According to recent statistics, the plastics industry in the United States generated an estimated $432.3 billion in shipments and employed approximately 982,000 workers in 2020.
While the industry has undoubtedly brought about many benefits, it also poses various safety hazards to workers, including exposure to harmful chemicals, fire, and physical injuries.
The risks faced by workers in the plastic manufacturing industry include exposure to hazardous chemicals and materials, as well as physical hazards such as moving machinery and ergonomic stressors. These hazards can cause serious injuries, such as burns, cuts, and respiratory problems.
In addition to the human cost, these injuries can also significantly impact the financial health of businesses through lost productivity and increased healthcare costs.
Plastic manufacturing companies must take proactive steps to protect workers from these potential hazards to ensure a safe working environment. This includes implementing safety protocols and training programs and investing in equipment and technology designed to reduce the risk of accidents and injuries.
By doing so, companies can protect their workers and improve their bottom line by reducing costs associated with workplace accidents and injuries.
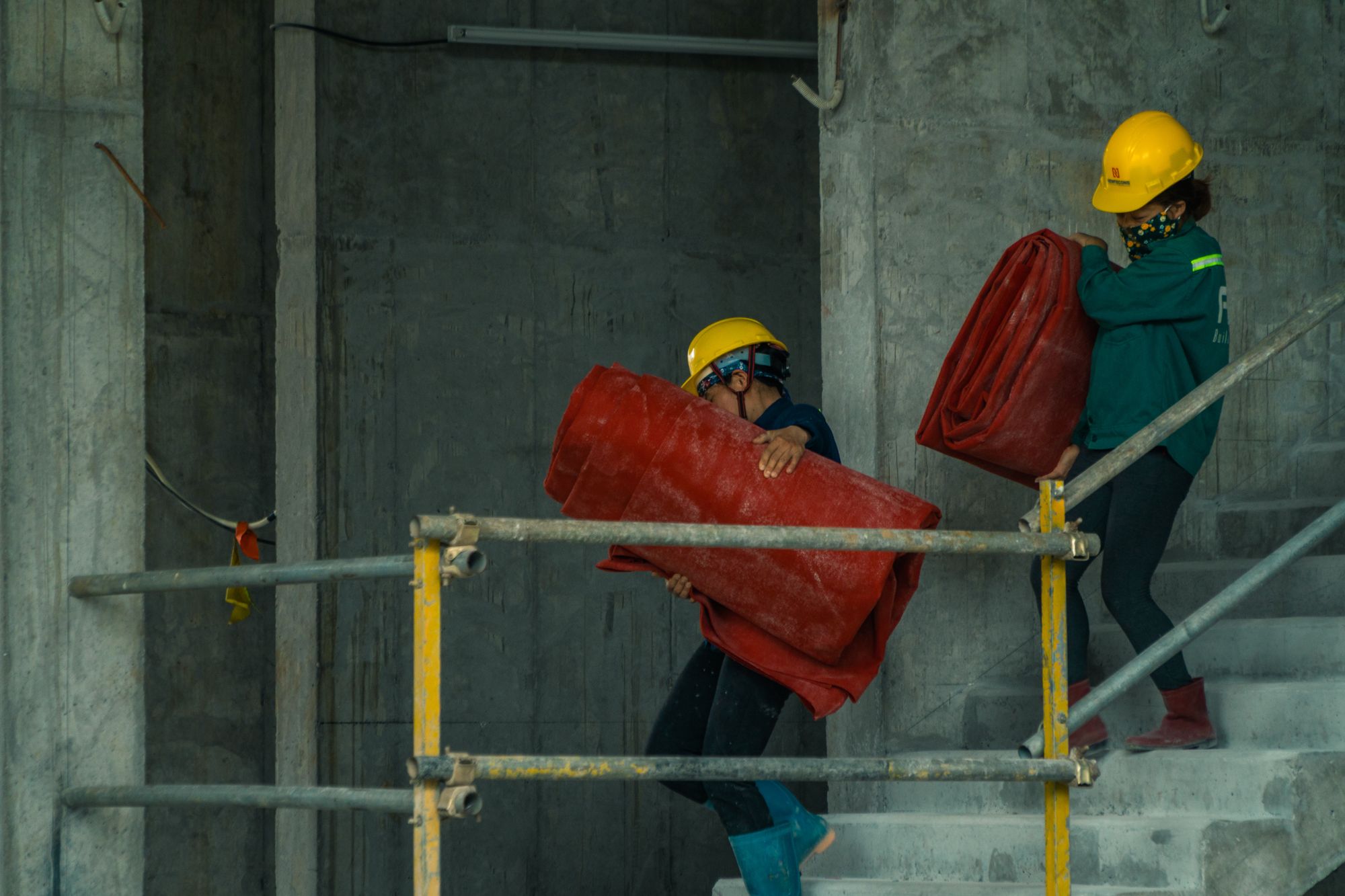
This article will explore the various ways to protect plastic manufacturing workers from potential hazards. We will examine the key safety risks associated with plastic manufacturing and provide practical solutions for mitigating these risks.
By following the guidelines presented in this article, plastic manufacturers can create a safer working environment for their employees, reduce the risk of accidents, and improve the overall efficiency of their operations.
Here's what we shall cover in this post:
- Common Hazards in Plastic Manufacturing
- Hazard Communication in Plastic Manufacturing
- Fire Safety in Plastic Manufacturing
- Machine Guarding in Plastic Manufacturing
- Lockout/Tagout Procedures in Plastic Manufacturing
- Emergency Response in Plastic Manufacturing
- Health and Wellness Programs for Plastic Manufacturing Workers
- Conclusion
- Key Takeaways
Common Hazards in Plastic Manufacturing
Plastic manufacturing is a complex process that involves various steps, machinery, and chemicals. While plastic products have become essential to our daily lives, plastic manufacturing facilities can also pose certain hazards.
Identifying and taking appropriate measures to prevent these hazards is crucial to ensure a safe working environment.
Chemical Hazards: One of the most significant hazards in plastic manufacturing is exposure to chemicals. The chemicals used in plastic manufacturing, such as polyvinyl chloride (PVC) and styrene, can be toxic and pose health risks to workers.
Exposure to these chemicals can lead to respiratory problems, skin irritation, and other health problems. Workers must take appropriate precautions, such as wearing protective clothing and masks, and employers must ensure that workers are trained on how to handle these chemicals safely.
Fire and Explosion Hazards: Plastic manufacturing facilities often use large machinery, which can generate heat and create a risk of fire and explosion. Flammable materials, such as solvents and chemicals, can also increase the risk of fire and explosion.
Employers must ensure that machinery is maintained regularly, and workers must be trained on how to operate the machinery safely. Additionally, fire suppression systems should be in place and tested regularly.
