A study by the Food Marketing Institute and the Grocery Manufacturers Association estimates that the direct costs of one recall can cost a corporation up to $10 million.
What can you do to avoid getting yourself into such a costly situation? Several other firms use lot traceability during manufacturing to better track the movements of their products. This article takes an in-depth look at manufacturing lot traceability. It also takes a look at implementing end-to-end tracking in your company.
Lot tracking's primary goals are to maintain quality control and compliance criteria. Lot tracking, in particular, gives producers the ability to spot product flaws and make the required corrections to stop them from happening again.
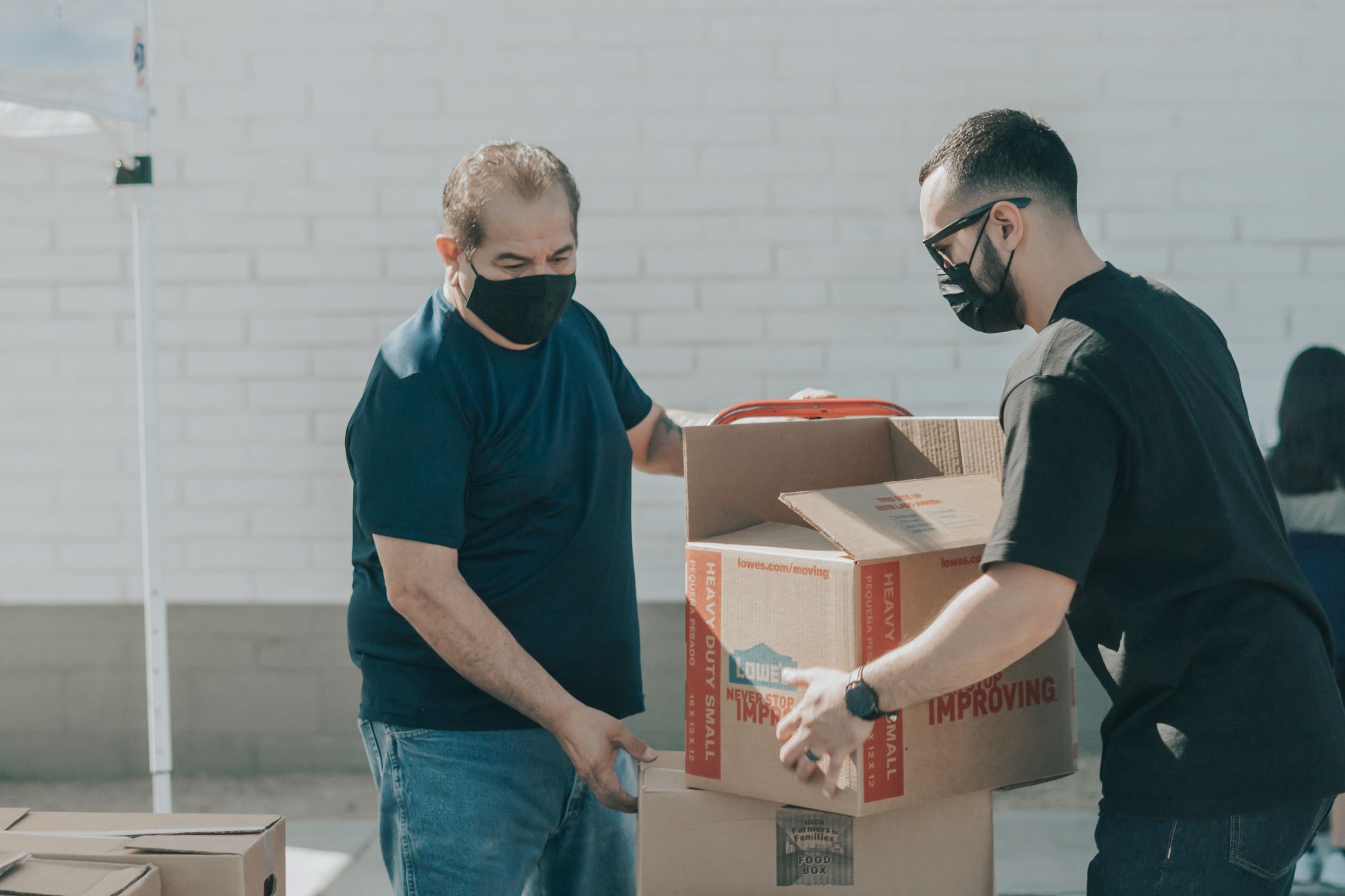
It aids in keeping track of any recalls or defects so that when necessary, these problems may be immediately resolved. The fact that lot-tracking software automates many lot-tracking tasks. It makes it simple to handle and keep track of your product data. This is one of the main advantages of using it for this operation.
We will go through the fundamentals of lot tracking in this article. We will also discuss how lot-tracking software can make this process easier for manufacturers. The following are the topics covered:
- What Are Lots?
- What Is Lot Tracking?
- Benefits of Lot Tracking in Manufacturing
- Why Is Lot Traceability Important?
- Which Manufacturing Industries Use Lot Tracking?
- How to Implement Lot Traceability Solutions?
- Lot Tracking Best Practices
- Stock Keeping Units Vs Lot Numbers
- Conclusion
- Key takeaways
What Are Lots?
A lot is a batch of goods created or gathered into a single, recognizable unit. The unit is tracked separately in inventory and recognized by a common lot number. Typically, all of the items in a particular lot have something in common. For example, a common manufacture date, production variation, or expiration date.
- It is possible to generate a lot number based on a particular date and time. For instance, lot numbers can represent the time of a purchase order, the time of delivery, or the time of reception.
- Perishable goods, medicinal supplies, or anything else with a short shelf life may all be tracked by the lot because of the timestamp attached to it.
- Timestamps might or might not be visible on the packaging, but they should be recorded someplace, like in a supply chain management system.
What is Lot Size?
The quantity of an item purchased for delivery on a particular date or produced in a single production run is referred to as the lot size. In other words, the entire quantity of a product ordered for manufacturing is what is essentially meant by lot size.
- A lot size in the financial markets is a measurement or quantity increment. It is suitable for or specified by the party making the offer to buy or sell it.
- A significant component of many lean manufacturing systems is producing fewer lots at once. The lot size is directly affected by development and inventory. There are additional elements that are equally important but less obvious.
- Small batch sizes reduce system variability and guarantee consistent production. It improves quality, makes scheduling easier, lowers inventory, and promotes ongoing improvement.
How Are Lot Numbers Used?
They are used to follow a collection of items from start to finish across the full supply chain. For instance, in the auto business, a lot of batch numbers could be used to identify a batch of red paint that was used to paint a collection of cars. Additionally, a given batch of spark plugs can include only that one number.
The lot batch can rapidly determine which vehicles are using the recalled item if the need for a parts recall arises. Any type of manufacturing can experience recalled items, which may be due to performance or safety concerns. Contamination or manufacturing mistakes may have led to the recall of food or medical products. In short:
- Lot numbers are unique identifiers used to track batches of products, often through the production, distribution, and sale of goods.
