Today's businesses are constantly under pressure to meet ever-increasing demands for products and services. In order to meet these demands, companies must have a streamlined and efficient work order process. However, many businesses find it difficult to create and implement a satisfactory work order process using manual methods.
MRP (material requirements planning) is a computer-aided management system used in manufacturing industries. MRP systems help companies manage the flow of materials from raw material suppliers to product manufacturing units. A well-functioning MRP system helps reduce the overall cost by ensuring that the correct amount of materials is ordered at the correct time and in the correct quantities.
In today’s guide, we’ll thoroughly learn about leveraging MRP systems for seamless work order processes. Let’s take a look at the table of content below:
- Manufacturing Resource Planning (MRP) Explained
- I. Understanding MRP Systems
- II. Streamlining Work Order Processes with MRP Systems
- III. Overcoming Implementation Challenges
- Frequently Asked Questions (FAQs) Associated with Leveraging MRP Systems for Seamless Work Order Processes
- Wrapping Up
- How Deskera Can Assist You?
Let's get started!
Manufacturing Resource Planning (MRP) Explained
Manufacturing Resource Planning (MRP) systems are powerful software tools designed to streamline and optimize the work order processes within manufacturing organizations. These systems integrate various functions, such as inventory management, production planning, and scheduling, to ensure efficient utilization of resources and timely completion of work orders.
MRP systems play a crucial role in modern manufacturing environments by automating and centralizing the work order management process, providing real-time visibility and control, and ultimately improving overall operational efficiency.
Work order processes involve a series of steps, from order creation to materials procurement, scheduling, production, and final delivery. Managing these processes manually can be time-consuming, error-prone, and inefficient. MRP systems address these challenges by automating and coordinating work order activities, facilitating accurate material planning, optimizing resource allocation, and providing comprehensive tracking and monitoring capabilities.
By leveraging MRP systems, organizations can achieve seamless work order processes, resulting in reduced lead times, improved productivity, enhanced customer satisfaction, and cost savings. These systems enable organizations to respond quickly to changing production demands, efficiently manage materials and inventory levels, and ensure optimal utilization of resources. With centralized and real-time data, decision-makers can make informed choices, identify bottlenecks, and take corrective actions promptly.
In summary, MRP systems are indispensable tools for manufacturing organizations seeking to streamline their work order processes. By automating and optimizing key tasks, these systems enable organizations to achieve higher efficiency, better resource utilization, and improved customer satisfaction. In the following sections, we will explore in detail how MRP systems can be leveraged to enhance work order management.
I. Understanding MRP Systems
Following, we've discussed thoroughly about MRP systems. Let's learn:
A. Definition and Functionality:
Manufacturing Resource Planning (MRP) systems are software solutions specifically designed to assist organizations in managing and optimizing their manufacturing operations. These systems provide a centralized platform that integrates various functions and processes involved in production planning and control, inventory management, and work order management.
MRP systems are built on the principles of Material Requirements Planning (MRP), which was developed in the 1960s to address the challenges of inventory management and production planning. Over time, MRP systems have evolved to encompass a broader range of functionalities and capabilities.
Key Features and Functionalities of MRP Systems:
Demand Forecasting and Planning: MRP systems analyze historical data, market trends, and customer demand to forecast future demand accurately. This helps organizations plan their production schedules, material requirements, and capacity accordingly.
Inventory Management: MRP systems provide real-time visibility into inventory levels, allowing organizations to track stock availability, monitor stockouts, and optimize inventory holding costs. These systems automatically generate purchase orders or production orders based on inventory requirements and lead times.
Work Order Management: MRP systems enable efficient creation, tracking, and management of work orders. They automate the process of creating work orders based on customer orders, sales forecasts, or production plans. Work orders are tracked through each stage of production, ensuring timely completion and efficient resource allocation.
Material Planning and Procurement: MRP systems calculate material requirements based on the Bill of Materials (BOM), production schedules, and inventory levels. They generate purchase requisitions or release manufacturing orders to procure materials in a timely manner. This helps organizations avoid material shortages, minimize stockouts, and optimize procurement costs.
Production Scheduling and Capacity Planning: MRP systems create optimized production schedules by considering factors such as machine availability, labor capacity, and material availability. They help organizations balance workloads, avoid bottlenecks, and ensure optimal utilization of resources.
Real-time Tracking and Reporting: MRP systems provide real-time visibility into work order status, inventory levels, and production progress. This allows organizations to track the progress of work orders, identify delays or issues, and take corrective actions promptly. Reports and analytics generated by MRP systems help in monitoring performance, identifying areas for improvement, and making data-driven decisions.
Benefits of Implementing an MRP System in an Organization:
Improved Efficiency: MRP systems automate manual processes, reducing paperwork, errors, and the time required for tasks such as work order creation, material planning, and scheduling. This leads to increased productivity, shorter lead times, and improved on-time delivery performance.
Enhanced Resource Utilization: MRP systems optimize resource allocation by considering factors such as availability, capacity, and skill sets. This ensures that the right resources are assigned to each work order, minimizing idle time and improving overall resource utilization.
Inventory Optimization: By providing real-time visibility into inventory levels, MRP systems help organizations optimize inventory holdings, reduce stockouts, and avoid excess inventory. This leads to cost savings, improved cash flow, and better inventory turnover ratios.
Accurate Material Planning: MRP systems calculate material requirements based on production schedules and inventory levels, ensuring that materials are available when needed. This reduces material shortages, minimizes production disruptions, and improves overall production efficiency.
Timely Decision-making: With comprehensive data and reporting capabilities, MRP systems enable informed decision-making. Managers have access to real-time information on work order status, inventory levels, and production performance, allowing them to identify bottlenecks, address issues, and make timely adjustments to meet customer demands.
Scalability and Adaptability: MRP systems are designed to handle the complexities of manufacturing operations, making them suitable for organizations of all sizes. They can accommodate changes in production volume, product mix, and customer requirements, providing the flexibility needed to adapt to evolving business needs.
In conclusion, implementing an MRP system in an organization offers numerous benefits, including improved efficiency, enhanced resource utilization, optimized inventory management, and timely decision-making. By automating and streamlining key manufacturing processes, MRP systems empower organizations to achieve higher productivity, cost savings, and customer satisfaction.
B. Work Order Management in MRP Systems
Concept of Work Orders and Their Significance in Manufacturing Operations:
Work orders are fundamental documents or instructions that communicate the tasks, resources, and specifications required to complete a specific job or project within a manufacturing operation. They serve as the primary communication tool between different departments and individuals involved in the production process.
The significance of work orders in manufacturing operations is as follows:
Task Clarity: Work orders provide detailed instructions, including the scope of work, materials required, and specific procedures to follow. They ensure that everyone involved understands the objectives, timelines, and quality standards associated with the job.
Resource Allocation: Work orders specify the resources needed for each task, such as labor, equipment, and materials. By clearly defining resource requirements, work orders help optimize resource allocation, minimize bottlenecks, and ensure efficient utilization of available assets.
Workflow Coordination: Work orders facilitate coordination between different departments, such as production, procurement, and maintenance. They serve as a reference point, ensuring that each department knows its responsibilities, dependencies, and deadlines, thus promoting smooth workflow throughout the manufacturing process.
Tracking and Accountability: Work orders enable organizations to track the progress of each task and monitor individual and team performance. They establish accountability by clearly assigning responsibilities and tracking completion against established timelines and milestones.
How MRP Systems Handle Work Order Creation, Tracking, and Completion
MRP systems play a vital role in managing work orders by automating and streamlining the processes associated with their creation, tracking, and completion. Here's how MRP systems handle these aspects:
Work Order Creation:
- MRP systems automatically generate work orders based on various triggers, such as customer orders, production plans, or inventory levels.
- Work orders include essential information such as job details, materials required, routing instructions, and due dates.