Electrical Hazards: Electrical hazards are another common hazard in plastic manufacturing facilities. Faulty wiring, improperly grounded equipment, and overloaded circuits can create a risk of electrocution.
Workers must be trained in electrical safety and understand the risks associated with working with electrical equipment. Electrical equipment should also be maintained regularly and inspected to ensure it is safe to use.
Mechanical Hazards: Machinery used in plastic manufacturing can also pose a risk of injury. Workers can get caught in machinery or be struck by moving parts, leading to serious injuries or even death.
Employers must ensure that machinery is equipped with appropriate guards and safety features to prevent accidents. Workers must also receive adequate training on how to operate the machinery safely.
Noise Hazards: Plastic manufacturing facilities can generate a lot of noise, which can lead to hearing loss over time. Employers must provide hearing protection to workers and take steps to reduce noise levels where possible.
Regular monitoring of noise levels can help employers identify areas where noise levels are excessive and take appropriate action.
Personal Protective Equipment (PPE) For Plastic Manufacturing Workers
Personal Protective Equipment (PPE) is critical in any manufacturing industry, and the plastic manufacturing industry is no exception. Plastic manufacturing involves various hazards that can pose risks to workers' health and safety.
PPE is essential to protect workers from these hazards and prevent workplace accidents. Here are some essential PPE for plastic manufacturing workers:
- Eye and Face Protection: Plastic manufacturing involves the use of machines and tools that can produce small particles or debris that can fly into workers' eyes. Workers should wear safety goggles or face shields to protect their eyes and face from chemical splashes, dust, and debris.
- Respiratory Protection: During the plastic manufacturing process, fumes, vapors, and dust can be released into the air, posing significant risks to workers' respiratory health. Respirators such as masks or respirators are necessary to protect workers from inhaling harmful substances that can cause lung damage or other respiratory diseases.
- Hand Protection: Workers in plastic manufacturing are exposed to hot and sharp objects, chemicals, and moving machine parts, which can cause hand injuries. Gloves made from materials such as nitrile, neoprene, or butyl rubber can protect workers' hands from burns, cuts, and chemical exposure.
- Foot Protection: The plastic manufacturing process involves the use of heavy equipment, which can pose a risk of foot injuries. Workers should wear safety shoes or boots with protective toecaps and slip-resistant soles to prevent slips, trips, and falls.
- Body Protection: Workers should wear protective clothing such as coveralls or lab coats to protect their skin from chemical splashes, burns, or cuts. They should also wear safety harnesses when working at heights or on elevated platforms.
- Hearing Protection: Plastic manufacturing equipment such as grinders, mixers, and extruders can produce high noise levels that can cause hearing loss or other hearing-related problems. Workers should wear earplugs or earmuffs to protect their ears from loud noises.
It is essential to note that PPE should not be the only protective measure in plastic manufacturing. Employers should also implement engineering and administrative controls to minimize exposure to hazards. These include machine guards, ventilation systems, and proper training for workers on handling and operating machinery safely.
Hazard Communication in Plastic Manufacturing
Hazard communication is essential to safety management in the plastic manufacturing industry. It refers to the systematic way of conveying information about chemical hazards and safety measures to employees who work with or around hazardous chemicals.
Hazard communication aims to ensure that workers understand the risks associated with the chemicals they handle and can take appropriate safety measures to protect themselves and others.
Importance of Hazard Communication: Hazard communication is critical to the safe handling of chemicals in the plastic manufacturing industry. It is essential to provide workers with the necessary information to protect themselves from hazards and prevent accidents or incidents.
Employers are responsible for communicating hazard information to their employees and providing them with the necessary training to ensure their safety.
OSHA's Hazard Communication Standard: OSHA's Hazard Communication Standard requires employers to communicate information on hazardous chemicals to their employees.
The standard includes requirements for labeling, safety data sheets, and employee training. The goal is to ensure that employees have access to information on hazardous chemicals in their workplace and know how to protect themselves from exposure.
Labeling Requirements: Labeling is an essential component of hazard communication. Chemical manufacturers and importers are required to label all containers of hazardous chemicals with the product name, hazard warnings, and the name and address of the manufacturer or importer.
Employers are responsible for ensuring that labels are not removed or defaced and that all containers are properly labeled.
Safety Data Sheets: Safety data sheets (SDSs) provide detailed information on hazardous chemicals, including their physical and chemical properties, health effects, and emergency procedures.
Employers must obtain SDSs for all hazardous chemicals in their workplace and make them available to employees. SDSs should be accessible to employees and located in a central location in the workplace.
Employee Training: Employers must provide employees with training on the hazards of the chemicals they work with and the appropriate safety measures to take.
Training should cover the requirements of the Hazard Communication Standard, including labeling, safety data sheets, and emergency procedures. Employees should also be trained on the use of personal protective equipment (PPE) and how to respond to spills or exposures.
Hazardous Chemical Inventory: Employers should maintain an inventory of hazardous chemicals in the workplace. The inventory should include the name of the chemical, the manufacturer, and the location of the chemical in the workplace. The inventory is useful for emergency responders in the event of an accident or spill.
Emergency Procedures: Employers should have emergency procedures in place in the event of a chemical spill or exposure. Employees should be trained on emergency procedures, including how to respond to a spill or exposure, use emergency equipment, and evacuate the area.
Employers should also have an emergency response team in place to handle spills or exposures.
Ergonomic Considerations in Plastic Manufacturing
Plastic manufacturing involves various processes that require a lot of manual work. Workers are required to lift, carry, push, and pull heavy loads, work in awkward postures, and perform repetitive motions.
These activities can result in work-related musculoskeletal disorders (WMSDs), which can be debilitating and costly for both employees and the company. To prevent WMSDs, it is essential to consider ergonomic factors in plastic manufacturing.
Here are some of the ergonomic considerations that can help reduce the risk of WMSDs:
- Workstation design: The design of the workstation should take into consideration the worker's body size, the task to be performed, and the tools and equipment required. The workstation should be adjustable to accommodate different body sizes and allow workers to work in a neutral posture.
- Tool and equipment design: The design of tools and equipment should be ergonomic to minimize the amount of force required to use them. Tools should be designed to fit the worker's hand, and the handles should be cushioned to reduce pressure on the hand.
- Manual material handling: Manual material handling is one of the leading causes of WMSDs in plastic manufacturing. Employers should provide lifting equipment such as forklifts, hoists, and conveyors to reduce the amount of manual material handling required by workers.
- Training: Proper training in ergonomics can help workers identify ergonomic risk factors and learn how to prevent WMSDs. Workers should be trained on proper lifting techniques, the importance of taking breaks, and how to adjust workstations to fit their body size.