- Lot numbers are usually assigned to a specific batch of products as they are manufactured. This allows the manufacturer to track and control the quality of each batch of goods.
- Lot numbers are also used to identify and trace back the source of goods in case of recalls or other issues.
- Lot numbers are typically printed on the packaging of goods and can also be found in invoices and shipping documents.
- Lot numbers are used by retailers to track the movement of goods from the manufacturer to the store.
- Lot numbers are also used to track expiration dates and monitor sales and returns.
- Lot numbers are essential for businesses to ensure quality control and to maintain product safety.
What Is Lot Tracking?
The ability to trace a batch of manufactured goods along the whole supply chain is referred to as lot tracking, also known as batch tracking. A batch is a collection of goods produced in the same production run. The batch uses the same raw materials and under the same manufacturing circumstances.
- The requirements for traceability for large-scale inventory management that supports domestic or international supply chains might be extremely detailed.
- And for companies that deal with perishable commodities, potentially dangerous products, or almost any commodity with an expiration date.
- Traceability becomes an even more challenging issue. However, tracking at the lot (or batch) level is not only for perishables.
- To know your landing costs, costs at a specific period, and/or the shelf life of a finished commodity, lot-level tracking is required. This is even for something as simple as a t-shirt.
- Lots are a popular component of inventory management strategies used by companies in this retail sector. With the use of a lot tracking system, producers can give each batch of products a special lot number.
- They can then use that number to access details about the batch. This includes the location of storage or distribution, the origin of the raw materials, and the expiration date.
- While a serial number serves to identify a specific product, a lot number is applicable to multiple finished goods.
This can help you save a lot of time and money while lowering the possibility of human error. In general, lot tracking is a crucial step for producers who want to guarantee the reliability and security of their goods.
This procedure can be streamlined and made more effective and efficient by the use of digital lot tracking. This can be done by using food inventory management software.
Benefits of Lot Tracking in Manufacturing
Organizing data
If you routinely use lot tracking, you will get a real-time view of where your inventory items are, in what quantities, and how much they are worth. Lot tracking needs you to write down each inventory movement.
Knowing which products or materials are utilized most frequently allows you to make the most of the space in your inventory and the resources allotted to the various stock-keeping units. This is a critical skill to have in stock-keeping.
Monitoring expiration dates
Businesses in sectors that work with perishable items can monitor the expiration dates of their materials or products. Businesses can monitor the expiration dates of their materials or products by using lot monitoring. Inventory waste is reduced to a minimum by using the First In First Out (FIFO) or First Expired First Out (FEFO) technique and lot tracking.
Identify the root of the problem
Lot tracking contains thorough reporting that can be utilized to determine why a certain lot is producing so many returns. For instance, to determine why a certain lot is producing so many returns.
Recognize trends in inventory
Which product batches are moving quickly? Is there a relationship between the season and a specific lot number's slow-moving stock? Rich insights can be obtained using advanced analytics dashboards and lot reporting.
Assist in preventing waste, spoilage, and contamination
Some products don't keep well on the shelf. Lot reports can aid in inventory management and the sale of goods that are getting close to their expiration dates. They can also aid in the prevention of wasteful spending or unsaleable goods.
Quality assurance
A business can recognize problems and link them to certain events, people, or products. This is done by putting in place the right traceability procedures. This makes it possible for firms to identify anomalies on the part of suppliers. It also allows firms to identify employee training shortages and identify issues with machinery, among other things.
Last but not least, it gives them a chance to fix the issues and significantly lower the number of defective products that reach consumers.
- The success of any manufacturing company depends on the quality of its products. By locating production flaws and determining their main causes.
- Lot tracking helps enhance product quality. By enhancing the quality of their products and elevating client happiness, manufacturers can lower customer complaints.
- Product recalls can be decreased via lot tracking as well. Lot tracking can be used in a recall to locate the recalled goods and separate them from the rest of the stock. Both the company's reputation and financial losses could be reduced as a result.
Lot tracking supports the manufacturing sector in numerous ways overall. It can boost customer satisfaction, help with root cause analysis, and enhance product quality. Any manufacturing company that wants to succeed must implement a good lot tracking system.
Prevent human mistakes
Contrary to popular belief, some businesses do track lots manually. Using lot management software to automate this procedure can help prevent expensive mistakes or tracking delays.
Recognize actual landing costs
Since all the items in a lot were acquired at once, lot tracking aids in a better understanding of what your actual landing expenses are. As opposed to, for example, average costs based on SKU.
Streamlining compliance
According to Good Manufacturing Practices (GMP) outlined by the US Food and Drug Administration, lot monitoring is necessary for makers of both food and beverage and life sciences products.
FDA released the most recent version of the Code of Federal Regulations. It stated "Records shall be maintained of examinations of raw materials, packaging materials, and finished products.
The FDA also requires the maintenance of guarantees or certifications of suppliers that verify compliance with Food and Drug Administration regulations and guidance documents or action levels.
- Maintaining batch records on paper as a lot tracking system is not only time-consuming but also prone to human mistakes.
- A digital lot tracking system makes sure that audit procedures are followed. All the data is accurately collected and saved along the whole supply chain. This is done from a trustworthy source.
- In industries like food, pharmaceuticals, automotive, aviation, etc., where even the tiniest discrepancy could be hazardous to human health and wellness.
- Lot tracking is a need. You are always prepared for an inspection if you have the documentation pertaining to the lifecycle of your lots on hand.
Better commercial choices
Making better business decisions is made possible by streamlining crucial operational processes. This is done by improving visibility and communication. Both of which contribute to increased profitability.
Specialized performance
Informed by nearly three decades of industry experience and designed with chemical and process makers in mind. Our software offers functionality that is as specific as your demands and keeps you up to date.
Efficient traceability
One of the most significant issues facing modern manufacturers is product recalls. The Food and Drug Administration (FDA) of the United States has documented a total of 1,010 recall news announcements from 2017 to 2020.
- The FDA stresses the value of technologically enabled traceability for comprehensive outbreak and recall response.
- The FDA has outlined the New Era of Smarter Food Safety Blueprint. Accessible, trustworthy digital batch records guarantee that faulty or contaminated items are taken off the market as soon as feasible.
Additionally, having a digital lot monitoring system helps producers cut down on waste brought on by product recalls. Traditional techniques of production tracking result in data silos. These techniques have significant visibility holes in the process.
- Data gathered by lot tracking enables a company to pinpoint the particular batches and stage of production where an issue first appeared. This is in the event of a faulty or contaminated product. This allows them to identify the problem's fundamental cause.
- Instead of losing all items connected to broad attributes like the time period a product was manufactured. This causes the recall of the fewest number of products that are affected. Even the distribution of contaminated or defective items can be avoided with this level of process visibility.
Simpler recalls of products
Knowing precisely which customers received the defective products makes product recalls far more effective. In this manner, you avoid having to call back every item you sold within the predetermined time range. This could be detrimental to consumer happiness and your company's overall performance.
