Have you ever wondered how much inventory loss your business might be experiencing without even realizing it? Inventory discrepancies—whether due to miscounts, theft, or system errors—can significantly impact your bottom line.
This is where inventory audits come in, ensuring accuracy, minimizing losses, and keeping your financial records in check. Without a structured audit process, businesses risk inefficiencies, compliance issues, and financial misstatements.
An inventory audit is a systematic process that verifies stock levels, assesses discrepancies, and ensures that recorded inventory matches physical counts. It plays a crucial role in maintaining financial accuracy and operational efficiency.
Whether you run a small retail business or a large manufacturing enterprise, a well-executed inventory audit helps identify problems early, preventing costly mistakes and improving overall inventory control.
To streamline this process, businesses are increasingly turning to ERP solutions like Deskera ERP. Deskera offers real-time inventory tracking, automated reconciliation, and detailed audit reports, reducing human errors and improving accuracy.
Its AI-powered analytics help businesses detect discrepancies faster, while barcode and RFID integration make physical audits more efficient. With Deskera ERP, companies can simplify complex inventory audits and maintain compliance with industry regulations.
In this guide, we’ll explore everything you need to know about inventory audits—from different types of audits and step-by-step processes to common challenges and best practices.
Whether you're conducting a routine cycle count or a full-scale statutory audit, understanding these key concepts will help you optimize your inventory management strategy.
What is an Inventory Audit?
An inventory audit is a process that verifies whether a company’s recorded inventory levels match the actual physical stock. It ensures that financial records accurately reflect what is available in warehouses, retail stores, or manufacturing facilities. By cross-checking inventory data against physical counts, businesses can detect discrepancies caused by human error, theft, damage, or system inefficiencies.
This auditing process goes beyond just counting stock—it evaluates the accuracy of inventory tracking methods and identifies potential weaknesses in inventory management. Audits can be conducted internally by store owners or warehouse managers, but many businesses also rely on external auditors for an unbiased assessment. A thorough inventory audit helps organizations improve inventory control, minimize losses, and ensure compliance with financial reporting standards like GAAP and IFRS.
Regular inventory audits provide a clear picture of a company’s supply chain health. They help businesses spot problematic SKUs, improve inventory accuracy, and refine stock replenishment strategies. Additionally, audits can highlight operational inefficiencies, such as delays in updating inventory records after receiving or shipping goods.
With modern ERP systems like Deskera ERP, companies can automate much of the inventory audit process. Deskera’s real-time tracking, barcode scanning, and AI-driven analytics help businesses quickly identify discrepancies and streamline reconciliation. By leveraging technology, companies can conduct more frequent and precise audits, reducing manual errors and enhancing overall inventory management.
Types of Inventory Audits
An inventory audit is a systematic process of verifying a company's inventory records against its actual stock to ensure accuracy. It helps businesses maintain proper financial reporting, prevent losses, and optimize inventory management.
1. Physical Inventory Count
A physical inventory count is the most comprehensive type of inventory audit, requiring businesses to manually count all inventory and compare it to the recorded figures in their inventory management system.
How It Works:
- All stock is counted, including items in the warehouse, sales floor, or production areas.
- The count is compared with accounting records or inventory management software.
- Any discrepancies are investigated, such as theft, damage, or clerical errors.
Business Impact:
- Ensures accuracy in financial reporting and regulatory compliance.
- Identifies inventory shrinkage due to theft, misplacement, or errors.
- Helps businesses maintain the right stock levels, preventing stockouts or overstocking.
Challenges:
- Can be time-consuming and disruptive, especially for large businesses.
- Requires careful planning to minimize business interruptions.
2. Cycle Counting
Instead of conducting a full physical inventory count, cycle counting involves auditing a subset of inventory on a rotating schedule.
How It Works:
- Inventory is divided into groups based on frequency and importance.
- Higher-value items (Category A in ABC analysis) may be counted more frequently than lower-value items.
- Discrepancies are addressed immediately to maintain ongoing accuracy.
Business Impact:
- Minimizes disruption to operations compared to full physical counts.
- Increases inventory accuracy over time, reducing the risk of errors.
- Helps identify patterns in inventory shrinkage and supply chain inefficiencies.
Challenges:
- Requires a structured system to ensure all inventory is counted periodically.
- Might miss large discrepancies if only a small portion is counted at a time.
3. ABC Analysis
ABC analysis categorizes inventory based on value and impact on revenue, ensuring that high-value items receive more scrutiny during audits.
How It Works:
- Inventory is classified into three categories:
- A (High-value, Low-quantity items) – Typically 20% of inventory but accounts for 80% of revenue.
- B (Moderate-value items) – About 30% of inventory and 15% of revenue.
- C (Low-value, High-quantity items) – About 50% of inventory and 5% of revenue.
- Audits focus more on Category A items, as errors in high-value inventory have greater financial impact.
Business Impact:
- Ensures efficient use of resources by prioritizing valuable inventory.
- Reduces the risk of major financial losses due to mismanagement of high-value stock.
- Improves inventory turnover rates and stock availability.
Challenges:
- Requires accurate classification and periodic review to adjust for shifting demand.
4. Cut-Off Analysis
This audit ensures transactions are recorded in the correct financial period by pausing warehouse operations during the audit.
How It Works:
- Shipping and receiving operations are temporarily halted.
- Auditors verify that inventory received before the period-end is included in that period.
- Helps prevent misreporting by ensuring that financial statements accurately reflect stock movements.
Business Impact:
- Prevents overstating or understating inventory values in financial statements.
- Ensures compliance with accounting and tax regulations.
- Reduces errors in profit calculations, as misdated transactions can affect revenue recognition.
Challenges:
- Requires coordination between finance and warehouse teams.
- Can temporarily disrupt operations.
5. Analytical Procedures
This method uses financial metrics to assess inventory accuracy instead of manual counting.
How It Works:
- Common metrics analyzed include:
- Inventory turnover ratio (how frequently inventory is sold and replaced).
- Gross margins (profitability of inventory).
- Days inventory on hand (DOH) (average time stock is held before being sold).
- These figures are compared against historical data and industry benchmarks to detect irregularities.
Business Impact:
- Helps identify slow-moving stock, potential fraud, or errors.
- Reduces the need for time-consuming physical audits.
- Supports demand forecasting and strategic decision-making.
Challenges:
- May not detect physical stock losses such as theft or spoilage.
- Requires accurate and up-to-date financial records.
6. Overhead Analysis
Overhead analysis helps businesses determine the indirect costs associated with inventory.
How It Works:
- Evaluates fixed costs like rent, utilities, and storage.
