How to keep your cargo in perfect condition? Seems easy enough, right? Wrong! Without even realizing it, you could be taking actions that endanger your shipment.
The freight industry is expanding at astounding rates, and shipping is a significant industry. However, with the exploding popularity of online shopping, this growth has brought along some accidents as well. Therefore, it's critical to understand what you must do specifically to protect your cargo.
In today’s guide, we’ll learn on how you can keep your cargo in perfect condition, and its related concepts. Let’s take a look at the table of content ahead:
- Common Causes of Cargo Damage
- Parties that Physically Handle Cargo
- Top Tips to Avoid Cargo Damage in the Supply Chain
- Cargo Shifting and Weight Distribution
- Dunnage
- Security
- Choosing the Right Container
- The Container Check
- Consider Safety and Unpacking
- Knowing the Specific Documentation and Inspection Requirements
- Responsibilities of the Shipping Line with Respect to Cargo
- What happens Next in the Case of Damaged Cargo?
- Defending Against the Dangers of Cargo Damage
- Conclusion
- How Deskera Can Assist You?
Let's get started!
Common Causes of Cargo Damage
Following, we’ve discussed some common causes of cargo damage. Let’s learn:
1. Improper Packing:
Cargo that is inadequately packed, or not packed at all, is vulnerable to damage from shifting, moisture, and other environmental factors. Care should be taken to ensure that all items are properly secured, padded, and boxed with appropriate materials that will protect them from damage during transit.
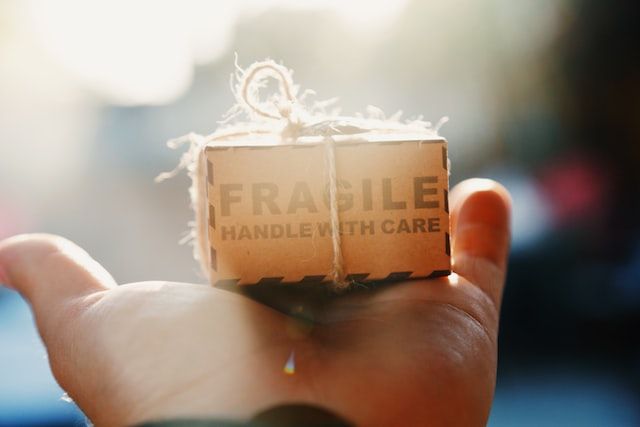
2. Poorly Designed Packaging:
Even when cargo is properly packed, if the packaging itself is poorly designed, it can still be damaged in transit. Packaging should be designed to withstand the rigors of transportation and be able to protect its contents from impacts, bumps, and other forces that might cause damage.
3. Inclement Weather:
Inclement weather, such as rain, snow, wind, and extreme temperatures, can all cause cargo to be damaged. Moisture, in particular, can corrode metal containers, weaken cardboard boxes, and cause other types of damage.
4. Improper Loading:
Cargo that is not loaded securely, or is overloaded, can easily be damaged in transit. Care should be taken to ensure that cargo is properly secured and loaded on to the transport vehicle in a way that will minimize the risk of damage.
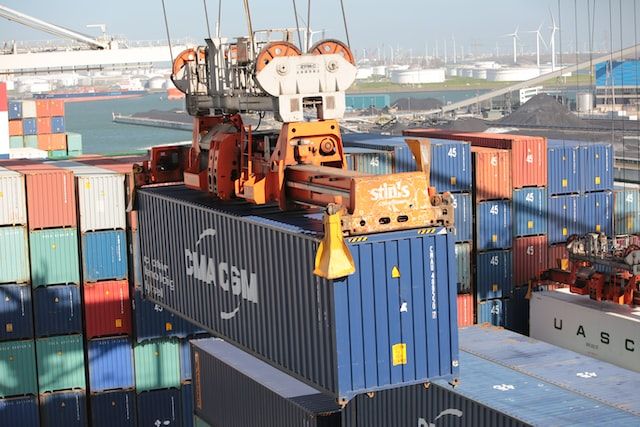
5. Poor Road Conditions:
Potholes, rough terrain, and other poor road conditions can damage cargo during transit. It is important to check the road conditions before a shipment is sent and to ensure that the transport vehicle is suitable for the journey. It may also be necessary to use protective materials or packaging to help protect the cargo from damage.
Parties that Physically Handle Cargo
The following parties may physically handle cargo on a typical international full container shipping route:
- Supplier/factory loading the cargo
- Local trucker delivering the cargo to a local warehouse
- The local dray company moving the cargo from the warehouse to the terminal
- The origin terminal
- Transshipment terminal
- Arrival port terminal
- Customs or the customs warehouse (if there are any customs hold)
- The local trucker at the arrival port for final delivery
The container is handled physically at each of these locations by different parties.
When at sea, rough waters are common for ships. Cargo that isn't properly secured will inevitably move. The most prevalent sources of cargo damage include water damage, impacts to the container, and damages from improper lashing and stuffing.
Following, we've discussed them in detail. Check out:
Water Damage
Water damage in cargo can cause significant losses for both the shipper and the carrier. It can cause damage to the goods contained in the shipment, resulting in loss of value or even total destruction.
Moreover, it can also cause corrosion and rusting of the cargo container and other parts of the ship, resulting in costly repairs or replacement.
Additionally, water damage can lead to mold growth, which can cause health risks to those handling the cargo. Finally, water damage can also lead to a delay in delivery and a decrease in customer satisfaction.
Ineffective Stuffing and Lashing
The importance of good container stuffing cannot be overstated. Shifting of the cargo, uneven weight distribution, poor container selection, poor pallet loading, and poor labelling are the most common causes of cargo damage.
Top Tips to Avoid Cargo Damage in the Supply Chain
Since the supply chain plays a significant role in your company, you must make sure that the product is delivered to clients in acceptable shape.
Further, you must make sure the product is delivered unharmed to satisfy any customer, save money, avoid rework loops, and promote short-, medium-, and long-term business growth.
Following, we’ve discussed some important recommendations that will help your supply chain experience less freight damage.
1. Adequate Packaging Procedures to Prevent Shipment Damage
The first and perhaps most crucial step in minimizing cargo damage is remembering this. Using the right packing management techniques will lower overall overhead costs because packaging costs represent a relatively small portion of all supply chain expenses. Pick the appropriate size and package.