You already have a good reason to establish a lot tracking system if you are struggling with any of the factors mentioned.
Greater effectiveness
Less time is wasted searching around warehouses for a certain item or ingredient. You can get a real-time view of your whole inventory with lot tracking. Inventory counts and manufacturing both benefit from this.
Inventory management
Processes for inventory management and order fulfillment can be made better with lot tracking. Manufacturers can specify when a product must be sold by and guarantee that the oldest products are distributed first. They can do this by allocating lot numbers based on expiration dates.
The storage location of a batch can be included in batch records. This makes it easier to locate product groups. This improves the effectiveness of fulfillment operations.
Traceability and lot monitoring for inventory management:
- Lot monitoring and traceability are the foundation of effective warehouse management.
- It starts the moment items are received. This functionality facilitates strategic decision-making and offers complete, real-time visibility into your inventory. When combined with wireless barcoding.
- These functions are supported by ERP in a single, integrated system, providing you with total control right down to the lot number.
- The software is designed to help chemical, and process manufacturers meet their particular needs for chemical inventory management.
With the help of bin location capabilities, you can identify and barcode each position in your warehouse using a standard naming scheme. For instance, "Aisle 1, Level 1" on a pallet rack. You may scan any location using wireless barcoding to get a 360-degree view of your inventory.
Lot control is essential while keeping finished goods in storage as well, letting you use a built-in quality management module. It enables you to keep track of which tests should be performed on which goods. It also allows you to keep track of whether the outcomes adhere to the requirements for the specific lot.
Why Is Lot Traceability Important?
The food supply chain and other manufacturing industries rely on lot management and traceability. This is a key component of ensuring product quality and safety.
- Businesses can rapidly spot potential faults and take remedial action to stop them from happening again. This is done by tracking finished items from the supplier to the table.
- Keeping track of the production dates and the sources of each batch of goods is part of lot management.
- If there is a problem with a certain batch, this information is useful since it can assist firms in identifying the problem's root cause.
Moreover, lot management can assist companies in monitoring their inventory levels. This helps ensure that they always have enough products available to meet client demand.
The capacity to trace a product back to its source is known as traceability. Because it enables companies to promptly identify and recall goods that might be contaminated or otherwise harmful. This is significant in the food supply chain.
- Businesses can identify any problems with the manufacturing process and take action to fix them. Businesses can also take action by tracing items back to their source. For maintaining the safety and quality of food items, lot management and traceability are both crucial.
- Businesses can stop issues before they start and ensure the safety of their clients by tracing products from the source to the table.
- Your company can guarantee that its products are always of the highest caliber. By enhancing lot management and increasing traceability.
- For producers, lot traceability has always been crucial, but lately, it has become even more crucial.
- Leaders in many industries now understand that firms cannot afford to function without effective lot traceability for all of their products. This is a major challenge for many firms. This is in light of the 2018 global food recalls.
The importance of lot tracking, however, extends far beyond the worst-case situations of product recalls. Even if a company is fortunate enough to never have to issue a recall, being able to follow every batch from start to finish will have numerous advantages beyond simply responding to manufacturing problems:
- Improves customer service
- Increases the effectiveness of warehouse and logistics operations
- Assists in avoiding FDA or USDA scrutiny and fines
- It makes it much easier and quicker to recall faulty or unsafe products
- It helps to identify where issues are occurring in a manufacturing or sourcing process.
Which Manufacturing Industries Use Lot Tracking?
Lot tracking is an effective way for manufacturing industries to track and monitor their production and ensure that their products meet quality standards. It is a process of keeping track of each lot of a product from when it is produced until it's delivered to the customer.
Lot tracking is used in various industries, including food and beverage, pharmaceutical, medical device, and automotive. In these industries, lot tracking is vital to meet safety and quality standards.
A crucial aspect of the manufacturing sector is batch tracking, which is useful for companies across a wide range of industries. The following are some of the major industries that gain from lot tracking:
Pharmaceutical Manufacturing
Pharmaceutical manufacturers also use lot tracking to monitor the production of their products. This includes tracking the ingredients used in the production process, the expiration dates of the products, and any recalls that may have occurred. Lot tracking also helps manufacturers to identify and address any issues that may arise during production, such as contamination.
When working with drugs, the same laws and rules apply. It is important to handle these drugs cautiously. Therefore having access to the most recent product information helps to guarantee everyone's safety. Additionally, it is simple to identify the root cause of any human errors.
Food and Beverage Manufacturers
In the context of food production facilities, lot tracking is a critical component. It's critical to monitor individual batches as goods are warehoused and prepped for production and distribution. It is also used in Food tracking. This guarantees the standardization of products and adherence to laws pertaining to
- Storage conditions
- Perishable inventory
- Ingredients
- Storage conditions
- And other factors
Cosmetics Manufacturing
The production of cosmetics frequently uses organic raw materials and other components. These components can not resist high temperatures or rough handling without becoming harmed. As a result, lot monitoring is essential to this industry. It guarantees that batches remain fresh, safe for consumers, and traceable in the event of a problem.
Manufacturing in General
For all kinds of production processes, lot tracking can be helpful. This allows businesses to track their sources better and enhance quality control. Lot tracking is a crucial component of production. Regardless of whether you're making textiles, electronics, machinery, or anything else.
Important Factors for Manufacturers of Chemicals and Processes
You may track safety and quality documentation like certificates of analysis along with your raw materials. You may track raw materials using ERP software. It provides lot tracking and traceability for the chemical and process manufacturing sector. You can track such papers down to the lot level with ERP.
- First in, first out (FIFO) and FEFO (first expired, first out) inventory tracking is also made possible by lot control for raw materials.
- FIFO tracking means that the oldest lot is used first, which means that your inventory is being cycled. This aids in tracking the things you've had for a while. This allows you to see whether you've been overbuying by aging your inventory (and helps you adjust future ordering ).
- FEFO tracking refers to the usage of the first lot to expire. It's possible that some of the goods you receive later may have an impending expiration date. This is because it has a lower shelf life or was shipped out of order.
To ensure optimal use and reduce waste, ERP provides the capability to automatically choose the first lots to expire. As well as the oldest inventory. For producers of food, consumables, and personal care items, lot monitoring is critical. The ability to trace a lot is crucial. Because of concerns about expiration and shelf life for both materials and finished goods. Lot tracking and traceability are essential.
Which Products Need Lot Tracking Numbers?
A lot tracking system can be useful for many items, but it is more expensive to implement because each lot requires its own storage space. It can not be kept with similar batches of the same product.
Naturally, there are some products for which lot tracking becomes crucial. The following goods are sold or produced in the US, and the US Food and Drug Administration (FDA) is in charge of ensuring their safety.
A lot tracking system is required for any product that needs FDA approval. This is due to an expiration date or because it contains substances that must be regulated. Here are some examples of product categories that the FDA regulates:
- Medical supplies
- Food and beverages
- Cosmetics
- Household cleaners
- Certain electronic devices
- Vitamins and supplements
Lot tracking is a best practice in warehouse management that aids in the organization and storage of inventory for online stores. It is used to guarantee quality assurance, traceability, and correct fulfillment.