- Determines how overhead costs impact product pricing and profit margins.
- Allocates these costs correctly in financial statements.
Business Impact:
- Helps optimize pricing strategies by factoring in real inventory costs.
- Ensures compliance with accounting regulations regarding cost allocation.
- Improves financial planning and budget accuracy.
Challenges:
- Requires detailed financial tracking to separate direct vs. indirect costs.
7. Freight Cost Analysis
This audit ensures that shipping costs are properly tracked and included in inventory valuation.
How It Works:
- Auditors review freight invoices and contracts to verify accurate shipping costs.
- Analyzes shipping efficiency, delays, and damage rates.
- Identifies potential cost-saving opportunities in transportation.
Business Impact:
- Helps control supply chain costs by identifying inefficiencies.
- Ensures that freight costs are correctly accounted for in inventory valuation.
- Helps businesses negotiate better shipping rates.
Challenges:
- Requires tracking of multiple freight carriers and varying cost structures.
8. Finished Goods Cost Analysis
This audit is crucial for manufacturers, ensuring that the recorded cost of completed products is accurate.
How It Works:
- Examines direct costs (raw materials and labor) and indirect costs (overhead).
- Verifies that finished goods are valued correctly in financial records.
Business Impact:
- Ensures proper cost allocation and profit margin calculation.
- Helps in pricing strategy and profitability analysis.
Challenges:
- Requires precise cost tracking throughout the production process.
9. Product Reconciliation (Inventory Count Reconciliation)
This process corrects discrepancies between physical stock and recorded data.
How It Works:
- Compares actual inventory with financial records.
- Identifies missing, stolen, or misreported stock.
- Adjustments are made to ensure records reflect reality.
Business Impact:
- Reduces shrinkage and prevents fraud.
- Ensures inventory data is reliable for decision-making.
Challenges:
- Requires consistent tracking and investigation of discrepancies.
10. Invoice Matching (Match Invoices to Shipping Log)
Verifies that received inventory matches purchase orders and invoices.
How It Works:
- Cross-checks invoices with shipping logs and warehouse receipts.
- Ensures correct quantity and pricing were billed.
Business Impact:
- Prevents overpayments and fraud.
- Ensures suppliers adhere to contract terms.
Challenges:
- Labor-intensive if done manually; best automated through ERP software.
11. Inventory Layers Audit (LIFO/FIFO Verification)
An inventory layers audit verifies that inventory valuation methods such as FIFO (First-In-First-Out) or LIFO (Last-In-First-Out) are correctly applied.
How It Works:
- Auditors review how inventory cost layers are recorded and valued over time.
- Ensures that FIFO, LIFO, or Weighted Average methods align with financial reports and tax filings.
- Checks for potential cost manipulation or misstatements in inventory valuation.
Business Impact:
- Ensures compliance with accounting standards (GAAP, IFRS).
- Helps businesses accurately assess cost of goods sold (COGS) and profit margins.
- Affects tax liability, as LIFO or FIFO can lead to different taxable income amounts.
Challenges:
- Requires detailed transaction tracking for each inventory purchase and sale.
- Complexity increases for businesses with frequent stock replenishments.
Each audit method serves a specific purpose, helping businesses optimize inventory management, prevent losses, and ensure accurate financial reporting.
Step-by-Step Process for Conducting an Inventory Audit
Conducting an inventory audit ensures that stock records match actual inventory levels, helping maintain accuracy, compliance, and operational efficiency. Below is a structured step-by-step process for conducting an effective inventory audit.
Step 1: Define the Scope and Objectives
Before starting the audit, determine its purpose and scope.
- Identify whether the audit is for financial reporting, fraud detection, or operational efficiency.
- Choose the type of inventory audit (Physical Count, Cycle Counting, Inventory Layers Audit, etc.).
- Define the timeframe and frequency of the audit (quarterly, annually, or continuously).
Step 2: Gather and Review Inventory Records
Before counting physical stock, review existing inventory records to identify discrepancies.
- Collect inventory reports from the ERP system or inventory management software.
- Retrieve relevant documents such as purchase orders, sales records, invoices, and shipping logs.
- Identify items with high variance rates, slow-moving stock, or frequent adjustments.
Step 3: Plan the Audit Process
A well-structured audit plan ensures efficiency and minimizes disruptions.
- Assign responsibilities to auditors or inventory staff.
- Choose an audit method (Full Physical Count, Cycle Counting, ABC Analysis, etc.).
- Set up a cut-off point to pause incoming and outgoing inventory transactions during the audit.
- Arrange the necessary tools, such as barcode scanners, checklists, and inventory tracking software.
Step 4: Conduct the Physical Inventory Count
This is the core step where stock is manually verified.
- Cross-check physical stock with recorded data, using barcode scanning if applicable.
- Count high-value and high-variance items first to catch significant discrepancies.
- Use a double-checking process where a second team verifies critical counts.
- Document missing, damaged, or excess stock separately.
Step 5: Perform Inventory Reconciliation
Once counting is complete, compare physical inventory with system records.
- Identify discrepancies such as overstock, shortages, or missing items.
- Investigate causes such as theft, misplacement, accounting errors, or supplier issues.
- Adjust records in the inventory management system or ERP.
Step 6: Analyze Costing and Inventory Valuation
Ensure that inventory valuation aligns with accounting standards.
- Verify whether the FIFO, LIFO, or Weighted Average method is applied correctly.
- Check that inventory valuation follows GAAP, IFRS, or company-specific policies.
- Assess the impact of inventory valuation on Cost of Goods Sold (COGS) and financial statements.
Step 7: Audit Documentation and Reporting
Proper documentation is essential for compliance and future audits.
- Prepare an inventory audit report summarizing findings, discrepancies, and corrective actions.
- Maintain records of the counting process, adjustments, and financial impact.
- If necessary, submit the audit report to internal management, external auditors, or tax authorities.
Step 8: Implement Corrective Measures and Process Improvements
Use audit insights to enhance inventory accuracy and prevent future discrepancies.
- Strengthen inventory tracking systems by adopting ERP software or barcode/RFID scanning.
- Train staff on inventory handling best practices.
- Adjust reorder levels and safety stock policies to prevent shortages or overstocking.
- Plan regular cycle counts instead of waiting for the next full audit.
A well-executed inventory audit helps businesses identify inefficiencies, reduce losses, and improve stock accuracy. By following these steps, companies can streamline operations and maintain financial integrity.
How to Plan for an Inventory Audit
Effective planning is crucial for a smooth inventory audit. Without proper preparation, audits can become disorganized, time-consuming, and costly. Below are key steps to ensure a well-structured and efficient inventory audit.
