Make-to-order methods can save production costs by up to 24%, according to Harvard Business School research. Many companies are turning to this method to increase efficiency and reduce costs. Make-To-Order (MTO) is a process that allows manufacturers to produce goods only when an order is placed.
Make-To-Order (MTO) is an important business model for many industries, from manufacturing to retail. This model relies on the customer to place an order for a product or service, and then the company produces it specifically for them.
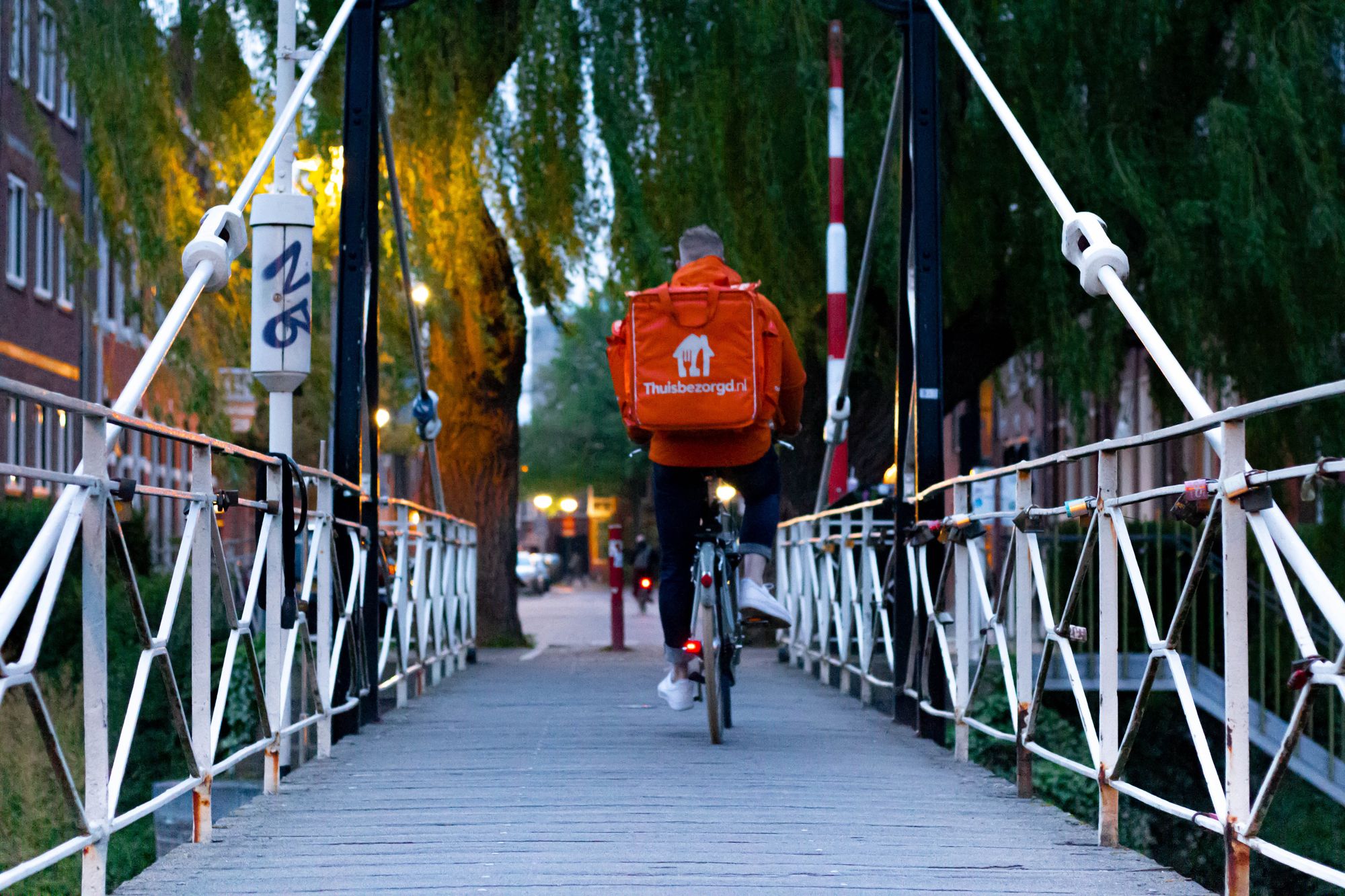
This process contrasts the traditional Make-to-Stock (MTS) production process. MTS involves producing large quantities of goods in anticipation of customer demand.
In this article, we'll look at how MTO works, the benefits it provides, and the challenges it brings. We'll also explore how companies use MTO to serve their customers better and stay competitive in the market.
Here’s what we shall cover in this post:
- What Is Make-To-Order?
- Make-To-Order Planning Process
- 7 Benefits of Using the Make-To-Order Strategy
- Challenges of Make-To-Order Manufacturing
- Make-To-Order vs. Make-to-Stock
- Best Practices for Make-To-Order Manufacturing
- Industry Trends in Make-To-Order Manufacturing
- Conclusion
- Key Takeaways
What Is Make-To-Order?
