Are you seeking to understand how a multi-level bill of materials can assist you in enhancing operational efficiency? If your answer is yes, then you are on the right page.
In today's rapidly evolving and competitive business landscape, operational efficiency has become a paramount goal for organizations seeking to optimize their processes, reduce costs, and deliver superior products to the market. At the heart of achieving operational excellence lies a powerful tool known as the Multi-Level Bill of Materials (BOM).
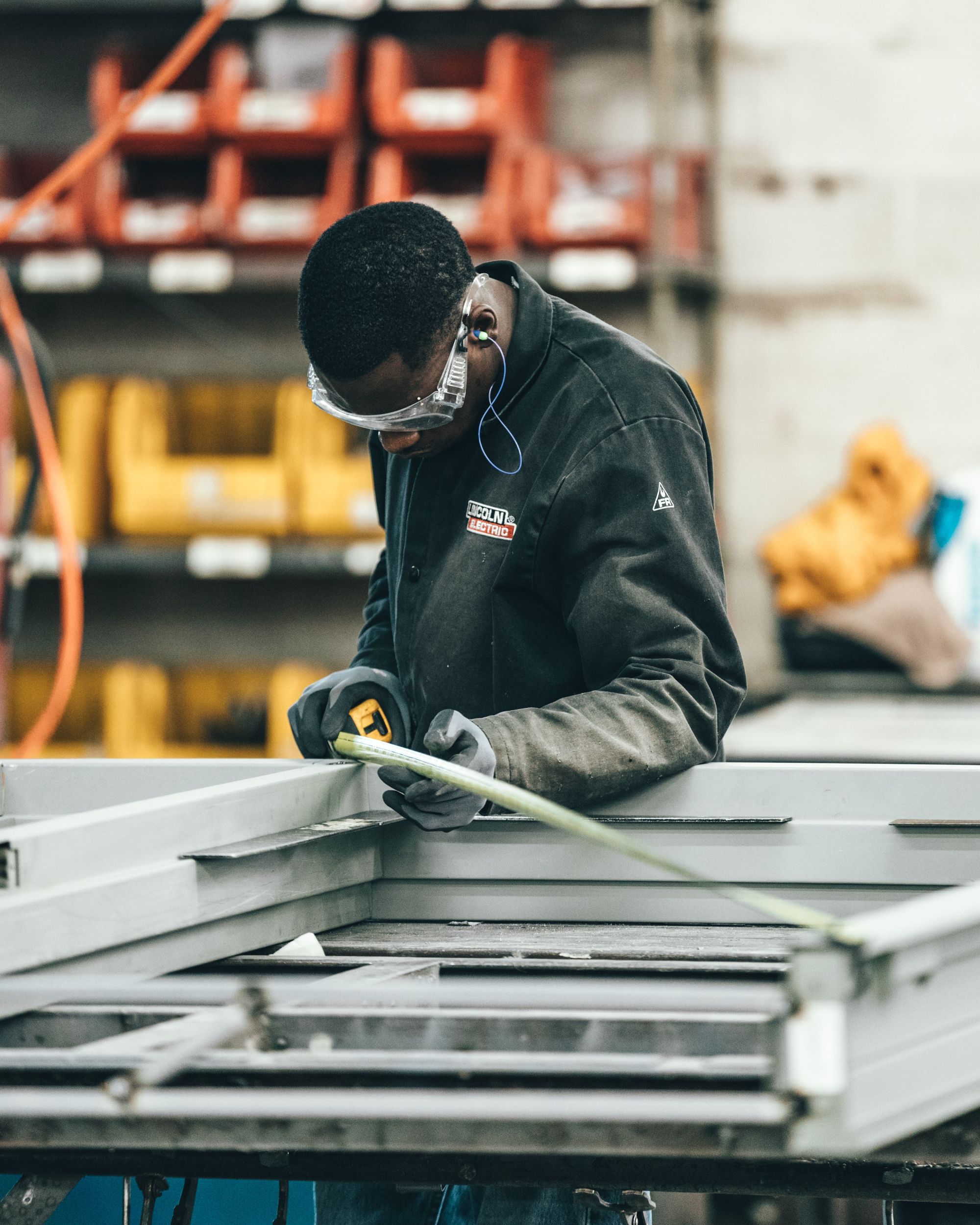
This comprehensive framework provides a structured and insightful view of a product's composition, from its individual components to the final assembly. By leveraging the potential of a Multi-Level BOM, businesses can unlock a multitude of benefits that extend far beyond mere inventory management.
From clear visibility and efficient planning to streamlined production processes and continuous improvement, the Multi-Level BOM acts as a cornerstone for driving operational efficiency to new heights.
In this exploration, we embark on a journey to delve into the various dimensions of operational efficiency that are enhanced through the implementation of a Multi-Level BOM.
Whether you are a production manager striving for optimized workflows, an engineer seeking to elevate design integration, or a business leader committed to staying competitive in a dynamic market, this exploration will equip you with the insights and knowledge needed to harness the potential of a Multi-Level BOM.
The topics covered in this article are:
- What is a Multi-Level Bill of Materials?
- What is Operational Efficiency?
- Importance of Operational Efficiency
- Unlocking Operational Efficiency with Multi-Level Bill of Materials
- How Does a Multi-Level BOM Contribute to Sustainable Practices?
- Can a Multi-Level BOM be Adapted for Different Industries?
- How Can Deskera Help You with a Multi-Level Bill of Materials?
- Key Takeaways
- Related Articles
What is a Multi-Level Bill of Materials?
A Multi-Level Bill of Materials (BOM) is a hierarchical structure used in manufacturing and production processes to define the components, materials, and assemblies required to create a finished product. It outlines the relationships and dependencies between various parts and subassemblies, showing how they come together to form the final product.
In a multi-level BOM, each level represents a different level of assembly or subassembly. The top level is the finished product, and subsequent levels break down the product into its constituent parts and subassemblies. This hierarchical representation helps in understanding the complete manufacturing process and assists in managing inventory, procurement, and production planning.
Here's an example of a multi-level BOM for a simple product like a bicycle:
- Level 1 (Top-Level): Bicycle
- Level 2: Frame
- Level 3: Front Fork
- Level 3: Rear Triangle
- Level 2: Wheels
- Level 3: Front Wheel Assembly
- Level 3: Rear Wheel Assembly
- Level 2: Handlebars
- Level 2: Brakes
- Level 3: Front Brake Assembly
- Level 3: Rear Brake Assembly
- Level 2: Gears
- Level 3: Gear Shifter Assembly
- Level 3: Gear Mechanism Assembly
- Level 2: Seat Assembly
In this example, the bicycle is the top-level assembly, and it consists of various subassemblies like the frame, wheels, handlebars, brakes, gears, and seat. Each subassembly can have further levels of components until the individual parts that make up the subassemblies are listed.
A multi-level BOM is a crucial tool for manufacturers and production planners as it provides a clear understanding of the product structure and helps in managing the procurement of materials, scheduling production tasks, estimating costs, and ensuring that all required components are available at the right time for assembly. It also supports effective inventory management and quality control throughout the production process.
What is Operational Efficiency?
Operational efficiency refers to the extent to which an organization can optimize its processes, resources, and activities to achieve maximum output while minimizing input or resource wastage.
It's a measure of how well an organization uses its resources to produce goods or services and deliver value to its customers. Operational efficiency is often a key goal for businesses as it directly impacts profitability, competitiveness, and overall success.
Key aspects of operational efficiency include:
- Process Optimization: Streamlining and improving business processes to eliminate inefficiencies, reduce bottlenecks, and enhance overall workflow. This involves identifying and eliminating redundant or unnecessary steps, automating manual tasks, and implementing best practices.
- Resource Utilization: Efficiently allocating and utilizing resources such as labor, materials, equipment, and time. This may involve optimizing production schedules, managing inventory levels, and minimizing downtime.
- Cost Reduction: Identifying and minimizing unnecessary costs while maintaining or improving product quality and customer satisfaction. This could involve negotiating better supplier deals, reducing waste, and optimizing energy consumption.
- Time Management: Ensuring that tasks and processes are completed in a timely manner, reducing lead times, and improving response times to customer needs. Time efficiency can lead to faster product delivery and better customer service.
- Quality Improvement: Striving to produce consistent and high-quality products or services by implementing quality control measures, standardized processes, and continuous improvement initiatives.
- Flexibility and Adaptability: Being able to quickly adjust to changes in demand, market conditions, or internal factors. Operational efficiency includes the ability to scale up or down as needed and adapt to unforeseen challenges.
- Employee Engagement: Engaging and empowering employees to contribute to process improvements, share ideas, and take ownership of their work. Engaged employees are often more motivated to find ways to enhance efficiency.