1. Determine the Timing of the Audit
Since physical inventory counts often require halting operations, selecting the right time is critical.
- Schedule the audit when disruptions to business operations will be minimal.
- Avoid high-demand periods (e.g., year-end for retail businesses) to prevent delays in fulfillment.
- Consider roll forwards and roll backs if conducting the physical count before or after year-end:
- Roll Forward: Start with the last recorded inventory, add purchases and costs, then subtract the cost of goods sold (COGS).
- Roll Back: Set a cutoff date, then ignore transactions after that date in the next physical count to align with financial reporting.
2. Organize the Inventory Before the Audit
A well-organized warehouse simplifies the audit process and reduces counting errors.
- Minimize mixed pallets: Store similar items together and use a consistent storage method (e.g., 36 cases per pallet).
- Handle damaged, obsolete, or returned inventory:
- Write off or write down obsolete stock.
- Repair or reshelve damaged items before the audit.
- Keep a dedicated space for returned products awaiting processing.
- Ensure clear labeling: Mark bins, shelves, and storage locations for easy identification.
3. Prepare Essential Documentation
Auditors require specific records to verify inventory accuracy. Gather the following in advance:
- Inventory records (stock reports, valuation records, adjustments)
- Purchase invoices and shipping/receiving reports
- Proof of inventory ownership (certificates of ownership, bills of sale)
- Inventory management policies and written procedures for stock handling
- Cutoff procedures used for financial reporting
4. Assign and Train Personnel
Proper staffing ensures accurate and efficient auditing.
- Assign two-person teams for counting, ideally employees who don’t usually work together, to minimize fraud and errors.
- Dedicate counting personnel to the audit process without other distractions.
- Train employees on inventory counting best practices and the use of barcode scanners or mobile systems.
- Arrange for knowledgeable warehouse personnel to assist auditors in locating and verifying inventory.
- Conduct a dry run audit to familiarize staff with the process and determine the necessary workforce.
5. Minimize Work-in-Process (WIP) Inventory
Work-in-process inventory can complicate audits since it requires percentage-of-completion calculations.
- Reduce WIP stock as much as possible before the audit to simplify inventory valuation.
- If WIP is unavoidable, document its progress and ensure accurate cost allocation.
6. Consider Additional Storage Locations
Inventory stored in multiple locations must be accounted for.
- Third-Party Logistics (3PL) inventory: Request third-party warehouses to count inventory on the same date as the primary audit and submit records.
- Offsite storage: Ensure all satellite warehouses, retail stores, or manufacturing locations conduct synchronized counts.
7. Utilize Technology for Efficiency
The right technology can speed up the audit process and improve accuracy.
- Inventory management software (IMS): Choose a system that provides real-time stock updates instead of outdated data.
- Cycle counting automation: Use an IMS that triggers counts based on ABC analysis, item movement, or predefined frequency.
- Warehouse management system (WMS):
- Run the WMS on mobile devices to facilitate real-time data entry.
- Use barcode scanners to reduce manual entry errors.
- Automate comparisons between counted and recorded inventory.
- Integrated accounting and inventory systems: A unified platform simplifies financial reconciliation and auditing.
Planning is essential for a successful inventory audit. By carefully scheduling the audit, organizing inventory, preparing documentation, assigning trained personnel, minimizing WIP, accounting for external storage, and leveraging technology, businesses can ensure a seamless and accurate auditing process.
Inventory Audit Checklist
An inventory audit is a crucial process that ensures accuracy in inventory records, identifies discrepancies, and improves inventory management practices. Use this step-by-step checklist to plan, execute, and analyze your inventory audit efficiently.
1. Planning Stage
Create an Inventory Audit Schedule
- Determine the audit frequency based on business size and inventory complexity.
- Schedule the audit during slower periods to minimize disruptions.
- Consider quarterly, semi-annual, or annual audits based on inventory turnover rates.
Prepare Documents and Data
Gather all necessary records, including:
- Inventory management system reports
- Purchase and sales invoices
- Shipping and receiving documents
- Proof of inventory ownership (e.g., purchase orders, receipts)
- Past audit reports for comparison
Assess and Prepare Inventory
- Organize stock to prevent double-counting or missed items.
- Ensure all inventory is unpacked and accessible for counting.
- Handle damaged, obsolete, or returned items before the audit.
2. Execution Stage
Select Audit Procedures
Choose the most suitable audit method:
- Full Physical Inventory Count: Counts every item in stock.
- Cycle Counting: Periodic audits of specific inventory segments.
- ABC Analysis: Focuses on high-value and high-volume items.
- Cutoff Analysis: Ensures all transactions before and after the audit date are accounted for.
- Freight & Overhead Audit: Includes logistics and carrying cost verification.
Choose the Auditing Team
- Decide between an internal team or external auditors.
- Assign independent counters to prevent bias and errors.
- Ensure auditors have access to inventory records for verification.
Conduct the Physical Count
- Halt inventory movement during counting to maintain accuracy.
- Use barcode scanners, inventory software, or manual tally sheets.
- Cross-check stock levels with recorded data in the inventory system.
Reconcile Discrepancies
- Identify mismatches between physical count and recorded inventory.
- Investigate reasons for discrepancies, such as theft, damage, or clerical errors.
- Adjust records as needed to ensure accurate financial reporting.
3. Analysis Stage
Record and Review Audit Results
- Document final inventory levels, including any adjustments.
- Highlight major discrepancies and categorize them by cause.
Compare Findings with Previous Audits
- Identify trends in discrepancies, such as seasonal fluctuations.
- Determine if certain suppliers, products, or storage methods contribute to inventory errors.
Identify Causes of Shrinkage
- Evaluate potential reasons for inventory losses, such as:
- Theft (internal or external)
- Miscounts during receiving or shipping
- Supplier fraud or inaccurate deliveries
- Product damage or expiration
Improve Inventory Management Practices
- Implement better stock organization and labeling.
- Automate tracking with inventory management software.
- Enhance security measures to prevent theft or fraud.
- Optimize storage layouts to minimize misplacement and damage.
A well-executed inventory audit ensures accurate records, reduces losses, and enhances operational efficiency. Regular audits, combined with effective inventory management strategies, help businesses maintain financial accuracy and optimize stock levels.
The Importance of Inventory Audits
Inventory audits play a crucial role in maintaining accurate stock records, preventing losses, and ensuring smooth business operations. By conducting regular audits, businesses can identify discrepancies, optimize inventory management, and enhance financial reporting.
