Plastic manufacturing is a complex process and selecting the right ingredients is essential for the production of quality plastic products. The quality of a plastic product can be determined by the selection of the right ingredients and their proper combination. The selection of the right ingredients is of utmost importance in order to produce quality plastic products.
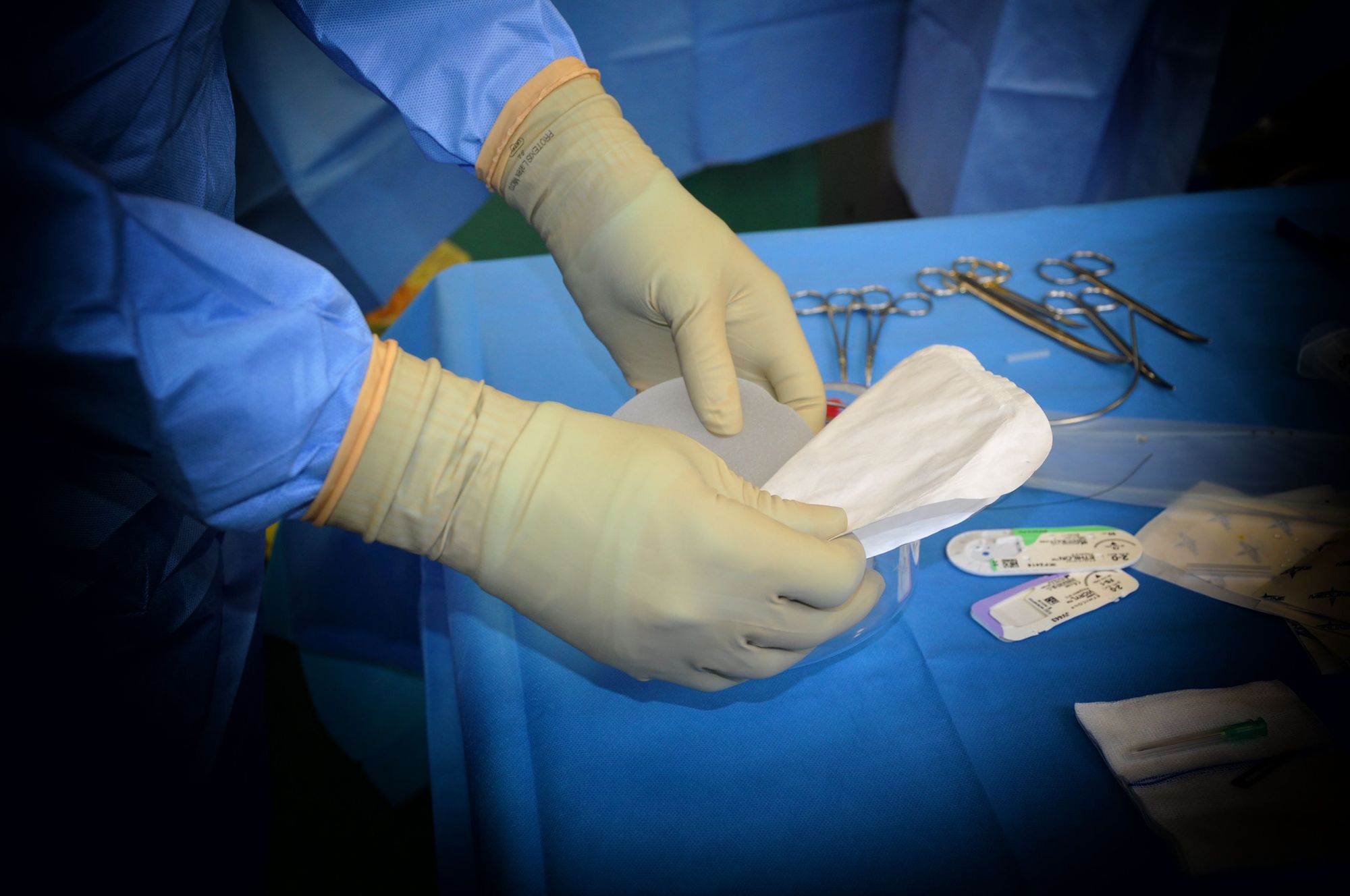
This article covers the following:
- Overview of plastic manufacturing.
