A well-structured and optimized production plan ensures streamlined operations, minimized costs, and increased customer satisfaction. However, many organizations still struggle with the complexities of managing materials, inventory, and production schedules, leading to inefficiencies and missed opportunities.
Enter Material Requirements Planning (MRP), a dynamic system that has revolutionized production planning by providing accurate and real-time insights into material needs and scheduling.
According to industry statistics, companies that have implemented MRP systems have witnessed remarkable improvements in their production processes. In fact, a recent survey of manufacturing firms revealed that those utilizing MRP experienced an average reduction of 25% in lead times and a substantial decrease of 40% in excess inventory levels.
In this article, we will explore the transformative potential of MRP in improving production planning. We will delve into the core components of MRP, discuss its benefits, and provide practical insights on implementing and leveraging MRP systems effectively.
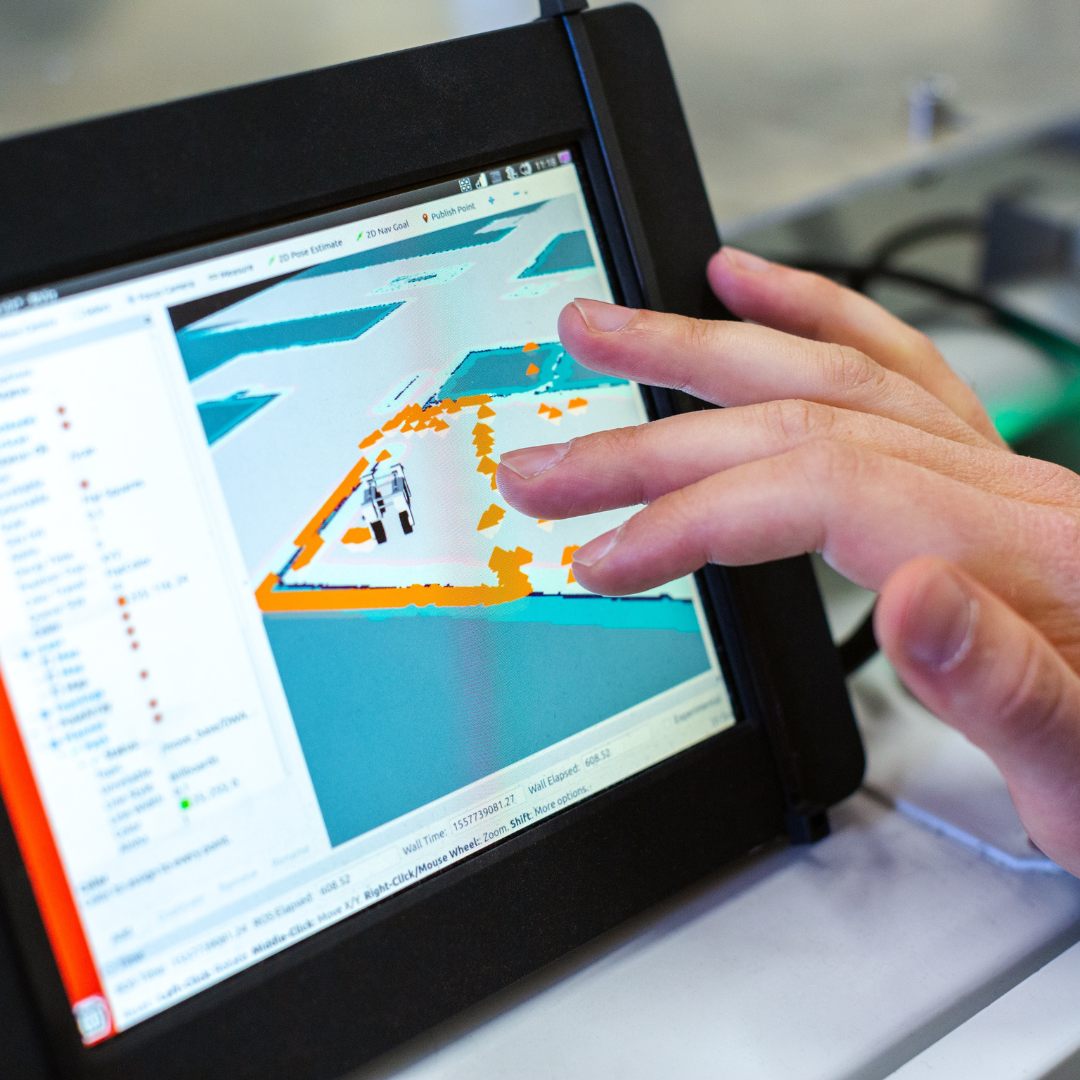
By harnessing the power of MRP, businesses can enhance their production planning capabilities and achieve greater operational efficiency in today's dynamic manufacturing landscape.
- Concept of Production Planning and its Significance in Manufacturing
- Challenges Faced in Production Planning and the Need for Effective Solutions like Material Requirements Planning (MRP)
- Understanding Material Requirements Planning (MRP)
- Benefits of Using MRP for Production Planning
- Implementing MRP in Production Planning
- Utilizing MRP Outputs for Production Planning
- Best Practices for Successful MRP Implementation
- Case Studies
- Conclusion
- How can Deskera Help You?
- Key Takeaways
- Related Articles
Concept of Production Planning and its Significance in Manufacturing
Production planning is a strategic process that involves the coordination and optimization of resources, materials, and processes to ensure efficient and timely manufacturing operations.
It encompasses various activities such as forecasting demand, scheduling production activities, managing inventory levels, and allocating resources effectively. The primary objective of production planning is to meet customer demand while minimizing costs and maximizing productivity.
The significance of production planning in manufacturing cannot be overstated. It serves as the foundation for operational success and enables organizations to achieve their production goals.
Here are some key reasons why production planning is crucial in the manufacturing industry:
- Meeting Customer Demand: Effective production planning ensures that products are manufactured in the right quantities, at the right time, and with the desired quality to meet customer demand. By aligning production schedules with market forecasts and customer orders, organizations can avoid stockouts or excess inventory, resulting in improved customer satisfaction and retention.
- Optimal Resource Utilization: Production planning helps in optimizing the utilization of resources such as labor, machinery, and raw materials. By analyzing production capacity and resource availability, manufacturers can allocate resources efficiently, minimize idle time, and reduce costs.
- Cost Reduction: Efficient production planning enables cost reduction by minimizing inventory carrying costs, avoiding rush orders or expedited shipping, and optimizing production schedules. By streamlining operations, organizations can eliminate waste, reduce lead times, and improve overall cost-effectiveness.
- Improved Efficiency: A well-structured production plan ensures smooth coordination of various manufacturing activities, such as procurement, production, and distribution. This leads to improved operational efficiency, reduced bottlenecks, and increased productivity.
- Effective Decision-Making: Production planning provides valuable insights and data that support informed decision-making. By analyzing production forecasts, capacity constraints, and resource requirements, organizations can make strategic decisions regarding production volumes, resource investments, and process improvements.
Challenges Faced in Production Planning and the Need for Effective Solutions like Material Requirements Planning (MRP)
Production planning is a complex process that involves numerous challenges for manufacturing organizations. These challenges can hinder operational efficiency, increase costs, and impact customer satisfaction. To overcome these obstacles, businesses often turn to solutions like Material Requirements Planning (MRP) to streamline their production planning processes.
Here are some common challenges faced in production planning and the need for effective solutions like MRP:
Demand Forecasting and Variability: Accurately forecasting customer demand is crucial for production planning. However, demand variability, changing market trends, and unforeseen events can make it difficult to predict demand accurately.
MRP addresses this challenge by considering factors such as historical sales data, market trends, and customer demand patterns to generate more accurate forecasts and adapt production plans accordingly.