Ensure impact protection is provided but refrain from using too much compression or slack. Avoid any kind of damage, including rips, dents, tears, bumps, punctures, and water damage.
Keep the package's maximum weight restriction in place. Foam or bubble plastic can be used to close up any gaps inside the box. Use spill-resistant sealing procedures with strong adhesive tape.
2. Employ Adequate Palletizing Techniques
To avoid packaging touching the pallet's edges or leaving empty spaces between packages, standardize the sizes of your packages and match them to the proper size of pallets. Use corner posts and stretch film to help each handle unit stay in place.
It takes the correct amount of wrapping and tension to hold items on pallets. Don't stack boxes like "pyramids"; stack them like bricks instead. Pallets must be frequently inspected and rotated in order to keep an ample supply of serviceable pallets on hand.
For big and bulky products, a reliable strapping solution that can reliably secure heavy weights is required.
Check the following points on how you can employ this technique:
1. Group products of similar size, shape, and weight together.
2. Stack the heaviest items at the bottom of the pallet.
3. Shrink wrap, stretch wrap, or metal or plastic strapping can be used to secure the weight.
4. Use dunnage or other materials to fill any gaps or voids in the pallet.
5. Put a cover over the pallet to shield it from moisture, grime, and dust.
6. Place a pallet jack or a hand truck under the pallet for easy movement.
7. Tag the pallet with proper identification, including the weight and number of pieces.
8. Label the pallet with destination information, including the customer's name, address, and zip code.
3. Implementing Proper Labelling to Save Personnel Resources and Avoid Additional Handling
During the shipping process, labels assist shippers in making decisions. It is important to mark the content's tolerance for additional weight. Mention the maximum weight that the box or package can support before being crushed as well as a warning that the contents are fragile.
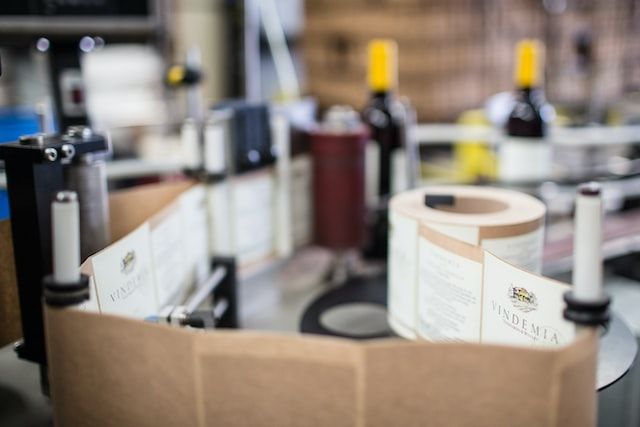
Remember that each pallet should have a label that is unblemished, damage-free, concise, and easy to read.
Check the following points that will help you with labelling process:
1. Ensure that all products are properly labelled with clear and concise information.
2. Utilize automated labelling processes to ensure accuracy and efficiency.
3. Ensure labels include all necessary information such as product name, weight, lot number, expiration date, etc.
4. Utilize barcode and RFID technology to ensure accuracy and reduce manual handling.
5. Train personnel on proper handling and labeling procedures.
6. Implement a tracking system to monitor labelling accuracy and overall labeling process.
7. Implement a feedback system to ensure labelling accuracy and to address any issues quickly.
8. Utilize a system to track and monitor labeling activities to ensure labeling accuracy.
9. Implement a quality assurance system to ensure proper labeling and reduce potential for errors.
4. Optimize your Loading Techniques
Stable and consistent stacking is required. Equal weight distribution across the pallets is required, and the height must remain constant. Place the heaviest load on top of the lightest load.
Extensive documentation, tried-and-true techniques, and procedures are essential when it comes to loading freight. As said previously, to protect the products from shifting, don't stack boxes or pallets twice, use a cushion to stop swings from damaging the products, and fill in any gaps with the appropriate amount of dunnage.
Check the following points:
1. Implement an integrated cargo management system: An integrated cargo management system can help streamline the loading process by automatically tracking all cargo information, including quantity, size, and weight, and quickly identifying any discrepancies. This can help ensure that the cargo is loaded onto the correct vessel and that the load is balanced and secure.
2. Utilize loading automation technology: Automated loading systems can help reduce the amount of physical labor involved in loading cargo, as well as reduce the risk of human error. Automated loading systems can also monitor the load and quickly detect any discrepancies.
3. Utilize electronic weigh scales: Electronic weigh scales can quickly and accurately measure the weight of the cargo and help ensure that the load is balanced and secure.
4. Adopt a proactive maintenance plan: Regularly maintaining loading equipment such as conveyors and forklifts can help prevent malfunctions and delays in the loading process.
5. Ensure proper labeling and documentation: Proper labeling and documentation can help reduce the risk of errors and ensure that the correct cargo is loaded onto the correct vessel.
5. Include an Effective Containerization Procedure
In essence, a container is a package that, due to its robustness and ease of handling by carriers with the proper tools, enables the storage and transportation of items without the risk of a collision.
Find the container's center of gravity and distribute the weight evenly across the ground, leaving no empty spaces. Make sure the containers are immaculate and devoid of any signs of prior transit by inspecting them.
Use longitudinal and/or transverse lashings as needed, keeping voids to a minimum. When the container is opened, keep a safe distance away from the doors without applying any pressure to avoid any mishaps.
6. Stop Container Sweating and Rain
It is less expensive to prevent harm than to repair it. Make sure there is adequate ventilation, and to keep containers dry, use the right kind of pallets and desiccants.
Implement the following points:
- Put tarps on top of the container to block rainwater.
- Make sure the container is sealed properly and that there are no holes or cracks that can allow moisture to enter.
- To lower the humidity inside the container, use a dehumidifier.
- Use a waterproof cover or tarp to shield the container from the elements if it is kept outside.
- Regularly check the container to ensure sure there are no fractures or gaps that could allow rain or perspiration to enter.
- If the container will be left outdoors for an extended period of time, consider using a container shelter or a tent to keep it dry.
7. The Importance of Warehouse Conditions in Reducing Cargo Damages
The first step to smarter working is a logical warehouse management layout. Cross docks and warehouses should have clear, unobstructed aisles so that employees and equipment can move about easily.
By using the right system, you can make more space available in your warehouse, guard against product damage, and hasten truck loading and unloading.