Make-to-order (MTO) is a manufacturing process where a customer places an individual order with a company. The company produces the item to meet the customer's specifications. This production system is usually used for custom orders, where a customer may order a product with a unique design, size, color, or other features.
- MTO differs from the mass production process, where a company produces a standard product to the exact specifications. MTO can quickly fill orders for multiple customers.
- The MTO system treats each order as an individual project and must be created from scratch. It can be time-consuming and expensive. But it allows companies to provide customers with products tailored to their exact specifications.
- The MTO system can be used in various industries. These include manufacturing, electronics, automotive, and textiles.
- For example, luxury car manufacturers often use make-to-order systems to allow customers to customize their vehicles. These systems enable customers to customize their vehicles with different colors, trim levels, and engine options.
- Other companies may offer custom-made furniture or clothing. These can be made-to-order according to each customer's specifications.
- Companies that use the MTO approach tend to benefit from lower inventory costs. They also tend to have higher customer satisfaction and higher profits.
The MTO system offers many advantages for businesses, such as quickly adapting to changing customer needs and tastes. It also allows companies to reduce inventory costs since they don’t have to keep large quantities of finished goods on hand.
Additionally, MTO systems help businesses improve customer service. MTO systems enable companies to improve customer service by providing personalized products and services. This process can be costly and time-consuming.
Make-To-Order Examples
Make-To-Order (MTO) is a manufacturing process that explicitly produces goods at the customer's request. It is the opposite of a make-to-stock (MTS) process, which produces goods even without an existing customer order.
As such, make-to-order processes are rare. It is due to the added complexity of manufacturing for specific requests. However, it is still an essential and valid production process for certain types of products. Here are some examples of make-to-order processes.
Customized Clothing: Customized clothing is an excellent example of an MTO process. A customer may request a specific type of clothing with particular measurements, materials, and colors.
Much like furniture, the entire process must be adjusted to meet the customer’s needs. The process may involve selecting suitable materials and designing the clothing. Then having it sewn according to the customer’s specifications.
Food Service: Make-to-order is also commonly used in restaurants and other food service establishments. This allows customers to customize their orders by adding or removing certain ingredients. This system ensures that customers always get the exact meal they want.
Specialty Parts: Specialty parts are often made-to-order as a manufacturer does not stock them. These parts are typically produced to meet a specific customer’s needs and may involve a particular type of material and design.
For example, a customer may order a custom-made part for a car engine, which must be produced according to the customer’s specifications.
Make-to-order processes can be complex and require significant customization. However, they are still essential and valid production processes for certain types of products. The examples above illustrate some of the most common types of MTO production processes.
Make-To-Order Planning Process
The Make-To-Order Planning process is ideal for businesses that produce customized goods and services. It allows them to tailor their offerings to individual customers. The main steps in the Make-To-Order Planning Process are:
1. Define Customer Requirements
The first step in the Make-To-Order Planning process is to define the customer's requirements. It involves understanding the customer's needs, wants, and expectations and then translating those into an actionable plan.
- It requires close communication between the customer and the production team.
- It ensures that the customer's needs are clearly understood and addressed.
- This step should involve analyzing customer feedback, previous experiences, and other relevant information. It is done to ensure the customer's expectations are met.
2. Develop a Plan
After gathering the customer's requirements, the next step is to develop a plan to meet their needs. It involves creating a timeline, budget, and resources needed to complete the project.
It should include establishing milestones and targets. It will ensure progress is tracked and measurable. It's also essential to account for any potential risks or obstacles during the project.
3. Develop a prototype
The next step is to develop a product prototype, which will be used to test the product's design and performance. This prototype should be tested to ensure it meets the customer's requirements. This step is critical to ensure the product is suitable for the customer's needs.
4. Develop a Production Schedule
The next step is to create a production schedule. It involves determining the order of operations. It includes assigning tasks to team members and setting deadlines. It's essential to ensure that the production schedule is realistic and achievable while considering potential risks or delays.
5. Implement the Plan
It involves ensuring that the plan is followed and that team members are accountable for their tasks. It's also essential to monitor progress and make adjustments as needed.
This step should involve regular communication between team members. It ensures everyone is on the same page and that potential issues are addressed promptly.
6. Monitor and Adjust
It involves regularly checking in with team members to track progress and ensure that the plan is followed. It also involves making adjustments to ensure the project stays on track. This step should involve regular communication between the customer and the production team. It is to provide the customer's needs are met.
7. Create a Delivery Plan
The final step in the make-to-order planning process is to create a delivery plan. It involves determining the best way to ship the product to the customer and any associated costs. It's essential to ensure that the delivery plan is cost-effective and efficient.
It is essential to take into account any potential risks or delays. The delivery plan should also include any special instructions or requirements that must be followed to ensure successful delivery.
By following these steps, businesses can ensure that their customers get exactly what they need in a timely and efficient manner.
Why Do Businesses Use the Make-To-Order Strategy?
Businesses use this strategy to manufacture products in response to customer demand instead of producing goods in anticipation of customer demand.
Through make-to-order, businesses can better serve their customers. They can provide personalized goods that meet their needs and expectations.
- It eliminates the need to maintain large inventories. It can reduce costs as businesses don't have to pay for storage or warehousing fees.
