification laws.
- Keeping up with changes in the regulatory landscape, such as new laws and regulations or changes to existing laws and regulations.
- Ensuring compliance with industry-specific regulations, such as for food and beverage production, automotive production, and pharmaceutical production.
Technological Challenges
The technological challenges in manufacturing can be summed up as follows:
- Automation: Automation is a major challenge for manufacturers, as it requires a substantial investment of resources and time to implement. Automated processes can increase efficiency and reduce costs but require careful planning and implementation.
- Quality Control: Quality control is an important part of the manufacturing process and is essential to ensuring consistent quality products. Quality control involves designing and implementing processes to ensure that products meet customer requirements and are free from defects.
- Data Management: Manufacturers must manage vast amounts of data related to production, materials, customers, and more. This data must be collected, stored, and used in a timely and efficient manner to maximize efficiency and ensure accuracy.
- Supply Chain: Managing a complex and global supply chain is a major challenge for manufacturers. Supply chain issues can lead to delays in production, increased costs, and reduced customer satisfaction.
- Cybersecurity: With the increasing prevalence of cyber attacks, manufacturers must take steps to ensure their systems and data are secure. This includes implementing strong security policies and procedures, training employees, and investing in the right technology and hardware.
The Impact of Manufacturing Challenges
Manufacturing challenges can have a wide range of impacts on businesses. This can include decreased production, increased costs, delays in deliveries, and decreased customer satisfaction. Additionally, manufacturing challenges can lead to a decrease in profit margins and a decrease in market share.
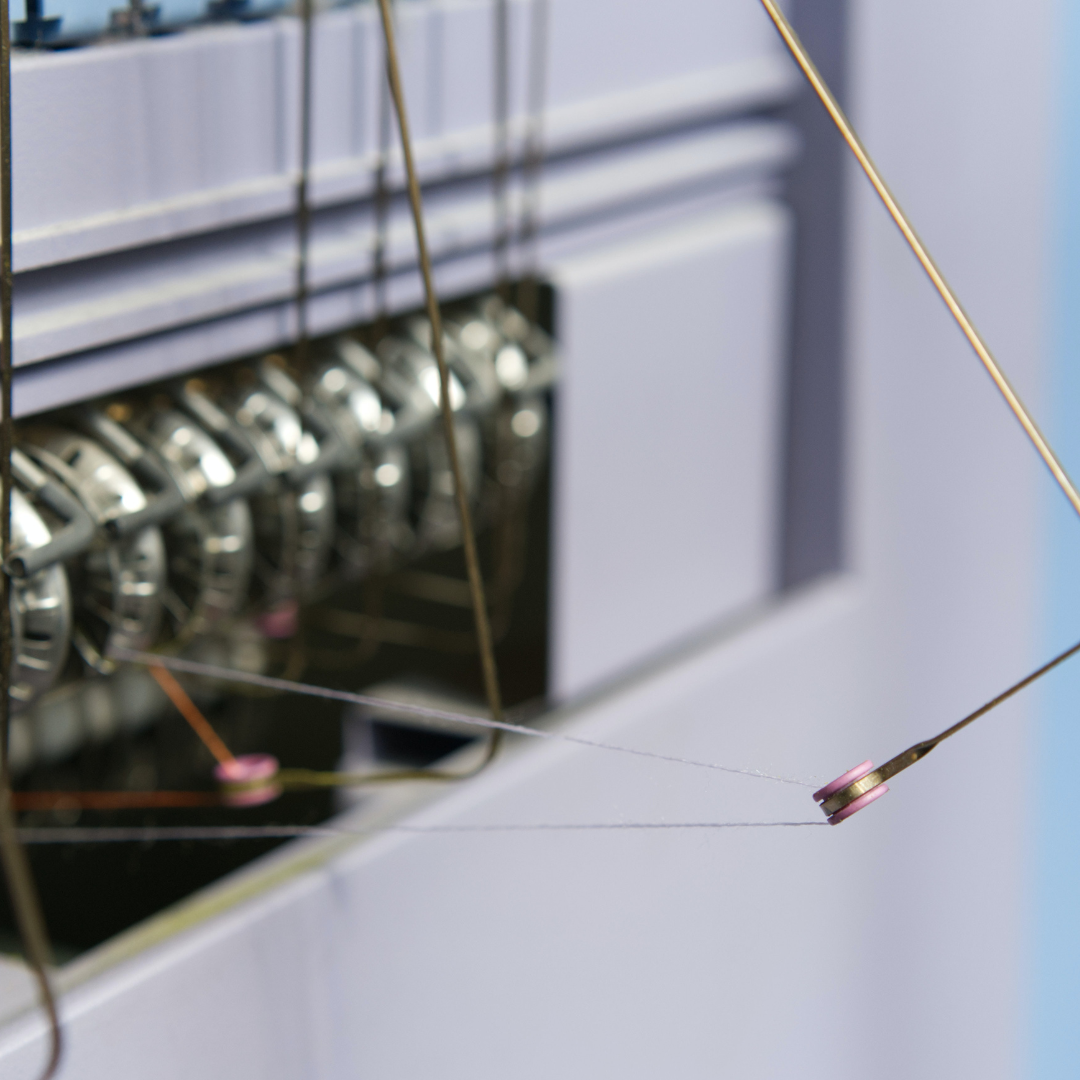
Manufacturing challenges can also lead to a decrease in brand reputation and customer loyalty. Ultimately, manufacturing challenges can have a negative impact on a business, leading to decreased revenue and decreased competitiveness in the marketplace.