8. Reliable Material-Handling Tools
Utilize machinery that can adapt to the environment well to increase efficiency and speed while reducing accidents and bad outcomes. Make that all of your material-handling equipment is operating correctly. It includes strapping machines, trucks, pallet jacks, cranes, forklifts, and loading/unloading systems.
Following, we’ve discussed them in detail. Check out:
1. Pallet jacks: Pallet jacks are a great material-handling tool for cargo to be in perfect condition. They are designed to lift and transport heavy loads without damaging the cargo.
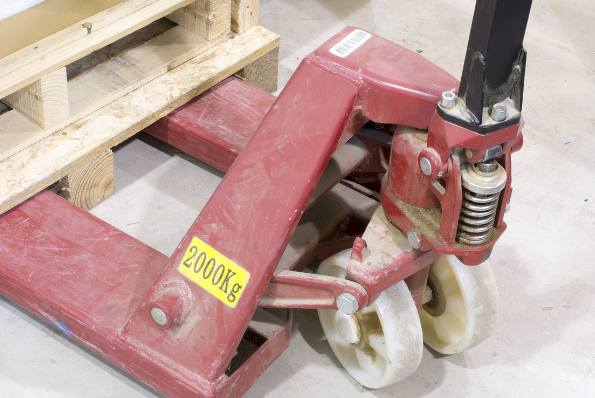
2. Lift trucks: Lift trucks are a great tool for handling large and heavy loads. They feature a broad variety of attachments for carrying various types of cargo and can lift up to 8,000 lbs.
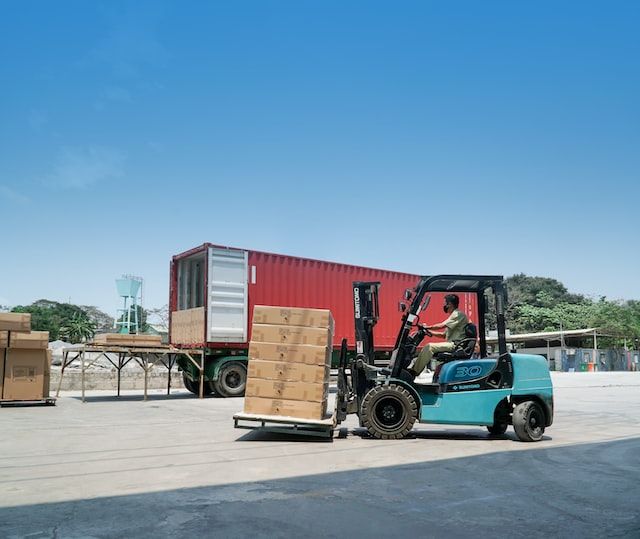
3. Dolly carts: Dolly carts are a great tool for moving bulky items. They are designed to support heavy loads and can be used to move large and bulky items with ease.
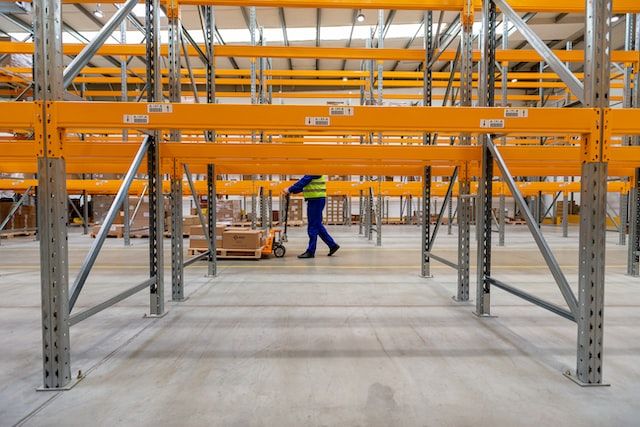
4. Forklifts: Forklifts are a great tool for moving large and heavy loads. They are designed to carry heavy loads and are able to lift and move them with ease.
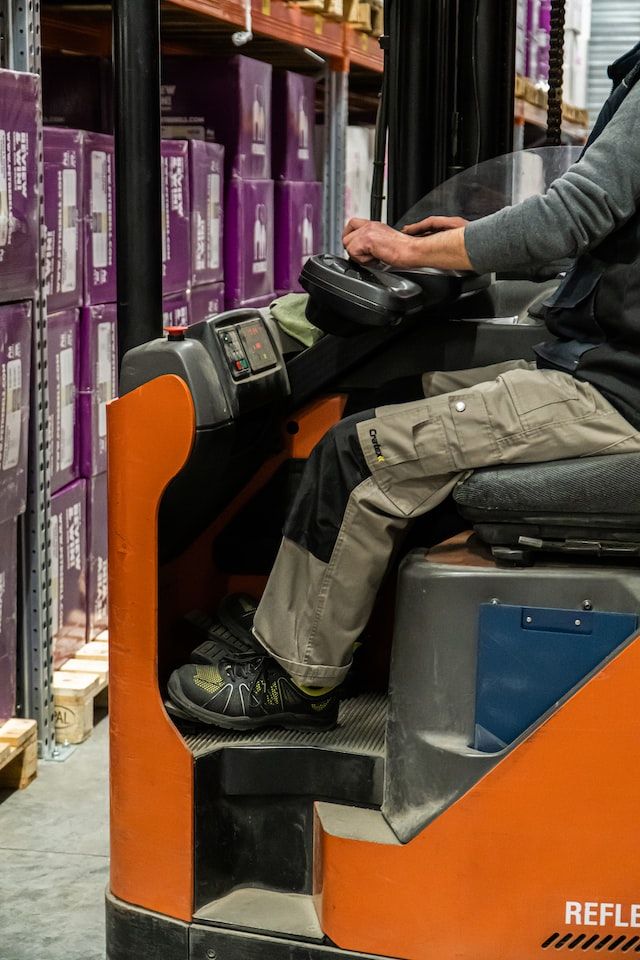
5. Conveyor belts: Conveyor belts are a great tool for moving large loads in a safe and efficient manner. They are designed to move large items with ease and are perfect for moving cargo in perfect condition.