- MRP systems consider factors such as resource availability, capacity, and material availability to ensure feasible work order creation.
Work Order Tracking:
- MRP systems provide real-time visibility into the status and progress of work orders.
- Organizations can track the movement of work orders through different stages of production, such as scheduling, material procurement, and actual production.
- MRP systems allow users to view key information related to work orders, such as estimated completion times, actual start and end times, and any delays or issues encountered.
Work Order Completion:
- MRP systems facilitate the recording of completed tasks, including the actual time taken, resources utilized, and any deviations from the original plan.
- Upon completion, MRP systems update the status of the work order, making it available for further processing, such as quality control, packaging, or shipping.
- The data captured during work order completion is utilized for reporting, performance analysis, and generating insights for continuous improvement.
Challenges Faced by Organizations When Managing Work Orders Manually:
Managing work orders manually can pose several challenges for organizations, leading to inefficiencies and potential errors. Some of the key challenges are:
Manual Data Entry and Errors: Manual work order management involves extensive paperwork, manual data entry, and handwritten instructions, which increase the likelihood of errors, inaccuracies, and misinterpretations. This can lead to delays, rework, and compromised product quality.
Lack of Real-time Visibility: Manual work order management often lacks real-time visibility into the status and progress of tasks. It becomes challenging to track work order status, identify bottlenecks, and take timely corrective actions. This can result in production delays, missed deadlines, and customer dissatisfaction.
Inefficient Communication and Coordination: Manual work order management relies heavily on verbal communication, phone calls, and physical handoffs of paperwork. This can cause miscommunication, delays in information sharing, and coordination issues between different departments, leading to confusion and disruptions in the production process.
Resource Allocation Challenges: Manual work order management makes it difficult to optimize resource allocation effectively. Without a centralized system, it is challenging to balance workloads, assign resources efficiently, and address conflicts or overlaps in resource availability.
Limited Reporting and Analysis: Manual work order management lacks the ability to generate comprehensive reports and analytics. This hampers organizations' ability to analyze performance, identify trends, and make data-driven decisions for process improvement and optimization.
In summary, organizations face numerous challenges when managing work orders manually, including data entry errors, lack of real-time visibility, inefficient communication, resource allocation issues, and limited reporting capabilities. MRP systems address these challenges by automating and streamlining work order processes, enabling organizations to achieve greater efficiency, accuracy, and overall operational effectiveness.
II. Streamlining Work Order Processes with MRP Systems
Following, we've discussed thoroughly streamlining work order processes with MRP systems. Let's learn:
A. Work Order Creation and Scheduling:
Automation of Work Order Creation:
MRP systems automate work order creation by considering production demand and inventory levels. Here's how it works:
a. Production Demand: MRP systems analyze customer orders, sales forecasts, and production plans to determine the required quantity and timing of work orders. They consider factors such as order priority, due dates, and lead times to generate work orders accordingly.
b. Inventory Levels: MRP systems monitor inventory levels in real-time and automatically trigger work order creation when stock falls below a certain threshold. This ensures that production can continue seamlessly without interruptions caused by material shortages.
c. Bill of Materials (BOM): MRP systems utilize the BOM, which specifies the components and quantities required for each product, to generate accurate and complete work orders. The system calculates the material requirements based on the BOM and ensures that all necessary components are included in the work order.
Optimization of Work Order Scheduling:
MRP systems optimize work order scheduling to maximize efficiency and minimize downtime. The following techniques are employed:
a. Resource Availability: MRP systems consider the availability of resources such as machinery, equipment, and labor when scheduling work orders. They ensure that the necessary resources are available and not overbooked, preventing conflicts and bottlenecks.
b. Capacity Planning: MRP systems analyze the capacity of production resources and balance workloads across different work centers or production lines. By considering the available capacity and the estimated time for each operation, the system generates an optimized schedule that minimizes idle time and maximizes resource utilization.
c. Priority Sequencing: MRP systems incorporate priority rules to sequence work orders based on factors like due dates, customer commitments, or production constraints. This ensures that urgent or high-priority orders are given appropriate precedence, minimizing the risk of delays and meeting customer expectations.
Benefits of Automated Work Order Creation and Scheduling:
Time Efficiency: MRP systems significantly reduce the time required for work order creation and scheduling. Automation eliminates manual paperwork, data entry, and decision-making processes, enabling faster generation and assignment of work orders. This improves overall operational efficiency and accelerates the production process.
Resource Optimization: Automated work order creation and scheduling in MRP systems facilitate better resource allocation. By considering resource availability, capacity, and production requirements, the system ensures that the right resources are assigned to each work order. This minimizes idle time, maximizes resource utilization, and avoids overloading or underutilization of production assets.
Minimized Downtime: MRP systems optimize work order scheduling to minimize downtime. By carefully managing the sequence and timing of work orders, the system reduces waiting times, changeovers, and setup times. This leads to smoother operations, reduced production bottlenecks, and improved overall equipment effectiveness (OEE).
Improved Production Planning: Automated work order creation and scheduling provide organizations with better production planning capabilities. By aligning work orders with production demand, inventory levels, and resource availability, MRP systems enable organizations to meet customer requirements in a timely manner. This helps minimize stockouts, prevent production delays, and enhance customer satisfaction.
Enhanced Visibility and Coordination: MRP systems offer real-time visibility into work order status, production progress, and resource availability. This facilitates better coordination between different departments and individuals involved in the production process. With improved communication and collaboration, organizations can respond promptly to changes, address issues proactively, and maintain smooth workflow throughout the production cycle.
In summary, leveraging MRP systems for automated work order creation and scheduling brings significant benefits to organizations. These benefits include time efficiency, optimized resource allocation, minimized downtime, improved production planning, and enhanced visibility and coordination. By streamlining these critical aspects, MRP systems contribute to overall operational excellence and help organizations meet production targets effectively.
B. Material Planning and Procurement:
MRP systems play a vital role in facilitating material planning and procurement for work orders. They automate the process of determining material requirements, generating purchase orders, and managing relationships with suppliers and vendors.
Here's how MRP systems achieve seamless material planning and procurement:
Material Requirement Calculation:
MRP systems automatically calculate material requirements based on the Bill of Materials (BOM) and inventory levels. The following steps are involved:
a. Bill of Materials (BOM): MRP systems utilize the BOM, which lists all the components and their quantities needed to manufacture a product, to determine the material requirements for each work order. The BOM serves as the foundation for the system's material planning calculations.
b. Production Schedule: MRP systems consider the production schedule and the quantities of products to be manufactured within a specific timeframe. By analyzing the BOM and the production schedule, the system calculates the quantities of raw materials, components, and subassemblies required for each work order.
c. Inventory Levels: MRP systems continuously monitor inventory levels in real-time. They compare the projected material requirements with the available inventory and determine whether additional materials need to be procured. If the inventory falls below the predetermined threshold, the system automatically generates purchase requisitions or purchase orders to replenish the stock.
Automatic Purchase Order Generation:
Once the material requirements are calculated, MRP systems generate purchase orders to procure the necessary materials. The system automates this process based on predefined rules and parameters:
a. Vendor Management: MRP systems maintain a database of approved suppliers and vendors. They store information such as vendor details, pricing agreements, lead times, and performance metrics.
b. Purchase Requisition: When the system identifies a need for materials, it generates a purchase requisition. The requisition includes the quantity, specifications, and delivery date required for each material.
c. Supplier Selection: MRP systems evaluate the available suppliers based on predefined criteria, such as pricing, lead times, quality, and past performance. The system selects the most suitable vendor for each material and initiates the purchase order creation process.
d. Purchase Order Creation: MRP systems automatically generate purchase orders based on the purchase requisitions. The purchase orders contain detailed information about the materials, quantities, delivery dates, pricing, and terms and conditions.
