Improving quality control in chemical manufacturing is critical for producing high-quality products that meet customer expectations and comply with industry standards and regulations. This involves a systematic approach to ensuring that all products meet the required quality standards.
In this article, we will discuss in detail various ways to improve quality control in chemical manufacturing.
- Establish a Quality Control Plan
- Train Employees
- Implement Quality Control Checks
- Use Quality Control Tools
- Maintain Equipment
- Conduct Supplier Evaluations
- Continuously Improve
- Conclusion
Establish a Quality Control Plan
Establishing a quality control plan is critical to improving quality control in chemical manufacturing. The quality control plan should outline the specific quality standards that must be met for each product, from raw material selection to final product testing. It should also include procedures for identifying and correcting any quality issues that arise during the manufacturing process. Here are some steps to follow to establish a quality control plan:
- Define Quality Standards: Start by defining the quality standards for each product. This includes purity and composition requirements, physical and chemical properties, packaging and labeling requirements, and environmental and safety regulations.
- Identify Critical Control Points: Identify critical control points in the manufacturing process where quality control measures must be applied. Critical control points are points in the process where failure to meet quality standards could result in a product that is out of specification or unsafe.
- Develop Quality Control Procedures: Develop quality control procedures for each critical control point. These procedures should include instructions for testing and monitoring the process to ensure that quality standards are met. Procedures should also include instructions for corrective actions to be taken in case quality standards are not met.
- Determine Sampling Plans: Determine sampling plans for each critical control point. This includes how often samples should be taken, how many samples should be taken, and which tests should be performed on the samples.
- Define Acceptance Criteria: Define acceptance criteria for each test that will be performed. Acceptance criteria should specify the minimum acceptable result for each test. If a sample fails to meet the acceptance criteria, corrective action should be taken.
- Develop Record Keeping Procedures: Develop record-keeping procedures to document the results of quality control tests and corrective actions taken. Records should include the date and time of the test, the test result, and any corrective actions taken.
- Review and Update: Review the quality control plan regularly to ensure that it reflects current best practices and industry standards. Update the plan as necessary to address changes in the manufacturing process or regulatory requirements.
By following these steps, chemical manufacturers can establish a comprehensive quality control plan that will ensure that all products meet the required quality standards.
Train Employees
Training employees is an important step in improving quality control in chemical manufacturing. Employees who are properly trained can identify and prevent quality issues, perform quality control tests accurately, and take corrective actions when necessary. Here are some steps to follow when training employees:
- Define Job Responsibilities: Start by defining each employee's job responsibilities related to quality control. This includes identifying the critical control points in their area of responsibility, outlining the quality control procedures they are responsible for following, and explaining the corrective actions they should take if quality standards are not met.
- Provide General Training: Provide general training on quality control principles, industry standards, and regulatory requirements. This should include topics such as Good Manufacturing Practices (GMP), quality control tools and techniques, laboratory safety, and proper documentation practices.
- Provide Job-Specific Training: Provide job-specific training on quality control procedures for each critical control point. This includes training on how to perform tests accurately, how to interpret test results, and how to take corrective actions when necessary.
- Monitor Performance: Monitor employee performance regularly to ensure that quality control procedures are being followed correctly. This can include observing employees as they perform quality control tests, reviewing documentation to ensure that tests are being performed at the required frequency, and analyzing test results to ensure that they are within acceptable limits.
- Provide Refresher Training: Provide refresher training regularly to ensure that employees stay up-to-date with best practices and regulatory requirements. Refresher training can also be provided when changes are made to quality control procedures or when new products are introduced.
By following these steps, chemical manufacturers can ensure that all employees are properly trained in quality control procedures and can perform their job responsibilities effectively. This will help prevent quality issues and ensure that all products meet the required quality standards.
Implement Quality Control Checks
Implementing quality control checks is a critical step in improving quality control in chemical manufacturing. Quality control checks are used to ensure that products meet the required quality standards and comply with industry regulations. Here are some steps to follow when implementing quality control checks:
- Identify Critical Control Points: Identify the critical control points in the manufacturing process where quality control checks must be performed. This includes points in the process where failure to meet quality standards could result in a product that is out of specification or unsafe.