1. Ensures Accurate Inventory Records
- Verifies that the physical stock matches recorded inventory data.
- Reduces errors caused by miscounts, misplaced items, or clerical mistakes.
- Prevents stockouts and overstocking by maintaining precise stock levels.
2. Improves Financial Reporting and Compliance
- Ensures inventory valuation aligns with accounting standards.
- Helps maintain accurate cost of goods sold (COGS) calculations.
- Supports compliance with tax regulations, audits, and financial disclosures.
3. Identifies Shrinkage and Losses
- Detects inventory losses due to theft, damage, or supplier fraud.
- Helps businesses investigate the root cause of discrepancies.
- Provides insights into trends that may indicate internal fraud or operational inefficiencies.
4. Enhances Operational Efficiency
- Improves warehouse organization and stock placement.
- Streamlines inventory tracking, reducing manual errors.
- Identifies slow-moving or obsolete stock that needs reallocation or discounting.
5. Strengthens Supply Chain and Vendor Management
- Ensures accurate order fulfillment and supplier deliveries.
- Helps detect inconsistencies in vendor shipments and pricing.
- Allows businesses to renegotiate terms with suppliers based on audit findings.
6. Facilitates Better Decision-Making
- Provides data-driven insights for purchasing and inventory planning.
- Helps optimize reorder points and stock replenishment strategies.
- Assists in budgeting and forecasting by analyzing inventory trends.
7. Reduces Costs and Increases Profitability
- Minimizes unnecessary purchases by maintaining accurate stock levels.
- Lowers holding costs associated with excess or obsolete inventory.
- Prevents revenue loss from stock shortages and unfulfilled orders.
Regular inventory audits are essential for maintaining accurate records, ensuring financial compliance, and optimizing supply chain operations. By integrating audits into business processes, companies can reduce losses, improve efficiency, and enhance profitability.
Common Challenges in Inventory Audits
Conducting an inventory audit is a crucial part of inventory management, but it comes with several challenges that can impact accuracy, efficiency, and compliance. Below are some of the most common challenges businesses face during inventory audits and ways to mitigate them.
1. Data Discrepancies
- Differences between recorded and actual inventory levels.
- Errors due to manual data entry or outdated inventory records.
- Incorrect stock adjustments leading to inaccurate financial reporting.
Solution: Implement automated inventory management systems and perform regular cycle counts to catch discrepancies early.
2. Inefficient Inventory Organization
- Poorly labeled storage areas making it difficult to locate items.
- Mixed pallets and disorganized stock increasing counting errors.
- Lack of a standardized storage system slowing down audits.
Solution: Organize inventory systematically, using clear labeling, barcode scanning, and warehouse management systems (WMS).
3. Human Errors in Counting
- Miscounts due to fatigue or distractions.
- Double counting or missing items during physical audits.
- Lack of proper training for staff conducting the audit.
Solution: Use barcode scanners, assign two-person teams for verification, and train employees on best practices for inventory counting.
4. Inventory Shrinkage
- Theft, damage, or fraud leading to missing stock.
- Supplier fraud, misdeliveries, or miscounted shipments.
- Unrecorded inventory adjustments causing inconsistencies.
Solution: Strengthen internal security measures, implement stock tracking, and conduct surprise spot checks to detect potential fraud.
5. Challenges with Work-in-Process (WIP) Inventory
- Difficulty in assessing partially completed goods.
- Complexity in determining the exact value of WIP items.
- Variations in production stages affecting audit accuracy.
Solution: Minimize WIP inventory before audits and use tracking systems to estimate completion percentages accurately.
6. Lack of Audit Readiness
- Incomplete or missing inventory records.
- Unprepared warehouse staff unfamiliar with audit procedures.
- Delayed audits due to disorganization and lack of planning.
Solution: Maintain updated records, conduct pre-audit checks, and ensure staff are trained on inventory audit processes.
7. Disruptions to Business Operations
- Freezing inventory movement during audits halting normal operations.
- Long audit durations causing delays in order fulfillment.
- Increased costs due to additional labor and extended operational downtime.
Solution: Schedule audits during off-peak hours or use rolling audits to minimize disruptions.
8. Challenges in Multi-Location Audits
- Inconsistent inventory records across multiple warehouses or retail locations.
- Difficulty in tracking inventory transfers between locations.
- Third-party inventory storage complicates stock reconciliation.
Solution: Implement centralized inventory management software with real-time tracking and integrate third-party inventory reporting.
9. Compliance and Reporting Issues
- Difficulty in meeting tax and regulatory compliance requirements.
- Incorrect financial reporting due to inventory miscalculations.
- Inability to provide auditors with necessary documentation.
Solution: Keep detailed records of inventory transactions, follow standardized accounting methods, and use ERP systems for compliance tracking.
10. Technology and Integration Challenges
- Outdated systems leading to slow or inaccurate data retrieval.
- Lack of integration between inventory, accounting, and audit tools.
- Errors from manual data entry due to reliance on spreadsheets.
Solution: Invest in modern inventory management software that integrates seamlessly with accounting and auditing systems.
Addressing these challenges proactively can lead to smoother inventory audits, better financial accuracy, and improved inventory control. Businesses should focus on leveraging technology, streamlining processes, and training personnel to minimize errors and inefficiencies.
Best Practices for Effective Inventory Audits
Inventory audits play a vital role in maintaining accurate stock records, ensuring compliance, and minimizing losses. To streamline the process and improve accuracy, businesses should follow these best practices.
1. Identify & Prioritize Inventory Items
- Determine which inventory items to audit based on value, turnover rate, and risk of shrinkage.
- For initial or annual audits, include the entire product catalog.
- For routine audits, focus on high-value, high-risk, or frequently sold items using ABC analysis.
Pro Tip: Use inventory categorization methods (e.g., ABC analysis) to allocate audit resources effectively.
2. Gather Essential Documentation
- Keep inventory records, invoices, purchase orders, and shipping receipts readily available.
- Maintain proof of inventory ownership, such as bills of sale or supplier contracts.
- Provide auditors with an inventory management protocol document to ensure clarity.
Pro Tip: Ensure all documents are digitized and accessible through inventory management software for real-time verification.
3. Schedule Recurring Audits
- Perform full physical audits at least once a year.
- Conduct cycle counts on a quarterly, monthly, or weekly basis to catch discrepancies early.
- Align audit schedules with business cycles to minimize disruptions (e.g., avoid peak sales periods).
Pro Tip: Use inventory management software to set automated reminders for periodic audits.
4. Implement a Systematic Audit Approach
- Define audit objectives, including stock valuation, shrinkage analysis, and process efficiency.