- Increased Costs: Manufacturing challenges can lead to increased costs due to the need for additional resources, labor, and materials to produce a product. This can lead to higher prices for the end consumer.
- Reduced Quality: Manufacturing challenges can lead to lower-quality products due to inferior materials, processes, or techniques used. This can lead to customer dissatisfaction and a negative reputation for the company.
- Delayed Deliveries: Manufacturing challenges can lead to delays in delivering products to customers due to the need to fix any issues or make changes to the product. This can lead to a negative customer experience.
- Lost Revenue: Manufacturing challenges can lead to a loss of potential revenue due to the need to spend more time and resources to correct any issues. This can lead to a decrease in profits.
- Lower Productivity: Manufacturing challenges can lead to a decrease in productivity due to the need to fix any issues or make changes to the product. This can lead to a decrease in output.
- Safety Concerns: Manufacturing challenges can lead to safety concerns due to inferior materials or processes used. This can put workers at risk and can lead to costly legal issues.
- Environmental Impact: Manufacturing challenges can lead to an increased environmental impact due to the need to fix any issues or make changes to the product. This can lead to higher carbon emissions and pollution.
- Lack of Innovation: Manufacturing challenges can lead to a lack of innovation due to the need to fix any issues or make changes to the product. This can lead to a decrease in new products and services.
How do Manufacturing Challenges Affect Businesses?
Manufacturing challenges can have a significant effect on businesses, both negatively and positively.
On the negative side, manufacturing challenges can lead to higher production costs, lower quality products, delays in delivery, and customer dissatisfaction. These can all lead to decreased profits, decreased sales, and a negative impact on the company’s reputation.
On the positive side, companies can use the challenges to their advantage by developing innovative solutions that improve their competitive edge.
Here is how we can sum up the effects on businesses:
1. Increased costs: Manufacturing challenges can lead to increased costs due to delays, damage, defects, and other issues. This can lead to decreased profits and higher prices for customers.
2. Quality problems: Poor quality control can lead to customer dissatisfaction and a negative reputation for the business.
3. Waste: Poorly managed production processes can lead to excessive waste and inefficiency. This leads to increased costs and lost profits.
4. Risk: Manufacturing challenges can lead to increased risk of liability and legal action.
5. Time: Manufacturing challenges can lead to delays in production, which can lead to missed deadlines and lost opportunities.
5 Effects of Manufacturing Challenges on Consumers
Like companies, consumers, too, get affected by the manufacturing challenges. From raised prices to decreased quality, there are multiple hassles the consumers may face.
- Higher Prices: Many manufacturing challenges, such as lack of raw materials, inadequate infrastructure, and labor shortages, can lead to higher costs of production, which can be passed on to consumers through higher prices.
- Poor Quality Products: When manufacturers are unable to produce quality goods due to a lack of resources, the products available to consumers may be of lower quality than expected or desired.
- Longer Delivery Times: Manufacturing challenges such as labor shortages, supply chain disruptions, and limited production capacity can lead to longer lead times and delayed deliveries.
- Limited Product Selection: When manufacturers are unable to keep up with consumer demand due to limited production capacity or lack of resources, the selection of products available to consumers may be limited.
- Disruption in Services: When manufacturers experience disruption in their production processes, it can lead to disruption in services and products as well. This can lead to inconvenience, disappointment, and frustration for consumers.
Strategies for Overcoming Manufacturing Challenges
Companies can draw a variety of strategies for overcoming manufacturing challenges. Let’s see what these strategies are.
- Improve Collaboration: Improving collaboration between the different departments within your manufacturing organization can help identify and address potential issues. Utilize tools such as videoconferencing, project management software, and enterprise resource planning (ERP) systems to facilitate better communication and collaboration.
- Automate Processes: Automating processes can help reduce or eliminate manual errors and streamline production. Implementing robotic systems, automated inspection systems, and other automation solutions can help increase efficiency and reduce waste.
- Utilize Data Analytics: Data analytics can help identify areas for improvement and increase visibility into production processes. Leveraging data analytics to identify trends, refine processes, and optimize operations can help improve the efficiency of your manufacturing operations.
- Invest in Training: Investing in training for your staff can help to ensure that they have the skills and knowledge they need to perform their jobs effectively. Investing in professional development opportunities can also help to reduce turnover and build a more skilled and engaged workforce.