- Technology Integration: Leveraging technology and automation to streamline processes, improve accuracy, and reduce manual intervention. This could involve using software for inventory management, customer relationship management (CRM), and other operational tasks.
Operational efficiency is not a one-time achievement but an ongoing effort. Many organizations use techniques such as Lean, Six Sigma, Total Quality Management (TQM), and continuous improvement methodologies to drive operational efficiency.
By continuously assessing and refining their processes, organizations can achieve higher productivity, reduced costs, improved customer satisfaction, and a stronger competitive position in the market.
Importance of Operational Efficiency
Operational efficiency is of paramount importance to businesses and organizations across various industries for a multitude of reasons. Here are some key reasons why operational efficiency is important:
- Cost Savings: Improved operational efficiency leads to reduced wastage of resources, optimized processes, and streamlined workflows. This directly translates into cost savings by minimizing unnecessary expenditures, lowering production costs, and decreasing overhead expenses.
- Increased Profitability: When organizations operate more efficiently, they can produce more output with the same or fewer resources. This increased output often results in higher revenue and profit margins. By maximizing revenue and minimizing costs, businesses can enhance their bottom line.
- Competitive Advantage: Operational efficiency can be a significant source of competitive advantage. Efficient organizations can offer products or services at competitive prices while maintaining good quality. This can attract more customers and increase market share, helping the organization stay ahead of competitors.
- Enhanced Customer Satisfaction: Efficient operations lead to faster response times, shorter lead times, and improved product or service quality. This, in turn, enhances customer satisfaction and customer loyalty. Satisfied customers are more likely to become repeat buyers and recommend the organization to others.
- Flexibility and Adaptability: Efficient organizations are better equipped to respond to changes in the market, customer preferences, and unforeseen challenges. They can quickly adjust production levels, adapt to new technologies, and meet changing demands, enabling them to remain resilient in a dynamic business environment.
- Innovation and Growth: Operational efficiency frees up resources, both financial and human, that can be redirected toward innovation and growth initiatives. When businesses are not bogged down by inefficiencies, they have more capacity to invest in research and development, explore new markets, and expand their product or service offerings.
- Employee Morale and Engagement: Streamlined processes and clear workflows contribute to a more organized and productive work environment. Employees are less likely to feel frustrated by unnecessary obstacles, and they can focus on meaningful tasks. This can lead to higher morale, increased job satisfaction, and greater employee engagement.
- Risk Management: Operational efficiency often involves improved quality control and risk management practices. By identifying and addressing potential issues early in the process, organizations can reduce the likelihood of defects, errors, and other operational disruptions that could negatively impact reputation and customer trust.
- Sustainability and Environmental Impact: Operational efficiency can lead to reduced resource consumption and waste generation, contributing to a smaller environmental footprint. By minimizing energy usage and waste, organizations can align their operations with sustainability goals and contribute to a more eco-friendly approach.
- Strategic Focus: Efficient organizations have the capacity to dedicate more time and resources to strategic planning and decision-making. They can focus on long-term goals, explore new business opportunities, and make well-informed decisions that align with their overall vision.
In summary, operational efficiency is not just about cutting costs; it's a fundamental driver of business success. It enables organizations to operate at their full potential, deliver value to customers, remain competitive, and achieve sustainable growth in a rapidly changing business landscape.
Unlocking Operational Efficiency with Multi-Level Bill of Materials
Using a Multi-Level Bill of Materials (BOM) can be a powerful strategy for unlocking operational efficiency within a manufacturing or production environment.
Here's how an effective multi-level BOM can contribute to operational efficiency:
Clear Visibility and Planning
Clear visibility and planning emphasize the importance of having a multi-level Bill of Materials (BOM) in providing a comprehensive view of the product structure and how it contributes to operational efficiency. Let's delve deeper into this concept:
Clear Visibility:
A multi-level BOM offers a detailed breakdown of the entire product, from the top-level assembly down to the smallest components. This visibility allows all stakeholders, including production managers, engineers, designers, and procurement teams, to have a clear understanding of the product's composition and how various parts come together.
With clear visibility, everyone involved in the production process can:
- Understand Product Complexity: The BOM illustrates the hierarchy of subassemblies and components. This understanding is crucial for assessing the complexity of the production process and identifying potential challenges or areas for improvement.
- Visualize Dependencies: Stakeholders can see how different components and subassemblies depend on each other for the final product's functionality. This knowledge helps in planning assembly sequences and avoiding bottlenecks.
- Identify Critical Components: Critical components that impact product functionality or quality can be easily identified. This allows for focused quality control efforts and ensures that these components meet the necessary standards.
- Enhance Collaboration: Clear visibility fosters better communication and collaboration between different departments. Engineers can work closely with production teams to ensure that the product is designed in a way that optimizes manufacturability.
Effective Planning:
A multi-level BOM greatly aids in effective planning across various aspects of production:
- Production Scheduling: Production managers can create accurate and realistic production schedules based on the BOM. They know which components need to be available at specific times to avoid delays and minimize idle time.
- Resource Allocation: With knowledge of the components and their quantities, teams can allocate resources such as labor, equipment, and workspace more efficiently. This prevents overloading specific resources and ensures a balanced production flow.
- Materials Procurement: Procurement teams can plan material orders based on the BOM, taking into account lead times, quantities, and delivery schedules. This minimizes the risk of material shortages and reduces the need for rush orders.
- Capacity Planning: The BOM helps in determining the required production capacity to meet demand. This includes evaluating whether existing equipment and facilities can handle the production volume or if additional resources are needed.
- Resource Optimization: By analyzing the BOM, organizations can identify opportunities to optimize resource usage. For example, if two products share similar components, production runs can be synchronized to reduce changeover time and increase efficiency.
- Identifying Process Improvements: The BOM highlights each step of the assembly process. This makes it easier to identify inefficiencies or areas where improvements can be made, such as reducing handling time or automating certain tasks.
In summary, the clear visibility and planning enabled by a multi-level BOM empower organizations to make well-informed decisions, efficiently allocate resources, and optimize production processes. This ultimately leads to smoother operations, reduced lead times, minimized waste, and higher overall operational efficiency.
Effective Inventory Management
Effective inventory management is a critical aspect of operational efficiency, and a multi-level Bill of Materials (BOM) plays a key role in achieving this. Let's explore how a multi-level BOM contributes to efficient inventory management in more detail:
Bill of Materials (BOM) and Inventory Management:
A BOM provides a structured breakdown of the components required to assemble a product. It outlines the quantities and relationships between various parts, subassemblies, and the final product.
This hierarchical representation enables organizations to effectively manage their inventory by offering the following benefits:
- Optimal Stock Levels: With a multi-level BOM, you have a clear understanding of the quantities of each component needed for different levels of assembly. This knowledge helps you maintain optimal stock levels of raw materials, subassemblies, and finished goods. You can prevent excessive inventory that ties up working capital or shortages that disrupt production.
- Accurate Demand Forecasting: By analyzing historical data and production requirements outlined in the BOM, you can accurately forecast demand for each component. This assists in aligning procurement and production schedules to meet customer demands without overstocking.
- Lead Time Management: The BOM provides information on lead times for procuring each component. With this knowledge, you can plan orders well in advance to account for lead times and avoid production delays caused by late or missing components.
- Supplier Collaboration: Sharing the BOM with suppliers enhances collaboration and communication. Suppliers gain insight into your requirements and production schedules, enabling them to better align their deliveries with your needs. This reduces the risk of stockouts and helps build stronger supplier relationships.
- Reduced Excess and Obsolete Inventory: By having a clear view of component quantities and usage, you can avoid over-ordering materials that might become excess or obsolete. This prevents unnecessary costs associated with storing or disposing of unused inventory.
- Efficient Production Runs: The BOM allows you to synchronize production runs based on common components. This reduces changeover time and enables you to utilize existing inventory efficiently, minimizing production interruptions.
- Batch and Lot Tracking: In industries where traceability is crucial, such as pharmaceuticals and electronics, the BOM facilitates batch and lot tracking. You can trace the origin of each component and quickly identify and address issues related to quality or defects.
- Just-In-Time (JIT) Manufacturing: JIT manufacturing aims to minimize inventory levels by receiving materials and producing products only as needed. The BOM is essential for JIT, as it guides the precise timing and quantities of material orders and production runs.
- Cost Optimization: By understanding the components' costs outlined in the BOM, you can make informed decisions about sourcing strategies and negotiate better deals with suppliers. This contributes to cost optimization and better utilization of financial resources.
- Space Utilization: With accurate inventory management based on the BOM, you can optimize warehouse space by storing components and subassemblies efficiently. This reduces storage costs and improves overall warehouse organization.