Integration with Suppliers and Vendors:
MRP systems facilitate seamless material procurement by integrating with suppliers and vendors. This integration streamlines the communication, order processing, and delivery processes:
a. Electronic Data Exchange (EDI): MRP systems can exchange electronic data with suppliers and vendors through EDI. This enables automated order placement, order confirmation, invoicing, and shipment notifications. It eliminates manual data entry, reduces errors, and expedites the procurement process.
b. Vendor Portal Integration: MRP systems can integrate with vendor portals or supplier portals, allowing direct access to product catalogs, pricing information, and real-time stock availability. This integration improves transparency, enables self-service ordering, and reduces the time and effort involved in communication with suppliers.
c. Delivery Tracking and Visibility: MRP systems integrate with shipping and logistics systems to provide real-time tracking of material deliveries. Organizations can monitor the status of incoming shipments, estimated delivery dates, and any delays. This visibility helps plan production schedules, manage inventory levels, and address potential supply chain disruptions proactively.
In summary, MRP systems streamline material planning and procurement for work orders by automatically calculating material requirements based on the BOM and inventory levels. They generate purchase orders, integrate with suppliers and vendors, and enable seamless communication and collaboration throughout the procurement process. This automation and integration lead to improved efficiency, reduced lead times, and better control over the material supply chain.
C. Work Order Tracking and Progress Monitoring
MRP systems enable real-time tracking of work orders, providing organizations with visibility into their status and progress. These systems offer centralized platforms that streamline work order tracking and progress monitoring. Here's how MRP systems facilitate efficient tracking and monitoring:
Real-time Work Order Tracking:
MRP systems provide real-time visibility into the status and progress of work orders. This includes tracking their movement through different stages of the production process. The system captures and updates information such as start and end times, task completion percentages, and any associated notes or comments. Real-time work order tracking allows organizations to monitor the current state of each order, identify potential bottlenecks or delays, and make informed decisions accordingly.
Centralized System for Monitoring:
Having a centralized system for monitoring work order progress offers several benefits, including improved visibility and coordination:
a. Improved Visibility: MRP systems consolidate work order data into a centralized repository, accessible to authorized personnel. This enables stakeholders to view and analyze the status of work orders, production schedules, and associated details in real-time. It provides a comprehensive overview of the entire manufacturing process, facilitating better decision-making, and allowing for proactive action to address any issues or bottlenecks.
b. Enhanced Coordination: A centralized system enables better coordination between different departments involved in the work order process. Production teams, procurement personnel, and managers can access the system to view the status of work orders, allocate resources, and communicate effectively. This eliminates silos, improves cross-functional collaboration, and ensures that everyone is aligned and working towards a common goal.
Alerts and Notifications:
MRP systems can generate alerts and notifications to address any delays or issues that arise during the work order process. These proactive notifications serve as early warnings, allowing organizations to take corrective actions promptly. Some key functionalities include:
a. Delay Notifications: MRP systems can automatically identify potential delays based on predefined parameters, such as expected completion dates, task durations, or material availability. When a delay is detected, the system generates an alert to notify relevant stakeholders, enabling them to assess the situation, identify the root cause, and implement necessary corrective measures.
b. Resource Conflicts: MRP systems can detect resource conflicts or scheduling overlaps, such as when a resource is assigned to multiple work orders simultaneously. The system generates notifications to inform managers or schedulers about the conflicts, allowing them to reassign resources, adjust schedules, or resolve conflicts proactively.
c. Production Issues: If production issues arise during the work order process, such as quality concerns or equipment failures, MRP systems can generate notifications. These notifications trigger immediate action, alerting the appropriate personnel to address the issue, minimize disruptions, and maintain production efficiency.
d. Milestone or Completion Notifications: MRP systems can send notifications when significant milestones are achieved or work orders are completed. These notifications serve as progress updates, allowing stakeholders to track the overall progress of the production process and celebrate successful milestones.
In summary, MRP systems enable real-time tracking of work orders, provide a centralized system for monitoring progress, and generate alerts and notifications to address delays or issues. These capabilities enhance visibility, coordination, and responsiveness, ultimately leading to improved operational efficiency, reduced downtime, and timely completion of work orders.
D. Resource Allocation and Capacity Planning
MRP systems play a crucial role in optimizing resource allocation for work orders, including labor, equipment, and machinery. They also incorporate capacity planning to ensure efficient utilization of resources. Here's how MRP systems achieve these objectives:
Optimizing Resource Allocation:
MRP systems optimize resource allocation by considering various factors such as availability, skills, and requirements of work orders. Here's how they achieve this:
a. Resource Availability: MRP systems maintain a centralized database of available resources, including labor, equipment, and machinery. They consider resource availability when assigning tasks to ensure that the required resources are accessible and not overbooked.
b. Skills and Qualifications: MRP systems can track the skills and qualifications of labor resources. They match the required skills for a particular work order with the skills of available labor, allowing for the efficient assignment of tasks to individuals with the necessary expertise.
c. Work Order Prioritization: MRP systems can prioritize work orders based on various criteria, such as due dates, customer commitments, or production constraints. This ensures that resources are allocated to higher-priority work orders, optimizing the use of limited resources and maximizing customer satisfaction.
d. Scheduling and Sequencing: MRP systems take into account the estimated duration of tasks, resource availability, and dependencies between tasks. By considering these factors, the system generates optimized schedules that minimize idle time, reduce setup times, and avoid conflicts in resource allocation.
Role of Capacity Planning:
Capacity planning is a critical component of MRP systems. It involves assessing the available production capacity and aligning it with the demand for work orders. Here's how capacity planning ensures efficient resource utilization:
a. Capacity Assessment: MRP systems analyze the available capacity of labor, equipment, and machinery. This includes evaluating factors such as shift schedules, maintenance downtime, and planned production interruptions. The system captures and maintains data on the capacity of each resource to determine the overall production capacity.
b. Demand vs. Capacity Balancing: MRP systems compare the demand for work orders with the available capacity. They consider factors such as task durations, resource requirements, and the estimated production volume. By aligning the demand with the available capacity, the system identifies potential overloads or underutilization of resources.
c. What-if Analysis: MRP systems enable what-if analysis to assess the impact of changes in demand, production volumes, or resource availability. This allows organizations to simulate different scenarios and make informed decisions regarding resource allocation and capacity adjustments.
d. Long-term Capacity Planning: MRP systems also support long-term capacity planning by forecasting future demand and identifying potential capacity constraints. This helps organizations make strategic decisions regarding resource expansion, equipment investments, or hiring plans to meet future production targets.
Benefits of Accurate Resource Allocation and Capacity Planning:
Accurate resource allocation and capacity planning within MRP systems offer several benefits in meeting production targets:
a. Optimal Resource Utilization: MRP systems ensure that resources are allocated efficiently, avoiding overutilization or underutilization. This minimizes idle time, reduces costs, and maximizes productivity, leading to improved operational efficiency.
b. Improved Scheduling and On-time Delivery: Accurate resource allocation and capacity planning enable realistic scheduling of work orders. This helps organizations meet production deadlines, reduce lead times, and enhance on-time delivery performance.
c. Proactive Resource Management: MRP systems allow organizations to proactively manage their resources. By identifying potential capacity constraints or bottlenecks, organizations can take preemptive actions, such as adjusting schedules, reallocating resources, or investing in additional capacity, to ensure smooth production operations.
d. Better Decision-making: Accurate resource allocation and capacity planning provide organizations with reliable data and insights. This facilitates data-driven decision-making regarding resource investments, production prioritization, and overall operational strategy.
e. Customer Satisfaction: Efficient resource allocation and capacity planning contribute to meeting customer demands promptly. By optimizing resources and ensuring on-time delivery, organizations can enhance customer satisfaction, strengthen relationships, and gain a competitive edge in the market.