- Job rotation: Job rotation can help reduce the risk of WMSDs by allowing workers to perform different tasks throughout the day. This reduces workers' time in awkward postures or performing repetitive motions.
- Breaks: Frequent breaks can help reduce the risk of WMSDs by allowing workers to rest and recover. Breaks should be provided frequently, and workers should be encouraged to take them.
- Posture: Workers should be encouraged to maintain a neutral posture while working. This means keeping their back straight, shoulders relaxed, and feet flat on the floor.
Chemical Safety in Plastic Manufacturing
Chemical hazards in plastic manufacturing:
- Plastic manufacturers use a variety of chemicals, such as monomers, solvents, and catalysts, which can be hazardous to worker health.
- Exposure to these chemicals can cause skin and eye irritation, respiratory problems, and even cancer.
- Some chemicals, such as vinyl chloride, are highly toxic and can cause serious health problems with even short-term exposure.
- Handling and storing chemicals can also pose a significant hazard, as they may be flammable, explosive, or reactive.
The importance of chemical safety:
- Chemical safety is crucial in plastic manufacturing to protect workers from exposure to hazardous chemicals.
- It is also important to protect the environment from the release of harmful chemicals.
- Poor chemical safety can result in serious injuries or illnesses and can also result in costly fines and legal action.
Chemical safety measures:
- Employers should provide workers with appropriate personal protective equipment (PPE) to prevent skin and respiratory exposure to chemicals.
- Employers should also ensure proper ventilation in areas where chemicals are used, stored, or transported.
- Labels and safety data sheets (SDS) should be available for all chemicals used in the workplace.
- Workers should be trained in properly handling and storing chemicals, including proper disposal procedures.
- Employers should conduct regular hazard assessments to identify potential chemical hazards and implement appropriate control measures.
Chemical safety regulations:
- Several regulations govern chemical safety in the workplace, including the Occupational Safety and Health Administration's (OSHA) Hazard Communication Standard.
- This standard requires employers to communicate information about hazardous chemicals to workers, including labeling requirements and SDS availability.
- The Environmental Protection Agency (EPA) also regulates the use of chemicals in manufacturing to protect the environment from harmful chemical exposure.
Chemical safety best practices:
- Employers should develop and implement a comprehensive chemical safety program, including hazard assessment, worker training, and PPE selection and use.
- Employers should also ensure that all chemicals are properly labeled and stored and that safety data sheets are easily accessible to workers.
- Regular safety audits and hazard assessments should be conducted to ensure that chemical safety protocols are effective and up-to-date.
- Employers should also consider substituting hazardous chemicals with less hazardous alternatives where possible.
Fire Safety in Plastic Manufacturing
Fire safety is critical to any manufacturing facility, and plastic manufacturing is no exception. The nature of plastic production involves high temperatures, flammable materials, and various ignition sources, making the risk of fires significant. Here are some essential points about fire safety in plastic manufacturing:
- Understanding the Risks: It is crucial to understand the potential hazards in the manufacturing process that could lead to fires. The various materials used in plastic production are highly flammable, and the high temperatures involved in the manufacturing process can ignite these materials. Additionally, the presence of ignition sources, such as electrical equipment, hot surfaces, and friction from machinery, could spark fires.
- Fire Prevention: Prevention is the best approach to fire safety. Conduct regular equipment maintenance and keep machinery clean and free from debris. Install spark detection systems to detect any sparks that could cause fires, and use flame-resistant materials for construction. Proper storage and handling of flammable materials is also important. Maintain clear, unobstructed pathways and exits for easy evacuation in case of fire. Incorporate fire alarm inspection software to ensure all alarms are functioning properly and are regularly inspected.
- Fire Suppression Systems: Fire suppression systems such as sprinklers, water mist systems, or clean agent systems can help suppress fires before they spread. These systems should be regularly maintained and tested to ensure they are in proper working condition.
- Emergency Response Plan: Develop an emergency response plan to ensure a timely and efficient response to any fire outbreak. The plan should include a clear evacuation procedure and assign specific roles and responsibilities to employees to ensure everyone knows what to do in case of a fire.
- Regulatory Compliance: Plastic manufacturing facilities must comply with local and national fire safety regulations. Compliance ensures that the facility is equipped with the necessary safety measures to prevent fires, suppress them if they occur, and ensure safe evacuation in case of a fire.
Electrical Safety in Plastic Manufacturing
The use of electricity in plastic manufacturing processes is vital for the production of high-quality products. However, it poses a risk to workers if not handled properly. Therefore, electrical safety is essential in plastic manufacturing to prevent accidents, injuries, and loss of life.
Importance of Electrical Safety in Plastic Manufacturing:
Electricity is used to power various machines and equipment in plastic manufacturing. However, it is crucial to ensure that the equipment is used safely to avoid hazards such as electrocution, electric shock, and electrical burns. Workers need to be trained on electrical safety and use personal protective equipment (PPE) when working around electrical equipment.
Common Hazards in Electrical Equipment:
The following are some common hazards associated with electrical equipment in plastic manufacturing:
- Electric shock: Electric shock occurs when the body is exposed to an electrical current, causing a flow of electric charge through the body. It can result in burns, heart failure, or even death.
- Arc flash: Arc flash occurs when an electrical current flows through the air between two conductors, causing a bright flash of light and intense heat. It can cause burns, eye damage, and hearing loss.
- Electromagnetic fields: Electromagnetic fields (EMF) are generated by electrical equipment and can cause biological effects such as headaches, nausea, and fatigue.
- Electrical burns: Electrical burns occur when the skin comes into contact with an electrical current. They can be severe and cause permanent damage to the skin and underlying tissues.
Measures for Electrical Safety:
The following measures can be taken to ensure electrical safety in plastic manufacturing:
- Regular maintenance of electrical equipment: Regular maintenance of electrical equipment is essential to ensure that it is in good working condition and safe to use.
- Proper grounding of electrical equipment: Grounding ensures that electrical equipment is connected to the ground to prevent electrical shocks.
- Use of circuit breakers: Circuit breakers protect electrical equipment from electrical surges and prevent electrical fires.
- Proper labeling of electrical equipment: Proper labeling of electrical equipment ensures that workers are aware of the potential hazards associated with each piece of equipment.
- Use of personal protective equipment (PPE): Workers should use PPE such as gloves, safety glasses, and insulated tools when working around electrical equipment.
Machine Guarding in Plastic Manufacturing
Machine guarding is critical to workplace safety, particularly in plastic manufacturing, where machines and equipment are used to shape, mold, and cut plastic materials.
Without proper machine guarding, workers are at risk of injury or even death from the moving parts of machines or accidental contact with hazardous materials.
Understanding the Purpose of Machine Guarding: Machine guarding is an essential safety measure that aims to protect workers from the potential hazards associated with machines and equipment used in the manufacturing process.