In summary, a multi-level BOM empowers organizations to manage their inventory efficiently by providing a comprehensive and structured overview of component requirements.
This knowledge leads to reduced carrying costs, minimized stockouts, improved demand forecasting, and streamlined procurement processes, all of which contribute to enhanced operational efficiency.
Resource Allocation
Resource allocation is a critical aspect of operational efficiency, and a multi-level Bill of Materials (BOM) plays a significant role in optimizing the allocation of resources within a manufacturing or production environment.
Let's dive deeper into how a multi-level BOM contributes to effective resource allocation:
Resource Allocation and Multi-Level BOM:
Resource allocation involves assigning and distributing various resources such as labor, equipment, workspace, and time to different tasks and processes. A multi-level BOM provides a detailed breakdown of the components and subassemblies required to manufacture a product.
This breakdown facilitates efficient resource allocation in the following ways:
- Balanced Workload: With a multi-level BOM, you can see the production requirements at each level of assembly. This enables you to evenly distribute the workload across workstations, teams, or shifts. Balancing the workload prevents bottlenecks, overburdened resources, and underutilized capacity.
- Labor Planning: By understanding the components needed for each level of assembly, you can allocate skilled workers appropriately. Skilled workers can be assigned to tasks that require their expertise, while less skilled tasks can be delegated to appropriately trained personnel.
- Equipment Utilization: The BOM helps you identify which equipment or machinery is required for specific assembly steps. This allows you to allocate equipment efficiently, reduce idle time, and ensure that the right tools are available when needed.
- Scheduling Efficiency: Accurate resource allocation based on the BOM contributes to more precise production scheduling. You can plan the sequence of assembly steps and allocate resources in a way that minimizes downtime and optimizes production output.
- Minimized Changeovers: When different products share common components, the BOM helps you schedule production runs to minimize changeover times. This approach reduces the time and effort required to switch between different products, enhancing overall efficiency.
- Space Management: The BOM provides insight into the space requirements for different components and subassemblies. This information aids in organizing the workspace, ensuring that materials and equipment are stored in a way that maximizes efficiency and accessibility.
- Real-time Adjustments: If unforeseen changes occur, such as a delay in component delivery, the BOM allows you to quickly adjust resource allocation and production schedules. This agility helps in adapting to changing circumstances without disrupting the entire process.
- Resource Optimization: By analyzing the BOM, you can identify opportunities to optimize resource usage. For instance, you can group similar assembly tasks together to minimize setup time and enhance resource efficiency.
- Capacity Planning: A well-structured BOM aids in capacity planning by providing insights into the production volume and resource requirements for different products. This information helps in determining whether existing resources can meet demand or if additional resources are needed.
- Collaborative Decision-Making: The BOM serves as a common reference point for various departments involved in resource allocation, such as production, engineering, and operations. Collaborative decision-making based on accurate and shared information leads to more effective resource allocation.
In summary, a multi-level BOM enables organizations to allocate resources efficiently by providing a comprehensive breakdown of component requirements and assembly processes.
This knowledge leads to balanced workloads, optimized equipment utilization, improved scheduling, and better overall resource management, all of which contribute to enhanced operational efficiency.
Demand Forecasting and Capacity Planning
Demand forecasting and capacity planning are crucial elements of operational efficiency, and a multi-level Bill of Materials (BOM) can significantly contribute to both aspects.
Let's delve deeper into how a multi-level BOM helps in demand forecasting and capacity planning:
Demand Forecasting and Capacity Planning with Multi-Level BOM:
Demand Forecasting:
Demand forecasting involves predicting the number of products that customers will purchase over a specific time period. Accurate demand forecasting helps organizations plan their production schedules, manage inventory levels, and ensure that they can meet customer demands without overstocking or stockouts.
A multi-level BOM plays a vital role in demand forecasting by providing a structured view of the components required to assemble the final product:
- Granular Analysis: The BOM breaks down the product into its constituent parts and subassemblies. This granularity allows you to analyze the historical demand patterns for each component and subassembly, providing insights into their individual demand trends.
- Predictive Modeling: By examining past sales data and considering factors such as seasonality, market trends, and economic indicators, you can develop predictive models for future demand. These models can be applied to each level of the BOM to estimate component and subassembly requirements.
- Accurate Production Planning: Armed with a clear understanding of the components needed for each product, you can create production plans that align with the forecasted demand. This minimizes the risk of overproduction or underproduction and ensures efficient resource allocation.
- Effective Inventory Management: Accurate demand forecasts derived from the BOM enable better inventory management. You can adjust your material orders based on expected demand, preventing excess inventory and reducing carrying costs.
Capacity Planning:
Capacity planning involves determining the production capacity needed to meet forecasted demand. It ensures that an organization's resources, such as labor, equipment, and workspace, are aligned with production requirements.
A multi-level BOM facilitates effective capacity planning in the following ways:
- Understanding Resource Requirements: The BOM outlines the components and subassemblies required for each product. This information helps you calculate the resources (labor hours, machine time, etc.) needed for each assembly step.
- Resource Allocation: Based on the BOM, you can allocate resources efficiently to different production stages. This includes scheduling labor shifts, managing equipment availability, and optimizing workspace usage.
- Production Sequencing: The BOM aids in determining the sequence of assembly steps. This sequencing is essential for optimizing resource allocation and preventing production bottlenecks.
- Workload Balancing: With insights from the BOM, you can distribute production tasks across workstations and teams evenly. Balancing the workload prevents overloading specific resources and ensures consistent production flow.
- Scalability: As demand fluctuates, the BOM allows you to scale production up or down based on the number of finished products required. This scalability ensures that you can meet demand without straining resources.
- Resource Investment: The BOM helps in making informed decisions about investing in additional resources, such as hiring more staff or acquiring new equipment, to accommodate increased demand.
- Lean Manufacturing: Lean principles emphasize producing only what is needed when it is needed. The BOM guides lean manufacturing practices by providing insights into material and resource requirements for each assembly step.
In summary, a multi-level BOM serves as a valuable tool for demand forecasting and capacity planning.
It enables organizations to accurately estimate future demand, align production plans with that demand, allocate resources effectively, and ensure that the right capacity is available to meet customer needs.
This results in optimized production processes minimized waste, and enhanced operational efficiency.
Streamlined Production Processes
This point emphasizes how a multi-level Bill of Materials (BOM) contributes to streamlined production processes. Let's explore in more detail how a well-structured BOM helps optimize and improve the efficiency of production operations:
Streamlined Production Processes with Multi-Level BOM:
A streamlined production process refers to an optimized workflow where tasks and activities are organized and executed in a smooth and efficient manner. A multi-level BOM is a valuable tool that supports streamlined production processes in several ways:
- Assembly Sequencing: The BOM provides a clear hierarchy of components and subassemblies, indicating the order in which they need to be assembled. This sequencing helps production managers plan and organize the production flow, reducing the need for backtracking and minimizing unnecessary handling.
- Task Prioritization: With a detailed BOM, you can identify critical components or subassemblies that play a significant role in the final product's functionality or quality. Production teams can prioritize the assembly of these critical elements to ensure that they are installed correctly and with proper attention to detail.
- Reduced Errors and Rework: The BOM helps operators and assemblers follow a structured assembly process. Clear instructions and component lists minimize the risk of errors, missteps, and incorrect installations, reducing the need for rework and improving overall product quality.
- Minimized Handling Time: By understanding the sequence of assembly steps and the components needed at each stage, production teams can minimize unnecessary handling and movement of materials. This reduces assembly time and lowers the chances of damage or defects during the assembly process.
- Optimized Workstation Layout: The BOM provides insights into the space requirements for different components and subassemblies. This information aids in designing an efficient workstation layout, ensuring that tools, materials, and equipment are positioned for easy access and reduced ergonomic strain.
- Efficient Equipment Utilization: Production managers can use the BOM to schedule equipment and machinery based on the specific components and subassemblies required. This prevents equipment bottlenecks and ensures that each piece of machinery is utilized optimally.
- Standardization of Processes: The BOM supports process standardization by clearly defining the steps needed to assemble the product. This uniformity simplifies training for new employees and reduces the likelihood of process variations that can lead to errors.
- Rapid Training and Onboarding: New employees can be trained more efficiently when following a structured assembly process outlined in the BOM. This minimizes the learning curve and helps new hires become productive more quickly.
- Continuous Improvement: The BOM serves as a reference point for evaluating and optimizing production processes. By analyzing the assembly sequence and identifying areas for improvement, organizations can implement continuous improvement initiatives to enhance efficiency over time.