For instance, you can use a lot monitoring system to make sure that the products that first arrived in the FDA-approved warehouse are also the first to be fulfilled. If you're concerned about your finished products going past their expiration dates.
Most crucially, in the event of a recall or other safety issue, these items also include substances that must be tracked back to the lot number. Cradle-to-grave lot traceability is required by the U.S. Food and Drug Administration (FDA) for all products that enter the food supply chain. It is also required for nutraceuticals and personal care items like shampoo and soap.
Manufacturers will be required to conduct a simulated recall during an FDA audit. In a mock recall, an FDA representative will select a random lot number and give you a limited amount of time—typically two hours—to inform all of the customers who purchased the lot of the need to recall their products. During this time, you must provide all the information you can about the material.
How to Implement Lot Traceability Solutions?
The implementation of lot traceability has proven difficult for many businesses. It necessitates the smooth integration of multiple distinct systems. It also requires the availability of a vast deal of information. This degree of comprehensive information has historically been difficult to locate.
- Many manufacturers have had to make do with fragmented solutions because they lack a single unified platform that enables data flows from all stages of the production process to be tracked and evaluated.
- The new agreement, however, is concentrated on a certain set of approaches that, compared to all others, provide a quicker and more thorough implementation of lot traceability.
- The new agreement is a more comprehensive implementation of lot traceability.
- One of the most important instruments for lot traceability has always been manufacturing ERP software. Manufacturing ERP software is today more powerful and essential than ever.
According to the requirements of each particular firm, a decent ERP software solution ought to provide some or all of the lot traceability features listed below. The following are some of the lot traceability features listed below:
- Automated quality controls that identify distribution or process irregularities
- Manufacture and expiration date tracking
- Supplier tracking that enables inputs to be traced back to their sources
- Distribution tracking that shows where each batch goes after production
- Formula and process tracking tools, including modification logs
- Integration with lot management hardware systems, like barcode scanners
Lifecycle of a Lot
How does lot tracking appear in an ERP/MRP system then?
- As an illustration, an inventory worker can easily print out a distinctive, automatically generated label. This label can be attached to the box of received products. This label can be used to identify the particular lot while receiving goods.
- The following worker only needs to glance at the ERP system to determine what their role is and what materials they must select from which lot and storage location. The next handling action, such as moving products to the shop floor, takes place.
- After manufacturing is complete, the fresh, distinctive labels are applied to the goods and put in the warehouse.
- The warehouse worker can pick products from stock once they need to be picked up from the warehouse and transported to the customer again. This is done in accordance with instructions from the ERP system.
- To verify they are handling the appropriate things and receive immediate feedback from the system, workers may even use barcode scanners for double-checking.
In the unlikely event that the originally planned lots cannot be used, it is always possible to manually intervene and inform the software on which lots were actually used.
Bi-directional Traceability
The capacity to trace both directions is referred to as bi-directional traceability. It can be done forward or backward. When using forward traceability, it is possible to follow a product from the supplier from whom the raw materials were obtained. This is done all the way through the manufacturing process, distribution, and sale.
The product is then re-examined until it reaches the final consumer as a finished good. The backward traceability, which is typically used during recalls, is the opposite of this farm-to-fork traceability. It reveals:
- the warehouse from which a finished product was shipped
- the batch in which it was produced
- the raw materials used in its production, and
- the supplier from which the raw materials were purchased.
It starts with receiving the vendor lot number for each material. Then matching it to the internal lot number generated by the organization is how this process operates. This makes it easier to obtain all the information regarding vendor and customer shipments.
- Bi-directional traceability helps organizations ensure the quality of their products and services.
- By tracking the development process, organizations can easily identify any issues or flaws before they become serious problems. This helps them quickly address any problems and prevents them from becoming costly.
- By tracking the process from raw materials to end-user, organizations can identify any inefficiencies and make the necessary improvements to ensure their products are delivered on time and within budget.
- Additionally, traceability also helps organizations understand how their products and services are being used, allowing them to make quick changes and improvements to ensure customer satisfaction.
Overall, bi-directional traceability is an invaluable tool for organizations looking to maximize efficiency and quality in their software development and supply chain management processes.
By allowing organizations to track their development process and supply chains from start to finish, it helps them identify and address any issues quickly and easily. Additionally, traceability also helps organizations stay informed about their competitors and make the necessary changes to stay ahead of the market.
Essential Features of Lot Tracking Software
Any ERP system must have the ability to track lots of inventory. It offers total product lot tracking, which is crucial for recalls and regulatory compliance. Some of the main characteristics of lot-tracking software include the following:
Lot Identification
Lot tracking software should be able to assign a unique identifier to each batch or lot, helping businesses to keep track of different products and batches. This identifier should include basic information about the product, such as its manufacturing date, expiration date, and batch number.
Lot Traceability
Lot tracking software should be able to trace the journey of each batch or lot from the moment it is manufactured or produced to the moment it is sold or consumed. This traceability feature should include information such as the location of the product at any given time, who handled it, and any changes that have been made to the product.
Quality Assurance
Quality assurance is an essential part of any product-based business. Lot tracking software should be able to track product quality throughout its journey and provide detailed reports. This includes information such as the product’s composition, any contaminants present, and whether or not it meets the required standards.
Regulatory Compliance
Lot tracking software should also be able to help businesses comply with relevant regulations, such as industry standards and government regulations. This includes features such as automated notifications when products do not meet the required standards or when they are past their expiration date.
Automation
Automation is key when it comes to lot-tracking software. Automated processes can help reduce manual labor and ensure accurate and up-to-date data. Automation can also help businesses save time and money by streamlining processes, such as automatically generating reports and notifications.
Lot Creation
Users are able to create new product lots using this capability. All pertinent lot data, including the manufacturing date, expiration date, and batch number tracking, can be stored in the software.
Lot Reporting
Users can create reports on product lots using a function called lot reporting. This data can be used to identify trends, evaluate risk, and decide whether to order a product recall or take other actions.
Lot tracking software is an invaluable tool for businesses that ship and produce products in batches. By utilizing the essential features mentioned above, businesses can ensure that their products are tracked and monitored throughout their journey and that they are compliant with all relevant regulations.
Lot Tracking Best Practices
The processes involved in order fulfillment and inventory management can both be enhanced by lot tracking. Here is a summary of lot tracking best practices that you should think about using in your logistics operations. You'll receive considerably more detailed reporting and accurate inventory as a result.
Lot adhering
It's really simple and self-explanatory with this one. By counting inventory at the lot level, incrementing or decrementing inventory from the appropriate lot, and adding the lot number as a scannable barcode or a visual sticker. You adhere to your lot procedure when you use the lot adhering method.
Fulfillment by lot
You must now take care to fill from the suitable lot as you are adhering to lots. Lots are often not fulfilled by lot by retailers who utilize them as part of their inventory management system.