- Adopt Lean Manufacturing Practices: Lean manufacturing is a system of production that seeks to eliminate waste and optimize production. Adopting lean manufacturing principles can help reduce costs, increase efficiency, and improve quality.
- Invest in Quality Control: Investing in quality control measures can help ensure that your products meet customer expectations and regulatory requirements. Utilizing tools such as statistical process control (SPC) and design of experiments (DOE) can help to reduce defects and improve product quality.
Cost Reduction Strategies
When businesses are looking to fight challenges, cost reduction can be a good starting point. But how do they go about it? What are the ways in which they can lower the costs of manufacturing processes?
The following factors can help them out.
- Automate processes: Automating processes can help reduce costs by reducing labor costs and increasing efficiency.
- Reduce energy consumption: Reducing energy consumption can help reduce costs by reducing utility bills.
- Re-evaluate suppliers: Evaluating suppliers can help reduce costs by finding better prices and terms.
- Outsource non-essential tasks: Outsourcing non-essential tasks can help reduce costs by allowing the business to focus on core processes.
- Implement Lean Manufacturing principles: Lean Manufacturing principles can help reduce costs by eliminating waste and increasing efficiency.
- Utilize technology: Technology can help reduce costs by increasing efficiency and reducing manual processes.
- Relocate production: Relocating production can help reduce costs by taking advantage of lower labor costs in other countries.
- Reduce inventory: Reducing inventory can help reduce costs by reducing overhead and storage costs.
- Negotiate with vendors: Negotiating with vendors can help reduce costs by getting better prices and terms.
- Increase production yields: Increasing production yields can help reduce costs by reducing waste and increasing efficiency.
Improved Processes
Improved processes help manufacturing businesses by providing more efficient and cost-effective ways of manufacturing products. They lead to increased productivity, higher quality products, lower costs, and enhanced customer satisfaction.
Improved processes also enable businesses to compete better in the marketplace, as well as create new opportunities for expansion and innovation. Improved processes also help businesses improve their environmental sustainability and reduce their carbon footprint.
Increased Efficiency
Improved processes and strategies can help manufacturing businesses increase their efficiency by reducing waste and maximizing resources. This can lead to higher productivity, improved quality, and cost savings.
Improved Quality
By streamlining processes and implementing best practices, manufacturers can reduce defects and ensure that the products they produce are of the highest quality. This can help to strengthen customer relationships and improve the reputation of the business.
Faster Time to Market
Improved processes and strategies can help manufacturers reduce their time to market. This can help them to better meet customer needs and remain competitive in their industry.
Improved Employee Satisfaction
By streamlining processes, manufacturers can reduce tedious or repetitive tasks and create a more enjoyable and productive work environment. This can lead to increased employee satisfaction, which can have a positive impact on the business.
Higher Profitability
By improving processes and strategies, manufacturers can reduce costs and improve quality, leading to higher profitability. This can help the business to invest in new technologies, expand operations, and create new jobs.
Automation
A powerful tool like automation can be helpful in manufacturing by increasing efficiency and accuracy, reducing labor costs, improving quality, and reducing waste. It can also help to improve safety by reducing the need for human workers to work in hazardous environments. Automation can also help to streamline processes and reduce cycle times, allowing for faster production.
Summary of Manufacturing Challenges
Let’s walk through the summary of manufacturing challenges as discussed in this article.
Conclusion
The manufacturing industry has been rocked by unprecedented challenges in recent years. These challenges, such as increased competition, increased customer expectations, and the need to become more agile and efficient, are not easily overcome. However, with the right strategies and solutions, manufacturers can successfully overcome these challenges and thrive in today’s volatile business environment.
By leveraging technology, such as automation and analytics, manufacturers can become more efficient and flexible. Additionally, by optimizing their supply chain, manufacturers can reduce costs and improve their responsiveness to customer needs. Finally, by improving their product development process, manufacturers can ensure they are creating products that meet the changing needs of their customers.
These strategies can help manufacturers overcome the challenges they face and remain successful in the current market. By implementing the right strategies and solutions, manufacturers can become more agile, efficient, and cost-effective. This will allow them to compete and thrive in today’s ever-changing business environment.
How can Deskera Help You?
Deskera can help companies overcome manufacturing challenges by providing a comprehensive suite of software solutions, such as ERP, CRM, eCommerce, and more.
These solutions can help streamline production processes, automate inventory management and tracking, and provide real-time visibility into operations. Deskera can also help companies increase operational efficiency, reduce operational costs, and improve customer service.