- Lean Manufacturing: The BOM aligns with lean manufacturing principles by eliminating waste, reducing unnecessary steps, and focusing on value-added activities. This lean approach leads to a more efficient production process with fewer delays and bottlenecks.
In summary, a well-structured multi-level BOM is a cornerstone of streamlined production processes. It guides production teams through a structured assembly sequence, reduces errors, optimizes resource usage, and supports continuous improvement efforts. By aligning production operations with the BOM, organizations can achieve higher levels of efficiency, lower costs, and improved product quality.
Quality Control and Traceability
This point emphasizes how a multi-level Bill of Materials (BOM) contributes to quality control and traceability in manufacturing and production processes. Let's delve deeper into how a BOM enhances quality control practices and enables effective traceability:
Quality Control and Traceability with Multi-Level BOM:
Quality control refers to the systematic measures and processes put in place to ensure that products meet specific standards and fulfill customer expectations. Traceability involves the ability to track and document the origin, history, and movement of components, materials, and products throughout the supply chain and production process.
A well-structured multi-level BOM plays a vital role in both quality control and traceability:
- Component Verification: The BOM provides a clear list of components required for each level of assembly. Quality control teams can use this information to verify that the correct components are used and that they meet quality standards before assembly.
- Assembly Verification: During the assembly process, operators can reference the BOM to ensure that each component is correctly installed in the proper sequence. This minimizes the risk of assembly errors and ensures that the final product meets design specifications.
- Inspection Points: The BOM helps define critical inspection points within the assembly process. Quality control teams can focus on these points to perform detailed inspections, test functionality, and verify that quality standards are maintained.
- Batch and Lot Tracking: For products that require batch or lot tracking, the BOM provides the necessary information to associate specific components with a particular batch or lot. This traceability enables quick identification and recall of products if quality issues arise.
- Root Cause Analysis: In the event of a quality issue or defect, the BOM allows for effective root cause analysis. By tracing back through the BOM, organizations can identify which components or assembly steps may have contributed to the problem.
- Supplier Quality Management: The BOM helps track the quality of components provided by different suppliers. If quality issues arise, organizations can use the BOM to identify which supplier's components are affected, enabling targeted quality improvement efforts.
- Regulatory Compliance: Certain industries, such as aerospace and medical devices, have strict regulatory requirements for traceability and quality control. The BOM provides the necessary documentation and visibility to ensure compliance with these regulations.
- Continuous Improvement: When quality issues are detected and addressed, the BOM helps monitor the effectiveness of corrective actions over time. This supports a culture of continuous improvement and ensures that similar issues are prevented in the future.
- Enhanced Supplier Collaboration: Sharing the BOM with suppliers allows them to understand the criticality of their components in the final product. This can lead to improved collaboration, better communication, and higher-quality components.
- Customer Confidence: Effective quality control and traceability practices supported by the BOM enhance customer confidence. Knowing that products undergo rigorous inspection and can be traced back to their components instills trust and ensures customer satisfaction.
In summary, a multi-level BOM acts as a central reference point for quality control and traceability efforts. It helps ensure that products meet quality standards, enables quick identification and resolution of issues, supports regulatory compliance, and enhances overall product quality.
By utilizing the BOM for quality control and traceability, organizations can maintain a strong reputation, minimize risks, and deliver high-quality products to their customers.
Rapid New Product Introductions
This point emphasizes how a multi-level Bill of Materials (BOM) contributes to rapid new product introductions (NPI) within a manufacturing or production environment. Let's explore in more detail how a BOM facilitates efficient NPI processes:
Rapid New Product Introductions (NPI) with Multi-Level BOM:
New Product Introductions (NPI) involve the process of designing, developing, and bringing a new product to market quickly and efficiently.
A well-structured multi-level BOM plays a crucial role in achieving rapid NPI by providing a clear roadmap for designing and producing the new product:
- Component Identification: When introducing a new product, engineers and designers can use the BOM to identify the necessary components and subassemblies required for the product's design. This ensures that all required elements are considered during the design phase.
- Design Integration: The BOM acts as a bridge between design and production. Designers can create the product's design while referencing the BOM to ensure that the design is aligned with manufacturing capabilities and constraints.
- Feasibility Assessment: By reviewing the BOM, production, and engineering teams can assess the feasibility of producing the new product. They can identify any potential challenges related to component availability, assembly complexity, or resource requirements.
- Prototype Development: During the prototyping stage, the BOM guides the assembly of prototypes, ensuring that they are built with the correct components and subassemblies. This allows for accurate testing and validation of the product's functionality.
- Supplier Engagement: Sharing the BOM with suppliers early in the NPI process helps establish collaboration and communication. Suppliers can better understand the component requirements and specifications, facilitating faster sourcing and procurement.
- Resource Planning: The BOM aids in planning resource allocation for the new product's production. This includes scheduling labor, securing equipment, and ensuring that production capacity aligns with anticipated demand.
- Production Setup: The BOM provides a clear sequence of assembly steps for the new product. Production teams can use this information to set up assembly lines, arrange workstations, and ensure that the production process is efficient and organized.
- Testing and Validation: The BOM helps define the testing and validation requirements for the new product. Quality control and testing procedures can be developed based on the BOM to ensure that the product meets quality standards.
- Efficient Ramp-Up: As production volumes increase during the NPI phase, the BOM helps scale up production while maintaining consistency and quality. It guides the production teams in managing increased demand while avoiding bottlenecks.
- Continuous Improvement: As the new product is introduced and produced, the BOM serves as a reference for evaluating the efficiency of the NPI process. Any challenges or inefficiencies identified during NPI can be addressed for future product introductions.
In summary, a multi-level BOM is a valuable tool for achieving rapid and successful new product introductions. It ensures that all aspects of design, production, and resource allocation are aligned, enabling a smooth transition from design to production and accelerating time-to-market.
By leveraging the BOM for NPI, organizations can effectively manage complexity, reduce risks, and bring innovative products to market faster and more efficiently.
Supplier Collaboration
This point highlights how a multi-level Bill of Materials (BOM) fosters effective supplier collaboration in manufacturing and production processes. Let's delve deeper into how a BOM facilitates collaboration with suppliers:
Supplier Collaboration with Multi-Level BOM:
Supplier collaboration involves close cooperation and communication between manufacturers and their suppliers to ensure the timely and efficient supply of components and materials needed for production.
A well-structured multi-level BOM serves as a foundation for building strong supplier relationships and streamlining supply chain interactions:
- Clear Component Requirements: The BOM outlines the specific components and subassemblies required for a product. Sharing this detailed information with suppliers helps them gain a clear understanding of the components they need to provide and their respective quantities.
- Accurate Specifications: The BOM includes specifications for each component, such as dimensions, materials, and quality standards. Suppliers can use this information to ensure that the components they deliver meet the required specifications.
- Timely Procurement: By sharing the BOM with suppliers, they can align their production and procurement schedules with your needs. This reduces lead times and ensures that components are available when needed, preventing production delays.
- Synchronized Production: Suppliers can use the BOM to synchronize their own production schedules with your production needs. This coordination helps prevent overproduction or underproduction of components, reducing excess inventory or shortages.
- Collaborative Planning: The BOM provides a common reference point for collaborative planning discussions between manufacturers and suppliers. Both parties can assess the production requirements and identify potential challenges or opportunities for improvement.
- Early Engagement: Sharing the BOM early in the product development process allows suppliers to provide input and feedback on component design, materials, and sourcing options. This early engagement can lead to cost savings and improved component quality.
- Cost Estimation: Suppliers can use the BOM to estimate the costs associated with producing the required components. This information helps manufacturers assess the overall cost of production and make informed decisions about sourcing strategies.
- Quality Assurance: Suppliers can align their quality control processes with the BOM specifications to ensure that components meet the required quality standards. This contributes to higher overall product quality.
- Continuous Improvement: Suppliers can collaborate with manufacturers to identify opportunities for process improvement and cost reduction. By analyzing the BOM and production requirements together, both parties can work toward mutual efficiency gains.
- Risk Mitigation: Effective collaboration allows suppliers to anticipate changes in demand or product specifications. This enables them to proactively address potential supply chain disruptions and minimize risks to production.
- Transparency: Sharing the BOM fosters transparency between manufacturers and suppliers. Suppliers gain insight into your production needs, enabling them to align their resources and capabilities to meet your requirements.
In summary, a multi-level BOM is a powerful tool for facilitating supplier collaboration and optimizing the supply chain. It promotes clear communication, synchronized production schedules, accurate component specifications, and efficient procurement processes.
By leveraging the BOM for supplier collaboration, organizations can enhance supply chain efficiency, reduce lead times, improve product quality, and ultimately achieve greater operational efficiency.