- Standardize inventory counting procedures using predefined checklists and methodologies.
- Train staff on audit processes to maintain consistency across different locations.
Pro Tip: Create audit templates and use barcode or RFID scanning to eliminate manual counting errors.
5. Conduct Unbiased Audits
- If possible, involve external auditors for an impartial assessment.
- Avoid assigning audits to employees responsible for daily inventory management to prevent bias.
- Encourage auditors to evaluate theft, damage, and process inefficiencies objectively.
Pro Tip: Rotate internal audit teams periodically to gain fresh perspectives on inventory discrepancies.
6. Leverage Technology for Accuracy
- Use barcode scanners, RFID technology, or mobile inventory apps to automate data collection.
- Integrate inventory management systems (IMS) with accounting and sales platforms for real-time tracking.
- Utilize AI-driven forecasting tools to detect patterns in inventory discrepancies.
Pro Tip: Deskera ERP is an inventory tracking solution with real-time audit capabilities.
7. Reconcile Discrepancies Promptly
- Compare physical counts with recorded data and identify mismatches.
- Investigate causes of discrepancies, such as theft, supplier errors, or mislabeling.
- Adjust records accordingly and update inventory policies to prevent future inconsistencies.
Pro Tip: Use analytics dashboards to track recurring issues and take proactive corrective actions.
8. Record & Share Audit Results
- Document findings, including stock discrepancies, shrinkage rates, and process inefficiencies.
- Share reports with key stakeholders, including management, finance, and warehouse teams.
- Use audit insights to refine inventory management strategies and reduce future errors.
Pro Tip: Maintain historical audit records to track trends and measure inventory performance over time.
9. Implement Cycle Counting
- Instead of full-scale audits, conduct cycle counts on small inventory segments regularly.
- Use a rotating schedule to audit different product categories throughout the year.
- Focus on fast-moving or high-value items to prevent significant losses.
Pro Tip: Set up automated cycle counting triggers within your inventory software to reduce manual workload.
10. Improve Inventory Security & Controls
- Restrict unauthorized access to inventory storage areas.
- Use security cameras and track employee access to prevent theft and fraud.
- Implement strict check-in and check-out procedures for high-value goods.
Pro Tip: Leverage RFID tags for real-time tracking of expensive or high-risk inventory.
An effective inventory audit ensures stock accuracy, enhances financial reporting, and minimizes losses. By adopting systematic audit procedures, leveraging technology, and maintaining strict documentation, businesses can improve inventory control and optimize operations.
How Deskera ERP Helps with Inventory Auditing
Deskera ERP is a comprehensive enterprise resource planning solution that simplifies and enhances inventory auditing. With its robust inventory management features, businesses can conduct accurate, efficient, and data-driven audits.
Here’s how Deskera ERP can support your inventory auditing process:
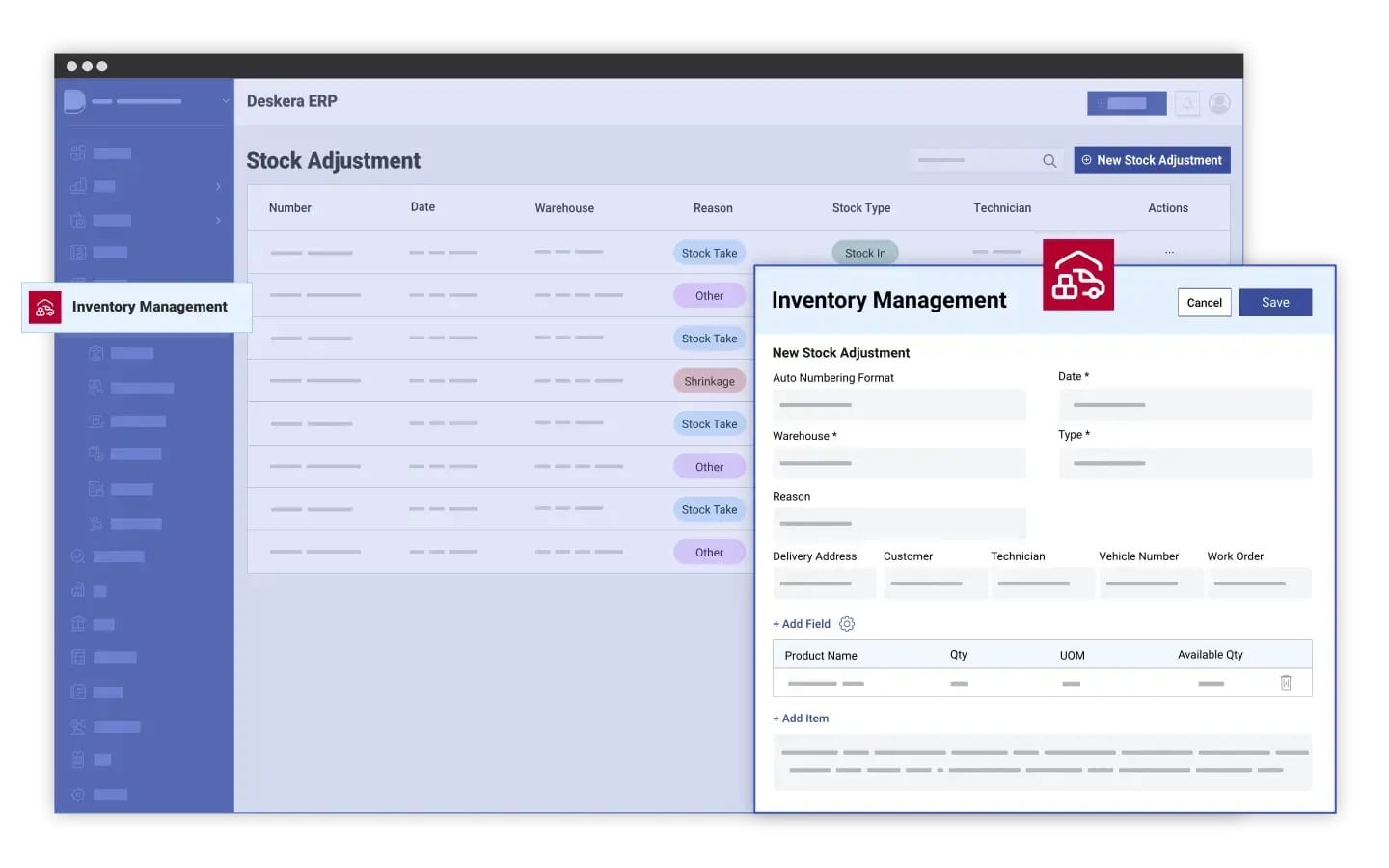
1. Automated Inventory Tracking & Real-Time Data Access
- Deskera ERP continuously updates inventory records with real-time stock movements, eliminating manual data entry errors.