- Understanding the plastic production process.
- What are the different types of plastic production?
- Cost-effective ingredients for plastic production
- What are the common chemicals used in plastic production?
- How to select the best ingredients for plastic production?
- What are some of the benefits of selecting the right ingredients?
Overview of Plastic Manufacturing
Plastic manufacturing is the process of producing plastic products from raw materials such as polymers and resins. Plastic products are widely used in many industries, from consumer goods to medical equipment and automotive parts.
The process of plastic manufacturing involves several steps, including the selection of raw materials, the design of the product, the molding process, and the finishing and packaging of the product.
The first step in plastic manufacturing is the selection of raw materials. Polymers and resins are the most commonly used materials in plastic manufacturing. Polymers are large molecules composed of repeating structural units held together by chemical bonds.
Examples of polymers used in plastic manufacturing include polyethylene, polypropylene, polystyrene, polyvinyl chloride, polycarbonate, and polyurethane. Resins are natural or synthetic substances that are solid at room temperature and can be melted and molded.
Examples of resins used in plastic manufacturing include polyester, polyacrylate, polyamide, polylactic acid, polyvinyl acetate, and polyethylene terephthalate. The next step in plastic manufacturing is the design of the product. This step involves the creation of a prototype, which is used to test the product for strength, flexibility, and other properties.
The prototype will determine the size, shape, and other characteristics of the final product. The molding process is the third step in plastic manufacturing. This step involves injecting molten plastic into a die or mold to create a three-dimensional product.
Common molding processes include injection molding, blow molding, and rotational molding. The fourth step in plastic manufacturing is the finishing and packaging of the product.
This step involves cleaning, inspecting, and packaging the product for shipment to the customer. The product may also be painted or have other finishes applied. Plastic manufacturing is a complex process that requires a great deal of expertise and specialized equipment. It is important to ensure that the process is performed correctly to ensure the quality of the finished product.
Understanding the Plastic Production Process
Plastic production has become a cornerstone of modern manufacturing, with plastic products finding their way into homes, businesses, and virtually every other aspect of everyday life.
As with any type of manufacturing process, understanding the plastic production process is key to producing high-quality, reliable products. Here, we’ll take a look at the steps involved in plastic production, from raw materials to finished products.
Raw Materials Like any other type of manufacturing, plastic production starts with raw materials. These materials can vary based on the type of plastic product being made but typically include a type of plastic resin, a colorant, and various additives.
Depending on the application, these materials may also include fillers, lubricants, and UV stabilizers. Molding Once the materials are prepared, the next step in the plastic production process is molding.
This involves melting the raw material and then injecting it into a mold, where it takes the shape of the product. The mold can be made of metal or plastic, depending on the type of product being made.
Finishing Next is the finishing and post-molding steps. This can include trimming, drilling, buffing, and other secondary processes to give the product its final shape and features.
The finished product is then ready for inspection, packaging, and shipping. Inspection is an important part of the plastic production process, as it ensures that the finished product meets quality standards.
Quality assurance teams typically inspect the product for defects, ensuring that the product meets the customer’s specifications. If any defects are found, corrective action is taken to ensure that the product meets the customer’s requirements.
Packaging Once the product passes inspection, it is ready to be packaged. This is typically done using plastic bags or clamshells but can also include boxes and other packaging materials.
The packaging is designed to protect the product and make it easier to transport. Shipping The final step in the plastic production process is shipping. The product is carefully packed and shipped to the customer or distributor, ensuring that it arrives safely and on time.
Understanding the plastic production process is essential for any manufacturer looking to produce high-quality, reliable products. By following these steps, manufacturers can ensure that their products are safe, reliable, and of the highest quality.
What are the Different Types of Plastic Production?
Plastic is one of the most versatile materials used in the manufacturing world. It is used in a wide variety of industries and applications, including construction, medical, and industrial.
With its versatile properties, plastic can be formed into many different shapes and sizes and used in a range of ways. Plastic production is the process of creating plastic goods from raw materials such as plastic pellets, powders, and granules. These materials are then heated, cooled, and formed into a desired shape.
Depending on the application, plastic goods can be produced through a variety of processes, such as injection molding, extrusion, thermoforming, and blow molding. Injection Molding Injection molding is one of the most popular methods of plastic production.