- It can also help reduce inventory obsolescence risk, as businesses only produce goods when a customer orders.
- With this strategy, businesses can meet the specific needs of their customers by providing personalized goods that meet their exact specifications. It can differentiate them from their competitors and give them a competitive advantage.
- Businesses can reduce production lead times by producing goods when needed. They can also get goods to their customers more quickly.
- It can increase customer satisfaction and loyalty, as customers receive their goods more quickly. Make-to-order also allows businesses to remain flexible and agile.
- The make-to-order strategy is a strategy that is used by businesses to make products. It gives companies a greater degree of control over the production process.
- By controlling the production process, companies can ensure that the products they provide meet their quality standards. They can also ensure that their products are made to their specifications.
By producing goods in response to customer demand, businesses can quickly adjust to changes in the market. They can also meet the changing needs of their customers. It can help companies remain competitive in a rapidly changing environment.
Customization for Make-To-Order Manufacturing
Customization for make-to-order manufacturing is customizing a product to meet a customer's unique needs. This process involves altering the design, material, and manufacturing processes to accommodate an individual's or business's specific needs.
Customization for make-to-order manufacturing is beneficial to both the customer and the manufacturer. The product is tailored to the customer's specific needs, making it more cost-effective and efficient. For the manufacturer, the process reduces costs by eliminating the need for inventory and the demand for costly mass production.
Design and Material Selection:
The design and material selection process is a critical part of customization for make-to-order manufacturing.
- The customer will work with the manufacturer to choose the right design, materials, and manufacturing processes to meet their needs. It often involves working with the customer to create a prototype. Then testing the product to ensure it meets the customer's specifications.
- The manufacturing process is a crucial part of customization for make-to-order manufacturing. The manufacturer will use the customer's specifications to choose the right equipment and manufacturing processes.
- It often involves using specialized equipment and processes, such as CNC machining and 3D printing, to produce the product.
Quality control is an integral part of customization for make-to-order manufacturing. The manufacturer must ensure the product meets the customer's specifications and is of the highest quality. They may use automated quality control systems to ensure that the product meets the customer's requirements.
Automation for Make-To-Order Manufacturing
Automation for make-to-order manufacturing is a process used to automate the production of custom-made products. It is used to ensure that the products are of high quality and are delivered on time.
- Automation for make-to-order manufacturing can improve efficiency and reduce costs.
- Automation can also increase the speed of production.
- It helps to reduce human error and provides a level of consistency in the product that would take a lot of work to achieve with manual processes.
- Automation for make-to-order manufacturing involves the use of robots and computer-controlled systems.
- These systems are programmed to perform specific tasks such as cutting, welding, and assembly. The robots can work quickly and accurately to create products with the required specifications.
Automation for make-to-order manufacturing can be expensive to install and maintain. Additionally, robots may need help completing more complicated tasks like welding.
Automation tools:
ERP Systems: Enterprise resource planning (ERP) systems are one of the most popular automation tools for make-to-order manufacturing.
ERP systems are designed to provide a comprehensive view of the entire production process. It involves everything from raw material ordering and inventory tracking to order processing and shipping. ERP systems can integrate with existing business processes. They provide powerful analytics to help manage production operations.
Manufacturing Execution Systems: Manufacturing execution systems (MES) are automated manufacturing process management systems. They are designed to monitor and control the production process in real-time.
MES solutions track and control resources such as machines, materials, and personnel. MES solutions are used to maximize production efficiency. MES systems can automate making-to-order production processes' scheduling, tracking, and management.
Automated Data Collection: Automated data collection is a powerful automation tool for make-to-order manufacturing. Automated data collection solutions allow for real-time data capture and analysis of production processes.
It enables manufacturers to track and control all aspects of the production environment. Automated data collection solutions are designed to improve accuracy and reduce errors. They also increase production efficiency.
7 Benefits of Using the Make-To-Order Strategy
Over the past few years, the make-to-order (MTO) strategy has become increasingly popular in the manufacturing industry. The make-to-order (MTO) strategy can be highly beneficial to an organization. Here are six benefits of using the MTO strategy.
1. Increased Product Variety
Businesses can offer a wider variety of products to meet customer needs by making products to customer orders. This makes it easier for companies to differentiate their products from competitors and attract more customers.
2. Reduced Inventory Costs
Since products are not made in anticipation of customer demand, businesses can reduce inventory costs. They don't need to store large quantities of finished products. It can help companies to save money and improve their bottom line.
3. Improved Cash Flow
Using the make-to-order strategy can also help improve a company's cash flow. By only producing goods after an order has been placed, companies can ensure that they are not spending money on producing items that may not be sold. It can help companies maintain a healthy cash flow and ensure they are not investing in unsold inventory.
4. Enhanced Product Quality
By making products to order, businesses can ensure that they meet the customer's exact requirements. It can help improve product quality and increase customer satisfaction.
5. Reduced Wastage
As products are only made when there is a customer order, businesses can reduce waste. They don't need to store large amounts of finished products which may not be sold. It can help reduce the waste associated with producing items that may not be sold.