- Automated tracking reduces discrepancies between recorded and actual stock levels.
Benefit: Ensures up-to-date inventory data, reducing errors and reconciliation time.
2. Built-In Audit Reports & Historical Data Analysis
- Generate detailed audit reports, including stock valuation, discrepancies, and movement history.
- Compare audit results with previous periods to identify recurring issues.
Benefit: Improves audit accuracy with structured data insights.
3. Cycle Counting & Customizable Audit Schedules
- Supports periodic cycle counting instead of full physical audits, reducing operational disruptions.
- Allows businesses to customize audit frequency based on inventory type and value.
Benefit: Reduces the workload and enables more frequent, targeted audits.
4. Barcode & RFID Integration for Faster Audits
- Deskera ERP supports barcode and RFID scanning, ensuring quick and accurate inventory counting.
- Minimizes human errors in manual counting by automating data collection.
Benefit: Speeds up the audit process and enhances accuracy.
5. AI-Driven Discrepancy Detection
- Identifies stock mismatches and unusual inventory fluctuations using AI-powered insights.
- Helps in detecting potential shrinkage, theft, or mismanagement.
Benefit: Proactively addresses inventory discrepancies before they escalate.
6. Seamless Integration with Accounting & Supply Chain Modules
- Syncs inventory audits with financial statements and supplier records for transparent reporting.
- Tracks purchase orders, supplier deliveries, and stock adjustments in one unified system.
Benefit: Ensures compliance and simplifies financial reconciliation.