In this process, melted plastic is injected into a mold cavity where it cools and hardens into the desired shape. Injection molding is used to create a variety of products, including automotive parts, electronics, and medical devices.
Extrusion
Extrusion is another type of plastic production process. In this method, plastic pellets are melted and forced through a die, which forms the plastic into a desired shape. Extrusion is used to create a wide range of products, including pipes, rods, and extruded sheets.
Thermoforming
Thermoforming is a plastic production process that involves heating a plastic material and then forming it into a desired shape. This process is often used to create packaging and other products that require a precise shape.
Blow Molding
Blow molding is a plastic production process that involves heating a plastic material and then inflating it to form it into a desired shape. This process is frequently used to create hollow objects such as plastic bottles and copper bottles.
Rotational Molding
Rotational molding is a type of plastic production process that involves heating a plastic material and then rotating it in a mold to form the desired shape. This process is used to create a variety of products, including toys, fuel tanks, and plastic containers.
These are just some of the different types of plastic production processes used to create a wide range of products. Each process has its own advantages and disadvantages, so it’s important to consider the application and desired product when deciding which process to use.
Cost-Effective Ingredients for Plastic Production
Plastic production is a major component of the manufacturing industry and one that requires the use of cost-effective ingredients. With the cost of plastic production rising and the demand for reduced production costs, manufacturers must find innovative ways to reduce their costs while ensuring the quality of their products.
One of the most common ingredients used in plastic production is polyethylene. This is a petroleum-derived product that is highly versatile and serves as a base for many different types of plastic products.
Polyethylene is an affordable option for many plastic manufacturers, but it does have some drawbacks. For instance, the environmental impact of using this type of plastic is often an issue. Another cost-effective ingredient used in plastic production is PVC.
This is a type of plastic that is often used in construction and other industrial applications. PVC is a durable and long-lasting plastic, making it a great option for cost-effective plastic production.
It also has a relatively low environmental impact and is recyclable. Another cost-effective option for plastic production is PET. This is a type of plastic that is derived from recycled materials, such as water bottles and plastic bags.
PET is a versatile plastic that is used in a variety of applications, including food packaging and medical products. It is also a cost-effective option due to its recyclable nature.
The last cost-effective ingredient used in plastic production is polypropylene. This is a plastic that is derived from petroleum products, but it is more eco-friendly than polyethylene.
It is also more cost-effective than other types of plastic, as it is recyclable and can be used in a variety of applications. When it comes to plastic production, cost-effective ingredients are an important factor in reducing costs.
Using the right ingredients can save money and help to reduce the environmental impact of plastic production. By researching the different types of plastic available, manufacturers can find the right ingredients that are cost-effective and have a low environmental impact.
What are the Common Chemicals Used in Plastic Production?
When it comes to manufacturing plastic, the use of chemicals is essential. Chemicals are used to give plastic its desired properties, such as flexibility, strength, and durability. Different types of plastic require different combinations of chemicals, but there are some that are commonly used in plastic production.
The most common chemical used in plastic production is polyethylene (PE). PE is a type of thermoplastic that is derived from petroleum. It is one of the most versatile plastics and is used for a wide range of products, from supermarket bags to medical tubing.
This type of plastic is relatively cheap, strong, and has a low melting point. Polyvinyl chloride (PVC) is another common plastic that is made from chlorine and ethylene. It is commonly used to produce pipes, window frames, and cable insulation.
PVC is durable and resistant to fire and water but can release toxic chemicals when heated. Acrylonitrile butadiene styrene (ABS) is a type of plastic made from acrylonitrile, butadiene, and styrene.
It is typically used to produce a wide range of products, including computer keyboards and LEGO bricks. ABS is strong and heat-resistant, but it can be difficult to weld. Polypropylene (PP) is another type of thermoplastic that is made from propylene.
This plastic is rigid and resistant to many chemicals, which makes it ideal for food packaging and medical equipment. PP is also relatively inexpensive and easy to mold. Polystyrene (PS) is a type of plastic that is commonly used to produce disposable items, such as plates, cups, and cutlery.
It is lightweight and can be molded into various shapes. However, it is not very strong and can easily be damaged. Finally, polycarbonate (PC) is a type of plastic that is widely used in the automotive industry.