This usually happens as a result of a lack of software protocols that guarantee the correct SKU is being fulfilled from the correct lot. As well as a lack of warehouse staff awareness of why they need to fulfill the lot. Every time you fulfill, fulfill at the lot level so that you may maintain your accurate inventory shelf life and overhead costs.
Integrate barcode scanning
Regardless of the tracking numbers your company uses, this is a solid practice for inventory management. Bar codes can assist save time and prevent errors by eliminating much of the manual effort and data entry that would otherwise be needed for lot tracking. The bar codes can also be used to identify the location of the lot. We strongly advise its use.
Store your items carefully
Many companies will decide to keep their products in the same places and store them with the lot numbers. Aside from assisting businesses in quicker and more thorough recall responses, storing lots with a little foresight can stop workers from unintentionally selecting or transporting products that are flawed, subject to recall, contaminated, or past their sell-by date.
Method for out-of-date items
Lot expiration dates should be entered into your inventory management system. This is especially important for products with short shelf lives.
To avoid letting this inventory go to waste, you may use lot reporting to automate specific promotions or discounts. For example, you may use lot reporting to automate specific promotions or discounts for items that are getting close to their sell-by or expiration dates.
Software for lot tracking
Lot tracking is not used by all shops, and among those who do, not all of them have the same specifications. The same is true of inventory management software; not all of it is made equal. In the end, though, doing everything manually is simply not feasible for huge operations. Or enterprises that want to become enormous operations.
Comprehensive inventory management software may assist with traceability for all codes and goods across the supply chain. In addition to managing lot tracking.
Manufacturing ERP Checklist
Here are some things to look for in an ERP system and demand from your ERP software vendor if you're interested in adopting lot traceability in your manufacturing processes. Also, you can also shop around for a new ERP or upgrade your present system.
Generally, your potential ERP software provider should be able to offer you a system that can track raw materials as they are received, materials through manufacturing, and completed products through the distribution chain.
This includes the entire distribution chain, all the way to the final consumer. Your ERP system's lot traceability capabilities should, but should not be limited to, the following to accomplish this effectively:
- Provide automated QA/QC checks that identify flaws/anomalies in the manufacturing process and the distribution channel;
- Track manufacturing and expiration (shelf-life) dates;
- Track third-party vendors to trace raw materials back to their original supplier;
- Track distribution channels to confirm and document the final destination of every production lot and every finished product received by end customers;
- Completely integrate system-generated lot information.
However, you want to make sure the system's lot traceability functionality can give you precise and trustworthy answers to the following concerns before plunging in and actually buying a new or replacement ERP:
- Which raw materials, and how many of each, were employed in the production of a certain good or lot?
- Who supplied these raw ingredients, when did they come in, and, if appropriate, is their shelf life clearly marked?
- Who (in your organization) approved the quality-assurance processes and tests that were performed on a particular lot after production?
- Which distributors/resellers, when, and from which precise lot were given finished goods for distribution?
- Which end users and when did they get your distributors' finished goods?
Lot traceability is a crucial tool for all production operations. Rapid, precise, and dependable inventory and production workflows and reporting are made possible by specialized manufacturing ERP software. As a result, manufacturers will achieve high-level, corporate-wide traceability. This will ultimately save time, precious resources, and money spent on fixing flawed processes or recalling dangerous or defective goods.
Manufacturers must now more than ever meet stringent consumer standards for a finished product that is no less than "perfect". This is because of the boom of e-commerce and online purchasing. They have no alternative but to include lot traceability in their operations.
Stock Keeping Units Vs Lot Numbers
For tracking and traceability purposes, identifiers other than lot numbers are also utilized. SKUs, are used to identify products based on details like the manufacturer, price, color, and available alternatives. This is different from lot numbers, which are used to track products as a whole. SKUs are retailer-specific codes that can be used to conduct stock-level and sales reports for a particular SKU.
They can also be used to scan inventory using a scanner. They can also display related products on an e-commerce site based on shared characteristics, and more. One SKU delivered in bulk at a single time is referred to as a lot. In short, the difference between SKUs and Lot Numbers is as follows:
- Purpose: SKUs are primarily used for tracking an item for sale, while lot numbers are used for tracking a batch of products. Lot numbers are useful for tracking the production process, quality control, and other operations related to manufacturing a product.
- Identification: SKUs are typically composed of numbers and letters, and are used to identify a specific item. Lot numbers, on the other hand, are usually composed of only numbers and are used to identify a batch of products produced together.
- Usage: SKUs are used for tracking stock levels and sales, while lot numbers are used for tracking production runs and quality control.
- Data: SKUs contain information about the product, such as size, color, and price. Lot numbers, however, contain information about the production process, such as when the product was made and which production line was used.
- Timing: SKUs are associated with individual products, so they change when a product is sold or returned. Lot numbers, on the other hand, are associated with a batch of products, so they remain the same until the entire batch has been sold or returned.
Overall, SKUs and lot numbers are two important tools used by businesses in the retail industry. While they are both used for tracking and identification, they have different purposes and contain different types of data. Understanding the differences between SKUs and lot numbers is essential for any business dealing in retail.
Serial Numbers Vs Lot Numbers
It is easier to understand the distinction between serial numbers and lot numbers. Serial numbers are one-to-one, as opposed to lot numbers, which are one-to-many, meaning that one lot number is assigned to numerous items or SKUs. As a result, a single product is given a single serial number.
Using an automobile as an example, each one has a unique vehicle identification number (VIN). There may be black, eight-cylinder 2001 Ford Mustangs in existence, each with a unique VIN number. In short, the difference between Serial Numbers and Lot Numbers is as follows:
- Definition: A serial number is a unique number assigned to an item that identifies it from all others. A lot number is a unique number assigned to a particular batch of items being produced.
- Tracking: Serial numbers allow for the tracking of individual items, while lot numbers track batches of items.
- Example: A serial number might be used to track a specific computer, while a lot number might be used to track a batch of computers that were all made from the same materials.
- Length: Serial numbers are usually longer than lot numbers and may include letters and numbers. Lot numbers are typically shorter and only include numbers.
- Structure: Serial numbers usually have a specific structure, while lot numbers are more random.
- Location: Serial numbers are usually found on the item itself, while lot numbers can be found on the packaging or invoice.
- Validity: Serial numbers are usually valid for the life of the item, while lot numbers are typically only valid for the duration of the production run.
- Scope: Serial numbers are typically used to track individual items, while lot numbers are used to track batches of items.
- Traceability: Serial numbers can be used for traceability purposes, while lot numbers are not usually used for traceability.
Other Uses of Lot and Serial Numbers
Serial and lot numbers can also be used for extra inventory management and customer service objectives.
Other Uses in Inventory Management
Lot numbers and serial numbers support inventory management in addition to tracking throughout the manufacturing process. Orders are completed by:
Quality control: By recording serial numbers, companies can occasionally link consumer complaints to specific lot numbers. This can be a sign that there was an issue with the manufacturing of some batches, which might need a recall or a modification to the production method.