Cost Analysis and Optimization
This point emphasizes how a multi-level Bill of Materials (BOM) supports cost analysis and optimization efforts within a manufacturing or production environment.
Let's explore in more detail how a BOM contributes to effective cost analysis and optimization:
Cost Analysis and Optimization with Multi-Level BOM:
Cost analysis involves assessing the various expenses associated with producing a product, while cost optimization aims to identify opportunities to reduce these expenses without compromising quality or functionality.
A well-structured multi-level BOM plays a crucial role in both cost analysis and optimization:
- Component Cost Breakdown: The BOM provides a detailed breakdown of the components and subassemblies required for a product. Each component's cost can be tracked and analyzed, allowing for a comprehensive understanding of the total production cost.
- Direct and Indirect Costs: The BOM helps distinguish between direct costs (materials and labor directly involved in production) and indirect costs (overhead, utilities, etc.). This differentiation enables a more accurate assessment of cost drivers.
- Supplier Comparison: By analyzing component costs across different suppliers, manufacturers can identify cost variations and negotiate favorable terms. The BOM allows for informed decisions about sourcing strategies and potential cost savings.
- Value Engineering: Engineers and designers can review the BOM to identify opportunities for value engineering. This involves optimizing designs and components to achieve the same or improved functionality at a lower cost.
- Alternate Materials: The BOM facilitates the evaluation of alternate materials or components that may offer cost savings without compromising product quality or performance. This can lead to more economical sourcing decisions.
- Batch and Lot Costs: For industries that require batch or lot tracking, the BOM helps allocate costs to specific batches or lots. This ensures accurate cost analysis for products with varying production runs.
- Labor Cost Allocation: The BOM aids in allocating labor costs to specific assembly steps. This helps identify labor-intensive processes and opportunities for process improvement or automation.
- Cost of Goods Sold (COGS) Analysis: The BOM is a foundation for calculating the COGS, a key financial metric that directly impacts profitability. Accurate COGS analysis helps in pricing strategies and profit margin optimization.
- Total Cost of Ownership (TCO): Beyond production costs, the BOM contributes to assessing the TCO, which includes factors like maintenance, warranties, and end-of-life costs. TCO analysis informs decisions about product lifecycle management.
- Lean Manufacturing: The BOM supports lean principles by identifying waste, inefficiencies, and unnecessary costs in the production process. This information guides efforts to streamline processes and eliminate non-value-added activities.
- Continuous Improvement: As production and sourcing strategies evolve, the BOM serves as a reference point for ongoing cost analysis and optimization initiatives. Regular updates to the BOM support a culture of continuous improvement.
In summary, a multi-level BOM is a valuable tool for analyzing and optimizing production costs.
It empowers organizations to identify cost drivers, explore cost-saving opportunities, and make informed decisions that contribute to improved profitability and operational efficiency.
By leveraging the BOM for cost analysis and optimization, manufacturers can achieve better cost control, enhanced financial performance, and a competitive edge in the market.
Continuous Improvement
This point emphasizes how a multi-level Bill of Materials (BOM) contributes to continuous improvement within a manufacturing or production environment. Let's delve deeper into how a BOM supports continuous improvement efforts:
Continuous Improvement with Multi-Level BOM:
Continuous improvement, often referred to as Kaizen or Lean philosophy, involves ongoing efforts to identify, analyze, and implement enhancements in processes, products, and operations.
A well-structured multi-level BOM serves as a valuable tool for facilitating and sustaining continuous improvement:
- Process Analysis: The BOM provides a detailed breakdown of the assembly process, allowing teams to scrutinize each step and identify inefficiencies, bottlenecks, or areas for improvement.
- Root Cause Analysis: In the event of quality issues, defects, or production delays, the BOM helps trace back to the source of the problem, enabling teams to identify root causes and implement corrective actions.
- Data-Driven Decision-Making: By analyzing BOM data, teams can make informed decisions backed by quantitative insights, enabling them to prioritize improvement initiatives based on real data.
- Standardization: The BOM defines standardized processes and components, minimizing process variations that can lead to errors. Consistency in processes supports continuous improvement by providing a stable foundation for enhancements.
- Identifying Waste: The BOM aligns with Lean principles by highlighting waste in the production process, such as excessive inventory, overprocessing, or unnecessary transportation. Teams can target these areas for improvement.
- Benchmarking: By comparing BOM data across different product lines or manufacturing facilities, organizations can identify best practices and success stories that can be replicated for improvement.
- Kaizen Events: The BOM provides a reference point for Kaizen events—focused improvement workshops where cross-functional teams collaborate to address specific process challenges or opportunities.
- Iterative Design: During product development, the BOM supports iterative design and prototyping. As improvements are identified and tested, the BOM guides the incorporation of changes into subsequent iterations.
- Feedback Loop: The BOM serves as a feedback loop for continuous improvement. As changes are made to the assembly process, components, or design, the BOM is updated to reflect these improvements.
- Sustainability: The BOM can be used to evaluate the environmental impact of the product's components and processes. Continuous improvement efforts can include identifying eco-friendly alternatives.
- Employee Engagement: Involving employees in continuous improvement initiatives based on BOM insights fosters a culture of engagement, empowerment, and ownership of the production process.
- Real-Time Adaptation: As market conditions, customer preferences, or supply chain dynamics change, the BOM allows organizations to adapt quickly and make necessary adjustments for continuous improvement.
In summary, a multi-level BOM is a versatile tool that supports continuous improvement across various aspects of manufacturing and production. It enables teams to analyze processes, identify waste, implement changes, and monitor the impact of improvements.
By leveraging the BOM for continuous improvement, organizations can enhance efficiency, reduce costs, improve quality, and maintain a competitive edge in a rapidly evolving market.
How Does a Multi-Level BOM Contribute to Sustainable Practices?
A Multi-Level Bill of Materials (BOM) can contribute to sustainable practices in several ways, playing a significant role in promoting environmental responsibility and reducing the ecological impact of production processes.
Here's how a Multi-Level BOM supports sustainable practices:
- Material Selection: The BOM provides a detailed breakdown of components and materials used in a product. This information enables manufacturers to make informed choices about the materials they use, opting for more sustainable and eco-friendly options.
- Environmental Impact Assessment: By analyzing the BOM, organizations can assess the environmental impact of their products and processes. This assessment includes evaluating factors such as carbon footprint, energy consumption, and resource usage.
- Life Cycle Analysis: The BOM facilitates life cycle analysis, helping manufacturers understand the environmental impact of a product from raw material extraction to disposal. This analysis guides decisions to minimize environmental harm at each stage.
- Eco-Friendly Alternatives: The BOM allows manufacturers to explore and integrate eco-friendly components, materials, or manufacturing processes that reduce pollution, waste, and resource consumption.
- Design for Sustainability: Engineers can use the BOM to design products with sustainability in mind, considering factors like recyclability, reusability, and extended product life cycles.
- Waste Reduction: A well-structured BOM aids in optimizing production processes, which can lead to reduced material waste, better inventory management, and decreased scrap rates.
- Supplier Collaboration: Sharing the BOM with suppliers encourages them to provide sustainable materials and components, fostering a supply chain that aligns with environmentally responsible practices.
- End-of-Life Considerations: The BOM helps manufacturers plan for the end of a product's life cycle, including recycling or proper disposal of components, minimizing environmental impact.
- Resource Efficiency: With a clear view of component requirements, organizations can optimize resource allocation, reducing excess consumption of energy, water, and raw materials.
- Regulatory Compliance: Many industries face environmental regulations. The BOM assists in ensuring compliance by tracking and documenting the use of compliant components and materials.
- Transparency and Reporting: A comprehensive BOM supports transparency and reporting efforts related to sustainability initiatives, allowing organizations to communicate their eco-friendly practices to stakeholders.
- Continuous Improvement: By analyzing BOM data and assessing environmental impact, organizations can continuously improve their sustainability efforts over time, seeking ways to further reduce their ecological footprint.
Incorporating sustainability into the BOM-driven decision-making process can lead to a more responsible and ethical approach to manufacturing.
By making conscious choices at the component and material level, organizations can contribute to a healthier planet while maintaining operational efficiency and delivering high-quality products.
Can a Multi-Level BOM be Adapted for Different Industries?
Yes, a Multi-Level Bill of Materials (BOM) can indeed be adapted for different industries. The fundamental concept of a BOM, which outlines the hierarchical structure of components and subassemblies required to manufacture a product, is applicable across a wide range of industries.
The adaptability of a Multi-Level BOM lies in its flexibility to accommodate the specific needs and complexities of different sectors. Here's how:
- Manufacturing Industry: In traditional manufacturing, a Multi-Level BOM is commonly used to plan and execute the production of physical goods. It ensures that the correct components are assembled in the right sequence to create finished products.