- Define Quality Control Procedures: Develop quality control procedures for each critical control point. These procedures should include instructions for testing and monitoring the process to ensure that quality standards are met. Procedures should also include instructions for corrective actions to be taken in case quality standards are not met.
- Determine Sampling Plans: Determine sampling plans for each critical control point. This includes how often samples should be taken, how many samples should be taken, and which tests should be performed on the samples.
- Define Acceptance Criteria: Define acceptance criteria for each test that will be performed. Acceptance criteria should specify the minimum acceptable result for each test. If a sample fails to meet the acceptance criteria, corrective action should be taken.
- Perform Quality Control Tests: Perform quality control tests according to the defined procedures and sampling plans. This includes performing physical, chemical, and microbiological tests to ensure that products meet the required quality standards.
- Document Results: Document the results of quality control tests and corrective actions taken. This includes recording the date and time of the test, the test result, and any corrective actions taken. Documentation should be accurate, complete, and readily accessible.
- Review and Analyze Results: Review and analyze quality control test results regularly to identify trends or patterns that may indicate quality issues. Use this information to make improvements to the manufacturing process or quality control procedures.
By following these steps, chemical manufacturers can implement effective quality control checks that will ensure that all products meet the required quality standards and comply with industry regulations.
Use Quality Control Tools
Using quality control tools is an effective way to improve quality control in chemical manufacturing. These tools help to identify quality issues, monitor the manufacturing process, and track improvements over time. Here are some quality control tools that can be used in chemical manufacturing:
- Statistical Process Control (SPC): SPC is a method used to monitor and control a process by tracking process data over time. This helps to identify trends and patterns that can indicate a potential quality issue. SPC involves creating control charts that plot process data against upper and lower control limits. Any data points that fall outside these limits indicate a process that is out of control and requires corrective action.
- Pareto Analysis: Pareto analysis is a tool used to identify the most significant quality issues. It involves creating a Pareto chart that shows the frequency and relative importance of each quality issue. This helps to prioritize quality improvement efforts and focus resources on the most significant issues.
- Root Cause Analysis (RCA): RCA is a method used to identify the underlying cause of a quality issue. It involves asking a series of "why" questions to drill down to the root cause of the problem. Once the root cause has been identified, corrective actions can be taken to prevent the issue from recurring.
- Failure Mode and Effects Analysis (FMEA): FMEA is a tool used to identify potential failure modes in a process and their potential effects on product quality. This helps to prioritize quality improvement efforts and focus resources on the most critical failure modes.
- Six Sigma: Six Sigma is a data-driven methodology used to improve process quality by reducing defects and variability. It involves using statistical analysis to identify and eliminate sources of variation in a process. Six Sigma projects typically aim to achieve a defect rate of less than 3.4 defects per million opportunities.
By using these quality control tools, chemical manufacturers can identify quality issues, monitor the manufacturing process, and track improvements over time. This helps to ensure that all products meet the required quality standards and comply with industry regulations.
Maintain Equipment
Maintaining equipment is an essential aspect of improving quality control in chemical manufacturing. Well-maintained equipment is less likely to break down or produce inconsistent results, which can lead to product quality issues. Here are some steps that can be taken to maintain equipment:
- Create a maintenance schedule: Develop a maintenance schedule that outlines when equipment should be serviced and what tasks should be performed during each service. This schedule should be based on the manufacturer's recommendations and take into account the frequency of use and the nature of the equipment.
- Train personnel: Train personnel on how to properly use and maintain equipment. This includes providing training on how to perform routine maintenance tasks, such as cleaning and lubrication, and how to identify potential equipment issues.
- Conduct regular inspections: Conduct regular inspections of equipment to identify potential issues before they become major problems. This includes inspecting the equipment for signs of wear and damage, checking for proper alignment, and verifying that all safety features are functioning correctly.