Inventory Management: Managing inventory levels is a delicate balancing act. Excess inventory ties up working capital and incurs holding costs, while inadequate inventory can lead to stockouts and missed production targets.
MRP helps optimize inventory management by considering demand forecasts, lead times, and production schedules to determine the appropriate inventory levels, reducing excess and shortages.
Resource Allocation: Allocating resources effectively is essential for meeting production targets. Challenges arise when resources such as labor, machinery, and materials are not adequately allocated, leading to inefficient utilization or bottlenecks. MRP considers resource availability, capacity constraints, and production schedules to optimize resource allocation and ensure smooth operations.
Production Scheduling and Sequencing: Determining the optimal sequence and schedule of production activities is a complex task. Factors like setup times, production lead times, and dependencies between different production processes can make scheduling challenging.
MRP helps in sequencing and scheduling production activities based on demand, resource availability, and constraints, minimizing idle time and improving overall efficiency.
Real-time Adaptability: Production planning must be adaptable to changes in demand, supply disruptions, or other unforeseen events. Manual planning processes may struggle to respond quickly to changes. MRP systems provide real-time updates and visibility into production plans, allowing organizations to make timely adjustments, reroute materials, and adapt schedules to meet changing circumstances.
Understanding Material Requirements Planning (MRP)
In the realm of production planning, Material Requirements Planning (MRP) stands as a powerful tool that revolutionizes the way manufacturing organizations manage their materials, inventory, and production schedules.
MRP enables businesses to achieve optimal efficiency, minimize costs, and meet customer demands with precision. By understanding the fundamentals of Material Requirements Planning, manufacturers can harness its potential to transform their production planning processes.
Definition of MRP and Explain its Purpose in Production Planning
Material Requirements Planning (MRP) is a dynamic system that helps manufacturing organizations efficiently manage their production processes by determining the quantity and timing of materials needed for production. It serves as a comprehensive approach to production planning, enabling businesses to synchronize material availability with production schedules, optimize inventory levels, and meet customer demands effectively.
The primary purpose of MRP in production planning is to ensure the availability of required materials at the right time and in the right quantities. By analyzing production schedules, customer orders, and inventory data, MRP generates a detailed plan that outlines the materials needed for each production order.
This includes identifying the raw materials, components, and subassemblies required, along with their quantities and delivery dates.
MRP plays a crucial role in streamlining production processes and achieving operational efficiency.
Its purpose can be summarized as follows:
- Demand-driven Planning: MRP considers customer demand forecasts and actual orders to determine the materials required for production. By aligning production with demand, MRP helps avoid overproduction or underproduction, reducing inventory carrying costs and improving customer satisfaction.
- Inventory Optimization: MRP ensures optimal inventory levels by analyzing inventory data, lead times, and production schedules. It helps organizations avoid excess inventory, minimize stockouts, and reduce holding costs, contributing to cost savings and efficient resource allocation.
- Production Schedule Coordination: MRP synchronizes material availability with production schedules, ensuring that materials are procured and delivered in a timely manner. It helps in minimizing production delays, maximizing utilization of resources, and maintaining smooth production flow.
- Resource Planning: MRP takes into account the availability and capacity of resources such as labor, machinery, and equipment. It helps in allocating resources efficiently, preventing bottlenecks, and ensuring that production operations are adequately supported.
- Visibility and Control: MRP provides real-time visibility into material requirements, inventory levels, and production schedules. This enables organizations to proactively manage potential supply chain disruptions, make informed decisions, and maintain control over their production processes.
In summary, MRP serves as a vital tool in production planning by optimizing material availability, synchronizing production schedules, and enabling efficient resource allocation. By leveraging MRP, manufacturing organizations can enhance their operational efficiency, reduce costs, and improve customer satisfaction.
Key components of MRP (BOM, inventory data, and lead times)
Material Requirements Planning (MRP) relies on several key components to effectively manage production planning. These components provide the necessary information and data to generate accurate material requirements and production schedules.
Here are the essential components of MRP:
- Bill of Materials (BOM): The Bill of Materials is a comprehensive list of all the materials, components, subassemblies, and their quantities required to manufacture a finished product. It serves as a hierarchical structure, breaking down the product into its constituent parts. The BOM specifies the relationships and dependencies between the various components, providing a foundation for MRP calculations.
- Inventory Data: Accurate inventory data is crucial for MRP. It includes information on the current stock levels of raw materials, components, and finished goods. Inventory data encompasses the quantities on hand, quantities on order, and quantities allocated for specific production orders. MRP relies on this data to determine whether additional materials need to be procured or if existing inventory can be utilized for upcoming production orders.
- Lead Times: Lead times refer to the time required for materials to be procured, produced, and delivered. MRP incorporates lead times for each material based on historical data or supplier-provided information. Lead times encompass factors such as processing time, transportation time, and order fulfillment time. By considering lead times, MRP can generate accurate production schedules and ensure that materials are available when needed.
These key components work together to enable MRP to generate precise material requirements and production schedules. The BOM provides the structure and breakdown of the product, inventory data ensures availability of materials, and lead times factor in the time required for procurement and production processes.
By leveraging these components, MRP optimizes production planning, minimizes inventory costs, and enhances operational efficiency in manufacturing organizations.
How MRP helps in managing material availability and production schedules
MRP plays a crucial role in managing material availability and production schedules by providing accurate and timely information for effective decision-making.
Here's how MRP helps in these areas:
Material Availability:
MRP ensures that materials are available when needed for production. By analyzing the BOM, current inventory levels, and production schedules, MRP calculates the precise quantities of materials required. It takes into account factors such as lead times, order quantities, and safety stock levels to determine when and how much of each material should be procured.
This helps prevent stockouts and ensures that materials are on hand at the right time, minimizing production disruptions and delays.
Procurement Planning:
MRP assists in planning and managing the procurement of materials. It generates purchase orders or requisitions based on the material requirements, considering lead times and delivery schedules.
MRP helps optimize procurement by identifying the appropriate quantities to order, taking into account minimum order quantities, supplier constraints, and economic order quantities. This streamlines the procurement process, reduces excess inventory, and ensures a steady flow of materials for production.
Production Schedules:
MRP aids in creating accurate production schedules by aligning material availability with production requirements. It considers the quantities of materials needed, lead times, available resources, and capacity constraints. MRP generates a detailed schedule that outlines when each production order should start and when materials should be available.
This enables organizations to optimize their production processes, avoid bottlenecks, and maintain a smooth flow of operations.
Demand-Driven Planning:
MRP operates on a demand-driven planning approach. It takes into account customer orders, sales forecasts, and market demand to determine the material requirements. By aligning production with actual demand, MRP helps organizations meet customer needs while minimizing excess inventory and reducing the risk of overproduction.
Real-Time Updates and Adjustments:
MRP provides real-time updates and visibility into material availability and production schedules. It takes into account changes in customer demand, production delays, material shortages, or supplier constraints. MRP continuously recalculates and adjusts the material requirements and production schedules accordingly.
This allows organizations to respond quickly to changes, make informed decisions, and adapt their production plans to meet evolving market conditions.
MRP helps manage material availability and production schedules by accurately calculating material requirements, facilitating procurement planning, optimizing production schedules, and incorporating real-time updates. By leveraging MRP, organizations can ensure a steady supply of materials, minimize production disruptions, and achieve efficient production planning in the manufacturing process.
Benefits of Using MRP for Production Planning
The implementation of Material Requirements Planning (MRP) in production planning brings a multitude of benefits for manufacturing organizations. MRP serves as a powerful tool that optimizes efficiency, streamlines operations, and enhances overall productivity.
In this section, we will explore the significant benefits that arise from utilizing MRP in the context of production planning, showcasing its transformative potential for manufacturing enterprises.