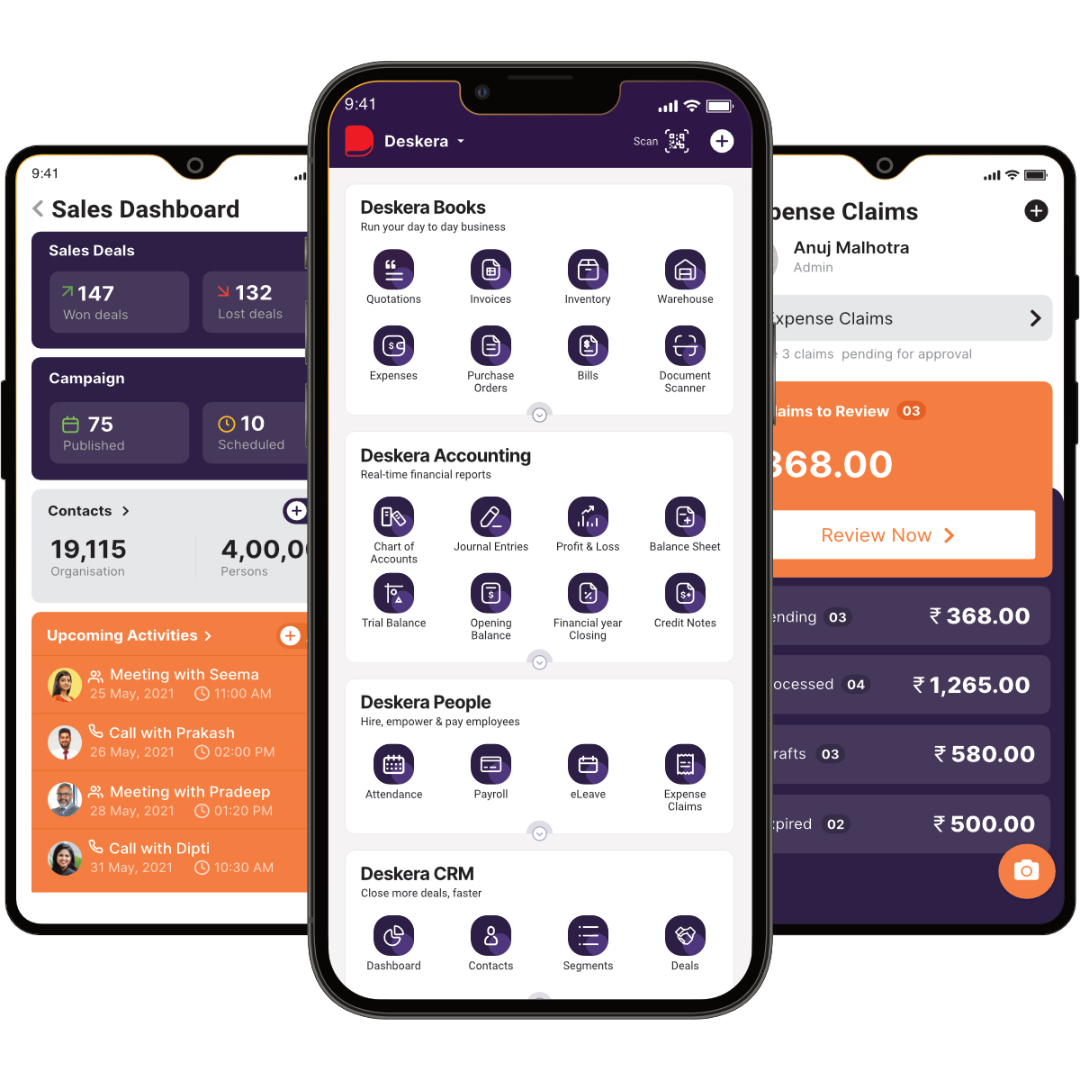
Here are some of the ways Deskera ERP and MRP systems can help you:
- Make a manufacturing schedule
- Maintain a Bill of Materials
- Produce detailed reports
- Create your own dashboard, among other things!
Deskera Books is accounting software that can help streamline business operations. It provides features such as invoicing, financial reporting, and bookkeeping, allowing businesses to save time and money. It also offers inventory management and payroll services, helping businesses manage their finances more effectively.
Deskera CRM helps businesses manage their customer relationships and streamline their sales processes. It provides features such as contact and lead management, automation of sales processes, customer support, and reporting.
Deskera People can help streamline HR processes such as payroll, onboarding, leave management, and performance reviews. It can also help with recruiting, training and development, employee engagement, and analytics.
Key Takeaways
- Manufacturing is a critical component of the global economy, and it presents many challenges to businesses.
- Companies must navigate a complex landscape of regulatory compliance, cost containment, and quality assurance.
- Manufacturing challenges refer to any issues or difficulties encountered during the production of goods or services.
- These issues may include long lead times, high costs, insufficient resources, outdated technology, inadequate facilities, or inefficient processes.
- Capacity planning is the process of determining the production capacity needed by an organization to meet changing demands for its products.
- Quality control is the process of ensuring that products and services meet certain standards of quality.
- Cost reduction is the process of identifying and eliminating unnecessary costs in order to increase profits.
- Supply chain management is the process of managing and coordinating the flow of materials and information between suppliers, manufacturers, distributors, and customers.
- Automation is the use of technology to automate processes and reduce labor costs.
- Rising labor costs, global competition, and supply chain complexity are some of the economic challenges for companies.
- Compliance, labor laws, industry-specific regulations are some of the regulatory challenges.