- Keep records: Keep detailed records of all equipment maintenance and repairs. This includes documenting the date and type of maintenance performed, as well as any issues that were identified during the maintenance process. These records can be used to track equipment performance over time and identify trends that may indicate the need for additional maintenance or repairs.
- Replace worn or damaged parts: Replace worn or damaged parts as soon as they are identified. This helps to prevent equipment failure and ensures that the equipment is producing consistent results.
By maintaining equipment, chemical manufacturers can reduce the risk of equipment failure and ensure that all products meet the required quality standards. This can also help to reduce downtime and increase productivity, leading to improved efficiency and profitability.
Conduct Supplier Evaluations
Conducting supplier evaluations is another important step in improving quality control in chemical manufacturing. Chemical manufacturers often rely on raw materials and other supplies from external suppliers, and it is essential to ensure that these suppliers are meeting quality standards. Here are some steps that can be taken to conduct supplier evaluations:
- Define supplier requirements: Define the quality requirements for each supplier, including the specifications for the materials or supplies they provide, delivery times, and other performance criteria. These requirements should be based on industry standards and the specific needs of the manufacturing process.
- Develop a supplier evaluation system: Develop a system for evaluating suppliers that includes both qualitative and quantitative measures. This can include surveys, audits, and inspections to assess the supplier's quality control processes and their ability to meet the defined requirements.
- Assess supplier performance: Assess supplier performance regularly to identify any issues that may impact product quality. This includes evaluating their delivery performance, product quality, and responsiveness to requests for information or support.
- Establish corrective actions: Establish corrective actions to address any issues identified during the supplier evaluation process. This may include providing feedback to the supplier, implementing new quality control measures, or terminating the supplier relationship if necessary.
- Monitor supplier performance: Monitor supplier performance over time to ensure that they are meeting the defined quality requirements. This includes tracking performance metrics and implementing continuous improvement initiatives to improve supplier performance.
By conducting supplier evaluations, chemical manufacturers can ensure that they are receiving high-quality materials and supplies from reliable suppliers. This helps to reduce the risk of quality issues and improve the overall quality control process. It can also help to build stronger relationships with suppliers and establish a more reliable supply chain.
Continuously Improve
Continuous improvement is an essential aspect of improving quality control in chemical manufacturing. It involves regularly reviewing and evaluating processes, identifying areas for improvement, and implementing changes to achieve better results. Here are some steps that can be taken to implement a continuous improvement process:
- Establish a culture of continuous improvement: Create a culture where all employees are encouraged to identify areas for improvement and suggest solutions. This can be done through training, communication, and incentives that promote innovation and continuous learning.
- Gather data: Gather data on the manufacturing process and product quality to identify areas for improvement. This includes collecting data on product defects, customer complaints, and process inefficiencies.
- Analyze data: Analyze the data to identify trends and patterns that may indicate opportunities for improvement. This can be done using statistical tools such as control charts, Pareto charts, and cause-and-effect diagrams.
- Develop improvement initiatives: Develop improvement initiatives based on the data analysis. This can include process changes, equipment upgrades, and employee training programs.
- Implement improvements: Implement the improvements and monitor their impact on product quality and process efficiency. This includes tracking key performance indicators and conducting regular reviews to assess the effectiveness of the improvements.
- Repeat the process: Continuously review and evaluate the manufacturing process and product quality to identify new areas for improvement. This involves a cycle of continuous improvement that is ongoing and never-ending.
By implementing a continuous improvement process, chemical manufacturers can improve product quality, reduce waste and costs, and increase efficiency and profitability. This approach helps to create a culture of innovation and continuous learning that is essential for long-term success in the industry.
How can Deskera Help You?
Deskera's integrated financial planning tools allow investors to better plan their investments and track their progress. It can help investors make decisions faster and more accurately.
Deskera Books can assist you in automating your accounting and mitigating business risks. Deskera makes it easier to create invoices by automating many other procedures, reducing your team's administrative workload.