Advantages of implementing MRP in production planning
Material Requirements Planning (MRP) offers numerous advantages for manufacturing organizations when implemented in production planning processes. By leveraging MRP, businesses can optimize their operations, enhance productivity, and achieve cost savings. Here are some key advantages of implementing MRP in production planning:
Improved Inventory Management: MRP enables organizations to optimize inventory levels by accurately forecasting material requirements based on production schedules and customer demands. By ensuring that materials are procured and available when needed, MRP helps minimize excess inventory and reduces holding costs. This leads to improved cash flow, reduced risk of obsolescence, and increased working capital efficiency.
Enhanced Production Scheduling: MRP generates detailed production schedules that take into account material availability, resource capacity, and lead times. By synchronizing production activities with material availability, MRP helps organizations optimize their production schedules, minimize idle time, and reduce production bottlenecks. This leads to improved throughput, increased on-time delivery, and enhanced overall operational efficiency.
Accurate Demand Forecasting: MRP utilizes demand forecasting techniques to accurately predict customer demand. By analyzing historical data, market trends, and customer orders, MRP provides insights into future demand patterns. This helps organizations align their production plans with customer needs, reduce stockouts, and improve customer satisfaction.
Effective Resource Planning: MRP considers resource availability, capacity constraints, and production schedules to optimize resource allocation. By ensuring that the right resources are available at the right time, MRP helps organizations minimize downtime, utilize resources efficiently, and achieve optimal production output. This leads to improved resource utilization and cost savings.
Timely Procurement and Supplier Management: MRP generates purchase orders or requisitions based on material requirements, lead times, and supplier information. This enables organizations to procure materials in a timely manner, maintain good relationships with suppliers, and negotiate favorable terms.
MRP helps in supplier management by providing visibility into material demand and delivery schedules, ensuring a smooth supply chain flow.
Data Visibility and Decision-Making: MRP provides real-time visibility into material requirements, inventory levels, and production schedules. This allows organizations to make informed decisions regarding production planning, resource allocation, and material procurement.
MRP's data-driven approach facilitates better decision-making, helps identify bottlenecks or inefficiencies, and supports continuous improvement initiatives.
How MRP improves inventory management by ensuring optimal stock levels and reducing excess or shortages
MRP plays a crucial role in improving inventory management by ensuring optimal stock levels and reducing both excess inventory and shortages. Here's how MRP achieves these improvements:
Accurate Demand Forecasting: MRP utilizes demand forecasting techniques to accurately predict customer demand. By analyzing historical sales data, market trends, and customer orders, MRP generates reliable demand forecasts. This helps organizations estimate the required inventory levels for each material based on expected demand, allowing them to plan and procure materials accordingly.
Material Requirements Calculation: Using the Bill of Materials (BOM) and demand forecasts, MRP calculates the exact quantities of materials needed for production. By considering lead times, production schedules, and safety stock levels, MRP determines the optimal inventory levels for each material. This ensures that sufficient quantities are available to meet production requirements while minimizing the risk of excess or shortage.
Just-in-Time (JIT) Inventory: MRP facilitates the implementation of Just-in-Time inventory practices. Instead of maintaining high levels of inventory, MRP helps organizations procure materials and components just in time for production. This approach minimizes the carrying costs associated with excess inventory, such as storage, depreciation, and obsolescence, while ensuring that materials arrive when needed.
Order Point and Reorder Point Management: MRP establishes order points and reorder points for materials based on lead times and demand patterns. When inventory levels reach the order point, MRP triggers the procurement process to replenish the stock, ensuring that materials are available before shortages occur. This proactive approach prevents stockouts and production disruptions.
Minimization of Excess Inventory: By accurately calculating material requirements and coordinating production schedules, MRP helps organizations avoid overstocking. Excess inventory ties up valuable working capital, increases carrying costs, and reduces profitability. MRP ensures that materials are procured and used as needed, minimizing the risk of excess inventory and associated costs.
Prevention of Shortages: MRP ensures that materials are available in sufficient quantities and at the right time for production. By considering lead times, production schedules, and demand forecasts, MRP helps organizations proactively manage their inventory to prevent shortages. This minimizes production disruptions, avoids delays in order fulfillment, and maintains customer satisfaction.
Overall, MRP improves inventory management by accurately forecasting demand, calculating material requirements, facilitating JIT practices, managing order points, minimizing excess inventory, and preventing shortages. By optimizing inventory levels, manufacturing organizations can reduce costs, improve cash flow, and enhance operational efficiency in their production planning processes.
Discuss how MRP enhances production scheduling by providing accurate timelines and resource allocation
MRP (Material Requirements Planning) enhances production scheduling by providing accurate timelines and facilitating efficient resource allocation. Here's how MRP achieves these improvements:
- Accurate Material Availability: MRP considers the availability of materials required for production. By analyzing the Bill of Materials (BOM), current inventory levels, and lead times, MRP determines the availability of materials at each stage of production. This information enables production schedulers to accurately plan and schedule production activities, ensuring that materials are available when needed.
- Real-Time Production Updates: MRP provides real-time updates on material requirements and inventory levels. As production progresses and materials are consumed, MRP dynamically adjusts the production schedule accordingly. This allows production schedulers to have an accurate view of the current production status and make necessary adjustments to optimize the schedule.
- Optimization of Resource Allocation: MRP takes into account resource availability and capacity constraints. By analyzing production schedules, resource capabilities, and lead times, MRP assists in optimizing the allocation of resources such as labor, machinery, and equipment. It ensures that the right resources are available at the right time for each production order, minimizing idle time and maximizing resource utilization.
- Coordination of Production Activities: MRP synchronizes production activities by aligning material availability with production schedules. It considers the lead times of materials and production processes, allowing production schedulers to plan and sequence activities accordingly. MRP provides a clear roadmap for the timely completion of each production order, ensuring smooth workflow and minimizing bottlenecks.
- Handling of Schedule Changes: MRP is designed to handle changes and disruptions in production schedules. When there are changes in customer demands, material availability, or resource constraints, MRP recalculates the production schedule and adjusts timelines accordingly. This flexibility allows production schedulers to adapt to changes efficiently and maintain optimal production flow.
- Optimization of Lead Times: MRP considers lead times for both materials and production processes. By factoring in the time required for material procurement, production, and assembly, MRP generates accurate timelines for each production order. This helps production schedulers plan and allocate resources effectively, ensuring that production orders are completed on time.
Implementing MRP in Production Planning
Implementing MRP (Material Requirements Planning) in production planning brings about significant advantages for manufacturing organizations. MRP serves as a powerful tool that optimizes material availability, streamlines production processes, and enhances overall efficiency.
In this section, we will explore the key considerations and steps involved in implementing MRP in production planning.
Outline the steps involved in implementing MRP effectively
Implementing MRP (Material Requirements Planning) effectively in production planning involves several key steps. Here is an outline of the process:
- Assess Organizational Readiness: Evaluate the organization's readiness for MRP implementation. This includes assessing the existing production planning processes, understanding the availability and accuracy of data, and identifying any potential barriers or challenges.
- Define Objectives and Goals: Clearly define the objectives and goals of implementing MRP. Determine what specific improvements and outcomes the organization seeks to achieve through MRP, such as reducing lead times, optimizing inventory levels, or improving production scheduling accuracy.
- Gather and Organize Data: Collect relevant data required for MRP implementation, such as Bill of Materials (BOM), inventory levels, lead times, production schedules, and customer demand data. Ensure the accuracy and consistency of data to ensure reliable MRP calculations and planning.
- Select MRP Software or System: Choose an appropriate MRP software or system that aligns with the organization's requirements and capabilities. Consider factors such as functionality, scalability, ease of use, integration with existing systems, and vendor support.
- Set Up MRP Parameters: Configure the MRP software/system by defining parameters such as planning horizon, safety stock levels, order quantities, lead times, and reordering policies. Customize the system to align with the organization's specific production planning needs and preferences.