In summary, MRP systems optimize resource allocation for work orders and incorporate capacity planning to ensure efficient utilization of resources. Accurate resource allocation and capacity planning lead to optimal resource utilization, improved scheduling, proactive resource management, better decision-making, and enhanced customer satisfaction. These capabilities help organizations meet production targets effectively and maintain a competitive advantage.
III. Overcoming Implementation Challenges
Following, we've discussed thoroughly overcoming implementation challenges systems. Let's learn:
A. Change Management and Training:
Implementing an MRP system and transitioning from manual processes can pose several challenges for organizations. These challenges range from resistance to change to the need for upskilling employees.
Here's a detailed look at the associated challenges and the importance of change management strategies and employee training:
Challenges Associated with Implementing MRP Systems and Transitioning from Manual Processes:
a. Resistance to Change: Introducing a new system often encounters resistance from employees who are accustomed to manual processes. They may feel apprehensive about learning and adapting to the new system, fearing job security or increased workload.
b. Cultural Shift: MRP systems bring about a cultural shift within an organization. The transition from traditional, paper-based processes to a digital, automated system requires employees to adopt new ways of working and embrace technology. This cultural shift can be challenging to navigate.
c. Data Accuracy and Consistency: Migrating from manual processes to an MRP system involves digitizing and centralizing data. Ensuring the accuracy and consistency of data during the transition is crucial to prevent errors and discrepancies that may impact system performance and decision-making.
d. Process Reengineering: Implementing an MRP system often involves reengineering existing processes. This requires evaluating and modifying workflows, roles, and responsibilities. Resistance to change or lack of clarity in new processes can hinder implementation success.
e. Technical Integration: Integrating an MRP system with existing enterprise systems, such as ERP or CRM, may pose technical challenges. Compatibility issues, data migration, and system integration complexities need to be addressed during the implementation process.
Importance of Change Management Strategies and Employee Training:
a. Addressing Resistance and Building Buy-In: Change management strategies are essential to overcome resistance and build employee buy-in. Clear communication about the benefits of the MRP system, addressing concerns, involving employees in decision-making, and providing support throughout the transition help alleviate resistance and foster acceptance.
b. Training and Upskilling: Comprehensive training programs are crucial to equip employees with the necessary knowledge and skills to effectively use the MRP system. Training should cover system functionalities, data input and retrieval, reporting, and troubleshooting. Upskilling employees ensures a smooth adoption and utilization of the new system.
c. Process Documentation and Standardization: Change management includes documenting and standardizing processes to ensure consistency and clarity. This documentation helps employees understand new workflows, roles, and responsibilities. It serves as a reference during the transition and provides guidelines for working with the MRP system.
d. Data Management and Accuracy: Implementing an MRP system necessitates robust data management practices. Ensuring data accuracy and consistency is crucial during the transition. Data cleansing, data migration, and establishing data governance processes are essential to maintain the integrity of the system.
e. Ongoing Support and Continuous Improvement: Change management strategies should include ongoing support and continuous improvement initiatives. Providing ongoing training and support post-implementation helps employees adapt to the system and address any challenges. Encouraging feedback and incorporating user suggestions drive continuous improvement of the MRP system and enhance user satisfaction.
In summary, implementing an MRP system and transitioning from manual processes can present challenges related to change resistance, cultural shifts, data accuracy, process reengineering, and technical integration. To overcome these challenges, organizations must employ change management strategies, provide comprehensive training, address concerns, and foster a culture of ongoing support and continuous improvement. By effectively managing the change and empowering employees, organizations can ensure a smooth adoption and maximize the benefits of the MRP system.
B. Data Integrity and Integration
Data Integrity in MRP Systems:
Data integrity is of paramount importance in MRP systems as it directly impacts the accuracy and reliability of the system's outputs and decision-making processes. Here's why data integrity is crucial and the challenges associated with data accuracy and consistency:
Importance of Data Integrity:
a. Accurate Decision-Making: MRP systems rely on accurate and reliable data to generate accurate production plans, material requirements, and resource allocations. Data integrity ensures that decisions made based on the system's outputs are valid and aligned with the organization's goals.
b. Efficient Resource Utilization: Data integrity is essential for optimizing resource allocation. When data is accurate, organizations can effectively plan and allocate labor, equipment, and materials, minimizing downtime, avoiding bottlenecks, and optimizing resource utilization.
c. Inventory Management: Accurate and consistent data in MRP systems is crucial for efficient inventory management. It ensures that the system's calculations and recommendations for inventory levels, reorder points, and safety stock are reliable. This helps avoid stockouts, minimize excess inventory, and reduce carrying costs.
d. Planning and Forecasting: Data integrity is fundamental for accurate planning and forecasting in MRP systems. Reliable historical data and consistent inputs enable organizations to make informed predictions about future demand, production volumes, and resource requirements, facilitating effective decision-making and long-term strategic planning.
Challenges with Data Accuracy and Consistency:
a. Manual Data Entry: Manual data entry increases the risk of errors, inconsistencies, and omissions. Transcribing data from paper-based systems or relying on human input without proper validation processes can lead to data inaccuracies and compromise system performance.
b. Data Duplication and Redundancy: Inaccurate or redundant data entries can result from inadequate data validation and verification processes. Duplicate or redundant data can create confusion, impact reporting accuracy, and cause discrepancies in calculations and planning.
c. Lack of Data Governance: In the absence of proper data governance practices, data quality standards may not be established or enforced. This can lead to inconsistent data formats, inadequate data validation rules, and a lack of clarity regarding data ownership and responsibilities.
d. Integration Challenges: Integrating data from multiple sources or legacy systems into an MRP system can be challenging. Inconsistent data formats, varying data structures, and data migration complexities can compromise data integrity during the integration process.
Integration of MRP Systems with Other Enterprise Systems:
MRP systems often integrate with other enterprise systems, such as Enterprise Resource Planning (ERP) and Customer Relationship Management (CRM) systems, to streamline operations and enhance data exchange. Here's an overview of this integration:
ERP Integration:
MRP systems and ERP systems are closely aligned and often integrated to facilitate seamless data exchange and improve overall operational efficiency. Key aspects of ERP integration include:
a. Data Synchronization: Integration enables the synchronization of data between the MRP and ERP systems. This ensures that relevant information, such as sales orders, inventory levels, production schedules, and financial data, remains consistent across both systems.
b. Streamlined Workflows: Integration between MRP and ERP systems enables streamlined workflows and better coordination between different functions, such as manufacturing, procurement, sales, and finance. It allows for smoother order processing, accurate financial reporting, and improved decision-making.
c. Demand Planning: Integration with ERP systems provides MRP systems with real-time demand data, allowing for accurate demand planning. This integration ensures that the MRP system considers current demand trends, customer orders, and sales forecasts from the ERP system when generating production plans and material requirements.
CRM Integration:
Integrating MRP systems with CRM systems facilitates efficient management of customer-related information, order processing, and sales forecasting. Key aspects of CRM integration include:
a. Customer Order Management: Integration enables the automatic transfer of customer orders from the CRM system to the MRP system. This ensures that customer demands are accurately captured and reflected in the production planning and work order processes.
b. Sales Forecasting: CRM integration provides MRP systems with real-time sales data and forecasts. This integration enhances the accuracy of demand planning and enables organizations to align production capacities and material requirements with expected customer orders.
c. Order Tracking and Customer Communication: Integration allows for seamless tracking of orders and provides real-time updates to customers. It ensures that customers have access to accurate order status information, promoting transparency and enhancing customer satisfaction.
In summary, data integrity is crucial in MRP systems, as accurate and consistent data is essential for decision-making, resource utilization, inventory management, and planning. Challenges related to data accuracy and consistency can arise from manual data entry, duplication, lack of data governance, and integration complexities. Furthermore, integrating MRP systems with ERP and CRM systems enhances operational efficiency, data synchronization, and streamlined workflows, ultimately leading to improved productivity, accurate demand planning, and enhanced customer satisfaction.