Deskera also offers a suite of integrated applications to help businesses manage their financials, inventory, and operations. Furthermore, other business aspects such as HR (Deskera People), CRM (Deskera CRM), and ERP are provided by Deskera. These could be crucial and can help short sellers keep track of their businesses and make better decisions.
Conclusion
Improving quality control in chemical manufacturing requires a systematic approach that includes establishing a quality control plan, training employees, implementing quality control checks, using quality control tools, maintaining equipment, conducting supplier evaluations, and continuously improving the manufacturing process. By implementing these steps, chemical manufacturers can improve quality control and produce high-quality products that meet customer expectations and comply with industry standards and regulations.
Related Articles
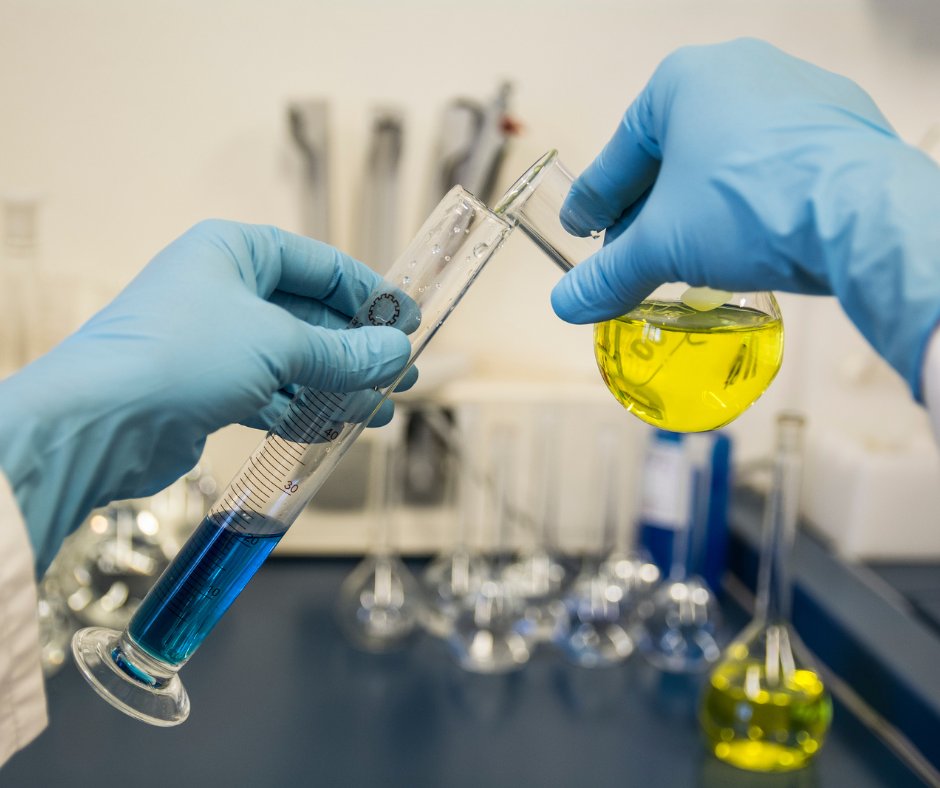
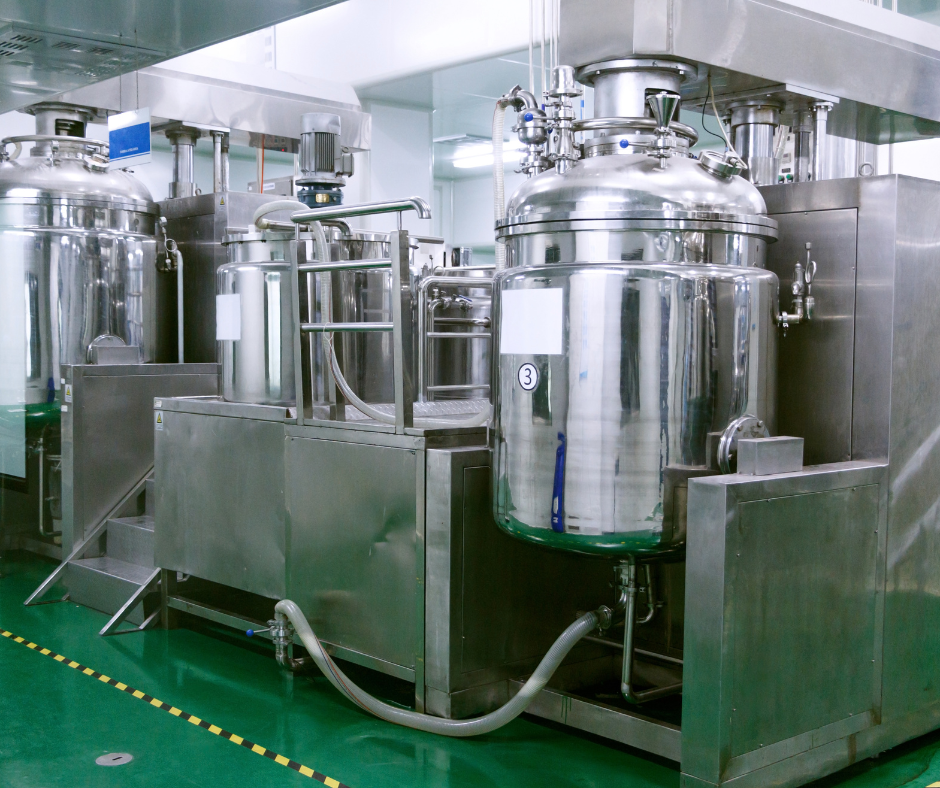
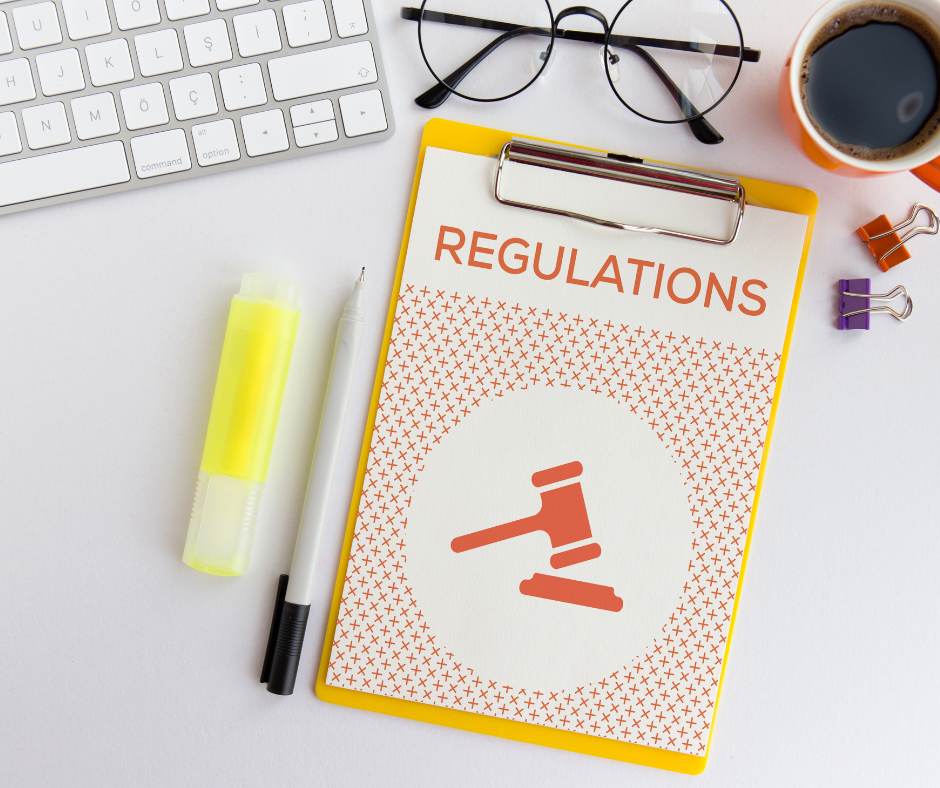