- Perform Initial Data Input and Validation: Input the gathered data into the MRP system and validate its accuracy and consistency. This includes verifying the correctness of BOMs, updating inventory levels, and ensuring that lead times are accurately reflected. Address any data inconsistencies or errors to ensure reliable MRP calculations.
- Run MRP Calculations: Initiate the MRP calculations based on the input data and configured parameters. The MRP system will generate material requirements, production schedules, and procurement plans based on the defined parameters, demand forecasts, and inventory levels.
- Analyze and Review MRP Results: Analyze the MRP results to understand the material requirements, production schedules, and recommended procurement plans. Review the results for accuracy, feasibility, and alignment with organizational goals. Identify any discrepancies or issues that need to be addressed.
- Implement Action Plans: Develop action plans based on the MRP results. This may include adjusting production schedules, revising procurement plans, addressing capacity constraints, or resolving any material availability issues. Coordinate with relevant departments and stakeholders to implement the necessary actions.
- Monitor and Continuously Improve: Monitor the performance of MRP implementation by tracking key metrics such as inventory turnover, on-time delivery, and production schedule adherence. Continuously review and refine the MRP parameters and processes based on feedback, performance evaluation, and changing business needs.
- Provide Training and Support: Train relevant employees on how to effectively use the MRP system and interpret its outputs. Provide ongoing support and guidance to ensure the smooth implementation and utilization of MRP in production planning processes.
By following these steps, organizations can implement MRP effectively, optimize their production planning, and leverage the benefits of accurate material availability, streamlined production schedules, and efficient resource allocation.
Importance of accurate data input, including BOMs, inventory levels, and lead times
Accurate data input is of paramount importance when implementing MRP (Material Requirements Planning) in production planning. The accuracy of data, including Bill of Materials (BOMs), inventory levels, and lead times, directly impacts the effectiveness and reliability of MRP calculations and planning.
Here are the key reasons why accurate data input is crucial:
Reliable Material Requirements Calculation: Accurate BOMs are essential for determining the precise quantities of materials required for production. Each component listed in the BOM must be correct and up-to-date to ensure that the MRP system generates accurate material requirements. Any errors or omissions in the BOM can lead to incorrect calculations and result in material shortages or overstocking.
Optimal Inventory Management: Accurate inventory levels are crucial for MRP to effectively plan material procurement and production schedules. Inputting correct inventory data allows the MRP system to determine the actual availability of materials. This helps prevent stockouts or excess inventory, optimizing inventory levels and reducing carrying costs.
Timely Procurement and Supplier Management: Accurate lead times for materials play a significant role in MRP calculations. Lead times reflect the time required for procurement, production, and delivery of materials. Inputting precise lead times ensures that the MRP system generates realistic production schedules and procurement plans. It helps organizations avoid delays in material availability, maintain good relationships with suppliers, and optimize the supply chain flow.
Accurate Demand Forecasting: Accurate data input, including historical sales data and customer demand patterns, enables MRP to forecast future demand accurately. Reliable demand forecasting is crucial for aligning production plans with customer needs, optimizing inventory levels, and ensuring on-time delivery. Inaccurate demand data can lead to underestimation or overestimation of material requirements, resulting in either shortages or excess inventory.
Efficient Resource Allocation: Accurate data on lead times, production processes, and resource availability enables MRP to optimize resource allocation. By considering the time required for production and the availability of resources, MRP can generate realistic production schedules and efficiently allocate resources such as labor, machinery, and equipment. This minimizes idle time, maximizes resource utilization, and improves overall operational efficiency.
Reliable Decision-Making: Accurate data input provides a solid foundation for making informed decisions in production planning. Reliable data ensures that the outputs generated by the MRP system are trustworthy and can be used as a basis for decision-making. It enables organizations to effectively plan and allocate resources, set realistic production schedules, and make informed procurement decisions.
Utilizing MRP Outputs for Production Planning
Utilizing the outputs generated by MRP (Material Requirements Planning) is a critical step in effective production planning. MRP provides valuable information and insights that help organizations optimize their production processes, streamline resource allocation, and enhance overall operational efficiency. In this section, we will explore how the outputs of MRP can be effectively utilized in production planning to drive informed decision-making and achieve better outcomes.
Outputs generated by MRP, such as material requirements, purchase orders, and production schedules
MRP (Material Requirements Planning) generates several key outputs that are vital for effective production planning. These outputs provide valuable information and serve as actionable insights for managing material availability, procurement, and production schedules.
Here are the key outputs generated by MRP:
Material Requirements:
One of the primary outputs of MRP is the determination of material requirements. MRP calculates the quantities of materials needed for each production order based on factors such as Bill of Materials (BOM), demand forecasts, and inventory levels. The material requirements output specifies the quantities of each material required and the timing for their availability throughout the production cycle.
Purchase Orders:
MRP generates purchase orders based on the material requirements. Purchase orders are formal requests to suppliers for the procurement of materials. MRP considers lead times, desired delivery dates, and order quantities to create purchase orders that ensure timely availability of materials. These purchase orders facilitate effective supplier management and help maintain a smooth supply chain flow.
Production Schedules:
MRP generates production schedules that outline the timing and sequencing of production activities. The production schedules consider factors such as material availability, resource allocation, lead times, and customer demand. These schedules provide a clear roadmap for the execution of production orders, ensuring that production activities are organized and completed in a timely manner.
Capacity Requirements:
MRP assesses the resource capacity required to fulfill the production schedules. It considers factors such as labor availability, machinery capacity, and production lead times to estimate the capacity requirements. This output helps production planners identify any capacity constraints or bottlenecks and make necessary adjustments to optimize resource allocation and meet production demands.
Exception Reports:
MRP generates exception reports that highlight any deviations or issues in the production planning process. These reports flag situations such as material shortages, excess inventory, production delays, or resource conflicts. Exception reports allow production planners to quickly identify and address any abnormalities, enabling proactive problem-solving and minimizing disruptions in the production process.
Planning Parameters:
MRP provides recommendations for planning parameters such as safety stock levels, reorder points, and order quantities. These parameters help organizations establish guidelines for inventory management, material procurement, and production planning. MRP calculates these parameters based on factors like demand variability, lead times, and desired service levels, assisting in achieving optimal inventory levels and reducing stockouts or excess inventory.
The material requirements output enables accurate procurement planning, ensuring materials are available when needed. Purchase orders facilitate efficient supplier management, ensuring timely material deliveries. Production schedules enable effective resource allocation and sequencing of production activities.
Capacity requirements help optimize resource utilization, and exception reports enable proactive problem-solving. Lastly, planning parameters guide inventory management and improve overall production efficiency.
How to interpret and utilize these outputs effectively for production planning
Interpreting and utilizing the outputs generated by MRP (Material Requirements Planning) effectively for production planning requires careful analysis and informed decision-making.
Here are key steps to interpret and utilize these outputs effectively:
Review Material Requirements:
Carefully analyze the material requirements output provided by MRP. Assess the quantities of materials needed for each production order and the timing of their availability. Compare the material requirements with current inventory levels to identify any potential shortages or excess inventory. This analysis helps in making informed decisions regarding material procurement and inventory management.
Procurement Planning:
Utilize the purchase orders generated by MRP to initiate timely procurement of materials. Review the purchase orders and ensure they align with supplier lead times and delivery schedules. Communicate effectively with suppliers, monitor the progress of procurement, and address any issues or delays promptly. Effective procurement planning ensures that materials are available when required, reducing production disruptions.
Optimizing Production Schedules:
Examine the production schedules generated by MRP. Assess the sequencing and timing of production activities based on material availability and resource constraints. Identify any potential bottlenecks or conflicts in resource allocation. Consider adjusting the production schedules to optimize resource utilization and minimize idle time. Regularly monitor and update the production schedules as per changing demands and resource availability.