- Aerospace and Defense: In this industry, where precision and safety are paramount, a Multi-Level BOM helps manage intricate assemblies, track materials for compliance, and ensure traceability for critical components.
- Automotive: Automotive manufacturing relies on BOMs to organize the multitude of components that make up a vehicle, from engines to electronics, enabling efficient assembly lines and quality control.
- Electronics: Electronics manufacturers utilize BOMs to manage the complex arrays of components in devices, ensuring correct placements, soldering, and testing.
- Medical Devices: BOMs play a critical role in the production of medical devices, ensuring adherence to regulations, tracking sterilization processes, and maintaining the highest quality standards.
- Consumer Goods: In industries producing consumer goods like appliances or furniture, a Multi-Level BOM aids in coordinating assembly lines, optimizing inventory, and monitoring production costs.
- Food and Beverage: In the food industry, a BOM outlines ingredients and packaging, ensuring accurate recipe formulations, allergen management, and compliance with nutritional labeling requirements.
- Pharmaceuticals: BOMs are integral to pharmaceuticals for managing drug formulations, tracking active ingredients, and maintaining consistency in manufacturing processes.
- Construction: Construction projects benefit from BOMs to coordinate materials, plan for stages of construction, and ensure accurate cost estimation.
- Energy and Utilities: In energy production, BOMs assist in managing the complex systems of equipment and components needed for power generation and distribution.
- Technology: For software development, a BOM can represent the hierarchy of code modules and libraries that comprise an application, facilitating version control and software releases.
In each of these industries, a Multi-Level BOM can be adapted and customized to meet specific requirements, such as compliance standards, quality control measures, regulatory considerations, and the unique characteristics of the products being manufactured.
Whether in traditional manufacturing or cutting-edge technology, the versatility of a Multi-Level BOM makes it a valuable tool for achieving operational efficiency and excellence across diverse sectors.
How Can Deskera Help You with a Multi-Level Bill of Materials?
Deskera MRP is an integrated software solution designed to help businesses manage their manufacturing processes, including multi-level bills of materials.
Here’s how Deskera can assist you with the multi-level bill of materials:
- Multi-Level BOM Creation and Management: Manage product structures with ease using the multi-level bill of materials. Assign multiple components to a single product. Identify components and subcomponents of each product, and easily track their usage, movement, and costs.
- Improve Productivity: Deskera will help you improve productivity because it facilitates the automatic generation of bills of materials, thereby helping to reach your production goals faster. It also automates the process of managing and maintaining multi-level bills of materials.
- Enhances Collaboration: By increasing the visibility and communication between the departments of your company, Deskera will help improve collaboration between different teams. In fact, it also allows multiple users to access and edit the bill of materials. All of this will also facilitate faster and more informed decision-making.
- Improve Inventory Costs: With Deskera, you will be able to improve your inventory costs as the accuracy of data with a single source of truth for the entire bill of materials is ensured. Through Deskera, all the required documents can be automatically generated from this single source of information. Lastly, through the automatic generation of a bill of materials, manual errors will be reduced.
- Reduce Production Costs: By streamlining the process of the bill of materials through Deskera, operation costs will be reduced. In fact, the time and resources spent on managing and updating complex bills of materials will also be reduced.
Key Takeaways
A Multi-Level BOM is a structured document that outlines the hierarchical breakdown of components and subassemblies required to manufacture a product, providing a clear view of its composition and assembly sequence.
A Multi-Level BOM enhances operational efficiency by providing insights for clear planning, optimized resource allocation, streamlined production, effective inventory management, quality control, and more.
The ways in which effective multi-level bill of materials can contribute to operational efficiency are:
- Clear Visibility and Planning: A multi-level BOM provides a comprehensive view of the entire product structure, including subassemblies, components, and their relationships. This visibility allows for better production planning, accurate scheduling, and resource allocation. Production managers can make informed decisions about materials procurement, labor allocation, and production timelines.
- Effective Inventory Management: With a multi-level BOM, you can track the quantities of each component required for different levels of assembly. This helps in maintaining optimal inventory levels, reducing excess stock, and preventing shortages. Efficient inventory management reduces carrying costs and ensures that required materials are available when needed, minimizing production delays.
- Resource Allocation: By understanding the components needed at each level of assembly, you can allocate resources such as labor and equipment more efficiently. This prevents overburdening specific workstations or teams and ensures a balanced production process.
- Demand Forecasting and Capacity Planning: A multi-level BOM enables better demand forecasting based on the number of finished products to be produced. This information is crucial for capacity planning and adjusting production levels to meet changing demand patterns.
- Streamlined Production Processes: Multi-level BOMs help identify bottlenecks and potential inefficiencies in the production process. By analyzing the relationships between components and subassemblies, you can optimize the sequence of assembly steps, reduce handling time, and minimize the risk of errors.
- Quality Control and Traceability: With a detailed BOM, you can establish quality control checkpoints at various assembly stages. This ensures that each component is correctly installed and that the final product meets quality standards. Additionally, traceability becomes easier, enabling you to track the origin of any defects and take corrective actions.
- Rapid New Product Introductions: When introducing new products or making modifications to existing ones, a multi-level BOM allows for efficient planning and coordination. You can quickly identify which components need to be modified or sourced and assess the impact on the overall production process.
- Supplier Collaboration: Sharing the multi-level BOM with suppliers facilitates better collaboration and communication. Suppliers can better understand your requirements, lead times, and production schedules, which can lead to more reliable deliveries and smoother procurement processes.
- Cost Analysis and Optimization: A multi-level BOM provides a clear breakdown of costs associated with each component and assembly level. This enables cost analysis and identifies opportunities for cost optimization, whether through sourcing alternative materials, negotiating better deals with suppliers, or improving production processes.
- Continuous Improvement: Regularly reviewing and updating the multi-level BOM promotes a culture of continuous improvement. By analyzing production data and feedback, you can identify areas for enhancement and implement changes to further optimize operational efficiency.
Incorporating a multi-level BOM into your operational processes enhances transparency, coordination, and decision-making. It empowers your organization to streamline production, reduce waste, improve resource utilization, and ultimately achieve higher levels of operational efficiency.
By embracing the principles embedded within a Multi-Level BOM, organizations can navigate the intricate balance between efficiency and quality, agility and precision. The BOM empowers manufacturers, engineers, and decision-makers to orchestrate harmonious and synchronized operations, delivering products that meet and exceed customer expectations while driving competitiveness and sustainability.
Overall, Deskera MRP will serve as a comprehensive solution for managing multi-level bills of materials. It will help streamline your bill of materials, automate production processes, track production costs, monitor supplier performance, improve supply chain management, streamline production planning, reduce inventory errors, optimize production scheduling, track production costs, and help you maximize efficiency with the multi-level bill of materials.