7. User Role-Based Access for Secure Auditing
- Restricts inventory access based on user roles, preventing unauthorized modifications.
- Logs all inventory adjustments to track changes and maintain audit integrity.
Benefit: Enhances security and accountability in the auditing process.
8. Mobile Accessibility for Remote Auditing
- Deskera’s cloud-based system allows auditors to access data from anywhere using mobile devices.
- Enables warehouse staff to perform audits on the go, reducing paperwork.
Benefit: Provides flexibility and improves productivity during audits.
Deskera ERP streamlines the inventory auditing process by automating tracking, minimizing errors, and providing deep analytical insights. Whether you need cycle counting, AI-driven audit analysis, or seamless financial integration, Deskera ERP ensures accurate and efficient inventory audits.
Key Takeaways
- Importance of Inventory Audits – Regular inventory audits help businesses maintain accurate stock records, prevent shrinkage, improve financial reporting, and enhance operational efficiency.
- Inventory Audit Checklist – A structured approach, including scheduling audits, preparing documents, conducting physical counts, reconciling discrepancies, and analyzing results, ensures a smooth and accurate audit process.
- Planning for an Inventory Audit – Establishing a clear audit schedule, gathering necessary documents, and preparing inventory in advance helps streamline the audit process and reduce errors.
- Executing an Inventory Audit – Selecting appropriate audit procedures, defining the audit team, ensuring a controlled counting environment, and using digital tools improve accuracy and efficiency.
- Reconciling and Analyzing Audit Results – Identifying mismatches between records and physical counts, investigating discrepancies, and comparing findings with past audits help uncover potential issues like theft or mismanagement.
- Common Challenges in Inventory Audits – Errors in data entry, stock discrepancies, shrinkage, lack of standardization, and inefficient auditing methods can impact the accuracy and effectiveness of inventory audits.
- Best Practices for Effective Inventory Audits – Prioritizing high-value inventory, scheduling regular audits, maintaining accurate documentation, leveraging technology, and conducting unbiased reviews improve audit reliability.
- Leveraging Technology in Inventory Audits – Tools such as barcode scanners, RFID tracking, cloud-based inventory management software, and automated reconciliation systems enhance audit accuracy and efficiency.
- Compliance and Regulatory Considerations – Adhering to accounting standards, tax regulations, and industry-specific requirements ensures that inventory audits meet legal and financial compliance needs.
- How Deskera ERP Helps with Inventory Auditing – Deskera ERP streamlines inventory audits with real-time tracking, automated reporting, AI-driven discrepancy detection, barcode scanning, and seamless financial integration.
Related Articles
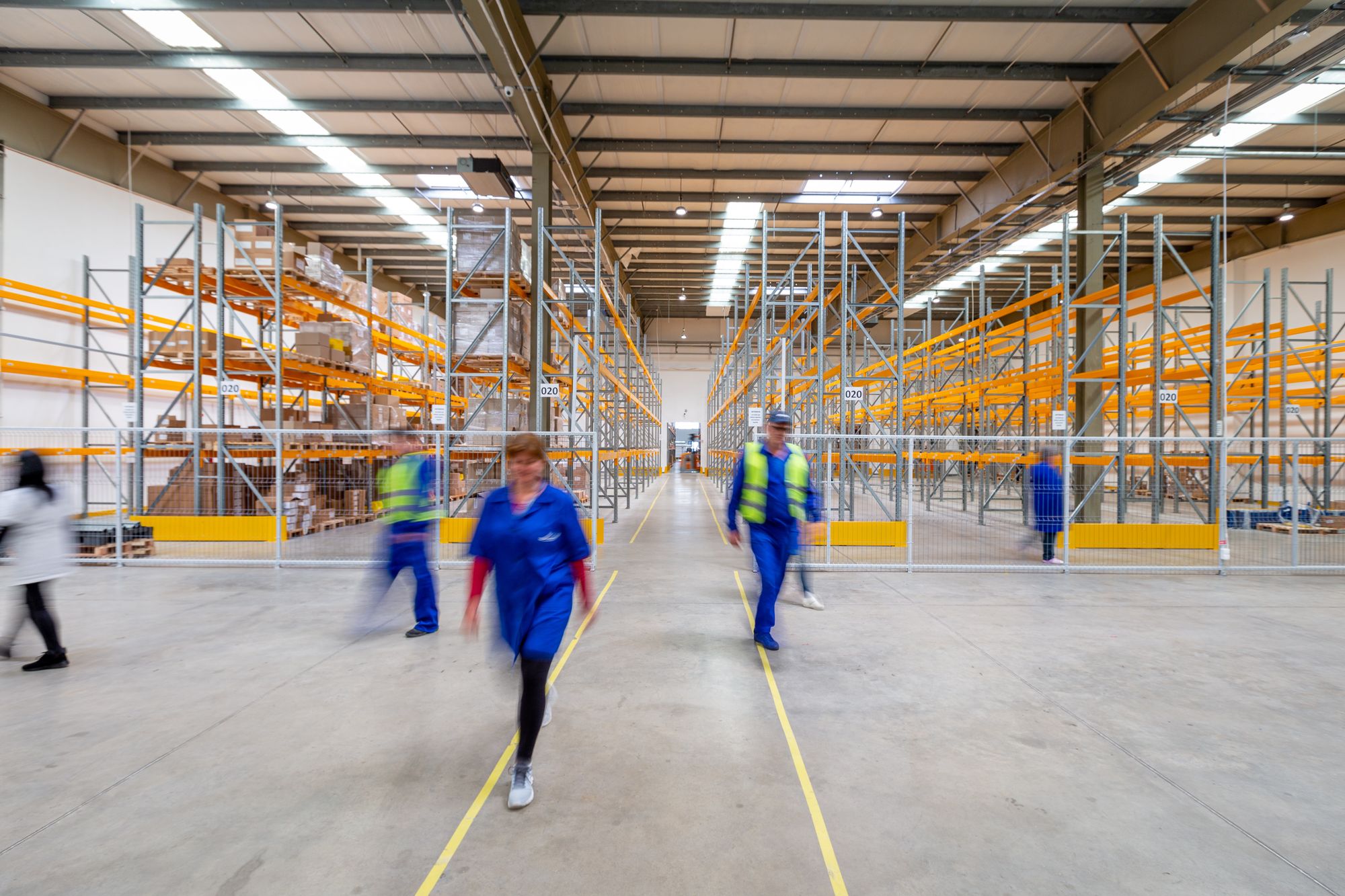
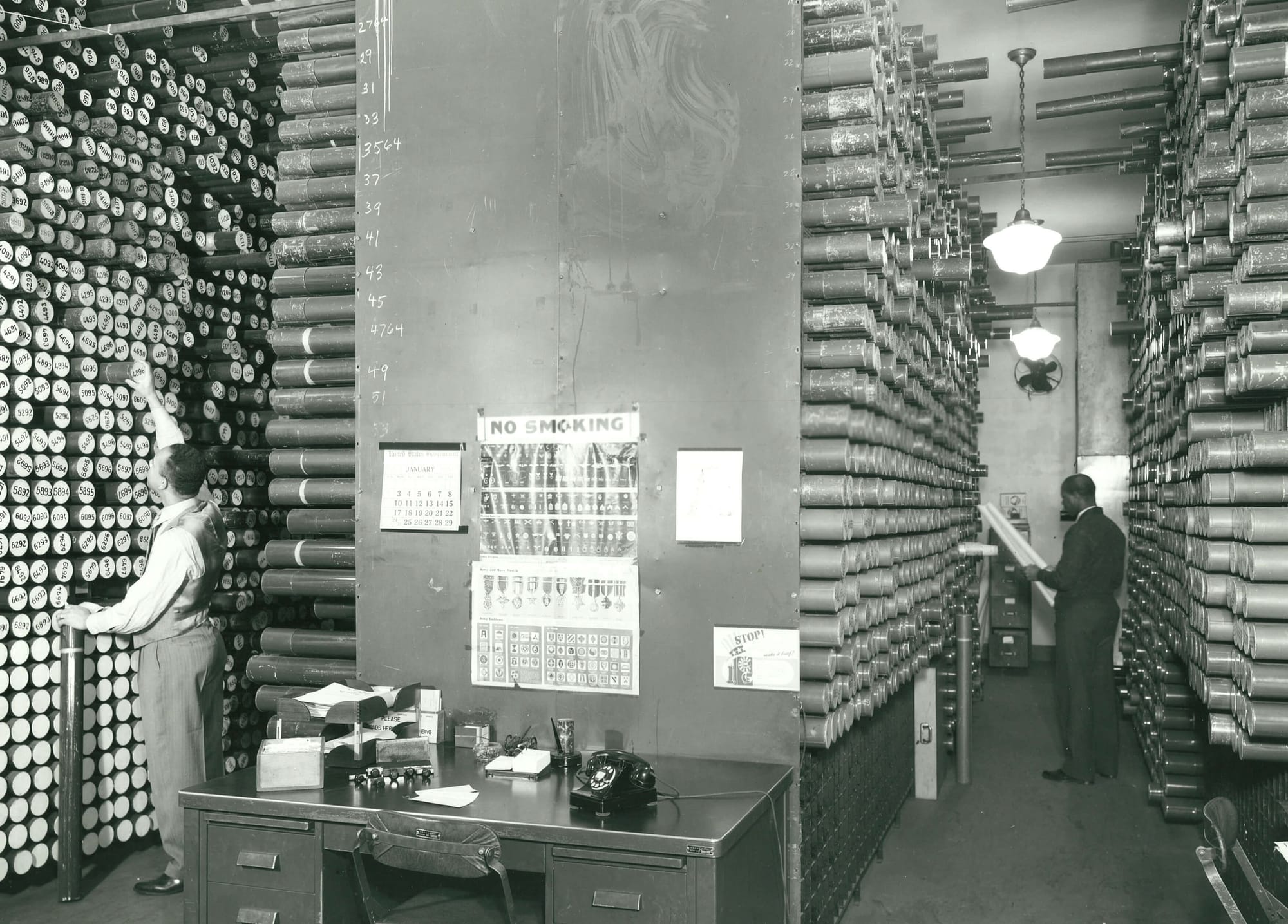

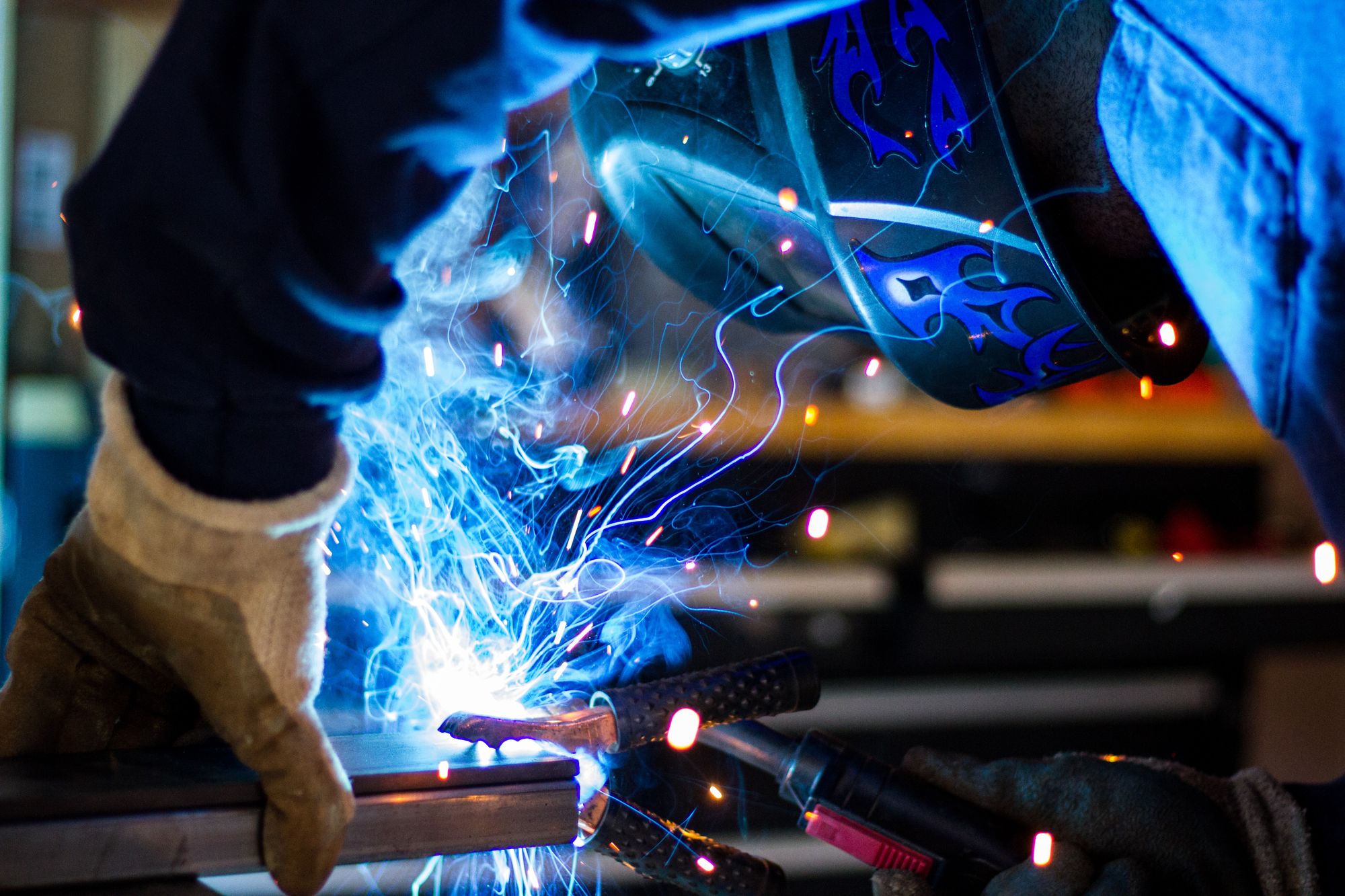
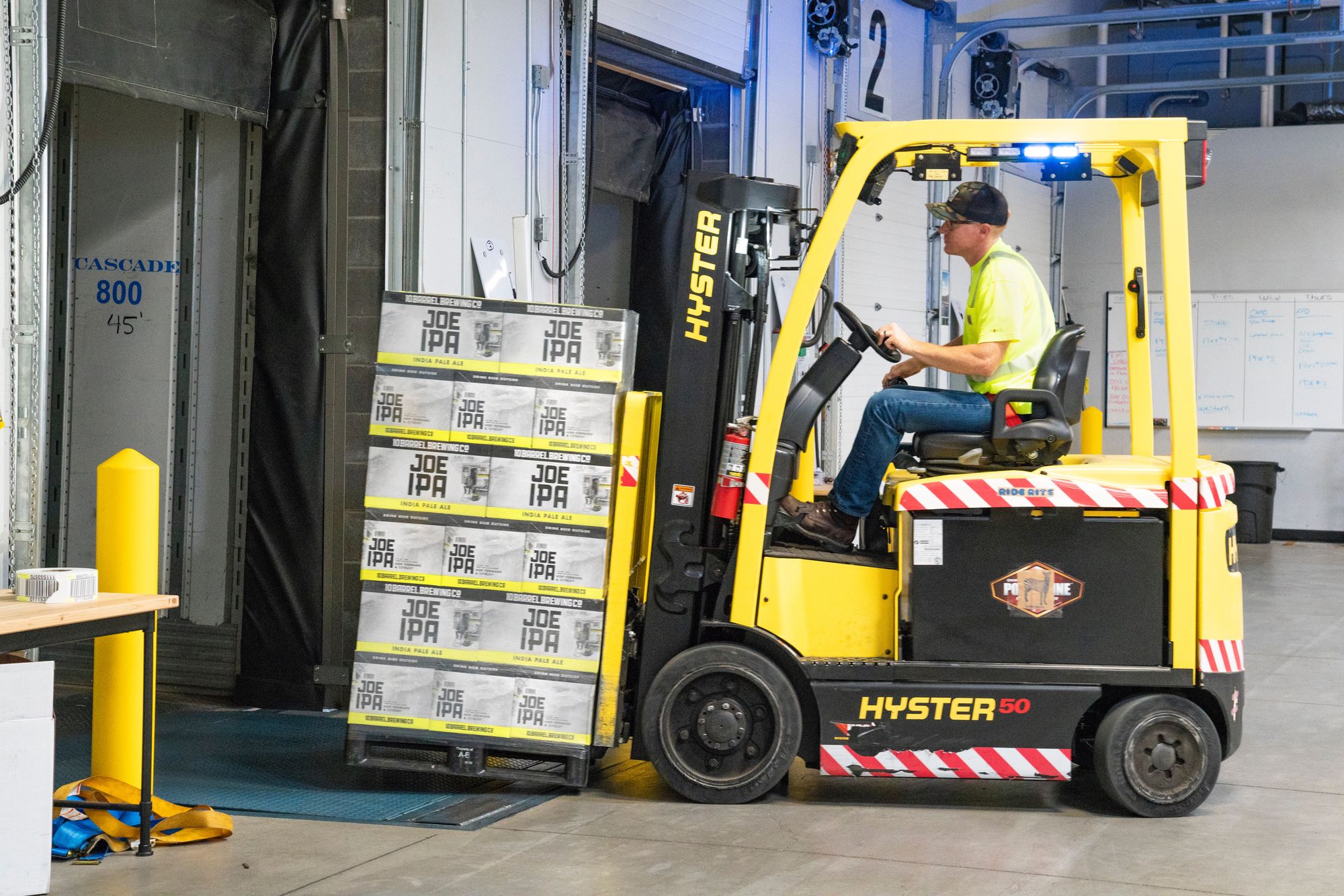