6. Improved Efficiency
Using the make-to-order strategy can also help improve the efficiency of a manufacturing process. Businesses can reduce their lead times by making products to order and meeting customer deadlines easier. Additionally, the make-to-order strategy can reduce the time spent on packaging and shipping. The item is produced only after an order is placed.
7. Increased Customer Satisfaction
The make-to-order strategy can help increase customer satisfaction by allowing companies to produce goods that meet the exact specifications of the customer's order.
It can result in a better overall customer experience, as customers will receive exactly what they ordered on time. The make-to-order strategy can also help companies build a reputation for excellent customer service.
Overall, the make-to-order strategy can provide many benefits to companies in the manufacturing industry. These benefits make the make-to-order strategy an attractive option for many manufacturers.
Challenges of Make-To-Order Manufacturing
Make-to-order or MTO manufacturing is a popular production system in modern manufacturing. While this system offers many advantages, there are also some key challenges. These challenges must be addressed to make MTO manufacturing successful. This section will discuss the most common challenges of MTO manufacturing.
1. Extended Lead Times
A significant challenge of MTO manufacturing is that it often takes longer to produce a finished product than it would with a make-to-stock production system.
Each product must be custom-made to meet the customer's exact specifications. It requires more time and resources. As a result, MTO manufacturers must be prepared to quote longer lead times to their customers.
2. Increased Production Complexity
MTO manufacturing is much more complex than other production systems due to its highly customized nature. Each product must be designed and produced according to specific customer requirements.
These can be difficult to manage and track. Manufacturers must also be prepared to troubleshoot any issues that arise during production. These products are often highly specialized.
3. Restricted Production Quantities
MTO production is usually limited to small-batch production, as most customers only require a few items. It can be challenging for manufacturers as their production capacity is limited, and they may need help to meet large orders. Manufacturers must understand their customers' needs and be prepared to meet them accordingly.
4. Limited Automation
Automation is often used to streamline production and reduce costs. But this is not always possible with MTO manufacturing. Due to the highly customized nature of these products, automated manufacturing processes are often only feasible sometimes.
It can be challenging for manufacturers as they must rely on manual processes, which can be time-consuming and costly.
There are some challenges associated with MTO production. Manufacturers must address these challenges to make their operations successful. By understanding the challenges and addressing them appropriately, manufacturers can ensure that their MTO operations are successful.
Make-To-Order vs. Make-to-Stock
When managing a successful supply chain, businesses must consider their production strategies. Two of the most common strategies are make-to-order and make-to-stock. Although these strategies may seem similar, they have some distinct differences.
Make-to-Stock: Make-to-stock (MTS) is a production strategy in which goods are manufactured in anticipation of customer demand. MTS is a widely used strategy among manufacturers, as it helps to ensure that customer needs are met on time.
- MTS helps to reduce costs by eliminating the need for companies to maintain large inventories of raw materials, as the items are already produced. It helps to reduce overhead costs, as it removes the need for additional storage and transportation costs.
- MTS helps to increase efficiency by enabling companies to respond quickly to customer orders. It is especially beneficial for companies that operate in fast-paced markets. They need to meet customer needs quickly.
- MTS helps to improve quality by enabling companies to standardize production processes. It ensures that products are consistently produced with the same quality standards.
Difference between MTO and MTS
Production Model: At a high level, make-to-order production models are built to meet customer needs. This model is more flexible and allows companies to create custom products based on customer specifications.
In contrast, make-to-stock models are designed to produce and store products that are already in demand. This model is more efficient and cost-effective but less customized than the make-to-order model.
Inventory: Make-to-order production models don't require the company to maintain an inventory of products. It allows the company to save on costs associated with storing and maintaining inventory.
On the other hand, make-to-stock models require the company to maintain an inventory of products. It increases the costs associated with production.
Lead Time: Make-to-order production models tend to have longer lead times. It is due to the customization involved in creating the product. In comparison, make-to-stock models are more efficient and can have shorter lead times.
Flexibility: Make-to-order production models are more flexible and can quickly adapt to changing customer needs. In comparison, make-to-stock models are more rigid and cannot accommodate changes as easily.
Cost: Make-to-order production models tend to be more expensive due to the customization involved. On the other hand, make-to-stock models are more cost-effective. It is due to the efficiency and lower costs associated with maintaining an inventory.
Risk: MTO production strategies have higher risk since there is no guarantee that goods will be sold after production. MTS production strategies have lower risk since goods are produced before customer orders. So there is less chance of them going unsold.
Both Make-To-Order and Make-to-Stock production strategies have their advantages and disadvantages. Understanding their differences is essential to make the right choice for your business. To learn in-depth on this refer to our article on Make-To-Order vs. Make-To-Stock.
Best Practices for Make-To-Order Manufacturing
For make-to-order manufacturing to be successful, it is crucial to follow certain best practices. Here are the seven best practices for make-to-order manufacturing:
Understand Your Customers' Needs
The first and foremost step in make-to-order manufacturing is deeply understanding your customers' needs. It helps to determine the exact specifications that need to be fulfilled to produce the product.
It is also essential to understand the customer's timeline and budget. It ensures that the product can be delivered within the specified deadline.