The primary purpose of machine guarding is to prevent accidental contact with moving parts, such as belts, gears, pulleys, or blades, that can cause serious injuries or even death.
Types of Machine Guarding: Different types of machine guards can be used in plastic manufacturing, depending on the machine or equipment used. Some common types of machine guards include barrier guards, fixed guards, interlocked guards, and adjustable guards.
Each type of machine guard serves a specific purpose and is designed to protect workers from specific hazards.
Best Practices for Machine Guarding: To ensure the safety of workers in plastic manufacturing, it is crucial to follow best practices for machine guarding. This includes conducting regular risk assessments to identify potential hazards and designing, installing, and maintaining machine guards that meet industry standards and regulations.
Additionally, all workers must be trained on the proper use and maintenance of machine guards and be required to wear appropriate personal protective equipment (PPE) when working with machines and equipment.
The Role of Employers: Employers have a critical role to play in ensuring machine guarding is implemented effectively in plastic manufacturing facilities. Employers must ensure that all machines and equipment are equipped with the appropriate machine guards and that workers are properly trained on their use.
Employers must also conduct regular inspections and maintenance of machine guards to ensure they are functioning correctly and replace or repair them as needed.
The Importance of Worker Involvement: Worker involvement is essential in ensuring machine guarding is effective in plastic manufacturing. Workers should be involved in the risk assessment process and in the selection and installation of machine guards.
Additionally, workers must be trained on the proper use and maintenance of machine guards and encouraged to report any issues or concerns about machine guarding.
The Consequences of Inadequate Machine Guarding: Failure to implement adequate machine guarding can result in serious injuries or even death to workers. Additionally, inadequate machine guarding can result in regulatory fines, legal liability, and damage to the company's reputation.
Lockout/Tagout Procedures in Plastic Manufacturing
Lockout/tagout (LOTO) is a safety procedure that ensures machinery and equipment are completely shut off and cannot be restarted before maintenance or repair work is performed.
In plastic manufacturing, where machinery and equipment are utilized extensively, LOTO is essential to protect workers from the hazards associated with working on or around machines. Below are some points outlining the importance of LOTO procedures in plastic manufacturing:
Overview of Lockout/Tagout Procedures: Lockout/tagout is a process that requires employees to follow specific procedures when working on or around machines that could cause injury if they were to start unexpectedly. The procedures involve isolating the machine from all energy sources, including electricity, hydraulics, and pneumatics.
Once the machine is isolated, a lockout or tagout device is placed on it, indicating that the machine will not be used until the authorized person removes the device.
Importance of LOTO Procedures: The primary purpose of lockout/tagout procedures is to prevent the accidental start-up of machines or equipment, which could result in serious injury or death.
In the plastic manufacturing industry, machinery and equipment often involve high speeds, moving parts, and hot or sharp materials, so implementing LOTO procedures to protect workers from potential hazards is essential.
Elements of an Effective LOTO Program: An effective LOTO program should include written procedures, employee training, regular inspections, and equipment maintenance.
Written procedures should include a detailed explanation of how to perform LOTO procedures and the roles and responsibilities of each employee involved. Employee training should cover the importance of LOTO procedures, how to perform them, and what to do in case of an emergency.
Regular inspections should ensure that all equipment is in proper working condition and lockout/tagout devices are properly used. Finally, equipment maintenance should be performed regularly to minimize the risk of equipment failure.
LOTO Devices: LOTO devices are used to ensure that machinery or equipment cannot be started while maintenance or repair work is being performed.
Many types of LOTO devices are available, including lockout hasps, lockout tags, lockout tape, and cable lockout devices. These devices are designed to be easy to use and prevent machinery or equipment's accidental start-up.
Training and Education: Implementing LOTO procedures requires proper training and education for all employees involved. Workers must be trained in the proper use of lockout/tagout devices and procedures and the potential hazards associated with machinery and equipment.
They should also be educated on the importance of following safety guidelines and procedures to prevent accidents and injuries.
Compliance with OSHA Standards: The Occupational Safety and Health Administration (OSHA) has established specific standards for lockout/tagout procedures in the workplace.
These standards are designed to protect workers from potential hazards associated with machinery and equipment. Compliance with OSHA standards is essential to ensure a safe and healthy work environment for all employees.
Benefits of LOTO Procedures: Implementing LOTO procedures provides numerous benefits to both workers and employers. By implementing proper LOTO procedures, workers are protected from potential hazards associated with machinery and equipment, reducing the risk of accidents and injuries.
Employers also benefit from reduced liability and decreased downtime due to accidents and injuries.
Emergency Response in Plastic Manufacturing
Emergency Response Plan
The first step in emergency response is to have an Emergency Response Plan (ERP) in place. An ERP is a written document that outlines the procedures for responding to emergencies such as fires, chemical spills, and other incidents.
The ERP should include contact information for emergency services, evacuation procedures, and the responsibilities of employees during an emergency.
First Aid and Medical Treatment
Injuries can occur during plastic manufacturing, and it is important to have first aid supplies and trained personnel available. The ERP should include procedures for providing first aid and emergency medical treatment.
Employees should be trained in basic first aid procedures such as CPR and the use of a defibrillator.
Communication
Clear communication is crucial during an emergency. The ERP should include procedures for communicating with employees, emergency services, and other stakeholders. It is essential to have a system for quickly notifying all employees of an emergency and providing updates throughout the emergency.
Equipment and Facilities
Having the right equipment and facilities in place can help minimize the damage caused by an emergency. This includes fire suppression equipment such as fire extinguishers and sprinkler systems, emergency lighting, and evacuation routes. It is important to regularly inspect and maintain this equipment to ensure it is functioning correctly.
Regular Drills
Regular emergency response drills are essential to ensure that employees know what to do in an emergency. The ERP should include procedures for conducting drills, and all employees should be required to participate.
Regular drills help identify potential problems with emergency response procedures and allow for adjustments before an actual emergency occurs.
Post-Emergency Review
After an emergency, it is important to conduct a review to identify what worked well and what needs to be improved.
This review should be conducted as soon as possible after the emergency and involve all employees who were involved in the response. The review results should be used to update the ERP and improve emergency response procedures.
Health and Wellness Programs for Plastic Manufacturing Workers
Plastic manufacturing is an industry that requires a lot of physical and mental effort, and workers in this industry can be at risk of various health issues. Health and wellness programs can help employees maintain good health, reduce the risk of injuries, and improve their overall quality of life.
Here are some points on health and wellness programs for plastic manufacturing workers:
Importance of health and wellness programs:
- Health and wellness programs help workers maintain their physical and mental well-being, which can lead to increased productivity, fewer accidents, and lower healthcare costs for employers.