Resource Allocation:
Utilize the capacity requirements output to optimize resource allocation. Evaluate the resource capacity needed to meet production demands and identify any capacity constraints or imbalances. Adjust resource allocation to ensure a smooth workflow and avoid overloading or underutilizing resources. Optimize labor, machinery, and equipment allocation to minimize idle time and maximize production efficiency.
Exception Management:
Regularly review the exception reports generated by MRP. Identify any deviations or issues such as material shortages, production delays, or excess inventory. Investigate the root causes of these exceptions and take corrective actions promptly. Addressing exceptions effectively helps in maintaining production schedules, minimizing disruptions, and improving overall efficiency.
Continuously Monitor and Improve:
Continuously monitor the performance of the production planning process using MRP outputs. Track key metrics such as inventory turnover, on-time delivery, and production schedule adherence. Compare actual outcomes with planned outputs to assess the accuracy and effectiveness of MRP calculations. Use this feedback to refine planning parameters, adjust inventory management strategies, and optimize production planning over time.
Collaboration and Communication:
Effective interpretation and utilization of MRP outputs require collaboration and communication among different departments involved in production planning. Foster communication between production planners, procurement teams, and other stakeholders. Share relevant MRP outputs, discuss insights, and collaborate on decision-making to ensure alignment and coordinated efforts in production planning.
Significance of real-time updates and adjustments in response to changes in demand or supply
Real-time updates and adjustments in response to changes in demand or supply play a crucial role in production planning and are of significant importance for organizations. In today's dynamic and volatile business environment, market conditions, customer demands, and supplier capabilities can change rapidly.
Therefore, the ability to adapt and respond quickly to these changes is essential for maintaining operational efficiency and meeting customer expectations. Here's why real-time updates and adjustments are significant:
Firstly, real-time updates enable organizations to stay informed about changes in demand patterns. By continuously monitoring market trends and customer demands, businesses can adjust their production plans accordingly. Real-time updates provide valuable insights into shifts in demand, allowing organizations to proactively allocate resources, adjust production schedules, and optimize inventory levels.
This agility ensures that production remains aligned with customer needs, reducing the risk of overstocking or stockouts.
Secondly, real-time updates facilitate effective supply chain management. By having up-to-date information on supplier capabilities and availability, organizations can adapt their procurement strategies and address any potential supply disruptions. Real-time updates allow for timely communication with suppliers, enabling proactive collaboration and mitigation of potential delays or shortages. This ensures a smooth flow of materials and minimizes the impact on production schedules.
Thirdly, real-time adjustments help organizations optimize resource allocation. By promptly responding to changes in demand or supply, businesses can optimize the allocation of resources such as labor, machinery, and equipment. Real-time adjustments enable production planners to reassign resources, reschedule production activities, and prioritize critical orders. This agility ensures that resources are utilized efficiently, minimizing downtime and maximizing productivity.
Furthermore, real-time updates and adjustments enhance customer satisfaction. By swiftly responding to changes in demand, organizations can meet customer requirements and deliver products on time. Real-time adjustments enable organizations to manage order priorities, expedite production for urgent orders, or adjust delivery schedules based on changing customer needs. This responsiveness strengthens customer relationships, enhances brand reputation, and increases customer loyalty.
Lastly, real-time updates and adjustments enable organizations to optimize operational performance and reduce costs. By closely monitoring and adjusting production plans in response to changes in demand or supply, businesses can minimize waste, reduce inventory holding costs, and avoid production bottlenecks. Real-time adjustments also help in identifying inefficiencies and process improvements, leading to enhanced operational effectiveness and cost savings.
Best Practices for Successful MRP Implementation
Implementing MRP (Material Requirements Planning) successfully requires careful planning, diligent execution, and adherence to best practices. In this section, we will explore the key best practices that organizations should consider to ensure a smooth and effective MRP implementation process.
Importance of cross-functional collaboration and communication within the organization
Cross-functional collaboration and communication within an organization are of utmost importance, especially when implementing MRP (Material Requirements Planning) for production planning. In today's complex business environment, where multiple departments and functions are involved in the production process, effective collaboration and communication are crucial for successful MRP implementation.
Here's why cross-functional collaboration and communication are important:
Shared Understanding and Alignment: MRP implementation requires a shared understanding of goals, processes, and responsibilities across different departments. Collaborative efforts ensure that everyone involved has a clear understanding of how
MRP will impact their roles and how they contribute to the overall success of production planning. It helps align the efforts of various departments towards a common objective, minimizing conflicts and promoting synergy.
Integrated Data and Information Sharing: MRP relies on accurate and up-to-date data from multiple sources, including sales, production, inventory, and procurement. Cross-functional collaboration ensures the integration of data from various departments, enabling a holistic view of the production process.
Effective communication facilitates the sharing of information across departments, ensuring that relevant data is available to support MRP calculations and decision-making.
Timely Response to Changes: Collaborative communication enables prompt identification and response to changes in demand, supply, or production schedules. When different departments are connected and communicate effectively, they can quickly share information about market trends, customer demands, and supplier capabilities.
This enables timely adjustments in production plans, resource allocation, and procurement strategies, minimizing disruptions and maximizing agility.
Efficient Problem-Solving: Collaboration brings together diverse perspectives and expertise from different departments. When issues or challenges arise in MRP implementation, cross-functional collaboration allows for comprehensive problem-solving.
By leveraging the collective knowledge and skills of individuals from different functional areas, organizations can identify root causes, explore alternative solutions, and implement effective measures to overcome obstacles.
Continuous Improvement: Collaboration and communication foster a culture of continuous improvement. By encouraging feedback and open dialogue between departments, organizations can identify areas for optimization and enhancement in the MRP implementation process.
Collaborative efforts enable the sharing of best practices, lessons learned, and success stories, facilitating organizational learning and driving continuous improvement in production planning.
Change Management: MRP implementation often involves significant changes in workflows, processes, and roles within the organization. Effective cross-functional collaboration helps manage this change by involving key stakeholders from different departments in the planning and decision-making process.
It ensures that employees are informed about the purpose, benefits, and impact of MRP, fostering buy-in and support for the implementation.
Need for regular monitoring, evaluation, and continuous improvement of the MRP system
Regular monitoring, evaluation, and continuous improvement of the MRP (Material Requirements Planning) system are essential for ensuring its effectiveness and maximizing its benefits. Implementing MRP is not a one-time task but an ongoing process that requires ongoing attention and refinement.
Here are key reasons highlighting the need for regular monitoring, evaluation, and continuous improvement of the MRP system:
Performance Assessment
Regular monitoring allows organizations to assess the performance of the MRP system against predetermined goals and objectives. By tracking key performance indicators such as on-time delivery, inventory turnover, production schedule adherence, and resource utilization, organizations can evaluate the effectiveness of MRP in meeting production planning requirements. Monitoring provides valuable insights into areas of improvement and identifies any gaps or deficiencies in the system.
Identification of Bottlenecks and Challenges
Continuous monitoring helps in identifying bottlenecks, challenges, and areas of inefficiency within the MRP system. By analyzing data, feedback, and reports, organizations can pinpoint areas where the system may be causing delays, shortages, or excess inventory. Regular evaluation highlights any shortcomings in data accuracy, lead time estimation, or resource allocation. This enables organizations to take corrective actions and optimize the MRP system for better performance.
Adaptation to Changing Business Environment
Business environments are dynamic, and market conditions, customer demands, and supplier capabilities can change rapidly. Regular monitoring and evaluation of the MRP system enable organizations to adapt to these changes effectively. By staying updated on market trends, customer preferences, and supplier performance, organizations can make necessary adjustments to the MRP system. This ensures that production planning remains aligned with the evolving business landscape.