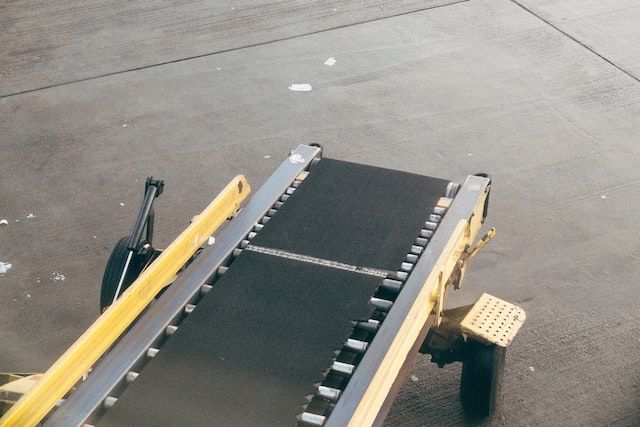
9. Enhance your Handling Techniques
Employees are compelled to handle packages improperly and damage products for a variety of reasons, including poor judgement, a lack of work ethic, inadequate training, and a high-pressure environment to produce more. Employees must obtain sufficient training on how to operate machinery safely at work.
Operators of forklifts, for example, need to be aware of weight limitations when lifting heavy objects. Maintaining your workforce's training enables you to ensure maximum productivity, minimal accidents, and product damage.
10. Work with a Reliable 3PL Provider to Ensure that your Cargo is in Top Shape
The top 3PL companies to use if you want your cargo to be in perfect condition are DHL, FedEx, and UPS. You can be confident that your goods will arrive in the same condition it did when it left your facility because to the lengthy history of dependability and safety that these companies have demonstrated in the delivery industry.
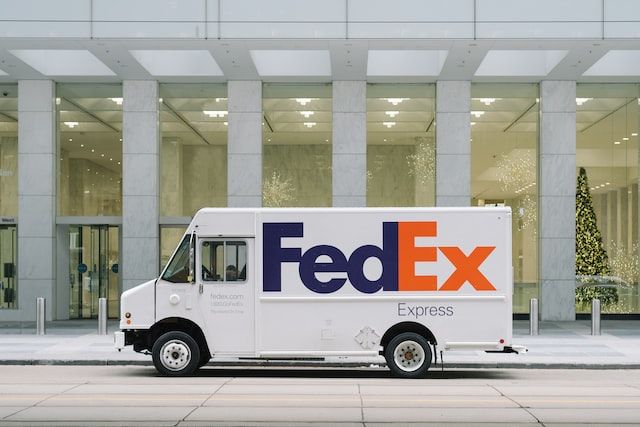
You can boost productivity, reduce damage that occurs during transit, let your company focus on its core skills, and ultimately improve service level and return on investment by outsourcing the administration of your logistics to a 3PL provider (ROI).
Consider the cost of moving the items as well as their security. Increase the packaging's tensile strength to account for Less Than Truck Load (LTL) shipments, where more manipulation takes place.
11. Develop a Supply Chain Strategy
Make a plan to lessen product damage and enhance the indicators that guarantee the correct delivery of the things to your client and keep it up to date. This plan should cover everything from packaging design to consolidation strategies and the choice of suitable transport & logistics modes.
12. Establish and Uphold a Culture of Constant Improvement
Continuous improvement is the process of constantly seeking for ways to make the supply chain more efficient. Make sure your company has an automated container loading system that enables waste operations that do not create value for the consumer to be identified and eliminated.
Organizations should foster an atmosphere of trust and cooperation in order to develop and maintain a continuous improvement culture. A culture of continuous improvement should be championed by senior leadership, and actively promoted and supported by all employees. It should be implemented in all areas of the business, from the production line to marketing and sales.
Organizations should also encourage employees to be creative and innovative when it comes to finding ways to improve processes and products. Employee motivation and reward should be achieved through incentives such as rewards and recognition. Employees should receive training to ensure they have the information and abilities needed to properly execute changes.
Finally, organizations should use data to measure and track the effectiveness of the improvement initiatives. This will help to ensure that the organization is making progress and that the initiatives are meeting the desired goals.
Cargo Shifting and Weight Distribution
When loading a vehicle, weight distribution and cargo movement are crucial factors to take into account. Cargo shifting is the movement of cargo from one location to another within the vehicle, either horizontally or vertically.
Weight distribution is the process of ensuring that the weight of cargo is evenly distributed across the vehicle, both horizontally and vertically. This enhances the vehicle’s overall performance and stability.
Improper cargo shifting and weight distribution can lead to an unbalanced vehicle, which can cause the vehicle to be difficult to control or cause damage to the vehicle. When loading a vehicle, it is important to make sure that cargo is evenly distributed and securely tied down to prevent movement during transit.
Dunnage
Dunnage is a type of equipment used in the shipping industry to create a buffer between items and walls of a container, reduce shifting or other damage due to movement of the items during transit, and provide additional protection to fragile items. A number of materials, such as wood, foam, plastic, and cardboard, can be used to create dunnage.
Further, it is placed between items, along walls and corners, and on top of items to prevent them from shifting and potentially becoming damaged during transit. Dunnage is also used to ensure items remain in place during transportation and minimize the amount of space taken up by the items.
Security
No seal can stop a criminal. Its main objective is to inform individuals of the time and place of a container break-in. Bolts that seal are desirable. Always check the seal to make sure it is the right sort. Pull on the seal to make that it is properly locked.
At all times, keep a log of the date and the seal number. The seal number must be entered on all shipping documents before they are stored away in a secure location. Never let someone else seal a container on your behalf. Who can verify their sincerity?
Finally, schedule a convenient time for the delivery of your cargo to minimize the amount of time the container is outside and the possibility of theft.
Choosing the Right Container
The right container to use for cargo depends on the size and type of cargo that needs to be shipped. Generally, the larger the cargo, the larger the container needed. The type of cargo will also determine the best container to use.
For smaller cargo, such as documents and small packages, a standard 20-foot container might be sufficient. These containers are typically used for general cargo and can easily be loaded and unloaded.
For larger cargo, such as heavy machinery and vehicles, a 40-foot container might be the best option. These containers are designed to accommodate heavier cargo and can be loaded from the top or the side.