Establish Clear Communication
Clear communication between the customer and the company is essential for make-to-order manufacturing. It will ensure that the customer is well-informed about the process and that their expectations are met. It is also crucial to ensure that the customer is regularly updated about the product's progress.
Use Technology to Track the Manufacturing Process
Technology can be used to track the progress of the manufacturing process. It will help ensure the product is delivered on time and to the expected standards. It will also help identify potential issues and make necessary changes to the process if required.
Adhere to Quality Standards
Quality should be given utmost importance during make-to-order manufacturing. It is essential to ensure that the product is of the highest quality and meets the customer's specifications. It will help to maintain customer satisfaction and trust in the company.
Establish Flexible Production Schedules
Establishing flexible production schedules is critical to ensure that the product can be delivered on time. It is vital to adjust quickly to changes in customer specifications and timelines. It will help ensure that the product is delivered per the customer's expectations.
Adopt Lean Manufacturing
Lean manufacturing is a process that helps to optimize the manufacturing process and reduce waste. It will help ensure the product is made efficiently and with minimal wastage. It will also help to reduce costs and ensure that the product is delivered on time and within budget.
Maintain Inventory
Maintaining an inventory of the components and materials required for the product is essential. It will help to ensure that there is no shortage of supplies and that the product can be delivered on time. It is also crucial to have a backup supply of components in case of any delays in the manufacturing process.
Following the above best practices will help to ensure that the product is made efficiently and delivered on time. It will also help to maintain quality standards and customer satisfaction.
Industry Trends in Make-To-Order Manufacturing
Make-To-Order manufacturing is an industry that has been rapidly evolving over the past few years, with new trends emerging every day. As the industry continues to grow and develop, it's crucial to stay up to date on the latest trends. It is so that businesses can stay competitive and profitable. Here are the most important industry trends in make-to-order manufacturing:
1. Automation
Automation is one of the most prominent trends in make-to-order manufacturing. Automation has the potential to increase efficiency, reduce costs, and improve quality. Automation can be used to streamline processes, reduce manual labor, and increase the speed of production.
It can result in higher output and faster delivery times. Automation can also reduce energy consumption and the number of materials used, resulting in cost savings. Automation can also help reduce waste, improve safety, and increase productivity.
2. Additive Manufacturing
Additive Manufacturing also known as 3D printing, is a form of additive manufacturing. It is becoming increasingly popular in the manufacturing sector. Additive manufacturing has the potential to revolutionize the industry. Its ability to produce complex parts quickly and cost-effectively.
Additive manufacturing offers the ability to produce parts with complex geometries and unique features. It would otherwise be impossible to achieve with traditional manufacturing methods. This technology can also reduce lead times and eliminate the need for tooling, resulting in significant cost savings.
3. Cloud Computing
Cloud computing is becoming an increasingly important trend in make-to-order manufacturing. Cloud computing offers manufacturers the ability to access and store data from anywhere.
It can improve collaboration and communication between departments. It also provides access to analytical tools that can be used to optimize operations. Cloud computing can also automate processes, reduce costs, and increase efficiency.
4. Digital Manufacturing
Digital manufacturing is another trend gaining traction in the sector. Digital manufacturing uses digital tools and technologies to improve product design, production, and management.
It includes the use of 3D modeling and simulation, as well as data analytics and artificial intelligence. Digital manufacturing can reduce the time to market. It can also improve product quality and increase efficiency.
5. Collaborative Platforms
Collaborative platforms are becoming increasingly important in the manufacturing sector. Collaborative platforms allow manufacturers to connect with customers, suppliers, and partners. This will enable manufacturers to share data and insights. This can help to streamline the manufacturing process.
It can also reduce costs and improve communication and collaboration. Collaborative platforms also offer the ability to monitor and control production in real-time. It enables manufacturers to respond quickly to changes in demand.
To remain competitive, manufacturers must stay abreast of the latest developments and trends in the sector. These trends have the potential to revolutionize the industry. It will result in improved efficiency, reduced costs, and higher-quality products.
How can Deskera Help You?
Deskera software is a cloud-based business software. It is designed to help you manage and streamline your business operations. It offers a complete suite of integrated applications for business management.
These include inventory control, order management, accounting, and more. It is an ideal solution for businesses that need to manage just-in-time manufacturing.
Deskera MRP is the one tool that lets you do all of the above. With Deskera, you can:
- Control production schedules
- Compile a bill of materials
- Produce thorough reports
- Make your own dashboard.
Deskera ERP is a complete solution that allows you to manage suppliers, track supply chain activity in real time, and streamline a range of other company functions.