C. Continuous Improvement and Optimization
Continuous Improvement and Optimization of Work Order Processes within MRP Systems:
Continuous improvement and optimization are vital for organizations to maximize the benefits of MRP systems and enhance overall efficiency in work order processes. Here's why continuous improvement is necessary and how organizations can leverage data analytics and performance metrics to identify areas for improvement:
Need for Continuous Improvement and Optimization:
a. Adaptation to Changing Demands: Market demands, customer requirements, and internal processes evolve over time. Continuous improvement ensures that work order processes within MRP systems remain aligned with changing demands, allowing organizations to stay competitive and meet customer expectations.
b. Streamlined Workflows: Continuous improvement helps identify and eliminate bottlenecks, redundancies, and inefficiencies in work order processes. Streamlining workflows through optimization minimizes waste, reduces lead times, and improves overall operational efficiency.
c. Cost Reduction: Continuous improvement and optimization aim to identify cost-saving opportunities. By analyzing work order processes, organizations can identify areas where costs can be reduced, such as minimizing material waste, improving resource utilization, or optimizing production schedules.
d. Quality Enhancement: Continuous improvement helps organizations enhance the quality of their products and services. By analyzing data and performance metrics, organizations can identify areas where quality issues may arise and implement measures to prevent or address them, thereby improving customer satisfaction and reducing rework.
Leveraging Data Analytics and Performance Metrics:
a. Data Collection and Analysis: MRP systems generate vast amounts of data related to work order processes, resource utilization, production output, and cycle times. Organizations can leverage data analytics tools to collect, analyze, and visualize this data, gaining insights into the performance of work order processes.
b. Key Performance Indicators (KPIs): Organizations can define and track KPIs related to work order processes, such as on-time delivery, production cycle time, resource utilization, or material waste. Performance metrics provide a quantitative measure of process efficiency and serve as a benchmark for continuous improvement efforts.
c. Root Cause Analysis: Data analytics allows organizations to conduct root cause analysis to identify underlying factors contributing to inefficiencies or issues in work order processes. By analyzing patterns, trends, and correlations in the data, organizations can pinpoint the root causes of problems and implement targeted improvements
d. Process Optimization: Data analytics can highlight process bottlenecks, identify areas of underutilized resources, or reveal opportunities for automation. With this information, organizations can optimize work order processes, redesign workflows, or make informed decisions about resource allocation to improve overall efficiency.
e. Predictive Analytics: Advanced data analytics techniques, such as predictive analytics, enable organizations to forecast future demand, optimize production schedules, or proactively identify potential issues. By leveraging predictive analytics models, organizations can make data-driven decisions to prevent delays, minimize disruptions, and optimize resource utilization.
f. Continuous Monitoring and Feedback: Organizations should establish a feedback loop by continuously monitoring performance metrics, reviewing data analytics insights, and gathering feedback from stakeholders. This ensures that improvements are tracked, evaluated, and refined over time, leading to a culture of continuous improvement.
In summary, continuous improvement and optimization of work order processes within MRP systems are essential for organizations to adapt to changing demands, streamline workflows, reduce costs, and enhance quality. By leveraging data analytics and performance metrics, organizations can gain insights into process performance, identify areas for improvement, and make data-driven decisions. This iterative process of analyzing data, implementing improvements, and monitoring outcomes enables organizations to achieve higher levels of efficiency, productivity, and customer satisfaction.
Frequently Asked Questions (FAQs) Associated with Leveraging MRP Systems for Seamless Work Order Processes
Following, we’ve discussed detailed frequently asked questions (FAQs) associated with leveraging MRP systems for seamless work order processes. Let’s learn:
Q1: What are MRP systems and how do they manage manufacturing operations?
A: MRP systems, short for Manufacturing Resource Planning systems, are software solutions that help organizations manage and control various aspects of their manufacturing operations. They automate processes such as work order creation, tracking, and resource allocation to ensure efficient production.
Q2: How do MRP systems handle work order creation and tracking?
A: MRP systems automate work order creation based on factors like production demand and inventory levels. They generate work orders with detailed instructions and track their progress through different stages of production, providing real-time visibility into their status.
Q3: What is the significance of work orders in manufacturing operations?
A: Work orders are essential documents that communicate the tasks, resources, and specifications required to complete a specific job or project within a manufacturing operation. They provide clarity, facilitate resource allocation, coordinate workflow, and enable tracking and accountability.
Q4: What challenges do organizations face when managing work orders manually?
A: Organizations face challenges such as manual data entry errors, limited visibility into work order status, inefficient communication and coordination, and difficulties in resource allocation when managing work orders manually. These challenges can lead to delays, errors, and inefficiencies in the production process.
Q5: How do MRP systems optimize resource allocation for work orders?
A: MRP systems optimize resource allocation by considering factors such as resource availability, skills, task priorities, and capacity. They automate the assignment of resources, ensuring that the right resources are allocated to each work order to maximize efficiency and productivity.
Q6: What is capacity planning, and how does it ensure efficient resource utilization in MRP systems?
A: Capacity planning is the process of assessing available production capacity and aligning it with the demand for work orders. In MRP systems, capacity planning ensures efficient resource utilization by balancing workloads, optimizing production schedules, and proactively addressing potential bottlenecks.
Q7: Why is data integrity important in MRP systems, and what challenges are associated with it?
A: Data integrity is crucial in MRP systems as it ensures the accuracy and reliability of the system's outputs and decision-making processes. Challenges associated with data integrity include manual data entry errors, data duplication, lack of data governance, and complexities in integrating data from various sources.
Q8: How do MRP systems integrate with other enterprise systems like ERP and CRM?
A: MRP systems integrate with enterprise systems like ERP and CRM to streamline operations and enhance data exchange. Integration with ERP systems enables data synchronization, streamlined workflows, and demand planning. Integration with CRM systems facilitates customer order management, sales forecasting, and improved customer communication.
Q9: Why is continuous improvement important in work order processes within MRP systems?
A: Continuous improvement is essential to adapt to changing demands, streamline workflows, reduce costs, and enhance quality in work order processes. It ensures that organizations remain competitive, maximize efficiency, and deliver value to customers.
Q10: How can organizations leverage data analytics and performance metrics to improve work order processes in MRP systems?
A: Organizations can leverage data analytics and performance metrics to identify areas for improvement, analyze root causes, optimize processes, and make data-driven decisions. Data analytics provides insights into performance, while performance metrics serve as benchmarks for continuous improvement efforts.
Wrapping Up
Implementing an MRP system and leveraging its capabilities for seamless work order processes brings numerous benefits to organizations. From automating work order creation and scheduling to optimizing resource allocation and facilitating material planning, MRP systems play a pivotal role in streamlining manufacturing operations.
The integration of MRP systems with other enterprise systems, such as ERP and CRM, enhances data exchange, streamlines workflows, and improves overall operational efficiency. By ensuring data integrity, organizations can rely on accurate and reliable information to make informed decisions and drive continuous improvement.
Change management strategies and comprehensive employee training are essential to successfully implement MRP systems and overcome resistance to change. By addressing challenges associated with data accuracy and consistency, organizations can maintain reliable data for optimal system performance.
Continuous improvement and optimization of work order processes within MRP systems are crucial to adapt to changing demands, streamline workflows, reduce costs, and enhance quality. Leveraging data analytics and performance metrics enables organizations to identify areas for improvement, make data-driven decisions, and foster a culture of continuous improvement.
In conclusion, by leveraging MRP systems for seamless work order processes, organizations can achieve greater efficiency, improved resource utilization, enhanced customer satisfaction, and a competitive edge in the dynamic manufacturing landscape. Embracing the power of MRP systems and continuously optimizing work order processes pave the way for operational excellence and long-term success.