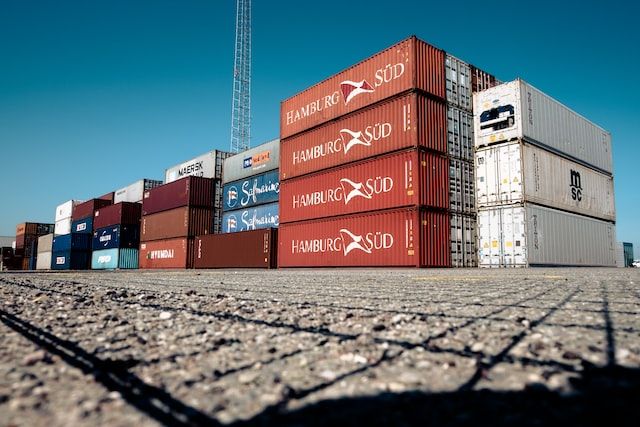
It is also important to consider the type of cargo when choosing the right container. For hazardous cargo, such as chemicals or flammable materials, special containers must be used to ensure the safety of the cargo and those transporting it.
In addition, for food-related cargo, insulated containers are often used to ensure that the cargo stays fresh and is not affected by temperature fluctuations during transit.
Finally, if the cargo needs to be shipped overseas, it is important to choose the right container for international shipping. These containers need to be certified to meet international regulations and standards.
Overall, the right container for shipping cargo overseas depends on the type of cargo, destination, and regulations of the destination country. It is important to ensure that the container meets all international regulations and standards in order to ensure safe and secure shipment of the cargo.
Ultimately, make sure that you consider the size and weight of the cargo, as well as any special requirements for shipping the cargo, in order to select the best container for the job.
The Container Check
For your own peace of mind, take your time looking over the container. It is mainly because residues could be hazardous or contaminate your shipment. And that needs to be avoided at all costs.
Also, make sure that you return the container for cleaning if you are unsure. Watch for structural issues such ruined post rails or corner castings. As a result, cargo can experience harm. Make sure the doors can be locked firmly. Reject the container if in doubt!
Keep the container dry at all times. Are there any openings caused by using the tools that might let moisture in? Make that the gaskets are not brittle, worn, or damaged. Keep an eye out for any stains around the door since they may point to a prior leak.
Detect corrosion (rust is porous). To check for tiny holes in the container, shine a light through it.
Finally, beware of taped-up vents and out-of-date labels because they may be misleading and result in delays.
Carry your Container with Care
The likelihood of cargo damage can be considerably reduced by investing just a few minutes. If you fail to discover defects that a court finds that due diligence would have disclosed, you can find that your insurance claim is drastically reduced or even dismissed.
Prepare a thorough Packing Plan
Most operators charge by container load. The more stuff you can put inside the container, the cheaper it will be per unit to ship your goods. It is a good idea to develop a packing strategy in order to increase the fill factor.
Remember that the likelihood of the cargo shifting is decreased by the container having less vacant spots. If the cargo is not entirely inside the container, start by evenly covering the floor area. If openings must be made, try to make them in the center to allow for securing the cargo by slamming it up against the side walls.
Equal amounts of weight must be applied from side to side and end to end. Always keep the center of gravity as low as feasible. Never exceed the container's maximum cargo or the permissible weights for the trip.
A vertical separator can be employed to hold the upper layer in place if it does not extend the entire length of the container. If necessary, use an interlocking stow. Unitized goods are frequently more stable and easier to load. To stop the cargo from spilling out when the doors are open, the face of the stow should be strongly shored and blocked.
The heavier items should be placed in the center of the container. Lighter objects should be placed on top of larger, heavier items in the container's bottom. Always stack liquids on top of dry goods.
In order to prevent leaks from occurring from vibration, store drums and barrels with the bung facing up and, if at all possible, apart. To minimize damage, it is advised to utilize two layers of dunnage.
Ensure that you are aware of the lashing locations' safe loading limitations. Never mix unsuitable cargoes, such as frequently perspiring cargoes with moisture-sensitive cargoes.
Consider Safety and Unpacking
Don't forget to consider the equipment the consignee will use to unpack the container. Prior to opening a container, always read the labels and warnings on the outside.
You must leave the area right away if the contents appear to be leaking or are in any other way hazardous. Move the container to a safe location and call the fire department if it is particularly hot. Allow any gas to escape before placing it in the container.
Always take note of how the container looks from the outside. Are there any dents, rust, or holes present? Check the interior of the container for any damage and note it. It is best to snap pictures whenever you can because they might support any claims.
Make sure the seal is the right kind and that the supporting documentation's serial number matches. Has the seal been tampered with? Keep the seal intact until you're sure the cargo is all there and in working order.
It is advised to wear overalls and safety goggles. Utilizing a strap that is cinched around the door stanchions makes logical. By doing this, the doors won't open, and things won't fall on you. You can remove the strap and fully open the container once you are certain that you are secure.
In order to avoid damage from the wind slamming them shut, secure doors when they are open. The container needs to be cleaned to the level that you would anticipate receiving it.
Check the following points when considering safety and unpacking of cargo. Let’s learn:
1. Prior to unpacking the cargo, inspect it for any signs of damage or tampering.
2. Carefully unpack the cargo and inspect it for any signs of damage, tears, or punctures.
3. Dispose of any packaging material that is not recyclable.
4. Wear protective gloves and clothing when unpacking the cargo.
5. Put the cargo away from any dangerous materials in a safe and secure location.
6. Ensure that all cargo is labeled properly and securely.
7. Make sure you keep all goods in a safe, secure, and cool environment.
8. Do not move the cargo until it has been inspected for safety.
9. Refrain from using any power tools or heavy machinery to move the cargo.
10. Report any damaged cargo to the relevant authorities immediately.
Knowing the Specific Documentation and Inspection Requirements
Items that are eligible for Pre-Shipment Inspection (PSI) should be kept close to the entrance. A packing list might need to be attached to the inside of the container door in some destinations. Some countries of destination also require the inclusion of wood treatment certificates. Give an accurate weight for the cargo.
Responsibilities of the Shipping Line with Respect to Cargo
Officials keep an eye on inexperienced local stevedores while they are constantly on deck. It is regularly checked to ensure that lifting and lashing equipment is up to manufacturer standards and in good working order. Remove any vulnerable equipment as soon as possible. There are always spare parts on board.
Stowage planning is only as effective as the data fed into it. The shipping business makes sure the crew has full access to information such as stack and weight restrictions, stowage position plans, and other details.
Furthermore, stows must be safe and secure, hatch lids and tank tops must not be overstressed, and container racking restrictions must not be violated. Throughout the voyage, crew members routinely inspect the stow.
Every stowage method is carefully inspected before sailing. Inspecting base sockets, twist locks, galvanized rods, and securing points are required for this.