- These programs can also improve employee morale, job satisfaction, and retention rates, as workers feel valued and supported by their employers.
- In addition, by promoting healthy habits and reducing the risk of illness, health and wellness programs can benefit the wider community by decreasing the spread of communicable diseases and reducing the burden on healthcare systems.
Components of health and wellness programs:
- Health and wellness programs can include a wide range of activities, such as fitness classes, health screenings, mental health counseling, nutrition education, and smoking cessation programs.
- Employers can also offer incentives such as discounts on gym memberships, healthy meal options, and financial rewards for meeting health goals.
- These programs can be tailored to the specific needs and interests of employees and can be delivered through a variety of channels, including in-person classes, online resources, and mobile apps.
Benefits of physical activity:
- Physical activity is an important component of health and wellness programs, as it can help workers maintain a healthy weight, reduce the risk of chronic diseases, and improve mental health and mood.
- In addition, regular exercise can help workers build strength, endurance, and flexibility, reducing the risk of musculoskeletal injuries on the job.
- Employers can encourage physical activity by providing on-site fitness classes, organizing walking or running clubs, or providing access to fitness equipment in the workplace.
Importance of mental health support:
- Mental health is an important aspect of overall well-being, and workers in the plastic manufacturing industry may be at risk of stress, anxiety, or depression due to the demands of their job.
- Employers can provide access to mental health counseling or resources to help workers manage stress and maintain a healthy work-life balance.
- Additionally, employers can promote a positive workplace culture by encouraging open communication, offering flexible work schedules, and providing opportunities for professional development and growth.
Nutrition education:
- Good nutrition is an important part of maintaining overall health and can help workers maintain a healthy weight, reduce the risk of chronic diseases, and increase energy and productivity.
- Employers can offer nutrition education classes or workshops, provide healthy meal options in the workplace, or offer incentives for employees to make healthier food choices.
- Additionally, employers can provide resources or referrals to registered dietitians or nutritionists to help workers develop personalized nutrition plans.
Importance of sleep:
- Adequate sleep is essential for overall health and well-being, and can help workers stay alert, focused, and productive on the job.
- Employers can promote good sleep habits by offering flexible work schedules, limiting overtime, and providing a comfortable and quiet work environment.
- Employers can also provide education on good sleep habits and encourage workers to prioritize sleep as part of their overall health and wellness routine.
Safety Culture in Plastic Manufacturing
Safety culture refers to an organization's attitudes, beliefs, perceptions, and values regarding safety. It includes the organization's commitment to safety, the level of communication and collaboration among employees regarding safety, and the level of employee engagement and participation in safety-related activities.
Safety culture is essential in the plastic manufacturing industry, where workers are exposed to numerous hazards and risks. Creating and maintaining a safety culture can help reduce the number of accidents and injuries in the workplace, as well as increase productivity and morale among workers.
Here are some key points to consider when building a safety culture in plastic manufacturing:
- Leadership and Management Commitment: Building a safety culture starts with strong leadership and management commitment to safety. The management should take the lead in promoting a safety culture by prioritizing safety, providing resources for safety initiatives, and actively participating in safety activities.
- Communication and Collaboration: Open communication and collaboration between employees and management is essential for promoting safety in the workplace. Workers should be encouraged to report hazards and incidents without fear of retaliation, and management should take immediate action to address any concerns raised by workers.
- Continuous Improvement: A safety culture should be continuously improved by regularly reviewing and updating safety policies, procedures, and practices. This involves conducting regular safety audits, analyzing incident reports, and implementing corrective actions to prevent future incidents.
- Employee Engagement and Participation: Encouraging employee engagement and participation in safety initiatives can help build a strong safety culture. Workers should be involved in identifying and mitigating hazards, participating in safety committees, and providing feedback on safety policies and practices.
- Recognition and Reward: Recognizing and rewarding workers for their safety contributions and achievements can help reinforce a safety culture. This can include safety bonuses, safety awards, and public recognition for safety accomplishments.
- Risk Assessment: Regularly assessing the risks and hazards in the workplace can help identify potential safety issues and prevent accidents. Risk assessment involves identifying hazards, evaluating the likelihood and severity of potential incidents, and implementing controls to mitigate the risks.
- Safety Data Analysis: Analyzing safety data, such as incident reports and injury rates, can help identify patterns and trends that can inform safety initiatives. Data analysis can also help evaluate the effectiveness of safety policies and practices.
How Deskera Can Assist You?
Deskera MRP allows you to closely monitor the manufacturing process. From the bill of materials to the production planning features, the solution helps you stay on top of your game and keep your company's competitive edge.
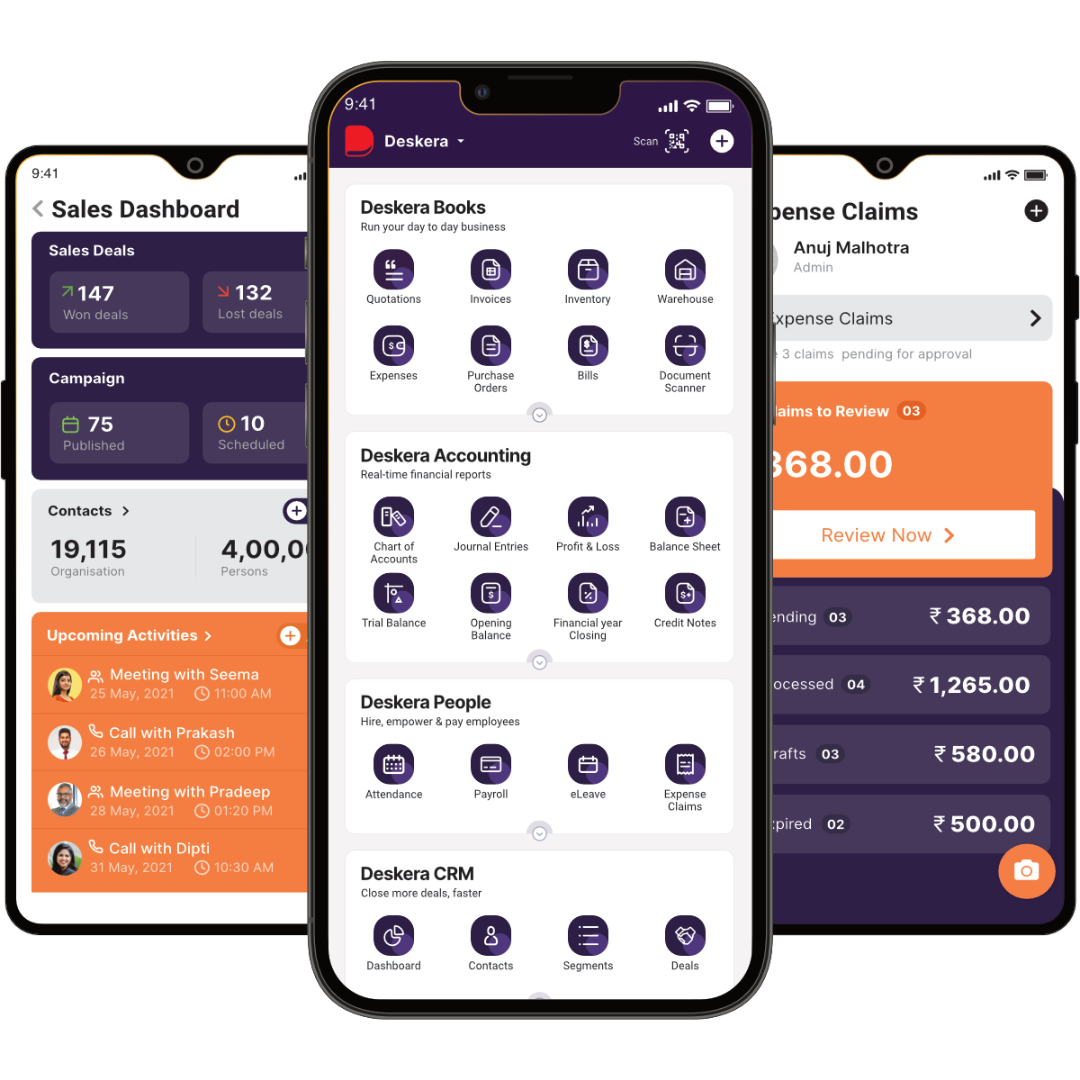
Deskera ERP and MRP system can help you:
- Manage production plans
- Maintain Bill of Materials
- Generate detailed reports
- Create a custom dashboard
Deskera ERP is a comprehensive system that allows you to maintain inventory, manage suppliers, and track supply chain activity in real-time, as well as streamline a variety of other corporate operations.