How Deskera Can Assist You?
Deskera ERP and MRP systems help you to keep your business units organized. The system's key features of demand forecasting with Deskera include as follows:
- Establish Demand Forecasting Process
- Automate Data Collection
- Monitor Market Trends
- Analyze Historical Data
- Estimate Future Demand
- Adjust Production Levels
- Manage Supply Chain...and much more!
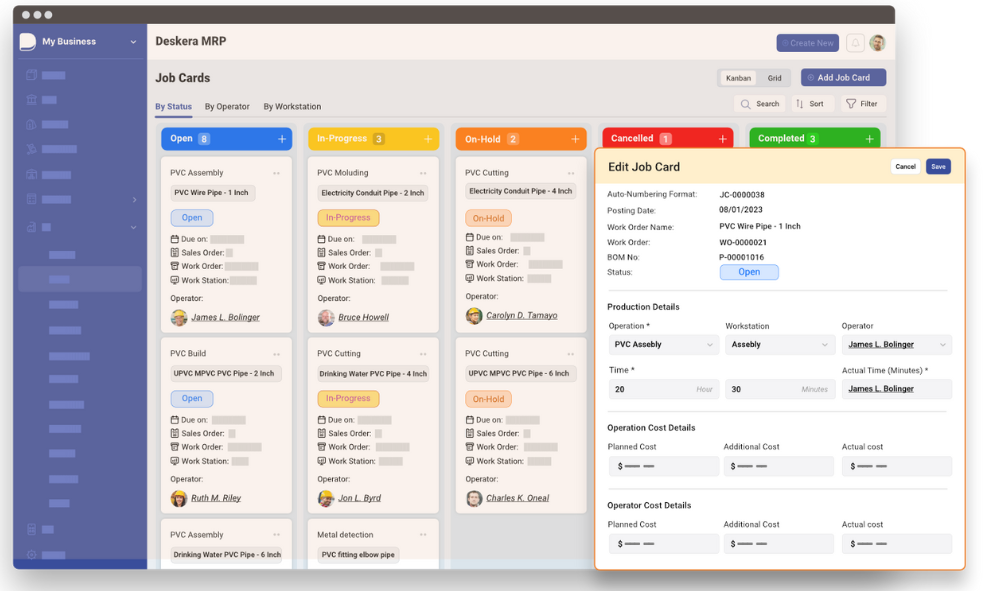
- Deskera's integrated financial planning tools enable investors to better plan and track their investments. It can assist investors in making faster and more accurate decisions.
- Deskera CRM is a powerful solution that manages your sales and helps you close deals quickly. It not only enables you to perform critical tasks like lead generation via email, but it also gives you a comprehensive view of your sales funnel.
- Deskera Books allows you to better manage your accounts and finances. Maintain good accounting practices by automating tasks like billing, invoicing, and payment processing.