The IMDG code, national law, and the ship's dangerous goods document of compliance all dictate how dangerous items should be separated. Hazardous materials are always inspected after loading to make sure they are safely stored and free of leaks.
Storage is restricted to areas where reefer containers can be wired into power sources. Crew members routinely check the temperature settings of all reefers while the ship is in motion. The temperatures that the shipper has requested are applied to all reefers. Cargo that is not containerized is given a stow for protection.
Weight restrictions for stacks shouldn't ever be exceeded. To prevent late arrivals from winding up on deck or on top of the stack, heavy containers are kept in stages.
The shipping line has a number of responsibilities in respect to cargo:
1. To ensure the safe and timely delivery of the cargo. The shipping line must arrange for the loading, transport, and unloading of the cargo in accordance with the terms of the contract. It is responsible for ensuring that the cargo is adequately packed and secured prior to shipment, and for ensuring that all necessary paperwork and documentation is completed accurately and in a timely fashion.
2. To provide adequate insurance cover for the cargo. Shipping lines are responsible for arranging for the appropriate amount of insurance cover to protect the cargo in transit.
3. To cover any losses or harm done to the goods while it was in transit. The shipping line is liable for any losses or damages caused to the cargo during transit and is responsible for covering any costs associated with such losses or damages.
4. To provide timely and accurate information regarding the status of the cargo. Further, the shipping line is responsible for providing timely and accurate information regarding the whereabouts of the cargo, including its location, estimated time of arrival, and any delays or issues encountered during transit.
5. To guarantee adherence to pertinent rules and regulations. It is the shipping line's responsibility to make sure that it complies with all applicable laws and rules. This includes ensuring that all paperwork is completed appropriately, cargo is loaded and unloaded safely, and that the vessel is operated safely and in accordance with the laws and regulations of the particular country or region.
Additionally, the shipping line must keep records of all documents related to the shipment, including bills of lading, and other documents.
What happens Next in the Case of Damaged Cargo?
A thorough inspection is required when the container is received at the warehouse. See if there is any obvious damage to the container by looking at it from the outside.
Once the unloading process has started and there is obvious damage to the cargo, stop it immediately and call your carrier and, if the cargo is insured, your insurance company. If there has been serious damage recorded, your carrier can elect to send a surveyor to jointly unpack the cargo.
To file a damage claim, you must send your carrier the supporting documentation listed below:
- Photos
- Survey Report
- Packing List
- First Notice of Intent to Claim
- Container Destuffing Tally Sheet
- Shipper’s Commercial Invoice
- Detailed Claim Statement (the calculation of the loss, based on the commercial value of the cargo)
- Delivery Receipt
- Certificate of Independent Destruction or Proof of Salvage Value (to prove the cargo is indeed damaged and can be sold on a secondhand market.)
After the carrier has reviewed the claim, it will be established where along the route the probable injury may have happened. The ocean carrier will determine the claim's settlement amount and send a letter to that effect if the damage occurs while the cargo is in their care.
They might contest it if they weren't the ones who filled the container, though, if it turns out that damage could have occurred for other reasons, like improper stuffing. In this case, you will need to file the claim with additional parties.
The average claim for damaged cargo is settled in three to six months.
Defending Against the Dangers of Cargo Damage
Undoubtedly, there are actions that you as a forwarder or shipper can take to reduce the possibility of cargo damage. The fundamental safety measures include working with reliable carriers, purchasing cargo insurance, and following industry-standard stuffing guidelines.
For greater in-depth analysis and real-time alerts for high-value or condition-sensitive cargo, think about using IoT devices linked to a smart platform like Deskera.
Conclusion
To keep your cargo in perfect condition, there are several steps you should take.
First, it is important to properly package and protect your cargo. Make sure to use clean and dry packing materials, such as cardboard boxes, bubble wrap, foam, stretch wrap, and tape. Pack the cargo securely and make sure to include cushioning materials to absorb any shock or vibration.
Second, it is important to select the right type of shipping container. Depending on the type of cargo, you may need to use a reinforced, insulated, or temperature-controlled shipping container. Consider the weight and size of the cargo and the environment in which it will be stored.
Third, it is important to monitor the temperature and humidity levels during transit. Use a temperature-controlled container and check the readings regularly. Monitor the conditions inside the container and make sure it is within the required temperature and humidity levels.
Finally, it is important to properly label the cargo. Make sure to include the type of cargo, the origin and destination, and any special instructions for handling. This will help ensure that the cargo is handled properly and arrives in perfect condition.
By following these steps, you can help ensure that your cargo arrives in perfect condition. Let's take a look at the final checklist before we end this guide.
Final Checklist to Ensure that Cargo Arrives in Perfect Condition
There are a few things that you can do to ensure that your cargo arrives in perfect condition. Here's a checklist of tips:
1) Make sure that you're loading and unloading procedures are followed correctly.
2) Make sure that all the gear is properly loaded and secured.
3) Ensure that there are no punctures or tears in the containers or packaging material.
4) Keep an eye on the weight and balance of the shipment during transport.
5) Make sure that all cargo is clearly and securely labelled.
6) Check for any damage on arrival and report it immediately to the carrier.
How Deskera Can Assist You?
Deskera ERP is a comprehensive system that allows you to maintain inventory, manage suppliers, and track supply chain activity in real-time, as well as streamline a variety of other corporate operations.