Deskera Books enables you to manage your accounts and finances more effectively. Maintain sound accounting practices by automating accounting operations such as billing, invoicing, and payment processing.
Deskera CRM is a strong solution that manages your sales and assists you in closing agreements quickly. It not only allows you to do critical duties such as lead generation via email, but it also provides you with a comprehensive view of your sales funnel.
Deskera People is a simple tool for taking control of your human resource management functions. The technology not only speeds up payroll processing but also allows you to manage all other activities such as overtime, benefits, bonuses, training programs, and much more. This is your chance to grow your business, increase earnings, and improve the efficiency of the entire production process.
Conclusion
Protecting plastic manufacturing workers from potential hazards is critical to ensuring the industry's sustainability. The process starts with identifying the potential hazards, assessing the risks associated with them, and implementing control measures to minimize the likelihood of accidents and injuries.
Employers must prioritize the health and safety of their workers by providing them with the appropriate personal protective equipment and conducting regular training sessions to enhance their awareness of potential hazards.
Employers must also ensure that their workers know emergency procedures and evacuation plans in case of accidents or other unforeseen incidents. In addition, employers must implement effective communication channels that enable workers to report any safety concerns or issues they encounter during their work.
Ultimately, it is essential to recognize that protecting plastic manufacturing workers from potential hazards is a moral responsibility and a legal obligation. As such, companies must adhere to relevant safety regulations and guidelines to minimize the risk of legal action resulting from accidents or injuries in the workplace.
With proper attention to safety and a commitment to ongoing improvements in hazard identification and control, the plastic manufacturing industry can continue to thrive while safeguarding the health and well-being of its workforce.
Key Takeaways
- Plastic manufacturing is an important industry, but it comes with potential hazards that can harm workers.
- Workers in plastic manufacturing facilities are exposed to hazards such as noise, fumes, and hazardous chemicals.