Continuous Process Improvement
Monitoring and evaluation provide opportunities for continuous process improvement. By gathering feedback from stakeholders, analyzing performance data, and benchmarking against industry standards, organizations can identify areas for optimization within the MRP system. Regular evaluation enables organizations to refine planning parameters, streamline workflows, enhance data accuracy, and improve the overall efficiency of production planning processes.
Technology Advancements
Technology is constantly evolving, and new features, functionalities, or upgrades may become available for the MRP system. Regular monitoring and evaluation allow organizations to stay informed about technological advancements in MRP software and assess their relevance to their specific production planning needs. By embracing technological advancements, organizations can enhance the capabilities and performance of the MRP system.
Employee Training and Development
Regular monitoring and evaluation provide insights into employee performance and training needs related to the MRP system. By identifying areas where employees may require additional training or support, organizations can invest in their development. Continuous improvement efforts also create a learning culture where employees can contribute their insights and suggestions for enhancing the MRP system.
Case Studies
The following case studies provide insights into the benefits of implementing MRP for fruitful production planning.
Case Study 1: Toyota Motor Corporation
Toyota Motor Corporation, one of the world's largest automotive manufacturers, successfully implemented MRP (Material Requirements Planning) to enhance their production planning process. With a complex supply chain and multiple production facilities worldwide, Toyota faced challenges in managing material availability and optimizing production schedules.
By implementing MRP, they achieved the following:
- Efficient Material Planning: MRP allowed Toyota to accurately determine material requirements based on production schedules, customer demands, and inventory levels. By analyzing the Bill of Materials (BOM) and considering lead times, MRP enabled Toyota to ensure the availability of materials at each stage of production. This reduced stockouts, improved procurement efficiency, and minimized production disruptions.
- Streamlined Production Schedules: MRP provided Toyota with accurate timelines for each production order, considering material availability and resource constraints. This enabled them to optimize production schedules, minimize idle time, and maximize resource utilization. The real-time updates and adjustments in response to changes in demand or supply allowed Toyota to adapt quickly and maintain smooth production flow.
Case Study 2: General Electric (GE)
General Electric (GE), a multinational conglomerate, implemented MRP to improve their production planning process across various divisions, including aviation, healthcare, and energy.
MRP helped GE achieve the following benefits:
- Improved Material Availability: MRP allowed GE to efficiently manage material availability by analyzing BOMs, inventory data, and lead times. By accurately forecasting material requirements, GE ensured that the right materials were available at the right time for each production order. This reduced material shortages, minimized production delays, and improved overall efficiency.
- Enhanced Resource Allocation: MRP enabled GE to optimize resource allocation by considering resource availability and capacity constraints. By aligning production schedules with resource capabilities, GE maximized the utilization of labor, machinery, and equipment. This led to increased productivity, reduced idle time, and improved operational efficiency.
- Effective Production Planning: MRP provided GE with accurate and reliable production schedules. By synchronizing material availability, production activities, and lead times, GE achieved efficient production planning. This resulted in reduced cycle times, improved on-time delivery, and enhanced customer satisfaction.
These real-life case studies illustrate the successful implementation of MRP in production planning, showcasing its benefits in improving material availability, streamlining production schedules, optimizing resource allocation, and enhancing overall operational efficiency.
Conclusion
In conclusion, Material Requirements Planning (MRP) is a valuable tool for improving production planning in manufacturing organizations. It provides a systematic approach to manage material availability, optimize production schedules, and allocate resources efficiently. By analyzing factors such as the bill of materials, inventory data, and lead times, MRP ensures accurate material availability, real-time production updates, and optimization of resource allocation.
MRP enhances production scheduling by providing accurate timelines and facilitating efficient resource allocation. It synchronizes production activities, handles schedule changes, and optimizes lead times, resulting in improved productivity and reduced production delays. Moreover, MRP contributes to effective inventory management by ensuring optimal stock levels and reducing excess or shortages.
Implementing MRP requires careful consideration of factors such as accurate data input, cross-functional collaboration, and regular monitoring and evaluation. By following best practices and utilizing the outputs generated by MRP, organizations can enhance their production planning processes, achieve better operational efficiency, and meet customer demands more effectively.
How can Deskera Help You?
Deskera ERP and MRP systems help you to keep your business units organized. The system's primary functions are as follows:
- Keep track of your raw materials and final items inventories
- Control production schedules and routings
- Keep a bill of materials
- Produce thorough reports
- Make your own dashboards
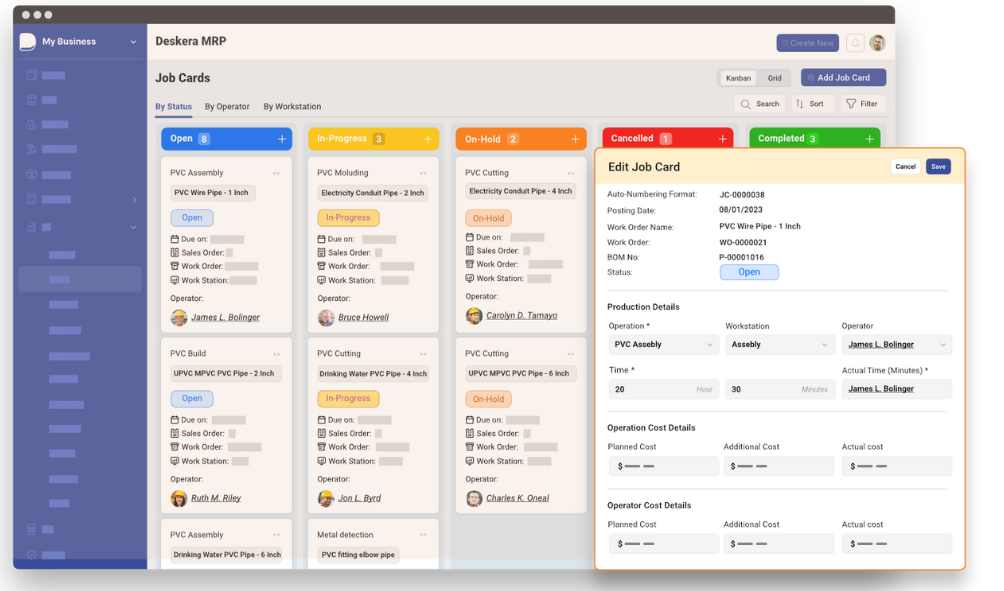
Deskera's integrated financial planning tools enable investors to better plan and track their investments. It can assist investors in making faster and more accurate decisions.
Deskera Books allows you to better manage your accounts and finances. Maintain good accounting practices by automating tasks like billing, invoicing, and payment processing.
Deskera CRM is a powerful solution that manages your sales and helps you close deals quickly. It not only enables you to perform critical tasks like lead generation via email, but it also gives you a comprehensive view of your sales funnel.
Deskera People is a straightforward tool for centralizing your human resource management functions.
Key Takeaways
- Material Requirements Planning (MRP) is a valuable tool for improving production planning in manufacturing organizations.
- MRP considers factors such as the bill of materials, inventory data, and lead times to ensure accurate material availability.
- Real-time production updates provided by MRP enable production schedulers to have an accurate view of the current production status and make necessary adjustments.
- MRP optimizes resource allocation by considering resource availability and capacity constraints, maximizing productivity, and minimizing idle time.
- MRP synchronizes production activities by aligning material availability with production schedules, ensuring smooth workflow, and minimizing bottlenecks.
- MRP handles schedule changes efficiently by recalculating the production schedule and adjusting timelines accordingly.
- Effective implementation of MRP requires accurate data input, including bill of materials, inventory levels, and lead times.
- Cross-functional collaboration and communication within the organization are crucial for successful MRP implementation.