- Deskera People is a straightforward tool for centralizing your human resource management functions.
Final Takeaways
We've arrived at the last section of this guide. Let's have a look at some of the most important points to remember:
- Manufacturing Resource Planning (MRP) systems are powerful software tools designed to streamline and optimize the work order processes within manufacturing organizations.
- These systems integrate various functions, such as inventory management, production planning, and scheduling, to ensure efficient utilization of resources and timely completion of work orders.
- Manufacturing Resource Planning (MRP) systems are software solutions specifically designed to assist organizations in managing and optimizing their manufacturing operations.
- MRP systems calculate material requirements based on the Bill of Materials (BOM), production schedules, and inventory levels. They generate purchase requisitions or release manufacturing orders to procure materials in a timely manner. This helps organizations avoid material shortages, minimize stockouts, and optimize procurement costs.
- By providing real-time visibility into inventory levels, MRP systems help organizations optimize inventory holdings, reduce stockouts, and avoid excess inventory. This leads to cost savings, improved cash flow, and better inventory turnover ratios.
- Work orders provide detailed instructions, including the scope of work, materials required, and specific procedures to follow. They ensure that everyone involved understands the objectives, timelines, and quality standards associated with the job.
- MRP systems analyze the capacity of production resources and balance workloads across different work centers or production lines. By considering the available capacity and the estimated time for each operation, the system generates an optimized schedule that minimizes idle time and maximizes resource utilization.
Related Articles
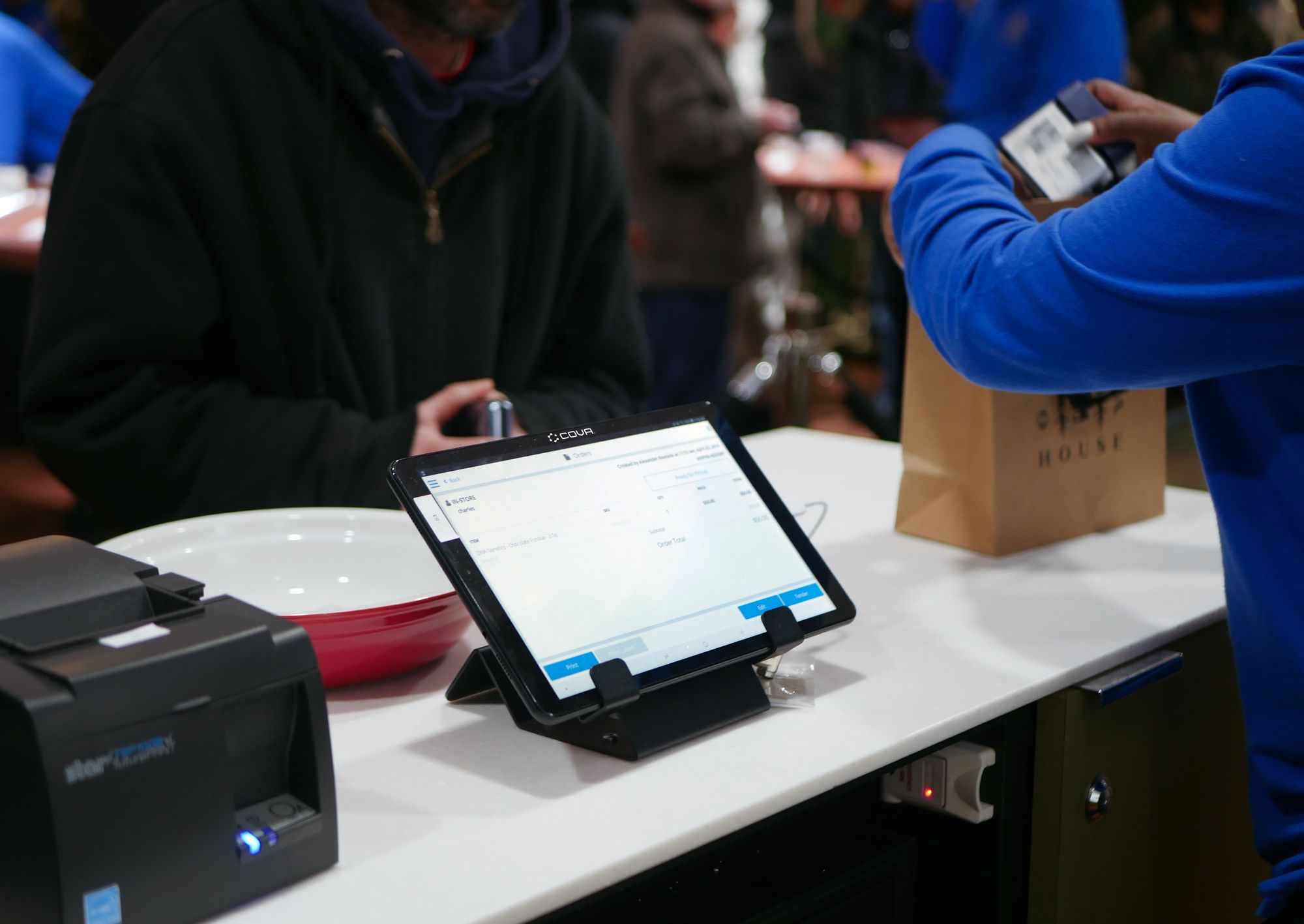
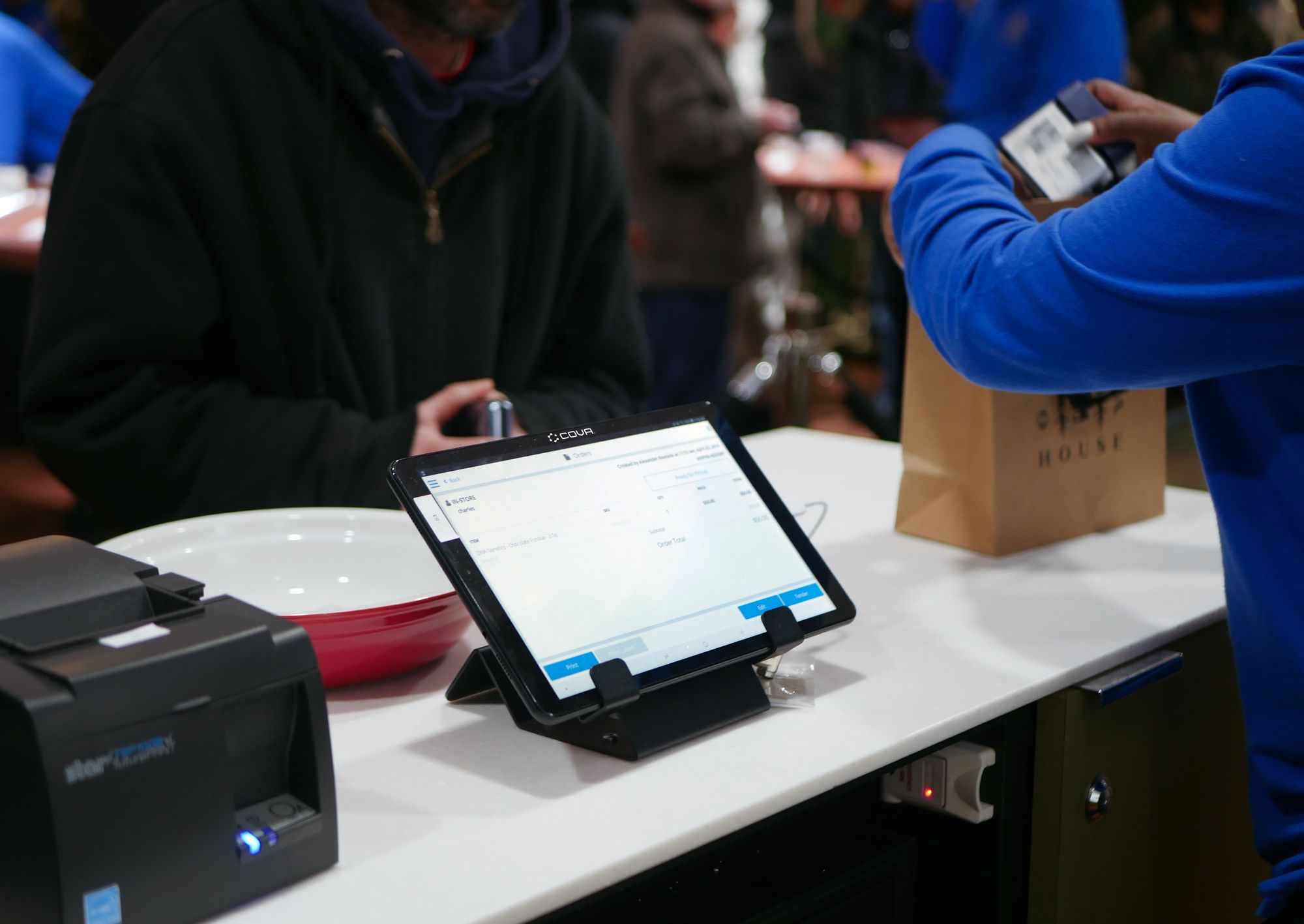
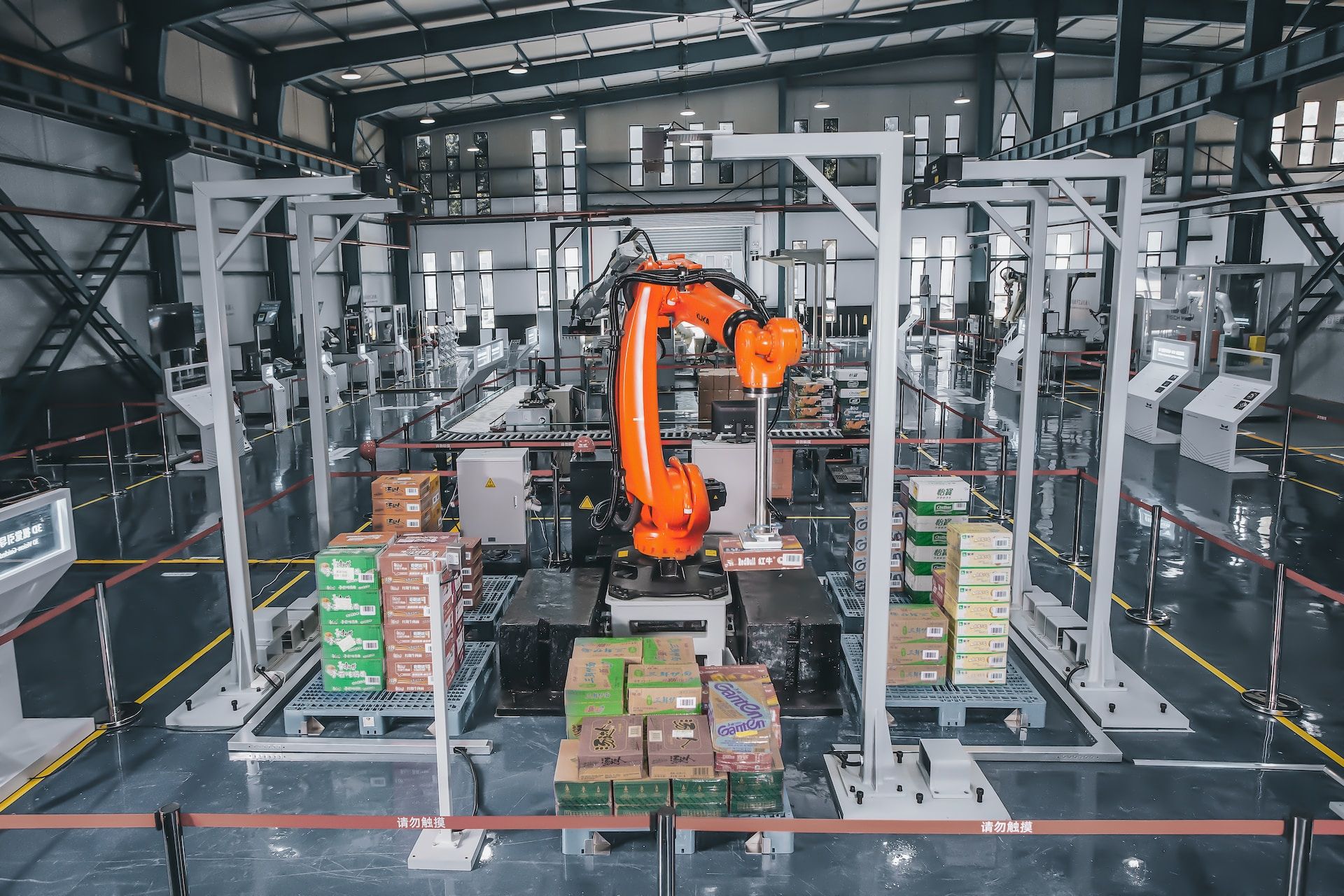
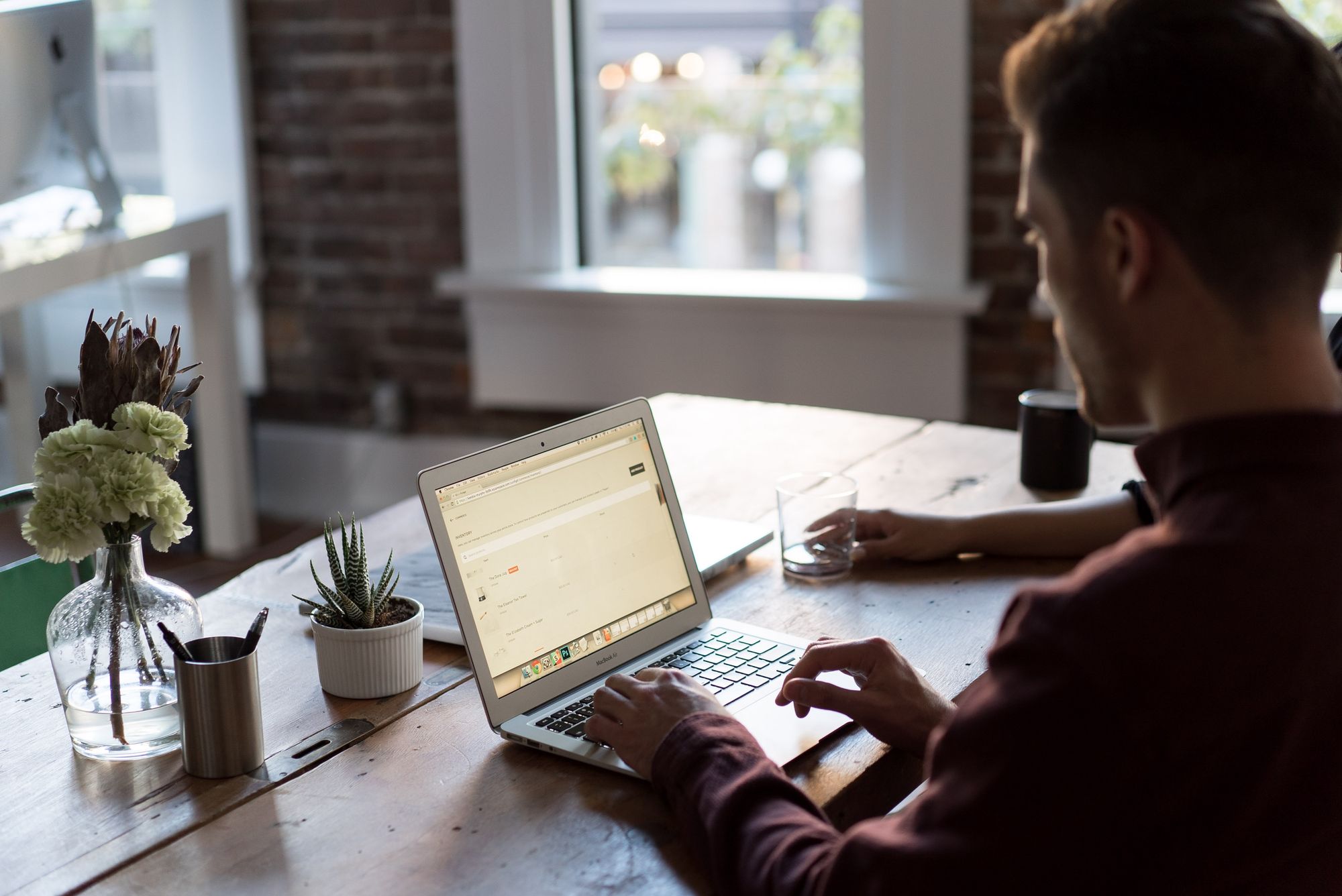
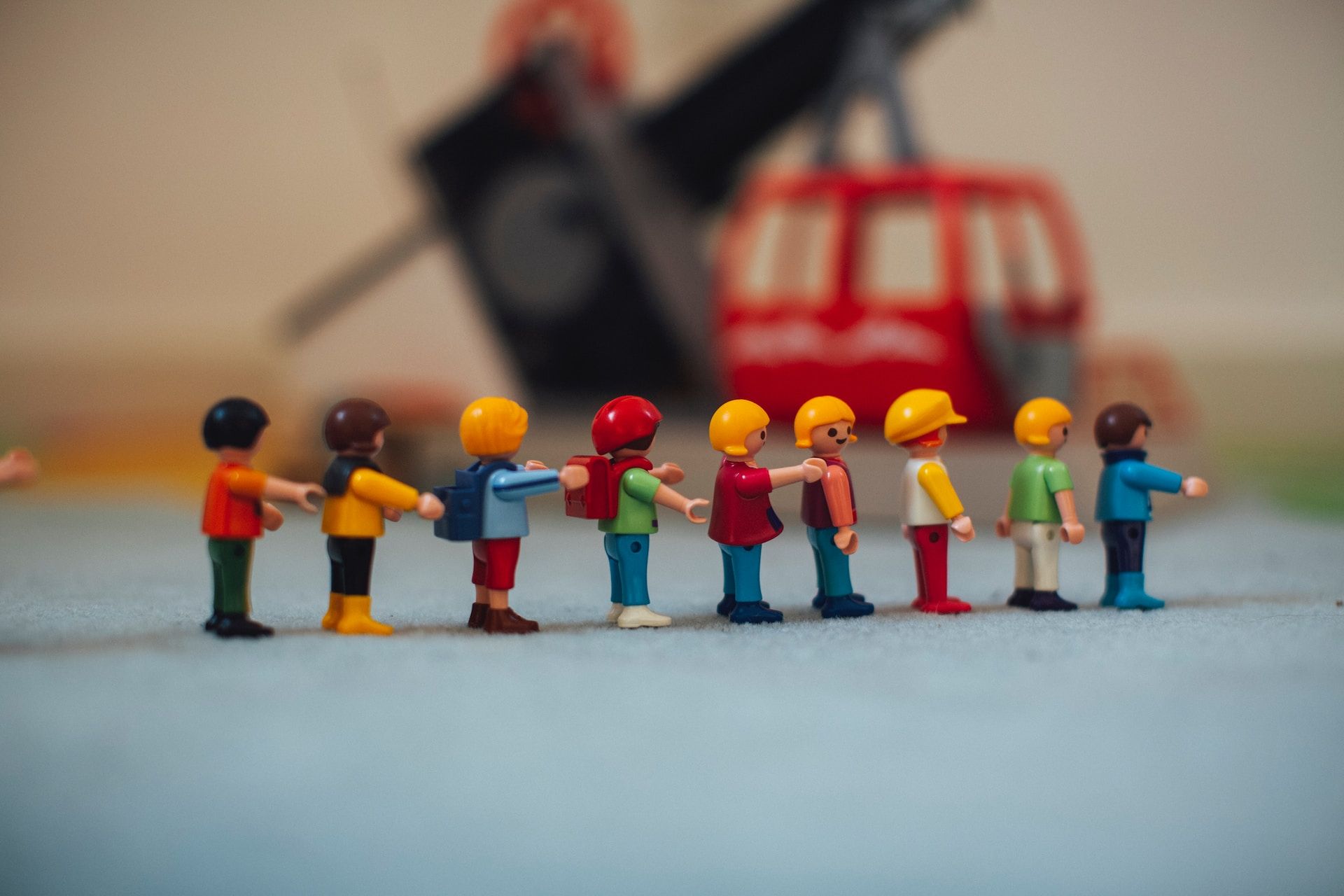