It is strong and shatter-resistant, making it ideal for car windows. PC is also used to manufacture eyeglass lenses and medical equipment. These are some of the most common chemicals used in plastic production. Each type of plastic has its own unique properties and applications, so it is important to choose the right chemical for the desired product.
How to Select the Best Ingredients for Plastic Production?
When it comes to producing plastic, selecting the right ingredients is essential to ensure that the end product is of high quality and meets safety standards. The wrong ingredients can lead to weak or brittle plastic, or worse can cause health risks to those who handle it.
To ensure that you select the best ingredients for plastic production, here are some tips to consider:
Start by understanding your plastic production process. Knowing what type of plastic you’ll be producing and the type of equipment you’ll be using will help you determine the best ingredients for the job.
Consider the various types of plastics and their properties. Different types of plastic will require different ingredients, so it’s important to research the properties of the plastic you’ll be using.
Look into the additives that can be used to improve the plastic’s performance. Additives such as flame retardants, UV stabilizers, and colorants can all have an effect on the plastic’s final performance.
Research the suppliers of the ingredients you’ll be using. Make sure that the suppliers are reputable and that the ingredients they provide are of high quality.
Test the ingredients before using them. Testing the ingredients before adding them to your plastic production process will help to ensure that the final product is of the highest quality.
By considering these tips, you’ll be able to select the best ingredients for plastic production and create a high-quality product. It’s important to remember that plastic production is a complex process and requires careful consideration of the ingredients used to ensure that the end product meets safety and performance standards.
What are Some of the Benefits of Selecting the Right Ingredients for Plastic Production?
When it comes to plastic production, selecting the proper ingredients is extremely important. Not only can the wrong ingredients lead to a substandard product, but they can also be hazardous to the environment and human health.
First, the right ingredients can lead to a high-quality product. The right ingredients can ensure that the plastic will be durable and have the desired characteristics such as strength, flexibility, and resistance to heat, chemicals, and UV radiation.
This will allow the plastic to be used in a variety of applications. Second, the right ingredients can help to make the plastic production process more efficient. For example, the right ingredients can be used to create specific shapes and colors, which can reduce the amount of time and energy required to manufacture the product.
Furthermore, the right ingredients can help to speed up plastic production and reduce costs. Third, the right ingredients can help to make plastic more environmentally friendly. By using renewable, organic, or biodegradable raw materials, manufacturers can create plastics that are more sustainable and less likely to harm the environment.
Finally, the right ingredients can help to make plastic safer for human health. Certain ingredients can be used to make the plastic non-toxic or resistant to bacteria or fungi.
This can be especially important for products that will come into contact with food or other substances that are consumed by humans. In conclusion, selecting the right ingredients for plastic production is extremely important.
Not only can the wrong ingredients lead to a substandard product, but they can also be hazardous to the environment and human health. By using the right ingredients, manufacturers can create high-quality, efficient, and environmentally friendly plastics that are safe for human use.
How Can Deskera Assist You?
As a manufacturer, you must keep track of your inventory stock. The condition of your inventory has a direct impact on production planning. It also has a direct impact on people and machinery use and capacity utilization.
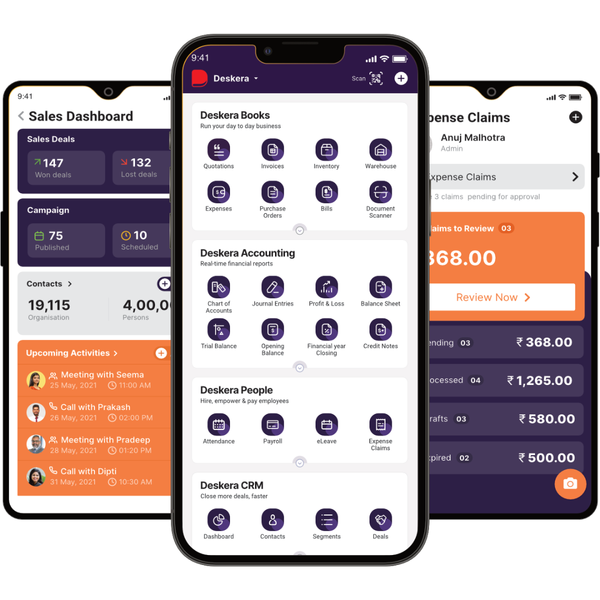
Deskera MRP is the one tool that lets you do all of the above. With Deskera, you can:
- Control production schedules
- Compile a Bill of Materials
- Produce thorough reports
- Make your dashboard
Deskera ERP is a complete solution that allows you to manage suppliers and track supply chain activity in real-time. It also allows you to streamline a range of other company functions.