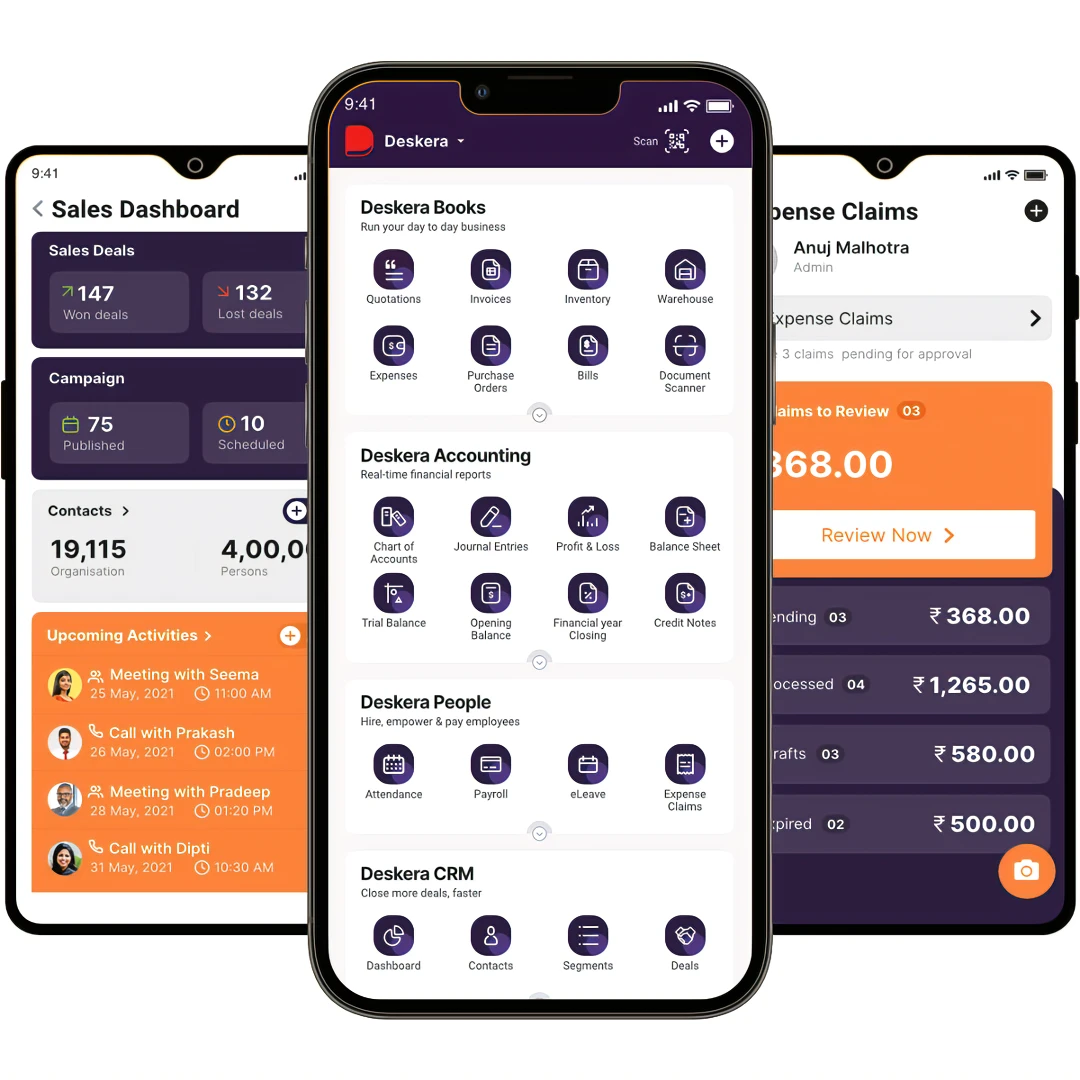
Deskera ERP and MRP system can help you:
- Manage production plans
- Maintain Bill of Materials
- Generate detailed reports
- Create a custom Dashboard
Deskera Books enables you to manage your accounts and finances more effectively. Maintain sound accounting practices by automating accounting operations such as billing, invoicing, and payment processing.
Deskera CRM is a strong solution that manages your sales and assists you in closing agreements quickly. It not only allows you to do critical duties such as lead generation via email, but it also provides you with a comprehensive view of your sales funnel.
Deskera People is a simple tool for taking control of your human resource management functions. The technology not only speeds up payroll processing but also allows you to manage all other activities such as overtime, benefits, bonuses, training programs, and much more. This is your chance to grow your business, increase earnings, and improve the efficiency of the entire production process.
Final Takeaways
We've arrived at the last section of this guide. Let's have a look at some of the most important points to remember:
- Packaging should be designed to withstand the rigors of transportation and be able to protect its contents from impacts, bumps, and other forces that might cause damage.
- When at Sea, rough waters are common for ships. Cargo that isn't properly secured will inevitably move. The most prevalent sources of cargo damage include water damage, impacts to the container, and damages from improper lashing and stuffing.
- Using the right packing techniques will lower overall overhead costs because packaging costs represent a relatively small portion of all supply chain expenses. Pick the appropriate size and package. Ensure impact protection is provided, but refrain from using too much compression or slack.
- During the shipping process, labels assist shippers in making decisions. It is important to mark the content's tolerance for additional weight. Mention the maximum weight that the box or package can support before being crushed as well as a warning that the contents are fragile.
- Proper labeling and documentation can help reduce the risk of errors and ensure that the correct cargo is loaded onto the correct vessel.
- Utilize machinery that can adapt to the environment well to increase efficiency and speed while reducing accidents and bad outcomes. Make that all of your material-handling equipment is operating correctly. It includes strapping machines, trucks, pallet jacks, cranes, forklifts, and loading/unloading systems.
- The top 3PL companies to use if you want your cargo to be in perfect condition are DHL, FedEx, and UPS. You can be confident that your goods will arrive in the same condition it did when it left your facility.