Related Articles
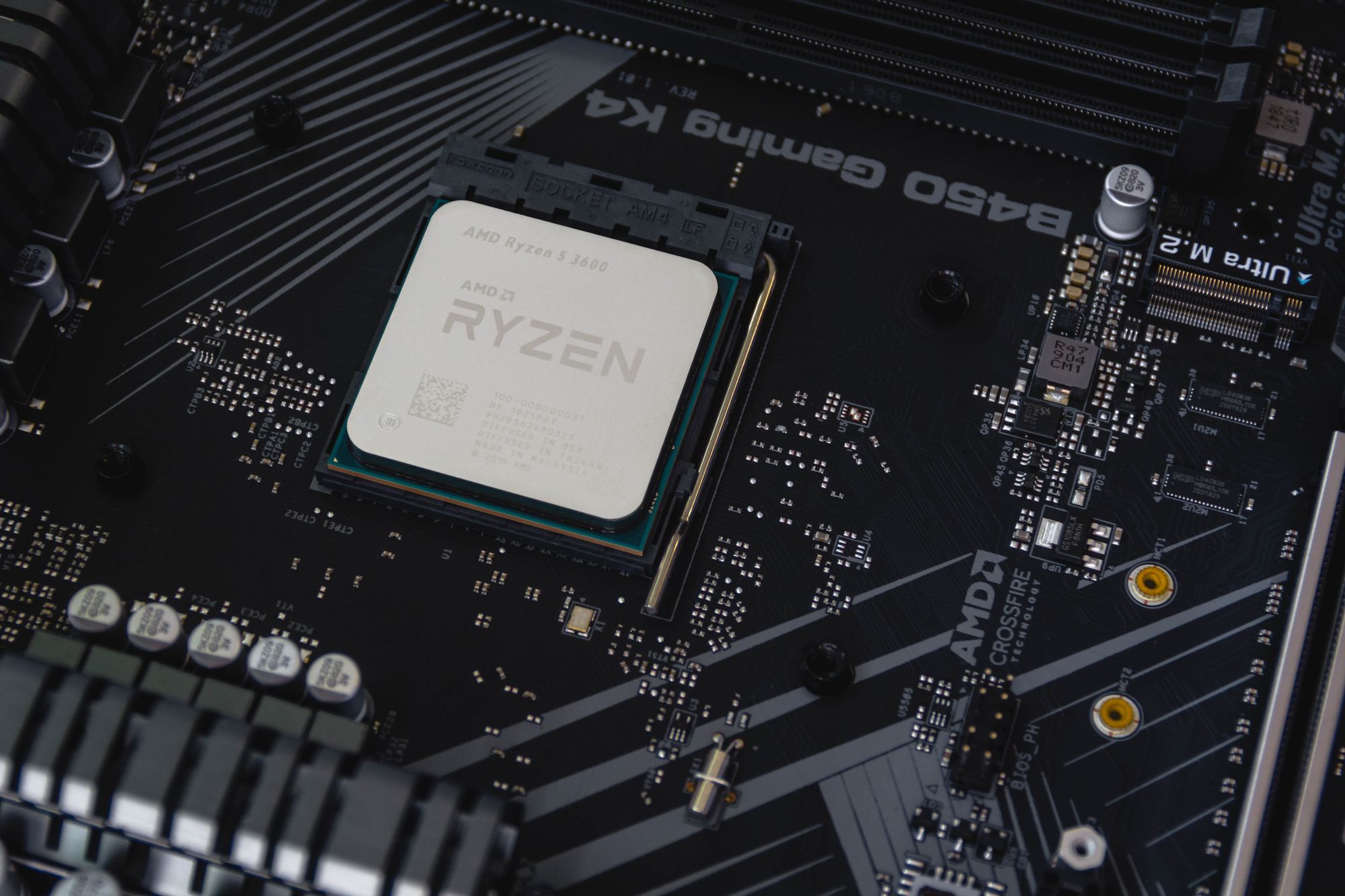
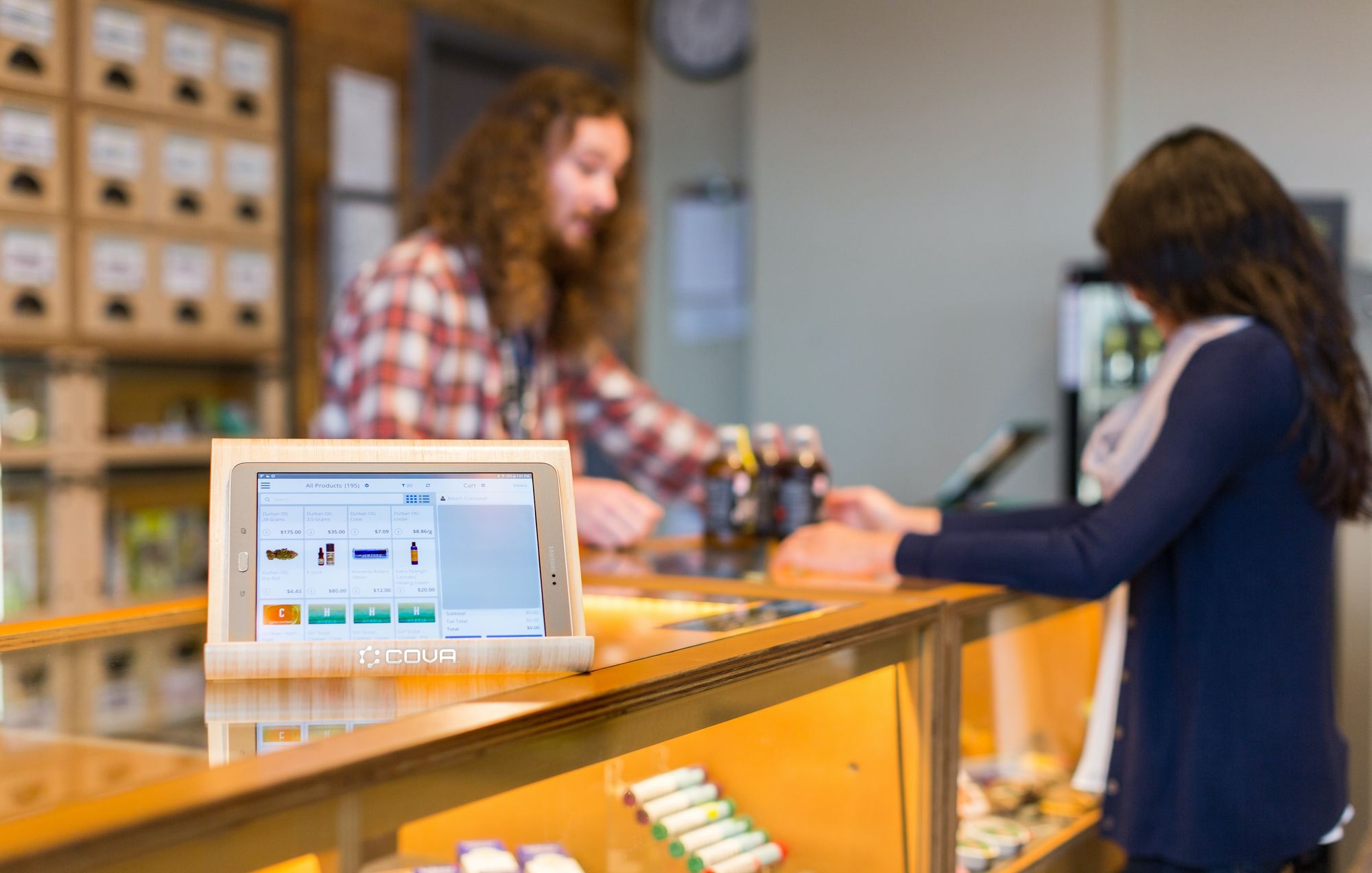