- Quality control and automation are some of the technological challenges for companies.
- Companies often faces hurdles like increased costs, reduced quality, delayed deliveries as the impact of challenges.
- Improving collaboration, automating processes, and investing in training are some ways in which companies can overcome manufacturing challenges.
- Automation and improved processes can be instrumental in overcoming various challenges in manufacturing.
Related Articles
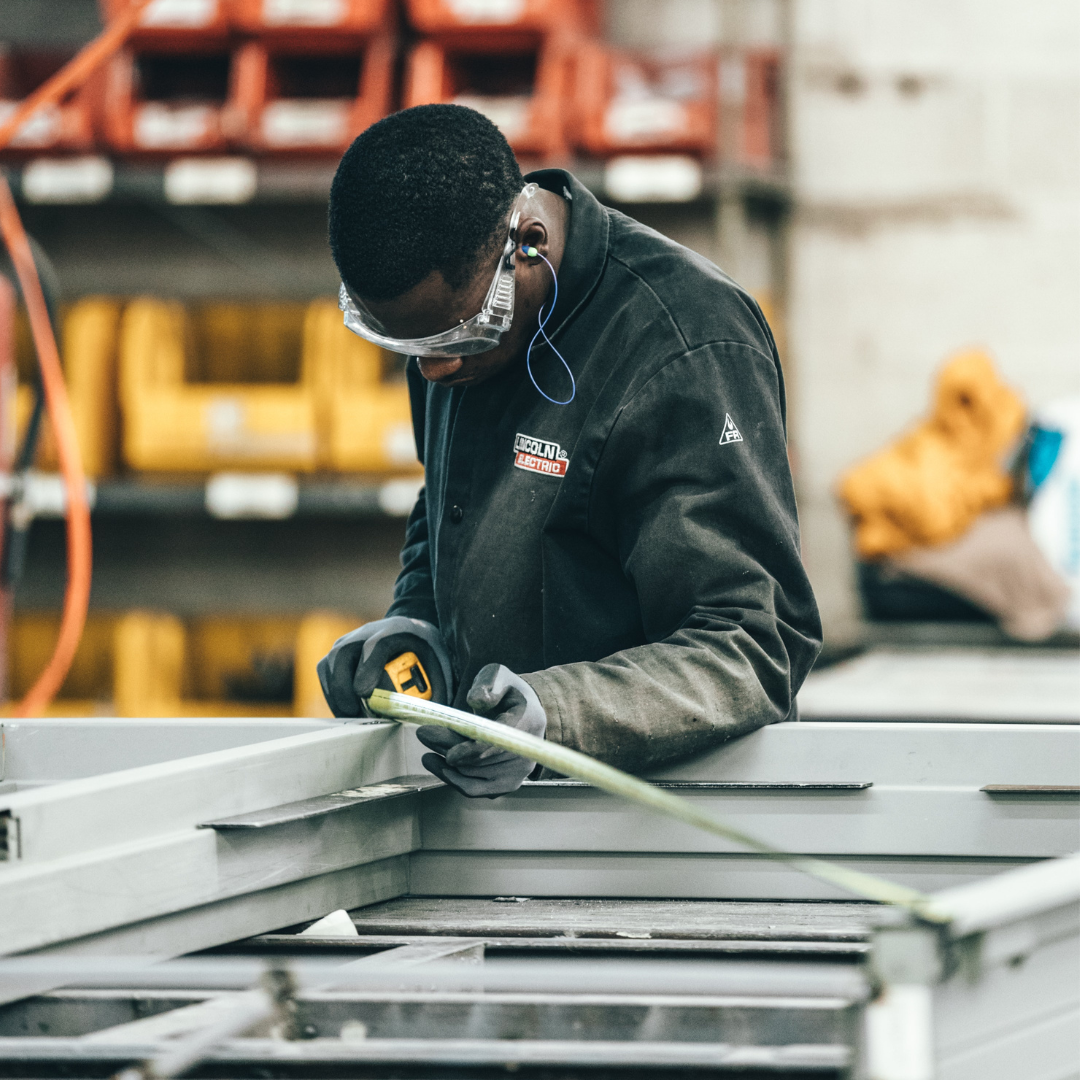