Legal compliance: In some circumstances, it may be necessary for your company to supply serial and lot numbers for every manufactured good. The company must supply serial and lot numbers for every manufactured good.
To keep customers safe, businesses that sell pyrotechnics, medical supplies, and other goods must have a mechanism to identify each product. The pyrotechnics must be able to identify each product. Products can be effectively taken off stores or production if there is a manufacturing issue.
Product recalls: Lot and serial numbers make it simple for customers to recognize products that have been recalled. If a product recall is necessary, you can let customers know the lot numbers involved.
This way they can quickly determine whether their purchases need to be exchanged. These figures also make it simpler to identify the stock that needs to be removed from shelves and to identify the defective parts.
Customer Service
Lot numbers and serial numbers are critical for consumers during the buying process. They are also critical for monitoring products from the warehouse to the retailer. Customers use serial numbers to identify compatible devices, such as smartphone battery chargers. These numbers can be used by customers to pinpoint the specific products that are giving them trouble.
- When submitting a complaint, the customer can provide more precise criticism of the business. The customer can also provide more precise criticism of the business by mentioning the particular product. This enables the business to look into the situation and possibly prevent a product recall.
- When companies offer warranties for their products, serial and lot numbers are also crucial. Due to the fact that not all items are covered by the same guarantees, these identification codes are used to identify products and components.
- These codes make it simple for both businesses and customers to determine whether warranties are applicable to a given product or component.
- The lot and serial numbers are essential when it comes to monitoring the production process.
They are also essential when it comes to putting in place a successful inventory management system. These identifying codes enable businesses to identify possible issues with product components. Customers can learn immediately about product compliance.
How can Deskera Help You?
As a manufacturer, you must keep track of your inventory stock. The condition of your inventory has a direct impact on production planning. It also has a direct impact on people and machinery use and capacity utilization.
Deskera MRP is the one tool that lets you do all of the above. With Deskera, you can:
- Control production schedules
- Compile a Bill of Materials
- Produce thorough reports
- Make your own dashboard.
Deskera ERP is a complete solution that allows you to manage suppliers and track supply chain activity in real time. It also allows you to streamline a range of other company functions.
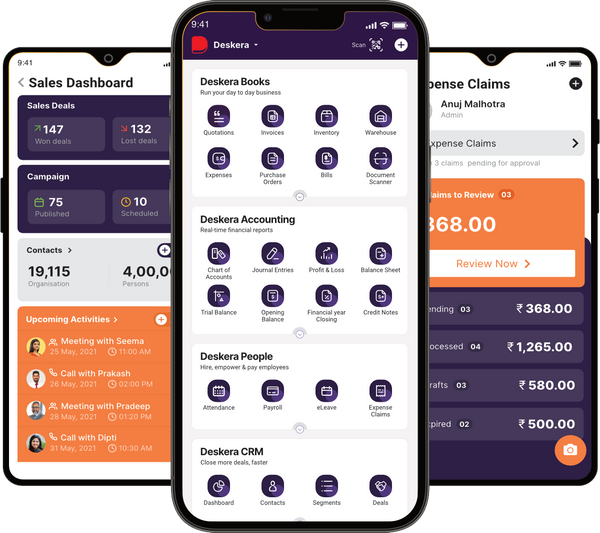
Deskera Books allows you to manage your accounts and finances better. It helps maintain good accounting standards by automating billing, invoicing, and payment processing tasks.
Deskera CRM is a powerful tool that organizes your sales and helps you close deals rapidly. It enables you to perform crucial tasks like lead generation via email and gives you a comprehensive view of your sales funnel.
Deskera People is a straightforward application for centralizing your human resource management activities. Not only does the technology expedite payroll processing, but it also helps you to handle all other operations such as overtime, benefits, bonuses, training programs, and much more.
Conclusion
Users can give identification labels to production runs, or "lots". These can then be traced throughout the supply chain, thanks to lot tracking and traceability. These could be unfinished products, intermediates, or raw materials.
Employers can scan and save data about the material. This includes its position in the warehouse, when it was received, who the supplier is, and when it was purchased. This is all because of ID Labels.
The ability to track lots from the beginning to the end of the supply chain. Beginning with the supplier who sends the raw materials, moving through the manufacturing process, and ending with distribution and sale. When the finished product reaches end users, is referred to as "cradle-to-grave" traceability.
The need for lot traceability in manufacturing has never been greater than it is now. This is due to rising consumer awareness of safety issues and the improvement in product quality. Despite its importance, there are still manufacturers out there who have not included lot traceability in their workflow. Or are unable to do so.
Key takeaways
- Lot tracking aids in company optimization, quality control, and product recall. It also helps keep track of expiration dates, maintain regulatory compliance, and manage product recall. Lot tracking also aids in managing product recall, among other things.
- For businesses that must adhere to tight standards, having a good tracking and traceability system is essential. Regardless of what the business sells, putting in place traceability mechanisms is a smart idea.
- Lot tracking refers to documenting and following the flow of stock using lot numbers. These numbers are issued to various shipments and product batches.
- Companies will be able to learn which materials were used in which products. Which suppliers the supplies originated from, which customers purchased the items, etc., thanks to this chance.
- As a business expands, manual lot tracking becomes increasingly challenging. However, with the help of inventory management software, which unifies all related processes onto a single platform. Lot tracking can now be done largely automatically.
- Employee data entry is facilitated by an ERP system that has robust lot tracking capabilities. This is done by using tools like barcode scanners and labeling.