Related Articles
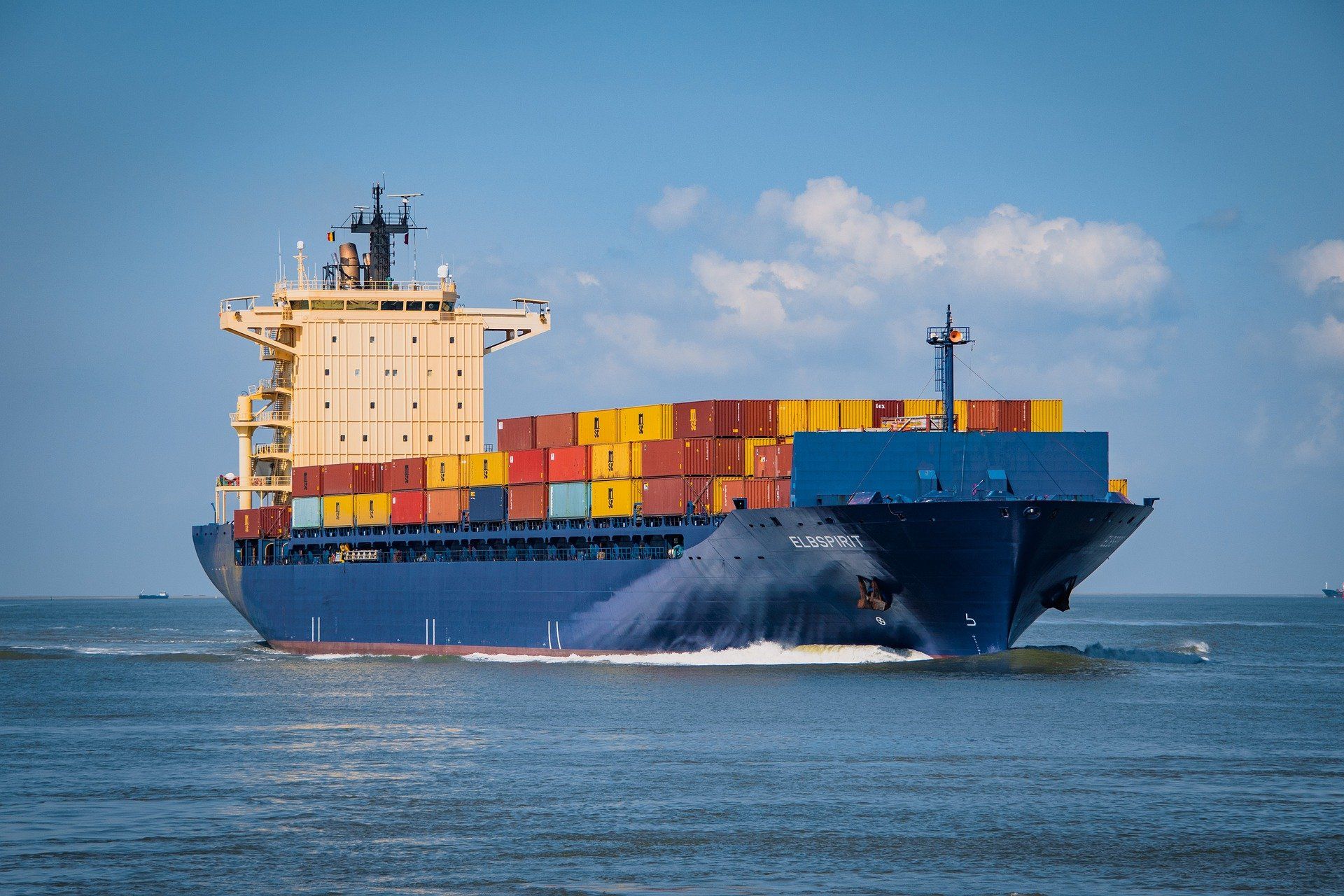
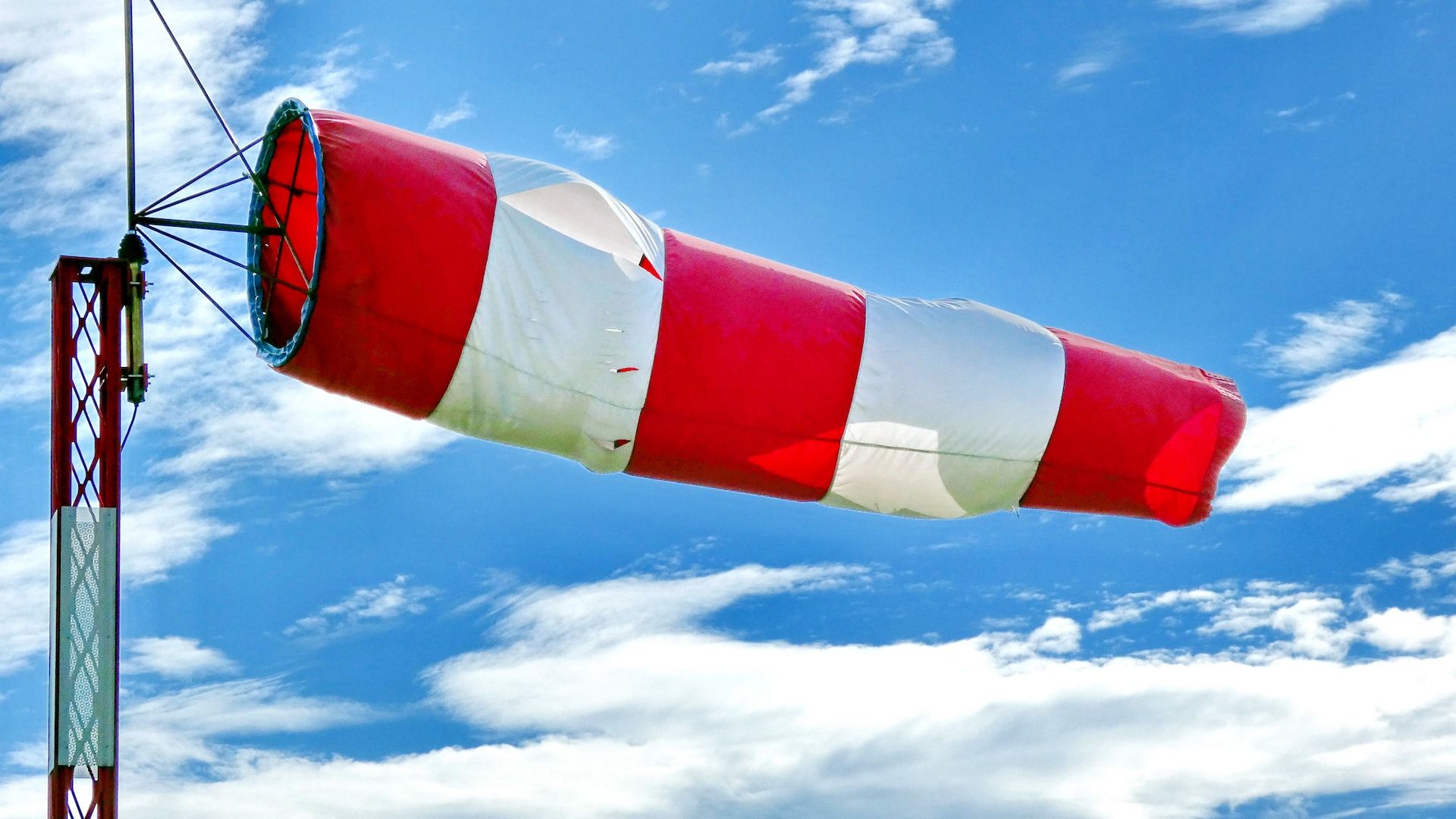