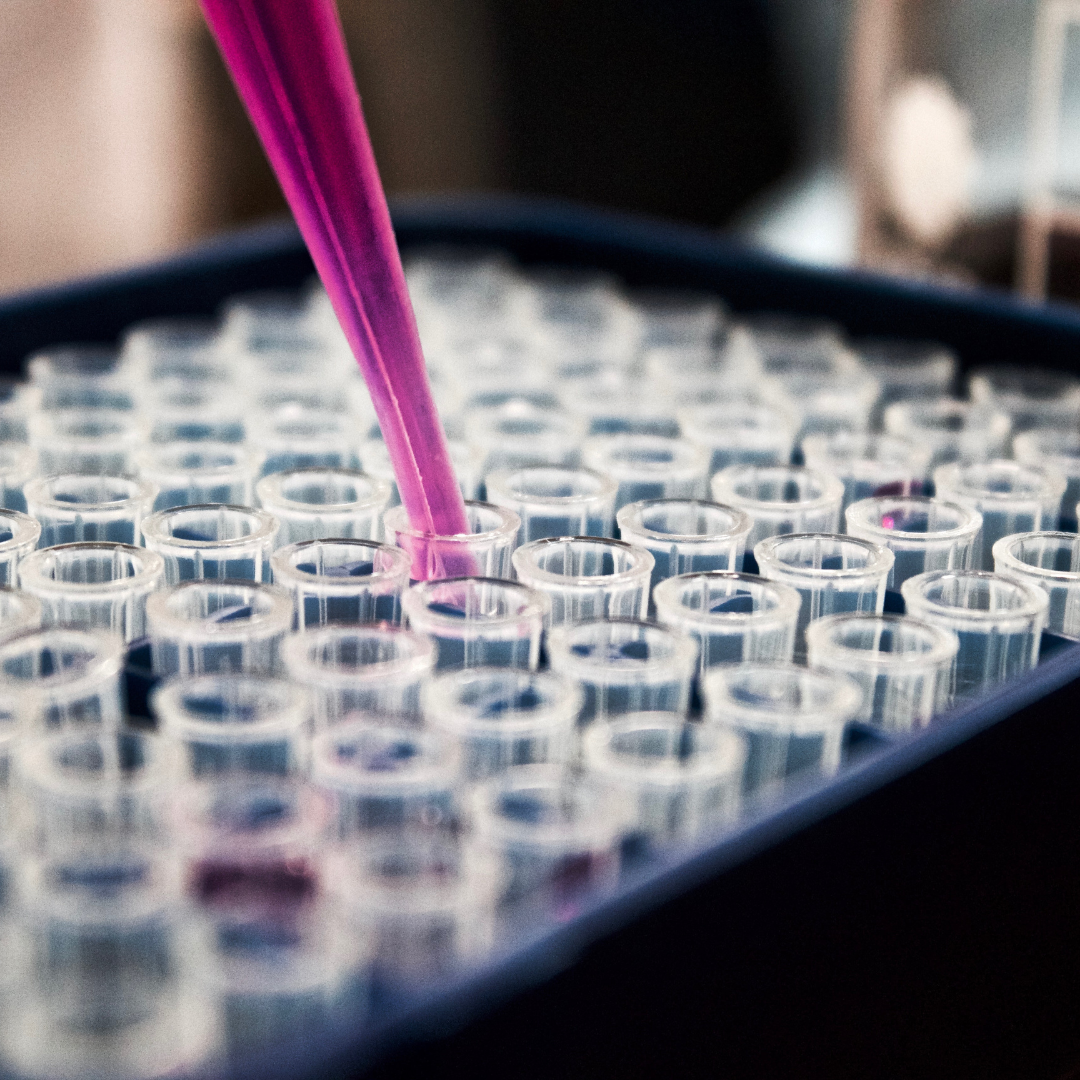
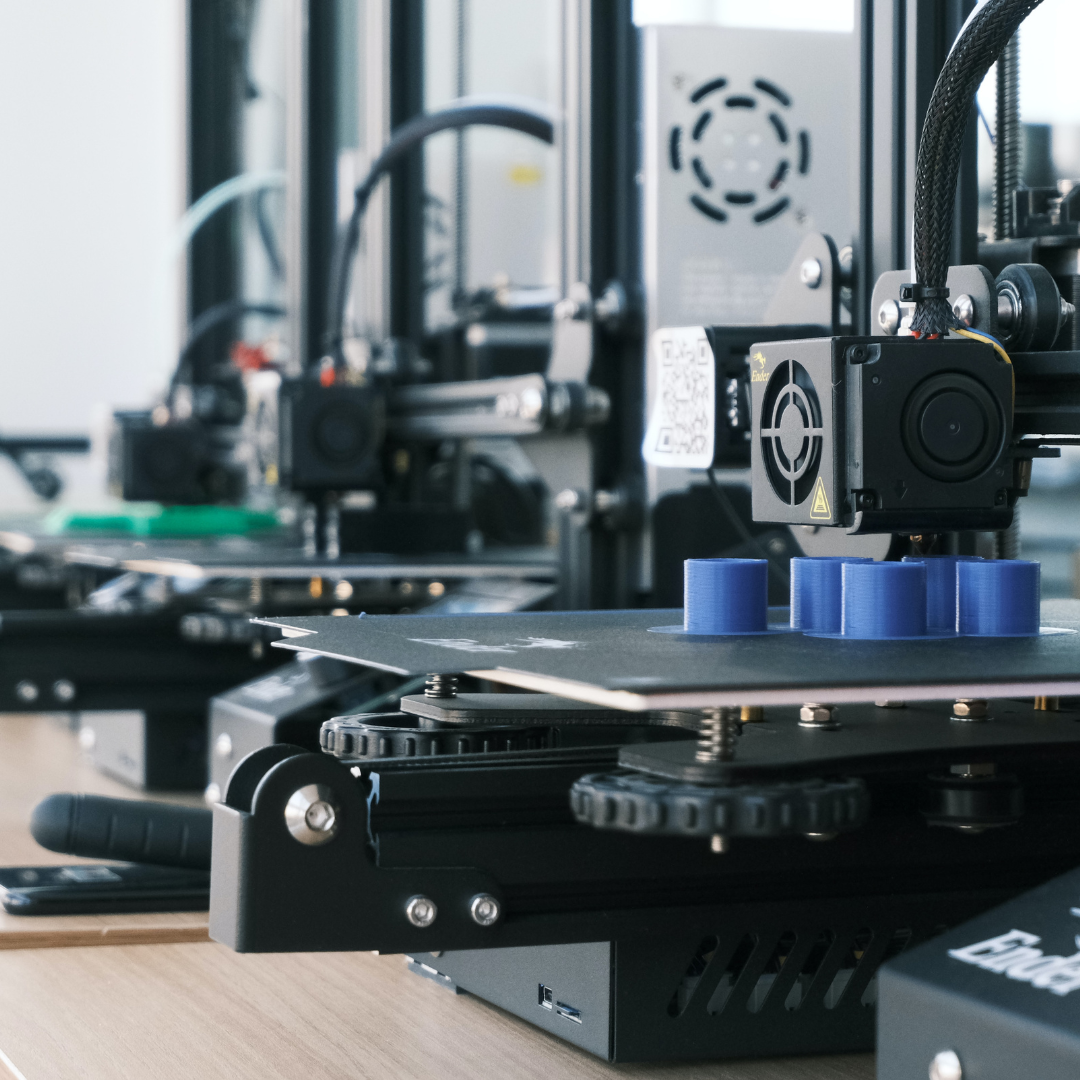
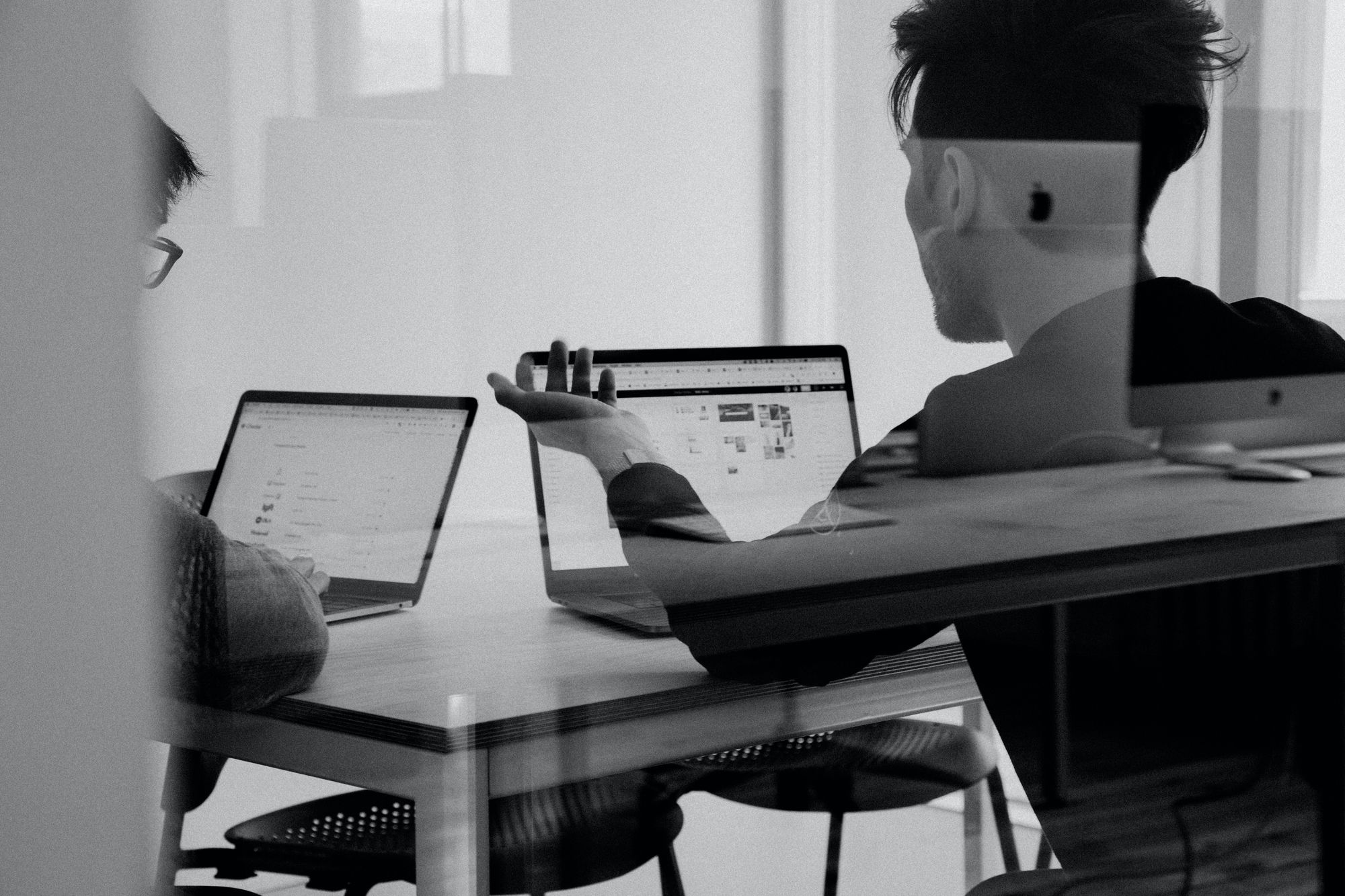