Related Articles
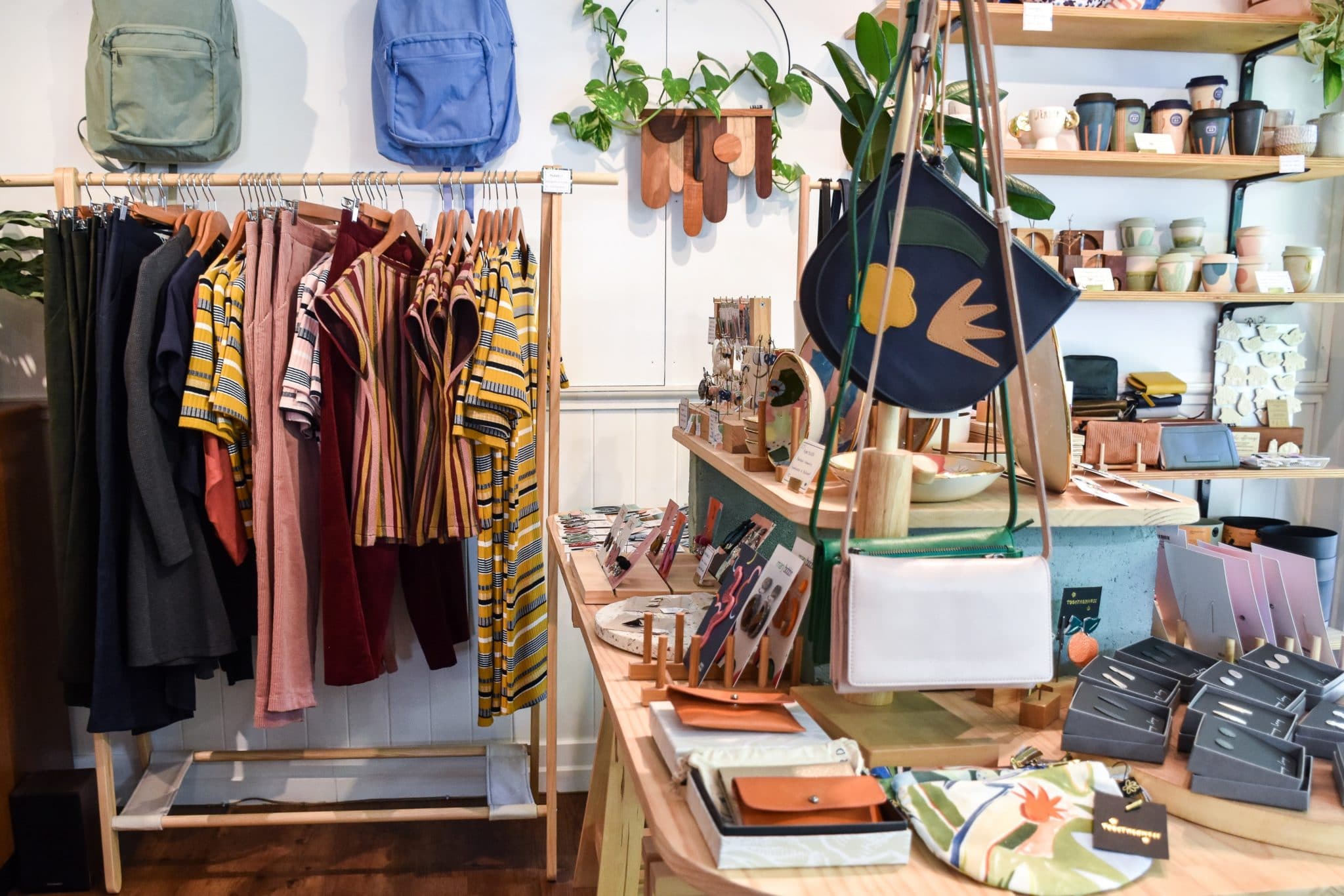
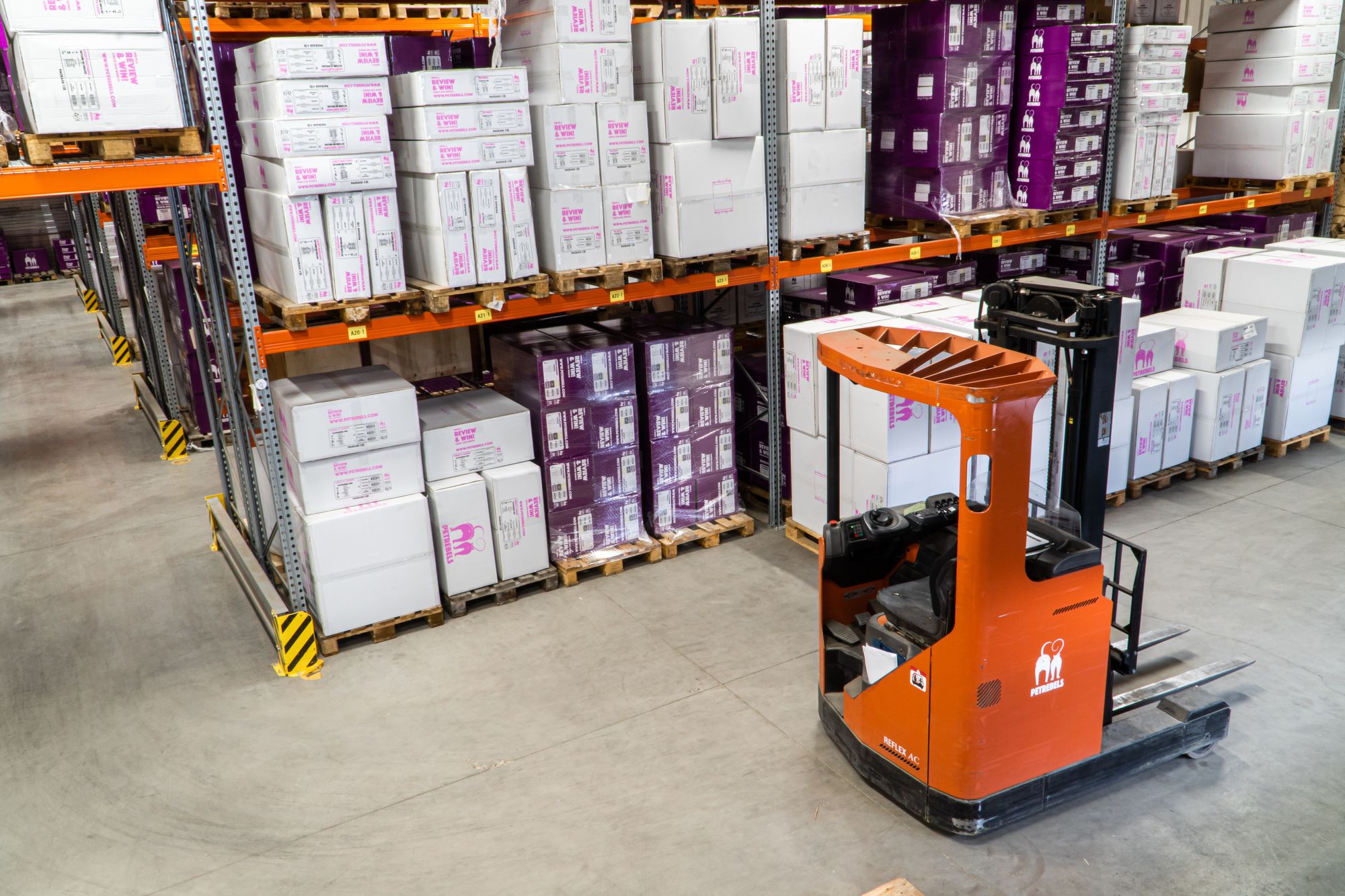