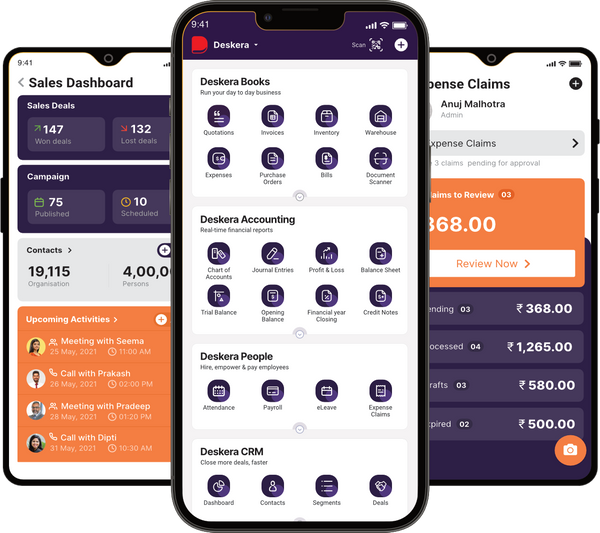
Deskera Books allows you to manage your accounts and finances better. It helps maintain good accounting standards by automating billing, invoicing, and payment processing tasks.
Deskera CRM is a powerful tool that organizes your sales and helps you close deals rapidly. It enables you to perform crucial tasks like lead generation via email and gives you a comprehensive view of your sales funnel.
Deskera People is a straightforward application for centralizing your human resource management activities. Not only does the technology expedite payroll processing, but it also helps you to handle all other operations such as overtime, benefits, bonuses, training programs, and much more.
Conclusion
Make-to-order production is a great way to keep a business competitive in an ever-changing marketplace. By customizing products to meet customer needs. Companies can ensure they are providing the best possible product to their customers. Additionally, make-to-order production allows companies to save money and time.