Deskera Books allows you to manage your accounts and finances better. It helps maintain good accounting standards by automating billing, invoicing, and payment processing tasks.
Deskera CRM is a powerful tool that organizes your sales and helps you close deals rapidly. It enables you to perform crucial tasks like lead generation via email and gives you a comprehensive view of your sales funnel.
Deskera People is a straightforward application for centralizing your human resource management activities. Not only does the technology expedite payroll processing, but it also helps you to handle all other operations such as overtime, benefits, bonuses, training programs, and much more.
Key Takeaways
- Plastic manufacturing is the process of producing plastic products from raw materials such as polymers and resins.
- Quality assurance teams typically inspect the product for defects, ensuring that the product meets the customer’s specifications.
- Acrylonitrile butadiene styrene (ABS) is a type of plastic made from acrylonitrile, butadiene, and styrene.
- One of the most common ingredients used in plastic production is polyethylene.
- When it comes to producing plastic, selecting the right ingredients is essential to ensure that the end product is of high quality and meets safety standards.
Related Articles:
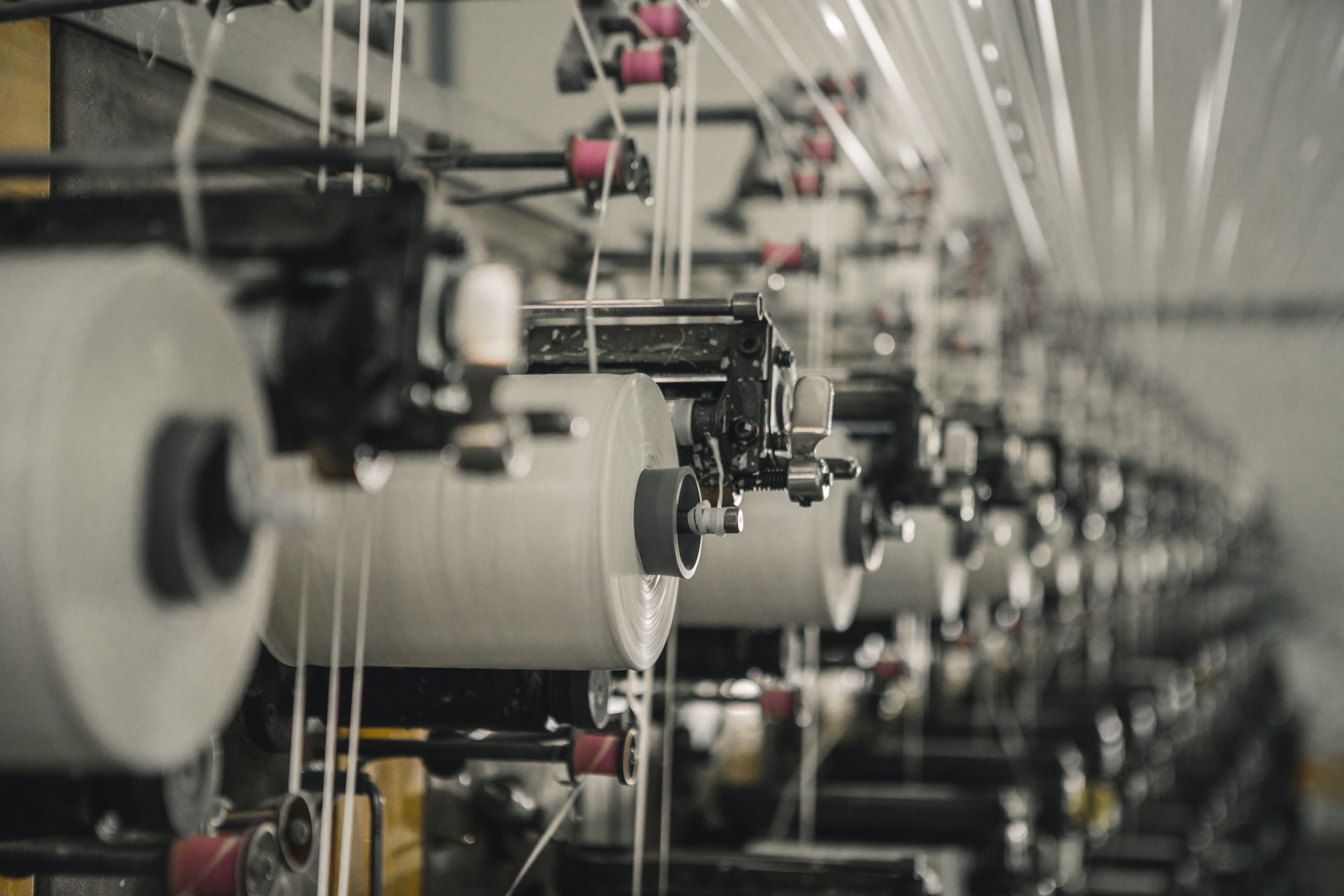
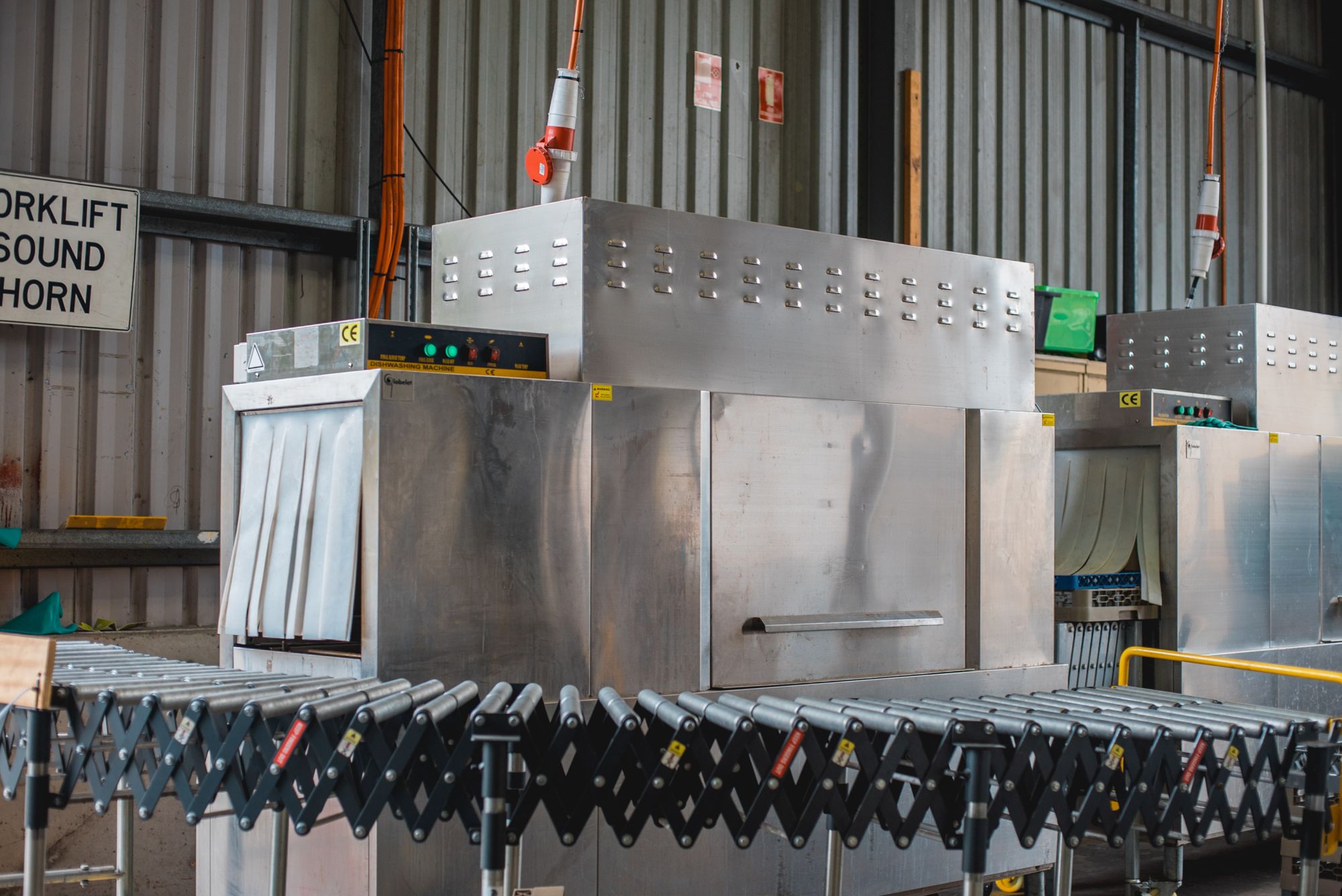
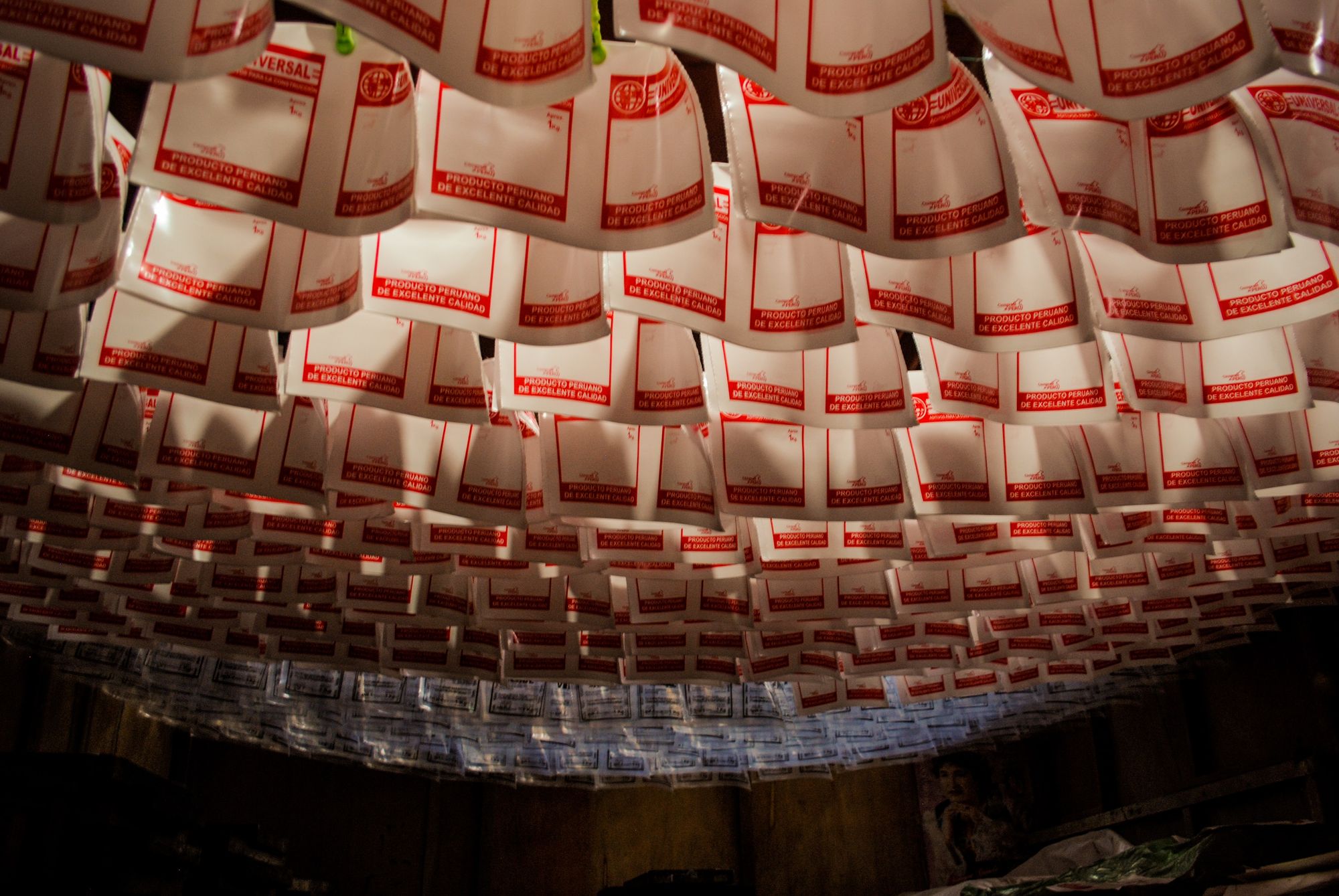
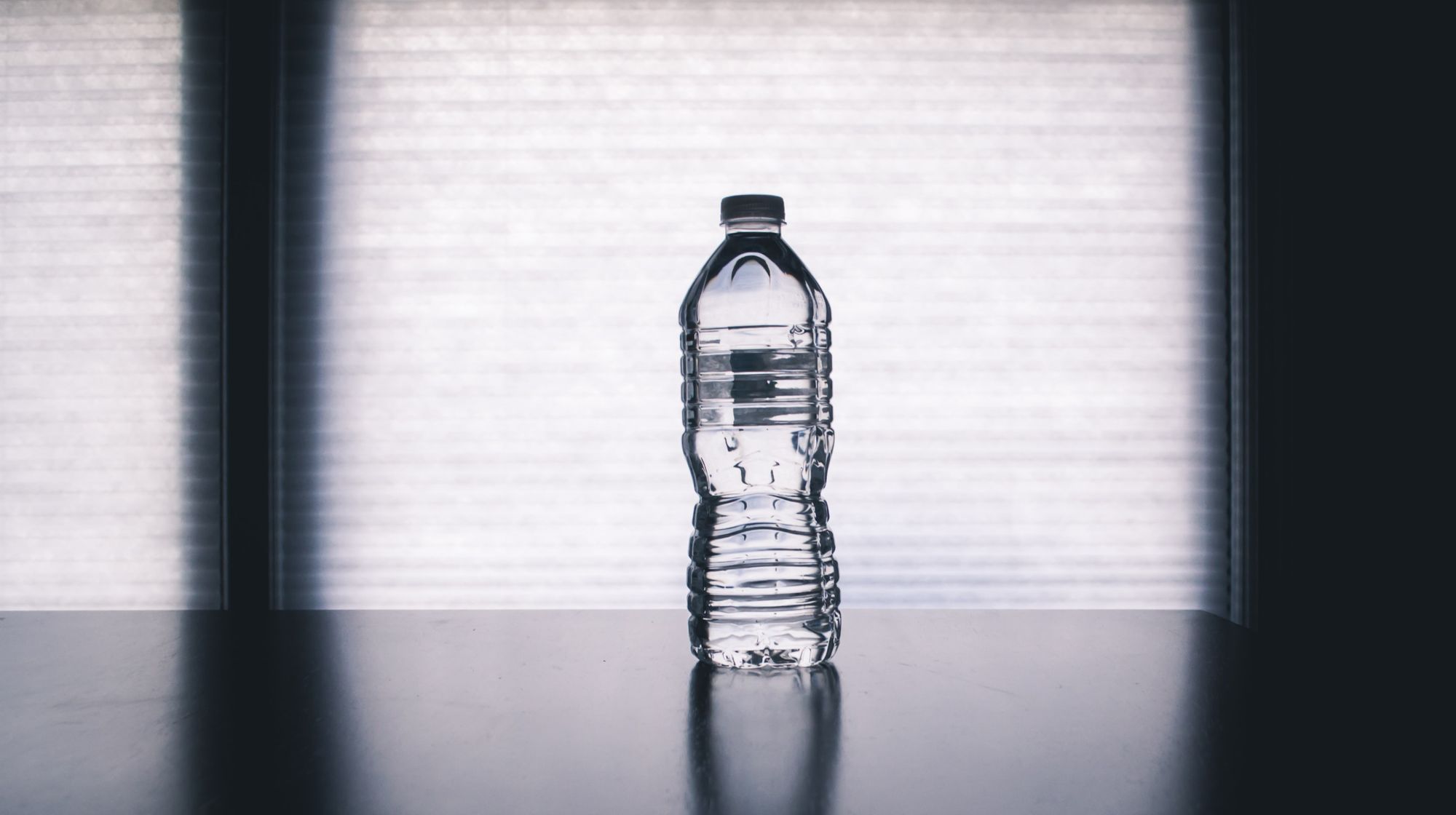