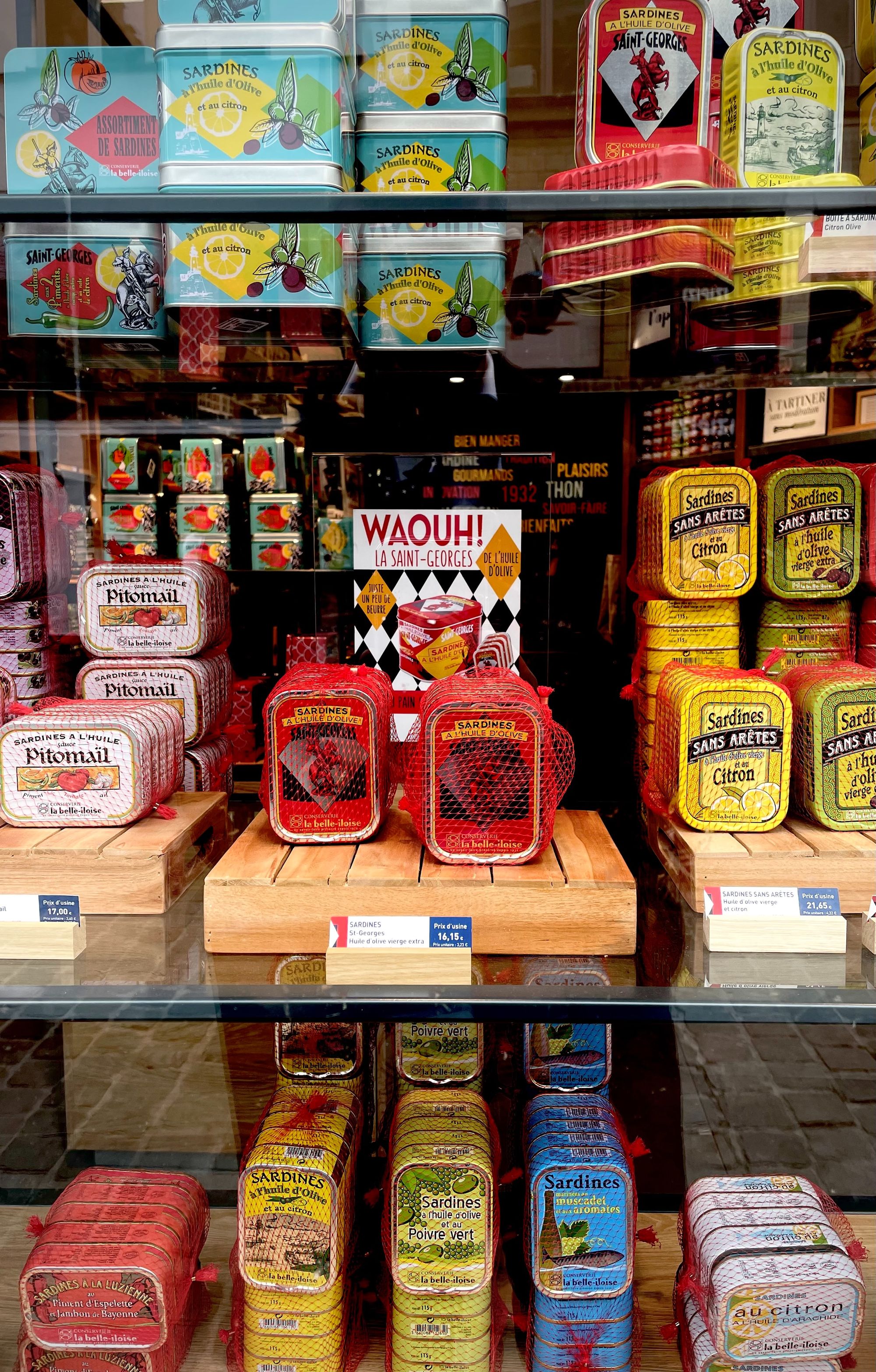
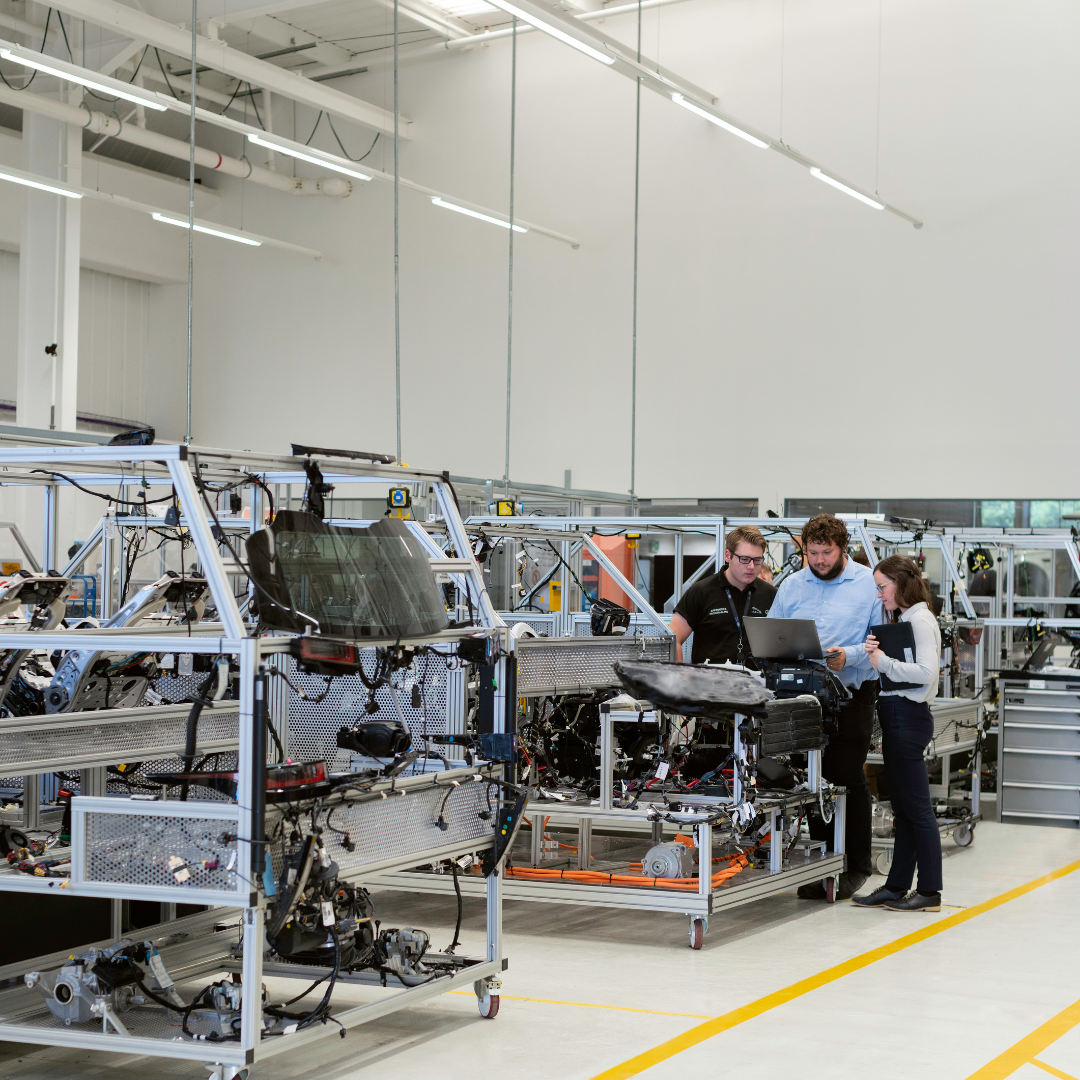