- The main objective of plastic manufacturing companies should be to minimize or eliminate risks of exposure to these hazards.
- Employers should conduct risk assessments to identify potential hazards and implement appropriate measures to control or eliminate the risks.
- Personal protective equipment (PPE) such as gloves, eye protection, and respirators can be used to protect workers from chemical hazards.
- Workers should be trained on how to use PPE properly and when to replace it to ensure maximum protection.
- Employers should provide adequate ventilation systems to control fumes, vapors, and other harmful substances in the workplace.
- Good housekeeping practices, such as keeping the workplace clean and orderly, can help reduce the risk of slips, trips, and falls.
- Workers should receive adequate training on handling and using machinery to reduce the risk of injuries.
- Employers should conduct regular maintenance and inspections of machinery to identify and correct any potential hazards.
Related Articles
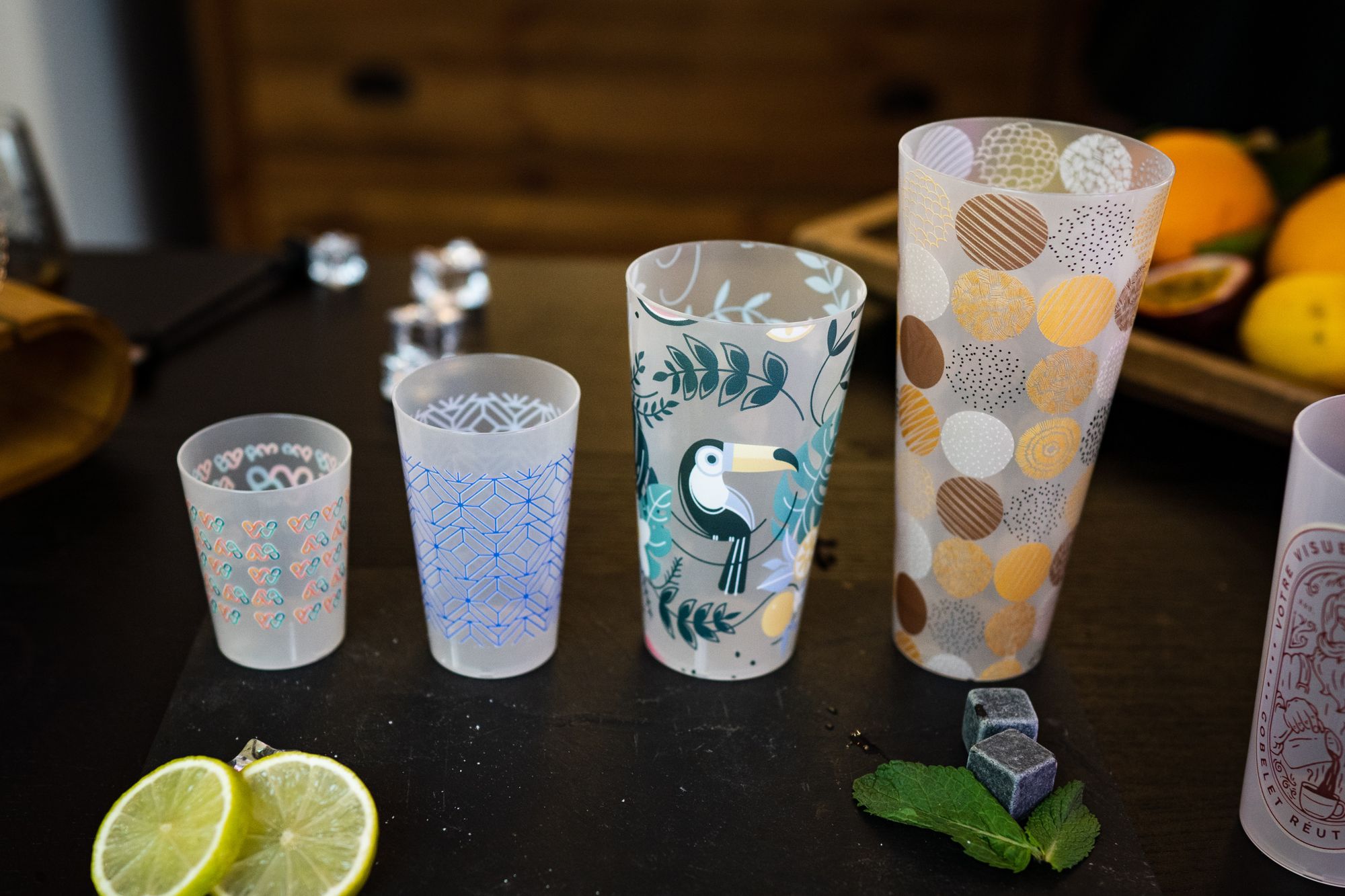
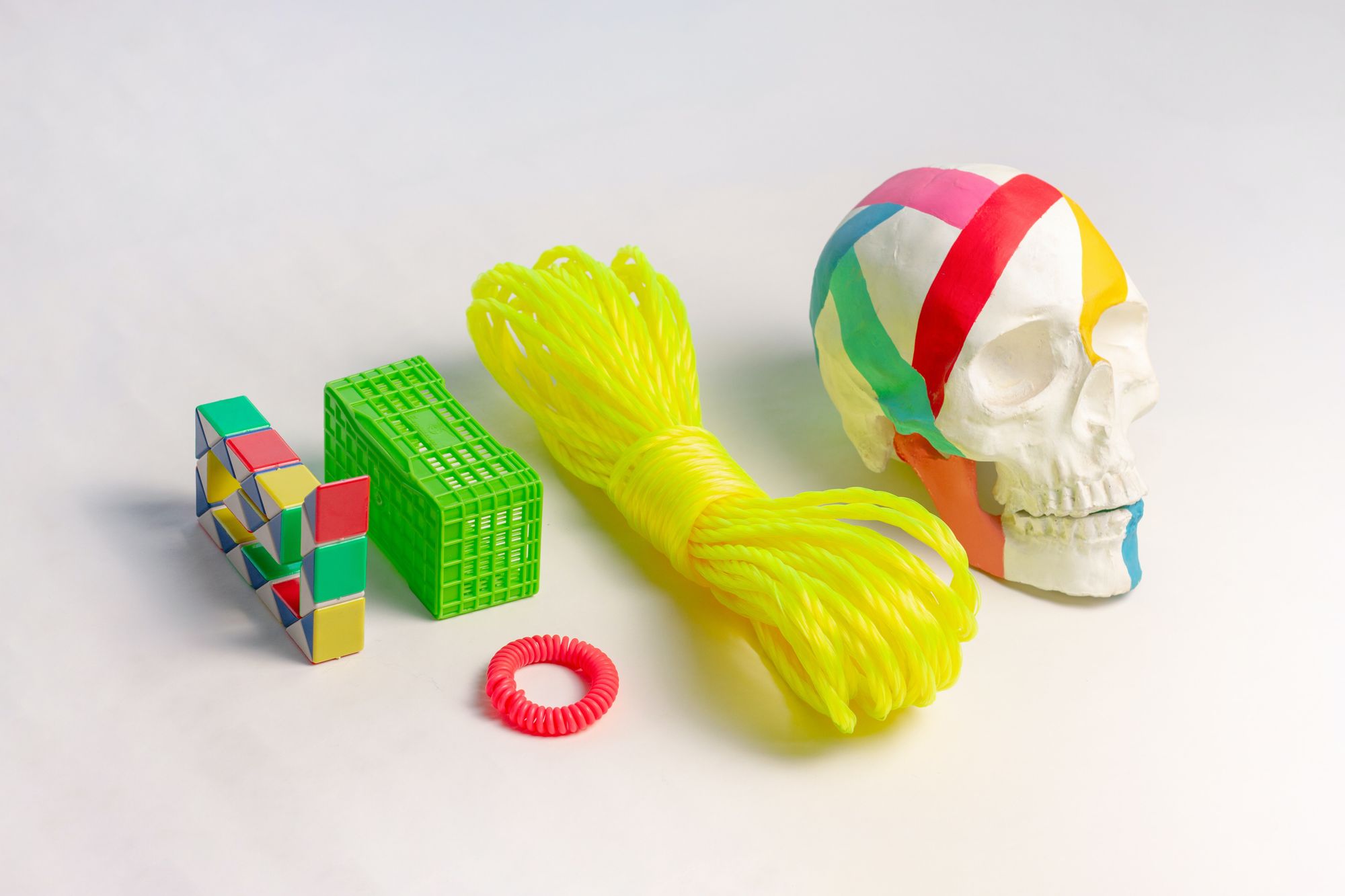
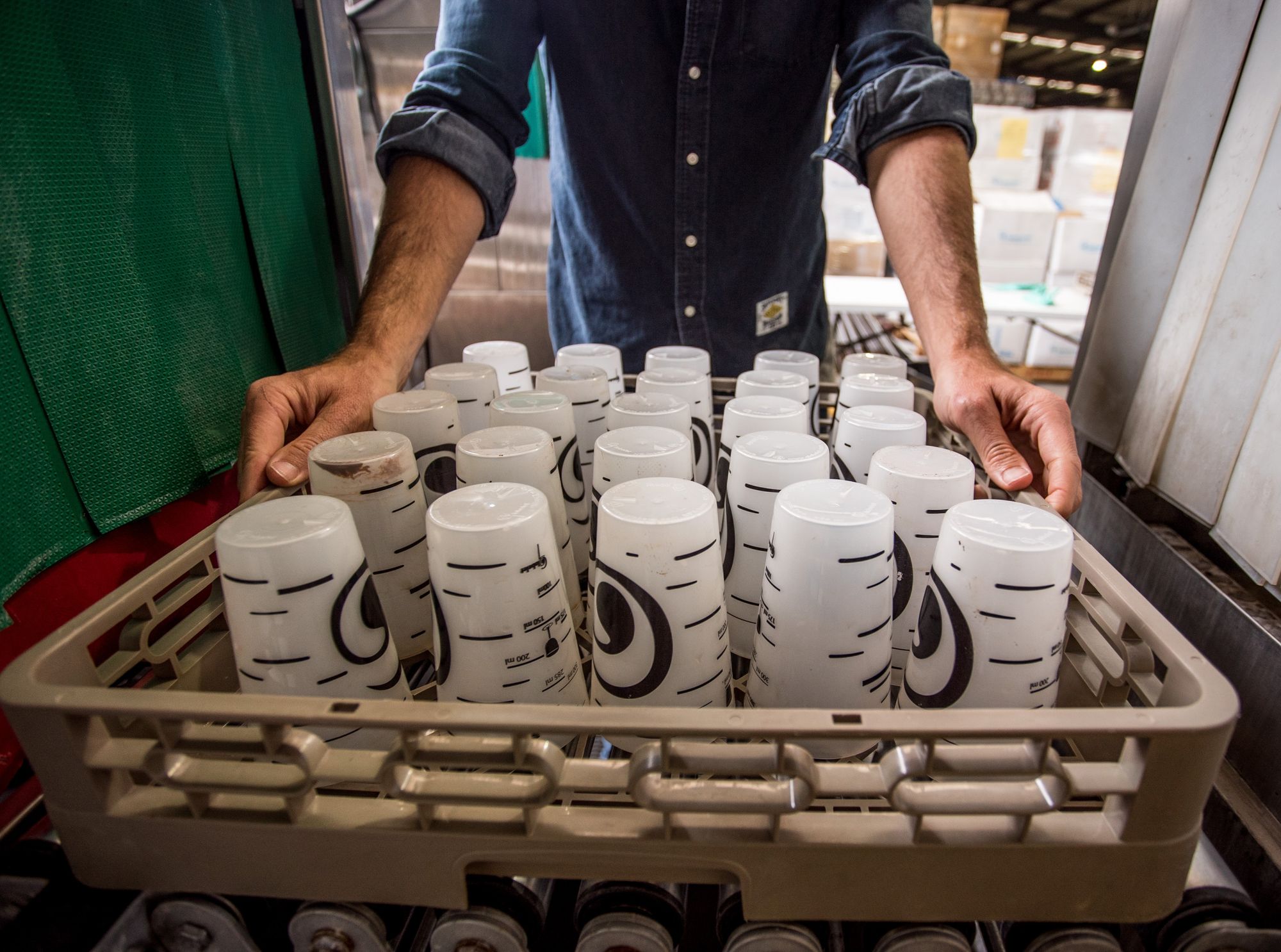
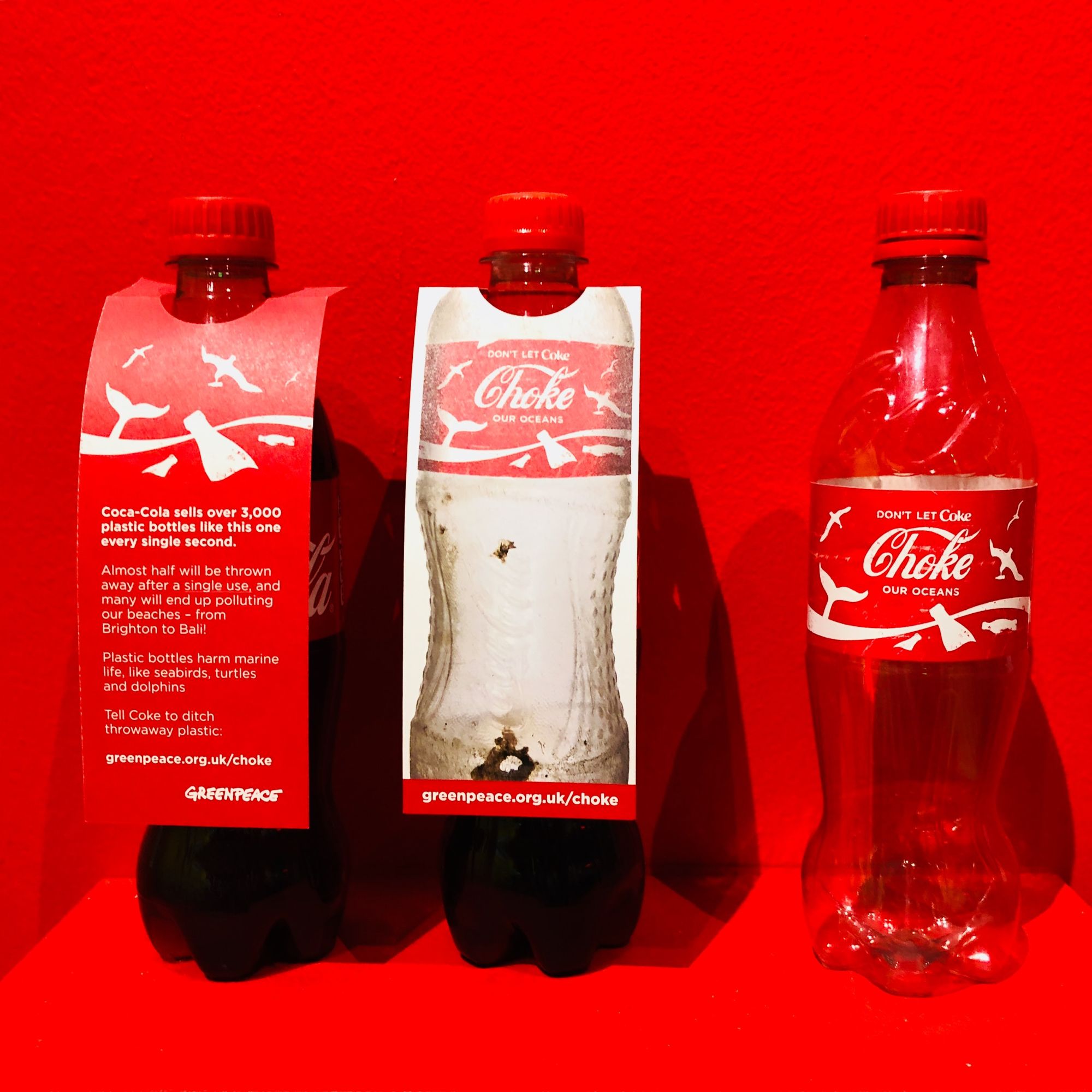