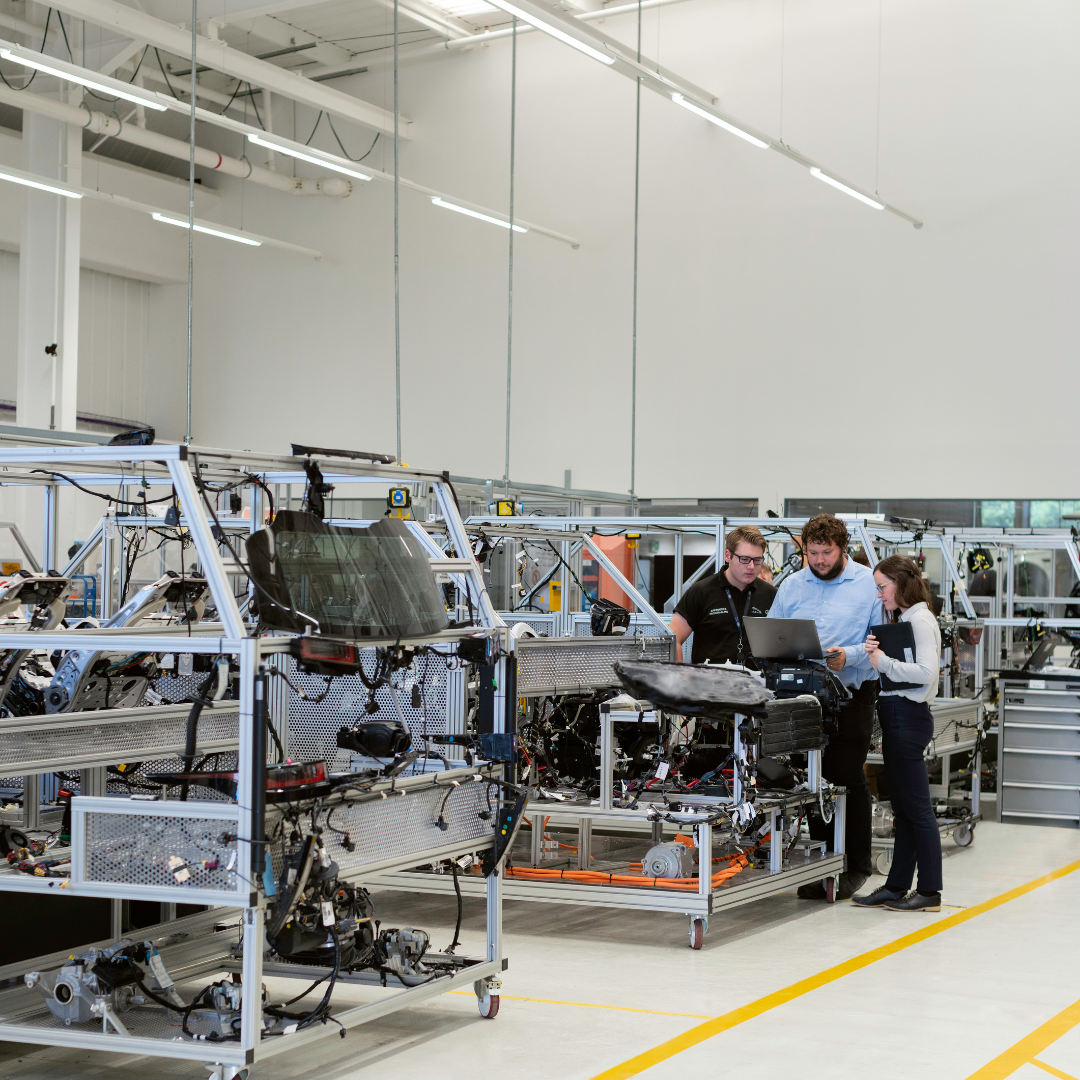
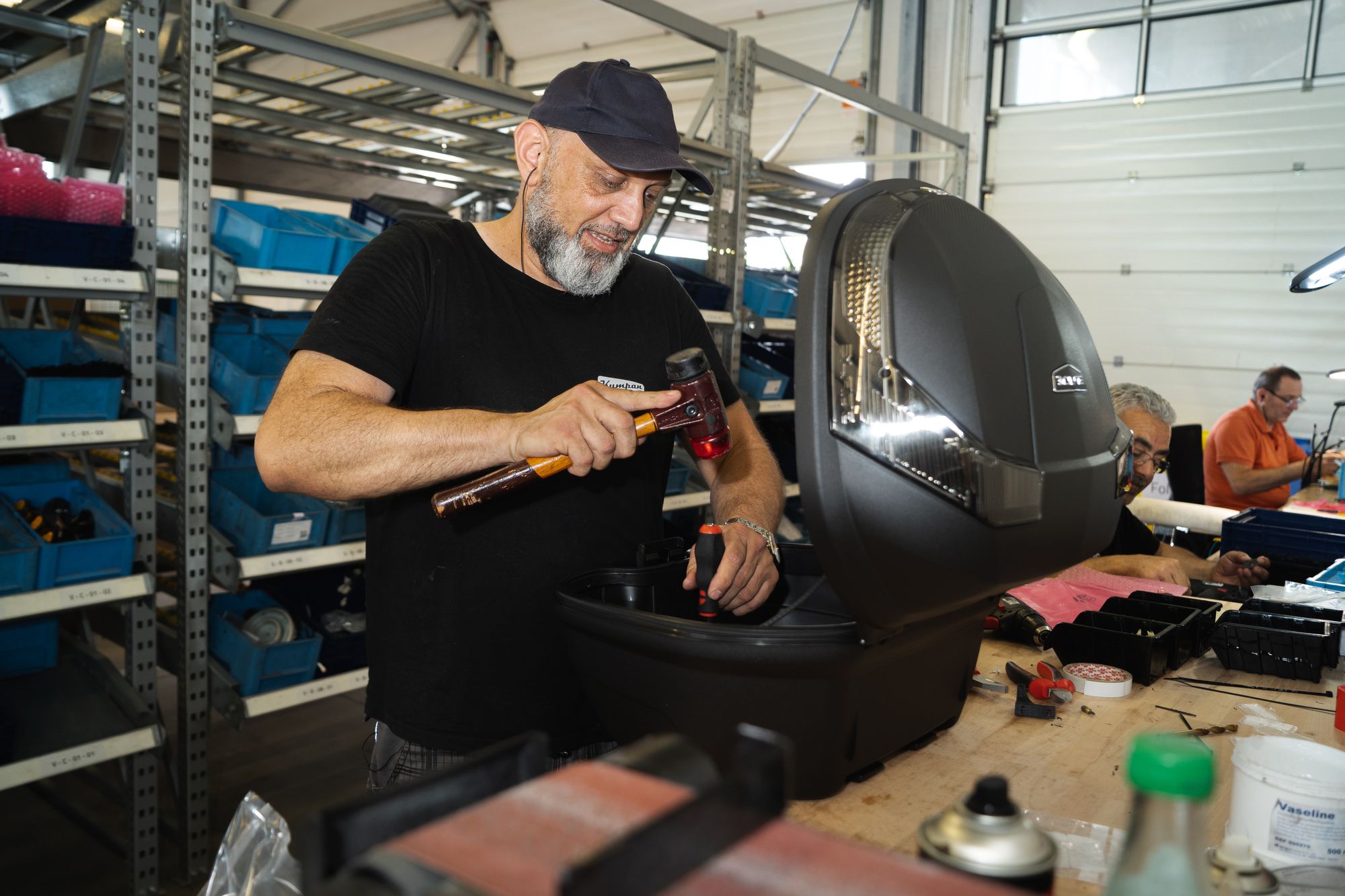
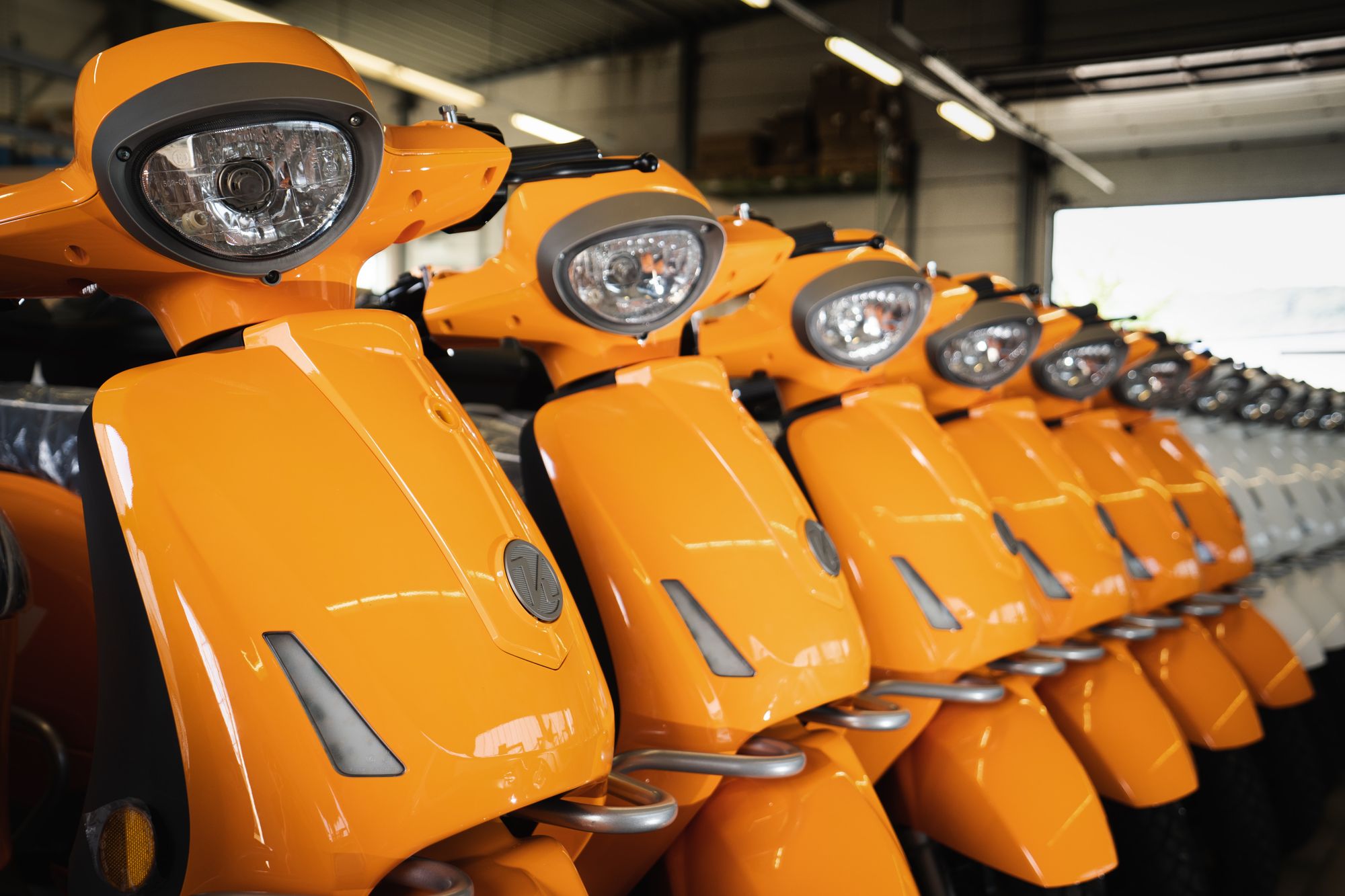
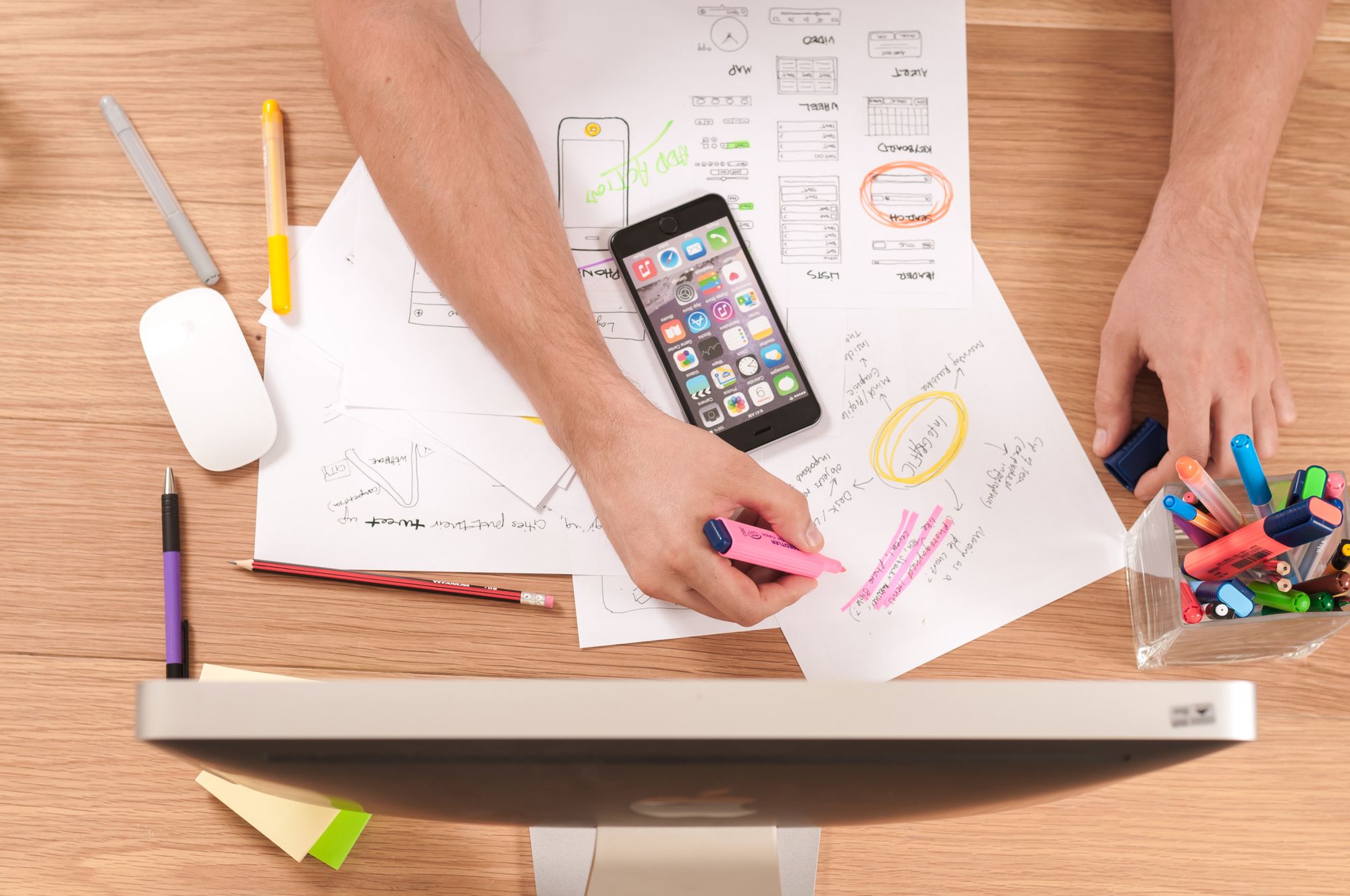