It is done by eliminating the need for overstock or excess inventory. Not only does this help companies to keep costs low, but it also allows them to focus on providing a higher quality product. By utilizing make-to-order production, businesses can remain competitive and satisfy their customers.
One of the main benefits of MTO is that businesses can avoid the risks associated with overproducing or underproducing items. Additionally, this manufacturing method allows businesses to respond better to customer demands. It will enable companies to create custom products quickly and efficiently.
MTO is an excellent option for businesses that produce highly customized items or a wide variety of options. Companies can ensure that they meet customer needs by producing items only on demand. They can also create products that are of the highest quality.
Key Takeaways
- Make-to-order (MTO) is a production process that allows customers to customize products to their specifications.
- Customers can benefit from MTO in the form of greater flexibility, higher quality, improved customer experience, and tailored product designs.
- Manufacturers must consider their production capabilities and customer needs when implementing an MTO process.
- MTO systems should include strategies for inventory management and scheduling. It ensures that customer orders can be fulfilled on time.
- Effective communication between all stakeholders is essential to ensure a successful MTO process.
- Software and automation technologies can be used to streamline the MTO process, reducing costs and improving efficiency.
- A thorough understanding of customer requirements is necessary to create an effective MTO system.
- Training staff on the MTO process is essential to ensure everyone understands the system and how it works.
- Make-to-order production can be beneficial for manufacturers and customers if implemented correctly.
- MTO requires careful design and engineering to ensure the final product meets customer requirements.
Related Articles
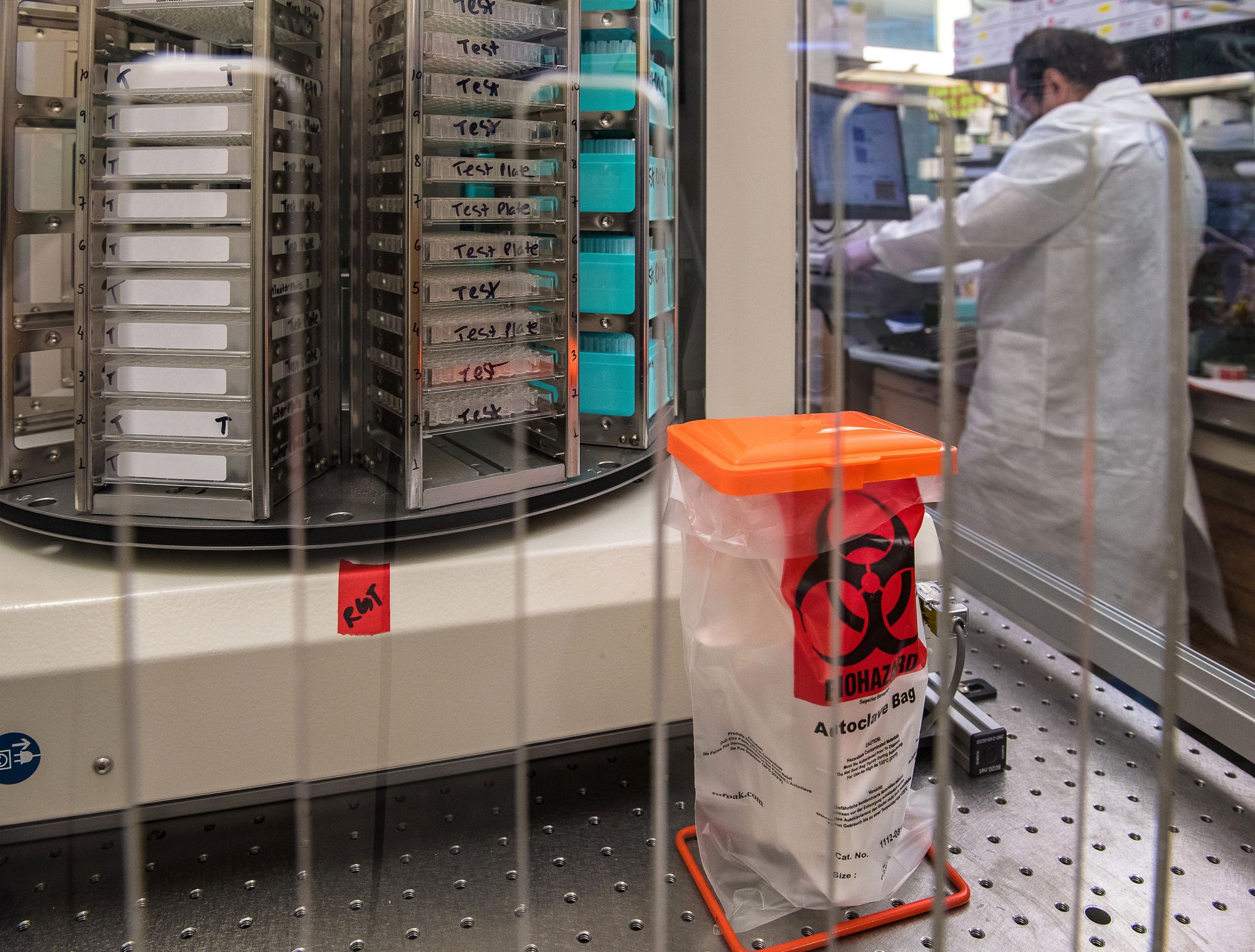
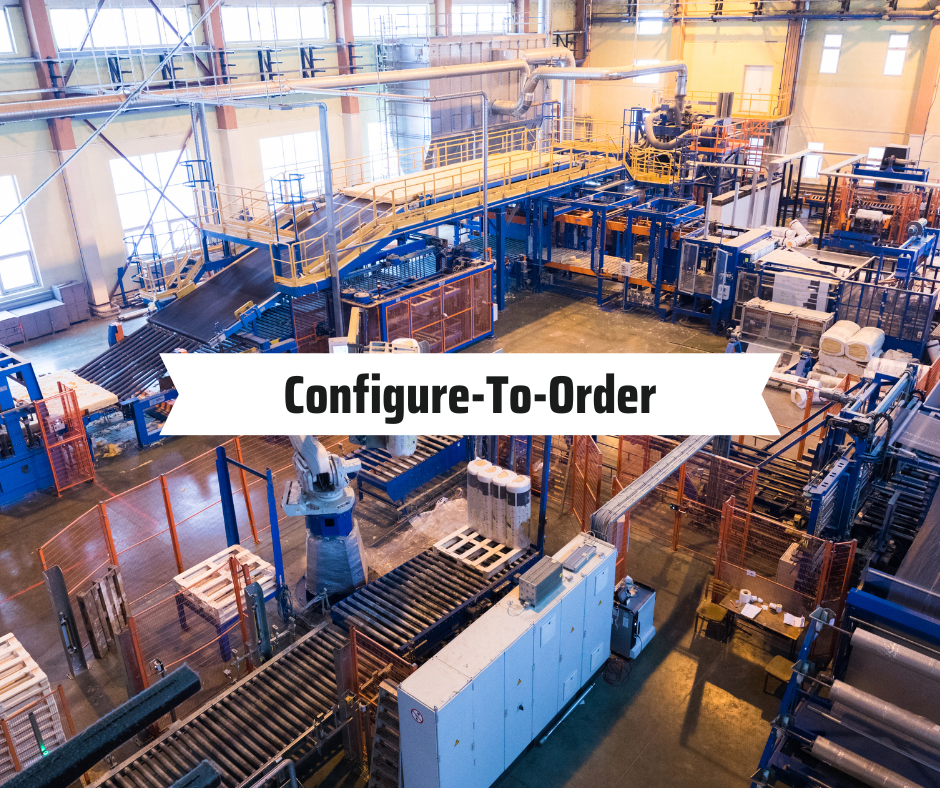
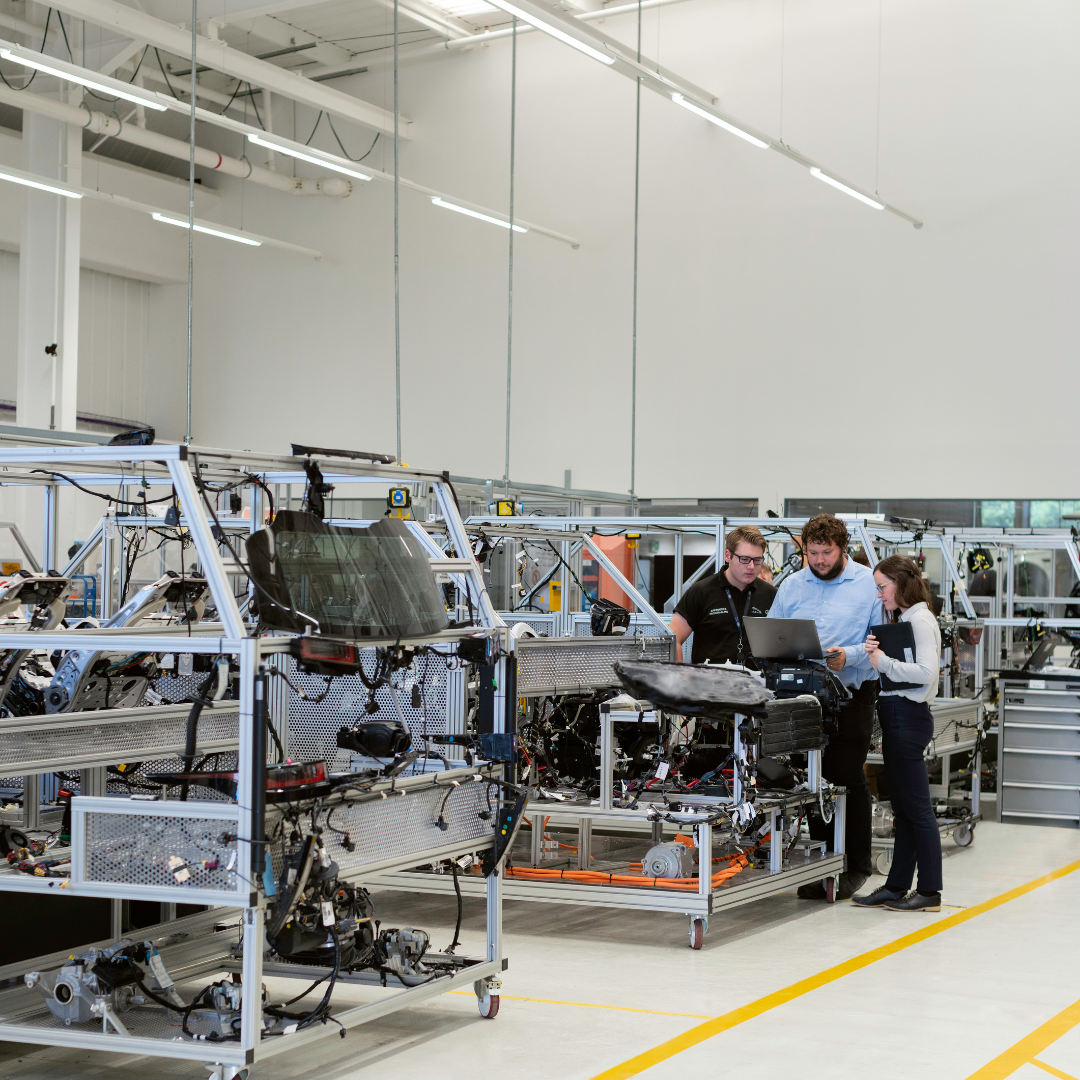
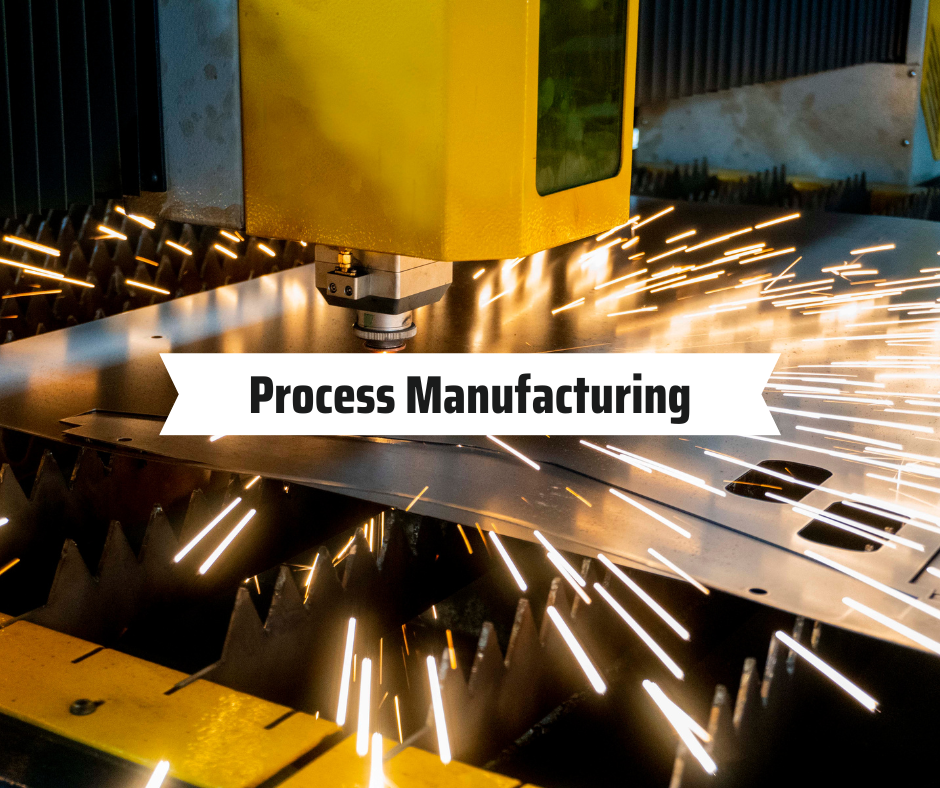