- Regular monitoring, evaluation, and continuous improvement of the MRP system are essential to ensure its effectiveness and adaptability.
- Successful implementation of MRP has been observed in real-life case studies, such as Toyota Motor Corporation and General Electric, showcasing the benefits of improved material availability, streamlined production schedules, and optimized resource allocation.
Related Articles
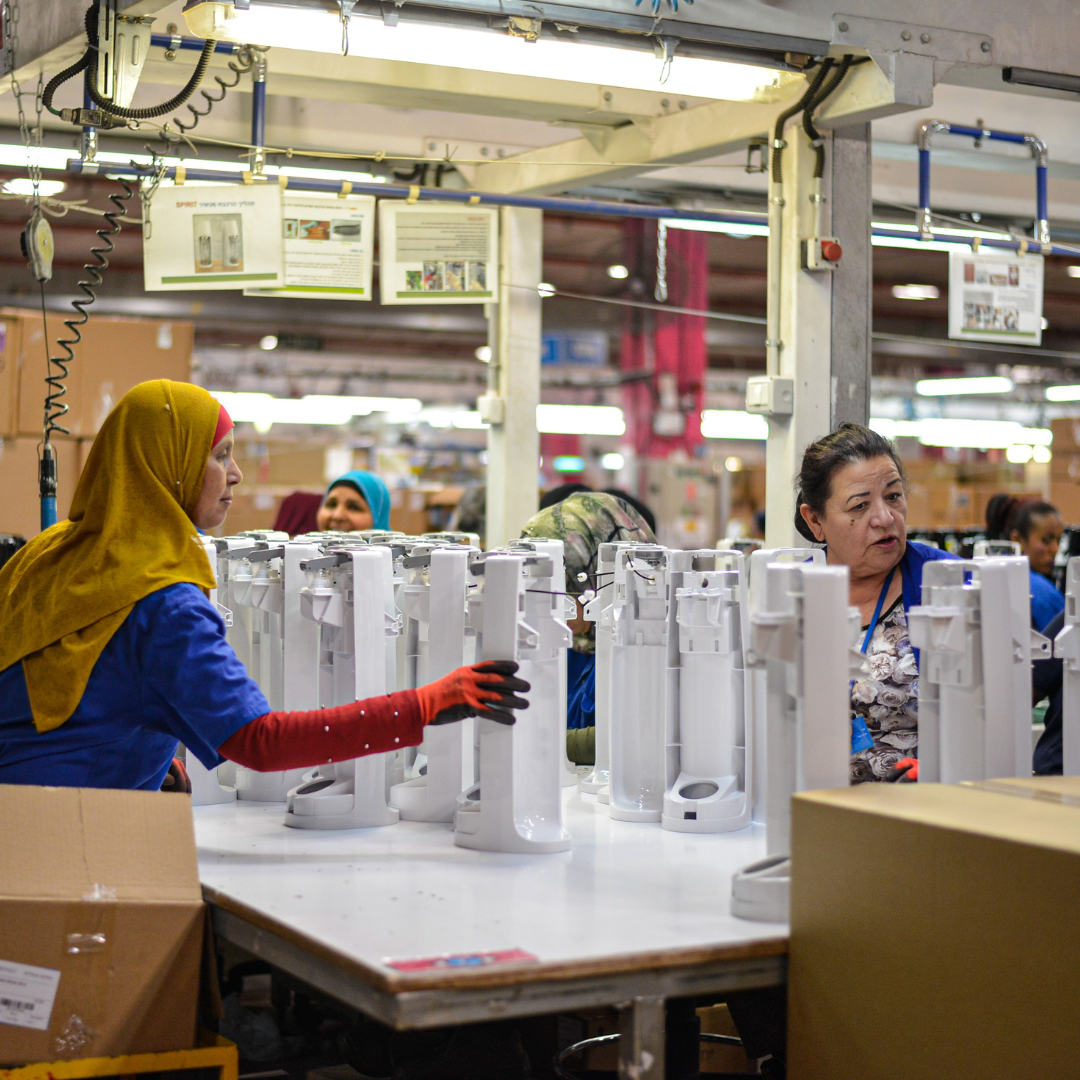
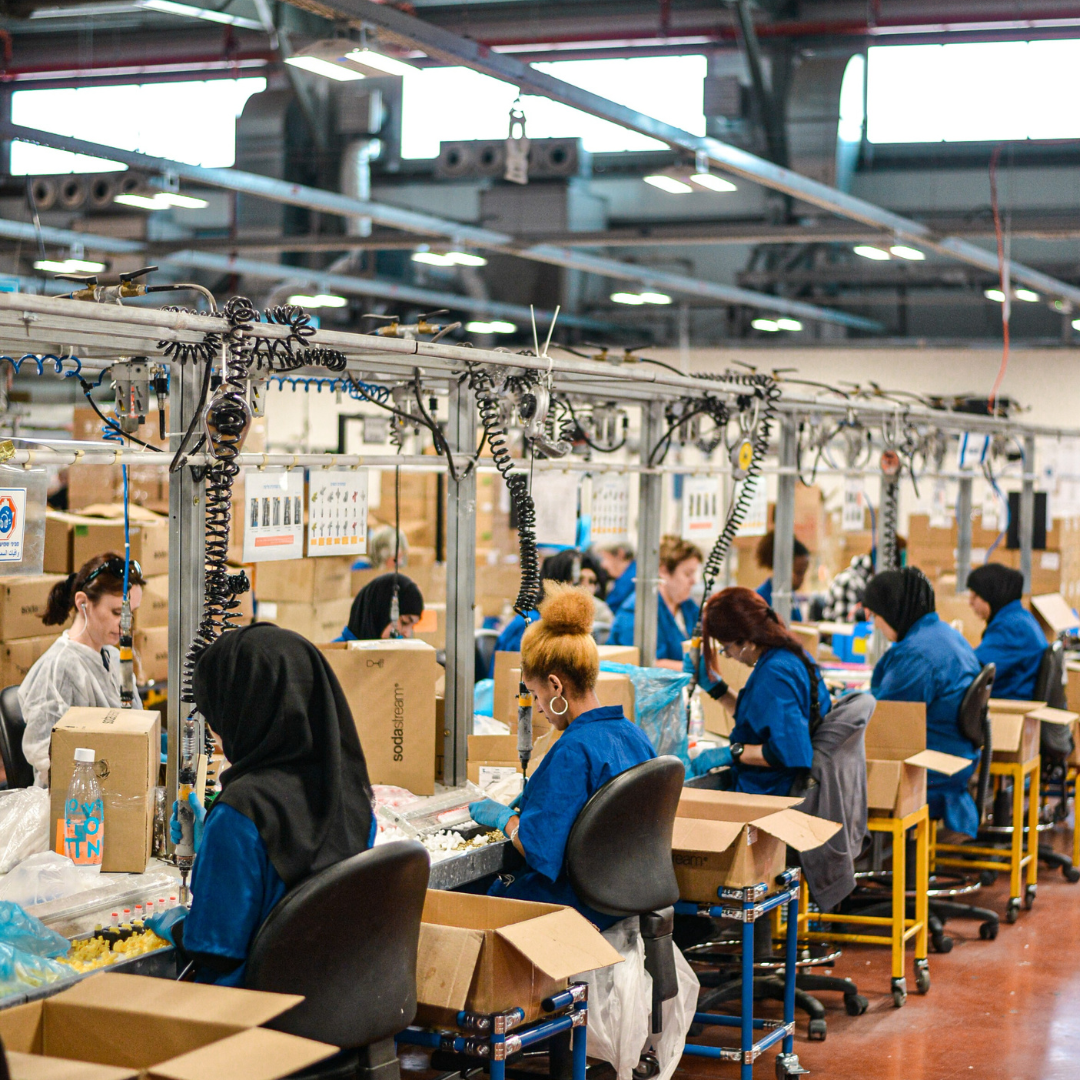
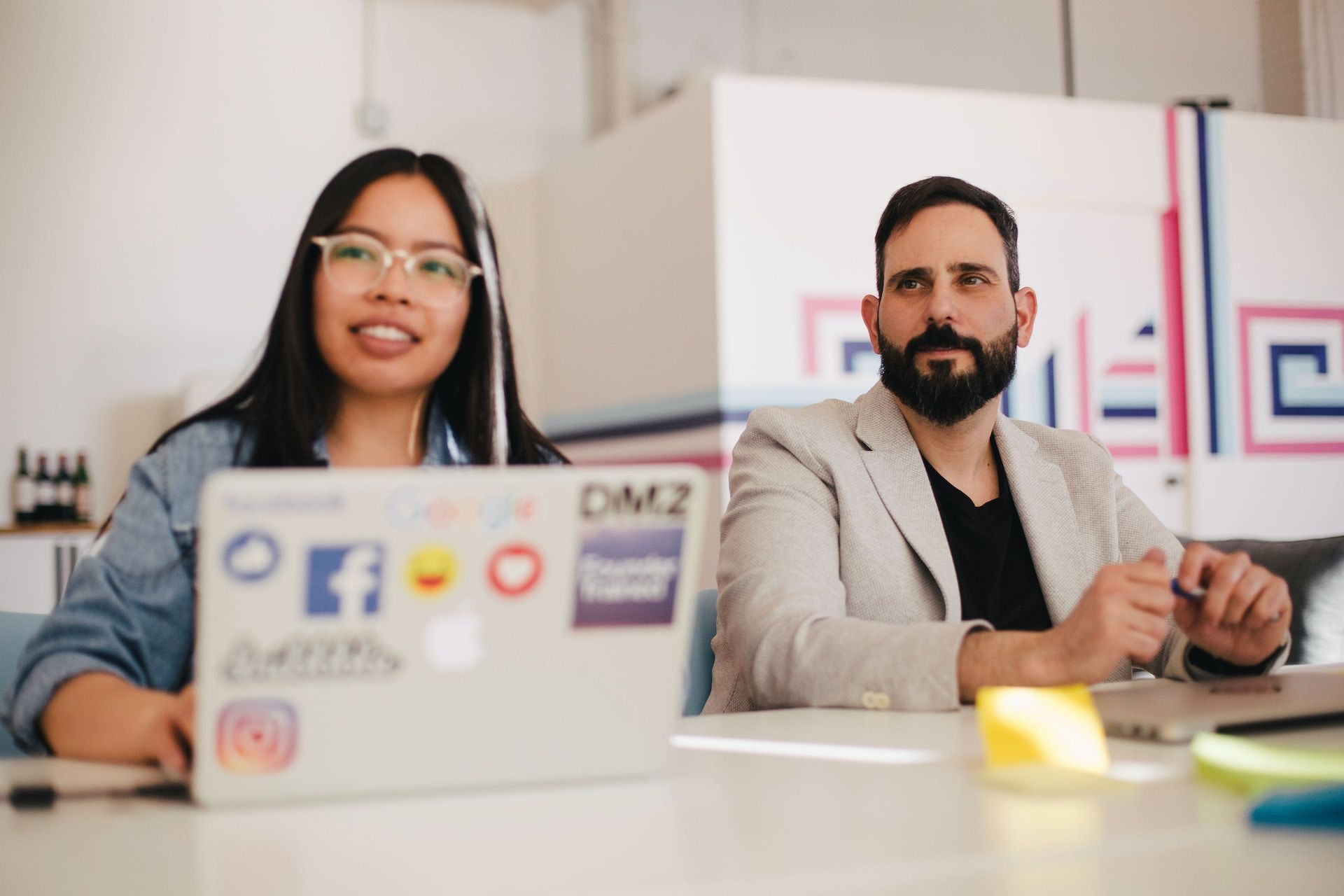
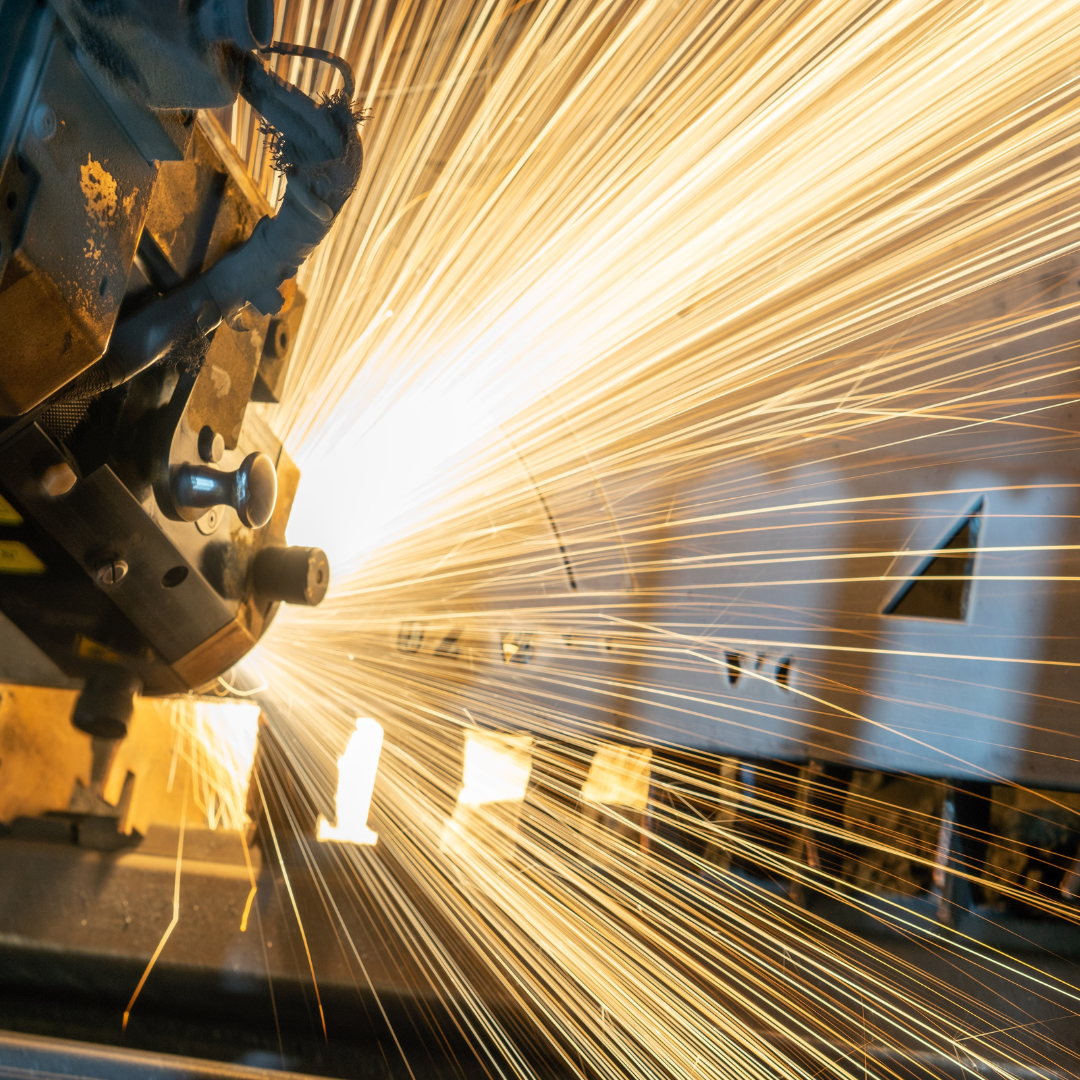